Algas SDI Phoenix SH Manual

Models: SH100 – SH200
Operations & Maintenance
Manual
151 South Michigan Street, Seattle, Washington, USA 98108
Tel: 206-789-5410 Fax: 206-789-5414 Web: www.algas-sdi.com
This manual covers units built after S/N:
FILE: MANUAL PN 57002 SH100-SH200 rev 05-18-2022

WARNING
Read the OPERATION MANUAL before operating this equipment.
This equipment uses LPG and Natural Gas – flammable
fuels. Inherent hazards exist and a thorough
understanding of the equipment is required to allow safe
operation and maintenance.
Allow only a TRAINED and FULLY QUALIFIED
PERSON to service this equipment.
Any time a component must be replaced, use the same
type, model, etc. DO NOT SUBSTITUTE! The
consequences from such actions are unpredictable
and may lead to dire consequences.

Symbols and Conventions
Special symbols are used to denote hazardous or important information.
You should familiarize yourself with their meaning and take special
notice of the indicated information.
Please read the following explanations thoroughly.
GENERAL WARNING OR CAUTION
Indicates hazards or unsafe practices which can result in
damage to the equipment or cause personal injury. Use
care and follow the instructions given.
FLAMMABLE GAS HAZARD
Indicates a potential hazard which can result in severe
personal injury or death. Use extreme care and follow the
instructions given.
ELECTRICAL DISCONNECT REQUIRED
Indicates a potentially dangerous situation which can result
in severe personal injury or death or damage to equipment.
Use great care and follow the instruction given.
PARTS AND PRICES
For parts and prices contact your Algas-SDI distributor.
ASDI CONTACT NUMBERS
If you have questions, need help with your equipment,
or want information on other products, contact your
distributor or Algas-SDI at:
Telephone: +1 206 762 4357
Facsimile: +1 206 789 5414
Email: sales@algas-sdi.com
Internet: http://www.algas-sdi.com

Table of Contents
1. INTRODUCTION................................................................................................................................... 1
PRODUCT DESCRIPTION .............................................................................................................................. 1
MAJOR COMPONENTS.................................................................................................................................. 2
2. INSTALLATION .................................................................................................................................... 3
HANDLING ................................................................................................................................................... 3
STORAGE.................................................................................................................................................... 3
CHECKLIST BEFORE INSTALLATION............................................................................................................... 4
INTAKE ........................................................................................................................................................ 4
EXHAUST .................................................................................................................................................... 4
ACCESS ...................................................................................................................................................... 4
ENVIRONMENT............................................................................................................................................. 4
PREPARING THE BURNER............................................................................................................................. 4
INSTALLING THE FLAME SUPERVISION........................................................................................................... 5
INSTALLING THE IGNITER .............................................................................................................................. 6
CHAMBER WALL........................................................................................................................................... 6
BURNER MOUNTING..................................................................................................................................... 7
BURNER PIPING........................................................................................................................................... 8
SUPPLY PIPING ........................................................................................................................................... 8
SUPPLY PIPING ........................................................................................................................................... 9
CHECKLIST AFTER INSTALLATION ................................................................................................................. 9
PREPARE FOR START UP/ADJUSTMENT ...................................................................................................... 10
3. OPERATION ......................................................................................................................................... 1
INITIAL SETUP ............................................................................................................................................. 1
STEP 1: RESET THE SYSTEM ........................................................................................................................ 2
STEP 2: IGNITE THE BURNER ........................................................................................................................ 2
STEP 3: SET THE HIGH FIRE FUEL FLOW....................................................................................................... 3
STEP 4: SET THE LOW FIRE FUEL FLOW ....................................................................................................... 3
STEP 5: STOP PROCEDURE.......................................................................................................................... 4
4. MAINTENANCE.................................................................................................................................... 5
MAINTENANCE............................................................................................................................................. 5
MONTHLY CHECKLIST (OPTIONAL)................................................................................................................ 5
ANNUAL CHECKLIST..................................................................................................................................... 6
5. TROUBLESHOOTING.......................................................................................................................... 1
TROUBLESHOOTING PROCEDURES ............................................................................................................... 1
SPARE PARTS LIST MODELS SH100 –SH200.............................................................................................. 3
SPARE PART LIST MODELS SH100 –SH200................................................................................................ 4

Algas-SDI Operation and Maintenance Manual - SH100-SH200 2-1
1. INTRODUCTION
Product Description
The Phoenix SH (Simple Heat) packaged burner is a direct-fired nozzle-
mix burner, that utilizes an integral air blower designed to operate with
fixed combustion air over a wide turndown range.
The Phoenix SH burners are available in three models all with straight
combustors.
SH100 (1,000,000 Btu/hr)
SH150 (1,500,000 Btu/hr)
SH200 (2,000,000 Btu/hr
For performance and operational specifications refer to the Phoenix SH
Specification Sheet.
Figure 1.1 – Phoenix SH Burner

Installation
Algas-SDI Operation and Maintenance Manual - SH100-SH200 2-2
Major Components
The Phoenix SH Burners consists of the following components
(Refer to Figure 1.2):
Burner Body
Burner Nozzle
Burner Rear Cover
Combustor
Fuel Inlet Block
Blower Mounting Block
Igniter
Flame Rod or UV Scanner Adapter
O-rings
Orifice Plates
Integral Blower
Control Valve and Actuator
Ratio Regulator
Air proving pressure switch
Utilizing a nozzle mix design, fuel enters through the center of the body
while air is supplied by the integral blower and enters around and through
the inlet holes in the nozzle. Fuel flow is controlled by the control valve
and air flow remains fixed throughout its operating range. Combustion
takes place within the nozzle and combustor.
Figure 1.2 – Major Components

Installation
Algas-SDI Operation and Maintenance Manual - SH100-SH200 2-3
2. INSTALLATION
Handling
Verify that the area is clean.
Protect the burner from weather, dirt and moisture.
Protect burner from excessive temperature and humidity.
Transport in original shipping container.
Use appropriate support equipment, i.e. harnesses, straps,
chains etc. when lifting burner components.
Take care not to drop or damage the burner.
Storage
Verify that the burner is clean and free of damage.
Store burner in a cool, clean, dry room.
After ensuring that everything is present and in good
condition, keep the burner in the original package if
possible.

Installation
Algas-SDI Operation and Maintenance Manual - SH100-SH200 2-4
Checklist Before Installation
Intake
To allow use of fresh combustion air from outdoors, provide an
opening in the room of at least one square inch per 4,000 BTU/hr. In
the presence of corrosive fumes or materials in the surrounding
environment, supply burner with clear air from an uncontaminated
area or provide a filtering system which shall not impede burner
operation.
Exhaust
Do not allow exhaust to accumulate in the work area. Provide means
for exhausting them from the furnace and the building.
Access
Install the burner in such a way that you can get easy access for
inspection and maintenance.
Environment
Verify the local environment matches the operating specifications of
the burner. Check the following items:
Type and supply pressure of the fuel
Availability of enough fresh, clean combustion air
Humidity, altitude, and temperature of air
Absence of damaging corrosive fumes or materials in the air
Prevent direct exposure to water
Preparing the Burner
Several components must be installed on a burner before it can
operate. See installation instructions below.

Installation
Algas-SDI Operation and Maintenance Manual - SH100-SH200 2-5
Installing the Flame Supervision
Both flame rod and UV scanner flame supervision options are offered
with Phoenix SH burners (Refer to igure 2.1) . Check Phoenix SH
specification sheet to verify availability.
CAUTION: 7000-volt ignition transformer must be used to supply
power to igniter. If equipment other than those that are recommended
are used, performance may vary from Algas-SDI published values.
Install the flame supervision into the ½” NPT opening in the
rear cover.
Verify that you connect the flame supervision of a burner to
the electrical circuit of that burner.
WARNING: If you connect the flame supervision of a burner to the
flame safety system of the wrong burner, you can cause fires and
explosions.
Figure 2.1 – Installing the Flame Supervision and Igniter
Igniter
Flame
Supervision

Installation
Algas-SDI Operation and Maintenance Manual - SH100-SH200 2-6
Installing the Igniter
Verify the gap between the center electrode and grounding
rod is no less than 1.5mm and no more than 2.0mm.
Install the igniter into the opening opposite to the flame
supervision in the rear cover (Refer to Figure 2.1)
CAUTION: Do NOT apply any assembly compound to the threads of the
igniter. You can cause bad grounding of the spark plug if you apply grease
to it. Bad ground of the spark may result in a weak spark.
Chamber wall
Provide an opening in the chamber wall at least ½” larger in
diameter than the outside diameter of the combustor.
Provide an accessible pressure tap on the chamber wall to
measure the pressure inside the firing chamber. The
pressure tap should be located near the burner.
Verify that the wall of the chamber is strong enough to
support the weight of the burner. If necessary, reinforce the
area where you plan to install the burner to support the
weight of the burner.
Refractory furnace walls must allow for thermal expansion as
recommended by the refractory supplier – the wall should
apply no stress on the combustor or refractory layer
surrounding the combustor. Expansion joints built into the
furnace wall shall permit the furnace shell, combustor or
burner block surrounding the combustor to move as a unit in
the event of unequal expansion in the refractory wall and
furnace shell.

Installation
Algas-SDI Operation and Maintenance Manual - SH100-SH200 2-7
Burner Mounting
Mount the burner to the chamber wall using customer
supplied
M10 X 1.5mm bolts (4X) and M10 lock washers (4X).
Verify the gasket that was supplied with the burner is
installed between the burner and the chamber wall.
Verify the gasket does not leak.
To ensure that radiated heat doesn’t reach the exterior of the
chamber, insulate the combustion tube over the length
contained within the chamber wall filling and clearance
completely. If the firing tube extends beyond the chamber
wall thickness, DO NOT insulate the exposed end of the
tube.
Figure 2.3 – Alloy Combustor Chamber Mounting

Installation
Algas-SDI Operation and Maintenance Manual - SH100-SH200 2-8
Burner Piping
The burner is factory assembled and shipped as ordered.
NOTE: If it is required to redirect piping be sure to meet the following
conditions:
Ratio regulator spring housing (1) is pointing up.
Arrow on the ratio regulator points in the direction of gas
flow.
Integral fuel orifice and both O-rings (2) are re-installed.
Same straight run of pipe (3) remains between the ratio
regulator and the burner.
Figure 2.4 – Burner Piping
Supply Piping
Inlet pressure to the ratio regulator (if supplied) should be as specified on
the Phoenix SH Specification Sheet. It should not exceed the maximum
pressure rating of the ratio regulator.
Locate the valve train close to the burner. The gas must
reach the burner during the fixed trail for ignition.
Sufficiently size shut off valves in the valve train.
1
3
2

Installation
Algas-SDI Operation and Maintenance Manual - SH100-SH200 2-9
Supply Piping
Inlet pressure to the ratio regulator should be no less than inlet
pressure specified in the Phoenix SH specification sheet. It should not
exceed the maximum rated pressure of the ratio regulator.
Locate the valve train close to the burner. The gas must
reach the burner during ignition trial.
Shut off valves upstream of the ratio regulator must be
sufficiently sized.
Minimize piping elbows.
Checklist After Installation
To verify proper system installation, do the following:
Verify that there are no leaks in the gas and air lines.
Verify all components of the flame monitoring control system
are properly installed. This includes verifying that all
switches are installed in correct locations and all wiring,
pressure and impulse lines are properly connected.
Verify components of spark ignition system are installed and
functioning properly.
Verify that the blower rotates in the correct direction. If
incorrect, have a qualified electrician rewire the blower to
reverse its rotation.
Verify all valves are installed in the proper location and
correctly orientated relative to the gas or air flow direction.

Installation
Algas-SDI Operation and Maintenance Manual - SH100-SH200 2-10
Prepare for Start Up/Adjustment
After installation of the burner system components is complete, the
following shall be followed to prepare for adjustment:
Set the air flow switch so that is drops out at 20% below the
maximum pressure of the combustion air blower.
Set the low gas pressure switch at 20% below the gas
pressure measured at the inlet to the main gas valve train.
Set the high gas pressure switch at 20% above the gas
pressure measured at the inlet to the main gas valve train.
Close all the burner shut-off valves.
Try to light a burner before the purge and other timing relays
have finished their cycles. Verify that the flame monitoring
system indicates a flame failure.
Trip pressure switches and other limit interlocks. Verify that
the main gas valve train closes.
DANGER: If simulated limits or simulated flame failures do not shut
down the fuel system with the required failure response time,
immediately correct the problem and retest before proceeding.

Algas-SDI Operation and Maintenance Manual - SH100-SH200 3-1
3. Operation
DANGER: The Phoenix SH burners are designed to mix fuel with air
and burn the resulting mixture. All fuel burning devices can produce
fires and explosions if improperly applied, installed, adjusted,
controlled, or maintained. DO NOT bypass any safety feature; fire or
explosion could result. Never try to light a burner if it shows signs of
damage or malfunction.
Initial Setup
Upon adjustment of a Phoenix SH Burner for the first time, you must
follow the steps listed below to ensure proper setup and operation.
Each step listed are explained in full detail in the next sections.
1. Reset the system
2. Ignite the burner
3. Set high fire fuel flow
4. Set low fire fuel flow
5. Stop Procedure.
Figure 3.1 – Pressure Taps Locations
TAP A
TAP C
TAP D

Maintenance/Commissioning
Algas-SDI Operation and Maintenance Manual - SH100-SH200 4-2
Step 1: Reset the system
Close automatic and manual gas valves.
Start combustion air blower
Step 2: Ignite the burner
WARNING: This procedure assumes burner is installed with a flame
monitoring control system and is serviceable. It also assumes normal
low fire setpoint is being used, refer to the Phoenix SH specification
sheet.
If low fire gas is too low to be used for ignition consider increasing low
fire.
Make sure pressure taps C and D are open.
Connect manometer to pressure taps C and D.
Verify combustion air blower is running.
Drive the gas control valve to low fire.
Open all manual gas valves feeding the burner.
Initiate the ignition sequence through the flame monitoring
control system.
Verify that the burner has ignited, through flame monitoring
and visual observation (optional).
NOTE: If the burner does not ignite:
a) Try to ignite again after allowing flame monitoring control
system to purge the air out of gas piping.
b) If the burner does not ignite after one or two additional
attempts, see troubleshooting section of this document.

Maintenance/Commissioning
Algas-SDI Operation and Maintenance Manual - SH100-SH200 4-2
STEP 3: Set the high fire fuel flow
If the burner has ignited, drive the main gas control valve to
high fire.
Measure the gas differential pressure.
Adjust fuel control valve until gas differential pressure value
aligns with high fire value in Phoenix SH specification sheet.
NOTE: The Phoenix SH gas orifice is sized to optimize performance
for 10% excess air at high-fire.
Once chamber pressure and temperature conditions
stabilize, repeat step 3.
Check the gas inlet pressure at the ratio regulator. This
should be at or greater than pressure stated in the Phoenix
SH specification sheet. It should not exceed the maximum
pressure rating of the ratio regulator.
Remove manometer from pressure taps.
Close pressure taps.
DANGER: Insufficient gas inlet pressure may cause the ratio regulator
to remain full open if there is a loss of air flow to the burner. This can
cause excess fuel operation and the possible accumulations of
unburned fuel in the chamber. In extreme cases, this may cause
explosions or fires.
STEP 4: Set the low fire fuel flow
Drive the main gas control valve to low fire.
Adjust the control valve in provided fuel piping to provide the
desired low fire gas flow.
NOTE: Measuring low gas pressures at low fire can prove difficult,
and it may be necessary to rely on visual inspection of the flame. This
is especially true when gas turndowns greater than 10:1 are being
used. The main intent is to provide a stable flame with good flame
signal at a firing rate that will not cause the chamber temperature to
overshoot.

Maintenance/Commissioning
Algas-SDI Operation and Maintenance Manual - SH100-SH200 4-2
Step 5: Stop Procedure
WARNING: Do not turn the combustion air blower off until the
chamber temperature is below 250°F (121°C). This will prevent hot
gases from back flowing into the burner and blower causing damage
to the burner.
Stop the burner through the burner control system.
Run the combustion air blower until the chamber
temperature drop below 250°F (121°C).
Shut off the combustion air blower.
Close all manual gas valves to the burner.

Maintenance/Commissioning
Algas-SDI Operation and Maintenance Manual - SH100-SH200 4-2
4. Maintenance
Maintenance
Preventative maintenance is the key to a reliable, safe and efficient
system. The core of any preventive maintenance system is a list of
periodic tasks.
The following are suggestions for monthly and annual checks:
NOTE: The monthly and yearly lists are an average interval. In the case of
a dirty environment, service interval may need to be shortened.
WARNING: Extreme caution must be taken due to the potential of
flammable vapor being exposed to the atmosphere creating an ignition.
Do not operate any equipment that may create a spark during
maintenance.
WARNING: High voltage ignition transformer can cause severe injury or
death when handled incorrectly. Do not perform maintenance until power
has been disconnected from ignition transformer.
Monthly Checklist (Optional)
Leak test safety shut-off valves for tightness of closure.
Test air pressure switch settings by checking switch
movements against pressure settings and comparing with
actual impulse pressure.
Visually check ignition cable and connectors.
Inspect impulse piping for leaks.
Clean and inspect burners.
Verify that the following components are not damaged or
distorted:
burner nozzle
igniter
flame supervision
combustor
If applicable, remove and clean all the orifice plates.

Maintenance/Commissioning
Algas-SDI Operation and Maintenance Manual - SH100-SH200 4-2
Annual Checklist
Inspect flame supervision devices for good condition and
cleanliness.
Check for proper inlet air/gas ratios.
Test all the alarm systems for proper signals.
Check igniters for proper gap.
Check valve motors and control valves for free, smooth
action and adjustment.
Check for proper operation of ventilating equipment.
Test the interlock sequence of all safety equipment;
manually make each interlock fail, noting that related
equipment closes or stops as specified by the manufacturer.
Test the flame monitoring control system by manually
shutting off gas to burner.
Test main fuel hand-valves for operation.
Clean or replace the combustion air blower filter (if used).
This manual suits for next models
2
Table of contents
Other Algas SDI Burner manuals
Popular Burner manuals by other brands
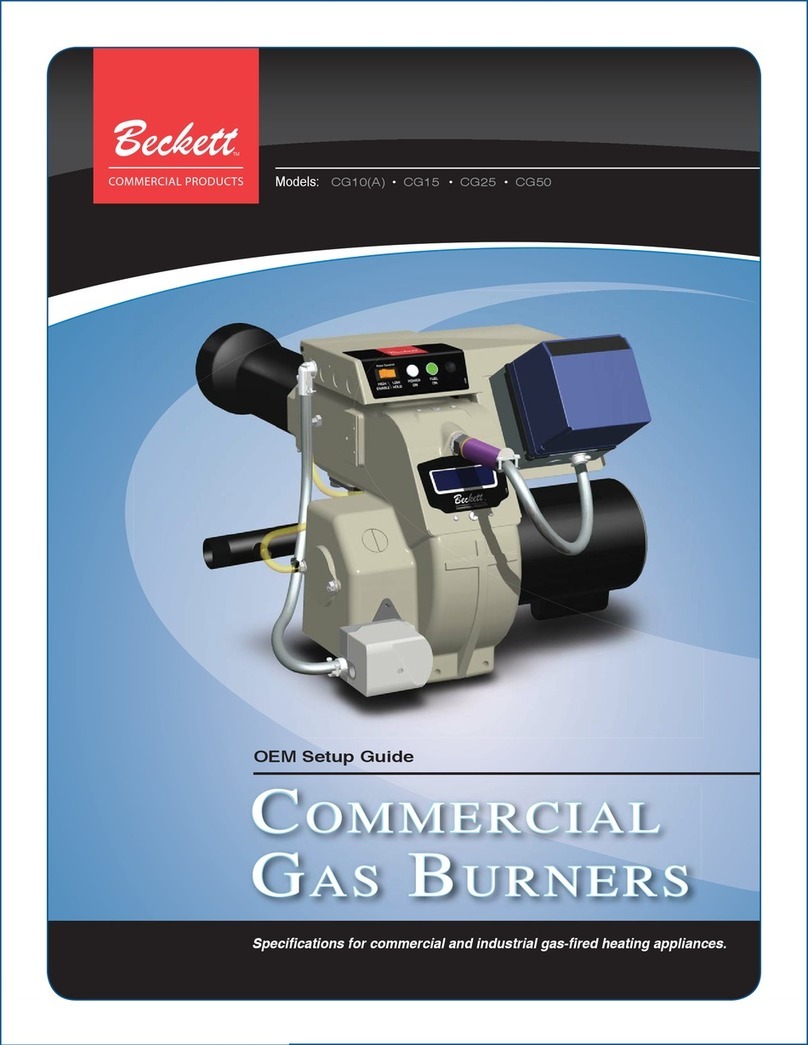
Beckett
Beckett CG10(A) Setup guide
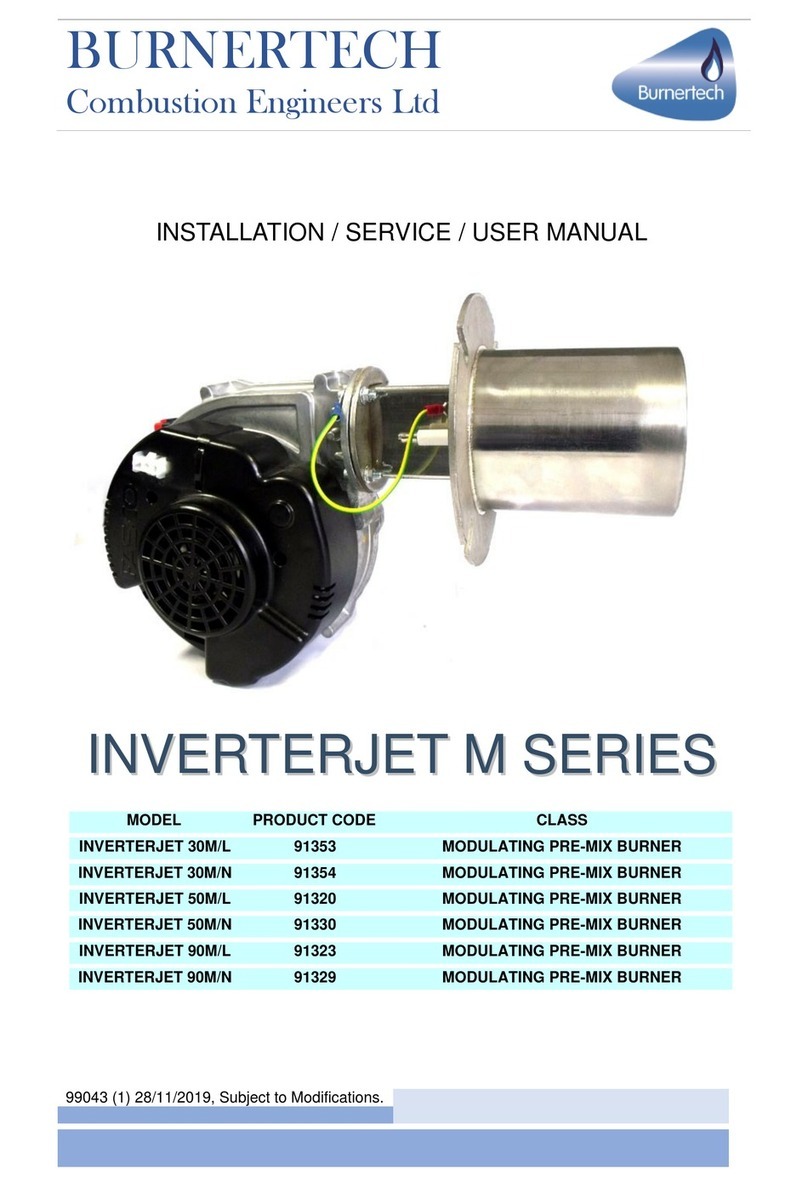
Burnertech
Burnertech INVERTERJET M Series INSTALLATION / SERVICE / USER MANUAL

Campingaz
Campingaz 360 Grill Instructions for use
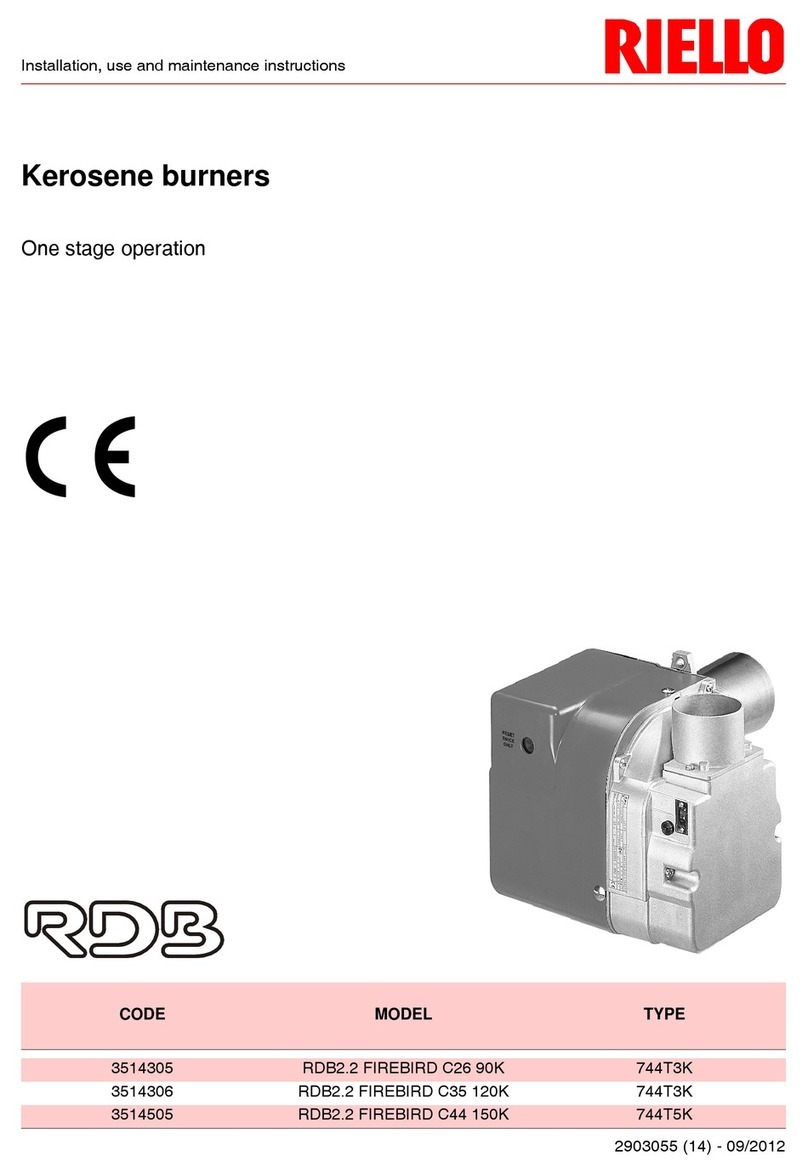
Riello
Riello RDB Installation, use and maintenance instructions

Riello
Riello RS 190 Installation, use and maintenance instructions
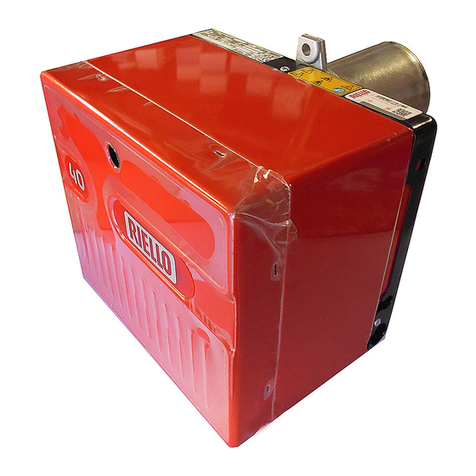
Riello
Riello G5 444T50 Operation guide
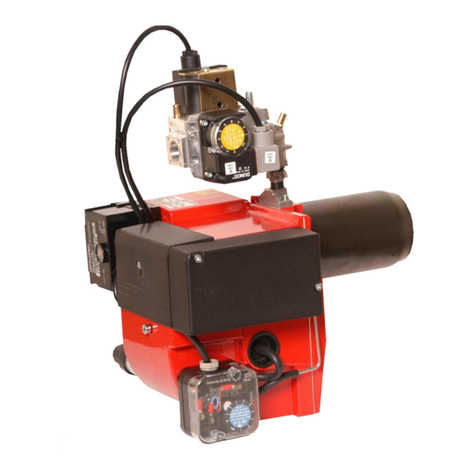
Bentone
Bentone STG 120/2 Installation and maintenance instruction
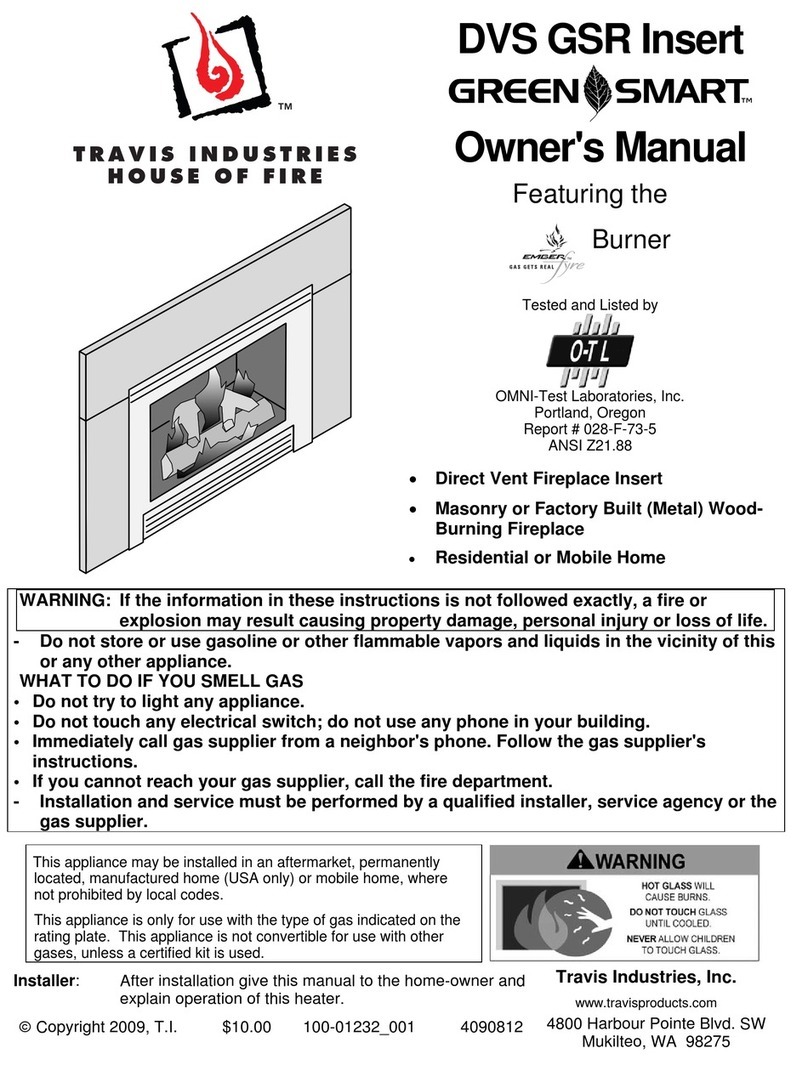
Travis Industries
Travis Industries DVS GSR Insert owner's manual

Sovelor
Sovelor AUTOGAZ User and Maintenance Book
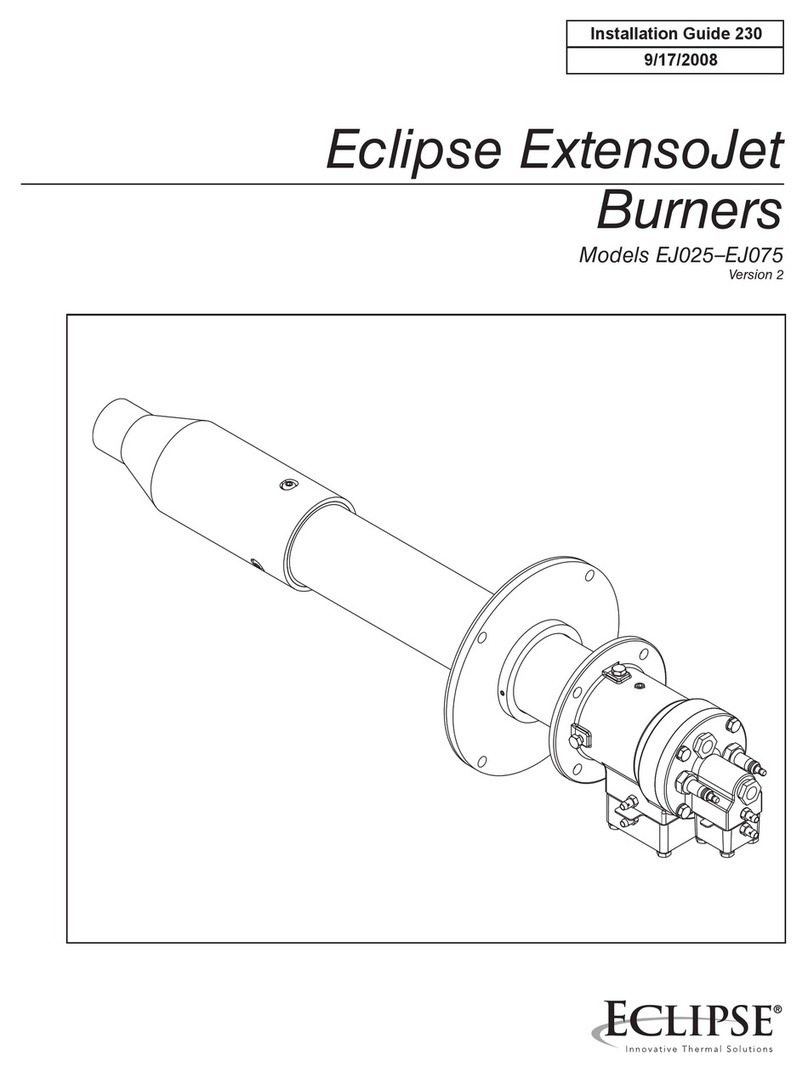
Eclipse
Eclipse ExtensoJet EJ025 installation guide

AOG
AOG IRB-18 instructions
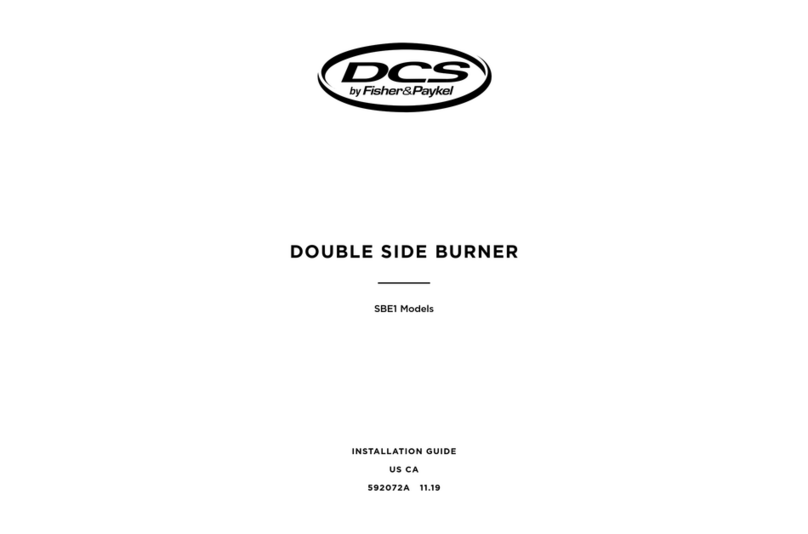
Fisher & Paykel
Fisher & Paykel DCS SBE1-142-N installation guide