AMCI SV160E2 User manual

M
ICRO CONTROLS INC.
ADVANCED
U
s
e
r
M
a
n
u
a
l
Manual #: 940-0S252
E2 Technology

ADVANCED MICRO CONTROLS INC.
GENERAL INFORMATION
Important User Information
The products and application data described in this manual are useful in a wide variety of different applica-
tions. Therefore, the user and others responsible for applying these products described herein are responsible
for determining the acceptability for each application. While efforts have been made to provide accurate infor-
mation within this manual, AMCI assumes no responsibility for the application or the completeness of the
information contained herein.
UNDER NO CIRCUMSTANCES WILL ADVANCED MICRO CONTROLS, INC. BE RESPONSIBLE OR
LIABLE FOR ANY DAMAGES OR LOSSES, INCLUDING INDIRECT OR CONSEQUENTIAL DAM-
AGES OR LOSSES, ARISING FROM THE USE OF ANY INFORMATION CONTAINED WITHIN THIS
MANUAL, OR THE USE OF ANY PRODUCTS OR SERVICES REFERENCED HEREIN.
No patent liability is assumed by AMCI, with respect to use of information, circuits, equipment, or software
described in this manual.
The information contained within this manual is subject to change without notice.
This manual is copyright 2020 by Advanced Micro Controls Inc. You may reproduce this manual, in whole or
in part, for your personal use, provided that this copyright notice is included. You may distribute copies of this
complete manual in electronic format provided that they are unaltered from the version posted by Advanced
Micro Controls Inc. on our official website: www.amci.com. You may incorporate portions of this documents
in other literature for your own personal use provided that you include the notice “Portions of this document
copyright 2020 by Advanced Micro Controls Inc.” You may not alter the contents of this document or charge a
fee for reproducing or distributing it.
Standard Warranty
ADVANCED MICRO CONTROLS, INC. warrants that all equipment manufactured by it will be free from
defects, under normal use, in materials and workmanship for a period of [18] months. Within this warranty
period, AMCI shall, at its option, repair or replace, free of charge, any equipment covered by this warranty
which is returned, shipping charges prepaid, within eighteen months from date of invoice, and which upon
examination proves to be defective in material or workmanship and not caused by accident, misuse, neglect,
alteration, improper installation or improper testing.
The provisions of the "STANDARD WARRANTY" are the sole obligations of AMCI and excludes all other
warranties expressed or implied. In no event shall AMCI be liable for incidental or consequential damages or
for delay in performance of this warranty.
Returns Policy
All equipment being returned to AMCI for repair or replacement, regardless of warranty status, must have a
Return Merchandise Authorization number issued by AMCI. Call (860) 585-1254 with the model number and
serial number (if applicable) along with a description of the problem during regular business hours, Monday
through Friday, 8AM - 5PM Eastern. An "RMA" number will be issued. Equipment must be shipped to AMCI
with transportation charges prepaid. Title and risk of loss or damage remains with the customer until shipment
is received by AMCI.
24 Hour Technical Support Number
24 Hour technical support is available on this product. If you have internet access, start at www.amci.com.
Product documentation and FAQ’s are available on the site that answer most common questions.
If you require additional technical support, call (860) 585-1254. Your call will be answered by the factory dur-
ing regular business hours, Monday through Friday, 8AM - 5PM Eastern. During non-business hours an auto-
mated system will ask you to enter the telephone number you can be reached at. Please remember to include
your area code. The system will page an engineer on call. Please have your product model number and a
description of the problem ready before you call.
Waste Electrical and Electronic Equipment (WEEE)
At the end of life, this equipment should be collected separately from any unsorted municipal waste.

20 Gear Drive, Plymouth Ind. Park, Terryville, CT 06786
Tel: (860) 585-1254 Fax: (860) 584-1973 http://www.amci.com 3
TABLE OF CONTENTS
General Information
Important User Information ..................... 2
Standard Warranty ................................... 2
Returns Policy .......................................... 2
24 Hour Technical Support Number ........ 2
WEEE Statement ..................................... 2
About this Manual
Audience .................................................. 7
Applicable Units ...................................... 7
Navigating this Manual ............................ 7
Manual Conventions ................................ 8
Trademarks and Other Legal Stuff .......... 8
Revision Record ....................................... 8
Revision History ............................ 8
Manual Layout ......................................... 9
Reference: SV160E2 Specifications
E2 Product Family ................................... 11
The SV160E2 Family .............................. 11
General Functionality ................... 11
Safe Torque Off Functionality ....... 12
Network Data Format .................... 12
Specifications ........................................... 13
Indexer Functionality ............................... 14
Driver Functionality ................................. 14
Servo Control ........................................... 15
Absolute Encoder ..................................... 16
Stall Detection .......................................... 16
Available Discrete Inputs ......................... 16
Home Input .................................... 16
CW Limit Switch or
CCW Limit Switch ...................... 16
Start Indexed Move Input .............. 17
Emergency Stop Input ................... 17
Stop Jog or
Registration Move Input .............. 17
Capture Encoder Position Input ..... 17
General Purpose Input ................... 17
Enabling the Driver .................................. 17
STO Option .............................................. 18
Basic Functionality ........................ 18
Additional Functionality ................ 18
Reference: SV160E2 Specifications
(continued)
Status LED’s ............................................ 19
Drive Status LED .......................... 19
Module Status (MS) LED ............. 19
Network Status (NS) LED ............ 20
SV160E2 Connectors ............................... 20
Ethernet Connectors ...................... 20
Digital Inputs Connector ............... 21
Power Connector ........................... 21
Torque and Power Curves ........................ 22
Power Supply Sizing ................................ 22
Regeneration (Back EMF) Effects ........... 23
Compatible Connectors and Cordsets ...... 24
Ethernet Connector ....................... 24
Input Connector ............................ 24
Power Connector ........................... 24
Ethernet Cordset ........................... 24
Input Cordset ................................. 24
Power Cordset ............................... 24
Reference: Motion Control
Definitions ................................................ 25
Units of Measure ........................... 25
Profile Position ............................. 25
Encoder Position ........................... 25
Continuous Torque ....................... 25
Peak Torque .................................. 25
Home Position ............................... 26
Count Direction ............................. 26
Target Position .............................. 26
Relative Coordinates .......... 26
Absolute Coordinates ......... 26
Immediate Stop Deceleration ........ 26
A Simple Move ........................................ 27
Controlled and Immediate Stops .............. 28
Host Control .................................. 28
Hardware Control ......................... 28
Basic Move Types .................................... 29
Relative Move ............................... 29
Controlled Stops ................. 29
Immediate Stops ................. 29
Absolute Move .............................. 30
Controlled Stops ................. 30
Immediate Stops ................. 30

TABLE OF CONTENTS
SV160E2 User Manual
ADVANCED MICRO CONTROLS INC.
4
Reference: Motion Control
(continued)
CW/CCW Jog Move ..................... 31
Controlled Stops ................. 31
Immediate Stops ................. 31
CW/CCW Registration Move ....... 32
Controlled Stops ................. 33
Immediate Stops ................. 33
Indexed Moves ......................................... 34
Axis Follower Moves ............................... 35
Controlling Moves In Progress ................ 36
Jog Moves ..................................... 36
Registration Moves ....................... 36
Absolute and Relative Moves ....... 36
Disabling the Motor ................................. 36
Reference: Move Profile
Calculations
Constant Acceleration Equations ............. 37
Variable Definitions ...................... 37
Total Time Equations .................... 39
Reference: Homing an SV160E2
Definition of Home Position .................... 41
Definition of Homing Speed .................... 41
Position Preset .......................................... 41
CW/CCW Find Home Commands ........... 41
Homing Inputs .......................................... 41
Homing Configurations ............................ 41
Homing Profiles ....................................... 42
Home Input Only Profile .............. 42
Profile with Overtravel Limit ....... 43
Controlling Find Home
Commands In Progress .......................... 44
Controlled Stops ........................... 44
Immediate Stops ........................... 44
Reference: Configuration Mode
Data Format
Modes of Operation .................................. 45
Configuration Mode ...................... 45
Command Mode ........................... 45
Power Up Behavior .................................. 45
Data Format .............................................. 45
Command Mode Data Formats ................ 46
Output Data Format .................................. 47
Configuration Word 0 Format ...... 47
Reference: Configuration Mode
Data Format (cont’d)
Read Data Blocks ..................................... 49
Extended Drive Status ................... 49
Remaining Read Data Blocks ....... 49
Write Data Blocks .................................... 50
Block 1: Data Config Block .......... 50
Block 2: I/O Config Block ............ 50
Block 3: Motor Config Block ....... 51
Block 5: Velocity Control
Loop Config Block ...................... 52
Block 6: Position Control
Loop Config Block ...................... 53
Block 15: Save Config To
Flash Block ................................. 53
Input Data Format ..................................... 54
Config Mode Input Word 0 ........... 54
Config Mode Input Word 1 ........... 55
Invalid Configurations .............................. 55
Reference: Command Mode Data
Format
Command Bits Must Transition ............... 57
Data Format .............................................. 57
Output Data Format .................................. 57
Command Word 0 .................................... 58
Command Word 1 .................................... 59
Command Blocks ..................................... 60
Absolute Move .............................. 60
Relative Move ............................... 61
Hold Move .................................... 61
Resume Move ................................ 62
Immediate Stop ............................. 62
Find Home CW ............................. 63
Find Home CCW ........................... 63
Jog CW .......................................... 64
Registration Move CW ................. 64
Axis Follower Moves .................... 65
Jog CCW ....................................... 66
Registration Move CCW ............... 66
Preset Position ............................... 67
Reset Errors ................................... 67
Enable Driver or
Preset On Enable ......................... 68
Disable Driver ............................... 68
Input Data Format ..................................... 69
Status Word 0 Format ................... 69
Status Word 1 Format ................... 70
Notes on Clearing a Driver Fault .............. 72

20 Gear Drive, Plymouth Ind. Park, Terryville, CT 06786
Tel: (860) 585-1254 Fax: (860) 584-1973 http://www.amci.com
SV160E2 User Manual
TABLE OF CONTENTS
5
Reference: Braking Resistor
Calculations
Overvoltage Threshold Parameter ........... 73
Required Information ............................... 73
Determine System Inertia ........................ 74
Determine the Deceleration Rate ............. 74
Determine Peak Braking Power ............... 74
Determine Minimum Braking
Resistor Value ........................................ 75
Determine Maximum Braking
Resistor Value ........................................ 75
Determine Average Power Rating ........... 75
Determining the Braking Resistor ........... 76
Reference: Configuring Network
Interfaces
Firewall Settings ...................................... 77
Disable All Unused Network Interfaces .. 77
Configure Your Network Interface .......... 77
Test Your Network Interface ................... 78
Task 1: Installing the SV160E2
Location ................................................... 79
Safe Handling Guidelines ........................ 79
Prevent Electrostatic Damage ........ 79
Prevent Debris From
Entering the Unit ......................... 79
Remove Power Before Servicing .. 79
Operating Temperature Guidelines .......... 79
Mounting .................................................. 79
SV160E2 Outline Drawing ............ 80
SV160E2 Mounting ....................... 80
Connecting the Load ...................... 80
Power Connector ...................................... 81
Compatible Connectors
and Cordsets ................................ 81
Power Wiring ........................................... 82
Input Connector ....................................... 82
Compatible Connectors
and Cordsets ................................ 83
CNFL-5M Color Code and
Shield Wire .................................. 83
Cable Shields ................................. 83
DC Input Wiring ...................................... 84
Sinking Sensors Require a
Pull Up Resistor .......................... 84
STO Input Wiring .................................... 85
Extending the STO Cabling ........... 85
Task 1: Installing the SV160E2
(continued)
Network Connectors ................................. 86
Compatible Connectors
and Cordsets ............................... 86
TIA/EIA-568 Color Codes ............ 86
EtherNet/IP Connections .......................... 87
Non-DLR Applications ................. 87
DLR Applications ......................... 87
PROFINET Connections .......................... 87
Non-MRP Applications ................ 87
MRP Applications ......................... 87
Modbus TCP Connections ....................... 87
Task 2: Set the IP Address and
Protocol
Determine the Best Method for
Setting the IP Address 89
Use Factory Default Settings ................... 89
Use the Embedded Web Server ................ 90
Use the AMCI NET
Configurator Utility ................................ 93
Task 3: Implicit Communications
with an EDS
Obtain the EDS file .................................. 97
Install the EDS file ................................... 97
Start the EDS Hardware
Installation Tool .......................... 97
Install the EDS File ....................... 98
Host System Configuration ...................... 100
Add the SV160E2 to Your Project ........... 100
SV160E2 Properties Setup ....................... 101
General Tab ................................... 101
Connection Tab ............................. 101
Configuration Tab ......................... 101
Buffering the I/O Data ............................. 102
Task 4: EtherNet/IP Explicit
Messaging
Required Message Instructions ................ 103
Create Four New Data Files ..................... 103
Add the Message Instructions to
your Ladder Logic .................................. 104
Troubleshooting ....................................... 107

TABLE OF CONTENTS
SV160E2 User Manual
ADVANCED MICRO CONTROLS INC.
6
Task 5: Modbus TCP Configuration
Enable Modbus TCP Protocol .................. 109
Modbus Addressing .................................. 109
Modbus Table Mapping ........................... 109
Host Addressing ....................................... 109
AMCI Modbus TCP Memory Layout ...... 110
Supported Number of Connections .......... 110
Supported Modbus Functions ................... 111
Supported Modbus Exceptions ................. 111
Task 6: PROFINET Network
Configuration
Basic Steps ............................................... 113
Download the GSDML files .................... 113
GSDML File Installation .......................... 113
Configure the PROFINET Network ......... 113
Add the SV160E2 to the
PROFINET Network .............................. 114
Configure the SV160E2 ........................... 116
Set the I/O Configuration ......................... 117
Set the SV160E2 Device Name ............... 118
Verify and Download the
New Configuration ................................. 118
MRP Installations ..................................... 119
Configure the SV160E2 as an MRC ........ 119

20 Gear Drive, Plymouth Ind. Park, Terryville, CT 06786
Tel: (860) 585-1254 Fax: (860) 584-1973 http://www.amci.com 7
ABOUT THIS MANUAL
Audience
This manual explains the installation and operation of AMCI’s SV160E2 Integrated Servo Motors. It is writ-
ten for the engineer responsible for incorporating these products into a design as well as the engineer or tech-
nician responsible for their actual installation.
Applicable Units
This manual applies to all of the units in the SV160E2 family. Each unit contains a two port Ethernet switch,
which simplifies network wiring. When the EtherNet/IP protocol is used, the unit can act as a node in a
Device Level Ring (DLR). When PROFINET is enabled, the unit supports the Media Redundancy Protocol
(MRP) and can be incorporated in PROFINET installations that use a redundant ring topology.
Navigating this Manual
This manual is designed to be used in both printed and on-line forms. Its on-line form is a PDF document,
which requires Adobe Acrobat Reader version 7.0+ to open it. You are allowed to select and copy sections for
use in other documents and add notes and annotations. If you decide to print out this manual, all sections con-
tain an even number of pages which allows you to easily print out a single chapter on a duplex (two-sided)
printer.
Read this chapter to learn how to navigate through this manual and familiarize
yourself with the conventions used in it. The last section of this chapter highlights
the manual’s remaining chapters and their target audience.

ABOUT THIS MANUAL
SV160E2 User Manual
ADVANCED MICRO CONTROLS INC.
8
Manual Conventions
Three icons are used to highlight important information in the manual:
NOTES highlight important concepts, decisions you must make, or the implications of those
decisions.
CAUTIONS tell you when equipment may be damaged if the procedure is not followed
properly.
WARNINGS tell you when people may be hurt or equipment may be damaged if the pro-
cedure is not followed properly.
The following table shows the text formatting conventions:
Manual Conventions
Trademarks and Other Legal Stuff
The AMCI logo is a trademark of Advanced Micro Controls Inc. “CIP” is a trademark of Open DeviceNet
Vendor Association, Inc. “EtherNet/IP” is a trademark of ControlNet International, Ltd. under license by
Open DeviceNet Vendor Association, Inc. “PROFINET” is a registered trademark of PROFIBUS & PROFI-
NET International (PI). “Adobe” and “Acrobat” are registered trademarks of Adobe Systems Incorporated.
All other trademarks contained herein are the property of their respective holders.
Revision Record
This manual, 940-0S252 is the third release of this manual. It was released on April 13th, 2020. It improves
information throughout the manual on the Safe Torque Off (STO) option and adds clarifications to several
areas.
Revision History
940-0S251: September 10th, 2019 - Improved Virtual Axis Move information. Updates torque curve draw-
ing
940-0S250: August 23rd, 2019 - Initial Release
Format Description
Normal Font Font used throughout this manual.
Emphasis Font Font used for parameter names and the first time a new term is introduced.
Cross Reference When viewing the PDF version of the manual, clicking on a blue cross refer-
ence jumps you to referenced section of the manual.
HTML Reference When viewing the PDF version of the manual, clicking on a red cross reference
opens your default web browser to the referenced section of the AMCI website
if you have Internet access.

20 Gear Drive, Plymouth Ind. Park, Terryville, CT 06786
Tel: (860) 585-1254 Fax: (860) 584-1973 http://www.amci.com
SV160E2 User Manual
ABOUT THIS MANUAL
9
Manual Layout
You will most likely read this manual for one of two reasons:
If you are curious about the Integrated Servo Motor products from AMCI, this manual contains the
information you need to determine if these products are the right products for your application. The first
chapter, SV160E2 Specifications contains all of the information you will need to fully specify the right
product for your application.
If you need to install and use an Integrated Servo Motor product from AMCI, then the rest of the man-
ual is written for you. To simplify installation and configuration, the rest of the manual is broken down
into references and tasks. Using an Integrated Servo Motor product requires you to complete multiple
tasks, and the manual is broken down into sections that explain how to complete each one.
Manual Sections
Section Title Page
Num. Section Description
SV160E2 Specifications 11 Complete specifications for the SV160E2 products.
Motion Control 25 Reference information on how the SV160E2 can be used to control
motion in your application.
Move Profile Calculations 37 Reference information on calculating detailed move profiles.
Homing an SV160E2 41 Reference information on how to set the home position of the
SV160E2.
Configuration Mode Data
Format 45 Reference information on the format of the network data to and
from the SV160E2 that is used to configure it.
Command Mode Data
Format 57 Reference information on the format of the network data to and
from the SV160E2 that is used to command it.
Braking Resistor
Calculations 73 Calculations required to size the braking resistor for proper power
dissipation during deceleration.
Configuring Network
Interfaces 77 Basic instructions for the task of configuring network interfaces on
your computer or laptop.
Installing the SV160E2 79 Task instructions covering how to install an SV160E2 on a
machine. Includes information on mounting, grounding, and wir-
ing specific to the units.
Set the IP Address and
Protocol 89 Task instructions that covers the options for setting the IP address
and protocol on an SV160E2.
Implicit Communications
with an EDS 97 Task instructions that cover how to add an SV160E2 to an
EtherNet/IP host that supports the use of EDS files.
EtherNet/IP Explicit
Messaging 103 Task instructions for adding message instructions to you host con-
troller program that write data to the SV160E2 through message
instructions.
Modbus TCP
Configuration 109 Task instructions for communicating with an SV160E2 using the
Modbus TCP protocol.
PROFINET Network
Configuration 113 Task instructions that covers how to add an SV160E2 to a
PROFINET network.

ABOUT THIS MANUAL
SV160E2 User Manual
ADVANCED MICRO CONTROLS INC.
10
Notes

20 Gear Drive, Plymouth Ind. Park, Terryville, CT 06786
Tel: (860) 585-1254 Fax: (860) 584-1973 http://www.amci.com 11
REFERENCE 1
SV160E2 SPECIFICATIONS
E2 Product Family
The SV160E2 is an addition to the family of E2 products from AMCI. E2 products incorporate E2 Technol-
ogy, a common Ethernet network interface that allows them to operate over the EtherNet/IP, Modbus TCP,
and PROFINET industrial networks. The E2 product family encompasses stepper and servo integrated
motion control products, resolver based encoder products, and specialty I/O products for sensor interface and
motion control.
The SV160E2 Family
The SV160E2 units combine a servo indexer, driver, and
160W BLDC motor that can be attached to any popular
industrial network. Each SV160E2 attaches to your Ether-
net network and communicates using the EtherNet/IP,
Modbus TCP, or PROFINET protocols.
E2 Technology products are simple and intuitive, allow-
ing easy transition between multiple common industrial
Ethernet protocols without the need to physically switch
parts. An advanced web server integrated into all AMCI
E2 Technology devices facilitates simple device configu-
ration and troubleshooting via a web-browser. Further-
more, an impressive array of advanced features for each
supported protocol has been incorporated into the devices
to meet many unique application requirements.
Each unit has two Ethernet ports which are internally con-
nected through an onboard, two port, 10/100 Mbps ether-
net switch. These ports allow you to wire your network in
a “daisy-chain” fashion, which may lower network wiring
costs and complexities.
The two ports also allows units to function as members of a
redundant Device Level Ring (DLR) network when using
the EtherNet/IP protocol or as clients in a Media Redun-
dancy Protocol (MRP) network when using PROFINET.
In DLR environments, the SV160E2 units act as Beacon-
Based Ring Nodes. All units can process beacon packets at the default rate of every 400 microseconds. Beacon-
based nodes can respond faster to network changes than nodes that only process Announce packets.
General Functionality
Each SV160E2 has four integrated parts:
An indexer that accepts commands over an Ethernet connection using the EtherNet/IP, PROFINET, or
Modbus TCP protocol
A 6.0 A continuous, 13.0 A peak BLDC driver that accepts 48 to 80 Vdc as its input power source
A high torque 160 watt BLDC motor
An absolute multi-turn encoder.
The availability of the EtherNet/IP, PROFINET, and Modbus TCP protocols makes the
SV160E2
unit easy to
integrate into a wide variety of control systems.
This manual is designed to get you up and running quickly with an SV160E2 prod-
uct from AMCI. As such, it assumes you have some basic knowledge of servo sys-
tems.
Figure R1.1 SV160E2

SV160E2 SPECIFICATIONS
SV160E2 User Manual
ADVANCED MICRO CONTROLS INC.
12
The SV160E2 Family (continued)
General Functionality (continued)
This combination of host and driver gives you several advantages:
Sophisticated I/O processing can be performed in the host (PLC or other controller) before sending
commands to the SV160E2 unit
All motion logic is programmed in the host, eliminating the need to learn a separate motion control lan-
guage
The integral two port Ethernet switch simplifies network cabling
The DLR interface eliminates single point failures in EtherNet/IP environments
The MRP interface eliminates single point failures in PROFINET environments.
An SV160E2 is powered by a nominal 48 to 80 Vdc power source, and can accept surge voltages of up to
100 Vdc without damage. The continuous motor torque is fully programmable from 0.1 Nm to 0.50 Nm with
the Continuous Torque Limit parameter. The peak motor torque, which is used during times of acceleration
and deceleration, is fully programmable up to 1.3Nm with the Peak Torque Limit parameter. These program-
mable torque settings makes the SV160E2 suitable to a wide range of applications.
The SV160E2 units have four 12 to 24 Vdc inputs that are used by the indexer. Configuration data from the
host sets the function of these inputs. Each input can be individually configured as a:
CW or CCW Limit Switch
Home Limit Switch
Capture Position Input (Will capture the encoder position.)
Stop Manual or Registration Move Input
Start Indexed Move
Emergency Stop Input
General Purpose Input
Safe Torque Off Functionality
The SV160E2 can be ordered with STO (Safe Torque Off) functionality under the part number
SV160E2-STO. Safe Torque Off allows you to remove power from the motor without removing power from
the drive. This reduces implementation costs and restart times.
The STO functionality requires two dedicated inputs. The SV160E2-STO uses inputs 3 and 4. When an
SV160E2-STO is ordered, additional circuitry is added to these inputs for the STO functionality. This addi-
tional circuitry makes the inputs unsuitable for other functions such as end of travel limit switches or home
inputs.
STO is a hardware only solution and is not dependant on software running within the SV160E2-STO. Both of
the STO inputs must be powered by a 12 to 24 Vdc source to enable the drive. When power is removed from
either of these inputs, power to the motor is directly removed from the power stage through the additional cir-
cuitry. The machine will come to an uncontrolled coasting stop if the motor is in motion when the STO fea-
ture triggers. Power remains removed from the motor until the inputs are reactivated, the fault status bits are
cleared, and the driver is re-enabled.
Network Data Format
In order to support any host that communicates with the EtherNet/IP, PROFINET, or Modbus TCP protocols,
the format of the 32 bit integer values read from and written to the SV160E2 is programmable. The parameter,
called
Data Endian
, controls the order of the two 16-bit words in the 32 bit value. Least significant word first
is called
little endian
, most significant word first is called
big endian
. Rockwell Automation controllers use
lit-
tle endian
format, while the default PROFINET and Modbus format is
big endian
.

20 Gear Drive, Plymouth Ind. Park, Terryville, CT 06786
Tel: (860) 585-1254 Fax: (860) 584-1973 http://www.amci.com
SV160E2 User Manual
SV160E2 SPECIFICATIONS
13
Specifications
Network Interface
10/100baseT. Two switched ports.
Supports EtherNet/IP, PROFINET, and Modbus
TCP. EtherNet/IP-DLR and PROFINET-MRP
extensions also supported.
Physical Dimensions
See page 80
Weight
3.4 lbs. (1.5 kg.)
Weight is without mating connectors
Maximum Shaft Loads
Radial: 45 lbs. (200N) at end of shaft
Axial: 13.5 lbs. (60N)
Maximum Operating Temperature
203°F /95°C (Note that this is the operating tem-
perature of the electronics, not maximum ambi-
ent temperature. An over-temperature fault
occurs at this point and current is removed from
the motor.)
Over Temperature Fault
Over-temperature faults are reported in the Net-
work Input Data.
Inputs
Electrical Characteristics:
Single ended sinking.
Accept 10.6 to 27 Vdc without the need for an
external current limiting resistor. Optoisolated,
1500 Vac/dc isolation.
Motor Inertia
48 x 10-6 kg·m2
Torque Constant
0.124 Nm/A. Torque generated by the motor
can be estimated by multiplying the Torque
Constant by the motor current reported in the
Network Input Data.
Continuous Torque
Programmable from 0.10 to 0.50 Nm in 0.01 Nm
steps.
Peak Torque
Programmable to 1.30 Nm in 0.01 Nm steps.
Motor Counts per Turn
16,384
Internal Encoder
Absolute 31 bit multi-turn encoder 16,384 counts
per turn.
Environmental Specifications
Input Power ....... 48 to 80 Vdc, surge to 100 Vdc
without damage to unit.
Ambient Operating Temperature
............ -40° to 122°F (-40° to 50°C)
Storage Temperature
............ -40° to 185°F (-40° to 85°C)
Humidity ............ 0 to 95%, non-condensing
IP Rating ............ IP64
Status LED’s
See Status LED’s section starting on page 19.
Connectors and Cables
All mating connectors are available separately
under the following AMCI part numbers.
Connector AMCI Part # Wire Strip Length Connection Type
Ethernet MS-28 18 AWG max. 0.197 inches Screw Terminals
I/O MS-37 20 AWG max. 0.197 inches Screw Terminals
Power MS-41 16 AWG max. 0.197 inches Screw Terminals
Cable AMCI Part # Length
Ethernet CNER-5M 5 meter
Digital I/O CNFL-5M 5 meter
Power CNGL-5M 5 meter

SV160E2 SPECIFICATIONS
SV160E2 User Manual
ADVANCED MICRO CONTROLS INC.
14
Indexer Functionality
The table below lists the functionality offered by the indexer built into the AMCI SV160E2 units.
Table R1.1 Indexer Functionality
Driver Functionality
This table summarizes the features of the servo motor driver portion of the SV160E2 units.
Table R1.2 Driver Functionality
Feature Description
Multiple Network
Protocols The SV160E2 units can be configured to communicate with EtherNet/IP,
PROFINET, or Modbus TCP protocols. This allows easy setup and
communication with a wide range of host controllers.
EtherNet/IP-DLR The SV160E2 units act as Beacon-Based Nodes in Device Level Ring environ-
ments. This functionality results in the fastest response to changes in the redun-
dant network.
PROFINET-MRP SV160E2 units have Media Redundancy Protocol support, which adds redun-
dancy to the PROFINET protocol.
Programmable
Inputs Each of the inputs can be programmed as a Home Limit, Over Travel Limit, Cap-
ture Input, Manual Jog Stop, Start Indexed Move, E-Stop, or a General Purpose
Input.
Programmable
Parameters PID variables, running speed, acceleration, and deceleration, are fully program-
mable.
Homing Allows you to set the machine to a known position. An SV160E2 homes to a dis-
crete input.
Jog Move Allows you to drive the motor in either direction as long as the command is active.
Axis Follower Move Allows you to treat the SV160E2 as a motion axis by constantly updating position
and velocity data to the unit. Linear and Circular axes are both supported.
Relative Move Allows you to drive the motor a specific number of counts in either direction from
the current location.
Absolute Move Allows you to drive the motor from one known location to another known
location.
Registration Move Allows you to jog the motor in either direction based on a command from your
host controller. When a controlled stop is issued, the move will continue for a pro-
grammable number of steps before coming to a stop.
Indexed Move Allows you to program a move that is held in memory. The move is run when one
of the programmable inputs makes a transition.
Hold Move Allows you to suspend a move, and optionally restart it, without losing your posi-
tion value.
Resume Move Allows you to restart a previously held move operation.
Immediate Stop Allows you to immediately stop all motion if an error condition is detected by
your host controller.
Feature Benefits
Continuous and Peak
Torque Control Continuous and peak torque control give an SV160E2 the ability to drive the
motor at its rated steady state power limit as well as increase its torque out-
put during times of acceleration and deceleration.
Over Temperature
Detection An SV160E2 sets a warning bit in the network data when the internal tem-
perature of the unit approaches its safe operating threshold.
Over Temperature
Protection Protects your SV160E2 from damage by removing power from the motor if
the internal temperature of the driver exceeds the safe operating threshold of
203°F/95°C.

20 Gear Drive, Plymouth Ind. Park, Terryville, CT 06786
Tel: (860) 585-1254 Fax: (860) 584-1973 http://www.amci.com
SV160E2 User Manual
SV160E2 SPECIFICATIONS
15
Servo Control
The SV160E2 uses three control loops to control the position and velocity of the motor. The inner most loop
is the current loop. The optimum PID values for the current loop are solely dependant on motor characteris-
tics. These values are set at the factory during the final test of the SV160E2 and are stored in the device’s
flash memory. In order to simplify programming, these current loop values are not available to the end user
since they are optimized at the factory.
The next inner loop is the velocity loop. This is implemented as a PI loop that includes a programmable low
pass filter on the velocity feedback. This filter is used to reduce high frequency stability issues that may exist
in some applications.
The outer most loop is the position loop. This is a full PID loop that generates the velocity setpoint for the
velocity PI loop.
The position setpoint, SPPOS in the figure below, is generated and updated by the SV160E2 through the
motion profile generator. The velocity feed forward value, FFVEL in the figure below, is also generated by the
motion profile generator.
Figure R1.2 Cascade PID Loop Control
The P, I, and D variables of the position loop, as well as the P and I variables of the velocity loop, can be
directly programmed as part of the configuration data. This gives the end user the ability to fine tune parame-
ters in applications that require the highest performance levels. This can also complicate system startup. To
simplify the startup procedure as much as possible, starting values for these variables are published later in
this manual for load inertia values from one to twenty times the motor inertia value.
–
–
+
+
+
+
++
+
+
=
=
=
=
Velocity
Calculation
with
Programmable
LowPass Filter
Current
PID Loop
Motor
Power
Stage
BLDC
Motor
ABS Encoder
Position Feedback
Current
Feedback
Velocity Feedback
KP_VEL
512
+
–
X
KP_POS
32,768
X
KD_POS
32,768
dt
E
POS
(t)
X
KI_VEL
4,096
Ed
VEL
X
∫
0
0
KI_POS
262,144
Ed
POS
X
∫
I
I
D
P
V
elocity
PI Loop
Factory
Set
Current
PID Loop
Position
PID Loop
P
SPPOS
FFVEL
SP
VEL
SP
CUR
E
VEL
E
VEL
EPOS
EPOS

SV160E2 SPECIFICATIONS
SV160E2 User Manual
ADVANCED MICRO CONTROLS INC.
16
Absolute Encoder
The absolute encoder has a fixed resolution of 16,384 counts per turn. The absolute encoder is a multi-turn
device that encodes a total of 217 turns, yielding a full thirty-one bits of position resolution. The Profile and
Encoder positions are reported back with a range of ±230 counts, and range from -1,073,741,824 to
1,073,741,823
Like many intelligent absolute encoders on the market today, the absolute encoder in the SV160E2 uses a bat-
tery backed circuit to count zero crossings while power is removed from the rest of the device. The battery
life is 10 years in the absence of power. The circuit will accurately track position as long as the shaft acceler-
ation is limited to 160,000 degrees/sec2,(444.4 rev/sec2), or less.
Stall Detection
A motor stall is detected when the Encoder Position differs from the calculated Profile Position by a pro-
grammed amount. This amount is programmed with the Maximum Position Error Limit parameter. Stalls can
occur because the programmed Continuous Torque Limit or Peak Torque Limit values are set too low, the
move’s programmed acceleration or deceleration values are set too high, or the loads’ torque requirements
have increased due to a mechanical change in the system.
When a stall is detected:
1) The Stall_Detected bit is set in the data reported to the host controller.
2) The Profile Position is set equal to the Encoder Position.
3) The SV160E2 preforms an immediate stop. The rate of deceleration during an immediate stop is
programmable with the Immediate Stop Deceleration parameter. The immediate stop deceleration can be
programmed from 1,500,000 steps/sec2to 15,999,000 steps/sec2. The SV160E2 will stop all motion
immediately if the Immediate Stop Deceleration parameter is set to zero.
4) Once the immediate stop completes, the SV160E2 checks the difference between the Encoder Position and
calculated Profile Position. If the error is less than the programmed Maximum Position Error Limit
parameter the motor will stay enabled. If the error exceeds the Maximum Position Error Limit parameter,
the motor is disabled and a Position_Invalid bit is set to “1” to signal the host controller of the error.
Available Discrete Inputs
The standard SV160E2 has four discrete DC inputs, Inputs 1 - 4. The SV160E2-STO has two discrete DC
inputs, Inputs 1 and 2, in addition to its two STO inputs. These discrete DC inputs accept a nominal 12 to 24
Vdc signal and their functionality is fully programmable. The active state of each input is also programmable.
Programming their active states allow them to act as Normally Open (NO) or Normally Closed (NC) contacts.
All of these inputs are open collector sinking and share their common connection. The remainder of this sec-
tion describes the available functionality.
Home Input
Many applications require that the machine be brought to a known position before normal operation can
begin. This is commonly called “homing” the machine or bringing the machine to its “home” position. An
SV160E2 allows you to define this starting position in two ways. The first is with a Position Preset command.
The second is with a sensor mounted on the machine. When you define one of the inputs as the Home Input,
you can issue commands to the SV160E2 that will cause the unit to seek this sensor. How the SV160E2 actu-
ally finds the home sensor is described in the reference chapter Homing an SV160E2 starting on page 41.
CW Limit Switch or CCW Limit Switch
Each input can be defined as a CW or CCW Limit Switch. When used this way, the inputs are used to define
the limits of mechanical travel. For example, if you are moving in a clockwise direction and the CW Limit
Switch activates, all motion will immediately stop. At this point, you will only be able to jog in the counter-
clockwise direction.

20 Gear Drive, Plymouth Ind. Park, Terryville, CT 06786
Tel: (860) 585-1254 Fax: (860) 584-1973 http://www.amci.com
SV160E2 User Manual
SV160E2 SPECIFICATIONS
17
Available Discrete Inputs (continued)
Start Indexed Move Input
Indexed Moves are programmed through the Network Data like every other move. The only difference is that
Indexed Moves are not run until a Start Indexed Move Input makes a inactive-to-active state transition. This
allows an SV160E2 to run critically timed moves that cannot be reliably started from the network due to data
transfer lags.
Emergency Stop Input
When an input is defined as an Emergency Stop, or E-Stop, Input and it is activated, motion will come to an
Immediate Stop. The move cannot be restarted. The Immediate Stop Deceleration parameter, described on
page 26, is used to decelerate the load. If a stall is not detected during the stop, the motor will return to the
Profile Position value. If a stall is detected during the stop, the SV160E2 will disable the motor and issue a
Position_Invalid fault. See Stall Detection on page 16 for a description of the stall detection process.
Any move, including a Jog or Registration Move, cannot begin while this input is active.
Stop Jog or Registration Move Input
When an input is configured as a Stop Jog or Registration Move Input, triggering this input during a Jog
Move or Registration Move will bring the move to a controlled stop. The controlled stop is triggered on an
inactive-to-active state change on the input. Only Jog Moves and Registration Moves can be stopped this
way, all other moves ignore this input.
Capture Encoder Position Input
As described in the Start Indexed Move Input and Stop Jog or Registration Move Input sections above, an
SV160E2 can be configured to capture the encoder position value on a transition of a discrete DC input.
General Purpose Input
If your application does not require one or more of the inputs, you can configure the unused inputs as General
Purpose Inputs. The inputs are not used by the SV160E2, but their on/off state is reported in the network data
and is available to your host controller.
Enabling the Driver
The SV160E2 performs multiple checks before enabling power to the motor.
The unit must be in Command Mode.
A Configuration error must not exist.
The unit must pass its internal checks. (The Module_OK status bit must equal “1”.
The power stage must not be in an over temperature or over current condition.
The DC Bus Voltage must be between 19 Vdc and 95 Vdc.
When using the Over Voltage Threshold parameter, the input voltage must be less than 90% of this
value. (If the Threshold is set to 79.2 Vdc, the input voltage cannot exceed 79.2*0.9 = 72 Vdc.)
If configured, an Emergency Stop input must not be active.
The encoder must pass its operational checks and be providing a valid position
The difference between the Profile Position and the Encoder Position must be less than ±4,096 counts
or the Preset_On_Enable bit must be set. (When set, the Encoder Position is set to the Profile Position
when the motor is enabled.
On STO units, the STO_Active and STO_Failure bits must both be “0”. (See below for a description of
the STO Option.)

SV160E2 SPECIFICATIONS
SV160E2 User Manual
ADVANCED MICRO CONTROLS INC.
18
STO Option
As stated previously, the STO option adds additional circuitry that allows power to be removed from the
power stage of the motor directly. This is a hardware only solution. If either of the two redundant inputs is
inactive, power is removed. This state cannot be overridden by software control.
Inputs 3 and 4 are used as the redundant STO inputs. When an SV160E2 is ordered with the STO functional-
ity, additional components are added to the PC board that directly connects these two inputs to the power
stage of the motor.
An SV160E2-STO reports two additional status bits to the host controller; STO_Active, and STO_Failure.
Basic Functionality
STO_Active: Normally ‘0’, this bit is set to ‘1’ when power is removed from the motor because one or
both of Inputs 3 and 4 are inactive. This bit resets itself to ‘0’ when both inputs are active.
STO_Failure: Normally ‘0’, this bit is set to ‘1’ when either or both of Inputs 3 and 4 are inactive, but
the power stage is reporting that it is still active. If this occurs, the SV160E2 will attempt to disable the
power stage through its programming and will refuse to accept move commands. This bit cannot be
cleared by commands from the host controller. It can only be cleared by cycling power to the unit.
Figure R1.3 Basic STO Operation
Additional Functionality
The STO option adds an additional configuration parameter called the Discrepancy Timer Limit. The factory
defaults leave this parameter at 0, which disables the additional functionality. When set to a non-zero value,
the SV160E2-STO performs additional checks to monitor the STO signals for proper operation. The range of
values for the Discrepancy Timer Limit is 0, and 50 to 3,000. The values of 50 to 3,000 represent time in mil-
liseconds.
In normal STO operation, the two redundant inputs change state simultaneously. The inputs being in different
states is an indication of a wiring issue or hardware fault. The Discrepancy Timer Limit parameter sets:
the maximum time that the two inputs can be in different states before the SV160-STO triggers an
STO_Failure non-clearable fault
the minimum time that an input must stay stable between state changes, both active-to-inactive and
inactive-to-active
When recovering from an STO event, if the inputs are active for less than the Discrepancy Timer Limit, the
SV160STO triggers the STO_Failure non-clearable fault.
STOA
STOB
Normal
Operation
Normal
Operation
STO
Cleared
Drive
Re-Enabled
In STO
STO_Active
STO_Failure
Driver_Fault
Drive_Enabled
Enable_Drive
Inputs
Cmd
Status
Drive Enabled on
0 1 transition of
the Enable
_
Drive bit.

20 Gear Drive, Plymouth Ind. Park, Terryville, CT 06786
Tel: (860) 585-1254 Fax: (860) 584-1973 http://www.amci.com
SV160E2 User Manual
SV160E2 SPECIFICATIONS
19
Status LED’s
Each SV160E2 has three status LED’s. As shown in figure R1.4, these LED’s are located on the rear cover.
Drive Status LED
The Drive Status LED is a bi-color red/green LED. This LED shows the state of the unit as a whole.
Figure R1.4 Drive Status LED States and LED Locations
Module Status (MS) LED
The Module Status LED is a bi-color red/green LED. The state of the LED depends on the state of the net-
work adapter module.
Table R1.3 Module Status LED States
LED State EtherNet/IP Definition Modbus TCP Definition PROFINET Definition
Off No Power No Power No power
Alternating
Red/Green
Initializing: Power up Self-Test
Communications failure. There is a communications error between the main processor and
the ethernet co-processor within the unit. You must cycle power to the SV160E2 to attempt
to clear this fault.
Flashing
Green
Initializing: Waiting for valid physical connection to the
network.
Successful write to flash memory. Power must be cycled to the unit before additional
commands can be written to it.
Steady Green Drive and Network are
operational. Drive and Network are
operational. Device Name or IP Address
are set.
Flashing Red
Initializing: IP Address conflict. Initializing: Device Name or
IP Address are not set.
If the Network Status LED is also flashing, the IP Address or Network Protocol has been
changed. Cycle power to the unit to continue. If the Network Status LED is in any other
state, a write to flash memory has failed. Cycle power to the unit to clear this fault.
No Power
No Faults, Drive Enabled,
No Motion
Red Green Off
No Faults, Drive Enabled,
Motion Occurring
Drive Enabled, Command
Error or Input Error
Drive Disabled
Drive Disabled and
Command or Input Error
Configuration Error
or Encoder Fault
Unit Fault
1 Second 1 Second

SV160E2 SPECIFICATIONS
SV160E2 User Manual
ADVANCED MICRO CONTROLS INC.
20
Status LED’s (continued)
Network Status (NS) LED
The Network Status LED is a bi-color red/green LED. The state of the LED depends on the protocol the
SV160E2 is configured to.
Table R1.4 Network Status LED States
SV160E2 Connectors
Ethernet Connectors
Figure R1.5 shows the placement of the connectors on an SV160E2
unit. Figure R1.6 shows the pinout of the Ethernet connectors when
viewed from the back of the SV160E2. Each Ethernet port on the
SV160E2 is an “auto-sense” port that will automatically switch
between 10baseT and 100baseT depending on the network equip-
ment it is attached to. Each port also has “auto switch” capability.
This means that a standard cable can be used when connecting the
SV160E2 to any device, including a personal computer.
Figure R1.6 Ethernet Connector Pinout
The connector is a standard four pin D-coded female M12 connector that is rated to IP67 when the mate is
properly installed. Note that the orientation of the key differs between the two ports.
LED State EtherNet/IP Definition Modbus TCP Definition PROFINET Definition
Off No Power No power or no TCP
connections
No power, duplicate IP
address on the network,
mismatch in Device Name,
or no connection to IO Con-
troller.
Alternating
Red/Green Power up Self-Test Power up Self-Test Power up Self-Test
Flashing
Green
Ethernet connection.
No Implicit CIP con-
nections, but Explicit
CIP connections may
exist.
Indicates number of connec-
tions with 2 second delay
between group. The
SV160E2 supports up to
five concurrent connections.
On-line, Stop state. A con-
nection with the IO Control-
ler is established and it is in
its STOP state.
Steady Green Valid Ethernet network
and CIP connections Should not occur. LED
should always flash when
network is connected.
On-line, Run state. A con-
nection with the IO Control-
ler is established and it is in
its RUN state.
Flashing Red
If the MS LED is
steady green: Network
Connection Timeout Not Implemented Not Implemented
If the MS LED is blinking green: IP Address or Network Protocol changed: Cycle
power
Steady Red Duplicate IP address on network. Not Implemented.
Figure R1.5 SV160E2 Connector Locations
POWER: 48 to 80 Vdc
MS
NS STATUS
PORT 1 PORT 2I/O
Pin 1: +Tx
Pin 2: +Rx
Pin 4: –Rx
Pin 3: –Tx
ETHERNET
Por ts 1 & 2
Table of contents
Other AMCI Servo Drive manuals
Popular Servo Drive manuals by other brands
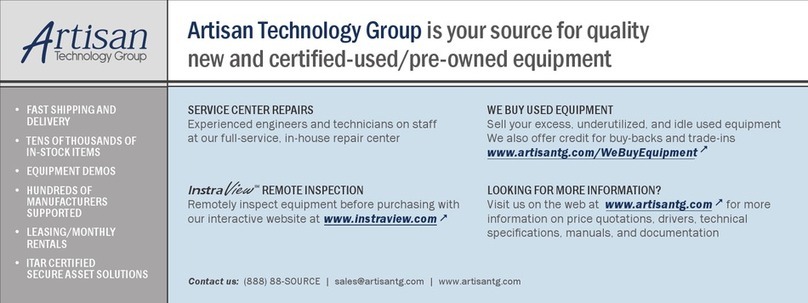
Sanyo Denki
Sanyo Denki PY Series Installation and operation manual
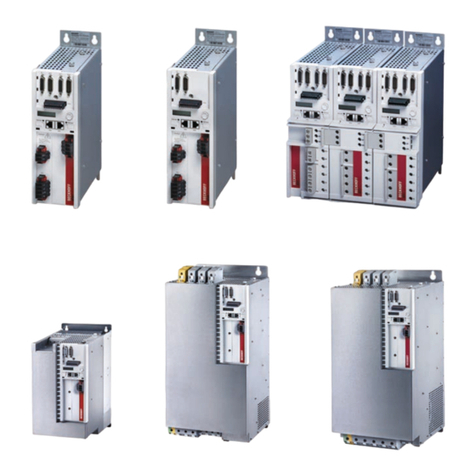
Beckhoff
Beckhoff AX5000 Series Tuning guide
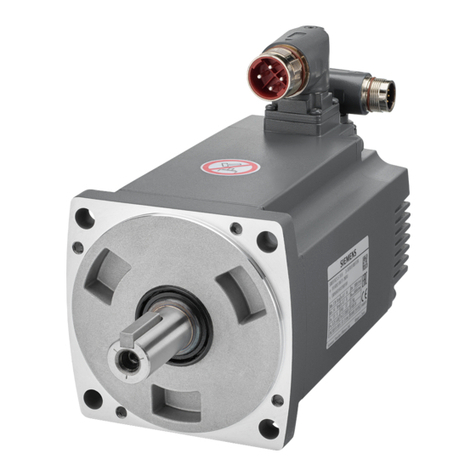
Siemens
Siemens SINAMICS V90 operating instructions
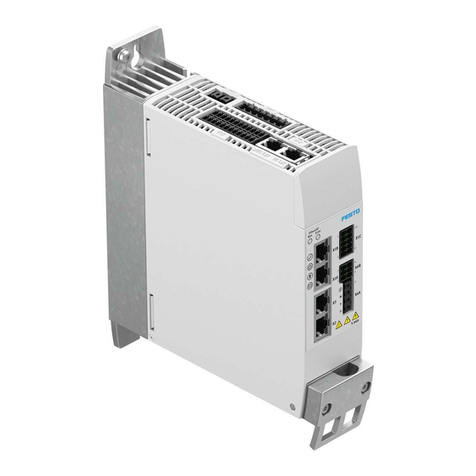
Festo
Festo CMMT-AS Series Translation of the original instructions
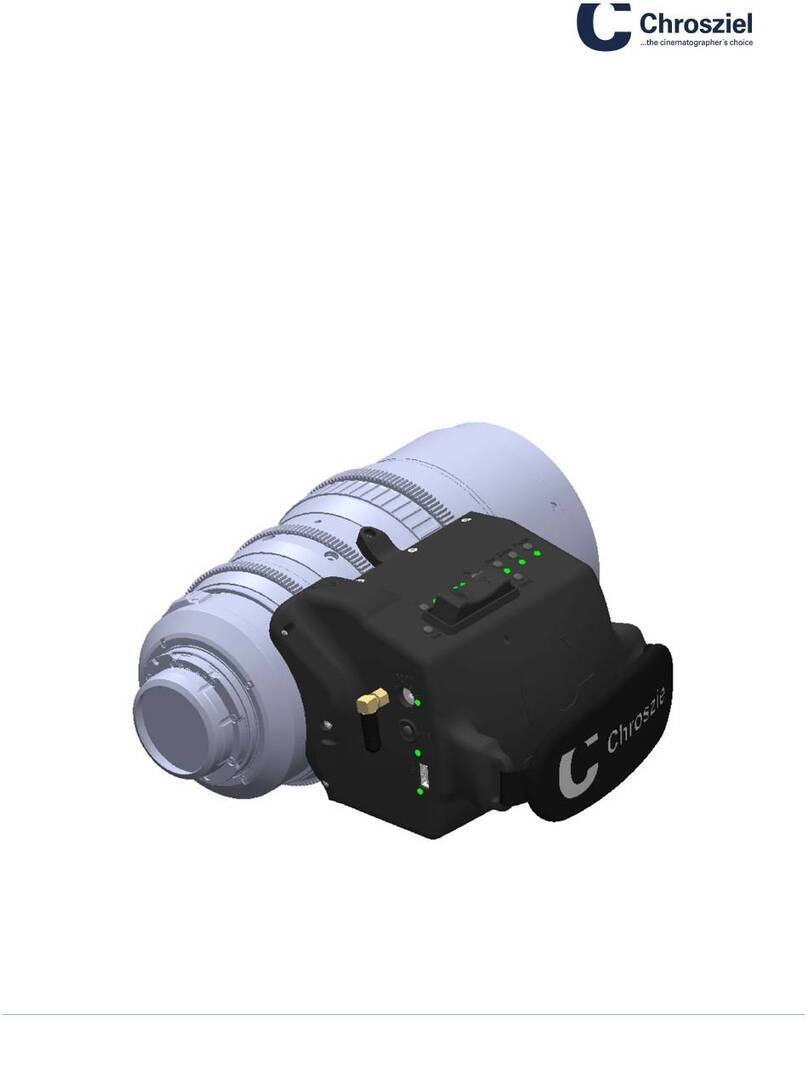
Chrosziel
Chrosziel CDM-FLEX-FIZ operating manual
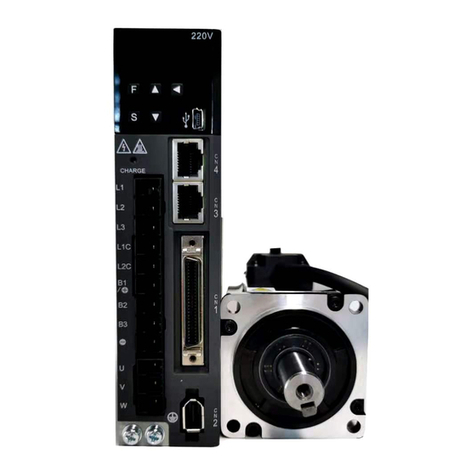
HNC Electric
HNC Electric HSD7-E Series user manual