BEKA BA458C User manual

Issue: 5
1st December 2010
BA458C
Intrinsically safe
Panel mounting
Batch Controller
Issue 5

2
1. Description
2. Operation
2.1 Operator controls
2.2 Power supply failure
3. Intrinsic Safety Certification
3.1 ATEX certificate
3.2 Zones, gas groups & T rating
3.3 Power supply
3.4 Inputs
3.4.1 Input 1
3.4.2 Input 2
3.5 Switch outputs
3.6 External switches
3.7 Inhibit & security links
3.8 Certification label information
4. System Design for Hazardous Area
4.1 System certificates
4.2 Use with Zener barriers
4.2.1 Power supply
4.2.2 Pulse inputs
4.2.2.1Switch contact
4.2.2.2Proximity detector
4.2.2.3Voltage pulse
4.2.3 4/20mA analogue input
4.2.4 Switch outputs
4.3 Use with galvanic isolators
4.3.1 Power supply
4.3.2 Inputs
4.3.3 Switch outputs
4.4 External switches
4.5 Inhibit link
4.6 Security link
5. Installation
5.1 Location
5.2 Installation procedure
5.3 EMC
6. Configuration Menus
6.1 Security
6.2 Navigation
6.3 Default configuration
6.4 System settings
6.4.1 Language
6.4.2 User controls
6.4.3 Signal input
6.4.4 4mA calibration
6.4.5 20mA calibration
6.4.6 Lineariser
6.4.7 Restart
6.4.8 Output 2
6.4.9 Output 3
6.4.10 Optional outputs 4, 5 & 6
6.4.11 Pulse output
6.4.12 Clear grand total
6.4.13 Defaults
6.4.14 Security
6.4.15 User screens
6.4.16 Display
6.4.17 Output options
6.4.16.1 Control 2
6.4.16.2 Control 3
6.4.16.3 Flow alarm
6.4.16.4 Reset status
6.4.16.5 Batch status
6.4.17.6 Pulse output
6.5 Batch settings
6.5.1 Scale Points (Non-linear
pulse inputs)
6.5.2 Scale Factors (Non-linear
pulse inputs)
6.5.3 Scale Factor (Linear pulse
inputs)
6.5.4 Scaling (4/20mA input)
6.5.5 Batch D.P.
6.5.6 Batch Legend
6.5.7 Batch Limit
6.5.8 Batch Names
6.5.9 Batch Size
6.5.10 Select Batch
6.5.11 Batch History
6.5.12 CONTROL2delay
6.5.13 CONTROL2stop
6.5.14 CONTROL3delay
6.5.15 CONTROL3stop
6.5.16 Count Mode
6.5.17 Overrun Compensation
6.5.18 Batch Cycles
6.5.19 Restart Delay
6.6 Rate settings
6.6.1 Rate Scaling (Pulse inputs)
6.6.2 Rate D.P. (Pulse inputs)
6.6.3 20mA Display (4/20mA input)
6.6.4 Rate Legend
6.6.5 Timebase
6.6.6 Rate Filter
6.6.7 Flow Alarm
6.6.8 Clip-Off
7. Calibration Examples
8. Maintenance
8.1 Fault finding during commissioning
8.2 Fault finding after commissioning
8.3 Servicing
8.4 Routine maintenance
8.5 Guarantee
8.6 Customer comments
9. Accessories
9.1 Tag number
10. Index
Appendix 1 User Screens
Appendix 2 Diagnostic Information menu
Appendix 3 FM & cFM Approval for use in
USA & Canada.
CONTENTS
The BA458C is CE marked to show compliance with the
European Explosive Atmospheres Directive 94/9/EC
and the European EMC Directive 2004/108/EC

3
1. DESCRIPTION
The BA458C is a panel mounting intrinsically
safe batch controller primarily intended to
control the dispensing of liquids, solids or
components in a hazardous area. It is a
second-generation instrument that replaces
both the BA350BP and the BA350BC.
Although incorporating sophisticated control
functions, the BA458C is easy to operate and
configure. Batch status and the function of the
front panel push-buttons are shown on the
backlit graphic display which is visible in all
lighting conditions. The instrument can
provide single, dual or three stage control and
may be used with both pulse and 4/20mA
analogue output flowmeters.
The BA458C has been certified intrinsically
safe by European Notified Body Intertek
Testing Services (ITS) to the ATEX Directive
94/9/EC.
The BA458C is also FM approved for use in
the USA and cFM approved for use in Canada,
these approvals are described in Appendix 3.
Housed in a robust 72 x 144 panel mounting
DIN enclosure, the controller has an IP65 front
panel and is supplied with a gasket to seal the
joint between the instrument and the panel.
2. OPERATION
Fig 1 shows a typical BA458C dispensing
application. The BA458C controller
incorporates programmable input scaling so
that the total and rate displays may be in any
engineering units such as litres or gallons.
The operator enters or selects, via the front
panel push-buttons, the setpoint which is the
required volume to be dispensed. Control 1 is
energised immediately the Start push-button is
operated, followed by Control 2 after a
programmable time delay. Towards the end of
the batch, Control 2 is de-energised a
programmable volume before the batch
setpoint is reached when Control 1 is also de-
energised.
By operating a small bypass valve from Control
1 and the main control valve from Output 2, the
flow can be started and stopped slowly thus
reducing batching errors and flow surges. If
less accuracy is required, single stage control
can be accomplished using just Control 1 and
one control valve.
Control 1 is a dedicated output, but Outputs 2
and 3 may be configured as control, pulse or
batch status outputs.
Fig 1 Typical batch control application
If additional outputs are required, three more
may be added as a factory installed option.
The BA458C incorporates a selection of
operator display screens allowing the installer
to choose a display which only present
essential information to the operator.
To prevent accidental or unauthorised
adjustments, the operator and configuration
menus may be protected by separate security
codes. The configuration menu may also be
protected by a security link connected between
terminals at the rear of the instrument. This
link may be hard-wired, or connected to a
panel mounting key-switch when frequent
changes are required.
Fig 2 shows a simplified block diagram of the
controller.
Fig 2 Simplified block diagram of BA458C

4
2.1 Operator Controls
The BA458C batch controller may be
configured with a variety of operator display
screens. Each set of screens provides a
different level of information, some including
graphical displays. All the screens identify the
function of the front panel push-buttons which
have the following functions.
START Causes Control 1 to be energised
which will start the batch. The screen
will display ‘Running’ until the batch
is completed, or the STOP push-
button is operated.
STOP Operating this button during a batch
immediately de-energises Control 1
and Control Outputs 2 & 3 if they are
used, causing the batch to pause.
‘Paused’ will be displayed on the
screen. During a pause any input
signal continues to be counted.
The batch may be resumed at any
time by pressing the Start button, or it
may be aborted by operating the
Reset button.
At the end of each batch the Control
Output(s) will be de-energised and
‘Complete’ will be displayed on the
screen.
RESET After completion of a batch the batch
controller must be reset before the
next batch can be started.
After resetting the screen displays
‘Ready’. Input signals are ignored
until the Start button is operated.
Note: Two selectable options
modify the reset function.
Quick Restart eliminates the need
to manually reset the BA458C at
the end of each batch. When a
batch is complete the batch
controller will display the volume
that has been dispensed.
Operating the Start pushbutton will
reset the batch controller and start
another batch. See section 6.4.7
Auto Restart enables the batch
controller to run continuously. At
the end of each batch the
controller waits for a
programmable time before
automatically resetting and starting
another batch. This sequence will
continue until a programmable
number of batches has been
completed or the Stop button is
operated. See section 6.4.7
MENU Operating this button gives access
to the Operator Menu that may be
protected by a four digit security
code. This menu may be
configured to give the operator
access to any, or none of the
following functions:
Select Batch Select 1 of 9
pre-entered
setpoints
Batch Size Adjust 1 or all 9
setpoints.
Batch History Show size of last
10 batches.
Configure Full access to
the instruments
configuration
menu.
If no items are contained in the menu
the operator can only start, pause
and stop a batch. Inclusion of the
Select Batch function allows the
operator to select the batch setpoint
from one of nine pre-entered values.
To aid identification, each setpoint
may be identified by a name having
up to sixteen digits.
If included in the menu, the Batch
Size function allows the adjustment
of all the pre-entered batch setpoints
Batch History shows the size of the
last ten batches which have been
completed.
The Configure function provides
operator access to the batch
controller configuration menus
described in section 6. Entry to
these menus is protected by an
external security link between
terminals 18 and 19 and an optional
four digit security code.

5
2.2 Power supply failure
If the power supply for the BA458C fails during
a batch, the instrument will remember the
quantity of product dispensed when the supply
failed, together with the number of cycle
completed if autostart is being used. When
power is restored, the batch controller will
return in the Paused condition displaying the
amount of product dispensed prior to the
failure. Operating the Start pushbutton will
complete the batch.
If the supply failure occurs when the batch
controller is in the Ready or Complete state,
the controller will return in the same state when
power is restored.
3. INTRINSIC SAFETY CERTIFICATION
3.1 ATEX certificate
The BA458C has been issued with EC-Type
Examination Certificate by Notified Body
Intertek Testing Services (ITS) confirming
compliance with the European ATEX Directive
94/9/EC for Group II, Category 1G equipment,
EEx ia IIC T5. The instrument bears the
Community Mark and, subject to local codes of
practice, may be installed in any of the
European Economic Area (EEA) member
countries. i.e. Austria, Belgium, Denmark,
Finland, France, Germany, Greece, Ireland,
Italy, Luxembourg, The Netherlands, Portugal,
Spain, Sweden and the United Kingdom.
ATEX certificates are also accepted in Norway,
Iceland, Liechtenstein, Switzerland and The
Czech Republic.
This instruction manual describes installations
which conform with BS EN60079:Part14
Electrical Installation in Hazardous Areas.
When designing systems for installation
outside the UK, the local Code of Practice
should be consulted.
3.2 Zones, gas groups and T rating
The BA458C has been issued with EC Type
Examination certificate ITS03ATEX21379
confirming that it complies with the
requirements for Group II Category 1 G
equipment; EEx ia IIC T5 (Tamb –40 to 60oC)
as specified in the ATEX Directive. When
connected to a suitable system the BA458C
may be installed in:
Zone 0 explosive gas air mixture
continuously present.
Zone 1 explosive gas air mixture
likely to occur in normal
operation.
Zone 2 explosive gas air mixture not
likely to occur, and if it does
will only exist for a short
time.
Be used with gases in groups:
Group A propane
Group B ethylene
Group C hydrogen

6
Having a temperature classification of:
T1 450oC
T2 300oC
T3 200oC
T4 135oC
T5 100oC
At an ambient temperature between –40 and
+60oC.
Note: the guaranteed operating temperature
range of the batch controller is –20 to +60oC
This allows the BA458C to be installed in all
Zones and to be used with most common
industrial gases.
WARNING installation in Zone 0
When installed in a Zone 0 potentially
explosive atmosphere requiring
apparatus of Category 1G, the batch
controller shall be installed such that
even in the event of rare incidents, an
ignition source due to impact or friction
between the aluminium enclosure at the
rear of the instrument mounting panel
and iron/steel is excluded.
3.3 Power supply
When installed in a hazardous area the
BA458C must be powered from a EEx ia IIC
certified Zener barrier or galvanic isolator
having output parameters equal to or less
than: Uo = 28.0V dc
Io = 96mA dc
Po = 0.84W
The maximum equivalent capacitance and
inductance between power supply terminals 1
and 2 is: Ci = 0.015µF
Li = 8µH
To determine the maximum permissible cable
parameters, Ci and Li must be subtracted from
the maximum cable capacitance and
inductance specified by the certificate of the
barrier or isolator powering the batch
controller.
3.4 Inputs
The BA458C has two alternative inputs.
Input 1 (terminals 11 & 12) is for devices that
require powering by the batch controller such
as switch contacts, a proximity detector or a
photodetector. Input 2 (terminals 13, 14, 15,
16 & 17) complies with the requirements for
simple apparatus and is for the connection of
devices having a voltage or current output
such as a magnetic pickup or an analogue
4/20mA current.
Note: Inputs 1 and 2 can not be used
simultaneously.
3.4.1 Input 1
Terminals 11 and 12 may be connected to any
transducer having input parameters equal to or
greater than: Ui = 10.6V dc
Ii = 20mA dc
Pi = 0.05W
They may also be connected to any device
such as a switch contact complying with the
requirements for simple apparatus.
The maximum permitted cable parameters for
the cable plus the transducer connected to
terminals 11 & 12 in a IIC hydrogen gas are:
Co + Ci transducer ≤2.3µF max
Lo + Li transducer ≤90mH max
See system certificates for maximum limits for
IIB and IIA gases.
3.4.2 Input 2
Terminals 13, 14, 15, 16 and 17 comply with
the requirements for Simple Apparatus
allowing any device certified EEx ia IIC with
output parameters equal to or less than:
Uo ≤28V dc
Io ≤100mA dc
Po ≤0.66W
to be connected.
This allows devices with a certified voltage
pulse output or a certified 4/20mA analogue
current output to be connected directly to the
batch controller.
The maximum equivalent capacitance Ci and
inductance Li of terminals 13 to 17 is:
Ci = 0.018µF
Li = 0.02mH
To determine the maximum permissible cable
parameters, Ci and Li must be subtracted from
the maximum permissible cable capacitance
and inductance specified by the certificate for
the device connected to input 2.
See system certificates for maximum limits for
IIB and IIA gases.

7
3.5 Switch outputs
Control 1 and Outputs 1 & 2 are separate
galvanically isolated solid state switches. The
EC-Type Examination Certificate specifies that
under fault conditions the voltage, current and
power at each switch output will not exceed
those specified for simple apparatus in Clause
5.4 of EN50020:2002. This allows each of the
BA458C switch outputs to be connected to any
intrinsically safe circuit protected by a certified
Zener barrier or galvanic isolator providing that
the output parameters of each circuit are less
than: Uo ≤28V dc
Io ≤200mA
Po ≤0.85W
The maximum equivalent capacitance and
inductance of each BA458C switch output are:
Ci = 0.04µF
Li = 0.02mH
To determine the maximum permissible cable
parameters, Ci and Li must be subtracted from
the maximum cable capacitance and
inductance specified by the certificate of the
barrier or isolator connected to the switch.
3.6 External switches
For applications requiring the batch controller
to be operated via large industrial push-
buttons, terminals S1 to S7 may be connected
to six external switches.
Terminals S1 to S7 have the following
combined output safety parameters:
Uo = 14.7V dc
Io = 99mA dc
Po = 0.6W
The switches and associated wiring connected
to the terminals must comply with the
requirements for simple apparatus. i.e. they
must have IP20 protection and be capable of
withstanding a 500V rms insulation test to
earth for one minute. Most industrial push-
buttons satisfy these requirements
The total maximum permitted cable
parameters for all the cables connected to
terminals S1 to S7 in a IIC hydrogen gas are:
Co ≤0.15 µF
Lo ≤0.48mH
These are not restrictive and allow a significant
distance between the switches and the
instrument.
3.7 Inhibit and Security Links
The inhibit and security links have the following
combined output safety parameters:
Uo = 11.7V dc
Io = 2.4mA dc
Po = 7mW
A wire link may be connected between the
terminals, or if frequent changes are required
switches may be used. These switches and
associated wiring must comply with the
requirements for simple apparatus. i.e. they
must be mechanically activated, have IP20
protection and be capable of withstanding a
500V rms insulation test to earth for one
minute.
The total maximum permitted cable
parameters for all the cables connected to
terminals 18, 19 & 20 in a IIC hydrogen gas
are: Co ≤1.5µF
Lo ≤1H
These are not restrictive and do not limit the
separation between the batch controller and
the switches.
3.8 Certification Label Information
The certification label is fitted in a recess on
the top outer surface of the enclosure. It
shows the ATEX certification information plus
BEKA associates name, location, instrument
serial number and year of manufacture. Non
European certification information may also be
included.

8
4. SYSTEM DESIGN FOR HAZARDOUS
AREAS
4.1 System Certificates
In addition to the EC-Examination Certificate,
ITS have issued two System Certificates for
the BA458C batch controller. One defines
how the BA458 may be used with Zener
barriers and the other with galvanic isolators.
Both are divided into two sections to cover
input signal sources in the hazardous and the
safe area.
Interface Certificate No.
Zener barriers Ex03E21380
Galvanic isolators Ex03E21381
System Certificates are Certificates of
Conformity which are primarily issued for
installation guidance in the UK. They do not
form part of the certification to the ATEX
Directive.
4.2 Use with Zener barriers
Zener barriers are the least expensive
intrinsically safe interface between a safe and
hazardous area. However they do not provide
isolation and require a high integrity earth
connection that may be expensive to install.
For a single BA458C batch controller
installation it may be less expensive and
complicated to use galvanic isolators when a
high integrity earth connection is not already
available.
Any Zener barrier certified EEx ia IIC by an
EEC approved certification body may be used,
providing that the safety parameters are within
the limits specified by the BA458C EC-
Examination Certificate. Only one polarity of
Zener barrier, i.e. positive or negative, may be
used with each BA458C batch controller
installation.
To assist with system design, the Zener barrier
System Certificate specifies the safety
description of barriers that may be used and
lists the maximum permitted cable parameters.
Fig 3 illustrates the basic circuit that is used for
all BA458C installations protected by Zener
barriers. Although the BA458C batch
controller will operate from a wide range of
input sources, only one source may be
connected at any time.
Alternatively the input source may be located
in the safe area. Fig 4 shows how an
additional Zener barrier may be used to
transfer the signal from the safe area to the
batch controller in the hazardous area. For
switch contact and open collector inputs the
additional end-to-end resistance of the Zener
barrier must not prevent the input at the batch
controller terminals passing through the batch
controllers input switching thresholds.
Fig 3 Batch controller powered via a Zener
barrier with input in hazardous area.
Fig 4 Batch controller protected by galvanic
isolators with Input in safe area

9
4.2.1 Power supply
Usually a BA458C batch controller is powered
from the safe area via a positive polarity 28V
300ΩZener barrier which has an end-to-end
resistance of about 340Ω. The BA458C
consumes a maximum current of 33mA and
requires a minimum voltage of 11V between
terminals 1 and 2. When powered from a
28V 300ΩZener barrier, the supply voltage in
the safe area must be between 22.2V and the
maximum working voltage of the barrier which
is usually about 26V.
CAUTION
The safety components within the batch
controller limit the voltage between terminals
1 and 2 at 15V. If the batch controller is
directly connected to a 15V or greater power
supply without a Zener barrier or equivalent
series resistor, the instrument will consume
a large current for a few seconds and then
shut-down to prevent permanent damage.
To test a BA458C batch controller in a safe
area workshop, terminals 1 & 2 should be
connected to a 24V dc power supply via a
330Ωresistor.
4.2.2 Pulse inputs
As shown in Figs 3 and 4 the BA458C batch
controller may be connected to a wide variety
of pulse transducers and sources in the
hazardous or safe area. Input 1 is for pulse
sources that need powering by the batch
controller such as switch contacts or a 2-wire
proximity detector. Input 2 is for voltage pulse
inputs such as the magnetic pickup in a turbine
flowmeter, or a voltage pulse output from a
flowmeter.
The following table shows the switching
thresholds for the various transducers, plus the
maximum operating frequency and the input
terminal numbers. For reliable counting the
input signal must fall below the lower switching
threshold and rise above the upper threshold.
Switching
thresholds Freq
max Input
terminals
Switch 100Ω1000Ω100Hz 12 & 11 +
Proximity
detector 1.2mA 2.1mA 5 kHz 12 & 11 +
Open
collector 2kΩ10kΩ5kHz 12 & 11 +
Magnetic
pickup 10mV 30mV 5kHz 16 & 15 +
Low
voltage
pulse 1V 3V 5kHz 16 & 14 +
High
voltage
pulse 3V 10V 5kHz 16 & 13 +
Note: Only one input may be used at a time.
4.2.2.1 Switch contact input
Any mechanically activated switch contact
located in the hazardous area may be
connected directly to terminals 12 & 11
providing the switch has IP20 protection and
can withstand a 500V rms insulation test to
earth. Most magnetically activated reed relays
used in turbine flowmeters comply with this
requirement.
The maximum operating frequency for a switch
contact input is 100Hz.
4.2.2.2 2-wire proximity detector input
Any EEx ia certified intrinsically safe 2-wire
proximity detector complying with NAMUR
switching thresholds may be used, providing
the input safety parameters of the proximity
detector are equal to or greater than:
Ui ≥10.6V dc
Ii ≥20mA dc
Pi ≥50mW
If located in the same hazardous area as the
batch controller the proximity detector may be
directly connected to terminals 12 & 11
When programmed to operate with a proximity
detector, the maximum input frequency of the
BA458C batch controller is 5kHz.
4.2.2.3 Voltage pulse input
Voltage pulse sources may be connected
directly to input 2, the terminals used depend
upon the input magnitude – see the table in
section 4.2.2. All these terminals comply with
the requirements for simple apparatus and
they may be directly connected to any EEx ia
certified intrinsically safe voltage source within
the hazardous area. The source must be able
to withstand a 500V rms insulation test to earth
for one minute and have output parameters
equal to or less than:
Uo ≤28V dc
Io ≤100mA dc
Po ≤0.66W
This enables the BA458C to be connected
directly to most flowmeters incorporating a
certified intrinsically safe magnetic pickup, or a
certified intrinsically safe amplifier producing a
high level pulse output. The BA458C has
three selectable voltage switching thresholds,
for magnetic pickups, low voltage pulses and
high voltage pulses.
When programmed to operate with a voltage
pulse source, the maximum input frequency of
the BA458C batch controller is 5kHz.

10
4.2.3 4/20mA analogue input
The BA458C can also accept an analogue
4/20mA input representing rate of flow from a
current source, not a current sink. Loop
powered flow transmitters require an additional
power supply. The analogue input terminals
comply with the requirements for simple
apparatus allowing almost any intrinsically
safe 4/20mA signal to be connected directly to
the batch controller.
Voltage
drop Freq.
Max. Input
terminals
4/20mA 0.6V 2Hz 16 & 17+
4.2.4 Switch outputs
Each of the three switch outputs is a
galvanically isolated single pole solid state
switch as shown in Fig 5.
Fig 5 Equivalent circuit of each switch output
The output is polarised so current will only flow
in one direction. Terminals A1, A3 and A5
should be connected to the positive side of the
supply. The ‘on’ and ‘off’ performance of each
switch output is:
Ron = 5Ω+ 0.7V
Roff = greater than 1MΩ
Any hazardous area intrinsically safe circuit
may be switched by one of these outputs
providing the output safety parameters of the
circuit are less than the maximum input
parameters of the switch. Alternatively the
switch contact may be transferred to the safe
area via a Zener barrier which again must have
safety parameter less than the maximum input
safety parameters of the switch.
Notes: Because of the series protection
diode, some test meters may not
detect a closed switch output.
Terminals A7 to A12 are for optional
factory fitted outputs 4, 5 and 6.
WARNING
These switch outputs should not be
used for critical safety applications.
When the BA458C power supply is turned off
or disconnected, all BA458C switch outputs will
open.
4.3 Use with galvanic isolators
Galvanic isolators are probably the simplest
intrinsically safe interface as they provide
isolation and do not require a high integrity
earth connection.
Any galvanic isolator certified EEx ia IIC by an
EEC approved certification body may be used
providing that the safety parameters of the
isolator terminals are compatible with the
safety parameters of the batch controller
terminals to which the isolator is connected.
To assist with system design, the galvanic
isolator System Certificate specifies the safety
description of the galvanic isolators that may
be used and lists the maximum permitted cable
parameters.
Fig 6 illustrates the basic circuit that is used for
all BA458C installations protected by galvanic
isolators. Although the BA458C batch
controller will operate from a wide range of
input sources, only one source may be
connected at any time.
Alternatively the input source may be located
in the safe area. Fig 7 shows how an
additional isolator may be used to transfer the
input signal from the safe area to the batch
controller in the hazardous area.
4.3.1 Power supply
Any certified galvanic isolator may be used to
power the BA458C providing the output safety
parameters are less than the maximum
permitted input safety parameters of terminals
1 & 2. In addition to matching the safety
parameters, the isolator must be capable of
supplying at least 11V to terminals 1 & 2 at
33mA.
CAUTION
The safety components within the batch
controller limit the voltage between
terminals 1 and 2 at 15V. If the batch
controller is directly connected to a 15V or
greater power supply without a galvanic
isolator or equivalent series resistor, the
instrument will consume a large current for
a few seconds and then shut-down to
prevent permanent damage. To test a
BA458C batch controller in a safe area
workshop, terminals 1 & 2 should be
connected to a 24V dc power supply via a
330Ωresistor.

11
Fig 6 Batch controller powered by a galvanic
isolators with input in hazardous area.
Fig 7 Batch controller protected by galvanic
isolators with input in the safe area.
4.3.2 Inputs
When the batch controller is powered from a
galvanic isolator, the pulse and analogue
inputs remain the same as described in
sections 4.2.2 and 4.2.3. Only when the input
transducer or source is in the safe area, as
shown in Fig 7, are galvanic isolators required
in the input circuit.
Any EEx ia IIC certified galvanic isolator may
be used providing that the safety parameters
of the isolator terminals are compatible with the
safety parameters of the batch controller input
terminals to which it is connected. The
galvanic isolator must also be able to transfer
the required type of input into the hazardous
area.
4.3.3 Switch outputs
WARNING
These switch outputs should not be
used for critical safety applications.
When the batch controller is powered from a
galvanic isolator, the switch outputs remain the
same as described in section 4.2.4 Only when
the switch output is required in the safe area is
a galvanic isolator required. A wide variety of
switch transfer isolators are available with a
selection of relay and solid state outputs.
Again the output parameters of the galvanic
isolator must be less than the maximum
permitted input parameters of the batch
controller switch.
4.4 External switches
For applications requiring the batch controller
to be operated via large industrial push-
buttons, four external switches may be
connected as shown in Fig 2. Unlike the front
panel pushbuttons, each external switch has a
dedicated operating and configuration function.
Switch
number Switch function when
Operating Configuring
S1 Start Down
S2 Stop Up
S3 Reset P
S4 Menu E

12
Section 3.6 describes the use of external
switches in the hazardous area, but they may
also be located in the safe area.
A certified intrinsically safe relay or a galvanic
isolator with a switch contact output is required
to transfer the switch contact from the safe to
the hazardous area. The combined permitted
input safety parameters for batch controller
terminals S1 to S7 are zero, therefore Zener
barriers can not be used.
Fig 8 shows how the external Stop buttons
may be located in the safe and hazardous
areas.
Fig 8 Stop buttons in hazardous & safe areas
4.5 Inhibit link
Linking terminals 18 and 20 together inhibits
the batch controller input. If linked during a
batch, dispensing will continue but it will not be
shown on the batch display. These terminals
may only be connected to a hazardous area
mechanically operated switch having IP20
protection and able to withstand an ac test
voltage of 500V to earth for one minute. See
section 3.7.
4.6 Security link
Access to the configuration menus is only
available when terminals 18 & 19 are linked
together – see section 6.1. These terminals
may only be linked together at the instrument,
or connected to a hazardous area
mechanically operated switch having IP20
protection and able to withstand an ac test
voltage of 500V to earth for one minute. See
section 3.7.
5. INSTALLATION
5.1 Location
The BA458C is housed in a robust aluminium
enclosure with a toughened glass window
mounted in a Noryl bezel. The front of the
instrument provides IP65 protection and a
gasket seals the joint between the instrument
enclosure and the panel. The instrument may
be installed in any panel providing the
environmental limits shown in the specification
are not exceeded.
Fig 9 shows the overall dimensions of the
BA458C and the panel cut-out. To achieve an
IP65 seal between the instrument enclosure
and the panel, the smaller cut-out must be
used and the instrument secured with four
panel mounting clips.
The BA458C liquid crystal display has
maximum contrast when viewed from directly
ahead and slightly below the centre line of the
instrument.
Fig 9 BA458C dimensions

13
5.2 Installation Procedure
a. Insert the BA458C into the instrument
panel cut-out from the front of the
panel.
b. Fix panel mounting clips to opposite
sides of the instrument and tighten until
the instrument is secure as shown in
Fig 10. Four clips are required to
achieve an IP65 seal between the
instrument enclosure and the panel.
c. Connect the panel wiring to the rear
terminal block(s) as shown in Fig 10.
To simplify installation, the terminals
are removable so that panel wiring can
be completed before the instrument is
installed.
5.3 EMC
The BA458C complies with the requirements of
the European EMC Directive 89/336/EEC. For
specified immunity all wiring should be in
screened twisted pairs.
To prevent circulating currents, cable screens
should only be earthed at one point in the safe
area.
Fig 10 Installation and terminal connections

14
6. CONFIGURATION MENUS
The BA458C batch controller is configured via
the front panel pushbuttons. Configuration
functions are contained in three easy to use
sub-menus, ‘System Settings’, ‘Batch Settings’
and ‘Rate Settings’. A fourth sub-menu
‘Information’ shows how the instrument has
been configured.
Although the BA458 batch controller contains
many sophisticated functions, it remains simple
to operate and configure. Menu navigation is
explained in section 6.2. Guided by on-screen
prompts, the use of the configuration functions
is intuitive, but all the functions are fully
described in this manual.
6.1 Security
To prevent unauthorised or accidental
adjustment, the configuration menus can only
be accessed when an external link is fitted
between terminals 18 and 19 as shown below.
Terminals Access to
18 and 19 configuration menus
Linked Yes
Not linked No
When authorised personnel need to make
frequent configuration adjustments, the
security link terminals may be wired to a key
switch located in the hazardous area.
The configuration menus may also be
protected by a user selectable four digit
security code.
A separate four digit user selectable security
code may be applied to the operator menu
6.2 Navigation
The BA458C is configured via the front panel
push-buttons which are soft-keys identified on
the display screen.
This manual contains simplified drawings of
the batch controller display screens associated
with most functions. Although some screens
may consist of multiple pages that are
automatically accessed by scrolling through
the options, in this manual they are shown on
one page with the default option in bold.
Within this manual push-buttons are shown in
italics e.g. P or Up push-button and legends
displayed by the batch controller are shown
within inverted commas e.g. 'Running'.
When the batch controller is displaying ‘Ready’
access to the main configuration menu is
obtained by pressing the Pand Ebuttons
simultaneously or, if enabled, via the Operator
Menu. The configuration menu can not be
accessed while the batch controller is running.
Once within the main menu the Up and Down
buttons move the highlight bar between sub-
menus. When the required option has been
highlighted, operating the Pbutton will access
the sub-menu.
The highlight bar is static when indicating a
menu or sub-menu. When indicating an option
which has to be selected, or a variable that has
to be entered, the highlight bar flashes on and
off.
The configuration main menu comprises four
sub-menus:
System Settings Defines function of batch
controller including
outputs & display
screen.
See Fig 11 & section 6.4
Batch Settings Defines batch
parameters.
See Fig 14 & section 6.5
Rate Settings Defines rate parameters.
See Fig 16 & section 6.6
Information Lists all the batch
controller settings and
allows the Grand Total
to be read.
See Appendix 2
Highlighting the required function within the
sub-menu and operating the Ppushbutton will
enter the function menu. Functions offer a
choice of options or an invitation to enter a
variable.
To select an option in a function menu
Press the Up or Down button to move the
flashing display highlight bar to the
required option, operating the E button will
then store the selected option and move
the display up one level to the sub-menu.
To enter a variable
Variables are entered digit by digit, the
flashing digit being adjusted using the Up
or Down button. When a digit is set as
required operating the Pbutton will
transfer control to the next digit. When all
the digits have been adjusted, operating
the E button will store the variable and
move the display up one level to the sub-
menu.

15
When navigating through the menus the push-
button(s) should be held until the required
screen is displayed.
Note:
Functions that are dependent on a higher level
option are automatically removed from the sub-
menu when the higher level option is not
selected. e.g. If the batch controller is
configured for a pulse input, all the calibration
functions associated with a 4/20mA input will
be automatically removed from the menus.
6.3 Default configuration
Unless otherwise requested at the time of
ordering, BA458C batch controllers will be
supplied configured as follows:
System Settings
Language English
Operator control Both Local &
Remote.
Signal Input Open Collector
Lineariser Off
Restart Normal
Output 2 Unused
Output 3 Unused
Optional outputs 4, 5 & 6 Unused
Pulse Output Display / 1
Grand Total Cleared
Security
Config. Code 0000
Operator Code 0000
Operator Menu
Batch Sizing On
Batch Select On
History On
Config. Menu On
Operator Screens Screen 1
Batch Settings
Scale factor (Linear pulse) 000001.
Scaling (4/20mA input) 000001.
Batch D.P. 00000000.
Batch Legend No legend
Batch Limit 99999999
Batch Names Batch 1
Batch Size 00000000.
Select Batch Batch 1
CONTROL2delay 0000
CONTROL2stop 00000000.
CONTROL3delay 0000
CONTROL3stop 00000000.
Count Mode Up
Overrun Comp Off
Batch Cycles 1
Restart Delay 00 : 00 : 00
Rate Settings
Rate Scaling 000001.
Rate D.P. 00000.0
20mA Display 00100.0
Rate Legend No legend
Timebase Seconds
Rate Filter
Smoothing 2
Jump-Out 4
Flow Alarm 00000.0
Inhibit Time 0000
Clip-Off 00000.0
Default parameters may be globally restored
see section 6.4.13

16
Fig 11 System Settings

17
6.4 SYSTEM SETTINGS
See Fig 11.
6.4.1 Language
The BA458C can display operating messages
and menus in three different languages:
Deutsch
English
Francais
Set Language
Highlight the required language and press Eto
enter the selection.
6.4.2 User Control
The BA458C batch controller may be
controlled by the front panel pushbuttons, by
remote switches or by both the front panel
switches and the remote switches.
Local
Remote
Both
Set user Controls
Highlight the required option and press Eto
enter the selection.
6.4.3 Signal Input
A wide variety of analogue and digital
transduces and sources may be connected to
the batch controller.
Open Collector
Prox Detector
Switch Contact
Magnetic pickup
Voltage Pulse
4/20mA
4/20mA Sq. Law
Set Input Type
Notes: Input terminals vary depending upon
the type of input, see sections 4.2.2
and 4.2.3.
The brilliance of the display backlight
is reduced when open collector,
proximity detector or switch contact
inputs are selected.
6.4.4 4mA Calibration
Note: Only necessary when 4/20mA input is
used
When the BA458C batch controller is supplied
the analogue current input will have been
accurately factory calibrated, it is only
necessary to perform this calibration as part of
routine maintenance.
To perform the calibration connect a 4 to 20mA
current source to batch controller terminals 16
& 17(+) and adjust the input current to exactly
4mA. To achieve maximum batch controller
performance, the accuracy of the current
source should be greater than ±0.025% (4uA).
To prevent the batch controller calibration
being accidentally corrupted the instruction has
to be confirmed before it will be executed.
Calibrate
Cancel
CAL. (Inject 4mA)
Highlight the ‘Calibrate’ option and operate the
E pushbutton, which will result in the
confirmation screen being displayed. To
perform the calibration highlight ‘Continue’ and
press E, after a few seconds the display will
return to the System setting menu.
Continue
Cancel
Are you sure?
6.4.5 20mA Calibration
This function is identical to the 4mA calibration
described in the previous section 6.4.4, but a
20mA input current should be used.
6.4.6 Lineariser (Pulse inputs)
The 16 point straight line lineariser will
compensate for k-factor non-linearity in turbine
flowmeters.
This function turns the lineariser on and off,
calibration parameters are entered in the Batch
Setting menu – See sections 6.5.1 and 6.5.2 .
On
Off
Set Lineariser
Highlight the required setting and press Eto
enter the selection.

18
6.4.7 Restart
This function determines what happens at the
end of each batch. There are three options:
Normal: The display screen shows the
volume that has been
dispensed. Before another
batch can be started the Reset
push-button must be operated.
The screen will then display
‘Ready’.
Quick: The display screen shows the
volume that has been
dispensed. Operating the Start
pushbutton will reset the batch
controller and start another
batch.
Auto restart: The display screen shows the
volume that has been
dispensed. After a configurable
restart delay (See 6.5.19) the
batch controller automatically
resets and starts another batch.
The number of batch cycles to
be performed is defined by the
Batch Cycle function, which is
contained in the Batch Setting
menu. See 6.5.18
Normal
Quick
Auto
Set Batch Restart
Highlight the required option and press Eto
enter the selection.
6.4.8 Output 2
Output 2 is an isolated single pole solid state
switch contact that is connected to terminals
A3 and A4. It may be configured to output any
one of six different signals, or may be unused.
Unused
Control 2
Control 3
Flow alarm
Reset status
Batch status
Pulse Output
Set O/P 2 Function
Highlight the required option and press Eto
enter the selection.
Note: Two or more of the outputs may be
configured to output the same function.
6.4.9 Output 3
As Output 2 except terminals are A5 and A6.
6.4.10 Optional outputs 4, 5 and 6
Only available when factory fitted option is
installed in the BA458C batch controller.
Configuration is the same as for Output 2,
except terminal numbers are:
Output Terminal numbers
4 A7 & A8
5 A9 & A10
6 A11 & A12
6.4.11 Pulse Output
Any of the batch controller outputs may be
configured as a pulse output. The number of
output pulses is proportional to the total
volume dispensed by the batch controller.
This Pulse Output function enables the pulse
output frequency to be reduced by one of five
dividing factors between 10 and 100,000.
Display / 1
Display / 10
Display / 100
Display / 1000
Display / 10000
Display / 100000
Set Output Rate
Highlight the required option and press Eto
enter the selection.
Note: Maximum output frequency is 4 Hz.
6.4.12 Clear Grand Total
The Grand Total is a record of the total
quantity of product dispensed since the Grand
Total was last reset to zero. It must be zeroed
every time the batch controller scaling is
changed
The Grand Total can be viewed in the
Information section of the System Menu – see
section 6.2. CAUTION
After zeroing the old grand total
can not be recovered
To prevent the Grand Total being accidentally
zeroed, the clear instruction has to be
confirmed before it will be executed.
Clear G Total
Cancel
Clear Grand Total

19
If ‘Clear G Total’ is highlighted and the E
pushbutton operated, a second screen will be
presented. To confirm that the Grand Total is
to be zeroed highlight ‘Continue’ and press E
which will result in the instruction being
executed.
Continue
Cancel
Clear Grand Total
6.4.13 Defaults
This function allows the configuration defaults
listed in section 6.3 to be globally restored.
Although useful for defining a starting point
when commissioning a batch controller, the
settings overwritten by this command can not
be recovered
CAUTION
After restoring default configuration the
previous settings can not be recovered.
To prevent the default settings being
accidentally restored, the instruction has to be
confirmed before it will be executed.
Restore Defaults
Cancel
Restore Defaults
If ‘Restore Defaults’ is highlighted and the E
pushbutton operated, a second screen will be
presented. To confirm that the defaults are to
be restored, highlight ‘Continue’ and press E
which will result in the instruction being
executed.
Continue
Cancel
Restore Defaults
6.4.14 Security
A summary of instrument security is contained
in section 6.1 of this manual.
This security function enables the four digit
security codes protecting the configuration and
operator menus to be defined. It also allows
the contents of the operator menu to be
selected.
Config Code
Operator Code
Operator Menu
Security
Highlighting the required function and pressing
Pwill result in a selection menu being
displayed.
Each of the two security codes is entered digit
by digit, when all four digits have been set,
pressing Ewill enter the code and return the
display the security menu.
0000
Set Config Code
Note: Default code 0000 disables the
security function and allows
unrestricted access to the menu.
Access to the Configuration Menus is
also protected by an external link as
described in section 6.1
Contents of the Operator Menu are defined by
toggling the ‘On / Off’ box associated with
each item. To make the selection, highlight
the item to be changed and operate the P
button. The item may then be turned ‘On’ or
‘Off’ using the Up or Down push-buttons.
Batch Sizing: On
Batch Select: On
History On
Config Menu: On
Set Operator Menu
Pressing Ewill enter the selection, another
item may then be selected or the display
returned to the Security menu by pressing E
again.

20
6.4.15 Operator Screens
The user screen may be selected from six
different formats that are shown in Appendix 1.
They show different information and have
different display sizes so that the operator is
only presented with the essential information
necessary to operate the batching system.
Some screens include graphical information
allowing batch progress to be rapidly
assessed. Screen formats are shown in
Appendix 1.
Screen 6 is intended for commissioning and
shows all engineering information including
output status and flow rate.
SCREEN 1
SCREEN 2
to
SCREEN 6
Set User Screen
Highlight the required option and press Eto
enter the selection.
6.4.16 Display
The display contrast and backlight brilliance
are adjustable using this function. The two
adjustments are made with the Up and Down
buttons, the amplitude of each being shown on
a horizontal bargraph. Control is transferred
between brilliance and contrast by operating
the Ppushbutton.
After adjustment pressing Eenters the
changes and returns the display to the System
Menu.
6.4.17 Output options
Control 1 is a dedicated output that is always
connected to terminals A1 and A2. Control 1
is energised immediately the Start button is
operated and de-energised when the batched
volume equals the batch setpoint.
Outputs 2 and 3 may be configured to output
six different signals or they may be unused as
described in sections 6.4.8 & 9. The following
sections describe each of these selectable
signals.
6.4.17.1 Control 2
This output is similar to Control 1. It is
energised a configurable time
CONTROL2delay after Control 1 is energised
and de-energised a configurable batched
volume CONTROL2stop before Control 1 is
de-energised. Fig. 1 shows the operation
diagrammatically.
6.4.17.2 Control 3
This output is identical to Control 2 except
delays are defined by CONTROL3delay and
CONTROL3stop.
6.4.17.3 Flow alarm
This output is described in section 6.6.7
6.4.17.4 Reset status
The reset status output indicates when the
batch has been started and when the controller
has been reset and is ready to start another
batch. See Fig 12.
Fig 12 Reset status timing
6.4.17.5 Batch status
The batch status output is the inverse of
Control 1 except that it does not close if a
pause is initiated during a batch. See Fig 13.
Fig 13 Batch status timing
6.4.17.6 Pulse output
This output is described in section 6.4.11
Table of contents
Other BEKA Controllers manuals
Popular Controllers manuals by other brands
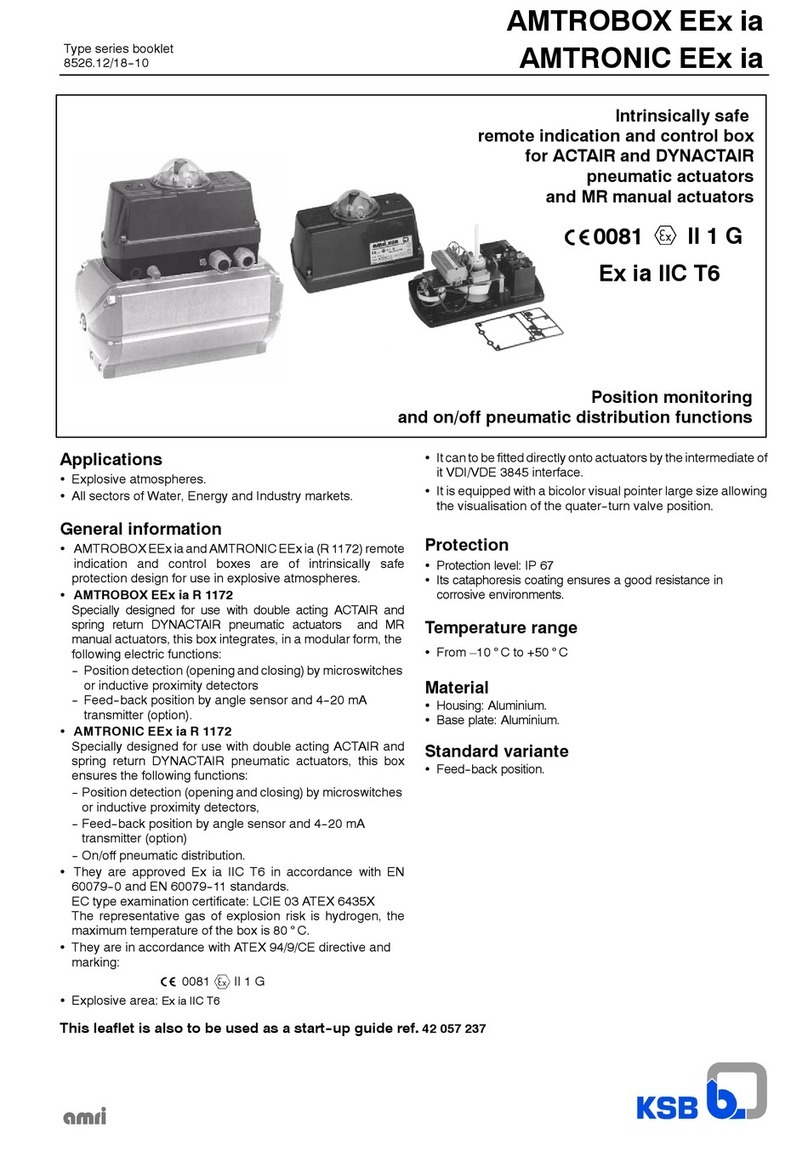
KSB
KSB AMTROBOX EEx ia General information
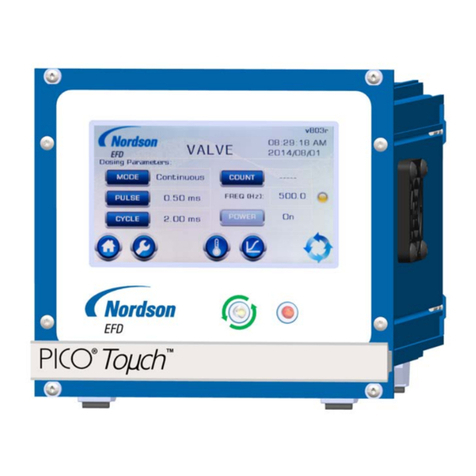
Nordson EFD
Nordson EFD PICO Touch operating manual

Mitsubishi Electric
Mitsubishi Electric AG-150A Instruction book
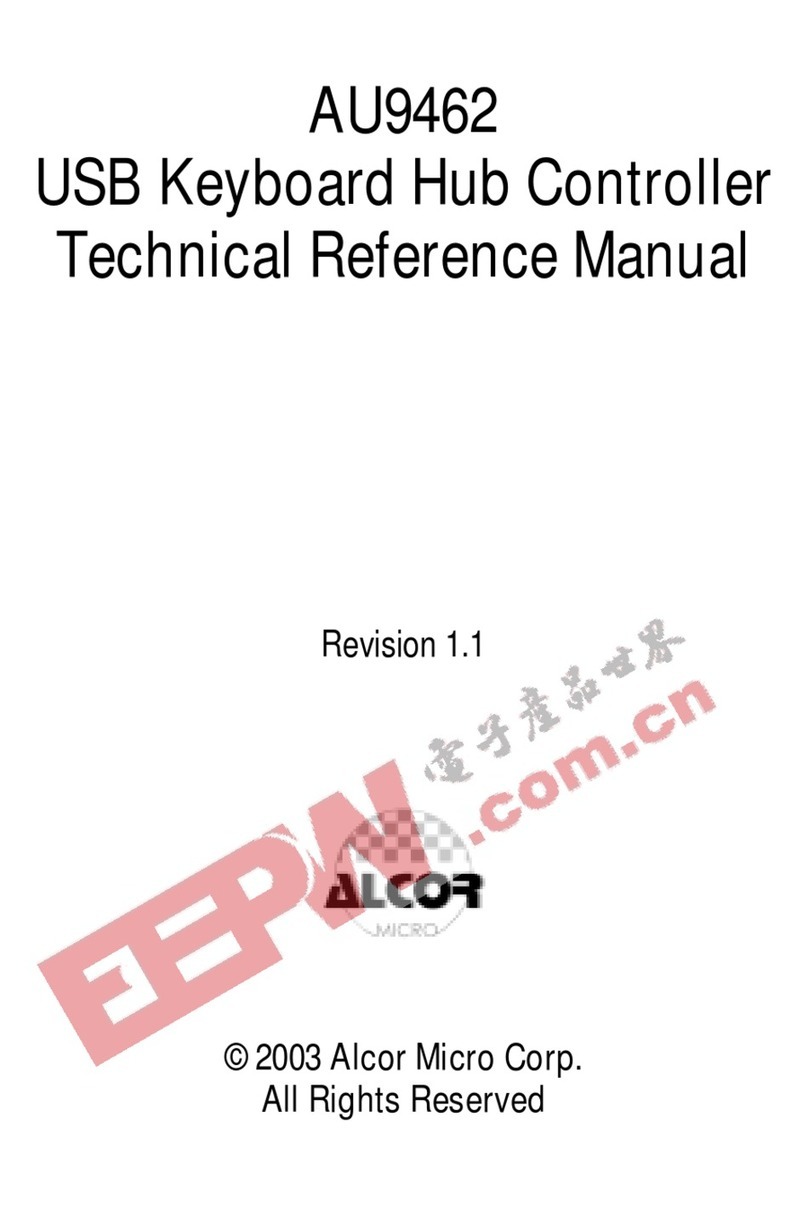
Alcor Micro
Alcor Micro AU9462 Technical reference manual
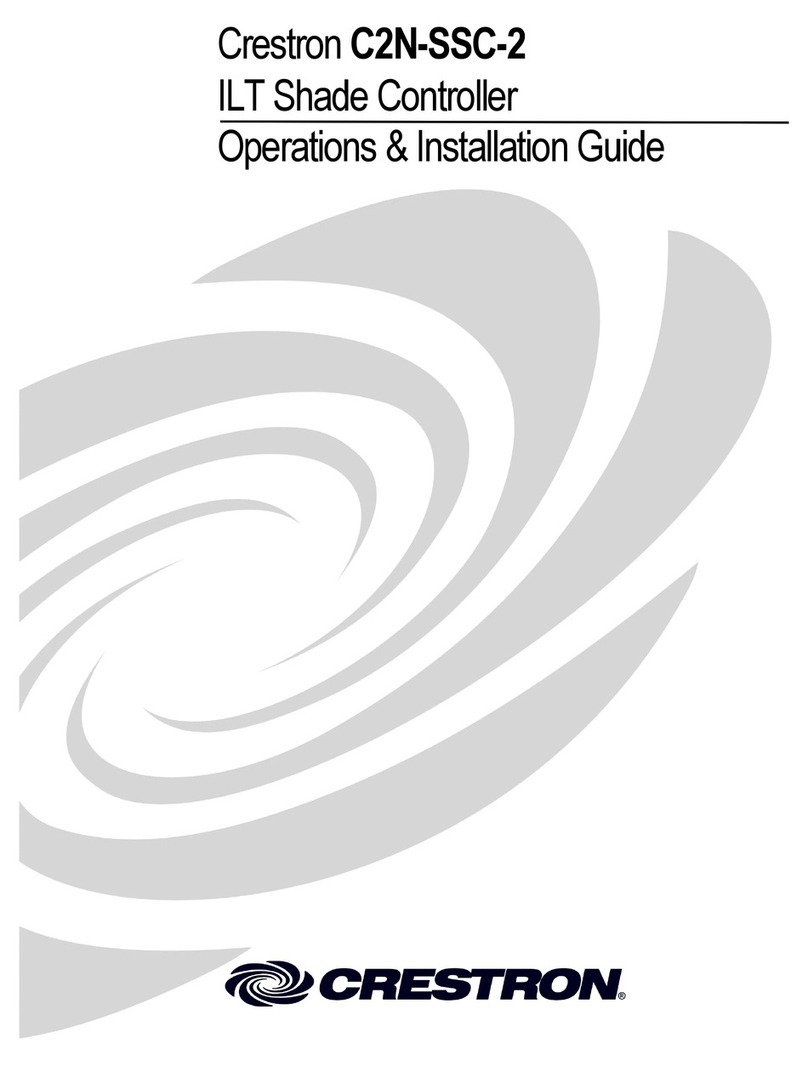
Crestron
Crestron C2N-SSC-2 Operations & installation guide
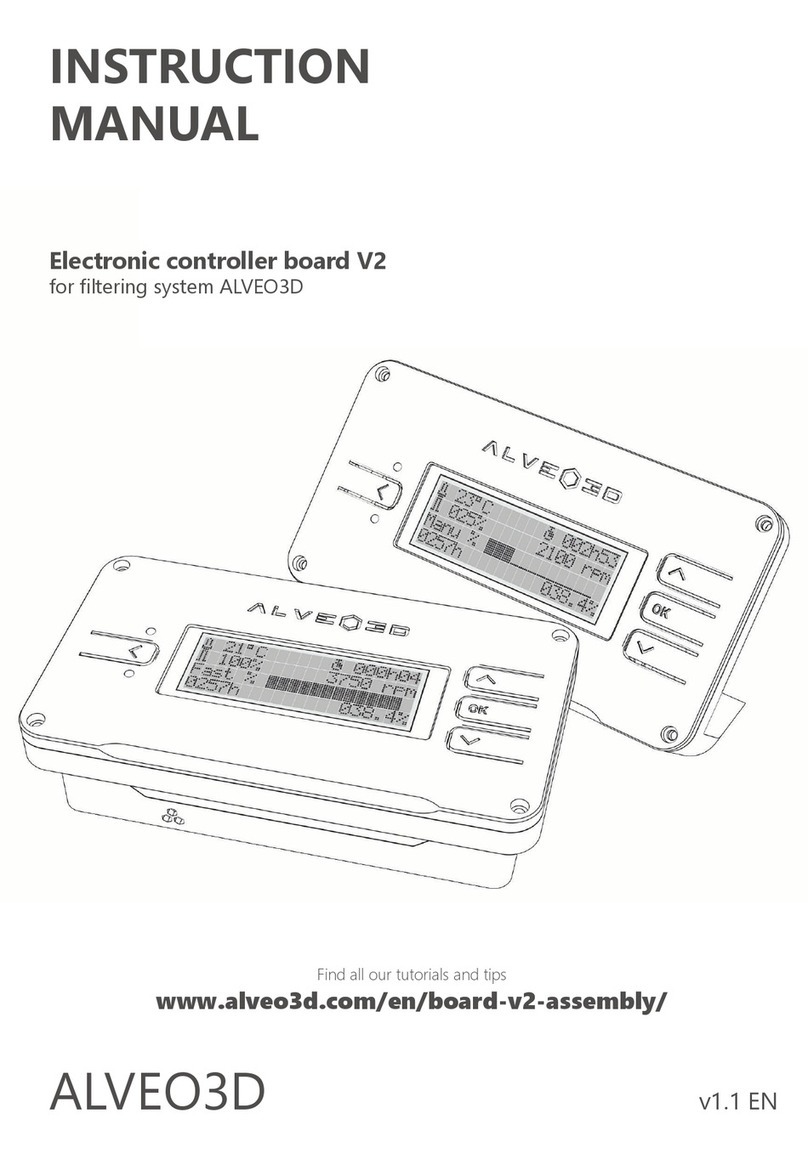
ALVEO3D
ALVEO3D V2 instruction manual
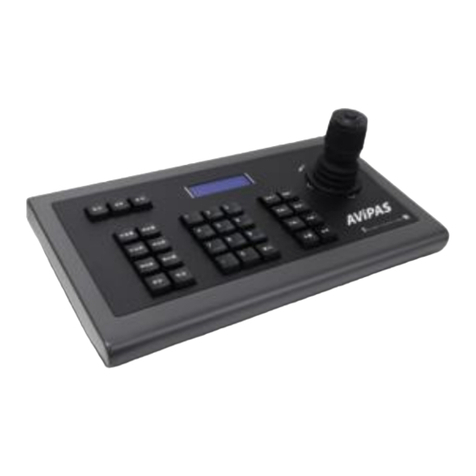
Avipas
Avipas AV-3104SE user manual
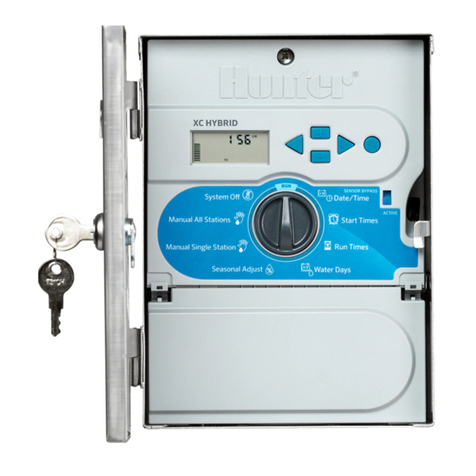
Hunter
Hunter XC hybrid Owners manual and programming instructions
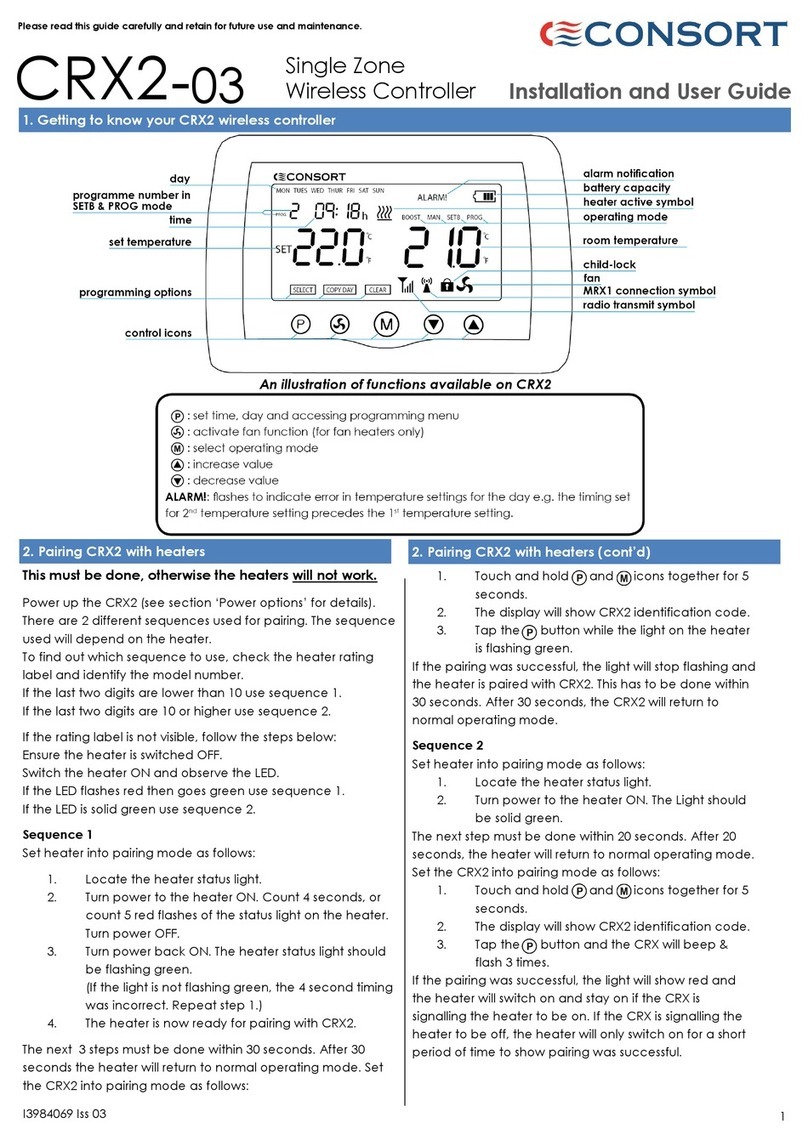
Consort
Consort CRX2-03 Installation and user guide
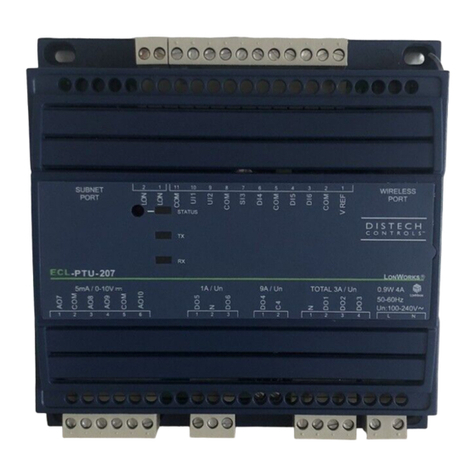
Distech Controls
Distech Controls ECL-PTU-207 user guide

Centork
Centork 482 Series Installation and Maintenance user Manual
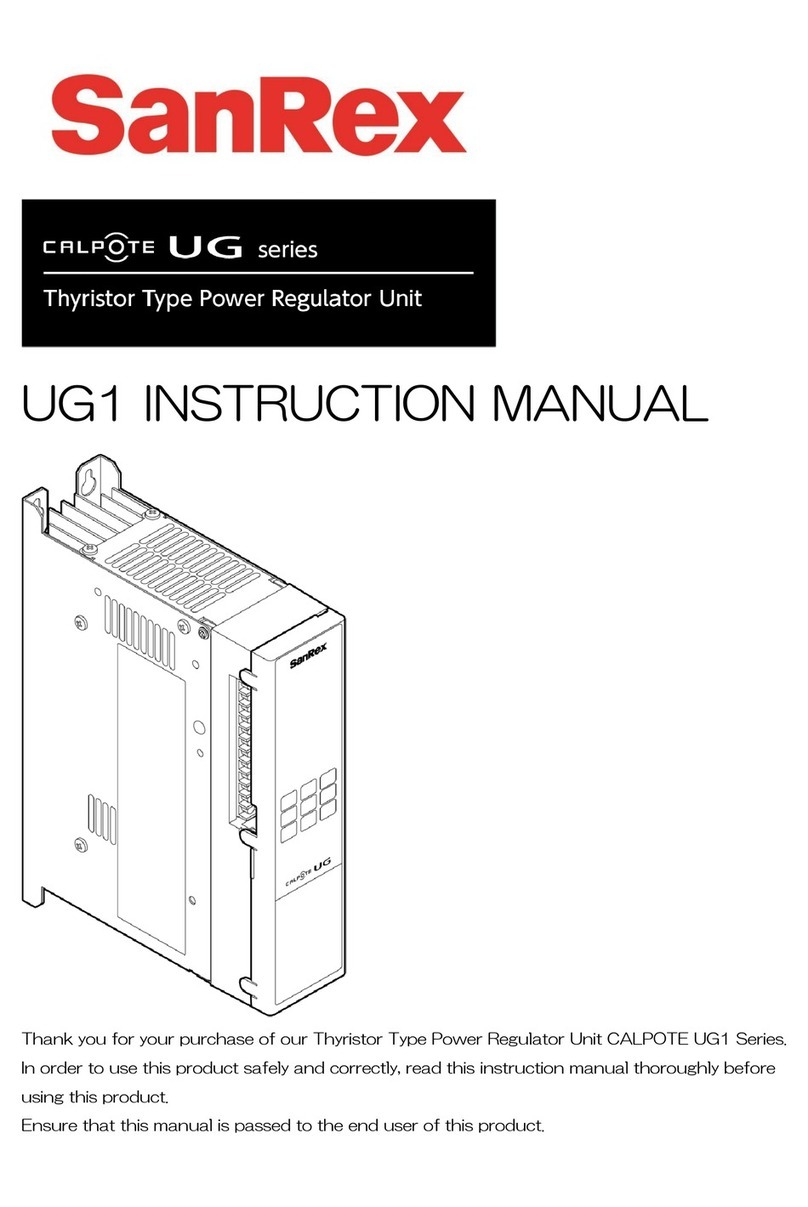
SanRex
SanRex CALPOTE UG Series instruction manual