BERG KOMPBERG BKB22 TWIN Operating instructions

OperatingandMaintenanceManual
KOMPBERGBKB22TWIN
BOOSTERS

Ladies and Gentlemen,
We heartily welcome you among our valued Customers and thank you for your trust to purchase an
BERG Kompressoren GmbHs.
We are sure you will be fully satisfied with both the choice you have made and the cooperation you
started with us. Our compressors are machines of top quality, which is the guarantee for a long years
and reliable performance.
Our sales and service staff is available to answer all your queries regarding the installation and
operation of your compressor. You are also encouraged to use our warranty and post-warranty
technical service.

1.
Important notes .....................................................................................................
4
1.1.
Applications ................................................................................................................
4
1.2.
Operation ....................................................................................................................
4
1.3.
Other remarks and instructions ...................................................................................
4
2.
Operating safety rules ...........................................................................................
4
2.1.
Basic requirements for safe transport and positioning of the boosters ........................
4
2.2.
Operating safety requirements ....................................................................................
5
2.3.
Other hazards .............................................................................................................
5
2.4.
Explanation of symbols ...............................................................................................
6
3.
Setting ..................................................................................................................
6
3.1.
Room requirement ......................................................................................................
6
3.2.
Power supply system requirement ..............................................................................
6
3.3.
Compressed air connection ........................................................................................
6
3.4.
Compressed air treatment ..........................................................................................
7
4.
Technical description ............................................................................................
7
4.1.
Applications ................................................................................................................
7
4.2.
Main components .......................................................................................................
7
4.3. The compressor ..........................................................................................................
7
4.4.
Electric motor ..............................................................................................................
8
4.5.
End cooler ..................................................................................................................
8
4.6.
Booster compressor frame ..........................................................................................
8
4.7.
Control and protection equipment ...............................................................................
9
5. Technical data ....................................................................................................
10
6.
Operating description ..........................................................................................
10
6.1. Air circuit ...................................................................................................................
10
6.2. Lubrication system ....................................................................................................
10
6.3. Oil pressure control ...................................................................................................
11
7.
Unit operation and maintenance .........................................................................
12
8.
Periodic maintenance and servicing ...................................................................
13
9.
Procedure for important service operations ........................................................
13
9.1. Oil filter replacement .................................................................................................
13
9.2. Vent cartridge replacement (fig. 174-22-000) ............................................................
14
9.3.
Check valve cartridge replacement (563-38-000) ......................................................
14
9.4. Oil change ................................................................................................................
15
9.5. V-belts tension ..........................................................................................................
15
10. Troubleshooting ................................................................................................
16
11. Consumables ....................................................................................................
16

1. Important notes
1.1. Applications
The compressor is intended for compressing air only. Its use to compress other gases
requires prior agreement with machine manufacturer or vendor. Such agreement must be
made in writing. The compressor may not be used for any purpose other than specified.
1.2. Operation
While operating the compressor:
-Observe the instructions provided in the Manual and Warranty Book.
-Technical and operating checks should be performed by the manufacturer or
authorised service, using the manufacturer’s parts and consumables.
-During the warranty period, use only manufacturer’s parts and consumables.
1.3. Other remarks and instructions
-The KOMPBERG BKB22 TWIN booster compressor will reach its maximum
compression pressure only when 1.0-1.3 MPa is applied on the suction side from
the screw compressor,
-Operators should observe general H&S rules for boosters; also the technical
supervision body regulations for pressure equipment shall apply,
-An air tank selected individually by our technicians is necessary to ensure proper
functioning of the KOMPBERG BKB22 TWIN boosters.
2. Operating safety rules
The present rules are valid for BERG compressors. In addition to the H&S and Technical
Supervision regulations applicable to compressors, their assemblies and accessories, the
safety instructions given below should be followed in particular. The operators are
supposed to observe safe work practices. It is the user’s responsibility to continuously
maintain the compressor fully operable. Components and equipment considered to be no
longer suitable for safe operation should be promptly replaced. Adjustments, installation,
operation, maintenance and servicing should be entrusted only to properly trained,
qualified and authorized staff.
The limit values (pressure, temperature, time settings etc.) are given in the Technical
Data section.
The limit values may not be changed by the user.
The manufacturer accepts no responsibility for any injury, damage of equipment or the
compressor itself, at present and in the future, resulting from user’s negligence and failure
to observe the installation, operation and maintenance requirements contained herein. No
responsibility is also taken for failure to observe valid safety standards relating to the
equipment and qualified staff.
2.1. Basic requirements for safe transport and positioning of the boosters
In addition to the general H&S and Technical Supervision regulations, the following rules
must be observed:
-Use only H&S compliant and approved by the Technical Supervision lifting
equipment to lift the compressor. Fix in place all rotating or loose parts of the
machine before lifting it. It is strictly forbidden to stand in the hazardous range of
the lift operation. Machine movement can be accelerated or slowed down only
within applicable limits.
-The compressor is transported on wooden pallets which should be secured against
movement during transport. Fasten the compressor frame with cargo straps to
appropriate holders on the vehicle platform to prevent it from sliding or overturning.
-All screw and pipe connections should be of appropriate size and designed for a
given operating pressure.
-The compressor is not designed to operate outdoors.

-The compressor should be installed in a closed room, in cool and clean ambient
air. Never block air flow to and from the room. Ensure sufficient flow of cooling air
and extraction of heated air out of the room.
-The air sucked in should contain no vapours or flammable gases, e.g. paint
thinners, that might cause internal fire.
-There can be no objects close to the air inlet that could be sucked in with a jet of
air.
-The pressure conduit connecting the compressor with the compressed air line
should allow free expansion due to generated heat. It may not touch hot objects or
combustible materials.
2.2. Operating safety requirements
In addition to the requirements contained in the sections: boosters operating description;
Start up; Maintenance; the following rules should be observed:
-The compressor is intended for compressing air only.
-All safety equipment must be in place while operating the machine.
-The factory-mounted safety equipment may not be removed.
-There are hot parts in the compressor – conduits, air and oil coolers, screw
assembly. They will scald when touched.
-No unauthorized modifications in the control systems are allowed. After power
failure, the compressor must be restarted when the power supply is recovered.
-It is prohibited to remove the yellow-green electric shock-prevention conductors.
-No additional equipment can be mounted on the air tank.
-No welding or any other repairs can be done on the tank.
-The plugs and other tank components can be removed only after tank
depressurisation to the atmospheric pressure.
-General safety rules should apply while depressurising the air tank. The air must
be vented slowly. Keep the air stream away from people.
-Do not allow oil spill around the compressor.
-It is strictly prohibited to service the safety valves or to change their settings.
-Do not change settings in pressure switches above the value given in the
identification plate or in the Manual.
-Fulfil the obligation to register the compressor tank with the relevant technical
inspection body. Two sets of the required documents of the air tank (if provided)
and safety valve are included with the compressor documentation.
-Do not remove the pressure sensor or converter (temperature converter).
2.3. Other hazards
Strictly observe the data given in the product technical documentation to avoid any
hazards during the installation, switching on/off and maintenance of the compressor. The
risks that could not have been eliminated during the design stage are described in the
table below.
Assembly
Residual risk Action
Precautions
air cooler, guard, frame
minor cuts
touching avoid touching, wear
protective gloves
putting sharp objects
do not put any objects
fan guard and fan
injury
through the protection
through the protection
mesh with the fan
mesh, do not put any
running
objects on it
damage of wire adequate guard for the
metallic parts and
electric shock
insulation upstream power supply lead; check
electric wire
the motor breaker, live
the wire insulation for
metallic parts
damages

2.4. Explanation of symbols
Pictograms located on the compressor are described below. Explanation is provided
below any of them.
For technical reasons, it is impossible to attach pictograms in the very vicinity of the
points of risk.
MACHINE STARTS
DANGER OF SCALDS
DANGER OF ELECTRIC
AUTOMATICALLY
SHOCK
3. Setting
3.1. Room requirement
-The compressor requires no foundations. It must be seated on a hard and even
surface. Consider load capacity of the floor-ceiling, if the machine is installed in a
building.
-Strictly observe the minimum distances from walls and other machines. In case of
installation of several compressors, pay attention to the direction of cooling air flow;
no compressor should suck air which is heated by other machine.
-Protect the room in which the compressor is installed from negative temperatures.
The inlets and outlets to and from the room should be located in such a manner to
protect the interior from weather conditions.
-Heat generated during compression should be extracted outside (or to other
rooms), and fresh air should be supplied from the outside.
-If the gravity ventilation is insufficient (windows, openings in wall etc.) in the
compressor room, force air exchange using ventilators. To ensure sufficient heat
extraction, the ventilators should have summarised capacity around 15 – 20 %
higher than the total cooling air requirement for all compressors in the room.
-The air temperature in the room should range between +5°C to +40°C.
-Provide sufficient room for maintenance operations.
3.2. Power supply system requirement
The booster compressor is designed to be supplied by a five-conductor 400 V AC, 50 Hz
power line. If only four conductor line is available, bridge the PE and N terminals in the
cabinet terminal block.
The cross sectional area of conductors should be matched to the current drawn by the
booster compressor.
-3 x 50 mm2+ PE wire is recommended for the KOMPBERG BKB22 TWIN with a
motor power output of 45 kW (i.e. 2x22 kW).
The KOMPBERG BKB22 TWIN booster should be supplied from a switchgear
provided with a time delay fuse (rated for 125 A) and a breaker allowing to completely
cut the power supply out.
Connect the compressor as specified in the attached electric diagram.
3.3. Compressed air connection
Connect the compressor to the compressed air system with a flexible conduit.
It is recommended to use galvanized steel or plastic tubing for the compressed air
system. If conditioning equipment is provided for the compressed air (filters, drier), the
existing piping should be replaced with a new one, unless the air supplied previously has
not been conditioned by similar equipment.

Compressed air connection for KOMPBERG BKB22 TWIN
3.4. Compressed air treatment
Depending on the desired quality of compressed air, additional equipment for air
purification such as dehydrators, filters or drier should be installed downstream the
compressor.
Our specialists will select appropriate equipment free of charge.
4. Technical description
4.1. Applications
The KOMPBERG series booster compressors are intended for boosting air pressure from
1.0-1.3 MPa (KOMPBERG BKB22 TWIN) on the suction side, to 2.5-4.0 MPa on the
pressure side. The booster is provided with an oil filter and end cooler.
4.2. Main components
The booster compressor comprises an oil piston compressor with “V” cylinder
arrangement at 90° angle. The compressor is driven by an electric motor with a belt
transmission. A common frame supports the compressor, motor and air end cooler with
fans and filters.
4.3. The compressor
It is a single-stage compressor with two cylinders, one-side action, with “V” cylinder
arrangement at 90° angle.
The compressor has a tunelled iron cast crankcase. The crankcase bottom serves also
as an oil sump with the oil suction filter built in. The oil filter is installed in the oil pump.
Two cylinders with valves are mounted to the crankcase. The valves are held in place in
their seats in the head with adjustment bolts through special thrust sleeves. The cylinders
have special ribs to ensure efficient heat removal.
The crankshaft forged of increased impact-resistant steel is supported on two rolling
bearings. On one side, the crankshaft is provided with a cone end for pulley mounting,
whereas the other end drives the oil gear pump.
On a skin-hardened crank pin of the shaft, two connecting rods with thin-wall double-split
bearing bushings are mounted.
There are no separate heads in the compressor, as the cylinder and head is a one-
component iron cast. Both cylinders are linked with a common suction collector, at the
inlet side, and with the air end cooler, at the outlet side.
Pneumatichose

4.4. Electric motor
The booster compressor is driven by a squirrel-cage, AC electric motor. The motor is
designed for an intermittent run, for maximum 20 starts per hour. The compressor is
driven by the motor via a belt transmission.
4.5. End cooler
The cooler in the KOMPBERG boosters is made of vertical ribbed steel tubes connected
with horizontal collectors at the ends. The cooler has welded construction. In the upper
cooler collectors, valves for draining condensate and a relief solenoid valve are provided.
Air circulation in both solutions is forced by a fan driven by an electric motor.
4.6. Booster compressor frame
The KOMPBERG BKB22 TWIN booster frame, on which the motor and compressor are
supported, is made of plate and seated on four shock absorbers.
Booster KOMPBERG BKB22 TWIN
1.
Compressor 8. Cooler
2.
Electric motor 9. Oil filter
3.
Belt tensioner 10. Pressure transmitter
4.
Breather 11 Safety valve
5.
Belt transmission cover 12.
Solenoid valve - unload
6.
Intake collector 13. Solenoid valve - intake
7.
Solenoid valve 14. Mesh filter

4.7. Control and protection equipment
The unit is provided with the following control and protection equipment:
In the suction collector, a mesh filter is installed with two solenoid valves:
5/4" valve (or ¾") is placed behind the mesh filter and supplies air to the booster
suction side. This valve is only open when the compressor is pressing an air.
The
3/8" valve is located on the opposite side of the suction manifold and is used
to relieve the suction side of the compressor during start-up and idle run.
A ¼" solenoid valve (for high pressure) is installed on the aftercooler to relieve the
pressure on the compressor's discharge side during start-up and idle run.
All used solenoid valves are normally closed, so they shall be in the closed position when
they aren't electric supplied. When the booster is switched on (switch in START position),
the relief valves on the booster suction and discharge sides first open (when the motor is
stopped) for possible their relief and next the motor starts after a few seconds.
After the start-up, when the motor switches from Y (star) to (delta), the relief valves close
and the air supply valve opens to provide the air to the booster suction side. When the
preset discharge pressure is reached, the booster switches to idle run, i.e. the relief
valves open and the booster inlet valve closes.
A suction pressure sensor is also mounted on the suction manifold, which protects the
compressor (booster) against excessive pressure ratio, together with a discharge
pressure sensor (which must be mounted on a high pressure air receiver).
A safety valve is placed on the aftercooler to protect the compressor (booster) against
excessive increasing overpressure. There is also an oil pressure sensor placed on the oil
pump, which protects the compressor against incorrect oil pressure and the wrong
direction of rotation.
The maximum pressure ratio of the booster equals 4. The maximum pressure that the
booster can generate on the discharge side depends on the suction pressure.
The pressure ratio πis determined by the following formula:
where: π– pressure ratio, Pd– absolute discharge pressure, Ps– absolute suction pressure.
It means that the maximum absolute discharge pressure which a booster can generate is
four times greater than the absolute suction pressure. If the pressure ratio value is
exceeded, the booster switches to idle run.
After switch off the compressor (motor is stopped) there may be an overpressure in the
suction manifold and in the aftercooler. It’s necessary to keep this in mind when
performing any maintenance work.

5. Technical data
KOMPBERG BKB22 TWIN
Overpressure MPa 4,0
Suction overpressure MPa 1,0
Efficiency *)
m
3
/h
600
m
3
/min
10
Weight of compressor kg
1200
Weight of electrical box 8
Dimensions of compressor (LxWxH) mm 1607x851x1955
Dimensions of electrical box (LxWxH) mm 278x500x1600
Suction air connection G2
Compressed air connetion G1¼
Inlet height dimension mm
747
Outlet height dimension mm
587
Ambient temperature
0
C
from +5 to +40
Air temperature on the outlet
0
C
approx.20 above ambient temperature
Noise level L**)
dB(A)
82
Compressor V3.7.C
Number of cylinders 2
Cylinders diameters mm 72
Piston stroke mm 85
Rotational Speed
rpm
900
Volume of oil
dm
3
3,6
Using oil up g/h ≤8,5
Motor power
kW
2 x 22
Motor rotational speed
rpm 3000
Feed voltage
400V / 50Hz / 3Ph
*) - capacity measured acc. to ISO 1217, 1999
**) - momentary value of acoustic pressure corrected by C characteristic does not exceed 130 dB;
- equivalent acoustic pressure level corrected by A characteristic does not exceed 85 dB(A).
6. Operating description
6.1. Air circuit
The air supplied to the head passes through the head chamber and suction valve to the
cylinder. Once compressed in the cylinder, the air is forced through the pressure valve to
the end cooler.
After being cooled, the air passes through filters (option) and is supplied to the air tank.
As water condenses during the cooling and compressing process, the KOMPBERG
BKB22 TWIN booster cooler is provided with a valve for draining the condensate.
6.2. Lubrication system
Oil sucked by the gear pump is initially purified in the suction filter. Oil is forced through
the fine filter to the hole in the crankshaft, and further on through gaps in the crank pin to
the crank bearing bushings and pins.

6.3. Oil pressure control
Oil pressure in the lubrication system with the compressor running should be between 0.2
– 0.4 MPa, and the value should be checked on a pressure gauge connected to the oil
pomp connection pipe.
The adjustment should be performed when the compressor has heated up and
after the state of heat balance has been reached, i.e. after 0.5 hour of work. Secure
the locknut and cap nut back when the adjustment is finished.
Oil pomp
Manometer connection
Adjust the oil pressure by unscrewing
(decreasing the pressure) or tightening
(increasing the pressure)
Lock the screw with a locknut
Screw on the box nut.

Pressure gauge connection
Oil pressure measurement
Unscrew the nut
7. Unit operation and maintenance
Before each start and at least once a day:
-check oil level in the crankcase and top it up if necessary,
-check the connections,
-open the breather valve for about 10 seconds (the valve should be closed during
normal operation).
ventvalve
opened closed

8. Periodic maintenance and servicing
In order to ensure fault-free performance of the unit, observe the below listed
instructions relating to periodic checks and maintenance.
-Clean the external surfaces,
every 500 working hours
especially those of the cooler and
compressor cylinders.
(made by the user)
-
Tension drive belts, replace
if worn excessively.
every 2000 working hours
or once a year
if booster doesn't work 2000 per one year -
Change oil.
- Change oil filter.
(made by the authorized Ber
g
Kompressoren service)
every 2000 working hours - Change vent cartridge.
(made by the authorized Berg
-Change the rings and valves.
- Change non return valve cartridge.
Kompressoren service)
ever
y
6000 workin
g
hours
(made by the authorized Berg
-
Change V-drive belts.
Kompressoren service)
Disconnect the unit from its power source and depressurise it to the atmospheric
pressure before you proceed with any of the above service operations.
9. Procedure for important service operations
9.1. Oil filter replacement
- Turn off the booster compressor, close the valve on the discharge and
suction lines.
- Turn off power supply and secure it against being reconnected by
unauthorized persons.
- After waiting for at least 5 minutes, open the safety valve on the radiator
by pulling the stem.
- Replacing the filter is best done using a special key.
- Before screwing on the new filter, apply a thin layer of oil on the oil
filter gasket. Then screw on the filter by hand, without using any tool.
- Slowly open the valves on the suction and discharge lines
- Start the compressor and check for leaks.
Hot oil.

9.2. Vent cartridge replacement (fig. 174-22-000)
-Turn off the booster compressor, close the valve on the discharge
and suction lines.
-Turn off power supply and secure it against being reconnected by
unauthorized persons.
-After waiting for at least 5 minutes, open the safety valve on the
radiator by pulling the stem.
- Disconnect the hose from the vent cover
- Unscrew the vent cover.
- Replace the insert with a new one.
- Assemble the vent in the reverse order.
-Slowly open the valves on the suction and discharge lines.
-Start the compressor and check for leaks.
9.3. Check valve cartridge replacement (563-38-000)
-Turn off the booster compressor, close the valve on the discharge and
suction lines.
-Turn off power supply and secure it against being reconnected by
unauthorized persons.
-After waiting for at least 5 minutes, open the safety valve on the radiator by pulling
the stem.
-Undo the screws and remove the valve body from the side of the compressed air
network
-Replace the check valve insert with a new one
-Assemble the check valve in the reverse order
-Slowly open the valves on the suction and discharge lines
-Start the compressor and check for leaks.
1. Check valve
2. Nut
3. Allen screw
4. Spring washer
5. Valve body
6. Valve body
1
.
C
ove
r
2
.
T
an
k
3
.
G
as
k
et
4
.
Fil
ter cartr
idg
e

9.4. Oil change
-Replace used oil after pre-heating the machine; this way, the oil will quickly
-and thoroughly leave the tank. Always replace oil filter when replacing oil.
-Turn off the booster compressor, close the valve on the discharge
and suction lines.
-Turn off power supply and secure it against being reconnected by
unauthorized persons.
-After waiting for at least 5 minutes, open the safety valve on the radiator by pulling
the stem.
-Drain the oil completely and screw the drain plug back in.
-Pour new oil through the inlet to reach the max level mark.
-Screw the threaded plug tightly by hand into the oil inlet.
-Slowly open the valves on the suction and discharge lines
-Start the compressor and check for leaks and the oil level, replenish if necessary.
Use only:
Synthetic compressor oil PNEUMOIL ST150 (KOMPBERG BKB22)
Booster
Oil*
Quantity
KOMPBERG BKB22 TWIN
COL0045
(synthetic)
2 x 3,6 l
* 5 L package
9.5. V-belts tension
In order to obtain the correct tension of V-belts, loosen or tighten the nut 1.
Correct belt tension parameters.

10. Troubleshooting
Symptoms
Cause
Remedy
knocking in the loose crank bolts tighten the bolts
crankshaft bushings worn out replace the big end bushings
assembl
y
bearings worn out replace the main bearings
bad contact between working tighten the set screw in the head
valve and head seat cover
excessive play between piston replace sleeve and fit new one to
knocking in the head sleeve and piston pin piston pin
c
y
linde
r
excessive play of rings in piston replace piston rings
g
rooves
valve plate or spring cracked in replace the plate, check cylinder
the valve bearing surface
severe overheating causing remove and clean the piston and
cylinder bearing surface, check oil
other acoustic piston seizing
quality
disturbances in
large amounts of carbon
the compressor
check the piston rings fit in
deposits on the cylinder bearing
g
rooves
sur
f
ace
oil is too viscous or check oil quality, replace if
contaminated necessary
oil temperature insufficient quantity of oil replenish until maximum level is
too high reached
bearings fitted too close fit properl
y
contaminated bearings rinse bearings
leaking or damaged working repair and check valves for
valves tightness
protection for piston rings in remove deposits from rings and
reduced grooves grooves
compresso
r
excessive wear replace the rings in piston rings
performance leaking connection between the find and repair leakage
compressor and air system
safety valves are leaking gas blow or replace the valve with new
one
increase in the intercooler contaminated clean and wash the intercooler
compressed ai
r
contaminated surfaces in clean heads and cylinders
temperature cylinders and heads
pressure gauge overflow valve ill-adjusted tighten the overflow valve screw
indicates that
the pressure is
not enough oil in the crankcase add oil
too low
11. Consumables
Name Part No.
Quantity
1 Oil filter MFS0006 2
2 Vent cartridge UFW0003 2
3 V-belt MPK0012 4
4 Synthetic oil PNEUMOIL ST150 COL0045*
2 x 3,6 L
*5L package

Other manuals for KOMPBERG BKB22 TWIN
1
Table of contents
Popular Extender manuals by other brands

PI Manufacturing
PI Manufacturing HDMI-CAT6-60M-2 Operation manual
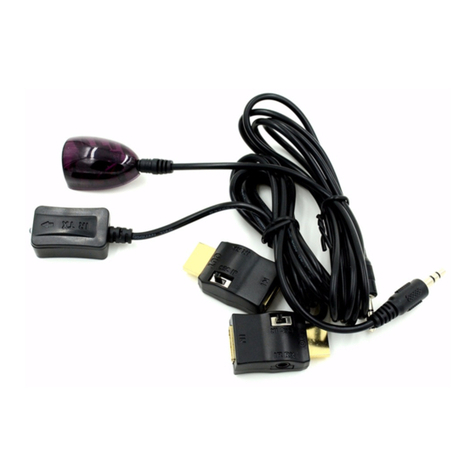
LINK-MI
LINK-MI LM-HEX01 user manual
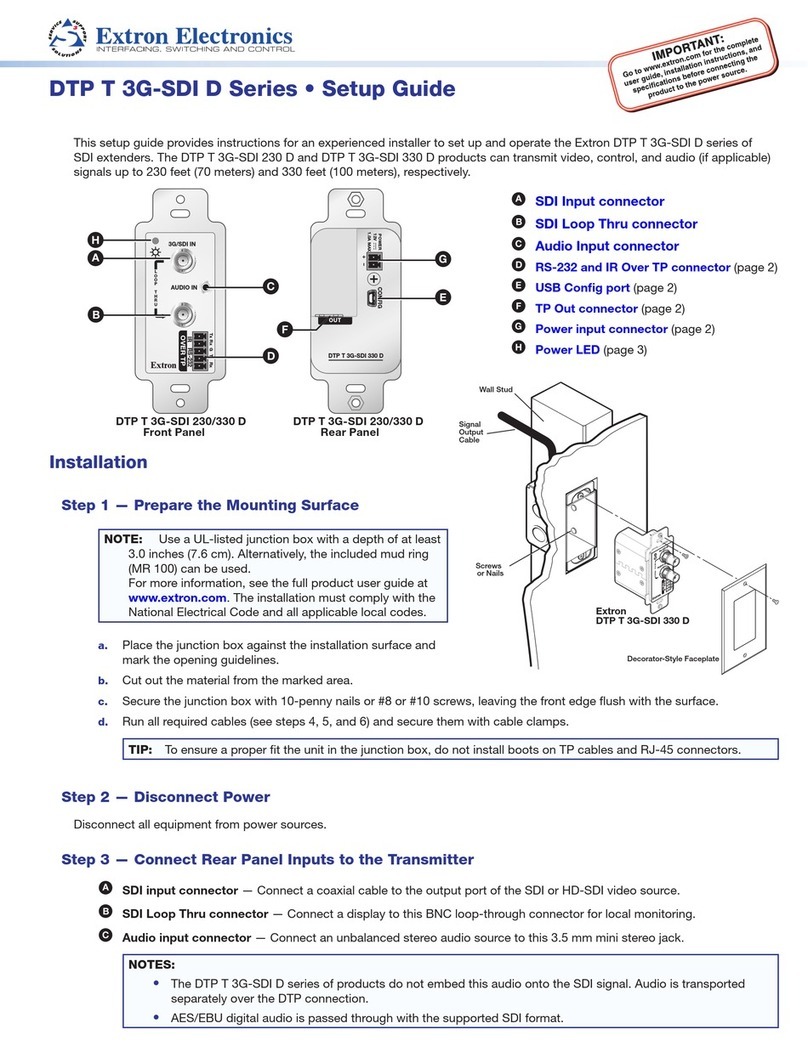
Extron electronics
Extron electronics DTP T 3G-SDI 230 D Setup guide

Schumacher Electric
Schumacher Electric PBI1812 owner's manual

Intelix
Intelix AVOCat AVO-SVA2-WP installation manual
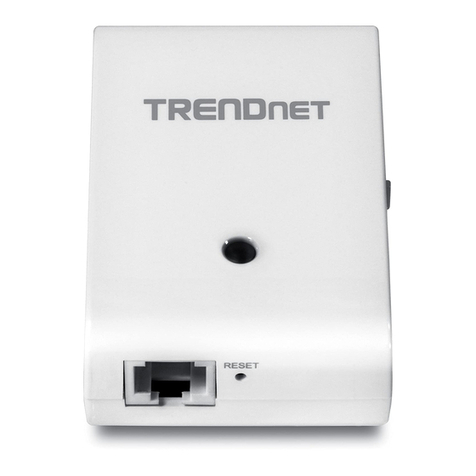
TRENDnet
TRENDnet TEW-713RE Quick installation guide