Bühler technologies Fluidcontrol BCM-MS User manual

Fluidcontrol
Installation and Operation Instructions
Original instructions
Bühler Condition Monitor
BCM-MS, BCM-LS
BE150104
03/2021
Bühler Technologies GmbH, Harkortstr. 29, D-40880 Ratingen
Tel. +49 (0) 21 02 / 49 89-0, Fax: +49 (0) 21 02 / 49 89-20
E-Mail: [email protected]
Internet: www.buehler-technologies.com

Bühler Technologies GmbH, Harkortstr. 29, D-40880 Ratingen
Tel. +49 (0) 21 02 / 49 89-0, Fax: +49 (0) 21 02 / 49 89-20
Internet: www.buehler-technologies.com
E-Mail: [email protected]
Read this instruction carefully prior to installation and/or use. Pay at-
tention particularly to all advises and safety instructions to prevent in-
juries. Bühler Technologies can not be held responsible for misusing
the product or unreliable function due to unauthorised modifications.
All rights reserved. Bühler Technologies GmbH 2021
Document information
Document No...........................................................BE150104
Version......................................................................... 03/2021

BCM-MS, BCM-LS
Contents
1 Introduction..................................................................................................................................................................................................................... 3
1.1 Intended Use.........................................................................................................................................................................................................3
1.2 Functionality......................................................................................................................................................................................................... 3
1.2.1 Temperature Measurement..............................................................................................................................................................3
1.2.2 Moisture Measurement......................................................................................................................................................................3
1.2.3 Relative Humidity.................................................................................................................................................................................3
1.2.4 Conductivity Measurement.............................................................................................................................................................. 4
1.2.5 Measuring Relative Permittivity..................................................................................................................................................... 4
1.2.6 Level Measurement............................................................................................................................................................................. 4
1.2.7 Operating Hours Counter ................................................................................................................................................................. 4
1.2.8 Data Logger ........................................................................................................................................................................................... 4
1.2.9 Oil Condition..........................................................................................................................................................................................5
1.2.10 Determining The Remaining Useful Lifetime (RUL)...................................................................................................................5
1.2.11 Scope And Basic Parameters For Automatic Condition Analysis And RUL Calculation .................................................. 6
1.2.12 List Of All Measured And Derived Parameters............................................................................................................................ 6
1.2.13 Calibration And Sensor Function Test............................................................................................................................................7
1.2.14 List Of Parameter Outputs For Specific Commands.................................................................................................................. 8
1.3 BCM-MS model key ...........................................................................................................................................................................................10
1.4 BCM-LS model key .............................................................................................................................................................................................10
1.5 Scope Of Delivery...............................................................................................................................................................................................10
2 Safety instructions........................................................................................................................................................................................................ 11
2.1 Important advice................................................................................................................................................................................................11
2.2 General hazard warnings ................................................................................................................................................................................11
3 Installation and connection .......................................................................................................................................................................................13
3.1 Dimensions ..........................................................................................................................................................................................................13
3.2 Installation .......................................................................................................................................................................................................... 14
3.3 Electrical Connections.......................................................................................................................................................................................15
3.3.1 Analog Current Outputs (4..20 mA) - Measurement Without Load Resistor....................................................................16
3.3.2 Analog Current Outputs (4..20 mA) - Measurement With Load Resistor ..........................................................................16
3.3.3 Load Resistor Size................................................................................................................................................................................16
3.3.4 Calibration............................................................................................................................................................................................ 17
4 Operation and Control................................................................................................................................................................................................ 18
4.1 RS232 Communication..................................................................................................................................................................................... 18
4.1.1 Serial Port (RS232)...............................................................................................................................................................................18
4.1.2 Command List......................................................................................................................................................................................18
4.1.3 Setting Analog Current Outputs....................................................................................................................................................23
4.1.4 Output Triggering............................................................................................................................................................................. 24
4.1.5 Save Triggering .................................................................................................................................................................................. 24
4.1.6 Configuration For Automatic Condition Analysis ................................................................................................................... 24
4.2 CAN Communication........................................................................................................................................................................................25
4.2.1 CAN Interface.......................................................................................................................................................................................25
4.2.2 CANopen................................................................................................................................................................................................25
4.3 Before Initial Use ............................................................................................................................................................................................... 35
4.4 Initial Operation ................................................................................................................................................................................................ 35
4.4.1 Initial Operation With RS232 Port..................................................................................................................................................35
4.4.2 Initial Operation With CAN Interface .......................................................................................................................................... 36
4.4.3 Function Range Depending On Configuration......................................................................................................................... 36
4.5 Application Example ........................................................................................................................................................................................ 37
5 Cleaning And Maintenance.......................................................................................................................................................................................38
6 Service and repair.........................................................................................................................................................................................................39
6.1 Troubleshooting ................................................................................................................................................................................................39
6.2 BCM-MS accessories ........................................................................................................................................................................................ 40
6.3 Accessories BCM-LS.......................................................................................................................................................................................... 40
7 Disposal........................................................................................................................................................................................................................... 41
iBühler Technologies GmbHBE150104 ◦ 03/2021

BCM-MS, BCM-LS
8 Appendices.....................................................................................................................................................................................................................42
8.1 BCM-LS Technical Data ....................................................................................................................................................................................42
8.2 BCM-MS Technical Data ..................................................................................................................................................................................43
8.3 Standard pin assignment .............................................................................................................................................................................. 44
8.4 Permissible Mechanical Loads...................................................................................................................................................................... 44
8.5 Error Bits Key.......................................................................................................................................................................................................45
8.6 Load Factor Of A System................................................................................................................................................................................. 46
9 Attached documents...................................................................................................................................................................................................47
ii Bühler Technologies GmbH BE150104 ◦ 03/2021

BCM-MS, BCM-LS
1 Introduction
1.1 Intended Use
The BCM-MS200 and BCM-LS200 are used to measure and document changes in the properties of hydraulic and lubricating me-
dia and simultaneously measure the humidity and temperature. The respective measured values used to detect changes in the
properties as well as the temperature and humidity are detected continuously, saved and can be read out at any time using a
serial port. If the measured values deviate from a saved reference, this indicates changes which should be interpreted and in-
vestigated further.
Measured changes in the oil parameters can provide information about condition changes, e.g. oil aging, refreshing, changes or
water ingress. Damages can then potentially be detected early or even avoided. This allows taking suitable measures to avoid
serious machine malfunctions and prolong maintenance and oil change intervals. Furthermore, measured parameters and
changes in these can be used to derive and document information related to system maintenance carried out or the use of the
prescribed lubricant type.
The following chapters explain which situations changes in the condition can be detected. The sensor records the following
physical oil parameters and their time curve:
– temperature
– relative humidity
– conductivity
– relative fluid permittivity
– Liquid level (BCM-LS200 only)
Since the conductivity and relative permittivity in particularly greatly depend on the temperature, the sensor is able to convert
these parameters to a fixed reference temperature. The sensor continuously measures at various temperatures for this conver-
sion and uses this data to determine the temperature gradients of the parameters.
Determining the temperature gradient requires several temperature cycles when commissioning the sensor. During operation,
the temperature gradient is also continuously adjusted when oil is changed or ages.
1.2 Functionality
1.2.1 Temperature Measurement
A PT1000 platinum resistance sensor measures the oil temperature. The measuring range spans from -20°C to 120°C. Since the
resistance sensor is located directly in the oil, the conductivity of the surrounding medium should not exceed 3µSm (-1).
1.2.2 Moisture Measurement
The relative humidity (formula symbol: φ) is measured using a capacitive transducer. The capacitive moisture detector detects
the relative humidity within a measuring range of 0% to 100%. If free water or emulsions are present, the sensor shows 100%.
Since the moisture detector is located directly in the oil, the conductivity of the surrounding medium should not exceed 3µSm
(-1).
1.2.3 Relative Humidity
Relative humidity φ means the ratio between the actual amount of free water in the oil (ρW) compared to the maximum possible
free water at the saturation limit (ρW,max).
=ρ.
φ100 % (3-1)
w
ρw max
Since the saturation limit, i.e. the maximum amount of water it can hold ρW,max, greatly depends on the temperature, the relative
humidity changes with the temperature even if the absolute water content remains constant. As a rule, oil can hold more water
as the temperature rises before reaching the saturation limit.
3Bühler Technologies GmbHBE150104 ◦ 03/2021

BCM-MS, BCM-LS
1.2.4 Conductivity Measurement
Fresh oils have a characteristic conductivity. Since the conductivity is oil-specific due to manufacturing variations, it already
serves as a criterion for distinguishing oils. To be able to distinguish between oils based on conductivity, the conductivity at a
specific temperature or the change in conductivity above the temperature must be significantly distinct.
The introduction of impurities (solid/liquid) can also be detected provided this changes the conductivity at a specific temperat-
ure or the conductivity above the temperature.
Oil changes, oil mixing and contaminations can therefore be detected under the above conditions based on the conductivity.
Please also keep in mind that batch variances and oil aging can also affect conductivity.
Conductivity can change due to various aging processes, so in this case the aging process can also be tracked with conductivity.
The measuring range of conductivity ranges from <100 to approx. 800,000pS/m.
Since conductivity greatly depends on the temperature (a higher oil conductivity has a negative effect on the accuracy of the
measurement), the sensor internally converts to a reference temperature of 40°C. Another parameter for this conversion is the
temperature gradient of the parameter, which can also be used to define oil as specified above.
1.2.5 Measuring Relative Permittivity
The relative permittivity єOil of the fluid is a measure of its polarity. Base oils and additive packages with a different chemistry
and from different manufacturers can have different polarities. The polarity and the polarity trend of the fluid above the tem-
perature are therefore properties which under certain circumstances, e.g. taking into account batch variances, can be used to
determine oils being confused, mixed or refreshed.
Oils typically change their polarity throughout the aging process. If this causes a significant change in polarity, the aging process
can also be monitored. The measuring range for relative permittivity is 1...7.
Since the relative permittivity depends on the temperature, the sensor internally converts to a reference temperature of 40°C.
Another parameter for this conversion is the temperature gradient of the parameter, which - as specified above - can also be
used to define oil.
NOTICE!When used in highly conductive fluids, measuring the relative permittivity can be subject to cross-influence despite
the built-in compensation.
1.2.6 Level Measurement
The sensor features capacitive level detection. The liquid level is measured using the same principle as the dielectric constant.
The reference used for measurement is the dielectric constant determined by the sensor. This process allows capacitive detec-
tion of the liquid level without specifying the type of fluid.
NOTICE!When used in highly conductive fluids, the liquid level can be subject to cross-influence despite the built-in compensa-
tion.
1.2.7 Operating Hours Counter
The sensor has a built-in operating hours counter in which the values are retained after a power interruption. After the inter-
ruption, the counter continues from the last value prior to the interruption.
1.2.8 Data Logger
The built-in operating hours counter which starts as soon as the sensor is connected to power, allows allocating the measured
characteristics to a point in the operating hours. The timestamp, the four factors temperature, oil moisture, conductivity and re-
lative dielectric constant as well as the other derived characteristics are saved to the sensor ring buffer. Over 6000 datasets total
can be saved to the buffer.
4 Bühler Technologies GmbH BE150104 ◦ 03/2021

BCM-MS, BCM-LS
1.2.9 Oil Condition
Oil aging generally refers to any change in parameters and properties of the oil over its life. The goal is to use the changes to de-
rive significant aging processes in the oil using the parameters measured with the sensor. The automatic oil condition analysis,
however, goes beyond this. The goal here is to not only determine aging, but also other changes in the condition. Possible condi-
tion changes are:
– oil aging (e.g. oil oxidation)
– contamination with foreign fluids
– water ingress (e.g. high water content or free water)
– oil changes, including changing to the wrong type of oil
– Oil refreshing
– oils being mixed
The goal of automatic analysis is to help the user interpret the characteristics and determine various conditions and changes in
the condition from the current measurement data and the saved data history. Detecting conditions and changes in the condi-
tion as part of the rule base used, however, is only reliable if the measurements and their quality generally permit this interpret-
ation.
A detailed description of all detectable condition changes and how to query, save and configure parameters can be found in the
appendix.
1.2.10 Determining The Remaining Useful Lifetime (RUL)
In addition to classifying various conditions or condition changes, another sensor function is to determine the remaining useful
lifetime (RUL) based on available data.
Here we distinguish between two different approaches.
The following illustration is an example trend of a aging parameter over the operating time.
After an oil change, the oil parameters do not (significantly) change over a long period. After the so-called incubation period
(phase I), once certain additives (antioxidants) are depleted, oil aging then accelerates, often progressively (phase II).
PhaseII is characterised by an accelerated aging process, thus change in the aging parameters. In this area the signal trend of
the various measured parameters can be used to extrapolate a predetermined aging limit, thus is the remaining useful lifetime
(RUL).
A default parameter for the aging limit is factory preset. For specific information on setting the aging limits, please contact
Bühler Technologies GmbH Service.
NOTICE!The limits should be adjusted to the specific application. The remaining useful lifetime determined is a guideline de-
termined through linear extrapolation. Please note, aging processes can also be non-linear.
Incubation time
Phase II
Phase I
Aging
Time
Fig.1: Theoretical aging
5Bühler Technologies GmbHBE150104 ◦ 03/2021

BCM-MS, BCM-LS
Since the characteristics measured in phase I do not change, the RUL also cannot be determined based on characteristics. During
this phase, however, the RUL can be estimated based on the thermal stress at the measuring point. This is permissible so long as
the temperature is the decisive stress factor for the oil and decisive in the aging rate (Arrhenius law). The sensor continuously
detects a temperature histogram for this purpose. Furthermore, data can only be transmitted for comparable applications and
the same types of oil.
NOTICE!We will gladly assist you with the necessary parameter settings for calculating the RUL based on thermal stress (Phase
I). Please contact Bühler Technologies GmbH Service.
1.2.11 Scope And Basic Parameters For Automatic Condition Analysis And RUL
Calculation
Some basic parameters must be taken into account for the automatic condition analysis:
– Changes in the condition can only be determined if the information is included in the measured parameters. For example,
the measured parameters typically do not provide any information about the depletion of antioxidants.
– Individual critical changes in the oil can overlap in extreme cases so the resulting overall change does not reflect this condi-
tion.
– The respective conditions or condition changes have detection limits where the underlying signal changes or change gradi-
ents are not detected.
– The automatic condition analysis can be distorted due to cross-influences.
– The RUL calculation is only a rough estimate. In open systems with uncontrollable contamination and systems with strongly
varied operating conditions the uncertainty of the characteristics information increases. The parameter settings further
greatly affect the results.
– A purely mathematical estimate of the RUL based on measured burden factors cannot predict spontaneous condition
changes.
Overall, a sufficient data volume and purposeful parameter settings will typically yield a satisfactory accuracy and prediction of
the aging process.
1.2.12 List Of All Measured And Derived Parameters
The 5 original characteristics above are measured to define the oil condition. These parameters and their meaning are again lis-
ted in the table below.
# Parameter Abbre-
viation
Unit Explanation
1 Operating hours Time h runs when powered
2 Temperature T °C Oil temperature
3 Relative permittivity (rel. DK) P - Fluid polarity. Fresh oils differ in P and can therefore be distinguished.
Furthermore, P changes with oil aging.
4 Conductivity C pS/m Fresh oils differ in C and can therefore be distinguished. Furthermore,
C changes with oil aging.
5 rel. oil humidity RH % Rel. humidity between 0 and 100%
61 Liquid level L % Liquid level between 0 and 100
Tab.1: Original characteristics determined
The parameters depend on the temperature, which is compensated by the sensor. This compensation involves two additional
temperature gradients used to assess the condition.
# Original parameter Derived characteristic
Abbreviation
Unit Explanation
1 P PTG 1/K rel. DK - temperature gradient
2 C CTG (pS/m)/K Conductivity - temperature gradient
3 RH HTG %/K rel. oil humidity - temperature gradient
Tab.2: Derived temperature gradients
The sensor uses the original parameters P, C and RH as well as the determined temperature gradients PTG, CTG and HTG to cal-
culate the temperature-compensated parameters P40 and C40 and H20, H40 in the same unit as the respective original para-
meter.
NOTICE!The accuracy of determining PTG, CTG and HTG as well as the quality of the temperature compensation depend on the
fluid.
6 Bühler Technologies GmbH BE150104 ◦ 03/2021

BCM-MS, BCM-LS
# Original parameter Derived characteristic
Abbreviation
Explanation
1 P P40 rel. DK at reference temperature of 40 °C
2 C C40 Conductivity at reference temperature of 40 °C
3 RH RH202 1rel. oil humidity compensated to 20 °C oil temperature
Tab.3: Temperature-compensated characteristics
1 Compensation of relative humidity to 20°C greatly depends on the fluid, temperature profile and other factors
The sensor in turn uses original parameters, the temperature gradients and the compensated characteristics to determine time
gradients. The time gradients particularly provide information about the type of change in state.
# Original parameter Derived characteristic
Abbreviation
Unit Explanation
1 P40 LGP40 1/h Long-term gradient of P40
2 P40 MGP40 1/h P40 gradient over mean period
3 P40 SGP40 1/h Short-term gradient of P40
4 C40 LGC40 (pS/m)/h Long-term gradient C40
5 C40 MGC40 (pS/m)/h C40 gradient over mean period
6 C40 SGC40 (pS/m)/h Short-term gradient of C40
7 T LGT K/h Long-term gradient of oil temperature
8 T SGT K/h Short-term gradient of oil temperature
9 H20 SGH20 %/h Short-term gradient of H2O
Tab.4: Time gradients
Rapid changes indicate e.g. oil being added, but depending on the extent, slow gradients can indicate contamination with a for-
eign fluid or oil aging. Here the sensor determines short-term gradients with an averaging period of a few hours and long-term
gradients with an averaging period of several hundred to several thousand hours.
Please refer to chapter Error Bits Key [> page45] for a list of all parameters used in the assessment.
1.2.13 Calibration And Sensor Function Test
The sensor is developed to be exposed to the specified loads over prolonged periods.
For fluids or applications where there is no experiential base related to the long-term stability of the sensor, the sensor should
be inspected and calibrated at a laboratory at least every 2 years.
7Bühler Technologies GmbHBE150104 ◦ 03/2021

BCM-MS, BCM-LS
1.2.14 List Of Parameter Outputs For Specific Commands
The sensors support a series of commands to output the measured, deduced and calculated oil parameters. The following tables
list the responses to individual commands. Depending on the sensor firmware version, the order or even the contents of the out-
put may vary.
# Parameter name Unit Explanation
1 Time h Sensor operating hours counter
2 T °C Fluid temperature
3 L % Oil level in relation to measuring range (for level sensors only)
4 P - Relative fluid permittivity
5 P40 - Relative fluid permittivity compensated to 40°C fluid temperature
6 C pS/m Fluid conductivity
7 C40 pS/m Fluid conductivity compensated to 40°C fluid temperature
8 RH % Relative fluid humidity
9 RH20 % Relative fluid humidity compensated to 20°C (room temperature) fluid temperature (only
output if sensor not configured to AH output)
10 AH ppm Absolute water content of the fluid
(only output if sensor calibrated accordingly for this oil)
11 TMean °C Average fluid temperature since starting teach-in, or indicates oil refilling
12 PCBT °C Temperature of electronics or sensor
13 RULT h Temperature-based remaining useful lifetime (RUL) of the oil
14 RULLG h Long-term gradient- and limit-based RUL of the oil
15 RUL h Combined and weighted RUL
16 APP40 % Aging progress (AP) based on P40 and set limits
17 APC40 % AP based on C40 and set limits
18 AP: % Combined and weighted AP
19 fB - Temperature load factor since starting teach-in, or indicates oil refilling
20 OAge h Oil age, time since starting teach-in, or indicates oil refilling
21 ERC - Summary auto-detected oil conditions
Tab.5: Response to command "RVal"
# Parameter name Unit Explanation
1 Time h Sensor operating hours counter
2 PTG 1/k Temperature gradient of relative permittivity
3 CTG ln(pS/m)/
K
Temperature gradient of the natural logarithm of conductivity
4 HTG %/K Temperature gradient of relative humidity
5 LGP40 1/h Long-term gradient of P40
6 LGC40 (pS/m)/h Long-term gradient of C40
7 LGT K/h Long-term gradient of oil temperature
8 MGP40 1/h P40 gradient over mean period
9 MGC40 (pS/m)/h C40 gradient over mean period
10 SGP40 1/h Short-term gradient of P40
11 SGC40 (pS/m)/h Short-term gradient of C40
12 SGT K/h Short-term gradient of oil temperature
13 SGH20 %/h Short-term gradient of H20
Tab.6: Response to command "RGrad"
8 Bühler Technologies GmbH BE150104 ◦ 03/2021

BCM-MS, BCM-LS
# Parameter name Unit Explanation
1 AO1 - Configuration for analog output 1
2 AO2 - Configuration for analog output 2
3 ETrig - Error-triggered save to history (1 = on, 0 = off)
4 TrAu min Periodic dataset transfer as output for RVal command with an interval of the minutes spe-
cified (range 1..60minutes, if set to 0, automatic transfer is off)
5 ORef - Automatic teach-in status
(0: completed, 1..30: in progress, >30: not started)
6 COEN - CANopen communication (0: off, 1: on)
7 Memlnt min Interval at which data is saved to history (default: 20minutes)
8 COSpd kBit/s CAN bus speed
9 COID - Sensor nodeID
10 COHBeat ms Sensor CANopen heart beat
11 TPDO1ID - TPDO 1COB-ID for CANopen
12 TPDO2ID - TPDO 2 COB-ID for CANopen
13 TPDO1Type - TPDO 1 type for CANopen
14 TPDO2Type - TPDO 2 type for CANopen
15 TPDO1Timer ms TPDO 1 timer for CANopen
16 TPDO2Timer ms TPDO 2 timer for CANopen
17 RULowr h Timer for overwriting the RUL calculation (if a system sensor fails, the replacement sensor
can have the RUL value of the previous sensor the RUL counts down from)
Tab.7: Response to command "RCon"
# Parameter name Unit Explanation
1 LimP40% 5 Oil aging limit for P40 in % from fresh oil value (default: 5%)
2 LimC40% % Oil aging limit for C40 in % from fresh oil value up (default: 300%), permissible downward
deviation is automatically calculated from this specification
3 LimT °C Maximum permissible oil temperature
(if exceeded, the corresponding bit is set in ERC, default: 85°C)
4 LimTMean °C Average maximum permissible oil temperature
(if exceeded, the corresponding bit is set in ERC, default: 65°C)
5 RULh h Reference value for the oil lifetime in hours (specified by machine manufacturer)
17 RULfB - Oil life reference value (specified by machine manufacturer)
Tab.8: Response to command "RLim"
# Parameter name Unit Explanation
1 RefStat - Automatic teach-in status
(0: completed, 1..30: in progress, >30: not started)
2 RefC40 pS/m Taught-in fresh oil conductivity reference value at 40°C
3 RefP40 - Taught-in fresh oil relative permittivity reference value at 40°C
4 RefCTG (pS/m)/K Taught-in conductivity temperature gradient reference value
17 RefPTG 1/K Taught-in relative permittivity temperature gradient reference value
Tab.9: Response to command "RORef"
9Bühler Technologies GmbHBE150104 ◦ 03/2021

BCM-MS, BCM-LS
1.3 BCM-MS model key
BCM - MS200 - 1DC2A
Type designation
Outputs
1DC2A
Multisensor
BCM Bühler Condition Monitor
M
1x CANopen/2x analog
Sensor
S
Process connection
0G3/4"
Item no. Model
1550001000 BCM-MS200-1DC2A
1.4 BCM-LS model key
BCM - LS200 - 1DC2A / xxx
Type designation
Outputs
1DC2A
Multisensor incl. liquid level measurement
BCM Bühler Condition Monitor
L
1x CANopen/2x analog
Sensor
S
Process connection
0G3/4"
Length
200 mm
375 mm
615 mm
Item no. Model
1550002200 BCM-LS200-1DC2A/200
1550002375 BCM-LS200-1DC2A/375
1550002615 BCM-LS200-1DC2A/615
1.5 Scope Of Delivery
– Bühler Condition Monitor BCM
– Product Documentation
10 Bühler Technologies GmbH BE150104 ◦ 03/2021

BCM-MS, BCM-LS
2 Safety instructions
2.1 Important advice
This device may only be used if:
– The product is being used under the conditions described in the operating- and system instructions, used according to the
nameplate and for applications for which it is intended. Any unauthorized modifications to the device will void the warranty
provided by Bühler Technologies GmbH,
– the specifications and markings in the type plate are observed,
– the limits in the data sheet and the instructions must be observed,
– monitoring equipment / protection devices must be connected correctly,
– the device is protected from mechanical damage and vibration,
– service and repairs not described in these instructions is performed by Bühler Technologies GmbH,
– using genuine replacement parts.
These operating instructions are a part of the equipment. The manufacturer reserves the right to change performance-, specific-
ation- or technical data without prior notice. Please keep these instructions for future reference.
Signal words for warnings
DANGER
Signal word for an imminent danger with high risk, resulting in severe injuries or death if not avoided.
WARNING
Signal word for a hazardous situation with medium risk, possibly resulting in severe injuries or death if not
avoided.
CAUTION
Signal word for a hazardous situation with low risk, resulting in damaged to the device or the property or
minor or medium injuries if not avoided.
NOTICE
Signal word for important information to the product.
Warning signs
These instructions use the following warning signs:
General warning General information
2.2 General hazard warnings
The equipment must be installed by a professional familiar with the safety requirements and risks.
Be sure to observe the safety regulations and generally applicable rules of technology relevant for the installation site. Prevent
malfunctions and avoid personal injuries and property damage.
The operator of the system must ensure:
– Safety notices and operating instructions are available and observed,
– The respective national accident prevention regulations are observed,
– The permissible data and operational conditions are maintained,
– Safety guards are used and mandatory maintenance is performed,
– Legal regulations are observed during disposal,
– compliance with national installation regulations.
11Bühler Technologies GmbHBE150104 ◦ 03/2021

BCM-MS, BCM-LS
Maintenance, Repair
Please note during maintenance and repairs:
– Repairs to the unit must be performed by Bühler authorised personnel.
– Only perform conversion-, maintenance or installation work described in these operating and installation instructions.
– Always use genuine spare parts.
– Do not install damaged or defective spare part. If necessary, visually inspect prior to installation to determine any obvious
damage to the spare parts.
Always observe the applicable safety and operating regulations in the respective country of use when performing any type of
maintenance.
The method for cleaning the devices must be adapted to the IP protection class of the devices. Do not use cleaners which could
damage the device materials.
12 Bühler Technologies GmbH BE150104 ◦ 03/2021

BCM-MS, BCM-LS
3 Installation and connection
3.1 Dimensions
BCM-LS200: L = 200 mm, Level measuring range = 115 mm
8 pin A Coding (Male)
8 pin A Coding (Male)
Sealing ring
Sealing ring
Level measuring range
Connection dimensions BCM-LS200
Connection dimensions BCM-MS200
Distance from oil sump
13Bühler Technologies GmbHBE150104 ◦ 03/2021

BCM-MS, BCM-LS
3.2 Installation
The sensor is a screw-in sensor with ¾" thread. The level sensor must be screwed vertically into application tank from above, the
BCM-MS200 can either be installed sideways in the tank or in a flow pipe using a line adapter.
Condition monitoring requires the bottom 5 cm of the sensor to be bathed in oil for Level 200/375/615. The probe head of the
BCM-MS200 should always be in oil. Maximum pressure and temperature ratings should generally be observed in the sensor
placement.
Screw the sensor into a prepared mount inside the tank. A profiled sealing ring seals this from the oil side. To ensure proper
sealing, the seal face of the sensor mount should be specially prepared and have a maximum roughness value of Rmax=16. The
tightening torque for the sensor is 45Nm ±4.5Nm.
Tank
Consumer
Pump
Line adapter
Item no.: 1590001005
Fig.2: Installation options
Tank Tank
Fig.3: Installation options
To ensure proper function, please observe the following guidelines related to sensor mounting position and location.
– To analyse an oil volume characteristic of the oil condition, the sensor should not be immediately in the oil sump of the tank.
– For tank top installation, it will preferably be mounted near the return or flushing pipe.
– Ensure the sensor is fully covered in oil regardless of the system operating situation. Particularly note the varying oil volume
of the tank or potential inclination. Avoid foam in the tank.
– When installing the return or flushing pipe, please note the flushing pipe must not run dry in any operating situation.
– To avoid thermal factors as much as possible, the sensor should not be installed in the immediate vicinity of hot components
and parts (e.g. motor).
– Varying oil temperatures are required to enable converting the characteristics to a reference temperature. The greater the
temperature fluctuations, the quicker the temperature gradient can be determined.
14 Bühler Technologies GmbH BE150104 ◦ 03/2021

BCM-MS, BCM-LS
Tank
Tank
Fig.4: Installation recommendations
3.3 Electrical Connections
WARNING Faulty power supply
Danger to life – risk of injury
The device must be installed by an electrician.
Observe national and international regulations on the installation of electrical equip-
ment.
Power supply as per EN50178, SELV, PELV, VDE0100-410/A1.
To install, switch off the machine and connect the device as follows:
Pin/assignment
Sensor cover top view Standard cable colour
white
brown
green
yellow
grey
pink
blue
red
Housing/shield
Fig.5: Sensor plug pin assignment
The permitted operating voltage is between 9V and 33VDC. The sensor cable must be shielded.
To ensure protective class IP67, only use suitable plugs and cables. The tightening torque for the plug is 0.1Nm.
15Bühler Technologies GmbHBE150104 ◦ 03/2021

BCM-MS, BCM-LS
3.3.1 Analog Current Outputs (4..20 mA) - Measurement Without Load Resistor
The current should be measured with a suitable ammeter as shown below.
Sensor cover top view
Fig.6: Measuring the analog 4...20 mA outputs without load resistances
Please refer to chapter Calibration [> page17] for how to allocate the measured current to the parameter.
3.3.2 Analog Current Outputs (4..20 mA) - Measurement With Load Resistor
To measure the currents of the analog current outputs, a load resistor must be connected to each output as shown below. De-
pending on the supply voltage, the load resistance should be between 25Ohm and 200Ohm. A voltmeter can now be used to
measure the voltage which drops over the respective resistance.
Sensor cover top view
Fig.7: Connecting the load resistances to measure the analog 4..20 mA outputs
The default configuration is intended for oil temperature on channel 1 and relative humidity on channel 2.
The channel assignment can be changed and is described in chapter Setting Analog Current Outputs [> page23].
3.3.3 Load Resistor Size
The load resistance cannot be selected arbitrarily. It must be adjusted to the supply voltage of the sensor. The maximum load
resistance can be calculated using the formula (6 -1). Or you can alternatively use the table here.
Rmax / Ω=USupply / V ∙ 25 (Ω/V) – 200 Ω 25 Ω ≤ Rmax Ω 200 Ω (6-1)
Rmax in Ω Usupply in V
25 9
50 10
100 12
150 14
200 16
Tab.10: Determining the load resistance based on the supply voltage
16 Bühler Technologies GmbH BE150104 ◦ 03/2021

BCM-MS, BCM-LS
3.3.4 Calibration
Output quantity X Output range Quantity equation Formula
T in °C -20°C...120°C
/U / V .
XR / Ω 8750 - 55°C
(°C
°C =/A)
(6-2)
RH in % 0%...100%
/U / V .
XR / Ω 6250 - 25%
(%
%=/A)
(6-3)
H20; H40 in % 0%...100%
/U / V .
XR / Ω 6666,67 - 33,33%
(%
%=/A)
(6-4)
AH in ppm 0ppm...AHScl
/U / V .
XR / Ω
ppm =AHScl / ppm
16 .10-3 A-AHScl / ppm
4
(6-5)
P; P40 1...5
=U / V .
XR / Ω 266,67 - 0,3333
1
A
()
< 5 mA: Teaching in or sensor partially exposed to air
(6-6)
C; C40 in pS/m 100pS/m... 1000100 pS/m
=U / V .
XR / Ω 6,667 - 333233
pS
A
()
/pS/m.107pS
m
< 5 mA: Teach-in
(6-7)
AP in % 0%...100%
=U / V .
XR / Ω 6250 - 25 %
%
A
()
(6-8)
L in % 0%...100%
=U / V .
XR / Ω 6250 - 25 %
%
A
()
(6-9)1
log(C); log(C40) in
pS/m
1pS/m...1000000 pS/m
=
U / V .
XR / Ω 375 pS
A
()
/pS/m-
10 1,5 log
()pS
m
()
(6-10)2
Tab.11: Calculating the output parameter for the analog current outputs
By default, the current outputs show the temperature between -20°C and 120°C and the relative humidity between 0 and
100%. The upper limit for the absolute humidity (AHScl) is required to scale the analog current outputs. This is freely program-
mable. However, the limit is oil-specific and must be determined at a laboratory along with the other parameters required to
measure the absolute humidity.
Please contact Bühler Technologies GmbH Service in this regard. The current outputs are scaled linear.
lout in mA 4 5 12 20
T in °C -20 -11.25 50 120
RH, H20, H40 in % 0 6.25 50 100
AH in ppm 0 0.0625*AHScl 0.5*AHScl AHScl
P; P40 Teach-in mode enabled 1 2.867 5
C; C40 ibn pS/m Teach-in mode enabled 100 466807 1000100
log(C); log(40) in pS/m 1 2.37 1000 1000000
AP: 0 6.26 50 100
L 0 6.25 50 100
Tab.12: Scaling the analog current outputs
17Bühler Technologies GmbHBE150104 ◦ 03/2021

BCM-MS, BCM-LS
4 Operation and Control
NOTICE
The device must not be operated beyond its specifications.
4.1 RS232 Communication
Communication with the sensor takes place either via serial RS232 port, CANopen or via two analog 4...20mA outputs.
The sensors come standard with RS232 port enabled. In this mode it’s quite easy to configure the analog interface and to config-
ure the CANopen communication parameters. If necessary, a RS232 command can then be used to switch to CANopen interface
(see chapter Write Commands [> page20], command WCOEN), which will be applied after restarting the sensor.
We recommend the software ("CMSensorDataViewer" and "CMSensorConfig") available for download at www.buehler-technolo-
gies.com to configure and/or operate the sensor via PC. The software provides easy access to sensor data and configuring the
sensor without the use of terminal programs when operating the sensor via PC.
If the sensor is in CANopen mode, the RS232 port can be permanently switched to Index 0x2020, Subindex3, which will be ap-
plied after restarting the sensor.
If the sensor is in CANopen mode, the RS232 port can also be changed temporarily. In this case, connect the sensor to the RS232
port configured accordingly and whilst booting, press the pound key (#) until the sensor responds with its ID. If the sensor does
not respond within 10seconds after connecting power, repeat the process.
4.1.1 Serial Port (RS232)
The sensor has a serial port which can be used to read and configure it. This requires a PC and the corresponding terminal pro-
gram or a readout software. Both are detailed in the following chapters.
First you will need to select an existing free COM port on your PC to connect the sensor to. A suitable communication cable for
the serial connection between the sensor and PC/control unit is available under Item no. 1590001001. If the PC does not have a
standard COM port, you can also use serial port cards or USB to serial adapter, Item no. 1590001002.
When starting the sensor in CAN mode, it must first be changed to RS232 mode. After connecting the sensor to power, the sensor
checks the line to determine whether it’s connected to a serial port and if a defined character ("#") is sent, which must be set
during start-up. If the character is not sent, the sensor switches to CANopen mode. If it understands the sent character, it
switches to communication via RS232. Here the command for RS232 mode can be permanently enabled.
When restarting the sensor, it will then automatically start in RS232 mode and the above steps can be skipped.
4.1.1.1 Interface Parameters
– Baudrate: 9600
– Data bits: 8
– Parity none
– Stop bits: 1
– Flow control: No
4.1.2 Command List
The following lists all interface commands for communication with the sensor.
These can be sent to the sensor via terminal program, e.g. Microsoft Windows HyperTerminal.
18 Bühler Technologies GmbH BE150104 ◦ 03/2021
This manual suits for next models
1
Table of contents
Other Bühler technologies Measuring Instrument manuals

Bühler technologies
Bühler technologies BCI 24-D Series Reference guide

Bühler technologies
Bühler technologies GAS 222.20 User manual

Bühler technologies
Bühler technologies FCT User manual

Bühler technologies
Bühler technologies 222 AMEX Series Owner's manual
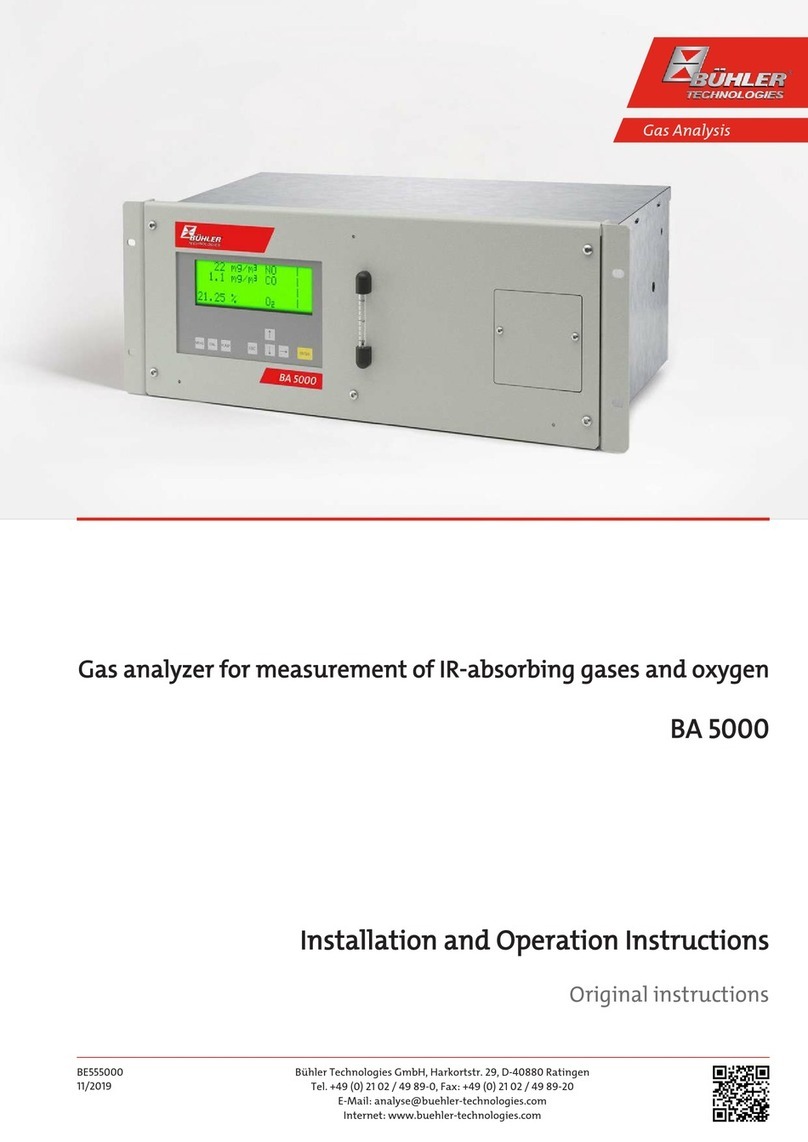
Bühler technologies
Bühler technologies BA 5000 User manual
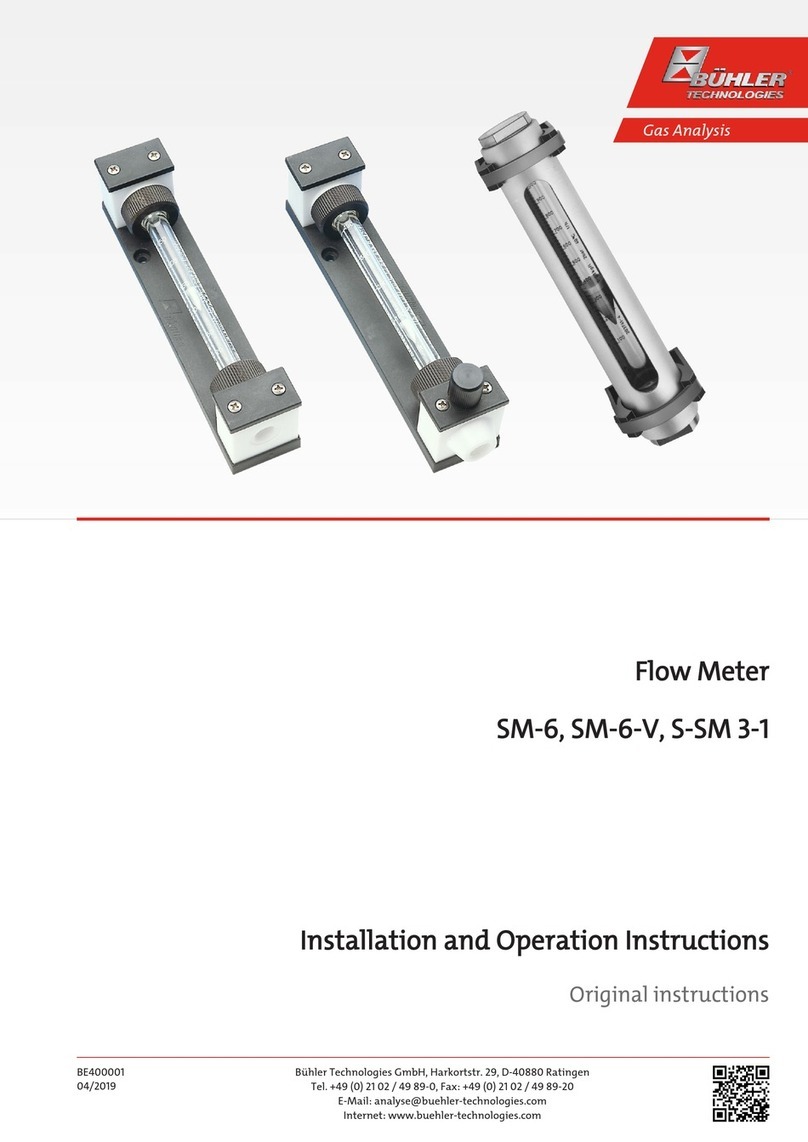
Bühler technologies
Bühler technologies SM-6 Series User manual

Bühler technologies
Bühler technologies SM-6 Series Owner's manual

Bühler technologies
Bühler technologies GAS 222.15 User manual

Bühler technologies
Bühler technologies GAS 222.35U Installation instructions

Bühler technologies
Bühler technologies GAS 222.35 User manual