Aircalo LAGON User guide

- 1 -
START UP AND
MAINTENANCE LEAFLET
AIR HANDLING UNIT
LAGON

- 2 -
CONTENTS
N° Section Page
1 SAFETY CONSIDERATIONS 2
2 PREINSTALLATION 3
3 SETTING UP 3
4 RIGGING 4
5 ASSEMBLING 5
6 COILS CONNECTION 7
7 ELECTRICAL CONNECTION 9
8 MAINTENANCE 11
1. SAFETY CONSIDERATIONS
This unit comply with EU « Electromagnetic compatibility (CEM) » 89/336/CEE, to be
incorporated in an installation.
Installation must comply with CEM requirements.
Air handling equipment is designed to provide safe and reliable service when operated within
designed specifications. To avoid injury to personnel and damage to equipment or property
when operating this equipment, use good judgment and follow safe practices.
The painted panels are covered with plastic film protection. Remove this protection after
installation.
Never enter an enclosed fan cabinet or reach into a unit while the fan is running.
Lock open and tag the fan motor power disconnect switch before working on a fan. Take
fuses with you and note removal on tag. Electric shock can cause personal injury or death.
Check the assembly and component weights to be sure that the rigging equipment can
handle them safely.
Do not open door or remove access panel fasteners until fan is completely stopped.
Pressure developed by a moving fan can cause excessive force against the panel which can
injure personnel.
Do not work on dampers until their operators are disconnected.
Drain water coil in case of no use, in order to avoid freeze risk in the winter.
Transmit this instruction leaflet to user and insure one copy stays on the unit.

- 3 -
2. PREINSTALLATION
Check items received against packing list. Notify Aircalo of any discrepancy in the 24H.
Do not stack unit components or accessories during storage. Stacking can cause damage.
Chose a dry storage site. Do not store unit on a vibrating surface. Cover entire unit with a
tarp or plastic coverall. Extend cover under unit if stored on ground. Secure cover with
adequate tiedowns or store indoors. Be sure all coil connections have protective shipping
caps.
3. SETTING UP
Air handling unit Lagon are heavy and voluminous units. The setting up must be studied in
advance. In particular it is necessary to control the support WEIGHT ability.
It is recommended to settle air handling unit in a dedicated room.
In the case of roof installation, check the extreme wind speed known on the site. Eventually
insure a special air unit roof fastening.
Provide adequate space for unit service access (fan
shaft and coil removal, filter removal, motor access,
damper linkage access, etc.) as shown in Fig.
Usually space clearance is arranged on 1 side only.
However, it is possible to arrange clearance on both
side, as the panel at back is removable.
To prevent excessive build-up of condensate in drain
pan, adequate trap clearance must be provided
beneath the unit as indicated in page 8. See water
connection, Condensate Drain section
It is recommended to settle on the service face all components like actuators, electrical
panels, valves ...
Components of the air units have to be assembled on site according the dimensional and
general drawing supplied with the equipment.
When several units are delivered at the same place and same time, it is essential to clarify
the components belonging to each unit before assembling. In many cases, the components
can fit together, but the performances are different from unit to another.
Check also the direction of assembling (i.e. the air flow direction can guide the orientation of
each component).

- 4 -
4. RIGGING
Lagon units can be rigged by means of the lifting brackets on bottom of unit.
Components are shipped fully assembled. Do not remove shipping skids or protective
covering until unit is ready for final placement.
Use slings and spreader bars as applicable to lift unit.
Do not remove protective caps from coil piping connections until ready to connect piping.
Do not remove protective cover or grease from fan shaft until ready to install sheave.
Lay rigid temporary protection such as plywood walkways in unit to prevent damage to
insulation or bottom panel during installation.
1 bar kit per complete unit. Kit is to be used for each component.
Slide the bars approx. 15 cm out of the frame. Set the slings securely.
Do not lift unit by coil connections or headers.

- 5 -
Units must be installed on a flat floor.
Check components are correctly alined, in order to avoid any leakage.
5. ASSEMBLING
Assembling of air unit components must be done from one end to the other (preferably from
suction to discharge).
Except if unit a one only component, stick the
supplied black strip join on the aluminium profile.
When access is possible into the
component (through door or access panel),
the components must be coupled with bolt
and screws at corners.

- 6 -
If internal access is impossible, then the
components must be carefully placed side by side
in order to squeeze regularly the black strip join all
around the coupling faces.
The components will be linked together with 3
supplied external braces. Screw directly on the
aluminium profile.
When square & cap option is supplied, fit the caps directly on aluminium frame once all
components are assembled.
EXTERNAL UNITS
The units for external use are supplied with roof delivered as kit, to be assembled on site.
Roof can be fitted only when the air unit
components are completed all together.
One slope roofs are horizontal. Water can stay
on it without any risk of corrosion or infiltration.
Two slopes roofs are delivered with ridgepole
arrangement in order to make the roof tilt on
both side. Ridgepole is normally assembled at
factory.
The roof plates have to be fitted into
each other starting from one end of the
air unit.
Insure approx. 200 mm extension over
the air unit edges. Use self drilling
screws and seal plate. Screw directly on
the aluminium profile all around the unit.
Space between 2 screws : 200 mm max.
Eventually less if the wind on the site are
strong. Check the roof is firmly fitted and
able to face the wind forces. If supplied,
fit the white screw caps on the screws
head.
Take off the plastic film protection when
roof assembling has been achieved.
(
1
)
(2)
Fill with silicon all roof
plates interlocking.

- 7 -
If air handling unit has inlet and or outlet through the bottom face, the unit must be
heightened (see local regulation).
NOTE : When unit are outside, it is necessary to prevent any risk of freeze on water coils.
(i.e. use actuated damper – see below).
6. COILS CONNECTION
WATER COILS CONNECTIONS
Connection must be done without any mechanical efforts on the coil itself.
Air relief valve must be settled at each high point of the circuit and decanting bowl with
emptying valve at low points.
Connections can be dismantled in order to allow easier maintenance operation. Free space
is necessary around the unit to let possible eventual coils dismantling.
Use preferably flange connections.
Typically, coils are piped by connecting the supply at the bottom and the return at the top.
This is not always the case, especially if the coil hand has been changed in the field. Coils
must be piped for counterflow; otherwise, a capacity reduction of 5% for each coil row will
result. To ensure counterflow, chilled water coils are piped so that the coldest water meets
the coldest air. Hot water coils are piped so that the warmest water meets the warmest air.
Check temperature and pressure plated on coil before opening the circuit.
STEAM COILS
Position the steam supply connection at the top of the coil, and the return (condensate)
connection at the bottom. The coil tubes must incline downwards toward the return header
connection for condensate drainage. Dilatation arrangement are required at connection.
Figure illustrates the normal piping components and the
suggested locations for high, medium, or low-pressure
steam coils. The low-pressure application (zero to 15
psig) can dispense with the ¼-in. petcock for continuous
venting located above the vacuum breaker (check valve).
NOTES:
1. Flange or union is located to facilitate coil removal.
2. Flash trap may be used if pressure differential
between steam and condensate return exceeds 5 psi.
3. When a bypass with control is required.
4. Dirt leg may be replaced with a strainer. If so, tee on
drop can be replaced by a reducing ell.
5. The petcock is not necessary with a bucket trap or any
trap which has provision for passing air. The great
majority of high or medium pressure returns end in hot
wells or deaerators
which vent the air.

- 8 -
Note the horizontal location of the 15-degree check valve, and the orientation of the
gate/pivot. This valve is intended to relieve any vacuum forming in the condensate outlet of a
condensing steam coil, and to seal this port when steam pressure is again supplied to the
coil. It must not be installed in any other position, and should not be used in the supply line.
For coils used in tempering service, or to preheat outside air, install an immersion thermostat
in the condensate line ahead of the trap. This will shut down the supply fan and close the
outdoor damper whenever the condensate falls to a predetermined point, perhaps 120 F.
NOTE: Do NOT use an immersion thermostat to override a duct thermostat and open the
steam supply valve.
For vacuum return systems, the vacuum breaking check valve would be piped into the
condensate line between the trap and the gate valve instead of open to the atmosphere.
Figure illustrates the typical piping at the end of every
steam supply main. Omitting this causes many field
problems and failed coils.
NOTES:
1. A bypass is necessary around trap and valves when
continuous operation is necessary.
2. Bypass to be the same size as trap orifice but never
less than 1/2 inch.
COILS FREEZE-UP PROTECTION
WATER COILS — If a chilled water coil is applied with outside air, provisions must be made
to prevent coil freeze-up.
Install a coil freeze-up thermostat to shut down the system if any air temperature below 36 F
is encountered entering the water coil. Follow thermostat manufacturer’s instructions.
For outdoor-air application where intermittent chilled water coil operation is possible, one of
the following steps should be taken:
• Install an auxiliary blower heater in cabinet to maintain above-freezing temperature around
coil while unit is shut down.
• Drain coils and fill with an ethylene glycol solution suitable for the expected cold weather
operation. Shut down the system and drain coils.
STEAM COILS — When used for preheating outdoor air in pressure or vacuum systems, an
immersion thermostat to control outdoor-air damper and fan motor is recommended. This
control is actuated when steam supply fails or condensate temperature drops below an
established level, such as 120 to 150 F.
A vacuum breaker should also be used to equalize coil pressure with the atmosphere when
steam supply throttles close. Steam should not be modulated when outdoor air is below 40 F.
On low-pressure and vacuum steam-heating systems, the thermostat may be replaced by a
condensate drain with a thermal element. This element opens and drains the coil when
condensate temperature drops below 165 F. Note that condensate drains are limited to 5
psig pressure.

- 9 -
CONDENSATE DRAIN
Install a trapped condensate drain line at unit drain connection. Use 1-in. standard pipe.
Measure maximum design negative static pressure upstream from the fan. Referring to Fig.
hereunder, height “H” must be equal to or larger than negative static pressure at design
operating conditions. Prime enough water in trap to prevent losing seal (Differential 1). When
the fan starts, Differential 2 is equal to the maximum negative static pressure.
Negative pressure :
H1 = 2 P
H2 = H1/2
At start up, check by hand with 1 bottle of water that condensate drain run properly.
7. ELECTRICAL CONNECTION
MOTOR CONNECTION
Please refer to the start up and maintenance leaflet of E-motor manufacturer supplied with
this unit (carefully choose cable diam. acc. power, length, starting arrangements … etc and
follow electrical connection instructions).
If unit is supplied with air inlet damper, check fan can be started only if damper is previously
open.
At start up, check fan rotation direction. Absorbed intensity can not exceed intensity stamped
on motor.
NOTE : Factory-supplied drives are prealigned and tensioned, however, we recommend that
you check the belt tension and alignment before starting the unit. Always check the drive
alignment after adjusting belt tension.
Make sure that fan shafts and motor shafts are parallel and level. The most common causes
of misalignment are nonparallel shafts and improperly located sheaves. Where shafts are not
parallel, belts on one side are drawn tighter and pull more than their share of the load. As a
result, these belts wear out faster, requiring the entire set to be replaced before it has given
maximum service.

- 10 -
ELECTRIC HEATERS
ELECTRICAL COILS CONTROL
Electric heaters box panel (not supplied) must control verify that minimum airflow
requirement (minimum coil face velocity, fpm) will be met, especially on applications where
variable air volume is supplied.
Electrical heaters must be switched off automatically in any case of fan stop. We recommend
an airflow pressure differential switch to prevent the heater from operating when the fan is
not in operation or airflow is restricted or insufficient.
At electric heater stop, a refreshment fan running time is required to de-energize the heater.
Fan must run approx. 10 mn. Check in the worse situation (inlet air max. temp.) that this time
is sufficient to cool the heaters.
In the case of 2 speeds fan or variable speed fan the heater power must be reduced
proportionally.
Over-temperature protection
Each heater has factory-installed manual reset thermal cutout for over-temperature
protection. The manual reset cutout is a bi-metal disk-type cut-out. This thermal cutout is
load carrying and is installed in each heater sub-circuit.
Typical over-temperature origin :
- Heaters are energized while fan is not running
- Dirty filters
- Dampers stay closed
- Belts wear
Typical heater wiring schematic

- 11 -
8. MAINTENANCE
FAN - MOTOR - DRIVE
Electric motors are supplied with life greased ball bearings.
R Type fan are supplied with life greased ball bearings.
F Type fans have to be grease filled every 20 000 Hours
Belt & Pulleys
When installing or replacing belts, always use a complete set of new belts. Mixing old and
new belts will result in the premature wear or breakage of the newer belts.
1. Always adjust the motor position so that V-belts can be installed without stretching over
grooves. Forcing belts can result in uneven stretching and a mismatched set of belts.
2. Tighten belts by turning motor-adjusting jackscrews. Turn each jackscrew an equal
number of turns.
3. Equalize belt slack so that it is on the same side of belt for all belts. Failure to do so may
result in uneven belt stretching.
GENERAL MAINTENANCE
Monthly
a) Clean filters and/or replace 2 times / year.
Quarter
a) Grease fill fan and motor bearings acc. Manufacturer instructions.
b) Check belts and pulley estate and tighten.
Yearly
Additionally to previous controls :
a) Check general aspect of the whole air unit externally as well as internally (corrosion) and
clean all parts.
b) Check damper, adjust open/close position. (Do not grease the damper bearing when
material is nylon).
c) Check the condensate drain and condensate trolley contents
e) Clean the fan rotor.
SPARE PARTS
Parts number, codification and designation are identified on supply of serial number stamped
on the air unit identification plate.

- 12 -
14 Avenue Cassiopée
33160 Saint Médard en Jalles
Tel : 05 56 70 14 00 - Fax : 05 56 70 14 09
www.aircalo.fr
M 5-08-09
Table of contents
Popular Fan manuals by other brands
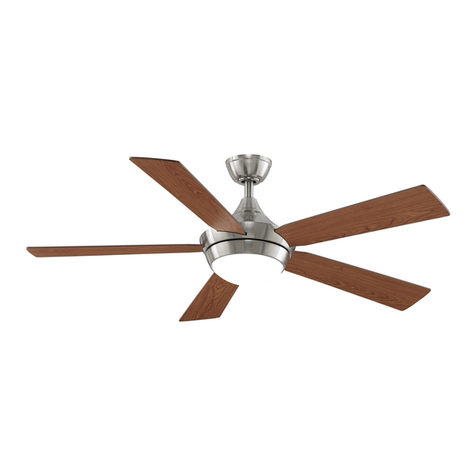
Fanimation
Fanimation FP8062 Series owner's manual
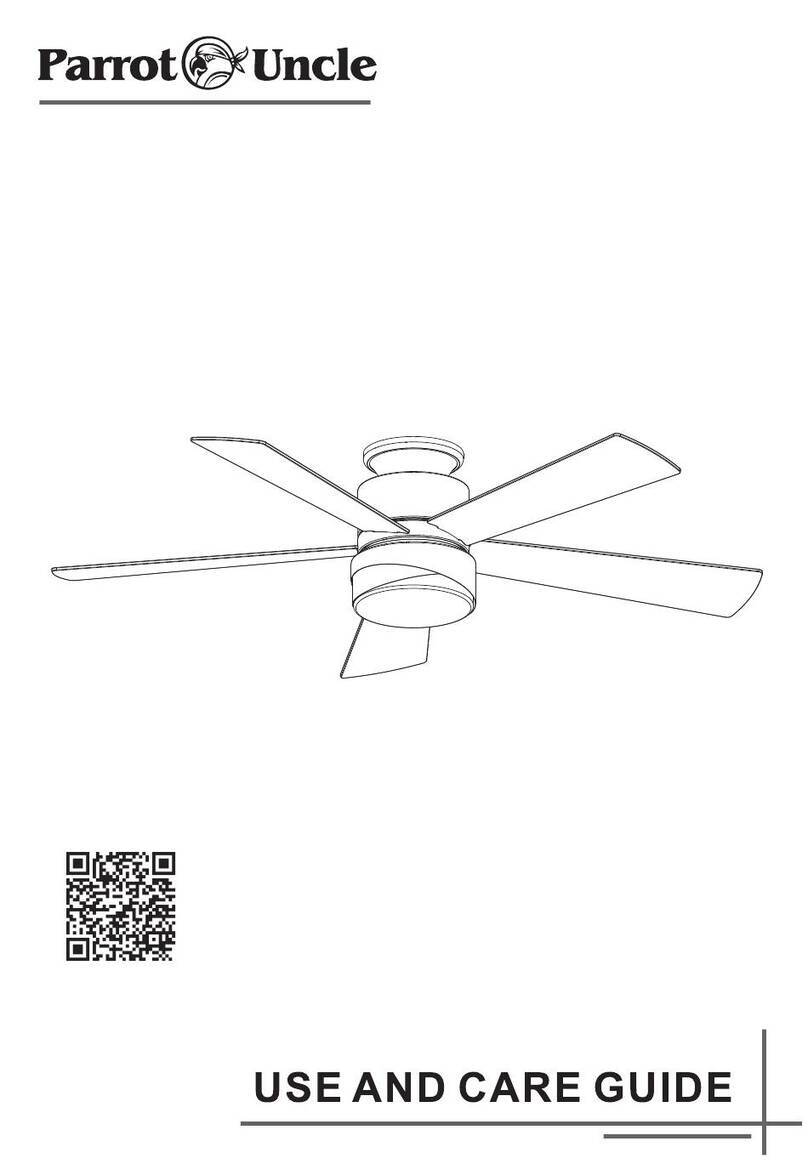
Parrot Uncle
Parrot Uncle F6115-SMART Use and care guide
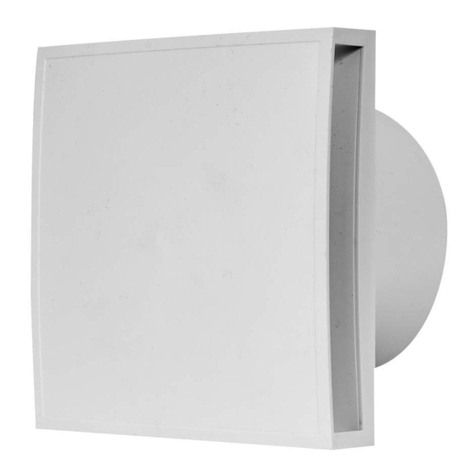
Europlast
Europlast EET Series instruction manual

Addvent
Addvent Whisper Silent AVX100WT Installation and Maintenance
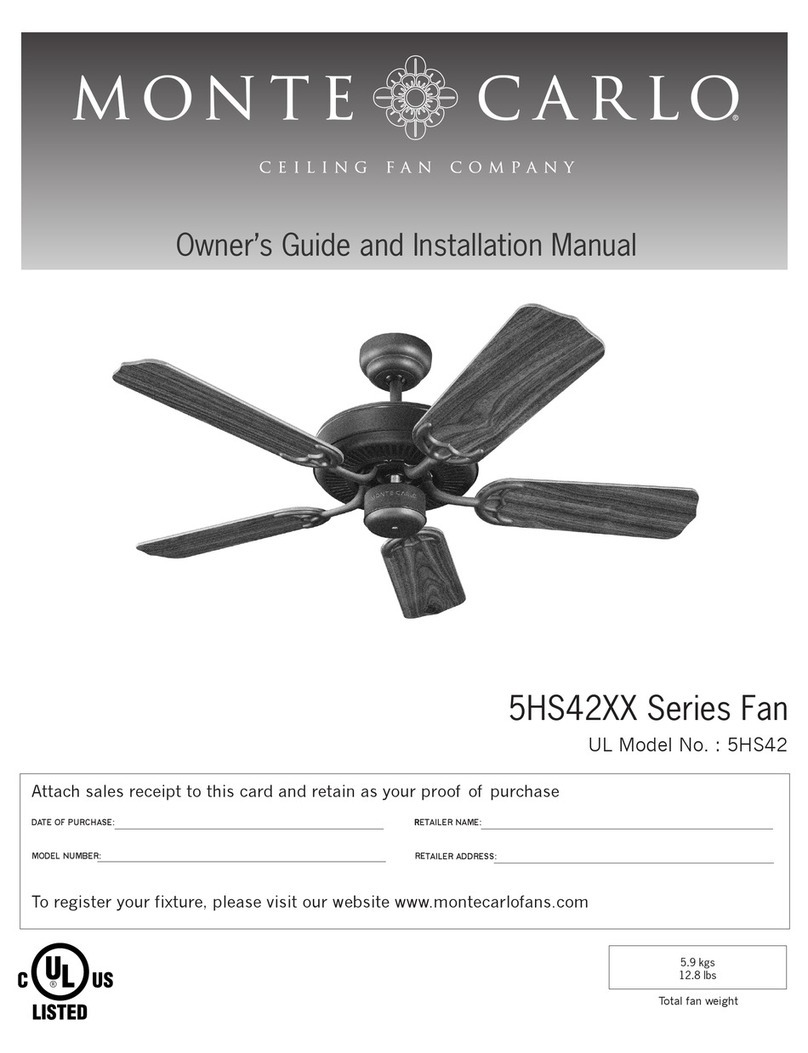
Monte Carlo Fan Company
Monte Carlo Fan Company 5HS42XX Series owner's guide
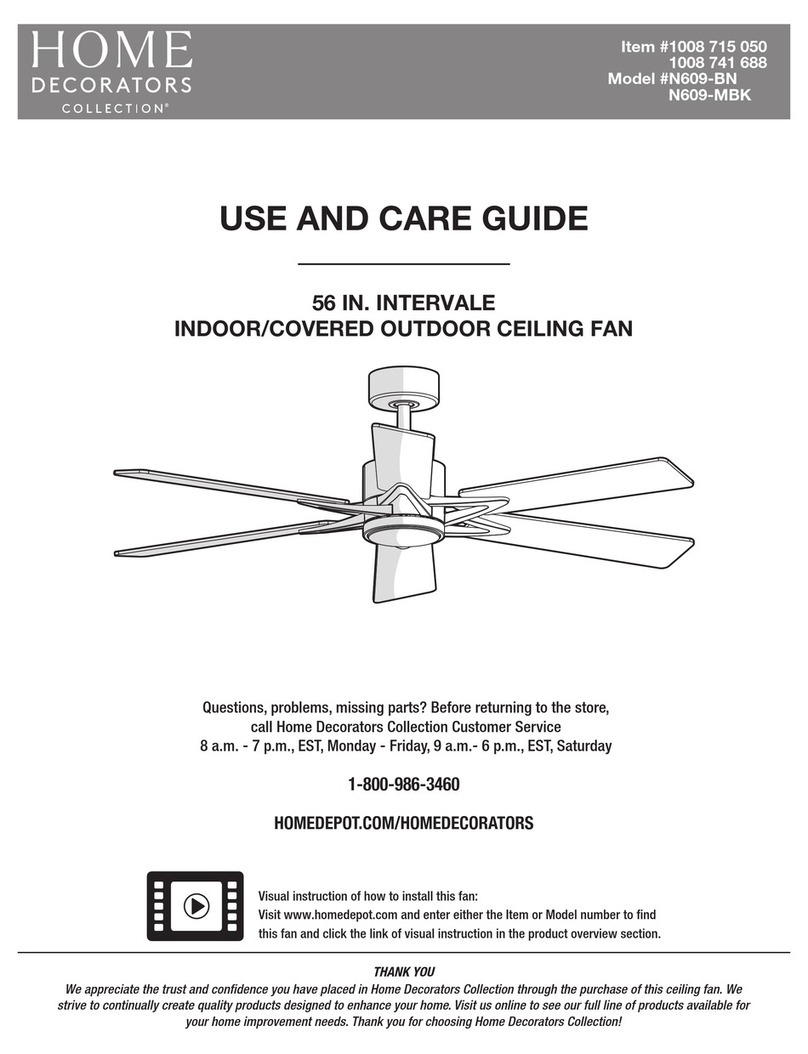
Home Decorators Collection
Home Decorators Collection N609-BN Use and care guide

Siegenia
Siegenia AERO AEROMAT VT WRG 1000 Operating and care instructions
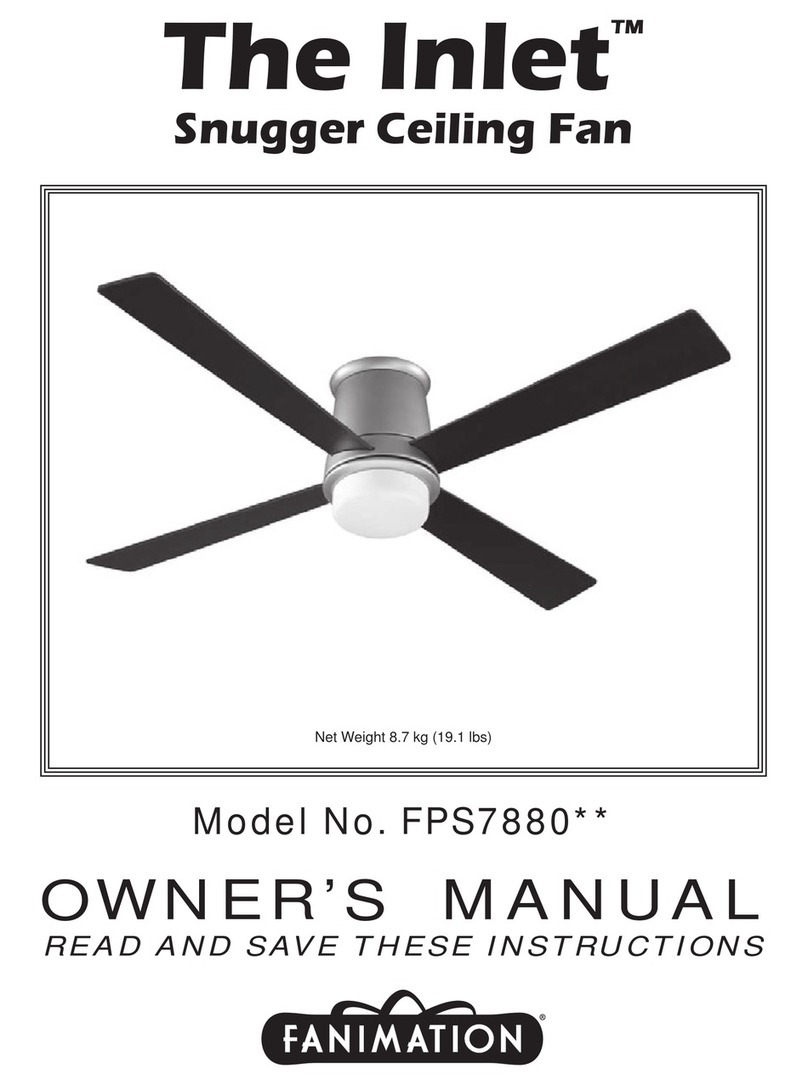
Fanimation
Fanimation The Inlet FPS7880 Series owner's manual

Singer
Singer SFR40-5 BL instruction manual
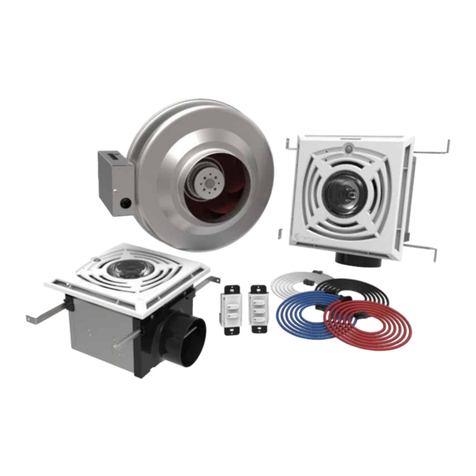
Fantech
Fantech Serenity Series Installation and operation manual

BLAUBERG Ventilatoren
BLAUBERG Ventilatoren Turbo 100 user manual

Vertiv
Vertiv CoolBlastT Series operating instructions