Aerotech QNP3 Series User manual

Revision: 1.02.00
QNP3 Series
Hardware Manual

Global Technical Support
Go to www.aerotech.com/global-technical-support for information and support about your Aerotech products. The website
provides downloadable resources (such as up-to-date software, product manuals, and Help files), training schedules, and
PC-to-PC remote technical support. You can also complete Product Return (RMA) forms and get information about repairs
and spare or replacement parts. For immediate help, contact a service office or your sales representative. Have your
customer order number available before you call or include it in your email.
United States (World Headquarters)
Phone: +1-412-967-6440
Fax: +1-412-967-6870
Email: service@aerotech.com
101 Zeta Drive
Pittsburgh, PA 15238-2811
www.aerotech.com
United Kingdom Japan
Phone: +44 (0)1256 855055
Fax: +44 (0)1256 855649
Email: service@aerotech.co.uk
Phone: +81 (0)50 5830 6814
Fax: +81 (0)43 306 3773
Email: service@aerotechkk.co.jp
Germany China
Phone: +49 (0)911 967 9370
Fax: +49 (0)911 967 93720
Email: service@aerotechgmbh.de
Phone: +86 (21) 5508 6731
Email: service@aerotech.com
France Taiwan
Phone: +33 2 37 21 87 65
Email: service@aerotech.co.uk
Phone: +886 (0)2 8751 6690
Email: service@aerotech.tw
This manual contains proprietary information and may not be reproduced, disclosed, or used in whole or in part without the
express written permission of Aerotech, Inc. Product names mentioned herein are used for identification purposes only and
may be trademarks of their respective companies.
Copyright © 2016-2018, Aerotech, Inc., All rights reserved.

QNP3 Hardware Manual Table of Contents
Table of Contents
QNP3 Series Hardware Manual 1
Table of Contents 3
List of Figures 5
List of Tables 6
Safety Procedures and Warnings 7
EU Declaration of Conformity 8
Chapter 1: Overview 9
1.1. Understanding Basic QNP3Stage Operation 10
1.2. Environmental Specifications 11
1.3. Linearity and Temperature Effects 12
1.4. Basic Specifications 13
1.5. Vacuum Operation 14
Chapter 2: Mechanical Specifications and Installation 15
2.1. Unpacking and Handling the Stage 15
2.2. Dimensions 16
2.3. Securing the Stage to the Mounting Surface 21
2.4. Attaching the Payload to the Stage 23
2.5. Cable Bend Radius 26
Chapter 3: Electrical Specifications and Installation 27
3.1. Piezo Connectors 28
3.2. Piezo Wiring 30
3.3. Electrical Specifications 31
3.4. Machine Direction 32
3.5. Travel Limits 33
Chapter 4: Maintenance 35
4.1. Service and Inspection Schedule 35
4.2. Cleaning and Lubrication 35
4.3. Poling the Piezo Actuator 36
4.4. Troubleshooting 37
Appendix A: Warranty and Field Service 39
Appendix B: Revision History 41
Appendix C: Piezo Engineering Tutorial 43
C.1 The Direct and Inverse Piezoelectric Effect 43
C.2 Piezo Actuator Materials 43
C.2.1 RoHS Exemption 43
C.3 Properties of Piezo Actuators 43
C.3.1 Displacement Performance 43
C.3.2 Hysteresis Effects 44
C.3.3 Creep and Drift 46
C.3.4 Force and Displacement 46
C.3.4.1 Force Versus Displacement Characteristics 46
C.3.4.2 Displacement With a Constant External Load 47
C.3.4.3 Displacement With an External Spring Load 48
C.3.5 Capacitance 49
C.3.6 Heating and Power Dissipation 50
C.3.7 Environmental Effects 51
C.3.7.1 Humidity 51
www.aerotech.com 3

Table of Contents QNP3 Hardware Manual
C.3.7.2 Temperature 51
C.3.7.3 Vacuum 52
C.4 Piezo Stage Properties and Nomenclature 52
C.4.1 Accuracy/Linearity 52
C.4.2 Resolution 54
C.4.3 Repeatability 55
C.4.4 Stiffness 55
C.4.5 Resonant Frequency 55
C.4.6 Load Ratings 56
C.4.7 Expected Lifetime 56
C.5 Amplifier Selection 57
Index 61
4 www.aerotech.com

QNP3 Hardware Manual Table of Contents
List of Figures
Figure 1-1: Single-Axis Stage Travel and Voltage Relationship 10
Figure 2-1: QNP3-100XYAZ-030-10Dimensions 16
Figure 2-2: QNP3-100XYAZ-100-10Dimensions 17
Figure 2-3: QNP3-150XYAZ-200-20Dimensions 18
Figure 2-4: QNP3-100XYAZ-030-10 Mounting Plate (-MP)Dimensions 19
Figure 2-5: QNP3-100XYAZ-100-10 Mounting Plate (-MP)Dimensions 19
Figure 2-6: QNP3-150XYAZ-200-20 Mounting Plate (-MP)Dimensions 19
Figure 2-7: QNP3-100XYAZ-030-10 Tabletop (-TT1)Dimensions 20
Figure 2-8: QNP3-100XYAZ-100-10 Tabletop (-TT1)Dimensions 20
Figure 2-9: QNP3-150XYAZ-200-20 Tabletop (-TT1)Dimensions 20
Figure 2-10: Mounting Hole Locations 22
Figure 2-11: Mounting Hole Locations (Tabletop) 25
Figure 3-1: Piezo Actuator Wiring 30
Figure 3-2: Machine Direction 32
Figure C-1: Strain (displacement) behavior of a ferroelectric material like PZT with an applied electric
field driven to its excitation limits 44
Figure C-2: Typical hysteresis curve of a piezoelectric stack actuator operating from -30V to +150V 45
Figure C-3: Force vs. displacement output of a piezo actuator at various applied voltages 46
Figure C-4: Displacement of a piezo stage or actuator with a constant external load 47
Figure C-5: Displacement of a piezo stage or actuator driving against an external spring of stiffness
ke 48
Figure C-6: Estimated power dissipated as a function of frequency and applied voltage for a typical
piezo actuator with a 4 µF capacitance 51
Figure C-7: Raw measurement results from an accuracy and linearity test of a 100 μm piezo stage 53
Figure C-8: Example accuracy error calculated from the measurement data shown in Figure 1-7 54
Figure C-9: Illustration showing how linearity is calculated based on measurement data taken from a
100 μm piezo nanopositioning stage 54
Figure C-10: Maximum sinusoidal peak-peak voltage of a given amplifier with various piezo stack
capacitances 58
Figure C-11: Voltage and current waveforms for the profile commanded in Example 1 59
Figure C-12: Voltage and current waveforms for the profile commanded in Example 2 60
www.aerotech.com 5

Table of Contents QNP3 Hardware Manual
List of Tables
Table 1-1: Model Numbers and Options 9
Table 1-2: Minimum Acceptable Environmental Specifications 11
Table 1-3: QNP3 Series Specifications 13
Table 2-1: Stage to Mounting Surface Hardware 21
Table 2-2: Customer Mounting Features 24
Table 3-1: Piezo Connector Pin Description 29
Table 3-2: Electrical Specifications 31
Table 4-1: Troubleshooting 37
6 www.aerotech.com

QNP3 Hardware Manual Table of Contents
Safety Procedures and Warnings
Read this manual in its entirety before installing, operating, or servicing this product. If you do not understand
the information contained herein, contact an Aerotech representative before proceeding. Strictly adhere to
the statements given in this section and other handling, use, and operational information given throughout
the manual to avoid injury to you and damage to the equipment.
The following statements apply wherever the Warning or Danger symbol appears within this manual. Failure
to observe these precautions could result in serious injury to those individuals performing the procedures
and/or damage to the equipment.
D A N G E R : This product contains potentially lethal voltages. To reduce the possibility of
electrical shock, bodily injury, or death the following precautions must be followed.
1. Access to the QNP3 and component parts must be restricted while connected to a power
source.
2. Do not connect or disconnect any electrical components or connecting cables while
connected to a power source.
3. Disconnect electrical power before servicing equipment.
4. All components must be properly grounded in accordance with local electrical safety
requirements.
5. Operator safeguarding requirements must be addressed during final integration of the
product.
W A R N I N G : To minimize the possibility of electrical shock, bodily injury or death the
following precautions must be followed.
1. Cables can pose a tripping hazard. Securely mount and position all system cables to avoid
potential hazards.
2. Do not expose this product to environments or conditions outside of the listed
specifications. Exceeding environmental or operating specifications can cause damage to
the equipment.
3. The QNP3 stage must be mounted securely. Improper mounting can result in injury and
damage to the equipment.
4. Use care when moving the QNP3 stage. Lifting or transporting the QNP3 stage improperly
can result in injury or damage to the QNP3.
5. This product is intended for light industrial manufacturing or laboratory use. Use of this
product for unintended applications can result in injury and damage to the equipment.
6. If the product is used in a manner not specified by the manufacturer, the protection
provided by the product can be impaired and result in damage, shock, injury, or death.
7. Do not operate the QNP3 at higher voltages or different polarity than stated in Section 3.3.
to prevent damage to the stage.
8. Do not disassemble the QNP3. Disassembly could expose the user to high voltages.
Disassembly will result in a loss of linearity and void the warranty.
9. Do not exceed the maximum push/pull forces stated in Section 2.4. to avoid damaging the
piezo drives or misadjusting the positioner.
10. Do not drop the QNP3 or subject it to any mechanical shock to avoid damaging sensitive
internal components.
11. Operators must be trained before operating this equipment.
12. All service and maintenance must be performed by qualified personnel.
www.aerotech.com 7

Table of Contents QNP3 Hardware Manual
EU Declaration of Conformity
Manufacturer
Aerotech, Inc.
Address
101 Zeta Drive
Pittsburgh, PA 15238-2811
USA
Product
QNP3
Model/Types
All
This is to certify that the aforementioned product is in accordance with the applicable requirements of the
following Directive(s):
2014/35/EU Low Voltage Directive
2011/65/EU RoHS2 Directive
and has been designed to be in conformity with the applicable requirements of the following Standard(s)
when installed and used in accordance with the manufacturer’s supplied installation instructions.
EN 61010-1:2010 Safety Requirements for Electrical Equipment
Authorized Representative:
Simon Smith, European Director
Address:
Aerotech Ltd
The Old Brick Kiln, Ramsdell, Tadley
Hampshire RG26 5PR
UK
Name
/ Alex Weibel
Position
Engineer Verifying Compliance
Location
Pittsburgh, PA
Date
10/22/2018
8 www.aerotech.com

QNP3 Hardware Manual Overview
Chapter 1: Overview
N O T E : Aerotech continually improves its product offerings; listed options may be superseded at any
time. All drawings and illustrations are for reference only and were complete and accurate as of this
manual’s release. Refer to www.aerotech.com for the most up-to-date information.
Table 1-1: Model Numbers and Options
QNP3 Series Three-Axis, Parallel Kinematic, XYZ Piezo Nanopositioning Stage
QNP3-100XYAZ-030-10 30 μm x 30 μm x 10 μm closed-loop travel
QNP3-100XYAZ-100-10 100 μm x 100 μm x 10 μm closed-loop travel
QNP3-150XYAZ-200-20 200 μm x 200 μm x 20 μm closed-loop travel
Feedback (Optional)
-C Capacitance sensor feedback
Mounting Plate (Optional)
-MP Mounting plate for English and metric optical breadboard tables
Tabletop (Optional)
-TT1 Solid metric tabletop, covers aperture
www.aerotech.com Chapter 1 9

Overview QNP3 Hardware Manual
1.1. Understanding Basic QNP3Stage Operation
QNP3 stages have many operating characteristics that are unique to piezo actuator based systems. This
section describes some of the unique aspects of QNP3 stages. It is strongly recommended that all QNP3
stage users read the “Appendix C: Piezo Engineering Tutorial” (or at www.aerotech.com) for more detailed
information on operation principles and nomenclature.
Expansion Device
The piezo actuator in each QNP3 stage is an expansion device that expands proportionately with applied
voltage. This has some practical implications for stage use. When de-energized (0 V), the actuator will
compress and the stage will sit at one end of travel. When energized with positive voltage the actuator will
expand and the stage will move toward the opposite end of travel. When energized with negative voltage the
actuator will shrink and the stage will move further away from the center relative to the de-energized position.
Each QNP3 stage is marked with arrows that indicate the direction of expansion (i.e. the positive voltage
direction).
Figure 1-1: Single-Axis Stage Travel and Voltage Relationship
Open-Loop vs Closed-Loop Travel
All QNP3 stages with feedback (-C option) have an open-loop (OL) and closed-loop (CL) travel range (refer to
Section 1.4.). This refers to whether the stage is using feedback control (CL) or not (OL). QNP3 stages
purchased without feedback have an open-loop travel range only. The open-loop range is the travel that can
be achieved over the entire -30 to 150 V operation range. When the stage is in closed-loop (servo on), it
requires over-travel to account for a variety of operational conditions, so the closed-loop range is smaller.
Refer to Figure 1-1 for an illustration of QNP3 stage travel ranges. QNP3 stages with the -C option are
calibrated at the factory for optimal linearity over the specified closed-loop range only.
Unless otherwise specified, QNP3 stages configured at Aerotech default to open-loop operation and must be
commanded to enter closed-loop mode. By default, all open-loop motion commands control voltage and all
closed-loop motion commands control position. Refer to controller documentation for information on how to
turn the servo on and off and adjust default settings.
10 Chapter 1 www.aerotech.com

QNP3 Hardware Manual Overview
1.2. Environmental Specifications
W A R N I N G : Do not expose this product to environments or conditions outside of the listed
specifications. Exceeding environmental or operating specifications can cause damage to the
equipment.
The QNP3 stages are true nanopositioners. To achieve superior performance at the nanometer level, a very
well controlled environment is essential. Table 1-2 describes the minimally acceptable environmental
specifications for normal stage operation. Better control of the environment will yield better system
performance. Contact Aerotech for more information regarding your specific application and environment.
Humid environments are more detrimental to piezo actuators when they are held at high voltages for long
periods of time. For static positioning applications it is recommended that QNP3 stages be configured to
keep average voltage as low as possible to achieve maximum lifetime from the internal piezo actuator.
Operation in gaseous environments other than air may affect the rated operating voltage of the QNP3 stage.
Consult the factory for details.
W A R N I N G : Using the QNP3 in environments with relative humidity greater than 60% may
require a reduction in travel and max voltage to ensure a long operating life.
Table 1-2: Minimum Acceptable Environmental Specifications
Ambient
Temperature
The optimal operating temperature is 20° C ±2° C (68° F ±4° F). If at any time the
operating temperature deviates from 20° C degradation in performance could occur.
Storage: 0° to 40° C (32° to 104° F) in original shipping packaging
Humidity
Operating: <60% RH
Storage: <40% RH, non-condensing in original packaging. The stage should be
packaged with desiccant if it is to be stored for an extended time.
Altitude Operating: 0 m to 2,000 m (0 ft to 6,562 ft) above sea level
Vibration Floor or acoustic vibration will affect system performance. A quiet environment,
isolated from ground vibration is recommended for optimum performance.
Protection
Rating
The QNP3 stage is designed to operate in laboratories and clean production
environments. Operation in heavy dust environments could lead to contamination
inside the stage and degrade performance.
Use Indoor use only
www.aerotech.com Chapter 1 11

Overview QNP3 Hardware Manual
1.3. Linearity and Temperature Effects
Linearity is measured and calibrated for every QNP3 stage purchased with the -C feedback configuration.
Unless otherwise specified, it is measured 15 mm above the center of the tabletop with the stage mounted in
a standard horizontal position. The surface that the stage is mounted to must meet or exceed the
requirements in Section 2.3. to maintain the linearity measured at the factory.
Aerotech products are designed for and built in a 20°C (68°F) environment. Extreme temperature changes
could cause a decrease in performance or permanent damage to the QNP3. At a minimum, the
environmental temperature must be controlled to within 0.25ºC per 24 hours to ensure the QNP3
specifications are repeatable over an extended period of time. The severity of temperature effects on all
specifications depends on many different environmental conditions, including how the QNP3 is mounted.
Contact the factory for more details.
The Z-axis of the QNP3 is sensitive to thermal expansion because of its relatively small open loop travel (±1
µm). Therefore, the physical travel range of the stage will shift relative to the sensor feedback range as a
function of stage temperature. If the temperature of the stage changes by more than ±3 °C from the
temperature at which it was configured, the entire configured closed loop travel range will no longer be
achievable.
If the entire closed loop Z-axis travel cannot be achieved, adjust the Absolute Feedback Offset of the Z-Axis
in software to re-center the configured travel in the working range. Refer to Aerotech controller
documentation for more information on how to adjust the Absolute Feedback Offset. The working
temperature of the stage must be controlled to ±3 °C to ensure the entire closed loop range will be available
for the duration of a continuous process.
Configure the Absolute Feedback Offset in software as described in the Aerotech controller documentation
as part of the initial startup procedure for the QNP3 to ensure the working range of the Z-axis is adjusted to
the ambient temperature in its operating environment.
N O T E : QNP3 stages with feedback are paired with their drives and extension cables, if purchased, at
the factory. If a stage with feedback is operated with different drives, amplifier slots, or extension cable
lengths than it was initially paired with, the QNP3 may not maintain its specified linearity. New drive and
stage combinations can be re-qualified at Aerotech to maintain optimum performance.
12 Chapter 1 www.aerotech.com

QNP3 Hardware Manual Overview
1.4. Basic Specifications
Table 1-3: QNP3 Series Specifications
Specification(1) 100XYAZ-030-10 100XYAZ-100-10 150XYAZ-200-20
Closed-Loop Travel (X x Y x Z) 100 µm x 100 µm x
30 µm
100 µm x 100 µm x
10 µm
200 µm x 200 µm x
20 µm
Open-Loop Travel, -30 to +150 V (2) 36 µm x 36 µm x
12 µm
120 µm x 120 µm x
12 µm
240 µm x 240 µm x
25 µm
Resolution (3)
Closed-Loop
XY 0.1 nm 0.30 nm 0.40 nm
Z 0.15 nm 0.15 nm 0.15 nm
Resolution (3)
Open-Loop
XY 0.03 nm 0.15 nm 0.20 nm
Z 0.05 nm 0.05 nm 0.1 nm
Linearity (4, 5) XY 0.02% 0.01% 0.01%
Z 0.04% 0.02% 0.02%
Bidirectional Repeatability(6) XY 4 nm 2 nm 2 nm
Z 3 nm 1 nm 2 nm
Straightness XY <25 nm <10 nm 10 nm
Z <50 nm <20 nm 40 nm
2DFlatness (Over Full XYTravel) <10 nm <5 nm <10 nm
Pitch XY 10 µrad (2.1 arcsec) 2 µrad (0.4 arcsec) 2 µrad (0.4 arcsec)
Z 6 µrad (1.2 arcsec) 6 µrad (1.2 arcsec) 6 µrad (1.2 arcsec)
Yaw XY 5 µrad (1 arcsec) 10 µrad (2.1 arcsec) 20 µrad (4 arcsec)
Z 5 µrad (1 arcsec) 5 µrad (1 arcsec) 6 µrad (1.2 arcsec)
Stiffness (7)
(in direction of motion)
XY 10 N/µm 1.9 N/µm 1.3 N/µm
Z 25 N/µm 13 N/µm 8.7 N/µm
Unloaded Resonance of
Frequency (7)
XY 1850 Hz 490 Hz 330 Hz
Z 2200 Hz 1425 Hz 910 Hz
Resonant Frequency (7)
(200 gram load)
XY 950 Hz 350 Hz 260 Hz
Z 1390 Hz 910 Hz 670 Hz
Maximum Payload (8) 1 kg 1 kg 3 kg
Maximum Acceleration (9)
(Unloaded)
XY 400 m/s2115 m/s235 m/s2
Z2000 m/s22000 m/s21000 m/s2
Moving Mass (Unloaded) XY 0.24 kg 0.21 kg 0.58 kg
Z 0.05 kg 0.05 kg 0.10 kg
Stage Mass 0.53 kg 0.56 kg 1.3 kg
Material Anodized Aluminum(10)
Mean Time Between Failure 30,000 Hours
1. Specifications are per axis unless specified.
2. Value ±10%
3. Refer to Section C.4.2 Resolution for a description of resolution.
4. Certified with each stage (closed-loop feedback models only).
5. Measured approximately 15 mm above the carriage by an external metrology device. Refer to Section C.4.1 Accuracy/Linearity
for description of linearity specifications.
6. Specified as a 1 sigma (standard deviation) value. Refer to Section C.4.3 Repeatability for description of bidirectional
repeatability.
7. Value ±20%
8. On-axis loading is listed.
9. Maximum acceleration listed is the stage mechanical limitation. Achievable acceleration is a function of amplifier selection and
move parameters.
10. External elements are anodized aluminum. Some internal components are stainless steel. Other materials upon request.
www.aerotech.com Chapter 1 13

Overview QNP3 Hardware Manual
1.5. Vacuum Operation
Standard QNP3 stages are not designed to minimize outgassing in a vacuum environment. Aerotech can
specially prepare any of the QNP3 stages for a wide range of vacuum environments. When using a QNP3
stage that has been specially prepared for vacuum environments several additional precautions must be
taken to ensure proper operation.
1. The stage will be specially cleaned and sealed in a polyethylene bag at the factory. Do not remove the
stage from this bag until it is ready for use.
2. Only handle the stage in a clean environment using powder-free polyethylene gloves to prevent
contamination with oils and debris.
3. Use cleaned, vented, stainless steel fasteners when securing and mounting to the stage.
4. Piezo actuators cannot be operated at pressures from 10 to 10-2 Torr. The resistance of air dramatically
reduces in this range and voltage may arc across the piezo actuator and destroy it. Remove power from
the stage and disconnect it from its drive electronics during vacuum pump down operations to protect it
from damage.
5. Baking components at elevated temperatures before installation in a vacuum chamber can greatly
reduce initial outgassing from water vapor trapped in porous surfaces. QNP3 stages contain some heat
sensitive components. Bake out temperatures should not exceed 100° C to prevent damage. If higher
baking temperatures are required contact Aerotech to discuss the application. After bake out and
vacuum chamber pump down, the piezo actuator should be repoled, as described in Section 4.3.,
before beginning normal operation.
14 Chapter 1 www.aerotech.com

QNP3 Hardware Manual Mechanical Specifications and Installation
Chapter 2: Mechanical Specifications and Installation
W A R N I N G : QNP3 installation must be in accordance to instructions provided by this
manual and any accompanying documentation. Failure to follow these instructions could result
in injury or damage to the equipment.
2.1. Unpacking and Handling the Stage
N O T E : If any damage has occurred during shipping, report it immediately.
W A R N I N G : It is the customer's responsibility to safely and carefully lift the stage. Improper
handling could adversely affect the performance of the QNP3 stage.
lLift only by the base.
lDo not use the tabletop or cable as lifting points.
W A R N I N G : An unsecured QNP3 could be dragged off of a mounting surface by its
unsupported cable.
Carefully remove the QNP3 stagefrom its protective shipping container. Gently set the QNP3 stage on a
smooth, flat, and clean surface.
Before operating the QNP3 stage, it is important to let it stabilize at room temperature for at least 12 hours.
Allowing it to stabilize to room temperature will ensure that all of the alignments, preloads, and tolerances are
the same as they were when tested at Aerotech. Use compressed nitrogen or clean, dry, oil-less air to
remove any dust or debris that has collected during shipping.
Each QNP3 has labels listing the model number, system serial number, and axis identifier (typically X or Y).
The labels are located on the two D-connectors. These numbers contain information necessary for
maintaining or updating system hardware and software. Locate this label and record the information for later
reference. If any damage has occurred during shipping, report it immediately.
www.aerotech.com Chapter 2 15

Mechanical Specifications and Installation QNP3 Hardware Manual
2.2. Dimensions
N O T E : Aerotech continually improves its product offerings; listed options may be superseded at any
time. All drawings and illustrations are for reference only and were complete and accurate as of this
manual’s release. Refer to www.aerotech.com for the most up-to-date information.
Figure 2-1: QNP3-100XYAZ-030-10Dimensions
16 Chapter 2 www.aerotech.com

QNP3 Hardware Manual Mechanical Specifications and Installation
Figure 2-2: QNP3-100XYAZ-100-10Dimensions
www.aerotech.com Chapter 2 17

Mechanical Specifications and Installation QNP3 Hardware Manual
Figure 2-3: QNP3-150XYAZ-200-20Dimensions
18 Chapter 2 www.aerotech.com

QNP3 Hardware Manual Mechanical Specifications and Installation
Figure 2-4: QNP3-100XYAZ-030-10 Mounting Plate (-MP)Dimensions
Figure 2-5: QNP3-100XYAZ-100-10 Mounting Plate (-MP)Dimensions
Figure 2-6: QNP3-150XYAZ-200-20 Mounting Plate (-MP)Dimensions
www.aerotech.com Chapter 2 19

Mechanical Specifications and Installation QNP3 Hardware Manual
Figure 2-7: QNP3-100XYAZ-030-10 Tabletop (-TT1)Dimensions
Figure 2-8: QNP3-100XYAZ-100-10 Tabletop (-TT1)Dimensions
Figure 2-9: QNP3-150XYAZ-200-20 Tabletop (-TT1)Dimensions
20 Chapter 2 www.aerotech.com
This manual suits for next models
3
Table of contents
Other Aerotech Network Hardware manuals
Popular Network Hardware manuals by other brands

ADTRAN
ADTRAN NetVanta 1760-12F quick start
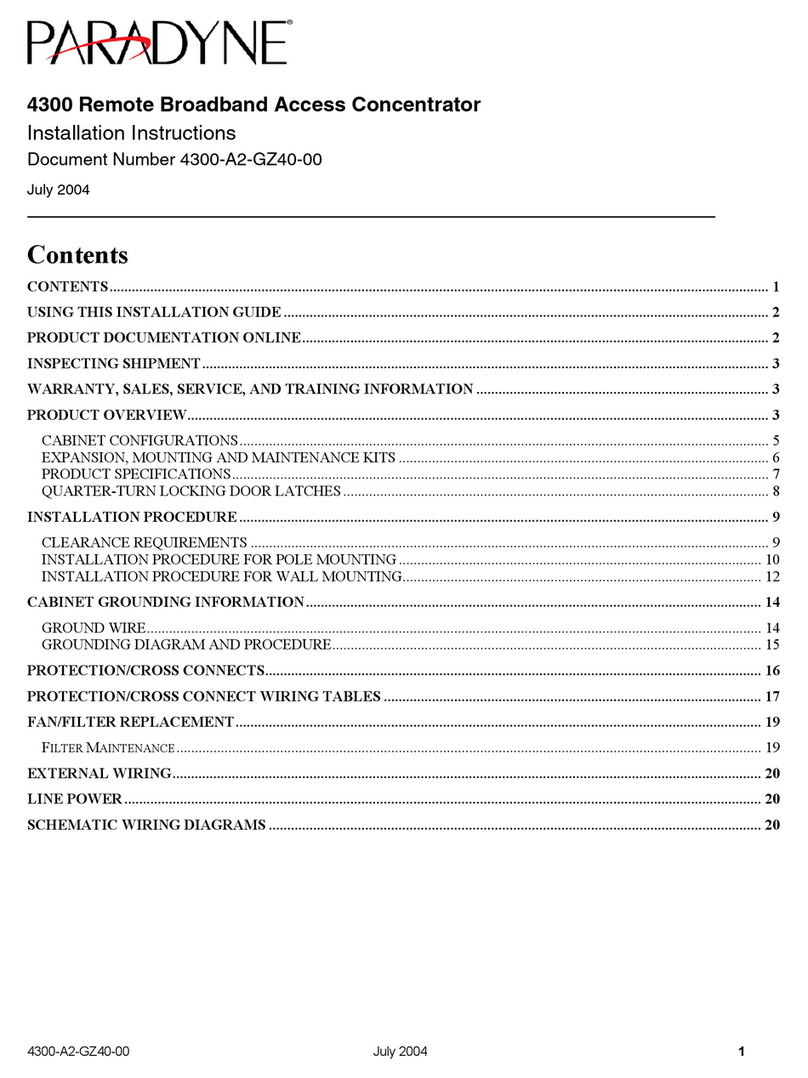
Paradyne
Paradyne 4300 installation instructions
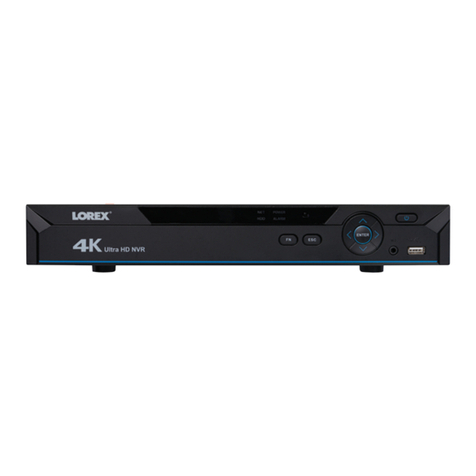
Lorex
Lorex LNR6100X Series Quick connection guide
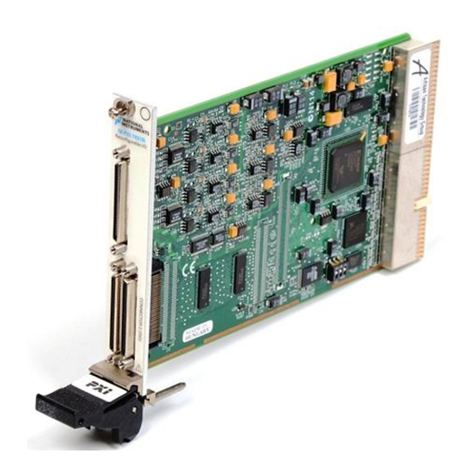
National Instruments
National Instruments NI PXI-7831R user manual

Siemens
Siemens Rider 11, Rider 13 H,Rider 11 Bio Workshop manual
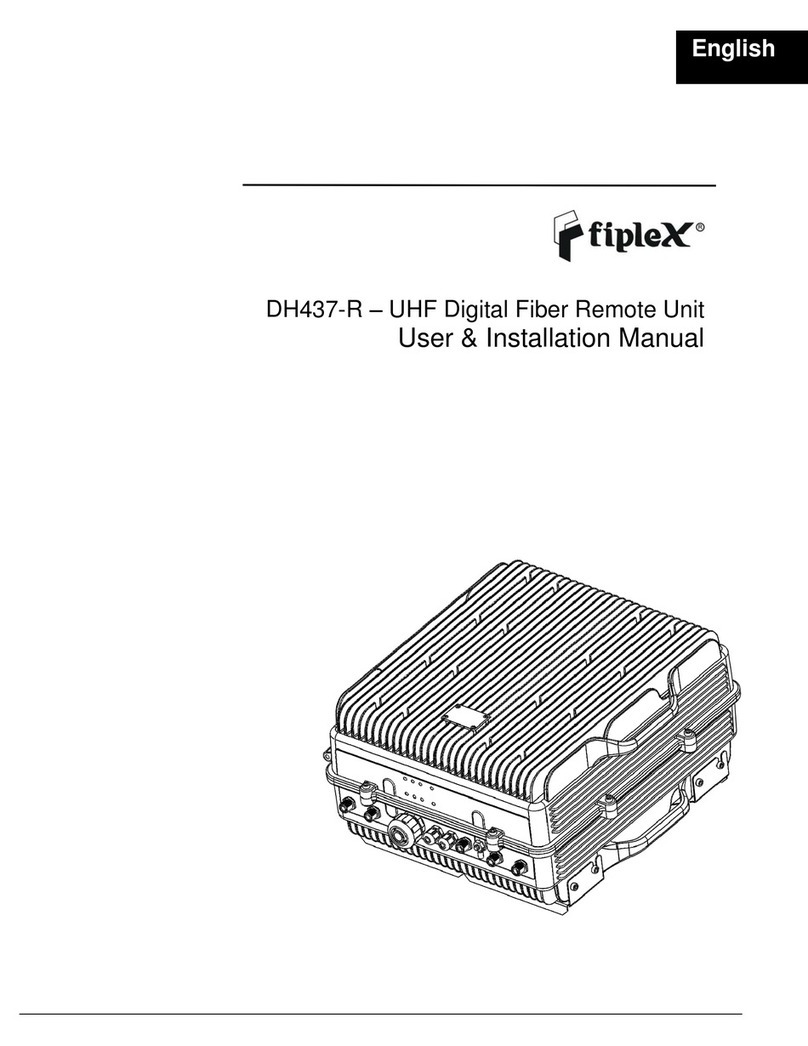
Fiplex
Fiplex DH437-R User & installation manual
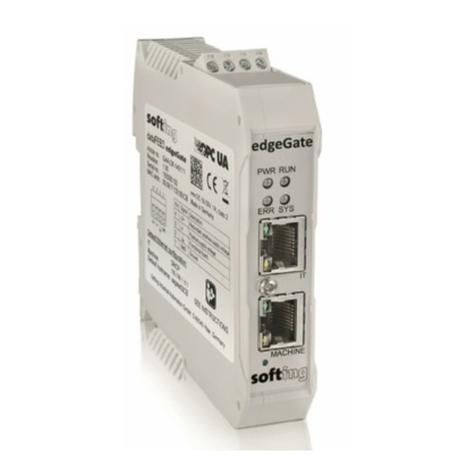
Softing
Softing dataFEED Series user manual
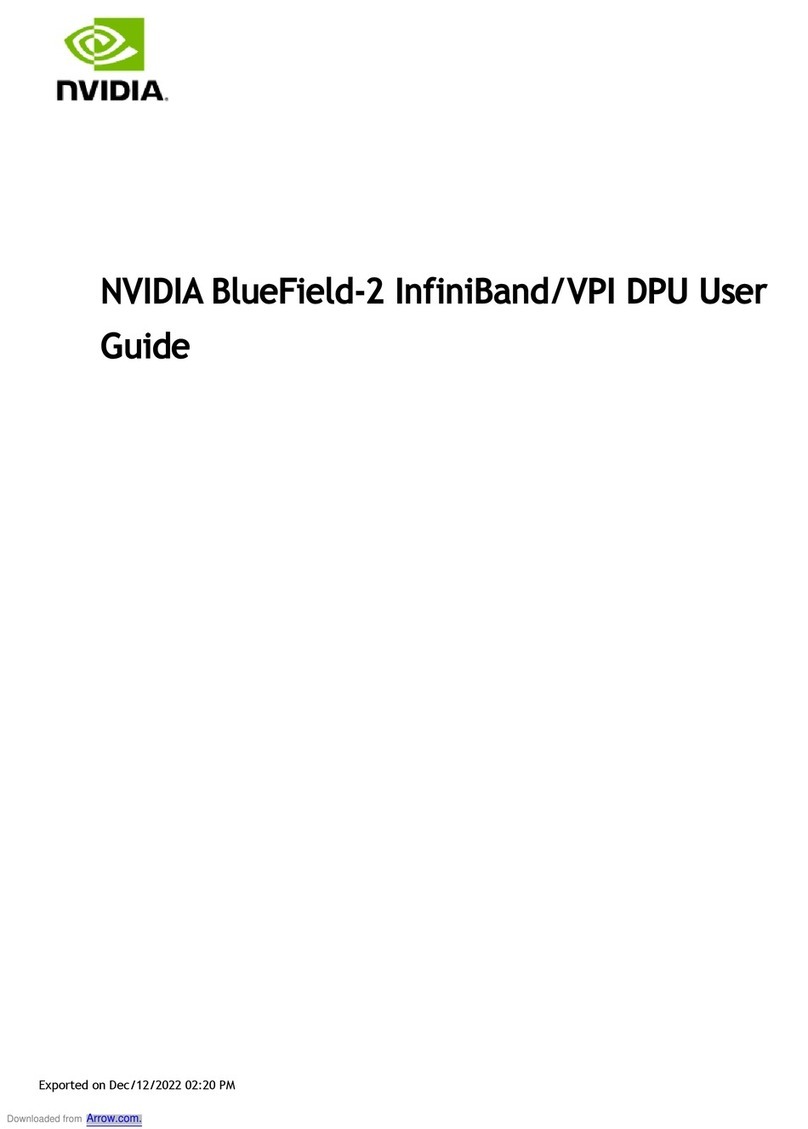
Nvidia
Nvidia BlueField-2 InfiniBand/VPI DPU user guide
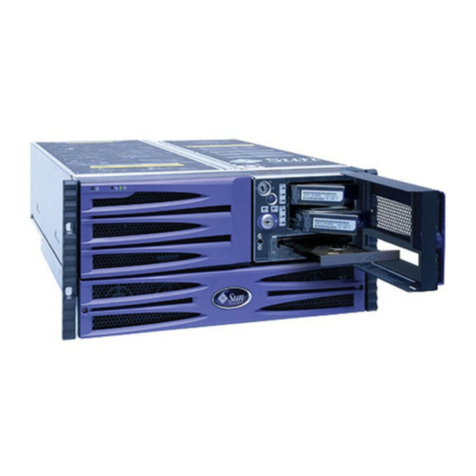
Sun Microsystems
Sun Microsystems StorEdge 3000 Series Installation, operation and service manual
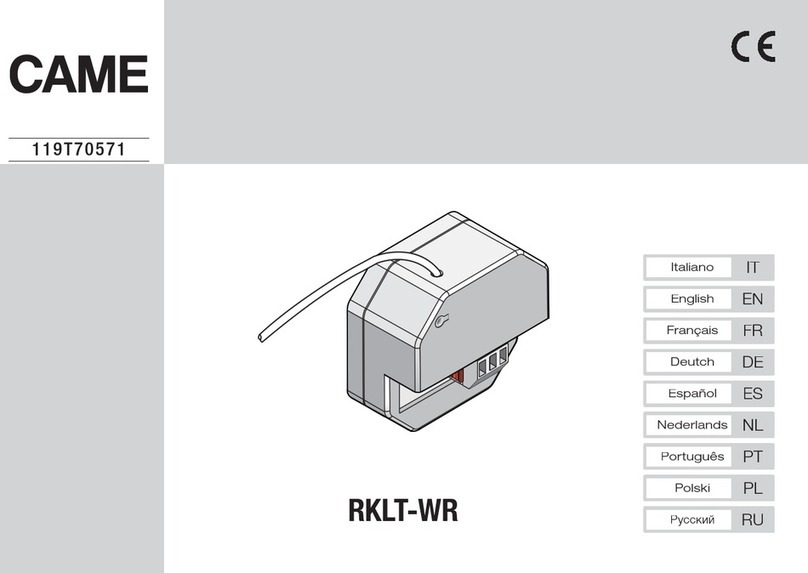
CAME
CAME RKLT-WR manual
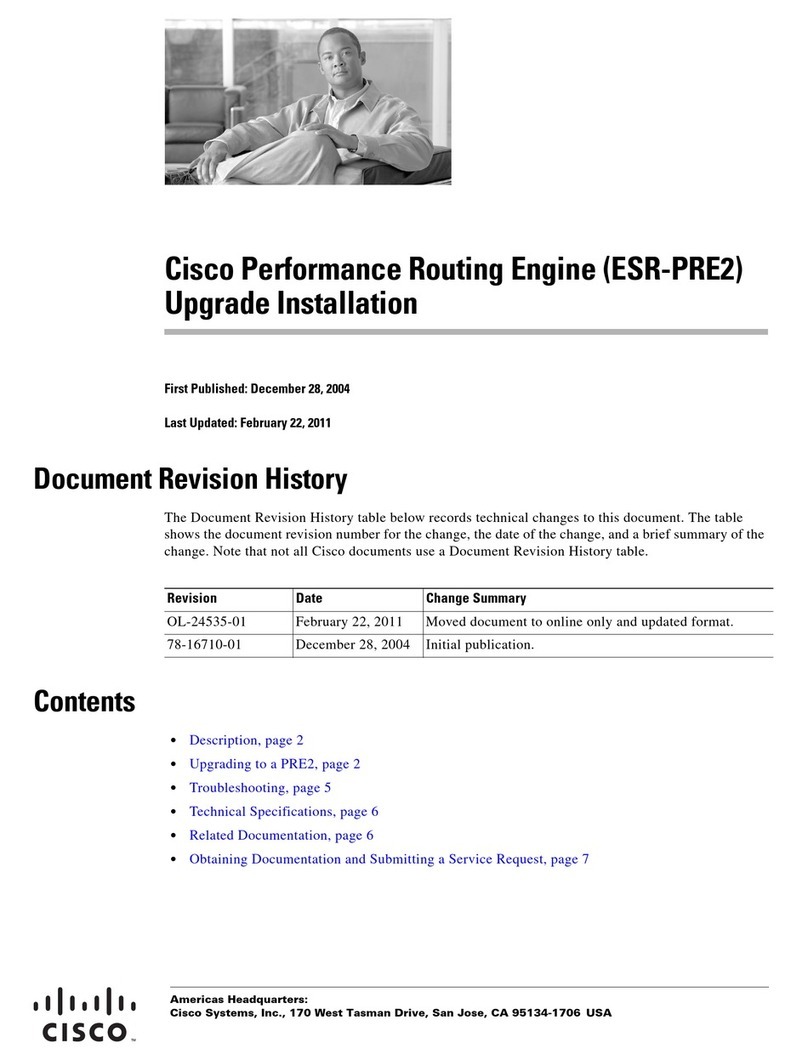
Cisco
Cisco ESR-PRE2 Upgrade Installation Guide
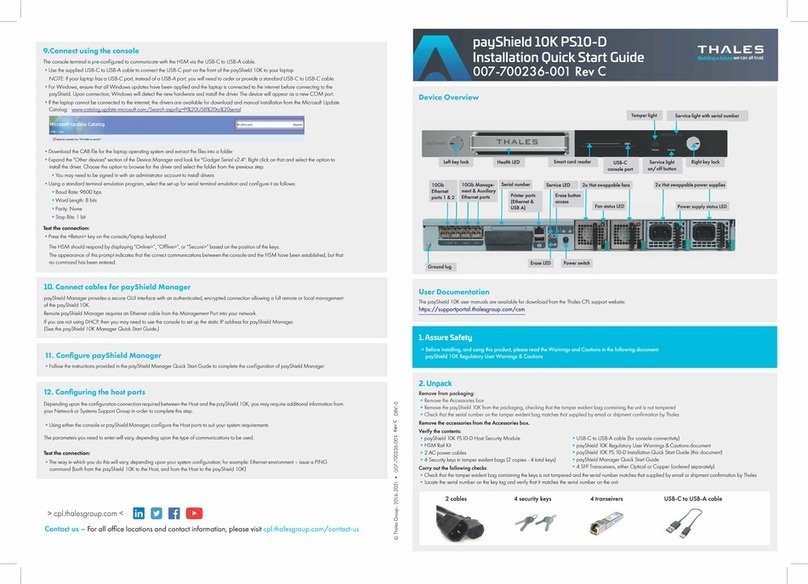
Thales
Thales payShield 10K PS10-D quick start guide