AMI 21 User manual

Model 21 Weld Head
Operation Manual
Part No.740122
Revision A

M O D E L 2 1
O P E R A T I O N M A N U A L
ii
iiii
ii
NOTICE
This document and the information contained herein is the property of Arc Machines, Inc... It is proprietary and submitted
and received in confidence. It shall be used only for the purpose for which it is submitted and shall not be copied in
whole or in part without the prior expressed written permission of Arc Machines, Inc.
The information in this document has been carefully reviewed and is believed to be accurate.
Information and instructions in this document are subject to change and Arc Machines, Inc. reserves the right to change
specifications and data without notice.
WARNING
The nature of the GTAW process creates some POTENTIAL HAZARDS. In accordance with international safety
regulations the EXCLAMATION SYMBOL indicates that this equipment is considered HAZARDOUS until an operator has
been made aware of these POTENTIAL HAZARDS by reading the appropriate Arc Machines, Inc. Power Supply and/or
Weld Head Operation Manual. The LIGHTNING FLASH SYMBOL indicates that there are potential electrical hazards.
The use and display of these symbols make it the OPERATOR’S RESPONSIBILITY TO INSURE THAT HE HAS READ
AND/OR BEEN MADE AWARE OF ALL OF THE SAFETY-RELATED ITEMS CONTAINED IN THESE MANUALS.
Publication Date : 4-15- 2011
Copyright 2011 by Arc Machines, Inc.
All rights reserved
Revision History
Revision ECO No. Change Description Date Appr.
- N/A Initial release 4/15/11 PP
A 6052 Updated select text and images 7/7/11 PP

M O D E L 2 1
O P E R A T I O N M A N U A L
iii
iiiiii
iii
Table o Contents
Table o ContentsTable o Contents
Table o Contents
1.0 INTRODUCTION................................................................................................1
1.1 SHOCK HAZARD WARNING............................................................................ 1
2.0 SPECIFICATION ...............................................................................................2
2.1 TUBE SIZES - STANDARD...............................................................................2
2.2 CURRENT - MAXIMUM..................................................................................... 2
2.3 DUTY CYCLE MODEL 21-500 ..........................................................................2
2.4 DUTY CYCLE MODEL 21-1000 ........................................................................2
2.5 CLAMP DIMENSIONS....................................................................................... 3
3.0 INSTALLATION INSTRUCTIONS .....................................................................4
3.1 CONTROLLER CONNECTIONS.......................................................................4
4.0 OPERATION INSTRUCTIONS ..........................................................................7
4.1 WELDHEAD USER INTERFACE ......................................................................8
4.1.1 DISPLAY LEGEND............................................................................................ 8
4.2 STARTUP PROCEDURE ..................................................................................9
4.3 SET ALIGNMENT PROCEDURE ......................................................................9
4.4 OPERATION PROCEDURE ............................................................................10
5.0 MAINTENENCE INSTRUCTIONS ...................................................................11
5.1 ELECTRODE REPLACEMENT PROCEDURE ...............................................11
5.2 COLLET CHANGE PROCEDURE ..................................................................12
5.3 ROTOR AND PARTS REPLACEMENT ..........................................................13
5.4 STARTUP PRELIMINARY CHECKLIST .........................................................14
5.5 OPERATION PRELIMINARY CHECKLIST.....................................................14
5.6 ELECTRODE LENGTH FORMULA ................................................................15
5.7 ELECTRODE LENGTH CHART...................................................................... 15
6.0 TROUBLESHOOTING..................................................................................... 16
6.1 MEANDERING WELD .....................................................................................16
6.2 MISALIGNMENT .............................................................................................16
6.3 INCORRECT ROTOR HOME POSITION ........................................................17
7.0 MAINTENANCE...............................................................................................18
7.1 CLEANING AND MAINTENANCE ..................................................................18

1
11
1
1.0 INTRODUCTION
The Model 21 is a weld head for automatic orbital tube welding. This manual covers basic
set up and maintenance of the Model 21-500 & Model 21-1000. The operator should have a
working understanding of the power supply being used and should understand this manual
before operating the weld head.
1.1 SHOCK HAZARD WARNING
WARNING: ELECTRIC SHOCK CAN KILL
Significant D.C. voltage is present after removal of input power
•Electrical parts may retain electrical charge
•Shut down the Orbital Weld Head System before unplugging the input cord
Chapter
1

M O D E L 2 1
O P E R A T I O N M A N U A L
2
22
2
2.0 SPECIFICATION
2.1 TUBE SIZES - STANDARD
21-500 – Standard 1/4”, 3/8”, and 1/2” collets with optional 1/8” and custom
sized collets
21-1000 – Standard 1/4", 3/8”, 1/2", 3/4", and 1” collets with optional custom
sizes
2.2 CURRENT - MAXIMUM
21-500 – 60 Amps
21-1000 – 100 Amps
2.3 DUTY CYCLE MODEL 21-500
40 welds/hour @ 30 Amps
30 welds/hour @ 40 Amps
20 welds/hour @ 60 Amps
2.4 DUTY CYCLE MODEL 21-1000
40 welds/hour @ 30 Amps
30 welds/hour @ 60 Amps
20 welds/hour @ 100 Amps
Chapter
2

M O D E L 2 1
O P E R A T I O N M A N U A L
3
33
3
2.5 CLAMP DIMENSIONS
Dimensions 21-500 21-1000
A 0.63 1.10
B 0.63 1.10
B open 1.27 2.00
C 0.48 1.40
D electrode 0.25 0.70

M O D E L 2 1
O P E R A T I O N M A N U A L
4
44
4
3.0 INSTALLATION INSTRUCTIONS
3.1 CONTROLLER CONNECTIONS
1. From a regulated air/argon source, connect a ¼” - 50 psi hose into the receptacle
fitting, labeled “CDA” [Clean Dry Air]. This fitting is a compression type and only
requires the bare ended hose to be pushed in. Ref Figure 1.
2. From the welding power supply, connect an Argon hose from the “Arc Gas
Output” fitting to the “Argon” receptacle. This fitting is a compression type and
only requires the bare ended hose to be pushed in. Ref Figure 1.
3. Insert the “Ground” and “Electrode” connectors into their respective receptacles
on the welding power supply. Twist to lock. Ref Figure 2.
4. Connect the 10-pin round connector to “Weldhead Control” on the power supply.
Ref Figure 2.
5. Connect the 25-pin semi-rectangular connector to “Auxiliary” on the power supply.
Ref Figure 2.
6. Connect the weldhead to the end of the Controller cable. The shape of the
mating ends and the pin location indicate connection orientation. Ref Figure 3.
7. If needed, plug the foot pedal cable into the foot pedal plug (B1 & B2 Modes).
Ref Figure 4.
8. Connect the cord from the 24VDC transformer to the chrome receptacle (Does
not apply to M207). Ref Figure 1.
9. Push end of Controller cable into bottom of weldhead. Push together until the two
latches click into closed position and securely hold the weldhead. Ref Figure 5.
Note
The 120AC/24DC transformer is only required if the welding power source does not
supply 24VDC.
Chapter
3

M O D E L 2 1
O P E R A T I O N M A N U A L
5
55
5
Figure 1
Figure 2
Figure 3
Argon from power supply Air from 50 psi source
24VDC supply
Ground
Electrode
Weldhead
Auxiliary

M O D E L 2 1
O P E R A T I O N M A N U A L
6
66
6
Figure 4
Figure 5
Push Controller cable into weldhead (left) until latches “click” closed (right).
Foot Pedal
Connection

M O D E L 2 1
O P E R A T I O N M A N U A L
7
77
7
4.0 OPERATION INSTRUCTIONS
Chapter
4

M O D E L 2 1
O P E R A T I O N M A N U A L
8
88
8
4.1 WELDHEAD USER INTERFACE
1. ON/OFF – Used to power on/off the weld head independent of the interface box
when changing heads.
2. MODE – Used to toggle between Field Mode (F) and Bench Mode (B).
3. SET ALIGN – Used to set the alignment of the inserts, referencing one side to the
other. Ref Section 4.3.
4. CYCLE – Used to actuate the weld head clamping and begin the weld cycle
(same function as right foot pedal). Ref Section 4.4.
5. ABORT – Used to abort the weld cycle and open the clamping jaws (same
function as left foot pedal).
6. Home Position Locator – Used to set the rotor home position with a 1/16” pin.
Ref Section 6.3.
7. Green LED – Used to identify status situation.
8. Red LED – Used to identify alarm situations.
9. DISPLAY – Used to indicate mode, status, and alarms as shown in the “Display
Legend”. Ref Section 4.1.1.
4.1.1 DISPLAY LEGEND
DISPLAY LEGENDDISPLAY LEGEND
DISPLAY LEGEND
Modes (green led)
SA = Set Alignment mode
F1 = Field Mode 1- no center pin, Cycle Abort to open
F2 = Field Mode 2 -center pin, Cycle Abort to open
B1 = Bench Mode 1-no center pin, Auto open
B2 = Bench Mode 2-center pin, Auto open
Status indicators (green led)
HP = Home Position – rotor is at home
AC = Auto Cooling – cooling cycle is in process
Alarms (flashing red led)
SS = Safety Switch – clamping motion is incomplete
CP = Center Pin – center pin has not completely protruded or retracted
HP = Home Position – rotor is not at home

M O D E L 2 1
O P E R A T I O N M A N U A L
9
99
9
4.2 STARTUP PROCEDURE
STARTUP PROCEDURESTARTUP PROCEDURE
STARTUP PROCEDURE
1. Make power supply and weldhead connections as described in Section 3.0. Turn
on power switch on controller and weldhead.
2. Set CDA clamping pressure to 50 PSI.
3. Set head purge flow to 15-25 CFH.
4. Toggle head purge to verify purge gas is flowing at weld head.
5. Proceed to Set Align Procedure.
4.3 SET ALIGNMENT PROCEDURE
SET ALIGNMENT PROCEDURESET ALIGNMENT PROCEDURE
SET ALIGNMENT PROCEDURE
1. Clamp both sides on straight tube to verify that collets are seated per the following
procedure.
Insert tube into jaws setting it into the back of the stationary collets
Depress the right foot pedal or press the cycle button on the weld head to clamp
side one.
Depress the right foot pedal or press the cycle button on the weld head to clamp
side two.
Depress the left foot pedal or press the abort button on the weld head to release
the tube.
2. Press “SA” button on the side of the weld head.
3. The display will indicate “SA”.
4. Insert alignment gauge into side one (right side) and use right foot pedal or press
the cycle button on the weld head to close clamp one.
5. Insert alignment gauge into side two (left side) and use right foot pedal or press
the cycle button on the weld head to close clamp two.
6. Slide calibration pin through alignment gauge to verify alignment.
7. If pin passes through without restriction press “Set Align” button again to zero
alignment.
8. If pin does not pass through, press the abort button or abort pedal and repeat
steps 2 – 7.

M O D E L 2 1
O P E R A T I O N M A N U A L
10
1010
10
Image above left, shows jaws open ready to receive sample tube to insure
collets are seated within the jaws.
Image above right, shows tube being removed from jaws after verifying
collets are seated. SET ALIGNMENT can now be started.
4.4 OPERATION
OPERATION OPERATION
OPERATION PROCEDURE
PROCEDUREPROCEDURE
PROCEDURE
1. Insert first part into the right side. Micro fittings can be pressed against the back
right side of the jaw, parts that do not have a 0.250” tube stub must be aligned
with the electrode, either by lightly making contact with the center pin (when in F2
or B2 mode), or by visually aligning it with the electrode.
2. Depress the right foot pedal or press the cycle button on the weld head to clamp
right side.
3. Insert second part into the left side of the weld head lightly pressing it against the
first part.
4. Depress the right foot pedal or press the cycle button on the weld head to clamp
left side.
5. Verify that the number shown on the display is “03” or less. If greater than “03”,
depress the left pedal or abort button on the head and repeat steps 1 – 4 above.
6. Setup ID purge through tubes to be welded.
7. Depress the right foot pedal or press the cycle button on the weld head to begin
weld process.
8. After the weld is completed, in Field Mode, press cycle to open the jaws; in Bench
Mode, the jaws will automatically open.
9. Repeat procedure for next weld joint.

M O D E L 2 1
O P E R A T I O N M A N U A L
11
1111
11
5.0 MAINTENENCE INSTRUCTIONS
5.1 ELECTRODE
ELECTRODE ELECTRODE
ELECTRODE REPLACEMENT PROCEDURE
REPLACEMENT PROCEDUREREPLACEMENT PROCEDURE
REPLACEMENT PROCEDURE
1. Set power supply to TEST mode.
2. Use commands from power supply to JOG rotor to the position shown below.
3. Turn electrode retaining cam, on rotor, counter-clockwise until slot is aligned with
electrode (Fig 1, Item ①).
4. Carefully remove electrode, use hemostats from tool kit if necessary.
5. Install new electrode, use hemostats from tool kit if necessary.
6. Check that electrode is bottomed out in rotor.
7. Turn electrode retaining cam clockwise to lock in electrode (Fig 2, Item ①).
8. Verify that the power supply is in TEST mode.
9. Use commands from power supply to return rotor to home position.
Chapter
5

M O D E L 2 1
O P E R A T I O N M A N U A L
12
1212
12
5.2 COLLET C
COLLET CCOLLET C
COLLET CHANGE PROCEDURE
HANGE PROCEDUREHANGE PROCEDURE
HANGE PROCEDURE
1. Turn off power to the Controller.
2. Insert the collet removal tool pin 1(Fig 1 Item 1) into the removal pocket of the
collet (Fig 2 Item 1) to be removed.
3. Press the handle of the removal tool (Fig 1 Item 3) towards the jaw (Fig 2 Item 2),
pivoting on pin 2(Fig 1 Item 2).
4. The collet will “snap” or “pop” out of the jaw.
5. Place the replacement collet in the jaw with one retaining pin (Fig 3 Item 2)
aligned with its respective retaining dimple (Fig 3 Item 1).
6. Press on the other side to seat the remaining retaining pin with its retaining
dimple.
7. Repeat the procedure for the other three collets.
8. If changing collet size be sure to replace the electrode with an appropriate sized
electrode. Ref Section 5.1.
9. After changing collets and electrode power up weld head and clamp to fully seat
the collets.

M O D E L 2 1
O P E R A T I O N M A N U A L
13
1313
13
5.3 ROTOR AND PARTS REPLACEMENT
ROTOR AND PARTS REPLACEMENTROTOR AND PARTS REPLACEMENT
ROTOR AND PARTS REPLACEMENT
1. With the jaws in the open position turn off the power to the Controller.
2. Remove the Torsion cap retaining screw (Fig 1 Item 1).
3. Relieve spring pressure on the torsion cap by loosening the torsion tension set
screw (Fig 1 Item 2).
4. Lift torsion cap off of weld head. If necessary, gently pry between the torsion cap
and top jaw #2 (Fig 1 Item 3).
5. Remove the three Phillips screws (Fig 1 Item 4).
6. Remove the jaw alignment shoulder bolt (Fig 1 Item 5).
7. Rotate bottom jaw #2 clockwise to clear the interlock with bottom jaw #1(Fig 2
Item 1).
8. Lift bottom jaw #2 off of the weld head.
9. Gently lift the stationary insulator out of the weld head (Fig 3 Item 1). Lift the
contact strip (Fig 4 Item 1) out of weld head. Gently lift the rotor assembly (Fig 4
Item 2) out of the weld head (rock rotor if necessary).
10.Inspect all components for wear and damage and replace as necessary.
11.Install the rotor verifying that the bottom edge of the gear is flush with the race
(Fig 4 Item 3).
12.Install the contact strip by pressing the opening on the contact strip onto the boss
of the power lug (Fig 4 Item 4).
13.Install the stationary insulator and verify that it is flush with bottom jaw #1 (Fig 3
Item 2).
14.Install bottom jaw #2, torsion cap and remaining hardware.

M O D E L 2 1
O P E R A T I O N M A N U A L
14
1414
14
5.4
5.45.4
5.4
STARTUP PRELIMINARY CHECKLIST
STARTUP PRELIMINARY CHECKLISTSTARTUP PRELIMINARY CHECKLIST
STARTUP PRELIMINARY CHECKLIST
Interface purge is connected to Arc Gas Output
Controller is plugged in (Does not apply to 207)
Foot pedal is connected (F Mode Only)
Remote pendent is connected (Optional)
Weld head interface cable is connected
Ground and electrode cables are connected
Air/Argon line is connected and set at 50 PSI
Controller power switch is in the ON position
5.5
5.55.5
5.5
OPERATION PRELIMINARY CHECKLIST
OPERATION PRELIMINARY CHECKLISTOPERATION PRELIMINARY CHECKLIST
OPERATION PRELIMINARY CHECKLIST
Collets are installed and fully seated
Correct length electrode is installed
Center pin cycles up and down
Weld head calibration procedure completed

M O D E L 2 1
O P E R A T I O N M A N U A L
15
1515
15
5.6
5.65.6
5.6
ELECTRODE
ELECTRODEELECTRODE
ELECTRODE LENGTH FORMULA
LENGTH FORMULA LENGTH FORMULA
LENGTH FORMULA
X = .954 for 21-500
X = 1.716 for 21-1000
Y = Tube OD
Z = Wall Thickness
Formula for calculating Electrode Length
= ((X-Y)/2) - ((Z/2) +. 01)
= ((Rotor Diameter-Tube OD)/2) - ((Wall/2) +. 01)
5.7
5.75.7
5.7
ELECTRODE
ELECTRODEELECTRODE
ELECTRODE LENGTH CHART
LENGTH CHART LENGTH CHART
LENGTH CHART
M21-500 Electrode Lengths
Tube OD Electrode
Length Wall Tip Dia. P/N
1/8” 0.395 .035 .005 TC04-0395-005
1/4" 0.325 .035 .005 TC04-0325-005
3/8” 0.260 .035 .005 TC04-0260-005
1/2" 0.195 .049 .005 TC04-0195-005
M21–1000 Electrode Lengths
Tube OD Electrode
Length Wall Tip Dia. P/N
1/4" 0.725 .035 .005 TC06-0725-005
3/8” 0.643 .035 .005 TC06-0643-005
1/2” 0.573 .049 .005 TC06-0573-005
3/4" 0.440 .065 .01 TC06-0440-01
1" 0.315 .065 .01 TC06-0315-01

M O D E L 2 1
O P E R A T I O N M A N U A L
16
1616
16
6.0 TROUBLESHOOTING
TROUBLESHOOTINGTROUBLESHOOTING
TROUBLESHOOTING
6.1 MEANDERING WELD
Welds beads that are not straight can usually be attributed to one of four things:
1. Incorrect purge flow, set flow to 15-25 CFH and retest.
2. Worn electrode, replace and retest.
3. Incorrect pressure between the contact strip and the rotor.
4. Worn rotor gear/race.
If steps 1 and 2 above did not solve the problem, follow the procedures shown in the
Section 5.3 with detail to:
1. Condition of the wave springs in the stationary insulator.
2. Wear on the contact strip.
3. Wear on the rotor gear and race (check for excessive axial play).
4. Replace worn parts.
6.2 MISALIGNMENT
To correct misalignment you must first identify what is causing the misalignment:
1. Carefully inspect each collet and jaw.
2. Check the tube clamping surfaces for irregularities.
3. Check the angled collet and jaw seats for irregularities.
4. Check the retaining pins and pockets for irregularities.
5. If any issues are found, correct or replace the part and check alignment.
6. Clamp on the calibration pieces.
7. Look through the pieces noting any irregularities in the joint between the two.
Misalignment similar to Fig 1 indicates that side 1 is over clamping, either loosen
the clamping adjustment screw or increase the air pressure.
Misalignment similar to Fig 2 indicates that side 2 is over clamping, either tighten
the clamping adjustment screw or reduce the air pressure.
Chapter
6

M O D E L 2 1
O P E R A T I O N M A N U A L
17
1717
17
8. If misalignment is in another axis or is not corrected by the above, the collets/jaws
may be damaged.
Figures 1 & 2
MISALIGNMENT
6.3 INCORRECT ROTOR HOME POSITION
If the rotor is not stopping in the correct home position the center pin will not operate.
If a weld is started when the rotor is not at home, a damaging arc out can occur. To
correct this situation:
1. With the jaws open and the power supply in TEST mode, send the rotor home.
2. Insert a 1/16” pin into the “Home Position Locator” (Ref Section 4.0, Item 6) to
depress the home switch release.
3. While holding this pin in the hole, jog the rotor into the correct home position.
4. Remove the 1/16” pin.
5. Send the rotor home again.
6. Check home position and repeat as necessary.
Table of contents
Popular Tools manuals by other brands

Chicago Electric
Chicago Electric 63409 Owner's manual and safety instructions
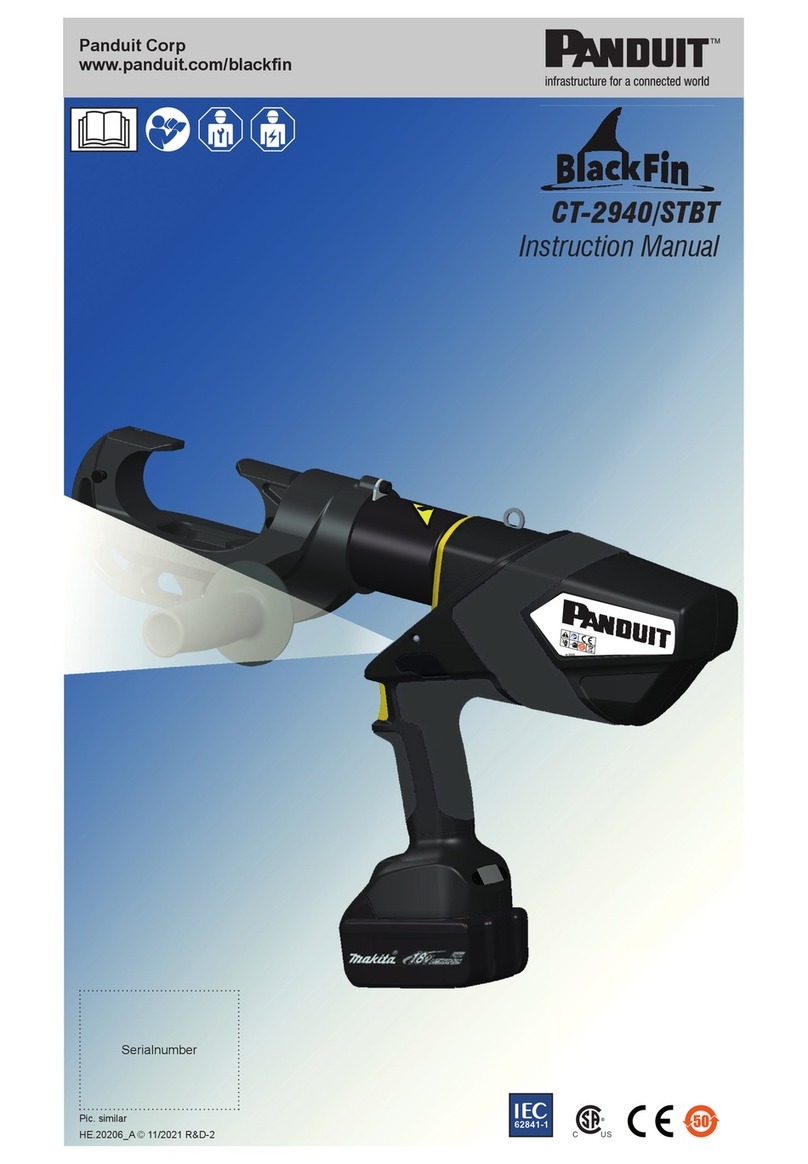
Panduit
Panduit BlackFin CT-2940/STBT instruction manual
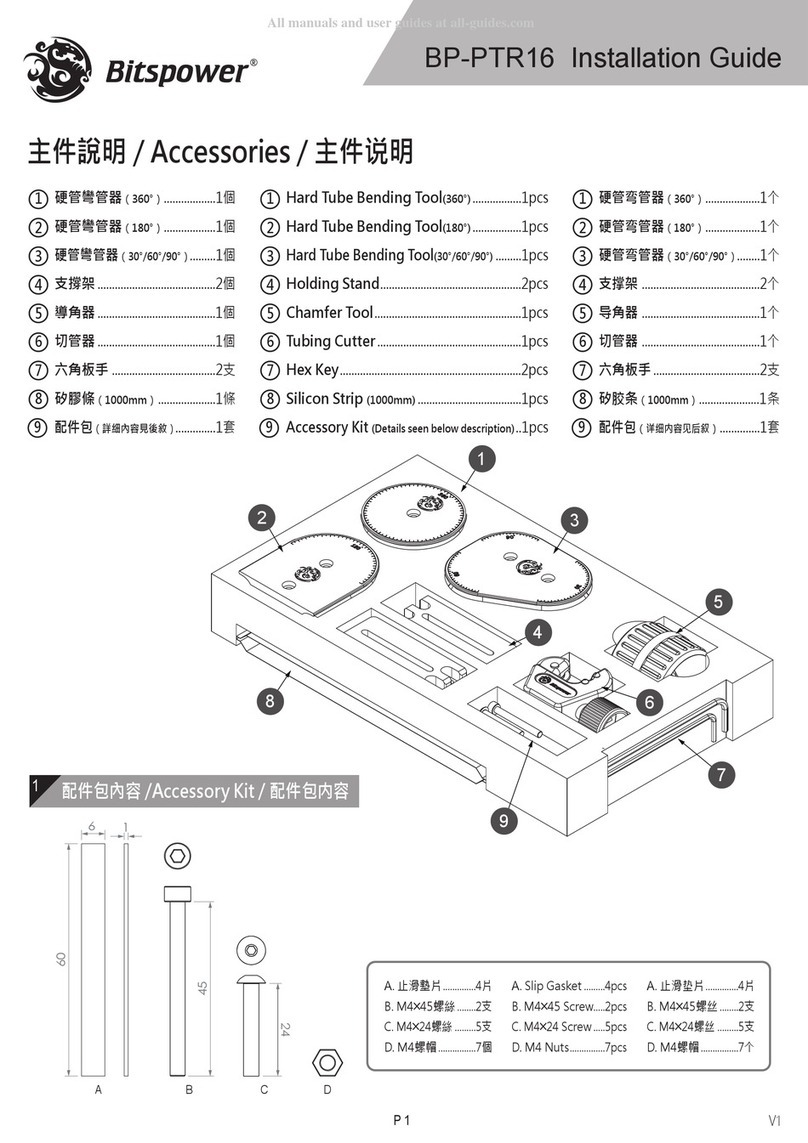
Bitspower
Bitspower BP-PTR16 installation guide
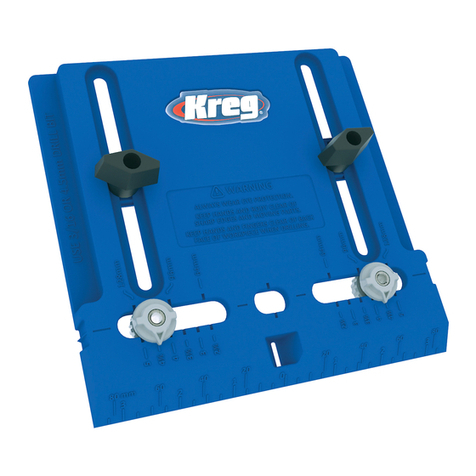
Kreg
Kreg KHI-PULL-INT owner's manual

Martor
Martor SECUNORM 500 quick start guide
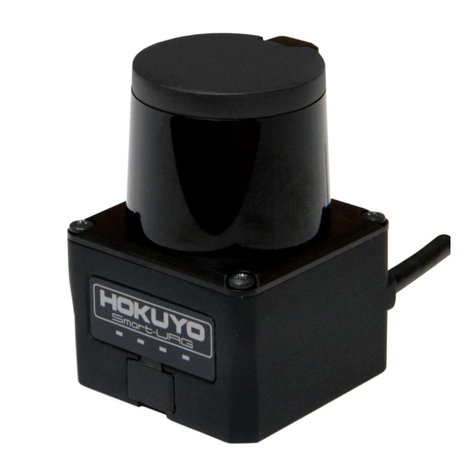
HOKUYO AUTOMATIC
HOKUYO AUTOMATIC UST Series instruction manual