ADTEK CS2-TM User manual

1/27 CS2-TM(Pulse)-OperatingManual2012-05-10
CS2-TM(Pulse Input)
T
O
TALIZER
/
BAT
C
H
/
IMMEDIATE VALUE
(for Flowmeter or Lengh/RPM)
CONTROLLER
USER MANUAL
■ DESCRIPTION
The CS2-TM(Pulse Input) is innovation totalizer. Adtek builds in
high technology with wide input range from 0.01Hz~ 140.00KHz with
auto-range function at same unit. There are three setting modes for
K factor, 1/K factor and flow speed to match the difference output
description of flowmeters.
The Totalizer provides high accuracy measurement, display,
control and communication (Modbus RTU mode) of Pulse from
flowmeter or encoder, approach switch, photo switch for length
control.
There are two display screen and 3 external control input
(DI) in standard and the optional 4 Relay, 1 Analogue, 1 Pulse
and RS485 port available. They are also support fantastic
control function as like as N, C, R mode for totalizer and batch
control.
■ FEATUTRES
● Measuring Pulse AUTO RANGE 0.01Hz~100KHz(optional:140KHz); Contact / NPN / PNP / Voltage Pulse can
be switch on rear of meter
● Dual display screen for 10 digital Totalizer or Batch counter + 4 2/3 Immediate Value(PV) or 6 digital
Batch programmable.
● 4 relay can be individual programmed to relative immediate value, totalizer or batch.
Relative to Immediate Value(PV): Functions settable Energized Mode Hi / Lo / Hi(Lo) Hold / Do / Go,
Hysteresys‚ Energized Delay, De-energized Delay, Energized latch or Energized by RS485
command.
Relative to Totalizer / Batch: N/C/R mode and energized time programmable.
● 3 external control input can be individual programmed for immediate value(PV) or totalizer / batch.
Immediate Value(PV): PV Hold / Reset for Maximum or Minimum Hold / DI / Reset for Relay
Energized Latch
Totalizer / Batch: Reset, Gate
● Analogue Output and Pulse Output available in option
● RS485(Modbus RTU mode), Baud Rate is up to 38400bps
● Comply to CE standard
FUNCTIONS
■ Input & Scaling 1Pulse/Flow-unit(K factor):
The decimal point of K Factor: Setting range from
0.0 to 0.0000.
Pulse/Flow-unit(K factor): Setting range from
0.0001 to 9999.9
Flow/Pulse (1/K factor):
The decimal point of 1/K Factor: Setting range from
0.0 to 0.0000.
Flow/Pulse(1/K factor): Setting range from 0.0001
to 9999.9
Valume/Hz:
The decimal point of pipe’s diameter: Setting range
from 0.0 to 0.0000.
Diameter of pipe: Setting range from 0.0 to 0.0000M
The decimal point of flow speed (Lengh/sec):
Setting range from 0.0 to 0.0000.
Flow Speed: Setting range from 0.0001 to 9999.9M
Input Range
The meter has been designed very wide input
range from 0.01Hz~100.00KHz(Option:
0.01Hz~140.00KHz) that can cover almost any
application for flowmeter. User doesn’t need to
specify the input range.
Three setting modes for flowmeters
There are three types setting for Pulse/Flow-unit(K
factor), Flow/Pulse(1/K factor) and Flow rate/Hz to
match the difference output description of
flowmeters. Engineer needs just to check the mode
of flowmeter and setting. The totalizer will
calculating the flow rate, and accumulation.

2/27 CS2-TM(Pulse)-OperatingManual2012-05-10
■ DISPLAY FUNCTIONS
A
uto Range:
Three mode selectable between Auto(Auto
range)/SEMi(Semi-Auto range)/MANUL(Manual
range)
Auto(Auto range): The decimal point will be auto
changed according to the input frequency so that
keep reading in the highest resolution.
SEMi(Semi-Auto range): The decimal point will be
auto changed according to the input frequency to
keep reading in the highest resolution under setting
position of decimal point.
MANUL(Manual range): The decimal point will be
fixed according to the setting of decimal point. So,
it’s possible to show “overflow”, if the input
frequency is over the display range.
Time out at Lowest frequency
In the case of low frequency, the totalizer can not
to identify that is low frequency and no input until
the next pulse input. Sometimes, it takes a long
period.
CS2-TM builds in a time out function to cut out
the reading. There are two modes MAnAL / AUto
can be selected.
MANUL(Manual): There is a period named ito
can be set from 0.0 sec~999.9sec. The reading will
display “0”, when the next pulse doesn’t input during
the setting time.
Auto(Auto range): The reading will display “0”,
when the next pulse doesn’t input during the time that
gave by formular of meter’s firmware.
Dual Display screens
Down screen can be Immediate Value(PV) and
Batch programmable; Up screen can be Totalizer
and Batch counter programmable.
Maximum Hold or Minimum Hold for PV
When the DSPLY function in【Input Group】set to be
MAX.H(Max. Hold) or Mini.H(Mini. Hold), The meter
will keep display in maximum (or minimum) value of
Immediate Value(PV) during power on, until manual
reset by front key in 【User Level】, Up/Down Key
function or【External Control Input(E.C.I.)】; The
Reset functions will be explan in detail in following.
Please paste the sticker M.H
on the red square LED to
identify the status of display.
Immediate Value(PV) Hold
When the External Control input set to be Pv.
HLd(PV Hold) function in【ECI Gruop】, The display
will be hold, when the E.C.I. is closed until the E.C.I.
is to be open.
Please paste the sticker P
V
.H
on the green square LED
of ECI to identify the status of display.
Max. ( Mini.) Hold & Reset PV Hold & Reset
Present
Value
ResetDataHold
by E.C.I. ON Level
Trigger
ON ON
Reset the Max.(or
Mini.) Hold by
E.C.I. or Front Key
ON
Level Trigger
Maximum Hold PV Hold
Present
Value
Write to display by RS485 command
The display can be written by RS485 command. At
meantime, the display is no longer according to the
input signal. In past, The meter normally receive
4~20mA or 0~10V from AO card or BCD card of PLC.
We support a new solution by RS485 writing in so
that can be save cost and wiring into PLC.
Low Cut
Setting range from -29999~+29999 counts.
Low Cut set to be +0.50
Low Cut set to be -0.10
-0.10
Low cut
function
Low Cut is set for 0.50, if the P
V
is
from -0.50~+0.50, that display will be 0. Low Cut is set for -0.10, if the PV
is under
(<= -0.10), that display will be -0.10.
PV according
to input signal
Present
Value
Low cut
function
0.50
-0.50
Present
Value PV according
to input signal
If the setting value is positive, it means the range
of absolute value will be 0; PV≤Setting value, the
display will be 0;
Ex:Low Cut is set for 0.10, if the display is from
-0.10~+0.10, that will be 0.
If the setting value is negative, it means the range
of under setting value will be 0; PV≤-Setting value,
the display will be 0;
Ex:Low Cut is set for -0.01, if the display is ≤-0.01,
and all the display will be 0.
Digital Fine Adjustment
Setting range from -19999~+29999 ;
Users can get Fine Adjustment by front key of the
meter, and “Just Key In” the value which user want
to show in the current input signals.
■ READING STABLE FUNCTIONS
A
verage Display update
Setting range: 1~99 times;
The meter’s sampling is 15cycle/sec. If the
AvG(Average) set to be 3, it means the meter is
sampling 3 readings, and calculating the average
then update display once. At meantime, the display
update will be 5 times/sec.
A
verage set to be 3
Remark: The higher average setting will cause the response time of Relay and Analogue output slower.
Sample 1
Sample 2
Sample 3
Sample 4
Sample 5 Sample 6 …….
Display Update Value =
(Sample 1 + Sample 2 + Sample 3)/3
Display Update Value =
(Sample 1 + Sample 2+ Sample 3)/3
Digital filter
Setting range from 0(None)/1~99 times. The digital
filter can reduce the magnetic noise in field.

3/27 CS2-TM(Pulse)-OperatingManual2012-05-10
■ RELAY FUNCTIONS ■ 3 External Control Inputs(E.C.I.)
Multi-Cross Function selection
4 relay can be programmable to relative Totalizer,
Batch, Batch Counter and Immediate Value(PV) with
individual functions.
Relative to Immediate Value(PV)
Relay energized mode Hi / Lo / Hi.HLd / Lo.HLd /
DO/ Go-1.2
Hi: Relay will energize when PV > Set-Point
Lo: Relay will energize when PV < Set-Point
Hi.HLd (Lo.HLd): When the PV Higher (or lower) than
set-point, the relay will be energized and hold until
manual reset by from key in【User Level】or【E.C.I.】.
DO: Relay is energized by RS485 command directly,
and no longer to compare with set-point of relay
Go-1.2: Go function with【Set-Point 1】and【Set-point
2】. Go relay energized when the condition is
set-point 1(Hi) > PV > set-point 2(Lo)
Hi / Lo / Go Relay
Energized Hi(Lo) Energized Hold &
Reset
Hi Setting
Hi RL Energized ON
Lo Setting
Lo RL Energized ON
ON
Go RL Energized ON
Hi.HLd(High Hold)
Rela
y
Ener
g
ized ON
Reset the relay Hold
by ECI or Front Key
ON
Level Trigger
Hi Setting
Hysteresis: Settable range from 0~9999 Counts
Relay energized delay: Settable range from
0.1(second)~9(minutes)59.9(seconds);
Relay de-energized delay: Settable range from
0.1(second)~9(minutes)59.9(seconds)
Start Delay Energized
/
De-energized
Delay & Hysteresis
Start Dela
y
Time
Start Band
Hi Setting
Relay
Energized ON
Inhibit
Inhibit
Energized delay tim
e
ON
H
y
steresis
De-energized
delay time
Hi Setting
Relay
Energized
Relative to Totalizer / Batch / Batch Counter
N/C/R Mode
The 3 mode are very useful idea to control the
totalizer and batch. The relay energized condition is
according to not only energized level, but also time
and reset for totalizer, batch and batch counter.
N MODE:
When the condition of Set Point is met:
1. the relay will be energized;
2. The totalizer will run as same as
usual; until manual reset by front key
or by rear terminal, the totalizer will
be reseted to “0” and the relay will be
de-energized.
Set
Point
Relay
Output ON
Totalizer
Manual
Reset
R MODE:
When the condition of Set Point is met:
1. The relay will be energized; until the
time is over Relay output time
rY.1(2).ot(Relay1(2) output time).
2. The totalizer will run as same as
usual; until the time is over Relay output
time rY.1(2).ot(Relay1(2) output
time),The totalizer will be reset to “0”.
ON
Auto
Reset
Relay output Time
Totalizer
Set
Point
Relay
Output
C MODE:
When the condition of Set Point is met:
1. The relay will be energized; until the
time is over Relay output time rY.1.ot
or rY.2.ot.
2. The totalizer will be reset to “0”, then
counts-up from “0”.
ON
Relay
Output
Set
Point
Auto
Reset Totalize
r
Relay output Time
Period of Relay on:
0:00.0~9(Minutes):59.9(Second)
Fo
r
Immediate
V
alue(PV)
Relative PV or Tare: The E.C.I. can be set to be
Rel.Pv(Relative PV) function. When the E.C.I. is
closed, the reading will show the differential value.
PV Hold: The E.C.I. can be set to be Pv.HLd(PV
Hold) function. The display will be hold when the
E.C.I. is closed, until the E.C.I. is to be open. Please
refer to the below figure.
Reset for Maximum or Minimum Hold: Please
refer to the below figure.
Max. ( Mini.) Hold & Reset PV Hold & Reset
Present
Value
Reset Data Hold
by E.C.I. ON
Level
Trigger
ON
ON
Reset the Max.(or
Mini.) Hold by
E.C.I. or Front Key
ON
Level Trigger
Maximum Hold
PV Hold
Present
Value
DI(Digital Input): The E.C.I can be set to be
DI(Digital Input) function, when the meter building in
RS485 port. The computer is easier to get a switch
status through the meter as like as DI of PLC.
Reset for Relay Energized Latch: If relay
energized mode was set to be Energized hold, the
E.C.I. can be set to be rY.rSt(Reset Relay function).
When the PV meets the condition of relay
energizing, the relay will be hold until the E.C.I. is
closed.
For Totalizer / Batch)
Gate for Energy / Batch
Energy Reset for Energy / Batch
Energy
Energy
/ Batch
Gate by E.C.I.
or Front Key
O
N
Level Trigge
r
ON ON ON Reset by E.C.I.
or Front Key
O
N
Ed
g
e Tri
gg
e
r
ON ON
Energy
/ Batch
Gate
Gate GAtE: Totalizer and Batch will be stop to
count, when E.C.I. Iis close.
Batch Gate bt.GtE: Batch will be stop to count,
when E.C.I. Iis close.
Totalizer Gate tL.GtE: Totalizer will be stop to
count, when E.C.I. Iis close.
Reset
ResetrESEt: Totalizer and Batch will be reset to “0”,
when E.C.I. Iis close.
Totalizer ResettL.rSt: Totalizer will be reset to “0”,
when E.C.I. Iis close.
Batch Resetbt.rSt: Batch will be reset to “0”, when
E.C.I. Iis close.
■ ANALOGUE OUTPUT FUNCTIONS
Relative to immediate value(PV), totalizer, batch or batch
count programmable.
Ao.LS: Setting range: -19999~+29999;
Analogue Output Low relative Low Scale
Ao.HS: Setting range: -19999~+29999;
Analogue Output relative High Scale
SCALE
Default: Ai.Lo: 0%, Ai.Hi: 100%; Lo.SC: 0.00, Hi.SC: 100.00
Chan
g
e to Ai.Lo: 0%, Ai.Hi: 75%; Lo.SC: 0.00, Hi.SC: 199.99
0.00
199.99
100.00
0.00%
100.00%
50.00%
INPUT
75.00%
0.00% 100.00%
50.00%
OUTPUT
199.99
100.00
0.00
Setted Scaling: Lo.SC: 0.00, Hi.SC: 199.99;
Desired Output: Ao.Lo: 50.00
(
PV
)
, Ao.Hi: 150.00
(
PV
)
50.00
150.00
SCALE

4/27 CS2-TM(Pulse)-OperatingManual2012-05-10
Fine Zero & Span Adjustment for Analog Output:
Users can get Fine Adjustment of analogue output
by front key of the meter. Please connect standard
meter to the terminal of analogue output. To press
the front key(up or down key) of meter to adjust and
check the meter the output.
Ao.Zro: Fine Zero Adjustment for Analog Output;
Setting range: -38011~27524;
Ao.Spn: Fine Span Adjustment for Analog Output;
Setting range: -38011~27524;
High Limited for Analog Output
0.00% 100.00%50.00%
OUTPUT
199.99
100.00
0.00
Setted Scaling: Lo.SC: 0.00, Hi.SC: 199.99;
DesiredOutput: Ao.Lo: 50.00
(
PV
)
, Ao.Hi: 150.00
(
PV
)
; Ao.LMt: 80.00%
50.00
150.00
SCALE
Ao.LMt: 80.00%(=130.00)
■ RS485 Communication
Protocol: ModBus RTU Mode
Baud Rate: Setting range:1200/2400/4800/ 9600/
19200/38400
Data Bits: Selectable 7 or 8 bits
Stop Bits: Selectable 1 or 2 bits
Parity: Selectable Even / Odd / None
Divice Number: 1~255
Remote Display function
The display can be written by RS485 command. In
past, the meter normally receive 4~20mA or 0~10V
from AO card or BCD card of PLC. We support a new
solution by RS485 writing in so that can be save cost
and wiring into PLC.
CS2 APPLICATION FOR RS485 WRINTING IN
RS 485
Modbus RTU Mode
(
u
p
to 38400b
p
s
)
RS485 wiring 1.2KM maximum
Terminate Resistor:
RL1
RL2
co
m
ECI
RL1
RL2
com
ECI
When the diPLY(Display Function) set to be RS485,
it means, the PV screen will show the number from
RS485 command & data. The data(number) will be
same as PV that will compare with set-point,
analogue output and ECI functions so that is to
control analogue output, relay energized and so on.
■ Pulse Output
Relative to Totalize
r
, batch or batch counte
r
Pulse dividerPLS.dv: Settable range from 1~9999.
PLS.dv set to be 1: It will output 1 pulse, when
totalizer increases “1Count”. Ex: It will output 1
pulse, when totalizer from 12345.678 increse to
12345.679,
PLS.dv set to be 1000: It will output 1 pulse,
when totalizer increases “1000Count”. Ex: It will
output 1 pulse, when totalizer from 12345.678
increase to 12346.678.
The maximum output is 1000Hz. Please sets lower
resolution of totalizer, when the output over 1000Hz.
Duty Cycle: 50%
Please specify Relay or Open Collect output in order
■ OEM function is welcome

5/27 CS2-TM(Pulse)-OperatingManual2012-05-10
■ APPLICATIONS
Flowmeter Controller - RS485 communication
Batch Control
A
O
A
L
RS 485
mVdc
信號輸出
電流分流器
Measuring Input
2
ENT/FN
▲
▲
▼L/min
RL1 RL
2
RL
3
RL4
E
C
1 E
C
2
E
C
3
CO
M
CS2-TM & CS2-PR APPLICATION FOR FLOWNETER / PRESSURE MEASURING
RS 485
Modbus RTU Mode
(
u
p
to 38400b
p
s
)
4 Relay Output for P
V
:
Mode: High or Low Energized / Energized Hold / DO
Functions: Start delay / Energized & De-energized
delay / Hysteresis
4 Relay Output for Totalizer / Batch:
Mode: N / C / R Mode
Analo
g
Out
p
ut 0~10V/0
(
4
)
~20mA
3 External Control Input:
Functions: Relative PV / PV Hold / Reset Max or Mini.
Hold / DI / Reset for Relay Energized Hold
Application: Thermal Switch / Circuit Breaker / Push
Button / ……
Display:
Mode: Measuring Value / Maximum Hold / Minimum
Hold / Reading value from RS485 command
AL
AL
流量計(Flowmeter)
ENT/FN
▲
▼
L/mi
n
RL1
RL
2
RL
3
RL4
C
I11
C
I
2
C
I
3
COM
RL
1
RL
2
RL3
RL4
CO
M
ECI1
ECI2
ECI3
ENT/FN
◄
▲
▼
K
g
/
Pulse
For batch control. Ex. Package Machine for Beer,
UP.dSP set to be Bt.Cnt , and dSPLY for down
screen set to be bAtCH , Relay 1 energized mode
set to be btCH.C , and set-point is 750mL. Relay
2 energized mode set to be totL.C , and set-point
is 24.
The Batch counter will count 1 and relay 1
energized when batch increase to 750mL. It
mens finishing 1 bottle beer. When Batch
counter in up screen increase to 24, the relay 2
energized to pack one box.
ENT/FN
?
?
mL
RL1
RL
2
RL3
RL4
COM
CI11
CI2
CI3
Up Screen for
Batch Counte
r
Down screen
for Batch
ENT/FN
?
?
mL
RL1 RL
2
RL3 RL4 COM
CI11 CI2 CI3
Up Screen for
Batch Counte
r
Down screen
for Batch
ON
Relay
Output
Set
Point
A
uto
Reset Batch
Relay output Time
Batch 21
1
24
Batch
Count
■ FRONT PANEL ■ INSTALLATION
ENT/F
N
?
?L/min
RL1 RL
2
RL
3
RL4
CO
M
C
I11
C
I
2
C
I
3
Comm. status
Relay status
Indication
Operation Key
Control Input
status
Engineer Unit
Up screen for
Totalizer Down screen
for PV or Batch
1.0~8.0 mm
FIX HOLDER:
104 mm(L) / W M3
PANEL CUT-OUT:
92+0.2(W) x 44+0.2(H) mm
ENT/
?
?
L/min
RL
RL
RL
RL
CO
CI
CI
■ DIMENSIONS ■ WIRING DIAGRAM
96.0
48.0
92.0+0.2
44.0+0.2
PANEL CUT-OUT
FRONT VIEW
Unit: mm
8.0 12.0
100.0
Dimensions: 96mm x 48mm x 120mm
Panel Cutout: 93mm x 45mm (advise)
D-S 1 2 3 4 5
NPN ON
PNP ON
M.C. ON
ON
5VP
12VPON
24VPON
D-S is on, when it is
on down side.
21 22 24 2523 27 2826 29 30 31 33 32 34
Relay 3
b
c
a
Relay 2
b
c
a
Relay 1
a
c
Relay 4
a
c
Analogue
output
A B
RS 485
port
ECI1 ECI3 COMECI2
External
Control Input
4 53
6 7 8 9 10
11
12
14
15
13
Terminal blocks:
10A/300Vac, M2.6,
M2.6, 1.3~2.0mm2
(16~22AWG)
AC
86~265V
DC 100~300V
DC 20~56V
AC230V
AUX. POWER
AC115V
ADH
ADL
Pulse Output
If the pulse output is to be selected,
the meter can be selected 3 relay
maximum(without Relay 4).
D-S
Dip-Switch
0V
+V
+IN
SIGNAL INPUT
Pulse
/
Freq.
FG
■ ORDERING INFORMATION
■ ORDERING INFORMATION
CS2−TM−
Input
Signal −Relay
Output −Analogue
Output −
RS 485
Port
−Pulse
Output −
Aux.
Powered
−
*Optional
Function Customize function is welcome. Please
contact with our sales window for detail.
CODE I/P RANGE
CODE RELAY O/P
CODE
ANALOG O/P
CODE
RS485 PORT
CODE
PULSE O/P CODE AXU. POWER
C 00
Contact
N
None
N
None
N
None
N
None
A
AC115/230V
N
NPN
R2
2 Relay
8
RS 485
C
Open Collect
P
PNP
R3
3 Relay
V
0(1) ~ 5 V
0 ~ 10 V
R
Relay Contact
V
Voltage Pulse
R4
4 Relay*
ADH
AC 85~265V
DC100~300V
05
5V pulse
I
0 ~ 10 mA
0(4)~20 mA
ADL
DC 20~56 V
12
12V pulse
24
24V pulse
* If the pulse output is to be
selected, the meter can be
selected 3 relay maximum.
OPTION 2 OPTION 3
OPTION 1
OPTION 5
OPTION 4

6/27 CS2-TM(Pulse)-OperatingManual2012-05-10
■ OPERATION:
■ ERORR MASSAGE
STEP DESCRIPTION DISPLAY FLASH REMARK
BEFORE POWER ON, PLEASE CHECK THE SPECIFICATION AND
CONNECTION AGAIN.
SELF-DIAGNOSIS AND ERROR CODE:
: Display is positive-overflow (Signal is over display range) (Please check the input
signal)
: Display is negative-overflow (Signal is under display range) (Please check the input
signal)
: ADC is positive-overflow (Signal is higher than input 120%) (Please check the input
signal)
: ADC is negative-overflow (Signal is lower than input -120%) (Please check the input
signal)
/ : EEPROM occurs error (Please send back to
manufactory for repaired)
/ : Calibrating Input Signal do not process (Please process Calibrating
Input Signal)
/ : Calibrating Input Signal error (Please check Calibrating
Input Signal)
/ : Calibrating Output Signal do not process (Please process Calibrating
Output Signal)
/ : Calibrating Output Signal error (Please check Calibrating
Output Signal)
■ FRONT PANEL:
Comm. status
Relay status
Indication
Operatio
n
Ke
y
Control Input
status
Engineer Unit
Up screen
for Totalizer Down screen
for PV or Batch
ENT/FN
L/min
RL1 RL
2
RL
3
RL 4
CO
M
C
I11
C
I
2
C
I
3
CS2-TM has two display screens and I/O status
indication for purposes.
Numeric Screens
Up screen: 0.28”(0.71cm) red high-brightness LED
for 10 digital totalizer.
Down screen: 0.28”(0.71cm) red high-brightness LED
for Immediate Value 4 2/3 digital or Batch 6 digital.
I/O Status Indication
Relay Energized: 4 square red LED
RL1
display when Relay 1 energized;
RL
2
display when Relay 2 energized;
RL
3
display when Relay 3 energized;
RL4
display when Relay 4 energized;
External Control Input Energized: 3 square green LED
ECI1
display when E.C.I. 1 close(dry contact)
ECI
2
display when E.C.I. 2 close(dry contact)
ECI3
display when E.C.I. 3 close(dry contact)
RS485 Communication: 1 square red LED
CO
M
will flash when the meter is receive or send data,
and CO
M
flash quickly means the data transient
quicker.
Stickers:
Each meter has a sticker what are functions and
engineer label enclosure.
Relay energized mode: H
H
H i L
o L
L D
O
E.C.I. functions mode:
PV.H(PV Hold) / Tare / DI /
M.RS(Maximum or Minimum Reset) /
R.RS(Reset fo Relay Latch)
Engineer Label: over 80 types.
Operating Key: 4 keys for
Enter(Function) /
Shift(Escape) /
Up key /
Down key
Setting Status Function Index
Up key Increase
numbe
r
Go back to previous
function index
Down key Decrease
numbe
r
Go to next
function index
Shift key Shift the setting
position
Go back to this
function index, and
abort the settin
g
Enter/Fun
key
Setting
Confirmed and
save to EEProm
From the function
index to get into
settin
g
status
Pass Word:
Setting range:0000~9999;
User has to key in the right pass word so that get
into【Programming Level】. Otherwise, the meter will
go back to measuring page. If user forget the
password, please contact with the service window.
Function Lock: There are 4 levels selectable for lock.
None: no lock all.
User Level: User level lock. User can get into user
level for checking but setting.
Programming Level: Programming level lock.
User can get into programming level for
checking but setting.
ALL: All lock. User can get into all level for
checking but setting.
Front Key Function
The
Key can be set to be the same function as the
setting of ECI1.
The
Key can be set to be the same function as the
setting of ECI2.
Ex. The ECI1 set to be Pv.HLd and the function
E.1=UP set to be YES in【ECI Group】. When user
presses
Key, the PV will hold as like as ECI1 close.
If the front key function has been set, the terminal
input for ECI will be disabling.

7/27 CS2-TM(Pulse)-OperatingManual2012-05-10
■ OPERATING DIAGRAM:
USER LEVEL
Power on
Sel
f
-diagnosis
(LED All
bright)
Totalizer
Batch
0−0−1
▲
▼
This page will
show out,
when dSPLY
set to be
bAtCH .
Pv : Present
Value(Immedia
te Value)
0−4
▲
▼
This page will
show out,
when pulse
output was to
specify in
order.
rY4.SP: Relay 4
Set-point
setting
0−8
▲
▼
M.rSt: Reset
for Maximum
& Minimum
storage
model
number
and
firmware
version
0−0−2
▲
▼
This page will
show out,
when PV is to
beset.
bAtCH: Batch
0−5
▲
▼
This page will
not show out,
when the
relay mode
was to be set
N/R/C mode
rY.rSt: Reset
for energized
latch of Relay
0−9
▲
▼
CS2-tM:
Model munber
PLS1.0:
firmware
version
ENT
MEASURING
PAGE
Press 1sec.
Press 1sec.
0−1
▲
▼
rY1.SP: Relay 1
Set-point
setting
0−6
▲
▼
Min: PV
Minimum
storage
0−0−1
▲
▼
Cyclic to first
page
0−2
▲
▼
rY2.SP: Relay 2
Set-point
setting
0−7
▲
▼
MAX: PV
Maximum
storage
ENT
Enter the
password to
get into
Programming
Level
Press
to enter &
settin
g
0−3
▲
▼
rY3.SP: Relay 3
Set-point
setting
YES
Correct?
NO
Default
=1000
ENT
INPUT
GROUP
ENT
RELAY
GROUP
ENT
EXTERNAL
CONTROL
INPUT
GROUP
ENT
ANALOGUE
OUTPUT
GROUP
▲
▼
A−1
▲
▼
Pv.bSE: Time
unit of
Immediate
Value(PV)
1/SEC 1/Min
1/Hour 1/dAY
B−1
▲
▼
rY.Sb: Start
band for Relay
energized
C−1
▲
▼
ECi.1:
External
Control Input 1
nonE rEL.Pv
Pv.HLd M.rSt
rY.rSt di GAtE
rESET tL.GtE
tL.rSt bt.GtE
bt.rSt
D−1
▲
▼
Ao.SEL:
Analogue
output relative
parameter
Totalizer/Batch
/PV selection
Pv bAtCH
totAL
A−2
▲
▼
The defference
mode selected
will show up
relative
parameters
F.tYP: Modes
description of
Flowmeter
PLS/F F/PLS
d.MUL.v
B−2
▲
▼
rY.Sd: Start
delay time for
Relay
energized
0:00.0~
9(M):59.9(S)
C−2
▲
▼
ECi.2:
External
Control Input 2
nonE rEL.Pv
Pv.HLd M.rSt
rY.rSt di GAtE
rESET tL.GtE
tL.rSt bt.GtE
bt.rSt
D−2
▲
▼
Ao.tYP:
Analogue
Output type
v.0~10 v.0-5
v.1-5 A.0-10
A.0-20 A.4-20
Next Page
Next Page
Next Page
Next Page
USER LEVEL
Press
for 1 second can back to Measuring Page
▼
▲
PROGRAMMING LEVEL
Press
for 1 second to back Measuring Page

8/27 CS2-TM(Pulse)-OperatingManual2015-04-24
A−3−1−1
▲
▼
The page will
show out,
when PLS/F is
to be set.
P/F.dP:
Decimal Point
of P/Flow(unit)
(K Factor)
0~0.0000
B−3
▲
▼
rY1.Md: Relay
1 energized
mode
oFF Lo Hi
Hi.HLd
Lo.HLd do
btcH.n btcH.r
btcH.C totL.n
totL.r totL.C
C−3
▲
▼
ECi.3:
External
Control Input 3
nonE rEL.Pv
Pv.HLd M.rSt
rY.rSt di GAtE
rESET tL.GtE
tL.rSt bt.GtE
bt.rSt
D−3
▲
▼
Ao.LS:
Analogue
Output relative
Low Scale
Immediate
Value(PV):
-19999~+29999
Totalizer/Batch:
0~9999999999
A−3−1−2
▲
▼
PLS/F:
P/Flow(unit)
(K Factor)
Setting
0.0000~999.99
B−4−0
▲
▼
The page will
show out,
when rY1.Md
set to be N/R/C
mode.
rY1.ot: Relay 1
energized time
0:00.0~
9(M):59.9(S)
C−4
▲
▼
dEbnc:
Debouncing of
external
control Input
5~255( x 8ms)
D−4
▲
▼
Ao.HS:
Analogue
Output relative
High Scale
Immediate
Value(PV):
-19999~+29999
Totalizer/Batch:
0~9999999999
A−3−2−1
▲
▼
The page will
show out,
when F/PLS is
to be set.
F/P.dP:
Decimal Point
of Flow/P
(1/K Factor)
0~0.0000
B−4
▲
▼
The page will
show out,
when rY1.Md
set to be Hi/Lo
mode.
rY1.HY: Relay
1 Hysteresis
0~5000 counts
C−5
▲
▼
E.1=UP:
E.C.I.1=UP; Up
key will be
same function
as E.C.I.1 set.
YES no
D−5
▲
▼
Ao.Zro:
Fine Zero
Adjustment for
Analog Output
Immediate
Value(PV):
-38011~+27524
Totalizer/Batch:
0~9999999999
A−3−2−2
▲
▼
F/PLS:
Flow/Pulse
(1/K Factor)
Setting
0.0000~999.99
B−5
▲
▼
The page will
show out,
when rY1.Md
set to be Hi/Lo
mode.
rY1.rd: Relay 1
energized
delay time
0:00.0~
9(M):59.9(S)
C−6
▲
▼
E.2=dn:
E.C.I.2=Down;
Down key will
be same
function as
E.C.I.2 set.
YES no
D−6
▲
▼
Ao.SPn:
Fine Span
Adjustment for
Analog Output
Immediate
Value(PV):
-38011~+27524
Totalizer/Batch:
0~9999999999
A−3−3−1
▲
▼
The page will
show out,
when d.MUL.v
is to be set.
diA.dP:
Decimal Point
of diameter of
pipe
0~0.0000
B−6
▲
▼
The page will
show out,
when rY1.Md
set to be Hi/Lo
mode.
rY1.Fd: Relay 1
de-energized
delay time
0:00.0~
9(M):59.9(S)
D−7
▲
▼
Z.S.CLr: Clear
Fine Zero /
Span
Adjustment for
Analog Output
nonE Ao.Zro
Ao.SPn both
A−3−3−2
▲
▼
The page will
show out,
when d.MUL.v
is to be set.
diAMt:
Diameter of
pipe setting
0.0000~999.99M
B−7
▲
▼
rY2.Md: Relay
2 energized
mode
oFF Lo Hi
Hi.HLd
Lo.HLd do
btcH.n btcH.r
btcH.C totL.n
totL.r totL.C
D−8
▲
▼
Ao.LMt:
Analog Output
High Limit
-0.00~110.00%
of FS
A−3−3−3
▲
▼
The page will
show out,
when d.MUL.v
is to be set.
vL.dP: Decimal
Point of Flow
speed
(Lengh/sec)
0~0.0000
B−8−0
▲
▼
The page will
show out,
when rY2.Md
set to be N/R/C
mode.
rY2.ot: Relay 2
energized time
0:00.0~
9(M):59.9(S)
A−3−3−4
▲
▼
The page will
show out,
when d.MUL.v
is to be set.
vL/ Hz:
Valume/Hz,
Flow speed
setting
0.0000~999.99
B−8
▲
▼
The page will
show out,
when rY2.Md
set to be Hi/Lo
mode.
rY2.HY: Relay
2 Hysteresis
0~5000 counts
ENT
RS485
GROUP
A−4
▲
▼
dP: Decimal
point of
set-point for
Realy
energized
0~0.0000
B−9
▲
▼
The page will
show out,
when rY2.Md
set to be Hi/Lo
mode.
rY2.rd: Relay 2
energized
delay time
0:00.0~
9(M):59.9(S)
E−1
▲
▼
AdrEs: Device
number of the
meter
1~255
Next Page Next Page Next Page

9/27 CS2-TM(Pulse)-OperatingManual2012-05-10
A−5
▲
▼
ttL.dP:
Decimal point
of totalizer
0~0.0000
B−10
▲
▼
The page will
show out,
when rY2.Md
set to be Hi/Lo
mode.
rY2.Fd: Relay 2
de-energized
delay time
0:00.0~
9(M):59.9(S)
E−2
▲
▼
bAUd: Baud
rate
1200 2400
4800 9600
19200 38400
A−6
▲
▼
UP.dSP:
Up screen
displays
totalizer or
batch Counter
noMAL Bt.Cnt
B−11
▲
▼
rY3.Md: Relay
3 energized
mode
oFF Lo Hi
Hi.HLd Go-1.2
Lo.HLd do
btcH.n btcH.r
btcH.C totL.n
totL.r totL.C
E−3
▲
▼
PritY: Parity
n.Stb.1 n.Stb.2
odd EvEn
A−7
▲
▼
oFL.Md:
overflow mode
of totalizer or
batch
ovFL rCYCL
B−12−0
▲
▼
The page will
show out,
when rY3.Md
set to be N/R/C
mode.
rY3.ot: Relay 3
energized time
0:00.0~
9(M):59.9(S)
A−8
▲
▼
SiGn: Sign of
accumulate up
or down
PStvE dUAL
B−12
▲
▼
The page will
show out,
when rY3.Md
set to be Hi/Lo
mode.
rY3.HY: Relay
3 Hysteresis
0~5000 counts
A−9
100.00
▲
▼
Pv.SPn:
Fine Span
Adjustment for
Immediate
Value(PV)
display
B−13
▲
▼
The page will
show out,
when rY3.Md
set to be Hi/Lo
mode.
rY3.rd: Relay 3
energized
delay time
0:00.0~
9(M):59.9(S)
A−10
▲
▼
S.CLr:
Clear Fine
Span
Adjustment for
Immediate
Value(PV)
display
B−14
▲
▼
The page will
show out,
when rY3.Md
set to be Hi/Lo
mode.
rY3.Fd: Relay 3
de-energized
delay time
0:00.0~
9(M):59.9(S)
A−11
▲
▼
dSPLY:
Display
Function for
down screen
Pv Mini.H
MAX.H RS485
bAtCH
B−15
▲
▼
The page will
not show out,
when pulse
output has
been
specified.
rY4.Md: Relay
4 energized
mode
oFF Lo Hi
Hi.HLd Lo.HLd
do btcH.n
btcH.r btcH.C
totL.n totL.r
totL.C
A−12
▲
▼
Lo.Cut:
Low Cut
-29999~+29999
B−16−0
▲
▼
The page will
show out,
when rY4.Md
set to be N/R/C
mode.
rY4.ot: Relay 4
energized time
0:00.0~
9(M):59.9(S)
Next Page Next Page

10 / 27 CS2-TM(Pulse)-Operating Manual 2012-05-10
A−13
▲
▼
ito.Md:
Input Time Out
Mode
AUto MAnUL
B−16
▲
▼
The page will
show out,
when rY4.Md
set to be Hi/Lo
mode.
rY4.HY: Relay
4 Hysteresis
0~5000 counts
A−14
▲
▼
The page will
show out,
when ito.Md
set to be
MAnUL .
Ito: The time of
time out
B−17
▲
▼
The page will
show out,
when rY4.Md
set to be Hi/Lo
mode.
rY4.rd: Relay 4
energized
delay time
0:00.0~
9(M):59.9(S)
A−15
▲
▼
rAnGE:
Input range
AUto SEMi
MAnUL
B−18
▲
▼
The page will
show out,
when rY4.Md
set to be Hi/Lo
mode.
rY4.Fd: Relay 4
de-energized
delay time
0:00.0~
9(M):59.9(S)
A−16
▲
▼
AvG: Average
display for
immediate
Value(PV)
A−17
▲
▼
d.Filt: Digital
Filter
A−18
▲
▼
The page will
show out,
when pulse
output
specified.
PLS.dv: Pulse
divider
A−19
▲
▼
P.CodE: Pass
code
A−20
▲
▼
F.LoCK:
Function lock
nonE USEr
EnG ALL
■ OPERATING STEPS:
USER LEVEL
DESCRIPTION PARAMETERS
POWER
ON Please check the specification
and wiring first.
Self-diagnosis (LED All bright)
Totalizer
Batch
model numbe
r
and
firmware version

11 / 27 CS2-TM(Pulse)-Operating Manual 2012-05-10
▼
Measuring Page
10 digital Totalizer or batch counter + 4 2/3
digital immediate Vale(PV) or
10 digital Totalizer + 6 digital Batch
Press
for 1 second can
back to Measuring Page
0−0−1
▲
▼
This page will show out, when dSPLY set
to be bAtCH .
Pv: Present Value;
0−0−2
▲
▼
This page will show out, when dSPLY set
not to be bAtCH .
bAtCH: Batch
0−1
▲
▼
rY1.SP: Relay 1 Set-point setting
Please check the setting of Relay
energized mode and keep in mind.
If the relay mode set to relative
immediate value, the energized mode
will be Hi or Lo.
If the relay mode set to relative totalizer
or batch, the energized mode will be
N/R/C.
Setting Range:
Immediate Value(PV):
-19999~+29999
Totalizer/Batch: 0~9999999999
Shift
Up
Down
Enter
0−2
▲
▼
rY2.SP: Relay 2 Set-point setting
Please check the setting of Relay
energized mode and keep in mind.
Setting Range:
Immediate Value(PV):
-19999~+29999
Totalizer/Batch: 0~9999999999
Shift
Up
Down
Enter
0−3
▲
▼
rY3.SP: Relay 3 Set-point setting
Please check the setting of Relay
energized mode and keep in mind.
Setting Range:
Immediate Value(PV):
-19999~+29999
Totalizer/Batch: 0~9999999999
Shift
Up
Down
Enter
0−4
▲
▼
This page will show out, when pulse
output was to specify in order.
rY3.SP: Relay 3 Set-point setting
Please check the setting of Relay
energized mode and keep in mind.
Setting Range:
Immediate Value(PV):
-19999~+29999
Totalizer/Batch: 0~9999999999
Shift
Up
Down
Enter
0−5
▲
▼
rY.rSt: Reset for energized hold of
Relay
Slecttable: YES / no
Up
Down
Enter
0−6
▲
▼
Min: PV Minimum storage;
The meter will save the minimum of
immediate vale(PV) during power on.
Review only
0−7
▲
▼
MAX: PV Maximum storage) ;
The meter will save the maximum of
immediate vale(PV) during power on. The
maximum can be reset by front key in
M.rSt of【User Level】. It will save newest
maximum after reset.
Review only
0−8
▲
▼
M.rSt: Maximum & Minimum reset;
The maximum and minimum can be reset
by front key in M.rSt of【User Level】. It
will save newest maximum and minimum
after reset.
Slecttable: YES / no
Up
Down
Enter
0−9
▲
▼
CS2-tM: Model number
PLS1.0: Frimware version
Review only
It will be announce in our
website when it has been
version changed.
0−0−1
▲
▼
Cyclic to first page
Press
for 1 second can back to
Measuring Page in any page.

12 / 27 CS2-TM(Pulse)-Operating Manual 2012-05-10
PROGRAMMING LEVEL
DESCRIPTION PARAMETERS
ENT
MEASURING PAGE
ENT
PASS CODE PAGE If user wants to change the
pass code, please go to step
A-20 to set. Please remind the
new pass code.
YES
Correct?
NO
Enter the pass code to get into
programming level.
▼▲
▼▲
▼▲
▼▲
INPUT
GROUP
RELAY
GROUP
EXTERNAL
CONTROL
INPUT GROUP
ANALOGUE
OUTPUT
GROUP
RS485
GROUP
PRESS
TO ENTER
PRESS
TO ENTER
PRESS
TO ENTER PRESS
TO ENTER
PRESS
TO ENTER
INPUT GROUP
DESCRIPTION PARAMETERS
EN
T
F N
INPUT GROUP INDEX In following page, press
for 1 second to back
INPUT GROUP INDEX.
A−1
▲
▼
Pv.bSE: Time unit of Immediate
Value(PV);
Please refer to the specification and
output of flowmeter, and then set the time
base.
Selectable: 1/SEC 1/Min 1/Hour
1/dAY
1/SEC: Flow/Second
1/Min: Flow/Minute
1/Hour: Flow/Hour
1/dAY: Flow/Day
Up
Down
Enter
A−2
▲
▼
The defference mode selected will show
up relative parameters following
F.tYP: Flow Rate type;
There three three types setting for
Pulse/Flow-unit(K factor), Flow/Pulse(1/K
factor) and Flow rate/Hz to match the
difference output description of
flowmeters. Engineer needs just to
check the mode of flowmeter and
setting. The totalizer will calculating the
flow rate, and accumulation.
Selectable: PLS/F F/PLS
d.MUL.v
PLS/F:Pulse/Flow(K Factor);
Settable the decimal point
of Pulse/Flow(K Factor)
and Pulse/Flow(K Factor)
F/PLS:Flow/Pulse(1/K Factor);
Settable the decimal
point of Flow/Pulse(1/K
Factor) and
Flow/Pulse(1/K Factor)
d.MUL.v: πr2x Flow Speed;
Settable the decimal
point of diameter of pipe,
flow speed and F
diameter of pipe, flow
speed.
Up
Down
Enter
Next P.
▼
▲
Press
for 1 second to back Measuring Page

13 / 27 CS2-TM(Pulse)-Operating Manual 2015-04-24
A−3−1−1
▲
▼
The page will show out, when F.tYP set
is to be PLS/F.
P/F.dP: Decimal Point of Pulse/Flow or K
factor;
Selectable:
0 / 0.0 / 0.00 / 0.000 / 0.0000
Up
Down
Enter
A−3−1−2
▲
▼
The page will show out, when F.tYP set
is to be PLS/F.
PLS/F: Pulse/Flow(K factor);
Setting Range: 0.0000~999.99
Shift
Up
Down
Enter
A−3−2−1
▲
▼
The page will show out, when F.tYP set
is to be F/PLS.
F/P.dP:Decimal Point of
Flow/Pulse(1/K factor);
Selectable:
0 / 0.0 / 0.00 / 0.000 / 0.0000
Up
Down
Enter
A−3−2−2
▲
▼
The page will show out, when F.tYP set
is to be F/PLS.
F/PLS: Flow/Pulse(1/K Factor);
Setting Range: 0.0000~999.99
Shift
Up
Down
Enter
A−3−3−1
▲
▼
The page will show out, when F.tYP set
is to be d.MUL.v.
diA.dP: Decimal Point of Diameter for
pipe;
Selectable:
0 / 0.0 / 0.00 / 0.000 / 0.0000
Up
Down
Enter
A−3−3−2
▲
▼
The page will show out, when F.tYP set
is to be d.MUL.v.
diAMt: Diameter of pipe;
Setting Range: 0.0000~9999.9M
Shift
Up
Down
Enter
A−3−3−3
▲
▼
The page will show out, when F.tYP set
is to be d.MUL.v.
vL.dP: Decimal Point of Flow Speed;
Selectable:
0 / 0.0 / 0.00 / 0.000 / 0.0000
Up
Down
Enter
A−3−3−4
▲
▼
The page will show out, when F.tYP set
to be d.MUL.v.
vL/HZ: Volume or Flow Rate/Hz;
Volume or Flow Rate/Hz
Setting Range: 0.0000~999.99
Shift
Up
Down
Enter
A−4
▲
▼
dP: Decimal Point of Relay Set-Point
The totalizer has been designed auto
range and decimal point moving to keep
highest resolution. Therefore, user has
to set the decimal point for set-point.
Selectable:
0 / 0.0 / 0.00 / 0.000 / 0.0000
Up
Down
Enter
A−5
▲
▼
ttL.dP: Decimal Point of Totalizer
Please don’t set the big difference
resolution between totalizer and
immediate value(PV) to cause totalizer
increasing too slowly.
Selectable:
0 / 0.0 / 0.00 / 0.000 / 0.0000
Up
Down
Enter
A−6
▲
▼
UP.dSP/ttL.Md: Up screen display
selection
The function is very useful to achieve batch
control. Plesae refer to the application of this
manual
Seletable:
noMAL(Normal): Up screen
display totalizer
Bt.Cnt(Batch Counter): Up screen
display btach Counter;
Up
Down
Enter
A−7
▲
▼
oFL.Md: Run Mode after overflow for
Totalizer/Batch/Batch count;
Selectable:
ovFL(overflow): Up screen will
show ovFL , when it is
over-flow.
rCYCL(Recycle): Up screen will
re-count from 0 , when it is
over-flow.
Up
Down
Enter
Next P.

14 / 27 CS2-TM(Pulse)-Operating Manual 2012-05-10
A−8
▲
▼
Don’t Care about the function
SiGn: Up & down count of Totalizer
accouding to + or – of PV
Selectable:
PStvE(Pasitive): Totalizer or
Batch will count increase
when immediate value(PV)
>0.
dUAL(Dual): Totalizer or Batch
will count increase when
immediate value(PV)>0.
A
nd, Totalizer or Batch will
count decrease when
immediate value(PV)<0.
Up
Down
Enter
A−9
▲
▼
100.00
Pv.SPn: Fine Span Adjustment for PV
display;
Users can get Fine Adjustment by front
key of the meter, and “Just Key In” the
value which user want to show in the
current input signals.
Setting Range: -29999~+29999
Shift
Up
Down
Enter
A−10
▲
▼
S.CLr: Clear Fine Span Adjustment
for PV display; Selectable:
no (No): Do not clear the fine
span adjustment.
yes(Yes): To clear the fine span
adjustment.
Up
Down
Enter
A−11
▲
▼
dSPLY: Display Function for down
screen
The display can be written by RS485
command. At meantime, the display is no
longer according to the input signal. In
past, The meter normally receive
4~20mA or 0~10V from AO card or BCD
card of PLC. We support a new solution
by RS485 writing in so that can be save
cost and wiring into PLC.
Selectable:
Pv(PV): Down screen shows
Immediate Value(PV)
bAtCH(Batch): Down screen
shows batch
Mini.H:Minimum Hold for
Immediate Value(PV)
MAX.H:Maximum Hold Immediate
Value(PV)
RS485(RS485): Remote display
from RS485 command of
master.
Up
Down
Enter
A−12
▲
▼
Lo.CUt:Low Cut
If the setting value is positive, it means
the range of absolute value will be 0; PV≤
Setting value, the display will be 0.
If the setting value is negative, it means
the range of under setting value will be 0;
PV≤-Setting value, the display will be 0.
Setting Range: ±29999 counts
Shift
Up
Down
Enter
A−13
▲
▼
ito.Md:Input Time Out Mode
In the case of low frequency, the
totalizer can not to identify that is low
frequency and no input until the next
pulse input. Sometimes, it takes a long
period.
CS2-TM builds in a time out function to
cut out the reading(to be “0”). There are
two modes MAnAL / AUto can be
selected.
Selectable:
Auto: The reading will display
“0”, when the next pulse
doesn’t input during the
time that gave by formular
of meter’s firmware.
MAnUL: The reading will display
“0”, when the next pulse
doesn’t input during the
setting time.
Up
Down
Enter
A−14
▲
▼
The page will show out, when ito.Md set
to be MAnUL.
Ito: Input Time Out;
The time setting for Input time out.
Setting Range: 0.0 sec~999.9sec
Shift
Up
Down
Enter
Next P.

15 / 27 CS2-TM(Pulse)-Operating Manual 2012-05-10
A−15
▲
▼
rAnGE(Range): Input frequency
range
Adtek builds in high technology with
wide input range from 0.01Hz~
140.00KHz with auto-range function at
same unit. However, we keep three way
for the input range selection as Auto
range, Semi-Auto range and manual.
※
When by the RS485 read present
value,can only choose MAnUL
Selectable:
Auto(Auto range): The decimal
point will be auto changed
according to the input
frequency so that keep
reading in the highest
resolution.
SEMi(Semi-Auto range): The
decimal point will be auto
changed according to the
input frequency to keep
reading in the highest
resolution under setting
position of decimal point.
MAnUL(Manual range): The
decimal point will be fixed
according to the setting of
decimal point. So, it’s
possible to show “overflow”,
if the input frequency is over
the display range.
Up
Down
Enter
A−16
▲
▼
AvG: Average
The meter’s sampling is 15cycle/sec. If
the AvG(Average) set to be 3, it means
the meter is sampling 3 readings, and
calculating the average then update
display once. At meantime, the display
update will be 5 times/sec.
Setting Range:
1(no function)~99 times
Shift
Up
Down
Enter
A−17
▲
▼
d.FiLt: Digital filter
The digital filter can reduce the magnetic
noise in field.
Setting range:
0(no function)/1~99 times.
Shift
Up
Down
Enter
A−18
▲
▼
PLS.dv: Pulse divider
PLS.dv set to be 1: It will output 1
pulse, when totalizer increases
“1Count”. Ex: It will output 1 pulse,
when totalizer from 12345.678 increse
to 12345.679,
PLS.dv set to be 1000: It will output 1
pulse, when totalizer increases
“1000Count”. Ex: It will output 1 pulse,
when totalizer from 12345.678 increase
to 12346.678.
Setting Range: 1~9999
The maximum output is
1000Hz. Please sets lower
resolution of totalizer, when
the output over 1000Hz.
Duty Cycle: 50%
Please specify Relay or Open
Collect output in order
Shift
Up
Down
Enter
A−19
▲
▼
P.CodE: Pass Code
Please remind and write down the new
pass code so that get into programming
level.
Setting Range: 0000~9999
Shift
Up
Down
Enter
Next P.

16 / 27 CS2-TM(Pulse)-Operating Manual 2012-05-10
A−20
▲
▼
F.LoCk: Function Lock
There are 4 levels selectable for lock.
Selectable:
nonE(None): no lock all.
USEr(User Level): User level
lock. User can get into user
level for checking but
setting.
EnG(Programming Level):
Programming level lock.
User can get into
programming level for
checking but setting.
ALL(All Level): User can get into
all level for checking but
setting.
Up
Down
Enter

17 / 27 CS2-TM(Pulse)-Operating Manual 2012-05-10
RELAY GRUOP
DESCRIPTION PARAMETERS
EN
T
F N
RELAY GROUP INDEX In following page, press
for 1 second to back
RELAY GROUP INDEX.
B−1
▲
▼
rY.Sb: Start band of Relay Output
Start Delay Energized
/
De-energized
Delay & Hysteresis
Start Dela
y
Time
Start Band
Hi Setting
Relay
Energized ON
Inhibit
Inhibit
Energized delay time
ON
H
y
steresis
De-energized
delay time
Hi Setting
Relay
Energized
Setting Range: 0~9999 counts
Shift
Up
Down
Enter
B−2
▲
▼
rY.Sd: Relay Output start delay time Setting Range:
0:00.0~9(M):59.9(S)
Shift
Up
Down
Enter
B−3
▲
▼
rY1.Md: Relay 1 energized mode
Relative Immediate Value(PV): Hi / Lo / Go
Hi / Lo / Go Relay
Energized
Hi(Lo) Energized Hold &
Reset
Hi Setting
Hi RL Energized ON
Lo Setting
Lo RL Energized ON
ON
Go RL Energized ON
Hi.HLd(High Hold)
Rela
y
Ener
g
ized ON
Reset the relay Hold
by ECI or Front Key
ON
Level Trigger
Hi Setting
Relative Totalizer / Batch / Batch Counter:
N / R / C Mode
N MODE:
When the condition of Set Point is met:
1. the relay will be energized;
2. The totalizer will run as same as
usual; until manual reset by front key
or by rear terminal, the totalizer will
be reseted to “0” and the relay will be
de-energized.
Set
Point
Relay
Output ON
Totalizer
Manual
Reset
R MODE:
When the condition of Set Point is met:
1. The relay will be energized; until the
time is over Relay output time
rY.1(2).ot(Relay1(2) output time).
2. The totalizer will run as same as
usual; until the time is over Relay output
time rY.1(2).ot (Relay1(2) output
time),The totalizer will be reset to “0”.
ON
Auto
Reset
Relay output Time
Totalizer
Set
Point
Relay
Output
C MODE:
When the condition of Set Point is met:
1. The relay will be energized; until the
time is over Relay output time rY.1.ot
or rY.2.ot.
2. The totalizer will be reset to “0”, then
counts-up from “0”.
ON
Relay
Output
Set
Point
A
uto
Reset Totalizer
Relay output Time
Selectable:
oFF:Turn off the Relay and
relative LED.
Lo:Low Level Energized; Relay
will energize when PV <
Set-Point.
Hi:High Level Energized; Relay
will energize when PV >
Set-Point.
Hi.HLd / Lo.HLd:High / Low
Level energized latch; When
the PV Higher (or lower) than
set-point, the relay will be
energized and hold until
manual reset by from key in
【User Level】or【E.C.I.】.
do:Digital Output; Relay is
energized by RS485 command
directly, and no longer to
compare with set-point of
relay.
btcH.n: Batch control with N
mode energized.
btCH.r: Batch control with R
mode energized
btCH.C: Batch control with C
mode energized.
totL.n: Totalizer control with N
mode energized.
totL.r: Totalizer control with R
mode energized.
totL.C: Totalizer control with C
mode energized.
Up
Down
Enter
B−4−0
▲
▼
The page will show out, when rY1.Md set
to be N/R/C mode.
rY1.ot: Relay 1 energized time
Setting Range:
0:00.0~9(M):59.9(S)
Shift
Up
Down
Enter
B−4
▲
▼
The page will show out, when rY1.Md set
to be Hi/Lo mode.
rY1.HY: Relay 1 Hysteresis
Setting Range: 0~5000 counts
Shift
Up
Down
Enter
B−5
▲
▼
The page will show out, when rY1.Md set
to be Hi/Lo mode.
rY1.rd: Relay 1 energized delay time
Setting Range:
0:00.0~9(M):59.9(S)
Shift
Up
Down
Enter
B−6
▲
▼
The page will show out, when rY1.Md set
to be Hi/Lo mode.
rY1.Fd: Relay 1 de-energized delay
time
Setting Range:
0:00.0~9(M):59.9(S)
Shift
Up
Down
Enter
Next P.

18 / 27 CS2-TM(Pulse)-Operating Manual 2012-05-10
B−7
▲
▼
rY2.Md: Relay 2 energized mode ….as Relay 1 Energized Mode…
Selectable: oFF / Lo / Hi /
Lo.HLd / Hi.HLd / do / btcH.n /
btCH.r / btCH.C / totL.n / totL.r /
totL.C
Up
Down
Enter
B−8−0
▲
▼
The page will show out, when rY2.Md set
to be N/R/C mode.
rY2.ot: Relay 2 energized time
Setting Range:
0:00.0~9(M):59.9(S)
Shift
Up
Down
Enter
B−8
▲
▼
The page will show out, when rY2.Md set
to be Hi/Lo mode.
rY2.HY: Relay 2 Hysteresis
Setting Range: 0~5000 counts
Shift
Up
Down
Enter
B−9
▲
▼
The page will show out, when rY2.Md set
to be Hi/Lo mode.
rY2.rd: Relay 2 energized delay time
Setting Range:
0:00.0~9(M):59.9(S)
Shift
Up
Down
Enter
B−10
▲
▼
The page will show out, when rY2.Md set
to be Hi/Lo mode.
rY2.Fd: Relay 2 de-energized delay
time
Setting Range:
0:00.0~9(M):59.9(S)
Shift
Up
Down
Enter
B−11
▲
▼
rY3.Md: Relay 3 energized mode ….as Relay 1 Energized Mode…
Selectable: oFF / Lo / Hi / Lo.HLd
/ Hi.HLd / do / btcH.n / btCH.r /
btCH.C / totL.n / totL.r / totL.C /
Go-1.2
Up
Down
Enter
B−12−0
▲
▼
The page will show out, when rY3.Md set
to be N/R/C mode.
rY3.ot: Relay 3 energized time
Setting Range:
0:00.0~9(M):59.9(S)
Shift
Up
Down
Enter
B−12
▲
▼
The page will show out, when rY3.Md set
to be Hi/Lo mode.
rY3.HY: Relay 3 Hysteresis
Setting Range: 0~5000 counts
Shift
Up
Down
Enter
B−13
▲
▼
The page will show out, when rY3.Md set
to be Hi/Lo mode.
rY3.rd: Relay 3 energized delay time
Setting Range:
0:00.0~9(M):59.9(S)
Shift
Up
Down
Enter
B−14
▲
▼
The page will show out, when rY3.Md set
to be Hi/Lo mode.
rY3.Fd: Relay 3 de-energized delay
time
Setting Range:
0:00.0~9(M):59.9(S)
Shift
Up
Down
Enter
B−15
▲
▼
rY4.Md: Relay 4 energized mode ….as Relay 1 Energized Mode…
Selectable: oFF / Lo / Hi /
Lo.HLd / Hi.HLd / do / btcH.n /
btCH.r / btCH.C / totL.n / totL.r /
totL.C
Up
Down
Enter
B−16−0
▲
▼
The page will show out, when rY4.Md set
to be N/R/C mode.
rY4.ot: Relay 4 energized time
Setting Range:
0:00.0~9(M):59.9(S)
Shift
Up
Down
Enter
B−16
▲
▼
The page will show out, when rY4.Md set
to be Hi/Lo mode.
rY4.HY: Relay 4 Hysteresis
Setting Range: 0~5000 counts
Shift
Up
Down
Enter
B−17
▲
▼
The page will show out, when rY4.Md set
to be Hi/Lo mode.
rY4.rd: Relay 4 energized delay time
Setting Range:
0:00.0~9(M):59.9(S)
Shift
Up
Down
Enter
B−18
▲
▼
The page will show out, when rY4.Md set
to be Hi/Lo mode.
rY4.Fd: Relay 4 de-energized delay
time
Setting Range:
0:00.0~9(M):59.9(S)
Shift
Up
Down
Enter

19 / 27 CS2-TM(Pulse)-Operating Manual 2012-05-10
EXTERNAL CONTROL INPUT(E.C.I.) GRUOP (standard function)
DESCRIPTION PARAMETERS
EN
T
F N
EXTERNAL CONTROL INPUT
GROUP INDEX
In following page, press
for 1 second to back
EXTERNAL CONTROL
INPUT GROUP INDEX.
C−1
▲
▼
ECi.1: External Control Input 1
Relative to immediate value(PV):
Max. ( Mini.) Hold & Reset
PV Hold & Reset
Present
Value
ResetDataHold
by E.C.I. ON
Level
Trigger
ON ON
Reset the Max.(or
Mini.) Hold by
E.C.I. or Front Key
ON
Level Trigger
Maximum Hold PV Hold
Present
Value
Relative to Totalizer / Batch / Batch
Counter
Gate for Energ
y
/ Batch
Energy
Reset for Energy / Batch
Energy
Energy
/ Batch
Gate by E.C.I.
or Front Key O
N
Level Trigger ON ON ON Reset by E.C.I.
or Front Key
O
N
Ed
g
e Tri
gg
er ON ON
Energy
/ Batch
Selectable
none:No function
rEL.Pv: (Relative PV) function.
When the E.C.I. is closed, the
reading will show the
differential value(ΔPV).
Pv.HLd The E.C.I. can be set to
be Pv.HLd(PV Hold) function.
The display will be hold when
the E.C.I. is closed, until the
E.C.I. is to be open. Please
refer to the below figure.
M.rSt: Reset for max./mini. Hold
or Memorize.
rY.rSt If relay energized mode
was set to be Energized
hold, the E.C.I. can be set to
be rY.rSt(Reset Relay
function). When the PV
meets the condition of relay
energizing, the relay will be
hold until the E.C.I. is
closed.
di(Digital Input): The E.C.I can
be set to be DI(Digital Input)
function, when the meter
building in RS485 port. The
computer is easier to get a
switch status through the
meter as like as DI of PLC.
GAtE(Gate): Totalizer, Batch
and Btach Counter will be
stop to count, when E.C.I. Iis
close.
rESEt(Reset for Totalizer &
Batch): Totalizer, Batch and
Btach Counter will be reset
to “0”, when E.C.I. Iis close.
tL.GtE(Gate for Totalizer/Batch
counter): Totalizer or Batch
Counter will be stop to
count, when E.C.I. Iis close.
tL.rSt(Reset for Totalizer):
Totalizer or Batch Counter
will be reset to “0”, when
E.C.I. Iis close.
bt.GtE(Gate for Batch): Batch
will be stop to count, when
E.C.I. Iis close.
bt.rSt(Reset for Batch): Batch
will be reset to “0”, when
E.C.I. Iis close.
Up
Down
Enter
Next P.

20 / 27 CS2-TM(Pulse)-Operating Manual 2012-05-10
C−2
▲
▼
ECi.2: External Control Input 2 Selectable: same as ECI1
…other as same as ECI1…
Up
Down
Enter
C−3
▲
▼
ECi.3: External Control Input 3 Selectable: same as ECI1
…other as same as ECI1…
Up
Down
Enter
C−4
▲
▼
dEbnc: Debouncing of external
control Input Setting Range: 5~255( x 8ms)
Shift
Up
Down
Enter
C−5
▲
▼
E.1=UP(E.C.I.1=UP )
The
Key can be set to be the same
function as the setting of ECI1.
Ex. The ECI1 set to be Pv.HLd and the
function E.1=UP set to be YES in【ECI
Group】. When user presses
Key, the PV
will hold as like as ECI1 close.
If the front key function has been set,
the terminal input for ECI will be
disabling.
Selectable:
YES : Up Key is to be same
function as ECI1
no : Up Key isn’t to be same
function as ECI1
Up
Down
Enter
C−6
▲
▼
E.2=dn(E.C.I.2=Down )
The
Key can be set to be the same
function as the setting of ECI2.
Selectable:
YES : Down Key is to be same
function as ECI2
no : Down Key isn’t to be same
function as ECI2
Up
Down
Enter
ANALOGUE OUTPUT GRUOP
DESCRIPTION PARAMETERS
EN
T
F N
ANALOGUE OUTPUT GROUP
INDEX
In following page, press
for 1 second to back
ANALOGUE OUTPUT
GROUP INDEX.
D−1
▲
▼
Ao.SEL: Analogue output relative
parameter Totalizer/Batch/Batch
Counter/Immediate Value(PV)
selection
Selectable
Pv: Present Value
bAtCH: Batch
totAL: Totalizer / Batch Counter
Up
Down
Enter
D−2
▲
▼
Ao.tYP: Analogue Output type
selection
Analogue output type has been fixed in
mA or V according to customer ordering.
Therefore, the type selection is for
ranges in same type.
Selectable:
Voltage Output:
v.0-10(0~10V) /
v. 0-5(0~5V) / v.1-5(1~5V) /
Current Output:
A.0-10(0~10mA) /
A.0-20(0~20mA) /
A.4-20(4~20mA)
Up
Down
Enter
D−3
▲
▼
Ao.LS: Analogue Output relative Low
Scale
Setting Range:
Immediate Value(PV):
-19999~+29999
Totalizer/Batch: 0~9999999999
Shift
Up
Down
Enter
接下頁
Other ADTEK Controllers manuals
Popular Controllers manuals by other brands
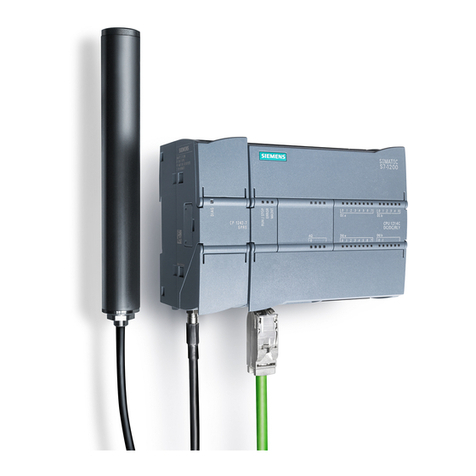
Siemens
Siemens SIMATIC NET S7-1200 operating instructions
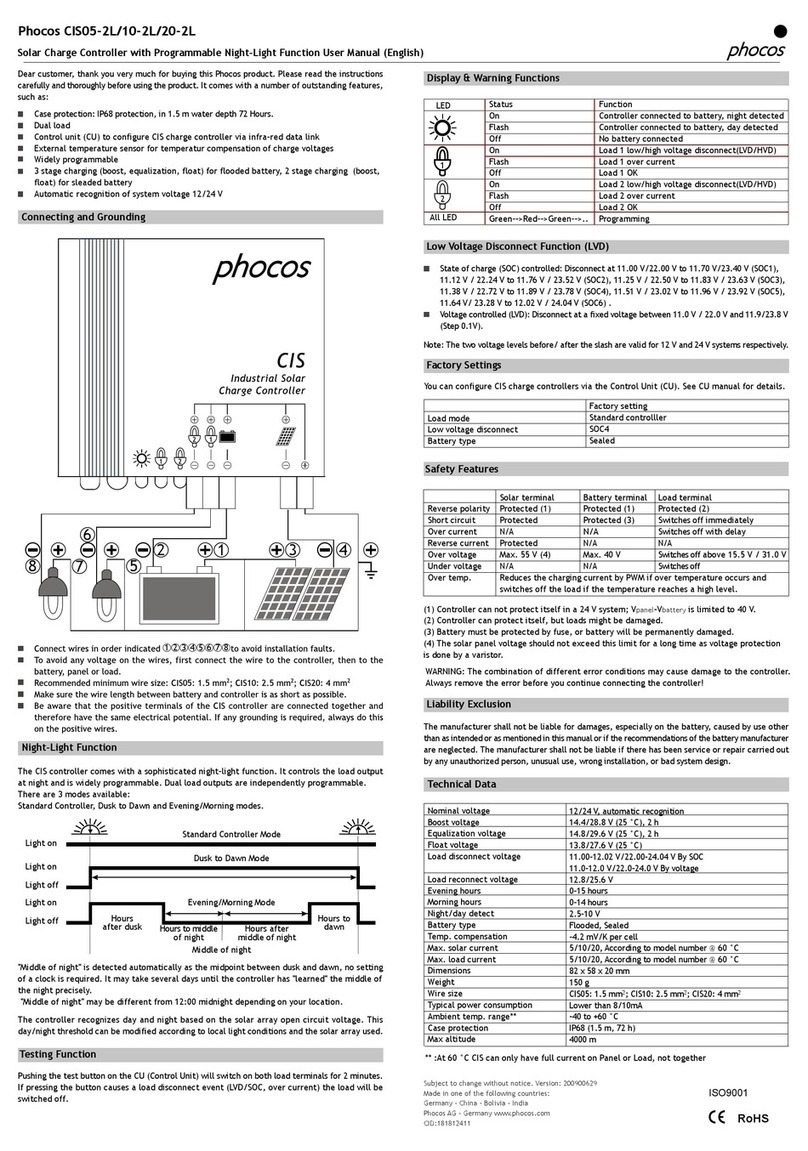
Phocos
Phocos CIS05-2L user manual
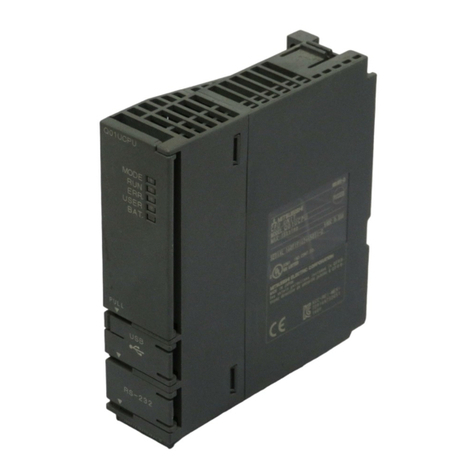
Mitsubishi Electric
Mitsubishi Electric MELSEC-Q00U(J)CPU user manual
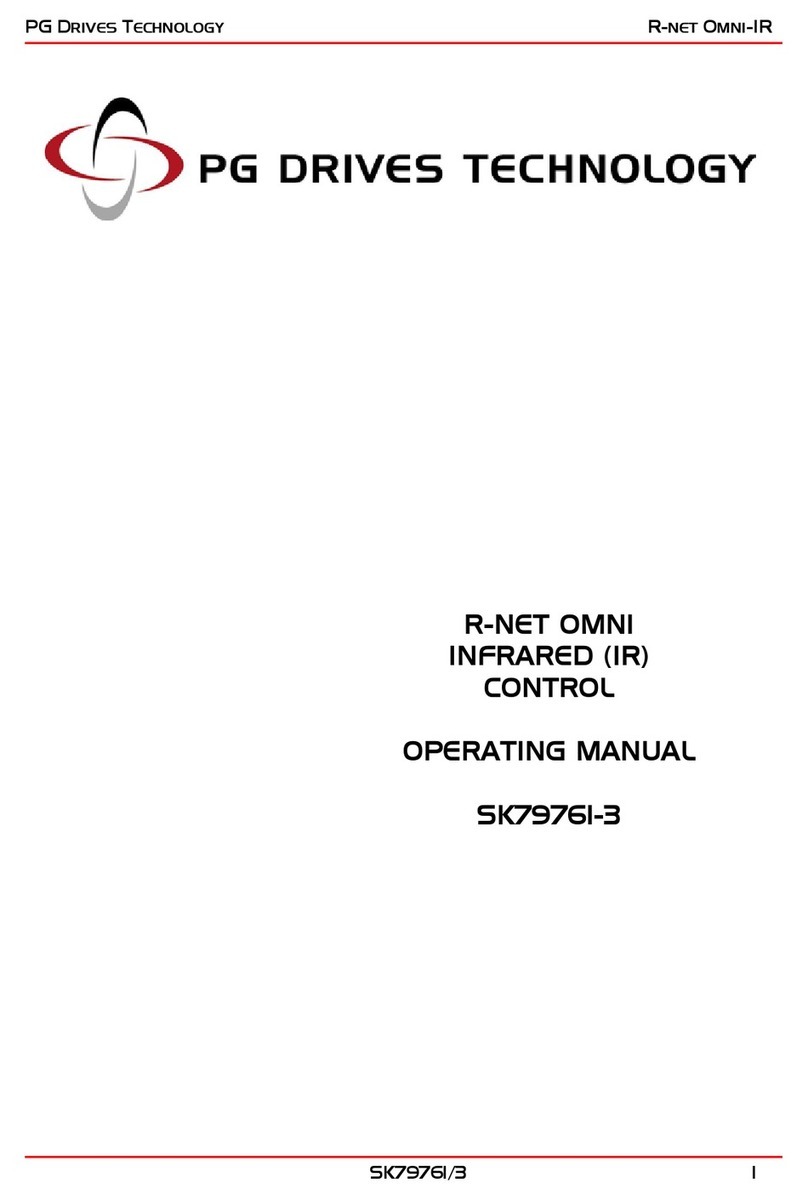
PG Drives Technology
PG Drives Technology SK79761-3 operating manual

Johnson Controls
Johnson Controls A350E Product/Technical Bulletin
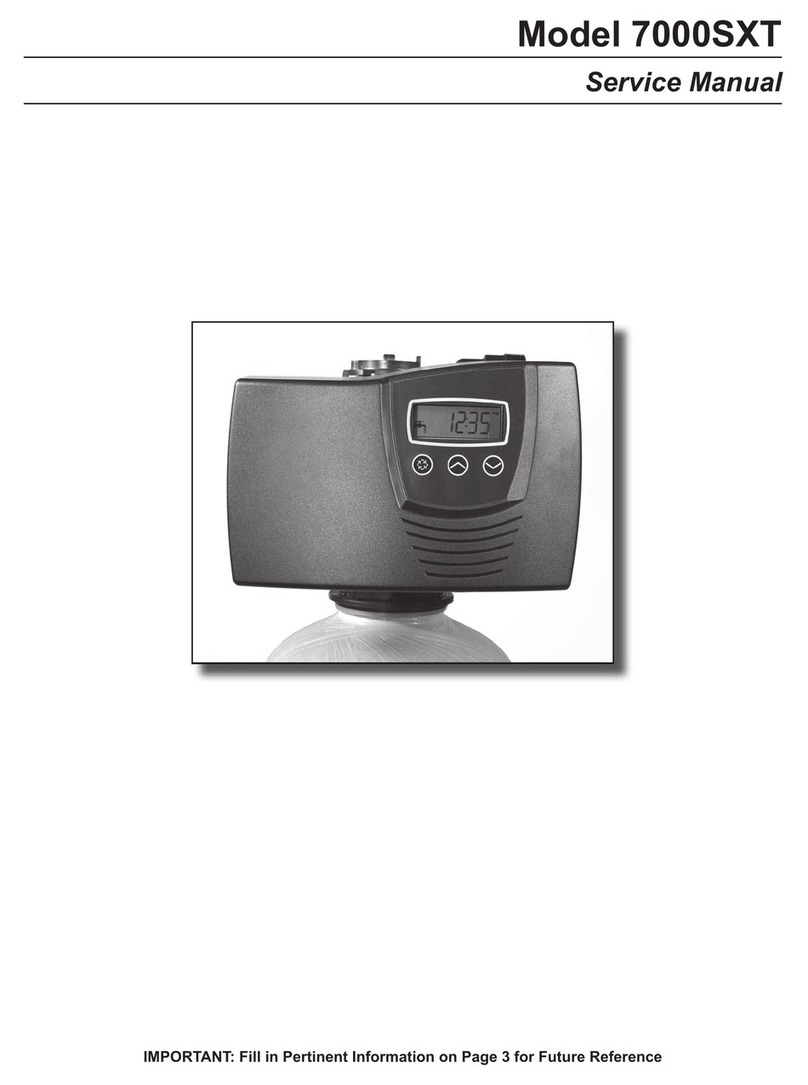
Fleck
Fleck 7000SXT Service manual