Agilebot GBT-S6A Series User manual

Product Manual
Mechanical Manual for GBT-S6A Series Robots

Product Manual
Mechanical Manual for GBT-S6A Series Robots
V1.2
Copyright, 2022 Agilebot Robotics Co., Ltd. All rights reserved!

Mechanical Manual for GBT-S6A Series Robots
Mechanical Manual for GBT-S6A Series Robots 3 / 49
The information in this Manual must not be considered as a commitment of Agilebot and may be
changed without prior notice. Agilebot assumes no responsibility for errors (if any) in this Manual.
Except as expressly specified in this Manual, nothing in this Manual shall be construed as any warranty
or guarantee made by Agilebot for personal loss, property damage or specific applicability.
Agilebot assumes no responsibility for any accidents or indirect injuries caused by the use of this
Manual or the product described therein.
This Manual and any parts thereof must not be reproduced or duplicated without written permission
from Agilebot.
Additional copies of this Manual may be obtained from Agilebot.
The original language of this Publication is Chinese.
International standard units are adopted in all publications. GB means Chinese national standard.
© Copyright, 2022 Agilebot Robotics Co., Ltd. All rights reserved!
Agilebot Robotics Co., Ltd.
Shanghai, China

Mechanical Manual for GBT-S6A Series Robots
Mechanical Manual for GBT-S6A Series Robots 4 / 49
Revision
Ver.
Date
Status
V1.0
Feb 25, 2023
Canceled
V1.1
Apr 3, 2023
Canceled
V1.2
Jul 6, 2023
Release

Mechanical Manual for GBT-S6A Series Robots
Mechanical Manual for GBT-S6A Series Robots 5 / 49
Table of Contents
Safety instructions................................................................................................................................6
1Handling and mounting .............................................................................................................12
1.1 Handling...............................................................................................................................12
1.2 Mounting..............................................................................................................................14
2Connection to controller............................................................................................................18
2.1 Connection to controller.......................................................................................................18
3Basic specification.....................................................................................................................19
3.1 Composition of robot............................................................................................................19
3.2 Diagram for overall dimensions and action range.................................................................21
3.3 Origin position and range of motion (ROM) ..........................................................................24
3.4 Wrist payload conditions ......................................................................................................25
4Mount the device onto the robot...............................................................................................26
4.1 Mount the end-effector to the front end of the wrist...............................................................26
4.2 Mounting surface..................................................................................................................27
4.3 About payload setting...........................................................................................................28
5Cabling and piping to end-effector ...........................................................................................31
5.1 Air pipe and electrical interfaces...........................................................................................32
6Maintenance and repair .............................................................................................................33
6.1 Maintenance and repair contents .........................................................................................34
6.2 Key points............................................................................................................................37
6.3 Repair..................................................................................................................................38
7Zero calibration method.............................................................................................................40
7.1 Summary .............................................................................................................................40
7.2 General calibration method ..................................................................................................41
7.3 Zero encoded data direct write.............................................................................................42
7.4 Confirmation of zero calibration results.................................................................................43
8Resolution of common faults ....................................................................................................44
Appendice............................................................................................................................................47
A. Regular Maintenance Sheet..............................................................................................................47
B. List of Bolt Strengths and Tightening Torques ...................................................................................48

Mechanical Manual for GBT-S6A Series Robots
Mechanical Manual for GBT-S6A Series Robots 6 / 49
Safety instructions
It is necessary to read and understand the contents described in this chapter before using robots.
In this Manual, the robot system refers to an integrated system integrating the industrial robot and its
controller, teach pendant, cables, software and other accessories. So, it is required to fully consider the
safety precautions of the user and the system.
Nobody is allowed to modify the industrial robot without authorization from Shanghai Agilebot Robotics
Co., Ltd. Shanghai Agilebot Robotics Co., Ltd. shall assume no responsibility for any damage to the
industrial robot or its components due to the use of any other components (software, tools, etc.) not
provided by Agilebot.
Shanghai Agilebot Robotics Co., Ltd. Assumes no responsibility for any consequences caused by
misuse of the industrial robot. The misuse includes:
➢Use the robot beyond the specified parameter range
➢Use it as a carrier for humans or animals
➢Use it as a climbing tool
➢Use it in explosive environments
➢Use it without safety protection
Besides safety precautions in this chapter, this Manual contains other safety instructions, which must
be followed as well.

Mechanical Manual for GBT-S6A Series Robots
Mechanical Manual for GBT-S6A Series Robots 7 / 49
Definition of user
The operators are defined as follows:
➢Operator
Perform power-on/off operation on the robot.
Start the robot program from the panel board.
➢Debugging Engineer
Operate the robot.
Perform teaching and programming debugging of the robot within the safety fence.
➢Maintenance Engineer
Operate the robot.
Perform teaching of the robot within the safety fence.
Carry out maintenance (repair, adjustment, replacement) operations on the robot.
The “Operator” is not allowed to enter the safety fence.
The "Debugging Engineer" and "Maintenance Engineer" can carry out operations within the safety
fence.
The operations within the safety fence include handling, setting, teaching, adjustment, maintenance, etc.
To carry out the operations within the safety fence, it is necessary to receive professional training on
the robot.
When operating, programming and maintaining the robot, the operator, programmer and maintenance
engineer must give a safety warning and wear at least the following protective articles.
➢Work clothes suitable for operations
➢Safety shoes
➢Safety helmets

Mechanical Manual for GBT-S6A Series Robots
Mechanical Manual for GBT-S6A Series Robots 8 / 49
Definition of safety records
This Manual includes safety warnings to ensure personal safety of the users and avoid any damage to
the machine tool and describes them with "Danger" and "Warning" in the main text based on their
importance in safety.
In addition, relevant supplementary explanations are described as "Caution".
Before use, the user must thoroughly read the precautions described in "Danger", "Warning" and
"Caution”.
Identification
Definition
Danger
It indicates dangerous situations possibly resulting in serious injury or death to
the user during incorrect operation.
Warning
It indicates dangerous situations possibly resulting in mild or moderate
personal injury or property damage during incorrect operation.
Caution
It provides supplementary explanations outside the scope of danger or
warning.
Please read this Manual carefully and keep it secure for easy reference at any time.

Mechanical Manual for GBT-S6A Series Robots
Mechanical Manual for GBT-S6A Series Robots 9 / 49
Steps for robot axis operation in emergency and abnormal situations
In emergency and abnormal situations where a person is trapped or surrounded by the robot, it is
required to immediately cut off the power supply to the robot controller, directly move the robot arm and
change its posture to help the operator get out of danger. When the robot controller is powered on,
press the Axis 3 brake release button as shown in the figure to release the brake. If the Axis 3 brake
cannot be released while the robot controller is powered on, open the outer cover and loosen the
mounting bolts of the Axis 3 unit to release the belt from the belt drive.
Warning
If the belt is directly disengaged, the Axis 3 may fall, possibly causing injury. Please take appropriate
measures before releasing belt engagement, e.g. supporting the Axis 3 with a block.
Caution
Please contact our technician to know about the recovery of belt tensioning.
Axis 3 brake release
button

Mechanical Manual for GBT-S6A Series Robots
Mechanical Manual for GBT-S6A Series Robots 10 / 49
Safety warning label
Both the robot and the controller bear several safety and information labels, which contain important
information related to the product. This information is very useful for all persons operating the robot
system, e.g. during mounting, maintenance or operation.
The safety labels are only graphical and applicable to all languages.
Caution
It is required to observe the safety and health signs on the product label. In addition, it is also necessary
to comply with the supplementary safety information provided by the system builder or integrator.
Sign
Description
An electric shock may occur if the internally energized parts of the
controller are touched when powered on.
Operation against the instructions may result in an accident of injury
and/or product damage. This is a warning message applicable to
certain functional requirements.
Grounding sign of controller
Electric shock
Keep your hand away from moving parts, otherwise your hand or
fingers may get stuck between the axis and the cover.
The robots equipped with telescopic covers do not pose the risk of
pinching hands or fingers. Therefore, they do not have this label.

Mechanical Manual for GBT-S6A Series Robots
Mechanical Manual for GBT-S6A Series Robots 11 / 49
Sign
Description
Never enter the work area while the robot is moving. Otherwise, the
robot may collide with the operator. This is very dangerous and may
cause serious safety issues.
Beware of burns due to high temperature.
Handling and hoisting
Beware of collision in the work area.

Mechanical Manual for GBT-S6A Series Robots
Mechanical Manual for GBT-S6A Series Robots 12 / 49
1 Handling and mounting
1.1 Handling
During transportation and handling, ensure that the robot is fixed securely and kept at the transportation
posture. Before the robot is lifted and transported, it is required to confirm that the screws and locating
pins fixing the robot have been removed. The robot can be handled for a short distance by two adults or
transported for a long distance by a forklift.
The weights of GBT-S6A series robots (excluding cables) are shown in the table below:
Robot model
Weight
GBT-S6A-500
16.5kg
GBT-S6A-600
17.3kg
GBT-S6A-700
18kg
Table 1.1
Caution
Properly choose the pickup points when manually handling the robot. Unsuitable pickup points may
easily result in finger pinching or other injuries as well as damage to the robot.
Caution
When a forklift is used, the robot must be securely fixed on the forklift and must not shake or move
relative to the forklift during transportation.

Mechanical Manual for GBT-S6A Series Robots
Mechanical Manual for GBT-S6A Series Robots 13 / 49
The transport posture of GBT-S6A robot is shown in Fig. 1.1:
Fig. 1.1 Transport Posture of GBT-S6A Robot
Axis No.
1
2
3
4
Angle/stroke
0°
150°
0mm
0°
Table 1.1 Axis Data at Transport Posture of GBT-S6A Robot
Human-powered transport location

Mechanical Manual for GBT-S6A Series Robots
Mechanical Manual for GBT-S6A Series Robots 14 / 49
1.2 Mounting
Parts required for mounting the robot:
S/N
Name
Number (PCS)
1
Hexagon socket screw M8 * 25 (GB/T 70.1-
2008[NOTE 1])
4
2
Spring washer M8
4
3
Flat washer M8 (GB/T 97.1-2002[NOTE 2])
4
4
Cylindrical pin φ6
2
The mounting dimensions are shown in Fig. 1.2:
Fig. 1.2 Mounting Dimensions of GBT-S6A Robot
Completely through
Through
Through
[NOTE]
1. GB/T 70.1-2008 Correspondence standard: ISO 4762:1997 Hexagon socket head cap screws
2. GB/T 97.1-2002 Correspondence standard: ISO 7089:2000 Plain washers –Normal series - product grade A

Mechanical Manual for GBT-S6A Series Robots
Mechanical Manual for GBT-S6A Series Robots 15 / 49
Mounting requirements:
Mounting base
required
Maximum surface roughness
0.5mm
Maximum tilt angle
0.5°
Minimum resonance frequency
30Hz
Storage
conditions
Minimum environmental temperature
-20℃
Maximum environmental temperature
50℃
Maximum humidity
90% RH (non-condensation)
Operating
conditions
Minimum temperature
5℃
Maximum temperature
40℃
Maximum humidity
80% RH (non-condensation)
Environmental
conditions
Indoors; avoid direct sunlight, dust, salt, metal powder or other pollutants; stay away
from water, flammable or other highly corrosive liquids and gases; avoid shock and
vibration.

Mechanical Manual for GBT-S6A Series Robots
Mechanical Manual for GBT-S6A Series Robots 16 / 49
Warning
Those designing or manufacturing the robot system with this product must read this Manual to
understand basic precautions before work. Otherwise, it is very dangerous and may result in serious
injury or significant damage.
Please use the robot system under the environmental conditions recorded in the Manual. This product
is designed and manufactured firstly for the purpose of typical indoor environments. Operation in an
environment unsatisfying the environmental conditions may not only shorten the service life, but also
cause serious safety issues.
Please use the robot system within the specified specifications. Operation beyond the specifications
may not only shorten the service life, but also cause serious safety issues.
When mounting the robot system, you must wear at least the following protective devices.
- Work clothes suitable for operations
- Safety helmets
- Protective shoes
Be sure to install an emergency stop device so that the operator can immediately stop the system.
Otherwise, it is very dangerous and may cause serious injury or significant damage to the robot system.
Ensure that the emergency stop switch of the teach pendant connected to the TP port can operate
properly when safety doors and other emergency stop or safety input signals are connected to the
emergency stop circuit connector.
Mount the robot in a position with sufficient space and ensure that the surrounding area of the end
fixture or the workpiece does not collide with walls or safety guards when the robot moves the
workpiece and is extending. A collision (if any) may cause serious personal injury or significant
equipment damage.
Fix the robot securely before power-on or operation. Otherwise, it is very dangerous - the robot may fall,
resulting in serious injury or significant damage to the robotic arm system.
Before mounting and operation, please ensure that all components of the robot are in place and free
from external defects. Missing or defective components may lead to improper operation of the robot. It
is very dangerous and may cause serious injury or significant damage.
Never use the robot near the devices generating powerful electromagnetic forces. Otherwise, it may
cause malfunction or defect of the robot.
Never use the robot in places subject to electromagnetic interference, electrostatic discharge or radio
frequency interference risk. Otherwise, it may cause malfunction of the robot.
Never use the robot in places exposed to flammable gases, dust, gasoline or solvents that may explode
or catch fire. Otherwise, it may cause serious accidents or fires involving injury (including death).
Never place your hands or fingers near the moving parts of the robot. Otherwise, it may cause hand
pinching and other injuries.
Never mount the robot controller upside down or tilted.

Mechanical Manual for GBT-S6A Series Robots
Mechanical Manual for GBT-S6A Series Robots 17 / 49
Warning
For the power cable, make sure to use a power plug or disconnector. Never connect it directly to the
power supply in the factory.
Never open the controller or robot cover except during maintenance. It is very dangerous when the
controller cover is opened. Even if the main power is turned off, the internal high-voltage charging unit
may cause electric shock as well.
Before connecting or disconnecting the cable, ensure that the power supply of the robot system is cut
off. It is very dangerous to connect or disconnect the cable in the power-on state. It may lead to electric
shock or controller failure.
Ensure that the plug should be plugged into the factory socket by a qualified operator.
The device must always be properly grounded to avoid electric shock.
Be sure to use a leakage circuit breaker for the power supply of the controller. Otherwise, it may cause
electric shock or system malfunction.
Make sure to disconnect the power plug when opening the front cover of the controller. It is very
dangerous to touch the power terminal inside the controller during power-on. It may cause electric
shock or serious safety issues.
When mounting the robot, please ground it through the controller cable. Make sure to install the
controller and connect its cable. Improper grounding may lead to fire or electric shock hazards. Prevent
the connector from being impacted or loaded during cabling. Never forcefully pull the cable during
connection.
Please make sure to turn off the power of the controller and related equipment and pull up the warning
sign (e.g. no power-on) before wiring. It is very dangerous for wiring in the power-on state. It may lead
to electric shock or robot system malfunction.
When the brake release unit or external short-circuit connector is used: When connecting/replacing the
brake release unit or external short-circuit connector, please turn off the power of the controller and the
brake release unit. Installation/removal of the connector in the power-on state may cause electric
shock.
Do not touch the terminal. Otherwise, it may cause electric shock, product damage or malfunction.
Caution
The corresponding robot S/N is indicated on the controller label. Connect the controller and the robot
correctly. In case of a mistake in the connection relationship, not only the robot system may not function
properly, but also it may cause safety issues.
According to the rigidity of the mounting platform, vibration (resonance) may occur during operation. In
case of vibration, increase the rigidity of the platform or change the speed or acceleration and
deceleration settings.
Please confirm that the pins are not bent before the connector is connected. If the pins are bent during
connection, it may damage the connector or cause the robot system to malfunction.

Mechanical Manual for GBT-S6A Series Robots
Mechanical Manual for GBT-S6A Series Robots 18 / 49
2 Connection to controller
2.1 Connection to controller
The connecting cables between the robot and the controller include power cables and signal cables.
Please connect each cable to the connector on the back of the mounting base. Don't forget to ground
the controller.
Warning
Before connecting the power of the controller, please connect the robot and the controller with a ground
wire. Electric shock may occur if the ground wire is not connected.
Warning
The connection of cables must be performed after disconnecting the power.
Do not wind the excess part (over 10m) of the robot cable into a loop. Otherwise, it may cause a
significant increase in cable temperature during certain robot actions, resulting in adverse effects on
cable sleeve.
Fig. 2.1 Diagram for Connection between GBT-S6A Robot and Controller
Power and signal cables

Mechanical Manual for GBT-S6A Series Robots
Mechanical Manual for GBT-S6A Series Robots 19 / 49
3 Basic specification
3.1 Composition of robot
The GBT-S6A series robot is composed of a base, a large arm, a small arm, a screw and a pipeline
package. Totally, 4 servo motors can drive the movement of 4 joints to achieve different forms of motion.
The following figure shows various motion joints and forward motion direction of the robot.
Fig. 3.1 Diagram for Motor Locations of GBT-S6A Robot
Fig. 3.2 Various Motion Joints and Forward Motion Direction of GBT-S6A
Caution
Do not move Axis 1 and 2 while the ball screw splines are under stress. Otherwise, it may cause
damage.
Axis 1 motor
Axis 1 arm
Axis 3 motor
Axis 2 motor
Axis 4 motor
Axis 2 arm
Ball screw

Mechanical Manual for GBT-S6A Series Robots
Mechanical Manual for GBT-S6A Series Robots 20 / 49
Model
GBT-S6A-500
GBT-S6A-600
GBT-S6A-700
Basic specification
Axes
4
4
4
Maximum reach
500 mm
600 mm
700 mm
Payload
Rated
2kg
2kg
2kg
Maximum
6kg
6kg
6kg
Axis 4 Moment of Inertia
Rated
0.01 kgm2
0.01 kgm2
0.01 kgm2
Maximum
0.12 kgm2
0.12 kgm2
0.12 kgm2
Axis 3 Down Force
100 N
100 N
100 N
Mounting method
Countertop-
mounted
Countertop-
mounted
Countertop-
mounted
Motion parameters
Axis Motion Range
Axis 1
±132°
±132°
±132°
Axis 2
±150°
±150°
±150°
Axis 3
200 mm
200 mm
200 mm
Axis 4
±360°
±360°
±360°
Axis Maximum Speed
Axis 1+2
5830 mm/s
6800 mm/s
7100 mm/s
Axis 3
1100 mm/s
1100 mm/s
1100 mm/s
Axis 4
2000°/s
2000°/s
2000°/s
Position Repeatability*1
Axis 1+2
0.015 mm
0.015 mm
0.015 mm
Axis 3
0.01 mm
0.015 mm
0.015 mm
Axis 4
0.01°
0.01°
0.01°
Standard cycle time *2
0.41s
0.42s
0.42s
Fig. 3.3 Performance Parameter Table of GBT-S6A
Caution
1. Even when the robot is used within the specification range, certain action programs may shorten the
lifespan of the reducer or cause overheating alarms.
2. Sometimes, it is impossible to reach maximum speed of each axis at a short action distance.
3. Please use the robot system and the controller under the environmental conditions recorded in the
Manual. This product is designed and manufactured firstly for the purpose of typical indoor
environments. Operation in an environment unsatisfying the environmental conditions may not only
shorten the service life, but also cause serious safety issues.
4. Please consult our company for use in the environments with high/low temperature, vibration, dust,
high concentration of cutting oil, etc.
This manual suits for next models
3
Table of contents
Other Agilebot Robotics manuals
Popular Robotics manuals by other brands

Artec
Artec T.REX Assembly instructions

ABB
ABB 180 Comfort operating instructions
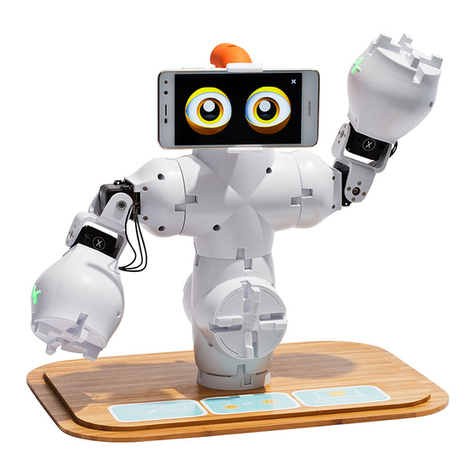
Share Robotics
Share Robotics Fable user guide
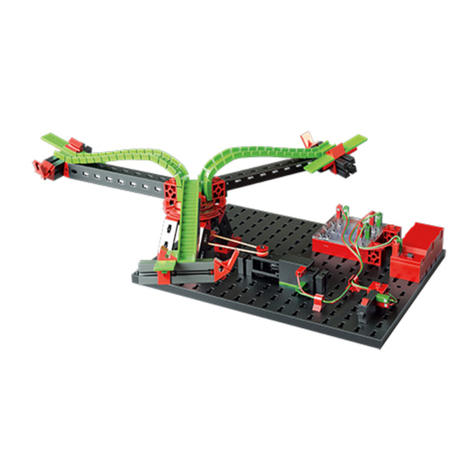
fischertechnik
fischertechnik Robotics BT Beginner Assembly instruction
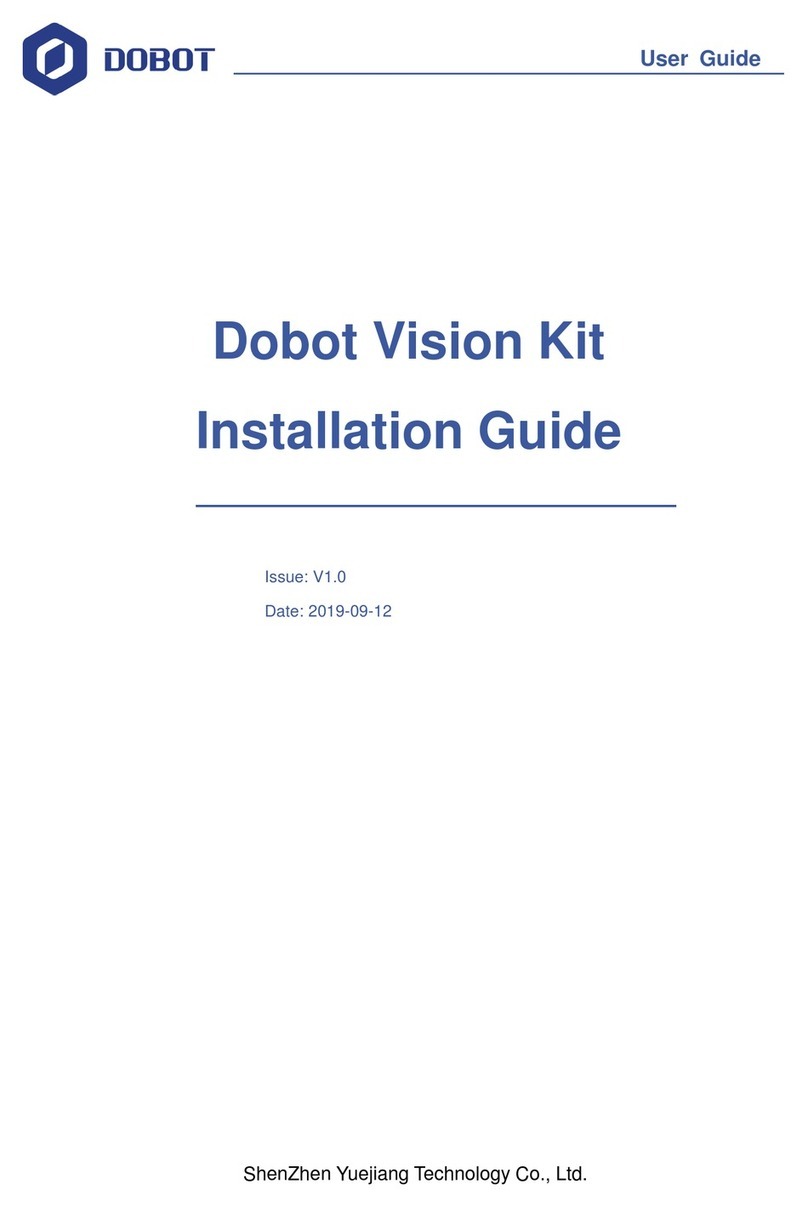
ShenZhen Yuejiang Technology
ShenZhen Yuejiang Technology Dobot Vision Kit installation guide
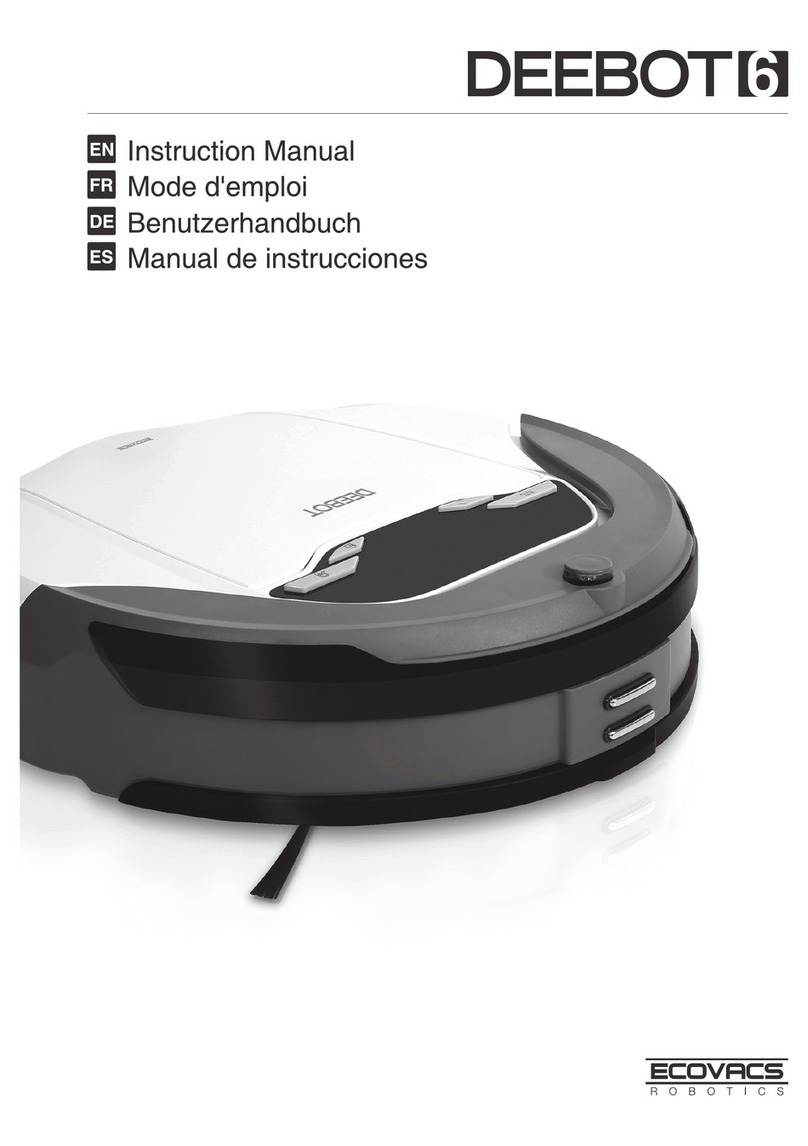
ECOVACS
ECOVACS Deebot 6 instruction manual

Pololu Corporation
Pololu Corporation Balboa 32U4 Schematic diagram
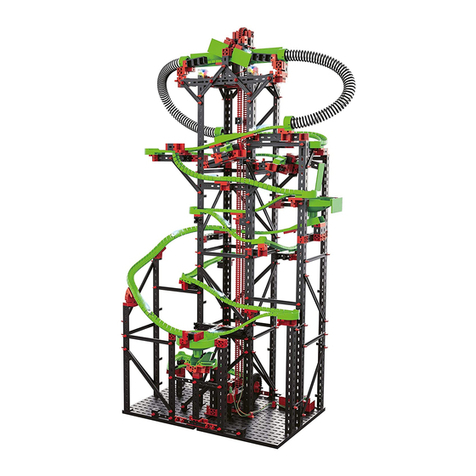
fischertechnik
fischertechnik PROFI Dynamic XXL Booklet
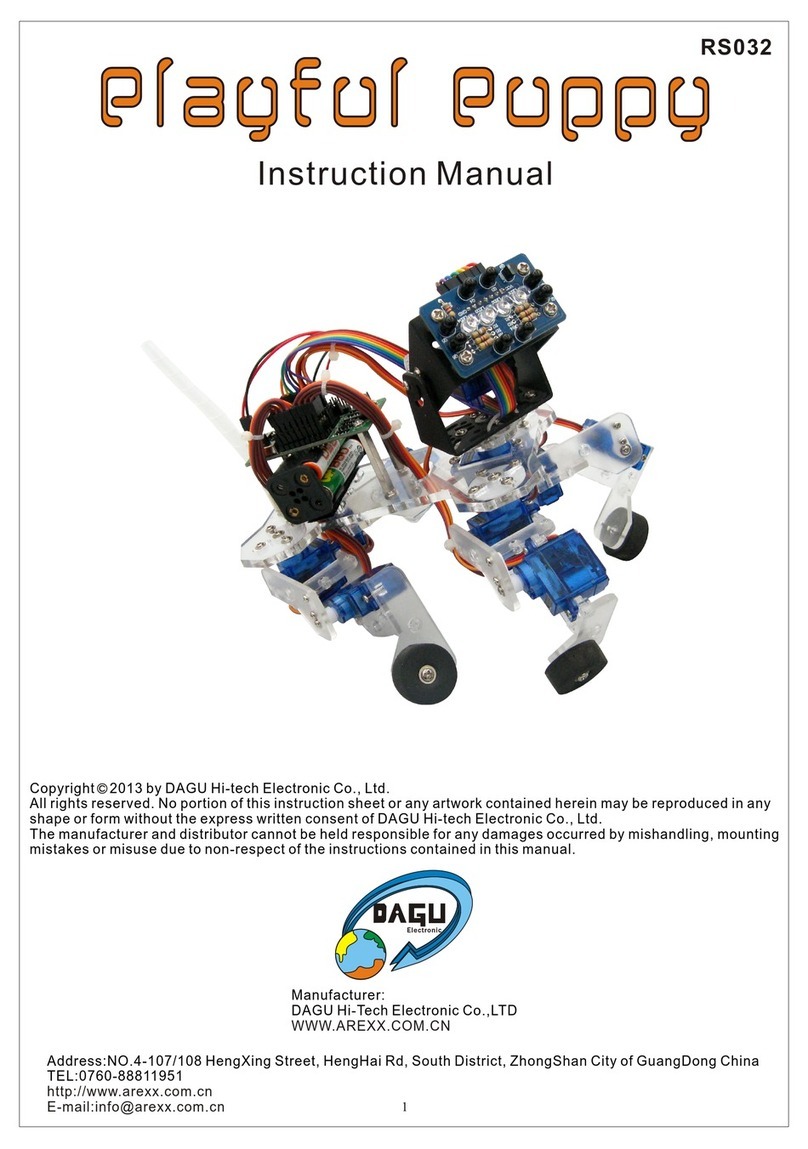
DAGU
DAGU Playful Puppy instruction manual
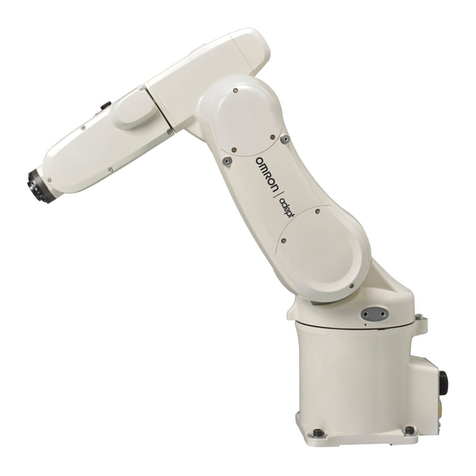
adept technology
adept technology Viper s650 user guide
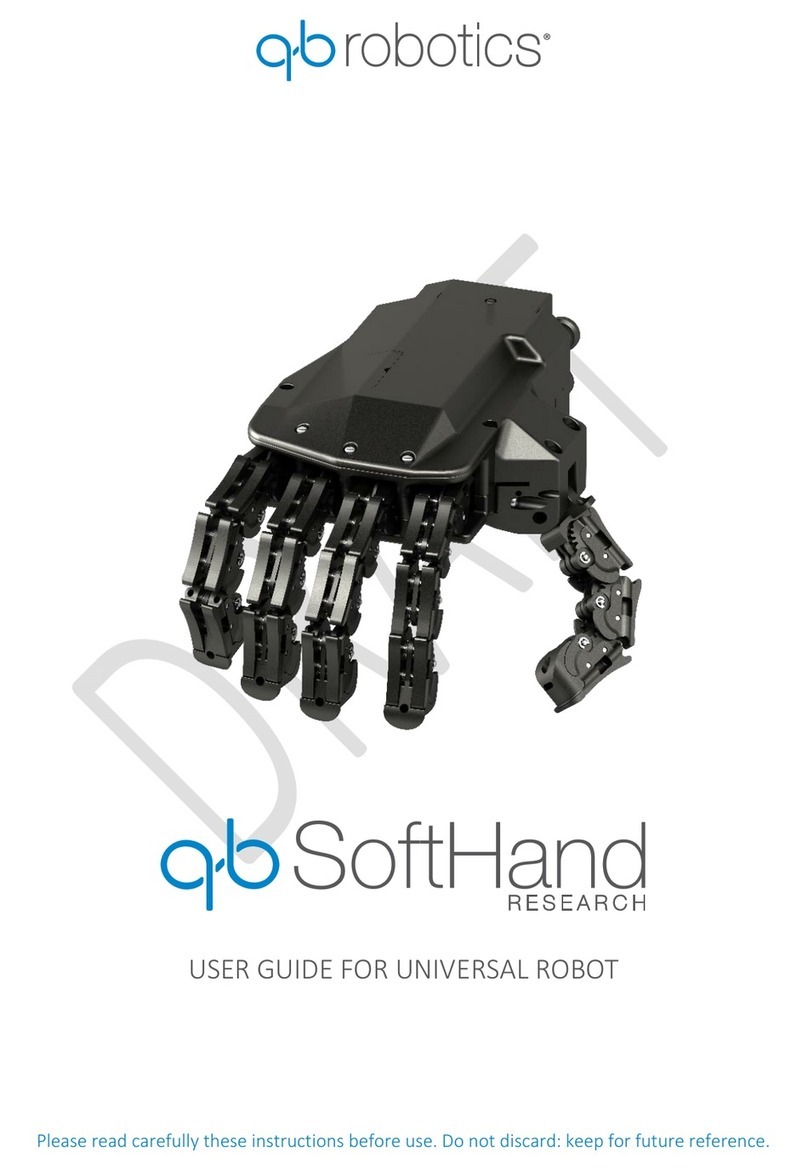
QB Robotics
QB Robotics qb SoftHand RESEARCH user guide
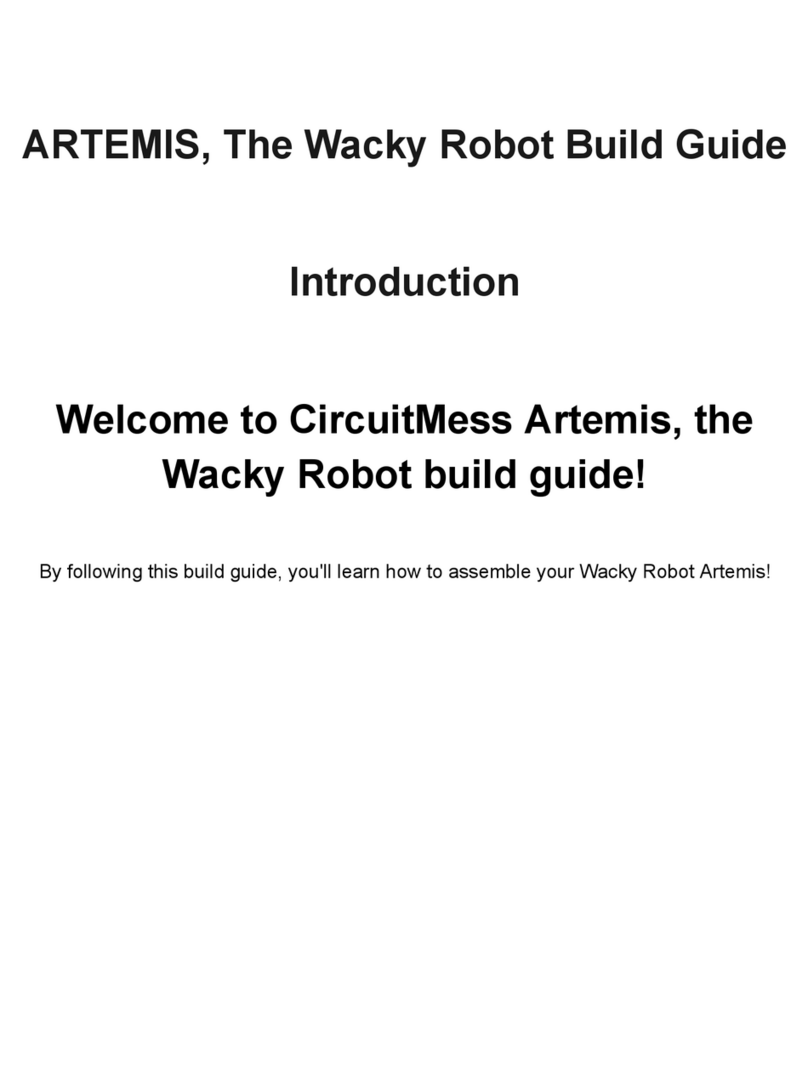
Circuitmess
Circuitmess Artemis Build guide