ADTEK CS2-RL User manual

CS2 SERIES –OPERATION MANUAL(EN)-2017-02-09-一般
1 / 39
CS2-RL
LINEARLY LINE SPEED / RPM CONTROLLER
CS2-F
FREQUENCY CONTROLLER
OPERATION MANUAL
■DESCRIPTION
CS2-RL(F) controller has been designed high accuracy measurement, display, control and
communication (Modbus RTU mode) of pulse(Frequency) or AC Frequency.
The innovation feature is auto-range input from 0.01Hz~ 100KHz(~140KHz in option). The display
resolution will be auto-changed to show the highest according to input frequency.
They are also building in 4 Relay outputs, 3 External Control Inputs, 1 Analogue output and 1
RS485(Modbus RTU Mode) interface with versatile functions such as control, alarm,
re-transmission and communication for a wide range of testing and machinery control
applications. Please refer to the detail description on pages 2/38~7/38.
There are not only controllers, but also an I/O interface in any system. ADtek built in
difference ideal for External Control input and Relay output as like as I/O module of PLC. It’s very
connivance to achieve remote monitoring and control by CS2 series.
■FEATURES
●Accuracy: ± 0.005%; Display range: 0~99999; Auto-range with Decimal
Point auto changed according to input frequency.
●Optional 4 relay can be programmed individual to be a Hi / Lo / Hi Latch
/ Lo Latch / Go energized with Start Delay / Hysteresis / Energized &
De-energized Delay functions, or to be a remote control.
●Analogue output and RS 485 communication port in option
●3 external control inputs can be programmed individual to be Tare
(Relative PV) / PV Hold / Maximum or Minimum Hold / DI (remote
monitoring) / Reset for Relay Energized Latch…. In standard.
●EMC, EMI, LVD Approved & RoHS
【CS2-RL LINEARLY LINE SPEED / RPM CONTROLLER】
●Measuring RPM / Linearly line speed / Frequency AUTO RANGE
0.01~100KHz / ~140KHz(optional) / Contact, NPN, PNP, Voltage pulse
can be switch on rear of meter.
【CS2-F FREQUENCY CONTROLLER】
●Measuring Frequency AUTO RANGE 0.01~100KHz /
~140KHz(optional) / Voltage pulse or sine wave(specify).
■APPLICATIONS
Models
●CS2-RL Motor Control / Machinery / Testing Equipments for Measuring, Alarm and Communication with
PC/PLC
Flexible 3 DI functions as like as Maximum/Minimum hold, PV hold and Relative PV.
On line testing station for appliance, check points of PCB as so on.
●CS2-F Switch Boards / Testing Equipments for Measuring, Alarm and Remote I/O with PC/PLC
Fantastic 4 Relay functions as like as Hi / Lo / Hi latch / Lo latch / DO(Remote control by PC/PLC).
Flexible 3 DI functions as like as Reset for Relay energized latch and Remote monitoring by PC/PLC.
Functions
●Safety & Protection Hi/Lo alarm and latch(hIhld / lOhld), Analogue output limited(aOlmt)
●Testing & Measuring Maximum/Minimum hold(maXhd / miNhd), PV hold(pVhld), Relative
PV/Tare/∆PV(reLpv)
●Remote Monitoring & Control RS485 communication port, Display function(rs485), ECI input
status( di), Relay energized( do)

CS2 SERIES –OPERATION MANUAL(EN)-2017-02-09-一般
2 / 39
■FUNCTION DEFINE
■Character Symbol
Factor function:
Settable range: 0.001~9.999
Display = Value of math with setting x Factor
The display can be proportioned by factor.
The typical application is compensation for gear
ratio.
Auto-range function:
Programmable: auto / semi / manul
●auto(Auto range):The decimal point will be auto
changed according to the input frequency so that
keep the display in the highest resolution.
Ex.: RPM of Motor: 7200RPM,Encoder: 1000ppr
The meter setting
[pVtyp]: rpm, [ppr]: 1000,
[range]: auto
(7200rpm x 1000ppr) / 60 = 120.000kHz
Frequency range is from 0~120.000kHz
The table is between input and display as below,
Freq. Input Display
0Hz 0.0000 RPM
166.65Hz 9.9999 RPM
1666.5Hz 99.999 RPM (Auto change)
16.665kHz 999.99 RPM (Auto change)
16.666kHz 1000.0 RPM (Auto change)
120kHz 7200.0 RPM
The input goes down to
166.65Hz 9.9999 RPM (Auto change)
●semi(Semi-Auto range):The decimal point will
be auto changed according to the input frequency
to keep the display in the highest resolution, but it
must be under setting position of decimal point.
It’s possible to show “ ovfl(overflow)”, if the input
frequency is too high to makeover the display
range.
Ex.: RPM of Motor: 7200RPM,Encoder: 1000ppr
as same as above,
The meter setting
[pVtyp]: rpm;[ppr]: 1000
[range]: semi;[dp]: 0.00
The table is between input and display as below,
Freq. Input Display
0Hz 0.0000 RPM
166.65Hz 9.9999 RPM (Auto change)
1666.5Hz 99.999 RPM (Auto change)
16.665kHz 999.99 RPM (Auto change)
16.666kHz ovfl RPM
120kHz ovfl RPM
The input goes down to
16.665kHz 999.99 RPM (Auto change)
In the case of input, the [dp]should set 0.0
to display full range of RPM and to get higher
resolution in lower RPM.
A b C d E F G H i J K L M
a b c de f gh i j kl m
n o P q r S t U v W X y Z
no p qr s t u v w x y z
1 2 34 5 6 7 8 90 / .
1234567 8 90/.
■Input Range & Mode
Input Range
The meter has been designed very wide input
range from 0.01Hz~100.00KHz(Option:
0.01Hz~140.00KHz) that can cover almost any
application for frequency measuring. User doesn’t
need to specify the input range.
Especially, they do not set the scale to relate
the input range. Users are just set the measuring
type(pVtyp) in [input group]. The display of
meter will show the value that user wants to show
such as RPM, Linearly Line Speed or Frequency.
Please refer to the description of Display Function.
Input mode Switchable
NPN / PNP / Voltage Pulse / Mech. Contact
and amplitude can be switched by switches on
rear of meter.
21
22
24
25
23
27
28
26
29
30
31
33
32
34
11
12
14
15
13
Dip
Switch
7
8
9
10
5
6
3
4
DIP SW
1
2
3
4
5
NPN
ON
PNP
ON
M.C.
ON
ON
5VP
12VP
ON
24VP
ON
D-S is on when it is in down site.
*The excitation supply of sensor can not be
changed. Please specify in ordering code.
■Display Functions
Multi-Display function
Programmable: lNspd / rpm / rps / hz
/ khz
The meter has desgined for mult-purpose. User
can set the display purpose in [pVtyp]of [input
group]such as lNspd(Linearly Line Speed),
rpm(RPM), rps(RPS), hz(Hz), khz
(kHz) that the meter will display according to the
input and setting to calculate. The meter will show
the relation parameters as below,
●lNspd: Pulse/rotation( ppr), Engineer
Units( m/mn / cm/mn / yd/mn / ft/mn),
Diameter of rotordiamt)
●rpm / rps: Pulse/rotation( ppr)
Auto change to
keep highest
resolution
Auto change to
keep highest
resolution

CS2 SERIES –OPERATION MANUAL(EN)-2017-02-09-一般
3 / 39
●manul(Manual range):The decimal point will be
fixed according to the setting of [dp]. The meter
will show ovfl(overflow), once the input goes
over the frequency that is relative 99999.
Ex.: RPM of Motor: 7200RPM,Encoder: 1000ppr
as same as above,
The meter setting
[pVtyp]: rpm;[ppr]: 1000
[range]: manul;[dp]: 0.00
The table is between input and display as below,
Freq. Input Display
0Hz 0.00 RPM
166.65Hz 9.99 RPM
1666.5Hz 99.99 RPM
16.665kHz 999.99 RPM
16.666kHz ovfl RPM
120kHz ovfl RPM
The input goes down to
16.665kHz 999.9 RPM
In the case of input, the [dp]should set
0.0to display full range of RPM.
Time out function
Programmable: auto / manul
In the case of low frequency, the meter can not to
identify that is low frequency and no input until the
next pulse input. Sometimes, it takes a long
period.
The meter builds in a time out function to cut out
the display to be “0”.
There are two modes auto / manul can be
programmed as below,
●manul(Manual): There is a period named ito
(input time out) can be set from 0.0sec~999.9sec.
The display will be “0”, once the next pulse doesn’t
input during the setting time.
●auto(Auto): The display will be “0”, once the next
pulse doesn’t input during the time that gave by
formula of meter’s firmware. Gerenally, the auto
time out is 4 times of 1/ frequency of last input
frequency.
Max / Mini recording
In order to review & trace the drifting PV, the
meters will keep the values of maximum and
minimum in [user level]during power on.
The maximum and minimum can be reset by
[ ecI_] or front key function. Please refer to the
operation on their description as below.
Maximum Hold or Minimum Hold for PV
When the [dsply]function in [input group]set
to be maXhd(Max. Hold) or miNhd(Mini. Hold), that
the meter will still display the values of PV in
maximum (or minimum) and the relative square
orange LED will be bright during power on, until
manual reset by front key in [user level],
Up/Down Key function has been done or ECI
terminal had been closed, if the ECI has set Mrst.
The meter will update immediately new
maximum(minimum) values after ECI is to be
opened, or press Up/Down Key again.
The Reset functions will be described in ECI
functions.
Please paste the sticker
M.H
on the right side of
orange square LED to identify the status of display.
Max. ( Mini.) Hold & Reset
Reset the Max
(Mini) Hold by
E.C.I. or F. Key
O
N
Level
Trigger
Maximum Hold
Present
Value
maXh
[dsply]
Mrst
[ecI_]
PV(Present value) Hold
When the [ ecI_](External Control input) set to be
pVhld(PV Hold) function in [eci group], that
display will be hold & kept, and the relative green
LED will be bright, when the ECI has been closed
or Up/Down Key function has been done, until it is
to be opened or press Up/Down Key again.
Please paste the sticker
PV.H
ECI
on the right side of
green square LED of ECI to identify the status of
display.
PV Hold & Reset
Present
Value
Reset Data
Hold by E.C.I.
or Front Key
O
N
Level
Trigger
ON
ON
PV Hold
pVhld
[ecI_]
Remote display by RS485 command
In past, The meter normally receive 4~20mA or
0~10V from AO card or BCD card of PLC. We
built-in a new solution by RS485 remote display
function which it can save costs of AO and wiring
connecting to PLC simultaneously.
When the [dsply]function set to be rs485, the
LED display no longer relative to the input signal on
the meter then the PV screen will show the data
from RS485 command. The data(number) will be
same as PV which it will compare with set-point,
relative to analogue output and ECI functions so
that is to control analogue output, relay energized
and so on.
Low Cut
Settable range from -19999~+29999 counts.
The users can set a value here to cut the display
value to show "0".
●If the setting value is positive, it expressed the
PV will be 0 which it's within the range of
absolute value;
Fix decimal
point resolution

CS2 SERIES –OPERATION MANUAL(EN)-2017-02-09-一般
4 / 39
PV< l Setting value l, the display will be 0
EX: Low Cut is set for 0.50, if the display is from
-0.50~+0.50, that will be 0.
Low Cut set to be +0.50
Low Cut is set for 0.50, if the PV is
from -0.50~+0.50, that display will be 0.
PV according
to input signal
Present
Value
Low cut
function
0.50
-0.50
)50
[lOcut]
●If the setting value is negative, it expressed the
PV will be X which it's under the setting value;
PV< Setting value, the display will be X(Setting
value).
EX: Low Cut is set for -0.01, if the display is <
-0.01, and all the display will be -0.01.
Low Cut set to be -0.10
-0.10
Low cut
function
Low Cut is set for -0.10, if the PV is
under (< = -0.10), that display will be -0.10.
Present
Value
PV according
to input signal
-)10
[lOcut]
Digital Fine Adjustment
Settable range from 0~99999 ;
Users can get "Fine Adjustment PV" by front key
on the meter for higher points, and if the user want
to show the current input signals that “Just Key-In”
the value.
Especially, the [pVspn]is not only in span of PV,
but also any higher point for [pVspn]. The meter
will be linearization automatively for full scale.
The adjustment can be cleared in function [Sclr].
Original display: 1750.0/30Hz
Digital fine adjust.: input 22Hz / 1320.0
New span from 1750.0 to1800.0
SCALE
0Hz
30Hz
15Hz
175)0
87%00
)0000
180)0
22Hz
132)0
INPUT
*Please make sure that the [pVspn]should be
over 50% of input range. That may be made
bigger error in span, if the interval is too narrow.
■Reading Stable Functions
Average Display update
Settable range: 1~99 times;
Jittery Display caused by the noise or unstable
signal. User can set number to average the
readings to get smoothly display.
Remark: The higher average setting will impact the
response time of Relay and Analogue
output slower.
The meter’s sampling is 15cycle/sec. If the
[ avg](Average) set to be 3, the meter will
express the sampling 3 readings and calculating
the average then update the display once. At
meantime, the display update will be 5 times/sec.
Average set to be 3
…….
Sample 1
Sample 2
Sample 3
Sample 4
Sample 5
Sample 6
…….
Display Update Value =
(Sample 1 + Sample 2 + Sample 3)/3
Display Update Value =
(Sample 4 + Sample 5 + Sample 6)/3
Digital filter
Settable range from 0(None)/1~99 times.
The digital filter can reduce the influence of
spark noise caused by magnetic of coil.
If the values of samples are over digital filter
band(fix in firmware and about 5% of stable reading)
3 times (Digital Filter set to be 3) continuously, the
meter will admit the samples and update the new
reading. Otherwise, it will be as treat as a noise
and skip the samples.
Digital Filter set to be 3
Digital Filter Band
The values of samples are
two times only, so that the
reading will admit the
samples.
Digital Filter Function
The values of samples are
over the filter band and three
times, so that the reading will
accept the samples, and
update the reading.
Digital Filter Function
Present
Value
■Front Key Functions
●The
Key can be set to be the same function as
the setting of [ecI1](ECI.1).
Ex. The [ecI1]set to be pVhld and the function
[E1=up]set to be yes in [eci group].
When user presses
Key, the PV will hold as
like as terminals of ECI1 close.
●The
Key can be set to be the same function as
the setting of [ecI2].
Ex. The [ecI2]set to be reLpv and the function
[E2=dn]set to be yes in [eci group].
When user presses
Key, the PV will show
relative value as like as terminals of ECI2
close.
●If the front key function has been set, the
terminal input for ECI will be disabling.

CS2 SERIES –OPERATION MANUAL(EN)-2017-02-09-一般
5 / 39
■Relay Functions
DO
The function has been desgined that is not only a
meter but also a I/O inteface. In the case of motor
control cabnet, it's normally can not get the remote
function. It's very easly to get the status of switch
and remote ON/OFF of the switch from CS2 series
with RS485 function.
If the [ry_.md]has been set do, the relay will
be energized by RS485 command directly, and no
longer to compare with set-point.
Start delay band and Start delay time
The functions have benn desgined for,
1.To avoid alarm for the starting current of
inductive motor(6 times of rated current).
2.If the ry_.md relay energized mode has been set
to be lo(Lo) or lOhld(Lo & latch), the relay
will be energized, when the meter is power on
and no input due to the "0" display. User can set
a band and delay time to inhibit the energized of
relay.
Start band(Fig.2-):
Settable range from 0~9999 Counts
Start delay time(Fig.2-):
Settable range from
0.0(second)~9(minutes)59.9(seconds);
Start Delay
Fig.2
Start Delay Time
Start Band
Hi Setting
Relay
Energized
ON
Inhibit
Inhibit
[ rYsb]
[ry_.sp]
[ rYsd]
Hysteresis(Fig.3-)
Settable range from 0~9999 Counts
The function is to avoid the relay on and off
frequently, when the display value is swing near by
the set point. The typical application is to control a
compressor. User can set a band to prevent the
relay on and off frequently.
Relay energized delay(Fig.3-)
Settable range from
0.0(second)~9(minutes)59.9(seconds);
The function is to avoid the miss action caused by
noise. Sometime, the display value will swing
caused by spark of contactor. User can set a
period to delay the relay energized.
Relay de-energized delay(Fig.3-)
Settable range from
0.0(second)~9(minutes)59.9(seconds)
CS2 series offer the 4 relay outputs with flexible
and versatile functions. They can be programmed
individually in [relay group]。Please refer to the
description as following;
Relay energized mode Hi / Lo / Go-1.2 / Go-2.3 /
Hi.HLd / Lo.HLd / DO
Hi(Fig.1-): Relay will be energized,
when PV > Set Point
Lo(Fig.1-): Relay will be energized,
when PV < Set Point
Go-1.2(Fig.1-): This function is programmable for
Relay 3 or 4 only. If the Relay 4 set to be
Go function, the relay will compare
between [ry1.sp]and [ry@sp].
Go relay energized when the condition is
[ry1.sp](Hi) > PV > [ry@sp](Lo)
Go-2.3(Fig.1-):. This function is programmable
for Relay 4 only. If the Relay 4 set to be
Go function, the relay will compare
between [ry@sp]and [ry#sp].
Go relay energized when the condition is
[ry@sp](Hi) > PV > [ry#sp](Lo)
Hi / Lo / Go Relay Energized
Hi Setting
Hi Relay Energized
ON
Lo Setting
Lo Relay Energized
ON
ON
Go Relay Energized
ON
ON
hi
lo
Go-12
[ry_.sp]
[ry_.sp]
[ry_.md]
Hi.HLd (Lo.HLd)
The relay energized and latched function is for
electrical safety and human protection.
For example, a current meter installed for over
current alarm of motor. Generally, over current of
motor caused by over load, mechenical dead lock,
aging of insulation and so on. In the case of alarm
of meter, if the user doesn't figue out the real
reason and re-start the motor. It may damage the
motor. The function is desgined that must be
manual reset the alarm after checking out and
solving the issue. It's very important idea for
electrical safety and human protection.
If the PV Higher (or lower) than set-point, the relay
will be energized and latch until manual reset by
from key in [user level]or [ eci](ECI) input.
Relay Energized Latch & Reset
Hi. HLd(Hi Latch)
Relay Energized
ON
Reset RelayLatch
by ECI or Front Key
ON
Level Trigger
Hi Setting
hIhld
[ry_.md]
rYrst
[ eci._]
[ry_.sp]

CS2 SERIES –OPERATION MANUAL(EN)-2017-02-09-一般
6 / 39
Energized / De-energized
Delay & Hysteresis
Fig.3
ON
Hysteresis
De-energized
delay time
Hi Setting
Relay
Energized
[ry_.sp]
[ry_.hy]
[ry_.rd]
[ry_.fd]
Energized delay time
Reset for Relay Energized Latch
If the relay energized mode has been set to be
hIhld(Energized latch), and the [ ecI_]can be
set to be rYrst(Reset Relay function). When the
PV meets the condition of relay energizing, the
relay will be energized and latch until the ECI is to
be closed.
■Analogue Output Functions
Please specify the output type either a 0~10V
■3 External Control Inputs(ECI)

CS2 SERIES –OPERATION MANUAL(EN)-2017-02-09-一般
7 / 39
CS2 series offer 3 point external control inputs.
They can be programmed individual with versatile
display and control functions. User programs
easier in [ecI group]. And front key function can
be set to execute ECI function. At meantime, ECI
terminals will be disable. Please refer to
description as below;
Relative PV or Tare
The [ ecI_]can be set to be reLpv(Relative PV)
function. When the ECI is closed, the reading will
show the differential value with PV or Tare.
Relative PV
Relative
PV( PV)
by ECI
ON
Level
Trigger
Present
Value
reLpv
[ecI_]
ECI_ has closed, and
then PV goes to “0”
ECI_ has opened,
and then display
shows PV
Relative PV
PV Hold
The [ ecI_]can be set to be pVhld(PV Hold)
function. The display will be hold when the E.C.I. is
closed, until the ECI is to be open. Please refer to
the below figures.
PV Hold & Reset
Present
Value
Reset PV Hold
by E.C.I. or
Front Key
O
N
Level
Trigger
ON
ON
PV Hold
pVhld
[ecI_]
Reset for Maximum or Minimum Hold
The [ ecI_] function can be set to be Mrst
function to reset the maximum and minimum value
by terminal of ECI.
Especially, the [dsply] function in [input group]
can be set to be to maXhd or miNhd to operate in
coordination with DO of PLC. It is easier to achieve
the maximum value testing in automation. Please
refer to the below figures.
Max. ( Mini.) Hold & Reset
Reset the Max
(Mini) Hold by
E.C.I. or F. Key
O
N
Level
Trigger
Maximum Hold
Present
Value
maXh
[dsply]
Mrst
[ecI_]
DI(Digital Input)
The [ ecI_] can be set to be dI (Digital Input)
function, when the meter building in RS485 port.
The computer is easier to get a switch status
through the meter as like as DI of PLC.
or 4(0)~20mA in ordering. The output low and high
can be programmable which it's related to various
display values. Reverse slope output is possible by
reversing point positions.
Output low corresponds to display Low[ aOls]
Settable range: -19999~+99999;
Setting the Display value Low to versus output
range Low(as like as 4mA in A4-20).
Output high corresponds to display High[ aOhs]
Settable range: -19999~+99999;
Setting the Display value High to versus output
range High(as like as 20mA in A4-20)
SCALE
Default: [aOls]: 0.00, [aOhs]: 100.00
Change to [aOls]: 50.00, [aOhs]: 19(99
OUTPUT
)00
0.00%
100.00%
50.00%
10)00
5)00
19(99
[aOhs]
[aOls]
*The range between [ aOhs]and [ aOls]should
be over 20% of span minimum; otherwise, it will
reflect the less resolution of analogue output.
High Limited for Analog Output
Settable range: 0.00~110.00% of output High;
User can set the high limit of output to avoid
destroying the receiver or protection system.
Set Scaling: [lOsc]: )00, [hIsc]: 19(99;
Output: [aOls]: 5)00 (Display value Low),
[aOhs]: 15)00 (Display value High);
[aOlmt]: 8)00%( of Output Range)
0.00%
100.00%
50.00%
OUTPUT
Ao.LMt: 80.00%
80.00%
SCALE
19(99
[hIsc]
)00
[lOsc]
10)00
5)00
[aOls]
15)00
[aOhs]
[aOlmt]
Fine Zero & Span Adjustment for Analog Output
■RS 485 Communication
CS2 series can be used as Remote Terminal

CS2 SERIES –OPERATION MANUAL(EN)-2017-02-09-一般
8 / 39
Users can get Fine Adjustment of analogue output
by front key on the meter. Please connect standard
meter to the terminals of analogue output. To press
the front key(up or down key) of meter for adjusting
and checking the output.
[aOzro]: Fine Zero Adjustment for Analog
Output;
Settable range: -38011~27524;
[aOspn]: Fine Span Adjustment for Analog
Output;
Settable range: -38011~27524;
Unit (RTU) for monitoring and controlling in a
SCADA (Supervisor Control And Data Acquisition)
system. It's not only can be read the measured
value and DI (external control inputs) status but
also controls the relays output (DO) via RS485
communication ports.
Protocol: ModBus RTU Mode
Baud Rate: Programmable 1200/2400/4800/
9600/19200/38400
Data Bits: 8 bits
Stop Bits: Programmable 1 bit or 2 bits
Parity: Programmable Even / Odd / None
Divice Number: Settable 1~255
Remote Display function
CS2 series has been built in an innovation function
call remote display function.
In past, The meter normally receive 4~20mA or
0~10V from AO card or BCD card of PLC. We
support a new solution by RS485 remote display
function so that can save cost of AO and wiring into
PLC.
CS2-PR & SC2-RL APPLICATION FOR PROCESS DC SIGNAL & TACHOMETER MEASURING
RS 485 Modbus RTU Mode (up to 38400bps)
4 Relay Output:
Mode: High or Low Energized / Energized Hold / DO
Functions: Start delay / Energized & De-energized
delay / Hysteresis
Analog Output 0~10V/0(4)~20mA
3 External Control Input:
Functions: Relative PV / PV Hold / Reset Max or Mini.
Hold / DI / Reset for Relay Energized Hold
Application: Thermal Switch / Circuit Breaker / Push
Button / ……
Display:
Mode: Measuring Value / Maximum Hold / Minimum
Hold / Reading value from RS485 command
AL
AL
RL 1
RL22
RL 3
RL 4
COM
CI11
CI2
CI3
ENT/FN
◄
▲
▼
Kg/cm
2
RL 1
RL22
RL 3
RL 4
COM
CI11
CI2
CI3
ENT/FN
◄
▲
▼
RPM
The data(number) will be same as PV that will
compare with set-point, relative to analogue output
and ECI functions so that is to control analogue
output, relay energized and so on
■ORDERING INFORMATION

CS2 SERIES –OPERATION MANUAL(EN)-2017-02-09-一般
9 / 39
CS2−RL−
Input
Mode
Input
level
−
Relay
Output
−
Analogue
Output
−
RS 485
Port
−
AUX.
POWER
−
*Optional
Function
Customize function is welcome. Please contact with our
sales for detail.
CODE
INPUT MODE
CODE
REALY OUTPUT
CODE
ANALOG O/P
CODE
RS 485 PORT
CODE
AUX. POWER
C
00
Contact
N
None
N
None
N
None
A
AC 115/230 V
N
NPN
R2
2 Relay
8
RS 485
P
PNP
R4
4 Relay
V
0(1) ~ 5 V
0 ~ 10 V
ADH*
*
AC/DC 85~264V
V
Voltage Pulse
ADL*
AC/DC 20~90V
05
5V pulse
I
0 ~ 10 mA
0(4)~20 mA
12
12V pulse
* ADH* will be available
at Jan. 2008
24
24V pulse
O
xx
Specify
U
P
Pick Up Sensor
* It means
RoHS
version.
OPTION 2
OPTION 3
OPTION 1
OPTION 4
Input mode and level
can be changed by
dip switches on rear
of meter
Please specify the range
of amplitude, If the input
mode has specified to be
pick up sensor.
CS2−F−
Input
Mode
Input
level
−
Relay
Output
−
Analogue
Output
−
RS 485 Port
−
AUX.
POWER
−
*Optional
Function
Customize function is welcome. Please contact with our
sales for detail.
CODE
INPUT MODE
CODE
REALY OUTPUT
CO
DE
ANALOG O/P
CODE
RS 485 PORT
CODE
AUX. POWER
V
Voltage Pulse
N
None
N
None
N
None
A
AC 115/230 V
05
5V pulse
R2
2 Relay
8
RS 485
12
12V pulse
R4
4 Relay
V
0(1) ~ 5 V
0 ~ 10 V
ADH*
*
AC/DC 85~264V
24
24V pulse
ADL*
AC/DC 20~90V
S
36
30~600Vac
I
0 ~ 10 mA
0(4)~20 mA
O
xx
Specify
* ADH* will be available
at Jan. 2008
OPTION 2
OPTION 1
* It means
RoHS
version.
OPTION 4
OPTION 3
■INSTALLATION
Please check the specification, wire diagrams and functions on the lable of the meter before
installation.
■Dimensions & Panel Cut Out
■Installation
96.0
48.0
93.0+0.2
45.0+0.2
PANEL CUT-OUT
FRONT VIEW
Unit: mm
8.0
12.0
100.0
Dimensions: 96mm x 48mm x 120mm
Panel Cutout: 93mm x 45mm (advise)
1.0~8.0 mm
FIX HOLDER:
104 mm(L) / W M3
R
L1
RL
2
2
R
L
3
R
L
4
COM
C
I1
1
C
I
2
C
I
3
ENT/FN
?
?
?
Kg/cm2
PANEL CUT-OUT:
92+0.2(W) x 44+0.2(H) mm
■Wiring Diagram

CS2 SERIES –OPERATION MANUAL(EN)-2017-02-09-一般
10 / 39
Connector
10A 300Vac, M2.6, 16~22AWG,
Max torque: 5Kg-cm
Please use cord end terminal.
2.0mm max
Please check the voltage of
power supplied first, and then
connect to the specified
terminals. Herein,
recommended that power
supplied to the meter with
protection by a fuse or circuit
breaker.
Power Supply
AC115/230V
AC85~264V
Isolation Transformer
L
N
G
L
N
G
1A Fuse
6
7
9
10
8
For input, RS485 and ECI
wiring, Herein recommended
to use twin with shielding
wire.
RS485 Communication Port
RS485 Port
30
31
32
A
B
Max. Distance: 1200M
Terminate Resistor
(at latest unit):
120~300ohm/0.25W
(typical: 150ohm)
【CS2-RL RPM/Linearlly Line Speed/Freq.Controller】
D-S
1
2
3
4
5
NPN
ON
PNP
ON
M.C.
ON
ON
5VP
12VP
ON
24VP
ON
D-S is on when it is in down site
21
22
24
25
23
27
28
26
29
30
31
33
32
34
Relay 1
c
a
Relay 4
c
a
Analogue
output
A
B
RS 485
port
Relay 2
b
c
a
Relay 3
b
c
a
Terminal blocks:
10A/300Vac, M2.6,
M2.6, 1.3~2.0mm2
(16~12AWG)
External
Control Input
FG
11
12
14
15
13
7
8
9
10
D-S
Dip-Switch
5
6
ECI1
ECI3
COM
ECI2
3
4
ADL
ADH
AC/DC 86~265V
AC/DC 20~90V
AC230V
AUX. POWER
AC115V
0V
+ Vdc
+IN
SIGNAL INPUT
Freqency/Pulse
Sensor input connection
D-S
1
2
3
4
5
NPN
ON
PNP
ON
M.C.
ON
ON
5VP
12VP
ON
24VP
ON
D-S is on when it is in down site
11
12
14
15
13
+Vdc
Out
0V
+IN
0V
+V
+Vdc
Out
0V
Please change the dip-switch on rear
of meter to match the input mode and
level.
【CS2-F Frequency Controller】
21
22
24
25
23
27
28
26
29
30
31
33
32
34
Relay 1
c
a
Relay 4
c
a
Analogue
output
A
B
RS 485
port
Relay 2
b
c
a
Relay 3
b
c
a
Terminal blocks:
10A/300Vac, M2.6,
M2.6, 1.3~2.0mm2
(16~12AWG)
External
Control Input
FG
7
8
9
10
5
6
ECI1
ECI3
COM
ECI2
3
4
ADL
ADH
AC/DC 86~265V
AC/DC 20~90V
AC230V
AUX. POWER
AC115V
11
12
14
15
13
SIGNAL INPUT
AC(SINE WAVE)

CS2 SERIES –OPERATION MANUAL(EN)-2017-02-09-一般
11 / 39
■OPERATIONS

CS2 SERIES –OPERATION MANUAL(EN)-2017-02-09-一般
12 / 39
■Front Panel
R L 1
RL 2
2
RL3
RL 4
COM
CI11
CI2
CI3
ENT/FN
?
?
?
mA
M.H
M.H
Comm. status
Relay status
Indication
Operation Key
Control Input
status
Engineer Unit
Display screen
Max. Hold status
Mini. Hold status
Numeric Screens
0.8”(20.0mm) red high-brightness LED for 5 digital
present value.
I/O Status Indicators
Relay Energized: 4 square red LED
RL1
display once Relay 1 has been energized;
RL2
display once Relay 2 has been energized;
RL3
display once Relay 3 has been energized;
RL4
display once Relay 4 has been energized;
External Control Input Energized: 3 square green
LED
ECI1
display once ECI.1 has been closed(dry contact)
ECI2
display once ECI.2 has been closed(dry contact)
ECI3
display once ECI.3 has been closed(dry contact)
RS485 Communication: 1 square orange LED
COM
will flash when the meter is receive or send
data, and
COM
flash quickly means the data
transient quicker.
Max/Mini Hold indication: 2 square orange LEDs
CO
M.H
displayed: To display function which
expressed it has been selected in Maximum or
Minimum Hold function.
Stickers:
Each meter with a sticker to describe what are the
functions and engineer label enclosure.
Functions stickers
Relay energized:
H H
HH Energized
H i
Hi Energized
L o
Lo Energized
L L
LL Energized
G O
Go Energized
Hi. H
Hi Energized & Latch
D O
RS485 Energized
Lo. H
Lo Energized & Latch
ECI functions:
PV Hold
Tare
Digital Input
Maximum or Minimum Reset
Reset fo Relay Latch
Engineer Label: over 80 types.
Operating Key: 4 keys for
Enter(Function) /
Shift(Escape) /
Up key /
Down key
Pass Code:
Settable range:0000~9999;
User must key-in the exactly pass cord for access
to [Programming Level]. Otherwise, the meter
will return to measuring page. If user forget the
pass code, please contact with your service
window.
Function Lock: There are 4 levels
programmable.
none(None): no lock at all. User can access to all
level for checking and setting.
user(User Level): User Level lock. User can
access to User Level for checking, but can not
setting.
eng(Programming Level): Programming level
lock. User can access to programming level for
checking, but can not setting.
all(ALL): All lock. User can access to all level for
checking but can not setting.
Front Key Function
The
Key can be set to be the same function as
the setting of [ecI1](ECI).
Ex. The [ecI1]set to be pVhld and the function
[E1=up]set to be yes in [eci group]. When
user presses
Key, the PV will hold as like as
terminals of ECI1 close.
The
Key can be set to be the same function as
the setting of [ecI2].
Ex. The [ecI2]set to be reL.pv and the function
[E2=dn]set to be yes in [eci group]. When
user presses
Key, the PV will show relative
value as like as terminals of ECI2 close.
If the front key function has been set, the
terminal input for ECI will be disabling.
■Operating Key:

CS2 SERIES –OPERATION MANUAL(EN)-2017-02-09-一般
13 / 39
*Please access to the Engineer Level to check and set the parameters when users start to run the meter
Operating Key: 4 keys for
Enter(Function) /
Shift(Escape) /
Up key /
Down key
The meter has desgined operation similar as PC's
and
Enter
. In any page, press
key means
"enter" or "confirm setting", and press
key means "escape(
Esc
)" or "shift".
In Engineer Level, the screen will return to Measuring Page after do not press any key over 2 minutes, or
press
for 1 second.
Function Index
Setting Status
(=
)
Enter/Fun key
(1) In any page, press
to access
the level or function index
(2) From the function index to
access setting status
(3) Setting Confirmed, save to EEProm and go to next
function index
(=
)
Shift key
(1) In measuring page, press
for 1 second to access user
level.
(2) In function index, press
for 1
second to go back upper level.
(3) In function group index, press
for 1 second to go back
measuring page
(4) In seting status, press
to Shift the setting
position.
(5) In seting status, press
for 1 second to abort
setting and go back this function index.
(=
)
Up key
(1) In function index, press
to
go back to previous function
index
(2) In setting status for function, press
to select
function
(3) During number Setting, press
can roll the digit
up
(=
)
Down key
(1) In Function Index Page, press
will go to the next Function
Index Page.
(2) In setting status for function, press
to select
function
(3) During number Setting, press
can roll the digit
down.
■Error Masage
BEFORE POWER ON, PLEASE CHECK THE SPECIFICATION AND CONNECTION AGAIN.
SELF-DIAGNOSIS AND ERROR CODE:
DISPLAY
DESCRIPTION
REMARK
ovfl
Display is positive-overflow (Signal is over
display range)
(Please check the input signal)
-ovfl
Display is negative-overflow (Signal is under
display range)
(Please check the input signal)
ovfl
ADC is positive-overflow (Signal is higher than
input 120%)
(Please check the input signal)
-ovfl
ADC is negative-overflow (Signal is lower than
input -120%)
(Please check the input signal)
eep
fail
EEPROM occurs error
(Please send back to manufactory for
repaired)
aiCng
pv
Calibrating Input Signal do not process
(Please process Calibrating Input
Signal)
aic
fail
Calibrating Input Signal error
(Please check Calibrating Input Signal)
aoCng
pv
Calibrating Output Signal do not process
(Please process Calibrating Output
Signal)
aoc
fail
Calibrating Output Signal error
(Please check Calibrating Output Signal)

CS2 SERIES –OPERATION MANUAL(EN)-2017-02-09-一般
14 / 39

CS2 SERIES –OPERATION MANUAL(EN)-2017-02-09-一般
15 / 39

CS2 SERIES –OPERATION MANUAL(EN)-2017-02-09-一般
16 / 39

CS2 SERIES –OPERATION MANUAL(EN)-2017-02-09-一般
17 / 39

CS2 SERIES –OPERATION MANUAL(EN)-2017-02-09-一般
18 / 39
■Operating Steps:
■User Level
INDEX
FUNCTION DESCRIPTION
PARAMETERS & SETTING
SET
POWER
ON
Please check the specification and
wiring diagrams firstly.
*****
Self-diagnosis (LED All bright)
cs@rl
Model
cs@rl:RPM/LinearllyLine Speed/Frequency
cs@f:Frequency
ver!4
Firmware version
168*8
Measuring Page
Press
for 1 second to access [User
Level]
0−0−1
pv
168*8
This page will show out, when
[dsply](step A-7) function has not set
to be pv .
pv(Pv): Present Value;
Press
for 1 second return
to Measuring Page
0−1
ry!sp
100)0
100)0
200)0
ry!sp(rY1.SP):Relay 1 Set-point
◘Please confirm the energized mode of
relay 1 before setting.
Settable range: 0~99999
Shift
Up
Down
Enter
0−2
ry@sp
100)0
100)0
100)0
ry@sp(rY2.SP):Relay 2 Set-point
◘Please confirm the energized mode of
relay 2 before setting.
Settable range: 0~99999
Shift
Up
Down
Enter
0−3
ry#sp
100)0
100)0
80)0
ry#sp(rY3.SP):Relay 3 Set-point
◘Please confirm the energized mode of
relay 3 before setting.
Settable range: 0~99999
Shift
Up
Down
Enter
0−4
ry$sp
100)0
100)0
50)0
ry$sp(rY4.SP):Relay 4 Set-point
◘Please confirm the energized mode of
relay 4 before setting.
Settable range: 0~99999
Shift
Up
Down
Enter
0−5
rYrst
no
no
yes
rYrst(rY.rSt): Reset for energized latch
of Relay;
If the [ry_.md](step B-3/7/11/15) set to be
hIhld or lOhld, and the present
value(PV) reach to the condition of relay
energising, the relay will be energized and
latching.
At mean time, user can reset the relay
latching in here.
Programmable: yes / no
yes(Yes): reset the relay
latching.
no(No): abort to reset the
relay latching.
&
Selection
Enter
◘Be careful, the relay has been
energizing and latching, if the
PV still reach to the condition
of relay energized, enven
user had set here to reset the
relay latching.
Next Page

CS2 SERIES –OPERATION MANUAL(EN)-2017-02-09-一般
19 / 39
0−6
min
)0
min(Min): the Minimum value of PV
saving;
The meter will save the minimum of PV
during power on, until reset in
[ Mrst](step 0-8). It will save newest
minimum PV after reset.
Review only
0−7
max
299(9
max(Max): the Maximum value of PV
saving;
The meter will save the maximum of PV
during power on, until reset in
[ Mrst](step 0-8). It will save newest
maximum PV after reset.
Review only
0−8
Mrst
no
no
yes
Mrst(M.rSt): reset the saved value of
Maximum & Minimum;
The values of maximum and minimum
can be reset in here. It will save newest
maximum and minimum after reset.
Programmable: yes / no
yes(Yes): to reset the saved
value of maximum and minimum.
no(No): abort to reset the
saved values of maximum
and minimum.
&
Selection
Enter
0−9
cs@rl
ver!4
Model of the meters
cs@rl:RPM/LinearllyLine Speed/
Frequency
cs@f:Frequency
ver!4(Ver 1.4): Firmware version
Review only
It will be announced in our
website www.adtek.com.tw,
when it had been versions
updated.
0−0−1
pv
168*8
Return to the first page
Press
for 1 second to back to
Measuring Page in any page.
Programming Level
INDEX
FUNCTION DESCRIPTION
PARAMETERS & SETTING
SET
168*8
MEASURING PAGE
enter
Pcode
Default:1000
0000
1000
Enter the pass code to access
Programming Level
If user wants to change the
pass code, please go to step
A-15 to set. Please remind the
new pass code.
Pass Code
INPUT
GROUP
RELAY
GROUP
EXTERNAL
CONTROL
INPUT GROUP
ANALOGUE
OUTPUT
GROUP
RS485
GROUP
PRESS
TO ACCESS
PRESS
TO ACCESS
PRESS
TO ACCESS
PRESS
TO ACCESS
PRESS
TO ACCESS
YES
Press
for 1 second to back Measuring Page
NO

CS2 SERIES –OPERATION MANUAL(EN)-2017-02-09-一般
20 / 39
Input Group
INDEX
FUNCTION DESCRIPTION
PARAMETERS & SETTING
SET
input
group
INPUT GROUP INDEX PAGE
In following pages, press
for 1 second to back INPUT
GROUP INDEX PAGE.
A−1
pVtyp
lNspd
lNspd
rpm
pVtyp: PV type selection
The meter has desgined for
mult-purpose. User can set the display
purpose in [pVtyp]of [input group]
such as lNspd(Linearly Line Speed),
rpm(RPM), rps(RPS), hz(Hz),
khz (kHz). The meter will show the
relation parameters as below,
Programmable:
lNspd:Linearly Line Speed;
rpm:RPM(Rotation/Minute)
rps:RPS(Rotation/Second)
hz:Hz(Frequency)
khz:kHz(Frequency)
&
Selection
Enter
A−2−1
ppr
1
1
9999
This function will be shown, once user
selects rpm / rps or lNspd in
[pVtyp]
ppr: Pulse/rotation setting
Settable range: 1~9999
Shift
Up
Down
Enter
A−2−2
Eunit
m/mn
m/mn
yd/mn
This function will be shown, once user
selects lNspd in [pVtyp]
Eunit: Engineer Unit of linearly line
speed
Programmable: m/mn / cm/mn
/ yd/mn / ft/mn
m/mn(M/min): Meter/Minute
cm/mn(CM/min):Centimeter/Minute
yd/mn(Yd/min): Yard/Minute
ft/mn(Ft/min): Feet/ Minute
&
Selection
Enter
A−2−3
diamt
)1000
)1000
(9999
This function will be shown, once user
selects lNspd in [pVtyp]
diamt:Diemeter of rotor
Settable range:
0.0001~9.9999M
Shift
Up
Down
Enter
A−3
pVdp
0
0
)0000
pVdp: Decimal Point setting;
There are two meanning as below,
1.The setting of decimal point is for
set-point of relay energized level, when
user sets to be auto in [range]
function.
2.The setting of decimal point is for
display value and set-point of relay
energized level, when user sets to be
manul or semi in [range] function.
Programmable:
0/ )0 /
)00 / )000 / 0.0000
&
Selection
Enter
A−4
factr
!000
!000
(999
factr: Factor of display value
Display = Value of math with setting x
Factor
The display can be proportioned by
factor.The typical application is
compensation for gear ratio.
Settable range: 0.001~9.999
Shift
Up
Down
Enter
Next Page
Other manuals for CS2-RL
1
This manual suits for next models
1
Table of contents
Other ADTEK Controllers manuals
Popular Controllers manuals by other brands

BEKA
BEKA BA458C manual
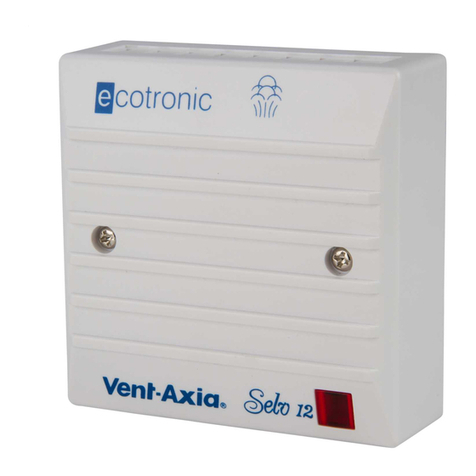
Vent-Axia
Vent-Axia 563531A Fitting and wiring instructions
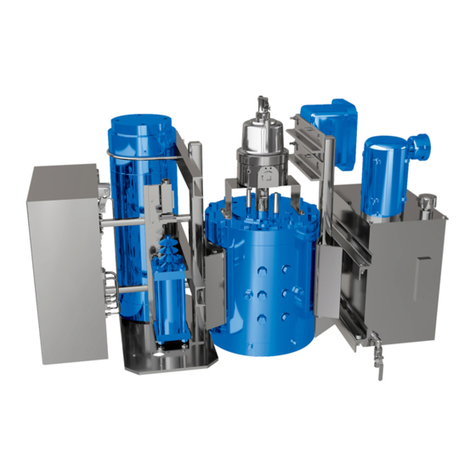
Emerson
Emerson Shafer ECAT Installation, operation and maintenance manual

Mitsubishi Electric
Mitsubishi Electric QJ81DL96 user manual
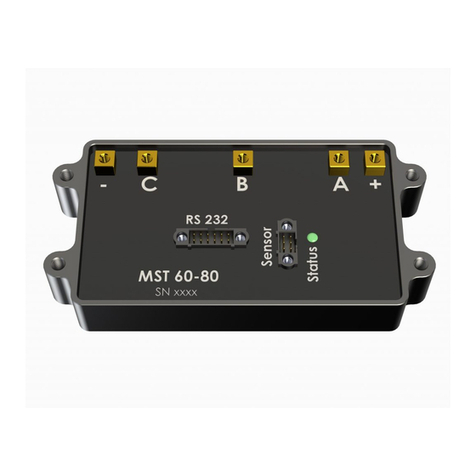
Plettenberg
Plettenberg MST60-80 Operational manual
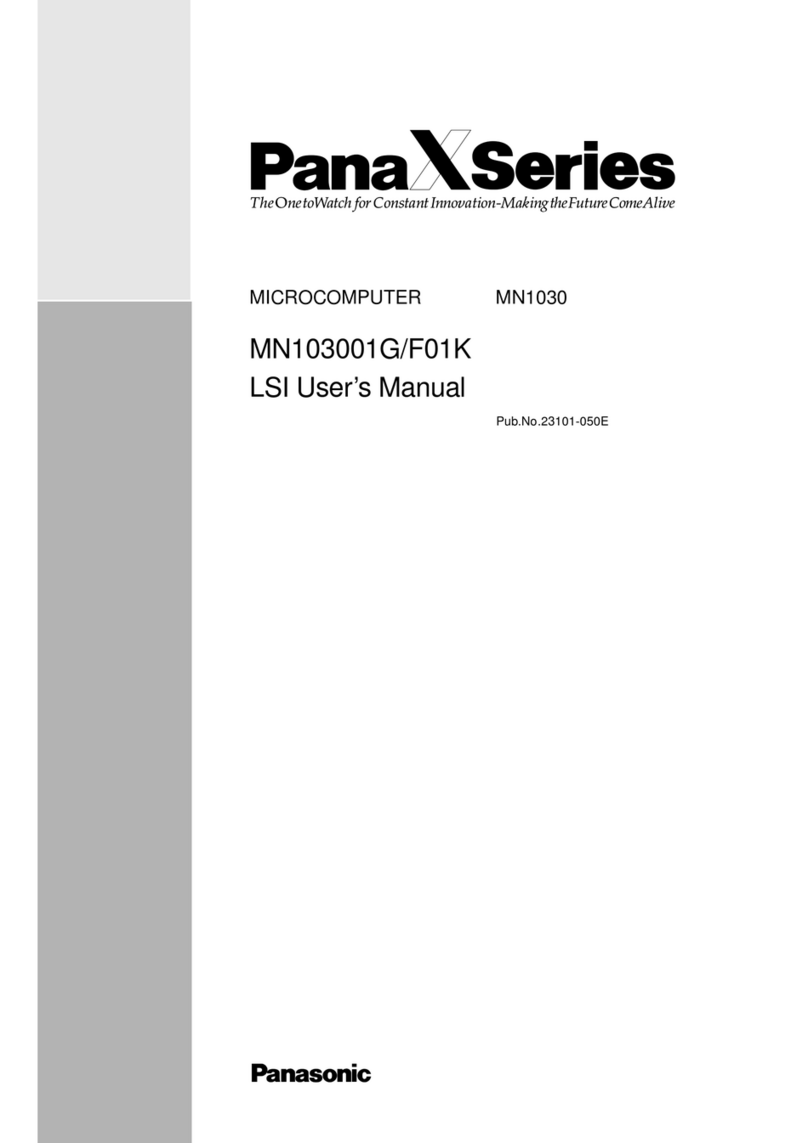
Panasonic
Panasonic MN103001G/F01K user manual