AutomationDirect CLICK PLUS C2-03CPU User manual

1
www.automationdirect.com/click-plc
3505 HUTCHINSON ROAD
CUMMING, GA 30040-5860
1-800-633-0405
C2-03CPU Quick Start Guide
Copyright© 2020, Automationdirect.com Incorporated/All Rights Reserved Worldwide
Before You Begin...
This guide provides a quick overview of installation and setup of your
CLICK PLUS CPU. It assumes some familiarity with the installation
and operation of industrial control equipment.
Please read and understand the information in this guide prior to
installation, operation, or servicing this equipment.
The CLICK PLUS User Manual provides full specifications and more
in-depth information on installation, setup,
programming and operation of the device. The
User Manual (C2-USER-M) is available in PDF
format by scanning this QR code or from https://
www.automationdirect.com/pn/doc/manual/
C2-USER-M. Extensive online help is also
available from within the CLICK software or at
https://www.automationdirect.com/clickplcs/free-software/
software-help.
What You’ll Need
CLICK PLUS CPU
PC, or Android or iOS mobile device (for setup/provisioning)
Click Software ver. 3.00 or later (PC) or Click App (mobile device)
24VDC power supply (SELV and Limited Energy)
(CLICK power supply C0-00AC or C0-01AC is recommended.)
Appropriate enclosure with vertical surface for DIN rail or surface mount
M4 screws, spring washers and flat washers if surface mounting
Ferrules and crimping tool for wire terminations (recommended)
An Option Slot cover (part #C2-FILL) is recommended if you are not
planning to use an Option Slot module. (Sold separately.)
Basic tools (screwdriver, wire stripper, etc.)
PLEASE REVIEW THE SAFETY WARNINGS ON THE
NEXT PAGE!
CLICK PLUS C2-03CPU
The CLICK PLUS C2-03CPU has the most
connectivity options in our CLICK PLUS
CPU family. It offers both Wi-Fi and Bluetooth
connection for simple wireless provisioning and
connectivity with the CLICK Mobile app. With
both RS-232 and RS-485 ports, you can connect
multiple serial devices. The RJ-45 Ethernet
port allows for a separate (secondary) network
connection apart from the Wi-Fi network.
Key Features
Real Time Clock/Calendar
Battery backup (battery sold separately)
RS-232 port
RS-485 port
micro-B USB port
microSD Card slot
RJ-45 Ethernet
WLAN
Bluetooth
Shown with optional C2-FILL
slot cover (sold separately)

2
www.automationdirect.com/click-plc
3505 HUTCHINSON ROAD
CUMMING, GA 30040-5860
1-800-633-0405
C2-03CPU Quick Start Guide
Copyright© 2020, Automationdirect.com Incorporated/All Rights Reserved Worldwide
Safety Warnings
Please follow these instructions for personal and operational safety.
WARNING Assumes that incorrect handling may cause hazardous
conditions, resulting in severe injury or death.
CAUTION Assumes that incorrect handling may cause hazardous
conditions, resulting in medium or slight injury, or
may cause equipment damage.
WARNING
Don’t use this equipment in a flammable or explosive
environment in order to avoid accidental injury or fire.
You should use external electromechanical devices that are
independent of the PLC (Programmable Logic Controller)
system to provide protection for any part of the system;
otherwise malfunction or output failures may result in a
hazardous accident.
24VDC power is required from a secondary circuit or a specific
power supply unit only.
Ensure the Ground Terminal of the Power Supply (C0-00AC/
C0-01AC) for the CLICK PLUS CPU is connected to Earth
Ground to avoid electric shock or equipment damage during a
short circuit.
Don’t operate the equipment with a nonconforming external
power supply to avoid electric shock, equipment damage or fire.
Don’t intentionally fault the wiring; this may cause equipment
damage or fire.
To avoid electric shock or malfunctions which might result in an
accident, don’t touch any terminal while the PLC power is on.
Don’t put metals (e.g. screwdriver) into vent holes, or drop trash
or foreign objects (e.g. wire cut-offs) into the device, in order to
avoid electric shock or equipment damage.
If the equipment is used in a manner not specified by the
manufacturer, the protection provided by the equipment may be
invalidated.
CAUTION
For use in Pollution Degree 2 Environment. Use and store the
equipment in an environment described in the specifications
(regarding temperature, humidity, vibrations, shock, etc.) in
order to avoid equipment damage or fire.
Ensure all wiring has strain reliefs in order to avoid damage to
insulation that might result in electric shock or fire.
Ensure secondary external power circuits are only live after PLC
control program is started; otherwise a malfunction or output
failure may result in a hazardous accident.
Don’t block the vent holes. This may cause an increase of inter-
nal temperature resulting in equipment damage or fire.
Don’t disassemble or modify equipment so as to avoid electric
shock, equipment damage, or fire.
Cut off all phases of the external power source before mainte-
nance work, thus avoiding electric shock or equipment damage.
Hardware Installation
ENCLOSURES
It is important to select the appropriate enclosure to ensure
safe and proper operation of your CLICK PLUS PLC
system. Please use this product in a metal enclosure/cabinet.
Control applications vary and yours may require additional
considerations. At a minimum your enclosure should include:
Conformance to electrical standards
Protection from the elements in an industrial environment
Common ground reference
Maintenance of specified ambient temperature
Access to equipment
Security or restricted access
Sufficient space for proper installation and maintenance of
equipment
CLEARANCES AND ORIENTATION
Mount the unit horizontally to
provide proper ventilation.
There is a minimum clearance
requirement of 2in. (51mm)
from all sides of the cabinet and
the equipment.
There is a minimum clearance
requirement of 1.5 in. (38mm)
from the wiring ducts and the
equipment
Do not mount the unit upside down, on a horizontal surface, or
in a vertical arrangement.
Minimum clearance requirement
of 51mm for A, B, and C.
Air
Flow
TX2
PORT2
PORT1
RX2
RX1
TX1
PWR
ERR
RUN
STOP
RUN
Air
Flow
TX2
PORT2
PORT1
RX2
RX1
TX1
PWR
ERR
RUN
STOP
RUN

3
www.automationdirect.com/click-plc
3505 HUTCHINSON ROAD
CUMMING, GA 30040-5860
1-800-633-0405
C2-03CPU Quick Start Guide
Copyright© 2020, Automationdirect.com Incorporated/All Rights Reserved Worldwide
Hardware Installation, continued
CAUTION
Discharge static electricity before installation or
wiring in order to avoid electric equipment damage.
MOUNTING
The CLICK PLUS can be mounted on DIN rail or surface
mounted using built-in mounting tabs.
When installing on DIN
rails, always use end brackets
on both ends of assembly.
(AutomationDirect p/n DN-EB35)
Use 35mm width DIN Rails.
Use M4 size screws when you
surface mount.
Tighten the screws with a spring
washer and a small round washer
and torque 0.5 to 0.6 N·m.
ANTENNA MOUNTING
The CLICK PLUS CPU uses a single 2.4 GHz antenna for
both Bluetooth and wireless LAN connections. It can use an
SE-ANT210 direct-mount antenna, but for a continuous
WLAN connection from within a metal enclosure an
SE-ANT250 remote-mount antenna is recommended.
Click
Pull tab
down.
Push tab
up until...
DIN Rail Mounting
Upper
Mounting Tab
Lower
Mounting Tab
Surface Mounting
SE-ANT250 Remote-mount antenna
WIRING
24VDC power is supplied to the CLICK PLUS CPU through
wiring connected from the power supply output to the 4-pin
connector located on the bottom of the CPU unit.
16–28 AWG wiring is supported. We recommend using
crimping ferrules on all wire terminations for a more secure
connection. The following crimping ferrules are recommend-
ed for the 24VDC power terminals.
Company
Type Model No. Compliant Wire
AutomationDirect
Ferrule V30AE000009
V30AE000041 0.2–0.5 mm2(22–26AWG)
* Maximum tightening torque is 0.22 to 0.25 N·m.
Take care not to contact adjacent terminal.
Please use SELV (as defined by UL61010-2-201) and Limited
Energy (as defined by UL61010-1, 9.4) power supply.
CLICK power supply C0-00AC or C0-01AC is recommended.
CAUTION
Do not operate without first installing safety
cover over power supply
leads.
CAUTION
DO NOT USE the PF connector. Leave this terminal
unconnected. Connecting the PF terminal to another
device may cause damage to the CLICK PLUS CPU.
Power supply symbols listed on the equipment are indicated
by the symbols shown below.
Name
Description Symbol
DC
Direct current IEC6047 No. 5031
G
Functional earthing IEC6047 No. 5017
CAUTION
Safety instruction for
battery replacement ISO 7000 No.0434B
I/O wiring is discussed in each module’s documentation.
24VDC
0V
unused
G
24VDC
0V
G
CLICK PLUS CPU
CLICK Power Supply
24VDC power is supplied to the CPU unit through wiring connected from
the power supply output to the 4-pin 24VDC input connector located on the
bottom of the CPU unit.
OPTION SLOT MODULE (OPTIONAL)
STACKABLE MODULES
(OPTIONAL)

4
www.automationdirect.com/click-plc
3505 HUTCHINSON ROAD
CUMMING, GA 30040-5860
1-800-633-0405
C2-03CPU Quick Start Guide
Copyright© 2020, Automationdirect.com Incorporated/All Rights Reserved Worldwide
1
3
Power 10+ minutes
2Remove Power
4
5
INSTALL OR REMOVE THE OPTION SLOT MODULE INSTALL OR REMOVE STACKABLE MODULES
1. Slide the expansion port LOCK lever to “UNLOCK” and
remove bus cover.
2. Align I/O module with right hand side of CPU, engaging bus
connector so that modules are flush.
3. Slide the “LOCK” lever firmly towards rear of modules, locking
them together.
1
2
3
To remove a module, work the installation steps in reverse.
INSTALL OR REPLACE THE BATTERY
(Lithium CR2032 battery, Part # D0-MC-BAT, not included)
1. Power up the CPU for at least 10 minutes to charge the CPU’s
capacitor prior to removing the
battery. This will retain function
memories. We recommend you
backup data memory before
replacing the battery.
2. Power off the CPU.
3. Pull out the battery holder. (This
may require a small screwdriver to
push in the tab and lift it when the
unit is mounted.)
4. Put in a new battery, with the
positive (+) polarity side facing the
battery holder.
5. Insert the battery holder into the
CPU and push it all the way in.
6. Power on the CPU.
Battery life is about 3 years. Replace
battery within 10 minutes of power off.
Hardware Installation, continued
1 Remove the Option Slot Cover (#C2-FILL)
if it was installed in the CPU, by grasping its
top and bottom front corners, squeezing and
pulling it forward.
2 Hold the
Option Slot
Module by the
top and bottom front
corners, align the PCB card
edge with the guide slots in the
CPU, and slide the module into
its slot. Press the module into place until it is
fully seated
3 Push the top and bottom locking clips
backward until they click into place.
Lift slightly on the locking clips until they
release, then slide each clip forward.
Reverse the procedure.
To install an Option Slot ModuleTo install an Option Slot Module
To remove an Option Slot Module
To remove an Option Slot Module
1 Remove the Option Slot Cover (#C2-FILL)
if it was installed in the CPU, by grasping its
top and bottom front corners, squeezing and
pulling it forward.
2 Hold the
Option Slot
Module by the
top and bottom front
corners, align the PCB card
edge with the guide slots in the
CPU, and slide the module into
its slot. Press the module into place until it is
fully seated
3 Push the top and bottom locking clips
backward until they click into place.
Lift slightly on the locking clips until they
release, then slide each clip forward.
Reverse the procedure.
To install an Option Slot ModuleTo install an Option Slot Module
To remove an Option Slot Module
To remove an Option Slot Module
1 Remove the Option Slot Cover (#C2-FILL)
if it was installed in the CPU, by grasping its
top and bottom front corners, squeezing and
pulling it forward.
2 Hold the
Option Slot
Module by the
top and bottom front
corners, align the PCB card
edge with the guide slots in the
CPU, and slide the module into
its slot. Press the module into place until it is
fully seated
3 Push the top and bottom locking clips
backward until they click into place.
Lift slightly on the locking clips until they
release, then slide each clip forward.
Reverse the procedure.
To install an Option Slot ModuleTo install an Option Slot Module
To remove an Option Slot Module
To remove an Option Slot Module
1 Remove the Option Slot Cover (#C2-FILL)
if it was installed in the CPU, by grasping its
top and bottom front corners, squeezing and
pulling it forward.
2 Hold the
Option Slot
Module by the
top and bottom front
corners, align the PCB card
edge with the guide slots in the
CPU, and slide the module into
its slot. Press the module into place until it is
fully seated
3 Push the top and bottom locking clips
backward until they click into place.
Lift slightly on the locking clips until they
release, then slide each clip forward.
Reverse the procedure.
To install an Option Slot ModuleTo install an Option Slot Module
To remove an Option Slot Module
To remove an Option Slot Module
CAUTION
Cut off all phases of the power source externally and wait 5 seconds before installing or removing the Option Slot
module or Stackable I/O of a running system.
CAUTION
Battery may explode if mistreated.
Do not recharge, disassemble, or dispose of in fire.

5
www.automationdirect.com/click-plc
3505 HUTCHINSON ROAD
CUMMING, GA 30040-5860
1-800-633-0405
C2-03CPU Quick Start Guide
Copyright© 2020, Automationdirect.com Incorporated/All Rights Reserved Worldwide
Setup & Provisioning via Bluetooth
The C2-03CPU can be configured over a Bluetooth, Ethernet
or micro USB connection. You will need a Windows®PC or
a mobile device (iOS or Android) and a appropriate antenna
or cable for the method you choose. This guide covers the
simplest cases—setting up a new CLICK PLUS device using
a mobile device over a Bluetooth connection or setup over
USB connection to a PC. For other setup and provisioning
methods, including the use of preconfigured provisioning files,
please see the CLICK PLUS User Manual or Software help file.
Connection Requirements
Method
Requirements
Bluetooth
2.4 GHz antenna* (SE-ANT210 or SE-ANT250)
* A remote-mounted antenna is recommended to connect with the enclosure closed.
PREPARE A MOBILE DEVICE FOR CONNECTION
Install the CLICK PLUS Provisioning App using one of
the QR codes below, or search for the app in the appropri-
ate app store (CLICK PLUS Provisioning, published by
Automationdirect.com).
FIND THE NEW CPU
Connect to the CPU as follows:
1. Open the CLICK PLUS Provisioning App.
2. Tap Start in the App.
3. Cycle power on the CLICK PLUS CPU or press the Pairing
button on the CLICK PLUS CPU for 1 second. (A factory-
default CPU will be in pairing mode for 30 seconds after power
is applied.) The blue BT LED will start flashing.
4. The App will find the CLICK PLUS PLC that’s in Provisioning
mode. The blue BT LED will be ON solid when the App is
connected to the PLC. Tap Next in the App to continue.
5. If the App detects that the PLC is factory new and the network
settings have not been configured, it will prompt you to Tap
Next to begin the provisioning process.
Apple Store Google Play Store
Pairing
Button
BT LED
Flashing

6
www.automationdirect.com/click-plc
3505 HUTCHINSON ROAD
CUMMING, GA 30040-5860
1-800-633-0405
C2-03CPU Quick Start Guide
Copyright© 2020, Automationdirect.com Incorporated/All Rights Reserved Worldwide
NAME THE CPU AND SELECT A PORT
6. Enter a name for the CPU and tap Next. Choose a unique name
if other CLICK PLCs are on your network.
7. Choose which network port to provision (wired or wireless).
CONNECT TO A WIRELESS ACCESS POINT
(SKIP FOR WIRED CONNECTION)
You will need an active Network Access point available within range
of the CLICK PLUS PLC, and know the password to allow the PLC
to connect to the Network.
8. The CLICK PLC will scan for any access point within range.
Select an Access Point and type in the correct password that the
PLC will need to connect.
SET UP NETWORK PARAMETERS
9. Once the PLC is connected to the wireless access point or wired
network, choose which IP address configuration to use, then
tap Next to continue.
9a. Use DHCP: Automatically assign a network IP address to
the CLICK PLUS PLC. This is often the simplest way to
connect.
9b. Use Default Fixed Address:
Wireless: 192.168.0.11 Wired: 192.168.0.10
9c. Use the following IP address: Manually enter valid IP
address, subnet mask, and gateway for your network.
10.The CLICK PLUS will connect to the network and exchange
configuration information. If the settings are correct, the App
will show the Completion screen and the network settings
of the CLICK PLUS can be viewed. If using a wireless
connection, the CLICK PLUS WLAN LED will also be ON.
The PLC is now connected to the network and accessible to PCs
running the CLICK Programming Software and connected to the
same network.
Setup & Provisioning via Bluetooth, continued

7
www.automationdirect.com/click-plc
3505 HUTCHINSON ROAD
CUMMING, GA 30040-5860
1-800-633-0405
C2-03CPU Quick Start Guide
Copyright© 2020, Automationdirect.com Incorporated/All Rights Reserved Worldwide
External Features
W
tts
micB
pn ot
(fpot )
(10/100)
tt
Pt
R
Pt
R485
pnsion
Connto
Wtnt
Pow
Tmin
By
(p)
Mic
C2-03CPU
Blink
LNK/ACT LED (Green)
On Connected to the network
Communicating
Disconnected from the network
Off
100MBIT LED (Orange)
On Communicating at 100Mbps
Communicating at 10Mbps or
disconnected from the network
Off
TX & RX LED (Green)
On Com Port Data Active
No CommunicationOff
ERROR LED (RED)
On Self Diagnostic
Error
Self Diagnostic
Warning
No ErrorOff
Blink
WLAN LED (Green)
On Link
Activity
No Link
Off
Blink
MICRO SD LED (Green)
On Mounted
Access
No SD Mounted
Off
Blink
POWER LED (Green)
On Power Good
USB Low
Power Mode
Power Failure
Off
Blink
BLUETOOTH LED (Blue)
On Link
Activity (per packet)
Blink
Disabled in PLC
(200ms flash)
No Link
Off
Blink
Pairing Mode
(500ms flash)
Blink
RUN LED (Green)
On CPU Run Mode
Initializing
Analog Module
CPU Program
Mode
Off
Blink
LED Status Indicators
Connecting via USB
To connect the CLICK PLUS CPU to a PC, use a USB A
to USB micro-B cable, such as the AutomationDirect
USB-CBL-AMICB6 cable.
1. Connect the cable between the CPU micro-B port and an
available USB port on your PC.
USB Cable
ADC Part #
USB-CBL-AMICB6
PC with
USB A Port
USB B
Port
CLICK Plus
PLC
2. Once connected open the Software and select the PLC Menu
and Connect.
3. In the Connect to PLC Window, select USB for Port Type.
4. For Com Port No., select the COMX (CLICK PLUS).
LOAD A PROJECT
The CLICK PLUS CPU is now ready to continue
configuration using the CLICK software and load a project.

8
www.automationdirect.com/click-plc
3505 HUTCHINSON ROAD
CUMMING, GA 30040-5860
1-800-633-0405
C2-03CPU Quick Start Guide
Copyright© 2020, Automationdirect.com Incorporated/All Rights Reserved Worldwide
Technical Specifications
Wireless LAN (WLAN) Specifications
Standard
IEEE 802.11/b/g/n
Frequency
2.4 GHz
Maximum Transmitting
Power
20.5 dBm (112mW)
Transmission Distance
Up to 30m with no interference
Line Speed
Up to 150 Mbps
WLAN Mode
Station
Security
WPA/WPA2/WPA2-Enterprise/WPS
Encryption
AES/RSA/ECC/SHA
Antenna
External
RF Certication
FCC/CE(Red)/IC/MIC/AS/NZS
Status Lamp
WLAN(Green)
Bluetooth Specifications
Standard
IEEE 802.15.1 v4.2 Bluetooth Low Energy
Frequency
2.4 GHz
Maximum Transmitting
Power
0 dBm (1mW)
Transmission Distance
Up to 10m
Line Speed
Up to 1 Mbps
Antenna
External
Association Certication
Bluetooth SIG
Pairing
Yes
RF Certication
FCC/CE(Red)/IC/MIC/AS/NZS
Status Lamp
BT (Blue)
Ethernet Port Specifications
Communications Ratings
10/100 Base-T
Cable Specications
Category 5
Auto MDI/MDI-X
Yes
Connector
RJ45
Address Settings
IP address assigned by DHCP
àFallback on DHCP failure: 169.254.x.x (APIPA)
Default Fixed Address:
àIP Address: 192.168.0.10
àSubnet Mask: 255.255.0.0
àDefault Gateway: 0.0.0.0
Manually congured Fixed Address
Status Lamp
LINK/ACT, 10/100
Power Specifications
Power Input Voltage Range
20–28 VDC Class 2
or SELV(Safety Extra-Low Voltage)
or Limited Energy Circuit power supply
Maximum Power Consumption
20W
Maximum Inrush Current
30A @ 1ms
Acceptable External Power Drop
Max 10ms (AC Power Failure with
C0-00AC or C0-01AC)
Wire Range
16–28 AWG
Wire Strip Length
7.0 mm
Wire Specication
Lead-free, heat resistant,
polyvinyl chloride insulated copper wire,
rated over 80°C
Screw Torque
2.0–2.2 lb-in [0.22–0.25 N·m]
24VDC Power Terminal Block
Replacement
AutomationDirect p/n C0-4TB
General Specifications*
Operating Temperature
32°F to 131°F (0°C to 55°C)
Storage Temperature
–4°F to 158°F (–20°C to 70°C)
Ambient Humidity
30% to 95% relative humidity (non–condensing)
Altitude
Up to 2,000m
Environmental Air
No corrosive gases
Pollution Degree 2 (UL840)
Environment
For Indoor Use Only
Weight
114g (4.0 oz)
Agency Approvals
UL61010 (File No. E157382, E316037);
CE (EN61131-2);
CUL Canadian C22.2
Radio Standards
FCC part15C (US)
RED Article3.2 (CE)
IC RSS-247 (Canada)
MIC Item 19 of Article 2-1. (Japan)
AS/NZS 4268 (Australia and NEW ZEALAND)
Other
RoHS 2011/65/EU Amendment (EU)2015/863
Bluetooth SIG, SD associate
* Isolate from shock, vibration and electric or ferromagnetic eld.
Keep out iron powder, moisture, oil or chemicals.
Indoor use only. Keep out of direct sunlight.
Please see User Manual for full environmental specications.
Meets EMC and Safety requirements. See the Declaration of Compliance for details.
Micro SD Card Slot Specifications
Type
microSD microSDHC
Format
FAT16 FAT32
Capacity
128MB to 2GB 4GB to 32GB
Status Lamp
MOUNTED/ACCESS

9
www.automationdirect.com/click-plc
3505 HUTCHINSON ROAD
CUMMING, GA 30040-5860
1-800-633-0405
C2-03CPU Quick Start Guide
Copyright© 2020, Automationdirect.com Incorporated/All Rights Reserved Worldwide
USB Programming Port Specifications
Communications Ratings
USB 2.0 Full Speed (12Mbps)
Connector
Micro USB Type B
Bus Power
USB Low power Mode: Max. 500mA USB power
supplied when USB cable is connected.
Disabled Functions:
SD card access
WLAN
Bluetooth
Stackable I/O
RUN Mode
Recommended Cable
AutomationDirect p/n USB-CBL-AMICB6
USB Cable Length
Max 15 ft.
Backup Battery Specifications
Type
CR-2032
(AutomationDirect #D0-MC-BAT recommended)
RS-232 Port Specifications
Communications Ratings
RS-232C
Port Settings
Baud rate: 2400, 4800, 9600, 19200, 38400,
57600, 115.2k bps
Data bits: 7 bit, 8 bit
Parity: None, Odd, Even
Stop bits: 1 bit, 2 bits
Connector
RJ12 phone jack
Power Supply to HMI
Supply 5V 200mA
Status Lamp
RX, TX
RS-485 Port Specifications
Communications Ratings
RS-485
Port Settings
Baud rate: 2400, 4800, 9600, 19200, 38400,
57600, 115.2k bps
Data bits: 7 bit, 8 bit
Parity: None, Odd, Even
Stop bits: 1 bit, 2 bits
Connector
3-wire terminal block
Terminal Type
Removable connector
(AutomationDirect p/n C0-03TB or equiv.)
Wire Size Range
16–28 AWG
Wire Specication
Copper, rated over 60°C
Screw Torque
Min 0.22 N·m [1.95 lb-in]
Screwdriver Size
0.4 x 2.5 mm
(AutomationDirect p/n TW-SD-VSL-1 or equiv.)
Pin Assignments
+: Dierential signal +
-: Dierential signal -
LG: Logic Ground
Status Lamp
RX, TX
Mechanical Drawings
Unit Dimensions: mm [in]
OPTIONAL
MODULE SLOT
BLUETOOTH
PAIRING
MODE SWITCH
MICRO USB
ETHERNET 10/100
SERIAL PORT RS-232
SERIAL PORT RS-485
POWER TERMINAL BLOCK
MICRO SD CARD
ANTENNA
STATUS LED's
85.0
3.35
101.8
4.01
46.6
1.83
46.4
1.83
FULLY EXTENDED
( OVERALL )
53.5
2.11
60.8
2.39
32.3
1.27
126.8
4.99
PART NO.
SE-ANT210
Technical Specifications, continued

10
www.automationdirect.com/click-plc
3505 HUTCHINSON ROAD
CUMMING, GA 30040-5860
1-800-633-0405
C2-03CPU Quick Start Guide
Copyright© 2020, Automationdirect.com Incorporated/All Rights Reserved Worldwide
FCC and ISED Regulatory Statements
The C2-03CPU has achieved modular radio certification on
a reference design for the United States and Canada . The
reference design has been certified for Part 15.247 (Intentional
Radiator) of the FCC rules and regulations, Industry Canada
RSS-210.
Per FCC 15.19(a)(3) and (a)(4) This device complies with
part 15 of the FCC Rules. Operation is subject to the follow-
ing two conditions: (1) This device may not cause harmful
interference, and (2) this device must accept any interference
received, including interference that may cause undesired
operation.
Note: This equipment has been tested and found to comply
with the limits for a Class A digital device, pursuant to part
15 of the FCC Rules. These limits are designed to provide
reasonable protection against harmful interference when the
equipment is operated in a commercial environment. This
equipment generates, uses, and can radiate radio frequency
energy and, if not installed and used in accordance with the
instruction manual, may cause harmful interference to radio
communications. Operation of this equipment in a residential
area is likely to cause harmful interference in which case the
user will be required to correct the interference at his own
expense.
The C2-03CPU complies with Part 15.247 modular (Inten-
tional Radiator) FCC rules and regulations. Changes or mod-
ifications not expressly approved by AutomationDirect could
void the user’s authority to operate the equipment.
Per RSS-Gen, Section 8.4 this device complies with Industry
Canada license-exempt RSS standard(s). Operation is subject
to the following two conditions: (1) this device may not cause
interference, and (2) this device must accept any interference,
including interference that may cause undesired operation of
the device.
Par RSS-Gen, Section 8.4 cet appareil est conforme à la norme
RSS Industrie Canada exempt de licence. Son fonctionnement
est soumis aux deux conditions suivantes: (1) cet appareil
ne doit pas provoquer d’interférences et (2) cet appareil doit
accepter toute interférence, y compris les interférences pouvant
causer un mauvais fonctionnement du dispositif.
Accessories
SE-ANT210
Whip/straight
2.4 GHz antenna,
IP65, connector
mount.
SE-ANT250
Dome
2.4 GHz antenna,
IP67, panel mount,
9.8ft/3m cable length.
C2-FILL
Snap-on CPU Option
Slot cover for applications
without an Option Slot
module present.
C0-3TB
Replacement terminal
block for the RS485
communications port.
Sold in packs of 2.
C0-4TB
Replacement terminal
block for the 24VDC
power connection.
Sold in packs of 2.
D0-MC-BAT
Replacement battery for
CLICK PLUS CPU units.
Table of contents
Other AutomationDirect Industrial Electrical manuals
Popular Industrial Electrical manuals by other brands
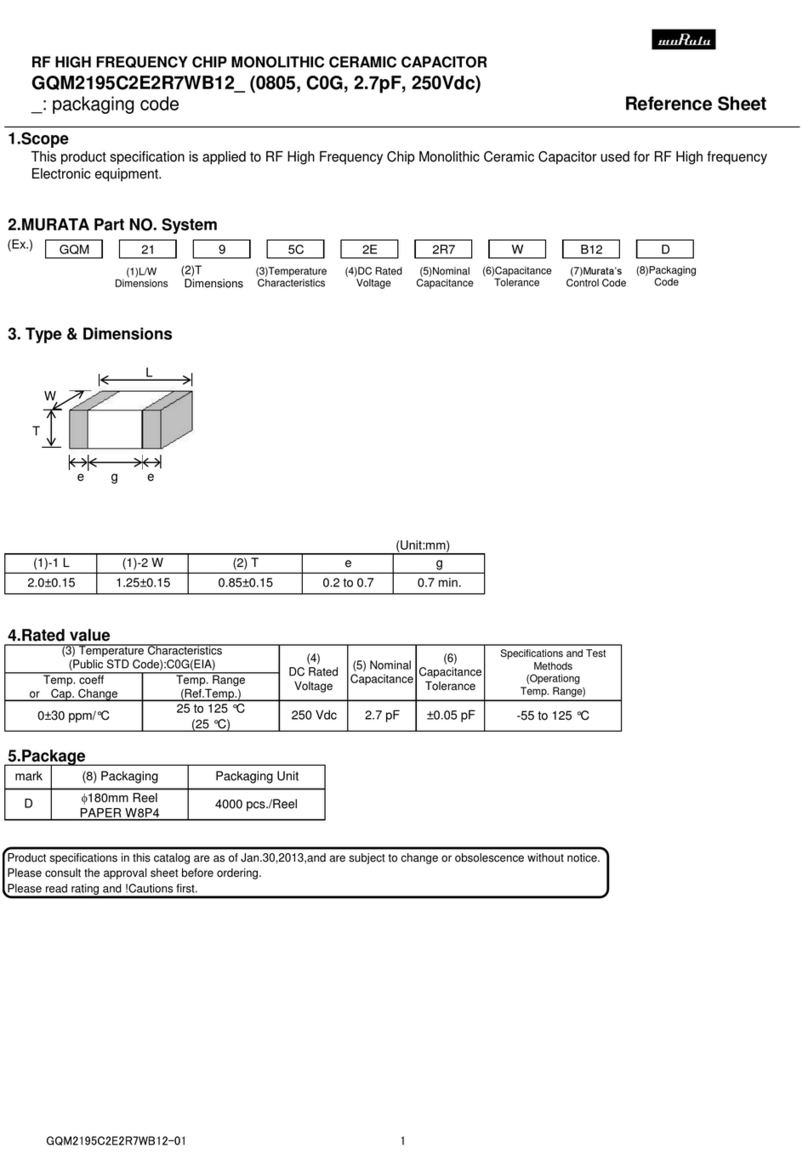
Murata
Murata GQM2195C2E2R7WB12 Series Reference sheet
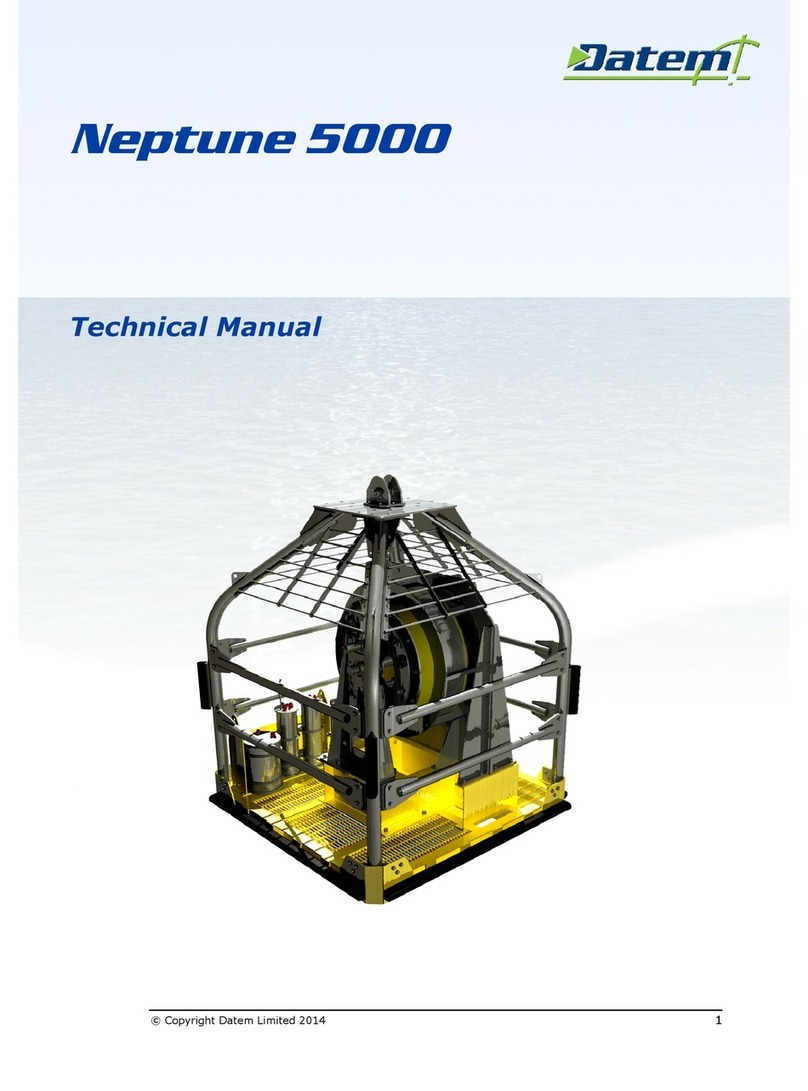
Datem
Datem Neptune 5000 Technical manual
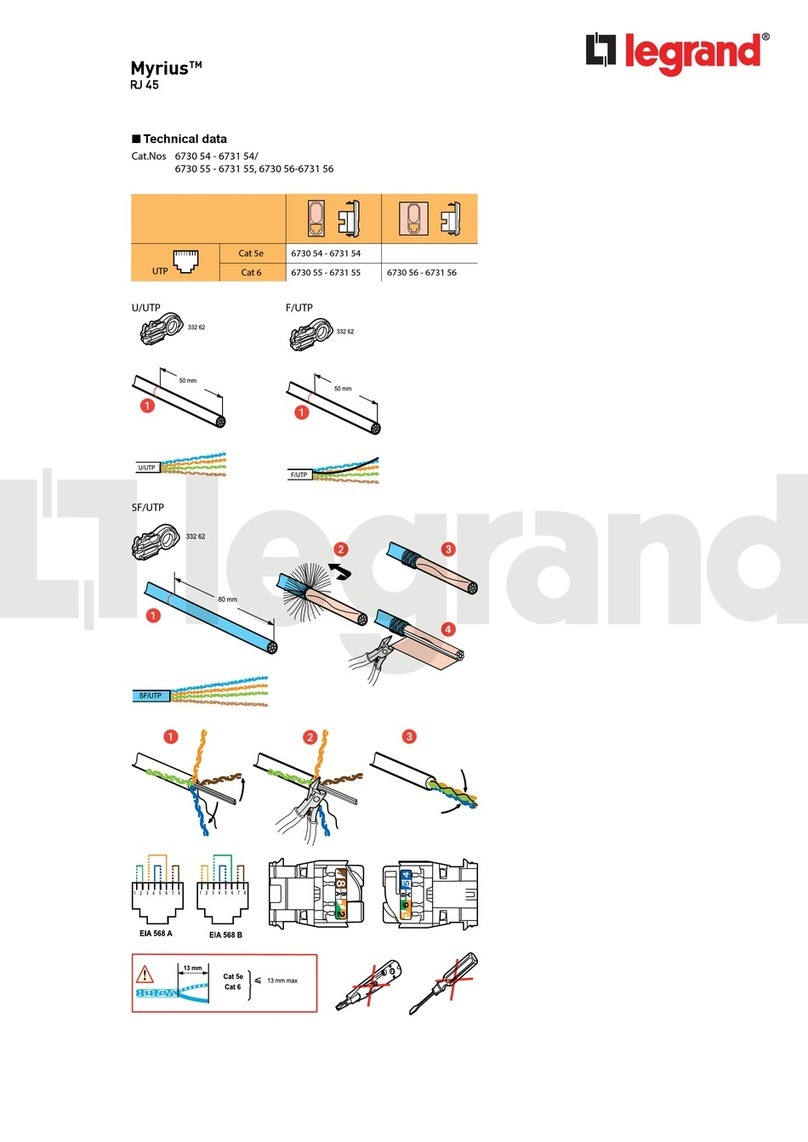
LEGRAND
LEGRAND Myrius RJ 45 manual
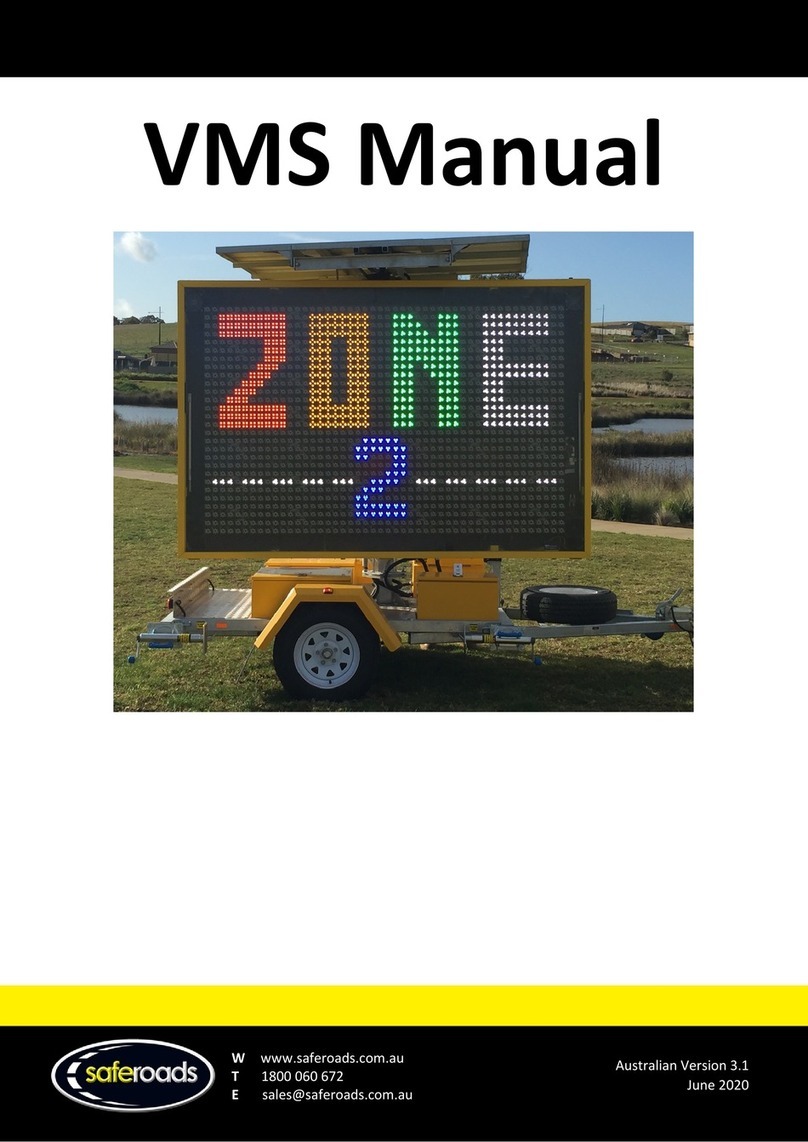
Saferoads
Saferoads Zone 2 VMS manual
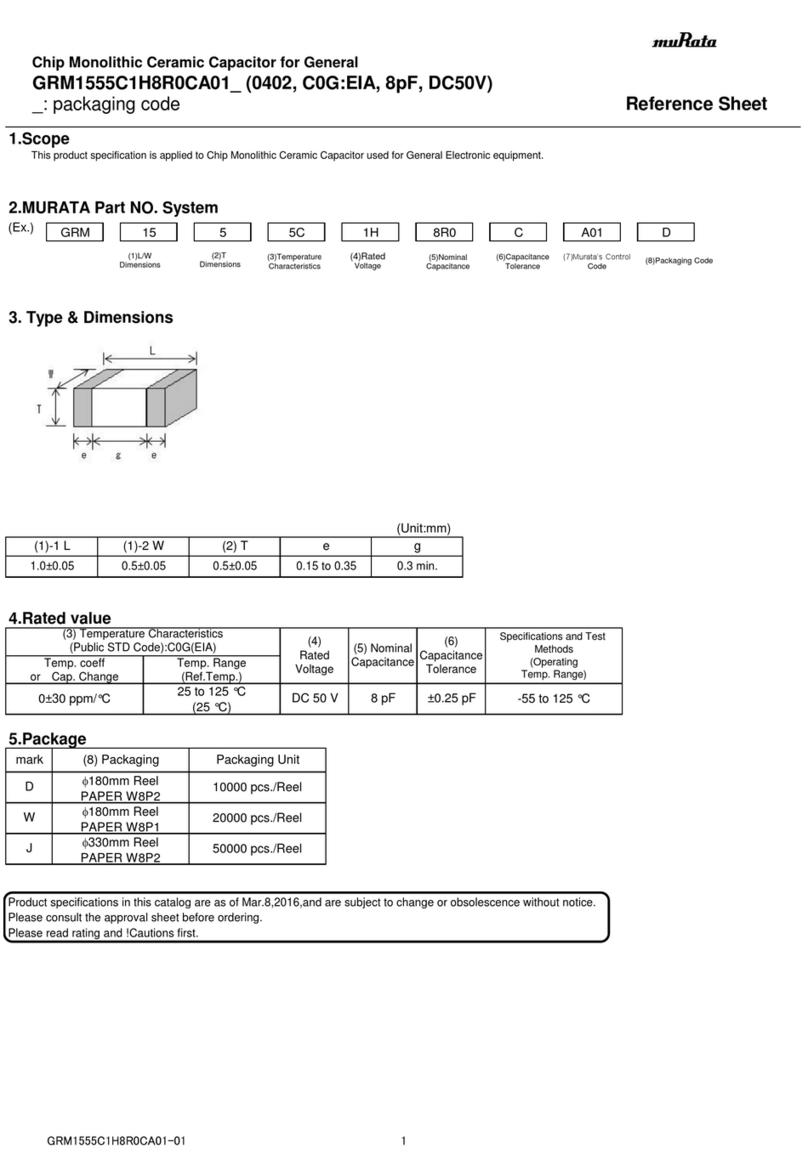
Murata
Murata GRM1555C1H8R0CA01 Series Reference sheet

Cooper Crouse-Hinds
Cooper Crouse-Hinds FSQ Series Installation & maintenance information