Bell System Practices COMBINATION 505D User manual

-~'
BELL
SYSTEM
PRACTICES
SECTION 167-676-301
AT&TCo
Standard
Issue
3,
March
1974
(
COMBINATION
505D/521A
POWER PLANT
OPERATING METHODS
CONTENTS
PAGE
1.
GENERAL
3
2.
LIST
OF TOOLS AND
TEST
APPARATUS
10
3. OPERATION
12
A. PWR CONT Bay Power Turnup Procedure
12
B.
PWR
CONT
Bay
Power
Turndown
Procedure
• •
17
C.
Transferring
Load
From
Regular
Motor-Alternator
to
Emergency
Motor-Alternator
•
18
D.
Transferring
Load
From
Emergency
Motor-Alternator
Back
to
Regular
Motor-Alternator
• •
19
E.
Removing Motor-Alternator From Service
F.
Restoring
Motor-Alternator
to
Service
G. Transferring
Motor-Alternators
From
DC
Drive Back
to
AC Drive
After
Power
Service
Frequency
Has
Returned
to
Normal, Plant Equipped With Frequency
20
21
Monitor
Circuit (ZH
option)
22
H.
Restoring
Motor-Alternators
to
Service
After
Overspeed
Shutdown
Occurs,
Motor-Alternators
Equipped
With
Overspeed
Shutdown Circuit (ZT
option)
I.
Restoring
Output
Voltage
Limiter Circuit
to
Normal
Operation,
Motor-Alternators
Equipped
With
Output
Voltage
Limiter
Circuit
(ZM
option)
• •
J.
Transferring
Load
From
Inverter
to
Emergency
Motor-Alternator
22
23
23
CONTENTS
K.
Transferring
Load
From
Emergency
Motor-Alternator
Back
to
Inverter
L.
Removing
Inverter
From
Service
M.
Restoring
Inverter
to
Service
4.
ROUTINE
CHECKS
A.
Clean
Ventilating
Passages
B.
Voltage
Transfer
Control
Circ~it
Check
(TRANSFER CONTROL
Bay)
C.
Transfer
Relay
Check
(TRANSFER
CONTROL
Bay)
D.
Motor-Alternator
High
and
Low
Voltage
Checks
E.
Motor-Alternator
Speed
Adjustments
(Motor-Alternators
Not
Equipped
With
TD
Relays)
F.
Motor-Alternator
Speed
Adjustments
(Motor-Alternators
Equipped
With
TD
Relays)
G.
KS-15994
and
KS-15626
Regular
or
Emergency
Motor-Alternator
Output
Voltage Limiter Check, Motor-Ait__-rnators
Equipped
With
Output
Voltage
Limiter
Ci:~
option)
H.
Motor-AI~rnator
Overspeed
Shutdown
(Circuit Check, Motor-Alternators Equipped
1
With
Overspeed
Shutdown
Circuit (ZT
~ption)
• •
I.
Motor-Alternator
Line Frequency
Monitor
Calibration
Check,
Plant
Equipped
With
Frequency
Monitor
Circuit (ZH
option)
PAGE
24
24
25
25
25
26
32
33
35
38
43
44
46
© American Telephone and Telegraph Company, 1974
Printed in U.S.A.
Page
1

SECTION
167-676-301
CONTENTS PAGE
J.
Inverter
OUTPUT
VOLTAGE
(M2)
Voltmeter
Calibration Check
46
K.
Inverter
Output
Voltage
Check
47
L.
Inverter
EARLY
WRN
MONITOR
Alarm
Check
47
M.
Inverter
EARLY
WRN MONITOROperation
Check •
47
N.
INV
TRFR
MONITOR
Alarm
Check
49
0.
INV
TRFR
MONITOR
Operation
Check
50
P.
Inverter
SHUT
DWN
MONITOR
Alarm
~~
. . "
Q.
Inverter
SHUT
DWNMONITOR Operation
Check • • 52
R.
Inverter
Shutdown Time
Delay
Check 55
S.
Inverter
Battery
Fuse
Alarm
Check
56
T.
Inverter
DC
Filter
Network
Fuse Alarm
Check • •
U.
Inverter
AC
Filter
Network
Fuse
Alarm
Check • •
V. PWR CONT
Bay
Line Current Check
W.
PWR
CONT
Bay
VR
Voltage
Relay
Check
X.
PWR
CONY
Bay
VA
Voltage
Relay
Check
Y. PWR CONY
Bay
NV
Relay Check
Z.
PWR
CONY
Bay
Electronic
Current
57
58
58
60
61
63
Regulator Check 64
AA.PWR
CONY
Bay
Cable
Overcurrent
Monitor
Switch Calibration Check
66
AB. PWR CONY
Bay
Failure
Alarm
Check
70
Page 2
CONTENTS
AC.
PWR
CONY
Bay
Electronic
Current
Regulator Failure
Alarm
Check
AD.
PWR CONT
Bay
Fuse
Alarm
Check
5.
TROUBLES
Tables
A.
Voltage
Settings
for
Operation
of
VR1
PAGE
71
72
72
Relay •
28
B.
TD
Relay AdJustment
C.
Transfer Control, Supl Transfer
Control,
Start
Control,
and
Emg
Start
Control
Bays
and
Motor-Alternators
Trouble
Chart •
D.
Inverters
Trouble Chart
E.
PWR CONY
Bay
Trouble Chart
Figures
1.
505D/521A
Power
Plant-Possible
Main
Configurations
2.
Typical
505D/521A
Power
Plant
(Power
Room)-Biock
Diagram •
3.
Typical
505/521A
Power
Plant
(Carrier
Room) Block Diagram
4. Control Panel
of
TRANSFER
CONTROL
Bay
5. Control Panel
of
SUPL
TRANSFER
CONTROL
Bay
6. KS-19738
Inverter
7.
Partial
View
of
521A
Power
Plant
Lineup-Cutaway
View
shows a KS-19738
Regular
Inverter
8. J86854C Control Panel
of
KS-19738 Regular
Inverter
9. PWR CONT
Bay
40
4
5
6
8
9
11
12
13
14
(
(

(
CONTENTS
PAGE
10.
Control Panel
of
PWR
CONT Bay
15
11. Illustration Showing Change
in
AC Output
Voltage
vs Time During Transfer From AC
to
DC
Drive • • • • •
40
12. Typical 70-Type
Fuse
Cap
56
13.
Fuse
Alarm Testing Cord·Tool Connection
57
14.
Gate
Waveform
75
15.
Master
Oscillator
Waveform
75
16. Masterand Slave OscillatorDrive Waveforms
75
17.
Unfiltered Inverter Output
Waveform
76
18.
Slave 01cillator
Waveform
76
1.
GENERAL
1.01
The
521A
inverter power plant may be used
in
combination with the
505D
motor-alternator
power plant. The 505D/521A power
plant
can
contain a maximum combination of seven
KS-15626,
KS-15993,
or
KS-15994
motor-alternators
and
KS-19738
inverters
including
the
emergency
motor-alternator. The combination plant supplies
ISS
3,
SECTION
167-676-301
power for the 12-coaxial system. Refer to Fig. 1
for
the
various 505D/521A power plant lineups.
The plant is primarily intended for use
in
the
L3
carrier
system
but
may
be
used
whenever
its
characteristics and design apply. Refer to Fig. 2
and Fig. 3for block diagrams
of
a typical505D/521A
power plant (power room and carrier room).
1.02
This section is reissued to add reference to
the
YB
and
YD
options and to revise
the
list
of
tools
and
test
apparatus
in
Part
2,
the
operating information
in
Part
3,
the routine checks
in
Part
4,
and the trouble information in
Part
5.
This reissue does not
affect
the
Equipment
Test
List.
Warning:
This
power
plant
includes
automatic
equipment
and
voltages
as
high
as
4400
volts.
Extreme
caution
should
be
exercised
to
prevent
the
accidental
starting
of
the
parts
of
the
power
plant
on which
maintenance
work
is
to
be
performed.
Before
starting
work
on
the
power
plant,
prevent
the
automaticstarting
of
equipment
by
removingfuses, blocldngrelays, operating
switches, etc,
as
necessary.
Caution:
While
performing
some
maintenance,
it
may
be
necessary
to
turn
the
power
down
on
the
associated coaxial
cabletoprevent
possibleswitchingtransients
from
damaging
the
associated
repeater
equipment. Before
turning
the
power
down
on
the
coaxial
cable,
be
certain
thai
all
associated
terminals
are
notified
of
the
Page 3

SECTION
167-676-301
PLANT
LINEUP
FOR
COMBINATION
505D
AND
521A
PLANTS
SHOWING
POSSIBLE
MAIN
CONFIGURATIONS
(FOR
16kVA
ONLY).
THE
505D
PLANT:
TRANSFER
CONTROL
BAYS,
J86448B
L2,
AND
J86448C
L2.
THE
521A
PLANT:
J86854A
REGULAR
INVERTER,
NO
START
CONTROL
BAYS
FOR
ALTERNATORS
ARE
SHOWN.
Page
4
ORIGINATING
TRANSFER
oomoc
'"
"'";,;i,i;;i~,mm.:,:,.m
INVERTERS
~----------------------------------~-J86854A(REGULAR)
~----------~-
WHENINVERTERS(6)AND{7)ARE
~
.""""''''
DDDDD
llllliiliil
ADDED,
A
J86448C
L7
UNIT
MUST
BE ADDEO TO
THE
ORIGINATING
TRANSFER
CONTROL
BAY,
J86448B
L2{PRESENTLY
AVAILABLE
ON
JOB
ANALYSIS
ONLYl.
ALT
EMERG
(I)
ALT
REG
{2)
EXISTING
PLANT
ORIGINATING
TRANS~ER
CONTROL BAY
J8644~
~
ALT
ALT
EMERG REG
(I)
(2)
EXISTING
PLANT
ORIGINATING
TRANSFER
CONTROL BAY
J86448B
L2
INV
REG
{3)
INV
REG
{4)
INV
REG
(5)
ADDEO
UNITS
(CONFIGURATION
I)
INV
REG
{6)
INV
REG
(7)
~~~:
1
T
SUPPLEMENTAL
TRANSFER
-==:]"'"
'"
"'""
"
INVERTERS
~--------------------------~-J86854A(REGULAR)
ALT
INV
REG REG
(3)
(4)
r-----------~-
WHENINVERTERS(6}AND(7)ARE
INV
INV
REG REG
(5)
(6)
ADDEO
UNITS
INV
REG
(7)
ADDEO,
A
J86448C
L7
UNIT
MUST
BE
ADDEO
TO
THE
1ST
SUPPLEMENTAL
TRANSFER
CONTROL
BAY,
J86448C
L2.
(CONFIGURATION
2)
FIRST
SUPPLEMENTAL
TRANSFER
CONTROL BAY
J86448C
L2
AND
L5
SECOND
SUPPLEMENTAL
TRANSFER
CONTROL BAY
J86448C
L2
--~
ALT ALT ALT ALT
EMERG
REG
REG
REG
(I)
(2)
(3)
(4)
EXISTING
PLANT
(CONFIGURATION
ALT
REG
(5)
3)
INVERTERS
~-------------J86854A(REGULAR)
~----------~-WHENINVERTERS(6)AN0(7)
ARE
INV
INV
REG
REG
(6)
(7)
ADDED
UNITS
ADDED,
A
J86448C
L7
UNIT
MUST
BE
ADDED
TO
THE
2ND
SUPPLEMENTAL
TRANSFER
CONTROL
BAY,
J86448C
L2
Fig.
1-505D/521A
Power
Plant-Possible
Main Configurations
(
(

(
TO
J86447A
PWR CONT
BAYS
FOR
COAXIALS
l201-202
WEST
AND
LZOI-202
EAST (SEE FIG.
3)
UNREGULATED
230
VAC
NOMINAL
60
HZ
MANUAL
BYPASS
SWITCH
AC
INPUT
POWER
NOMINAL
230
VAC
60HZ
ALTERNATOR
TRANSFER
CONTACTOR
CONTROL
CIRCUIT
~,..------E----,A~
DC
A-
DC
MOTOR
AC
MOTOR
SWITCH
MOTOR
y
CONTROLLER
I
I
I
AC
MOTOR
MOTOR-
ALTERNATOR
SET@§)
70-CELL
BATTERY
BATTERY
PLANT
NOMINAL
152
VAC
ISS
3, SECTION 167-676-301
UNREGULATED
230
VAC
~
E
TTO
OFFICE
UNREGULATED
230
VAC
ERMINAL
QUIPMENT
TO
J86447A
PWR
CONT
UN
REGULATED
t-•UN•R•E•G•U•L•A•T•E•D-2•3•0•V•A•C-+
BAYS
FOR COAX IALS
230
VAC
L203-204
WEST AND
NOMINAL
60HZ
L203-204
EAST
MANUAL
BYPASS
SWITCH
DC
MOTOR
~
DC
CONTROLLER
i -
y
MOTOR
I
I
AC
MOTOR
MOTOR-
ALTERNATOR
SET@])
ADDITIONAL
SUPPLEMENTARY
CHARGE
BAY
J86826B
INVERTER
TRANSFER
CO
NT
ACTOR
CONTROL
CIRCUIT
REGULAR
INVERTER
TO
AND
FROM
INVERTERS
3-6
INVERTER
~
NOTE:
AC
MOTOR
SWITCH
THE
FOLLOWING
CIRCUIT
SCHEMATIC
DRAWINGS
COVER
THIS
EQUIPMENT:
SD-81149-01
SD-81799-01
SD-81821-01
SD-81831-01
~~!
____________
1~------~!~----~i-
TPA
5
21052
Fig.
2-Typical
505D/521A
Pawer Plant (Power
Room)-Biock
Diagram
Page 5

SECTION
167·676-301
SD•81152-01
AND
SD-81164·01
J86447A
PWR
CONT
BAY
L201·202
WEST
J86447A
PWR
CONT
BAY
L201·202
EAST
COARSE COARSE
REGULATOR
REGULATOR
RELAY
CONTROL
RELAY
CONTROL
TO
Tl
TO
Tl
t 1
Tl
AND
T2
Tl
AND
T2
T5
lotOTOR
DR
I
YEN
lotOTOR
DRIVEN
TRANSFORMERS
T5
L3 COAXIAL
LINE
HIGH
VOLTAGE
TRANSFORMERS
HIGH
VOLTAGE
L3 COAXIAL LINE
TRANSFORMER
AND
T3
~
AND
T3
BUCK·
BOOST
BUCK-BOOST
TRANSFORMER
4400
VAC
MAXIMUM
TRANSFORMER
TRANSFORMER
4400
VAC
t~AX
I
MUt·1
OUTPUT OUTPUT
NOMINAL
60HZ t t NOMINAL 60HZ
u
""
>
0
""
NN
:X:
0
FINE
wo
FINE
1-<D
REGULATOR
<
-'-'
REGULATOR
ELECTRONIC
"'""
<-'Z
ELECTRON
I(!
.....
-
CONTROL
TO
T2
a:::J:
CONTROL
TO
T2
zo
:::>z
FROM
505D/52lA
POWER
ROOM
(SEE FIG.
2)
TPA
563759
Fig.
3-Typical
505D/521A Power Plant (Carrier
Room)-Biock
Diagram
forthcoming
actions
and
that
all
necessary
precautions
are
taken.
When
maintenance
work
has
been
completed,
be
certain
to
restore
the
circuits
to
normal
operation.
1.03 The combination plant provides nominal ac
outputs
of
230
volts,
60
Hz.
Each
motor-alternator
in
the plant consists of an alternator,
an ac motor, and a
de
motor. The motor-alternators
in
the
plant
normally operate from a nominal ac
input service voltage
of
230
volts,
60
Hz, and can
also operate from a
+
152
volt
(70-cell)
de
battery
plant. The motor-alternators
are
rated
at
10KV
A,
16KV
A,
or
21KVA (MD). The
inverters
in
the
plant always operate from a +152 volt
(70-cell)
de
battery
plant
and
are
rated
at
16KV
A.
1.04
The
instructions
given in this section
are
based
on
the
following
circuit
schematic
drawings.
For
detailed
descriptions
of
circuit
operation,
refer
to
the
corresponding
circuit
descriptions.
SD-81149-01,
Iss
21B-L3
Carrier Telephone, 230
V
AC
Power Supply Circuit,
Page
6
2 Motor-Alternator-Automatic
Control, 505D Plants
SD-81152-01, Iss
23-Power
Control Circuit
For
L3
Carrier
Telephone,
0-4400
Volts, 60 Cycles,
Regulated
Current,
1.5 Amps, 505D &
521A
Plant-J86447
SD-81164-01
Iss
8-Regulator
Circuit,
Current-
Electronic
Type-J86262A
SD-81799-01
Iss
8-L3
Carrier Inverter Plant, 521A
Plant,
Regular
Supply Control
Circuit-J86854A
SD-81821-01,
Iss 3D-Combination505D/521A Plants,
Regular Application Schematic
SD-81831-01,
Iss
4AR-Inverter
Circuit
For
L3
Carrier,
Regulated
Semi-
conductor Type, 16KV
A,
230V,
PF
(0.8-1.0)
Lag,
Single-Phase,
60-Hz-KS-
19738
(
(

(
If
this
section is to be used
with
equipment
or
apparatus
that
is associated with earlier
or
later
issues
of
the
circuit schematic drawings, reference
should be made to the SDs and CDs to determine
the
extent
of the changes and the manner in which
the section may be affected.
1.05
The voltage
that
is applied to
the
L3
coaxial
cable is
determined
by
the
length
of
the
power section. A power section is the series loop
through the center conductor
of
two coaxial lines
with the primary windings ofthe auxiliary transformer
at
each
repeater
point
connected in
series
with
the center conductor
of
the two coaxial lines. The
voltage
that
is applied to the
L3
coaxial cable is
obtained by stepping up the output voltage
of
each
motor-alternator and automatically regulating the
stepped up output to maintain a constant alternating
current
for
the
coaxial lines.
The
approximate
constant
current
used on
the
coaxial lines is 1.5
amperes for a
PSI
system
or
1.6
amperes
for
a
PS2 system. The alternating
current
for a power
section
is
held
constant
by
the
two
variable
motor-driven
autotransformers
in
the
associated
PWR
CONT
(power
control)
bay.
One
of
the
autotransformers
is used for coarse
adjustments
and
the
other
autotransformer
is
used
for
fine
adjustments. The coarse-adjust autotransformer is
controlled
by
a voltage relay and the
±3
percent
cams
of
the
fine-adjust
autotransformer.
The
fine-adjust
autotransformer
is controlled
by
an
electronic-regulating circuit. Both the coarse-adjust
and fine-adjust autotransformers respond to voltage
drops
across
a
resistance
that
is in
series
with
the L3 coaxial lines.
1.06
Each
motor-alternator
in
the
combination
plant
consists
of
a
de
motor,
an
ac motor,
and a self-excited alternator mounted on a common
shaft. .The motor-alternator, under manual control,
is
started
and
brought
up to normal
speed
and
voltage limits by the de motor. The drive is then
transferred
manually to the ac motor for normal
operating conditions. When
the
alternator
is on
ac drive, the field
of
the
de
motor is connected to
the
battery
through
a high
resistance.
An ac
power failure or low voltage condition automatically
disconnects the ac power from the ac motor, applies
battery
to the de motor, and short-circuits the high
field resistance
causing
the de motor
to
operate
and provide alternator drive.
1.07
The regular and emergency motor-alternators
in
the
plant
are
driven
by
the
ac
motors
ISS
3, SECTION 167-676-301
under
normal
operating
conditions. A
voltage
transfer
control circuit causes the motor-alternator
drive to automatically
transfer
from the ac motors
to the de motors when the ac input voltage drops
below approximately 80 percent
of
nominal value.
When
the
ac
input
power
is
restored,
the
motor-alternators will automatically
transfer
from
the de motors back to the ac motors when the ac
input
voltage
has
been
at
least
90
percent
of
nominal value for approximately 1 minute.
If
the
motor-alternator fails to keep
the
output
voltage
about
225
volts, the voltage relays will cause the
motor-alternator to
transfer
to the de motor.
If
the output voltage from a
regular
motor-alternator
drops below
205
volts
for
more
than
112
second,
the voltage relays will cause the load to
transfer
from the
regular
motor-alternator to the emergency
motor-alternator.
1.08
The emergency motor-alternator is used
as
a common emergency motor-alternator for a
combination of from
one
to six regular motor-alternators
and inverters. Under normal operating conditons,
the emergency motor-alternator
runs
continuously
at
no load and will automatically replace any
regular
motor-alternator
or
inverter
that
fails, goes low in
supplying outputvoltage,
or
is removed from service
for maintenance.
1.09
If
the
motor-alternators in
the
plant
were
operating
on
the
de motors (due to
an
ac
power failure) and all
the
motor-alternators were
transferred
back to
the
ac
motors
at
the
same
time (ac power restored),
the
resulting load
surge
might reduce the ac input voltage to the ac motors
below the line monitor
transfer
point. This could
cause
the
motor-alternators to
transfer
back and
forth repeatedly.
To
prevent the ac input voltage
to
the
ac
motors
from
dropping
below
the
line
monitor
transfer
point,
an
alternator-sequencing
circuit restores the motor-alternators in the
plant
to
ac
drive
sequentially
on
an
individual
basis
following
an
ac
power
failure
(ac
power
now
restored). The emergency motor-alternator would
be the first unit to
transfer
back to ac drive.
1.10
The plantcontains an originating TRANSFER
CONTROL
bay
and
as
many
SUPL
(supplementary) TRANSFER CONTROL
bays
as
required. The originating TRANSFER CONTROL
bay contains
the
common control circuit
that
is
used to
automatically
transfer
the
load
from
a
faulty
regular
motor-alternator to
the
emergency
motor-alternator and also contains the circuits
for
Page
7

SECTION 167-676-301
checking
the
automatic
transfer
from ac to de drive.
Originating TRANSFER CONTROL bays and SUPL
TRANSFER
CONTROL
bays
can
contain
the
motor-alternator
controls
for
one
or
two
motor-alternators. Refer to Fig. 4 and Fig. 5 for
control
panel
illustrations
of
the
TRANSFER
CONTROL and SUPL TRANSFER CONTROL bays.
1.11
A NOR-ALT BYPASS switch is provided in
the
originating TRANSFER CONTROL bay
or
SUPL (supplementary) TRANSFER CONTROL
bay
for
each
of
the
regular
motor-alternators in
the plant. When the NOR-ALT BYPASS switch
is in
the
NOR position,
the
load is connected
to
the
regular
motor-alternator
output
through
this
switch. When the NOR-ALT BYPASS switch is in
the ALT BYPASS position, depending on the wiring
connections
of
the
plant,
the
load is
connected
0
~
LV
0
~
~
DC
MDT
START
l
AC
MOT
l
r-SURT
l TST-.r-MAM
RUN---.
STOP
All
FAIL
~NOR
0
~NOR
0
~MOR
0
RLS
PWR
S£RV
either to the
output
of
the
emergency
alternator
(standard)
or
directly to the ac input power
(MD).
1.12
There
is
a
START
CONTROL
or
EMG
START
CONTROL
bay
for
each
of
the
motor-alternators in
the
plant. This bay contains
the relays, contactors, and resistors for controlling
the
starting
and operation
of
the motor-alternators.
1.13 A
frequency
monitor
circuit
(ZH option,
SD-81149-01) may be provided in
the
plant
for
the motor-alternators to monitor
the
ac input
service frequency.
If
the
frequency monitor circuit
is provided and the ac input service frequency drifts
out of limits, the motor-alternators will automatically
transfer
from ac to
de
drive. When the frequency
transfer
occurs,
the
FF
ALM lamp, PWR TRNS
&
FA lamp, and office audible
and
visual alarms
are
activated. When the ac input service frequency
~
0
EV
ELY
~
~
0
OC
MOT
START
l
AC
MOT
l
r-START l
TST-----.
r-
MAN
RUN---..
STOP
All
FAIL
~·0
~lOR
0
~•oRO
RLS
~®f@@J@@l
~
FRI
PIR PIR
0
TRMS
TRNS
TST
HA
ACO
HLV
0
~NOR
0 @ 0 0
0
Page 8
YM
0
PH
I
FRt:Q
Ff
PH
2
RESET
ALM
PK
3
00
NOTE:
THE .CONTROL PANEL OF
THE"TRANSFER
CONTROL" BAY CONTAINS
THE
COMMON
CONTROLS AND THE CONTROLS
FOR
ONE REGULAR AND
ONE
EMERGENCY MOTOR-ALTERNATOR.
Fig.
4-Control
Panel
of
TRANSFER
CONTROL Bay
0
ES-529919
(
(

/
(
ISS
3,
SECTION 167-676-301
~
~
0 0
v
LV
v
LV
0 ®® ®® 0
DC
MOT
START
l
AC
MOT
l
DC
MOT
START
l
AC
NOTl
~START
l
TST,
r-liAN
RUN----,
STOP
ALT
FAIL
r-START
l
TST--,
r-MAN
RUN-,
STOP
ALT
fAll
~NoRO
~NOR
0
~NOR
0
~NORO
~NoRO
~NoRO
RLS
RlS
f@@J@@J@)@J
f@@f@@f@ij
0 0
0
0
NOTE:
THIS
CONTROL
PANEL
OF A
"SUPL
TRANSFER CONTROL" BAY
CONTAINS
THE
CONTROLS
FOR
TWO
REGULAR
MOTOR-ALTERNATORS.
TPA
550929
Fig.
5-Control
Panel
of
SUPL
TRANSFER
CONTROL Bay
returns
to
normal,
the
FREQ
RESET
key
must
be
depressed
to
allow
the
motor-alternators
to
return
to ac drive.
Note:
•The
YB
option
has
been developed
to
provide a frequency monitor circuit with
automatic
reset
for
use
at
unattended
sites
or
where
line
frequency
transients
cause
frequent
transfers
of
the
plant
to de drive.
The automatic
reset
feature enables the plant
to
return
to ac drive without attention from
operating personnel. The
YD
option, which
may be added to the
YB
option, provides
an
additional feature which disables
the
frequency
monitor
prior
to
and
during
return
of
the
plant to ac drive.
YD
option is intended for
use
at
sites
using
ac
sources
which
cannot
accept
the
505D plant motor-alternators load
without reacting in a manner
that
affects
the
frequency monitor circuit
.•
1.14
An
output
voltage limiter circuit
(ZM
and
ZN
or
ZQ
options,
SD-81149-01)
may
be
provided in the plant to limit the motor-alternator
output
voltage
to
a
value
between
240
and
250
volts when
the
motor-alternators
are
driven
by
the unregulated
de
motors.
If
the
output
voltage
limiter circuit is provided in
the
plant,
the
16KVA,
KS-15994 L2 motor-alternators use
the
ZM
and
ZQ
options and the 16KV
A,
KS-15626
L2
motor-alternators
(MD)
use the
ZM
an9 ZN options.
If
the
ac
output
voltage from a de
motor
driven
motor-alternator
increases
to
240 volts,
the
voltage limiter circuit
will
regulate
the
alternator
field coil
current
to
hold
the
output voltage from
the
motor-alternator
between
240
and
250
volts
or
drive
the
output
voltage
down
toward
230
volts.
If
the
output
voltage from the motor-alternator is driven down
toward 230 volts,
the
output
voltage
may
stabilize
at
some
voltage
less
than
240 volts. When
the
motor-alternator
output
increases to
the
240 volts,
the
OVERVOLT lamp on
the
power
plant
lights
and
an
office visual and audible alarm is activated.
After the ac outputvoltage from the motor-alternator
is
restored
to
normal,
the
RESET
OVERVOLT
(81)
key
must
be
depressed
to
extinguish
the
OVERVOLT lamp and
the
office visual and audible
alarms.
Page 9

SECTION
167-676-301
When the output voltage limiter circuit is provided
in the plant, a CLAMP DISABLE
(S1)
switch [may
be called LIMITER DISABLE
(S1)
switch] is included.
The
switch
can
be
used
to
bypass
the
output
voltage limiter circuit.
Under
normal
operating
conditions the
CLAMP
DISABLE (LIMITER
DISABLE)
(S1)
switch should be in the open position.
1.15
An overspeed shutdown circuit
(ZT
option,
SD-81149-01)
may
be
provided
in
the
combination plant for
the
motor-alternators. The
overspeed shutdown circuit is used to monitor the
frequency
of
the nominal 230-volt ac outputs from
the
motor-alternators.
If
the
frequency
of
the
230-volt ac output from a motor-alternator increases
(motor speed increases), a point will be reached
where
the
associated
OS1
relay will de-energize.
When the
OS1
relay de-energizes, the motor-alternator
will
shut
down,
the
OS
FAIL
and
AC MOT
&
ALT FAIL lamps on the plant light, and the office
visual
and
audible
alarms
are
activated.
After
the
motor-alternator
has
shut
down
due
to
a
de-energized OS1 relay,
the
NOR-STOP
key
on
the TRANSFER CONTROL bay must be operated
to the STOP position to re-energize the
OS1
relay.
1.16 Each inverter
in
the combination plant
must
be
started
manually by the inverter INPUT
(S501) switch. The load on
an
inverter
can be
manually disconnected from
the
inverter
by
the
OUTPUT
(S502)
switch. The CONTROL OFF switch
on
the
REGULAR PLANT CONTROL panel can
be used to disable
the
automatic control circuits
of
the inverter. Switches
are
provided for testing
the
alarm
circuits
of
the
inverter.
Alarms
are
provided in
the
inverter
to indicate fuse, circuit
breaker,
and
monitor
failures.
Refer
to Fig. 6
for
an illustration
of
the
KS-19738
inverter
and
Fig. 7
for
a partial view
of
a 521A power
plant
lineup.
Refer
to Fig. 8 for a photograph
of
the
REGULAR PLANT CONTROL panel.
1.17 The
plant
contains PWR CONT
bays
that
are
connected to the
L3
coaxial lines. Each
regular
motor-alternator
or
inverter will normally
power two PWR CONT bays. The required line
current
for
the
transmit
and receive lines
of
the
PWR CONT bay should be specifed on cards
or
tape
and
posted
directly above each
of
the
two
associated ammeters on the bay. The PWR CONT
bay is equipped with manual controls
that
allow
the
line
currents
to
be
raised
or
lowered
for
performing
tests
and maintenance work. Refer to
Fig. 9
for
an
illustration
of
the PWR CONT bay
Page
10
and
to Fig.
10
for
a control panel illustration
of
this bay.
1.18
•The
inverter checks in this section
are
to
be
used
when
the
inverter
is used in
the
505D/521A power plant.
For
inverter checks when
the inverter is used in a dedicated application, see
Section 161-233-301.•
1.19
Designations
used
in
this
plant
(controls,
etc.)
that
are
preceded
by
E
refer
to
the
emergency motor-alternator.
2.
LIST
OF
TOOLS
AND
TEST
APPARATUS
CODE
OR
SPEC
NO.
TOOLS
KS-6278
KS-6320
KS-19168
L1
265C
411C
R-1102
W1AY
720A
141
1W13A
DESCRIPTION
Connecting clips
(4
reqd)
Orange Stick
Cord, 6
Feet
Long,
14
Gauge
or
Equivalent, Equipped With Hubbell
Cap No. 5666
Burnisher
Test Picks
(2
reqd)
Spudger
Cord,
8-112
Feet
Long, Equipped
With two 360A Tools
(2
reqd)
•Battery
Pick-up Tool•
893
Cord, 3
Feet
Long, Equipped
With two 360A Tools
185-JO Cable, 3
Feet
Long,
(2
reqd)
3-Inch C Screwdriver
Connecting Jumpers
Relay Blocks
Insulating Tools
(
(

(
( OUTPUT (S502) SWITCH
CODE OR
SPEC
NO.
KS-3008
RELAY
COVER
OFFICE SERVICE
CIRCUIT BREAKERS
Stopwatch
ISS
3,
SECTION
167-676-301
!NV TRFR EARLY
WRN
CONTROL.
PANEL.
MONITOR
MONITOR
J86854C,l..l
J86854D,
l..l
J86854E,l..l
CABINET ALARM LAMP
~I
~DS502
LAMP
~f"INPUT
(S501)
SWITCH
F===~====~======~==~
DESCRIPTION
J86854A
INVERTER
(16 K\IA)
TRANSFER
PANEl..
J86854G,
Ll
OR
L.2
Fig.
6-KS-19738
Inverter
CODE OR
SPEC
NO
SHUT
OWN
MONITOR
J86854F,
L1
TRANSFER
NORMAL.
INVERTER
BY
PASS (56) SWITCH
TPA
563756
DESCRIPTION
KS-14510
Volt-Ohm-Milliammeter
*Variac,
W5HMT,
General Radio
Co., 240-Volt, 2-Ampere, Single
Phase,
50-
to 60-Hz
Input-0-
to
280-Volt Output
Weston Model622
AC-DC
Thermo
Voltmeter(300/150175/30/15)(See
Note
1)
Weston
Model
904
AC
Voltmeter,
True
RMS
(300/150)
Hewlett-Packard 5221A Electronic
Counter
Hewlett-Packard
202C
or
200CD
Oscillator
Tachometer, Boulin
Instrument
Corp., Type A or
No.
5
Tektronix
545B
Oscilloscope With
CA-Type Adapter
or
Equivalent
(Not
required
for
normal
maintenance)
*Registered trademark
of
the General Radio
Co.
Note
1:
•A
digital multimeter such as the
Hickok
3420
is
a preferable substitute for these
meters
.•
Note
2:
Equivalent may be substituted.
Page
11

SECTION 167-676-301
11-
------
-~
1!~===
:-:
~T:
::::
~~·lttvi~~;=:
r
;2~
j
~
:;
•
n••
"
~h
. •
'
...•
::::::
:
..
::::
....
:::::::··==::::::
••.
::::::::
:······==::::····
.......
:::::••..
:.=·.·
·.·.::.:.:.:.:.:.·.·.·.·.==.=.
:::;::::::::::::::
;~m~~mss~~m
m~mmmnn
;:,:.:.::::.:.:.:.::::=.:
••
:
••••
:::··
••••
::
:·
-• • :::::::=::::::·.·=
;::::..::;::::::::::
··············
..
...........
:!:::
:::::::::::::::::
....
::::::::::::;;
Fig.
7-Partial
View
of
521A
Power
Plant
Lineup-Cutaway
View
Shows a KS-19738 Regular
Inverter
3. OPERATION
A.
PWR CONT
Bay
Power
Turnup Procedure
3.01
To
turn
the power up on the associated
L3
lines
at
the
PWR
CONT bay,
proceed
as
follows.
Warning:
Before
turning
power
up
on
the
associated
L3
lines,
verify
that
men
are
not
working
on
the
associated
Jines
and
that
the
TURN
DOWN
lamp
on
the
PWR
CONT
bay
is
lighted
to
prevent
personnel
injuries
from
occurring.
Caution:
If
there
is
an
equalizing
repeater
or
a
remote
terminal
repeater
(fed
on
a
constant
basis)
in
the
power
section,
do
not
turn
the
power
up
until
the
power
has
Page 12
been
completely
turned
down
for
at
least
5
minutes.
At
these
locations,
a
plate
voltage
limiter
circuit
provides
a
load
on
the
plate
power
supply
to
limit
the
plate
voltage
when
the
power
is
being
turne
d
up
on
the
associated
L3
lines.
If
the
power
is
turned
down
on
the
L3
Jines
and
is
then
turned
back
up
before
the
minimum
5-minute
interval,
the
associated
amplifiers
and
regulators
will
be
subjected
to
excess
voltages.
(1)
Verify
that
all maintenance on the associated
L3
line or PWR CONT bay has been completed.
(2)
Operate
the
ACO key to
release
the
VSD
relay lock-up circuit which will close the
SS
contactor.

ISS
3, SECTION 167-676-301
REGUlAR
PLANT
C
ONTRO
L
,,
" .
'
I
O!J
P"llt
'tOl' A
G£
Fig
. 8- J86854C Control Panel
of
KS-19738 Regular Inverter
Note:
Failure to operate the
ACO
key when
the
audible
alarm
is
activated
will
prevent
the power
turnup
because the VSD relay circuit
will be locked up.
Requirement:
The audible
alarm
is
silenced.
(3)
Verify
that
the POWER CONTROL FAILURE
and TURNDOWN lamps
are
lighted on the
PWR CONT bay.
(4)
Verify
that
the
following
controls
on
the
PWR
CO
T bay
are
positioned
as
indicated.
COARSE CONTROL MANUAL-NOR AUTO
key to MANUAL
COARSE CONTROL RAISE-NOR-LOWER
key to NOR
FINE
CONTROL NOR-OFF switch to
OFF
(5)
Connect
the
PWR cable terminal plugs
that
are
associated
with
the
power
loop to
the
input
of the power
separation
filters.
(6)
Install
the
cover
that
is
used
to cover
the
PWR
cable
terminal
plugs
on
the
rear
of
the
power separation filter panel.
(7)
Install
the
COAXIAL
LINE
(A)
fuse
in
its
respective fuse holder.
Page 13

SECTION
167-676-301
I
lol
I I I I
·®~@·
I
I
HIGH
VOLTAGE
TRANSFORMER
CONTROL
PANELS
Fig.
9-PWR
CONT Bay
Page 14
(8)
Install the F3 and F4 fuses in their respective
fuse holders
if
they
were removed
during
the power turndown procedure.
(9) Position
the
warning
tag
on the PWR CONT
bay so
that
the "CABLE IN SERVICE" side
is displayed.
(10)
Verify
that
the UNREG-REG toggle switch
for the
AC
VOLTS
meter
is in
the
REG
position.
(11)
Operate
the
COARSE CONTROL RAISE·
NOR-LOWER key
to
the RAISE position
for
•2
seconds and then to NOR for approximately
SO
seconds.. Repeat this procedure until both
of the line current meters indicate approximately
1 ampere. Wait
45
seconds and then continue
with
(12).
Note: By gradually increasing the current,
the plate voltages
are
limited to safe values
while the electron tube heaters in the amplifiers
and regulators in the power loop are warming
up.
(12)
Operate
the
COARSE CONTROL RAISE-
NOR-LOWER key to
the
RAISE position
for
t2
seconds and then to NOR for approximately
30
seconds..
Repeat this procedure until
the
AC
VOLTS
meter indicates the nominal regulated
voltage (usually
230
volts).
Note: Allow the line voltage and current
to
stabilize and then continue with
(13).
(13)
Observe the indication on
the
PLT CUR
meter.
Requirement: The PLT
CUR
meter indicates
200
milliamperes.
Note:
If
the
requirement
in (13) is met,
proceed to (15).
If
the
requirement
is
not
met, continue with
(14).
(14)
Adjust
the
ADJ CUR potentiometer until
the
PLT
CUR
meter
indicates
200
milliamperes.
(15)
Observe
the
indications on
the
two line
current meters
of
the PWR CONT bay.
(
(

(
ODD
LINE
CURRENT
PLT
CUH
~
A
A&)R
JI@[email protected]@J7@
J2@[email protected]@J8@
METER----~-----J
•
FINE
CONTROL
NOR-
OFF
SWITCH
COARSE
CONTROL
RELAY
*
3%
VR
ADJ
®
-A
1/2
A
-A
1/2
A
VR
@@)@@@@
-A
112
A
AC
VOLTS
UNREG;!
SWITCH
DETERMINES
If
AC
VOLT/
METER
INDICATES UNREGULATED
OR
REGULATED INPUT
VOLTAGE
ISS
3,
SECTION
167-676-301
0
[6]
(@)
D
-A
112
A
VA
0
0
INPUT VOLTMETER
EVEN L.INE
CURRENT
METER
ACO
KEY
FUSE
MOUNTINGS
FUSE
PANEL
FUSE
BLOCK
ALARM
RELAY
*
5'!'.
TPA
505431
Fig. 10--Control Panel of PWR CONT Bay
Page
15

SECTION
167-676-301
Requirement:
The
line
current
meters
indicate the required line current.
Note
1:
The required line
current
should be
posted directly above the associated line current
meters.
Note
2:
If
the
line
current
indicated on
the
line
current
meters is
not
within
+0.01
ampere
of
the
posted
line
current
value,
trouble
conditions
may
be
present
in
the
associated
amplifiers and regulators
of
the power loop.
(16)
Verify
that
the
armatures
of
the VR and
VA
relays
are
midway
between
the
low
and high contacts.
(17)
Operate
the
COARSE CONTROL MAN-
UAL-NOR AUTO key to
the
NOR AUTO
position.
Requirement:
The
COARSE
CONTROL
MANUAL lamp extinguishes.
(18) Operate
the
FINE
CONTROL NOR-OFF
switch to
the
NOR position.
Requirement:
The
FINE
CONTROL
OFF
lamp
extinguishes.
After
a
time
delay
of
approximately 3 seconds,
the
ELECTRONIC
REGULATOR
FAILURE
lamp on
the
PWR
CONT bay extinguishes.
Note:
If
the
ELECTRONIC REGULATOR
FAlLURE lamp extinguishes, proceed to
(33).
If
the ELECTRONIC REGULATOR FAILURE
lamp remains lighted,
the
T2 autotransformer
is not in
the
midposition.
To
adjust
the
T2
autotransformer
to
the
midposition
and
to
extinguish
the
ELECTRONIC REGULATOR
FAILURE lamp, continue with
(19).
(19)
Operate
the
FINE
CONTROL NOR-OFF
switch to
the
OFF position.
Requirement:
The
FINE
CONTROL OFF
lamp lights.
(20)
Operate
the
COARSE CONTROL MAN-
UAL-NOR AUTO
key
to
the
MANUAL
position.
Requirement:
The
COARSE
CONTROL
MANUAL lamp lights.
Page 16
(21) Remove
the
front
cover
from
the
PWR
CONT
bay
that
is directly above the PLT
CUR (plate current) meter.
(22)
Loosen
the
wingnut
that
holds
the
T2
autotransformer in place.
(23) Pull
the
T2
autotransformer
outward
to
make
the
unit accessible.
(24)
Turn
the
knob
of
the
T2
autotransformer
until
the
pointer is in
the
midposition.
(25)
Push
the
T2
autotransformer
back
into
the PWR CONT bay and tighten the wingnut
that
holds the
autotransformer
in place. Verify
that
the autotransformer will
not
move.
(26)
Install
the
cover
that
was removed from
above
the
PLT CUR meter.
(27)
Observe
the
indication on
the
AC
VOLTS
meter.
Requirement:
The
AC
VOLTS meter should
indicate
the
nominal regulated voltage (usually
230 volts).
Note:
If
the
requirement
in (27) is
met,
proceed
to
(29).
If
the
requirement
is
not
met, continue with
(28).
(28)
Operate
the
COARSE CONTROL RAISE-
NOR-LOWER key to
the
necessary RAISE
or
LOWER position
for
1 second
and
then
to
NOR for approximately
15
seconds until
the
AC
VOLTS
meter
indicates
the
nominal
regulated
voltage (usually
230
volts). Repeat this procedure
until the
AC
VOLTS
meter
indicates
the
required
regulated voltage.
Note:
Allow the line voltage and
current
to
stabilize and then continue with
(29).
(29) Observe
the
indication on
the
PLT CUR
meter.
Requirement:
The PLT CUR meter indicates
200
milliamperes.
Note:
If
the
requirement
in (29) is
met,
proceed
to
(31).
If
the
requirement
is
not
met, continue with
(30).
(
(

(30)
Adjust
the
ADJ
CUR potentiometer until
the
PLT
CUR
meter
indicates
200
milliamperes.
(31)
Verify
that
the
armatures
of
the
VR
and
VA
relays
are
midway
between
the
low
and
high contacts.
(32)
Repeat
steps
(17)
and
(18).
(33)
Observe
the
indications on
the
two
line
current
meters (even
and
odd L3 lines)
of
the
PWR CONT bay.
Requirement:
The difference
between
the
two line
current
meter
indications should be
less
than
50
milliamperes for power sections
that
contain
15
or
less repeaters. The difference
between the two line
current
meter
indications
should be less
than
75 milliamperes
for
power
sections with
16
or
more repeaters.
Note:
If
the
requirement in
(33)
is
not
met,
trouble
conditions
may
be
present
in
the
associated
amplifiers
and
regulators
of
the
associated L3 lines
or
there
may be a
short
or
open in the associated L3 lines.
If
trouble
conditions
are
present,
turn
the power down
on the associated
L3
lines in accordance with
3.02, clear
the
troubles, and
then
repeat
the
entire power turn-up procedure beginning with
step
(1).
(34)
Observe
the
indications on
the
associated
L3 line pilot indicators.
Requirement:
The associated L3 line pilot
indicators indicate 0 +0.1dB.
(35)
Clear all associated
L3
line pilot alarms in
both directions of transmission.
Note:
If
the
associated L3 line pilot alarms
cannot
be
cleared,
measure
the
alarms
to
determine
their
locations
and
perform
the
necessary maintenance to clear
the
alarms.
(36)
Remove
the
J68839A (39A)
or
J68839B
(39B)
thermistor
control
set
from
the
associated L3 line and have
the
terminal switching
center
at
the
opposite end
of
the
power
loop
remove
their
thermistor
control
set
from
the
same L3 line.
ISS
3,
SECTION 167-676-301
(37)
If
no maintenance is to be performed
that
will require
the
use
of
the
protection lines,
restore the protection lines to normal operation.
(See Sections 359-010-125
and
359-075-301.) Notify
the
switching
centers
in
all
directions
of
transmission
that
the
protection lines have been
restored to normal operation.
Note
1:
The
protection
lines
should
be
restored to normal operation immediately
after
the power has been
turned
up so
that
emergency
transfers
to
the
protection lines can occur if
necessary.
Note
2:
After
restoring
the
associated
L3
power
loop
to
normal
operation,
it
may
be
necessary
to
equalize
the
power
loop
due
to
excessive line
current
variations.
Refer
to
the
appropriate
Bell
System
Practices
for
information on line equalization.
(38) Complete
the
restoration
portion
of
the
associated power disconnect-restoration card
or
cards (Form P-1643)
per
local instructions.
B.
PWR CONT Bay Power Turndown Procedure
3.02
To
turn
the
power
down on
the
associated
L3 lines
at
the
PWR
CONT bay,
proceed
as follows.
Caution:
Before
turning
the
power
down
on
the
associated
L3
lines,
notify
the
terminal
switching
centers
in
all
directions
of
transmission
of
the
forthcoming
actions.
Verify
that
no
associated
L3
switching
routines
are
to
be
performed;
verify
that
no
associated
repeater
or
line
maintenance
is
to
be
performed;
and
verify
that
no
other
associated
JYJUtine
checks
or
maintenance
are
to
be
performed
that
will
require
the
use
of
the
L3
protection
lines.
Verify
that
the
associated
L3
protection
lines
are
available
for
service.
Perform
the
necessary
procedures
to
remove
all
service
from
the
associated
L3
lines
(odd
and
even)
that
make
up
the
power
loop
served
by
the
PWR
CONT
bay.
(1)
Notify
the
terminal switching centers in all
directions
of
transmission
that
the
power is
to be
turned
down on a L3 power loop.
Page 17

SECTION 167-676-301
(2)
If
the
power
is
to
be
turned
down on a
regular
power loop,
transfer
the service
that
is normally on
the
regular
power loop over to
the
protection power loop.
If
the
power is to
be
turned
down on a
protection
power
loop,
and
the
protection power loop is carrying service,
transfer
the service on
the
protection power loop
back
to
the
regular
power loop
that
normally
carries
the
service. (See Sections 359-010-125
and 359-075-301.)
Note:
When
the
OUT SERV (green) lamp
on
the
associated REC
L3
line bay is lighted,
continue with
(3).
(3)
Connect
the
J68839A
(39A)
or
J68839B
(39B)
thermistor control
set
to
the
associated
L3
line and have
the
terminal switching
center
at
the
opposite end of
the
power loop
do
the
same.
The
thermistor
control
sets
will
protect
the
associated amplifiers and regulators in
the
main
switching stations.
Note:
Do
not disturb the
L3
line potentiometers.
(4)
Operate
the
FINE
CONTROL
NOR-OFF
switch to
the
OFF position.
Requirement:
The
FINE
CONTROL
OFF
lamp lights.
(5)
Operatethe
COARSE
CONTROL
MANUAirNOR
AUTO key to the MANUAL position.
Requirement:
The
COARSE
CONTROL
MANUAL lamp lights.
(6)
Verify
that
the UNREG-REG toggle switch
for
the
AC
VOLTS
meter
is in
the
REG
position.
(7)
Operate
the
COARSE
CONTROL
RAISE-NOR-LOWER
key
to
the
LOWER
position
•and
hold• until
the
AC
VOLTS
meter
on
the
bay indicates zero.
Requirement:
An audible alarm is activated
and the POWER CONTROL FAILURE lamp
lights
shortly
after
the
power
turndown
procedure is started. The TURNDOWN lamp
lights when the
AC
VOLTS meter on
the
bay
indicates 0 volts.
(8)
Depress the
ACO
key.
Page 18
Requirement:
The audible alarm is silenced.
(9)
Remove
the
COAXIAL
LINE
(A)
fuse from
its respective fuse holder in
the
PWR CONT
bay.
Note:
All power has now been removed from
the associated L3 power loop.
(10)
If
maintenance is to be performed on
the
PWR CONT bay, remove
the
F3 and F4
fuses from their respective fuse holders.
(11)
If
maintenance is to be performed on
the
coaxial cable, position
the
warning
tag
on
the PWR CONT bay so
that
the "MEN WORKING
ON CABLE" side is displayed.
(12)
Fill
out
the
disconnect portion
of
a power
disconnect-restoration
card
(Form P-1643)
for
each
party
or
crew
requesting
the
power
turndown. Place the cards in the ticket holder
directly below
the
warning
plate
on
the
PWR
CONT bay.
(13)
Verify
that
the
green
CA
TERM lamps on
the cable terminal panels for
the
associated
power loop
are
lighted.
Note:
The cable terminal panels
are
located
at
the
top
rear
of
the
line
bays
and
are
associated
with
the
power
separation
filter
panels.
(14)
Warning:
Be
certain
to
disconnect
the
PWR
cable
terminal
plugs
from
the
correct
line
bay
associated
with
the
power
loop
to
prevent
personnel
injuries
from
occurring.
(15)
Disconnect the PWR cable terminal plugs
that
are
associated
with
the
power
loop
from the input of the power separation filters.
Note:
The
PWR
cable
terminal
plugs
are
accessible
by
removing
the
panel
cover on
the
rear
of
the power separation filter panel.
C. Transferring Load From Regular
Motor-Alternator
to Emergency
Motor-Alternator
3.03
To
transfer
the
load
from
a
regular
motor-alternator
to
the
emergency
motor-alternator, proceed
as
follows.
(
(

Caution
1:
Load
transfers
should
be
kept
to
a
minimum
to
reduce
the
possible
switching
transients
that
might
appear
on
the
associated
L3
lines.
Caution
2:
Return
the
load
to
the
regular
motor-alternator
as
soon
as
possible
to
enable
the
emergency
motor-alternator
to
be
used
for
automatic
transfers
should
a
regular
motor-alternator
or
inverter
fail.
(1)
Verify
that
the
AMPS
meter
on
the
EMG
START CONTROL bay indicates zero.
(2)
Warning:
Do
not
touch
exposed
metal
parts
when
connecting
or
disconnecting
an
external
voltmeter
across
the
terminals
of
the
panel
voltmeter
on
the
EMG
START
CONTROL
bay
as
hazardous
voltages
are
present.
Connect the Weston Model
904
voltmeter, connected
for
the
300-volt scale,
to
the
Hubbell receptacle
(ZR
option) on
the
EMG START CONTROL bay.
If
the Hubbell receptacle
is
not provided
but
test
jacks have been locally wired in for
the
connection
of
an
external voltmeter, connect
the
Weston Model
904
voltmeter
to
the
test
jacks
on
the
bay.
If
the
Hubbell
receptacle
is
not
provided
and
test
jacks
have
not
been
locally
wired
in,
observe
warning
and
connect
the
Weston
Model
904
voltmeter across the terminals
of
the
panel voltmeter
on
the
bay.
Requirement:
The
Weston
Model
904
voltmeter should indicate the nominal no-load
voltage
as
specified by local instructions.
Note:
If
the
requirement
in (2) is
met,
proceed to
(4).
If
the requirement is not met,
continue with
(3).
(3)
Adjust the ALT VOLTS ADJ potentiometer
on
the
EMG START CONTROL
bay
until
the
Weston Model 904 voltmeter indicates
the
nominal no-load
voltage
as
specified
by
local
instructions.
(4)
Operate
the
START & MAN RUN key on
the
TRANSFER
CONTROL
or
SUPL
TRANSFER
CONTROL
bay
for
the
regular
motor-alternator
to
the
START & MAN RUN
position.
ISS
3, SECTION 167-676-301
Requirement:
The
START & MAN
RUN
lamp
lights
and
the
load
transfers
to
the
emergency motor-alternator.
(5)
Verify
that
the
AMPS
meter
on
the
EMG
START CONTROL bay indicates
the
nominal
output
current.
(6)
Observe the indication on
the
Weston Model
904 voltmeter
that
is connected to the EMG
START CONTROL bay.
Requirement:
The
Weston
Model
904
voltmeter indicates
the
nominal
output
voltage
of
230
+3
volts.
Note:
If
the
requirement
in (6) is
met,
proceed to
(8).
If
the
requirement is not met,
proceed to
(7).
(7)
Adjust
the
ALT VOLTS ADJ potentiometer
on
the
EMG START CONTROL
bay
until
the
Weston Model 904
voltmeter
indicates 230
volts.
(8)
Disconnect the Weston Model 904 voltmeter
from
the
EMG START CONTROL bay.
D. Transferring Load From Emergency
Motor-Alternator
Back
to
Regular
Motor-Alternator
3.04 To
transfer
the
load from
the
emergency
motor-alternator
back
to
the
regular
motor-alternator, proceed
as
follows.
Warning:
Do
not
touch
exposed
metal
parts
when
connecting
or
disconnecting
an
external
voltmeter
across
the
terminals
of
the
panel
voltmeter
on
the
START
CONTROL
bay
as
hazardous
voltages
are
present.
Caution:
Load
transfers
should
be
kept
to
a
minimum
to
reduce
the
possible
switching
transients
that
might
appear
on
the
associated
L3
Jines.
(1)
Connect
the
Weston
Model 904 voltmeter,
connected
for
the
300-volt
scale,
to
the
Hubbell receptacle (ZR option) on
the
START
CONTROL bay for the
regular
motor-alternator.
If
the
Hubbell
receptacle
is
not
provided
but
test
jacks
have
been
locally
wired
in
for
the
connection of an external voltmeter, connect the
Page
19

SECTION
167-676-301
Weston
Model 904
voltmeter
to
the
test
jacks
on
the
bay.
If
the
Hubbell
receptacle
is
not
provided
and
test
jacks
have
not
been
locally
wired in, observe warning and connect the Weston
Model 904 voltmeter across the terminals
of
the
panel voltmeter on
the
bay.
Requirement:
The
Weston
Model
904
voltmeter should indicate the nominal no load
voltage
as
specified by local instructions.
Note:
If
the
requirement
in
(1)
is
met,
proceed to
(3).
If
the
requirement
is
not
met,
continue with
(2).
(2)
Adjust the ALT VOLTS ADJ potentiometer
on
the
START
CONTROL
bay
until
the
Weston Model 904 voltmeter indicates the nominal
no-load voltage
as
specified by local instructions.
(3)
Operate
the
START & MAN RUN key on
the
TRANSFER
CONTROL
or
SUPL
TRANSFER
CONTROL
bay
for
the
regular
motor-alternator to the NOR position.
Requirement:
The
START & MAN RUN
lamp extinguishes and
the
load
transfers
back
to the
regular
motor-alternator.
(4)
Verify
that
the AMPS
meter
on the START
CONTROL bay for theregular motor-alternator
indicates
the
nominal
output
current.
(5)
Observe the indication on the Weston Model
904
voltmeter
that
is
connected
to
the
START CONTROL bay.
Requirement:
The
Weston
Model
904
voltmeter indicates the nominal
output
voltage
of
230
+3
volts.
Note:
If
the
requirement
in (5) is
met,
proceed to
(7).
If
the requirement
is
not
met,
continue with
(6).
(6}
Adjust the ALT VOLTS ADJ potentiometer
on
the
associated
START CONTROL
bay
until the Weston Model
904
voltmeter indicates
230
volts.
(7)
Disconnect the Weston Model
904
voltmeter
from the START CONTROL bay.
Page
20
E.
Removing
Motor-Alternator
From Service
3.05
To remove a motor-alternator from service,
proceed
as
follows.
Caution
1:
Operating
the
NOR-ALT
BY-
PASS
switch
on
a
regular
motor-alternator
to
the
ALT
BYPASS
position
may
cause
the
service
to
be
interrupted
on
the
L3
lines
associated
with
the
motor-alternator.
Caution
2:
Restore
the
motor-alternator
to
service
as
soon
as
possible
to
enable
the
emergency
motor-alternator
to
be
used
for
automatic
transfers
should
a
regular
motor-alternator
or
inverter
fail.
(1)
If
the motor-alternator to be removed from
service
is
supplying
power
to
the
load,
transfer
the
load from
the
motor-alternator
to
the associated emergency orregularmotor-alternator
in
accordance with 3.03
or
3.04.
(2)
Operate the
DC
MOT
START & TST-NOR-RLS
key on
the
TRANSFER CONTROL or SUPL
TRANSFER CONTROL
bay
for
the
associated
motor-alternator
which is
to
be removed
from
service to the DC MOT START & TST position.
Requirement:
The DC MOT START & TST
lamp lights and
the
motor-alternator
transfers
to
de
drive
(AR
relay
inside
of
associated
EMG START CONTROL or START CONTROL
bay should close).
(3)
Operate the STOP-NOR key on the TRANSFER
CONTROL or SUPL TRANSFER CONTROL
bay
for
the
associated
motor-alternator
to
the
STOP position.
Requirement:
The
motor-alternator
shuts
down
as
indicated
by
the
slowly
decreasing
indication
on
the
associated
EMG
START
CONTROL or START CONTROL bay voltmeter.
If
the
plant
is
equipped
with
an
overspeed
shutdown
circuit
(ZT option)
and
the
Class
A change in SD-81149-01,
Issue
25A has been
incorporated into
the
plant,
the
AC MOT &
ALT FAIL lamp should light.
Note:
Wait until
the
VOLTS
meter
on
the
associated EMG START CONTROL
or
START
CONTROL
bay
indicates zero before continuing
with
(4).
(
(
This manual suits for next models
1
Popular Inverter manuals by other brands
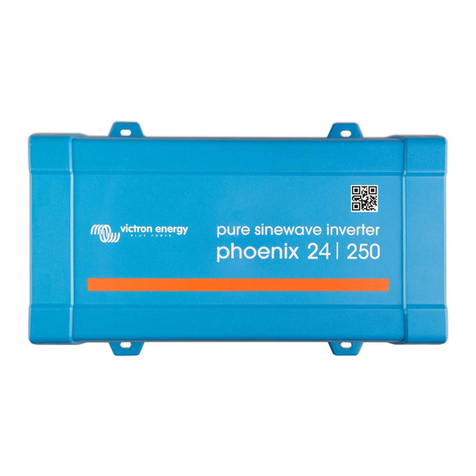
Victron energy
Victron energy Phoenix 12/250 manual
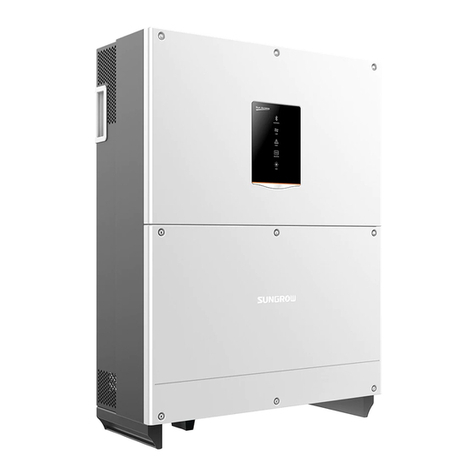
Sungrow
Sungrow SG125HV user manual

Xantrex
Xantrex PV-45208 Operation and maintenance manual

Growatt
Growatt MID 17-33KTL3-X Installation & operation manual

Mitsubishi Electric
Mitsubishi Electric FR-E720-0.1KNC instruction manual
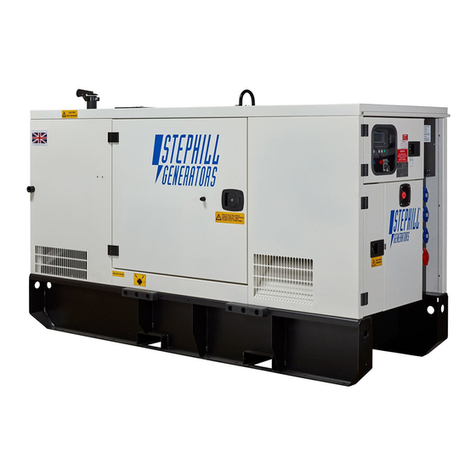
Stephill
Stephill SSDP30 Handbook