Anderson AV-9900 User manual

AndersonInstrumentCo.,Inc.
156AuriesvilleRd.
Fultonville,NY12072
Phone:518-922-5315
800-833-0081
www.anderson-negele.com
Instruction
Manual
Rev. 4.0
Doc. 1029
AV-9900
Field Setup
Guide
AV-9900
Microprocesor Based
HTST Recorder/Controller

Document Revision 3.0 2
Table of Contents
1. INTRODUCTION .................................................................................................................................................3
2. KEY PRODUCT FEATURES..............................................................................................................................4
2.1. HOT PRODUCT TEMPERATURE SENSOR ........................................................................................................... 4
2.2. DIVERSION SWITCHING ................................................................................................................................... 4
2.3. DIAGNOSTIC CIRCUITRY ................................................................................................................................. 4
2.4. PEN DRIVE MECHANISM AND CHART PRINTING.............................................................................................. 5
2.5. COLD PRODUCT RECORD - CONTROL .............................................................................................................. 5
2.6. HOT WATER LOOP CONTROL .......................................................................................................................... 5
3. HARDWARE DESCRIPTIONS ..........................................................................................................................6
3.1. CHART PLATE SEAL ........................................................................................................................................ 6
3.2. SECURITY MODE SELECTION SHUNT............................................................................................................... 7
3.3. KEYPAD .......................................................................................................................................................... 8
4. USER DISPLAY....................................................................................................................................................9
4.1. SETTING CONTINUOUS DISPLAY................................................................................................................. 9
4.2. SETTING SEQUENCE DISPLAY...................................................................................................................... 9
5. PASTEURIZED MILK ORDINANCE (PMO) APPENDIX I TESTING......................................................10
5.1. AV-9900 TESTING QUICK REFERENCE ......................................................................................................... 10
5.2. METER BASED TIMING FUNCTION – CHART VERIFICATION .......................................................................... 11
5.3. TESTS 2 AND 4 - TEMPERATURE ACCURACY ................................................................................................. 13
5.3.1. Pen Calibration.......................................................................................................................................13
5.3.2. Two Point Element Calibration...............................................................................................................14
5.3.3. Chart Calibration....................................................................................................................................17
5.4. TEST 3 - TIME ACCURACY............................................................................................................................. 18
5.5. TEST 8 - THERMOMETRIC RESPONSE ............................................................................................................. 18
5.6. TEST 10 - MILK TEMPERATURE AT CUT-IN AND CUT-OUT ............................................................................ 18
5.7. TEST 11 – CONTINUOUS FLOW HOLDING TUBES – HOLDING TIME ............................................................... 19
5.7.1. LED Indicators for “Loss of Signal” and “High Flow” Alarms ............................................................19
5.7.2. Accessing Flow Alarm Setpoints .............................................................................................................21
5.7.3. Accessing Flow Controller Setpoint........................................................................................................22
5.7.4. Appendix I - Test 11.2A Mag Flow Meter Based Timing Systems Continuous Flow Holding Time......23
5.7.5. Appendix I - Test 11.2B Continuous Flow Holding Tubes – Flow alarm ...............................................23
5.7.6. Appendix I - Test 11.2C Continuous Flow Holding Tubes – Low Flow / Loss-of-Signal Alarm.............24
5.7.7. Appendix I - Test 11.2D Continuous Flow Holding Tubes – Flow Cut-In and Cut-Out........................24
5.7.8. Appendix I - Test 11.2E Continuous Flow Holding Tubes – Time Delay Relay.....................................25
5.8. TEST 15 – ELECTRO MAGNETIC INTERFERENCE FROM HAND-HELD COMMUNICATION DEVICES ................. 26
6. DEFAULT PARAMETER VERIFICATION...................................................................................................27
6.1. STLR FUNCTION SETUP ................................................................................................................................27
6.2. STLR RECORDER SETUP ............................................................................................................................... 30
6.3. CHART SETUP................................................................................................................................................ 34
7. RUN MODE PARAMETER CHANGES..........................................................................................................37
7.1. CHART KEY................................................................................................................................................... 37
7.2. DISPLAY KEY ................................................................................................................................................ 38
7.3. SCROLL KEY ................................................................................................................................................. 38

Document Revision 3.0 3
1. Introduction
The AV-9900 High Temperature Short Time Controller provides all USPHS required functions associated with
recording pasteurized product temperature, signaling the flow diversion valve (F.D.V.), and recording the Flow
Diversion Valve position. Additional features allow for multiple diversion set-points, recording active diversion
setpoint, cold product recording - with optional control, and hot water control.
The remainder of this publication will serve as further introduction to the features of the AV-9900, as well outlining
procedures necessary to perform the PMO Appendix I tests.

Document Revision 3.0 4
2. Key Product Features
The AV-9900 Microprocessor Based Safety Thermal Limit Recorder incorporates many time proven features found in
earlier Anderson products. Ease of operation and high safety standards were brought together specifically to meet the
demands of the pasteurization process. Key features of the AV-9900 are as follows:
2.1. Hot Product Temperature Sensor
The Hot Product Sensor is a dual element, 1000 ohm Resistance Temperature Detector (RTD). The Primary RTD
supplies the recording - thermal limit signal input, with the Secondary RTD supplying a verification for that signal.
Sensors are available with a wide variety of sanitary connections featuring a 5-1/2” or 7-1/4” probe length.
Provision for the
Health Authority Seal
on the stainless steel conduit housing provides separate servicing of the probe,
and ease of installation. Overall response characteristics allow for cable runs of up to 500 feet.
Chart ranges are programmable, and are factory set to meet all Pasteurized Milk Ordinance (PMO) requirements. In
addition, criteria of 12 hour rotation and 1OF divisions have been met.
2.2. Diversion Switching
Diversion set-point circuitry provides for up to five selectable cut-in/cut-out temperatures. User configurable
parameters exist for displaying the active set-point. The current set-point is recorded to the chart for verification at
time of cut-
in. Diversion set-point values are easily modifiable upon breaking the Health Authority Seal, and entering the system
program mode. In addition to restricting access to the Run/Program shunt jumper, the chart plate seal also prevents
modifications to circuit boards and input/output wiring connections.
Flow Diversion Valve position is indicated by red and green lights on the chart plate, in addition to being recorded by
an event pen on the outside area of the chart. The event pen position is outward for forward flow on all diversion set-
points. Selection of the current diversion set-point is accomplished via the front mounted user keypad and display.
Five function keys become active, allowing the user to choose the desired set-point.
2.3. Diagnostic Circuitry
The AV-9900 provides fail-safe operation via internal self-diagnostics of the Hot Product Probe input signals. The
Primary RTD input signal is continually referenced against the Secondary RTD signal. The result is indicated on a
series of LED’s, located just above the user display, and labeled
Sensor Balance
. If both RTD elements are in
agreement by less than .5 OF , no LED’s are lit. Each increment of .5OF shift will light an LED. At the point at which
the elements differ greater than 2OF , the AV-9900 will go into automatic divert. In addition, the user display will
indicate that a
Probe Failure
has taken place. Until a replacement Hot Product Probe is installed, the unit will not
allow a forward flow condition to take place.

Document Revision 3.0 5
2.4. Pen Drive Mechanism and Chart Printing
The pen drive mechanism is similar to a dot-matrix print device in that a series of dots are placed down onto the paper
chart. This mechanism is fully alpha-numeric capable, allowing printing of ranges, units, alarm’s, etc. to the chart. All
four pens are housed within a small pen cartridge, in a straight line arrangement. As a result, all data printed to the
chart is on the same time line. No lag exists from pen to pen as with typical felt pen type recorders. Chart ranges and
scales are factory programmed, per applicable PMO requirements, but may easily be re-ranged in the field. Charts are
plain paper, and pre-printed only with circular ring divisions. Division spacing meets PMO requirements. User
defined scales and chart ranges are printed in one of four available colors.
2.5. Cold Product Record - Control
The AV-9900 may be configured to receive an input from an RTD, or mA transmitter, measuring the Cold Product
temperature as it exits the pasteurization loop. This function may be specified at time of order, or upgraded in the field
at a later date. A factory set, field modifiable scale has been programmed for the recording pen. Data will be recorded
in color allowing easy interpretation when reviewing chart information.
An additional option exists for controlling the Cold Product Cooling within the AV-9900. An optional PID Loop
Control function can be specified at time of order, or upgraded at a later date in the field. This function will receive its
input from the same probe measuring the Cold Product temperature. In turn, a desired set-point may be programmed,
with output signals interfacing to the cooling loop. The PID, or control functions, will vary the resulting output signal
based on rising above or falling below the desired Cold Product set-point.
2.6. Hot Water Loop Control
The AV-9900 may be configured to receive an input from an RTD, or mA transmitter, measuring the Hot Water Loop
temperature. This function may be specified at time of order, or upgraded in the field at a later date. In turn, a desired
set-point may be programmed, with output signals interfacing to the Hot Water Loop. The PID, or control functions,
will vary the resulting output signal based on rising above or falling below the desired Hot Water set-point.
If various products are being processed, up to five Hot Water Controllers are available (one for each STLR diversion
set-point). Each controller may have it’s own set-point and PID tuning parameters. When the operator selects a new
STLR diversion set-point, the corresponding Hot Water Controller is automatically selected. Again, Hot Water
Control set-points and PID tuning parameters would have been pre-programmed

Document Revision 3.0 6
3. Hardware Descriptions
In performing the required testing, access will be made to various areas of the AV-9900 hardware. Specifics are
illustrated as follows:
3.1. Chart Plate Seal
Provisions have been provided for placing the Regulatory Wire Seal in the upper right corner of the chart plate. When
in place, this seal prevents unauthorized access to not only the internal wiring, but also access to the Security Mode
Shunt (see next section).
Posts For
Health Authority
Wire Seal

Document Revision 3.0 7
3.2. Security Mode Selection Shunt
The AV-9900 is equipped with a movable shunt to allow toggling between RUN and PROGRAM modes of operation.
While in RUN mode, access is prevented to all system critical parameters (ranges, setpoint changes, etc.). Changes
may be made to display functions as well as selection of the currently active diversion setpoint. While in PROGRAM
mode, full access to all system parameters is allowed.
NOTE:Moving the Security Mode Selection Shunt to the PROGRAM position will
immediately
force the unit to
DIVERT flow. If already in DIVERT flow, the unit will remain in that mode even if the hot product temperature rises
above the active setpoint.
The following diagram illustrates the location of the Security Mode Selection Shunt, in addition to the settings, RUN
or PROGRAM.

Document Revision 3.0 8
3.3. Keypad
Located on the front chart plate of the unit is the USER KEYPAD. From here, access to the program parameters can
be gained. A description of each of the keys is as follows:
õUP ARROW Used to move through menus, or increase a value
öDOWN ARROW Used to move through menus, or decrease a value
÷LEFT ARROW Used to move through menus or digits of a parameter
øSCROLL (RIGHT
ARROW) Used to move through menus or digits of a parameter
ùESCAPE Used to cancel a flashing program prompt
úRESET Jump from within programming menus to the standard
operating screen
ûDISPLAY While in display RUN mode allows access to STLR diversion
setpoints as well as display viewing option parameters
üMODIFY Allows changes to be made to a currently displayed parameter
ýCHART Allows access to the
Change Chart Routines
þENTER Locks in changes made to a parameter

Document Revision 3.0 9
4. User Display
Also located on the front chart plate is the User Display. From here, data such as a digital readout of the STLR
temperature value may be viewed. This display will be utilized in selected areas of the Pasteurized Milk Ordinance
Appendix I testing.
Two options exist for the display; CONTINUOUS DISPLAY and SEQUENCE DISPLAY. When in continuous
mode, the selected parameter is viewable at all times on the display. This is the required mode for completion of the
Appendix I testing. While in sequence mode, various parameters scroll over the screen at a timed interval.
If the unit is set to SEQUENCE display mode, the following procedure will allow the unit to be placed in continuous
mode, with the STLR temperature visible:
4.1. Setting CONTINUOUS Display
1. Operation may be done with Security Mode Shunt in either position - no
changes required.
2. Press ûkey twice - you will see:
3. Press the ökey once.
4. If CONTINUOUS is not already flashing, press the økey.
5. With CONTINUOUS flashing, press the þkey once.
6. Press the úkey once to return to the main display.
7. Press öuntil STLR INP is displayed - this is the digital display of Hot
Product Temperature.
8. You may now complete the required testing.
4.2. Setting SEQUENCE Display
1. To return the display to SEQUENCE mode, proceed as follows:
2. Operation may be done with Security Mode Shunt in either position - no
changes required.
3. Press ûkey twice - you will see:
4. Press the ökey once.
5. If SEQUENCE is not already flashing, press the økey.
6. With SEQUENCE flashing, press the þkey once.
7. Press the úkey once to return to the main display.
8. The unit is now back in standard operation.
MODIFY <->
DISPLAY PARAMETERS
MODIFY <->
DISPLAY PARAMETERS

Document Revision 3.0 10
5. Pasteurized Milk Ordinance (PMO) Appendix I Testing
This section will provide specific procedures regarding the completion of the PMO Appendix I tests. Only AV-9900
specific information has been provided. For a detailed listing of the actual testing procedure, please refer to the
Pasteurized Milk Ordinance, Appendix I.
5.1. AV-9900 Testing Quick Reference
Test Description Variance From Printed PMO Appendix I Test
2 Recording Thermometers – Temperature
Accuracy
Pen printing not instantaneous – utilize display for test
3 Recording Thermometers – Time Accuracy Test to be started when AV-9900 prints a Major (bold)
time line, and ended when thirty minute dashed line
printed
4 Recording Thermometers – Check Against
Indicating Thermometer
Pen printing not instantaneous – utilize display for test
8 Recorder/Controller – Thermometric Response Pen printing not instantaneous – utilize display for test
10.1 Milk-Flow Controls – Milk Temperature at
Cut-In and Cut-Out; HTST Pasteurizers
Pen printing not instantaneous – utilize display for test
10.2 Milk-Flow Controls – Milk Temperature at
Cut-In and Cut-Out; HHST Pasteurizers and
Aseptic Processing Systems Using Indirect
Heating
Pen printing not instantaneous – utilize display for test
10.3 Milk-Flow Controls – Milk Temperature at
Cut-In and Cut-Out; HHST Pasteurizers and
Aseptic Processing Systems Using Direct
Heating
Pen printing not instantaneous – utilize display for test
11.1 Continuous Flow Holding Tubes – Holding
Time – HTST Pasteurizers
None – complete test as documented
11.2-A Magnetic Flow Meter Based Timing Systems
Continuous Flow Holding Time
Pen printing not instantaneous – utilize display LEDs’
#1 and #2 for test
11.2-B Continuous Flow Holding Tubes – Flow alarm Flow rate must be adjusted to go past High Flow
Setpoint. Cannot adjust High Flow Setpoint in RUN
mode as required by standard PMO test.
11.2-C Continuous Flow Holding Tubes – Low Flow /
Loss-of-Signal Alarm
Pen printing not instantaneous – utilize display LEDs’
#1 and #2 for test
11.2-D Continuous Flow Holding Tubes – Flow Cut-
In and Cut-Out
Pen printing not instantaneous – utilize display LEDs’
#1 and #2 for test
11.2-E Continuous Flow Holding Tubes – Time
Delay Relay
Pen printing not instantaneous – utilize display LEDs’
#1 and #2 for test
15 Electro Magnetic Interference From Hand-
Held Communication Devices
None – complete test as documented

Document Revision 3.0 11
5.2. Meter Based Timing Function – Chart Verification
ó Prior to completing tests, a check should be made to verify that the chart is properly programmed to
show the FLOW portion on the first 40 units of the chart. This configuration is REQUIRED. Procedure is
as follows:
1. Unit MUST be in PROGRAM mode – see Section 3.2
2. Press the ø key until the display shows:
3. Press the ö key.
4. Press the ø key until the display shows:
5. Press the ö key.
6. Press the økey until the display shows:
7. Press þkey once.
8. Press the økey until the display shows:
9. Verify that DIVISION “0” is programmed.
10. Use the ükey along with õö keys to make a change if necessary.
11. Press the økey until the display shows:
12. Verify that DIVISION “40” is programmed.
13. Use the ükey along with õö keys to make a change if necessary.
14. Press the økey until the display shows:
15. Verify that VALUE “0” is programmed.
SELECT <->
CONFIGURATION
RECORDING FUNCTION
SFLR INPUT/EVENT
CONFIGURE <->
RECORDING PENS
SFLR INP ZONE LOW
DIVISION
X
SFLR INP ZONE HIGH
DIVISION
X
SFLR INP ZONE LOW
V
ALUE
X

Document Revision 3.0 12
16. Use the ükey along with õö keys to make a change if necessary.
17. Press the økey until the display shows:
18. Verify that VALUE equivalent to the full scale output of the Flow Meter is programmed.
19. An example would be a meter that outputs 4.00 mA at 0 GPM flowrate, and 20.00 mA at 464 GPM flowrate.
The proper value to be entered into the ZONE HIGH VALUE would be 464. This value may be obtained
from the individual that commissioned the flow meter.
20. Use the ükey along with õö keys to make a change if necessary.
21. Press the úkey to return to the main display.
Flow Scale Value equals
full scale
output of flow
meter
40th. Ring
0th. Ring
SFLR INP ZONE HIGH
V
ALUE
X

Document Revision 3.0 13
5.3. Tests 2 and 4 - Temperature Accuracy
The AV-9900 provides two means for calibrating the instrument to match the indicating (reference) thermometer.
Both procedures require the unit to be in PROGRAM MODE of operation.
ó Prior to completing tests, a check should be made to verify that PEN and DISPLAY are in
agreement. If any discrepancy is present, a CHART CALIBRATION should be completed. See section
5.2.3 for details on this procedure.
The first section describes a single point calibration to bring the pen AND display into agreement with the indicating
thermometer at or near the normal operating temperature. This adjustment is typically used to remove minor
discrepancies between the AV-9900 and the Reference Thermometer. It is also often used during initial startup to
offset the pen so it tracks slightly lower than the indicating thermometer (0.5OF typical).
The second section describes the Two Point Calibration procedure which mimics a complete “factory” calibration.
This procedure is typically performed at one year service intervals, or at the time of Hot Product Sensor replacement.
5.3.1. Pen Calibration
The AV-9900 allows for fine tuning of the Pen and Display. This will allow removal of minor discrepancies
between the 9900 and the reference thermometer. In addition, an offset (0.5OF typical) may be established so
that the 9900 will display and record slightly less than the indicating thermometer.
22. After testing the accuracy using the PMO procedure, any discrepancy between the AV-9900 RECORDING
PEN/DISPLAY, and the indicating thermometer, may be adjusted by the remainder of this procedure.
23. Unit MUST be in PROGRAM mode – see Section 3.2
24. Press the ø key until the display shows:
25. Press the ö key.
26. Press økey if STLR is not flashing (Multiple function units only – Skip if ONLY STLR shows on the
display)
27. Press the þkey once.
28. Press the økey until the display shows:
29.
30. Press ükey once.
31. Cursor will appear under left most numeral.
SELECT <->
FUNCTION SETUP
STLR INP CORRECTION
.0 OF
(
or C
)

Document Revision 3.0 14
32. Use õö keys to make a change - this is desired amount of correction to the PEN.
33. When adjustment is complete, press the þkey once.
34. Press the úkey to return to the main display.
35. If the unit has been moved from SEQUENCE display to CONTINUOUS display for this test, it may be reset
at this point.
36. Follow standard temperature test practices to verify adjustments.
5.3.2. Two Point Element Calibration
The following procedure will allow the STLR Hot Product Input Sensor to be calibrated in accordance with
the verified indicating thermometer. This procedure will also allow the dual 1000 ohm STLR sensor input to
be properly balanced. During this test, we will be concerned with the temperature being shown on the AV-
9900 DISPLAY ONLY.
1. As described in section 4.1, the AV-9900 display should now be in CONTINUOUS DISPLAY mode,
and showing the STLR INP value (Hot product temperature)
2. After testing the accuracy using the PMO procedure, any discrepancy between the AV-9900 STLR INP
value shown on the display, and the indicating thermometer, may be adjusted by the remainder of this
procedure.
3. Break chart plate seal to gain access to internal wiring (Section 3.1).
4. Using Section 3.2 as a reference, locate the Security Mode Shunt on the HTST termination board.
5. Place the security shunt in the program position.
6. Press økey until FUNCTION SETUP is visible on front display.
7. Press ökey once.
8. Press økey until STLR is FLASHING on display.
9. Press þkey once.
10. Press økey until INPUT DISPLAY BOTH – NO is visible on display.
11. Press ükey once.
12. Press økey until YES is FLASHING on display.
13. Press þkey once.
14. Press õ key until STLR INP 1 and STLR INP 2 are both visible on display.

Document Revision 3.0 15
15. Recommended calibration temperatures for 120OF to 220OF chart would be 150OF for low end bath, and
at least as high as high diversion setpoint for high end bath.
16. Place Indicating Thermometer, Verified Reference Thermometer, and STLR probe in regulated low end
bath.
17. Verify that Indicating Thermometer matches Reference Thermometer.
18. Via display on front of AV-9900, note STLR INP 1 and STLR INP 2 temperature readings.
19. If an adjustment is needed to either STLR INP 1 or STLR INP 2 temperatures, proceed as follows. If Ok,
move to high end bath (step 37) and repeat test.
20. Press økey until CONFIGURATION is visible on front display.
21. Press ökey once.
22. Press økey until INPUTS is visible on front display.
23. Press ökey once.
24. Press økey until STLR is FLASHING on front display.
25. Press þkey once.
26. Press økey until the following is visible on display:
27. Use following example to determine change:
Reference indicates 150OF at actual 150OF
AV-9900 indicates 151OF at actual 150OF
Correction will be: -1.0 AT 151.0
28. Press ükey once.
29. Cursor will appear under left most numeral.
30. Use õö keys to make a change - this is desired amount of correction.
(-1.0 for example)
31. Hit þkey once.
32. Use õö keys to make a change - this is desired point at which to make correction. (151.0 for
example)
33. Hit þkey once.
STLR INPUT 1 CORR 1
.0 AT .0

Document Revision 3.0 16
34. Press økey until the following is visible on display:
35. Follow steps 28 through 33, entering the necessary correction values for STLR INP 2.
36. Hit úkey once.
37. Raise bath temperature to high end.
38. Via display on front of AV-9900, note STLR INP 1 & 2 temperature readings.
39. If an adjustment is needed to either STLR INP 1 or STLR INP 2 temperatures, proceed as follows. If
Ok, move to step 56.
40. Press økey until CONFIGURATION is visible on front display.
41. Press ökey once.
42. Press økey until INPUTS is visible on front display.
43. Press ökey once.
44. Press økey until STLR is FLASHING on front display.
45. Press þkey once.
46. Press økey until the following is visible on display:
47. Use following example to determine change:
Reference indicates 200.0OF at actual 200.0OF
AV-9900 indicates 200.5OF at actual 200.0OF
Correction will be: -.5 AT 200.5
48. Press ükey once.
49. Cursor will appear under left most numeral.
50. Use õö keys to make a change - this is desired amount of correction. (-.5 for example)
51. Hit þkey once.
STLR INPUT 1 CORR 2
.0 AT 100.0
STLR INPUT 2 CORR 1
.0 AT .0

Document Revision 3.0 17
52. Use õö keys to make a change - this is desired point at which to make correction. (200.5 for
example)
53. Hit þkey once.
54. Press økey until the following is visible on display:
55. Follow steps 48 through 53, entering the necessary correction values for STLR INP 2.
56. Hit úkey once.
57. Two point calibration is now complete. The unit calibration may be verified via temperature bath testing,
with additional correction made if required.
5.3.3. Chart Calibration
1. Unit MUST be in PROGRAM mode – see Section 3.2
2. Press the ø key until the display shows:
3. Press the ö key.
4. Press the ø key until the display shows:
5. Press the ö key.
6. Press ükey once.
7. Press the function key under YES to start chart calibration – be sure a paper chart is in proper recording
position.
8. Press the ýkey “3” times – a dot will be printed near the innermost ring of the chart. If the dot is NOT
directly on the FIRST chart ring, use the õö to make a change in position.
STLR INPUT 2 CORR 2
.0 AT 100.0
SELECT <->
CALIBRATION
CALIBRATION <->
CHART CALIBRATION

Document Revision 3.0 18
9. Once properly aligned to the innermost ring, press the ø key ONCE to begin calibrating the outer pen
position. Press the ýkey once to print a dot near the outer most ring. If the dot is NOT directly on the
100th chart ring, use the õö to make a change in position.
10. Once complete, press þkey once to save new calibration.
5.4. Test 3 - Time Accuracy
With the unit in RUN mode and while the chart is printing, use an accurate watch to test for time accuracy as follows:
1. Begin timing when the unit prints a MAJOR TIME LINE (solid color).
2. Stop timing when the mechanism prints the SECOND minor time line (second dotted line). The
elapsed time should be 30 minutes.
5.5. Test 8 - Thermometric Response
The standard testing procedure, as described in the Pasteurized Milk Ordinance, may be used with the exception that
the display must be utilized to start the stopwatch at the proper temperature. If the display is currently set to
SEQUENCE mode, refer to section 4 to place the display into CONTINUOUS mode.
The display will now show the current STLR INP temperature (hot product temperature), as well as the an indication
that the unit is above or below the diversion setpoint STLR OUT (OFF or ON).
To properly test for response time, simply start the stopwatch when the display reads a temperature 12 degrees below
the cut-in temperature. If the display moves to quickly or skips over the desired start temperature, you may start the
watch at a temperature 2-3 degrees below the desired temperature. The resulting test data should still be well within
the 5 second maximum. Stop the watch when the display changes from:
STLR OUT OFF to STLR OUT ON
5.6. Test 10 - Milk Temperature at Cut-in and Cut-out
The standard testing procedure, as described in the Pasteurized Milk Ordinance, may be used with the exception that
the display must be utilized to verify the proper cut-in / cut-out temperature.
To select a new pre-programmed diversion setpoint, proceed as follows:
1. From the main display, press the ûkey once.
2. All currently programmed diversion setpoints will now be displayed.
3. Each value will be above a FUNCTION KEY.
4. Press the key just under the desired value to activate the new diversion setpoint.

Document Revision 3.0 19
If a change is required to the Cut-out temperature or to the amount of dead-band between Cut-in and Cut-out,
proceed as follows:
1. Be sure that the unit is in PROGRAM MODE (Section 3.2).
2. Press the økey until the display shows:
3. Press the ökey once.
4. If STLR is not already flashing, press the økey (Multiple function units only – Skip if STLR only showing).
5. Press the þkey once.
6. Press the økey until the desired diversion setpoint is visible.
7. If you pass by the setpoint, use the ÷key to move backward.
8. Using the keys øand ÷you can view each of the diversion setpoints, and their associated dead-band value.
9. To modify a value, press the ükey once.
10. Use the õö keys to make the change.
11. Press the þkey when satisfied with the change.
12. When done making changes, press the úkey to return to the main display.
5.7. Test 11 – Continuous Flow Holding Tubes – Holding Time
PMO test 11 covers methods used to determine hold time of various system configurations. For AV-9900 systems
integrating the Safety Flow Limit Record function (Meter Based Timing), additional details have been provided to
assist in completing the required testing.
5.7.1. LED Indicators for “Loss of Signal” and “High Flow” Alarms
For AV-9900 systems integrating the SFLR function, mechanical relays have been interfaced with the Flow
Diversion Device control unit. As the AV-9900 even pen printing is not “real time” print, LED indicators
have been provided to give instantaneous feedback as to the position of the Loss of Signal and High Flow
alarm and associated relay position. They are located above the main user display, and are set as follows:
LED Number 1 – Tied to Loss of Signal (Low Flow) alarm / relay point
LED Number 2 – Tied to High Flow alarm / relay point
Prior to completing tests in this section, proper programming of the LED’s will need to be verified. Complete
procedure is as follows:
1. AV-9900 will need to be in PROGRAM mode – see Section 3.2 of this publication.
2. Press the økey until display shows:
3. Press the ökey once.
SELECT <->
CONTROLLER SETUP
SELECT <->
CONFIGURATION

Document Revision 3.0 20
4. Press the økey until display shows:
5. Press the ökey once.
6. Press the økey until display shows:
7. If display does not show “SFLR ALARM 1,” setting is incorrect. Use the üand õö
arrow keys to make necessary changes; þkey to accept change
8. Press the økey until display shows:
9. If display does not show “SFLR ALARM 2,” setting is incorrect. Use the üand õö
arrow keys to make necessary changes; þkey to accept change
10. When done making changes, press the úkey to return to the main display.
As indicated, the LED’s are tied directly to the action of the Loss of Signal and High Flow alarms and relays. The
following illustration shows proper operation of the flow alarms:
CONFIGURE <->
LEDS
LED 1 ACTUATOR <->
SFLR ALARM 1
LED 2 ACTUATOR <->
SFLR ALARM 2
100%
Loss of Signal = 5%
High Flow = 60%
Event Pen Inward
Event Pen Outward
LED 1 and 2 LIT
Active Below Relay Action
Active Above Relay Action
LED 1 LIT, LED 2 OUT
LED 1 OUT, LED 2 LIT
Table of contents
Other Anderson Controllers manuals
Popular Controllers manuals by other brands
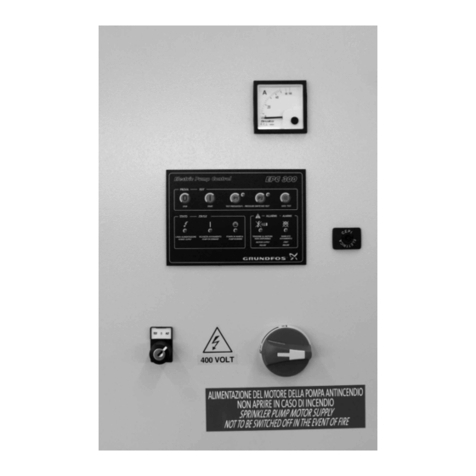
Grundfos
Grundfos EPC 300 Installation and operating instructions
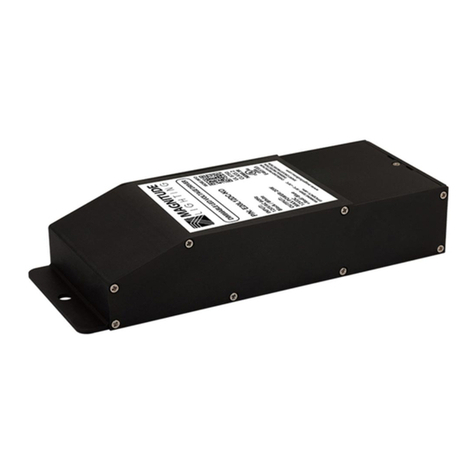
MAGNITUDE LIGHTING
MAGNITUDE LIGHTING E Series installation guide
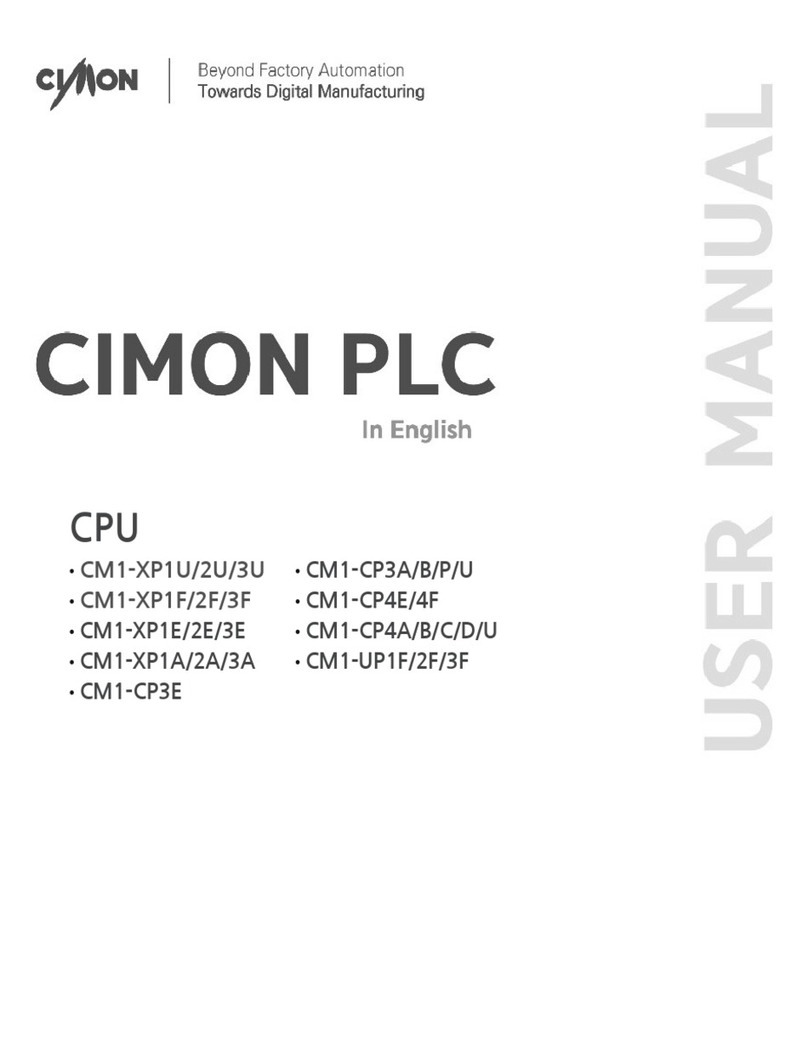
Cimon
Cimon CM1-XP1U user manual
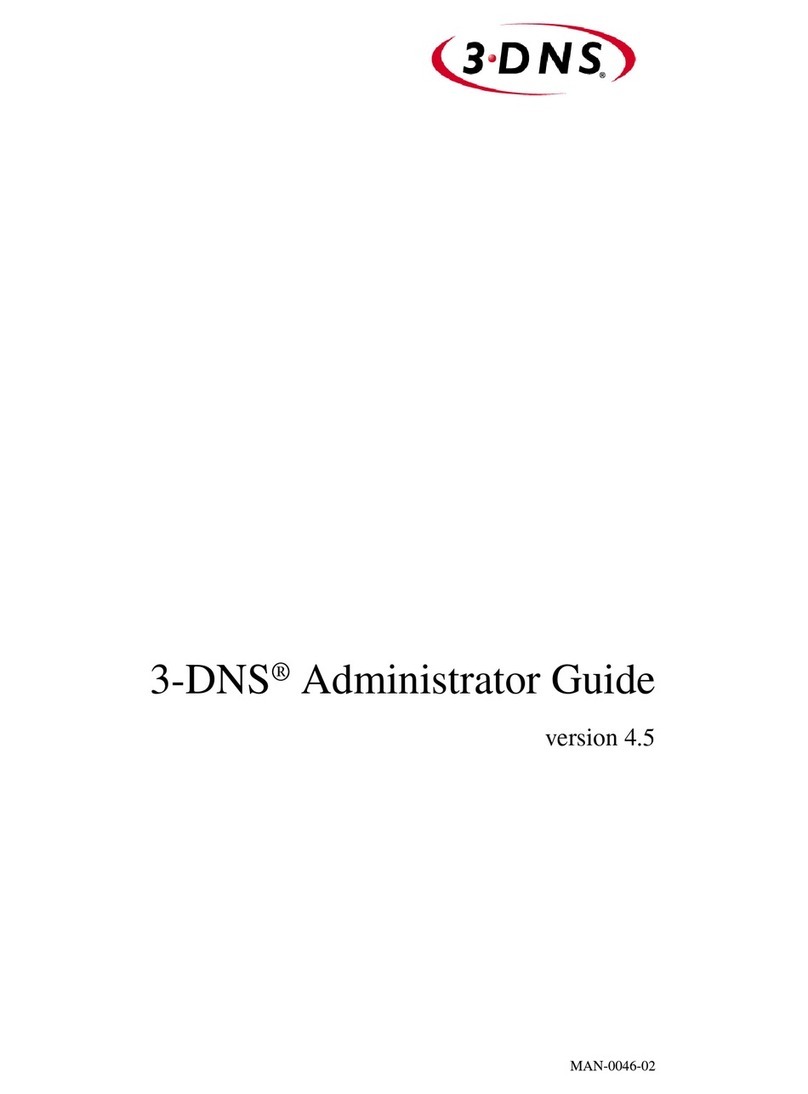
Dell
Dell 3-DNS Administrator's guide
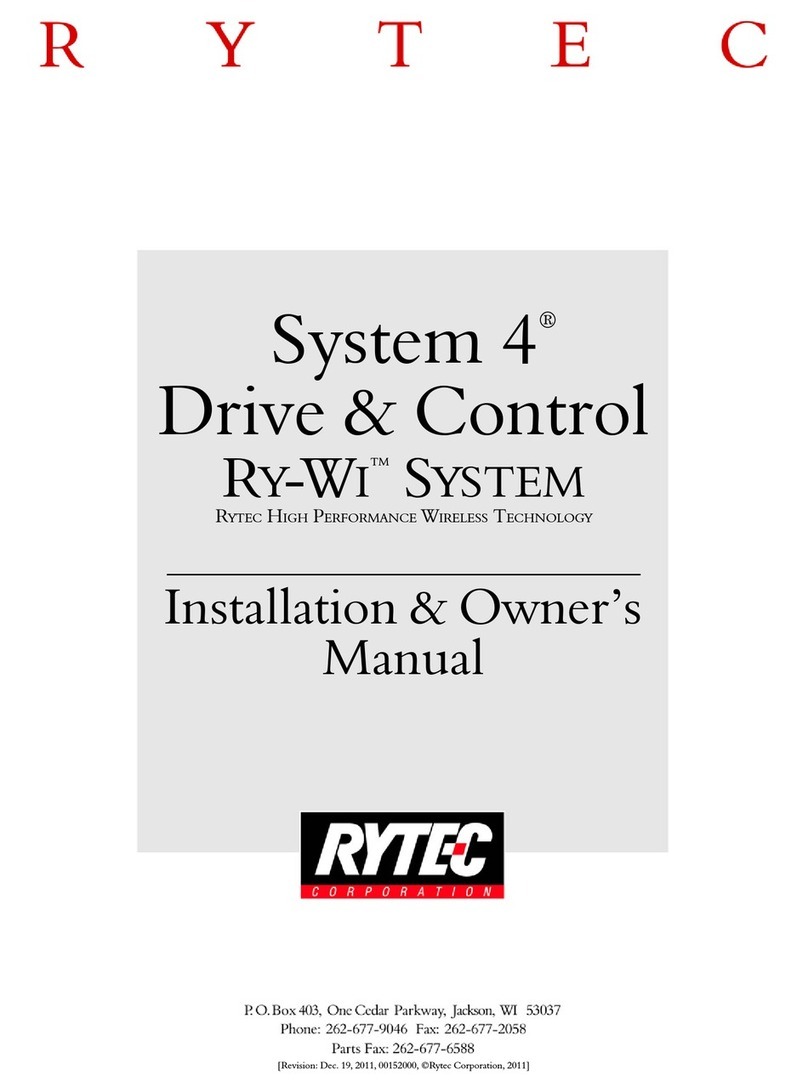
RYTEC
RYTEC System 4 Installation & owner's manual

Mitsubishi
Mitsubishi FX3U-485ADP(-MB) installation manual