Ansul Checkfire MP-N Installation instructions

002750
CHECKFIRE MP-N ELECTRIC
DETECTION & ACTUATION SYSTEM
Installation, Recharge, Inspection, and Maintenance Manual

This manual is intended for use with the CHECKFIRE MP-N (Mine
Permissible) Electric Detection and Actuation System.
Those who install, operate, inspect, or maintain this system
should read this entire manual. Specific sections will be of par-
ticular interest depending upon oneʼs responsibilities.
As with all electro-mechanical equipment, the electric detection
and actuation system needs periodic care to provide maximum
assurance that it will operate effectively and safely. Inspection
frequency shall be performed monthly, or sooner, depending on
operating and/or environmental conditions. Maintenance shall be
performed semi-annually, or sooner, depending on operating
and/or environmental conditions.
The application and use of the CHECKFIRE MP-N system is
limited to the application and uses described in this manual. For
other applications, contact your local authorized ANSUL distribu-
tor or the ANSUL technical representative in your area.
Note: The converted metric values in this document are provided
for dimensional reference only and do not reflect an actual
measurement.
ANSUL, CHECKFIRE, and the product names listed in this material are marks and/or registered
marks. Unauthorized use is strictly prohibited.

CHECKFIRE MP-N Electric
Detection and Actuation System Manual
REVISION RECORD
2012-MAY-18
2012-MAY-18 Complete manual has 02
been reformatted and
renumbered as Page 1
was deleted. All pages
have been changed to
Rev. 02 regardless of
previous revision number.
Revision indicators (䊳)
mark current technical
revisions only.
DATE PAGE REV. NO. DATE PAGE REV. NO.
Indicates revised information.


TABLE OF CONTENTS
2012-MAY-18 REV.02 PAGE i
CHECKFIRE MP-N Electric
Detection and Actuation System Manual
SECTION PAGES
TOTAL SYSTEM DESCRIPTION 1 – 2
SYSTEM COMPONENTS 3 – 6
Control Module 3
Manual and Automatic Actuators 3
LT-10-R Cartridge 4
Mounting Brackets 4
Linear Detection Wire 4
Thermal Spot Detector 4
Pneumatic/Linear Detector 5
Battery 5
End-of-Line Resistor 5
Check Valve 5
Release Circuit Test Module 6
Splicing Device 6
Extender Cable Assembly/Battery Extender 6
Cable Assembly
RS-232 PC Interface Cable Kit 6
USER INTERFACE 7 – 9
Field Terminations 7
Front Panel Indicators 8
Front Panel Buttons 9
Battery Connection 9
Battery Replacement 9
Enclosure 9
Cover Removal 9
Strain Relief Installation 9
Mounting 9
SYSTEM PLANNING 10 – 11
Hazard Identification 10
Pre-installation Guidelines 10 – 11
INSTALLATION 12 – 24
Installation Materials 12
Mounting Bracket Installation 12
Mounting to Existing CHECKFIRE MP Bracket 13
Manual Actuator Installation 13
Mounting the Control Module 14
Gas Motor Actuator Assembly 14
Control Module Wiring/Detection Wire Routing 14 – 18
Thermal Detector Installation 16 – 17
Pneumatic/Linear Detector Installation 18
Initiating Input/Pressure Switch Input Circuit No. 2 18
Release Circuit Lead Connector 19
New Battery Installation 19 – 21
Function Test 21 – 22
Placing the System in Service 23 – 24
IN CASE OF FIRE 25
RECHARGE 26
SECTION PAGES
INSPECTION AND MAINTENANCE 27 – 28
Daily Inspections 27
Maintenance 27 – 28
TROUBLESHOOTING 29 – 31
Diagnostics 29
History Buffer 29
Troubleshooting Table 30 – 31
PROGRAMMING 32 – 35
PC Programming 33
Explaining the Menu 33 – 35
APPENDIX 36
Release Circuit Test Module Instructions 36
Component Index 37
Component Dimensions 38 – 39
Detection Wire Fluid Resistance Capability 40

Explanation of safety alerts:
Indicates a hazardous situation in which a person will
experience serious personal injury or death if the situation is
not avoided.
Indicates a hazardous situation in which a person could
experience serious personal injury or death if the situation is
not avoided.
Indicates a hazardous situation in which a person could
experience minor or moderate personal injury if the situation
is not avoided.
Addresses practices not related to personal injury, such as a
system part malfunctioning, property damage, or system failure.
NOTICE
Addresses general practices or observations
related to system function that are not related
to personal injury.
䊱
!DANGER
!WARNING
!CAUTION
CAUTION
EXPLANATION OF SAFETY ALERTS
PAGE ii REV.02 2012-MAY-18
CHECKFIRE MP-N Electric
Detection and Actuation System Manual

TOTAL SYSTEM DESCRIPTION
2012-MAY-18 REV.02 PAGE 1
CHECKFIRE MP-N Electric
Detection and Actuation System Manual
FIGURE 1
003901
4
10
2
7
9
9
1
10
3
3
5
6
12
8
8
TYPICAL SYSTEM
TOTAL SYSTEM DESCRIPTION
The fire detection/suppression package is designed and approved
for use in mining vehicles, including those that operate in an explo-
sive methane/air atmosphere.
The CHECKFIRE MP-N Electric Detection and Actuation System,
FM Approval No. 3036795, is a modified version of the FM
approved SC-N Electric Detection and Actuation System, FM
approval No. J.I.0B8A8. The modification has been done to meet
the intrinsically safe requirements of MSHA.
Modification includes the addition of intrinsically safe circuitry to
the battery assembly and the main control board.
Due to the inability to make intrinsically safe wiring connections,
trouble and alarm relay contacts normally provided with the
CHECKFIRE SC-N control module have been removed on the
CHECKFIRE MP-N control module.
The complete CHECKFIRE MP-N system is composed of compo-
nents which are combined to provide automatic fire detection and
actuation for equipment hazard areas. The electric detection and
actuation system is designed for use only with ANSUL fire
suppression systems requiring pneumatic input as a means of
actuation.
The CHECKFIRE MP-N system is typically used with an ANSUL
A-101 Vehicle Fire Suppression system for 24-hour protection of
equipment. The system is particularly suited for the protection of
mining equipment that is subjected to extreme environmental and
physical conditions.
Some of its features include linear (wire) and/or spot (thermal)
detection, supervised circuitry, internally powered, adjustable
shutdown and discharge time delays, and auxiliary shutdown
relay.
CHECKFIRE MP-N Electric Detection and Actuation System
consists of the following components:
1. Control Module
2. Manual/Automatic Actuator
3. Mounting Bracket
4. Detection Wire
5. Thermal Detectors
6. Pneumatic/Linear Detection
7. Gas Motor
8. LT-10-R Cartridge
9. Check Valve
10. MSHA Approved Pressure Switch (by others) or pneumatic
shutdown device
11. Gas Motor Circuit Test Module (not shown)
12. Automatic Actuator
The control module is a self contained system, powered by its own
internal lithium battery. This allows the detection system to operate
around-the-clock without use of external power.
The control module may be installed where the ambient tempera-
ture is between –40 °F to 140 °F (–40 °C to 60 °C).
The CHECKFIRE MP-N Detection and Actuation System is
approved by MSHA for permissible applications in an explosive
methane/air atmosphere.

TOTAL SYSTEM DESCRIPTION (Continued)
Circuits
The first initiating circuit is the supervised detection circuit
designed to be connected to linear (wire), linear pneumatic, and/or
spot type thermal detectors that provide a contact closure input to
initiate a fire detected condition. The second initiating circuit is
designed to accept a contact closure type of actuating device such
as an electric manual pull station or a pressure switch. The initiat-
ing circuits are low impedance and designed to eliminate nuisance
alarms associated with contact bounce.
Two field programmable time delays provide timing of shutdown
and release functions associated with the operation of the detec-
tion initiating circuit No. 1 and initiating circuit No. 2.
NOTICE
If factory preset time delay periods are to be
extended, consider the lag time between fire
ignition and automatic initiation when using
thermal detection. Consequently, extending
one or more time delay periods will likely
extend the fire burn time.
• DETECTION INITIATING CIRCUIT NO. 1
The detection circuit consists of two time delays:
The first time delay is field programmed to assign the time
between alarm (initiation of the detection circuit) and the opera-
tion of the shutdown relay. The first time delay is field program-
mable for 5, 10, 20, or 30 seconds.
The second time delay is field programmed to assign the time
between the completion of the first time delay (when the shut-
down relay operates) and the operation of the release circuit.
The second time delay is field programmable for 0, 10, 20, or 30
seconds.
• INITIATING CIRCUIT NO. 2
The second input circuit (terminals 5 and 6) is field programma-
ble to be used as either an initiating input circuit to cause a
release output or as a pressure switch feedback input circuit
which will sound alarms and transfer the shutdown relay, but will
not cause a release output. If selected as an initiating circuit to
cause a release, its operation will override the first time delay
function and initiate a second time delay condition, causing the
shutdown relay to immediately operate and system release to
occur upon completion of the second time delay. When the
second input circuit is used as an initiating input circuit to cause
a release, the timing cycle of the second time delay can be
adjusted in steps from 0 to 30 seconds. However, the settings
of time delay 2 on initiating circuit No. 2 can never exceed the
settings of time delay 2 on initiating circuit No. 1.
Selection of the second initiating circuit as a pressure switch
feedback circuit will result in the operation of the alarm relay and
shutdown relay immediately upon receiving the signal. The
release circuit will not be initiated from this feedback circuit.
When the pressure switch feedback input circuit has operated,
the Alarm and Release LEDʼs, along with the audio sounder, will
pulse for 30 seconds at a fast rate and thereafter at a slow rate
until the pressure switch is reset and then the control module is
reset.
• A “DELAY” option is available for the operators use. Operation
of the “DELAY” button will restart the first time delay cycle if initi-
ated while the first time delay is active. Once the second time
delay has started, operation of the “DELAY” button has no
affect.
• The shutdown relay will operate after the first time delay cycle
or immediately upon actuation of the pressure switch feedback
circuit.
This relay can be used for vehicle shutdown or remote alarm
initiating.
TOTAL SYSTEM DESCRIPTION
PAGE 2 REV. 02 2012-MAY-18
CHECKFIRE MP-N Electric
Detection and Actuation System Manual

SYSTEM COMPONENTS
2012-MAY-18 REV.02 PAGE 3
CHECKFIRE MP-N Electric
Detection and Actuation System Manual
CONTROL MODULE
The Control Module, Part No. 427300, is the basis of the
CHECKFIRE MP-N detection system. The module cover and back
box is made of durable Noryl SE1gfN3 material with a flammability
rating of UL94 V-1. The back box contains the field interface termi-
nal block, battery, and field wiring entrance ports. The cover
assembly contains the control PC board assembly, sounder, oper-
ator interface panel, and environmental seal. The enclosure meets
International Standard IEC 529 requirements for dust and water
spray in all directions. Mounting pads allow mounting to any suit-
able flat surfaces. Steel mounting brackets are also available.
All circuitry, relays, switches, and LEDʼs are contained on a single
PC board. A board mounted receptacle mates with the plug-in
terminal block mounted in the back box. A high pitch sounder is
threaded into the cover and plugged into the PC board. The PC
board is encapsulated to provide added protection against mois-
ture and dust. An RS232 interface cable connector is provided for
field programming from a PC and for data retrieval from a trouble
and alarm history buffer. The PC board assembly contains a DIP
switch for optional manual programming functions without the use
of a PC. See Figure 2.
When installed in an area that is classified as hazardous in
accordance with the NEC Article 500, only equipment that has
been approved for use in those areas can be used. This require-
ment applies to programming equipment such as PCs that may
be used to program the CHECKFIRE MP-N.
FIGURE 2
002755
MANUAL AND AUTOMATIC ACTUATORS
The MSHA CHECKFIRE MP-N system is equipped with both
manual and automatic agent release devices.
Manual Actuator
A 1/4 in. NPT street elbow is supplied with the actuator for conve-
nient connection of the 1/4 in. actuation line to the fire suppression
system.
The manual actuator is designed with a RED palm button which is
attached to a cartridge seal piercing pin and a ring pin to guard
against accidentally piercing the cartridge seal. To initiate agent
release, the operator must pull out the ring pin and strike the RED
palm button. The manual actuator must be located near the oper-
atorʼs control station. See Figure 3.
PART NO. 416792
FIGURE 3
003912
Automatic Actuator
The MSHA CHECKFIRE MP-N controller is provided with an agent
release output which automatically and electrically actuates a gas
motor as a result of a detected fire condition.
Automatic actuation is accomplished using the gas motor to pierce
the seal of a nitrogen cartridge. The gas motor is made up of a
miniature gas cylinder with piston and rod, a chemical charge and
an electrical heating element.
When the heating element is energized by a small current from the
control module, the chemical charge is ignited, generating a gas
which drives the piston and rod outward. The gas produced by
ignition also locks the piston and rod in the outward position.
The piston rod pushes the cartridge seal puncture pin through the
cartridge seal to release the high pressure cartridge gas. The
release of the cartridges gas in turn pressurizes the agent tank
which causes agent release.
The gas motor must be replaced with gas motor replacement ship-
ping assembly, Part No. 416756, after firing.
The gas motor actuator, Part No. 416735, can be installed
remotely from the operatorʼs control station. See Figure 4.
PART NO. 416735
FIGURE 4
003913
!CAUTION
RING PIN
1/4 IN. NPT
STRIKE
BUTTON
GAS MOTOR
ACTUATOR
1/4 IN. NPT

LT-10-R CARTRIDGE
The LT-10-R cartridge (Figure 5) is a pressure vessel that is
factory-filled with nitrogen to 1800 psi at 70 °F (12400 kPa at 21
°C). The cartridge provides the pressure required to actuate the
connected fire suppression system. Following operation, the
cartridge must be replaced.
PART NO. 423423
FIGURE 5
000851
MOUNTING BRACKETS
The CHECKFIRE MP-N Detection and Actuation System offers
three types of steel mounting brackets.
The first type, Part No. 423525, is a combined bracket for mount-
ing the control module and the pneumatic actuator together. See
Figure 6.
The second type, Part No. 423528, is an individual bracket for
mounting the control module separate from the pneumatic actua-
tor. Note: When ordering this bracket, it is also necessary to order
the pneumatic actuator bracket, Part No. 416828. See Figure 6.
The third type, Part No. 423531, is a retrofit bracket for mounting
an MP-N module to any existing CHECKFIRE MP bracket.
All brackets can be fastened by either bolting or welding. Brackets
are painted with red enamel paint.
COMBINED BRACKET RETROFIT BRACKET
PART NO. 423525 PART NO. 423531
002756 002757
MODULE BRACKET ACTUATOR BRACKET
PART NO. 423528 PART NO. 416828
002758 008213
FIGURE 6
LINEAR DETECTION WIRE
The linear detection wire consists of two spring steel conductors
which are separated by a heat-sensitive insulator. At the tempera-
ture rating of the wire, 356 °F (180 °C), the insulator melts, allow-
ing the two conductors to make contact. This contact provides
electrical continuity between the two conductors. The linear detec-
tion wire is supplied in lengths of 100 ft. (30.5 m), Part No. 71230,
or 500 ft. (152.4 m), Part No. 71231, and must be ordered sepa-
rately. See Figure 7.
FIGURE 7
000855
THERMAL SPOT DETECTOR
Thermal detectors are normally open, contact closure devices.
The fixed temperature design of these detectors will cause the
contacts to close when the temperature of the surrounding air
reaches the set point temperature of the detector. See Figure 8.
FIGURE 8
000856
Thermal detectors are available in three preset temperatures as
shown below. Each temperature rating is stamped on the detector.
Rated Maximum
Operating Continuous
Temperature Use Temperature Detector
°F (°C) °F (°C) Color Part No.
270 (132) 234 (112) Blue 416218
325 (163) 280 (137) Red 416219
360 (182) 312 (155) Red 416220
SYSTEM COMPONENTS
PAGE 4 REV. 02 2012-MAY-18
CHECKFIRE MP-N Electric
Detection and Actuation System Manual
SPOT
DETECTOR
CABLE CLAMP
WITHOUT PROTECTIVE
TUBING, PART NO.
416762
CABLE CLAMP WITH
PROTECTIVE TUBING,
PART NO. 416214
MOUNTING
BRACKET,
PART NO.
416221
SAFETY
SHIPPING CAP
CARTRIDGE INSULATED
SPRING STEEL
CONDUCTORS

PNEUMATIC/LINEAR DETECTOR
The pneumatic/linear detector, Part No. 416113, consists of 35 ft
(10.7 m) of gas filled stainless steel tubing connected to a small
pressure responder. When the gas in the tubing heats up, the
increase in pressure operates the responder, thus closing the
detection circuit of the control module. The pneumatic/linear
detector will operate at a temperature of 900 °F (482 °C) over
12 in. (31 cm) or 300 °F (149 °C) over the total length. The detec-
tor assembly connects to the control module by means of a
special wire assembly which is supplied with the detector assem-
bly. See Figure 9.
FIGURE 9
000857
BATTERY
The CHECKFIRE MP-N control module uses one 3.6 VDC lithium
battery, Part No. 427308. All power required to run the detection
system can be provided from this battery. The battery is supplied
with two separate plug-in connectors. One connector is used for
plugging into MP-N modules and the other connector is used for
plugging into SC-N modules. CAUTION: Do not cut off unused
connector assembly. It must remain on battery module even
though it is not used. Simply tuck the extra connector assembly
along side the battery module when installing the cover. The
battery must be replaced annually, after discharge, or when the
YELLOW Battery LED and the Audio Alarm are pulsing. Refer to
Installation Section (page 19), New Battery Installation, for proper
battery replacement procedures. See Figure 10.
FIGURE 10
004877
END-OF-LINE RESISTOR
The End-Of-Line Resistor Assembly, Part No. 426520, is required
for supervision of the external input circuits. The end-of-line resis-
tor assembly is available in a package of 10, Part No. 426461.
Each package consists of 10 of the required components to
assemble 10 of the resistor assemblies. See Figure 11. The
package contains an instruction sheet, Part No. 423542, detailing
the assembly requirements.
FIGURE 11
003050
CHECK VALVE
The 1/4 in. check valve, Part No. 25627, is installed in the actua-
tion line between the manual/automatic actuator and the pneu-
matic actuator on the connected fire suppression system. This
check valve allows actuation pressure to flow to the fire suppres-
sion system, but does not allow pressure from other actuation
devices to back up into the manual/automatic actuator of the
CHECKFIRE MP-N system. See Figure 12.
Other actuation devices in the fire suppression system also
require check valves to be installed in the same fashion. This
prevents pressure from escaping through an actuator whose
cartridge was inadvertently removed.
FIGURE 12
000899
SYSTEM COMPONENTS
2012-MAY-18 REV.02 PAGE 5
CHECKFIRE MP-N Electric
Detection and Actuation System Manual
1 5/8 IN.
(4.1 cm)
1/4 IN. NPT
(BOTH ENDS)
DETECTOR
TUBE
CONNECTION TO
CONTROL MODULE
RESPONDER
LOCK
NUT
STRAIN RELIEF
CONNECTOR
CAP
TERMINAL BLOCK
WITH 4.7 K OHM
RESISTOR
SC-N
CONNECTOR
MP-N
CONNECTOR
NOTE: DO NOT CUT OFF
UNUSED WIRE
ASSEMBLY

RELEASE CIRCUIT TEST MODULE
The release circuit test module, Part No. 423541, is used in place of
the gas motor during test procedures to simulate squib actuation or
gas motor actuation on CHECKFIRE MP-N systems (indicator lamp
on). It is also used when verifying time delay durations. See Figure
13.
FIGURE 13
003015
SPLICING DEVICE
The In-Line Splice Kit, Part No. 428375, is required for detection
wire connection between the control module and the linear detec-
tion wire or between separate pieces of linear detection cable.
When the splicing device is used in the system, it is recommended
to fill the splice body, Part No. 426783, with a high grade of sili-
cone sealant (Dow Corning 737 or equal) to make a proper seal.
The kit consists of the necessary number of components to
assemble 10 complete assemblies. See Figure 14.
FIGURE 14
007045
EXTENDER CABLE ASSEMBLY/BATTERY EXTENDER
CABLE ASSEMBLY
The Extender Cable Assembly, Part No. 426601, is used to
conduct functional tests. It, along with the Battery Extender Cable,
Part No. 428042, allows separation of the cover from the enclo-
sure while maintaining circuit integrity. See Figure 15.
FIGURE 15
002978
RS232 PC INTERFACE CABLE KIT
The RS232 PC Interface Cable Kit, Part No. 423524, is required
to field program the MP-N module. The kit contains the cable
assembly and programming disc.
SYSTEM COMPONENTS
PAGE 6 REV. 02 2012-MAY-18
CHECKFIRE MP-N Electric
Detection and Actuation System Manual
EXTENDER
TEST CABLE,
PART NO. 426601
EXTENDER
BATTERY CABLE,
PART NO. 428042
LINEAR
DETECTION
WIRE
STRAIN RELIEF,
PART NO. 423546
SPLICE
BLOCK,
PART NO.
433284
OVERLAP
CONDUCTORS
UNDER SCREW
TERMINALS
LINEAR
DETECTION
WIRE
LINEAR
DETECTION
WIRE
LINEAR
DETECTION
WIRE
STRAIN RELIEF,
PART NO. 423546
SPLICE BODY,
PART NO. 426783
3/4 IN.
(2 cm)
3/8 IN.
(1 cm)

USER INTERFACE
This section is designed to give the user overall information on all
features and components pertaining to the CHECKFIRE MP-N
Control Module itself.
FIELD TERMINATIONS
Terminals 1 and 2 – Not Used
Terminals 3 and 4 – Detection Input Initiating Circuit No. 1
• Cable must be round jacketed, with an O.D. of 0.13 in. to 0.25
in., suitable for the intended usage
• Polarity need not be considered
Terminals 5 and 6 – Initiating Input Circuit No. 2
• Can be set up as either an initiating input circuit to cause a
release output or pressure switch feedback input
• When set up for pressure switch feedback input, operation does
not discharge system
• Polarity need not be considered
• Cable must be round jacketed, with an O.D. of 0.13 to 0.25 in.,
suitable for the intended usage
Terminals 7 and 8 – Release Circuit
• Polarity must be considered – Terminal No. 7 (+), Terminal No.
8 (–)
• 15 ft. maximum cable length between control module and pneu-
matic actuator
• Cable must be round jacketed, with an O.D. of 0.13 to 0.25 in.,
suitable for the intended usage
Terminals 9, 10, 11, 12 and 13 – Not Used
Terminals 14, 15, 16 – Shut Down Relay
• Cable must be round jacketed, with an O.D. of 0.13 in. to 0.25
in., suitable for the intended usage
• 3 amp maximum load
• Relay specification: 4A 250VAC, 3A 30VDC resistive
• Normally open, normally closed set of contacts
• Form “C” contact arrangement
• Contacts shown in normal condition – No. 14 (N.O.), No. 15
(Common), No. 16 (N.C.)
Terminal Block (see Figure 16)
• Terminal connections are sized for 12 - 24 AWG
• Terminal is labeled from left to right, No. 1 through No. 16
• The terminals are designed as follows:
1. Not Used
2. Not Used
3. + Detection Input
4. – Detection Input
5. Initiating Input Circuit No. 2 (+)
6. Initiating Input Circuit No. 2 (–)
7. + Release Output
8. – Release Output
9. Not Used
10. Not Used
11. Not Used
12. Not Used
13. Not Used
14. Shutdown N.O.
15. Shutdown Common
16. Shutdown N.C.
FIGURE 16
004446
USER INTERFACE
2012-MAY-18 REV.02 PAGE 7
CHECKFIRE MP-N Electric
Detection and Actuation System Manual
12345678 910111213141516
+–+–+– NOCNC

USER INTERFACE
PAGE 8 REV. 02 2012-MAY-18
CHECKFIRE MP-N Electric
Detection and Actuation System Manual
SOUNDER
GREEN
YELLOW
RED
YELLOW
FRONT PANEL INDICATORS (See Figure 17)
Battery Trouble (Yellow)
The yellow BATTERY LED will pulse once every 10 seconds when
the internal battery has reached its low-power threshold. Refer to
Installation Section (page 19) for proper battery replacement
procedure.
Battery must be replaced when yellow BATTERY LED is flash-
ing. Failure to replace battery will prevent the CHECKFIRE
module from activating a discharge. If a fire occurs, there could
be personal injury and/or property damage.
Power Normal (Green)
• LED pulses once every 3 seconds when indicating normal
power
• The green Power Normal LED pulses “on” once every 3
seconds indicating power is normal. If the power drops below an
acceptable level, the green Power LED will be extinguished.
Also, the Yellow Battery LED will pulse, indicating trouble.
Alarm (Red)
• The alarm LED will flash if an alarm condition exists. An alarm
condition is caused by operation of the detection circuit or oper-
ation of the manual pull/pressure switch input circuit. The alarm
condition will continue until the source of the alarm is removed
and the control module is reset.
DETECTION CIRCUIT NO. 1 ACTIVATION MODE – Upon
receipt of an input to the detection circuit, the Alarm LED and
the sounder will pulse at a rate of 2 times per second and will
continue at this rate until the first time delay period has expired.
After the first time delay, a second time delay mode is initiated.
This causes the LED and sounder to pulse at a rate of 4 times
per second.
After discharge, the LED and sounder will continue to pulse at
a rate of 4 times per second for 30 seconds. After that, it will
switch to the trouble mode and pulse once every 10 seconds.
INITIATING INPUT CIRCUIT NO. 2 – When programmed to
cause a release, the first time delay mode will be by-passed and
the LED will pulse at a rate of 4 pulses per second while the
second time delay runs through its timing cycle. After the time
delay setting is reached, it will pulse another 30 seconds at the
same rate. After that, the control module will go into the post-
discharge mode, at which time the Alarm LED and Release LED
will pulse at a rate of one pulse per 10 seconds.
PRESSURE SWITCH CIRCUIT (FEED BACK) – When pro-
grammed as a pressure switch circuit, the Alarm LED will pulse
a minimum of 30 seconds at 4 pulses per second. The control
module will then go into the post-discharge mode and the Alarm
and Release LED will pulse at a rate of one pulse per 10
seconds.
Detection Trouble (Yellow)
The Yellow Detection Trouble LED and the audio pulse once every
10 seconds when the control module detects a trouble in the
detection circuit. The control module will automatically return to
normal when the trouble is cleared.
Release Trouble (Yellow)
The Yellow Release LED and the audio will pulse at a rate of once
every 10 seconds when a trouble condition is detected in the
release circuit. The control module will return to normal when the
trouble condition is cleared.
The Release trouble will also pulse after the system has
completed a discharge cycle or a pressure switch feed back signal
has been received. The trouble signal in this condition is used to
indicate a recharge of the fire suppression system is necessary. A
Release trouble under either of these conditions can only be
cleared by resetting the control module.
Sounder (Audio)
The sounder gives the audio indication for all alarm and trouble
outputs. The sounder will pulse at the same rate as the visual
corresponding LED.
The sounder gives the audio indications of the various outputs.
The sounder is rated at 85 Db at 10 feet.
The pulse rates are as follows:
Alarm – Time Delay 1 = 2 pulses per second
Time Delay 2 = 4 pulses per second
Trouble – 1 pulse per 10 seconds
Loss of Power – 1 pulse per 10 seconds
Release Circuit Fired – 4 pulses per second for 30 seconds, then
1 pulse per 10 seconds
Low Battery – 1 pulse per 10 seconds
FIGURE 17
002760
!CAUTION

FRONT PANEL BUTTONS (See Figure 18)
Delay
• Pushing the “DELAY” button during the first time delay cycle will
restart the time delay cycle. If the second time delay cycle has
already started, the “DELAY” button will have no effect.
• The “DELAY” button can also be used to check the diagnostics
function. By depressing the delay button when the system is in
the trouble condition, the LEDʼs will flash a pattern code. Each
pattern code indicates a certain type of trouble. The code
pattern is prioritized. The first trouble must be fixed before
addressing the next one. Once the first trouble is taken care of,
depressing the “DELAY” button will cause the LEDʼs to indicate
the code for the next trouble, if there is one. When the “DELAY”
button is pressed, three short audio and visual indications will
acknowledge the switch has been depressed properly.
Reset
• The “RESET” button is used to re-initialize the control panel.
When depressed, it provides an indication that all LEDʼs and the
sounder are functional.
• It is used to upload the manual programming into the control
module.
• If trouble(s) has not been cleared, the trouble indication will
reappear after the RESET button is pressed.
• When the “RESET” button is pressed, three short audio and
visual indications will acknowledge the switch has been
depressed properly.
FIGURE 18
0002760
BATTERY CONNECTION
The 3.6 VDC internal lithium battery is connected to the control
module by a removable type plug. The battery is supplied with two
separate plug-in connectors. One connector is used for plugging
into MP-N modules and the other connector is used for plugging
into SC-N modules. CAUTION: Do not cut off unused connector
assembly. It must remain on battery module even though it is not
used. Simply tuck the extra connector assembly along side the
battery module when installing the cover.The battery must be
replaced annually or when the Yellow Battery LED and sounder
are pulsing. A label is attached near the battery mounting location
for recording the installation date.
Discharged lithium batteries may contain significant amounts of
unused energy and should be handled with care. Do not
compact for disposal. Before disposal, each battery must be fully
discharged and electrically isolated by enclosing in a plastic bag
and sealing the bag. Do not dispose of in fire. Check applicable
solid waste disposal regulations for proper disposal of more than
one battery.
BATTERY REPLACEMENT
• While in use, the battery requires replacement every year or
when the Yellow Battery LED and sounder are pulsing. The
battery must be replaced only by an authorized ANSUL service
representative.
• The battery is held in place by a battery strap requiring a special
tool for removal
• The shelf life of the battery is 8 years
• Control Module contains a label for recording battery replace-
ment date
• Refer to Installation Section for battery replacement procedure
(page 19), New Battery Installation
• Make certain used battery is disposed of properly
ENCLOSURE
• The enclosure is watertight. It meets the requirements of
International Standard IEC 529, “Degrees of Protection
Provided by Enclosures” for an IP 66 rating
COVER REMOVAL
• The cover is attached with four tamper-proof screws
• When removing and installing cover, make certain seal is always
correctly in place and not twisted
• Seal should always be kept clean
• A small amount of silicone lubricant will improve the seals effec-
tiveness.
STRAIN RELIEF INSTALLATION
• Always use Dow Corning 737 RTV Sealant or equal on all strain
relief and plug male threads
MOUNTING
There are four types of mounting options available for the
CHECKFIRE MP-N Control Module.
• Control Module can be mounted without a bracket. It has
molded-in mounting tabs on the back box. Note: Surface must
be suitable.
• Control Module can be mounted on a combined bracket which
will allow both the module and the manual actuator to be
mounted together.
• Control Module can be mounted on its own bracket and the
manual actuator can be also mounted on its own bracket.
• Control Module can be mounted to an existing CHECKFIRE MP
bracket by the use of a retrofit bracket.
The Control Module should never be mounted in an area
which is subject to pressure washing or steam cleaning.
!CAUTION
USER INTERFACE
2012-MAY-18 REV.02 PAGE 9
CHECKFIRE MP-N Electric
Detection and Actuation System Manual
RESET
BUTTON
RESETDELAY
DELAY
BUTTON

HAZARD IDENTIFICATION
Before the CHECKFIRE MP-N Electric Detection and Actuation
System is installed, the hazards to be protected must be identified.
These hazard locations determine where the detection wire or
thermal detectors and the fire suppression system nozzles are
required. While the agent nozzles in existing fire suppression
systems will point out the hazard areas, the following information
should still be reviewed to best determine detection requirements.
If an entire fire suppression/detection system is to be installed, this
information is vital in determining proper placement of discharge
nozzles and detection devices.
Fire Hazard Definition
A fire hazard is any area where an ignition source (high tempera-
ture or sparks) and fuel (flammable materials) may be found in
close proximity.
Examples of ignition sources are engines, exhaust piping,
turbochargers, battery compartments, electrical system equip-
ment, torque converters, transmissions, hydraulic pumps, parking
brakes, and friction from debris packed around parts.
Occasionally other components may reach high temperatures due
to malfunction. The potential danger from these components must
also be examined during hazard identification. A parking brake left
engaged is an example of a potential high temperature source.
Temperatures in excess of the detection wire or thermal detector
ratings will cause the detection system to activate thereby actuat-
ing the fire suppression system.
The above mentioned heat sources can cause fire when they
come in contact with flammable materials such as leaking fuel:
either broken fuel lines, slow leaks, broken hydraulic lines, or a
ruptured fuel tank. Type of Class A materials are part of the vehicle
itself such as electric wiring insulation, padding, plastic parts, the
packages on the vehicle, or debris due to poor maintenance.
These materials can contribute to the rapid buildup or spreading
of fire.
Other Considerations
Be aware that the propagation of fire from one area to another
may cause a hazard to be larger than originally determined. Liquid
fuel may spray, splash, or flow carrying the fire some distance
from the starting point. Radiation, sparks, or conduction through
metal can carry heat to an area where the danger of fire wouldnʼt
normally exist.
Also, consider the fire history of the equipment being protected or
of similar equipment. This information may be available through
company records or vehicle operators may have had first hand
experience enabling them to identify the locations of previous fires
as well as special hazards such as a hydraulic hose that frequently
ruptures.
Each hazard that is identified must have both fire suppression
system fixed nozzles and detection wire or thermal detectors.
Equipment Shutdown
Another factor to examine is equipment shutdown. Provisions
should be made to shut down any components that could possibly
add to the intensity of the fire (fuel pumps, hydraulic pumps,
engine, etc.) or any components that could possibly re-ignite the
fire once it has been suppressed (battery, electrical system).
Although a properly installed fire suppression/detection system is
the primary means of protecting equipment from fire, an effective
fire protection package also includes provisions for equipment
shutdown.
The CHECKFIRE MP-N control module contains 3 amp 30VDC
shutdown relay contacts to facilitate connection of shutdown
devices recommended by the vehicle manufacturer. Example:
opening or closing of coolant over-temperature alarm will bring
about properly sequenced engine shutdown on many vehicles.
Consult vehicle manufacturer for details.
PRE-INSTALLATION GUIDELINES
Before actually installing the CHECKFIRE MP-N Electric
Detection and Actuation System, review all of the following infor-
mation and plan (sketch) the system layout. This will help to avoid
any unforeseen installation problems. Once an acceptable layout
has been determined, record and keep it for future reference.
Control Module and Actuator Location
1. The control module and manual actuator must be mounted in
the cab or control area of the equipment being protected.
They must be positioned within arms reach of the operator to
enable manual operation of the red strike button on the
manual actuator as well as the delay and reset buttons (to
extend time delay) on the front of the control module, and
close enough so that the internal alarm can be heard.
2. The location must be suitable for bolting or welding if bolting is
impractical. The mounting surface must be flat to avoid strain on
the mounting bracket. The preferred mounting position is with
the CHECKFIRE MP-N control module in an upright position.
3. There must be room enough to allow for proper wiring
connection to the control module and to install the actuation
line from the fire suppression system to the manual actuator.
Also, the module and actuator should be accessible for peri-
odic inspection and maintenance. The components should be
mounted in a location that will not interfere with normal equip-
ment maintenance.
NOTICE
The ambient temperature in the mounting
environment must not fall below –40 °F
nor exceed 140 °F (–40 to 60 °C).
4. The gas motor actuator can be mounted in any convenient
location within 10 ft. (3.1 m) of the module, which is not
subject to damage or abuse. The gas motor actuator bracket
can be welded or bolted to a rigid surface.
Detection Wire Routing
The preferred method for routing linear detection wire is to begin
by connecting the detection wire directly to the CHECKFIRE MP-N
control module.
Because linear detection wire need only be routed through the
hazard area, another acceptable routing method is to use
stranded 16 AWG jacketed wiring connected to the control module
and routed to the beginning of the hazard area(s). At that point, a
splicing device, Part No. 428375, can be used to make the proper
connection between the stranded 16 AWG jacketed wire and the
start of the linear detection wire. This method can only be used
when the splicing device can be adequately protected from
damage and moisture.
1. The total length of detection wire must not exceed 100 ft.
(30.5 m). If possible, it should be run in a single continuous
loop. Splices are acceptable when they are kept to a minimum
and when they are made in accordance with the splicing tech-
nique found on Page 15 of Installation Section.
SYSTEM PLANNING
PAGE 10 REV. 02 2012-MAY-18
CHECKFIRE MP-N Electric
Detection and Actuation System Manual

PRE-INSTALLATION GUIDELINES (Continued)
2. Do not install the linear detection wire within 12 in. (30 cm) of
areas which will become extremely hot during operation, such
as engine block, exhaust manifolds, turbochargers. etc.
Note: Maximum installed ambient temperature at the wire
location is 221 °F (105 °C).
3. Avoid routing detection wire directly across an opening.
Where possible, install detection wire above the hazard area
or around the perimeter of a hazard compartment to react to
escaping heat. Do not allow struts, frame members, etc. to act
as heat shields between the hazard and the detection wire.
4. Avoid areas where the detection wire may be damaged, such
as outside the vehicle, near moving parts, in areas where
rocks or debris may be thrown by wheels, or in the way of
maintenance personnel.
5. To reduce its accessibility to damage, use only as much
detection wire as is necessary to cover the hazard area.
6. The minimum bend radius for detection wire must not be less
than 2 1/2 in. (65 mm).
Thermal Spot Detector Selection and Placement
Thermal detectors are used when single point detection is
required. They are selected by temperature range relative to the
hazard temperature. Table 1 indicates the thermal spot detector
rated operating temperature required according to the maximum
hazard temperatures.
Thermal Spot
Detector Maximum
Rated Operating Hazard
Temperature Temperature Detector
°F (°C) °F (°C) Color Part No.
_____________ ___________ ____ _______
270 (132) 234 (112) Blue 416218
325 (163) 280 (137) Red 416219
360 (182) 312 (155) Red 416220
TABLE 1
The placement of thermal spot detectors should be based on the
following requirements:
1. They can be wired directly to the control module using
approved cable. Cable must have a temperature rating of
392 °F (200 °C) minimum, 16-18 gauge, two conductor with
drain, minimum O.D. of 0.230 in. (5.8 mm). Again, placement
of the detectors should allow for incoming and outgoing wire
connections.
2. Secure the detector with the provided bracket and clamps.
Pneumatic/Linear Detection Tubing
1. When mounting tubing and responder, make certain they are
not in areas subject to damage.
2. Avoid routing detection tubing directly across an opening.
Where possible, install detection tubing above the hazard
area or around the perimeter of a hazard compartment to
react to escaping heat. Do not allow struts, frame members,
etc., to act as heat shields between the hazard and the detec-
tion tubing.
3. The detection tubing assembly is 35 ft (10.7 m) long. If more
than 35 ft (10.7 m) is required, additional assemblies can be
added. See wiring diagram details on instruction sheet
included with each Pneumatic/Linear Detection Shipping
Assembly.
System Layout
Once the system components have been selected and their loca-
tions have been determined, sketch the layout of the system. This
sketch should include the location of the components, as well as
the proposed detection wire routing, thermal detector locations,
and pneumatic actuation hose routing. Also, indicate areas where
the wire must pass through bulkheads so that there is an accept-
able routing from one hazard to the next. This sketch should be as
precise as possible to avoid any unforeseen installation problems
later.
SYSTEM PLANNING
2012-MAY-18 REV.02 PAGE 11
CHECKFIRE MP-N Electric
Detection and Actuation System Manual

INSTALLATION
Before installing the detection and actuation system, the System
Planning portion of this manual should have been reviewed for
particular application resulting in a system layout sketch. Always
read the procedure before installing each component to become
familiar with the correct installation steps as they apply to the
particular application and sketch.
NOTICE
For ease of installation, the fire suppression
system should be installed before the detection
and actuation system.
INSTALLATION MATERIALS
All hardware and tools should be on hand before beginning the
installation. Check the Component Index, Page 37, to make
certain all necessary system components are available.
Material to be supplied by the installer includes:
– Ample cable ties or 1/4 in. (6 mm) clamps to guide and support
the detection wire.
– Non-wire braid hose (1/4 in.) to be used as a protective cover-
ing for the detection or power wire at points of securement and
when passing through bulkheads.
– Actuation line (1/4 in. hydraulic hose) and fittings to connect the
electric detection and actuation system actuator to the fire
suppression system. (See applicable ANSUL Fire Suppression
Systems installation manual for additional details.)
Tools required to perform the installation include:
– Drill and Drill Bit Set (or welding equipment)
– 1/8 in. Blade Screwdriver
– 1/4 in. Blade Screwdriver
– Phillips Screwdriver
– Standard Sidecutters
– Small Sidecutters (1/4 in. cut)
– Wire Stripper
– Low Wattage Soldering Pencil (35 watt)
– Rosin Core Solder (60/40)
– Rubberized Electricianʼs Tape
MOUNTING BRACKET INSTALLATION
Three mounting bracket options are available:
• Mounting control module and pneumatic actuator on same
bracket
• Separate brackets for control module and pneumatic actuator
• Control module retrofit bracket to existing CHECKFIRE MP
bracket
Bolting
1. Using the bracket as a template, carefully mark the location of
the bracket mounting holes.
2. Center punch the premarked hole locations and drill 3/8 in.
(10 mm) holes through the mounting surface.
3. Secure the bracket to the mounting surface using appropriate
length of 5/16 in. (8 mm) bolts with flat washers, lockwashers,
and nuts. See Figure 19.
FIGURE 19
002761
Welding
NOTICE
Never weld on the vehicle frame without first
consulting the owner and vehicle manufacturer.
1. Carefully mark the location of the bracket.
2. Clean the mounting bracket and mounting surface using a
wire brush until clean steel surfaces are available for welding.
3. Secure the bracket to the mounting surface using 1/8 in.
(3 mm) fillet welds at the top, bottom, and both sides. See
Figure 20.
4. Remove all weld spatter from the bracket and mounting
surface.
5. Prime and paint the exposed bare metal of the bracket and
mounting surface.
FIGURE 20
002762
INSTALLATION
PAGE 12 REV. 02 2012-MAY-18
CHECKFIRE MP-N Electric
Detection and Actuation System Manual
WELD
WELD

MOUNTING TO EXISTING CHECKFIRE MP BRACKET
In some cases, retrofitting to an existing CHECKFIRE SC system
may be an option. To accomplish this, use retrofit bracket, Part No.
423531. This bracket can be mounted directly to the existing SC
bracket. See Figure 21.
NUTS AND BOLTS INCLUDED
WITH RETROFIT BRACKET
FIGURE 21
002763
MANUAL ACTUATOR INSTALLATION
Mounting
1. Remove jam nut from lower threads of actuator and slide
actuator through hole in mounting bracket.
NOTICE
Use washer, Part No. 416794, below
bracket only.
2. Reinstall jam nut and tighten firmly (see Figure 22).
3. Install ring pin but do not attach seal at this time.
FIGURE 22
003917
Installing The Fire Suppression System Actuation Line
Install 1/4 in. actuation hose from outlet on actuator to pneumatic
actuator on fire suppression system using a check valve at the
intersection of each actuation device branch. (See Figure 23.)
The CHECKFIRE MP-N System output (using LT-10-R cartridge)
can pressurize up to 75 lineal ft (22.8 m) of 1/4 in. actuation line
with up to eight agent tanks and/or accessories. Check valves are
used to protect against pressure loss if one or more actuator
cartridges are removed or damaged; and by isolating each branch
line, they reduce the overall lineal length of actuation line.
The fire suppression system could be accidentally actuated
causing the release of agent if the gas motor or LT-10-R
cartridge is installed at this time. Do not install these components
until the appropriate installation step is reached.
FIGURE 23
003901
!CAUTION
INSTALLATION
2012-MAY-18 REV.02 PAGE 13
CHECKFIRE MP-N Electric
Detection and Actuation System Manual
AUTOMATIC
ACTUATOR
ACTUATION
LINE
MANUAL
ACTUATOR
DETECTION
AND
ACTUATION
SYSTEM
MSHA
APPROVED
PRESSURE
SWITCH
(SUPPLIED BY
OTHERS) OR
PNEUMATIC
SHUTDOWN
DEVICE
RELIEF
VALVE
CHECK
VALVE
FIRE
SUPPRESSION
SYSTEM

MOUNTING THE CONTROL MODULE
The CHECKFIRE MP-N Control Module can be mounted to either
a flat, rigid surface or utilizing one of the three bracket options.
If mounting the control module to a flat, rigid surface, use the
appropriate fasteners.
If mounting the control module to the MP-N bracket, complete the
following steps:
1. With the bracket securely mounted, position the holes in the
control module mounting flanges over the threaded studs on
the bracket. Using the supplied mounting hardware, securely
fasten the control module to the bracket with four lock
washers and nuts.
2. If utilizing the MP retrofit bracket, first fasten the retrofit
bracket onto the existing MP bracket by using the supplied
fasteners. With the MP retrofit bracket securely fastened,
position the holes in the control module mounting flanges over
the threaded studs and securely fasten.
Remove the cover from the control module. If the internal 3.6
VDC battery is in place, disconnect the wire plug until the
field wiring is complete.
If the strain relief(s) and plug(s) are not in place, coat the male
threads with Dow Corning 737 RTV Sealant or equal and install in
holes of module back box.
At this point, the external field wiring can be installed.
GAS MOTOR ACTUATOR ASSEMBLY
Mounting
1. The gas motor must be mounted in a location where it will not
be subjected to damage or corrosion.
2. The gas motor can be mounting in either the horizontal or
vertical position.
3. It must be mounted within 10 ft (3.1 m) linear cable length of
the CHECKFIRE Control Module.
NOTICE
After automatic system actuation, the
internal gas motor device must be
replaced. Make certain assembly is
mounted in an accessible location.
4. Securely mount the actuator bracket, Part No. 54923, either
by welding or bolting to a rigid surface.
5. Remove locknut from gas motor body, position body in
bracket hole and reinstall locknut. Wrench tighten. See Figure
24. Note: For proper installation, make certain the gas
motor is threaded fully, 6 threads, onto the actuator body
and properly secured with the allen head set screw.
FIGURE 24
003925
CONTROL MODULE WIRING/DETECTION WIRE ROUTING
Mounting
1. Using the system layout sketch, investigate each point where
the wire will be secured to the vehicle. Keep in mind all the
guidelines in the System Planning Section. Do this on a
vehicle that has been operated recently to avoid securing the
wire too close to extremely hot components.
2. After the vehicle has cooled, loosely route the wire from the
start of the hazard throughout the proposed path through the
hazard areas. If splicing is required, see Splicing, Page 16, for
detailed information.
3. Secure the detection wire by completing the following steps:
See Figure 25.
a. Start at the beginning of the detection wire leading into the
hazard area. Secure the detection wire every 12 to 18 in.
(30 to 45 cm) using black nylon cable ties, Part No. 56691,
and protective coverings, Part No. 56692, at points of
securement. Secure more often if necessary. Attach the
wire to mounting surfaces, decks, struts, etc., always
keeping System Planning guidelines in mind.
NOTICE
The minimum bend radius for detection
wire must not be less than 2 1/2 in. (64
mm).
Detection wire must never be routed through a hole or
near sharp edges without being properly protected.
Failure to protect the wire from being cut or abraded
could cause it to short, causing a false discharge.
b. Secure the wire at least once immediately before it passes
through a hole in a vertical or horizontal surface. At the
hole, a 1/4 in. (6 mm) rubber sleeve, Part No. 56692, or a
special grommet to fit the hole should be used to protect
the wire from wear due to vibration. If the rubber sleeve
might slide from under the cable tie and off the wire, tape
the rubber sleeve to the wire using electricianʼs tape to
keep it from sliding (see Figure 25). This hose protection
should also be used at locations where the wire would rub
against other hard surfaces, rough edges, or sharp
corners.
FIGURE 25
000872
!CAUTION
INSTALLATION
PAGE 14 REV. 02 2012-MAY-18
CHECKFIRE MP-N Electric
Detection and Actuation System Manual
LOCK
NUT
GAS
MOTOR
SET
SCREW
ACTUATOR
BODY
CABLE TIE
1/4 IN.
RUBBER SLEEVE
TAPE AT
BOTH ENDS
Table of contents
Other Ansul Fire Alarm manuals
Popular Fire Alarm manuals by other brands
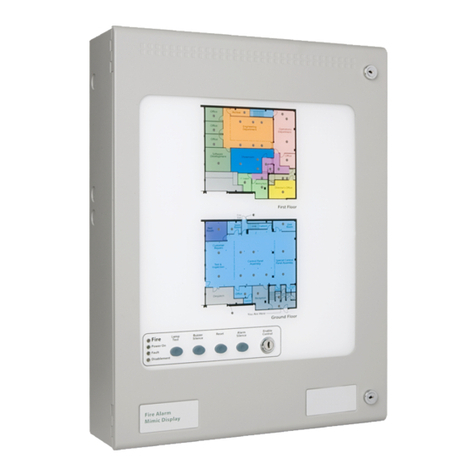
Kentec Electronics
Kentec Electronics Syncro Operation and maintenance manual
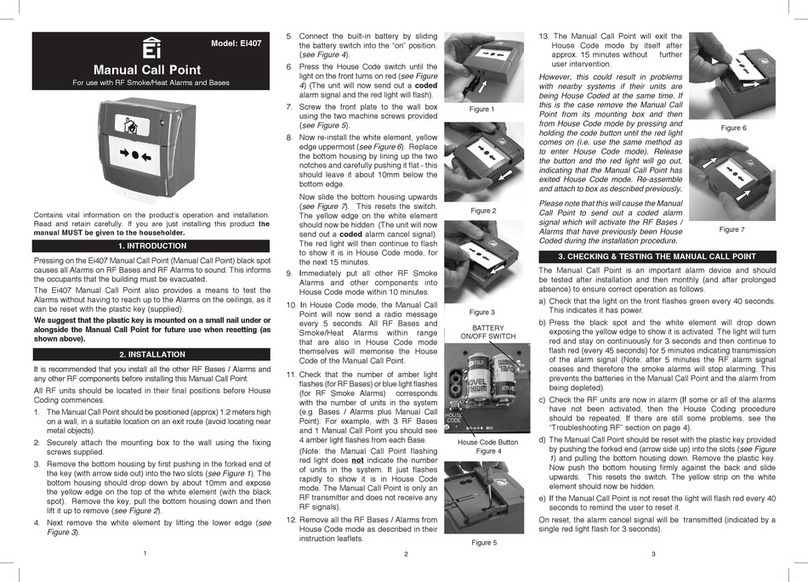
Ei Electronics
Ei Electronics Ei407 quick start guide

UniPOS
UniPOS FAMCO EXTENSION RELEASE instruction manual
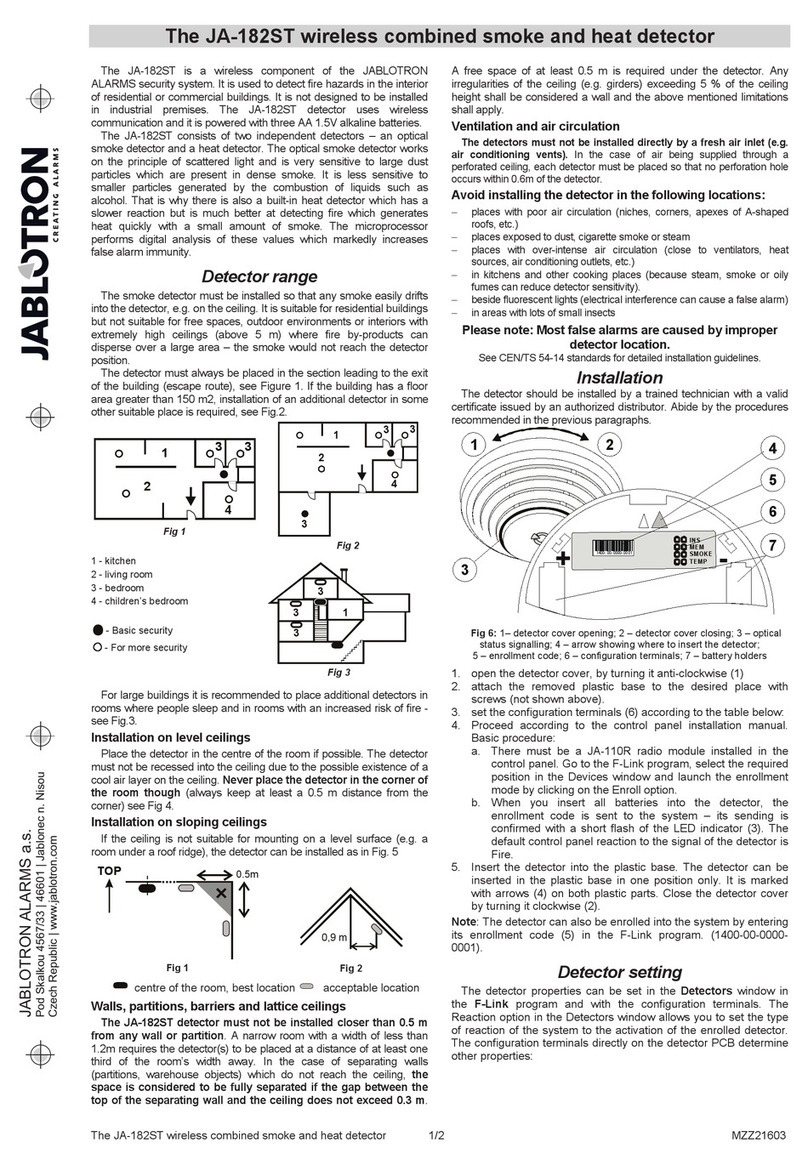
jablotron
jablotron JA-182ST quick start guide

Zeta
Zeta MKII-HR installation guide

Fire-Lite
Fire-Lite SENSISCAN 2000 Nstallation, operation and programming manual
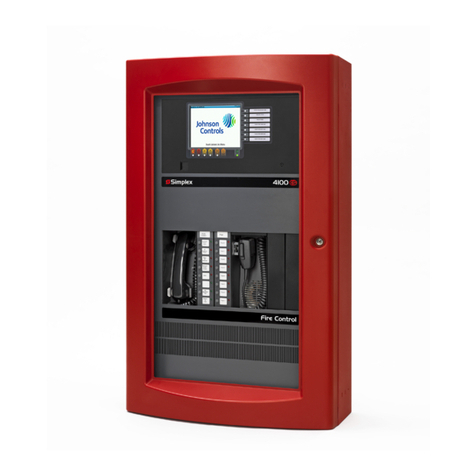
Simplex
Simplex SafeLINC 4100 Service instructions
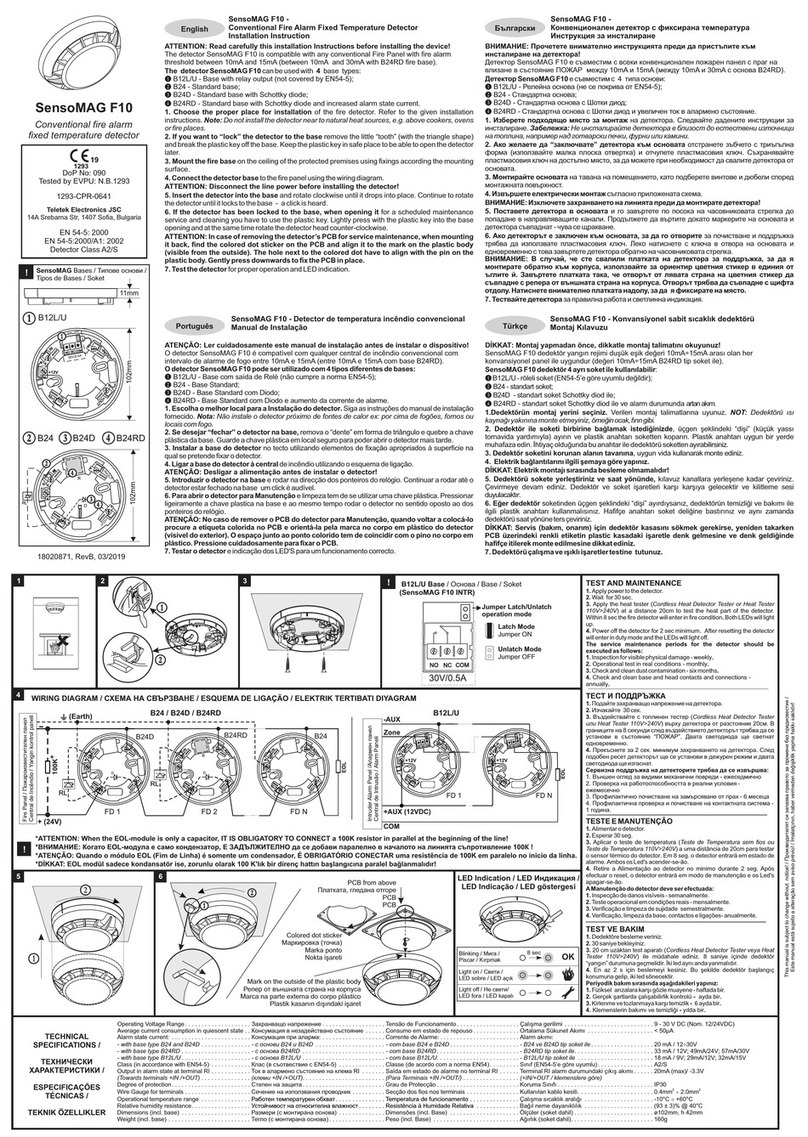
Teletek electronics
Teletek electronics SensoMAG F10 Installation instruction
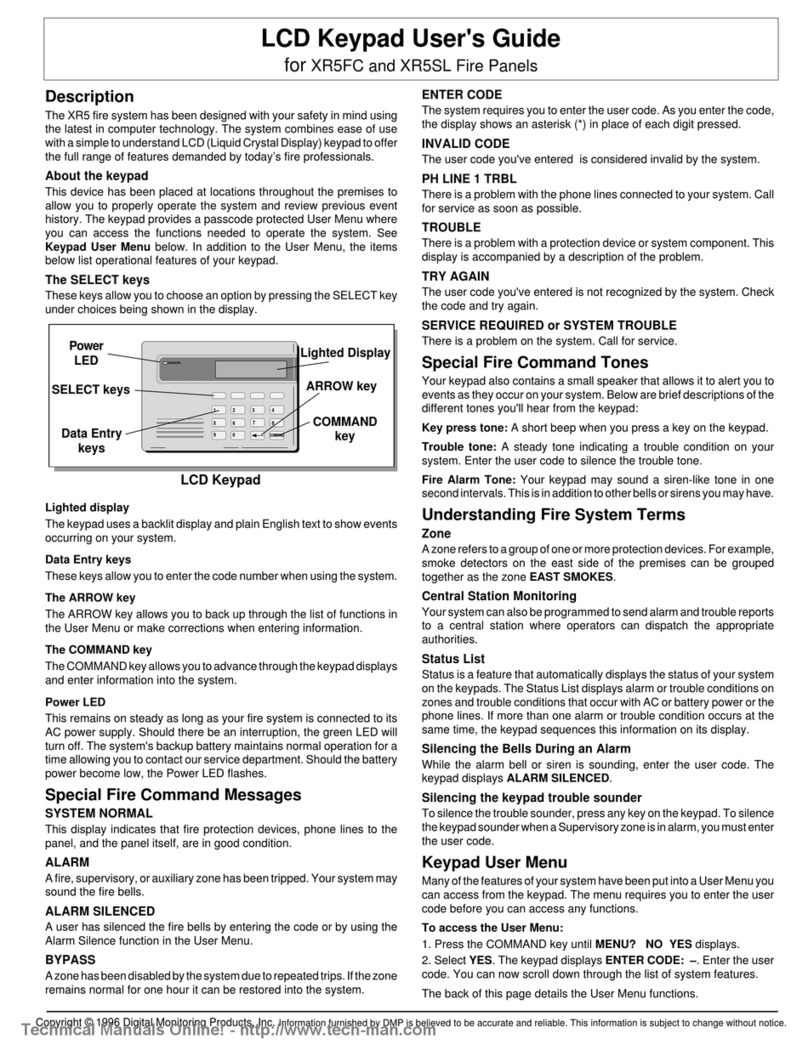
Digital Monitoring Products
Digital Monitoring Products XR5FC user guide
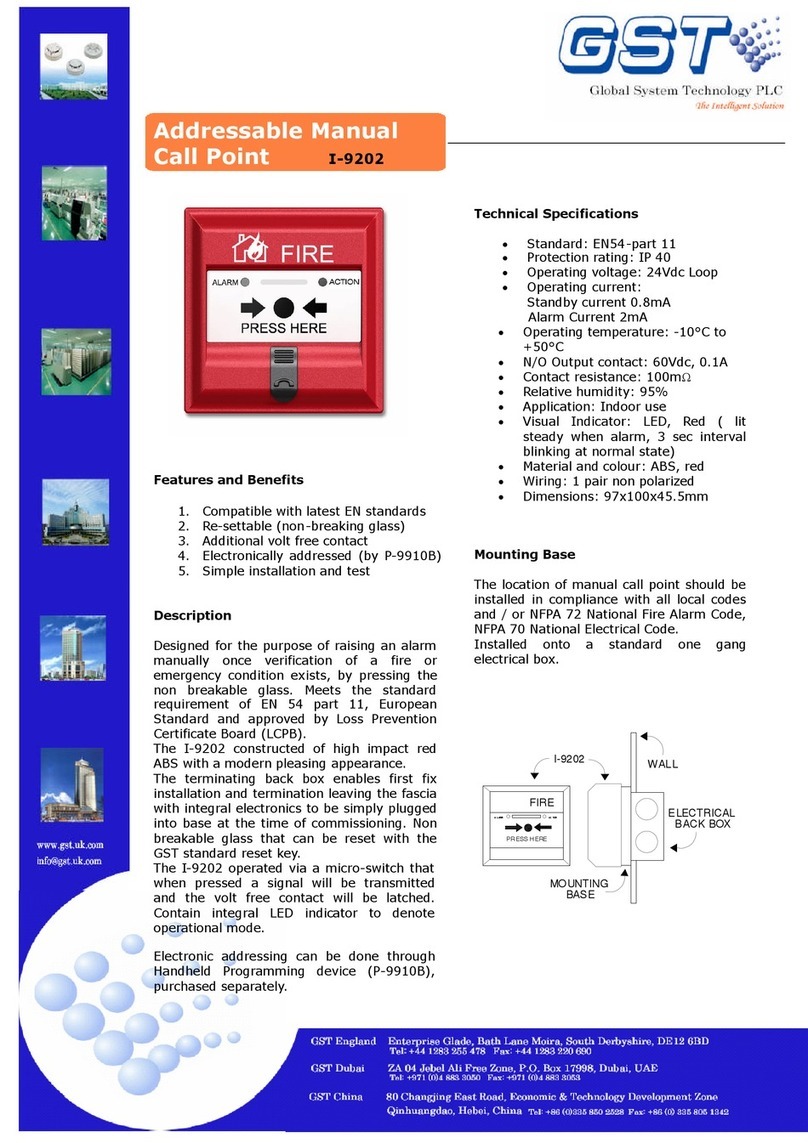
GST
GST I-9202 quick start guide

Honeywell
Honeywell Fire-Lite Alarms BG-12S manual
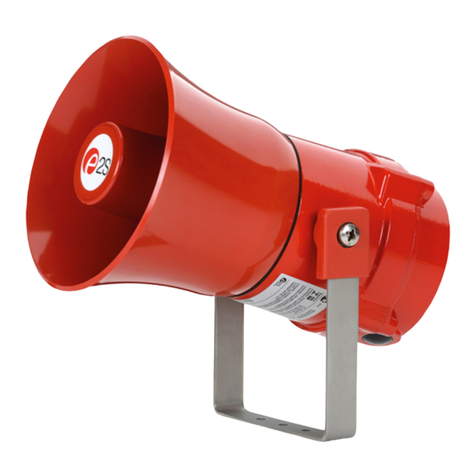
E2S
E2S BExTS110D instruction manual