Aerotech Ensemble CL User manual

P/N:EDU189
Revision: 4.09.00
Ensemble CL
Hardware Manual
RELAY TB206
NC
C
NO
OPTO IN TB205
+5V
C
0
1
2
3
4
5
6
7
OPTO IN TB204
C
0
1
2
3
4
5
6
7
GND
OPTO OUT TB203
OP
OM
0
1
2
3
4
5
6
7
OPTO OUT TB202
OP
OM
0
1
2
3
4
5
6
7
TB201
AGND
AIN+
AIN-
AOUT
J103
ETHERNET
AEROTECH.AEROTECH.
COMCOM
TM
J103
ETHERNET
AEROTECH.AEROTECH.
COMCOM
TM
J104
MOTOR FEEDBACK
ESTOP
TB101
J105
MOTOR
SUPPLY MOTOR
OUTPUT
TB102
28 VAC 10A MAX
0 VAC-CT
EXTERNAL
TRANSFORMER
REQUIRED
50/60Hz
A
B
High Voltage
DANGER!
C
ENB/FLT
MARKER
POWER
INPOS
AUX I/O
J104
MOTOR FEEDBACK
ESTOP
TB101
J105
MOTOR
SUPPLY MOTOR
OUTPUT
TB102
28 VAC 10A MAX
28 VAC 10A MAX 28 VAC 10A MAX
0 VAC-CT
EXTERNAL
TRANSFORMER
REQUIRED
50/60Hz
A
B
High Voltage
DANGER!
C
ENB/FLT
MARKER
POWER
INPOS
AUX I/O

Global Technical Support
Go to www.aerotech.com/global-technical-support for information and support about your Aerotech products. The website
provides downloadable resources (such as up-to-date software, product manuals, and Help files), training schedules, and PC-
to-PC remote technical support. You can also complete Product Return (RMA) forms and get information about repairs and
spare or replacement parts. For immediate help, contact a service office or your sales representative. Have your customer
order number available before you call or include it in your email.
United States (World Headquarters)
Phone: +1-412-967-6440
Fax: +1-412-967-6870
Email: service@aerotech.com
101 Zeta Drive
Pittsburgh, PA 15238-2897
www.aerotech.com
United Kingdom Japan
Phone: +44 (0)1256 855055
Fax: +44 (0)1256 855649
Email: service@aerotech.co.uk
Phone: +81 (0)50 5830 6814
Fax: +81 (0)43 306 3773
Email: service@aerotechkk.com.jp
Germany China
Phone: +49 (0)911 967 9370
Fax: +49 (0)911 967 93720
Email: service@aerotechgmbh.de
Phone: +86 (21) 3319 7715
Email: saleschina@aerotech.com
France Taiwan
Phone: +33 1 64 93 58 67
Email: sales@aerotech.co.uk
Phone: +886 (0)2 8751 6690
Email: service@aerotech.tw
This manual contains proprietary information and may not be reproduced, disclosed, or used in whole or in part without the
express written permission of Aerotech, Inc. Product names mentioned herein are used for identification purposes only and
may be trademarks of their respective companies.
Copyright © 2007-2015, Aerotech, Inc. All rights reserved.

Table of Contents Ensemble CL
Table of Contents
Table of Contents iii
List of Figures v
List of Tables vii
EC Declaration of Conformity ix
Safety Procedures and Warnings xi
Quick Installation Guide xiii
Chapter 1: Introduction 1
1.1. Drive and Software Compatibility 4
1.2. Electrical Specifications 5
1.2.1. System Power Requirements 6
1.3. Mechanical Design 7
1.4. Environmental Specifications 8
Chapter 2: Installation and Configuration 9
2.1. Power Connections 9
2.1.1. Control Supply Connections (TB103) 10
2.1.2. Motor Supply Connections (TB102) 11
2.1.3. Transformer Options 12
2.2. Motor Output Connections 15
2.2.1. Brushless Motor Connections 16
2.2.1.1. Powered Motor Phasing 17
2.2.1.2. Unpowered Motor and Feedback Phasing 19
2.2.2. DC Brush Motor Connections 22
2.2.2.1. DC Brush Motor Phasing 23
2.2.3. Stepper Motor Connections 24
2.2.3.1. Stepper Motor Phasing 25
2.3. Motor Feedback Connections (J104) 26
2.3.1. Encoder Interface (J104) 27
2.3.1.1. RS-422 Line Driver Encoder (Standard) 28
2.3.1.2. EnDat Encoder Interface (J104) 29
2.3.1.3. Resolute Encoder Interface (J104) 30
2.3.1.4. Analog Encoder Interface 31
2.3.1.5. Encoder Phasing 33
2.3.2. Hall-Effect Interface (J104) 35
2.3.3. Thermistor Interface (J104) 36
2.3.4. Encoder Fault Interface (J104) 37
2.3.5. End Of Travel Limit Input Interface (J104) 38
2.3.5.1. End Of Travel Limit Phasing 40
2.3.6. Brake Output (J104) 41
2.4. Emergency Stop Sense Input (TB101) 42
2.4.1. Typical ESTOP Interface 43
2.5. Auxiliary I/O Connector (J105) 44
2.5.1. Auxiliary Encoder Channel (J105) 45
2.5.2. Position Synchronized Output (PSO)/Laser Firing (J105) 47
2.5.3. Opto-Isolated Outputs (J105) 49
2.5.4. Opto-Isolated Inputs (J105) 51
2.5.5. High Speed User Inputs 4-5 (J105) 53
2.5.6. Analog Output 0 (J105) 54
2.5.7. Analog Input 0 (J105) 55
2.6. Aeronet Interface (J107/J108) 56
www.aerotech.com iii

iv www.aerotech.com
2.7. RS-232 Interface (TB104) 57
2.8. PC Configuration and Operation Information 58
Chapter 3: -I/O Expansion Board 59
3.1. Analog Output (TB201) 60
3.2. Analog Input (TB201) 61
3.3. Opto-Isolated Inputs (TB204, TB205) 62
3.4. Opto-Isolated Outputs (TB202, TB203) 65
3.5. User Power (TB204, TB205) 69
3.6. Brake / Mechanical Relay (TB206) 70
3.6.1. Brake Configuration Jumpers 70
3.6.2. Mechanical Relay Specifications 70
3.6.3. Brake / Mechanical Relay Interface Connector 71
Chapter 4: Standard Interconnection Cables 73
4.1. Joystick Interface 74
4.2. Handwheel Interface 76
Chapter 5: Maintenance 77
5.1. Control Board 78
5.2. Preventative Maintenance 80
Appendix A: Warranty and Field Service 81
Appendix B: Revision History 83
Index 85
Ensemble CL Table of Contents

Table of Contents Ensemble CL
List of Figures
Figure 1-1: Ensemble CL Networked Digital Drive 1
Figure 1-2: Functional Diagram 3
Figure 1-3: Dimensions 7
Figure 2-1: Control Supply Connections 10
Figure 2-2: Motor Bus Input Connections 11
Figure 2-3: Transformer Examples 12
Figure 2-4: 40 VDC Motor Power with a TV0.3-28-56-ST Transformer 13
Figure 2-5: Control and Motor Power Wiring using a TM3 or TM5 Transformer 14
Figure 2-6: Brushless Motor Configuration 16
Figure 2-7: Encoder and Hall Signal Diagnostics 18
Figure 2-8: Motor Phasing Oscilloscope Example 19
Figure 2-9: Hall Phasing with Oscilloscope 20
Figure 2-10: Brushless Motor Phasing Goal 21
Figure 2-11: DC Brush Motor Configuration 22
Figure 2-12: Clockwise Motor Rotation 23
Figure 2-13: Stepper Motor Configuration 24
Figure 2-14: Clockwise Motor Rotation 25
Figure 2-15: Line Driver Encoder Interface (J104) 28
Figure 2-16: Serial Data Stream Interface 29
Figure 2-17: Serial Data Stream Interface 30
Figure 2-18: Analog Encoder Phasing Reference Diagram 31
Figure 2-19: Analog Encoder Interface (J104) 32
Figure 2-20: Encoder Phasing Reference Diagram (Standard) 33
Figure 2-21: Position Feedback in the DiagnosticDisplay 34
Figure 2-22: Hall-Effect Inputs (J104) 35
Figure 2-23: Thermistor Interface Input (J104) 36
Figure 2-24: Encoder Fault Interface Input (J104) 37
Figure 2-25: End of Travel Limit Input Connections 38
Figure 2-26: End of Travel Limit Interface Input (J104) 39
Figure 2-27: Limit Input Diagnostic Display 40
Figure 2-28: ESTOPSenseInput (TB101) 42
Figure 2-29: Typical Emergency Stop Circuit 43
Figure 2-30: Auxiliary Encoder Channel (J105) 46
Figure 2-31: PSOInterface 48
Figure 2-32: Outputs Connected in Current Sinking Mode (J105) 50
Figure 2-33: Outputs Connected in Current Sourcing Mode (J105) 50
Figure 2-34: Inputs Connected in Current Sinking Mode (J105) 52
Figure 2-35: Inputs Connected in Current Sourcing Mode (J105) 52
Figure 2-36: High Speed User Inputs (J105) 53
Figure 2-37: Analog Output 0 (J105) 54
Figure 2-38: Analog Input 0 (J105) 55
Figure 2-39: Aeronet Connection with Three Discrete Drives 56
Figure 2-40: RS-232 Interface (TB104) 57
Figure 3-1: Ensemble CL with -IO Option Board 59
Figure 3-2: Analog Output 1 Connector (TB201) 60
Figure 3-3: Analog Input Typical Connection (TB201) 61
Figure 3-4: Opto-Isolated Inputs 63
Figure 3-5: Inputs Connected to a Current Sourcing Device 64
Figure 3-6: Inputs Connected to a Current Sinking Device 64
Figure 3-7: Opto-Isolated Outputs (-IOBoard) 66
Figure 3-8: Outputs Connected in Current Sourcing Mode 67
www.aerotech.com v

vi www.aerotech.com
Figure 3-9: Outputs Connected in Current Sinking Mode 68
Figure 3-10: Brake Connected to J104 71
Figure 3-11: Brake Connected to TB206 72
Figure 4-1: Single Axis Joystick Interface (to Aux I/O) 74
Figure 4-2: Two Axis Joystick Interface (to the Aux I/O of two drives) 74
Figure 4-3: Two Axis Joystick Interface (to the Aux I/O and I/O Board) 75
Figure 4-4: Handwheel Interconnection (to Aux I/O) 76
Figure 4-5: Handwheel Interconnection (to Aux I/O via a BBA32 Module) 76
Figure 5-1: Control Board Assembly 78
Ensemble CL Table of Contents

Table of Contents Ensemble CL
List of Tables
Table 1-1: FeatureSummary 2
Table 1-2: Accessories 2
Table 1-3: Ensemble Drive and Software Compatibility 4
Table 1-4: Electrical Specifications 5
Table 1-5: Physical Specifications 7
Table 2-1: Control Supply ACInput Wiring 10
Table 2-2: Control Supply Mating Connector 10
Table 2-3: Motor Supply Mating Connector 11
Table 2-4: TransformerOptions 12
Table 2-5: Motor Power Output Connections (TB102) 15
Table 2-6: Motor Power Output Mating Connector 15
Table 2-7: Wire Colors for Aerotech Supplied Cables (Brushless) 16
Table 2-8: Wire Colors for Aerotech Supplied Cables (DCBrush) 22
Table 2-9: Wire Colors for Aerotech Supplied Cables (Stepper) 24
Table 2-10: Motor Feedback Connector Pin Assignment (J104) 26
Table 2-11: Encoder Interface Pin Assignment 27
Table 2-12: Analog Encoder Specifications 31
Table 2-13: Hall-Effect Feedback Interface Pin Assignment (J104) 35
Table 2-14: Hall-Effect Feedback Interface Pin Assignment (J104) 36
Table 2-15: Encoder Fault Interface Pin Assignment (J104) 37
Table 2-16: End of Travel Limit Input Interface Pin Assignment (J104) 38
Table 2-17: Brake Output Pin Assignment (J104) 41
Table 2-18: Electrical Noise Suppression Devices 42
Table 2-19: Electrical Noise Suppression Devices 42
Table 2-20: TB101 Mating Connector 42
Table 2-21: Typical ESTOPRelay Ratings 43
Table 2-22: Auxiliary I/O Connector Pin Assignment (J105) 44
Table 2-23: Auxiliary Encoder Channel Pin Assignment (J105) 45
Table 2-24: PSOOutput Pin Assignment (J105) 47
Table 2-25: PSO Output Sources 47
Table 2-26: Port 0 Digital Output Connector Pin Assignment (J105) 49
Table 2-27: Digital Output Specifications 49
Table 2-28: Port 0 Digital Input Connector Pin Assignment (J105) 51
Table 2-29: PS2806-4 Opto-Device Specifications 51
Table 2-30: Port 0 High Speed Digital Input Connector Pin Assignment (J105) 53
Table 2-31: Input Voltage Jumper Configuration 53
Table 2-32: Analog Output Connector Pin Assignment (J105) 54
Table 2-33: Analog Input Connector Pin Assignment (J105) 55
Table 2-34: Aeronet Cable Part Numbers 56
Table 2-35: RS-232 Connector Pin Assignment (TB104) 57
Table 2-36: RS-232 Port Connector Mating Connector (TB104) 57
Table 3-1: -IO Expansion Board Jumper Configuration 59
Table 3-2: -IO Option Board Fuse Information 59
Table 3-3: Analog Output Connector Pin Assignment (TB201) 60
Table 3-4: Analog Output Mating Connector 60
Table 3-5: Analog Inputs Connector Pin Assignment (TB201) 61
Table 3-6: Analog Input Mating Connector 61
Table 3-7: PS2806-4 Opto-Device Specifications 62
Table 3-8: Port 1 Opto-Isolated Input Connector Pin Assignment (TB204) 62
Table 3-9: Port 2 Opto-Isolated Input Connector Pin Assignment (TB205) 62
Table 3-10: Opto-Isolated Input Mating Connector 62
www.aerotech.com vii

viii www.aerotech.com
Table 3-11: Port 1 Opto-Isolated Output Connector Pin Assignment (TB202) 65
Table 3-12: Port 2 Opto-Isolated Output Connector Pin Assignment (TB203) 65
Table 3-13: Opto-Isolated Output Mating Connector 65
Table 3-14: Output Specifications (TB202, TB203) 67
Table 3-15: User Common Connector Pin Assignment (TB204) 69
Table 3-16: +5 Volt Power Connector Pin Assignment (TB205) 69
Table 3-17: -IO Expansion Board Brake Jumper Configuration 70
Table 3-18: Voltage and Current Specifications (TB206) 70
Table 3-19: Brake / Mechanical Relay Connector Pin Assignment (TB206) 71
Table 3-20: Mating Connector 71
Table 3-21: Brake / Mechanical Relay Connector Pin Assignment (J104) 71
Table 4-1: Standard Interconnection Cables 73
Table 4-2: Cable Part Numbers 75
Table 5-1: LEDDescription 77
Table 5-2: Control Board Jumper Configuration 79
Table 5-3: Control Board Fuse Information 79
Table 5-4: LEDDescription 79
Table 5-5: Preventative Maintenance 80
Ensemble CL Table of Contents

Declaration of Conformity Ensemble CL
EC Declaration of Conformity
Manufacturer
Aerotech, Inc.
Address
101 Zeta Drive
Pittsburgh, PA 15238-2897
USA
Product
Ensemble CL
Model/Types
All
This is to certify that the aforementioned product is in accordance with the applicable requirements of the
following Directive(s):
2006/95/EC Low Voltage Directive
2011/65/EU RoHS2 Directive
and has been designed to be in conformity with the applicable requirements of the following documents
when installed and used in accordance with the manufacturer’s supplied installation instructions.
EN 61000-4-3 Radiated RFI/EMI Immunity
EN 61010-1 Safety requirements for electrical equipment
Name
/ Alex Weibel
Position
Engineer Verifying Compliance
Location
Pittsburgh, PA
Date
July 9, 2015
www.aerotech.com ix

Ensemble CL Declaration of Conformity
x www.aerotech.com
This page intentionally left blank.

Electrical Safety Ensemble CL
Safety Procedures and Warnings
The following statements apply wherever the Warning or Danger symbol appears within this manual. Failure
to observe these precautions could result in serious injury to those individuals performing the procedures
and/or damage to the equipment.
N O T E : Read this manual in its entirety before installing, operating, or servicing this product. If you do
not understand the information contained herein, contact an Aerotech representative before proceeding.
Strictly adhere to the statements given in this section and other handling, use, and operational information
given throughout the manual to avoid injury to you and damage to the equipment.
N O T E : Aerotech continually improves its product offerings; listed options may be superseded at any
time. All drawings and illustrations are for reference only and were complete and accurate as of this
manual’s release. Refer to www.aerotech.com for the most up-to-date information.
D A N G E R : This product contains potentially lethal voltages. To reduce the possibility of
electrical shock, bodily injury, or death the following precautions must be followed.
1. Disconnect electrical power before servicing equipment.
2. Disconnect electrical power before performing any wiring.
3. Access to the Ensemble CL and component parts must be restricted while connected to a
power source.
4. To minimize the possibility of electrical shock and bodily injury, extreme care must be
exercised when any electrical circuits are in use. Suitable precautions and protection must
be provided to warn and prevent persons from making contact with live circuits.
5. Install the Ensemble CL inside a rack or enclosure.
6. Do not connect or disconnect any electrical components or connecting cables while
connected to a power source.
7. Make sure the Ensemble CL and all components are properly grounded in accordance with
local electrical safety requirements.
8. Operator safeguarding requirements must be addressed during final integration of the
product.
D A N G E R : The Ensemble CL case temperature may exceed 70°C in some applications.
www.aerotech.com xi

xii www.aerotech.com
W A R N I N G : To minimize the possibility of electrical shock, bodily injury or death the
following precautions must be followed.
1. Use of this equipment in ways other than described by this manual can cause personal
injury or equipment damage.
2. Moving parts can cause crushing or shearing injuries. Access to all stage and motor parts
must be restricted while connected to a power source.
3. Cables can pose a tripping hazard. Securely mount and position all system cables to avoid
potential hazards.
4. Do not expose the Ensemble CLto environments or conditions outside of the listed
specifications. Exceeding environmental or operating specifications can cause damage to
the equipment.
5. If the Ensemble CL is used in a manner not specified by the manufacturer, the protection
provided by the Ensemble CL can be impaired and result in damage, shock, injury, or death.
6. Operators must be trained before operating this equipment.
7. All service and maintenance must be performed by qualified personnel.
8. The Ensemble CL is intended for light industrial manufacturing or laboratory use. Use of the
Ensemble CL for unintended applications can result in injury and damage to the equipment.
Ensemble CL Electrical Safety

Quick Installation Guide Ensemble CL
Quick Installation Guide
This chapter describes the order in which connections and settings should typically be made to the
Ensemble CL. If a custom interconnection drawing was created for your system (look for a line item on your
Sales Order under the heading “Integration”), that drawing can be found on your installation device.
RELAY TB206
NC
C
NO
OPTO IN TB205
+5V
C
0
1
2
3
4
5
6
7
OPTO IN TB204
C
0
1
2
3
4
5
6
7
GND
OPTO OUT TB203
OP
OM
0
1
2
3
4
5
6
7
OPTO OUT TB202
OP
OM
0
1
2
3
4
5
6
7
TB201
AGND
AIN+
AIN-
AOUT
J103
ETHERNET
AEROTECH.AEROTECH.
COMCOM
TM
J104
MOTOR FEEDBACK
ESTOP
TB101
J105
MOTOR
SUPPLY MOTOR
OUTPUT
TB102
28 VAC 10A MAX
28 VAC 10A MAX
0 VAC-CT
EXTERNAL
TRANSFORMER
REQUIRED
50/60Hz
A
B
High Voltage
DANGER!
C
ENB/FLT
MARKER
POWER
INPOS
AUX I/O
S/N -
P/N -
50/60HZ
85-240V~
1A MAX
CONTROL
SUPPLY
TB103
AC1
AC2
USB
TB104
+5V / 0.5A
RS232 TX/RS422 TX+
RS232 RX/RS422 TX-
RS422 RX-
RS422 RX+
GND
J106
USB
WARNING:
DISCONNECT POWER BEFORE
SERVICING
HAZARDOUS VOLTAGES PRESENT
UP TO 8 MIN. AFTER POWER IS
DISCONNECTED
J107
AERONET
OUTPUT
AERONET
INPUT
J108
Connect Motor Outputs (TB102) and Motor Feedback (J104).
Connect the PC to either the Ethernet (J103) or the USB (J106).
Connect any additional I/O as required (not shown).
Connect to the Control Supply (TB103).
Connect to the Motor Supply (TB102).
Note: Connect to ESTOP (TB101) in this step if applicable.
1
6
1
1
3
Connect a multi-axis Ensemble system with Aeronet (J107, J108).
2
4
5
6
3
6
5
3
2
Figure 1: Quick Start Connections
Topic Section
Motor Output Section 2.2. Motor Output Connections
Motor Feedback Section 2.3. Motor Feedback Connections (J104)
Aeronet Section 2.6. Aeronet Interface (J107/J108)
Ethernet / USB No Section / Standard Connection
Control Supply Section 2.1.1. Control Supply Connections (TB103)
Motor Supply Section 2.1.2. Motor Supply Connections (TB102)
Additional I/O User / Application dependent
www.aerotech.com xiii

Ensemble CL Quick Installation Guide
xiv www.aerotech.com
This page intentionally left blank.

Introduction Ensemble CL
Chapter 1: Introduction
Aerotech’s Ensemble CL(CompactLinear) network digital drive is a high performance linear amplifier
designed to eliminate the nonlinearities common with PWMamplifiers. The drive provides deterministic
behavior, auto-identification, and easy software setup. The Ensemble CL’s high performance double
precision floating point DSP controls the digital PID and current loops. All system configuration is done using
software-settable parameters, including control loop gains and system safety functions.
The Ensemble CL is offered with an optional encoder interpolation feature (-MXU), an auxiliary square wave
encoder input for dual loop control, dedicated analog and digital I/O (expandable with the -IO option), and
separate power connections for motor and control supply voltages.
RELAY TB206
NC
C
NO
OPTO IN TB205
+5V
C
0
1
2
3
4
5
6
7
OPTO IN TB204
C
0
1
2
3
4
5
6
7
GND
OPTO OUT TB203
OP
OM
0
1
2
3
4
5
6
7
OPTO OUT TB202
OP
OM
0
1
2
3
4
5
6
7
TB201
AGND
AIN+
AIN-
AOUT
J103
ETHERNET
AEROTECH.AEROTECH.
COMCOM
TM
J104
MOTOR FEEDBACK
ESTOP
TB101
J105
MOTOR
SUPPLY MOTOR
OUTPUT
TB102
28 VAC 10A MAX
28 VAC 10A MAX
0 VAC-CT
EXTERNAL
TRANSFORMER
REQUIRED
50/60Hz
A
B
High Voltage
DANGER!
C
ENB/FLT
MARKER
POWER
INPOS
AUX I/O
S/N -
P/N -
50/60HZ
85-240V~
1A MAX
CONTROL
SUPPLY
TB103
AC1
AC2
USB
TB104
+5V / 0.5A
RS232 TX/RS422 TX+
RS232 RX/RS422 TX-
RS422 RX-
RS422 RX+
GND
J106
USB
WARNING:
DISCONNECT POWER BEFORE
SERVICING
HAZARDOUS VOLTAGES PRESENT
UP TO 8 MIN. AFTER POWER IS
DISCONNECTED
J107
AERONET
OUTPUT
AERONET
INPUT
J108
Standard
Connector Description
J103 Ethernet Port
J104 Motor Feedback
J105 Auxiliary I/O
J106 USB Port
J107 Aeronet Output
J108 Aeronet Input
TB101 Emergency Stop Sense Input (ESTOP)
TB102 Motor Supply
TB102 Motor Output
TB103 Control Supply Output
TB104 RS232/Brake Power Supply
-IO Board Option
Connector Description
TB201 Analog I/O
TB202 Opto-Outputs
TB203 Opto-Outputs
TB204 Opto-Inputs
TB205 Opto-Inputs
TB206 Relay
Figure 1-1: Ensemble CL Networked Digital Drive
www.aerotech.com Chapter 1 1

2 Chapter 1 www.aerotech.com
Table 1-1: FeatureSummary
Standard Features
lLine driver square wave quadrature encoder input for position and velocity feedback
lLine driver square wave auxiliary quadrature encoder input or output for PSO
lFour opto-isolated user outputs
lSix opto-isolated user inputs(two high speed)
lOne 16-bit differential analog input (±10 V)
lOne 16-bit analog output (±10 V)
lDedicated 5-24 V Emergency Stop sense input
lSingle axis Position Synchronized Output (PSO)
lAbsolute Encoder support
lCalibration (refer to the EnsembleHelp file for more information)
lCamming (refer to the EnsembleHelp file for more information)
l10/100 BASE-T Ethernet port for use with Ethernet I/O modules
Options
-IO lOne 16-bit analog output (±10 V)
lOne 12-bit differential analog input
lOne fail-safe brake or user relay output
l16 optically isolated logic inputs (5 - 24 VDC), may be connected in current
sourcing or sinking mode
l16 optically isolated logic outputs (5 - 24 VDC), user defined as current
sourcing or sinking
-MXU Interpolation circuit allowing for analog sine wave input on the standard encoder
channel. Interpolation factor: 8,192
Table 1-2: Accessories
Accessories
MCK-NDRIVE Mating connector kit for J104 (J105 mate is always provided)
JI Industrial Joystick (NEMA12 (IP54) rated); refer to Section 4.1.
PS24-1 24 VDC, 1Apower supply for optional brake/relay output
BRAKE24-2 24 VDC, 2 A power supply for optional brake
Transformers
Refer to Section 2.1.3. for listings, wiring, and specifications
Cables
Interconnection A complete list of Aerotech cables can be found on the website at
http://www.aerotechmotioncontrol.com/manuals/index.aspx
Joystick/Handwheel Refer to Section 4.1. or Section 4.2.
Ensemble CL Introduction

Introduction Ensemble CL
The following block diagram shows a connection summary. For detailed connection information, refer to
Chapter 2 and Chapter 3.
D A N G E R : An external center-tapped power transformer is required! Do not connect the
motor power supply to a voltage greater than 28 VAC (2Ø).
Isolated
Power Supply
Filter
TB103
Control
Supply
Encoder +5V / Common
Brake +/- (with the -IO Option)
SIN, COS, MRK (RS-422)
CW, CCW, Home Limits;
Encoder Fault; Hall A, B, C;
Motor Over Temperature
-MXU
Option
J104
Motor
Feedback
Analog Output 0
Analog Input 0 +/-
2 High Speed Opto Inputs
4 Opto Inputs
4 Opto Outputs
SIN, COS, MRK (RS-422)
Encoder +5V / Common
PSO Output, Encoder Echo
Emergency Stop Sense Input
J105
Aux I/O
Aeronet Input
J108
Aeronet Output
J107
USB 2.0 Port
J106 Ethernet Port J103
Analog Input 1 +/-
Analog Output 1
16 Opto Outputs
(Sinking or Sourcing)
16 Opto Inputs
(Sinking or Sourcing)
Brake Power
Input or Relay
(jumper configurable)
TB201
-IO Option
TB202 /
TB203
Opto Out
TB204 /
TB205
Opto In
TB206
Relay
TB104
RS-232
RS-232
+5V /
Common
External
Transformer
Required
TB101
ESTOP
TB102
Motor
Supply
TB102
Motor
Output
Inrush
Limiting
Inrush
Limiting
28
VAC
CT
28
VAC
28V
28V
CT
A
B
C
A
B
C
Linear Power
Amplifier
Heatsink Over
Temperature
Figure 1-2: Functional Diagram
www.aerotech.com Chapter 1 3

4 Chapter 1 www.aerotech.com
1.1. Drive and Software Compatibility
The following table lists the available Ensemble drives and which version of the Ensemble software first
provided support for a given drive. Drives that list a specific version number in the Last Software Version
column will not be supported after the listed version.
Table 1-3: Ensemble Drive and Software Compatibility
Drive Type Firmware Revision First Software Version Last Software Version
CL - 1.01 Current
A 2.55 Current
CP A 1.00 Current
B 2.54 Current
Epaq(1) - 1.00 Current
A 2.55 Current
HLe - 2.51 Current
HPe - 2.51 Current
LAB - 4.04 Current
ML - 3.00 Current
MP - 1.00 Current
A 2.55 Current
QDe/QL/QLe - 5.01 Current
QLAB - 4.07 Current
(1) This section does not apply to the EpaqMR. The EpaqMR contains multiple ML or MP drives. Refer to
either the ML or MP drive type to determine the value for your EpaqMR.
Ensemble CL Introduction

Introduction Ensemble CL
1.2. Electrical Specifications
The safe operating range is load dependent.
Table 1-4: Electrical Specifications
Description CL 10
Motor Supply Input Voltage Two Phase 28 VAC (56 VAC with a center tap)
Input Frequency 50-60 Hz
Inrush Current 4 A
Maximum Continuous
Input Current
5 Arms
Input Current Refer to Section 1.2.1. System Power Requirements
Control Supply Input Voltage 85-240 VAC
Input Frequency 50-60 Hz
Inrush Current 16 A
Input Current .25 A max
Output Voltage (1) ±38V @ 10A
Peak Output Current (2) 10
Continuous Output Current (2) 5
Power Amplifier Bandwidth (selectable via
parameters)
2500 Hz maximum (software selectable)
Minimum Load Resistance 0.5 Ω
Output Impedance 0.2 Ω (each phase)
User Power Supply Output 5 VDC (@ 500 mA)
Modes of Operation Brushless; Brush; Stepper
Protective Features Peak current limit; Over temperature; RMScurrent limit;
Dynamic power dissipation limit; Designed to
EN61010/UL61010-1
Isolation Optical and transformer isolation between control and power
stages.
(1) Load Dependent
(2) Peak and continuous output current is load dependent (the amplifier will limit its output current based on velocity and motor
resistance).
www.aerotech.com Chapter 1 5

6 Chapter 1 www.aerotech.com
1.2.1. System Power Requirements
The following equations can be used to determine total system power requirements. The actual power
required from the mains supply will be the combination of actual motor power (work), motor resistance
losses, and efficiency losses in the power electronics or power transformer. An EfficiencyFactor of
approximately 50% should be used in the following equations.
Linear Motor
Pdiss[W] = MotorCurrentPeak[A] * TotalBusVoltage[V] * 3 / 2
Pin = SUM (Pdiss ) / EfficiencyFactor
Ensemble CL Introduction
This manual suits for next models
5
Table of contents
Other Aerotech Network Hardware manuals
Popular Network Hardware manuals by other brands
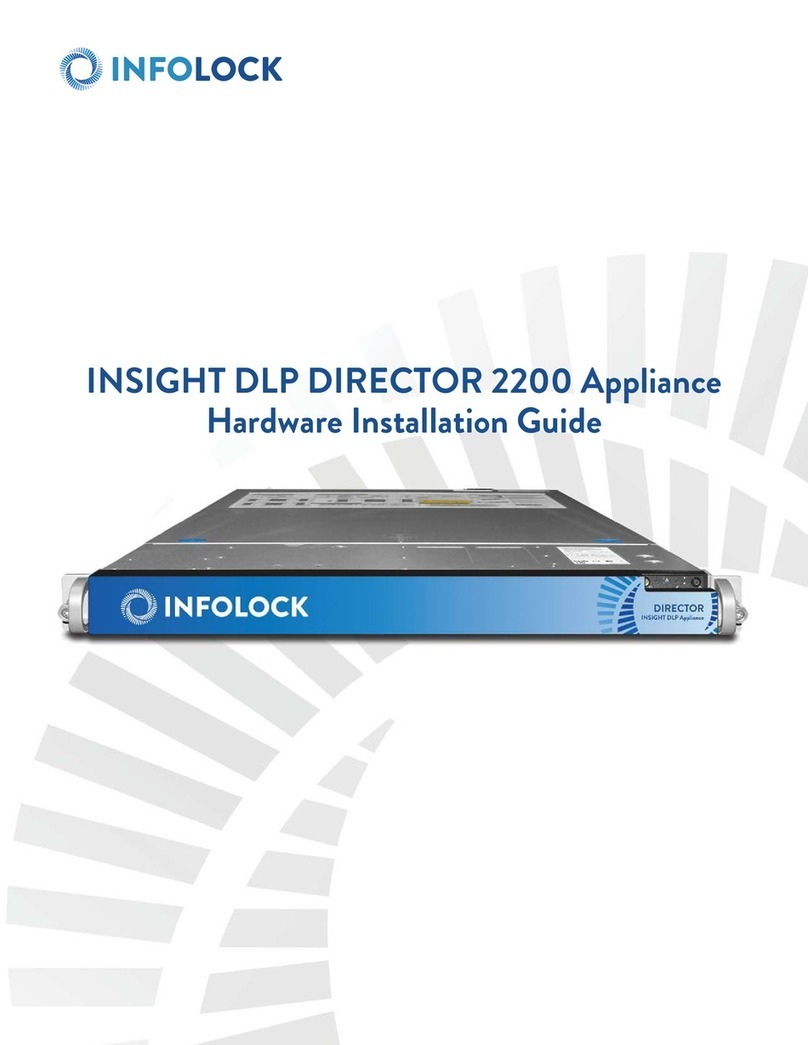
Infolock
Infolock Insight DLP Director 2200 Hardware installation guide
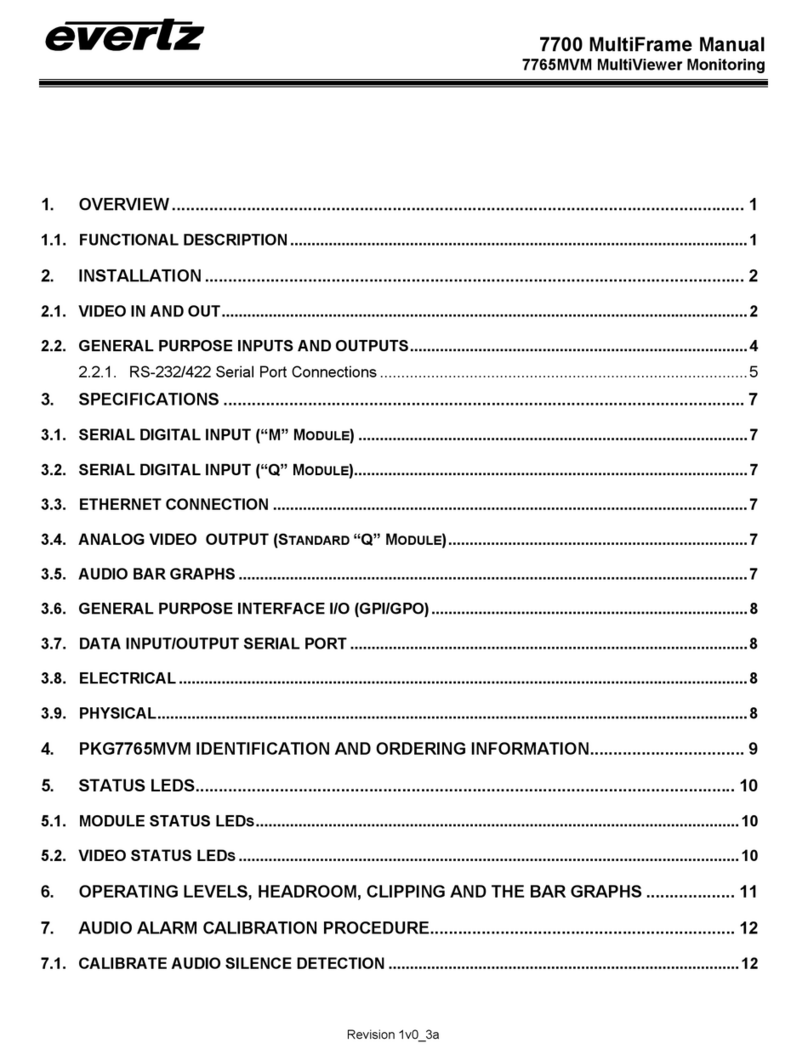
evertz
evertz 7700 Series manual
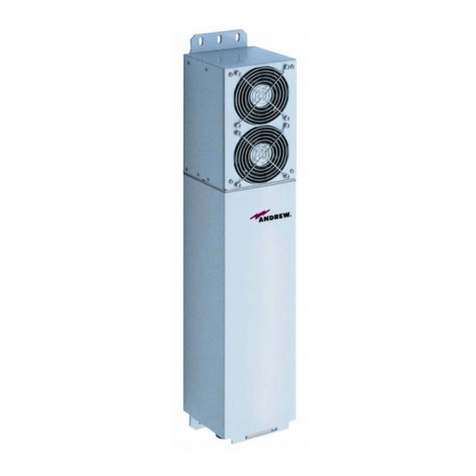
CommScope
CommScope ION-M17EHP/19P manual
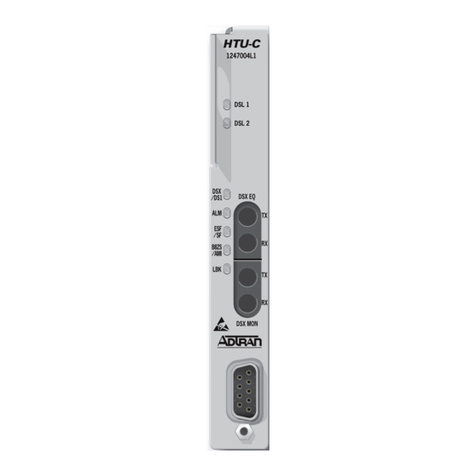
ADTRAN
ADTRAN HDSL 3192 HTU-C Installation and maintenance practice
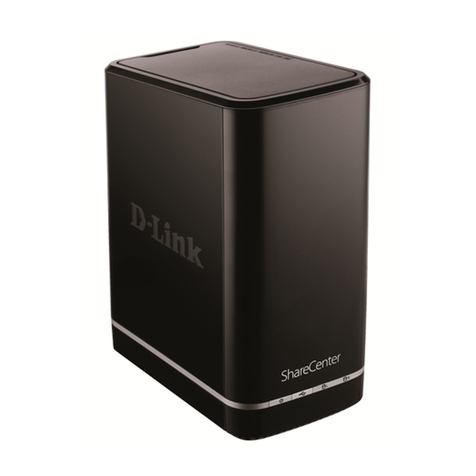
D-Link
D-Link ShareCenter DNS-320L user manual
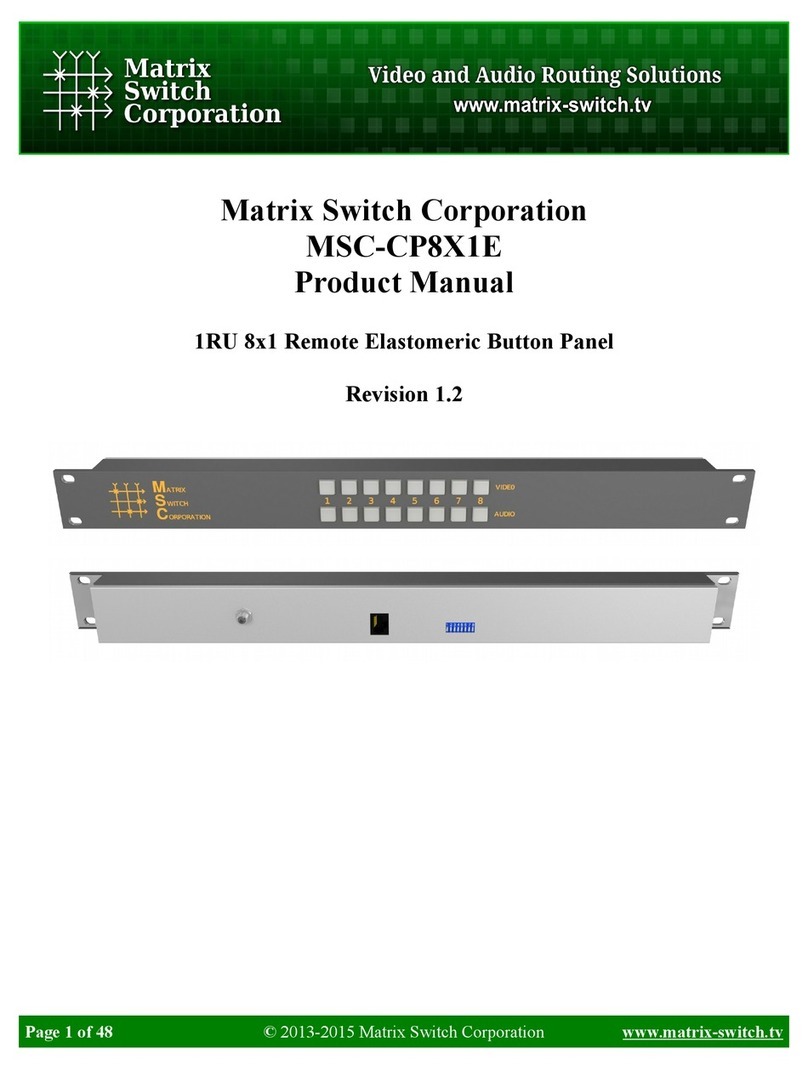
Matrix Switch Corporation
Matrix Switch Corporation MSC-CP8X1E product manual