AGRGS Castle EP2 User manual

Castle EP2
Controller
User’s manual
© AGRGS 2015

© AGRGS 2015 | Data subject to change without notice
43720016049057106 | en, eu, V5, 07. Dec 2015, page 2
Table of Contents
1. Introduction 4
2. Document revision 5
3. Controller and package description 6
3.1. Controller board elements description 6
3.2. Package content 6
4. Technical features 7
5. Controller functioning as ASC “Castle” 9
5.1. Conguration:“Registration board” 9
5.2. Conguration:“Turnstile” 10
5.3. Conguration: “Two-sided door” 11
5.4. Conguration:“Two one-sided doors” 11
6. Controller mounting and wiring instructions 13
6.1. Controller power supply 14
6.2. Contoller ports 15
6.3. Readers and contactors connection, general information 16
6.3.1. Smart card readers connection general rules 16
6.3.2. Wiegand readers connection 17
6.3.3. Touch memory readers and contactors connection 18
6.3.4. Key-pad readers connection 19
6.3.5. Important information on non-standard readers 20
7. Doors connection 21
7.1. Readers connection 21
7.2. Door locks connection, general information 22
7.2.1. Electromagnetic locks and latches connection 22
7.2.2. Electromechnical locks connection 23
7.2.3. Important information on locks and latches use 23
7.3. Door sensors connection 24
7.4. Request button connection 25
8. Turnstile connection 26
8.1. Control lines connection 26
8.2. Readers connection 27
9. Connecting the communicational lines and setting up the controller 28
9.1. Connecting the Ethernet 28
9.2. Setting up the controller IP-parameters 28
10. Alarm lock release line connection 29
11. Alarm system loop connection 31
12. Controller operation logic 32

© AGRGS 2015 | Data subject to change without notice
43720016049057106 | en, eu, V5, 07. Dec 2015, page 3
12.1. Starting the controller 32
12.2. Readers’indication line operation 32
12.3. Fire alarm system signals procession 32
12.4. Alarm system loop signal procession 32
12.5. Work of controller’s protection circuits 33
12.5.1. Controller power supply protection 33
12.5.2. Readers power supply protection 33
12.5.3. Controller output ports protection 33
12.5.4. Controller input ports protection 33
12.6. Operation logic in conguration“Turnstile” 33
12.6.1. Controlling the turnstile 33
12.6.2. Turnstile control panel 34
12.7. Operation logic in conguration“Doors” 35
12.7.1. Operating the readers and request buttons 35
12.7.2. Operating the block button 35
13. Troubleshooting 36
13.1. Power supply and starting the controller problems 36
13.2. Commutation quality problems 36
13.3. Readers connection problems 37
13.4. Control panel connection problems 37
13.5. Locks connection problems 37
13.6. Turnstile connection problems 37
14. Appendix1. Controller sound alerts 38
15. Appendix2. Controller lights indication 39
16. Appendix3. Controller conguration numeral parameters 40
17. Appendix4. Brief recommendations for cable selection 41
18. Appendix5. Character key-pad reader encoding 42

© AGRGS 2015 | Data subject to change without notice
43720016049057106 | en, eu, V5, 07. Dec 2015, page 4
1. Introduction
This document contains description and “Castle” controller installation and operation instructions.
“Castle” EP2 controller is designed to work as part of access control systems (ACS) “Castle”.
Each controller is able to control the turnstile, electromechanical wicket, one or two doors and
barrier gates or gates in a simplied mode.
Each controller reacts immediately (smart card reading, pushed button etc).
This feature is completely not depended on the controller number, communication
quality, personnel quantity or length of the commutation line.
Whether communicating with the server system or not, the controller decides to permit or deny
access on their own, basing on the key database and access modes stored in the controller non-
volatile memory.
All registered events are stored in non-volatile memory of the controller. Date and time of the event
are recorded basing on the embedded real-time clock testimony. If connection to the server exists,
events are automatically transferred to the ACS server.
This ensures maximum system reliability, controller independence from the server and speed of its
response to events.
“Castle” controller is certied to meet the next requirement documents:
•GOST R 51241-2008. Access control units and systems. Classication. General technical
requirements. Test methods.
•GOST R 50009-2000. Electromagnetic compatibility of technical equipment. Components of
intruder alarm systems. Requirement and test methods.
•GOST R 51317.6.1-99 (MEK 61000-6-1-97). Electromagnetic compatibility of technical
equipment. Immunity of technical equipment intended for use in residential, commercial and
light-industry environments. Requirements and test methods.
•GOST R 51317.6.3-99 (SISPR/MEK 61000-6-3-96). Electromagnetic compatibility of technical
equipment. Emission from technical equipment intended for use in residential, commercial
and light-industry environments. Limits and test methods.
Conformity certicate No. .RU.ME63.B03297.
The manufacturer is responsible for the accuracy of the documentation and after any hardware and
software revisions is obliged to add an information into the manuals.
The manufacturer does not guarantee product performance in the non-observance
of the installation rules and operation described herein.

© AGRGS 2015 | Data subject to change without notice
43720016049057106 | en, eu, V5, 07. Dec 2015, page 5
2. Document revision
Current
revision
Publish date Notes
0002 December 2012 First notes.
0003 May 2014 Readers connection diagrams added, some functions and features added.
0004 October 2015 Features revised, some functions and diagrams added.
0005 November 2015 English version.

© AGRGS 2015 | Data subject to change without notice
43720016049057106 | en, eu, V5, 07. Dec 2015, page 6
3. Controller and package description
3.1. Controller board elements description
The controller is a microprocessor board, packed in a metal case.
PWRT XR X
FD
RST
PRG
CONFIG
ON DIP
ADDRESS
Bip Bat-3V
RELE-1 RELE-2
K2K1
PORT 1
PORT 2
+12V
GND
DET+
DET–
+12V
GND
DATA0
DATA1
LED
PASS
RTE
GND
NO
COM
NC
+12V
GND
DATA0
DATA1
LED
PASS
RTE
GND
NO
COM
NC
RJ45
+12V
F+
F–
GND
STOP
Pic1. Controller board main components arrangement scheme.
Component Description
CONFIG Controller conguration dip-block.
RST Controller IP parameters “default”reset jumper.
K1 Relay operation indicator.
K2 Relay operation indicator.
PWR Controller power supply indicator (Green).
RX Incoming data indicator (Yellow).
TX Outcoming data indicator (Red).
FD Fire alarm port cut-o jumper.
3.2. Package content
Nos Item Qty
1 Controller in a metal case. 1pcs.
2 CD with an electronic copy of current manual. 1pcs.
3 Warranty card with the purchase date. 1pcs.
4 Diode 1N4007. 2pcs.
Table 1. Package content.

© AGRGS 2015 | Data subject to change without notice
43720016049057106 | en, eu, V5, 07. Dec 2015, page 7
4. Technical features
Measurements
Metal case dimensions 240 * 260 * 57mm
Board dimensions 100 * 100 * 25mm
Electrical characteristics
Voltage +10...15V
Consumption current Not more than 160m
Consumption power Not more than 3Wt
Maximum power relay outputs
switching voltage
30V
Maximum power relay outputs
switching current
10
Maximum “OC” type outputs
switching voltage
30V
Maximum “OC” type outputs
switching current
0.1
Built-in controller protection
circuits
1. Power supply:
◦Controller power supply protection against reverse polarity;
◦Readers power circuits protection against overload and over-voltage;
2. Communication line (Ethernet): Full galvanic insulation;
3. Input interfaces: Protection against overload and reverse polarity;
4. Output interfaces: Maximal current limitation, relay contacts protection against
overload and burning-out.
Interfaces
Commutation line One standard Ethernet port.
Exchange rate — 10Mb/s, semiduplex.
Readers connection Up to 2 readers with Wiegand or Touch memory output interface.
Sensors connection Up to 5 sensors with“open collector”(“OC”) or “dry contact”type output.
Indication outputs 2“OC”outputs.
Power relay outputs 2 relays, contact group is working on the switch.
Fire alarm connection Double wired line, galvanically insulated to connect multiple controllers to a single
loop.
Operating conditions
Air temperature From 0 to +45°C.
Air humidity Not exceeding 85% @ t° = 30°C.
Atmosphere pressure 84–106,7kPa.
Parameters when operating as a part of ACS
Execution devices support 1. Turnstiles with potential management and various organizations of pass
sensors.
2. Doors equipped with electromagnetic, electromechanical locks and latches.
Quantity of internal memory
kept keys
7000 *

© AGRGS 2015 | Data subject to change without notice
43720016049057106 | en, eu, V5, 07. Dec 2015, page 8
Quantity of internal memory
kept events
40000 *
Quantity of internal memory
kept access modes (time zones)
500 *
Antipassback and further zone
control
If connected to server — global Antipassback with adjustable monitoring time.
Zone control and employers location monitoring.
Autonomic controller status
indication
1. Sound indication of controller work and its conguration faults.
2. Visual power indication.
3. Visual Ethernet trac indication (income/outcome data).
Firmware update availability Firmware can be updated via any PC connected to ASC“Castle”.
Detaching the execution devices from the controller is not needed.
* Allocation of autonomic internal memory between keys, modes and events is adjustable. Abovementioned numbers
corresponds to one of possible option.

© AGRGS 2015 | Data subject to change without notice
43720016049057106 | en, eu, V5, 07. Dec 2015, page 9
5. Controller functioning as ASC “Castle”
EP2“Castle” controller is designed to work as part of a network ASC“Castle”, operating the
connected execution devices. Controllers are connected to server via Ethernet line.
EP2 controller can manage one of the following set of execution devices:
1. One door equipped with enter and exit readers.
2. Two doors equipped with reader and exit request button. Doors should be located not more
than 60m from the controller, which is limited by the locks’voltage drop.
3. Electomechanical gate of any conguration.
4. Employers timesheet registration without any execution devices connection.
Up to two readers with Wiegand 26/34 or Touch Memory input interface can be connected to the
controller as an identication equipment. Also there’s a availability to connect code panel reader.
5.1. Conguration: “Registration board”
This conguration is used for registration of employers arrivals and departures without using any
execution devices.
When locating the pass card to the reader, the system automatically records the cardholders pass to
enter or exit.
Pic2. Connecting the controller in“Registration board”conguration.
To work in this conguration the controller is connected to the power supply, commutation line
and two readers. One reader is used for work place arrivals registration, the other — for departures.
Registration table
Dip-switch 1 2 3 4 5 6 7 8
ON ON ON — Touch Memory
OFF OFF OFF OFF OFF OFF OFF OFF — Wiegand-26
Table2. Setting the CONFIG dip-switches for“registration board”conguration.

© AGRGS 2015 | Data subject to change without notice
43720016049057106 | en, eu, V5, 07. Dec 2015, page 10
5.2. Conguration: “Turnstile”
In this conguration the controller is commutated with:
• Turnstile;
• Turnstile control panel;
• “Entrance”reader;
• “Exit”reader.
Pic3. An example of“Turnstile”conguration equipment connection.
Turnstile
“Turnstile”
conguration
Pass sensors
normal state
Readers work interface selection Turnstile
management
variant
Readers
interface
1 2 3 4 5 6 7 8
ON ON ON —
normally open
ON Invalid combination ON ON — impulse
management
ON —
Touch Memory
ON “one-wired”interface OFF
OFF OFF —
normally close
OFF “strict” interface ON OFF — potential
management
OFF —
Wiegand-26
OFF “simplied”interface OFF
Table3. Setting the CONFIG dip-switches for“turnstile”conguration.
Notes:
• Pass sensors normal state — is the state when the turnstile arm is in its nominal (closed)
position.
• Management logic description is in section Operation logic in conguration“Turnstile”.

© AGRGS 2015 | Data subject to change without notice
43720016049057106 | en, eu, V5, 07. Dec 2015, page 11
5.3. Conguration: “Two-sided door”
In this conguration the controller is commutated with:
• “Entrance”reader;
• “Exit”reader;
• Lock;
• Door sensor (gerkon);
• Exit request button;
• Entrance request button;
• Door block button.
Pic4. An example of“Two-sided door”conguration equipment connection.
On the entrance and exit can be installed reader and request button. Separation of the entrance/
exit readers and request buttons allows the system to determine the direction of the pass more
correctly.
5.4. Conguration:“Two one-sided doors”
In this conguration the controller is commutated with:
• Up to two doors
• For each door:
◦Lock;
◦Door sensor (gerkon);
◦“Entrance”/ ”Exit” reader;
◦Exit request button (entrance).
• Door block button (blocks two doors simultaneously).

© AGRGS 2015 | Data subject to change without notice
43720016049057106 | en, eu, V5, 07. Dec 2015, page 12
Pic5. An example of“Two one-sided door” conguration equipment connection.
Doors
“Doors”conguration Pass sensors
normal state
Lock
management
Reader
and button
direction for
the rst door
Reader and
button direction
for a second
door
Readers
interface
1 2 3 4 5 6 7 8
ON —
two
doors
ON —
one
door
ON —
normally open
ON —
impulse
ON — exit
button, entrance
reader
ON — entrance
button, exit
reader
ON — Touch
Memory
OFF
— one
door
OFF
— two
doors
OFF OFF —
normally close
OFF —
potential
OFF — entrance
button, exit
reader
OFF — exit
button, entrance
reader
OFF —
Wiegand-26
Table4. Setting the CONFIG dip-switches for“doors”conguration.
Notes:
• Normal door sensor state is when the door is closed. For the most widely using sensors —
gerkons, the normal state is closed.
• Management logic description is in section Operation logic in conguration“Doors”.

© AGRGS 2015 | Data subject to change without notice
43720016049057106 | en, eu, V5, 07. Dec 2015, page 13
6. Controller mounting and wiring instructions
It is must to read this instruction and technical features carefully before starting of installment and
wiring.
For correct installation of the controller rst carefully read the required section if this manual that
corresponds to the needed conguration (door, doors, turnstile, table). Wisely chose the places
to mount controllers, readers, execution devices and sensors. Mark all xing points. Make lining
and xing of all the cables. Check for cut-o and short circuits in all lines carefully. Installment
of turnstile racks, barriers, gates, locks, sensors, etc. should be done according to passports and
instructions to the respective products.
When choosing controller placement and lining direction the following notes must be kept as a
rule:
1. The installation of the controller less then 1m away from any electric generators, magnetic
contactors, motors, AC relays, thyristor light regulators and other electrical interference
sources is highly not recommended.
2. All signal and low-voltage cables should be located at least 50cm away from AC power cables,
control cables of power motors, pumps, actuators, etc.
3. Only perpendicular signal and power cables is allowed.
4. Any signal cables extensions is to be done by welding. Power cables extensions can also be
done with terminals.
All incoming into the controller case cables should be properly fastened.
The specic cable type depends on the installation characteristics — internal, external or hanged-
out wiring, etc. Some recommendations on the cable selection can be found in this manual
Appendix 4. Brief recommendations for cable selection.
All connections and disconnections of any equipment is preferable to produce with the controller
power o.
The controller mounting placement is determined by the convenience of further maintenance.

© AGRGS 2015 | Data subject to change without notice
43720016049057106 | en, eu, V5, 07. Dec 2015, page 14
6.1. Controller power supply
Controller power supply is made by constant voltage of 10–15V, the current consumption of the
controller is not more than 160mA.
• When only controller is supplied by power unit the later should be installed in any convenient
location between the nearest supply panel and a controller and provide the output DC
voltage of 12V and a current of not less than 200mA.
• When power supply providing power also to readers, locks and other equipment, it should
carry the possibility to supply every equipment plus about 20% capacity in reserve.
• Power supply reserve capacity is needed for correct functioning of the controller during force-
majors such as communication line and readers power line short circuits, etc.
When force-majors occur the built-in controller protection circuits cut-o the power supplement
of the line being overload or shorted, but the controller current consumptions may increase during
the protection operation.
For example, when the power line of the reader, consuming normally 80mA is shortened the fuse
of 200mA is being turn o. By this the power consumption is raising with about 120–200mA. You
can chose the UPS from“BBP“, “SKAT“,“BRP“, “RIP“ trademarks, for example.
After power supply is installed it is connected to single-phase 220V power line. The power supply is
connected to the controller terminals as it shown on the picture below.
Pic6. Connection of the controller to the power supply.
For connection can be used any cables suitable by section size (better not less than 0.5mm2), VVG
(PVC insulated) for example.
Notes:
1. When using the power supply“BBP-20”it is recommended to install an additional battery
protection device (for example,“UGA-12”or “BKA”).
2. When using a power supply with metal case it is necessary to connect it to the protective
grounding.
3. When execution devices have ooring accumulating static electricity it is recommended to
connect these devices to the protective grounding.

© AGRGS 2015 | Data subject to change without notice
43720016049057106 | en, eu, V5, 07. Dec 2015, page 15
6.2. Contoller ports
Similar controller terminals are grouped into two“ports”. Each block is highlighted on board as
“PORT 1” and“PORT 2”.
Port
Terminal Function Terminal assignment
+12 Output Controller power supply, is equal to the controller voltage.
GND Common Common of the supply, also of PASS RTE.
DATA0 Input Reader’DATA 0 line.
DATA1 Input Reader’DATA 1 line.
LED Output Controller indication management line. Output with OC.
PASS Input Pass sensor.
RTE Input Request button.
GND Common Common of the supply, also of PASS RTE.
NO Relay normally open.
COM Common of relay.
NC Relay normally close.
Table5. Controller port terminal assignment.

© AGRGS 2015 | Data subject to change without notice
43720016049057106 | en, eu, V5, 07. Dec 2015, page 16
6.3. Readers and contactors connection, general information
Up to two readers with standard Wiegand or Touch memory output interface can be connected to
each controller.
Controller determines the readers’interface type directly after the power appliance.
Each reader is connecting to the controller terminal marked PORT1 or PORT2 on board.
Total current consumption of readers should not exceed 200mA, in excess the controller protection
circuit starts and cuts o the reader’s power.
When connecting the reader, consuming current of more than 200mA, it’s power“positive”should
be connected directly to the power supply terminals.
Purpose and number of readers and contactors to be connected are described in the manual’s
section corresponding on specic congurations of the equipment supported by this controller.
6.3.1. Smart card readers connection general rules
1. Readers are to be located in convenient for presenting the pass card places. Recommended
mounting height is 1.1–1.4m from the oor level as per terms of ergonomics.
2. Readers are connected to the controller with cables like 22AWG, 24AWG. It is not
recommended to use“twisted pair” cables for connection.
3. Do not place readers in wide spectrum electromagnetic noise sources zones. For example:
magnetic contactors, motors, electric generators, AC/DC transformers, UPS, AC relays, light
regulators, monitors, etc.
4. Place the reader cable at a distance exceeding 0.5m from all other cables, including the AC
power, computer, telephone or electromechanical locks power cables.
5. The distance between two standard read range readers (up to 15cm) should be at least 0.5m
in order to eliminate the mutual inuence. The distance should be increased proportionally
for an enhanced range readers, and reduced for shortened range.
Important notes on readers’use, incl. non-standard ones.
1. Many readers support several output interfaces simultaneously. For changing readers
interface into Wiegand its manual should be read. As a rule, this changing is performed by
shorting the internal reader lines or by dip-switches on the reader.
2. The parallel multiple readers’connection with a standard Wiegand interface is available. This
method can be used for enhanced access control level when, for example, two standard,
biometric and key-pad readers are connected as“entrance” devices.

© AGRGS 2015 | Data subject to change without notice
43720016049057106 | en, eu, V5, 07. Dec 2015, page 17
6.3.2. Wiegand readers connection
Wiegand standard interface’ electrical characteristics provide a guaranteed readers connection
range up to 100m, which is sucient for most cases. The connection range can be enhanced by
using appropriate cables and installation conditions up to 150m (check the Appendix 4. Brief
recommendations for cable selection).
To work with Wiegand interface readers the 8th DIP-switch on CONFIG block is to be set to OFF (set
by default).
Pic7. An example of connection of the reader with voltage equal to the controller’ voltage.
Pic8. An example of connection of the reader with voltage not equal to the controller’ voltage or consuming more
than500mA.
Picture notes:
• LED G — green reader LED (combined with sound beeper, as a rule);
• DATA0, DATA1 terminals — data transfer lines (0 and 1), LED — reader’ indication control line,
+12 — positive power supply, GND — common wire.
• LED line can be not connected if readers use its built-in indication.

© AGRGS 2015 | Data subject to change without notice
43720016049057106 | en, eu, V5, 07. Dec 2015, page 18
6.3.3. Touch memory readers and contactors connection
Touch memory standard interface’ electrical characteristics provide a guaranteed readers
connection range up to 15m.
Connected reader’ interface is determined by the controller at the power appliance.
Terminal jumper between DATA0 and LED2 must be set before the power supply
start, otherwise the interface will be set to Wiegand and Touch memory interface
reader will not work.
To work with Touch memory interface readers the 8th DIP-switch on CONFIG block is to be set
toON.
Pic9. An example of Touch memory contactor connection.
Pic10. An example of Touch memory output interface reader.
Pic11. An example of Touch memory contactor connection with built-in LED1.
Pic12. An example of Touch memory contactor connection with built-in LED2.

© AGRGS 2015 | Data subject to change without notice
43720016049057106 | en, eu, V5, 07. Dec 2015, page 19
6.3.4. Key-pad readers connection
Key-pad reader should have Wiegand-HID (6bit) Wiegand-Motorola (8bit) output interface to
be connected to the controller. The interface type is determined by the controller automatically.
When using other standards of key-pad readers it is a must to check their output interface
compliance and character encoding according to this manual Appendix 5. Character key-pad
reader encoding.

© AGRGS 2015 | Data subject to change without notice
43720016049057106 | en, eu, V5, 07. Dec 2015, page 20
6.3.5. Important information on non-standard readers
Some available on the market readers models do not meet their stated specications, and
therefore, either do not work at all or require some additional settings.
Readers that do not work at all are, for example,“KODOS” (high-ohm resistors do not provide
normal logic levels at the controllers’ terminals in the output stage of readers), BOLID 2000 proxy
reader (failure reasons are unknown for now), BOLID 2000 proxy(H) of some revisions (for example,
rev. 4 works properly , rev. 8 do not works at all) and a “PROXIMUS” (provides a completely non-
standard format card code, which is impossible to understand by any existing formula).
As per readers require additional settings — for example, SP-E1Quest, Skyros SP-E1Q readers
control receiver-board -15 form incorrect Wiegand interface checksum message.
Conclusion:
1. Wiegand standard interface’ electrical characteristics provide a guaranteed readers
connection range up to 100m, which is sucient for most cases. The connection range can
be enhanced by using appropriate cables and installation conditions up to 150m.
2. Many readers support several output standards simultaneously. For switching the reader into
Wiegand interface reader’s manual should be read. As a rule this can be done by shorting
readers’ internal lines, changing the dip-switches or by cutting a specially outed copper wires
in a proxy card of the reader.
3. The parallel multiple readers connection with a standard Wiegand interface is available. This
method can be used for enhanced access control level when, for example, two standard,
biometric and key-pad readers are connected as“entrance” devices.
Take note on Touch Memory interface Matix-II (not to be confused with Matrix-II EH) readers. They
are known for its rmware malfunction due to which the controller sometimes do not provide card
code although sound and light indication works properly. It leads for re-swiping the pass card or
disappearance of access events in the log when controller only registrates the card reading without
managing a door or turnstile.
Table of contents
Popular Controllers manuals by other brands
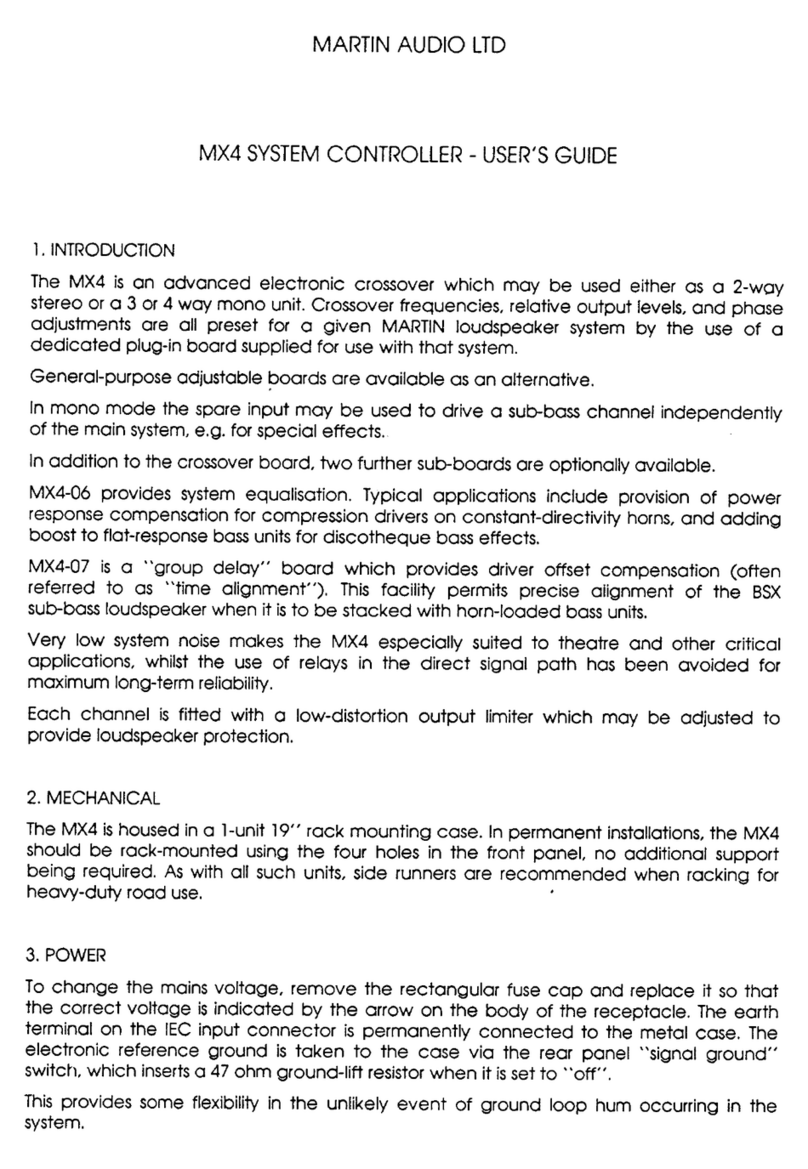
Martin Audio
Martin Audio MX4 user guide

Mitsubishi Electric
Mitsubishi Electric MELSEC iQ-R Series Introduction Guide

Thermal Dynamics
Thermal Dynamics iCNC Performance Operator's manual
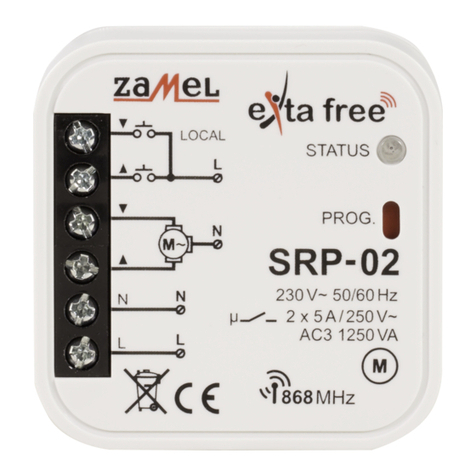
Zamel
Zamel SRP-02 manual

Berker
Berker 8536 52 00 operating instructions
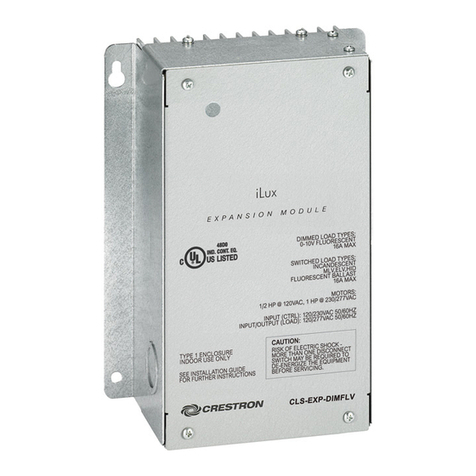
Crestron
Crestron CLS-EXP-DIMFLV installation guide
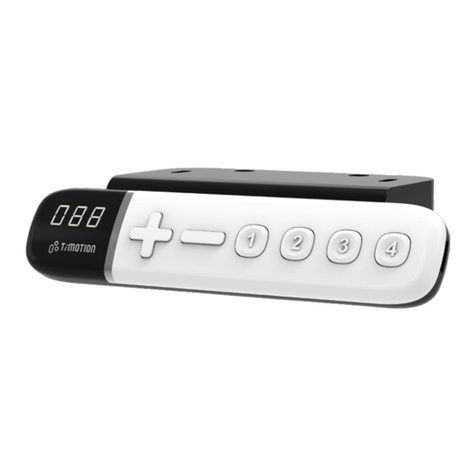
Timotion
Timotion TDH13P user manual
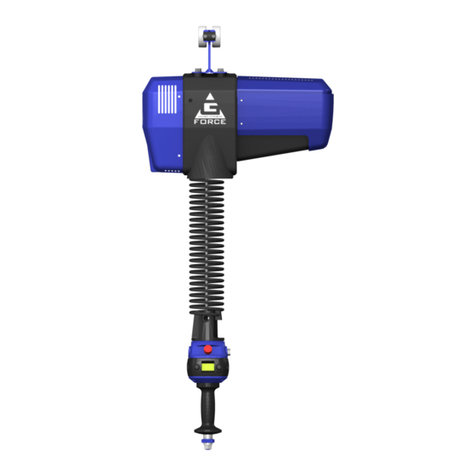
GORBEL
GORBEL G-Force Q2 Series Installation, operation & maintenance manual
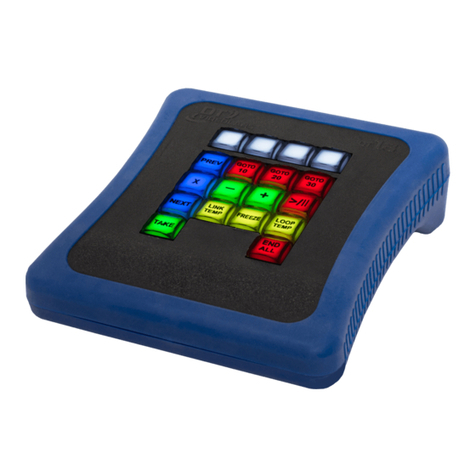
DT VIDEOLABS
DT VIDEOLABS DT18 quick start guide
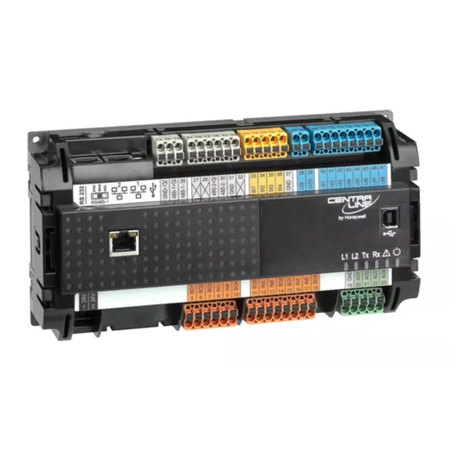
Honeywell
Honeywell Centra Line EAGLE Installation & commissioning instructions

LED Lights Canada
LED Lights Canada CCT Wall Mount Touch Panel Operation instructions
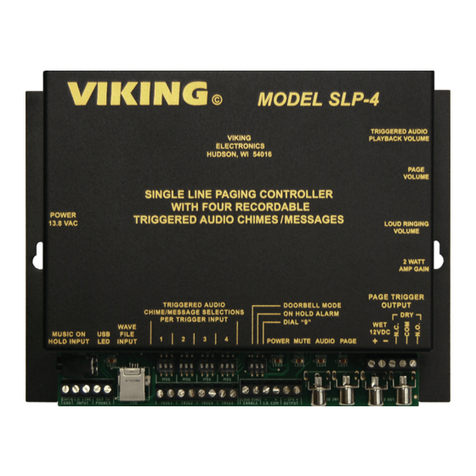
Viking
Viking SLP-4 Technical practice