ANALOX 2000 Series User manual
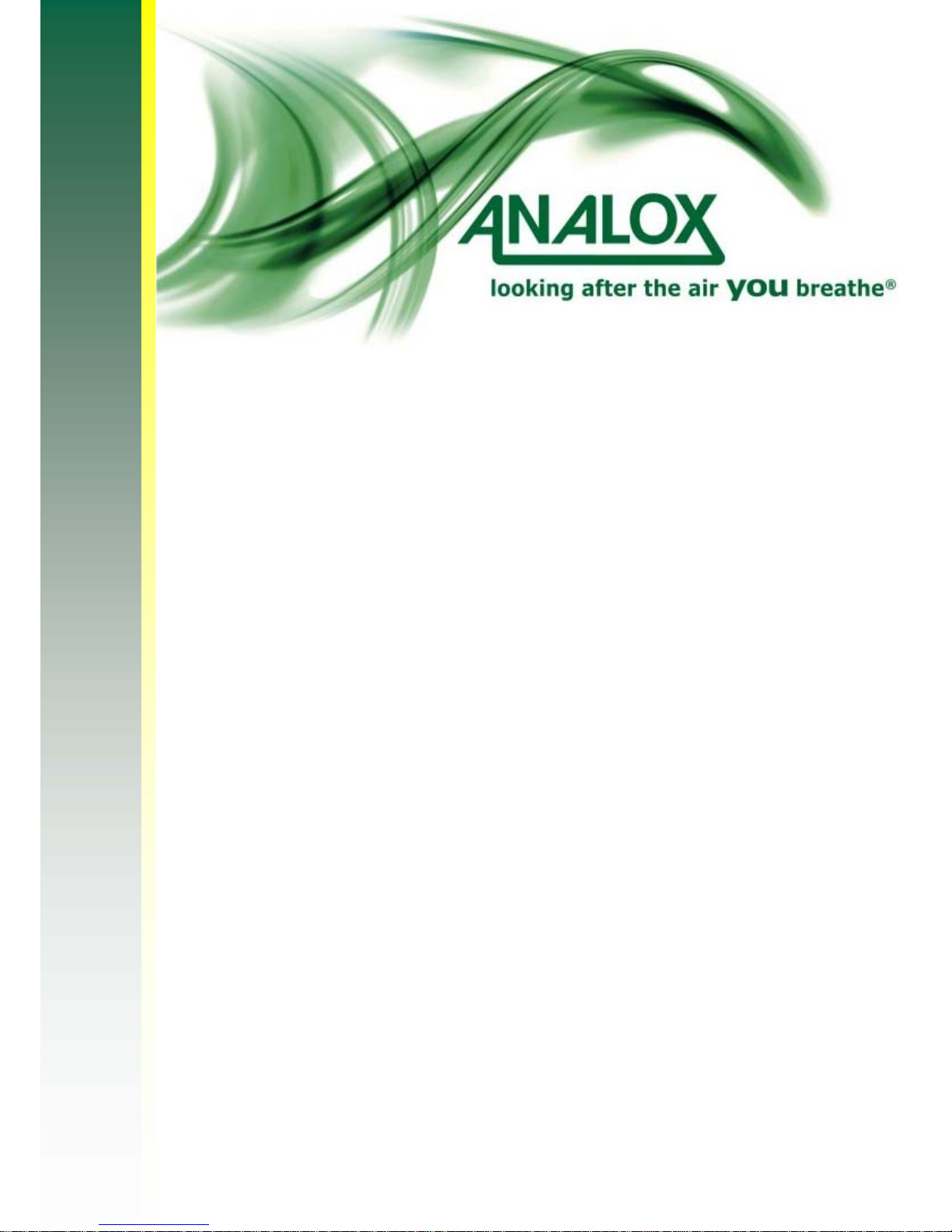
ANALOX 2000 Series - Flammable Gas Sensors
User Manual
Analox Sensor Technology Ltd
15 Ellerbeck Court, Stokesley Business Park
North Yorkshire, TS9 5PT
T: +44 (0)1642 711400 F: +44 (0)1642 713900
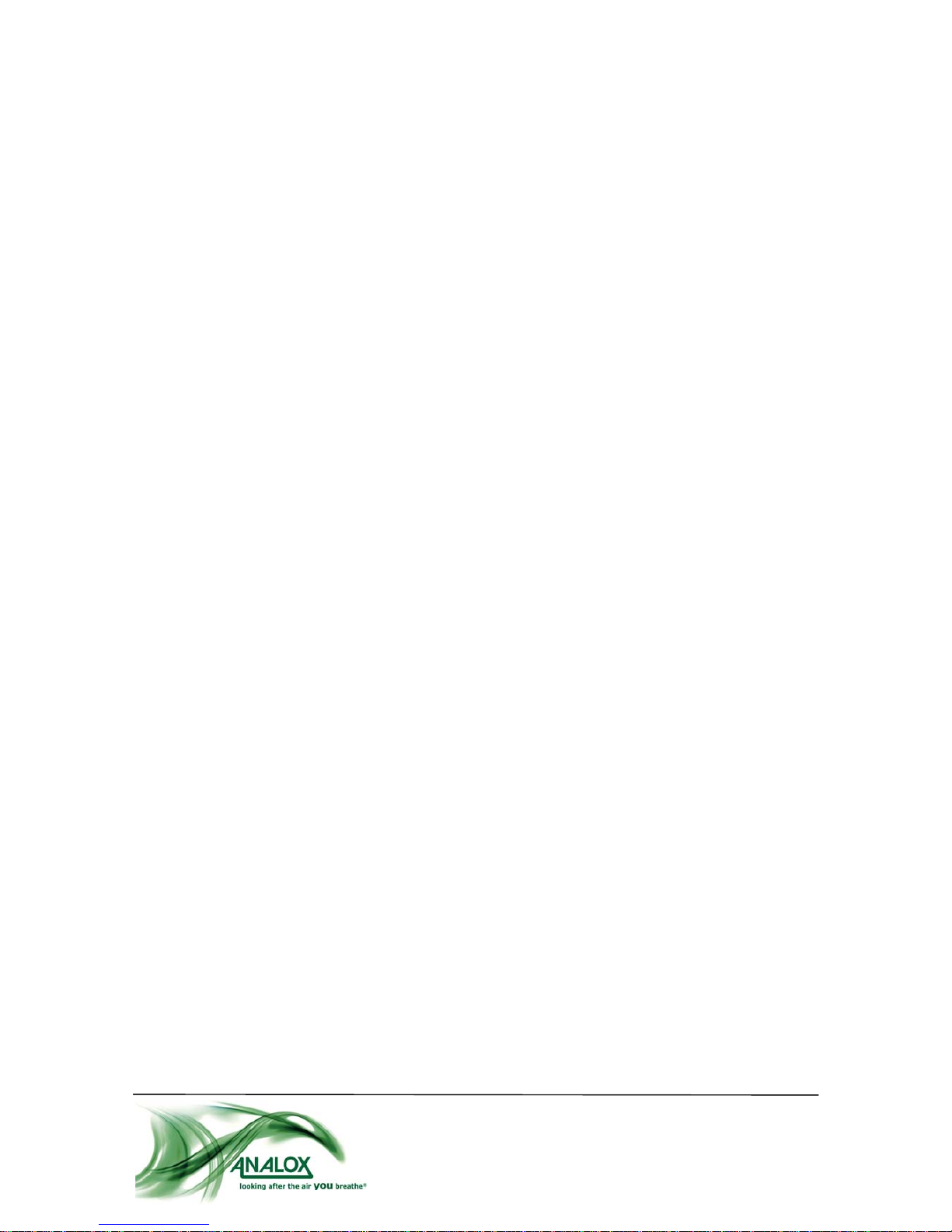
Analox 2000 – Flammable Gas Sensors – User Manual
Document Ref: SK0-810-04 January 2009
Page 2
CONTENTS
Introduction ....................................................................................................................................3
Principle of Operation............................................................................................................ 4
L.E.L. and U.E.L. ................................................................................................................... 5
Sensor Signal Cables ............................................................................................................6
Instrument Calibration ........................................................................................................... 7
Sensor Physical Details.........................................................................................................8
Electrical Connections ........................................................................................................... 9
Flammable Sensor Wiring Variations .................................................................................. 10
Accessories ......................................................................................................................... 11
Installation ........................................................................................................................... 11
Sensor Position ................................................................................................................... 11
Certification ......................................................................................................................... 12
Intrisically Safe System ....................................................................................................... 13
Chemical Poisoning............................................................................................................. 14
Sensor Element Life ............................................................................................................ 14
Sensor Response Time....................................................................................................... 14
Appendix ............................................................................................................................. 15
Cable Requirements....................................................................................................... 16/17
Disposal.............................................................................................................................. .18
Certificates
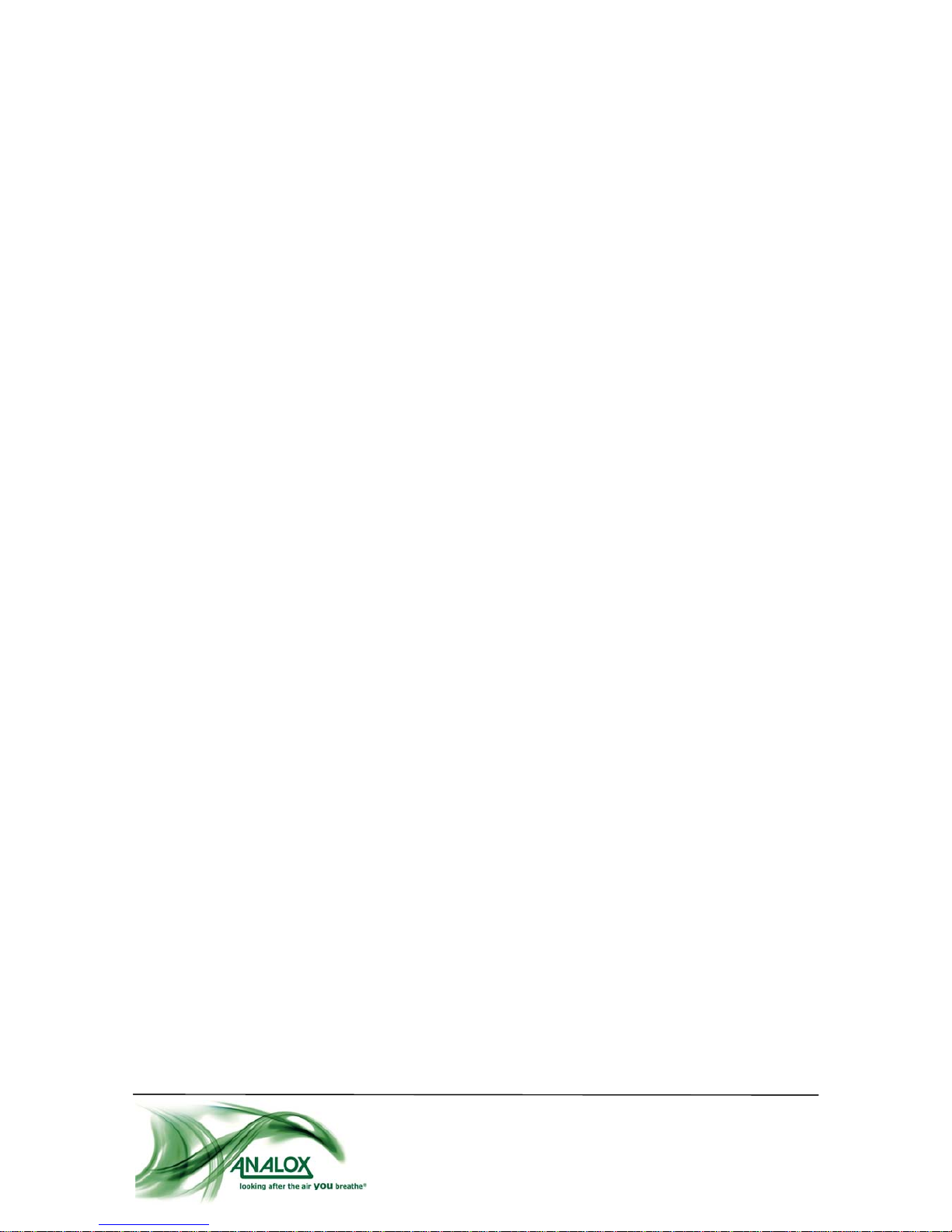
Analox 2000 – Flammable Gas Sensors – User Manual
Document Ref: SK0-810-04 January 2009
Page 3
ANALOX 2000 RANGE
FLAMMABLE GAS SENSORS
INTRODUCTION
The ANALOX 2000 Range of sensors are designed to detect Flammable gas, mainly Methane
(CH4) in ambient air monitoring applications. There are two models in the range:
a. Model 2000 which is of the Explosion proof type and
b. Model 2001 which is a lower cost, uncertified type, suitable for use in areas which are not
classified as being hazardous.
The Model 2000 consists of a stainless steel sensor unit certified Ex sd IIc T6, mounted on a cast
iron junction box, which is certified EEx e II T6. This model also carries an Intrinsically Safe
SYSTEM certificate Ex ias IIC. (details included later in this manual.)
The Model 2001 sensor unit is made from Acetal and contains a Ceramic sinter element. The
sensor is mounted on a IP65, mineral filled thermoplastic junction box. Both junction boxes include
screw type terminals for connection of signal cables.
The Model 2000 unit junction box includes 1 x 20mm threaded cable gland entry and 1 x 25mm
threaded cable gland entry. Certified blanking plugs are supplied with the unit.
The Model 2001 has a single 20mm cable gland fitted to the junction box.
The Pellistors used in the 2000 and 2001 sensors are of the Poison resistant variety. Both types of
sensor can be supplied with either VQ21 or VQ22 type Pellistors; Operating currents are 300 mA
and 175 mA respectively. The VQ21 has a larger active element and is slightly more resistant to
poisoning than the VQ22 but if the area to be monitored is unlikely to contain poisoning
substances then other considerations may determine which Pellistors are chosen. (See - Intrinsic
Safety applications)
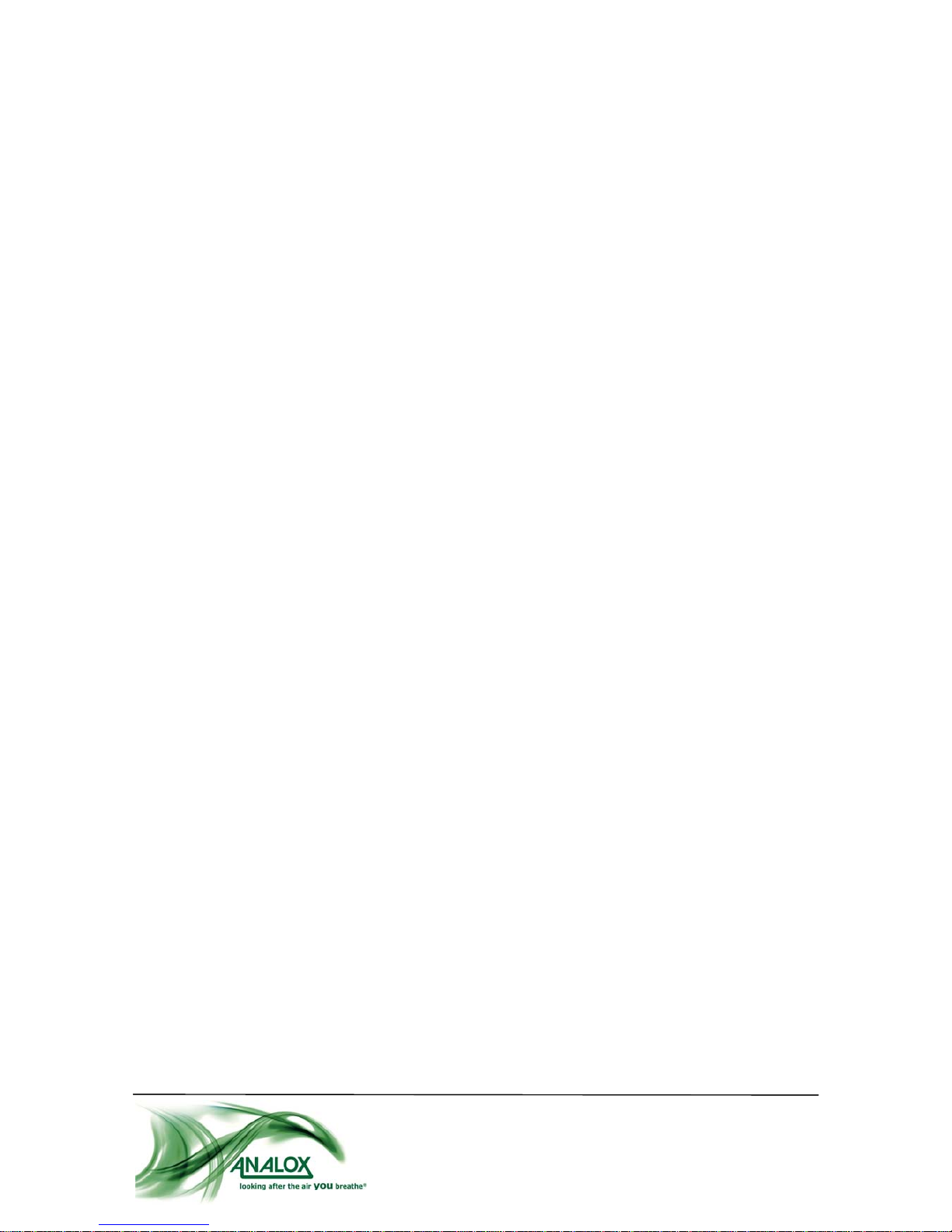
Analox 2000 – Flammable Gas Sensors – User Manual
Document Ref: SK0-810-04 January 2009
Page 4
PRINCIPLE OF OPERATION
Both sensors use the same devices to actually detect the presence of a flammable gas in the air
surrounding the sensing surface. The elements used in these sensors are of the Catalytic
Pellistor type and are sensitive to most common Combustible gases and vapors. A single sensor
assembly may therefore be used to detect a wide range of these gases. The devices are made
from two coils of very fine platinum wire which are embedded in separate beads of alumina. One
device is the detector and the other is a temperature compensating element. The detecting
element is treated with a catalyst which promotes oxidation of the gas and the compensating
element is treated with an oxidation inhibiting agent. The two elements are connected to the
Instrument in a Half Bridge configuration and the excitation current passing through them raises
their temperature to about 550 Deg C. At this temperature, the gas oxidises on the Detector
element and raises the temperature of the bead even further. This alters the resistance of the
detector bead and this change in resistance is measured by the instrument and converted to
produce a reading of the gas concentration, on the Instrument display. The output of the device
is essentially linear for most gases up to high concentrations, typically 100% LEL and the
response time to 25% LEL is about 2 or 3 seconds. Any pre-filtering of the gas before it reaches
the sensor may lengthen the response time. If the sensors are required to operate in high gas
concentrations for short periods, it has been found that for periods up to about 2 minutes, 10
second bursts of 8%, 10% and 80% methane in air, produce no ill effects. Prolonged exposure
can result in zero drift which may be reversed by operating for a short period in clean air.
Exposure to 40% concentration for longer periods, will begin to destroy the detector surface,
altering the Zero point and reducing the sensitivity. Whenever a sensor is exposed to high
concentrations of Combustible gas, the calibration should be rechecked as soon as possible.
The performance of the sensors may be temporarily impaired by operation in the presence of
certain volatile substances containing halogens or sulphur. The sensors may recover after a
short period of operation in clean air. Whenever the substance produces a permanent effect on
the catalyst, resulting in a large reduction in sensitivity the sensor is said to be Poisoned. Typical
substances which can cause poisoning are silicon oils and grease, anti-knock petrol additives
and phosphate esters. Activated carbon filters will provide adequate protection from poisoning in
most cases. Notwithstanding the above comments, the Combustible gas sensors have an
inherently long life. Although the sensors respond to most Combustible gases, the signals
produced vary in magnitude depending on the actual gas to which the sensor is exposed. The
sensors should normally be calibrated using 50% LEL Methane, ie 2.5% Methane in air.
NOTE : When the sensors are used to detect a different gas than that used for calibration, then a
correction factor should be applied to the readings obtained. A table showing conversion factors
for various gases is shown in Appendix A of this manual. (See also Instrument Calibration below)
WARNING: When a pellistor type sensor is exposed to concentrations of flammable gas
greater than 100% LEL (5% Methane in air) there eventually comes a point at which the signal
output from the sensor DECREASES as a result of an INCREASING concentration of the gas.
This is caused by the flammable gas displacing Oxygen in the sample and gradually inhibiting
the normal oxidation process, at the detecting element. Most monitoring instruments provide an
OVER-RANGE indication to inform the user of this condition.(See also L.E.L. and U.E.L.)
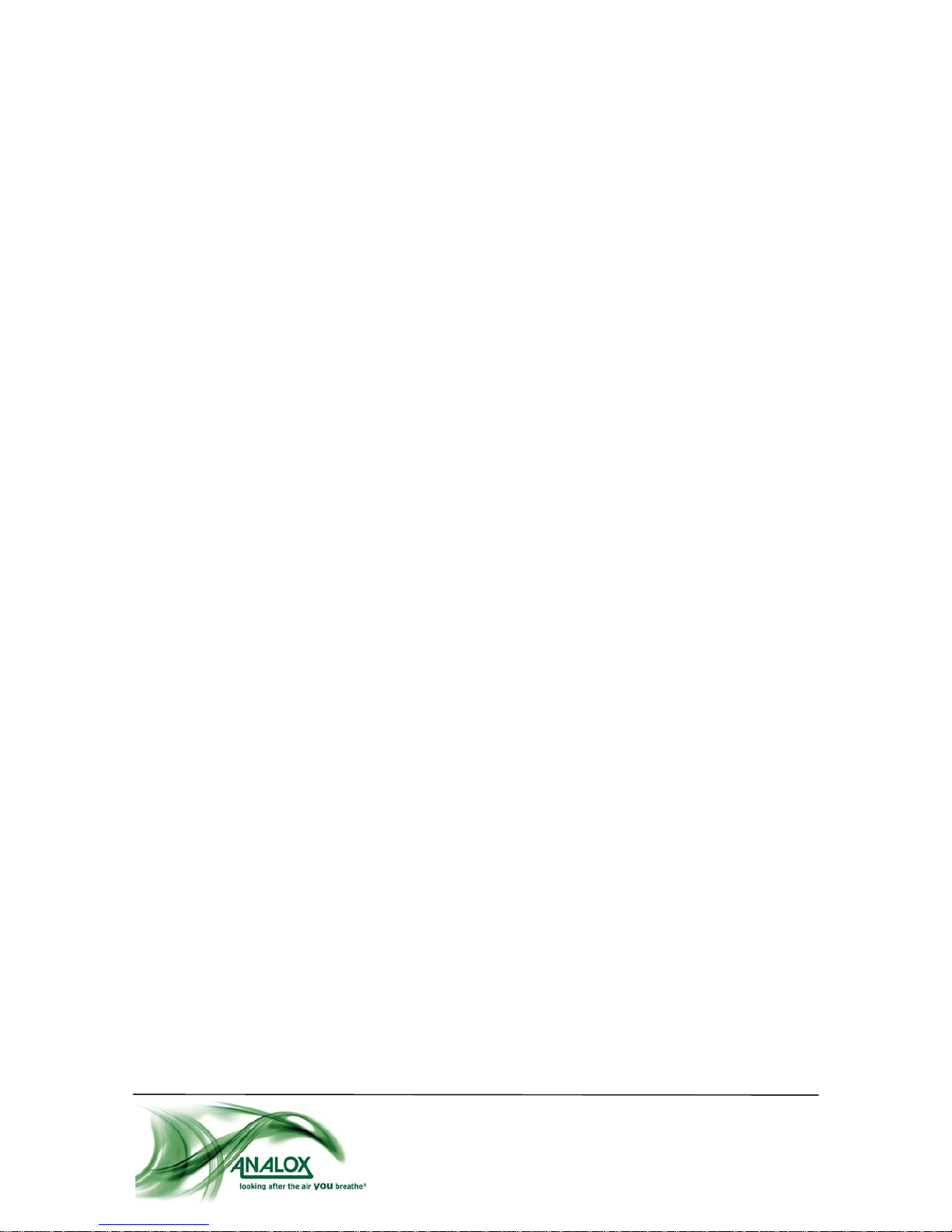
Analox 2000 – Flammable Gas Sensors – User Manual
Document Ref: SK0-810-04 January 2009
Page 5
L.E.L. and U.E.L.
The above principle of operation is only valid where the gas mixture to be sensed contains
Oxygen. It is therefore suitable for detection of leakage’s of gasest in atmospheric
surroundings, where it is important to know the level of concentration, well before a hazardous
situation arises. Flammable gas mixtures are only ignitable between certain fairly clear, but
experimentally defined limits. These levels are known as the 'Lower Explosive Limit' (L.E.L.)
and the 'Upper Explosive Limit' (U.E.L.). Typical L.E.L. figures for some common explosive
gases are as follows :
Methane (Natural Gas) 5% + 95% Air
Hydrogen 4% + 96% Air
Ammonia 16% + 84% Air
Ethylene 3% + 97% Air
Butane 1.9%+ 98.1% Air
Propane 2.1%+ 97.9% Air
If the gas concentration is below the L.E.L. then combustion cannot take place due to
insufficient gas, and if above U.E.L. level, there will be insufficient Oxygen present to sustain
combustion.
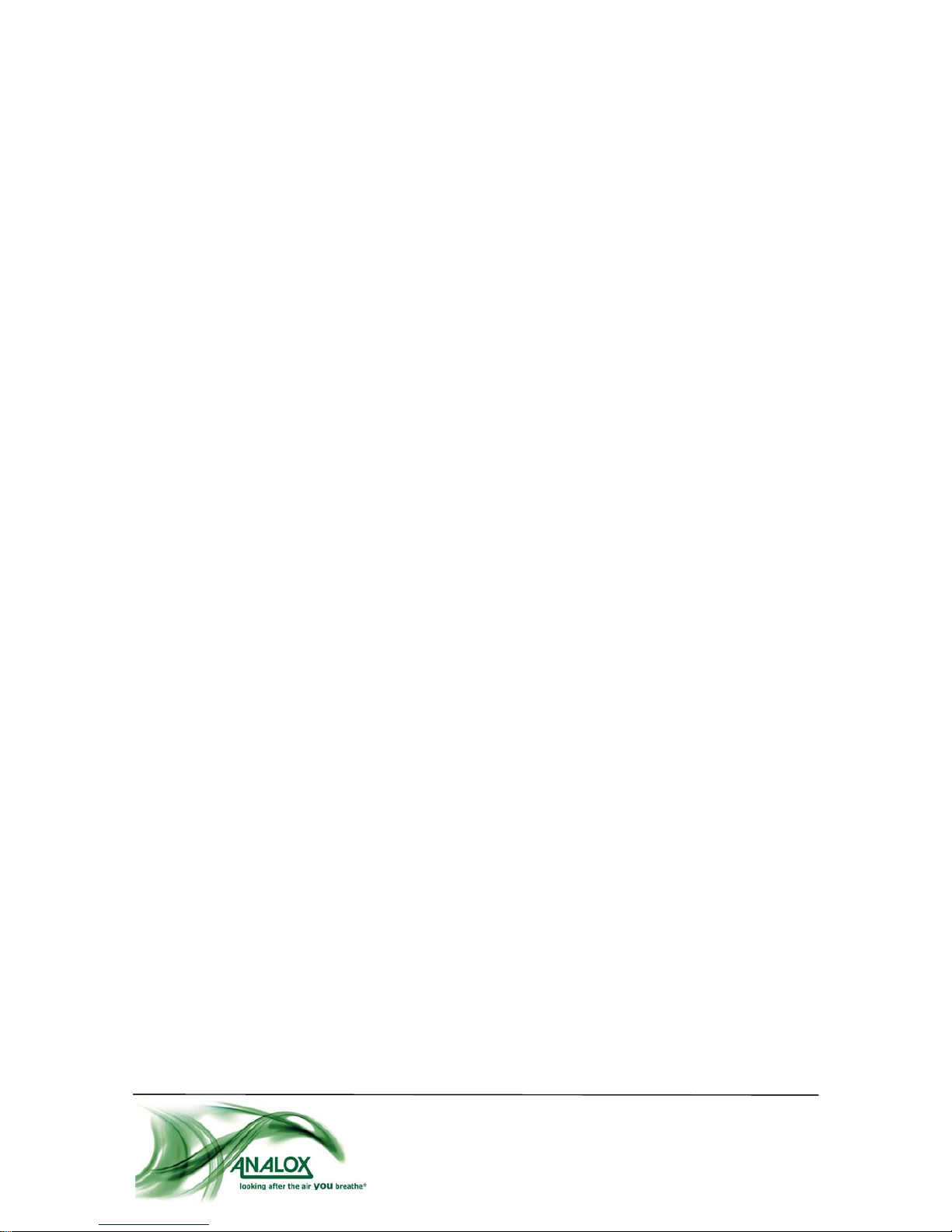
Analox 2000 – Flammable Gas Sensors – User Manual
Document Ref: SK0-810-04 January 2009
Page 6
SENSOR SIGNAL CABLES
All the S.A.E.P. Flammable gas sensors require a Three Core cable between the sensor and
the measuring instrument. Because of the relatively heavy current demands of the Pellistor type
of sensors, the connecting cables must be chosen with care. Pellistors of the VQ21 type, which
are normally fitted in the Model 2000 and Model 2001, require an operating potential (at the
Sensor) of 2.00 volts DC at a current of 300 milliamps. When a current of this magnitude is
passed along signal cables, any significant resistance in the cables will result in a drop in
voltage along the cables. As an example : Assume a cable run of 100 metres is required
between the monitoring instrument and the sensor and the cross sectional area of the cable
chosen is 1.00mm2. Most manufacturers quote the resistance of this cable to be 19.1 Ohms
per kilometre, therefore in this case, a 100 metre length will have a resistance of 19.1 / 10 =
1.91 Ohms. Bearing in mind that as far as the loop current is concerned, the actual conductor
length is 200 metres, (100m to the sensor and 100m back again) the total cable resistance in
this case is 3.82 Ohms. Using Ohm's law to calculate the voltage drop across the entire cable:
Voltage Drop = Current x Resistance
Where Voltage is in Volts : Current is in Amps & Resistance is in Ohms
Voltage Drop = 0.3 x 3.82 = 1.15 Volts
This means that if the monitoring instrument supplies a drive voltage of 2.00 volts then the
sensor will only have 0.85 Volts applied to it. (2.00v-1.15v=0.85v). The pellistor sensor will NOT
operate correctly in this condition.
NOTE: Although the ANALOX 2000 & 2001 sensors use a 3 wire connecting cable, only two of
the wires carry the sensor excitation current. The third wire is connected to the centre tap of the
'Half Bridge' configuration. It only carries a signal voltage at very low current and may therefore
be ignored as far as resistance effects are concerned. Most monitoring instruments designed to
operate with Flammable gas detectors of the Pellistor type, have the facility for compensating,
within limits, for this voltage drop. The ANALOX range of monitors, 1300 and 1320, allow the
drive voltage to be adjusted up to about 3.8 volts. So, in the case of the above installation, the
1.15 volt drop across the cable could be compensated by adjusting the monitoring instrument
drive voltage to 3.15 volts. It is not necessary to carry out all of these calculations every time an
installation is done - correct operation of the sensor can be achieved by measuring the voltage
AT THE SENSOR JUNCTION BOX TERMINALS, as per the installation instructions in the
relevant monitoring instrument handbook. Data regarding maximum possible lengths for a
selection of commonly used cables with 3 different Pellistor sensors, is included in Appendix B,
at the end of this manual. A further point, which is often overlooked is that the resistance of
copper cable has a temperature co-efficient. The effect of this variation in resistance due to
temperature changes, can be significant on very long cable runs, particularly if the cable has a
small cross sectional area and is subject to large variations in temperature. The measuring
instrument is unable to distinguish between a change in cable resistance and a genuine gas
signal. Copper cable resistance is normally quoted at 20C and will vary by approximately
0.4% per degree C, as the temperature changes above and below this value. Using the above
cable installation as an example, the total loop resistance was calculated to be 3.82 Ohms at
20C. If the temperature of the cable drops to 0C then the resistance will change to 3.80
Ohms. At first sight, this may not seem significant but could result in drift of the ZERO reading
on the monitoring instrument.
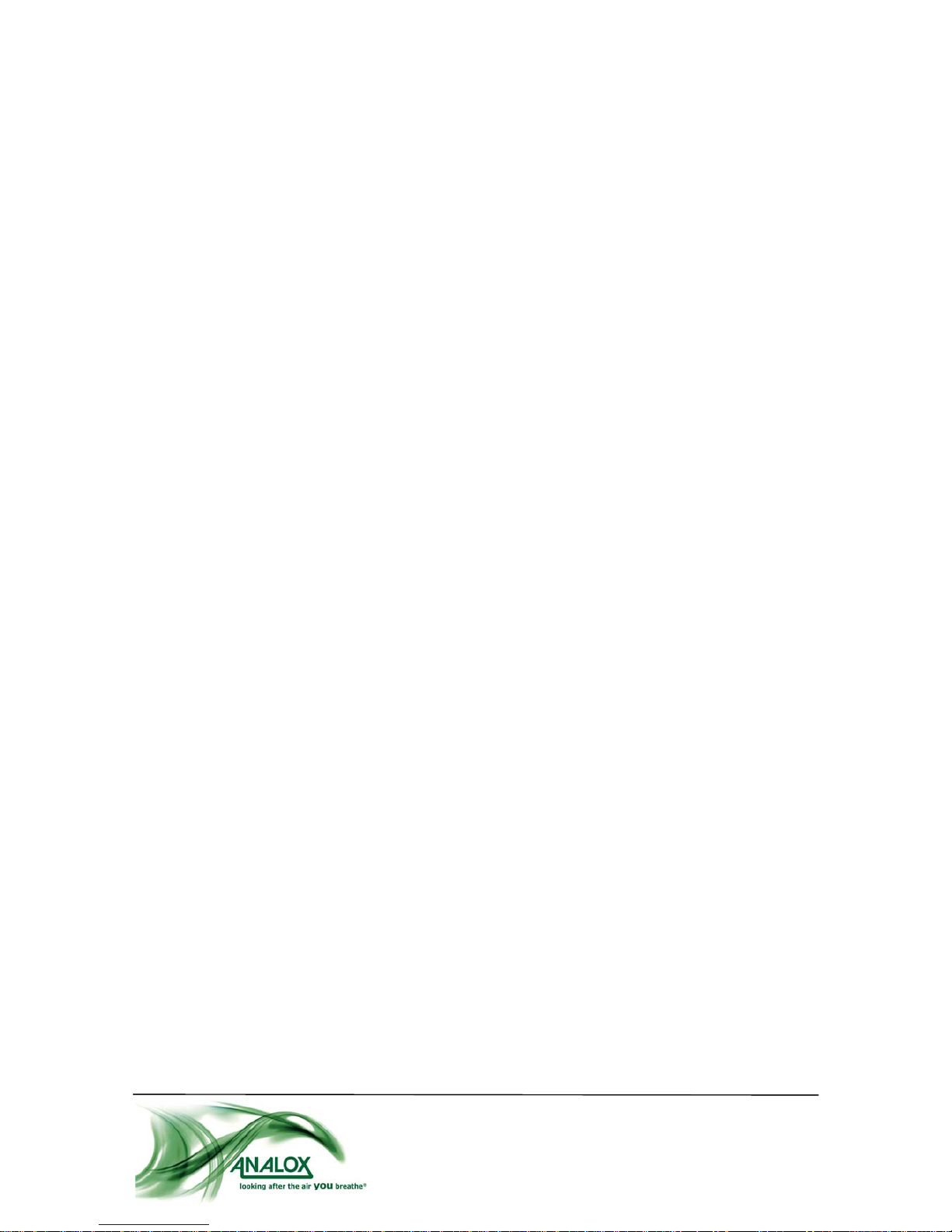
Analox 2000 – Flammable Gas Sensors – User Manual
Document Ref: SK0-810-04 January 2009
Page 7
INSTRUMENT CALIBRATION
There is some confusion over what is meant by the Sensitivity of instruments used to measure
the concentrations of combustible gas. Ideally, all units employing catalytic combustion as the
measuring principle should be calibrated in terms of percentage of potential combustibility,
where 100% scale reading represents an ignitable mixture, for a particular Gas/Air mixture. It is
unfortunate that the sensing elements are not equally responsive to all combustible gas/air
mixtures and although the sensitivity to a wide range of gases is similar to within a few percent
of L.E.L. and for all practical purposes, the inaccuracies may be ignored, it may be desirable in
certain cases to make allowances for these variations. It is therefore common practice to
calibrate units of this type over the range 0 - 100% L.E.L. where 100% scale is equal to the
actual percent concentration of the calibration gas, at the Lower Explosive Limit. e.g. An
instrument calibrated 0-100% L.E.L. Methane would effectively read 5% v/v at 100% scale and
one calibrated for Butane would indicate 100% scale at 1.9% gas concentration. Cross
sensitivities between a number of gases may be derived from the selection of data and
formulae given in Appendix A of this manual.
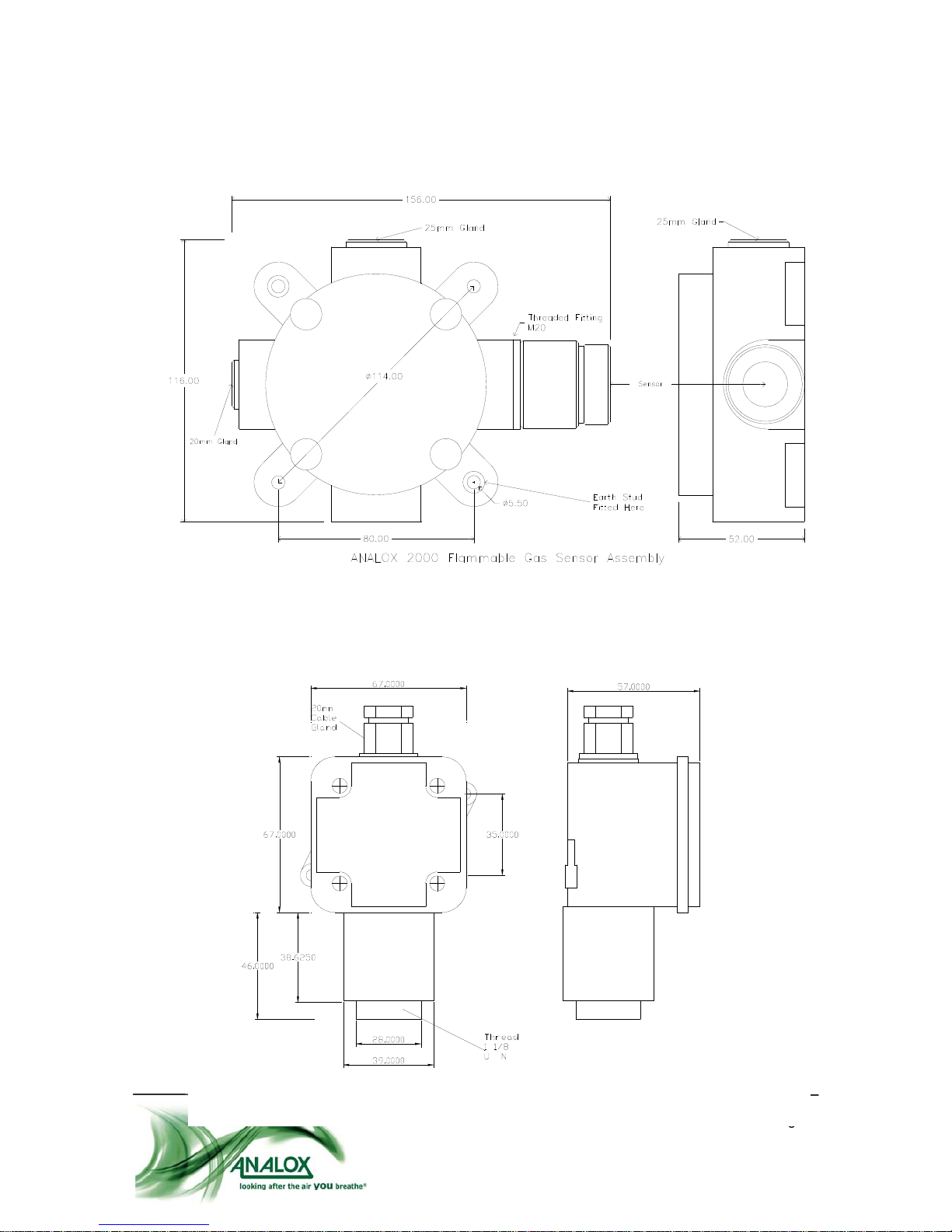
Analox 2000 – Flammable Gas Sensors – User Manual
Document Ref: SK0-810-04 January 2009
Page 8
SENSOR PHYSICAL DETAILS
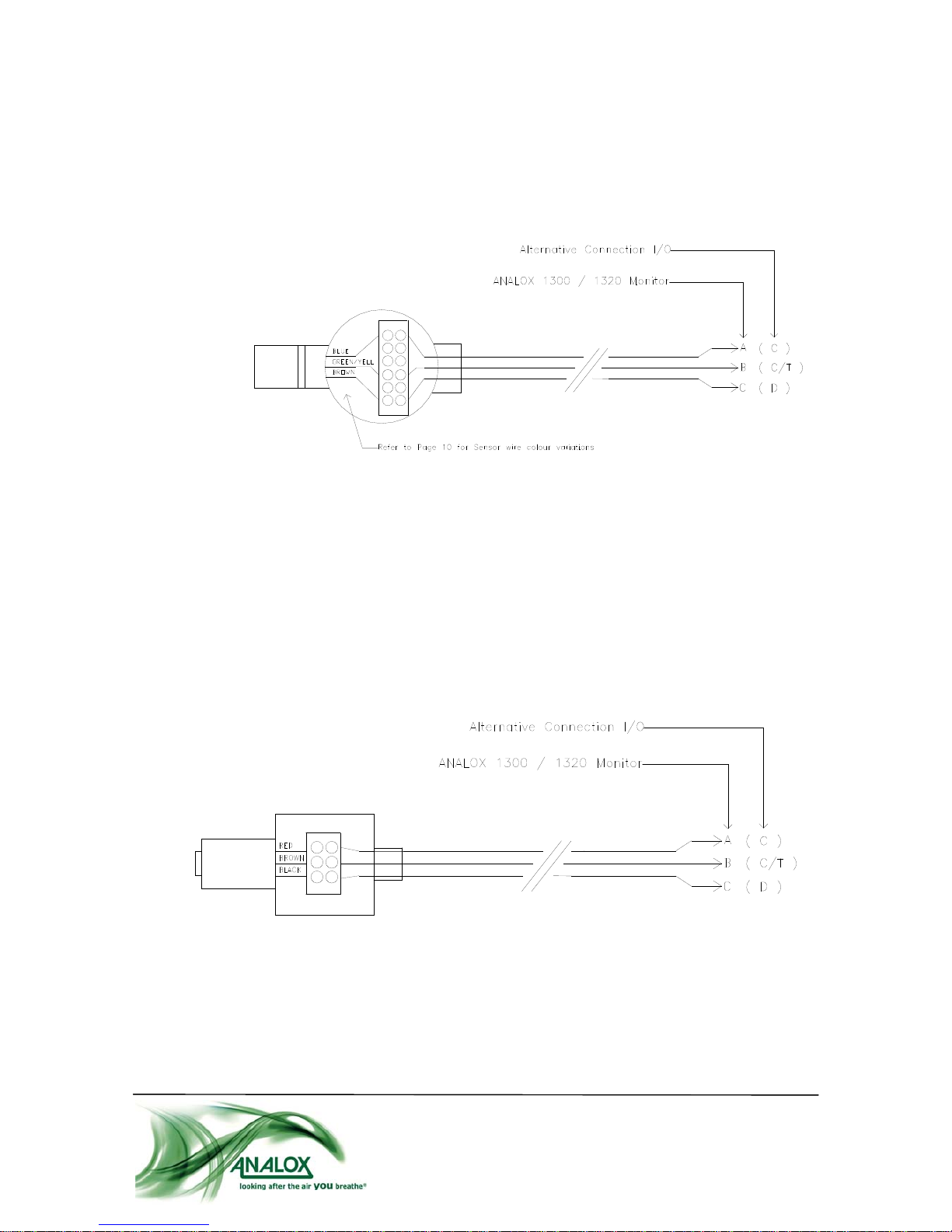
Analox 2000 – Flammable Gas Sensors – User Manual
Document Ref: SK0-810-04 January 2009
Page 9
ELECTRICAL CONNECTIONS
ANALOX 2000 SENSOR
ANALOX 2001 SENSOR
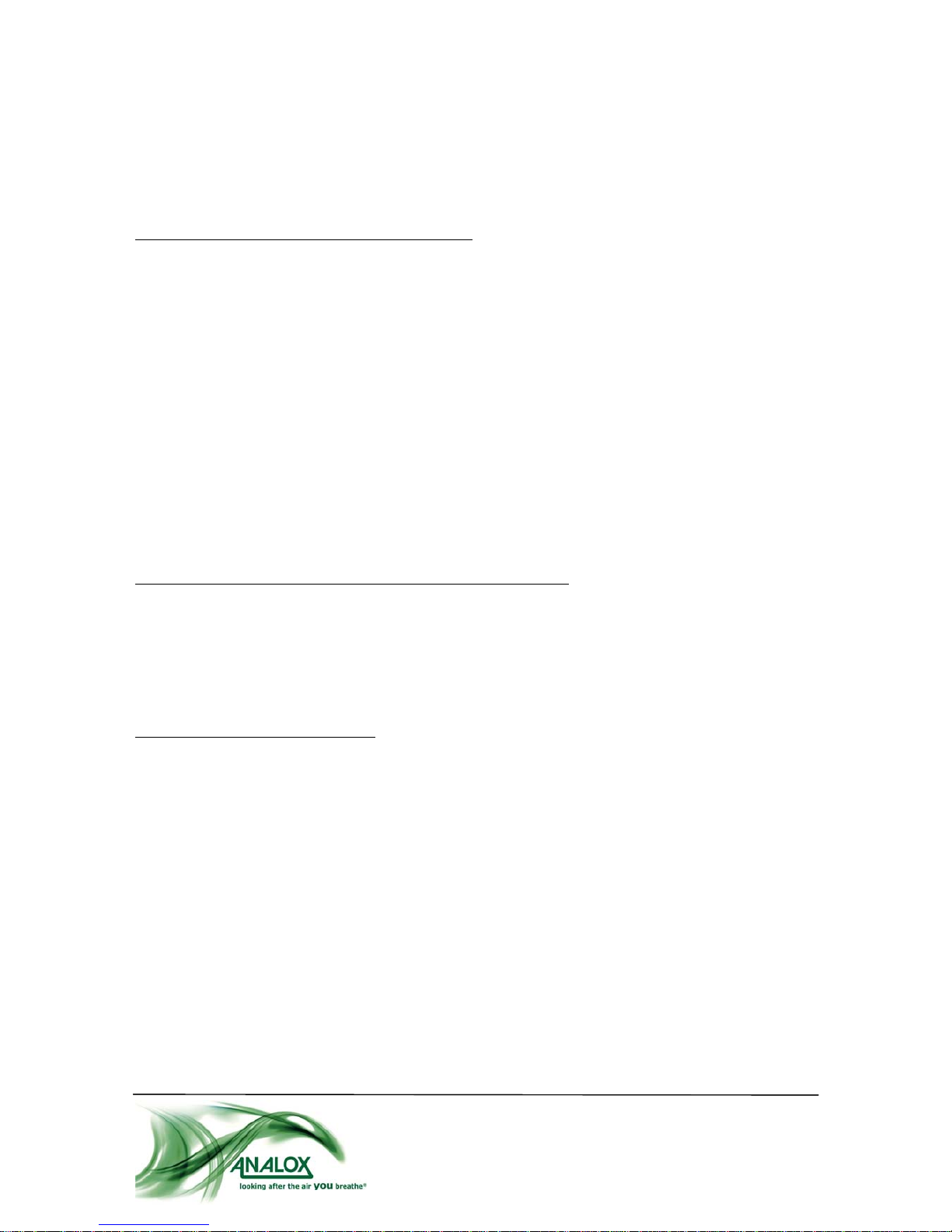
Analox 2000 – Flammable Gas Sensors – User Manual
Document Ref: SK0-810-04 January 2009
Page 10
FLAMMABLE SENSOR WIRING VARIATIONS
There are currently three different types of Sensor Head available from Analox and the Wiring
colours differ on each sensor. Details of the wiring colours are given below
a. EEV Stainless Steel, VQ4250 Exds Sensor has wiring colours :
BLUE, GREEN/YELLOW, BROWN
Where Blue is the Compensator Lead, which connects to the 'A' Terminal of the 1300.
Green/Yellow is the Signal output Lead which connects to the 'B' Terminal of the 1300.
Brown is the Detector Lead, which connects to the 'C' Terminal of the 1300
Due to possible confusion with European mains wiring colours (Blue, Green/Yellow, Brown)
and in the interests of safety, the manufacturer decided to change the colours of the wiring on
all new issues of this sensor.
The wiring colours on the latest issue of the Stainless Steel VQ4250 sensor are as follows :
RED, YELLOW, BLUE
Where Red is the Compensator Lead, which connects to the 'A' Terminal of the 1300.
Yellow is the Signal output Lead, which connects to the 'B' Terminal of the 1300.
Blue is the Detector Lead, which connects to the 'C' Terminal of the 1300.
b. GROVELY 210 Mod FLAM Stainless Steel Exds Sensor has wiring colours :
RED, GREEN, BLUE
Where Red is the Compensator Lead, which connects to the 'A' Terminal of the 1300.
Green is the Signal output Lead, which connects to the 'B' Terminal of the 1300.
Blue is the Detector Lead, which connects to the 'C' Terminal of the 1300.
c. ANALOX Black Acetal Sensor has the following wiring colours :
RED, GREEN, BLACK
Where Red is the Compensator Lead, which connects to the 'A' Terminal of the 1300.
Green is the Signal output Lead, which connects to the 'B' Terminal of the 1300.
Black is the Detector Lead, which connects to the 'C' Terminal of the 1300.
Sensors a. and b. are normally supplied fitted to an EExe Cast Iron Junction Box and together,
form the ANALOX 2000 Flammable gas sensor unit, suitable for use in Hazardous areas.
Sensor c. , the ANALOX 2001, is a less expensive alternative which can be used in areas
which are not classified as Hazardous.
IMPORTANT: IF THE SENSORS ARE INCORRECTLY CONNECTED, PERMANENT
DAMAGE COULD BE SUSTAINED WHEN POWER IS APPLIED.
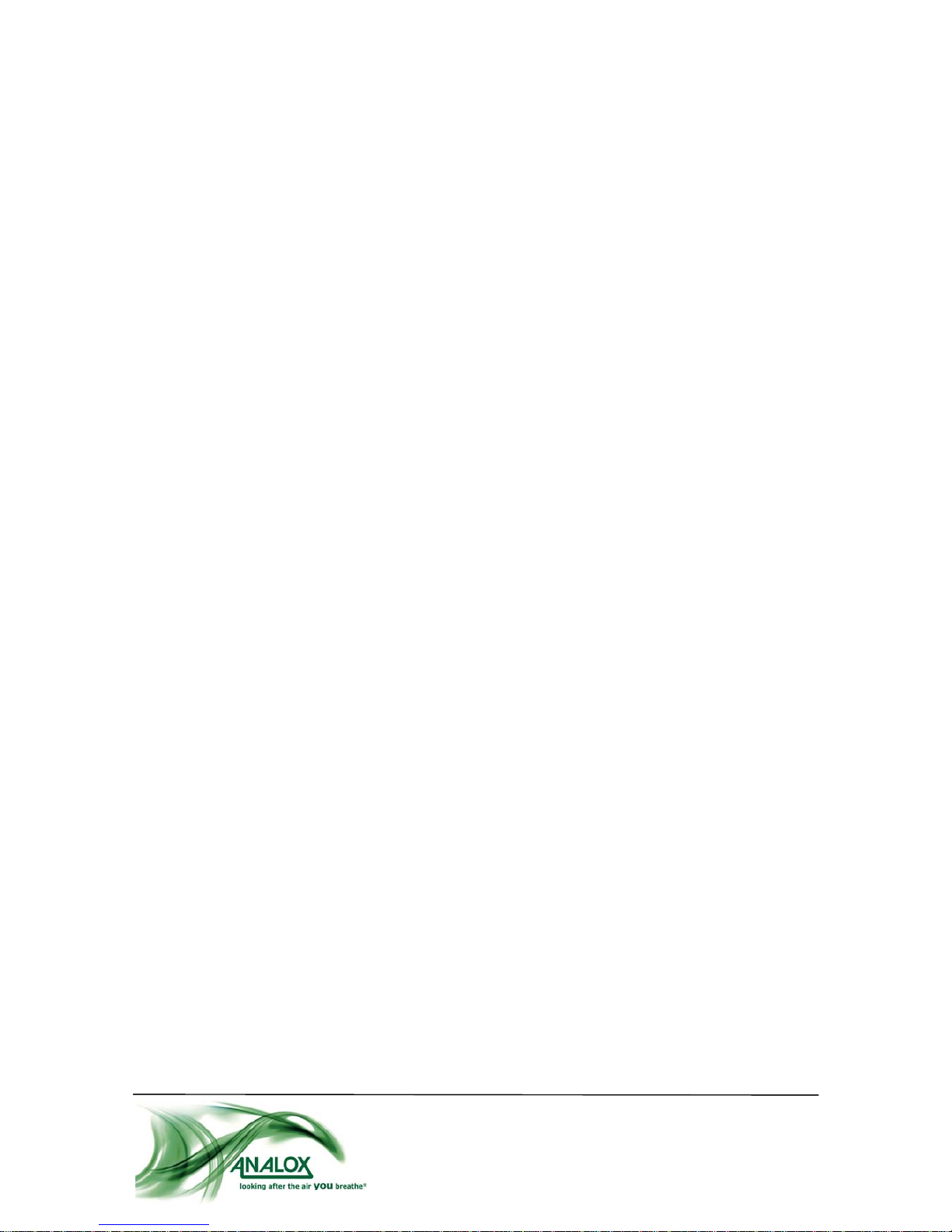
Analox 2000 – Flammable Gas Sensors – User Manual
Document Ref: SK0-810-04 January 2009
Page 11
SENSOR INSTALLATION
INSTALLATION
Care should be exercised during installation, not to damage the sintered element on the front
surface of the device. IT IS PARTICULARLY IMPORTANT THAT THEY ARE NOT EXPOSED
TO SILICON BASED SUBSTANCES OR HALOGENS, either during installation or in their
normal operating condition. This could lead to the sensors being Poisoned, as described above
in the 'OPERATING PRINCIPLE' section.
SENSOR POSITION
The type of gas to be detected determines, in general, the physical location of the sensor.
Whereas a gas that is heavier than air will require a low sensor mounting position, a lighter than
air gas will necessitate an elevated mounting point.
Consideration should be given to those areas where it is anticipated that leakage may occur eg.
in the vicinity of valves, pipe flanges, compressors etc. and also to the possibility of pockets of
gas collecting in the event of a leak. In this respect, heavier than air gases eg. propane or
butane, may tend to accumulate in floor ducts, pits etc. and ventilation should be provided for
these areas as a normal precaution. Lighter than air gases eg. methane or hydrogen will tend
to accumulate between ceiling joists, in roof spaces etc and similar consideration should be
given to adequate ventilation.
Additionally, the effects of any ventilation must be considered in the siting of gas sensors and it
may be prudent to mount sensors in air extraction ducts. However, excessive velocities can
affect the sensors and it may be necessary to provide a degree of draught protection. TABLE 1
on the next page, shows examples of molecular weights of some common flammable gases
and groups them in categories according to their weight, relative to air.
Lighter than Air Heavier than Air
Hydrogen 2.0 Methane 16.0 Ethane 30.1 Hydrogen Sulphide 34.0
Ammonia 17.0 Carbon Monoxide 28.0 Butane 58.1 Propane 44.1
Ethylene 28.0 Acetylene 26.0 Pentane 72.2 Toluene 92.1
Hexane 86.2 Heptane 100.2
TABLE 1. Relative Molecular weight of common gases NOTE: AIR = 29
The flammable sensors should be mounted with the sinter facing downward, whether it is
mounted high or low.
ACCESSORIES
Calibration adaptors and collecting cones are available for both types of sensor. Identification
and part Numbers are listed below.
Calibration adaptor for ANALOX 2000 when used WITHOUT Collecting cone : SA2 SO2 FLOW
Calibration adaptor for ANALOX 2000 when used WITH Collecting cone : SA2 FLOW1
Calibration adaptor for ANALOX 2001 when used With or WITHOUT Collecting cone :
SA2 FLOW1 Collecting Cone : SA2 PO2 CONEFLAM
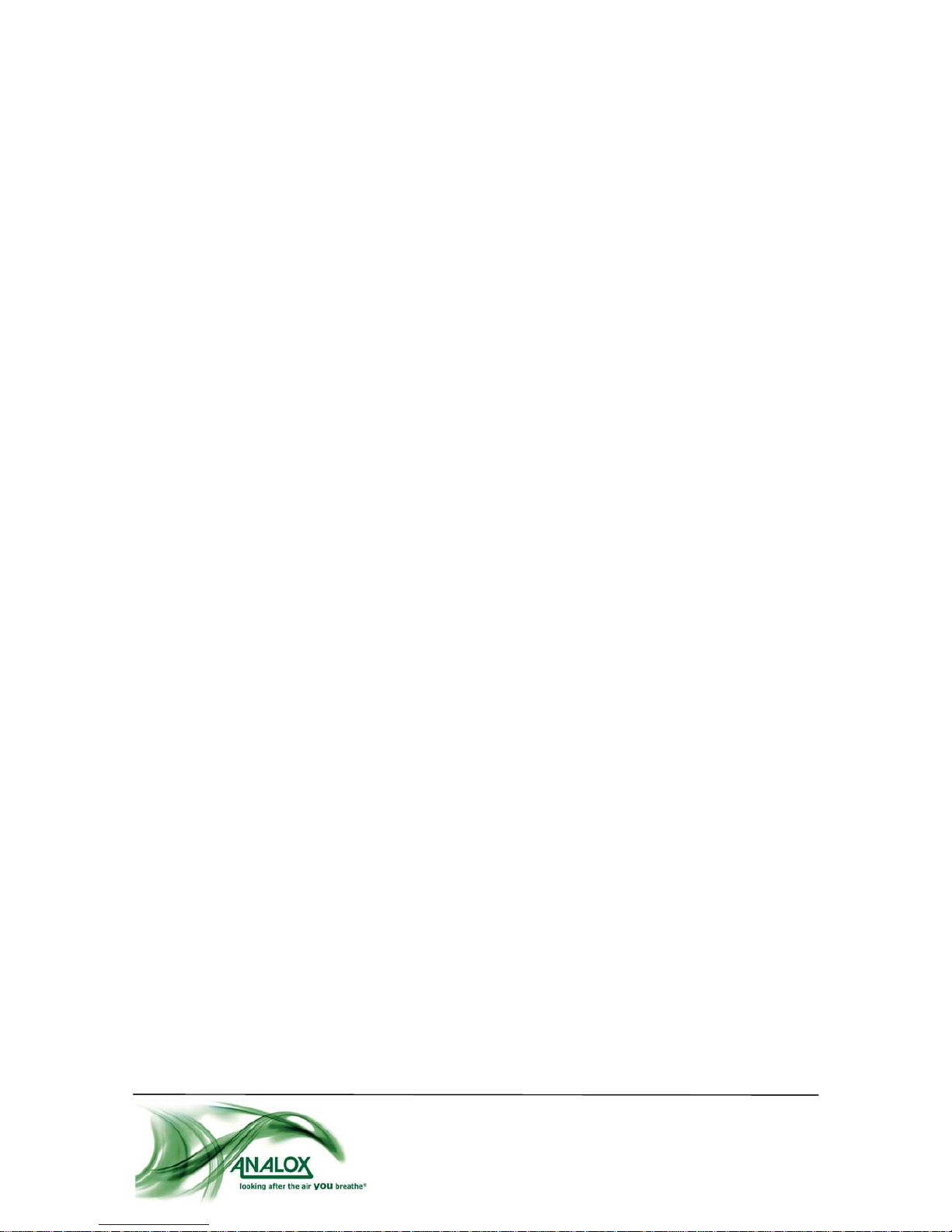
Analox 2000 – Flammable Gas Sensors – User Manual
Document Ref: SK0-810-04 January 2009
Page 12
Further details may be obtained from AST. Ltd., whose address, telephone and fax numbers
are on the front page of this manual.
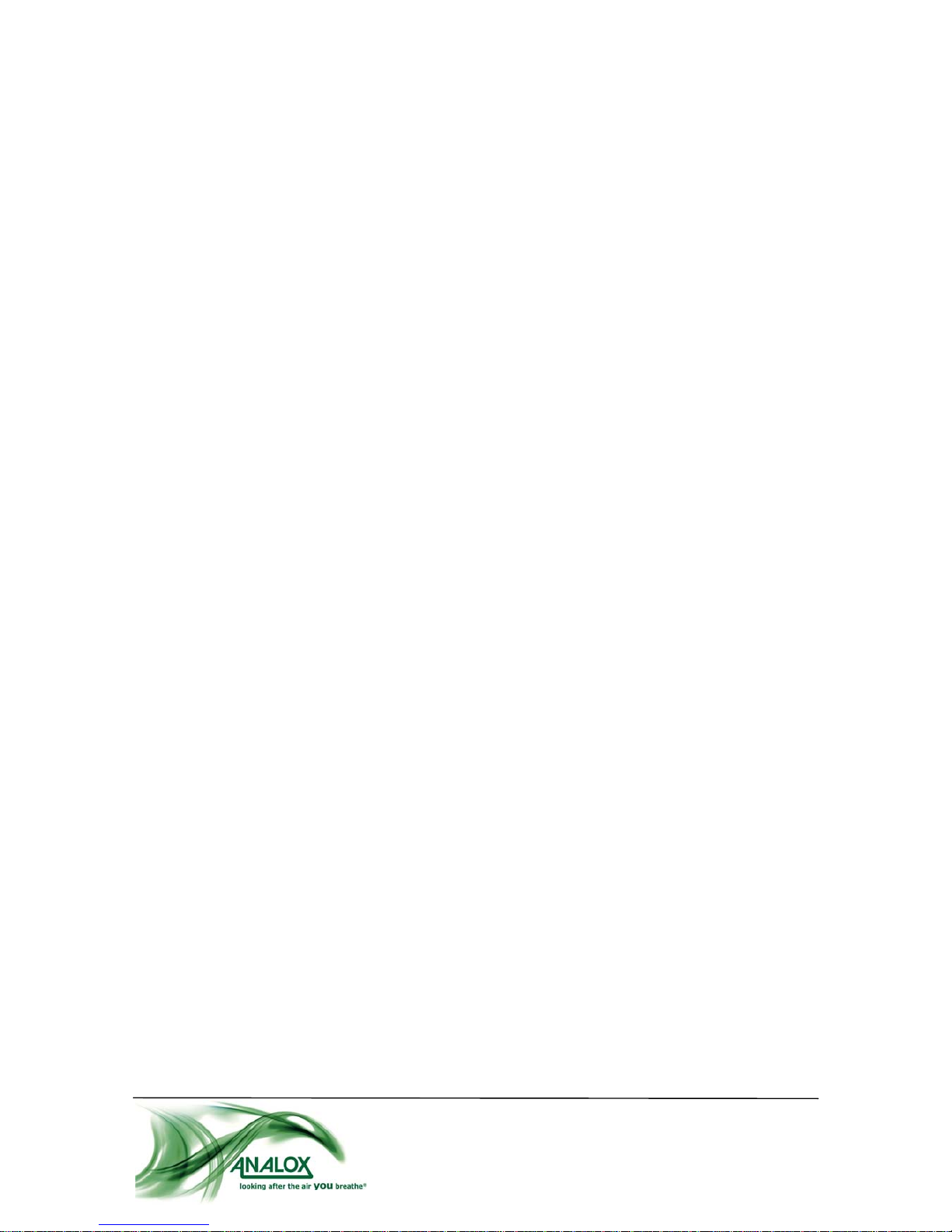
Analox 2000 – Flammable Gas Sensors – User Manual
Document Ref: SK0-810-04 January 2009
Page 13
CERTIFICATION
Areas into which gas sensors may be installed, may be classified as being potentially or
actually hazardous, in accordance with applicable legislation, or alternatively may be
unclassified. Hazardous areas are split into zones as defined in BS 5345 and IEC79-10, as
follows:
Zone 0: in which an explosive gas/air mixture is continuously present or present
for long periods.
Zone 1: in which an explosive gas/air mixture is likely to occur during normal
operation.
Zone 2: in which an explosive gas/air mixture is not likely to occur and if it does,
will only exist for a short period.
Zone 0 areas normally only permit the installation or use of Intrinsically Safe equipment,
classified Ex(ia) or in certain cases Ex(s) (Specially Certified for Zone 0).
Zone 1 areas normally only permit the installation or use of equipment certified as Flameproof
ie Ex(d) or any equipment suitable for Zone 0. In certain circumstances, Increased Safety
equipment, classified Ex(e) may be allowed. In addition, equipment certified Ex(ib), Ex(p) and
Ex(s) may be used in this Zone, but these classes are not generally related to Flammable
sensors.
Zone 2 areas normally permit the use of all classifications quoted for Zones 0 and 1 and in
addition, Ex(n), Ex(o) and Ex(q) - again, these latter classifications are not generally relevant to
Flammable sensors, but are shown for completeness.
Unclassified areas permit the installation or use of any equipment, whether certified or not.
From a certification point of view, sensors of the Catalytic type are considered as being a bit
unusual in that they contain a heated filament. Introduction of a heated filament into what may
be a potentially explosive atmosphere may seem to be inviting trouble! However, careful study
of Flame Arresting devices and materials since the introduction of the gauze arrestor of 'Davy
Lamp' fame, has led in the case of gas detection sensors, to the almost exclusive use of
sintered metal with a carefully selected pore structure. S.A.E.P certified sensors incorporate a
disc of sintered stainless steel between the pellistors and the surrounding atmosphere. Up to
the time of writing this manual, certification classifies the filament chamber with the special
protection class, Ex(s) combined with the appropriate terminal chamber, Ex(d) or Ex(e).
Combination of the appropriate certification classes ie Exs(d) or Exs(e) implies that the certified
equipment has been tested and is suitable for inclusion in areas which permit the use of (d) or
(e) classification, as appropriate.
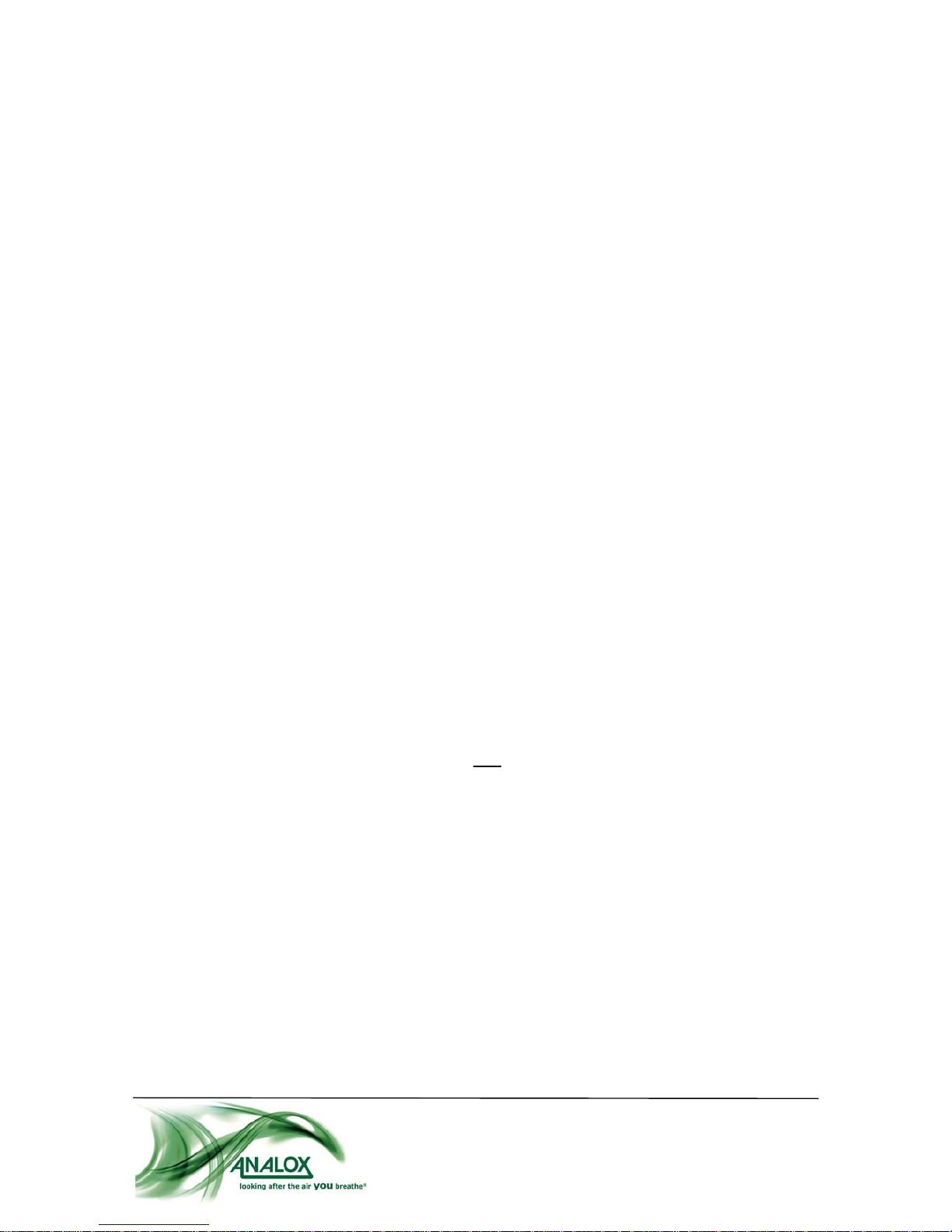
Analox 2000 – Flammable Gas Sensors – User Manual
Document Ref: SK0-810-04 January 2009
Page 14
INTRINSICALLY SAFE SYSTEM
The ANALOX 2000 sensor may be used as a component within an Intrinsically Safe SYSTEM
where the area to be monitored is classed as Zone 0 and therefore requires that any electrical
equipment system used therein be classified Ex ia. The ANALOX 2000 SYSTEM comprises the
following items:
a. The Sensor and its Junction box.
b. A combination of Zener Barriers.
c. Suitable connecting cable between the Zener barriers and the sensor junction
box.
However, due to the relatively high currents which flow in the cables (up to 300mAmps),
there are some constraints placed on the length and type of cable which may be used in the
Hazardous area. The constraints are due to the amount of energy which can be stored within
the inductance and capacitance of the cable. This energy could be released in the form of a
spark, if the cable becomes damaged, thereby causing a potentially dangerous condition.
Where relatively high currents are carried by a cable and the terminating impedance is low, as
is the case with Pellistor sensors, the parameter of main concern is the inductance of the
conductors. The Total Inductance of a conductor is directly proportional to its length so the
longer the cable, the higher the Inductance value. The parameters of the cables must meet the
specification laid down by the certifying authority (BASEEFA). The cable parameters are
included on the System certificates, copies of which are shown at the end of this manual. As
can be seen from the data, if a sensor with VQ21 type Pellistors is to be used in a Group IIC
application, ie Hydrogen or Acetylene present, then the maximum permissible TOTAL cable
inductance is 4.4uH (4.4 micro henries). This means that the cable run between the Zener
barriers and the sensor junction box in this application, will be restricted to about 6 metres. The
quoted length is based on a typical 3 core IS class cable (complying to DIN VDE 0165) which
has a quoted Inductance of 0.7 millihenries/Km., ie 0.7 microhenries per metre. From the
certificate schedule data, using a sensor fitted with VQ21 Pellistors for a Group IIC application,
the maximum permissible Inductance is 4.4uH. So, if the cable has an Inductance of
0.7uH/metre then the maximum length can be calculated:
Length = 4.4
= 6.29 metres.
0.7
This example illustrates the absolute worst case and for installations with less severe Gas
Groups, longer cables can be used. Also, if the sensor is fitted with VQ22 Pellistors, which
operate at a lower current (175 mAmps) the restrictions are again less severe.
Some calculated values for different applications using VQ21 and VQ22 Pellistors are shown
below. These calculations are based on a 3 core cable supplied by LAPPKABEL, 'OLMASS -
EB CY' part number 0045800.
2000 Sensor with VQ21 Pellistors.
Gas Group Maximum cable length
IIC 6.29 mtr.
IIB 19.00 mtr.
IIA 63.43 mtr.
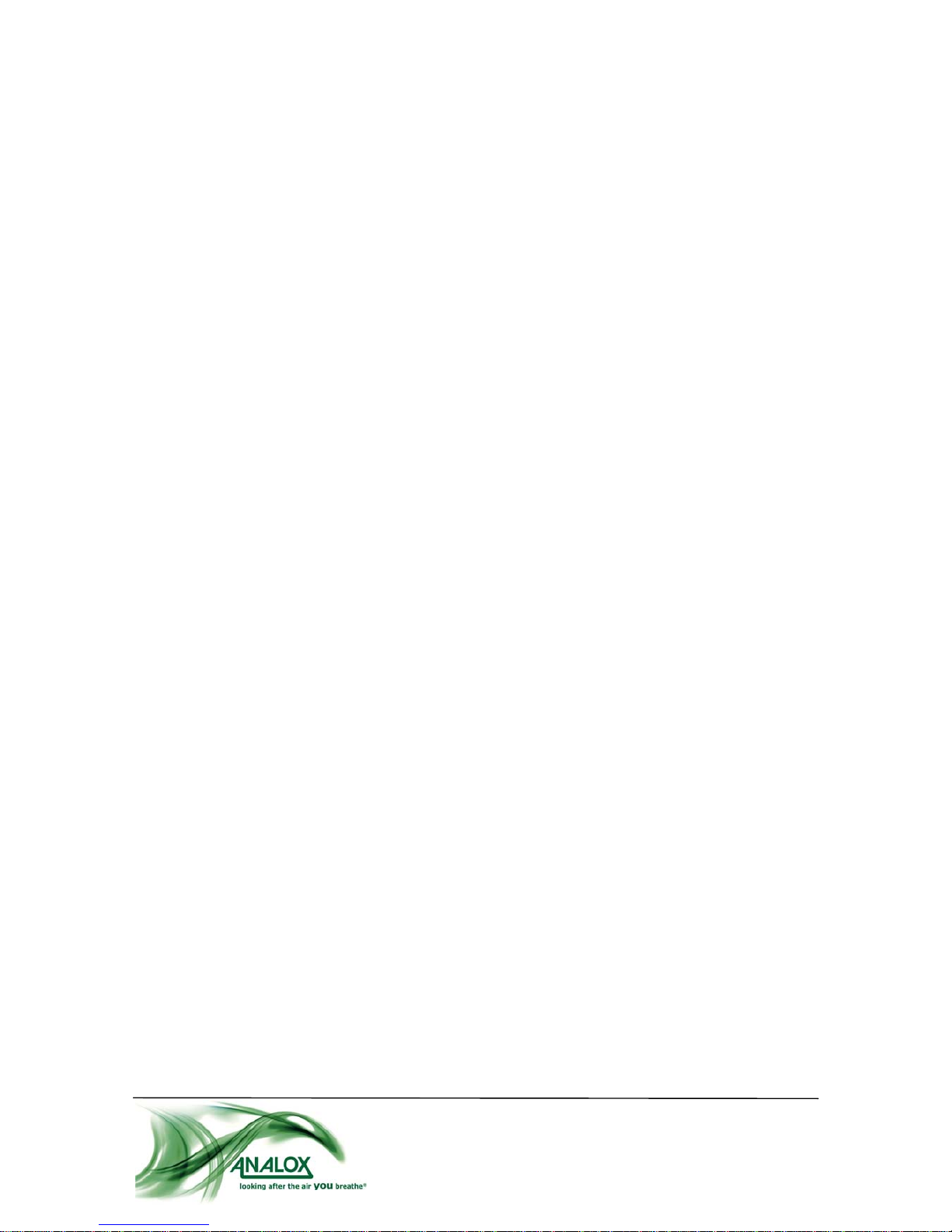
Analox 2000 – Flammable Gas Sensors – User Manual
Document Ref: SK0-810-04 January 2009
Page 15
2000 Sensor with VQ22 Pellistors.
Gas Group Maximum cable length
IIC 25.39 mtr.
IIB 76.14 mtr.
IIA 253.86 mtr.
SENSOR RESPONSE TIME
The time taken for the monitoring instrument to indicate the concentration of gas at the sensor
is dependent on two factors.
a. The speed of response of the actual detecting elements.
b. The ease of access of the gas to the detecting elements.
Since a. is fixed, careful design of the housing and flame arrestor is essential to ensure that the
gas diffuses as rapidly as possible on to the heated elements. The introduction of the sintered
disc does however increase the overall response time and other protection devices such as
splash guards, carbon filters etc. will inevitably degrade the speed even more. The design of
such devices, combined with the essential flame arresting sintered disc, is a compromise
between fast speed of response and other protection. The speed of response of a
sensor/instrument combination can be expressed in a number of ways, and is currently done so
by many manufacturers, in an attempt to show their instruments in a favourable light. S.A.E.P.
have adopted what is believed to be the only accurate way of expressing this parameter. Since
the response of a sensor is nominally exponential, irrespective of the gas concentration at the
sensor, the time to reach a specific percentage of the actual concentration of the gas applied, is
relevant. The most commonly chosen figure is 90% of final value and is usually quoted as the
'T90' time. S.A.E.P. quote the 'T90' time for the 2000 and 2001 sensors as less than 5 seconds,
when using Methane (CH4) as a test gas. Increased or decreased response times may be
expected from those gases with a more or less complex molecular structure.
SENSOR ELEMENT LIFE
It is very difficult to honestly define the lifetime of a catalytic sensor, particularly when the
conditions of use are outside the control of the manufacturer. There have been many cases
where sensors have continued to operate satisfactorily for many years. In other cases, the life
has been considerably less. The major causes of element failure, other than gradual
degradation, have been due to open circuit filaments or chemical poisoning. Open circuit
filaments can be caused by:
a. Incorrect connection to the power supply, resulting in one or both filaments burning
out.
b. Passing excessive current through the filaments by applying too high an excitation
voltage.
c. High concentrations of combustible gas/air mixture present at the sensor for
excessive periods of time.
d. Physical shock causing mechanical damage.
CHEMICAL POISONING
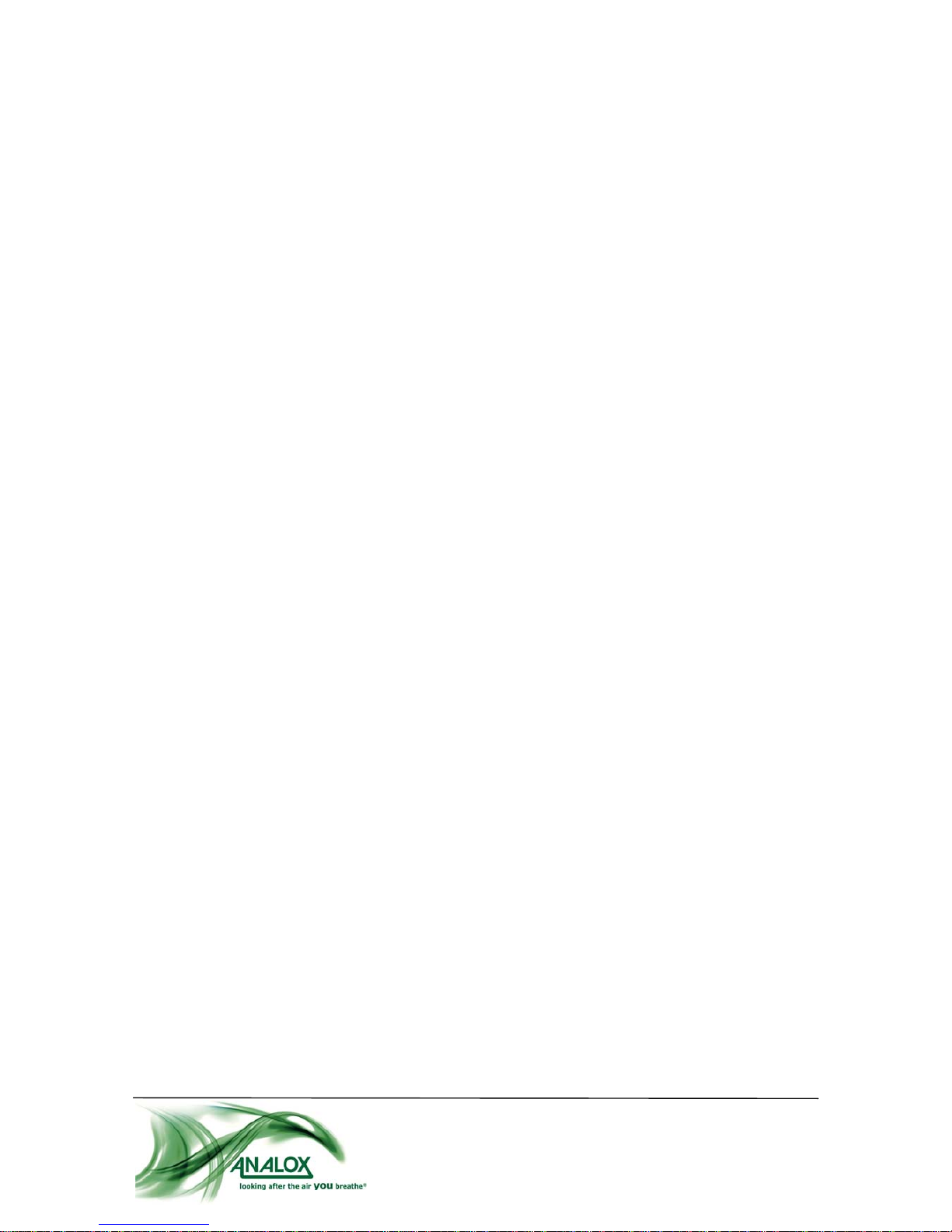
Analox 2000 – Flammable Gas Sensors – User Manual
Document Ref: SK0-810-04 January 2009
Page 16
This is an extremely complex problem on which, a considerable amount of research is currently
being carried out. It is well known that some substances can cause a significant reduction on
overall sensitivity of the system and in some cases, the effects are only temporary, in others a
permanent degradation in response can take place. Materials to be particularly avoided are,
Silicone, Lead and Sulphur compounds and Halogens. Whereas the importance of checking
sensors for sensitivity at frequent and regular intervals cannot be over stressed, in the event of
possible poisoning material being present, the procedure is doubly important. Preventative
measures can also be taken to reduce the possibility of poisoning when certain gases are to be
measured. These involve the introduction of an activated Carbon filter pack between the sensor
and the surrounding ambient atmosphere.
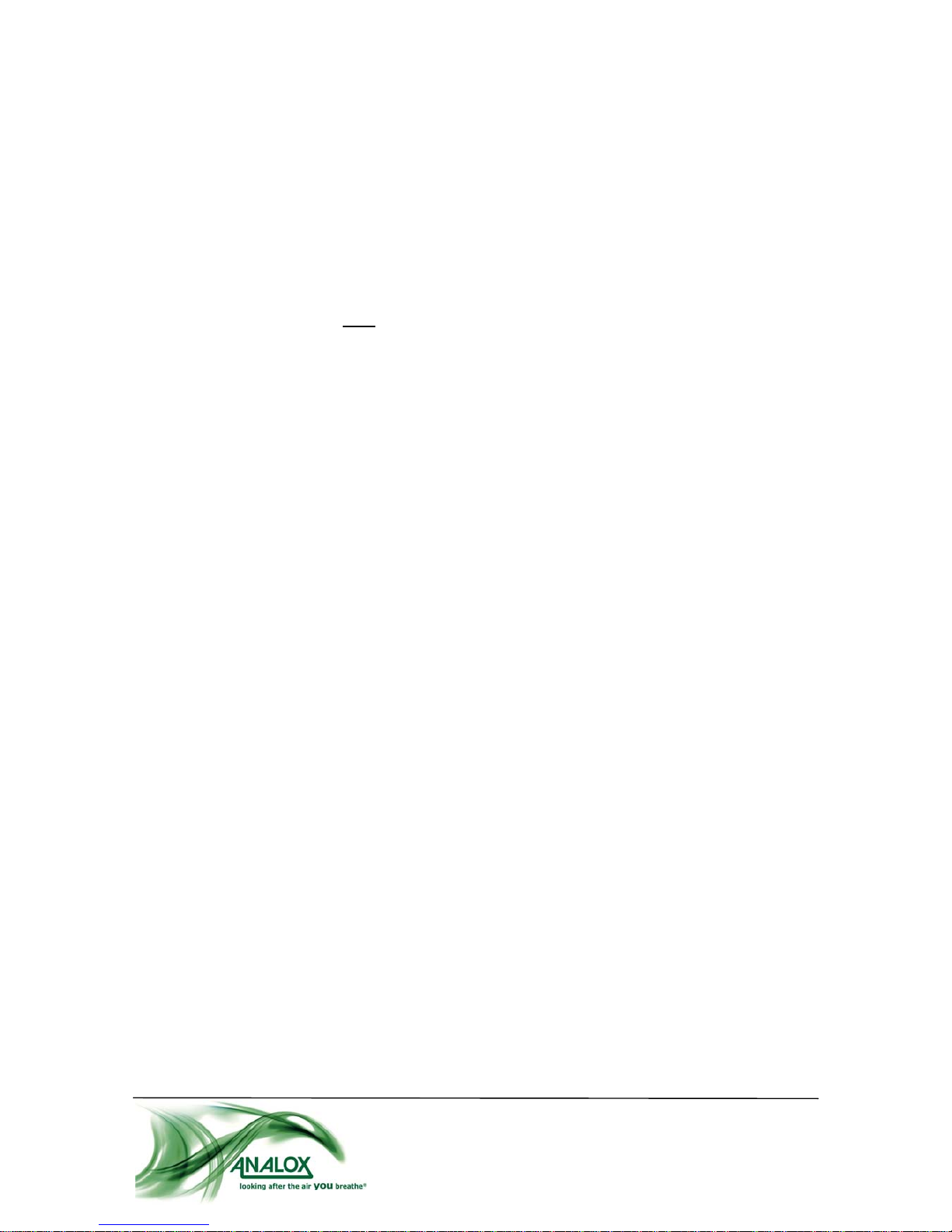
Analox 2000 – Flammable Gas Sensors – User Manual
Document Ref: SK0-810-04 January 2009
Page 17
APPENDIX TO ANALOX 2000 SERIES MANUAL
A feature of the Pellistor Combustible gas detectors is the almost universal response to LEL of
hydrocarbons. Almost all detectable gases produce a similar output at LEL. This table lists the
theoretical factors by which the signal with a Calibration gas should be multiplied to give the
equivalent signal for other gases. For example:
For an instrument calibrated with Methane K Methane=112.0
To find equivalent for n-Nonane K n-Nontane = 35.2
Signal at 50% LEL = 50% x 35.2 = 15.7% (Methane Scale)
112.0
Gas K
Acetaldehyde 67.3
Acetone 57.8
Ammonia 141.7
Benzine 45.6
n-Butane 65.5
cis-Butene-2 54.2
iso-Butyl Alchol 59.2
n-Butyric Acid 42.5
Carbon Oxysulphide 104.6
Cyclopropane 69.7
Dimethylamine 64.7
Dimethylsulphide 48.6
Ethyl Acetate 57.4
Ethyl Benzine 39.9
Ethyleneoxide 57.9
Ethylmercaptan 62.8
Hydrazine 50.4
Hydrogen Sulphide 45.6
Methyl Alcohol 96.2
Dimethyl Ether 70.0
Methyl Formate 75.0
Napthalene 38.1
n-Octane 41.9
Propane 61.8
Propylene 57.7
Propyne 46.5
Trimethylamine 54.3
m-Xylene 43.8
Gas K
Acetic Acid 60.8
Acetylene 63.6
n-Amyl Alcohol 36.6
Biphenyl 28.0
iso Butane 57.8
trans-Butene-2 56.7
Tert-Butyl Alcohol 83.1
Carbon Disulphide 19.8
Cyanogen 99.9
n-Decane 36.7
2,3 Dimethylpentane 44.6
1,4 Dioxane 50.0
Ethyl Alcohol 81.5
Ethylcyclopentane 44.4
Diethyl Ether 51.8
n-Heptane 43.2
Hydrogencyanide 53.4
Methane 112.0
Methylamine 86.5
Methylethylether 49.3
Methylmercaptan 67.9
Nitromethane 64.8
n-Pentane 51.3
n-Propyl Alcohol 52.7
Propyleneoxide 51.2
Toluene 45.2
Vinylethylether 46.9
p-Xylene 43.8
Gas K
Acetic Anhydride 51.5
Alkyl Alcohol 57.1
Aniline 44.1
1,3 Butadiene 62.5
Butene-1 50.8
n-Butyl Alcohol 38.4
n-Butyl Benzine 35.8
Carbon Monoxide 84.4
Cyclohexane 46.0
Diethelamine 64.7
2,2 Dimethylpropane 44.4
Ethane 75.8
Ethylamine 58.9
Ethylene 79.1
Ethyl Formate 49.5
n-Hexane 41.2
Hydrogen 85.8
Metyyl Acetate 55.6
Methylcyclohexane 49.4
Methylethylketone 46.2
Methylpropionate 57.2
n-Nonane 35.2
iso-Pentane 51.9
n-Propylamine 54.1
iso-Propylether 48.8
Triethylamine 44.6
o-Xylene 40.1
Since these factors are theoretical, they will only give a guide to the response expected in other
gases. For exact conversion factors, the Instrument should be calibrated using the relevant
gases.
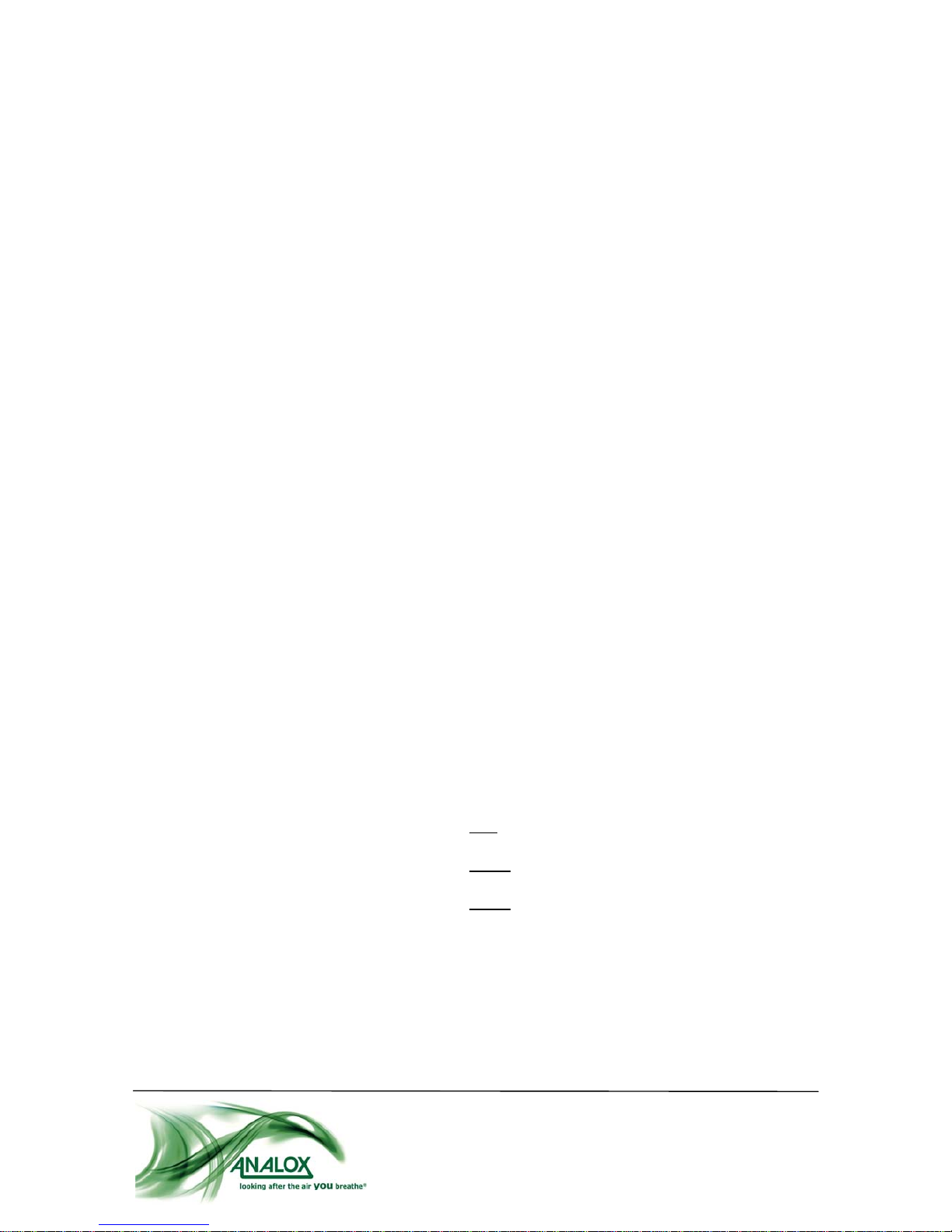
Analox 2000 – Flammable Gas Sensors – User Manual
Document Ref: SK0-810-04 January 2009
Page 18
FLAMMABLE SENSOR CABLE REQUIREMENTS
When using the present ANALOX 2000 or 2001 Flammable sensors with the Analox 1300/1320
instruments, the following data gives guidance to the maximum permissible cable lengths, for
wire having various cross sectional areas.
The usable cable length depends on several factors:
a Cross sectional Area in square millimetres (mm2) and hence the resistance of the wire.
b The operating current of the sensor
c The operating voltage of the sensor
d The maximum sensor excitation voltage available from the monitoring instrument
Cable resistance is normally quoted in Ohms per Kilometre and it should be bourne in mind that
when used with a sensor that the actual wire length is TWICE the distance from instrument to
sensor.
The Pellistors which can be used in the 2000/2001 have the following characteristics
Type Operating Voltage Operating Current
VQ21 2.0 volts 300 milliamps
VQ22 2.0 volts 175 milliamps
VQ23 2.0 volts 335 milliamps
The maximum sensor excitation voltage available from the 1300/1320 instruments is approx 3.8
Volts.
Assuming Maximum Sensor excitation voltage:
Maximum permissible voltage drop on the cable for the three types of sensor is as follows:
VQ21 3.8v – 2.0v = 1.8v
VQ22 3.8v – 2.0v = 1.8v
VQ23 3.8v – 2.5v = 1.3v
Therefore for the three different sensors the maximum wire resistance can be calculated
VQ21 max wire res. = 1.8 = 6.0 Ohms
0.3
VQ22 max wire res. = 1.8 = 10.28 Ohms
0.175
VQ23 max wire rex. = 1.3 = 3.88 Ohms
0.335
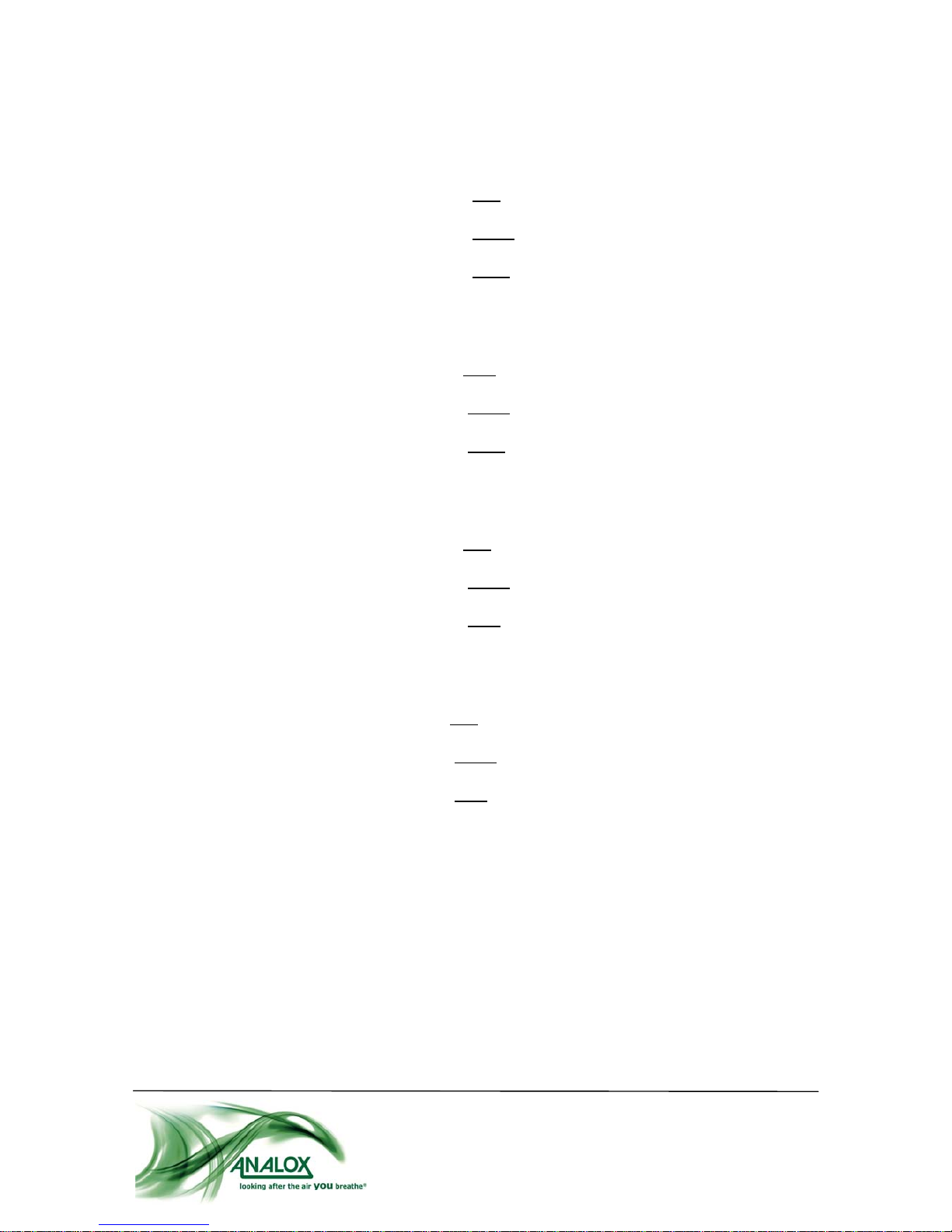
Analox 2000 – Flammable Gas Sensors – User Manual
Document Ref: SK0-810-04 January 2009
Page 19
Using: 1 0mm2 Cable with resistance 19.1 Ohms/Km (38.2 Ohms/loop)
VQ21 max. distance = 6 = .157Km or 157mtr
38.2
VQ22 max. distance = 10.28 = .269Km or 269mtr
38.2
VQ23 max. distance = 3.88 = .102Km or 102mtr
38.2
Using 1.5mm2Cable with resistance 12.5 Ohms/Km (25.0 Ohms/loop)
VQ21 max. distance = 6 = .240Km or 240mtr
25.0
VQ22 max. distance = 10.28 = .411Km or 411 mtr
25.0
VQ23 max. distance = 3.88 = .155Km or 155mtr
25.0
Using 2.0mm2Cable with resistance 9.7 Ohms/Km (19.4 Ohms/loop)
VQ21 max. distance = 6 = .309Km or 309mtr
19.4
VQ22 max. distance = 10.28 .529Km or 529mtr
19.4
VQ23 max. distance = 3.88 = .200Km or 200mtr
19.4
Using 2.5mm2Cable with resistance 7.6 Ohms/Km (15.2 Ohms/loop)
VQ21 max. distance = 6 = .394Km or 394mtr
15.2
VQ22 max. distance = 10.28 = .676Km or 676mtr
15.2
VQ23 max. distance = 3.88 = .255Km or 255mtr
15.2
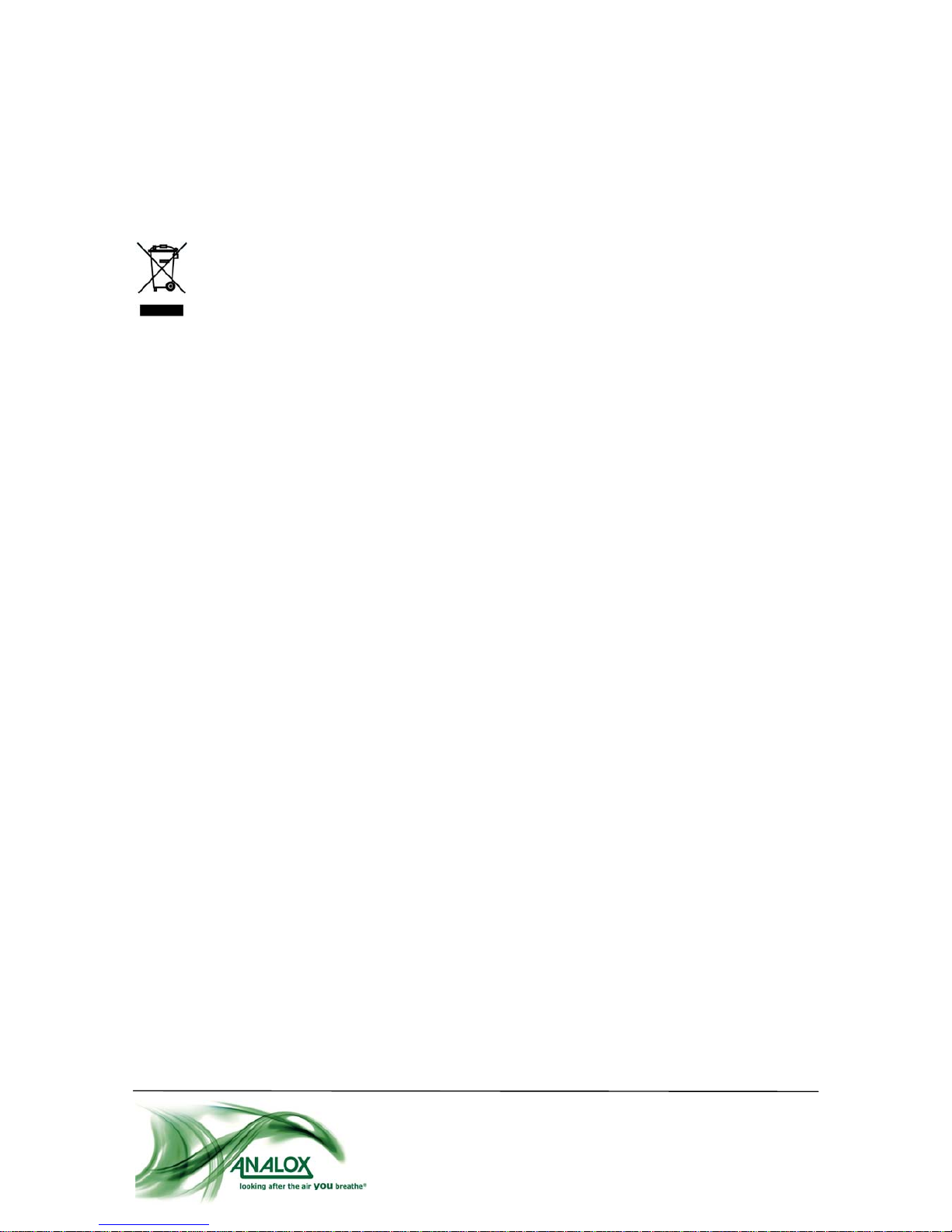
Analox 2000 – Flammable Gas Sensors – User Manual
Document Ref: SK0-810-04 January 2009
Page 20
DISPOSAL
According to WEEE regulation this electronic product can not be placed in household waste
bins. Please check local regulations for information on the disposal of electronic products in
your area.
Table of contents
Other ANALOX Accessories manuals
Popular Accessories manuals by other brands
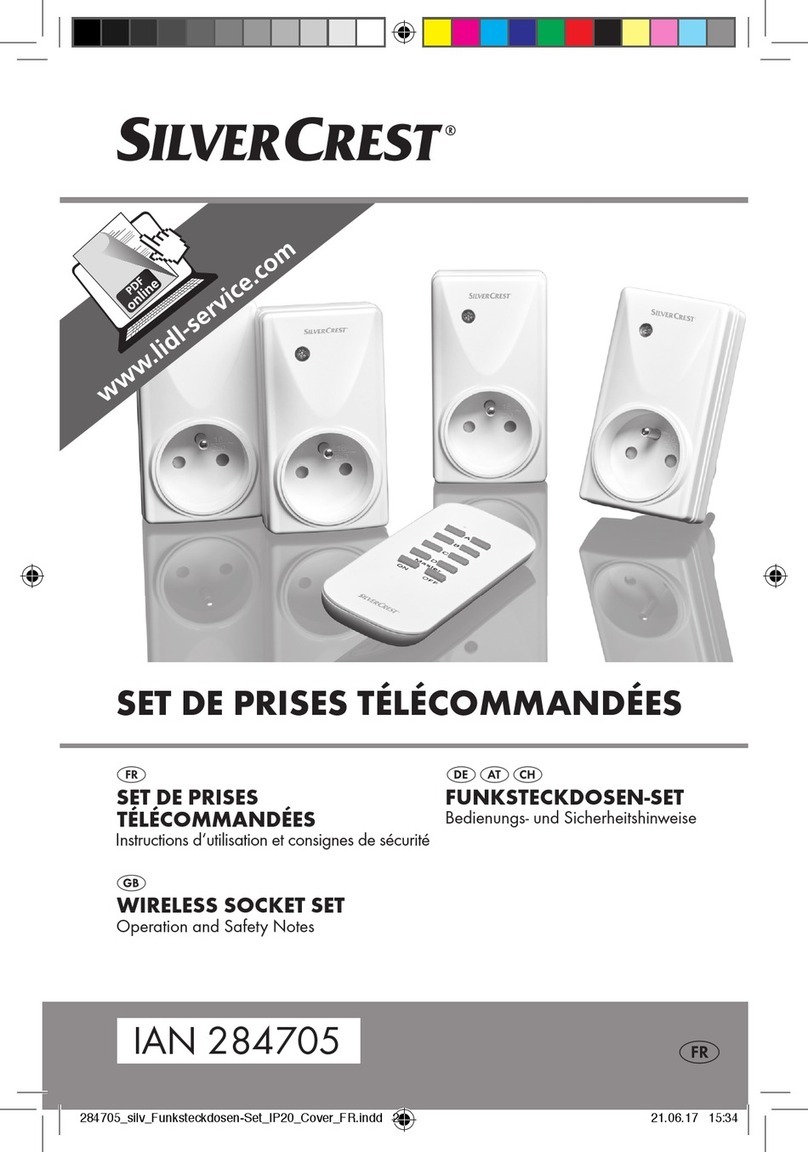
Silvercrest
Silvercrest 284705 Operation and safety notes
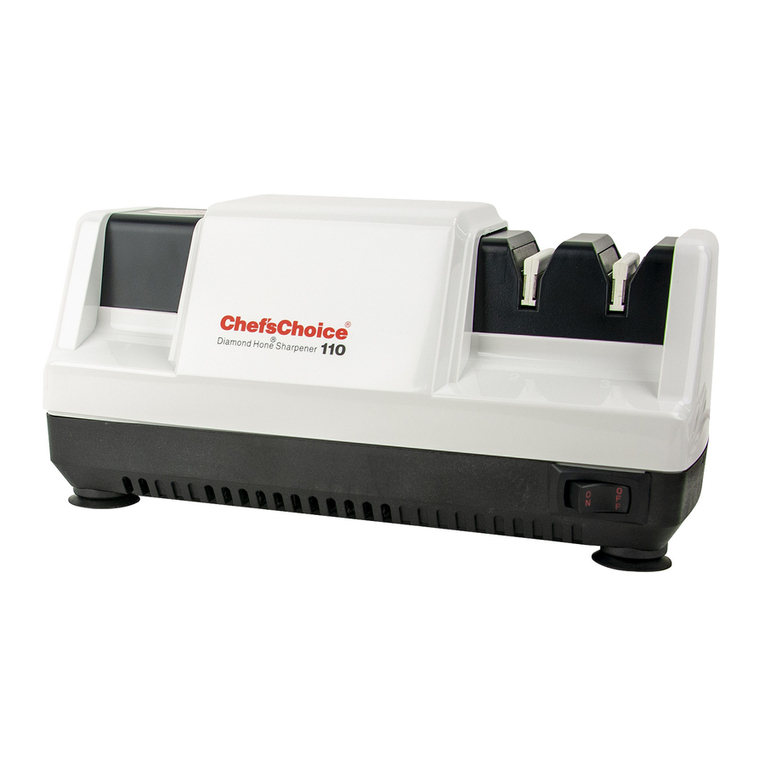
Chef's Choice
Chef's Choice Chef'sChoice Diamond Hone 110 user manual
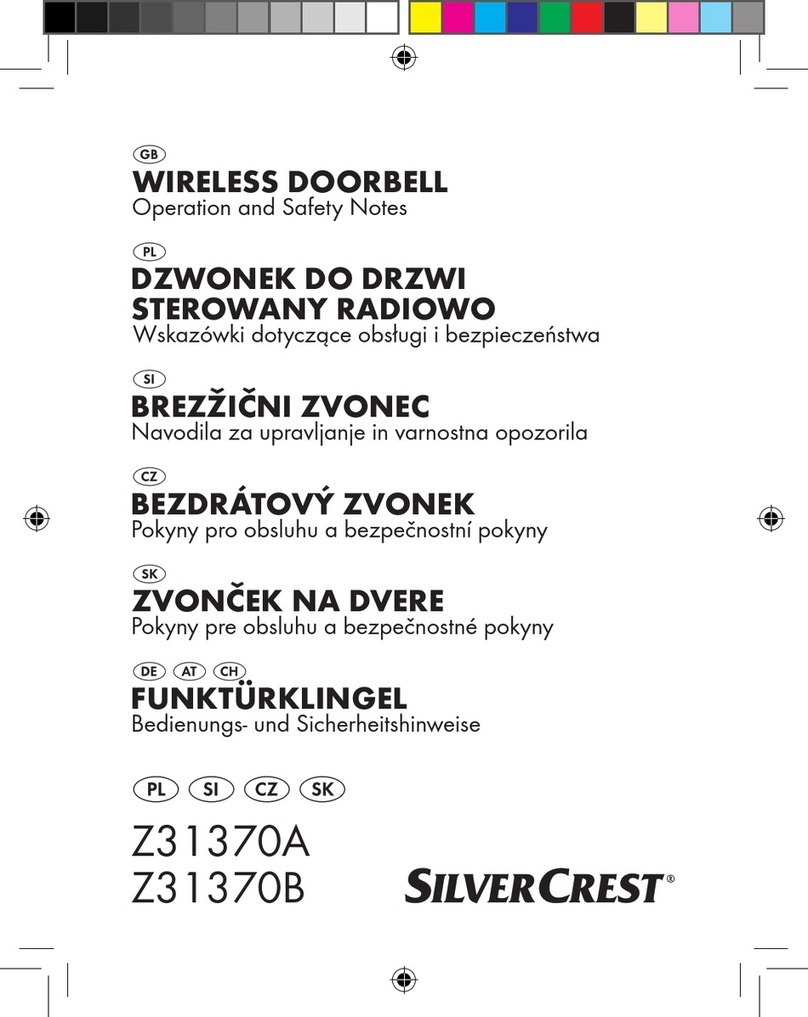
Silvercrest
Silvercrest Z31370A Operation and safety notes
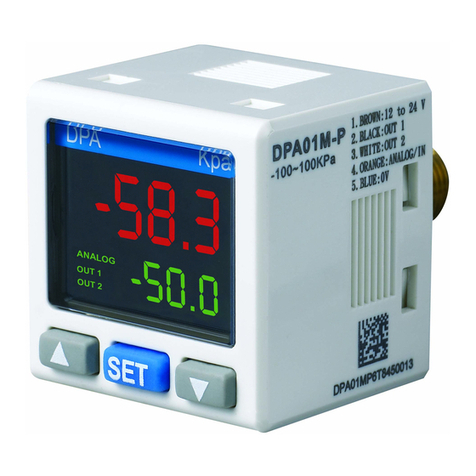
Delta
Delta DPA Series instruction sheet
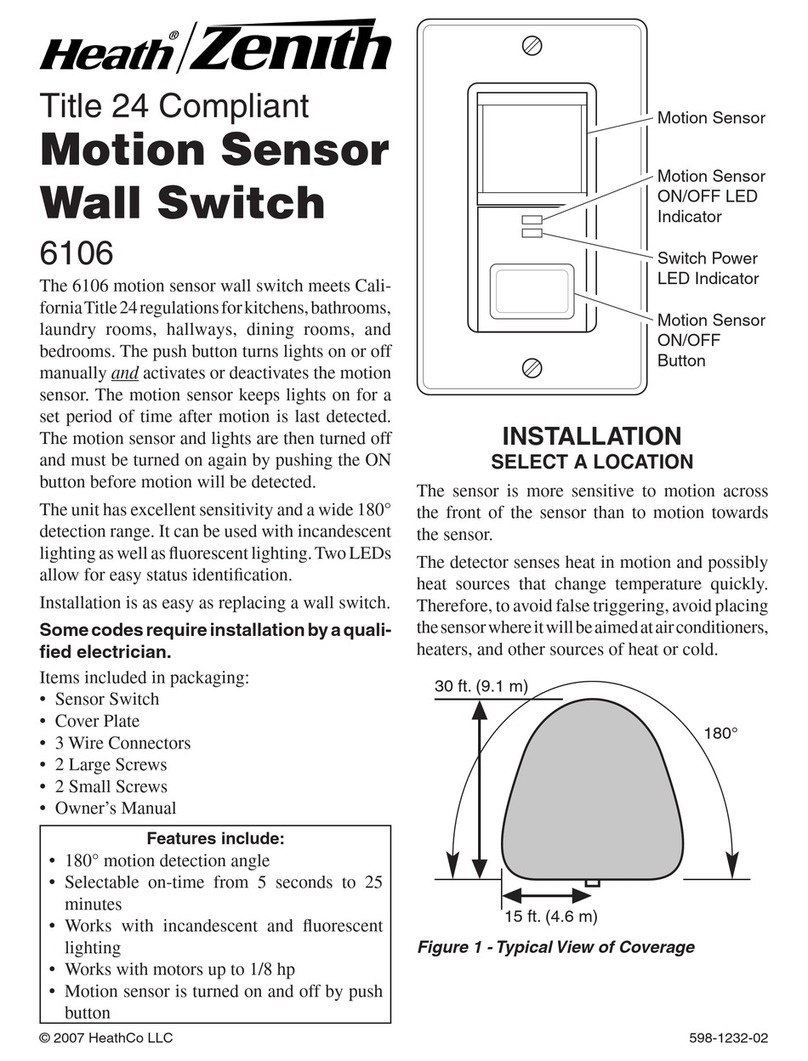
Heath Zenith
Heath Zenith 6106 installation guide
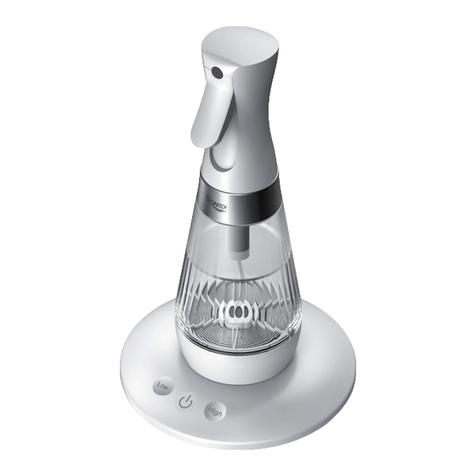
Biontech
Biontech BTS-1000 User guide book