ASP FSPO Manual

IOMFSPO 0515 American Stainless Pumps
Installation, Operation and Maintenance Instructions
Model FSPO
Description and Specifications: The Model FSPO is a close-coupled, end suction, single stage, open impeller, back
pullout centrifugal pump. Connections are NPT threaded. All wetted metal pump parts are 304SS or better. Most parts
are forged from stainless steel sheet. The seal plate is made of fiberglass reinforced Ryton. Standard O-rings and
elastomeric seal parts are Buna. Viton and EPR are optional. Motors are NEMA 56J frame, with a C-Face mounting
flange and a threaded shaft. All pumps use a mechanical seal to prevent leakage around the motor shaft.
Operating limits: The model FSP is designed for a maximum pressure of 50 PSIG, at a maximum temperature limit of
212F. Motor is limited to 20 starts per hour, evenly distributed.
Notice: Upon receipt of this equipment, inspect the carton and the equipment for any damages that might have
occurred during shipment and notify the carrier immediately. Damage that occurs during shipment is not the
responsibility of American Stainless Pumps. Failure to notify the carrier will place responsibility on the purchaser for any
repairs or damages occurring during shipment.
Safety Instructions: To avoid serious or fatal injury and/or property damage, read and follow all
instructions in this manual. Review all instructions and warnings included in this manual before
attempting any work on this pump or pump/motor assembly. Do not remove or alter any decals.
The motor used to drive this pump is an electrical device connected to a potentially lethal voltage
power source. Take all precautions required when working with or on the motor and its power source,
including but not limited to:
1. Always disconnect and lockout the electrical power source before attempting any connection, maintenance or
repairs. Failure to do so can cause electrical shocks, burns and death.
2. Install, ground and wire motors in accordance with all local and national electrical codes.
3. Install an all leg disconnect switch near the motor for quick access.
4. The electrical supply must match the motor nameplate specifications and the motor must be wired per the wiring
diagram on the motor to match the selected voltage. Incorrect wiring can cause fire and motor damage and will
void the warranty.
5. Most single phase motors and some three phase motors will have automatic thermal protection switches wired in
the motor. These switches will open and stop the motor if the motor overheats. As the motor cools, these switches will
close and start the motor automatically and unexpectedly.
6. Motors that do not have thermal overloads must have a properly sized contactors or magnetic starters and
overload switches (or fuses) in the starter panel. Three phase motors require all leg protection.
7. Use only stranded copper wire to motor and ground. Wire size must limit the maximum voltage drop to 10% of
the motor nameplate voltage at the motor terminals.
8. Three phase motors can rotate in either direction. The pump will operate properly only in one direction
(clockwise when looking from the motor end, counter-clockwise when viewed from the pump end). Operating the pump
in the reverse rotation may damage or destroy the pump and motor and voids the warranty.
Installation:
-Locate the pump as near to the liquid source as possible. The pump must be primed with little or no air in the case to
begin operation. The pump must be located below the liquid level when starting. This pump is not self priming.
-Protect the pump and motor from freezing. Although the pump may survive a freeze up, the mechanical seal and O-
Rings will not.
-Allow adequate space around the unit for service and ventilation.
-Units may be installed horizontally, at an angle or vertically with the motor on top. Do not mount the motor below the
pump as leakage from the pump will damage the motor and can cause a shock, burns or death.
-Units mounted horizontally should be located on a flat, rigid surface. Unit may be free standing, but some vibrations
may occur. If attached to a foundation, tighten hold down bolts before connecting the piping.
Page 1 of 5

Piping:
All piping must be independently supported. No piping loads may be carried by the pump.
Piping should be the same size or larger than the pump connections.
Proper Piping to the suction is critical for proper pump operation.
-Suction pipe should be short and direct, with a minimum of fittings and turns.
-Suction pipe must continuously rise to the pump to avoid air pockets. All pipe connections must be air tight.
-If suction pipe is larger than the pump, an eccentric reducer must be used with the straight side on top to avoid an air
pocket.
-If suction of pump is above the liquid source level, a foot valve or other isolation valve will be needed to prime the pump.
A continuous stream of liquid must be made available for the pump suction to hold its prime.
-Do not use a suction valve for throttling the pump. This will cause loss of prime and damage to the pump that is not
covered by warranty.
-Be sure that the source liquid level is sufficient to prevent vortices from drawing air into the pump.
-Install a valve on the discharge line for use in regulating the pump flow and for isolating the pump during maintenance
and inspection.
Rotation:
The model FSP will operate properly only in one direction (clockwise when looking from the motor
end, counter-clockwise when viewed from the pump end). Operating the pump in the reverse
rotation may cause the impeller to unscrew, breaking the shaft, damaging the pump and/or
the motor and voids the warranty.
-Three phase motors can rotate in either direction. Single phase motors normally only rotate in the proper direction.
-To check rotation, you must observe the motor shaft or fan from the back of the motor. Remove the end cover from the
center of the back of the motor by prying off the cap. You do not need to remove any screws on most motors. Quickly
switch on and off the motor and watch the shaft rotation as it slows down. Motor shaft should be turning in the clockwise
direction when viewed from the back of the motor.
-If motor is turning in the wrong direction, have a qualified electrician interchange two of the three motor power wires.
This should reverse the rotation.
-Check the rotation again. If it is correct, replace the end cover cap.
Operation:
-Pump must be completely primed before starting. Air in the suction lines or case must be vented.
-Do not operate the pump at or near zero flow. At zero flow, heat will build up in the pump and can cause extreme
damage to the pump, property damage and/or possible injury to operating personal. Minimum flows of 10% of the
pumps best efficiency point are recommended unless otherwise authorized by ASP.
-Do not operate the pump beyond the flow rates shown on published curves. Noisy pumps or the sounds of “pumping
rocks” may be signs of cavitation or operation beyond the pumps capacity.
-Check pump and motor for vibration. Vibration may be a sign of pipe strain, insufficient mounting or operation beyond
the pumps capacity.
Maintenance:
There is no scheduled maintenance required. Close-coupled pumps have no bearings. Bearings in the motors are
permanently grease lubricated and cannot be regreased. Mechanical seals will need to be replaced when leaking.
O-Rings may harden with age and may need to be replaced when they leak.
Motor Bearings and Pump Thrust:
-Open impellers generate significantly more thrust than do enclosed impellers. The Model FSP with a 4.38” diameter
impeller operating at 20 psig generates about 150 pounds of thrust. The motor bearing carries this thrust load.
-The standard jet pump motor and the standard FSP motor uses as a front and rear bearing a size 203 grease lubricated
bearing. This bearing has a B10 rated life of approximately 6,000 hours when operated with a thrust load of 150 pounds
at 3500 RPM. This rating means that 10% of all bearings operated in this condition will fail within 6,000 hours of
operation. The average bearing life will be 3 to 4 times this 6,000 hours.
-Pumps and motors that operate intermittently, or only operate 40 hours per week, will usually have acceptable bearing
lives with the standard jet pump motor bearing. Pumps that operate continuously, 24 hours per day, will have about 10%
of their thrust bearings fail in the first year of operation.
-Pumps operating at 1750 rpm do not have these thrust limitations.
-For service applications that are critical, for installations that are difficult to access, for pumps operating at
differential pressures above 25 psig, or for open impellers larger than 4.38”diameter, American Stainless
Pumps recommends that motors with larger thrust bearings and higher load ratings be used.
aspiomfspo 0415 Page 2 of 5

Disassembly: Disconnect and lockout the electrical power before attempting any disassembly.
Casing may contain hazardous fluids. Drain and flush and take necessary precautions.
It is not necessary to remove piping from the case to disassemble. Pump is a back pull-out design and unless casing
needs to be repaired or replaced, it can stay in place during servicing.
1. Close all valves and drain pump and pipes and flush if necessary.
2. Remove any motor hold down bolts.
3. Remove the four (4) case bolts (Item 7CS) with a 3/8” Allen wrench.
4. Pull the motor and pump internals back out of the case. Remove the case O-Ring and inspect for damage or
hardness. Remove the plastic spacers from the case bolts so they don’t get lost. You will need these spacers later.
5. If the motor is a three-phase motor, a locking screw is used to prevent the impeller from unthreading if started
in the wrong direction. The locking screw is installed with removable Locktite to prevent it from coming out during
operation. The locking screw may have left hand threads or right hand threads depending upon the motor manufacturer.
There should be a label on the pump case indicating the handedness of the locking screw. The screw can be removed
with a 1/8” Allen wrench. Call the factory if you are not certain of the handedness of the locking screw.
6. Remove the impeller by turning the impeller counterclockwise (when looking at the impeller from the pump end)
while holding the motor shaft. It may be necessary to remove the motor shaft cover plate in the center of the rear of the
motor to get access to the shaft. Using a screwdriver, wrench or vise grips, depending upon the motor manufacturer,
hold the shaft tightly against rotation while turning the impeller. Do apply any heat to the components.If you are
unable to hold the shaft in this manner, remove the rear motor housing and grip the motor shaft with vise grips or other
similar device (do not hold shaft where bearings will mount).
-It may be easier to remove the impeller using a screwdriver and a hammer, placing the screwdriver on the impeller vane
and striking a blow with the hammer to unscrew the impeller. The trick is to strike the impeller firmly enough to start the
unscrewing process, but not so hard as to damage the impeller. There is a video link on our website under Products -
Impeller Removal.
7. There may are spacers between the impeller and the motor shaft shoulder. These spacers locate the open
impeller vanes close to the case for efficient operation. Measure the thickness of this stack of spacers for future
reference. Do not lose these washers. You will need them for reassembly.
8. Remove the rotating element of the mechanical shaft seal. This element is held in place by the impeller only. If
the rotating element does not come off easily, it is stuck to the shaft. Use channel lock pliers or a screwdriver to pry the
element off the shaft.
9. Remove the seal plate. It should come off without force. If you plan to replace the stationary seat, you will need
to press it out from the back. Do not push with your finger as you will probably cut it on the edges of the seal plate when
the seal pushes out.
10. If the motor comes with a deflector, the deflector should be left in place or cleaned and replaced.
Assembly or Reassembly
-Assembly of the pump and motor may be easier when the motor is standing shaft up so that parts do not fall off.
-It is considered good practice to replace the mechanical seal and o-rings whenever you have to disassemble the pump.
1. If replacing the motor, and the new motor does not have a deflector, remove the deflector from the old motor
shaft and reuse.
2. Install the mechanical seal stationary seat into the Seal Plate (Item 460) by putting a suitable lubricant on the cup
seat and gently pressing into the seal plate bore. Be sure the seal seat is down all the way and is flat. Do not get
any lubricant on the seal faces. Use the foam sheet from the seal box or a clean rag to protect the seal face from dirt
and scratches while pressing into the seal plate. Place the seal plate onto the motor adapter plate.
3. Lubricate the sealing elastomers on the rotating assembly of the mechanical seal and press gently onto the
shaft. You may have to hold the seal in place until the impeller is installed.
4. Reinstall the spacers on the motor shaft end.
5. Thread the impeller onto the pump shaft. Be sure the impeller hub is tight against the shoulder of the motor
shaft. If you leave the impeller loose, when the motor starts up, the impeller will tighten up on the shaft so tightly that you
may not be able to remove it later. You will need to hold the motor shaft from the rear of the motor with a large
screwdriver, wrench or vise grips while tightening the impeller.
6. If the motor is a three-phase motor, a locking screw is used to prevent the impeller from unthreading if started
in the wrong direction. The locking screw may have left or right threads depending upon the motor manufacturer. Look
for the label on the pump case to determine the handedness of the locking screw or call the factory.
7. Install the case O-Ring. Replace if brittle, damaged or misshapen.
8. Join up the back pull out assembly with the case. Install the (4) case bolts. Insert the spacers onto the case
bolts between the case and the seal plate to reestablish the clearance between the pump case and the impeller. Tighten
the case bolts.
9. Install and tighten the motor base hold down bolts.
10. Install the pump and reconnect the wiring. See electrical warnings above.
11. Check the rotation of the pump by lightly bump starting the motor. Rewire if not rotating in the proper rotation.
aspiomfspo 0415 Page 3 of 5

Assembly (continued)
Setting Impeller Clearance:
-Impeller clearance to the case is critical to pump performance for 2900 or 3500 rpm pumps. It is less important and may
be ignored for 1750 rpm pumps.
-You will get maximum performance and efficiency (and maximum amp draw) with near to zero clearance. Factory
standard clearance is 8 to 12 mils. Spacer/Washers to adjust clearances are available in 10 mil and 15 mil thickness.
-You can have more or less than normal flow and head by changing this clearance. To increase clearance, remove
impeller spacer/washers. To decrease clearance, add impeller spacer/washers. Be aware that if you set the impeller
at near to zero clearance, and operate near maximum flow rates, you may overload the standard motor.
-Standard factory settings for spacers are 25 to 50 mils of spacer/washers to obtain 10 mil clearance. Since the
tolerances of the motor shaft and pump parts can stack up, some pumps may need more or less than this standard.
-Some special OEM assemblies will not have any spacers when the customer elects to accept reduced performance in
return for ease of assembly. The following are several possible methods for setting the clearance:
1. If the pump discharge piping is removed, you can look in the discharge port with a flashlight and see the impeller
to case clearance, and possibly measure it with a feeler gauge.
2. If you haven’t changed the impeller, the motor or the case, you can simply replace or duplicate the
spacer/washer pack that was installed when you disassembled the pump and have the same performance you had
originally.
3. For a rough measurement of spacers required, put one or several 7/16” or 1/2” washers behind the impeller.
Stand the pump vertically, with the impeller facing up. Place the case over the impeller and center it as much as possible
by eye. Measure the gap between the case flange and the seal plate flange in four places around the edges and take an
average. Remove the washers from behind the impeller and measure their total thickness. Subtract the case to seal
plate gap from the total thickness of the washers and you will get a rough estimate of the thickness needed behind the
impeller for a zero clearance. Subtract 10 mil for a standard factory clearance.
4. If you measure the total thickness of a 4.38” diameter impeller, from the face of the vanes at the tips to the back
of the hub behind the impeller, you should get a total thickness of about 0.900 inches. This impeller thickness will require
a washer/spacer pack of approximately 50 mils to get a factory clearance of 10 mils. A larger or smaller impeller
thickness will require fewer or more washer/spacers.
-Always check to make sure the impeller is not rubbing on the case prior to turning on the motor. Turn shaft by hand and
listening for a scraping sound. If you hear scraping, you need to remove washer/spacers from behind the impeller.
-If you are setting the clearances near to zero, be aware that the case and impeller do flex somewhat as pump pressures
change. Higher pressure near shutoff makes the case expand slightly and makes the impeller flex a little more. Some
pumps will rub at shutoff only and some will rub at runout only. The lighter weight and relative thinness of the stainless
steel materials means that the SSP parts are more flexible than a cast pump. Piping loads or poorly mounted motors
can twist the pump and cause the impeller to rub on the case at low clearances. You may have to adjust the piping loads
or increase the clearances to compensate for these conditions.
-Pump cases and impellers are not always perfectly aligned. You may have clearance at the top of the case where you
can measure it through the discharge port and have a rub at the bottom of the case. If you want to run at low clearances,
you may have to put different amounts of spacers on different bolts to correct for this misalignment.
Limited Warranty:American Stainless Pumps (ASP) warrants that its manufactured products are made of first class
materials and in a skillful and workmanlike manner, and when properly installed and maintained, will operate as
proposed in the company’s written documents. This warranty is in effect for a period of two years from shipment. We
will replace or repair any part that does not meet these warranties, FOB the factory.
-ASP will pass through to its customers any warranties granted by the manufacturers of motors and mechanical seals but
does not itself warrant these items.
-There are no other warranties, expressed or implied, except for the warranties given here. ASP does not warranty
against corrosion or erosion of its products when placed in service. Under no circumstances will ASP be liable for any
penalties or any incidental or consequential damages caused by the failure of its products, by late delivery or by any
other causes. This warranty may not be modified verbally by any employee or agent of ASP.
aspiomfspo 0415 Page 4 of 5

American Stainless Pumps
Stainless Steel Pumps for the Commercial Marketplace
www.aspumps.com 14032 S. Avalon Blvd. Los Angeles CA 90061
Phone (310) 630-8089 ~ Fax (310) 630-8095
Model FSP Exploded View.doc
11/29/2011
Model FSP Exploded View
Table of contents
Other ASP Water Pump manuals
Popular Water Pump manuals by other brands

Whale
Whale EP1632 manual
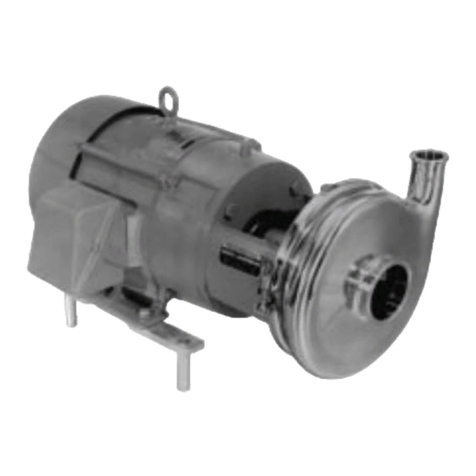
Tri-Clover
Tri-Clover C-Series Service & installation manual
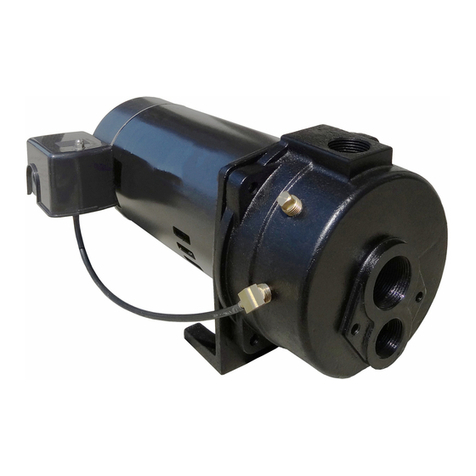
Utilitech
Utilitech EFCWJ10-L manual

Star
Star 148004 operating guide
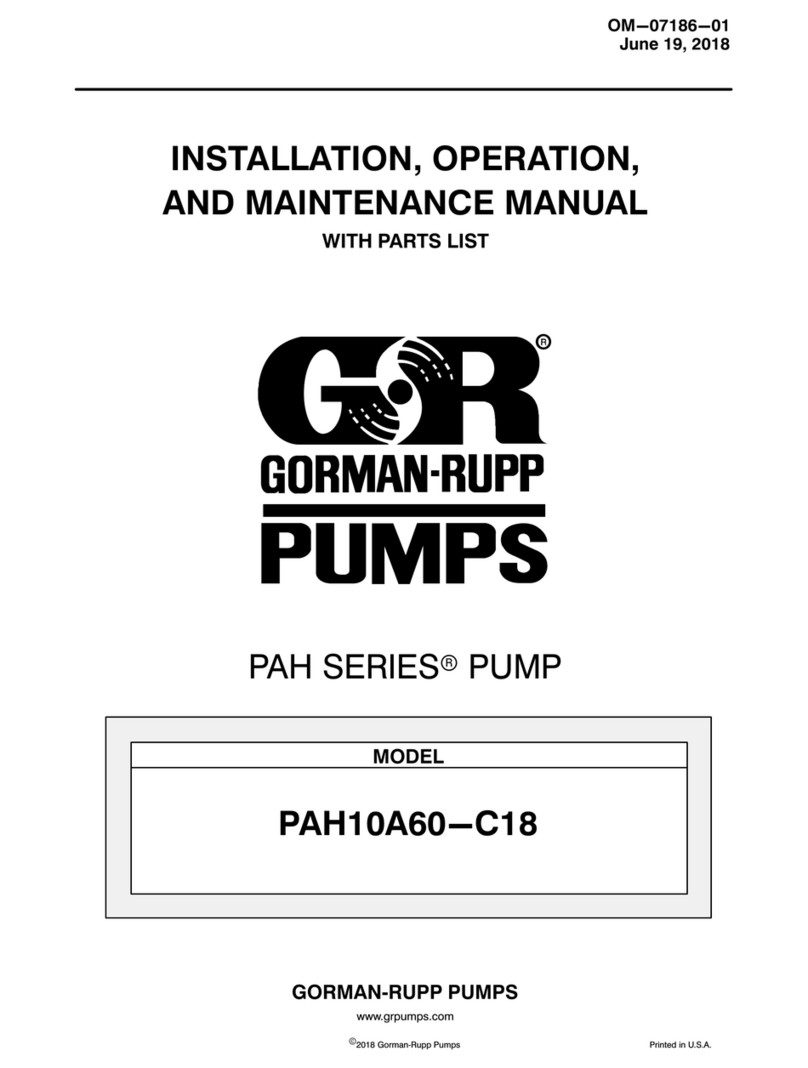
GORMAN-RUPP
GORMAN-RUPP PAH SERIES Installation, operation, and maintenance manual with parts list

ITT
ITT Goulds Pumps i-FRAME 3640 Installation, operation and maintenance manual

BUSCH
BUSCH R 5 series instruction manual
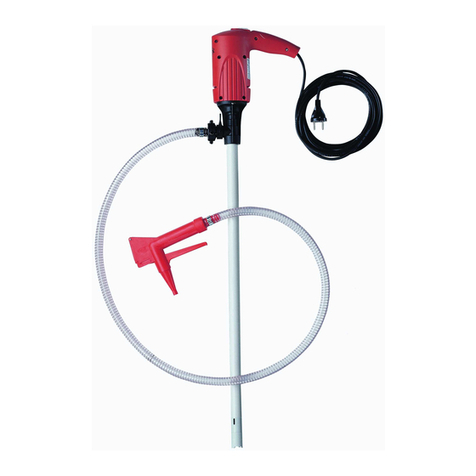
Flux
Flux JUNIORFLUX F310PP operating instructions
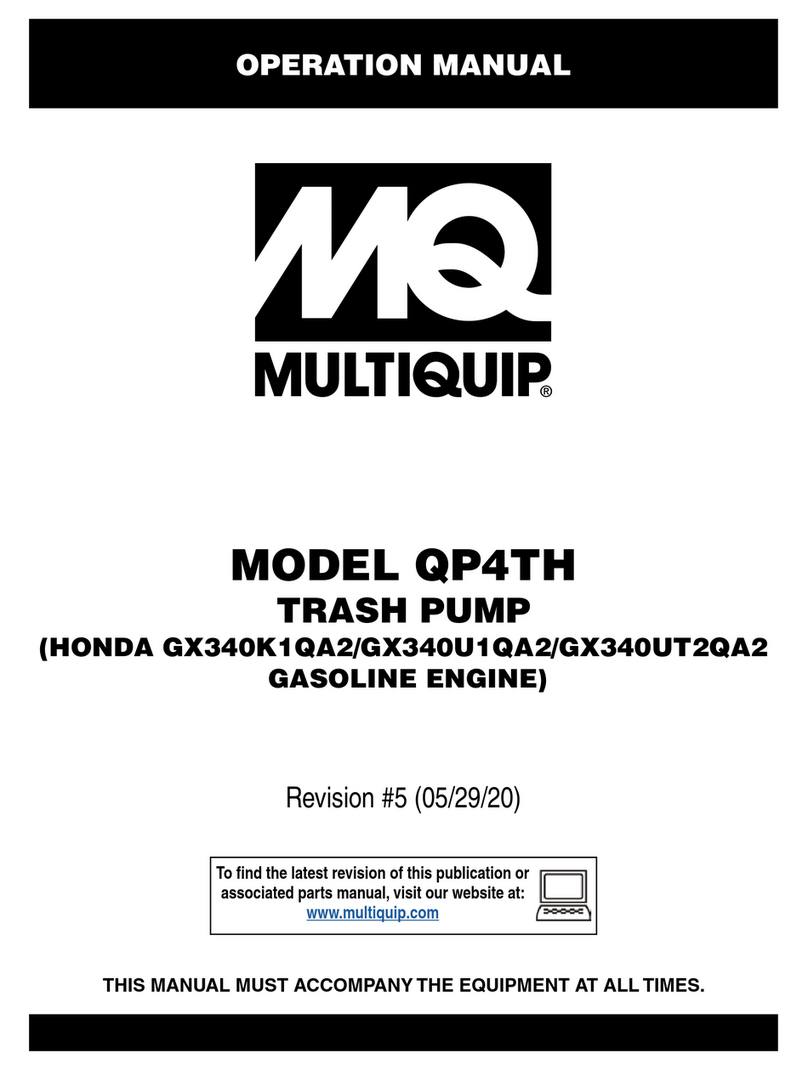
MQ Multiquip
MQ Multiquip QP4TH Operation manual

AMT
AMT 4294-98 Specifications information and repair parts manual

Macnaught
Macnaught BOP20 BP20-PH owner's manual
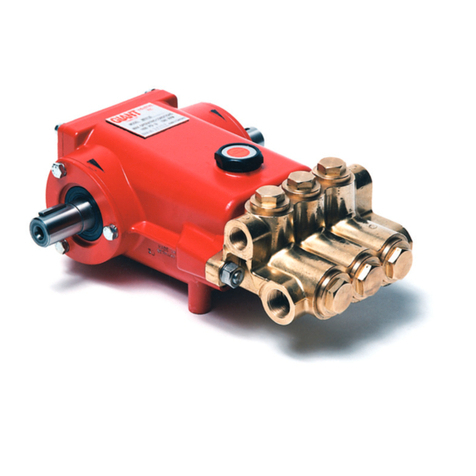
Giant
Giant SP100W Operating instructions/ repair and service manual