Axiom TWR-S12G128 User manual

D O C - 0 508- 0 1 0 , R E V D
Web Site: www.axman.com
TWR-S12G128
Demonstration Board for Freescale MC9S12G128
Microcontroller
USER GUIDE

T W R - 9 S 1 2 G 1 2 8 J A N U A R Y 4 , 2 0 1 1
U S E R G U I D E
2
CONTENTS
CAUTIONARY NOTES ..............................................................................................................4
TERMINOLOGY.........................................................................................................................4
FEATURES................................................................................................................................5
MEMORY MAP ..........................................................................................................................6
SOFTWARE DEVELOPMENT...................................................................................................6
DEVELOPMENT SUPPORT......................................................................................................7
OSBDM BOOTLOADER........................................................................................................ 7
BDM_PORT HEADER........................................................................................................... 7
POWER......................................................................................................................................8
POWER SELECT.................................................................................................................. 8
RESET SWITCH ........................................................................................................................8
LOW VOLTAGE RESET............................................................................................................8
TIMING.......................................................................................................................................9
COMMUNICATIONS..................................................................................................................9
RS-232.................................................................................................................................. 9
COM CONNECTOR........................................................................................................ 10
COM_EN......................................................................................................................... 10
LIN PORT............................................................................................................................ 11
LIN ENABLE.................................................................................................................... 11
LIN COM INPUT.............................................................................................................. 11
LIN_PWR OPTION.......................................................................................................... 11
MSTR OPTION................................................................................................................ 12
LIN-J1 CONNECTOR...................................................................................................... 12
CAN PORT.......................................................................................................................... 13
CAN TERMINATION ENABLE........................................................................................ 13
STANDBY MODE............................................................................................................ 13
USER PERIPHERALS.............................................................................................................14
POTENTIOMETER.............................................................................................................. 14
USER LED’S ....................................................................................................................... 14
PUSHBUTTON SWITCHES................................................................................................ 14
EDGE CONNECTOR PINOUT.................................................................................................15

T W R - 9 S 1 2 G 1 2 8 J A N U A R Y 4 , 2 0 1 1
U S E R G U I D E
3
FIGURES
Figure 1: Memory Map................................................................................................................6
Figure 2: BDM_PORT Header....................................................................................................7
Figure 3: PWR_SEL Option Header...........................................................................................8
Figure 4: Serial Connections ....................................................................................................10
Figure 5: COM1 Connector.......................................................................................................10
Figure 6: COM_EN Option Header...........................................................................................10
Figure 7: LIN Block Diagram.....................................................................................................11
Figure 8: JP3 Option Header...................................................................................................12
Figure 9: LIN Connector ...........................................................................................................12
Figure 10: CAN_PORT.............................................................................................................13
Figure 11: CAN Termination Enable.........................................................................................13
Figure 12: JP1 Option Header..................................................................................................14
Figure 13: Primary Edge Connector.........................................................................................15
Figure 14: Secondary Edge Connector ....................................................................................17
REVISION
Date
Rev
Comments
June 2, 2010
A
Initial Release
June 30, 2010
B
Updated / Corrected target MCU memory map. Updated reference to
MC9S12G Family Reference Manual
October 14, 2010
C
Final Updates, removed OSBDM disclaimer
January 4, 2011
D
Minor corrections from customer review

T W R - 9 S 1 2 G 1 2 8 J A N U A R Y 4 , 2 0 1 1
U S E R G U I D E
4
CAUTIONARY NOTES
1) Electrostatic Discharge (ESD) prevention measures should be used when handling this
product. ESD damage is not a warranty repair item.
2) Axiom Manufacturing does not assume any liability arising out of the application or use of
any product or circuit described herein; neither does it convey any license under patent
rights or the rights of others.
3) EMC Information on the TWR-S12G128 board:
a) This product as shipped from the factory with associated power supplies and cables,
has been verified to meet with requirements of CE and the FCC as a CLASS A product.
b) This product is designed and intended for use as a development platform for hardware
or software in an educational or professional laboratory.
c) In a domestic environment, this product may cause radio interference in which case the
user may be required to take adequate prevention measures.
d) Attaching additional wiring to this product or modifying the products operation from the
factory default as shipped may affect its performance and cause interference with
nearby electronic equipment. If such interference is detected, suitable mitigating
measures should be taken.
TERMINOLOGY
This development module utilizes option select jumpers to configure default board operation.
Terminology for application of the option jumpers is as follows:
Jumper –a plastic shunt that connects 2 terminals electrically
Jumper on, in, or installed = jumper is a plastic shunt that fits across 2 pins and the shunt is
installed so that the 2 pins are connected with the shunt.
Jumper off, out, or idle = jumper or shunt is installed so that only 1 pin holds the shunt, no 2
pins are connected, or jumper is removed. It is recommended that the jumpers be placed
idle by installing on 1 pin so they will not be lost.
Cut-Trace –a circuit trace connection between component pads. The circuit trace may be
cut using a knife to break the default connection. To reconnect the circuit, simply install a
suitably sized 0-ohm resistor or attach a wire across the pads.
Signal names followed by an asterisk (*) denote active-low signals.

T W R - 9 S 1 2 G 1 2 8 J A N U A R Y 4 , 2 0 1 1
U S E R G U I D E
5
FEATURES
The TWR-S12G128 is a demonstration board for the MC9S12G128 microcontroller; an
automotive, 16-bit microcontroller focused on low-cost, high-performance in a low pin-count
device. The MC9S12G128 provides16-bit wide accesses, without wait states, for all
peripherals and memories. The MC9S12G128 targets automotive applications requiring CAN
or LIN/J2602 communications. Examples include body controllers, occupant detection, etc…
The board is designed to interface to the Freescale Tower System, a modular development
platform which aids in rapid prototyping and tool-reuse. An integrated Open-Source BDM,
software tools, and examples provided with the development board make application
development and debug quick and easy. All MCU signals are available on one or both edge
connectors.
MC9S12G128, 100 LQFP
128K Bytes Flash
4096 Bytes EEPROM
8192 Bytes RAM
25MHz Bus Frequency
Internal Oscillator
SCI, SPI, MSCAN
Integrated Open Source BDM (OSBDM)
BDM_PORT header for external BDM cable support
1 ea. High-Speed CAN Physical Layer Transceiver
1 ea, Enhanced LIN Physical Layer Transceiver
RS-232 Serial Data Physical Layer Transceiver
On-board +5V regulator
Power input from OSBDM, Tower System, or input
vias at E1/E2
Power Input Selection Jumpers
Power input from USB-BDM
Power input from on-board regulator
Power input from Tower System edge connector
User Peripherals
4 User Push Button Switches
4 User LED Indicators
5K ohm POT w /LP Filter
User Option Jumpers to disconnect Peripherals
Connectors
BDM_PORT Connector for External BDM Cable
USB mini-AB Connector
2x5, 0.1” ctr, RS-232 Header
1x4, 4.2mm, Molex CAN Cable Connector
2x2, 4.2mm, Molex LIN Cable Connector
Specifications:
Board Size 3.55” x 3.20” overall
Power Input: +5V from USB connector or from Tower System
NOTE: LIN functionality requires +12V on LIN +V input or +12V at E1/E2 input.

T W R - 9 S 1 2 G 1 2 8 J A N U A R Y 4 , 2 0 1 1
U S E R G U I D E
6
MEMORY MAP
Figure 1 below shows the target device memory map. Refer to the MC9S12G Family
Reference Manual (RM) for further information.
Figure 1: Memory Map
Address
Module
Size
(Bytes)
0x0000–0x0009
PIM (port integration module)
10
0x000A–0x000B
MMC (memory map control)
2
0x000C–0x000D
PIM (port integration module)
2
0x000E–0x000F
Reserved
2
0x0010–0x0017
MMC (memory map control)
8
0x0018–0x0019
Reserved
2
0x001A–0x001B
Device ID register
2
0x001C–0x001F
PIM (port integration module)
4
0x0020–0x002F
DBG (debug module)
16
0x0030–0x0033
Reserved
4
0x0034–0x003F
CPMU (clock and power management)
12
0x0040–0x006F
TIM0 (timer module)
48
0x0070–0x009F
ATD (analog-to-digital converter, 10 bit, 8-channel)
48
0x00A0–0x00C7
PWM (pulse-width modulator)
40
0x00C8–0x00CF
SCI0 (serial communications interface)
8
0x00D0–0x00D7
SCI1 (serial communications interface)
8
0x00D8–0x00DF
SPI0 (serial peripheral interface)
8
0x00E0–0x00E7
Reserved
8
0x00E8–0x00EF
SCI2 (serial communications interface)
8
0x00F0–0x00F7F
SPI1 (serial peripheral interface)
8
0x00F8–0x00FF
SPI1 (serial peripheral interface)
8
0x0100–0x0113
FTMRG control registers
20
0x0114–0x011F
Reserved
12
0x0120
INT (interrupt module)
1
0x0121–0x013F
Reserved
31
0x0140–0x017F
CAN
64
0x0180–0x023F
Reserved
192
0x0240–0x027F
PIM (port integration module)
64
0x0280–0x02EF
Reserved
112
0x02F0–0x02FF
CPMU (clock and power management)
16
0x0300–0x03FF
Reserved
256
SOFTWARE DEVELOPMENT
Software development requires the use of a compiler or an assembler supporting the
HCS12(X) instruction set and a host PC running a debug interface. CodeWarrior Development
Studio is supplied with this board for application development and debug. Refer to the
supporting CodeWarrior documentation for details on use and capabilities.

T W R - 9 S 1 2 G 1 2 8 J A N U A R Y 4 , 2 0 1 1
U S E R G U I D E
7
DEVELOPMENT SUPPORT
Application development and debug for the target TWR-S12 board is supported through the
Open-Source Background Debug Mode (OSBDM) interface or an external BDM interface
connector. The OSBDM is fully supported in CodeWarrior and provides direct, non-intrusive
access to the target device internals. While in BDM mode, no internal resources are used.
Code stepping and break-points are fully supported.
Connection between a host PC and the target device is provided via a mini-B, USB connector.
The OSBDM is capable of providing power to the target board eliminating the need for external
power. Please note that power supplied by the OSBDM is limited by the USB specification.
When powered through the OSBDM, total current draw, including the OSBDM, TWR-S12
board, and Tower System must remain less than 500mA. Otherwise, the USB bus will cause
the host PC to disconnect the board. Damage to the host PC, target board, or Tower System
may result if this current limit is violated.
CAUTION:
When powered from the USB bus, do not exceed the 500mA maximum
current drain allowed under the USB specification. Damage to the
target board or host PC may result
OSBDM Bootloader
The OSBDM is pre-programmed with a bootloader application to allow field updates. The USB
bootloader communicates with a GUI application running on a host PC. The GUI application
allows the user to update OSBDM firmware easily and quickly. Option jumper JP401 enables
the bootloader at startup. This option header is not populated in default configuration. Refer
to Freescale Application Note AN3561 for details on using the GUI application and bootloader.
The application note may be found at www.freescale.com or at www.axman.com/support.
BDM_PORT Header
A compatible HCS12 BDM cable can also be attached to the 6-pin BDM interface header at J3.
This header allows the use of external programming/debug cables. Refer to the external
programming/debug cable documentation for details on use. The figure below shows the pin-
out for the DEBUG header.
Figure 2: BDM_PORT Header
J3
BKGD
1
2
GND
See the associated RM for complete DEBUG
documentation
3
4
RESET*
5
6
VDD

T W R - 9 S 1 2 G 1 2 8 J A N U A R Y 4 , 2 0 1 1
U S E R G U I D E
8
NOTE: This header is not installed in default configuration.
POWER
The TWR-S12 board may be powered from the OSBDM, from the Tower System, from the LIN
+V input, or 2 input vias at E1 & E2. The LIN +V input accepts +12V from the LIN bus and
uses an on-board regulator to create the board operating voltage. Input vias at E1 & E2 allow
connecting external power to the board if desired. An on-board regulator is used to create the
board operating voltage from this input.
Use of the on-board regulator requires input voltage between +7.V and +27V. However, input
voltage should be kept as low as possible to reduce device self-heating.
CAUTION:
This board does not apply reverse polarity protection on inputs E1 &
E2. Polarity for each input is clearly marked. Reverse input polarity
will damage the board.
Power Select
The PWR_SEL option header selects the input power source for the target board. When
powered from the Tower System, the OSBDM voltage output is disabled.
Figure 3: PWR_SEL Option Header
JP5
1
●
●
2
Select TWR voltage input
PWR_SEL
●
●
Select OSBDM voltage input (default)
●
●
Select on-board regulator input
RESET SWITCH
The RESET switch applies an asynchronous RESET input to the MCU. The RESET switch is
connected directly to the RESET* input on the MCU. Pressing the RESET switch applies a
low voltage level to the RESET* input. A pull-up bias resistor allows normal MCU operation.
LOW VOLTAGE RESET
The MC9S12G128 applies an internal Power-On Reset (POR) circuit and an internal Low
Voltage Reset (LVR) circuit to ensure proper device operation. The POR circuit holds the
MCU in reset until applied voltage reaches an appropriate level. The LVR forces the device

T W R - 9 S 1 2 G 1 2 8 J A N U A R Y 4 , 2 0 1 1
U S E R G U I D E
9
into reset if input voltage falls too low, protecting against brown-out conditions. A user
configurable Low-Voltage Detect (LVD) with interrupt output is also available. Consult the
MC9S12G Family Reference manual for details of POR, LVR, and LVD operation.
TIMING
The TWR-S12G128 internal timing source is active from RESET by default. An external 8MHz
crystal oscillator, configured for low-power operation, is also installed. Refer to the target
device RM for details on selecting and configuring the desired timing source.
COMMUNICATIONS
Communications options for the TWR-S12G128 include serial RS-232, LIN, and CAN. Serial
RS-232 communications is supported through a RS-232 physical layer device (PHY) and a 2x5
pin header. A high-speed, enhanced, LIN PHY provides LIN bus communications through a
2x2 Molex connector (pn 39-29-1048). A high-speed CAN PHY provides CAN bus
communications through a 1 x 4 Molex connector (pn 39-30-3045).
Connecting LIN cables require Molex housing, pn 39-01-2040 and pins, pn 39-00-0217.
Connecting CAN cables require Molex housing, pn 39-01-4040, and pins, pn 39-00-0217.
The COM_SEL option header connects the MCU SCI signal to either the LIN PHY or the RS-
232 PHY. See Figure 6 below for jumper position options. See Figure 4 below for jumper
position options.
RS-232
The TWR-S12G128 applies the MAX3387E, RS-232 physical layer transceiver (PHY) to
enable standard serial communications. A standard 2x5 “Berg” pin-header on 0.1” centers and
an IDC to DB9 cable supports connecting standard serial cables to the target board. Figure 4
below shows the SCI signal connections.
CAUTION:
The user must open CT2 when using PAD9/KWAD9 as an analog input or
as GPIO.
Similarly, CT3 must be opened when using PD1 as GPIO

T W R - 9 S 1 2 G 1 2 8 J A N U A R Y 4 , 2 0 1 1
U S E R G U I D E
10
Figure 4: Serial Connections
MCU Port Signal
Transceiver
Signal
COM
CONNECTOR
COMMENTS
+5V
J5-1
PS1//TXD0
TXD
J5-3
pull-up
PS0//RXD0
RXD
J5-5
PAD9/KWAD9/AN9
DTR
J5-7
CT2 (NC)
GND
J5-9
PD2
DSR
J5-2
pull-up
PD1
CTS
J5-4
CT3 (NC), pull-up
PAD10/KWAD10/AN10
RTS
J5-6
pull-up
TP2
J5-8
PAD8/KWAD8/AN8
INVALID*
CT4 (NO)
PAD15/KWAD15/AN15
FORCEOFF*
CT5 (NC)
NOTE: For normal RS-232 operation, FORCEOFF* should be actively driven to the high level.
Alternately, open CT5 to allow FORCEOFF* to float high.
COM Connector
A 2x5, 0.1”, standard “Berg” pin-header provides external connections for the SCI port. Figure
5 below shows the COM1 pin-out. The TWR-S12G128 ships with a DB-9 to 2x5 IDC
connector cable to interface the target board to standard serial cables.
Figure 5: COM1 Connector
2, 7
1
2
1, 7
TXD
3
4
CTS
RXD
5
6
RTS
1, 2
7
8
TP2
GND
9
10
NC
COM_EN
The COM_EN option header connects the MCU SCI port to either the SCI PHY or the LIN
PHY. Figure 6 below shows the option jumper configuration for the COM_EN option header.
Figure 6: COM_EN Option Header
2
4
6
Connects target MCU SCI port to LIN PHY to enable LIN bus
communications
1
3
5
COM_EN
2
4
6
Connects target MCU SCI port to RS-232 PHY to enable serial
communications (Default)
1
3
5
COM_EN

T W R - 9 S 1 2 G 1 2 8 J A N U A R Y 4 , 2 0 1 1
U S E R G U I D E
11
LIN Port
The TWR-S12G128 applies the MC33661 LIN bus physical layer device (transceiver) to
support LIN communications. The PHY may be configured as a Master or Slave node on the
LIN bus. LIN connectors J9 & J10 are configured in parallel to support pass-thru signaling.
Figure 7 below details the LIN block diagram.
Figure 7: LIN Block Diagram
The LIN interface provides optional features of slew rate control, network supply, and wake up
option. Refer to the MC33661 Reference Manual for detail on PHY functionality. The following
sections detail functionality for LIN option jumpers.
LIN Enable
The LIN PHY is enabled by default. Disable the PHY by connecting the test point, TP3, to
GND.
LIN COM Input
LIN inputs RX and TX are selectable using the COM_EN option header. Refer to Figure 6
above for details on configuring this header.
LIN_PWR Option
The LIN_PWR option jumper connects pin 1 of both LIN connectors to the +V input. In Master
mode, this option may be used to power LIN slave devices. This option requires +12V be
applied at E1/E2 inputs. In Slave mode, this option allows slave device to draw power from the
LIN network. For Slave mode configuration, external power should not be applied to the target
board. LIN_PWR is enabled by installing a shunt from JP3-1 to JP3-2. Refer to Figure 8
below.
MC33661
LIN PHY
J6 / J7
JP3
MSTR
(partial)
JP3
LIN_PWR
(partial)
CT6
MC9S12G128
RXD0
TXD0
COM_EN
(partial)

T W R - 9 S 1 2 G 1 2 8 J A N U A R Y 4 , 2 0 1 1
U S E R G U I D E
12
CAUTION:
If the target board draws power from the LIN bus in Slave mode, do
not apply external power at E1/E2 inputs. Damage to the board may
result.
NOTE:
If the target board powers the LIN bus in Master mode, +12V must be
applied externally at E1/E2 inputs.
MSTR Option
The MSTR option jumper allows the LIN transceiver to be configured for Master mode
functionality. Master mode may also be set using the INH pin on the PHY. Refer to the
MC33661 device datasheet for details on use and configuration. Refer to Figure 8 below.
Figure 8: JP3 Option Header
●
●
JP3
Connects LIN bus to +V input (default)
●
●
LIN_PWR
Enables LIN Master mode functionality (default)
2
1
NOTE: LIN PHY may also be configured as a Master Node using the INH pin. Refer to the LIN
PHY data sheet for details.
LIN-J1 Connector
The TWR-S12G128 supports two, 2 x 2 Molex connectors to interface to the LIN bus. Figure 9
below details the pin-out of the LIN bus connector.
Figure 9: LIN Connector
LIN Signal
4
3
+V
WAKE
2
1
GND
Front View –Looking into Connector
NOTE: LIN Port Connector –Molex 39-29-1048
Mates with; Housing –Molex 39-01-2040, Pin –Molex 39-00-0036

T W R - 9 S 1 2 G 1 2 8 J A N U A R Y 4 , 2 0 1 1
U S E R G U I D E
13
CAN Port
One, TJA1040T, High-Speed CAN physical-layer transceiver (PHY) is applied to support CAN
bus communications. A 4-pos, 4.22mm MOLEX connector interfaces to external CAN cabling.
Differential input CAN signals, are terminated with 120 ohms. Option headers, JP13 and JP15
allow the user to optionally disconnect signal termination. Avalanche diodes protect the CAN
PHY from voltage surges on the input differential signal lines. Figure 10 below shows the CAN
connector pin-out.
Figure 10: CAN_PORT
NC
GND
CANL
CANH
4
3
2
1
Front View –
Looking into
Connector
NOTE: CAN Port Connector –Molex 39-30-3045
Mates with; Housing –Molex 39-01-4040, Pin –Molex 39-00-0217
CAN Termination Enable
CAN bus termination of 120 ohm with virtual ground is applied to the differential CAN signals
on both channels. The SPLIT output from each PHY is connected to the virtual ground
providing common-mode stabilization. The differential CAN bus signal termination may be
removed using option header JP13 or JP15. To prevent signal corruption, both option jumpers
must be installed or both option jumpers must be removed. The CAN bus should not be
operated with only 1 signal termination applied. Figure 11 below details the option header
shunt positions.
Figure 11: CAN Termination Enable
●
●
Enables CANL termination
1
●
●
2
Enables CANH termination
JP6
Standby Mode
The CAN PHY is configured for normal mode by default. To enable standby (STB) mode,
apply a high logic level at test point TP1. Refer to the TJA1040T Reference Manual for use
and capabilities of the Standby Mode.

T W R - 9 S 1 2 G 1 2 8 J A N U A R Y 4 , 2 0 1 1
U S E R G U I D E
14
USER PERIPHERALS
User I/O includes 1 potentiometer, 4 push button switches, and 4 green LEDs for user I/O.
The USER (JP14) option header enables or disables each User I/O function individually. The
sections below provide details on user I/O. Figure 12 below shows the USER jumper settings.
Potentiometer
The TWR-S12G128 target board applies a single-turn, 5K, ohm potentiometer (POT) to
simulate analog input. The POT is connected to an ATD input on the target MCU and is
decoupled to minimize noise transients during adjustment. Figure 12 below shows the USER
jumper settings.
User LED’s
The TWR-S12G128 target board applies 4, green, LEDs for output indication. Each LED is
configured for active-low operation. A series, current-limit resistor prevents excessive diode
current. Each LED is connected to a timer channel on the target MCU. Figure 12 below
shows the USER jumper settings.
Pushbutton Switches
The TWR-S12G128 provides 4 push-button switches for user input. Each push-button switch
is configured for active-low operation and is connected to a key-wakeup input on the target
MCU. No bias is applied to these push-button inputs and use of target MCU internal pull-ups is
required for proper operation. Figure 12 below shows the USER jumper settings.
Figure 12: JP1 Option Header
JP1
Signal
ON
OFF
SW1
PAD4/KWAD4/AN4
Enabled
Disabled
SW2
PAD5/KWAD5/AN5
Enabled
Disabled
SW3
PAD6/KWAD6/AN6
Enabled
Disabled
SW4
PAD7/KWAD7/AN7
Enabled
Disabled
POT
PAD0/KWAD0/AN0
Enabled
Disabled
LED1
PT4/IOC4
Enabled
Disabled
LED2
PT5/IOC5
Enabled
Disabled
LED3
PT6/IOC6
Enabled
Disabled
LED4
PT7/IOC7
Enabled
Disabled
NOTE: User peripheral input/output is enabled by default.

T W R - 9 S 1 2 G 1 2 8 J A N U A R Y 4 , 2 0 1 1
U S E R G U I D E
15
EDGE CONNECTOR PINOUT
The TWR-S12 board connects to the Freescale Tower System using the 2 PCIe Edge
Connectors. Following the PCIe specification, the Bx signals are located on the top of the
board and the Ax signals are located on bottom. Pin B1 for the primary and secondary
connectors are at opposite ends of the board. The figures below show the pin-out of each
edge connector. Pin positions with no signal name shown are not connected.
Figure 13: Primary Edge Connector
5.0V Power
Pri_B01
Pri_A01
5.0V Power
Ground
Pri_B02
Pri_A02
Ground
Pri_B03
Pri_A03
Elevator Power Sense
Pri_B04
Pri_A04
Ground
Pri_B05
Pri_A05
Ground
Ground
Pri_B06
Pri_A06
Ground
PS6/SCK0
Pri_B07
Pri_A07
Pri_B08
Pri_A08
PS7/API_EXTCLK/SS0
Pri_B09
Pri_A09
PD3
PS5/MOSI0
Pri_B10
Pri_A10
PD4
PS4/MISO0
Pri_B11
Pri_A11
PD5
Pri_B11A
Pri_B12
Pri_A12
Pri_B13
Pri_A13
Pri_B14
Pri_A14
Pri_B15
Pri_A15
Pri_B16
Pri_A16
Pri_B17
Pri_A17
Pri_B18
Pri_A18
Pri_B19
Pri_A19
Pri_B20
Pri_A20
PD6
Pri_B21
Pri_A21
PD7
Pri_B22
Pri_A22
PB3
Pri_B23
Pri_A23
Pri_B24
Pri_A24
Pri_B25
Pri_A25
Ground
Pri_B26
Pri_A26
Ground
PAD7/KWAD7/AN7
Pri_B27
Pri_A27
PAD3/KWAD3/AN3
PAD6/KWAD6/AN6
Pri_B28
Pri_A28
PAD2/KWAD2/AN2
PAD5/KWAD5/AN5
Pri_B29
Pri_A29
PAD1/KWAD1/AN1
PAD4/KWAD4/AN4
Pri_B30
Pri_A30
PAD0/KWAD0/AN0
Ground
Pri_B31
Pri_A31
Ground
Pri_B32
Pri_A32
IOC3/PT3
Pri_B33
Pri_A33
IOC1/PT1
IOC2/PT2
Pri_B34
Pri_A34
IOC0/PT0
PB6
Pri_B35
Pri_A35
PB7

T W R - 9 S 1 2 G 1 2 8 J A N U A R Y 4 , 2 0 1 1
U S E R G U I D E
16
3.3V Power
Pri_B36
Pri_A36
3.3V Power
PWM7/KWP7/PP7
Pri_B37
Pri_A37
PWM3/ETRIG3/KWP3/PP3
PWM6/KWP6/PP6
Pri_B38
Pri_A38
PWM2/ETRIG2/KWP2/PP2
PWM5/KWP5/PP5
Pri_B39
Pri_A39
PWM1/ETRIG1/KWP1/PP1
PWM4/KWP4/PP4
Pri_B40
Pri_A40
PWM0/ETRIG0/KWP0/PP0
PM0/RXCAN
Pri_B41
Pri_A41
PS0/RXD0
PM1/TXCAN
Pri_B42
Pri_A42
PS1/TXD0
Pri_B43
Pri_A43
PS2/RXD1
MISO2/KWJ4/PJ4
Pri_B44
Pri_A44
PS3/TXD1
MOSI2/KWJ5/PJ5
Pri_B45
Pri_A45
VSSA (w/ NC CT)
SS2/KWJ7/PJ7
Pri_B46
Pri_A46
VDDA (w/ NC CT)
Pri_B47
Pri_A47
PA0
SCK2/KWJ6/PJ6
Pri_B48
Pri_A48
PA1
Ground
Pri_B49
Pri_A49
Ground
Pri_B50
Pri_A50
PA2
Pri_B51
Pri_A51
PA3
Pri_B52
Pri_A52
PA4
Pri_B53
Pri_A53
PA5
Pri_B54
Pri_A54
PA6
Pri_B55
Pri_A55
PA7
Pri_B56
Pri_A56
Pri_B57
Pri_A57
Pri_B58
Pri_A58
IOC7/PT7
Pri_B59
Pri_A59
IOC6/PT6
Pri_B60
Pri_A60
IOC5/PT5
XIRQ/PB5
Pri_B61
Pri_A61
IOC4/PT4
IRQ/PB4
Pri_B62
Pri_A62
RESET
Pri_B63
Pri_A63
Pri_B64
Pri_A64
ECLK/PB0
Ground
Pri_B65
Pri_A65
Ground
Pri_B66
Pri_A66
Pri_B67
Pri_A67
Pri_B68
Pri_A68
Pri_B69
Pri_A69
Pri_B70
Pri_A70
Pri_B71
Pri_A71
Pri_B72
Pri_A72
Pri_B73
Pri_A73
Pri_B74
Pri_A74
Pri_B75
Pri_A75
Pri_B76
Pri_A76
Pri_B77
Pri_A77
Pri_B78
Pri_A78
Pri_B79
Pri_A79
Pri_B80
Pri_A80
Ground
Pri_B81
Pri_A81
Ground
3.3V Power
Pri_B82
Pri_A82
3.3V Power

T W R - 9 S 1 2 G 1 2 8 J A N U A R Y 4 , 2 0 1 1
U S E R G U I D E
17
Figure 14: Secondary Edge Connector
5.0V Power
Sec_B01
Sec_A01
5.0V Power
Ground
Sec_B02
Sec_A02
Ground
Sec_B03
Sec_A03
Elevator Power Sense
Sec_B04
Sec_A04
Ground
Sec_B05
Sec_A05
Ground
Ground
Sec_B06
Sec_A06
Ground
SCK1/KWJ2/PJ2
Sec_B07
Sec_A07
Sec_B08
Sec_A08
SS1/KWJ3/PJ3
Sec_B09
Sec_A09
PC0
MOSI1/KWJ1/PJ1
Sec_B10
Sec_A10
MISO1/KWJ0/PJ0
Sec_B11
Sec_A11
Sec_B11A
Sec_B12
Sec_A12
Sec_B13
Sec_A13
Sec_B14
Sec_A14
Sec_B15
Sec_A15
PC1
Sec_B16
Sec_A16
PC2
Sec_B17
Sec_A17
PC3
PC4
Sec_B18
Sec_A18
PC5
Sec_B19
Sec_A19
Sec_B20
Sec_A20
Sec_B21
Sec_A21
Sec_B22
Sec_A22
Sec_B23
Sec_A23
Sec_B24
Sec_A24
Sec_B25
Sec_A25
Ground
Sec_B26
Sec_A26
Ground
Sec_B27
Sec_A27
PAD11/KWAD11/AN11
Sec_B28
Sec_A28
PAD10/KWAD10/AN10
PAD13/KWAD13/AN13
Sec_B29
Sec_A29
PAD9/KWAD9/AN9
PAD12/KWAD12/AN12
Sec_B30
Sec_A30
PAD8/KWAD8/AN8
Ground
Sec_B31
Sec_A31
Ground
Sec_B32
Sec_A32
Sec_B33
Sec_A33
Sec_B34
Sec_A34
PC6
Sec_B35
Sec_A35
PC7
3.3V Power
Sec_B36
Sec_A36
3.3V Power
Sec_B37
Sec_A37
Sec_B38
Sec_A38
Sec_B39
Sec_A39
Sec_B40
Sec_A40
Sec_B41
Sec_A41
PM2/RXD2
Sec_B42
Sec_A42
PM3/TXD2
PD0
Sec_B43
Sec_A43
Sec_B44
Sec_A44
Sec_B45
Sec_A45

T W R - 9 S 1 2 G 1 2 8 J A N U A R Y 4 , 2 0 1 1
U S E R G U I D E
18
Sec_B46
Sec_A46
Sec_B47
Sec_A47
Sec_B48
Sec_A48
Ground
Sec_B49
Sec_A49
Ground
PD1
Sec_B50
Sec_A50
PD2
Sec_B51
Sec_A51
Sec_B52
Sec_A52
Sec_B53
Sec_A53
Sec_B54
Sec_A54
Sec_B55
Sec_A55
Sec_B56
Sec_A56
Sec_B57
Sec_A57
Sec_B58
Sec_A58
Sec_B59
Sec_A59
Sec_B60
Sec_A60
Sec_B61
Sec_A61
Sec_B62
Sec_A62
Sec_B63
Sec_A63
Sec_B64
Sec_A64
Ground
Sec_B65
Sec_A65
Ground
Sec_B66
Sec_A66
Sec_B67
Sec_A67
Sec_B68
Sec_A68
Sec_B69
Sec_A69
Sec_B70
Sec_A70
Sec_B71
Sec_A71
Sec_B72
Sec_A72
Sec_B73
Sec_A73
Sec_B74
Sec_A74
Sec_B75
Sec_A75
Sec_B76
Sec_A76
Sec_B77
Sec_A77
Sec_B78
Sec_A78
Sec_B79
Sec_A79
Sec_B80
Sec_A80
Ground
Sec_B81
Sec_A81
Ground
3.3V Power
Sec_B82
Sec_A82
3.3V Power
Other manuals for TWR-S12G128
1
Table of contents
Popular Controllers manuals by other brands
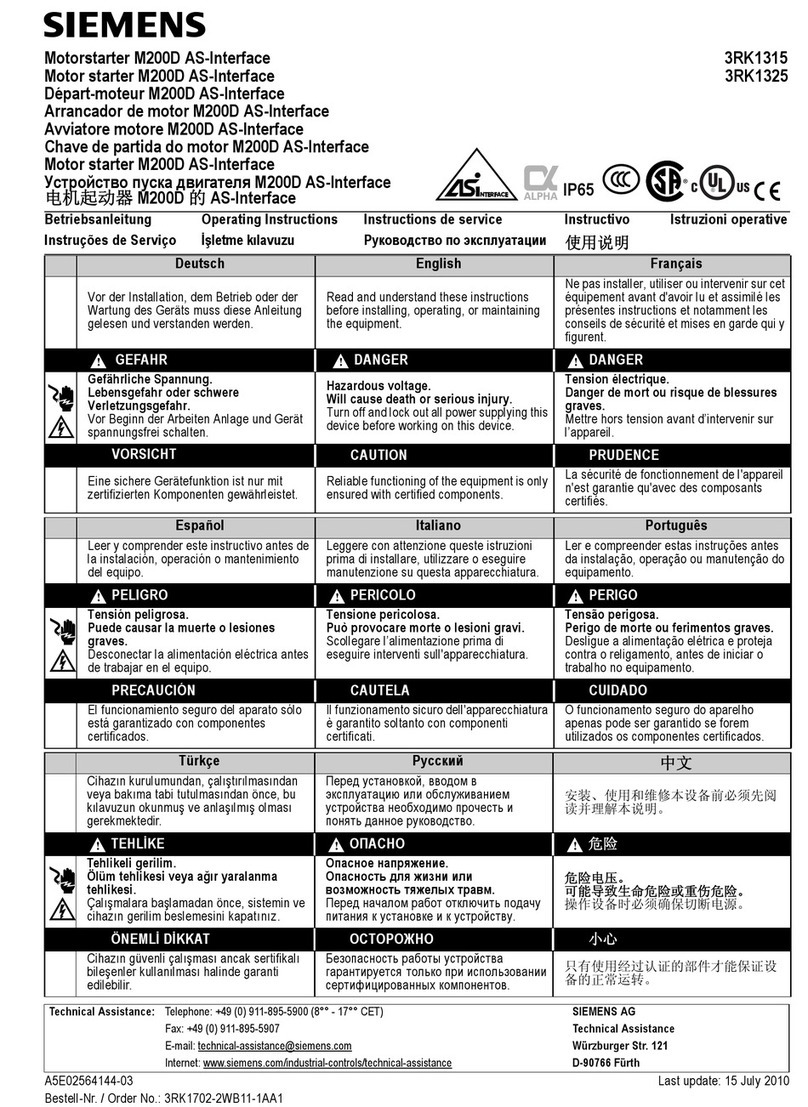
Siemens
Siemens SIRIUS M200D operating instructions
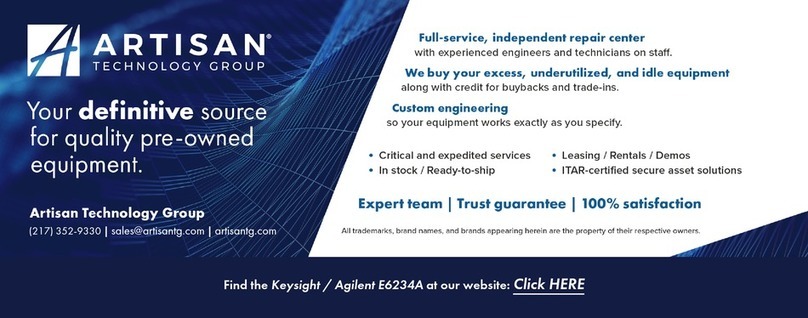
HP
HP VXI Pentium 75000 Series Hardware installation and configuration guide
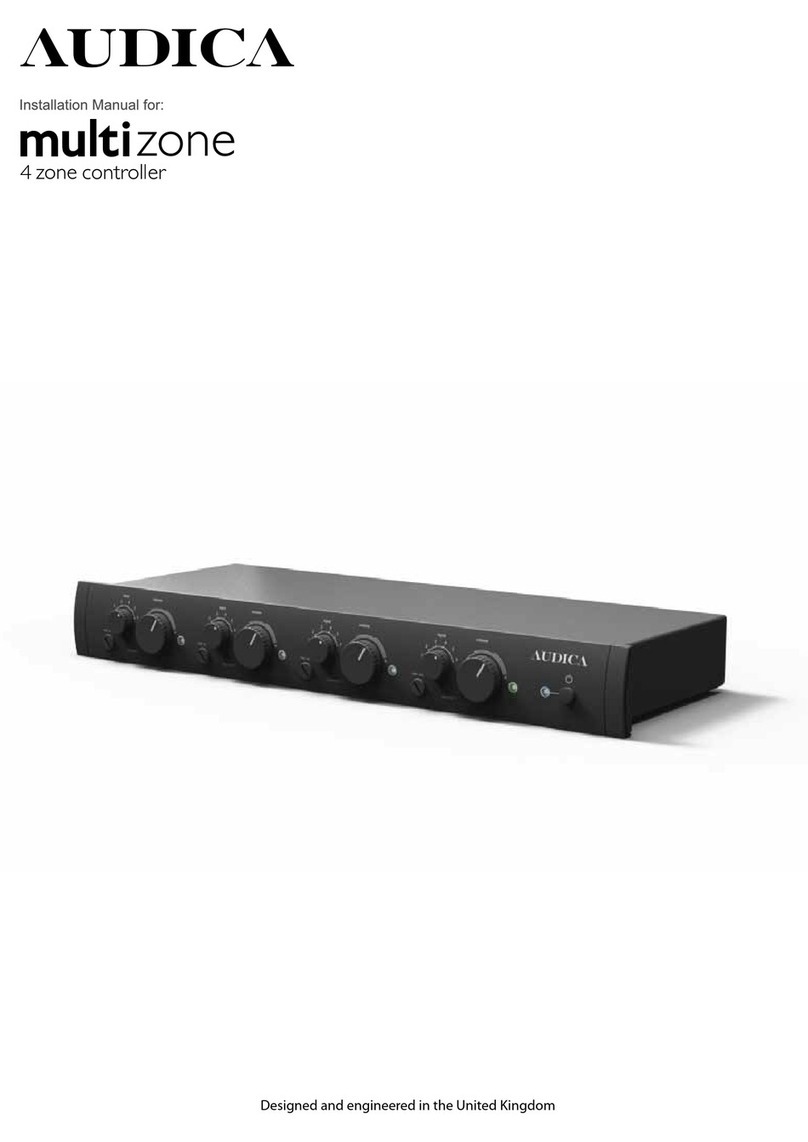
Audica
Audica MULTIzone installation manual

Effigy Labs
Effigy Labs Control Pedal Quick Start Guide and Limited Warranty

Simrad
Simrad IS40 Quick reference guide
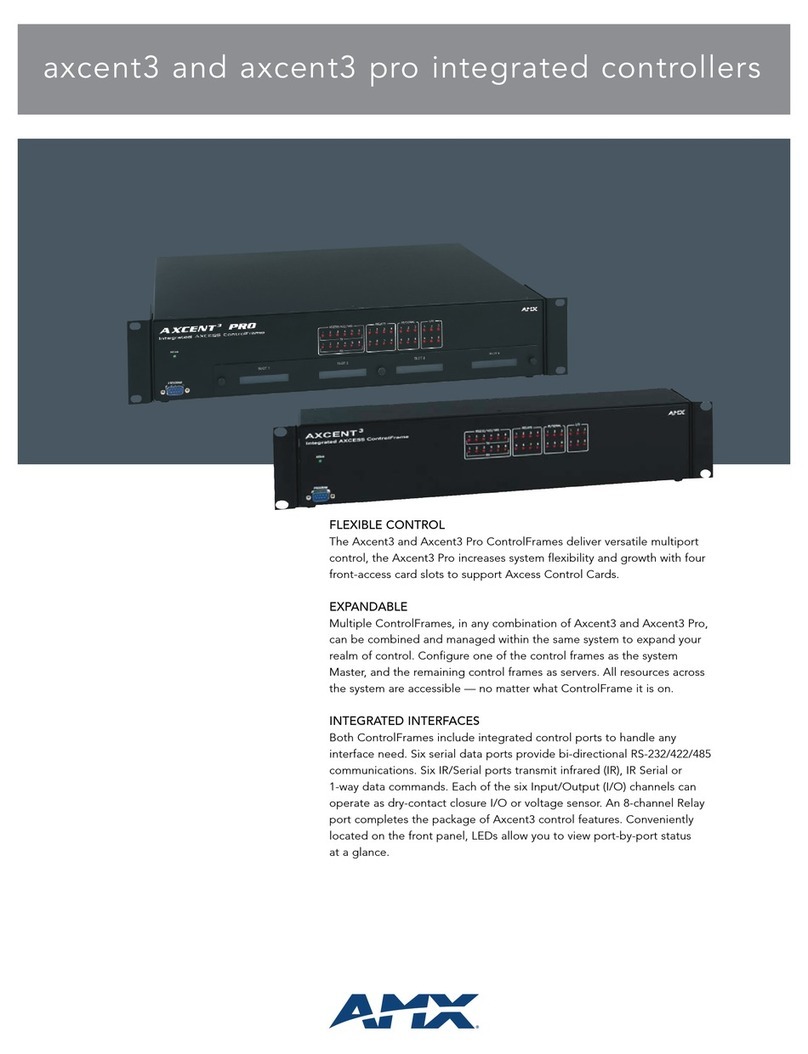
AMX
AMX Axcent3 pro Specifications

Cole Parmer
Cole Parmer TRACEABLE 4190 instructions
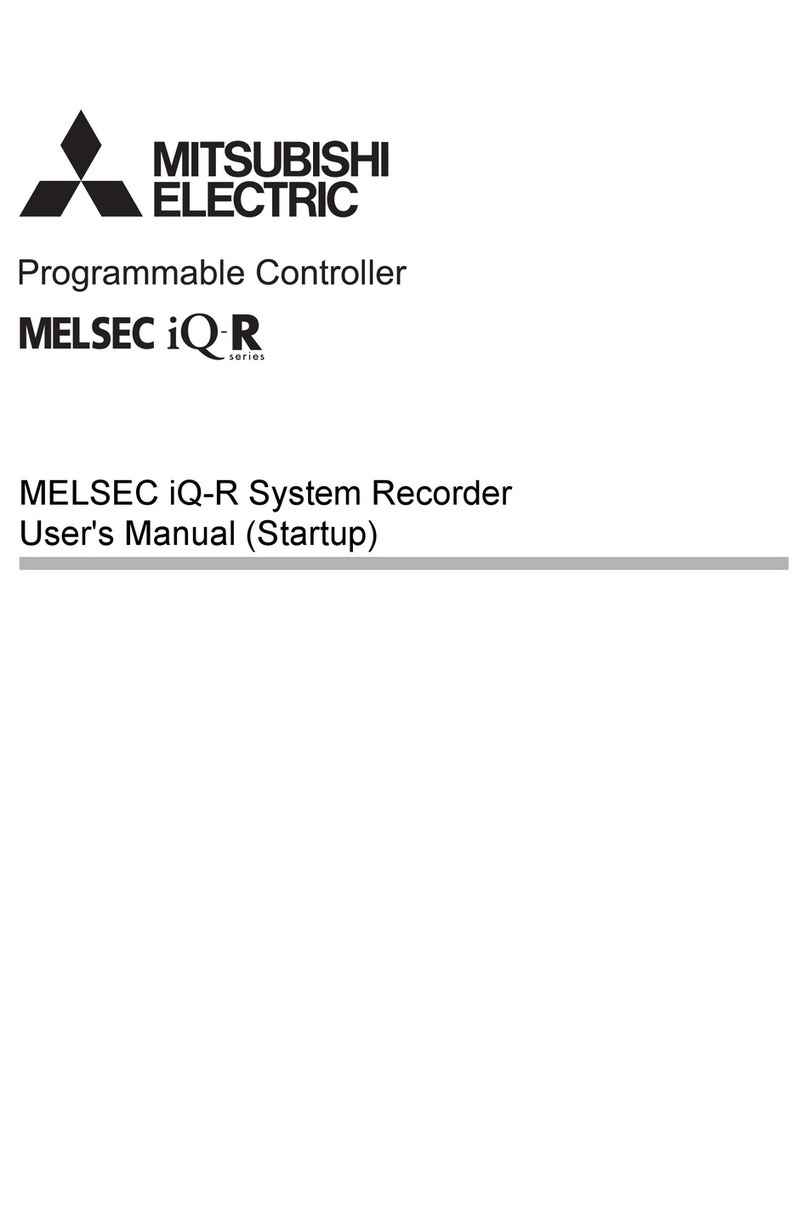
Mitsubishi Electric
Mitsubishi Electric MELSEC iQ-R Series user manual
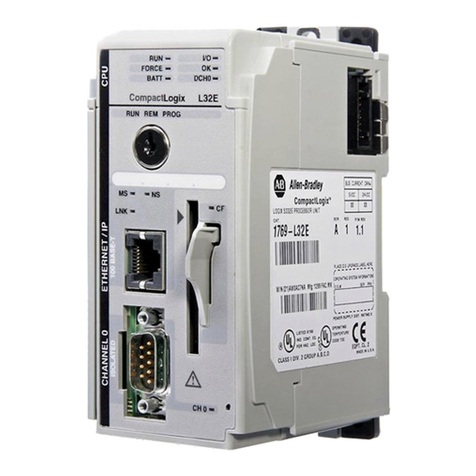
Rockwell Automation
Rockwell Automation Allen-Bradley Logix 5000 Series Programming manual
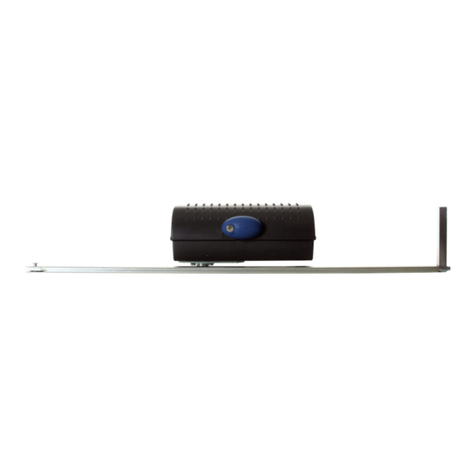
BFT
BFT IGEA LB Installation and user manual

Quantum Networks
Quantum Networks QN-I-200 Quick setup guide
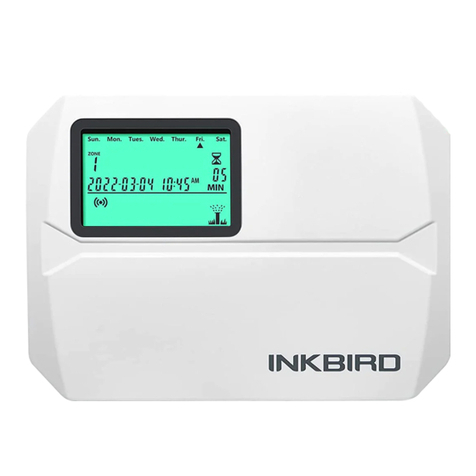
Ink Bird
Ink Bird IIC-800-WIFI user manual