Aplisens ERH-01 04-07 User manual

TECHNICAL PRODUCT DOCUMENTATION
ER5-1047
Page: 1
Pages: 17
Updating August 2010
LEVEL SWITCHES
TYPE ERH-01...04-07

TECHNICAL PRODUCT DOCUMENTATION
ER5-1047
Page: 2
Pages: 17
Updating August 2010
TABLE OF CONTENTS:
PAGE
1. INTRODUCTION 3
1.1. SAFETY INDICATIONS 3
1.1.1. Range of applications 3
1.1.2. Power supply connecting 3
1.1.3. Indications and warnings 3
1.1.4.
Power supply connecting 3
1.1.5. Indications and warnings 3
1.2. SUBJECT OF TECHNICAL PRODUCT DOCUMENTATION 4
1.3. APPLICATION, LEGAL DESIGNATIONS 4
1.4. DESIGN AND OPERATION PRINCIPLE 4
2. TECHNICAL DATA 5
3. ORDERING METHOD AND EXAMPLE 6
4. OPERATION INSTRUCTION 7
4.1 INSTALLATION INSTRUCTION 7
4.2 START-UP AND OPERATION INSTRUCTION 16
4.2.1 Preparing for start-up 16
4.2.2 Operation manual 16
4.3 MAINTENANCE INSTRUCTION 16
4.4 SAFETY INSTRUCTION 16
5. STORAGE AND TRANSPORT CONDITIONS 16
6. DELIVERY RANGE 17
6.1. Spare parts 17
7. WARRANTY CONDITIONS 17

TECHNICAL PRODUCT DOCUMENTATION
ER5-1047
Page: 3
Pages: 17
Updating August 2010
1. INTRODUCTION
1.1 SAFETY INDICATIONS
1.1.1 Range of applications
Level switches is designed for automatic adjustment, signalling or controlling of preset threshold
value of fluid level in open or closed (pressurized) tanks, in wide range of pressures and temperatures.
Other applications must be consulted with the producer.
Producer is not responsible for any damages, resulting from controller use, inconsistent with above
applications. The risk is born by the user only.
The element of proper use of that device is also following this technical documentation
recommendations.
1.1.2. Definitions used in the description
•Operator – person using the device according to its purpose (PN-EN 61010-1, July 2004),
•Technical inspection – person or group of persons, responsible for device use and maintenance,
and assuring appropriate trainings for OPERATORS (PN-EN 61010-1, July 2004),
1.1.3. Allowed operations range:
•For operator – level switch operation.
•Technical inspection – as for operator, also mechanical and electrical installation and adjustment
activities.
1.1.4 Power supply connecting.
Installation works and level switch start-up should be performed only by qualified electricians
or personnel trained under their supervision, according to valid regulations and electrotechnical
recommendations.
1.1.5 Indications and warnings.
In case of not following recommendations and warnings serious injuries and/or property damages
may occur. Operator must be properly trained by technical inspection and familiarized with all safety
recommendations and warnings.
For reliable and safe level switch operation it is required to assure proper transport, storage,
installation, start-up and maintenance.
In this technical documentation the important safety information are marked with the following
symbols:
This symbol means: Indication.
“Indication” shows action or process, especially important for proper device operation.
In case of not following such recommendation property damages may occur.
This symbol means : Warning.
“Warning” shows action or process, which in case of improper execution may
be dangerous for personnel or cause serious property damages.

TECHNICAL PRODUCT DOCUMENTATION
ER5-1047
Page: 4
Pages: 17
Updating August 2010
1.2SUBJECT OF TECHNICAL PRODUCT DOCUMENTATION
The subject of this technical product documentation is application, design and installation of level switches.
1.3APPLICATION, LEGAL DESIGNATIONS
Level switches are designed for double-position signalling of fluid minimum and maximum.
Designation according to Polish Classification of Products and Services (PKWiU): 26.51.70.0
Designation according to Systematic List of Products (SWW): -0918-132.
1.4DESIGN AND OPERATION PRINCIPLE
Level switches consists of two main groups, separated with diamagnetic partition:
•relay group, being the converting device part, unified for all types.
In the body there is intermediate magnet, directed with equal pole to the float magnet, and the
miniature connector, supplying electric impulses, resulting from magnet lever arm action, to the
connector contacts switching button. To the connector terminals external cables are connected,
guided though the cable gland.
•float group, being the level switch sensor group. Depending on level switch application, the float
group is different for each type, and float may look like cylinder with semicircular bowls or ball.
Constant magnet is connected directly or through the lever system to the float, which is directed with the
equal pole to the intermediate magnet of relay group. Float group magnet is protected by housing.
Level switch is activated by the fluid, through the float buoyant force. Fluid level changes cause float
group tilting, which through the magnetic coupling are transferred to the intermediate magnet, which lever
arm closes or opens miniature connector contact. The level switch operation principle is shown by the
following electric diagram. For the minimum level terminals NC-NC are shortened. When level rises,
terminals NC-NC remain shortened until reaching the maximum level. Then the snap switching takes place,
i.e. opening of terminals NC-NC and shorting of terminals NO-NO, which remain shorted until reaching
minimum level by the float.
Electric diagram

TECHNICAL PRODUCT DOCUMENTATION
ER5-1047
Page: 5
Pages: 17
Updating August 2010
2. TECHNICAL DATA
Table no. 1. Technical data
No.
Parameter Unit type ERH-01-07 ERH-02-07 ERH-03-07 ERH-04-07
1. Switching hysteresis
mm 10
20 ±15%
30
10
20 ±15%
30
min 50
±
15%
max 250±2%
min 100±15%
max 400±2%
min 32
±
15%
max 1350±2%
2. Maximum fluid temperature °C 70 70 70 70
3. Maximum operation pressure MPa 0.2 0.2 0.2 0.2
4. Rated contact voltage U
e
AC and DC V 24 24 24 24
5. Rated continuous current I
nc
A 10 10 10 10
6.
Rated contact current I
e
in category AC15 24 V
in category DC13 24 V
A
A
2.5
2.5
2.5
2.5
2.5
2.5
2.5
2.5
7. Contact life
in category AC15 U
e
=24V; I
e
=2.5A
in category DC13 U
e
=24V; I
e
=2.5A
connections
connections
10
7
5x10
6
10
7
5x10
6
10
7
5x10
6
10
7
5x10
6
8. Mechanical durability cycles 10
7
10
7
10
7
10
7
9. Ambient temperature °C -25…70 -25…70 -25…70 -25…70
10.
Weight
kg
- submersible version 1,8 2,0 2,1 3,0
- submersible acid-proof version 2,6 2,8 2,9 3,8
- 1 m cable 0,2 0,2 0,2 0,2
11. Minimum liquid density g/cm
3
0.6 0.6 0.6 0.6
12. Housing protection rating IP 68 68 68 68
ATTENTION!
Switching hysteresis (insensibility zones) in table 1 relate to fluid density 1x10
-3
kg/m
3
. Maximum et
switching hysteresis caused by fluid density change is approximately 1 mm for 0.1x10
-3
kg/m
3
.
Insensibility zones are constant for the given fluid. Overall and installation dimensions are shown on
attached dimensional drawings.
SWITCH’S WET PART SWITCH’S DRY PART
permanent magnets diamagnetic partition
float stroke limits miniature connector
magnets rotation
axis

TECHNICAL PRODUCT DOCUMENTATION
ER5-1047
Page: 6
Pages: 17
Updating August 2010
3. ORDERING METHOD
Ordering method for level switches ERH-01-07 and ERH-02-07
Type: ERH-01-07
ERH-02-07 (without version “4.0...4.6”)
Switching hysteresis:
-1 switching hysteresis h=10 mm
-2 switching hysteresis h=20 mm
-3 switching hysteresis h=30 mm
-4-0 Arm length A=125 mm, B=125 mm
-4-1 Arm length A=185 mm, B=80 mm
-4-2 Arm length A=250 mm, B=125 mm
-4-3 Arm length A=140 mm, B=120 mm
-4-4 Arm length A=100 mm, B=120 mm
-4-5 Arm length A=120 mm, B=80 mm
-4-6 Arm length A=150 mm, B=80 mm
Electric connector
-1 without cable
-2 with cable 3m length *(*- other cable length available on client request with
additional payment)
acid-proof version
ERH -01-07 - 1 - 1 -K
Example of ordering:
ERH -01-07 – 1-1 Level switches with switching hysteresis h=10 mm, without cable
Ordering method for level switches ERH-03-07
Type: ERH-03-07
Set switching hysteresis:
-1 set switching hysteresis min 100 mm max 400 mm
-2 set switching hysteresis min 50 mm max 250 mm
Electric connector
-1 without cable
-2 with cable 3m length* (*- other cable length available on client request with
additional payment)
acid-proof version
ERH -03-07 -1 - 1 - K
Example of ordering:
ERH -03-07-1- 1 level switches with set switching hysteresis min 100 mm max 400 mm, without cable

TECHNICAL PRODUCT DOCUMENTATION
ER5-1047
Page: 7
Pages: 17
Updating August 2010
Ordering method for level switches ERH-04-07
Type: ERH-04-07
Electric connector
-1 without cable
-2 with cable 3m length* (*- other cable length available on client request with
additional payment)
acid-proof version
ERH -04-07 -1 -K
Przykład oznaczenia
ERH -04 -07- 1 level switch with set switching hysteresis min 32 mm max 1350 mm, without cable
4. OPERATION INSTRUCTION
4.1 INSTALLATION INSTRUCTION
All level switches types should be connected to connecting pipes with connection flanges with
dimensions shown on the drawing below.
In version - 1 of electric connection (i.e. without sealed cable). External electric cable with external
dimension from Φ9 to max Φ13 should be introduced to galvanized pipe with internal diameter min. Φ14.
Pipe should be screwed to the terminal with taper thread R 3/4”. Check the connection tightness after
screwing. No leaks are allowed. The other pipe end should be placed in the gland of branch socket. Cables
in the head should be connected to terminals NC – NC, NO – NO, depending on requirements.
After cables connecting, screw the head cover, paying attention for sealing ring position, protecting
the tightness after immersing. In case of level switches with electric connection – 2 the connecting cable in
sealed by the producer, and does not require guiding in the pipe. Cable has GL certificate for direct guiding
in sea water. Cable ends are designed according to electric diagram in the technical product documentation.

TECHNICAL PRODUCT DOCUMENTATION
ER5-1047
Page: 8
Pages: 17
Updating August 2010
Connecting pipe example
It is recommended to weld the connection flange directly to the tank (without connection pipe).
Steel
4 screws
4 screws (2-sided)
(2-sided)
washers
nuts Float controller
holes at
4 holes
View „”W”

TECHNICAL PRODUCT DOCUMENTATION
ER5-1047
Page: 9
Pages: 17
Updating August 2010
Required controller installation method with electric connection in ver. -1
Caution:
Other types of cables may be used, but only up to external diameter max φ13.
1 – Branch socket is not supllied by manufacturer
2 - Cable YKOXS 5x1 with external diameter max φ13 is not supplied
3 – Pipe with connection (nut R 3/4” with taper thread), galvanized (Fe/Zn-
25 CD acc. to BN-84/3702-02). Like the cable, it is not supplied.
4 – Gland element
5 – level switch
6 – End with taper thread R 3/4”
hole
Φ14 – 4 holes at 90
o

TECHNICAL PRODUCT DOCUMENTATION
ER5-1047
Page: 10
Pages: 17
Updating August 2010
Pipe and cable sealing method with electric connection in ver. -1
Pipe and cable sealing method with electric connection in ver. –2
tapered
1. Cover
2. Head
3. Sealing ring φ70 x 3
4. Sealing ring φ17.3 x 2.4
5. End
6. Seal
7. Washer
8. Gland element
tapered
1. Cover
2. Head
3. Sealing ring φ70 x 3
4. Sealing ring φ17.3 x 2.4
5. End
6. Seal
7. Washer
8. Gland element
9. Glue EPIDIAN 5
10. Cable YKOXS 5x1

TECHNICAL PRODUCT DOCUMENTATION
ER5-1047
Page: 11
Pages: 17
Updating August 2010
Dimension drawing of level switch ERH-01-07
Ver. H [mm] L [mm]
-1 120 190
-2 140 230
-3 150 255
Φ14 – 4
holes
at 90
o
tapered

TECHNICAL PRODUCT DOCUMENTATION
ER5-1047
Page: 12
Pages: 17
Updating August 2010
Dimension drawing of level switch ERH-01-07-4
at
Φ14 – 4 holes
at 90
0
tapered

TECHNICAL PRODUCT DOCUMENTATION
ER5-1047
Page: 13
Pages: 17
Updating August 2010
Dimension drawing of level switch ERH-02-07
Ver. H [mm] L [mm]
-1 120 190
-2 140 230
-3 150 255
tapered
Φ14 – 4 holes
at 90
o

TECHNICAL PRODUCT DOCUMENTATION
ER5-1047
Page: 14
Pages: 17
Updating August 2010
Dimension drawing of level switch ERH-03-07
Ver. H [mm] L [mm]
-1 680 510
-2 450 380
Φ14 – 4 holes
at 90
0
tapered

TECHNICAL PRODUCT DOCUMENTATION
ER5-1047
Page: 15
Pages: 17
Updating August 2010
Dimension drawing of level switch ERH-04-07
holes
at
tapered
Φ14 – 4 holes
at 90
0

TECHNICAL PRODUCT DOCUMENTATION
ER5-1047
Page: 16
Pages: 17
Updating August 2010
4.2START-UP AND OPERATION INSTRUCTION
4.2.1 Preparing for start-up
Level switches may be installed in closed rooms or at least protected from weather conditions: rain,
snow, etc., and free from excessive chemical exhalations. After level switch unpacking and inspecting
it should be screwed to the connection pipe, placing the seal between pipe and level switch; it is
recommended to install the level switch with the gland down.
4.2.2 Operation manual
After connecting the electric circuit and checking its correct operation, the level switches do not
require any further operation.
4.3. MAINTENANCE INSTRUCTION
4.4
SAFETY INSTRUCTION
5. STORAGE AND TRANSPORT CONDITIONS
Level switches received from the producer should be stored in rooms free from chemical exhalations
and assuring environment temperature from 5 to 30°C and relative humidity from 30 to 80%. The level switch
technical condition should be checked at least once a year.
Level switches should be stored in the package, assuring protection from mechanical damages.
Level switches are packed in the carton box, drawing no. ER3-1313.
Level switches should be transported in the packages. Pay attention for immobilizing the level
switches during transport.
Level switch should be at least once a year subjected to detailed inspection,
paying attention for technical condition of parts, subjected to fluid influence
(float, bolts, cotter pins, magnet housing, lever, etc.), removing possible
impurities especially from the magnet housing and from the gap between body
and float lever.
For highly contaminated fluids the above activities should be performed more
frequently, in periods defined by the user, during the inspections of the whole
tank and equipment. Forming deposits, e.g. boiler scale, should be removed
mechanically or chemically, paying attention not to damage the level switches
parts.
After performed maintenance install the level switch.
Personnel installing level switches in objects should have general
knowledge of safety requirements and this documentation. Do not
perform level switch installation, when system is live.
Depending on object type and existing protection system the level
switch should be zeroed or earthed.
For this purpose properly marked rod is provided.

TECHNICAL PRODUCT DOCUMENTATION
ER5-1047
Page: 17
Pages: 17
Updating August 2010
6. DELIVERY RANGE
Level switch type ERH-01..-04-07 should be accompanied with:
Technical products documentation,
Declaration of Conformity
Warranty card.
6.1. Spare parts
On Customer’s special demand producer may supply the following spare parts against payment, according
to the ordered level switch type.
Table no. 2
No.
Spare part name Level switch type
ERH-01-
07 ERH-02-
07 ERH-03-
07 ERH-04-
07
1. Micro-switch type 83140 1 pc. 1 pc. 1 pc. 1 pc.
2. Float, drawing no. ER2-1024 1 pc. 1 pc. 1 pc. -
3. Float, drawing no. ER2-0565 - - - 1 pc.
4. Joint covering, drawing no. ER1-
1120 - 1 pc. - -
7. WARRANTY CONDITIONS
Warranty conditions are defined by the warranty card, effective in the Aplisens - Controlmatica
Ostrów Wlkp Poland company, attached to each level switch.
ATTENTION: The right of introducing design changes in the product, without deteriorating of its
operation parameters, is reserved.
Table of contents
Popular Switch manuals by other brands
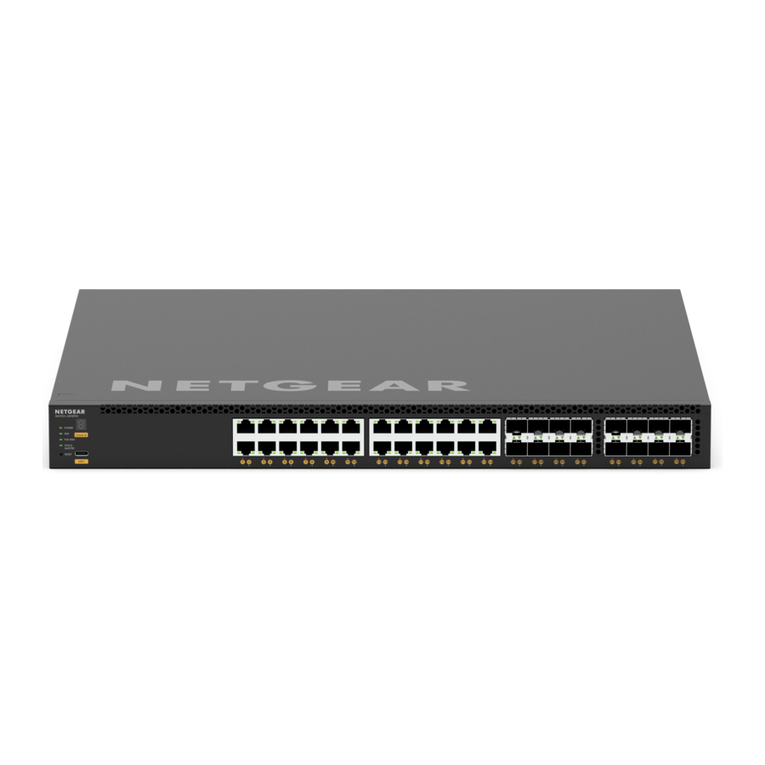
NETGEAR
NETGEAR M4350 Series installation guide
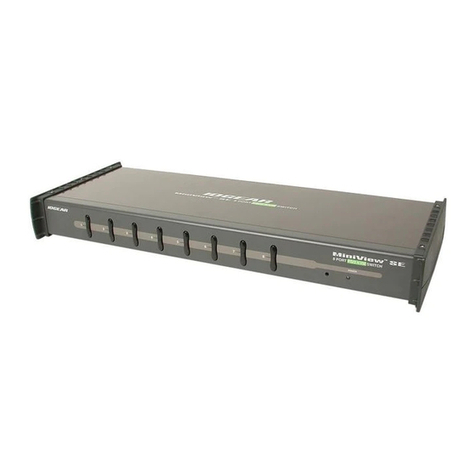
IOGear
IOGear MiniView Ultra GCS138 installation manual
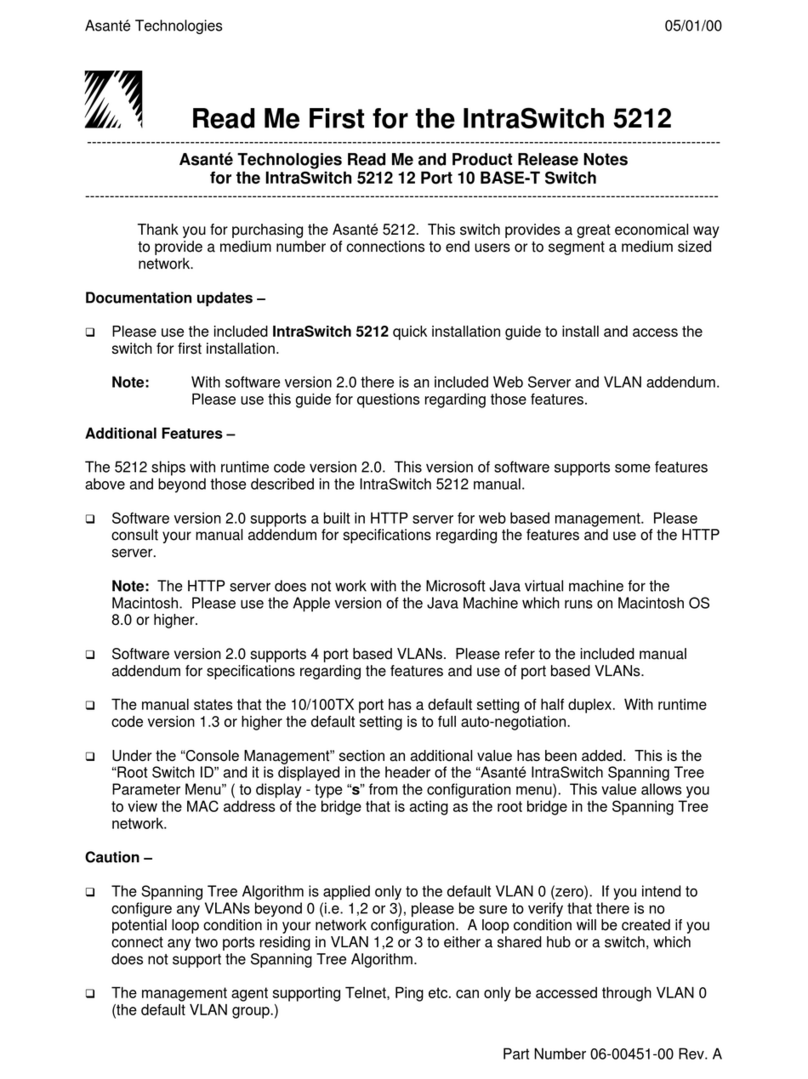
Asante
Asante IntraSwitch 5212 Product release notes
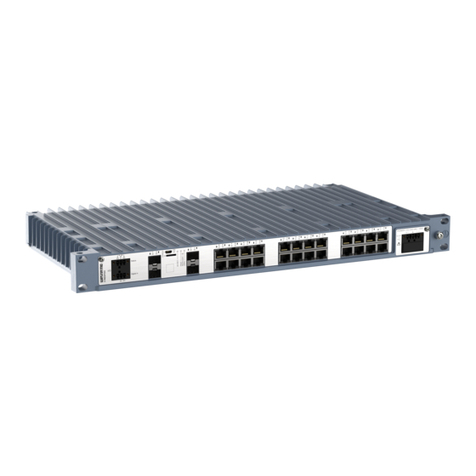
Westermo
Westermo RedFox 7528 Series user guide
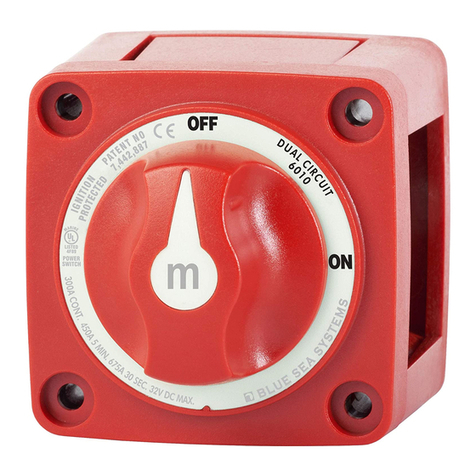
Blue Sea Systems
Blue Sea Systems Dual Circuit 6010 user manual
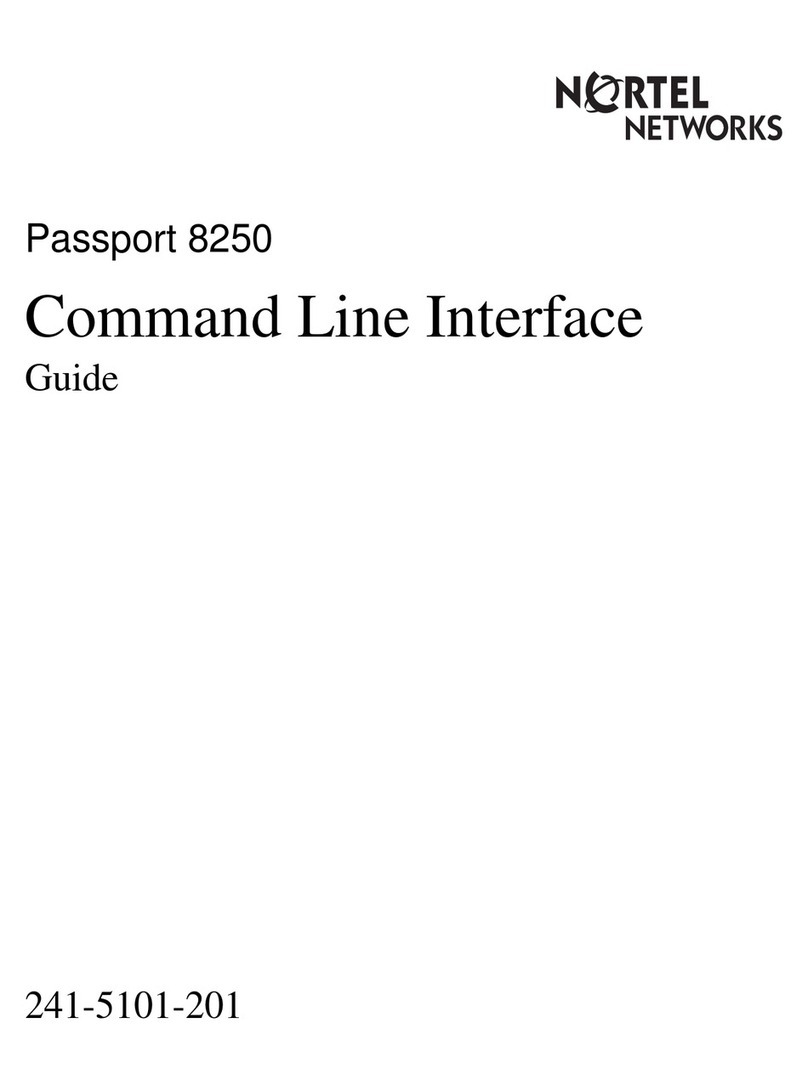
Nortel
Nortel Passport 8250 Command line interface guide