Alcolizer HH3 User manual

REF: HH3/HH4/LE5 & Centurion Sample Module Calibration WI V2 Page 1 © Alcolizer Technology
Uncontrolled when printed
HH3, HH4, LE5 and Centurion Sample
Module Calibration WI
Work Instruction
Di
Disclaimer –Internal Document note to reader
This document is intended for use within Alcolizer Technology only.
The contents of this document are not to be disclosed to parties outside of the
Company without permission from the appropriate Department Manager.
CHANGE STATUS
Version Number
Reason for Issue
Date
Authority
V2
Section 2.1 cleaning procedure
added. Section 8 requirements for
configuration loading upon
firmware change
April 2020
Product and
Quality
Manager
V1
Initial Release
Feb 2020
R&D and
Quality
Manager

REF: HH3/HH4/LE5 & Centurion Sample Module Calibration WI V2 Page 2 © Alcolizer Technology
Uncontrolled when printed
Contents
1Introduction .......................................................................................................................3
1.1 Risks and safety concerns ...........................................................................................3
1.2 Training requirements.................................................................................................3
Competency assessment to be completed prior to performing the tasks............................3
2Getting Started...................................................................................................................3
2.1 Cleaning Procedure .....................................................................................................4
3Device Parts .......................................................................................................................4
3.1 HH3/HH4 and LE5 Sample Module .............................................................................4
3.2 Centurion Sample Module ..........................................................................................5
3.3 HH3/HH4 and LE5 Main Module.................................................................................5
4Tools...................................................................................................................................6
5Calibration Workflow.........................................................................................................7
6Visual Inspection................................................................................................................8
7Download Logs and Update Firmware ..............................................................................8
8Configuration ...................................................................................................................10
9Pre Calibration Checks .....................................................................................................11
9.1 Initial Data Collection................................................................................................12
9.2 Device Preparation....................................................................................................12
9.3 Sample Module Leak Checks.....................................................................................13
9.4 Pump Volume Checks................................................................................................13
9.5 Backup Battery check................................................................................................13
9.6 Fuel Cell Temperature...............................................................................................13
9.7 Fuel Cell Voltage........................................................................................................14
9.8 Wet Gas Calibration ..................................................................................................14
9.9 Dry Gas Calibration....................................................................................................14
9.10 Calibration Gas.......................................................................................................15
9.11 Calibrate.................................................................................................................15
9.12 Calibration Result Display......................................................................................15
9.13 Validation Tests .....................................................................................................16
9.14 Calibration Lock Out ..............................................................................................16
10 Completing the final check List........................................................................................17
Annexure 1 - Dry Gas Conversion Table ..................................................................................18
Annexure 2 - Calibration Records Sheet.................................................................................19
Annexure 3 - Codes and Troubleshooting ...............................................................................20

REF: HH3/HH4/LE5 & Centurion Sample Module Calibration WI V2 Page 3 © Alcolizer Technology
Uncontrolled when printed
1Introduction
This Calibration Manual details the procedures for performing the calibration of the
Alcolizer alcohol breath testing device.
This manual is divided into various sections and sub-sections to enable the authorised
technician to access the required information with ease. It includes cautions and notes
applicable to calibration of Alcolizer alcohol breath testing device.
IMPORTANT NOTE
Calibration of the devices should only be performed by a qualified technical person using
certified alcohol solutions dry gas standards.
1.1 Risks and safety concerns
•Poor or inadequate lighting;
•Ergonomic hazards;
•Extremes of temperature;
•Slip, trip and fall hazards;
•Electrical hazards (e.g. appliances, power sockets, etc.);
•Fire hazards and Explosion Prevention
•Chemical hazards (e.g. cleaning products); and
•Fire and Explosion Prevention
•Manual handling
•Hazardous exposures (i.e. low humidity room, full gas bottle on the bench, fumes for
soldering, new assembly machines –don’t get in the way of an automated machine)
•RSI (i.e. crimping
•Alerts/fire alarm
•Onsite risk assessment –WHS manual
1.2 Training requirements
Competency assessment to be completed prior to performing the tasks.
2Getting Started
Prior to beginning the calibration procedure, ensure the following steps are taken and
precautions adhered too:
1. Read the entire manual carefully before calibrating the device for the first time.
2. If a dry gas standard is being used, ensure that the gas reference value has been
certified and a certification certificate is attached to the cylinder.
NOTE
Fuel cell sensors have different sensitivity parameters to wet and dry reference gas
standards, a correction factor must be applied when using dry gas as the calibration
standard to correctly correlate with wet gas solution standard.

REF: HH3/HH4/LE5 & Centurion Sample Module Calibration WI V2 Page 4 © Alcolizer Technology
Uncontrolled when printed
2.1 Cleaning Procedure
Morning start-up
•Turn gas bottles and compressed air valve on, Check you have sufficient gas before
calibrating.
•Ensure Aircon is on and the room temp is between 21-25 degrees Celsius.
•Check status of precalibration units in the service area and continue processing ie
calibrate, QC, dispatch to warehouse.
•Check recalibration tubs for units that require servicing. (Check for priority units &
ensure units dated earliest are processed first).
•Carry out calibration and repair as per work instructions.
Afternoon shut-down (15 minutes prior to end of day Monday to Thursday)
•Tidy workstation (Ensure if leaving units on bench they are in a tidy and organised
manor though it’s preferable to complete a set and clear then bench).
•Turn off gas bottles and compressed air line and purge the lines.
•Turn off computers & lights.
30 minutes prior to COB on Friday in addition to Afternoon shutdown protocol above
perform the following
•A deep clean. This includes sweeping, vacuum, wipe down benches, empty bins
make sure everything is clean and organised for Monday morning
3Device Parts
3.1 HH3/HH4 and LE5 Sample Module

REF: HH3/HH4/LE5 & Centurion Sample Module Calibration WI V2 Page 5 © Alcolizer Technology
Uncontrolled when printed
3.2 Centurion Sample Module
3.3 HH3/HH4 and LE5 Main Module
NOTE: For Centurion Main Module service refer to Centurion Main Module Service WI

REF: HH3/HH4/LE5 & Centurion Sample Module Calibration WI V2 Page 6 © Alcolizer Technology
Uncontrolled when printed
4Tools
•2mm Hex Screwdriver
•Torque Screwdriver with Phillips bit size PH1 and Hex bit number 2 (MUST be used
for pump and solenoid)
•Lint free microfiber cloth
•Henkel Loctite SF 7400 Coating –Red
•Super Lube - multipurpose synthetic-based oil with PTFE
•U-Tube manometer
•Small long nose pliers
•Scalpel
•Manual Calibration Station or Wet Gas Simulator
•Authorisation key
•Windows Computer with the latest version of AlcoCONNECT Toolbox (can be
downloaded from the web site https://www.alcolizer.com/software-updates/
Note
The torque screwdriver must be set to 30 ozf.in (21 cN.m).
Philips bit size PH1 to secure the solenoid and pump body. For the hex screws use the
Hex bit number 2.
ALWAYS CONFIRM THE SETTING BEFORE USE

REF: HH3/HH4/LE5 & Centurion Sample Module Calibration WI V2 Page 7 © Alcolizer Technology
Uncontrolled when printed
5Calibration Workflow
Visual inspection for physical damage to
the case-set or LCD, etc
Damaged:
Repair
Download logs and Update Firmware.
Charge the battery
(If Zero bars present )
Upload Configuration File
Calibrate
Internal Systems Check Fail:
Repair
Validation Testing
3 Positives, 3 Negatives
If positives within +/- 5% proceed
Battery won’t charge:
Replace the Battery
Log Calibration Data for Calibration
Certificate.
Pre Calibration Checks
If positives not within +/- 5%
Proceed to Repairs

REF: HH3/HH4/LE5 & Centurion Sample Module Calibration WI V2 Page 8 © Alcolizer Technology
Uncontrolled when printed
6Visual Inspection
•Turn the device on and check for physical damage, specifically:
oCase back and front - Replace Damaged Case-Set
oScreen - Replacing the LCD
oWrist strap if applicable
oButtons
oCharging port
oUSB port
7Download Logs and Update Firmware
•Device log records should be downloaded before any firmware updates, service or
calibration is performed.
•Connect the device to AlcoCONNECT Toolbox via the USB port.
•Enter Password 28128201 in the Set Access Field.
•Read Event Logs then save to file by date and serial number i.e.
20190416_24000745-40000987.
For example for Alcolizer staff save to A:\Service\Customer Logs
•Set the file path for Firmware location.
•File>>Options
•Firmware Upgrade Location tab
•Browse and select the firmware file
•Technician>>Check for Firmware Updates

REF: HH3/HH4/LE5 & Centurion Sample Module Calibration WI V2 Page 9 © Alcolizer Technology
Uncontrolled when printed
•Select Upload Do Not Close until Done appears
•Set device time if necessary, i.e. if the Main PCBA or backup battery has been
replaced. If the customer has made a request for change of time.
•Tools>>Set Device Time
•Sync Device to PC or Set Manually

REF: HH3/HH4/LE5 & Centurion Sample Module Calibration WI V2 Page 10 © Alcolizer Technology
Uncontrolled when printed
Note: A code error 32 is the most common error displayed after an update. Press the
power off key to turn the unit off. Then press the power key again to turn on the unit.
To avoid this error, ensure device is always switched off between firmware and
configuration uploads.
8Configuration
•Configuration files must be uploaded to the device when:
oA change to firmware has been applied to the device. This can either be an
upgrade or downgrade.
NOTE: Firmware downgrade is not a supported process and an error will occur.
Error 196/218: Could not set 1249 Configuration item not supported by device. Indicating
configuration reload is required.
oA PCBA is replaced.
•Connect the device to AlcoCONNECT via the USB port.
•Tools>>Device Config.
•Open from File.
•Select Configuration File.
•Add Serial Numbers and tick ✓Enable Upload (if the serial numbers are correct on
the device, this step is not necessary)
•Select Write to Device and Close.

REF: HH3/HH4/LE5 & Centurion Sample Module Calibration WI V2 Page 11 © Alcolizer Technology
Uncontrolled when printed
9Pre Calibration Checks
•Calibration should be performed in an environment where temperature is controlled
to between 21 to 25 degrees Celsius.
•Devices must be stabilised at temperature and off charge for a minimum of 1 hour
before performing any calibration or validation testing. 1.5 hours is preferred, 1 hour
is the absolute minimum.
•Ensure the gas reference value is certified and the supplier certification is attached
to the gas bottle or wet gas simulator.
•Centurion sample modules must be installed into an LE5 main module for calibration
•Remove the centurion sample module from the main module
1. Turn off the unit. Open the back of the unit and locate the red sample module.
Unscrew the bolt
2. Angle to lift off the bolt pin. Lower slightly then pull the module out
•Remove the red back cover and install on a body D cover (same as used for LE5)
•To remove the sample module from the red cover, insert a 3.5mm flat head
screwdriver into the side groove
•Move in an upward direction to dislodge the sample module
•Ensure the LE5 main module being used is running firmware version 1.33 or later
•Charge the device if zero bars are present using the Alcolizer Charging Cradle or
Power supply, Switch mode, 12V/1000mA.
•Fuel cell sensors have different sensitivity parameters to wet and dry reference gas
standards, a correction factor must be applied. PPM to Dry Gas Conversion Table see
Annexure 1: Reference Gas PPM to g/100mL BAC Dry Gas Conversion Table
•Refer to the Alcolizer device specific Alcohol Tester User Manual for:
oDevice operation function descriptions

REF: HH3/HH4/LE5 & Centurion Sample Module Calibration WI V2 Page 12 © Alcolizer Technology
Uncontrolled when printed
oActive and Passive breath test operation procedures
oUser Menu function descriptions
oAlcoCONNECT Toolbox download and operation
9.1 Initial Data Collection
•Note all pre-calibration data on the Alcolizer Calibration Records Sheet.
[See Annexure 2 - Calibration Records Sheet ]
•To access the User Menu press both the arrow keys at the same time and release.
•Using an arrow key navigate to About, press the Test button twice for:
oSerial Numbers
oFirmware Versions
oFor detailed information, select About from the menu and on the following
screen, press the test button for 5 seconds
oNote any error codes displayed on the screen, or any faults reported by the customer for
error code actions refer to Annexure 3 - Codes and Troubleshooting
oRecord the serial number found on the back of the unit and cross reference against the
serial number on the about menu
9.2 Device Preparation
Activate the AuthKey as follows:
1. Switch on unit.
2. Insert the AuthKey Cal USB security key into USB port. The security key symbol will
be displayed on the display screen when the connection is recognised.
To perform all pre calibration checks, use calibration Authkey access to access special
menu> Technician> system checks

REF: HH3/HH4/LE5 & Centurion Sample Module Calibration WI V2 Page 13 © Alcolizer Technology
Uncontrolled when printed
9.3 Sample Module Leak Checks
•Arrow back up the System Check menu list to Battery Voltage
oConnect the U-Tube Manometer to the Spigot on the
device and note the Manometer top fluid level position
reading.
oPress the Test button for 10 seconds (a Click will be
heard when the Test button is first pressed. This is the
pump solenoid pulling-in).
oCheck for leak by observing the lower fluid level
stability. Determine if the fluid level is staying steady or
if it is slowly creeping upwards by more than 0.01mL
(one division) within the 10 seconds test period.
If higher there is an unacceptable leak.
Refer to: Sample System Leak Checks
9.4 Pump Volume Checks
•Calculate the difference between the top level and lower level
readings this must be between 0.11 –0.13mL.
•If the pump volume is outside of this range the volume will
need to be set. Refer to Setting Pump Volume
9.5 Backup Battery check
Backup battery must be at 2.8V or higher. If not battery to be replaced.
9.6 Fuel Cell Temperature
Fuel Cell Temperature should be ±2C of ambient temperature
If the Fuel Cell Temperature is outside of temperature parameters: ( Service technician to
perform the following)
•Check the Fuel Cell is sitting on the Fuel Cell pins that connect
it to the PBCA. Four pins on each side are inserted into the
four holes on both sides of the Fuel Cell.
•Check the Fuel Cell pins on the PCBA are connected to the
PCBA. If not replace the PCBA. Refer Replacing the PCBA
•Leave the device for another hour to reach ambient
temperature.
•Replace the Fuel Cell refer Replacing the Fuel Cell
Top
Lower

REF: HH3/HH4/LE5 & Centurion Sample Module Calibration WI V2 Page 14 © Alcolizer Technology
Uncontrolled when printed
9.7 Fuel Cell Voltage
If fuel cell voltage is out of range (0.05V-0.15V)the instrument will fail calibration. Refer to
error code table for repair instruction. Ensure voltage is stable.
Wet Gas Calibration
If using wet gas solution to calibrate you must ensure the following:
•A fresh mouthpiece is used each time.
•The distance between mouthpiece inlet and simulator output, is as short as possible
to prevent or reduce condensation occurring which may affect calibration accuracy.
•WARNING: Condensation will significantly affect accuracy.
•A heated delivery tube is a mandatory method to use with wet gas simulators.
•Set the flow regulator to 12Lt/min.
•The Wet Gas Simulator has fresh solution installed and the solution temperature is
maintained at 34oC.
•Record Certified Calibration Reference Solution Value on the Calibration Records
Sheet.
•For devices set to 1.2Litres breath volume using 4 tests per calibration (1 calibration
and 3 validation tests) the wet gas solution should be changed at 20 calibrations @
1.2L/test
9.8 Wet Gas Calibration
If using wet gas solution to calibrate you must ensure the following:
•A fresh mouthpiece is used each time.
•The distance between mouthpiece inlet and simulator output, is as short as possible
to prevent or reduce condensation occurring which may affect calibration accuracy.
•WARNING: Condensation will significantly affect accuracy.
•A heated delivery tube is a mandatory method to use with wet gas simulators.
•Set the flow regulator to 12Lt/min.
•The Wet Gas Simulator has fresh solution installed and the solution temperature is
maintained at 34oC.
•Record Certified Calibration Reference Solution Value on the Calibration Records
Sheet.
•For devices set to 1.2Litres breath volume using 4 tests per calibration (1 calibration
and 3 validation tests) the wet gas solution should be changed at 20 calibrations @
1.2L/test
9.9 Dry Gas Calibration
If using dry gas solution to calibrate you must ensure the following:
•Ensure the dry reference gas 200-220PPM ethanol (BAC:0.081-0.090g/100ml)
•Turn valve on (1 turn anticlockwise) to commence calibration procedure. Ensure
valve is turned off (clockwise) after completion of calibration procedure.
•Ensure tube to mouthpiece connection is a friction fit (finger tight)
•Ensure pre-set flow rate valve is 12lts/min
•Press on/off push button to start gas flow and release to stop

REF: HH3/HH4/LE5 & Centurion Sample Module Calibration WI V2 Page 15 © Alcolizer Technology
Uncontrolled when printed
9.10 Calibration Gas
•Select Special Access Menu>>Technician Menu >>Calibration >> Cal Gas
•Enter the Calibration Gas value. The Test button moves the underline curser, the
arrow buttons change the number of the digit that is underlined.
9.11 Calibrate
•Select Special Access Menu>>Technician Menu >>Calibration >> Calibrate
•Press the Test button to start the Calibration process.
•After the internal self-check is completed the Ready screen will display. If self-check
is unsuccessful and error code will be displayed.
•Press the Test button to start calibration sequence.
The device displays a countdown sequence, 13 –12 –11 –10 - … at one second
intervals:
•Turn on the Calibration Gas flow when count is at the 10 second count
•When the count reaches ‘0’ the device will take a sample of the Calibration
Gas –Analysing Sample will be displayed.
•Turn off the calibration gas flow after the device has taken a sample and the
beep tone has ceased
9.12 Calibration Result Display
Once the device has completed Analysing Sample, the Calibration Results screen is
displayed.
•Pre-Cal Result:This shows the calibration gas value for
the old gain value.
•New Gain:This shows the new calibration gain value.
•Reference Gas:This is the calibration reference gas value
•Flow Rate:This shows the measured flow rate of the
calibration gas
•Backup Battery:This shows the backup battery voltage.

REF: HH3/HH4/LE5 & Centurion Sample Module Calibration WI V2 Page 16 © Alcolizer Technology
Uncontrolled when printed
•Recovering:This is the fuel cell recovery period. When this time-out reaches 0,
Press Key to continue will display.
•Press either the Test button or arrow buttons to return to the Calibration Menu
screen
9.13 Validation Tests
Validation tests must be performed to verify the calibration accuracy.
•Record the results of 3 Calibration Gas Tests with Zero test between
o1st Calibration Gas test
o1st Zero Test
o2nd Calibration Gas test
o2nd Zero
o3rd and final Calibration Gas test
o3rd and final Zero test
•All readings must be between ±5 percent of the reference gas value or as required
by local authority.
•If the readings are consecutively increasing or decreasing perform a 4th test
•If the 4th test continues to increase or decrease recheck the pump volume.
•After checking the pump volume perform an additional test, if the result continues
to increase or decrease replace the fuel cell.
•Ensure zero is the last test performed on the unit
•Ensure the screen says 190 days to recal
•Clean the unit and recharge the battery before returning to the customer
9.14 Calibration Lock Out
If using calibration authorisation key, once the device has been calibrated, another
calibration cannot be performed for 24 hours.

REF: HH3/HH4/LE5 & Centurion Sample Module Calibration WI V2 Page 17 © Alcolizer Technology
Uncontrolled when printed
10 Completing the final check List
Task
Completed
Serial number has been recorded
Yes / No
Firmware has been checked and upgraded if required
Yes / No
The serial number has been crossed checked
Yes / No
Fuel cell voltage is stable and not out of range
Yes / No
Back up battery has 2.8+ volts
Yes / No
Fuel cell temp is correct ±2°C
Yes / No
Initial gain has been recorded
Yes / No
Pump has been checked, clicking sound and for leaking
Yes / No
Check that gas reference used has a certificate attached to cylinder
Yes / No
Calibration gas value has been set in service menu
Yes / No
Device has been calibrated
Yes / No
New gain has been recorded <<not necessary?>>
Yes / No
Post calibration checks have been completed, passed and recorded
Yes / No
Install sample module into Centurion ( Centurion only)
Yes / No
After install on centurion perform zero test, positive test then final zero test
(Centurion only)
Yes / No
The unit has been given a final zero test
Yes / No
The unit now displays the correct calibration remain days depending on location
Yes / No
The unit has been cleaned
Yes / No

REF: HH3/HH4/LE5 & Centurion Sample Module Calibration WI V2 Page 18 © Alcolizer Technology
Uncontrolled when printed
Annexure 1 - Dry Gas Conversion Table
Dry Gas PPM to g/100mL BAC Conversion Table for Alcolizer
Technology
Fuel Cell Sensor Products
PPM
g/100mL
PPM
PPM
PPM
g/100mL
Value
Value
g/100mL
Value
g/100mL
Value
150
0.061
175
0.071
200
0.081
225
0.092
151
0.061
176
0.072
201
0.082
226
0.092
152
0.062
177
0.072
202
0.082
227
0.092
153
0.062
178
0.072
203
0.083
228
0.093
154
0.063
179
0.073
204
0.083
229
0.093
155
0.063
180
0.073
205
0.083
230
0.094
156
0.063
181
0.074
206
0.084
231
0.094
157
0.064
182
0.074
207
0.084
232
0.094
158
0.064
183
0.074
208
0.085
233
0.095
159
0.065
184
0.075
209
0.085
234
0.095
160
0.065
185
0.075
210
0.085
235
0.096
161
0.066
186
0.076
211
0.086
236
0.096
162
0.066
187
0.076
212
0.086
237
0.096
163
0.066
188
0.077
213
0.087
238
0.097
164
0.067
189
0.077
214
0.087
239
0.097
165
0.067
190
0.077
215
0.088
240
0.098
166
0.068
191
0.078
216
0.088
241
0.098
167
0.068
192
0.078
217
0.088
242
0.098
168
0.068
193
0.079
218
0.089
243
0.099
169
0.069
194
0.079
219
0.089
244
0.099
170
0.069
195
0.079
220
0.09
245
0.1
171
0.07
196
0.08
221
0.09
246
0.1
172
0.07
197
0.08
222
0.09
247
0.101
173
0.07
198
0.081
223
0.091
248
0.101
174
0.071
199
0.081
224
0.091
249
0.101

REF: HH3/HH4/LE5 & Centurion Sample Module Calibration WI V2 Page 19 © Alcolizer Technology
Uncontrolled when printed
Annexure 2 - Calibration Records Sheet

REF: HH3/HH4/LE5 & Centurion Sample Module Calibration WI V2 Page 20 © Alcolizer Technology
Uncontrolled when printed
Annexure 3 - Codes and Troubleshooting
Error Number
Error/Warning
When
Description
Action
6
Error
Starting a test
Fuel cell voltage is not
stable
Replace fuel cell. If the
error continues, replace
the sample module PCBA.
7
Error
During calibration
Gain Too Low
Assuming the calibration
procedure is being carried
out correctly:
Check for leaks and pump
volume.
Ensure the solenoid is
pulling.
If everything is okay,
replace the fuel cell.
8
Error
During calibration
Gain Too High
Assuming the calibration
procedure is being carried
out correctly:
Check for leaks and pump
volume.
Ensure the solenoid is
pulling.
If everything is okay,
replace the fuel cell.
15
Error
Starting a test
Fuel cell voltage Too
Low
Replace fuel cell. If the
error continues, replace
the sample module PCBA.
16
Error
Starting a test
Fuel cell voltage Too
High
Replace fuel cell. If the
error continues, replace
the sample module PCBA.
30
Error
Start-up (Restart)
A watchdog reset has
occurred
Reload firmware and
configuration files.
31
Error
Start-up
Settings have been
reset to factory defaults
Reload firmware and
configuration files.
Other manuals for HH3
1
This manual suits for next models
3
Table of contents
Popular Control Unit manuals by other brands
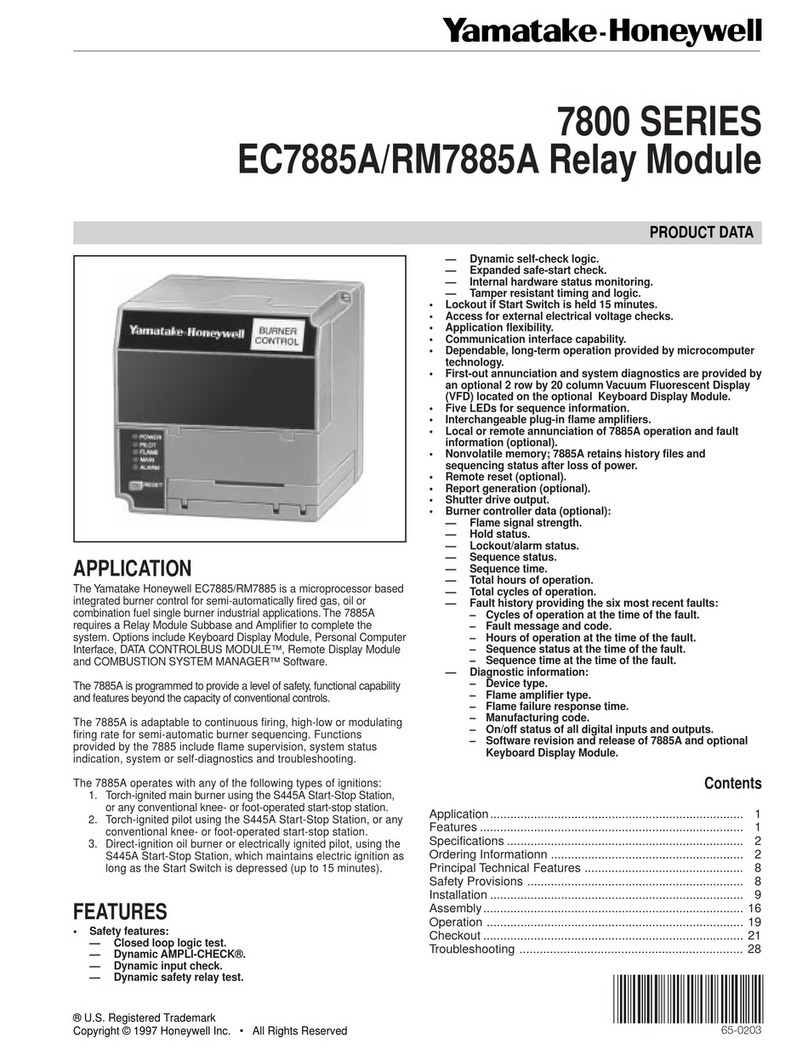
Yamatake-Honeywell
Yamatake-Honeywell 7800 Series Product data
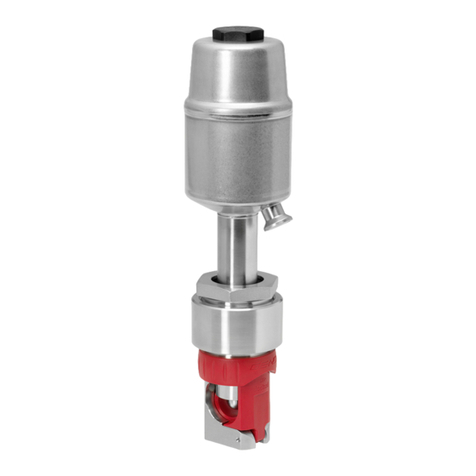
GEM
GEM Q40 operating instructions
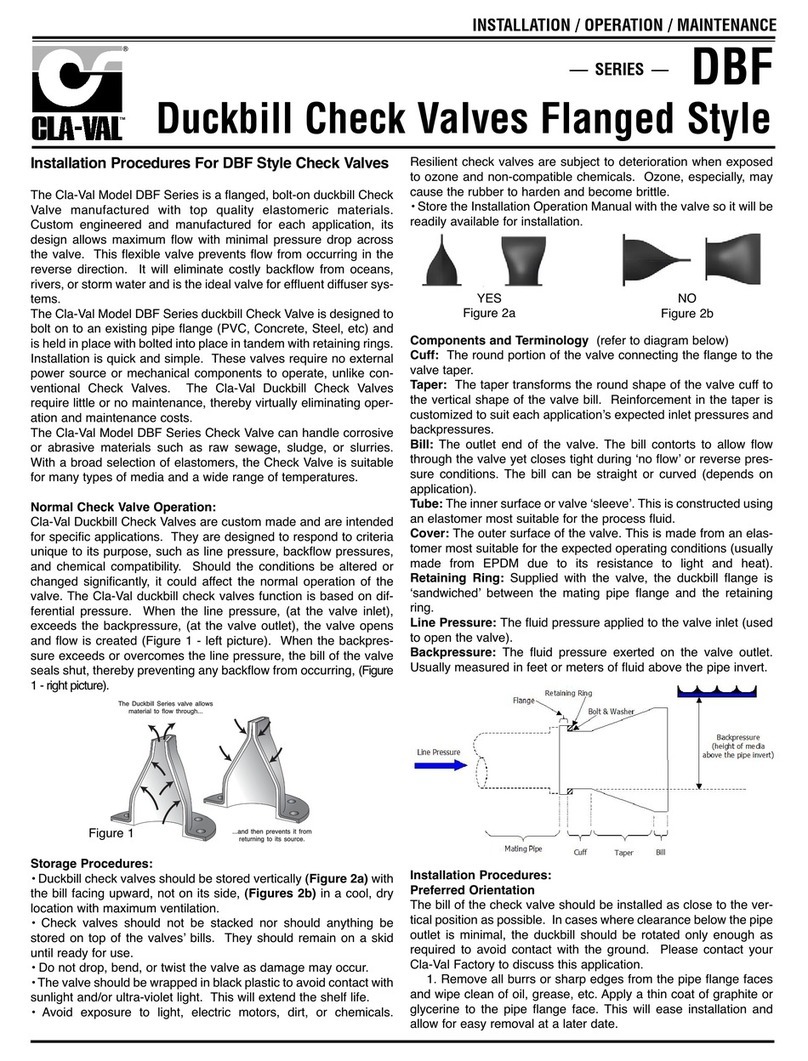
CLA-VAL
CLA-VAL DBF Series Installation operation & maintenance
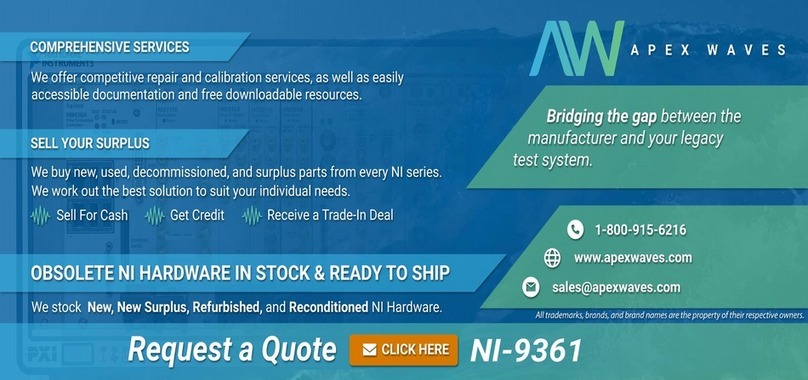
National Instruments
National Instruments NI-9361 CALIBRATION PROCEDURE

Nordson
Nordson Rhino SD2 CE manual
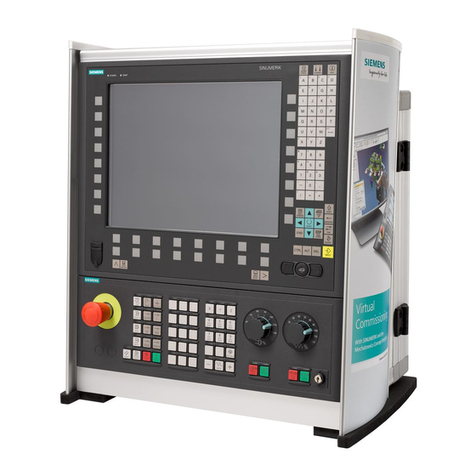
Siemens
Siemens SINUMERIK 840D Diagnostics guide
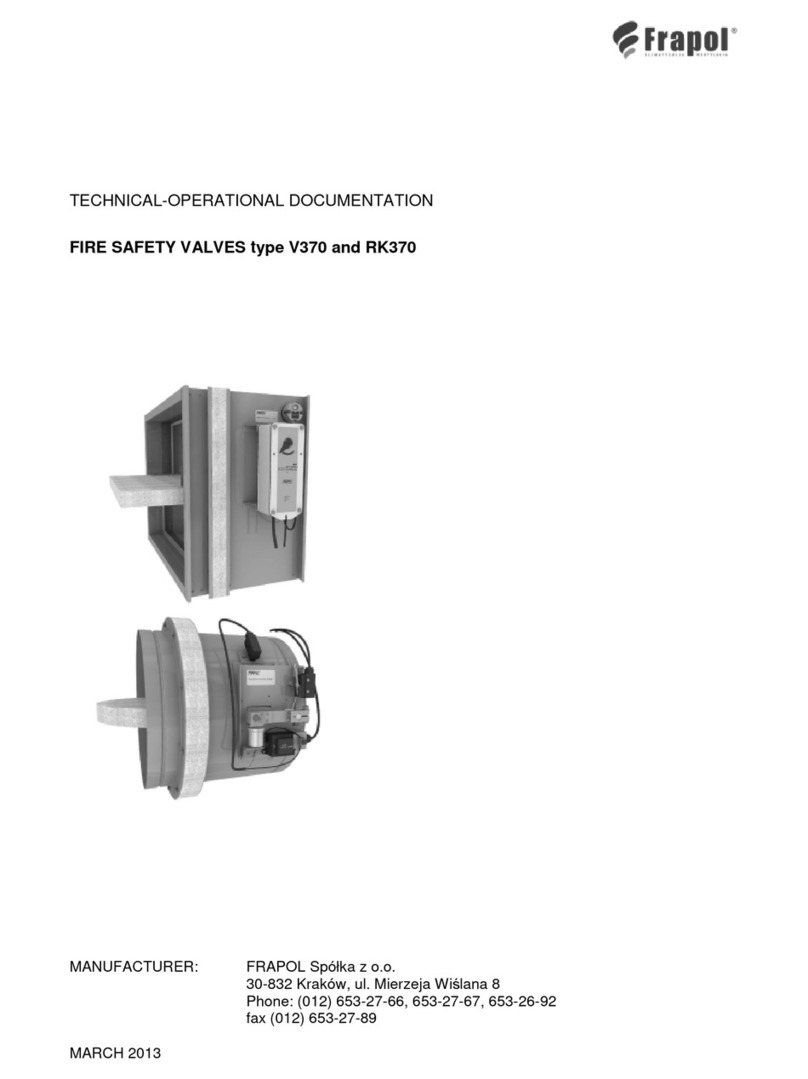
Frapol
Frapol V370 TECHNICAL-OPERATIONAL DOCUMENTATION
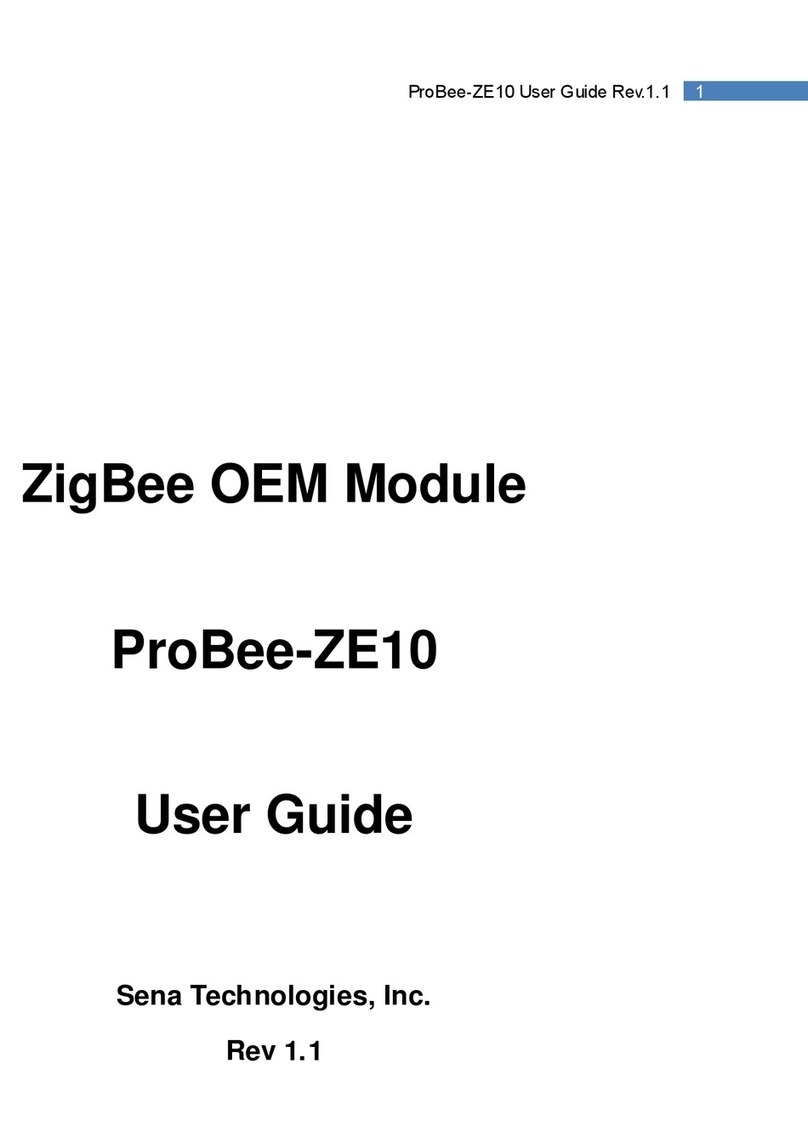
Sena
Sena ProBee ZE10 user guide
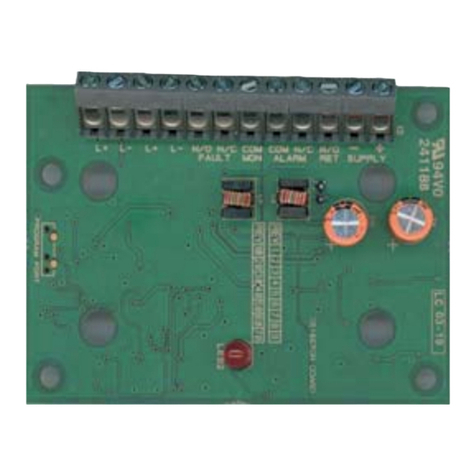
FireClass
FireClass FC410BDM Installation notes
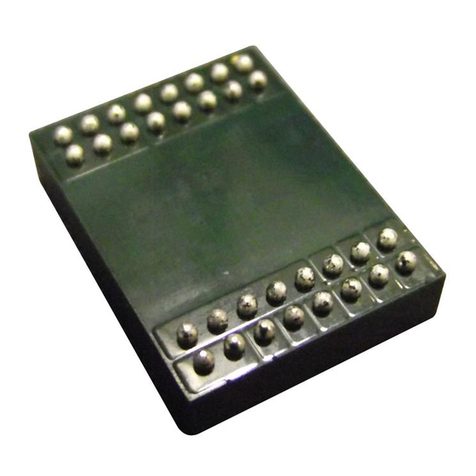
Linear Technology
Linear Technology LTM2892-I Demo Manual
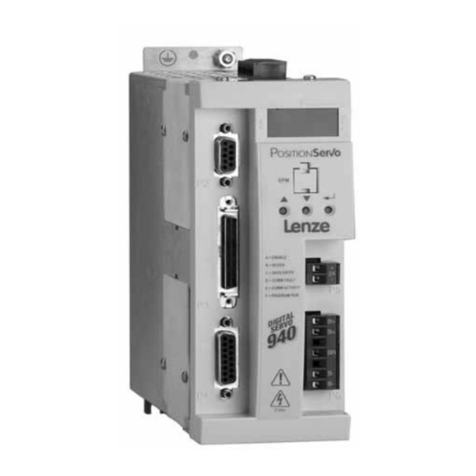
Lenze
Lenze AC Tech MotionView OnBoard PositionServo... reference guide
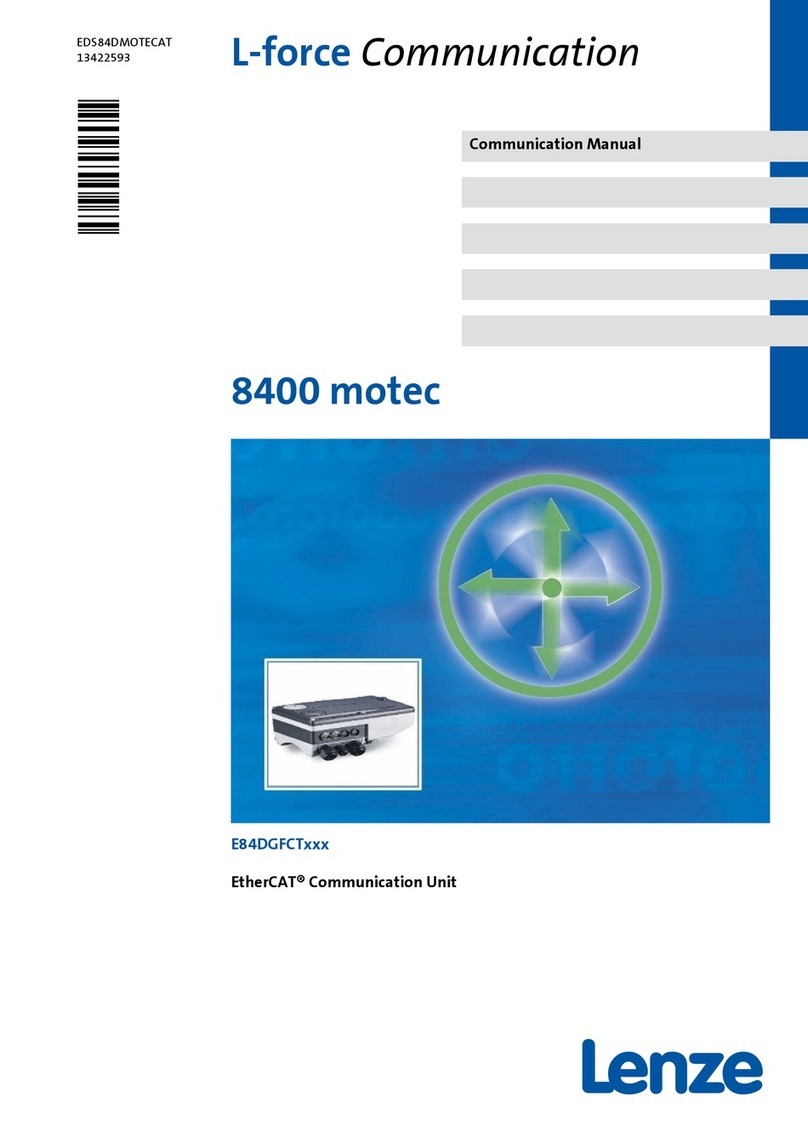
Lenze
Lenze 8400 motec Series Communications manual