Bühler technologies GAS 222.35 User manual

Gas Analysis
Installation and Operation Instructions
Original instructions
Sample gas probes
GAS 222.35
BE460062
09/2021
Bühler Technologies GmbH, Harkortstr. 29, D-40880 Ratingen
Tel. +49 (0) 21 02 / 49 89-0, Fax: +49 (0) 21 02 / 49 89-20
E-Mail: [email protected]
Internet: www.buehler-technologies.com

Bühler Technologies GmbH, Harkortstr. 29, D-40880 Ratingen
Tel. +49 (0) 21 02 / 49 89-0, Fax: +49 (0) 21 02 / 49 89-20
Internet: www.buehler-technologies.com
E-Mail: [email protected]
Read this instruction carefully prior to installation and/or use. Pay at-
tention particularly to all advises and safety instructions to prevent in-
juries. Bühler Technologies can not be held responsible for misusing
the product or unreliable function due to unauthorised modifications.
All rights reserved. Bühler Technologies GmbH 2021
Document information
Document No......................................................... BE460062
Version......................................................................... 09/2021

GAS 222.35
Table of Contents
1 Introduction..................................................................................................................................................................................................................... 2
1.1 Intended Use.........................................................................................................................................................................................................2
1.2 Type Plate............................................................................................................................................................................................................... 2
1.3 Scope of Delivery..................................................................................................................................................................................................2
1.4 Ordering instructions ........................................................................................................................................................................................ 3
1.5 Product Description............................................................................................................................................................................................ 3
2 Safety instructions.........................................................................................................................................................................................................4
2.1 Important advice .................................................................................................................................................................................................4
2.2 General hazard warnings ................................................................................................................................................................................. 5
3 Transport and storage ..................................................................................................................................................................................................6
4 Installation and connection ........................................................................................................................................................................................ 7
4.1 Installation site requirements......................................................................................................................................................................... 7
4.2 Installing the upstream filter .......................................................................................................................................................................... 7
4.3 Insulation............................................................................................................................................................................................................... 7
4.4 Connecting the Gas Line.................................................................................................................................................................................... 7
4.4.1 Blowback Connection......................................................................................................................................................................... 8
4.4.2 Connecting the Gas Line.................................................................................................................................................................... 8
4.4.3 Connecting the calibrating gas line (optional)........................................................................................................................... 8
4.5 Connecting the Blowback and Pressure Vessel (Optional) .....................................................................................................................8
4.6 Electrical connections ........................................................................................................................................................................................9
4.6.1 Connection via Terminal Strip......................................................................................................................................................... 9
4.6.2 Heated Pressure Vessel (Optional) ................................................................................................................................................. 9
5 Operation and Control................................................................................................................................................................................................ 10
5.1 Basic function of the probe controller.........................................................................................................................................................10
5.1.1 Regulator Functions...........................................................................................................................................................................10
5.1.2 Advanced functions for built-in blowback control (optional)...............................................................................................10
5.2 Use of menu functions ....................................................................................................................................................................................10
5.2.1 Menu Navigation Overview .............................................................................................................................................................11
5.2.2 Detailed description of the operational principle .................................................................................................................... 12
5.3 Description of menu functions ..................................................................................................................................................................... 12
5.3.1 Main Menu ........................................................................................................................................................................................... 12
5.3.2 Probe Controller Submenu [Display: Prob]................................................................................................................................. 13
5.3.3 Regulator Submenu for Heated Extension [Display: Adon] (Optional).............................................................................. 13
5.3.4 Submenu Blowback control [Display: bbc] (optional) .............................................................................................................14
6 Service...............................................................................................................................................................................................................................15
6.1 Maintaining the Filter Element......................................................................................................................................................................15
6.1.1 Replacing the upstream filter.........................................................................................................................................................16
6.2 Inlet filter blowback (within the process stream).................................................................................................................................... 16
6.2.1 Manual Blowback (Without Blowback Control) ........................................................................................................................ 17
6.2.2 Automatic Blowback (External Blowback Control)................................................................................................................... 17
6.2.3 Built-In Blowback Control (Optional)............................................................................................................................................ 17
7 Service and repair......................................................................................................................................................................................................... 18
7.1 Troubleshooting ................................................................................................................................................................................................ 18
7.2 Spare Parts and Accessories ........................................................................................................................................................................... 19
8 Disposal...........................................................................................................................................................................................................................20
9 Appendices......................................................................................................................................................................................................................21
9.1 Technical Data.................................................................................................................................................................................................... 21
9.2 Flow chart ............................................................................................................................................................................................................ 21
9.3 Dimensions .........................................................................................................................................................................................................22
9.4 Connection Diagram ........................................................................................................................................................................................23
9.5 Connection diagram heated pressure vessel............................................................................................................................................24
9.6 User book (Please make copies) ....................................................................................................................................................................25
10 Attached Documents...................................................................................................................................................................................................26
iBühler Technologies GmbHBE460062 ◦ 09/2021

GAS 222.35
1 Introduction
1.1 Intended Use
The sample gas probe is intended for installation into gas analysis systems in commercial applications.
Sample gas probes are among the main components in a gas conditioning system.
– Therefore also note the related drawing in the data sheet in the appendix.
– Before installing the device, verify the listed technical data meet the application parameters.
– Further verify all contents are complete.
Please refer to the type plate to identify your model. In addition to the job number/ID number, this also contains the article
number and model designation.
Please note the specific values of the device when connecting, and the correct versions when ordering spare parts.
1.2 Type Plate
Example:
GAS 222.35
100107323 462235009902000112213 001
230V 50/60Hz 440W
Material: 1.4571/1.4408/PTFE
Read manual!
Manufacturer and address
Model designation
Order no., Item no.
Material
Electrical supply
1.3 Scope of Delivery
– 1 x Sample gas probe
– 1 x Flange gasket and screws
– Product documentation
– Connection and mounting accessories (only optional)
2 Bühler Technologies GmbH BE460062 ◦ 09/2021

GAS 222.35
1.4 Ordering instructions
The item number is a code for the configuration of your unit. Please use the following model key:
4622235 0 9 9 0 X X 0 0 X X X 9 9 9 Product Characteristics
Flange / approval
0 DIN DN65 PN6
Power supply sample probe
1 115 V
2 230 V
Calibrating gas connection
0 No calibrating gas connection
1 6 mm
2 6 mm + check valve
3 1/4"
4 1/4" + check valve
Connection heated extension
0 No
Built-in temperature controller 1)
0 No
Blowback with air reservoir 2)
Air reservoir heating
1 Yes
9 No
Built-in blowback control 1)
1 Internal controller
9 No
Compressed air valve / valve voltage information
0 Manual
1 115 V
2 230 V
3 24 V
9 None (if no blowback requested)
Pneumatic drive for ball valve
9 N/A
Limit switch for pneumatic drive
9 No
Control valve for pneumatic drive
9 No control valve
1) The electronics can either be equipped with temperature controller for heated extension or blowback control
2) For flammable sample gas, always use inert gas for blowback. Probe blowback prohibited when using explosive gases!
1.5 Product Description
Probe Description
GAS 222.35 Probe with retractable inlet filter and blowback connection
Accessories Please refer to the data sheet at the end of this manual for accessories for this probe
3Bühler Technologies GmbHBE460062 ◦ 09/2021

GAS 222.35
2 Safety instructions
2.1 Important advice
Operation of the device is only valid if:
– the product is used under the conditions described in the installation- and operation instruction, the intended application
according to the type plate and the intended use. In case of unauthorized modifications done by the user Bühler Technolo-
gies GmbH can not be held responsible for any damage,
– when complying with the specifications and markings on the nameplates.
– the performance limits given in the datasheets and in the installation- and operation instruction are obeyed,
– monitoring devices and safety devices are installed properly,
– service and repair is carried out by Bühler Technologies GmbH,
– only original spare parts are used.
This manual is part of the equipment. The manufacturer keeps the right to modify specifications without advanced notice. Keep
this manual for later use.
Signal words for warnings
DANGER
Signal word for an imminent danger with high risk, resulting in severe injuries or death if not avoided.
WARNING
Signal word for a hazardous situation with medium risk, possibly resulting in severe injuries or death if not
avoided.
CAUTION
Signal word for a hazardous situation with low risk, resulting in damaged to the device or the property or
minor or medium injuries if not avoided.
NOTICE
Signal word for important information to the product.
Warning signs
In this manual, the following warning signs are used:
Warning against hazardous situations General notice
Warning against electrical voltage Disconnect from mains
Warning against respiration of toxic gases Wear respirator
Warning against acid and corrosive substances Wear eye/face protection
Warning against potentially explosive atmospheres Wear protection gloves
Warning against hot surface
4 Bühler Technologies GmbH BE460062 ◦ 09/2021

GAS 222.35
2.2 General hazard warnings
The equipment must be installed by a professional familiar with the safety requirements and risks.
Be sure to observe the safety regulations and generally applicable rules of technology relevant for the installation site. Prevent
malfunctions and avoid personal injuries and property damage.
The operator of the system must ensure:
– Safety notices and operating instructions are available and observed,
– The respective national accident prevention regulations are observed,
– The permissible data and operational conditions are maintained,
– Safety guards are used and mandatory maintenance is performed,
– Legal regulations are observed during disposal,
– compliance with national installation regulations.
Maintenance, Repair
Please note during maintenance and repairs:
– Repairs to the unit must be performed by Bühler authorised personnel.
– Only perform conversion-, maintenance or installation work described in these operating and installation instructions.
– Always use genuine spare parts.
– Do not install damaged or defective spare part. If necessary, visually inspect prior to installation to determine any obvious
damage to the spare parts.
Always observe the applicable safety and operating regulations in the respective country of use when performing any type of
maintenance.
DANGER Electrical voltage
Electrocution hazard.
a) Disconnect the device from power supply.
b) Make sure that the equipment cannot be reconnected to mains unintentionally.
c) The device must be opened by trained staff only.
d) Regard correct mains voltage.
DANGER Toxic, corrosive gases
The measuring gas led through the equipment can be hazardous when breathing or
touching it.
a) Check tightness of the measuring system before putting it into operation.
b) Take care that harmful gases are exhausted to a save place.
c) Before maintenance turn off the gas supply and make sure that it cannot be turned
on unintentionally.
d) Protect yourself during maintenance against toxic / corrosive gases. Use suitable pro-
tective equipment.
DANGER Potentially explosive atmosphere
Explosion hazard if used in hazardous areas.
The device is not suitable for operation in hazardous areas with potentially explosive at-
mospheres.
Do not expose the device to combustible or explosive gas mixtures.
5Bühler Technologies GmbHBE460062 ◦ 09/2021

GAS 222.35
3 Transport and storage
Only transport the product inside the original packaging or a suitable alternative.
The equipment must be protected from moisture and heat when not in use. They must be stored in a covered, dry and dust-free
room at a temperature between -20°C to 50°C (-4°F to 122°F).
6 Bühler Technologies GmbH BE460062 ◦ 09/2021

GAS 222.35
4 Installation and connection
4.1 Installation site requirements
Sample gas probes are intended for flange mounting.
– Installation site and installation position are determined based on requirements specific to the application.
– If necessary, the connection piece should be slightly tilted toward the centre of the channel.
– The installation site should be protected from the weather.
– In addition, adequate and safe access for installation and future maintenance work should be provided. Particularly follow
the uninstalled size of the probe tube!
If the probe is transported to the installation site in pieces, it will first need to be assembled.
4.2 Installing the upstream filter
The upstream filter, if necessary with matching extension, must be screwed in. The probe is then attached to the mating flange
using the included seals and screws.
4.3 Insulation
On heated probes completely insulate any exposed flange areas and, if applicable, the connection piece to absolutely prevent
thermal bridges. The insulating material must meet the application requirements and be weatherproof.
4.4 Connecting the Gas Line
The sample gas line must be carefully and properly connected using a suitable fitting.
This table provides an overview of the sample gas probe connections:
Probe
GAS 222
Reservoir
PAV01
Ball valve
pneumatic drive
Control valve
3/2-way solenoid
valve
Connecting flange 1) DN65/PN6/
DN3“-150 2)
Sample gas inlet G3/4
Sample gas outlet NPT 1/4
Blowback connection G3/8
Test gas connection 1) Tube Ø6 mm
Tube Ø1/4 2)
Filling port NPT 1/4
Condensate G1/2
Bypass NPT 1/4
Control air G1/8 G1/4
NPT 1/4
Tab.1: Gas Probe Connections (Varies by Model)
1) Varies by version.
2) Only GAS 222.xx ANSI and GAS 222.xx AMEX
WARNING Gas emanation
Sample gas can be harmful to the health!
Check the lines for leaks.
7Bühler Technologies GmbHBE460062 ◦ 09/2021

GAS 222.35
4.4.1 Blowback Connection
Without accessories installed for the blowback device, the blowback connection comes with a sealed G3/8 screw-in connection. If
you require blowback, you will need to undo this screw-in connection and ensure the blowback line is connected properly and
tight.
DANGER Toxic, corrosive gasses
Explosive or toxic gases can develop due to a leaking or open blowback connection.
4.4.2 Connecting the Gas Line
Please note the following items when connecting the sample gas line (NPT 1/4") on heated probes to prevent thermal bridges:
– Choose the shortest possible screw connection.
– Shorten the connection pipe for the sample gas line as much as possible. To do so, remove the insulation around the sample
gas line. This is done by loosening the fixing bolts.
CAUTION Fragile
The insulation is fragile. Handle with care, do not drop.
After connecting the sample gas line it must be braced and secured with the clamp.
Long sample gas lines may require additional support clamps along the way to the analysis system! Once all lines have been
connected and checked for leaks, carefully reinstall and secure the insulation.
WARNING Gas emanation
Sample gas can be harmful to the health!
Check the lines for leaks.
4.4.3 Connecting the calibrating gas line (optional)
Connecting the calibrating gas line requires a Ø6 mm or Ø1/4” pipe fitting.
If the calibrating gas connection was ordered with check valve, a Ø6 mm or Ø1/4” pipe can be connected directly to the check
valve.
4.5 Connecting the Blowback and Pressure Vessel (Optional)
The air lines must be connected carefully and properly, using suitable fittings.
If the probe is equipped with pressure vessel for efficient blowback (optional), a manual shut-off valve (ball valve) must be in-
stalled in the air supply, immediately upstream from the pressure vessel.
NOTICE
The operating pressure of the compressed air (inert gas) required for blowback must al-
ways be higher than the process pressure.
Required pressure differential min. 3 bar (44 psi).
DANGER Broken pressure vessel
Gas leak, danger due to flying parts.
Maximum operating pressure of the pressure vessel 10 bar (145 psi)!
The operating pressure reduces based on the operating voltage (see solenoid valve type
plate).
8 Bühler Technologies GmbH BE460062 ◦ 09/2021

GAS 222.35
4.6 Electrical connections
WARNING Hazardous electrical voltage
The device must be installed by trained staff only.
CAUTION Wrong mains voltage
Wrong mains voltage may damage the device.
Regard the correct mains voltage as given on the type plate.
Electric strength test
The necessary tests of all assemblies required to be tested were carried out at the factory (test voltage 1 kV or 1.5 kV depending
on component).
To check the electric strength again yourself, only do so on the respective individual components.
– Now perform the electric strength test against earth.
4.6.1 Connection via Terminal Strip
The probe has regulated, adjustable heating. The supply voltage is 115 V AC, 50/60Hz or 230 V AC, 50/60 Hz (see type plate).
The device is already wired to the controller.
Inside the controller housing is a terminal block for connecting the mains supply and the alarm output. The connection to the
included terminal blocks is shown in the attached connection diagram. For this purpose the plugs can be removed from their
sockets and reinserted once wired. The pin assignment is also printed onto the board.
If the heat dissipation is very high near the probe due to the application, the customer must install a shield to protect the probe
and regulator.
4.6.2 Heated Pressure Vessel (Optional)
A heated compressed air tank can optionally be used for blowback. Heated via self-regulating PTC heating cartridge to protect
against frost.
If the heater was ordered with the probe, it is pre-wired.
When retrofitting with a heater, it can be powered by the probe control unit.
Connect the connecting cable for the heater (mains connection 115/230 V AC) per the enclosed wiring diagram.
9Bühler Technologies GmbHBE460062 ◦ 09/2021

GAS 222.35
5 Operation and Control
NOTICE
The device must not be operated beyond its specifications.
5.1 Basic function of the probe controller
5.1.1 Regulator Functions
After switching on the combination the probe is heated up. The display with the current temperature will light up on the con-
troller. As long as the set operating range is has not yet been reached, the display will flash and the status contact is in Alarm po-
sition. Once the working range has been reached, the status contact switches and the display is steady.
The target temperature, the working range of the probe and the temperature unit (°C/°F) are set using the three control buttons
on the controller. This is described in chapter “Operation and use”.
The factory settings are: Unit: °C; target temperature: 180 °C; working range: ±10 °C
5.1.2 Advanced functions for built-in blowback control (optional)
After switching on the probe, blowback will always first be initiated.
Blowback is always indicated by the display alternating between the temperature and "bbon" (blow back on).
5.2 Use of menu functions
Overview of the operational principal:
Use this short description if you have experience with the device.
Operation is carried out by only the keys with the following functions:
Key Function
– Switch from measurement display to main menu
– Selection of the display menu item
– Accepting the changed value or selection
– Switch to the upper menu item
– Increase of the value of switching the selection
– Temporary display of the alternative measurement display (if option is installed)
– Switch to lower menu item
– Decrease of the value of switching the selection
– Temporary display of the alternative measurement display (if option is installed)
10 Bühler Technologies GmbH BE460062 ◦ 09/2021

GAS 222.35
5.2.1 Menu Navigation Overview
Temperature and status display
The probe temperature is indicated in 0.5°C increments. Press the Enter key to access the main menu.
The temperature can be displayed in Celsius or Fahrenheit. During operation the conditions of the
blowback controller (optional) is showed alternating with the probe temperature: Blowback active and manual operation
(refer to the description of the blowback controller or the relevant menu operation).
current temperature
Main menu Submenu Setting range
Prob
Probe controller
____
Global settings
toP
Exit main menu
E
Target temperature
tEMP
Alarm hysteresis
ALAr
Exit submenu
E
___
°C - °F
C
Adjust value
stores the value
wait 5s: do not save
Setting the probe temperature
within the range:
50 °C...200 °C / 122 °F...392 °F
Setting the display unit.
Available in Celsius or
Fahrenheit
Display
Temperature Selection menu
Selection menu
Exit
Selection menu
Exit
Display
Top Settings
Blowback interval
Alarm
Selection menu
Probe temperature
Blowback time
____
Setting range
Setting the alarm hysteresis
within the range: ±5°C...±30°C
Setting the temperature of the
heated extension within the range:
50 °C...200 °C / 122 °F...392 °F
Setting the alarm hysteresis
within the range: ±5°C...±30°C
Switching from automatic
to manual blowback
Setting the blowback
interval time
Setting the blowback time
within the range 5 s to 99 s
* Regulator for
heated
extension
(add-on)
(optional)
Display:
*
*
* Blowback
controller
(optional)
Display:
AdOn
bbc
* These menus
will only appear
if one of the
options is ins
talled.
Selection menu
Selection menu
Selection menu
Selection menu
Alarm hysteresis
Control mode
Temperature tEMP
Target temperature
Alarm ALAr
Exit
Exit submenu
E
Exit submenu
Exit E
____
___
Extension temperature
__:__
__.0
Auto
Auto - Hand
5 min...99h59min
5...59 s
Setting range
ctrl
tInt
t_bb
Control mode
Time of interval
Time of blowback
11Bühler Technologies GmbHBE460062 ◦ 09/2021

GAS 222.35
5.2.2 Detailed description of the operational principle
The detailed description will guide you through the menu step by step.
Connect the unit to the power supply and wait for the startup procedure to complete. At first the software version im-
plemented on the unit will be displayed for a brief period. The unit will then switch directly into measured value dis-
play.
Pressing the button will take you from display mode to the main menu. (The control will continue running whilst in
menu mode.)
Use these buttons to navigate the main menu.
After confirming a main menu item the associated submenu will open
Here you can configure operating parameters:
Cycle through the submenu to configure the parameters,
then confirm the menu item to be changed.
You can now set values within specific limits.
After confirming the value the system will save it. This will automatically return you to the submenu.
If no button is pushed for approx. 5 s, the unit will automatically return to the submenu. Changes to values will not be
saved.
The same applies to the sub- and main menu. The system will automatically return to display mode without saving
the (last) value changed. Parameters which were previously changed and saved will be retained and not reset.
NOTICE!After saving values with the Enter key they will be applied to the control.
ETo exit the main or submenu, select menu item E (Exit).
5.3 Description of menu functions
5.3.1 Main Menu
Regulator (probe)
From here you will be able to access all relevant temperature controller settings. The related sub-
menu allows you to select the target temperature and alarm thresholds.
Regulator for heated extension (add-on; only appears if option is installed)
From here you can access all relevant settings for the temperature regulator of the heated extension.
The related submenu allows you to select the target temperature and alarm thresholds.
Blow back control Only appears if option is installed)
From here you will be able to access all relevant settings for the probe blowback controller. You can
select the control mode, blowback interval and blowback time from the submenu.
Globale settings (ToP Settings)
Selection of the global temperature unit, either degree Celsius (C) or degree Fahrenheit (F).
Note: This menu item has no sub-item. The temperature unit is directly selected.
Exit main menu
Display → E
Selecting this will return you to display mode.
12 Bühler Technologies GmbH BE460062 ◦ 09/2021

GAS 222.35
5.3.2 Probe Controller Submenu [Display: Prob]
Regulator -> Target temperature (Temperature)
This setting is for the device temperature target value. The value can be set within a range from 50
°C (122 °F) to 200 °C (392 °F).
Note: The default value on delivery is 180 °C (356 °F).
Controller -> Alarm range
This item allows setting of the alarm range threshold for the optical alarm as well as for the alarm
relay. The alarm threshold may be set in the range from ±5 °C (±9 °F) to ±30 °C (±54 °F) with respect to
the nominal value.
Note: Default value at delivery is ±10 °C (±18 °F).
Exit submenu 1
Display → Submenu → E
Selecting this will return you to the main menu.
5.3.3 Regulator Submenu for Heated Extension [Display: Adon] (Optional)
Regulator -> Target temperature (Temperature)
This setting is for the device temperature target value. The value can be set within a range from 50
°C (122 °F) to 200 °C (392 °F).
Note: The default value on delivery is 180 °C (356 °F).
Controller -> Alarm range
This item allows setting of the alarm range threshold for the optical alarm as well as for the alarm
relay. The alarm threshold may be set in the range from ±5 °C (±9 °F) to ±30 °C (±54 °F) with respect to
the nominal value.
Note: Default value at delivery is ±10 °C (±18 °F).
Exit submenu 1
Display → Submenu → E
Selecting this will return you to the main menu.
13Bühler Technologies GmbHBE460062 ◦ 09/2021

GAS 222.35
5.3.4 Submenu Blowback control [Display: bbc] (optional)
Blowback control -> Control mode
Under this menu item you can switch between automatic blowback and manual operation.
When selecting Hand, the display will alternate between displaying the temperature and "Hand".
Blowback control -> Blowback interval (Time of interval)
Used to set the total blowback interval time.
The setting range is 5 minutes to 99 hours 59 minutes.
Use the and keys to set each digit and confirm with . The digit being set will flash.
Entry errors can be corrected after pressing the key. Exit the menu and return to it.
Note: 1) The default value on delivery is 10 minutes.
2) After selecting and confirming this value with a blowback cycle will automatically be initiated
and the interval will start.
3) Only applicable in automatic mode.
Blowback control -> Blowback time (Time of blowback)
Sets the time of the actual blowback.
The setting range is 5 to 59 seconds.
Use the and keys to adjust the settings.
Note: The default value on delivery is 10 seconds.
Exit submenu 1
Display → Submenu → E
Selecting this will return you to the main menu.
14 Bühler Technologies GmbH BE460062 ◦ 09/2021

GAS 222.35
6 Service
During maintenance, remember:
– The equipment must be maintained by a professional familiar with the safety requirements and risks.
– Only perform maintenance work described in these operating and installation instructions.
– When performing maintenance of any type, observe the respective safety and operation regulations.
DANGER Electrical voltage
Electrocution hazard.
a) Disconnect the device from power supply.
b) Make sure that the equipment cannot be reconnected to mains unintentionally.
c) The device must be opened by trained staff only.
d) Regard correct mains voltage.
DANGER The gas inside the filter, condensate and used filter elements may be caustic or corros-
ive.
Sample gas can be harmful.
a) Before maintenance turn off the gas supply and surge with air if necessary.
b) Exhaust sample gas to a safe place.
c) Protect yourself against toxic / corrosive gas during maintenance. Wear appropriate
personal protection equipment.
CAUTION Hot surface
Risk of burns
Depending on the operating parameters, the housing temperature may reach over 100
°C during operation.
Allow the unit to cool down before performing maintenance.
CAUTION Excess pressure
The unit mustn’t be pressurised or energised when opened.
If necessary, close the gas supply and ensure a safe pressure on the process end before
opening.
6.1 Maintaining the Filter Element
The probes feature a particle filter which needs to be changed as it becomes dirty.
To do so, disconnect the voltage supply and if applicable close the shut-off valve to the process or switch off the process.
CAUTION!Do not damage the rear filter seat.
NOTICE
The stainless steel filter elements can be cleaned with an ultrasonic bath and reused sev-
eral times; in this case always use new seals on the filter and handle plug.
15Bühler Technologies GmbHBE460062 ◦ 09/2021

GAS 222.35
6.1.1 Replacing the upstream filter
The effectiveness of cleaning a filter within a process is directly influenced by the available airflow (amount of gas). We there-
fore recommend using a pressure vessel directly on the probe.
With sufficient upstream filter blowback (within the process stream) the probes are maintenance-free. However, due to process
conditions the filter may clog over time. In this case the filter element will need to be replaced.
Proceed as follows:
– Slightly push in the handle at the back of the probe and turn 90° (handle must then be horizontal) and remove.
– Screw the dirty filter element out of the handle.
– Check the sealing faces on the handle, replace O-rings, then install the filter element and new seal. (The spare filter includes
O-rings and seals).
– Then insert the handle with the new or cleaned filter, push in slightly and turn 90° (handle must then be vertical). Pull on the
handle to verify the filter element is firmly seated.
NOTICE
The weather hood can only be closed again when the handle is completely vertical. In or-
der to do so, loosen the hood from the locking supports by lifting slightly and then fold
down. Ensure that the hood lock clicks into place correctly.
Condensate inside the pressure vessel
Depending on the installation site and application conditions a small amount of condensate may form inside the blowback air
pressure vessel. Open the drain screw at the bottom of the vessel and drain the condensate at least once a year.
If the probe needs to be serviced more frequently due to operating conditions, we recommend also draining the condensate at
these intervals.
CAUTION High pressure
Pressure vessel under pressure.
Before opening the condensate drain, close the air supply to the blowback control and
drain the vessel by manual blowback.
Pressing the main switch for the blowback control to interrupt the voltage supply.
6.2 Inlet filter blowback (within the process stream)
Be sure to use filtered air with a minimum rating of PNEUROP / ISO Class 4 for blowback:
Class Particles / m3
Particle size:
(1 to 5) µm
Pressure dew point
[°C]
Residual oil content
[mg / m3]
4to 1000
(no particles ≥ 15 µm)
≤ 3 ≤ 5
The following illustrations are intended to explain the context of the terms blowback time and blowback interval:
Blowback time
3 s
3 s
Test time
Blowback interval
Blowback valve
Sample gas valve
OPEN
OPEN
CLOSED
CLOSED
16 Bühler Technologies GmbH BE460062 ◦ 09/2021

GAS 222.35
6.2.1 Manual Blowback (Without Blowback Control)
The shut-off valve in the air supply (inert gas supply) to the pressure vessel must be open. The optional pressure gauge on the
pressure vessel shows the current operating pressure.
–Abruptly open the ball valve in the connecting line from the pressure vessel to the probe until the display on the pressure
gauge has dropped to the lowest reading.
6.2.2 Automatic Blowback (External Blowback Control)
Automatic blowback requires a shut-off valve downstream from the probe. The control unit for the system is designed for se-
quential valve control, i.e.:
1. Closing the shut-off valve downstream from the probe with a controller.
2. Open the solenoid valve between the pressure vessel and probe for approx. 10 seconds.
3. Open the shut-off valve downstream from the probe again.
Blowback can also be set as a closed process at intervals ranging from several minutes to hours or even days based on require-
ments.
6.2.3 Built-In Blowback Control (Optional)
All required parts are already built into the probe based on your purchase order.
Switching on the probe will first automatically trigger blowback. The set blowback interval will then start.
The display will indicate blowback. During the process the display will alternate between displaying the temperature and
"bbon" (blow back on).
Automatic blowback
Please refer to the menu description for how to change the blowback interval or blowback time. The factory settings are: Blow-
back interval: 10 minutes; blowback time 10 seconds.
Manual blowback – access via keys
Open the menu and set the built-in blowback control to manual blowback.
The display will alternate between the probe temperature and the "Hand" status (hand = manual). To start blowback, press one
of the keys or during normal operation (temperature being displayed).
The probe menus must be closed. During blowback the display will alternate between the probe temperature and "bbon".
Manual blowback – external control
Manual blowback may also be externally triggered at any time. This requires connecting a key (not included) per the connection
diagram in the appendix. The key must supply the probe with a 24VDC voltage signal. The external controller does not affect
the parameter settings.
17Bühler Technologies GmbHBE460062 ◦ 09/2021

GAS 222.35
7 Service and repair
This chapter contains information on troubleshooting and correction should an error occur during operation.
Repairs to the unit must be performed by Bühler authorised personnel.
Please contact our Service Department with any questions:
Tel.: +49-(0)2102-498955 or your agent
If the equipment is not functioning properly after correcting any malfunctions and switching on the power, it must be inspected
by the manufacturer. Please send the equipment inside suitable packaging to:
Bühler Technologies GmbH
- Reparatur/Service -
Harkortstraße 29
40880 Ratingen
Germany
Please also attach the completed and signed RMA decontamination statement to the packaging. We will otherwise be unable to
process your repair order.
You will find the form in the appendix of these instructions, or simply request it by e-mail:
7.1 Troubleshooting
CAUTION Risk due to defective device
Personal injury or damage to property
a) Switch off the device and disconnect it from the mains.
b) Repair the fault immediately. The device should not be turned on again before elim-
ination of the failure.
Problem / Malfunction Possible cause Action
No or reduced gas flow – Filter element clogged – Clean or replace filter element, clean
sampling tube
– Blowback (optional) not responding – Check solenoid valve, check pneumatic con-
trol
Temperature alarm – Heat-up not yet completed – Wait for heat-up to complete
– Pt100 failure – Send in probe for repair
– Heater / controller failure – Send in probe for repair
No heat output / no display – No / incorrect voltage – Power supply
– Controller failure – Send in probe for repair
Condensation forming – Heater failure – Send in probe for repair
– Thermal bridges at the sampling point – Insulate to eliminate thermal bridges
Error messages on the display
Error 01 – Probe temperature too high, line Pt100 dis-
connected
– Check Pt100 connection inside the controller
or send probe in for repair
Error 02 – Probe temperature too low, Pt100 short-cir-
cuit
– Send in probe for repair
Error 03 – Heated extension temperature too high,
line Pt100 disconnected
– Check Pt100 connection inside the controller
or send probe in for repair
Error 04 – Heated extension temperature too low,
Pt100 short-circuit
– Send in probe for repair
Tab.2: Troubleshooting
18 Bühler Technologies GmbH BE460062 ◦ 09/2021
Other manuals for GAS 222.35
1
Table of contents
Other Bühler technologies Measuring Instrument manuals
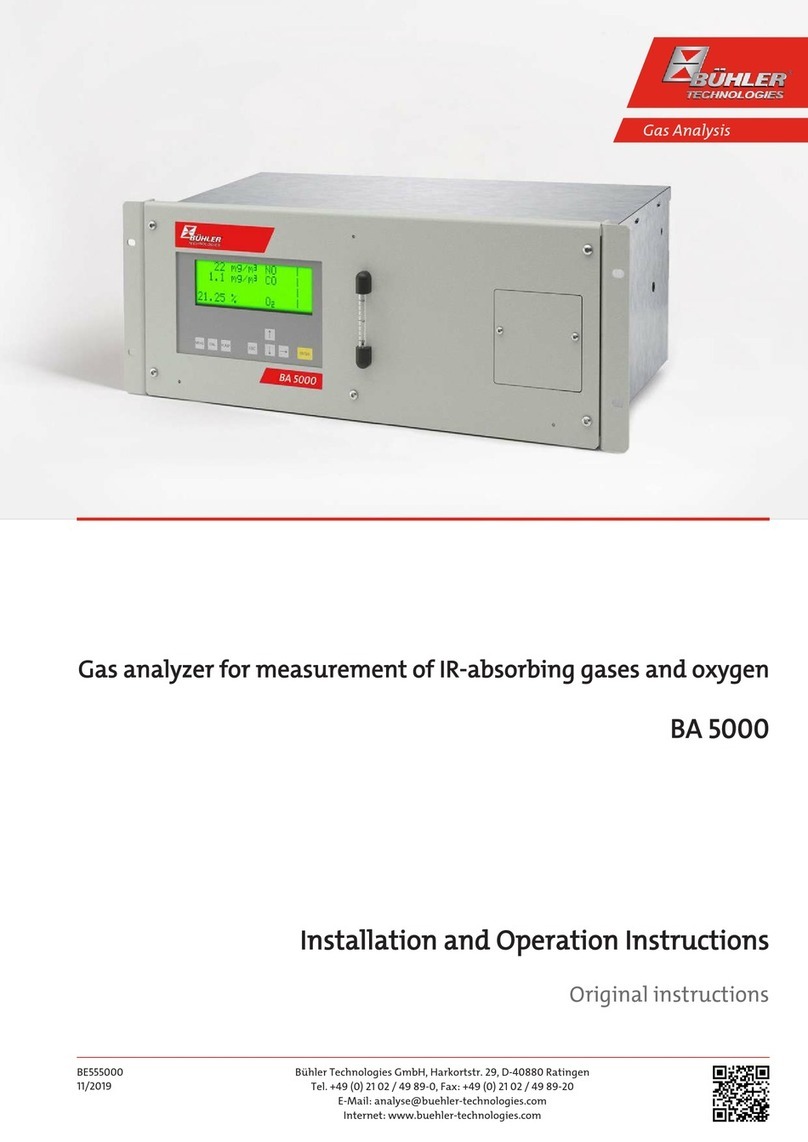
Bühler technologies
Bühler technologies BA 5000 User manual

Bühler technologies
Bühler technologies FCT User manual

Bühler technologies
Bühler technologies GAS 222.21 Owner's manual

Bühler technologies
Bühler technologies SM-6 Series Owner's manual
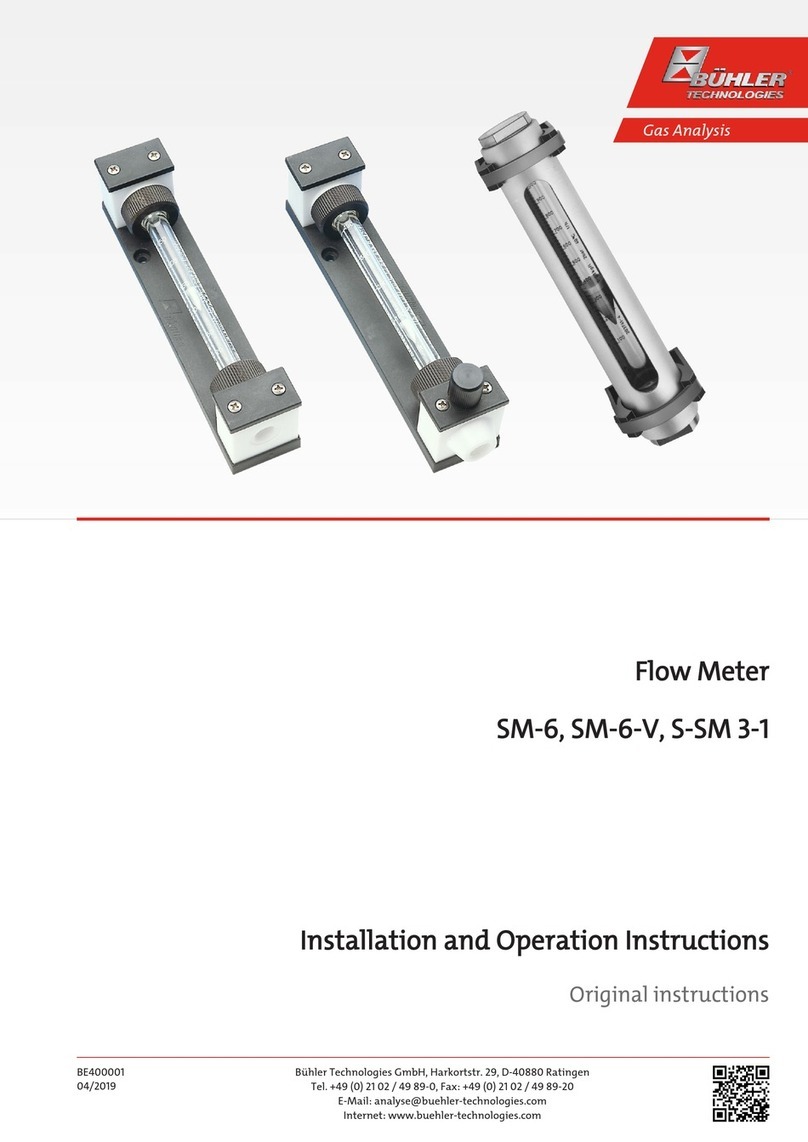
Bühler technologies
Bühler technologies SM-6 Series User manual

Bühler technologies
Bühler technologies GAS 222.15 User manual

Bühler technologies
Bühler technologies GAS 222.35U Installation instructions
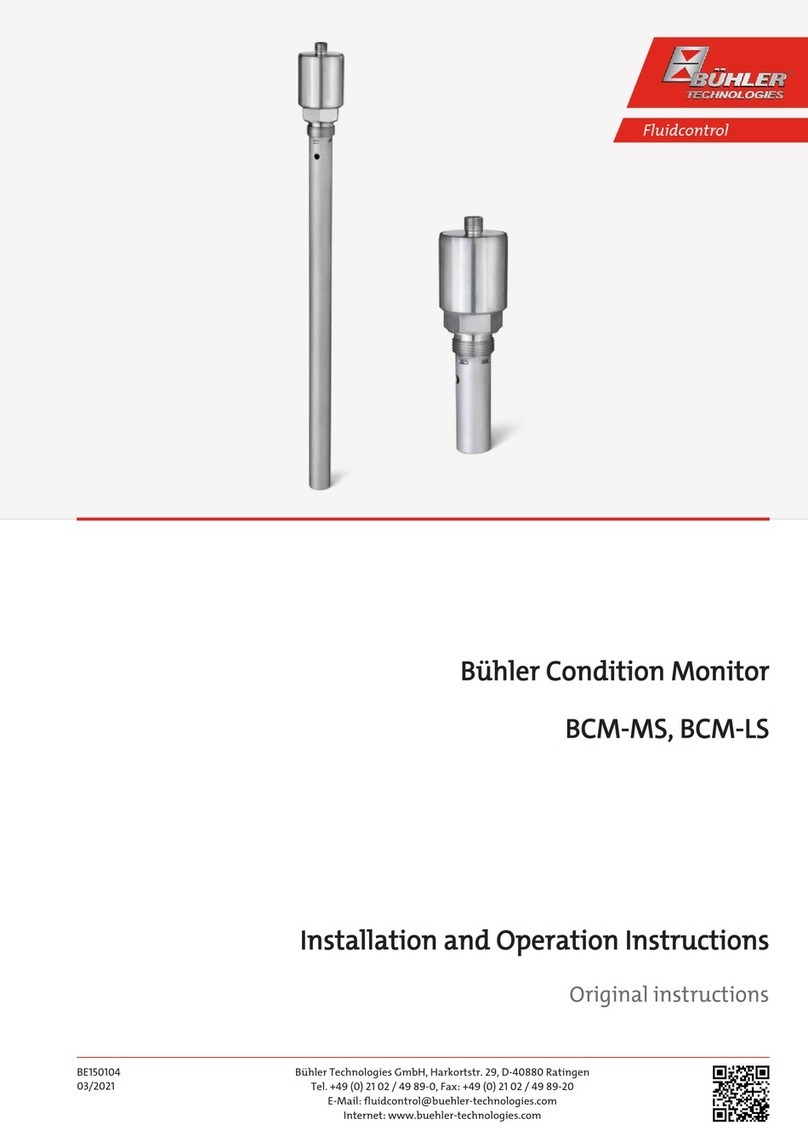
Bühler technologies
Bühler technologies Fluidcontrol BCM-MS User manual

Bühler technologies
Bühler technologies BCI 24-D Series Reference guide

Bühler technologies
Bühler technologies GAS 222.20 User manual