Basecam Electronics GPS IMU V.1.0 Service manual

Basecam GPS IMU V.1.0
GNSS-aided AHRS/IMU module
Features
•Integrated GNSS-antenna for a compact size
•Full set of navigation sensors 3-axis
gyroscope, 3-axis accelerometer, 3-axis
magnetometer, barometer (altimeter), GNSS
receiver (concurrent Galileo, GLONASS,
GPS / QZSS)
•Powerful MCU running UKF for a sensor
fusion at high rates
•Thermal stabilization helps to keep high
precision with the change of environmental
temperatures
•Interfaces UART, USB, CAN*, I2C*
•Onboard SD card for a high-rate data
logging with the actual date-time
information and flexible set of data to log
•Backup battery for a GNSS "warm start"
mode and real-time clock
•Open serial API protocol allows using this
sensor in various applications
•Compatible with all versions of the
SimpleBGC32 controllers**
•Functionality will be constantly improved
by the firmware updates
•Cost-effective solution compared to other
GNSS-enabled solutions on the market
* CAN and I2C interfaces will be implemented in future
releases of the firmware
** For full support of all functions of the Basecam GPS IM , it's
required to update the main controller's firmware to the
version 2.68b7 and above.
Overview
The Basecam GPS IMU is an GNSS-aided
compact AHRS/IMU module developed by
Basecamelectronics company to work as an
external IMU sensor* with all versions of
SimpleBGC32 controllers. It has much better
precision compared to the internal IMU sensor,
that allows improving precision of stabilization
in demanding applications, where the regular
IMU sensor does not work reliably.
GPS IMU connects to any free UART port of the
main controller and provides precise attitude
and heading information, that can be used as a
reference to correct the internal IMU sensor,
solving its common problems gyroscope drift,
an affection of linear accelerations, drift caused
by the changes in environmental temperature.
*Note that currently GPS IM module does not replace the
regular IM sensor, though this functionality may be
implemented in future.
Document revision 1.0.58 (20. May. 2019)
Hardware version 1.1
Firmware version 1.0
© Basecamelectronics® 2019 www.basecamelectronics.com

Basecam GPS IMU V.1.0
GNSS-aided AHRS/IMU module
Specifications
Mechanical
Size of the enclosure 71×57×20 mm
Weight 45 g
Mounting holes 3 mm × 4
Electrical Min Typ Max
Power supply 4.5 V 5 V 5.5 V
Drawn current (at 5V) 150 mA 400 mA
(warming
up)
Thermal stabilization 250 mWt 1500 mWt
Backup battery (CR1216)
- current drawn
in backup mode
- lifetime (estimated)
3V
16 µA
75 days
Communications
Interfaces 1× UART
1× USB
1× CAN*
1× I2C*
1× microSD
Max. baud rates UART 2 MHz, I2C 800 kHz, CAN 2
MHz
Protocols See "Basecam GPS_IMU Serial API
1.0.pdf" for a protocol specification
Data output · Raw sensors data (accelerometer,
magnetometer, barometer, gyroscope,
GNSS)
· Attitude (quaternion, DCM, Euler)
· Angular rate
· Navigation position and velocity
Max. data output rate 200 Hz (faster rates available by
request)
bsolute maximum ratings
Working temperature -40..+85 °C
Acceleration 1000G for 1 ms
ESD rating HBM Class 2, 2000 V
CDM Class 3, 250 V
Performance
Startup time 1 seconds (communication ready)
3 seconds (first valid data ready)
GNSS best lock time** Cold
Hot
26 s
1 s
GNSS receiver sensitivity Tracking & Navigation
Reacquisition
Cold start
Hot start
–165 dBm
–158 dBm
–146 dBm
–155 dBm
GNSS systems Galileo, GLONASS, GPS, QZSS
concurrently
GNSS receiver update rate 10 Hz
Internal update rates Gyroscope data
Accelerometer
Magnetometer
Attitude and heading
Position & velocity
2000 Hz
2000 Hz
50 Hz
200 Hz
200 Hz
Angular velocity limits ±2000 deg./sec.
Acceleration limits 16G
Magnetic field strength
limits
16 Gauss
Factory calibrations Gyroscope bias, accelerometer bias
and scale, magnetometer bias and
scale (at the single working
temperature point)
Thermal stabilization Setpoint (adjustable)
Time to warm up (typ.)
- from 0°C to 50°C
- from 20°C to 50°C
50 °C
40 sec.
25 sec.
* CAN and I2C interfaces will be implemented in future releases of the firmware
** WARNING: this version of GPS IM has small integrated GNSS antenna, so good conditions for reception of GNSS signal is strictly
required! If used indoor or in dense urban terrain, the startup time may be much longer the best specified values, or even no fix.
© Basecamelectronics® 2019 www.basecamelectronics.com

Basecam GPS IMU V.1.0
GNSS-aided AHRS/IMU module
Installation
When choosing a position for the GPS IMU module, take into account the following conditions that are
mandatory for a normal work of all sensors
Magnetometer as a magnetic field of the earth is very weak, even relatively small external magnetic
fields can distort the measurements. Try to keep magnetometer as far as possible from a soft iron
(ferromagnetic metal parts, screws) and a hard iron (permanent magnets). If it's hard to avoid those
factors, it's recommended to calibrate magnetometer after installing in a new position. Such calibration is
able to compensate affection of the hard iron and soft iron. It's extremely important to keep a
magnetometer far away from variable magnetic fields that can't be calibrated electric motors, power
supply cables, ferromagnetic parts that can change their position.
GNSS receiver keep a clear view of the sky from the top surface of the enclosure for the best GNSS-
signal reception; do not place metallic material that can obscure signal, too close to it; keep electronics
that emits EMI noise or strong signals that can interfere GPS signal, as far as possible.
Gyroscope and accelerometer try to minimize the level of vibrations, as they seriously impact these
sensors.
Barometer keep free access of outside air but prevent strong airflows that may create variations of
pressure inside the box where sensor is located.
Installing on a gimbal
SimpleBGC32 system supports several mounting positions for the GPS IMU on the stabilized platform,
on the gimbal's arms, or on the outer frame. All possible orientations are supported, with the condition
that axes of the device are aligned to axes of the IMU sensor in a normal position.
Choose a position considering requirements for a normal work of all sensors. Take into account that the
rotating joints between the external IMU and the stabilized platform may add additional errors caused by
the combination of errors in angles measured by the encoders, and flexibility of joints, arms or a
suspension of a gimbal.
Connecting to a gimbal and setting up
Please refer to "SimpleBGC32 User Manual 2.6x", section 18 "Using an external IMU sensor to improve the
precision of stabilization".
SimpleBGC32 GUI version 2.68b7+ provides a dedicated tool to show diagnostics information for the
connected GPS IMU module. Also, from this tool it's possible to make sensor's calibrations and to upgrade
firmware.
Sensor calibrations
The basic version of GPS IMU module comes with the simple factory calibrations. You can re-calibrate
© Basecamelectronics® 2019 www.basecamelectronics.com

Basecam GPS IMU V.1.0
GNSS-aided AHRS/IMU module
selected sensors at any time if for some reasons factory calibration becomes obsolete.
IMPORTANT: wait at least 1 minute after powering ON the device, to let it warm up to wor ing temperature! Otherwise,
calibrations will be not precise.
Calibrating magnetometer (biases and scales)
It is advised to re-calibrate magnetometer after the installation in a new mounting position or after
serious changes in the magnetic environment. Calibration removes the interference of the hard and soft
iron located near the device.
1. Press the service button 3 times quickly to start calibration.
2. Rotate device by all directions to collect data in multiple different orientations. This step is
divided into 2 phases
a) At the first 7-8 seconds system collects a time-separated data points. During this time, it's
important to make several long rotations by at least two axes. Green LED flashes with a
constant rate.
b) Then the system collects the remaining number of data points separated by the angle from
each other. The short pulse of green LED signals an acceptance of each new point. Rotate
device to different angles until the required number of points are collected.
3. When enough points are collected, the system computes calibrations values and emits a series of
short pulses by the green LED, which means that the calibration was finished successfully.
Calibrating gyroscope (biases only)
1. Make a single short press on the service button
2. Fix the device firmly, preventing any motion, rotation or vibration. Green LED flashes 2 times per
second while the device collects data. It takes several seconds.
3. When finished, system emits a series of short pulses by the green LED.
Calibrating accelerometer (biases and scales)
This procedure needs to place the device in 6 positions in a sequence, making each axis to point exactly
up and exactly down. The order of the sequence of positions does not matter.
1. Place the device in the first position in order (for example, Z-axis pointing down) and fix it. A
tolerance of 2-3 degrees is allowed.
2. Press the service button 2 times quickly to start calibration in this position.
3. During the calibration, the green LED flashes 2 times per second. When finished, it makes 2 short
flashes and device returns to normal operation.
4. Move the device to the next position in order and repeat steps 1-3.
© Basecamelectronics® 2019 www.basecamelectronics.com

Basecam GPS IMU V.1.0
GNSS-aided AHRS/IMU module
When all 6 positions are passed, system computes calibration values and emits a series of short pulses by
the green LED.
LED status indication
The multicolor LED signals the basic modes of operation by color
Green — GNSS receiver is used in a solution. This is the main working mode when there is a
good reception of the GNSS signal.
Yellow — GNSS receiver is not used; device provides attitude and heading information without
the compensation of accelerations; position and velocity information is undefined.
Red — hardware fault, device is not operational
When a connection to the external host is established and device sends data, LED flashes 2 times per
second.
Service button
•1 click – calibrate gyroscope
•2 clicks – calibrate accelerometer (single position)
•3 clicks – calibrate magnetometer
•long press – if connected by USB, enter mass-storage device mode. Device appears as a USB disc
allowing to work with the content of the installed SD card. Functions that require access to the SD
card (like calibrations, data logging) will be unavailable in this mode.
General configuration parameters
General configuration parameters are located in the "CONFIG.INI" which you can find in the root directory
of the SD card.
Name Default value Range Units Description
IMU_HEAT_TEMP 50 -40 – +80 °C Thermostat temperature for IMU
IMU_HEAT_PWR 500 0 – 1500 mW Maximum heater power for thermostat that
will be consumed from power supply
UART1_BR 115200 9600 – 921600 Bd Baud rate for UART1
UART1_AHRS_RATE* 0 0 – 200 Hz Frequency of sending data for AHRS_RATE.
Disabled when set to 0.
UART1_HELPER_RATE* 0 0 – 200 Hz Frequency of sending data for HELPER_RATE.
Disabled when set to 0.
UART2_BR 115200 9600 – 921600 Bd Baud rate for UART2
UTC_TIME_ZONE 0 0 – 24 Hour UTC time zone
DYNAMIC_MODEL 4 0 – 8 Dynamic platform model
© Basecamelectronics® 2019 www.basecamelectronics.com

Basecam GPS IMU V.1.0
GNSS-aided AHRS/IMU module
0 portable
2 stationary
3 pedestrian
4 automotive
5 sea
6 airborne with <1g acceleration
7 airborne with <2g acceleration
8 airborne with <4g acceleration
Remarks
* If parameter is enabled, module sends CMD_AHRS_HELPER or CMD_HELPER_DATA messages to the SimpleBGC32
gimbal controller. Use it for compatibility with the old versions of firmware prior to 2.68x that does not support
GPS_IMU module natively GPS_IMU should be mounted on the gimbal's frame and initiate sending data for correction
of the gimbal's internal IMU sensor.
Data logging
GPS IMU is able to save realtime data to log files in the on-board SD card in a format SCSV (semicolon-
separated values). Up to 2 independent channels can be configured (for example, to log some data at
high rates, other data at low rates).
Log configuration parameters are located in the "CONF_LOG.INI" which you can find in the root directory
of the SD card, and have the following format
LOG<ch>_<name>=<value>,
where
<ch> – channel (1 or 2)
<name> – name of the parameter or name of the data set
<value>– value of the parameter
To select which data to log, set "1" or "2" to the corresponding data sets, for example
LOG1_GYR_XYZ=0 - disabled
LOG1_GNSS_POS_LLA=1 - enabled, log instant values
LOG1_ACCEL_XYZ=2 - enabled, average values of the variable between log events
The full list of available datasets can be found in the document "Basecam GPS IMU Serial API" .
Additional parameters
•LOG<ch>_INTERVAL_MS – interval between the data samples, from 5 to 60000 ms.
•LOG<ch>_SYNC_PERIOD_MS – how often new portions of data will be synchronized with the file
allocation table (FAT)
NOTE: do not set SYNC_PERIOD_MS too low, because SD card has a limited lifetime resource for the write cycles.
•LOG<ch>_FILES_TO_ROTATE - number of files to keep in rotation scheme, 1..98. When the new log
file is created, the oldest file is deleted.
User-defined data logging
Host controller can send user-defined external data that will be logged together with the internal IMU
© Basecamelectronics® 2019 www.basecamelectronics.com

Basecam GPS IMU V.1.0
GNSS-aided AHRS/IMU module
data. To send data, use CMD_USER_DATA_LOG message. To define which data is enabled for logging in
configuration, use CMD_GET_USER_CONF_LOG message. The following parameters defines how to log
external data
•LOG_USER_CH<pipe_idx>_NAME=<name_of_pipe>
◦<pipe_idx> starts from 0
◦<name_of_pipe> - name to be logged in the header of log file. If pipe contains more than one
value, index will be appended
•LOG<ch>_USER_CH<pipe_idx>_CONF=<data_type>;<data_size>;<is_enabled> - data format for each
pipe
◦<ch> - main loggin channel, 1 or 2
◦<data_type> 1 - float, 2 - int32, 3 - int16
◦<data_size> number of values in a pipe, 1..15
◦<is_enabled> 1 if pipe should be logged, 0 to skip it
Example
LOG_USER_CH0_NAME=USER_TIMESTAMP
LOG _USER_CH0_CONF=3; ;
LOG_USER_CH _NAME=IMU_ANGLE
LOG _USER_CH _CONF= ;3;
LOG_USER_CH2_NAME=BATTERY_VOLTAGE
LOG_USER _CH2_CONF=3; ;
Log file rotation
Log file has format LOG<ch>_<NN>.CSV, where
<ch> - channel
<NN> - sequence number in a rotation queue
Each time device is restarted, NN is selected from the unused numbers (01..99). If the number of files
exceeds the maximum allowed (10 by default), file that goes next to the selected NN, is deleted.
Firmware update instructions
W RNING always load a proper firmware that matches the hardware version of the device! The latest
firmware can be downloaded from the www.basecamelectronics.com/Basecam_GPS_IMU/
Updating firmware from SD card
This option works even if the device is unresponsive (i,e, previous attempt of updating firmware was
failed and device is not accessible by any interface).
The sequence of actions to update the firmware from SD card
© Basecamelectronics® 2019 www.basecamelectronics.com

Basecam GPS IMU V.1.0
GNSS-aided AHRS/IMU module
1. Power off the device.
2. Copy the firmware file named "FWUPDATE.BIN" to the root directory of the SD card and install
card into the device.
3. Turn on the device power or connect by USB cable to PC
4. Wait for the firmware update process to finish.
LED indication during the firmware update
• Flashing green firmware updated is in progress
• Solid green firmware is successfully updated
• Solid red critical error, firmware can not be updated
Updating firmware from the SimpleBGC32 GUI
This option works if the GPS IMU module is connected to the main gimbal controller by the UART
interface and is fully functional.
1. Connect the main SimpleBGC32 controller to PC (over USB, bluetooth or any other ways).
2. Run SimpleBGC32 GUI and connect it to the main controller.
3. Open "External IMU" tab and configure Basecam GPS IMU as described in the SimpleBGC32 User
Manual (skip this step if it is already configured and works properly)
4. Press the "Show status" button to display information from the device in a new window
5. Press "Firmware update.." button, select *.hex file and press "Open". Firmware update process
starts.
Important note: do not interrupt the updating process - it will make device inaccessible by the U RT
anymore! You still can use other methods to update the firmware.
Updating firmware in USB DFU mode
This method works for experienced users only and requires additional steps to enter device into a
bootloader mode. Please contact our support for more information.
© Basecamelectronics® 2019 www.basecamelectronics.com

Basecam GPS IMU V.1.0
GNSS-aided AHRS/IMU module
Dimensions and pinout
© Basecamelectronics® 2019 www.basecamelectronics.com
47
47
3
71
19,6
11
12 10,9
56
40
R4,5
R4,5
Сoor din at e r oot
an d dir ect ion of axes
4,5
56
4,5
DIMENTI NS IN MILLIMETERS

Basecam GPS IMU V.1.0
GNSS-aided AHRS/IMU module
© Basecamelectronics® 2019 www.basecamelectronics.com
TX
+5V
RX
GND
+5V
GND
CAN_ L
CAN_ H
GND
SCL
SDA
+5V
Ser vice but ton Micr oUSB
I2С CAN UART
Table of contents
Popular Control Unit manuals by other brands
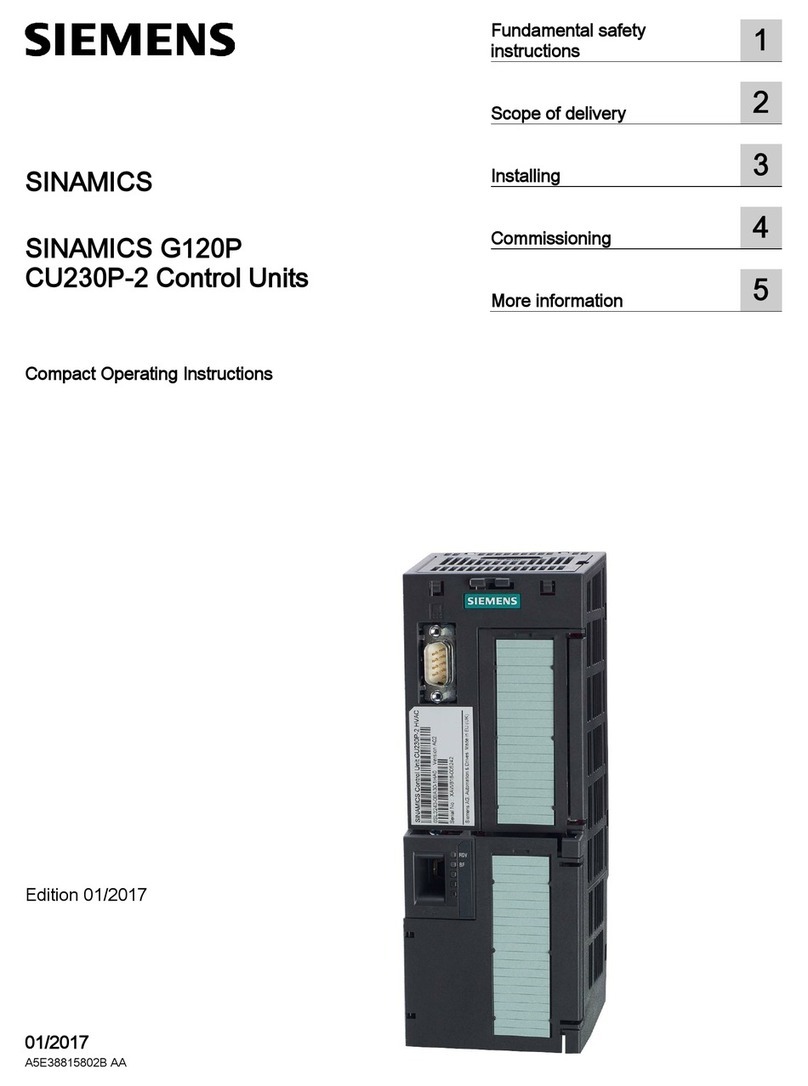
Siemens
Siemens SINAMICS G120P CU230P-2 Compact operating instructions

DSC
DSC PC5400 installation manual
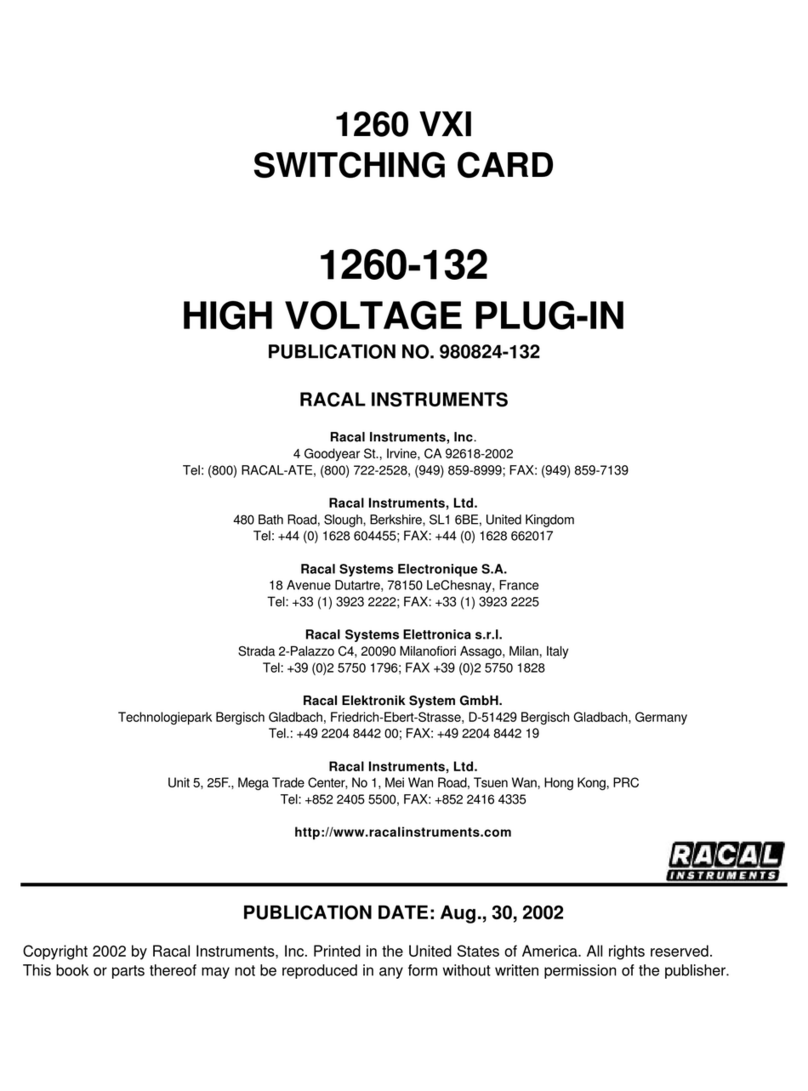
Racal Instruments
Racal Instruments 1260-132 manual
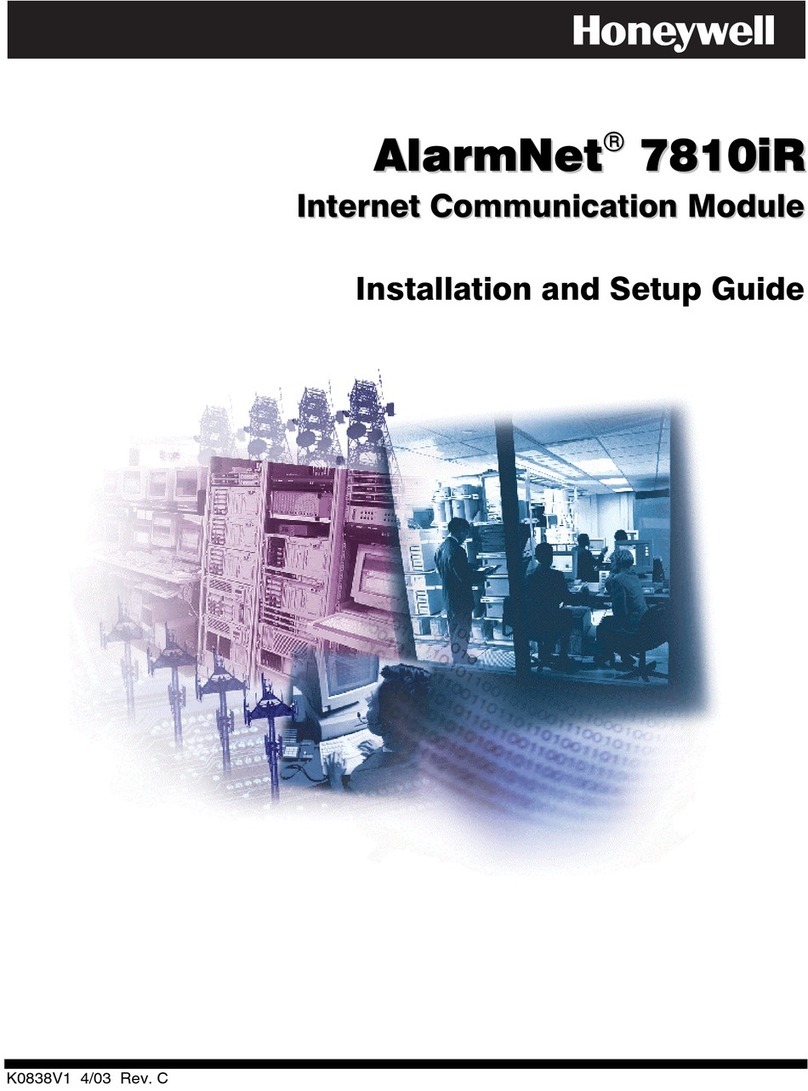
Honeywell
Honeywell AlarmNet 7810iR Installation and setup gude
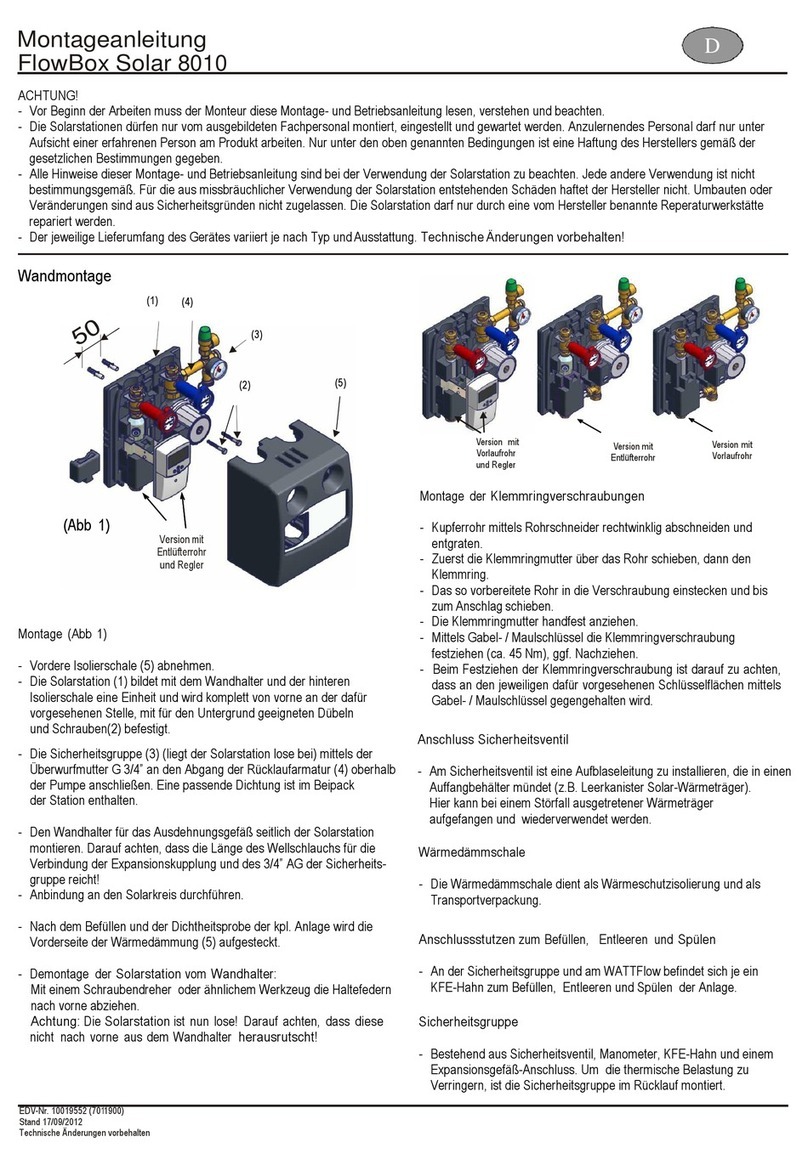
Watts Industries
Watts Industries FlowBox Solar 8010 installation instructions

Cisco
Cisco ATUC-4DMT-ISDN Installation and configuration
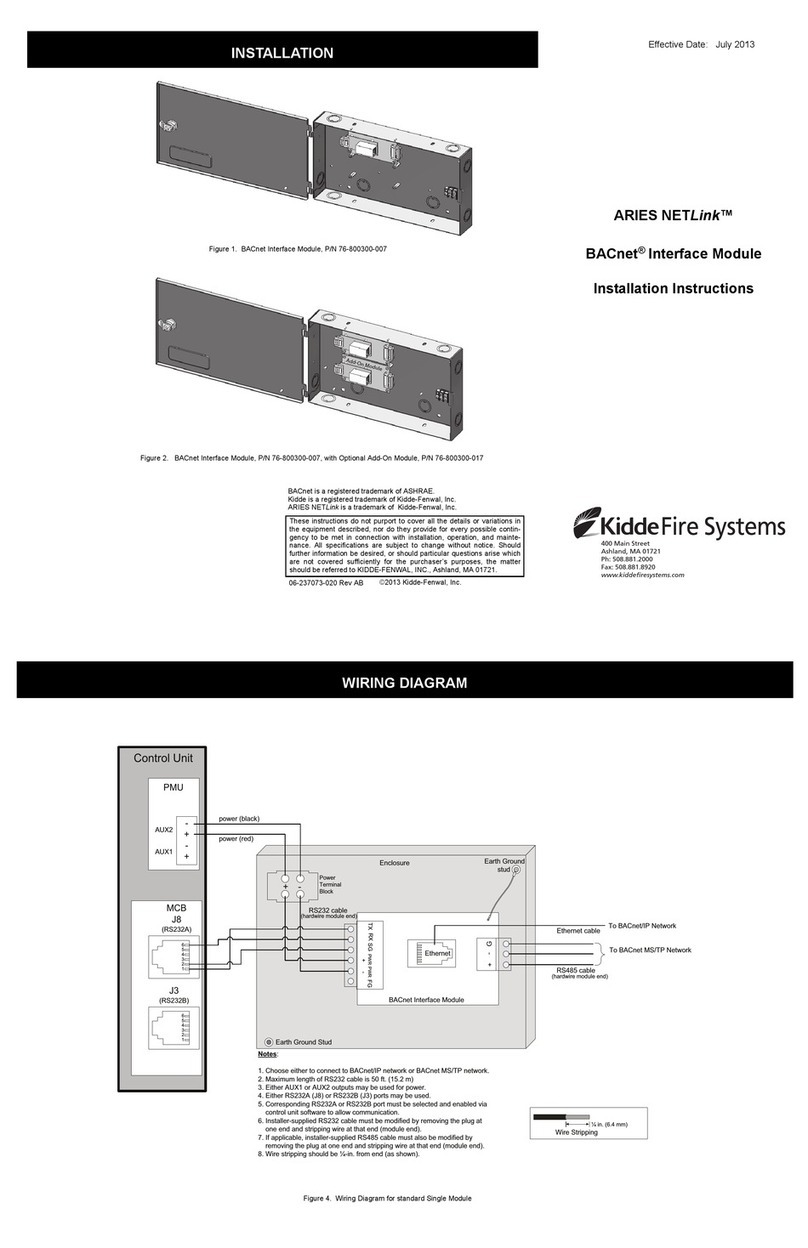
Kidde Fire Systems
Kidde Fire Systems ARIES NETLink 76-800300-007 installation instructions
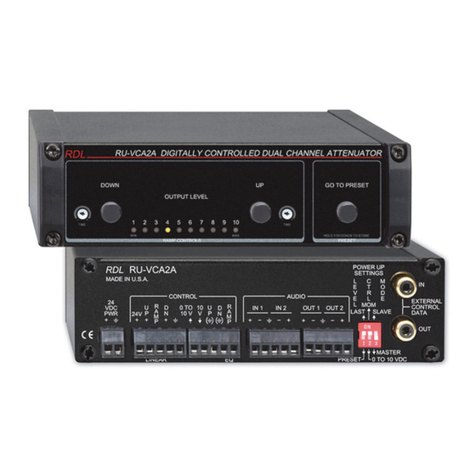
RDL
RDL RACK-UP Series Installation & operation
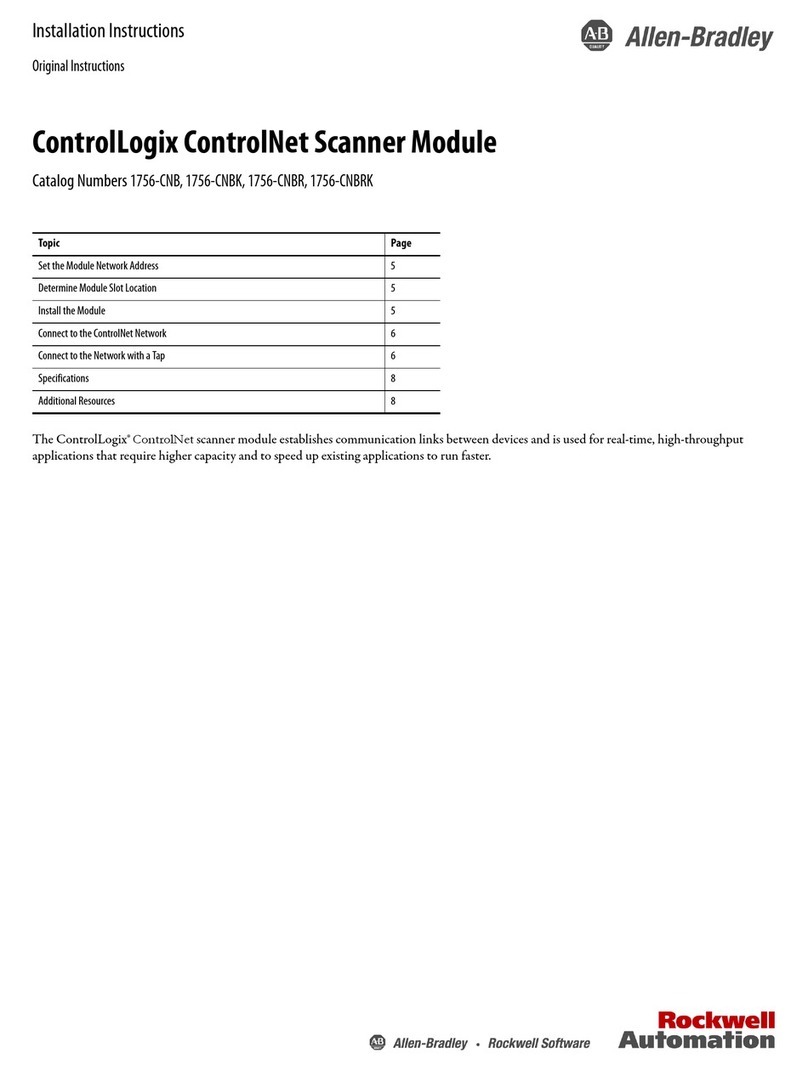
Allen-Bradley
Allen-Bradley ControlLogix ControlNet Scanner Module Installation instructions manual
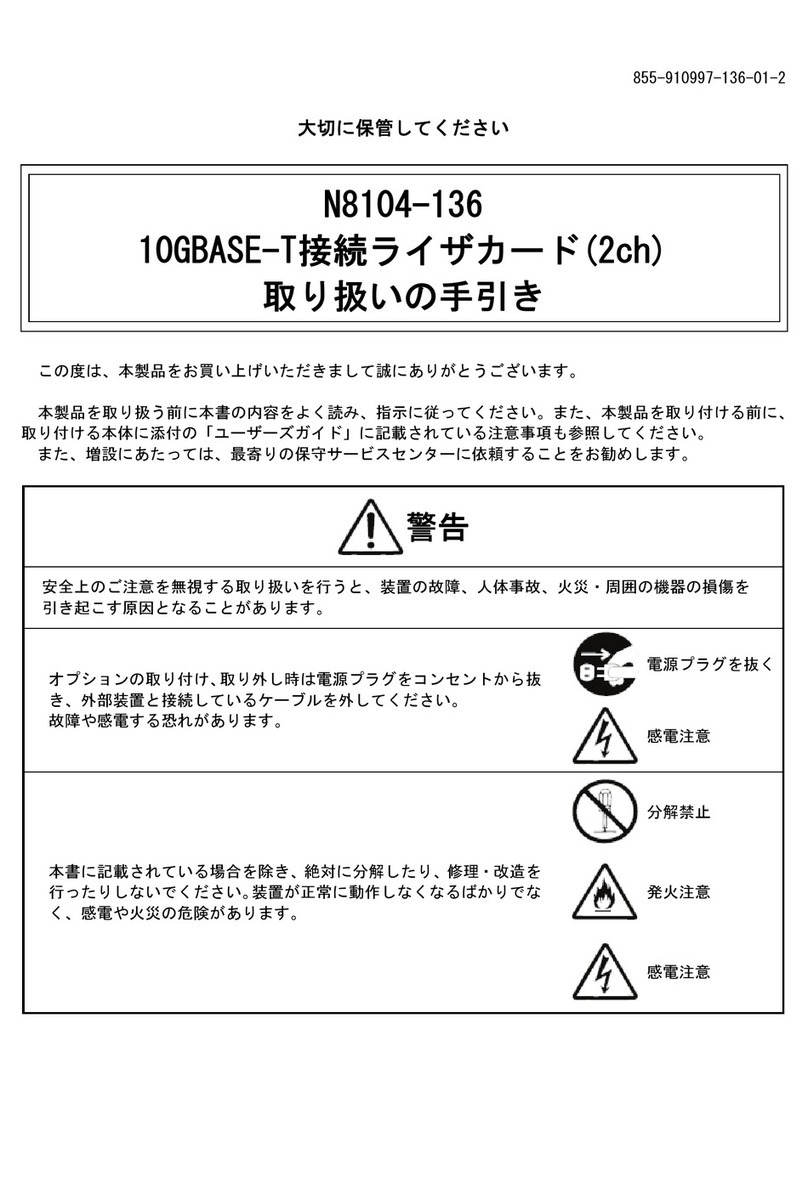
NEC
NEC 10GBASE-T user guide
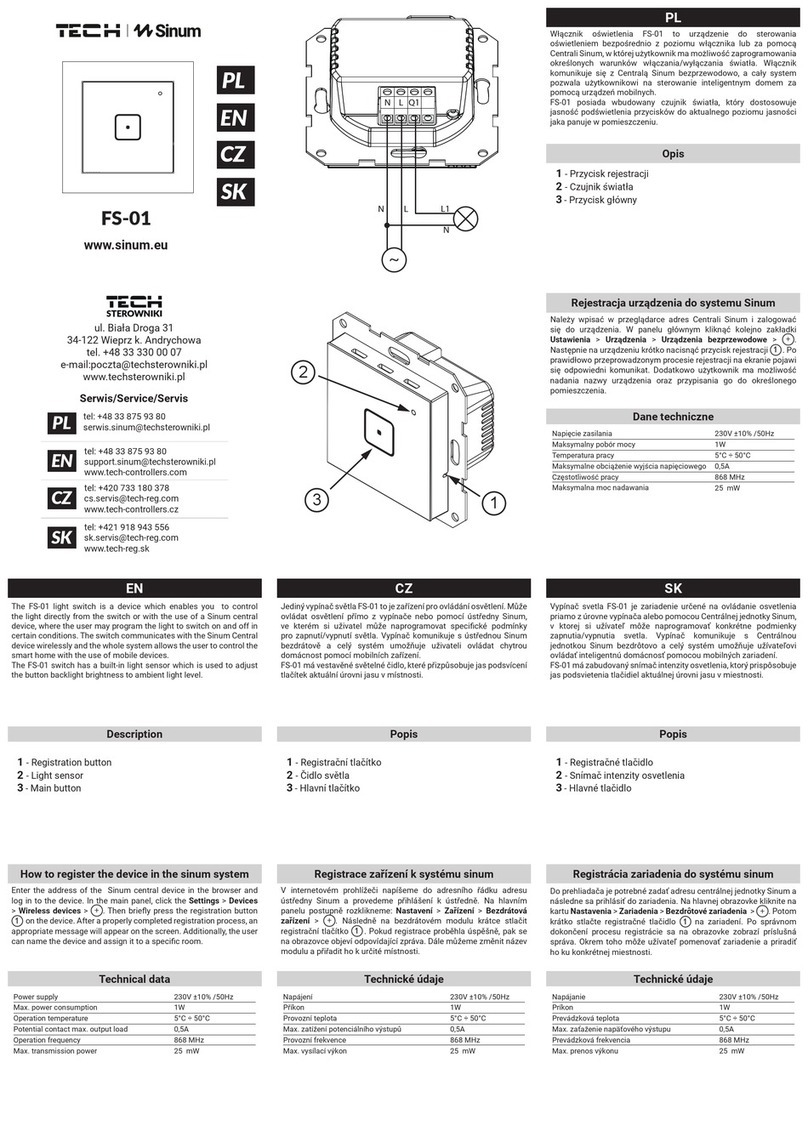
TECH
TECH Sinum FS-01 quick start guide
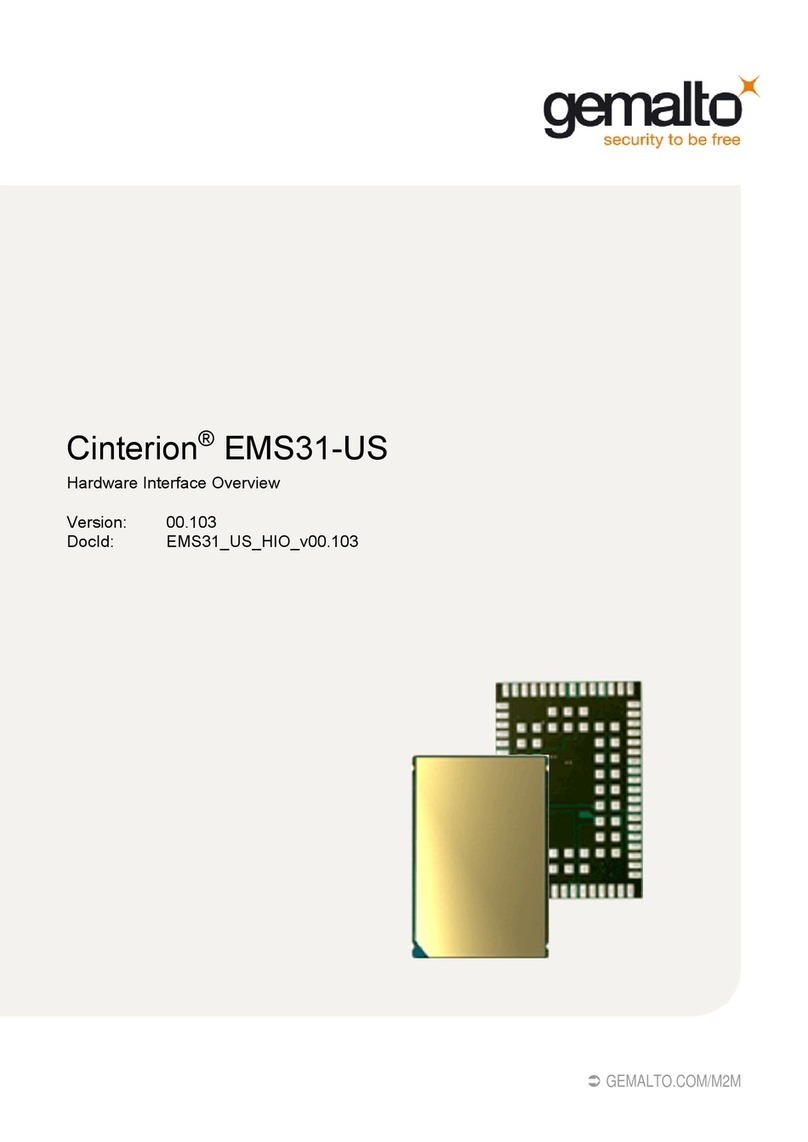
Gemalto
Gemalto Cinterion EMS31-US Hardware Interface Overview