Ballantine 340 User manual

90100141A
Printed in U.S.A.
MODEL
340
RF
MILLIVOLTMETER
BALLANTINE LABORATORIES, INC.
P.O.
BOX 97
BOONTON, NEW JERSEY 07005 USA
201·335·0900/TWX:
71
0·987-8380 JUNE 1972

WARRANTY
All
Ballantine Laboratories, Inc. products are
warranted against defects
in
materials and work-
manship. This warranty applies
for
one year from
the date
of
delivery, except
for
vacuum tubes and
batteries, or,
in
the
case
of
certain major compo-
nents listed in the instruction manual,
for
the
specified period.
We
will
repair
or
replace products
which prove to be defective during the warranty
period. No other warranty is expressed
or
implied.
We
are
not
liable
for
consequential
damages.
CERTIFICATION
The equipment supplied on
your
order meets
all
applicable published Ballantine
specifications
as
determined
by
thorough testing and inspection. Ballantine's calibration
measurements are traceable to the National Bureau
of
Standards.
All
instruments used
in
calibrating Ballantine products are standardized
by
systematic reference to NBS-trace-
able standards
as
described in the validation procedures shown below.
REFERENCE
STANDARDS
DC
10mV-750V
0.01-0.04%
20Hz-50kHz
0.5V-500V
0.03%
20Hz-10M
Hz
0.5V-100V
0.1%
DC-30MHz
0.5V-100V
0.5%
DC-700MHz
10W-0.5V
1%-
NBS
10MHz-1000MHz
1V-300V
1%-
NBS
_t
WORKING
STANDARDS
1kHz
TRANSFER
VM
BALLANTINE.
D1094
HF
TRANSFER
VM
BALLANTINE.
MODEL
393
MICROPOTENTIOMETERS
BALLANTINE
440
RATIO
TRANSFORMERS.
GERTSCH
CALIBRATION
CONSOLE 100Hz-100kHz FOR
0.25%
ACCURACY
INSTRUMENTS
LEVEL
CHECK-DAILY
ATTENUATOR
CHECK-
6
MONTH
~
DISTORTION
CHECK-
1
MONTH
FREQUENCY
RESPONSE
CHECK-
3
MONTH
GROUND
CURRENT
CHECK-
3
MONTH
•
CALIBRATION
CONSOLES 2Hz-20MHz FOR
1%-3%
ACCURACY
INSTRUMENTS
-
LEVEL
CHECK-
1 WEEK
.._
ATTENUATOR
CHECK-
6
MONTH
DISTORTION
CHECK - 3
MONTH
a
FREQUENCY
RESPONSE
CHECK-
3
MONTH
GROUND
CURRENT
CHECK-
3
MONTH
lr
CROSSCHECK CONSOLE 2-20MHz FOR
~
1%-3%
ACCURACY
INSTRUMENTS
LEVEL
CHECK-
1 WEEK
.._
ATTENUATOR
CHECK-
6
MONTH
DISTORTION
CHECK - 3
MONTH
FREQUENCY
RESPONSE
CHECK-
3
MONTH
GROUND
CURRENT
CHECK-
3
MONTH
Ballantine's QualityAssuranceprogram satisfied the requirements
of
MIL-0-9858.

1.
2.
INSTRUCTION BOOK CONTENTS
FOR
MODEL
340
RF
MILLIVOLTMETER
GENERAL
INFORMATION
Page
1
1.1
Features ................
..
.. ..
..
.. ..
..
.. ..
.
.. ..
..
.. ..
.. ..
.. ..
.
..
..
.
..
.
.. .. ..
.
.. ..
.
..
.. ..
..
.... .. .. .. ..
..
....
..
1
1.2
Some Applications of the Model 340 ..
.. ..
.. .. ....
.
..
.
..
..
.
.. .. ..
..
..
.
..
.. ..
..
.. ..
.
.. .. ..
.
.. ..
..
.. ..
. 1
1.3
Technical Characteristics ....................................................................... 1
OPERATION .....................................................................................................
..
1
1
1
2.1
Power Connection ...........
2.1.1 Line Voltage Conversion .........................................................................
2.2
Starting Procedure ...........
..
1
3
2.3
2.4
2.2.1
Warmup
Period
.. ..
Function of Controls
Voltage Measurements ..... ..........................................................................
2.4.1
For True RMS Voltage Measurements Below 30 mV ............................
..
2.4.2 For True RMS Voltage Measurements Above 30 mV ..............................
3
3
3
3
2.5
Possible Error Sources
..
..
....
..
.... .. .. ..
.. ..
.
.. .. ....
..
.
.. .. ....
.
..
....
..
..
.
.. .. ..
..
.. ....
..
.. .. .... ..
..
..
....
4
2.S.1
Indicator Remains in Extreme Left Position
.. .. ....
..
.
..
.. ..
..
.
..
.
..
..
.
.... .. ..
..
...
..
. 4
2.5.2
Indicator Remains in Extreme Right Position.......................................... 4
2.5.3
Indicator Reads High and Pointer Stays on &ale for Next Higher Range 4
2.5.4 Indicator Beats or Flutters
....
.................................................................... 4
2.5.5 Loading Errors ......................................................................................... 4
2.5.6 Voltage Drop in Connecting
Leads
.......................................................... 4
2.5.7 Stray Field Pickup .................................................................................... 5
2.5.8 Transmission Line Effects ........................................................................ 5
2.5.9 Ground Current Errors ............................................................................ 5
2.5.10 Response and Waveform Errors .............................................................. 5
2.6 Use of the DB
Scale
..
..
.. ..
..
.. ..
..
..
... ..
..
.
..
..
..
..
....
..
...
..
..
...
..
....
.. ..
..
..
......
.. .. ..
....
..
....
..
6
2.7 Effect of
DC
Component...................................................................................... 6
2.8 Overload Characteristics ..... 6
2.9 Effect of Power Line Voltage Variations .............................................................. 6
2.10
DC
Output ............................ ................................................................................ 6
3. CIRCUIT
DESCRIPTION
.......
..
............
..
...
..
........
..
.
..
.
..
............
..
..
..
..
.. ..
..
.
.. ..
.
.. .. ..
.
..
.
..
6
3.1
Probe .................................................................................................................... 7
3.1.1
Model 1340 Probe Attenuator ................................................................ 7
3.1.2 Model 2340 Coaxial Adapter .................................................................. 7
3.1.3 Model 4340 Probe
Tip
............................................................................ 7
3.1.4 Model 5340 Tee Adapter ........................................................................ 7
3.1.5 Model 6340 High Voltage Attenuator ...................................................... 7
3.2
Chopper Input
....
.. ..
.
..
..
..
..
..
.
.. ..
..
..
....
.. ..
..
.. .. ..
.. ..
....
.
.. .. ..
..
.. ..
..
..
.
....
..
..
.
.. ..
.
.. .. ..
..
..
.
..
.
..
..
7
3.3
..
Input Amplifier .................................................................................................... 8
3.4 Midsection Attenuator .......................................................................................... 8
3.5
Output Amplifier and Signal Rectifier .............. ................................................. 8
3.6 Power Supply ........................................................................................................ 8
4. MAINTENANCE ...............
..
..
..
....
..
....
..
.........
..
.
..
.
..
.....
..
..
....
..
..
.
..
.. ..
..
.. ..
.
....
..
..
.
..
.
..
..
. 8
4.1 .General ........ ..................... .............. .................................................................... 8
4.2
Recommended Maintenance
....
8
. I .

5.
6.
7.
4.3 Necessary Maintenance Equipment .
4.3.1 Stable Signal Source
4.3.2 Sensitive AC Vacuum Tube Voltmeter
4.3.3 Sensitive
DC
Vacuum Tube Voltmeter .
4.3.4 Tube Checker .
4.4 Removal of the Case .
4.5
2,000 Hour Check .
4.5.1 Scale Adjustment .
4.5.2 Sensitivity Adjustment
4.5.3 Noise Check .
4.5.4 Range Switching Check
4.5.5 DC Output Check
4.5.6 Stability with Line Voltage .
4.6 4,000 Hour Check
4.6.1 Chopper Supply Adjustment
SERVICING
AND
TROUBLESHOOTING
5.1
Necessary Equipment .
5.2
5.3
5.4
5.5
5.6
5.7
5
.1.1
Stable Signal Source
5.1.2
Sensitive AC Vacuum Tube Voltmeter .
5.1.3
Sensitive
DC
Vacuum Tube Voltmeter
5.1.4 Tube Checker .
Simple Service Problems .
5.2.1
Removal of the Instrument Case .
5.2.2 Pilot Light Replacement .
5.2.3
Fuse Replacement
5.2.4 Line Voltage Conversion .
General Instructions
Signal Tracing .
Chopper Replacement
Probe Replacement
Troubleshooting Chart .
SHIPPING INSTRUCTIONS .
REPLACEMENT
PARTS
LIST
Figure 1
Figure 2
Figure 3
Figure 4
Figure 5
Figure 6
ILLUSTRATIONS
AND
DIAGRAMS
Ballantine Model 340 RF Millivoltmeter with Adapters
Rack Panel Mounted Ballantine Model 340-S/2 RF Millivoltmeter
..
Model 340 Location of Controls .
Model 340 Input Impedance
Model 340 Transmission Line Errors
Model 5
340 VSWR .
Figure 7 Model 340 Simplified Schematic . . ...............
Figure 8 Model
340-
Right Hand Side View . ....................
Figure 9 Model
340-
Left Hand Side View, Input Shield Removed .
8
8
8
8
8
8
8
8
9
9
9
9
9
10
10
10
10
10
10
10
10
10
10
10
10
10
10
11
11
11
11
13
16
III
III
2
4
5
5
6
14
15
Figure
10
Model 340
Wiring
Diagram . .. ...................... ..
..
....
..
....
..
... Rear
TABLES
TABLE I
DB
Level Conversion 6
-
II
-
Page

Model
1340
Model
2340
Model
5340
Model
4340
Figure 1.
Ballantine
Model
340
RF
Millivoltmeter
with
Adapters
Figure
2.
Rack
Panel
Mounted
Ballantine
Model
340-S/2
RF
Millivoltmeter
-
III
-

1.
GENERAL
INFORMATION
1.1
Features Frequency Range 0.1 Me to > 1000 Me
The
Ballantine Model 340
RF
Millivoltmeter
is
a sensitive,
wideband, rms-responding voltmeter with a voltage range
from 300
p.
V to 3 V, frequency range of 100 kc to 700 Me,
logarithmic indicator and a basic accuracy of better than
4%.
It
brings to high frequency voltage measurements the same
convenience of logarithmic scales, sensitivity and accuracy
that has always been associated with Ballantine voltmeters.
A feature of the Ballantine Model 340
RF
Millivoltmeter
is
its rms response to distorted sinewave voltages. This is
particularly important at high frequencies because all exist-
ing calibration standards are based on rms-responding de-
vices.
High
frequency waveforms are often highly distorted
and the means for measuring this distortion are limited.
Signal voltages are measured
in
the Model 340 by a probe
which is connected to the voltmeter
by
3 feet of cable. This
allows positioning the probe exactly at the
point
at which
the voltage measurement
is
desired, thus minimizing errors
due to transmission effects.
The basic
input
to the probe is coaxial - a flexible
Ys
inch
diameter bellows is the center conductor and the outer con-
ductor is a Ys-24 external thread. For
input
voltages above
30 mV, a probe attenuator (Model 1340) is first connected
to the probe. This probe attenuator has the same flexible
center conductor and threaded outer conductor
as
the probe
itself. Customer-designed adapters can be used to make con-
nections to either the probe or the probe attenuator and
probe when the very shortest transmission paths are re-
quired. For less demanding applications the Model 340 is
supplied with a complete set of
input
adapters. A coaxial
adapter (Model
2340)
allows the probe to be connected to
female Type N and
BNC
connectors. A spring-loaded probe
tip (Model
4340)
is supplied for in-circuit measurements,
and a Tee-adapter (Model 5340)
is
available to match the
probe to a
50
ohm transmission line.
1.2 Some Applications
of
the
Model
340
RMS voltage measurement
in
grounded circuits
High
frequency transistor measurements
Voltage measurements on coaxial systems
High
frequency bridge measurements
1.3 Technical Characteristics
Voltage
Range 300
p.
V to 3 V
in
8 ranges of
10
db each
Response
Accuracy
Allowable
Max
Crest Factor
Scales
Probe Input
Impedance
Mean
Square
DC
Output
Input Power
Accessories,
Supplied
Accessories,
Optional
Vacuum Tubes
and
Semiconductors
Dimensions
(inches)
Weight
(pounds)
calibrated to 700 Me
True rms, all voltages
Specified in % of reading
at any
point
on the scale
0.1
-100 Me
±4%
100 -700 Me ± 10%
300
p.V
- 1
mV
1
mV
- 3
mV
3
mV
-10
mV
10
mV
-30
mV
30
mV
-100
mV
0.1 v - 0.3 v
0.3 v - 1.0 v
1.0 v - 3.0 v
200 -60
60 -20
20 -6
6 - 2
200 -60
60 -20
20 -6
6 - 2
Two logarithmic voltage scales,
0.95 to
3.3
and 3.0 to 10.6
One linear decibel scale, 0-10
300
p.V
-30
mV
30
mV
- 3 V >25 kQ and 4 pF
>
1MQand4pF
0.1 to 1.0 V repeated for each 10 db
ac
range. 20 kQ source impedance
115/230
V,
50-420
cps, 40 W
Probe Attenuator, Model 1340
Coaxial Adapter,
Model2340
Probe Tip, Model 4340
Tee Adapter, Model 5340
High
Voltage Attenuator, Model 6340
2-12AX7,
2-6AU6A,
1-6X4,
1-0A2,
1-0B2WA,
2-2NS25,
2
-S282G,
4-1N816,
5
-1N1692,
2 Probe diodes (BL Special)
Portable:
13
H,
7Y2
W,
9Y2
D
Rack:
SY2
H,
19
W,
8Y2
D
Portable or Rack, 16
Shipping weight: Portable 22, rack 34
2. OPERATION
2.1 Power Connection
The
voltmeter is supplied ready to operate
on
105
-125
V,
50 cps -420 cps or
210-
250
V,
50 cps -420 cps power line,
as
indicated
on
the decal mounted adjacent to the power cord.
2.1.1 Line
Voltage
Conversion from 115 V to 230 V
or vice versa is possible. For conversion from 115 V
operation to 230 V operation, connect the power trans-
former leads
as
follows:
Disconnect black-red lead from terminal 1 and
black-yellow lead from terminal
3,
and connect
- 1 •
both together to terminal
2.
Replace fuse
Fl
0.4
ampere by 0.2 ampere Slo-Blo fuse. Detailed in-
formation for 115 V
/230
V conversion is given
on the schematic at the end of this instruction book.
2.2
Starting Procedure
Insert the three-prong plug into a proper ac power outlet.
Use conversion unit where only two-prong outlets are avail-
able.
Turn
the function switch from OFF position.
The
pilot
light should glow.
The
instrument
is
ready for use after a
short warmup period.

ADJUSTMENT
PILOT LIGHT
FUSE
Figure
3. Model
340-
Location
of Controls
- 2 -

2.2.1
Warmup
Period
The
instrument
is
usable after approximately 20
sec-
onds. After
15
minutes the indication will be within
1.0% of the final value.
When
the instrument has
no~
been in use for many
months or has been stored in high humidity allow a
warmup period of at least one hour.
NO
SOURCE
OF
HEAT
SHOULD
BE
CLOSE
TO
THE
BACK
OF
THE
INSTRUMENT.
PERMIT
AIR
TO
CIRCU-
LATE
FREELY
AROUND
THE
VOLTMETER
TO
AVOID
EXCESSIVE
TEMPERATURE
RISE
IN
THE
INSTRUMENT.
The voltmeter is calibrated
in
the vertical position. For con-
venience
in
reading, a tilting device is provided beneath
the case.
2.3 Function
of
Controls (see
fig
3.
for control locations)
Function Switch
OFF Turns instrument
off.
STANDBY
Turns instrument on with the exception
of the chopper. Use this switch position
between series of measurements to pro-
long life of chopper.
METER Turns chopper on and allows instrument
to be used
as
a calibrated voltmeter.
NULL Biases meter on-scale with no signal in-
put. Use to set NULL adjustment and for
sensing voltages below the normal mini-
mum
reading
of
300 microvolts.
Range Selector
FULL
SCALE Selects voltage range of instrument
in
10
db steps. Voltages from 300
tL
V to 30 mV
are measured without probe attenuator.
Voltages from 30 mV to 3 V must be
measured with probe attenuator
in
place
as
well
as
with correct position of FULL
SCALE range selector.
Panel Adjustments
NULL
SENS
SCALE
With
shielded, open-circuit
input
on
1m
V
range, and function switch at NULL,
rotate NULL adjustment control for min-
imum i-ndication. This adjustment should
be made after a
15
minute warmup each
time the instrument
is
turned on and be-
fore the start of any critical measurements.
Allows a small adjustment
in
voltmeter
sensitivity to correct for changes due to
component aging.
Adjusts a biasing current to the indicator
so
that full scale on one range will cor-
respond exactly to bottom scale on the
next higher range.
- 3 -
2.4
Voltage Measurements
2.4.1
For
True
RMS
Voltage Measurements
Below
30
mV
Set
Function Switch
Range Selector
To
METER
30
mV
Connect the unknown voltage to the probe input using
the proper adapter
as
required and rotate the range
selector counterclockwise until an indication appears
on
the meter scale. Take the reading from the scale
indicated by the range selector. Because of the loga-
rithmic meter scale and Ballantine special design, the
accuracy of the measurement is the same at any
point
on
the scale.
After a
15
minute warmup, and whenever a series of
critical measurements are to be made
on
either the
1
mV
or 3
mV
range, check the NULL adjustment.
2.4.1.1 NULL Adjustment serves to "zero" or
cancel out small residual voltages in the
input
system of the voltmeter. Since these residuals
tend to be a function of time and temperature,
the adjustment should be made and checked
frequently for greatest accuracy.
To
make the NULL adjustment:
Set
To
Function Switch NULL
Range Selector 1 mV
Shield the probe
input-
for example, by con-
necting the Coaxial Adapter, Model 2340, to the
probe
but
not
screwing
it
all the way
on
to con-
nect the center conductors. Allow a few minutes
for any heat generated in handling the probe to
dissipate. Rotate the NULL adjustment for a
minimum
indication.
The
minimum indication should fall between
1 - 3 db on the meter scale. A higher null
is
an indication
of
excessive noise or thermal po-
tentials and should be investigated. (See para-
graph 4.5.3)
2.4.2
For
True
RMS
Voltage Measurements
Above
30
mV
Set
Function Switch
Range Selector
Attach
Probe Attenuator, Model 1340
To
METER
3 v
To
Probe
Connect the unknown voltage to the probe attenuator
input
using the proper adapter
as
required and rotate
the range selector counterclockwise until an indication
appears
on
the meter scale. Take the reading from the
scale indicated by the range selector.
After a
15
minute warmup and whenever a series of
critical measurements are to be made
on
either the
0.1 V or 0.3 V range, check the NULL adjustment (see
paragraph 2.4.1.1)

2.5
Possible Error Sources
The causes of some measuring difficulties are listed below:
2.5.1 Indicator Remains in Extreme Left Position
This condition may be caused by:
a)
Power cord disconnected
b)
Fuse open
c)
Function switch in OFF or
STANDBY
position
d)
Input
voltage lower than range selected
e)
Failure to remove Probe Attenuator for
measurements below 30 mV
2.5.2
Indicator Remains in Extreme Right Position
This condition may be caused by:
a)
Input
voltage higher than range selected
b)
Failure to attach Probe Attenuator for
measurements above 30 mV
c)
Excessive external fields
d)
Excessive ground currents
2.5.3
Indicator Reads
High
and
Pointer Stays on
Scale
for
Next
Higher
Range
This condition may be caused by:
a)
Function switch in NULL position
b)
Excessive external fields
c)
Excessive ground currents
2.5.4
Indicator Beats or Flutters
This condition may be caused by:
a)
Large spurious
input
voltage at or near 94 cps
b)
Strong magnetic fields such
as
exist adjacent to
certain power transformers and line voltage
regulators
c)
Noisy or unstable
input
signal
Because of the wide frequency range and high sensltlvtty
of
the Model 340, other measuring errors may be introduced
when proper measuring techniques are not used.
The
most
common error sources are listed below. A comprehensive
analysis of errors is given in NBS Conference
on
Standards
and Electronic Measurements paper "Techniques and Errors
in
High
Frequency Voltage Calibration," by Dr.
E.
Uiga
and
W.
F.
White. A copy of this paper is available without
charge from Ballantine Laboratories.
2.5.5
Loading Errors can occur whenever a source of
emf with other than zero source impedance is measured
by a voltmeter with other than infinite
input
imped-
ance. Current drawn
by
the voltmeter produces a volt-
age drop
in
the source impedance and the resulting
measured terminal voltage differs from the emf by the
amount
of
this voltage drop.
The
Model 340 is a high
input
impedance device. For
input
voltages below 30 m
V,
the low frequency input
impedance can be represented
as
more than 25,000
- 4 -
ohms in parallel with 4 pF. Above 30 mV the shunt
resistance can be considered infinite while the capaci-
tance remains approximately at 4 pF. However, at high
frequencies this situation changes. Both the resistive
and capacitive components
of
input
impedance are
frequency sensitive -shunt resistance decreases with
frequency, shunt capacitance increases. This
is
shown
in figure
4.
50k
30
20
IOk
7
3
2
I k
0.7
0.5
0.3
0.2
0.1
' '
--
I I
',
~T
RESISTANCE
'
'
IOpF
7
......_
h \
INPUT CAPACITANCE \
5------
--""'r-------'r'"-
------ --- -
_,
3 \
2 I I
"'
'
-INPUT
< 30mV '\. I
---INPUT
>
30mV
'
0.1
0.5 5 I0
50
100
200
400
700
FREQUENCY IN
Me
Fig.
4.
Model
340
Input
Impedance
For any critical voltage measurement
it
is
necessary to
check for loading errors by determining the actual
source impedance
of
the emf at the frequency of inter-
est and, with the aid
of
figure
4,
the
input
impedance
of the Model 340. The relationship between source
emf, Es, terminal voltage,
Vr,
source impedance, Zs,
and voltmeter impedance,
Zr,
is given by:
Zs
Es
=
Vr
(1
+
Zr
)
2.5.6
Voltage
Drop
in Connecting Leads can cause
appreciable errors at high frequencies when the induc-
tive reactance of these leads becomes large and the
input
impedance of the voltmeter has decreased from
its low frequency value.
The
situation is similar to the
loading error effects discussed in 2.5.5.
In
this case
the impedance of the connecting leads
is
analogous to
the source impedance.
Coaxial connections
i:o
the Model 340 should be made
whenever possible to reduce the error due to voltage
drop in connecting leads. The Model 2340 Coaxial
Adapter, supplied with the Model 340, converts the
probe
input
to accept female type N or
BNC
connect-
ors.
It
can be used,
as
can all the adapters, both with
and without the probe attenuator for measurements
over the entire voltage range.
The
Model 4340 Probe
Tip
with its associated ground
lead should not be used at higher frequencies if errors
due to the voltage drop
in
connecting leads
is
suspected.
The
inductance
of
the ground lead
is
approximately
0.1
1-'H
which at 100 Me represents a reactance of
63 ohms.

2.5.7
Stray Field Pickup
is
particularly troublesome
at high frequencies. Any loop in the signal input cir-
cuit can have a voltage induced in it that
is
proportional
to the area of the loop, the stray field density, and
the frequency.
Again, coaxial connections are the best when stray field
pickup
is
suspected. Location and removal of the of-
fending sources should be tried, and every attempt
made to reduce the loop area at the signal input.
2.5.8
Transmission Line
Effects
have to be consid-
ered whenever the distance between the voltage to be
measured and the Model 340 probe input
is
not negli-
gibly short compared to a wavelength. The Model 340
is
a high impedance device and will therefore introduce
reflections on any transmission line. These reflections
produce a voltage standing wave pattern. The magni-
tude of the voltage standing wave radio determines the
maximum difference that can exist between the source
of voltage to be measured and that indicated by the
Model 340. The actual difference will depend
on
the
distance between the source and the Model 340.
Figure 5 shows the error that will exist when the
Model 340
is
connected to the voltage source by a
short section of 50 ohm coaxial transmission line. This
set of curves
is
derived from transmission line equations
and the input capacitance of the Model 340 (see figure
4).
%ERROR
§::§.
XIOO
Es
30
LENGTH
(L)
IOcm
5 3 3
_I
I I
I~'""""
i/
:I
, I
OF
PROBE
OR
PROBE
-[-"LENGTH
(L)
ATTENUATOR
I I!/
INPUT I
~c/
I '
E
MODEL
340
ij
I
Ill\
PROBE!
I '
If
I
I
1----
ER
BELOW
30mV
·'l
,),
!j
·--ER
ABOVE
30mV 1
I
20
1
I
I
I
I
I
em
If
I I
10
f
~J
/V
,)
//
,
~
~
v v
,~~~
...
~
...
::,
b.:=
-~
...
.,.:::.;
0
20
30
50
70
100
200
300
500
700
FREQUENCY
IN
Me
ER
_ I
L•=1.2XI0-sf(cpslL(cm)
~
-COSL0-
aS1Nl
0 a
::;;;;
wC~o
Fig. 5. Model
340
Transmission
Line
Errors
Transmission line effects can be minimized
by
shorten-
ing the length of connection between source and Model
340. This may require the construction of specially
threaded adapters that will connect to the ground of
the Model 340 probe.
Transmission line effects may also be minimized
by
measuring
in
a matched 50 ohm transmission system.
For this application the Model 340 probe is first con-
nected to the Model 5340 Tee Adapter which
is
then
connected to the
50
ohm transmission line where the
measurement
is
desired. The maximum vswr of this
. 5 •
system
as
a function of frequency is shown in figure
6.
This tabulation shows the maximum errors that can
exist due to reflections caused by the Model 340, assum-
ing the transmission line itself
is
perfectly matched.
1.30
1.20
0::
3=
en
>
1.10
1.00
/
L
/ v
f.--
~
v
,/
--
-v
100
200
300
FREQUENCY
IN
Me
Fig. 6. Model
5340
VSWR
INPUT
>30mV
I
I
I
v
I INPUT
<37
/ v
500
700
2.5.9
Ground Current
Errors
can be particularly
troublesome whenever low-level, high frequency volt-
ages are measured. Special circuit precautions have
been made
in
the Model 340 to reduce the effects of
ground currents -either currents of power line fre-
qunecy or high frequencies. However, particularly with
high frequency ground currents, it
is
impossible to
completely eliminate these effects. Therefore every ef-
fort should be made to reduce the leakage from signal
sources into the power line ground. Avoid positioning
power line cords close to the Model 340 or to any low-
level sources that are being measured.
Work
at the
highest possible measurement levels.
2.5.10. Response and Waveform Errors are mini-
mized
in
the Model 340 because the instrument re-
sponds to the rms value of the input signal. This feature
is
particularly important
in
the calibration of the Model
340. All high frequency calibration devices (Micro-
potentiometers, A-T Voltmeters,
HF
Transfer Volt-
meters) are rms-responding.
When
they are used to
calibrate a Model 340, errors due to distortion in the
signal sources will be minimized.
The rms feature of the Model 340
is
likewise important
when measuring unknown voltages. Distortion
in
the
voltage will not lead to the uncertain reading of a peak-
responding or average-responding instrument. How-
ever, particularly at high frequencies, response and
waveform errors must still be considered when using
the Model 340.
If
the signal being measured
is
con-
nected to the Model 340 over a finite length
of
trans-
mission line -which in practice
is
always the
case-
and if the signal contains higher frequency harmonics,
these harmonics will be transmitted over a longer elec-
trical length than the fundamental. This longer length
will alter the amplitude of the harmonics at the input
of
the Model 340, in relationship to the amplitude of

the fundamental, and therefore alter the rms voltage
as
measured by the Model 340.
In
addition, above 700 Me
the Model 340 itself no longer exhibits a flat response
but
instead goes into a series resonant peak. Harmonics
above 700 Me will therefore be further emphasized and
the reading of the Model 340 will further depart from
a true rms indication of the signal voltage.
2.8
Overload
Characteristics
The
maximum
ac
voltage that should be applied directly to
the probe
is
10 volts.
The
maximum
ac
voltage that should
be applied to the probe attenuator
is
300 volts.
Higher
volt-
ages may damage one or both of the probe diodes.
TABLE
I
DB
LEVEL
CONVERSION
Reference Level Subtract from
DB
Readings on
FS
Ranges
~--~~---·
f-
lmV
3mV
IV,
I
mW
in 1000 Q
(dbv)
70db
60db
f-----·-
--
-----~----
---
·-
0.775
V,
I
mW
in 600 0
(dbm)
67.8 57.8
0.224 V, I
mW
in 50 Q 57.0 47.0
2.6
Use
of
the
DB
Scale
The
db
scale
of
the Model 340 is linear and reads from
0 to 10, corresponding to bottom scale and full scale voltage
readings.
To
convert db readings to various reference levels,
use Table
I.
To
simplify the conversion and to compute
db
levels of other
references, a handy db slide rule
is
available from Ballantine
Laboratories on request, free of charge.
2.7
Effect
of
DC
Component
The
input
signal to the probe
is
coupled to the two detector
diodes by 1000
pF
capacitors. Any de component of the
input
signal will be blocked by these capacitors and therefore
will not be measured.
The
probe and probe attenuator have
been tested to withstand 300 V
de.
Applying higher de
voltages may damage one or both of the probe diodes.
10mV
30mV
0.1
v 0.3 v
1.0
v
3.0V
50 db
40db
30db
20db
10db
Odb
--
f--
--
f-----
1-----
47.8 37.8 27.8 17.8 7.8
-2.2
---
37.0 27.0 17.0 7.0
-3.0
-13.0
2.9
Effect
of
Power Line Voltage Variations
Operation is possible with line voltages of 105 to 125 volts.
Variation of the line voltage within this range will not affect
the sensitivity of the instrument by more than
1%.
Some
readjustment of the
NULL
may be necessary if measure-
ments are being made on either the 1 mV or
0.1
V ranges.
Transient variations in the line voltage may introduce addi-
tional noise
on
these two ranges
as
well.
2.10
DC
Output
A de
output
is
available at the rear of the instrument case
through a
BNC
connector.
The
de
output
varies from 0.1
to 1.0 volts for each 10
db
ac
voltage range and
is
propor-
tional to the mean square of the ac input.
The
source im-
pedance is 20 kilohms.
3.
CIRCUIT DESCRIPTION
The
basic circuitry of this instrument is shown in figure
7,
Simplified Schematic, while a complete schematic and re- placement parts list are located at the end of this manual.
PROBE
CRI
CIA
R4
RFINPUT
R5
CIB
INPUT
AMP.
V
I,V2
-czlJCIO
CHOPPER
Gl
Rl4
MID.
SECTION OUTPUT
AMP,
ATTEN.
V3
,V4
R56flSCALE
R61
R58
-=
I'
METER
L---------------,
+
C3
R6
NULL
fRI04l
+
SYM.
ADJ.
RBI
Fig.
7.
Model
340
Simplified Schematic
- 6 -
R59
ft
DC
-=LIN.
Ql
+
DC
OUT.
R62
R60
DC
OUTPUT

3.1 Probe
The probe of the Model 340 is designed to convert
ac
volt-
ages, 300
fL
V to 3
V,
to equivalent de voltages on an rms
basis over a frequency range from 100
kc
to 700
Me.
The
probe consists, electrically, of a single input-dual
output
ceramic
input
capacitor, C1, of
1000-
1000 pF. The
input
ac
signal voltage is coupled through this capacitor to the
two germanium diode detectors, CR1 and CR2, which are
connected, in opposite polarity, to ground through R4 and
RS. These resistors serve to improve the high frequency
response
by
introducing a correction to the series resonance
of the diodes.
B~th
diodes are always operated with less than 30 mV ap-
phed
ac voltage. They are therefore always operated in that
region where their characteristics can be described
as
square-
law.
The
diodes are specially selected for resistance, thermal
chara~teristics,
and frequency response.
The
de outputs from
the dwdes, one negative and one positive, are connected over
decoupling filters R1-C2 and R2-C3 to a special low-noise
cable and then to the Model 340 chassis input. After being
converted to a 94 cps signal by means of a chopper, ampli-
fied,_
and detected, an equivalent de signal
is
averaged and
has lts square-root taken in the indicating meter to produce
a reading proportional to the rms of the ac input voltage
to the probe.
R6
is
use? to inject a current into
RS
controlled by the
NUL~
adjustment. The resulting voltage drop, adjusted
in
magmtude and polarity, serves to balance out any residual
de output from the probe with no
ac
signal input. R3 is
connecte~
to
RS
to maintain electrical symmetry at high
frequenoes.
The
pro?e
is
~oused
in
a double-walled tube to provide
thermal msulanon to the diode circuits. The inner wall car-
ries the signal ground.
It
is
connected at one end to the
diode grounds and the ground braids of the probe cable,
and at the other end
is
terminated
in
a Ys-24 thread to
match the probe adapters.
3.1.
~
Model
1340
Probe Attenuator is designed to
prov1de a stable 40 db attenuation over a frequency
range of 100 kc to 700 Me when connected ahead of
a Model 340 probe. This attenuation is used to reduce
ac
input
signals from
30m
V to 3 V to the range 300
p.
V
to_
30 mV where they can be measured by the probe
w1th
an rms response. Failure to use such an attenuator
ahead
of
the probe would drive the probe diodes out
of their square-law region and the resulting response
would no longer be rms.
The
attenuation
is
provided by a specially constructed,
factory-adjusted capacitor
Cl
and a fixed, mica disc
capacitor, C2. Physically the Model 1340 Probe At-
tenuator screws directly
on
to the Ys-24 thread of the
probe. Its
input
is
constructed exactly
as
the probe
input
-flexible bellows center conductor and Ys-24
ground shell. All adapters for the probe connect
as
well to the probe attenuator.
3.1.2 Model
2340
Coaxial Adapter is used to con-
vert the probe or probe attenuator
input
to a coaxial
connector mating with Type N or Type
BNC
female
connectors.
It
adds approximately
0.3
inch of trans-
mission line between the probe input and the front face
of a mating Type N connector and about 1 pF of added
input capacitance.
- 7 -
3. 1.3 Model
4340
Probe Tip
is
designed for in-circuit
measurement below approximately 100
Me.
It
consists
of a stainless-steel tip, covered with a spring-loaded
nylon insulator, that can be made either to press against
the point of measurement or be hooked on to a circuit
":ire.
An
a_ttached
ground cable with alligator clip pro-
vldes the s1gnal ground.connection. The inductance of
this ground lead, together with the added length of
transmission path of the probe tip, limits the use of
this adapter to relatively low frequencies.
3.1.4
Model
5340
Tee
Adapter
is
designed to allow
the use
of
the Model 340 for voltage measurements on
matched 50
ohm
transmission lines.
It
consists of a
milled aluminum block with a Type N male
input
con-
nector and Type N female output connector that can
be inserted in the transmission line under measurement.
The
Model 340 probe, with or without probe attenu-
~tor,
depending
on
the voltage being measured, screws
lnto the threaded portion of the aluminum block and
makes connection with the center conductor of the
block.
On
the opposite side of the block is an insulated
knob that
is
adj1.1sted
to one of two positions -for
input
signals above or below 30 mV. This knob con-
trols_
a pair of vanes that compensate for the change in
loadmg of the Tee Adapter when either the Model 340
with or without its probe attenuator is used.
Figure 6 shows the maximum uncertainty in measured
voltage that is introduced by the vswr of the Model
5340 Tee Adapter.
3.1.5
Model
6340
High Voltage Attenuator adapts
the Model 340 to voltage measurements from 3
to
300 V over the frequency range of 0.1 to 100
Me.
It
is connected to the Model 1340 Probe Attenuator
":hich in turr:
!s
connected to the probe itself, and
pro~
v1des
an addmonal 40 db of voltage attenuation.
The
added error is
1%
from
0.1
to 10 Me and
2%
from
10 to 100 Me.
3.2 Chopper Input
To convert the de output of the probe to ac, this instrument
uses a mechanical modulator or chopper, which
is
regarded
as
the best choice for this purpose, particularly because of
the low level involved.
Of
the various conversion means
available the mechanical modulator displays:
a.
The
highest conversion efficiency
b.
The lowest residual noise level
c.
The
lowest residual de
d.
The
lowest de drift
To
avoid dependence
on
power supply frequency and to re-
duce the effects of power supply hum, the chopper operates
at a frequency of 94 cps.
The
signal frequency after con-
version
i~
therefore
?~
cps.
The
chopper is driven by a
94 cps, blStable mulnv1brator using two rugged transistors
which convert
12
volts de
to
square wave
ac.
Since the tran-
sistors operate only
as
switches, they dissipate very little
power, leading to low internal temperatures and long life.
RS? permits a small adjustment of operation frequency,
whlle R81 provides for an adjustment of symmetry.
It
should
be noted that
if
the drive supply (7
pin
connector on top
of
unit)
is
removed with the power on, and then recon-
nected, the transistors will be saturated and the unit will not
restart until the .power
is
interrupted and reapplied. There
will be no damage done.

The input chopper
is
of
the single pole, double throw type
using gold alloy, twin contacts, designed especially for low
level operation. The de signals are coupled to the chopper
by
low-pass filters formed
by
C5, R10-C8 and C6,
Rll-C9.
ClO, C11, R12, and R14 couple the resulting ac output from
the chopper, at the correct impedance level, to the input
amplifier.
3.3
Input
Amplifier
The ac signal·(94 cps) from the chopper
is
sent to an input
amplifier having a gain of approximately 1,000. The ampli-
fier uses a dual triode, V1, and a pentode, V2, with overall
feedback stabilization
of
26 db or greater.
To
reduce noise
the bandwidth
is
severely restricted by making the plate load
of the last stage a parallel resonant circuit tuned to the signal
frequency.
To
further reduce noise the input triodes are
operated semi-starved, and metal film and deposited carbon
type resistors are used at all critical points. The heaters
of
the
input
triode are operated on de (rectified and filtered ac)
while the plate and screen supply for all these tubes are
stabilized by a gaseous regulator tube.
3.4
Midsection Attenuator
Signals from an
input
amplifier are sent to the output ampli-
fier via the midsection attenuator. This attenuator,
in
addi-
tion to providing range switching, permits the input signal-
to-noise ratio to increase whenever it introduces attenuation.
The attenuator
is
a simple resistive-divider type and employs
deposited carbon resistors.
3.5
Output
Amplifier
and
Signal Recrifier
Signals from the midsection attenuator are further amplified
in
the output amplifier, which
in
configuration
is
very similar
to the
input
amplifier. A dual triode, V3, and a pentode, V4,
are operated with overall feedback stabilization
of
26 db.
Again in the interest
of
low noise the triodes are operated
semi-starved, while the plate and screen potentials are de-
rived from a gaseous regulator tube.
In
contrast to the
input
amplifier, where all three tubes are
operated to provide voltage gain, the output tube of this
amplifier serves to convert voltage to current. This output
current drives two rectifiers, CR5 and CR6. CR5 delivers
a half-wave rectified current to the indicating meter
Ml.
CR6
delivers a similar current, of opposite polarity, to load
resistors R62 and R60 and the resulting voltage drop,
fil-
tered, is available
as
a de output proportional to the mean
square
of
the ac
input
to the probe. The currents through
both rectifiers are combined and go either to signal ground
directly or through compensating resistors R75, R76, R77
and R78 to ground. Compensation
is
necessary on the 1 mV
and
0.1
V ranges for the residual noise of the probe and
amplifier, and on the 30 mV and 3 V ranges for a slight non-
linearity
in
probe diode square-law characteristic.
3.6
Power Supply
All necessary operating potentials are derived from a line
operated power supply.
High
potentials for plates and
screens are obtained from rectified
ac,
rc filtered, and gaseous-
tube stabilized. All tube heaters except
Vl
are operated
on
ac balanced with respect to ground. The heater
of
V1
is
operated on rectified ac with rc filtering. R92, a potenti-
ometer across this de supply,
is
adjusted to provide mini-
mum hum
in
the input stages.
4. MAINTENANCE
4.1 General
The Model 340
is
designed for extended trouble-free service.
High
grade components operated below rating and low
operating temperature result
in
more than 3,000 hours of
expected operating periods without the need for amplifier
tube changes or circuit adjustments.
The purpose of periodic maintenance procedures
is
to assure
the specified accuracy, check the condition
of
the voltmeter
and detect and replace deteriorated tubes or components
before they have an appreciable effect on instrument per-
formance. The procedure
is
designed
not
only to measure
and correct voltmeter performance
at
the time
of
test, but
to
foresee the possible troubles and guarantee the instrument
accuracy through the next maintenance period.
4.2
Recommended Maintenance consists of two types of
periodic checks.
4.2.1 2,000 hour checks.
4.2.2
4,000 hour checks.
4.3
Necessary Maintenance Equipment
4,3.1 Stable Signal Source, adjustable from 10 mV
to 1 V, capable
of
being set to ±
~
%, frequency in
range 100
kc-
1 Me.
- 8 -
4.3.2
Sensitive AC Vacuum Tube Voltmeter, such
as
Ballantine Model 300H.
4.3.3
Sensitive
DC
Vacuum Tube Voltmeter, such
as
Ballantine Model 365.
4.3.4
Tube Checker
4.4
Removal
of
the Case
Place the voltmeter face down on a table. Remove the power
cord and the two
#10
binder head screws at the rear of the
case. Lift
up
the
case.
To
replace the case, proceed
in
re-
verse order.
WARNING:
When the instrument
is
operated
without
the case the
danger
of
electric shock exists. Take ex-
treme care
not
to come
in
contact with high voltage points.
The highest voltage
on
the chassis
is
400 V
de.
4.5
2,000
Hour Check consists of
the
following:
4.5.1 Scale Adjustment checks the scale linearity of
the logarithmic indicator.
It
is
equivalent to the zero
adjustment of a linear meter. For such adjustment
Set
Function Switch
. Range Selector
To
METER
10 mV

Apply a stable source of 100
kc-
1 Me to the probe
input. Adjust the amplitude to produce a meter reading
of exactly
10
on the
upper
voltage scale. Reduce the
source by exactly
10
db.
The
meter should now indicate
exactly 1
on
the lower voltage scale.
If
it does not,
rotate the SCALE
ADJ
control, R61, located at the
right
side of the front panel. Repeat this procedure
until readings
of
exactly 10 and 1 are obtained.
4.5.2 Sensitivity Adjustment corrects for any change
in overall gain due
to
aging of amplifier components,
tubes, probe diodes, or probe attenuator. For sensitivity
adjustment:
Set
Function Switch
Range Selector
To
NULL
1
mV
Adjust NULL adjustment according to paragraph
2.4.1.1. Then:
Set
Function Switch
Range Selector
To
METER
10
mV
Apply
10
mV, ±Y-4%, from a stable source of 100
kc-
1 Me to the probe input.
The
meter should read exactly
10 mV.
If
not, adjust SENS control located at the right
side of the front panel. Then:
Set
Function Switch
Range Selector
To
METER
1 v
Attach the Probe Attenuator, Model 1340, to the probe.
Apply 1
V,
±
Y-4%,
from a stable source of 100 kc -
1 Me to the probe attenuator.
The
meter should read
exactly 1
V.
Ordinarily no adjustment
to
the probe
attenuator should be necessary.
If
the error
on
the 1 V
range
is
less than 1
Yz%,
the SENS control should be
readjusted to split this error with and without probe
attenuator.
If
the error on the 1 V range
is
greater than
1Yz%, C1 should be adjusted for a 1 V reading by
rotating the
input
insulator of the probe
attenuator-
whose threads have been sealed with
Loctite-
with a
wrench designed to fit the two .062 inch holes spaced
.280 apart. After adjustment, the insulator should be
resealed with Loctite.
4.5.3 Noise Check is necessary to insure that the
original low noise level of the instrument
is
not
in-
creased by aging of components or environmental con-
ditions.
At
Ballantine Laboratories the noise
is
mea-
sured
as
follows:
With
probe open-circuited and
shielded,
Set
Function Switch
Range Selector
To
NULL
1
mV
- 9 -
Adjust NULL control for minimum indication. Record
the
db
scale meter reading. Then:
Set
Function Switch
Range Selector
To
NULL
30 mV
Record db scale meter reading.
The
difference in the
two meter readings should
not
exceed 1 db.
If
the
difference
i~
meter readings does exceed this figure,
all
components in the probe and
input
circuitry
up
to
and
including
V1
may be suspected.
The
noise level
is
of greatest importance when making
measurements on either the 1 mV or
0.1
V range.
On
other ranges the noise level can be appreciably higher
and
not
affect the accuracy of measurement.
4.5.4
Range Switching Check determines the accu-
racy
of
the midsection attenuator that is connected be-
tween V2 and V3.
To
check this attenuator, make the
NULL adjustment per paragraph 2.4.1.1 and then:
Set
Function Switch
Range Selector
To
METER
30
mV
Apply a stable source to the probe
input
of approxi·
mately
15
m
V.
Adjust the amplitude of the source until
the meter reads exactly
1.5
on
the
lower voltage scale.
Then
reduce the source by precise steps of
10
db, turn-
ing the range selector progressively to 10, 3 and 1 m
V.
The
meter should continue to indicate
1.5
±0.02
on
the lower voltage scale.
4.5.5
DC
Output Check determines the accuracy of
the de output.
Set
Function Switch
Range Selector
To
METER
10
mV
Apply a stable source from 100
kc-
1 Me to the probe
input
and adjust until the meter reads exactly 10 mV.
Now
connect an accurate de indicator to the de
output
BNC
connector at the rear of the instrument. This de
indicator should have high enough resistance
not
to
load the 20
kQ
de source resistance.
The
de indication
should be 1.0 V ±
1%.
If
it is not, adjust R60, the
DC
Output
Adjustment (see figure
8).
Now
reduce the amplitude of the
ac
source by exactly
10 db to 3.17 m
V.
The
de indication should be
0.1
V
± 1%.
If
it
is
not, adjust R63, the
DC
Linearity
Adjustment (see figure
8)
.
4.5.6 Stability with
Line
Voltage checks the overall
condition of the instrument.
Set
Function Switch
Range Selector
To
METER
10
mV

Apply a stable source of 100 kc - 1 Me to the probe
input. Adjust the amplitude of the source to obtain a
meter reading of exactly 10 m
V.
Check the line voltage
to make sure it
is
115-117
volts.
Now
adjust the line
voltage to 105 volts, and then to 125 volts.
The
meter
indication should not change by more than
1%.
If
it
does, the chopper supply voltage or frequency may be
in error, or the amplifier tubes may have aged beyond
acceptable limits (see 4.6.1 and 5.3).
4.6
4,000
Hour Check consists of all the tests listed under
the 2,000 hour check.
In
addition, all tubes should bechecked
and the chopper supply adjusted.
4.6.1 Chopper Supply Adjustment checks the fre-
quency and symmetry of the chopper supply.
Set
To
Function Switch METER
Range Selector
10
mV
Apply a stable
10
mV signal, 100 kc - 1 Me, to the
probe input. Adjust R82, Frequency Adjustment, for
a maximum meter indication (see figure
8)
.
Connect a wideband
ac
voltmeter across terminals 36
and 38 on the chopper driver board. Adjust R81,
Symmetry Adjustment, for a maximum voltmeter read-
.ing. Readjust R82, if necessary, for a maximum Model
340 meter indication (see figure
9)
.
5. SERVICING AND
TROUBLESHOOTING
In
case
of voltmeter malfunction, servicing by the user
is
feasible provided skilled personnel and recommended
equipment are available, and ·the procedure outlined in this
and Section 4 are followed.
It
should be mentioned that the
procedures
in
this manual are of a simplified nature. Refined
and comprehensive service and calibration require special-
ized equipment not normally available to the average user.
Therefore
if
trouble develops which cannot be corrected by
the procedures outlined here, or when a most accurate cali-
bration is desired, it is recommended that the instrument be
returned to Ballantine Laboratories, Inc.
The
instrument
should
in
all cases be preceded by a letter stating the nature
of the trouble or the desired service. (
See
Section 6 for
shipping instructions.)
5.1 Necessary Equipment
5.1.1 Stable Signal Source, adjustable from 10 mV
to 1 V, capable of being set to
±~%.frequency
in
range 100
kc-
1 Me.
5.1.2 Sensitive AC Vacuum Tube Voltmeter, such
as
Ballantine Model 300H.
5.1.3
Sensitive
DC
Vacuum Tube Voltmeter, such
as
Ballantine Model 365.
5.
1.4
Tube Checker
5.2
Simple Service Problems
5.2.1 Removal
of
the Instrument Case is required
for all servicing.
Place the voltmeter face down
on
a table. Remove the
power cord and the two #10 binder head screws at
the rear of the
case.
Lift
up
the
case.
To
replace, pro-
ceed
in
the reverse order.
WARNING:
When instrument
is
operated without
the case, the
danger
of
electric shock exists. Take
extreme care not to come in contact with the high
voltage points.
The
highest voltage on the chassis
is
400 V
de.
5.2.2
Pilot Light Replacement
The pilot lamp, Type 1815,
is
accessible
by
unscrewing
the red plastic cap located on the front panel.
5.2.3
Fuse
Replacement
The use is of the Slo-Blo type and is rated at 0.4 A for
115 V operation and 0.2 A for 230 V operation. The
fuse holder
is
of the extractor post type and
is
located
on the front panel.
5.2.4
Line
Voltage
Conversion
It
is
possible to operate the Model 340 for either a
115 V or 230 V line supply. The line voltage for which
the instrument is connected
on
leaving the factory
is
indicated on a decal located adjacent to the line cord.
At the rear of the instrument on the power cord re-
ceptacle bracket are three terminals marked
1,
2,
and
3.
The power transformer connections are
as
follows:
Terminal Power Transformer Leads
115 v
230
v
1 Black, Black-Red Black
2
No
Connection Black-Yellow,
Black-Red
3 Black-Yellow, Black-Green Black-Green
5.3
General Instructions
When
there is malfunction that is not simply corrected
by
any of the normal calibration adjustments (see Section
4)
the following procedure is recommended:
-10 -
5.3.1 Check all tubes
on
a reliable tube tester; replace
any tubes which exhibitlow gm, shorts, grid current, etc.
5.3.2
If
tube replacement does not restore normal
operation, check all de and
ac
operating potentials and
compare with those listed
on
schematic (Fig. 10)
located at the rear of the manual.
An
abnormal voltage
may give a clue to the nature of the
def~;ct.

5.3.3
If
neither
5.3.1
nor
5.3.2
indicates the nature of
the difficulty, make a thorough physical examination
for broken or discolored components, broken leads,
defective connections, etc.
5.4 Signal Tracing
If
the simple checks outlined in section
5.3
fail to reveal the
cause of malfunction, signal tracing should be tried
Set
To
Function Switch METER
Range Selector 10 mV
Apply a stable source of 10 m
V,
100
kc-
1 Me, to the input
of the probe.
With
a sensitive, accurate, high impedance
ac
voltmeter, check the
ac
signal voltages and compare with
those shown on the schematic (Figure 10) located at the
end of this manual. Any radical difference from those indi-
cated may provide a clue to the difficulty.
5.5 Chopper Replacement
If
it has been determined that the chopper needs replace-
ment, the procedure
is
as
follows (see figures 8 and
9)
:
5.5.1 Remove the instrument
case.
5.5.2 Remove the three screws that hold the shield
covering the input circuitry.
5.5.3 Disconnect the three bare copper leads running
from the base
of
the chopper.
Note
the connection for
each lead before removing.
5.5.4 Remove the 7 pin top connector from the top
of the chopper.
5.5.5 Remove the 2 screws which secure the chopper
base to the chassis.
5.5.6
The chopper may now be removed from the
instrument.
5.7
Troubleshooting Chart
5.5.7
Install the new chopper, observing the reverse
of the procedure above. Use the special
16w
thermal
emf solder provided.
5.6
Probe Replacement
The two signal diodes in the probe may be damaged by
applying excessive
ac
or de voltages to the probe. Should
the diodes be damaged the sensitivity of the instrument will
be greatly
in
error and cannot be corrected by the panel
SENS control.
It
is
recommended that if the probe diodes, or any other
probe components, are damaged, the entire instrument be
returned to Ballantine Laboratories for repair and recalibra-
tion. Special equipment and experienced personnel are avail-
able for this work.
Probe repairs by the user are most easily accomplished by
replacing the entire probe. The following procedure should
be followed:
5.6.1 Obtain a replacement probe assembly from
Ballantine Laboratories. Specify the serial number of
the instrument.
5.6.2 Remove the instrument case (see 5.2.1).
5.6.3 There are four probe connections just behind
the front panel, three connected to the feed-thru
capacitors and one to a ground lug. Carefully unsolder
these four connections, then unclamp the two coaxial
cables. The probe cable can now be pulled through
the opening in the front panel.
5.6.4 Insert the new probe cable through the panel,
reclamp the coaxial cables, and solder the four connec-
tions
as
before. Use the special low emf solder pro-
vided. Use
as
little solder
as
possible.
5.6.5 Check the sensitivity of the instrument, and ad-
just if necessary, following the procedure of paragraph
4.5.2.
To
assist in troubleshooting, this chart lists symproms, possible causes, and where possible, perti-
nent sections of this manual.
Symptoms Possible Cause Pertinent
and/or
Remedy Sections
Instrument inoperative
No
power, fuse blown
5.2.3
Pilot light does not light Defective power supply
3.6
Instrument indication with Function switch
in
NULL position
2.5.3
no
input
NULL control improperly adjusted
2.3
Noisy input tube
V1
4.5.3
Defective chopper
5.5
Instrument apparently operating Function switch in STANDBY
2.5.1
but no indication Defective chopper
5.5
-
11
-

Symptoms Possible Cause Pertinent
and/
or Remedy Sections
Instrument
is
out
of
calibration: Function switch in NULL 2.5.3
a.
on all ranges at low R61 SCALE adj
off
4.5.1
frequencies R56 SENS adj off 4.5.2
Defective tube or component
Defective probe 2.7, 2.8, 5.6
b.
on all ranges above 30 mV Model 1340 attenuator
off
4.5.2
at low frequencies
c.
on 1
mV
and
0.1
V ranges R104 NULL
ad
j off 2.4.1.1
R57, R71, R72, R75, R76
3.5
d.
on 30 mV and 3 V ranges R73, R74, R77, R78
3.5
R31-
R34 3.4
e.
on 3 mV and
0.3
V ranges
R31-R34
3.4
f.
on 10 mV and 1 V ranges
R31-
R34 3.4
g.
on all ranges at high Defective probe 3.1, 5.6
frequencies
h.
on all ranges above 30 mV Defective Model 1340 Probe Attenuator 3.1.1
at high frequencies
Excessive drift on most Instrument
in
warm or drafty location
sensitive range Defective
input
component
Excessive change
in
indication Weak or defective tubes
with line voltage change Chopper supply improperly adjusted 4.6.2
Chopper drive voltage low
Indication normal, de output C30, C31 defective or shorted
3.5
low or absent Defective resistor R59, R60, R62, R63
3.5
Defective diode CR6
Chopper supply frequency Defective resistor
R81-
R85 3.2
incorrect, not possible to Defective capacitor, C35, C36
3.2
correct with R82 Defective chopper
Cl
5.5
Defective transistor Q1, Q2 3.2
-
12
-

6. SHIPPING
INSTRUCTIONS
If
it should be necessary to return the instrument to Ballan-
tine Laboratories, Inc. make certain that at least four inches
of padding material surrounds the instrument to prevent
damage during shipment. Ship via Railway Express or
motor truck to
BALLANTINE LABORATORIES, INC.
90 Fanny Road
Boonton,
New
Jersey
-
13-

V7
OB2WA
V6
OA2
V5
6X4
Fig. 8. Model
340-
Right Hand Side View
.
14
-

LINE
VOLTAGE
CONVERSION
Figure 9. Model
340-
Left
Hand
Side View
Input
Shield
Removed
-
15
-
-----Ql
-----Q2
R81
SYM.
ADJ.
Table of contents
Other Ballantine Measuring Instrument manuals
Popular Measuring Instrument manuals by other brands
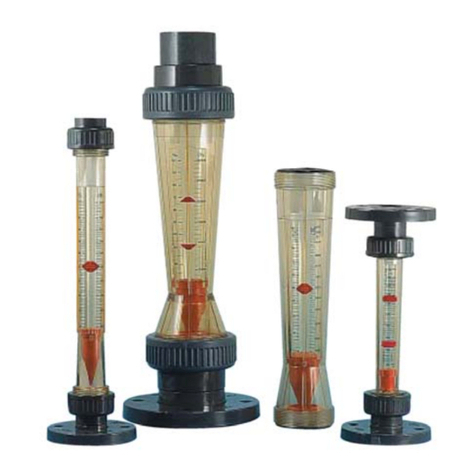
Kobold
Kobold KSM-**001 operating instructions

Burkert
Burkert FLOWave S 8098 operating instructions

Kobold
Kobold SWK operating instructions
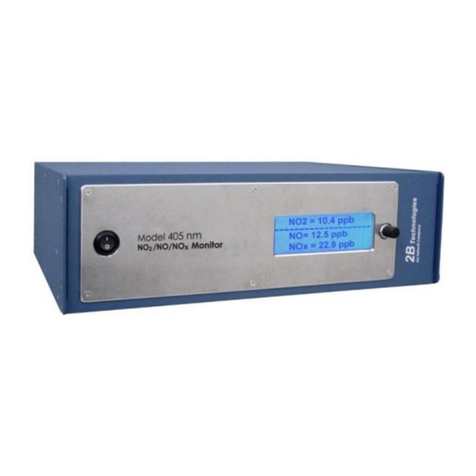
2B Technologies
2B Technologies 405 nm Operation manual
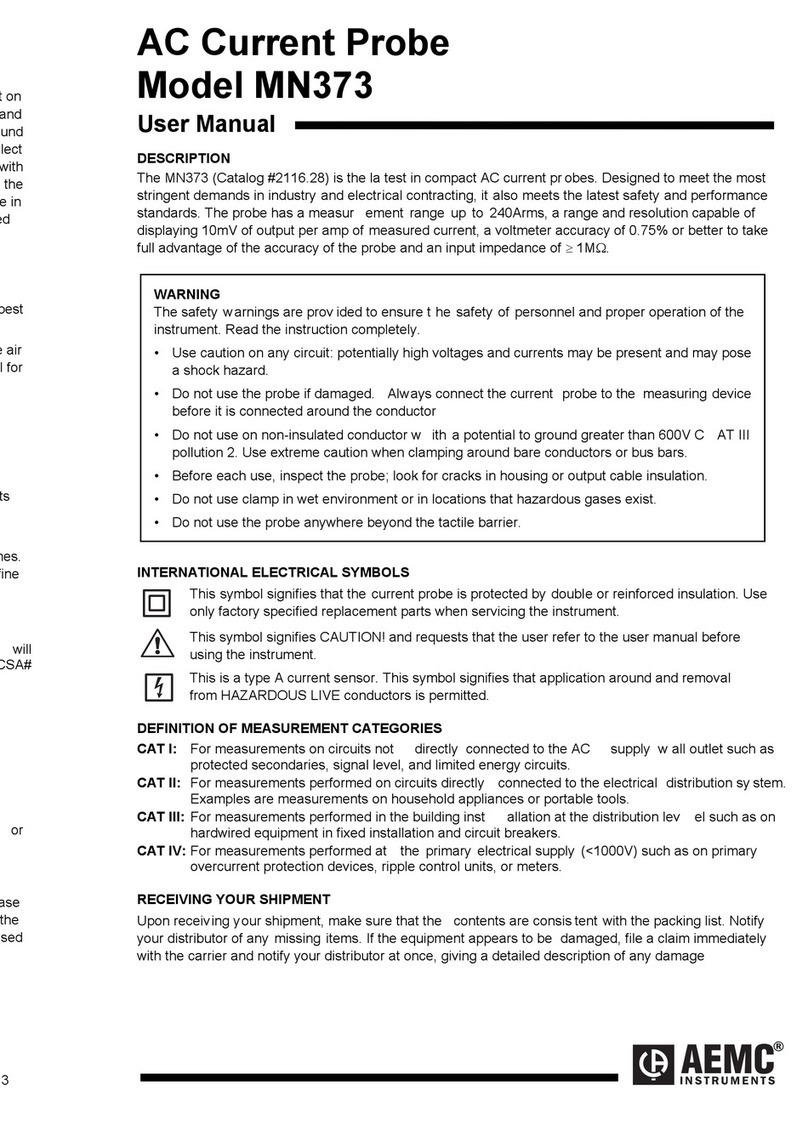
AEMC
AEMC MN373 user manual

PCB Piezotronics
PCB Piezotronics IMI SENSORS 646B01 Installation and operating manual