Allied BreakerLube CML Series Setup guide

Allied Construction Products, LLC www.alliedcp.com
BreakerLubeTM
CML Series
Electric Grease Pump
Safety, Installation, Operation, Maintenance and Parts
This manual was prepared to assist qualified personnel with the information necessary to
install, operate and maintain the Allied BreakerLube. Read, understand and follow the
information contained in the safety messages. Keep for future reference.
TM102783
-MAX-
-MIN-
BreakerLube

Allied Construction Products, LLC www.alliedcp.com
i TM102783_BreakerLube CML_15jul
Contact Information
3900 Kelley Ave
Cleveland, Ohio 44114 Tel: 216-431-2600
Revision History for Document No. TM102783
Continuous improvement of our products is an Allied policy. The material in this publication, including figures, captions,
descriptions, remarks and specifications, describe the product at the time of its printing, and may not reflect the product in the
future. When changes become necessary, these will be noted in the table below. Specifications are based on published
information at the time of publication. Allied Construction Products, LLC, reserves the right to change, edit, delete or modify the
content of this document, including descriptions, illustrations and specifications without prior notification. For product or
document updates go to www.alliedcp.com .
Table of Revision History
Effective Date Page Summary of Change
15, Jul 17,18,19,40,41,42,43,44,
45,46,47,48 Update figures for black and gray connectors. Update breaker models &
installation kits. Revise electrical diagrams. Revise parts tables and
figures for 2 & 3 element adapter kits. Add figures for items used in
electrical kits.
09, Jan 6 Technical Data Table revise lubricant output.
08, May Model change over
07, Apr 11, 22 & 28 Add 12 Volt Electrical kit
06, Nov 3,9,10,12,17,19,22,27,28,30 Add hose, update instructions, 5.2, 5.2.1, 2 update Figure 5-1
Add diagram for hydraulic/electric installation
Section 6-6, add hammers to chart
Add Section 6.6.3 pump Instruction for larger-size hammer models
Add Figure 6-8
Update parts list for hose kit.
Add parts for pilot circuit
Update table 9-1 for models BR2214, BR2518, BR3088 & BR7013 (M14,
M18, G88 & G130)
Update Table 2-1.
05, Jan 2 & 27 25 Add relay socket in electrical schematic.
Update description item 25
04, Oct Add Rammer Series Models
03, Aug 24-27, 12 & 30 Update parts list, update electrical kit diagram
03, Sep 27, 35-36 Add adjustable pump element (optional)
Release original issue of TM102783

Allied Construction Products, LLC www.alliedcp.com
ii TM102783_BreakerLube CML_15jul
Safety Information
Safety Statements and Hazard Alerts
Safety messages appear throughout this manual and
on labels affixed to the Allied equipment. Read and
understand the information communicated in safety
messages before any attempt to install, operate,
service or transport the Allied equipment.
Keep all safety labels clean. Words and illustrations
must be legible. Before operating this equipment,
replace damaged or missing labels.
Purpose of Safety Messages
Information provided in safety messages is important
to your safety. Safety messages communicate the
extent, magnitude and likelihood of injury associated
with unsafe practices such as misuse or improper
handling of the Allied equipment. Safety messages
also explain how injury from potential hazards can be
avoided.
Safety messages presented throughout this manual
communicate the following information:
1. Alert personnel to potential hazards
2. Identify the nature of the hazard
3. Describe the severity of the hazard, if
encountered
4. Instruct how to avoid the hazard
Safety Alert Symbol
The safety alert symbol is represented by the
exclamation point within an equilateral triangle. This
symbol means - ATTENTION, BECOME ALERT,
YOUR SAFETY IS INVOLVED.
Fig. S1 Safety Alert Symbol
The Safety Alert Symbol (Fig. S1), either used alone
or in conjunction with a signal word, is used to draw
attention to the presence of potential safety hazards.
Signal Words
“DANGER”, “WARNING” and “CAUTION” are signal
words used to express severity of consequences
should a hazard be encountered.
DANGER - Indicates an imminent hazard, which, if
not avoided, will result in death or serious injury.
WARNING - Indicates an imminent hazard, which, if
not avoided, can result in death or serious injury.
CAUTION - Indicates hazards which, if not avoided,
could result in serious injury or damage to the
equipment.
Pictograms
Safety messages may also include a pictogram in
addition to the safety alert symbol and signal word.
Pictograms provide another component of
information that will further enhance the effectiveness
of the hazard communication.
CAUTION
Hot surface - Burn injury if contacted.
Some components of the machinery
become hot during operation. Allow
parts and fluids to cool before handling.
Fig. S-2 Components of Safety Message - Typical
Signal Words Used for Non-Hazard Messages
Other message types appearing in this manual utilize
signal words 'IMPORTANT' and 'NOTE'. These
contain messages that describe instructions and
suggestions, but are not safety-related.
IMPORTANT – Identify instructions that if not
followed, may diminish performance; interrupt
reliability and production or cause equipment
damage.
NOTE – Highlight suggestions, which will enhance
installation, reliability, or operation.

Allied Construction Products, LLC www.alliedcp.com
iii TM102783_BreakerLube CML_15jul
Safety Information – [cont’d]
Safety, Information and Identification Labels
Information labels affixed to the Allied equipment
include safety warnings, identification and
instructions important to operation and service. Refer
to Figure “L-15” for their location on the equipment.
Keep all safety labels clean. Words and illustrations
must be legible. Before operating this equipment,
replace damaged or missing labels. For replacement,
refer to the appropriate Parts Manual for
identification.
Fig. Label Description
L1
READ INSTRUCTIONS - Decal directs personnel to the manual for
further information / instructions.
L2
Crush Point – Decal alerts personnel to maintain a safe distance
from moving parts.
L3
LUBRICATION POINT – Decal identifies lubrication points. Refer to
the manual(s) for grease type, re-lubrication schedules, procedures
and precautions that must be observed to prevent risk of equipment
damage if instructions are not followed or through unapproved
methods.
L4
Maximum Fill Line – Decal indicates the maximum fill line when
refilling the cartridge with lubricant. The decal also calls attention to
hazard if overfilled.
L5
Grease Refill - Decal identifies the location of the lube fitting used
for refilling the reservoir with grease.
L6
Manual Greasing – Decal identifies the location of the lube fitting
used to manually grease the bushing & tool. Use this lube fitting to
pre-fill lube lines and passages.
L7
Rotation Arrow – Indicates the direction in which the motor should
turn.
L8 ALLIED LOGO – This decal is the Allied brand identifier and is a
registered trademark of Allied Construction Products, LLC.
L9 BreakerLube Product Name – Decal identifies the product.
L10
Product ID Tag - Contains identifying information about the
equipment, including: Manufacturer’s name, model and series
number, maximum pressure and operating voltage.

Allied Construction Products, LLC www.alliedcp.com
iv TM102783_BreakerLube CML_15jul
Safety Information – [cont’d]
Fig. L11 Label Positions Identified
Table S-1 Labels
Item Part Name Part No Qty Description
L2 Crush Point 576737 1
L7 Rotation Arrow 1
L8 Allied 676652 1
L9 BreakerLube 679967 1
L10 Product ID Tag 1
-MAX-
-MIN-
BreakerLube
Front

Allied Construction Products, LLC www.alliedcp.com
v TM102783_BreakerLube CML_15jul
Safety Information – [cont’d]
Meaning of Pictograms
Pictograms are used to rapidly communicate
information. For the purposes of this manual and
labels affixed to the Allied equipment, pictograms are
defined as follows:
Read the manual
Refer to the manual for further
details
Procedures are explained in
the manual
Read the Service Manual For
Additional Information
Shut off carrier & remove key
before servicing
Personnel maintain a safe distance
Falling object
Unsupported loads
Personal Protection Equipment
Hearing protection
Safety eyewear
Gloves
Safety shoes
Falling part
Moving part (in direction
indicated by arrow)
Crush point
Crush / Entanglement
Moving Parts
Crush / Pinch point
Leaking fluid under
pressure
Hot surfaces
Gas / Oil under pressure
Electric Shock Hazard
Prohibited actions must be
avoided to prevent injury
and/or equipment damage
A prohibited action is
identified with an X-out or a
circle with a diagonal slash.
The check mark symbol is
used to indicate actions
and methods that are
recommended, correct and
approved
DO NOT REFILL HERE

Allied Construction Products, LLC www.alliedcp.com
vi TM102783_BreakerLube CML_15jul
Safety Information – [cont’d]
Attention Read the Manual
Improper installation, operation or maintenance of
the Allied equipment could result in serious injury or
death. Only qualified operators may operate the
Allied equipment. Personnel responsible for the
maintenance of the Allied equipment or its systems,
including inspection, installation or adjustments must
also be qualified. Operators and personnel
responsible for maintenance of this equipment
should read this manual. Other manuals, such as
those published by the manufacturer of the
machinery used along with the Allied equipment,
should also be read.
Qualified Person
For the purposes of this manual, a qualified person
is an individual that has successfully demonstrated
or completed the following:
Has read, fully understands and adheres to all
safety statements in this manual.
Is competent to recognize predictable hazardous
conditions and possesses the authorization,
skills and knowledge necessary to take prompt
corrective measures to safeguard against
personal injury and/or property damage.
Has completed adequate training in safe and
proper installation, maintenance and operation
of this Allied equipment.
Is authorized to operate, service and transport
the Allied equipment identified in Table 1.1.
Safety Information Overview
This manual contains important safety information
that must be followed so that unsafe situations may
be avoided. It’s important for all personnel working
with the Allied equipment to read this manual in its
entirety. Safety information is generic at the
beginning of this manual. As you continue reading
through later sections of this manual, instructions
and safety information become tool-specific and
operation-specific.
Allied has made every effort to provide information
as complete and accurate as possible for this
document. Allied cannot anticipate every possible
circumstance that might involve a potential hazard.
The warnings in this manual and labels affixed to the
Allied attachment are therefore not all inclusive.
General Construction Safety
Always follow procedures that promote safe
conditions for workers and bystanders. The standard
safety precautions expected and required of those
working in construction shall include, but not limited
to:
Locating existing underground service and utility
lines
Establishing pedestrian barriers
Using personnel protection equipment
appropriate to working conditions, etc.
Federal, State, Local and OSHA Construction
Guidelines and Regulations
Use the Allied equipment in accordance with all
federal, state and local regulations regarding
construction practices and public safety.
Identification of, and compliance to, governing
regulations are the responsibility of the owner and
operator.
In the United States, comply with the
recommendations of the Occupational Safety and
Health Administration standards of the U.S.
Department of Labor. For OSHA construction
guidelines contact your local federal government
office or write:
U.S. Government Printing Office Superintendent of
Documents P.O. Box 371954 Pittsburgh, Pa. 15250-
7954
Website: www.osha.gov
Ask for Construction Industry OSHA Standards
Stock #869-034-00107-6.
Owner’s Responsibilities
Ensure that only qualified personnel operate and
service the Allied equipment.
Ensure personnel protection equipment is available
to personnel and enforce the use of PPE
Ensure equipment is kept in safe operating condition
Ensure safety-related materials such as instructions
and including this manual are kept in a convenient
location so that they are easily accessible to
operators and maintenance personnel.

Allied Construction Products, LLC www.alliedcp.com
vii TM102783_BreakerLube CML_15jul
Safety Information – [cont’d]
Operational Safety Program
The safe and efficient use of the Allied equipment
depends upon proper installation, operation,
maintenance and repair. Operational safety
programs must encompass all of these elements.
Accident prevention through operational safety
programs are most effective when the equipment
owner further develops the program by taking into
account his own experience in using and
maintaining equipment.
Developing such programs will help minimize
equipment downtime, while maximizing service life
and performance. Most importantly, it will minimize
the risk of personal injuries.
Personal Protection Equipment (PPE)
Personal protection equipment (PPE) must be
available to any personnel operating or nearby the
equipment that may be exposed to hazards such as
falling, flying and splashing objects, or harmful
dusts, fumes, mists, vapors, or gases. Approved
PPE, when used correctly, helps protect against
certain harmful effects from exposure with the
identified hazard.
Examples of PPE include safety eyewear, safety
hat, hearing protection, dust mask, safety footwear,
and gloves. (Shown Pictograms of PPE is not all-
inclusive).
Those responsible for administering PPE shall train
personnel with the proper selection and use of PPE
to protect against misuse.
Safety Guards and Protective Barriers
A safety guard is a physical barrier designed to
prevent access to danger areas. Guards are fitted to
the Allied equipment to protect against unsafe
situations that could not be eliminated through
design measures. Guards are only effective when
properly installed and in place. Guards shall not be
removed unless for the purpose of inspection and
service of components. Reinstall all guards after
service or adjustments are completed.
Where it was not possible to prevent an unsafe
situation by means of a guard, safety messages
appear on the equipment, warning personnel of a
recognized hazard.
Additional guarding, not included with the Allied
equipment, is necessary at the operator’s station to
protect the operator and other nearby personnel
against flying debris from material being cut or
demolished. Do not handle, demolish or cut material
overhead without proper guards installed.
The control switch shall be located in a protected
area that is guarded against accidental operation of
the Allied work tool.
Unapproved Use or Modifications
In order to provide and maintain efficient operation
with reliable service, while ensuring operator safety,
the Allied equipment may not be used for any
purpose other than, for which it was intended. Use of
the Allied equipment, other than those cited in this
manual, may place personnel at risk of injury and/or
may subject the equipment to damage.
When making repairs, use only the manufacturer's
genuine parts. Substitute parts may not meet the
required standards for fit and quality, or may impair
function, safety and performance. The Allied
equipment shall not be modified or used in
unapproved applications unless written consent is
received from the Allied Engineering Department.

Allied Construction Products, LLC www.alliedcp.com
viii TM102783_BreakerLube CML_15jul
Table of Contents
Section Page
Contact Information & Document Revisions…. i
Safety Information…………….…..............……… ii
1.0 Introduction & Scope……………….…..…… 1
1.1 About of This Manual….…..…………….….… 1
1.2 Content Includes………………………………. 1
1.3 How to Order Replacement Manual…….…… 1
1.3.1 Related Publications…………………………. 1
2.0 Equipment Identification……………..…….... 2
2.1 Product Identification Tag……..………….……. 2
2.2 Owner’s Record of the Product….……..…..… 2
3.0 Warranty Protection Summary………..…... 3
3.1 Overview……………………………….……… 3
3.2 General Maintenance Policy..…..........……. 3
3.3 Allied Product Policies………………….……. 4
4.0 Product Description & Operating Principle 5
4.1 Description and Application 5
4.2 Familiarization of Main Components………….. 6
4.3 Operating Principle…………………………...… 7
5.0 Basic Pump Configuration…………………. 8
6.0 Installation…………………….………………. 11
6.1 Safety Precautions - General…………….….…. 11
6.2 Mounting Considerations / Location - General 11
6.3 General Installation Instructions –E / F / G / H 12
6.4 Install Short Lube Line to Breaker Port ‘G’ 15
6.5 Install Re-usable Fitting Instructions………… 15
6.6 Instructions for Installing Pump Element …… 15
6.7 Set up and Adjustments………………..……... 16
6.8 Adjustable Type Element – Option……….….. 16
6.9 Electrical Installation – General..……………… 17
6.10 Black Connector Identified……………..……. 17
Section Page
6.11 Gray Connector Identified……………………. 18
6.12-6.13 Examples of Various Wiring Diagrams 19
6.14 Install Instructions Using Auxiliary Valve….. 24
6.15 System Start-up Check List…………………. 24
6.16 Set-up and Adjustment………………………. 25
6.14 Unit Function and Performance Test……..…. 25
7.0 Maintenance………………………….…..……. 25
7.1 Maintenance - Safety Precautions………….... 25
7.2 Grease Level ‘MIN’ – ‘MAX’…………………. 25
7.3 How To Refill the Reservoir………….…..…. 26
7.4 Daily Walk-Around Inspections…..……..…….. 26
7.5 Replace Lube Lines – Pre-fill & Bleed……….. 27
7.6 Bypass BreakerLube & Grease By Hand…… 27
7.6.1 Grease Tool Bypass BreakerLube……….. 27
7.6.2 Grease Tool Direct At Front Head…………. 27
8.0 Removal (Uninstall) & Storage……………… 29
8.1 Removal From Carrier……………….…..…... 29
8.2 Remove Hoses…………….…………………... 29
8.3 Storage & Handling……………………………. 29
8.4 Reattach After Idle Period………….….……. 29
9.0 Troubleshooting………………….…...….…... 31
10.0 Technical Data……………………………….. 32
10.1 General Specifications…..………..…...…….. 32
10.2 General Dimensions……………….………….. 33
10.3 Electrical Connectors & Locations Identified 34
11.0 Spare Parts Information…………..……..... 35
10.0 Chisel Paste…………………………………. 48
How to Order Spare Parts – Order Form 49

Allied Construction Products, LLC www.alliedcp.com
ix TM102783_BreakerLube CML_15jul
Table of Contents – [cont’d]
List of Figures Page
S1 Safety Alert Symbol……………………………. ii
S2 Components of Safety Message - Typical….. ii
L11 Label Positions………………………………….. iii
Meaning of Pictograms……………………………. v
Example of Personal Protective Equipment…….. vii
2-1 Product Identification…………………………… 2
4-1 BreakerLube Plumbing to Breaker – Typical... 6
4-2 Familiarization of Pump Main Components 6
4-3 Operating Principle of Pump – General……… 7
4-5 Pump Element Assembly……………………… 7
4-6 Operating Principle of Low Level Control…… 7
5-1 Pump & Lube Line Configuration A/B/C/D/E/F 9
6-1 Mounting Location – Typical…………………. 11
6-2 Single Pump Element & Lube Line…………… 12
6-3 Lube Lines - Long & Short ‘Cut-to-Length’ 12
6-4 Add 2nd Pump Element & Bridge Into 1 Line 12
6-5 Configuration ‘G’ – Top View…………………. 13
6-6 Config. ‘E’ Add 2nd Pump Element & Lube Line 13
6-7 Port ‘G’ Location on Valve Housing…………… 14
6-8 3-Pump Elements Bridged Into Single Line 14
6-9 Assemble Fitting to Plain End of Hose……. 15
6-10 Pump Element Assembly……………………. 15
6-11 Tightening Torque – Pump Element……….. 15
6-12 Adjustable Type Pump Element…………….. 16
6-13 Adjustment Delivery Diagram……………….. 16
6-14 Delivery Adjustment OK, Lacking, Excessive 16
6-15 Location of Plug 28 & 41 on Pump Housing 17
6-16 Foot Treadle Inside Operator’s Cab………… 17
6-17 Pressure Switch & 3-Way Valve…………… 18
6-18 Black Connector (43) Identified……………… 18
6-19 Top View - Markings on Black Connector 18
6-20 Gray Connector (26) Identified…………… 18
6-21 Gray Connector 3-Poles Plus Ground…….. 19
6-22 Basic Wiring for Motor………………………. 19
6-23 Plug (41) 2-Pole with Ground…………….. 19
6-24 Electrical Diagram ‘2E’………………………… 20
6-25 Electrical Diagram ‘3E’……………………… 21
6-26 Electrical Diagram ‘3E’ Relay 1 & 2 Detail…. 22
6-27 Electrical Diagram ‘4E’……………………….. 23
6-28 Pre-lube Tool Shank Before Installing…….. 24
6-29 Location of Grease Fittings Identified………. 25
6-30 Pre-fill Non-factory Lube Lines…………….. 25
7-1 Grease Levels ‘MIN’ and ‘MAX’………………. 26
7-2 Unapproved Re-fill Method………………….. 27
7-3 Reservoir Re-fill Location Identified…………. 27
7-4 Delivery Adjust – ‘OK’, ‘Lacking’, ‘Excessive’ 27
7-5 Grease Fitting (25a) Identified on Relief Valve 28
7-6 Grease Tool - Location & Standing Position 28
7-7 Grease Tool - Prohibited Position Identified 29
7-8 Grease Tool - Risk of Damage to Seals…….. 29
10-1 Basic Pump Assembly – All Sides Identified 33
10-2 General Dimensions…………………………. 34
10-3 Location of Plug (28) & (41) Identified……… 35
11-1 Basic Pump Assembly – Parts Identified…. 36
11-3 thru 11-9 Adapter Kits – Parts Identified 41
List of Tables Page
Revision History of Document…………………… i
1.1 About This Manual…………………………….. 1
5.1 Basic Pump Assembly………………………… 8
5.2 Basic Pump – Overview of Configurations 8
10.1 General Specifications………………………. 33
11.1 Parts List Basic Pump Assembly……………. 37
11.5 – 11.7 Installation Kits – By Series………… 41
11.9 -11.10 Lube Line Kits 44
11.14 Electrical Kits………………………………… 47
12.1 Chisel Paste Packaging Information………. 49

Allied Construction Products, LLC www.alliedcp.com
1 TM102783_BreakerLube CML_15jul
1.0 Introduction and Scope
1.1 About this Manual
Prior to use, confirm that the information recorded on
the equipment’s identification label (Fig. 2-1)
corresponds with Table 1.1.
Table 1.1 About This Manual
Document ID No. TM102783
Type: Safety, Operation,
Maintenance, Installation &
Parts
Current Status: See Inside Cover
Product Name: BreakerLubeTM
Series / Generation: CML-II
Applicable Model[s]: 12 & 24VDC / 1 & 2 Gallon
Years of Production: Begin 2002
This manual has been prepared in support of the
product named in Table 1.1 and is intended to assist
the operator and maintenance personnel with the
information necessary for the safe and proper use of
the Allied equipment.
The spare parts list is also included in this manual.
Illustrations depicted in the Parts Information Section
are for purposes of parts identification and are not
intended for use in repair or service of the equipment.
Material presented in this manual, including tables,
figures, descriptions and captions, may show
equipment that is optional. Figures, captions, parts
tables and descriptions are intended solely for use
with the product identified in Table 1.1 and may not
be suitable for use with other models.
This manual is an integral part of this product. Keep it
in a convenient location so that it is easily accessible
for future reference.
1.2 Content Includes
Safety Section
Equipment Identification
Operating Principle
Configurations – Equipment Options
Installation Guidelines
Maintenance & Care
Recommended Lubricants
Priming / Pre-filling Lines
Troubleshooting
Removal & Storage
Technical Data / General specifications
Parts Information - Spare / Replacement
The publication identified in Table 1.1 was created
solely for information purposes and should not be
considered all-inclusive. If further information is
required, contact your local Allied dealer or the Allied
Customer Support Department.
The content of this document has been reviewed for
accuracy. Allied Construction Products, LLC has
endeavored to deliver the highest degree of accuracy
and every effort has made to provide information as
complete as possible. However, continuous
improvement of our products is an Allied policy. The
material in this publication, including figures,
captions, descriptions, remarks and specifications,
describe the product at the time of its printing, and
may not reflect the product in the future. A table of
revision history for this document is found on the
inside cover.
1.3 How To Order Replacement Publications
Replacement manuals may be ordered by contacting
your local Allied dealer or the Allied Customer
Support Department. Manuals may also be viewed
and downloaded at: www.alliedcp.com
1.3.1 Related Publications
Allied Construction Products, LLC offers the following
publications for the product identified in Table 1.1.
Further publications are not available at the
time of this release

Allied Construction Products, LLC www.alliedcp.com
2 TM102783_BreakerLube CML_15jul
2.0 Product Identification
2.1 Product Identification Tag
Fig 2-1 Product Identification
Refer to Figure 2-1. The Model and Series Number
assigned to this equipment can be found on the
Product Identification Tag
The Identification Tag is affixed to the pump housing.
It provides the following information:
Manufacturer’s name
Model Code
Series
P max Bar
Operating Voltage U= P=W
Confirm that the information contained on the Tag
corresponds with the information provided in Section
1, Table 1.1.
2.2 Record Product ID Information for Future
Reference
Your local Allied dealer requires complete information
about the equipment to better assist you with
questions regarding parts, warranty, operation,
maintenance, or repair.
Copy the Model and Series Number from the
Equipment Identification Tag to the space
provided below.
Indicate the date in which the Allied equipment
was placed into service.
Fill out the Warranty Registration form and return
to Allied Construction Products, LLC.
Product / Series BreakerLube CML
MFR:
Model Code
P. No:
Series Number:
In Service Date:
Registration Date
When inquiries are made, specify by name,
voltage, reservoir capacity and number of
pumping elements and lube lines, e.g.:
BreakerLube CML, 24VDC, 2 gallon, 2-pumping
elements bridged into 1 lube line 60’.
X BreakerLube
X CML (BPA units without pcb controller)
Operating Voltage
Reservoir Size
Pumping Elements – Qty
Relief Valves – Qty
Lube Lines – Qty & Length
Notes:

Allied Construction Products, LLC www.alliedcp.com
3 TM102783_BreakerLube CML_15jul
3.0 Warranty Protection Summary
3.1 Overview
The Allied equipment is delivered assembled and
factory tested. Upon receipt of the equipment, inspect
for possible shipping damage or loss.
Before this equipment is installed and used,
familiarize yourself with the features and functionality
of the unit. Refer to the technical data section of this
manual for specifications and dimensions. When
properly installed, operated and maintained by
qualified personnel, the Allied equipment will remain
productive with a minimum of service. Improper
installation, including failure to properly calibrate (test
and adjust) the equipment, may negatively impact
performance or subject the equipment to conditions
beyond its operating specifications.
The use of non-genuine parts or unapproved
lubricants, modifications, installation, service
methods and operation not in accordance with the
contents of this manual may cause loss of
performance, equipment failure or personal injury.
Warranty does not cover conditions, which in the
reasonable judgment of Allied Construction Products,
LLC, arise from improper installation / set-up, misuse,
unauthorized alteration, accident, or inattention to
maintenance requirements. Complete warranty terms
and conditions can be found in document 100785.
3.2 General Maintenance Policy
The following general maintenance policies outline
the minimum requirements for reducing failures and
minimizing unscheduled equipment downtime. The
owner is strongly encouraged to implement these
guidelines and further develop them to manage
particular applications and operating environments.
Owner's responsibility includes:
Ensure that personnel entrusted with installation,
operation, and maintenance of the Allied
equipment adhere to the following:
Read and fully understand the information
included in this manual.
Recognize that operating this equipment in
conditional applications, such as working
underwater, requires modifications to the
standard breaker and additional training for the
operator, maintenance and service personnel.
Use the Allied equipment only if it is in sound
operating condition. Take prompt action to rectify
any faults that, if left uncorrected, could lead to
further damage of this equipment or subsequent
damage to supporting equipment or personal
injury
Use the Allied equipment only for the purpose for
which it is intended.
Regularly conduct inspections of the equipment
and follow the recommendations found in the
Maintenance Section of this manual.
Understand effective communication is key to the
success of any maintenance program. Appointing
‘Who Does What’ ensures that all personnel
understand exactly what their specific
responsibilities include.
1. Establish maintenance responsibilities to be
performed by the Operator.
2. Establish maintenance responsibilities to be
performed by the Service Technician.
Recognize problems and know how to take
corrective action as outlined in the
Troubleshooting Section of this manual.
Allow only qualified operators and service
technicians to perform maintenance and repair.
Maintain written records of equipment
maintenance, service and repair. These records
are helpful if warranty coverage is ever in
question.
Each record shall include at least:
Date of service, maintenance or repair.
Description of the service, maintenance or repair
performed. Include part numbers if applicable.
Copies of purchase order(s) and invoice(s) for
repair parts and service.
The name and signature of the person
performing the service, maintenance or repair.

Allied Construction Products, LLC www.alliedcp.com
4 TM102783_BreakerLube CML_15jul
3.0 Warranty Protection Summary - [cont’d]
3.3 Allied Product Policies
In this manual, Allied recommends the use,
applications, maintenance and service consistent
with industry practices.
Allied assumes no responsibility for the results of
actions not recommended in this manual and
specifically the results of:
Improper Installation, Set-up, Calibration
Carelessness / Incorrect operating methods
Inattention to re-lubrication and other
maintenance requirements
Misuse / Unapproved applications
Inadequate or Absence of Training
Use of non-genuine Allied replacement parts
Unapproved modifications
Use of grease, which is not or is only
conditionally Pumpable
The use of a lubricant type that is unsuitable for
the application. Allied Chisel Paste is
recommended for all breaker models.
Contaminated lubricants.
Improper disposal of used or contaminated
lubricants.
These exclusions apply to damage to the Allied
equipment, associated equipment and injury to
personnel.

Allied Construction Products, LLC www.alliedcp.com
5 TM102783_BreakerLube CML_15jul
4.0 Product Description and Operation
4.1 BreakerLube Description and Application
Fig. 4-1 Configured with Single Pump & Lube Line. Breaker Shown with Single Lube Passage to Both Bushings
The BreakerLube CML Series is an electrically
operated grease dispensing pump. It is designed for
mounting on mobile construction vehicles and offers
a simple, effective and inexpensive method for
lubricating the bushing and tool. The fully automated
system eliminates the need to stop production to
manually lubricate the bushing and tool.
4.1.1 Benefits of BreakerLube
The BreakerLube offers the following benefits:
Increased uptime and overall productivity of the
Breaker, while reducing costs related to
downtime as in the course of stopping work to
manually grease the tool.
Safety is improved as operators are not required
to lubricate in hazardous areas
Increase service life of components. Lubrication
occurs while the breaker is in operation, when it
is of the most benefit
Will dispense the precise amount to maintain
sufficient lubrication while reducing costs from
excessive consumption with less waste and
environmental pollution.
With proper delivery, the constant replenishment
of grease flushes dust from bushings and seals
against entry.
Prevents down time and expensive repairs to
replace damaged parts caused when manual
greasing schedules are missed.
Prevents seal damage resulting from improper
grease methods. Grease is dispensed only when
breaker is operating.
4.1.2 Features of BreakerLube Include:
Compact size occupies less space. Mounts easily
to large and medium-size carriers
Proven reliability from simple design, with few
moving parts
Heavy-duty motor available in 12 or 24VDC.
Available with 1 or 2 gallon reservoir
Low-level control monitors grease level in
reservoir and activates if below ‘MIN’ mark
-MIN-
-MAX-

Allied Construction Products, LLC www.alliedcp.com
6 TM102783_BreakerLube CML_15jul
4.0 Product Description and Operation
Basic pump assembly is extremely customizable
offering numerous configuration possibilities to
suit the different requirements of breakers and
carriers
Accepts up to 3 pumping elements for increased
delivery output
Can be configured so that each pump is bridged
into a single lube line for large size breakers
needing maximum output or independently to
accommodate breakers having separate grease
passages to each bushing.
Clear reservoir provides immediate visual
monitoring of lubricant level
Large capacity reservoir extends run times before
refills
Re-fillable reservoir is quickly and easily refilled
with no special tools required. Can be bulk filled
or through grease nipple
Equipped with special pump elements for use
with Chisel Paste.
Delivery of grease up to NLGI No. 2 at
temperatures from -25C to 70C
System activation works with both electrically-
operated and pilot-operated controls for breaker
valve. (Note: Additional parts required for pilot-
operated control, not included in standard
installation kit)
Custom designed install kits facilitate quick
installations. Kits include a basic pump that’s
specifically configured to the size of the breaker
to ensure the proper amount of lubricant is
delivered. Also included are pre-filled lube lines,
fittings, mounting bracket and hardware. Ordering
information is found in Section 11.
4.2 Basic Pump Familiarization of Components
Fig. 4-2 Basic Pump Assembly BreakerLube CML Series
A Basic Pump Assembly
3 Reservoir
21 Pump Element
25 Pressure Relief Valve Assembly
26 Gray Connector Pre-wired With
4-conductor Cord for Low-Level
Control
43 Black Connector Pre-wired With
4-conductor Cord for Power
Supply to Motor
* Hardware for Mounting
25,a,b
21
43
26
24
3
*
A

Allied Construction Products, LLC www.alliedcp.com
7 TM102783_BreakerLube CML_15jul
4.0 Product Description and Operation
4.3 Operation
The power needed to operate the BreakerLube is
supplied by an external electrical source that is
controlled through a momentary switch. The heavy-
duty electric motor drives the cam that pushes the
piston through the grease filled chamber and
discharged through the open check valve.
Fig. 4-3. Pump Element – Cross Section View
1-Cam, 2-Piston, 3-Spring and 4-Check Valve.
The spring returns the piston and the chamber is re-
filled. The closed check valve prevents the back flow
of grease.
Fig. 4-4. Pump Element – Cross Section View
Piston Return Stroke, Check Valve Closed.
Fig. 4-5 Pump Element Assembly – Item 21
1-Piston 2-Spring 3-Check Valve
By design, the BreakerLube is a low capacity pump.
The pump’s discharge rate is purposely metered for
small quantities only.
4.4 Operation of Low-level Control
The basic pump assembly comes standard equipped
with a low level control. When wired to a light or
alarm, the operator is signaled that the grease level
inside the reservoir has fallen below the minimum
mark.
Fig. 4-6. Low-level Control 1-Magnetic switch, 2-
Electromagnetic switch, 3-Control Arm
4.4.1 Low-level Control - Full Reservoir
Refer to Figure 4-6. The magnetic switch (1) and
control arm (3) are attached to the stirring paddle.
With the grease level above the minimum mark, the
control arm pivots the magnetic switch out of range of
the electromagnetic switch (2).
4.4.2 Low-level Control - Empty Reservoir
The control arm pivots outward when the grease level
falls below the minimum mark. The normally open
electromagnetic switch will close when the magnetic
switch passes over it. The closed switch illuminates
the dash lamp.
Fig. 4-7 Item 28 Plug– 3 Pole Plus Ground
1
2
3
(+) RD/1
BK/3

Allied Construction Products, LLC www.alliedcp.com
8 TM102783_BreakerLube CML_15jul
5.0 Product Configuration
5.1 Introduction to Available Pump Configurations
The design of the basic pump assembly
is the same but differences are seen in
the way that it can be adapted to suit
the different needs of the carrier and
breaker.
A1) Basic Pump A102472
Input Voltage - 24VDC
Reservoir - 2 Gallon
w/ Single Element
A2) Basic Pump A102473
Input Voltage - 24VDC
Reservoir - 1 Gallon
w/ Single Element
A3) Basic Pump 102474
Input Voltage - 12VDC
Reservoir - 1 Gallon
w/ Single Element
Fig. 5-1 Basic Pump Assembly BreakerLube CML Series
Table 5.1 Basic Pump Assembly - Parts Common to A1, A2, A3.
A Basic Pump Assembly With Low Level Control and Single Pump Element (Specify 12VDC or 24VDC)
3 Re-fillable Reservoir. (Specify Size 1 or 2 Gallon)
21 Pump Element (Qty-1 included. Order additional elements separately)
24 Adapter
25 Pressure Relief Valve (Qty-1 included. Order additional relief valves separately)
26 Gray Connector Pre-wired with 4-conductor wire Cord for (Low-Level Control)
43 Black Connector Pre-wired with 4-conductor Cord (Power Supply to Motor)
* Mounting Hardware
Table 5.2 Several adaptations are available to suit different needs of the carrier and breaker, including:
B) Operating Voltage 12 or 24VDC (VAC also available upon request)
C) Reservoir Size 1 or 2 Gallon
D) Pump Element(s) 1 Standard, or Two Element Adapter or Three Element Adapter Kit
E) Separate Lube Passage Requires 2nd element , relief valve and lube line
F) Lube Line Kits Available in standard lengths of 40’, 60’, 80’ and come pre-filled.
A 2nd pre-filled hose is also included. It will attach to the breaker.
25,a,b
21
43
26
24
3
*
A

Allied Construction Products, LLC www.alliedcp.com
9 TM102783_BreakerLube CML_15jul
5.0 Product Configuration –[cont’d]
5.1.1 What the BreakerLube System Includes
Install kits are available from Allied. These custom
designed kits include a basic pump that’s specifically
configured to the size of the breaker to ensure the
proper amount of lubricant is delivered. Kits also
include pre-filled lube lines, fittings, mounting bracket
and hardware. Kit ordering information is found in
Section 11.
IMPORTANT
The breaker must be equipped with a qualified
grease connection port to attach the lube line.
5.1.2 Basic Pump Assembly A1, A2, A3
A. The basic pump assembly includes items shown
in Fig. 5-1. Begin configuration with the basic
pump. Select from A1, A2, or A3.
B. Identify the supply voltage of the carrier and
match it with the correct basic pump assembly.
Fig. B Match Carrier’s Supply Voltage
C. Choose size of reservoir 1 or 2 gallon. Mounting
considerations should include easy access for re-
filling and protection against damage. General
dimensions of the basic pump assemblies are
found in the Technical Data Section of this
manual.
Fig. C Select 1 or 2 Gallon Reservoir
D. Grease delivery is determined by the number of
pumping elements installed. For larger size
breakers, the BreakerLube is configured with the
2 or 3-Element Adapter Kit.
Fig. D Add Pump Elements to Increase Output
M
1
2
3
(+) (-) B
41
3C
D
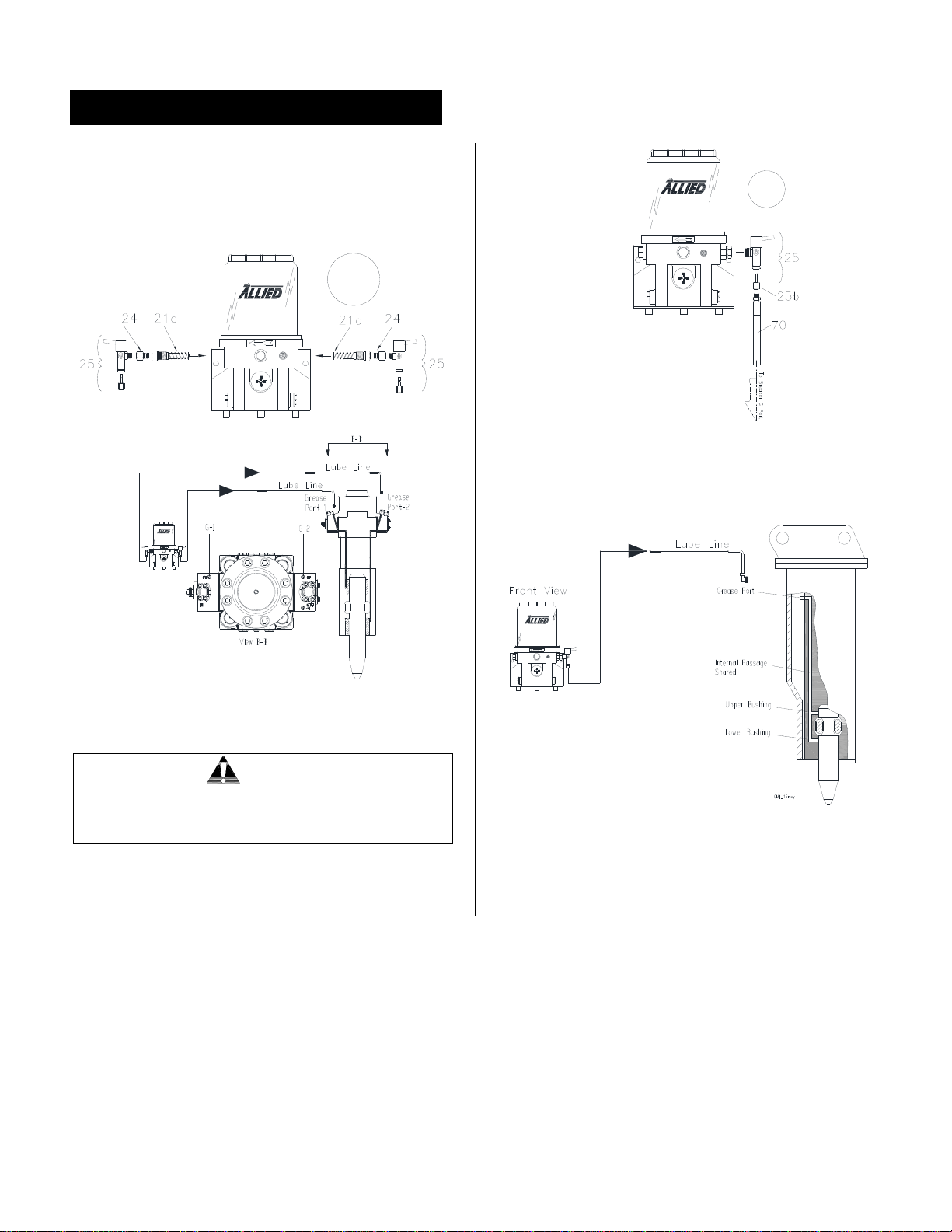
Allied Construction Products, LLC www.alliedcp.com
10 TM102783_BreakerLube CML_15jul
5.0 Product Configuration –[cont’d]
E. Some breakers have two separate grease
connection ports and passages that feed
bushings independently. Configure the basic
pump with two pump elements and provide each
with separate lube lines and relief valves.
Fig. E Breaker with Two Grease Ports - Bushings
With Independent Grease Passages
CAUTION
Each separate pump line must have a relief valve
installed.
F. Follow configuration ‘F’ for breakers designed
with a single grease passage to both the upper
and lower bushings will this.
Fig.-F1 Lube Line Kit (Item 70) Determined By
Carrier Reach
Fig.-F2 Single Feed Passage Lubricates Both
Bushings
-MIN-
-MAX-
BreakerLube
E
-MIN-
-MAX-
BreakerLube
-MIN-
-MAX-
BreakerLube F
-MIN-
-MAX-
BreakerLube
BreakerLube
Table of contents
Popular Water Pump manuals by other brands
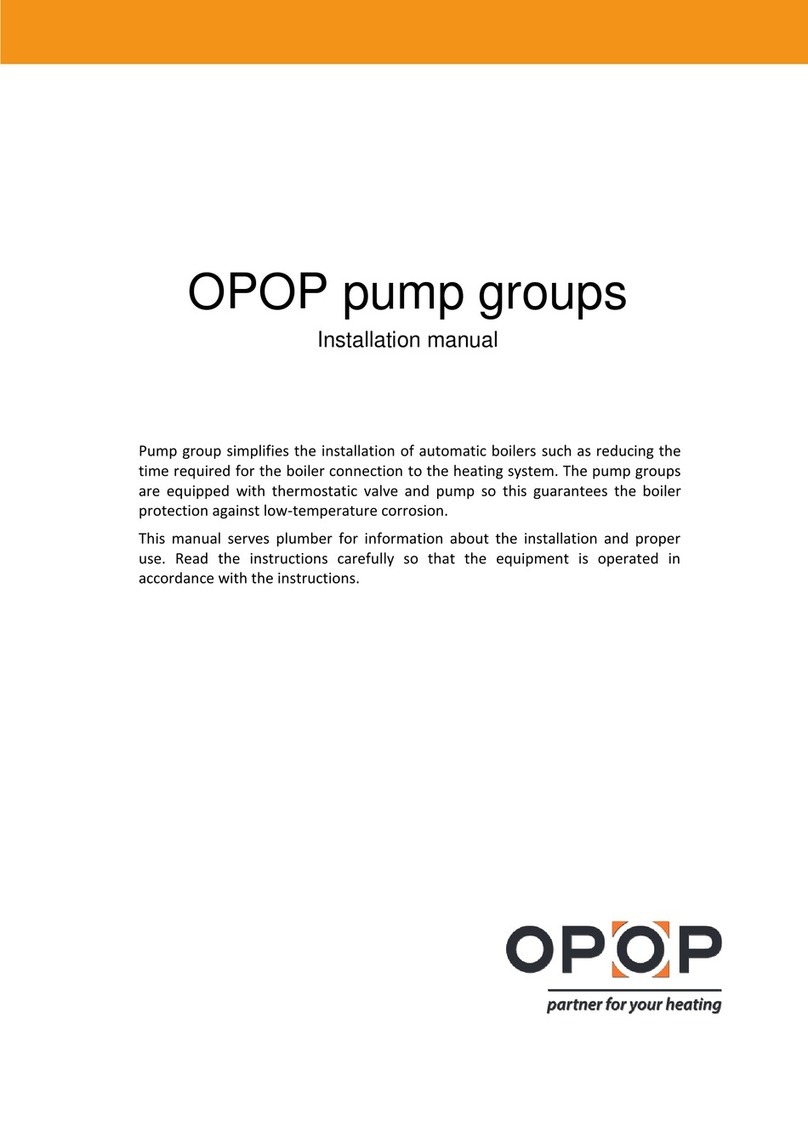
Opop
Opop Biopel 10 installation manual
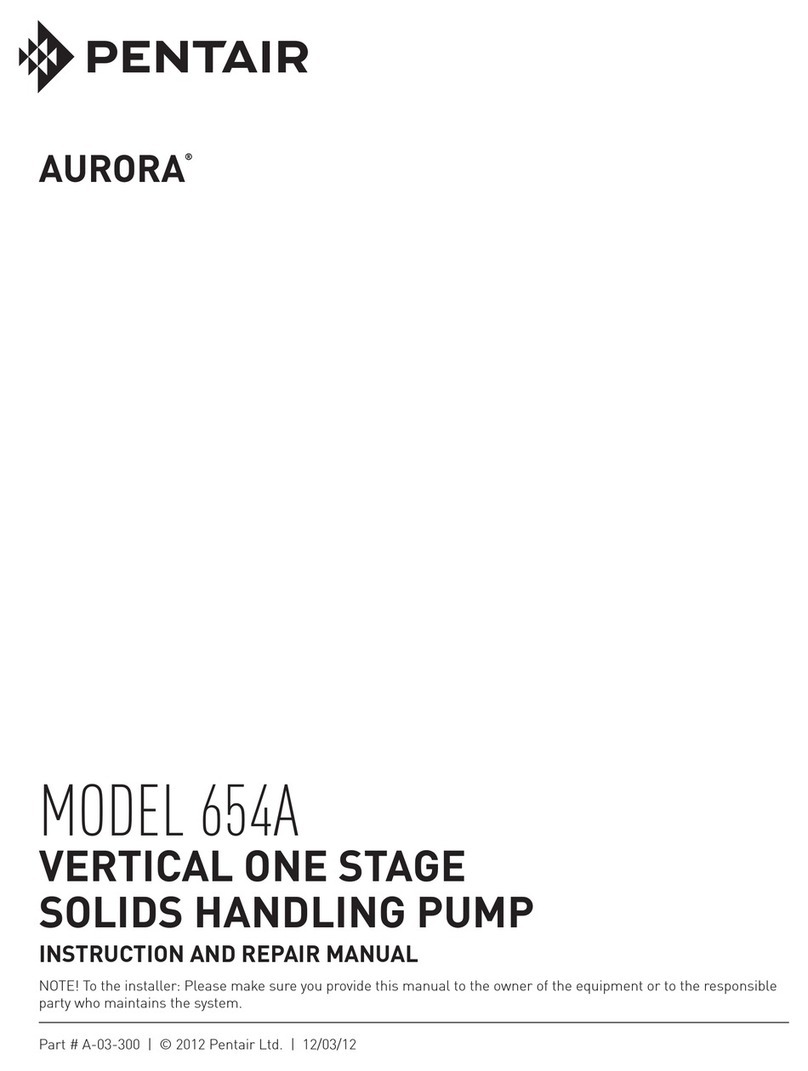
Pentair
Pentair AURORA 654A Instruction and repair manual
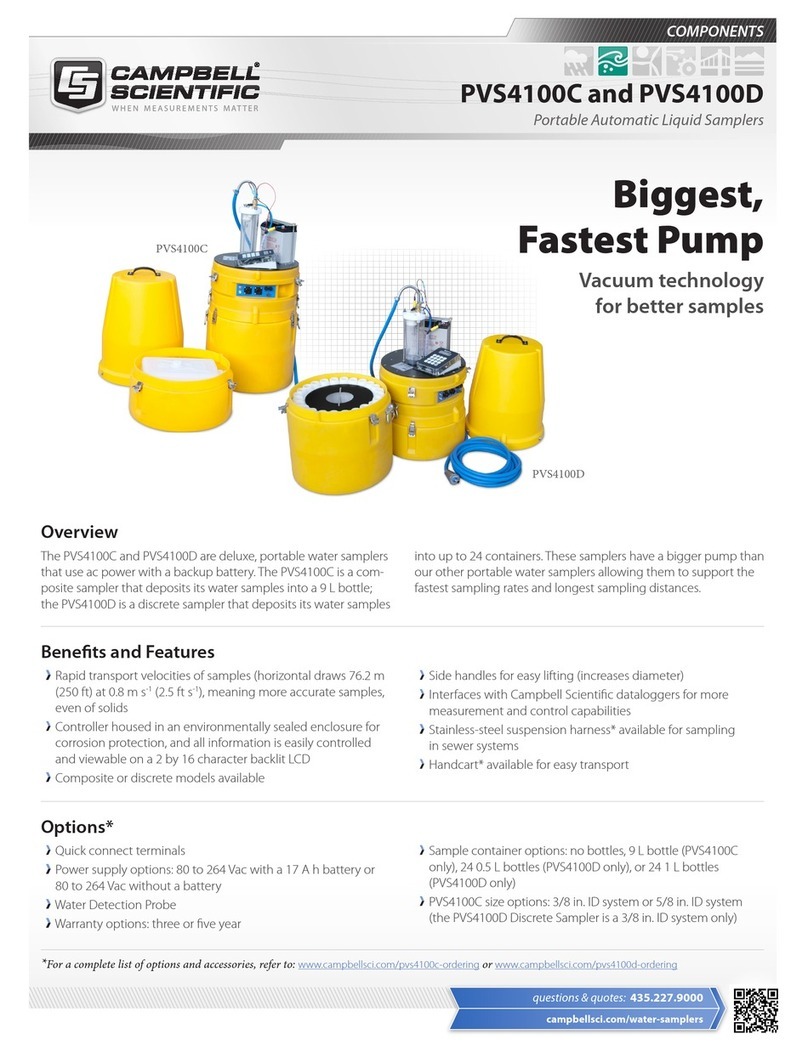
Campbell
Campbell PVS4100C Specifications
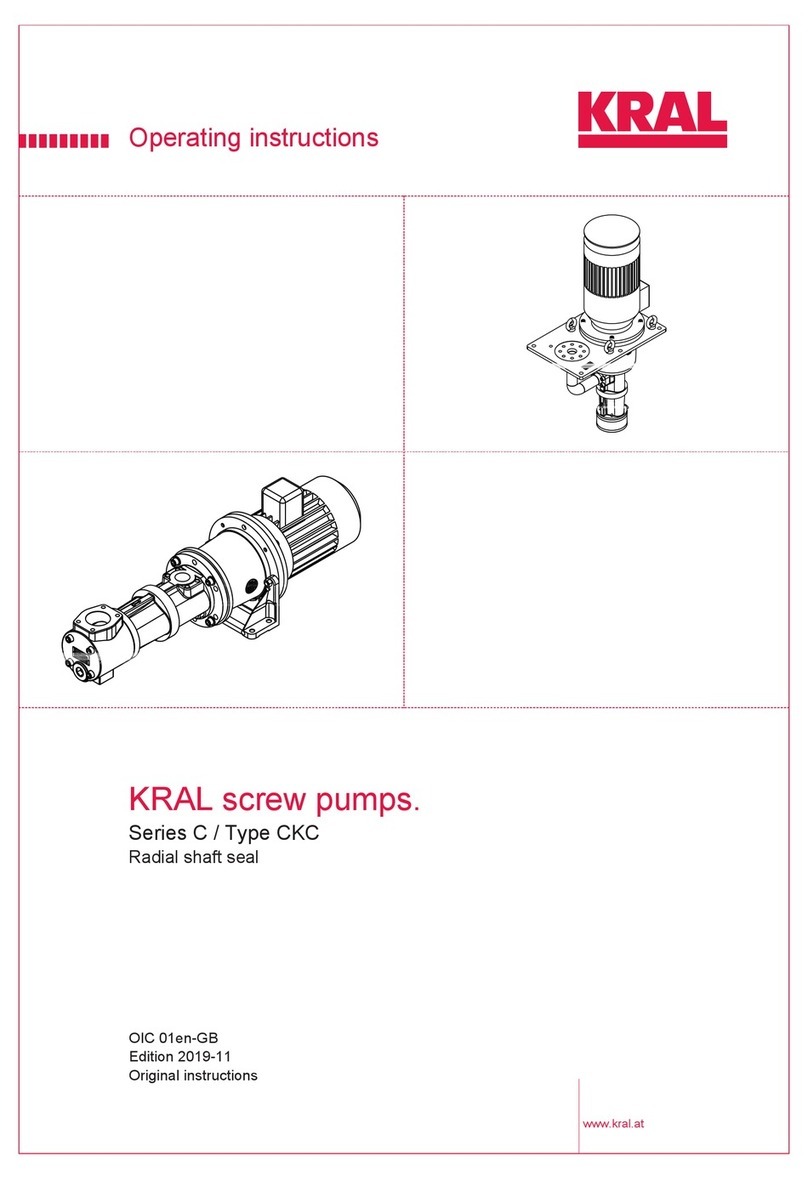
KRAL
KRAL Series C operating instructions
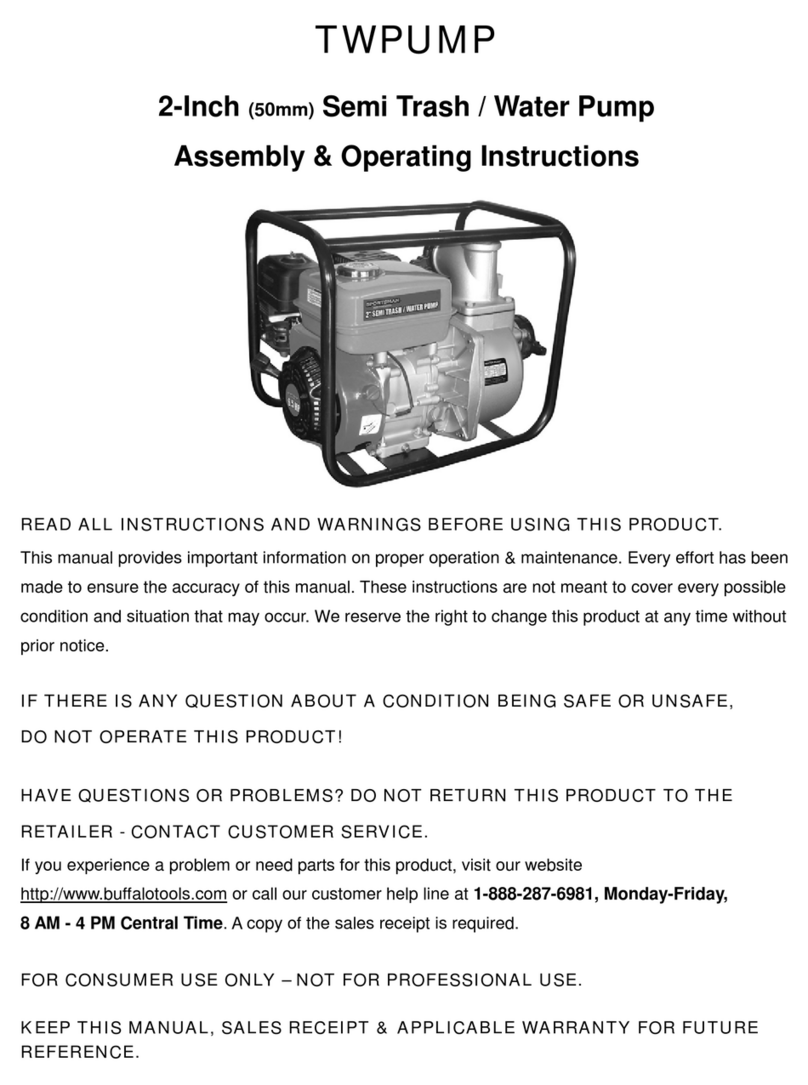
Buffalo Tools
Buffalo Tools TWPUMP Assembly & operating instructions

Kessel
Kessel Pumpfix F Comfort Instructions for assembly, operation and maintenance