Beckhoff CU2608 Operator's manual

Documentation
CU2608
8-port Ethernet Switch with IP67 protection class
2.0.0
2016-01-21
Version:
Date:


Table of contents
Table of contents
1 Foreword ....................................................................................................................................................4
1.1 Notes on the documentation............................................................................................................. 4
1.2 Safety instructions ............................................................................................................................ 5
1.3 Documentation issue status.............................................................................................................. 6
2 Product overview.......................................................................................................................................7
2.1 Introduction ....................................................................................................................................... 7
2.2 Basic function principles ................................................................................................................... 8
2.3 Technical data .................................................................................................................................. 9
3 Mounting and cabling .............................................................................................................................10
3.1 Dimensions ..................................................................................................................................... 10
3.2 Mounting ......................................................................................................................................... 11
3.3 Tightening torque for connectors .................................................................................................... 11
3.4 Power cable ................................................................................................................................... 13
3.5 Conductor losses ............................................................................................................................ 13
3.6 LED indicators ................................................................................................................................ 15
3.7 Ethernet cable................................................................................................................................. 16
4 Appendix ..................................................................................................................................................19
4.1 General operating conditions.......................................................................................................... 19
4.2 EtherCAT Box - accessories........................................................................................................... 20
4.3 Support and Service ....................................................................................................................... 21
CU2608 3Version: 2.0.0

Foreword
1 Foreword
1.1 Notes on the documentation
This description is only intended for the use of trained specialists in control and automation engineering who
are familiar with the applicable national standards.
It is essential that the following notes and explanations are followed when installing and commissioning
these components.
The responsible staff must ensure that the application or use of the products described satisfy all the
requirements for safety, including all the relevant laws, regulations, guidelines and standards.
Disclaimer
The documentation has been prepared with care. The products described are, however, constantly under
development. For that reason the documentation is not in every case checked for consistency with
performance data, standards or other characteristics. In the event that it contains technical or editorial errors,
we retain the right to make alterations at any time and without warning. No claims for the modification of
products that have already been supplied may be made on the basis of the data, diagrams and descriptions
in this documentation.
Trademarks
Beckhoff®, TwinCAT®, EtherCAT®, Safety over EtherCAT®, TwinSAFE®, XFC® and XTS® are registered
trademarks of and licensed by Beckhoff Automation GmbH & Co. KG.
Other designations used in this publication may be trademarks whose use by third parties for their own
purposes could violate the rights of the owners.
Patent Pending
The EtherCAT Technology is covered, including but not limited to the following patent applications and
patents: EP1590927, EP1789857, DE102004044764, DE102007017835 with corresponding applications or
registrations in various other countries.
The TwinCAT Technology is covered, including but not limited to the following patent applications and
patents: EP0851348, US6167425 with corresponding applications or registrations in various other countries.
EtherCAT® is registered trademark and patented technology, licensed by Beckhoff Automation GmbH,
Germany
Copyright
© Beckhoff Automation GmbH & Co. KG, Germany.
The reproduction, distribution and utilization of this document as well as the communication of its contents to
others without express authorization are prohibited.
Offenders will be held liable for the payment of damages. All rights reserved in the event of the grant of a
patent, utility model or design.
CU26084 Version: 2.0.0

Foreword
1.2 Safety instructions
Safety regulations
Please note the following safety instructions and explanations!
Product-specific safety instructions can be found on following pages or in the areas mounting, wiring,
commissioning etc.
Exclusion of liability
All the components are supplied in particular hardware and software configurations appropriate for the
application. Modifications to hardware or software configurations other than those described in the
documentation are not permitted, and nullify the liability of Beckhoff Automation GmbH & Co. KG.
Personnel qualification
This description is only intended for trained specialists in control, automation and drive engineering who are
familiar with the applicable national standards.
Description of symbols
In this documentation the following symbols are used with an accompanying safety instruction or note. The
safety instructions must be read carefully and followed without fail!
DANGER
Serious risk of injury!
Failure to follow the safety instructions associated with this symbol directly endangers the
life and health of persons.
WARNING
Risk of injury!
Failure to follow the safety instructions associated with this symbol endangers the life and
health of persons.
CAUTION
Personal injuries!
Failure to follow the safety instructions associated with this symbol can lead to injuries to
persons.
Attention
Damage to the environment or devices
Failure to follow the instructions associated with this symbol can lead to damage to the en-
vironment or equipment.
Note
Tip or pointer
This symbol indicates information that contributes to better understanding.
CU2608 5Version: 2.0.0

Foreword
1.3 Documentation issue status
Version Comment
2.0.0 - Migration
1.1.0 - Pin assignment for M12 socket added to introduction
1.0.0 - First public issue (technical data updated)
0.5.0 - draft
CU26086 Version: 2.0.0

Product overview
2 Product overview
2.1 Introduction
Fig.1: CU2608
8-port Ethernet switch in protection class IP67
The CU2608 Ethernet switch offers eight d-coded M12 Ethernet ports. Switches relay incoming Ethernet
frames to the destination ports. In full duplex mode, they prevent collisions.
They can be used universally in automation and office networks. It is installed either via two central 4mm
screws or two diagonally arranged 3mm screws.
The CU2608 meets the special requirements of real-time capable Industrial Ethernet solutions with
outstanding features:
• Compact design with IP67 plastic housing
• Eight d-coded M12 sockets
• 10/100 MBaud, half or full duplex, with automatic baud rate detection
• Cross-over detection: automatic detection and correction of crossover and straight-through Ethernet
cables
• Clear, fast diagnosis, one LED per Ethernet port
• Simple mounting in the field
CU2608 7Version: 2.0.0

Product overview
Socket pin assignment, 4-pin M12
Fig.2: Socket pin assignment, 4-pin M12
2.2 Basic function principles
Store and Forward
The switch operates according to the store-and-forward principle. Frames that are faulty (CRC error), too
short (< 64 bytes) or too long (> 1536 bytes) are generally not passed on.
Address Memory
The switch learns the MAC addresses of the connected devices for each port. Only frames that have these
addresses, broadcast/or multi-cast addresses, or which have unknown addresses are passed on to this port.
Because the switch remembers more than 1000 addresses for each port, it is also suitable for connecting
entire network segments. After approx. 5 minutes (Aging Time) unused addresses are removed from the
memory – if required, they are re-learnt again later.
Throughput
The switch can pass through up to 148800 Ethernet frames per second (Wire Speed).
PoE - Power over Ethernet
The CU20xx, CU22xx and CU26xx switches do not support PoE according to IEEE 802.3; they do not reveal
themselves as PSE (power sourcing equipment) or PD (powered devices). Any PSE connected to the switch
must therefore not apply a voltage.
No provision is made in the standard for passive interconnection or distribution.
Jumbo Frames
Jumbo Frames are oversized Ethernet telegrams with a length of more than 1518 bytes. They are used in
applications that require very high data throughput, for example.
The CU2208 (from hardware version 01) supports Jumbo Frames up to 9720 bytes on all ports. Please note
the following:
• Jumbo Frames only supported by ports with Gbit link
• Jumbo Frames place high demands on internal data transmission. It is therefore necessary to assess
the data throughput that can be achieved through the CU2208 for each individual application. Under
full load no more than 2 ports can be used for Jumbo Frames at the same time.
Jumbo Frames are not subject to standardization. It is therefore necessary to verify that the frames used by
the application are supported by the CU2208.
CU26088 Version: 2.0.0

Product overview
2.3 Technical data
Technical data CU2608-0000
Bus system Ethernet (all IEEE 802.3-based protocols)
Store-and-forward switching mode, unmanaged
Number of Ethernet ports 8
Ethernet interface 10BASE-T/100BASE-TX
Ethernet with M12, d-coded
Cable length up to 100m CAT5, switches cascadable as required
Baud rate 10/100Mbit/s, IEEE 802.3u auto-negotiation,
Half or full duplex at 10 and 100Mbit/s possible,
automatic settings
Diagnostics 1 LED per channel: link/activity, LED for power supply
Power supply Power supply and transfer via: M8 connector, 4-pin
Supply voltage 24VDC (-15 %/+20 %)
Current consumption typically 120 mA
Weight approx. 350 g
Dimensions without connector (W x H x D) approx. 126 x 60 x 26,5 mm
Mounting [}11] • Directly on mounting surface via two central 4mm
screws or two diagonally arranged 3mm screws.
• On ZS5300-0001 mounting rail.
permissible ambient temperature range during
operation
-30°C ... + 70°C
permissible ambient temperature range during
storage
-40°C ... + 85°C
Vibration/shock resistance conforms to EN 60068-2-6 / EN 60068-2-27
EMC immunity/emission conforms to EN 61000-6-2 / EN 61000-6-4
Protection class (according to EN60529) IP65, IP66, IP67
Installation position Any
Approval CE
CU2608 9Version: 2.0.0

Mounting and cabling
3 Mounting and cabling
3.1 Dimensions
Fig.3: Dimensions (all dimensions are given in millimeters)
Housing features
EtherCAT Box Narrow housing Wide housing
Housing material PA6 (polyamide)
Sealing compound Polyurethane
Mounting Two mounting holes Ø3mm for M3 Two mounting holes Ø3mm for M3
Two mounting holes Ø4.5mm for M4
Metal parts Brass, nickel-plated
Contacts CuZn, gold-plated
Current transfer max. 4 A
Installation position variable
Protection class in screwed state IP65/66/67 (according to EN 60529)/
Dimensions (H x W x D) approx. 126 x 30 x 26.5 mm approx. 126 x 60 x 26.5 mm
Weight approx. 125 g, depending on module
type
approx. 250 g, depending on module type
Approvals CE, cULus CE
CU260810 Version: 2.0.0

Mounting and cabling
3.2 Mounting
Note
Protect connectors against soiling
Protect all connections from contamination during module installation! Protection class IP65
can only be guaranteed if all cables and connectors are connected! Unused connections
must be protected with the appropriate connectors! Connector sets see catalogue.
Modules with narrow housing are installed with two M3 screws.
Modules with wide housing are installed with two M3 screws in the mounting holes in the corners or two M4
screws in the central mounting holes.
The bolts must be longer than 15 mm. The mounting holes in the modules have no thread.
Note when mounting that the overall height is increased further by the fieldbus connections. See the
Accessories section
Mounting rail ZS5300-0001
The mounting rail ZS5300-0001 (500 mm x 129 mm) allows time-saving configuration of the modules.
The rail is made of 1.5 mm thick stainless steel (V2A) and features ready-made M3 threads. The rail has 5.3
mm slots for mounting on the machine with M5 screws.
Fig.4: Mounting rail
The mounting rail is 500 mm long and enables the installation of 15 narrow modules, with a distance of 2 mm
between them. It can be shortened as required for your particular application.
3.3 Tightening torque for connectors
M8 connector
We recommend fastening the M8 connector with a torque of 0.4Nm.
CU2608 11Version: 2.0.0

Mounting and cabling
Fig.5: M8 connector
M12 connector
We recommend fastening the M12 connector with a torque of 0.6 Nm.
Fig.6: M12 connector
Torque wrench
Note
Ensure the proper torque is used
Use torque wrenches available from Beckhoff to tighten the connectors (see accessories
[}20])!
Fig.7: Torque wrench
CU260812 Version: 2.0.0

Mounting and cabling
3.4 Power cable
Ordering data
Order identifier Power cable Screw
connector
Contacts Cross-sec-
tion
Length
ZK2020-3200-0020 Straight socket, open end M8 4-pin 0.34 mm22.00 m
ZK2020-3200-0050 5.00 m
ZK2020-3200-0100 10.00 m
ZK2020-3400-0020 Angled socket, open end 2.00 m
ZK2020-3400-0050 5.00 m
ZK2020-3400-0100 10.00 m
ZK2020-3132-0001 Straight socket, straight
connector
0.15 m
ZK2020-3132-0005 0.50 m
ZK2020-3132-0010 1.00 m
ZK2020-3132-0020 2.00 m
ZK2020-3132-0050 5.00 m
ZK2020-3334-0001 Angled socket, angled connector 0.15 m
ZK2020-3334-0005 0.50 m
ZK2020-3334-0010 1.00 m
ZK2020-3334-0020 2,00 m
ZK2020-3334-0050 5.00 m
Further available power cables and the associated data sheets can be found in the Beckhoff catalogue or on
our website (http://www.beckhoff.de).
Technical data
Data
Rated voltage according to IEC61076-2-101 30 VDC
Contamination level according to IEC 60 664-1 3/2
Insulation resistance IEC 60 512-2 >109W
Current carrying capacity according to IEC 60512-3 4 A
Volume resistance according to IEC 60512-2 < 5mW
Protection class conforms to IEC 60529 IP65/66/67, when screwed together
Ambient temperature -30°C to +80°C
3.5 Conductor losses
The ZK2020-xxxx-yyyy power cables should not exceed the total length of 15 m at 4 A (with continuation).
When wiring, note that with a rated voltage of 24 V the function of the modules can no longer be guaranteed
from a voltage drop of 6 V. Variations in the output voltage from the power supply unit must also be taken
into account.
CU2608 13Version: 2.0.0

Mounting and cabling
Fig.8: Voltage drop in the power supply line
Example:
8 m power cable with 0.34 mm² cross-section has a voltage drop of 3.2 V at 4 A.
CU260814 Version: 2.0.0

Mounting and cabling
3.6 LED indicators
Ethernet
Fig.9: LEDs CU2608
An LED for each of the eight channels shows the current status.
Table1: LEDs per channel
LED Display
Link
Act
off No connection
on Connection available (link)
flashing Data transfer (act)
Supply voltage
Fig.10: Supply voltage
LED Display Meaning
24V Us (control
voltage)
off the power supply voltage, Us, is not present
green
illuminated
the power supply voltage, Us, is present
red
illuminated
Due to overload (current > 0.5A), the sensor supply generated from
the supply voltage Us was switched off for all sensors supplied from it.
24V Up (peripheral
voltage)
off the power supply voltage, Up, is not present
green
illuminated
The power supply voltage, Up, is present
CU2608 15Version: 2.0.0

Mounting and cabling
The peripheral voltage Up is not required in the CU2608 and is therefore passed through.
3.7 Ethernet cable
For connecting Ethernet devices, only use shielded Ethernet cables with a minimum specification of
category5 (CAT5) according to EN50173 and ISO/IEC11801.
Note
Wiring recommendations
Detailed recommendations for Ethernet wiring can be found in the documentation "Design
recommendations for EtherCAT/Ethernet infrastructure", which is available for download
from http://www.beckhoff.de/.
Ethernet uses four cable wires for signal transmission. Due to automatic cable detection (auto-crossing)
symmetric (1:1) or cross-over cables can be used between Ethernet devices from BECKHOFF.
A selection of pre-configured cables (up to 10 m) and cables sold by the meter is provided below. Other
cables with various lengths will be found in the full Beckhoff catalogue, and under www.beckhoff.de.
Sold by meter
Name Description
ZB9010 CAT 5e, 4-core, for fixed laying, not for M8 connectors
ZB9020 CAT 5e, 4-core, suitable for drag chain use, not for M8 connectors
ZB9030 PVC, Ø 4.9mm for M8 connectors
ZB9031 PUR, Ø 4.8mm for M8 connectors
ZB9032 PUR, Ø 5.4mm for M8 connectors, high flexibility
ZK1090-6161-00xxx: 2x M12 connector (d-coded), pre-assembled
Fig.11: ZK1090-6161-0xxx.
ZK1090-6161- 0005 0010 0020 0025 0050 0100
Length 0.5 m 1.0 m 2.0 m 2.5 m 5.0 m 10 m
CU260816 Version: 2.0.0

Mounting and cabling
ZK1090-6191-00xxx: M12 connector - RJ45 connector, pre-assembled
Fig.12: ZK1090-6191-0xxx
ZK1090-6191- 0005 0010 0020 0025 0050 0100
Length 0.5 m 1.0 m 2.0 m 2.5 m 5.0 m 10 m
ZK1090-6292-00xxx: M12 socket - RJ45 connector, pre-assembled
Fig.13: ZK1090-6292-0xxx
ZK1090-6292- 0005 0020 0050 0100
Length 0.5 m 2 m 5 m 10 m
ZK1090-9191-00xxx: 2 x RJ45 connector, patch cable
Fig.14: ZK1090-9191-0xxx
CU2608 17Version: 2.0.0

Mounting and cabling
ZK1090-9191- 0001 0002 0005 0010 0020 0030 0040 0050 0100 0150
Length 0.17 m 0.26 m 0.5 m 1.0 m 2.0 m 3.0 m 4.0 m 5.0 m 10 m 15 m
ZK1090-9191- 0200 0250 0300 0350 0400 0450 0500
Length 20 m 25 m 30 m 35 m 40 m 45 m 50 m
CU260818 Version: 2.0.0

Appendix
4 Appendix
4.1 General operating conditions
Protection classes according to IP code
The levels of protection are defined and divided into different classes in the IEC 60529 standard (DIN EN
60529). The designation follows the scheme below.
1st digit: Protec-
tion against
ingress of dust and
access to haz-
ardous parts
Meaning
0 Non-protected
1 Protection against access to hazardous parts with back of hand. Protection against
ingress of solid foreign objects = 50 mm diameter
2 Protection against access to hazardous parts with a finger. Protection against ingress
of solid foreign objects = 12.5 mm diameter
3 Protection against access to hazardous parts with a tool. Protection against ingress of
solid foreign objects = 2.5 mm diameter
4 Protection against access to hazardous parts with a wire. Protection against ingress of
solid foreign objects = 1 mm diameter
5 Protection against access to hazardous parts with a wire. Protection against ingress of
dust. Ingress of dust is not prevented completely, although the quantity of dust able to
penetrate is limited to such an extent that the proper function of the device and safety
are not impaired
6 Protection against access to hazardous parts with a wire. Dust-proof. No ingress of
dust
2nd digit: Protec-
tion against
ingress of water*
Meaning
0 Non-protected
1 Protection against dripping water
2 Protection against dripping water (housing tilted up to 15°)
3 Protection against spraying. Water sprayed at an angle of up to 60° from vertical must
not have any adverse effect
4 Protection against splashing. Water splashing against the housing from any direction
must not have any adverse effects
5 Protection against jetting.
6 Protection against powerful jetting.
7 Protection against the effects of temporary immersion. The quantity of water being
able to penetrate if the housing is submerged in water for 30 minutes at a depth of 1 m
must not have any adverse effects
*) These protection classes only define protection against ingress of water.
Chemical resistance
The resistance refers to the fieldbusbox housing and the metal components used.
CU2608 19Version: 2.0.0

Appendix
Type Resistance
Water vapor unstable at temperatures > 100 °C
Sodium hydroxide
solution
(pH value>12)
stable at room temperature
unstable > 40 °C
Acetic acid unstable
Argon (technically
pure)
stable
Legend
stable: service life several months
limited stability: service life several weeks
unstable: service life several hours, rapid decomposition
4.2 EtherCAT Box - accessories
Table2: Mounting
Ordering information Description
ZS5300-0001 Mounting rail (500mm x 129mm)
Table3: Labelling material, plug
Ordering information Description
ZS5000-0000 Fieldbus box set M8 (inscription labels, sealing plugs)
ZS5000-0002 Fieldbus box set M12 (inscription labels, sealing plugs)
ZS5000-0010 M8 plugs IP67 (50-off)
ZS5000-0020 M12 plugs IP67 (50-off)
ZS5100-0000 Inscription labels, blank, 4 strips of 10
ZS5100-xxxx Printed inscription labels on enquiry
Table4: Tool
Ordering information Description
ZB8800 Torque socket wrench with ratchet for molded-on M8 connector
ZB8800-0001 Ratchet for field-configurable M8 connector
ZB8800-0002 Ratchet for molded-on M12 connector
Note
Further accessories
You can find further accessories in the price list for fieldbus components from Beckhoff and
on our website at www.beckhoff.de.
CU260820 Version: 2.0.0
Table of contents
Other Beckhoff Switch manuals
Popular Switch manuals by other brands

United Electric Controls
United Electric Controls B117 Installation and maintenance instructions
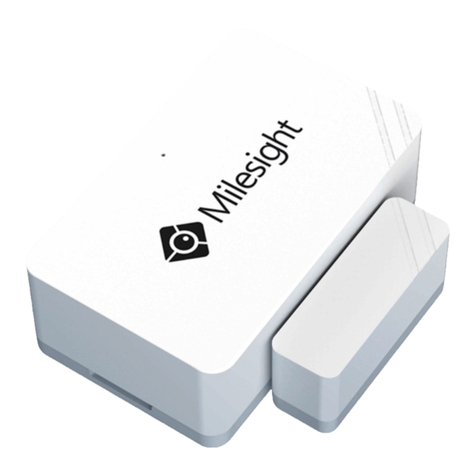
Milesight
Milesight WS301 user manual
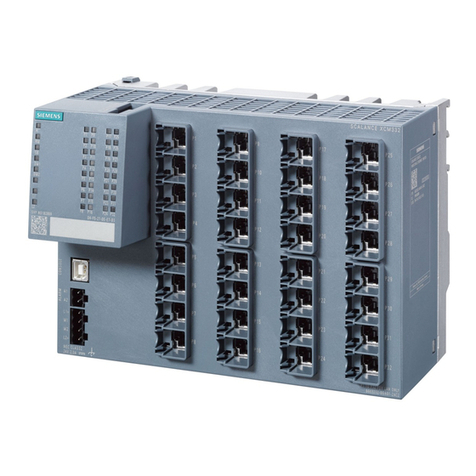
Siemens
Siemens SIMATIC NET SCALANCE XCM-300 product manual
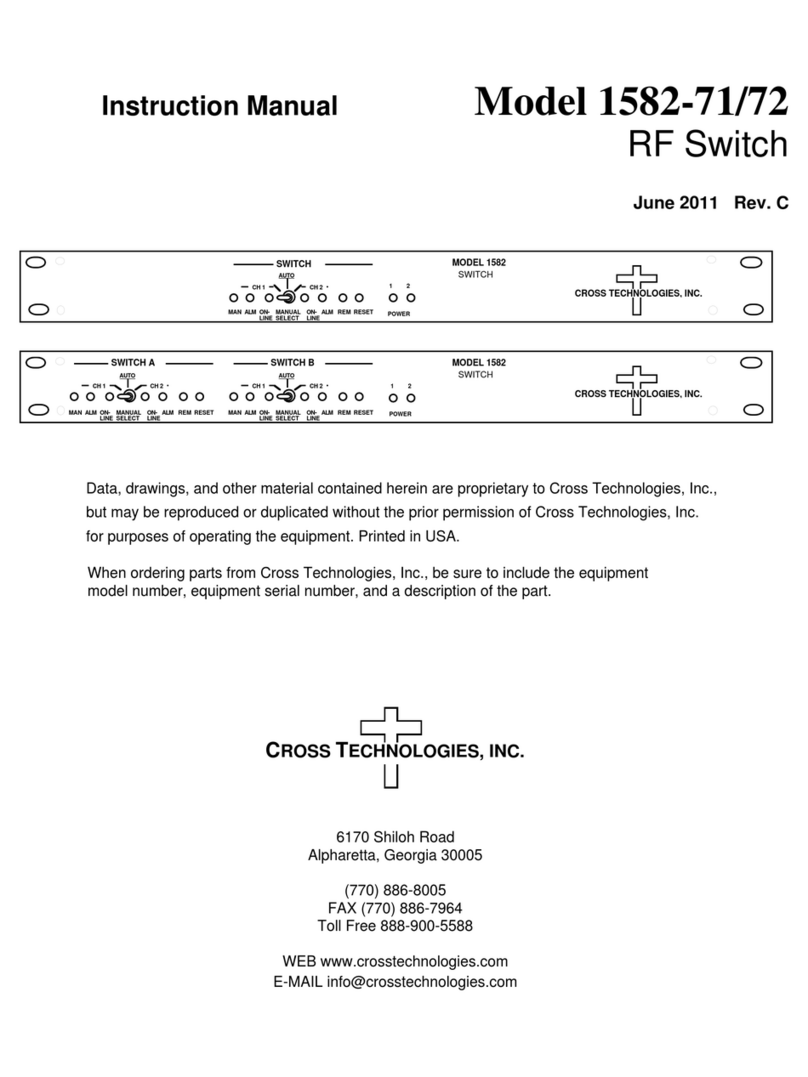
Cross Technologies
Cross Technologies 1582-71 instruction manual
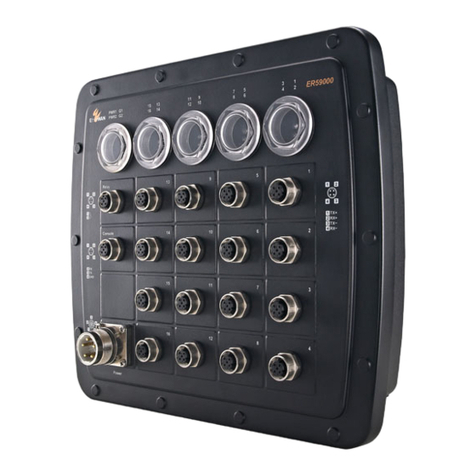
EtherWAN
EtherWAN ER59000 Series quick start guide
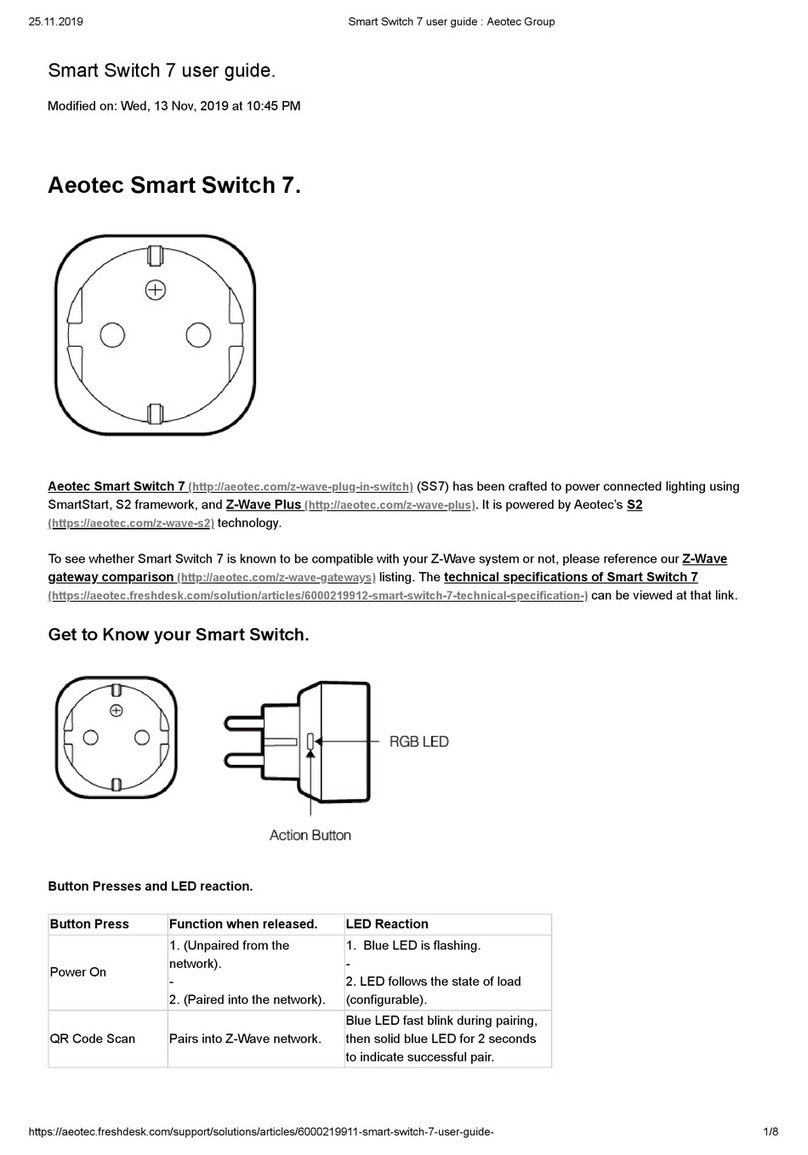
Aeotec
Aeotec Smart Switch 7 user guide