Betafence Robusta User manual

MOTORISED CANTILEVER
SLIDING GATES
Robusta®Bekamatic®
Industry
INSTALLATION MANUAL
Ed. 60761 April 2006 ENGLISH EN
60761BM IM Ind_ENG.indd 160761BM IM Ind_ENG.indd 1 08-05-2006 09:11:1008-05-2006 09:11:10

Bekamatic
®
Industry ed. April 2006 ENGLISH 2/21
Table of contents
1. Guidelines for installation . . . . . . . . . . . . . . . . . . . . . . . . . . 3
2. Guidelines for gate lifting . . . . . . . . . . . . . . . . . . . . . . . . . . 3
3. Foundations . . . . . . . . . . . . . . . . . . . . . . . . . . . . . . . . . . . . 4
3.1 Gates opening to the right . . . . . . . . . . . . . . . . . . . . . . . . . . . . 5
3.2 Gates opening to the left . . . . . . . . . . . . . . . . . . . . . . . . . . . . . 6
4. Preparations before gate installation . . . . . . . . . . . . . . . . . . . 7
4.1 Required fixation material . . . . . . . . . . . . . . . . . . . . . . . . . . . . 7
4.2 Installation of the ground anchors . . . . . . . . . . . . . . . . . . . . . . 8
4.3 Preparing installation levels . . . . . . . . . . . . . . . . . . . . . . . . . . . 9
5. Installation of the gate on the ground anchors . . . . . . . . . . . 9
6.
Installation of the lock post on the ground anchors
. . . . . . . . 10
7. Alignment and levelling of the gate . . . . . . . . . . . . . . . . . . 10
8. Adjustment of the mechanical end stops . . . . . . . . . . . . . . . 13
8.1 Adjustment of the front mechanical end buffering . . . . . . . . . . 13
8.2 Adjustment of the rear mechanical end buffering . . . . . . . . . . 14
9. Adjustment of the correct motor pressure . . . . . . . . . . . . . . 15
10. Power Supply . . . . . . . . . . . . . . . . . . . . . . . . . . . . . . . . . . 16
11. Adjustment and testing safety equipment: . . . . . . . . . . . . . 16
11.1 Induction system . . . . . . . . . . . . . . . . . . . . . . . . . . . . . . . . . 16
11.2 Safety Strips . . . . . . . . . . . . . . . . . . . . . . . . . . . . . . . . . . . . 16
11.3 End Switches . . . . . . . . . . . . . . . . . . . . . . . . . . . . . . . . . . . . 17
11.4 Alignment of the Photocells . . . . . . . . . . . . . . . . . . . . . . . . . . 17
12. Start the Self-Learning procedure . . . . . . . . . . . . . . . . . . . 19
60761BM IM Ind_ENG.indd 260761BM IM Ind_ENG.indd 2 08-05-2006 09:11:1308-05-2006 09:11:13

Bekamatic
®
Industry ed. April 2006 ENGLISH 3/21
1. Guidelines for installation
• A licensed technician or an installer who has had adequate product training by Betafence
N.V. should only install the gate.
• The integration of the gate in a fence may not create additional dangerous situations. Please
read carefully the warning document and consider the integration examples in the end user
manual delivered with the gate.
• The connection to the electrical power supply must be executed by a qualified technician and
according laws and standards on electrical installations that are applicable at that time.
2. Guidelines for gate lifting
• Gates are delivered completely assembled to the construction site.
• Lift-up points for the unloading and positioning during the installation
• The gate may only be lifted with the right equipment for manipulation and sufficient
dimensioned for the weight. By preference use a type flexible lift ropes with sufficient lifting
capacity.
60761BM IM Ind_ENG.indd 360761BM IM Ind_ENG.indd 3 08-05-2006 09:11:1308-05-2006 09:11:13

Bekamatic
®
Industry ed. April 2006 ENGLISH 4/21
3. Foundations
• Foundations prepared according to the corresponding
drawing.
- The gate may not be installed following the slope of the construction site. Make sure
that the foundation for the lock post is at the same level as the foundation for the
guiding post.
• Quality of the concrete B25 = cubic pressure resistance
25 N/mm2.
• Minimum 2 flexible ducts, minimum Ø 60 mm, for
electrical cables, at the position of the guiding post:
- 1 duct for the connection between the power source and the guiding post of the
gate.
- Do not put signal cables in the duct for power supply! Install an extra duct between
the gate and the point of operating.
- 1 duct for the cable connections between the guiding post and the lock post.
WARNING!
THE FOUNDATION PLANS PROVIDED ON THE NEXT PAGES SERVE ONLY AS AN
EXAMPLE! ALWAYS USE THE PLANS PROVIDED WITH THE ORDER DOCUMENT.
60761BM IM Ind_ENG.indd 460761BM IM Ind_ENG.indd 4 08-05-2006 09:11:1308-05-2006 09:11:13

Bekamatic
®
Industry ed. April 2006 ENGLISH 5/21
3.1 Gates opening to the right
60761BM IM Ind_ENG.indd 560761BM IM Ind_ENG.indd 5 08-05-2006 09:11:1308-05-2006 09:11:13

Bekamatic
®
Industry ed. April 2006 ENGLISH 6/21
3.2 Gates opening to the left
60761BM IM Ind_ENG.indd 660761BM IM Ind_ENG.indd 6 08-05-2006 09:11:1408-05-2006 09:11:14

Bekamatic
®
Industry ed. April 2006 ENGLISH 7/21
4. Preparations before gate installation
4.1 Required fixation material
Chemical anchors M16 x 250 mm (minimum 125 mm anchor depth and minimum 100 mm
above Finished Ground Level).
For the connection of:
- Guiding post (4 pieces)
- Lock post (4 pieces)
- Rear guiding roller set (4 pieces)
Chemical anchors M10 x 200 mm. 4 pieces for the connection of the support roll for the gate
open position.
WARNING!
DO NOT USE MECHANICAL ANCHORS AS THEY ARE NOT SUITABLE FOR THIS
APPLICATION!
60761BM IM Ind_ENG.indd 760761BM IM Ind_ENG.indd 7 08-05-2006 09:11:1408-05-2006 09:11:14

Bekamatic
®
Industry ed. April 2006 ENGLISH 8/21
4.2 Installation of the ground anchors
1. Put a tension line in the centre of the position
where the gate must be installed. From the
point of the lock post to the point where the rear
support roll has to come.
2. Position the templates of the guiding - and
lock post as well as the template of the rear
supporting wheels with the marked centre under
the tension line. Take in account the inter-
distances as mentioned on the foundations plans
provided with the order document.
3. Mark the position of the holes with a small
diameter concrete drill, this will help to centre
the final drill.
4. Drill the corresponding holes for the fixation
according the installation instructions of the
supplier of the chemical anchors. Drillings must
be in good vertical position.
5. Remove any dust and small particles from the
drill holes using a brush and hand pump. This will
ensure perfect adhesion between the resin for
the ground anchor and the concrete foundation.
6. Place the chemical anchors according to the
instructions of the supplier. Drying times must be
respected.
60761BM IM Ind_ENG.indd 860761BM IM Ind_ENG.indd 8 08-05-2006 09:11:1408-05-2006 09:11:14

Bekamatic
®
Industry ed. April 2006 ENGLISH 9/21
4.3 Preparing installation levels
1. Screw the bottom adjustment nuts on their
ground anchors and place the washers on the
nuts.
2. The guiding post position will serve as a reference
point for further installation of the other guiding
parts and posts. The bottom adjustment nuts of
the guiding post are levelled as reference towards
the concrete level +25 mm.
The nuts of each guiding position (rear guiding wheels,
rear support roll) should be perfectly horizontal one
between an other, so horizontal and vertical positions
of the main support elements of the gate is realized on
position of the gate during installation.
5. Installation of the gate on the ground anchors
1. The gate is positioned as a whole unit with the guiding post and the rear guiding wheels on
their corresponding ground anchors.
2. Chronological order of actions:
1. Remove packaging from the guiding post. Do not
remove the strap that holds the underbeam and
base plate together.
2. Bring the gate with the guiding post above the
ground anchors at ± 50 cm above the ground.
3. Open the access door of the guiding post. Pull off
the rubber seal
4. Remove the plate under the door by pulling it up
and pushing it towards yourself
5. When the power supply cables or other cables
are coming out of the concrete at the position of
the guiding post, put them trough the hole in the
base plate of the guiding post in to the cabinet.
6. Cut off the straps which fix the rear guiding
wheels to the under beam.
ATTENTION! Hold the wheels on their place
and prevent them from rolling onwards to the
guiding post as they might bump against a fixation of the induction system.
60761BM IM Ind_ENG.indd 960761BM IM Ind_ENG.indd 9 08-05-2006 09:11:1408-05-2006 09:11:14

Bekamatic
®
Industry ed. April 2006 ENGLISH 10/21
7. Now lower the gate until the rear guiding wheels and the guiding post is resting on
the washers of the ground anchors. Put on each ground anchor a washer and a nut.
Tighten the nuts slightly for temporary fixation. Remove straps from the base plate of
the guiding post.
ATTENTION! Beware that cables and wires are not crushed between surfaces while lowering
and positioning the gate on the ground anchors.
6.
Installation of the lock post on the ground anchors
1. Take off the lock post from the gate wing and bring it
to its ground anchors. Pull out the cables in the lock
post (type YSLY OZ 5 x 0,5 mm2 and connect the
corresponding (numbered) connectors with each other.
ATTENTION! Do not forget to put the seals (blue)
between the male & female connector for having
waterproof connections.
2. Push back the cables in the tube of the lock post until
the connectors are also in the tube. This will protect
them against water and will facilitate the uninstalling of photocells
3. Put the lock post on the ground anchors and install the upper washers with nuts. Tighten
the nuts slightly for temporary fixation
7. Alignment and levelling of the gate
1. Put the gate in manual mode by turning the threaded
rod anticlockwise until the teeth of the pinion don’t grip
in the teeth of the dental rack anymore.
2. Align the rear guiding wheels, the guiding post
according the gate centre line. Make sure that the wing
is running parallel in the guiding post.
The guiding post and the rear guiding wheels can be
moved laterally in the sleeves of the base plates.
When the alignment between the rear guiding wheels and the guiding post is done tighten
slightly the nuts of the ground anchors of the guiding post and rear guiding wheels.
Check if the gate moves easy by hand over the complete route of the wing during opening and
closing. Do this in slow motion as not all adjustments are done.
60761BM IM Ind_ENG.indd 1060761BM IM Ind_ENG.indd 10 08-05-2006 09:11:1508-05-2006 09:11:15

Bekamatic
®
Industry ed. April 2006 ENGLISH 11/21
3. Close the gate nearly completely by hand and align the
lock post. Make sure that the guiding rolls on top of the
wing are entering the catcher in the middle. Forcing on
one of the sides when adjusting is not tolerable.
4. Put the wing in the position that the rear guiding wheels
and the guiding wheels at the position of the guiding
post support it. Put a level in the middle between these
sets of guiding wheels. If necessary bring to horizontal
position by lowering or raising the rear guiding wheels
support by means of the nuts of the ground anchors.
Make sure to preserve the horizontal level of the base
plate.
WARNING!
IN ANY CASE DO NOT ADJUST WITH
THE M10 NUTS AND BOLTS FOR THE
CONNECTION OF THE BASE PLATE
AND THE WHEEL SUPPORT.
5. After alignment of the lock post and horizontal leveling
of the wing, adjust the height of the lock post so that
the support wheel under the front of the under beam is
slightly touching the ramp (of the lock post) just below
the horizontal surface. Beware to keep the vertical
levels and the positioning in the catcher of the lock
post. The height adjustment is done with the nuts of
the ground anchors.
IMPORTANT!
The support wheel in the under beam may not force from complete down position on the
ramp to enter the lock post.
6. After full adjustment of the gate, tension up all nuts from the ground anchors. Then cut
the lengths of the ground anchors 1/2 cm above the nuts, and paint afterwards against
corrosion.
60761BM IM Ind_ENG.indd 1160761BM IM Ind_ENG.indd 11 08-05-2006 09:11:1508-05-2006 09:11:15

Bekamatic
®
Industry ed. April 2006 ENGLISH 12/21
7. Gates with a free passage more than 6m00 have a support roll for the wing in open position.
Install that roll on the foundation as described as hereunder.
A correct adjustment of this roll is indispensable for a good functioning of a motorised
cantilever-sliding gate Bekamatic.
The adjustment is required as well for the correct height of the support roll as for the
perpendicular of the support roll towards the under beam of the wing.
A support roll installed too high will add undesired friction forces on the wing which are
increasing the further the wing is opened.
The height of the support roll must be adjusted when
the wing is approximately at 50 cm from completely
open position
At this position the support roll may make contact with
the underside of the under beam. Adjust the height
when necessary
G
Do not adjust the
tension system!
Support roll Rear guiding
wheels
Guiding wheels
in the guiding
post
OK Not OK
90° < 90°
60761BM IM Ind_ENG.indd 1260761BM IM Ind_ENG.indd 12 08-05-2006 09:11:1608-05-2006 09:11:16

Bekamatic
®
Industry ed. April 2006 ENGLISH 13/21
8. Adjustment of the mechanical end stops
ATTENTION!
The verification and/or the adjustment of the mechanical end buffering must always
be executed. When the end buffering is not adjusted properly it may cause severe
irreversible damage to some parts of the gate.
The mechanical end buffering is located on the front- and rear support of the guiding
wheels in the under beam. To have access to them the front and the rear of the under
beam must be opened.
8.1 Adjustment of the front mechanical end buffering
If the gate is installed correctly according the
foundation plan, then the front buffer doesn’t
need to be adjusted as the factory default setting
(default 13 cm) will be sufficient.
However if there is some deviation from the
foundation plan, or an obstacle at the rearside
of the gate is preventing the wing opening over
its full course, then adjust according to the
description below.
1. Remove the lower part of
the safety pressure strip
from its aluminum fixation
profile.
2. Remove the front cover
plate from the under beam
by unscrewing the 4 screws
(2 on both sides) of the under beam.
3. Unblock the counter nut. Turn the threaded rod counter-clockwise so that the rubber
stop is coming out of the under beam for 0.5 cm to 1.0 cm. Block the threaded rod
with the counter nut.
ATTENTION!
Do not turn clockwise! The default setting of 13 cm is minimum distance to apply.
4. Put back the cover plate to close the under beam
and tighten the screws with moderate force.
5. Re-fix the rubber profile from the safety pressure
strip on the aluminum profile. To aid the fixation
it is advised to spray some silicone lubricant on
the rubber fixation flaps and the sleeves in the
aluminum profile. Then push the flaps by hand in
the aluminum profile.
60761BM IM Ind_ENG.indd 1360761BM IM Ind_ENG.indd 13 08-05-2006 09:11:1608-05-2006 09:11:16

Bekamatic
®
Industry ed. April 2006 ENGLISH 14/21
8.2 Adjustment of the rear mechanical end buffering
The rear mechanical end buffering is preinstalled on the support of the rear guiding
wheels and is adjustable in length up to 45 cm maximum (Exception: for gates up
to 4m, adjustable length up to 20 cm maximum). This is the maximum allowable
adjustment with respect to the good functioning of the gate and applied forces.
Therefore we strongly advise to respect the dimensions of the foundation plans at all
time.
1. Remove the rear cover plate from the under
beam by unscrewing the 4 screws (2 on both
sides) of the under beam.
2. Close the gate so that there is a distance of 1,0
to 2,0 cm between the upper guiding rolls on top
of the wing and the bottom of the catcher on the
lock post.
3. Unblock the counter nut. Turn the threaded
rod counter-clockwise so that the rubber stop
is coming out of the under beam for 0,5 cm to
1,0-cm. Block the threaded rod with the counter
nut.
4. Put back the cover plate to close the under beam and tighten the screws with moderate
force.
60761BM IM Ind_ENG.indd 1460761BM IM Ind_ENG.indd 14 08-05-2006 09:11:1708-05-2006 09:11:17

Bekamatic
®
Industry ed. April 2006 ENGLISH 15/21
9. Adjustment of the correct motor pressure
1. Put the wing in the position that it is supported by the
rear guiding wheels and the wheels at the position of
the guiding post.
2. Turn the threaded rod clockwise.
3. Move the wing slightly back and forward. This will
prevent pushing a tooth of the dental wheel on top of
a tooth of the dental rack instead of gripping in each
other.
4. When, while turning the threaded rod, the vertical
movement of the drive stops, you must turn the rod in
for another 8 mm. This is the correct motor pressure.
Hint: the threaded rod is M12, so 4½ turns is
approximitly 8 mm.
5. Put back the cover plate underneath the door.
G
60761BM IM Ind_ENG.indd 1560761BM IM Ind_ENG.indd 15 08-05-2006 09:11:1708-05-2006 09:11:17

Bekamatic
®
Industry ed. April 2006 ENGLISH 16/21
10. Power Supply
1. Power source must be 240 VAC. Connect the power supply cable
on to the connectors of the main switch.
Cable coming from the main board to the gate, must be secured
according legislations for electrical installations applicable at that
time.
Use a low voltage power solid cable with a section according to the table underneath. (For
example : NYY JZ 3 x 2,5mm2 according to VDE0276 part 603, VDE 0271 and IEC 52)
Section (mm2) Maximum distance (m)
2,5 300
4 600
6 900
2. Switch the current on by turning the main switch in position “ON”.
WARNING:
THE CALUCULATIONS ARE DONE ON OUR GATE WITH ALL
OUR POSSIBLE ACCESSORIES. IF YOU ARE CONNECTING
MORE CONSUMERS TO IT, IT MAY BE NECESSARY TO USE
A BIGGER SECTION.
11. Adjustment and testing safety equipment:
11.1 Induction system
Check if the jumpers (J1 and J2) for connecting the stationary coil to
the decoder board are connected. Check if parameter B is set on ‘1’.
11.2 Safety Strips
Check if all safety strips are functioning correctly.
When the safety strip on the top of the wing is activated an “Sc”
indication must appear on the display of the controller board.
An “So” indication must appear when the safety strip at the rear of the
wing is activated.
“So” must be indicated when a safety strips, on the guiding post, in the
free passage of the gate is activated.
“Sc” must be indicated when a safety strips, on the guiding post, at the
closing side of the gate is activated.
L1
PE
N
Controller Display
60761BM IM Ind_ENG.indd 1660761BM IM Ind_ENG.indd 16 08-05-2006 09:11:1808-05-2006 09:11:18

Bekamatic
®
Industry ed. April 2006 ENGLISH 17/21
11.3 End Switches
Check if the inductive end switches are functioning correctly.
Move the wing until fully closed position by hand. The wing should be stopped by the
mechanical end stop and a “Lc” indication must appear on the display of the controller
board.
Move the wing until fully open position by hand. The wing should be stopped by the
mechanical end stop and a “Lo” indication must appear on the display of the controller
board.
11.4 Alignment of the Photocells
Align, for all the photocells (max. 4 pieces), installed on the gate, the transmitter with
the receiver. Therefore follow the procedure as described below. After alignment each
individual interruption of the IR-beam of a photocell must trigger a “Pc” indication on
the display of the controller.
1. One-pair photocell set-up
In a ‘one-pair photocell’ set-up, only one pair of photocells
is used. The receiver is placed in the guiding post and the
transmitter is placed in the end post.
It is mainly sufficient to align the photocells this way that
they ‘look’ at each other. To align the photocells, loosen the
‘block’-screw inside the photocell and manually align the
lens to ‘look’ at the other photocell.
ATTENTION! Do not forget to tighten the screw after completion of alignment.
Tip: if the photocells suffer from interference with sunlight and/or other light sources,
it is recommended to align the receiver so that is ‘looks down’ from the straight line
between the receiver and the transmitter.
2. Two-pair photocell set-up
In a ‘two-pair photocell’ set-up, two pairs of photocells are used. The receiver of
the first pair is placed in the guiding post and the corresponding transmitter is
placed in the end post. The receiver of the second pair is placed in the end post and
the corresponding receiver is placed in the guiding post. This way the two pairs of
photocells cannot interfere with each other.
SCREW
LED
LENS
60761BM IM Ind_ENG.indd 1760761BM IM Ind_ENG.indd 17 08-05-2006 09:11:1808-05-2006 09:11:18

Bekamatic
®
Industry ed. April 2006 ENGLISH 18/21
The alignment procedure is quit simple. It is mainly sufficient to align each pair of
photocells this way that they ‘look’ at each other. To align the photocells, loosen the
‘block’-screw inside the photocell and manually align the lens to ‘look’ at the other
photocell. Do not forget to tighten the screw after completion of alignment.
Tip: if the photocells suffer from interference with sunlight and/or other light sources,
it is recommended to align the receiver so that is ‘looks down’ from the straight line
between the receiver and the transmitter.
3. Three- or four-pair photocell set-up
In a ‘three- or four-pair photocell’ set-up, three or four pairs of photocells are used.
This means that always two receivers must be placed in the same post and that both
the transmitters must be placed in the opposite post. This set-up makes it possible
that the two pairs will interfere with each other. The only way to prevent interference
is excellent alignment of these two pairs of photocells. The following procedure may
be used.
Step 1: Disconnect one of the transmitters on the guiding post.
Step 2: Align the remaining transmitter so that it covers both receivers. This is ok if
the controller shows no PC error and the LED’s on both receivers are off.
Step 3: Turn the transmitter outwards so that it covers only his mating receiver. This
is ok when the controller shows a PC error and the LED of his mating receiver is off
and the LED of the other receiver is on.
60761BM IM Ind_ENG.indd 1860761BM IM Ind_ENG.indd 18 08-05-2006 09:11:1908-05-2006 09:11:19

Bekamatic
®
Industry ed. April 2006 ENGLISH 19/21
Step 4: Repeat step 1 to 3 for the other transmitter on the guiding post.
Step 5: If the alignment is well performed both transmitters will only cover their own
receiver.
Step 6: Repeat step 1 to 5 for the transmitters on the end post.
Tip: if the photocells suffer from interference with sunlight and/or other light sources,
it is recommended to align the receiver so that is ‘looks down’ from the straight line
between the receiver and the transmitter.
12. Start the Self-Learning procedure
ATTENTION!
During the self-learning cycle, the gate measures the time needed for one full cycle (open
– close or close – open). This time is stored into the non-volatile memory of the controller and
will be used as the motor protection. The first time a time-out occurs E7 will be indicated on the
controller display, the second time E5 will be indicated. When error code E5 is indicated, it
is necessary to investigate the cause of the time-out. A simple reset of the controller
and a new trigger for gate movement may cause irreversible damage of the drive
unit.
A new gate will always have done a self-learning cycle as a test when manufactured (otherwise
E9 will be indicated). Nevertheless we strongly advise to redo the cycle. Note that during the
cycle all safety devices are active, so take care not to trigger accidentally one of the safety
devices.
To start the self-learning, the controller must first be put in configuration mode and then in
special function mode. Configuration mode is indicated on the controller by a blinking decimal
point on the right-hand display. Special function mode is indicated by two blinking decimal
points.
60761BM IM Ind_ENG.indd 1960761BM IM Ind_ENG.indd 19 08-05-2006 09:11:1908-05-2006 09:11:19

Bekamatic
®
Industry ed. April 2006 ENGLISH 20/21
1. Configuration Mode
To prevent unauthorised change of the control parameters, this option is password protected.
The password is entered in the following way:
Set the selector switch on position 4
Press the [·]-key once, the display will read [P1]
Set the selector switch on position 7
Press the [·]-key once, the display will read [P2]
Set the selector switch on position 3
Press the [·]-key once, the display will read [P3]
Set the selector switch on position 5
Press the [·]-key once
The decimal point indication on the right display will start to blink, which means that you
are in the parameter configuration mode.
Remark:
If the procedure was not executed correctly, the controller will return to normal display
mode. Also, if you wait too long (more than 25s) to continue the password procedure, the
controller will return to normal display mode.
2. Special function mode
Put the controller in configuration mode as described in part 1
Set the selector switch on position 0
Press the [·]-key once
The two decimal points will blink simultaneously
Put the selector switch on 6
S.L. Is displayed => Self-Learn
Press the [·]-key, the gate will now start the Self-Learning.
The gate is now ready for use.
To have personalized parameter setting follow the procedure as indicated in the technical
handbook:
INTELLIGENT GATE CONTROL
IGC-300
THE GATE CAN NOW OPERATE AUTOMATICALY.
60761BM IM Ind_ENG.indd 2060761BM IM Ind_ENG.indd 20 08-05-2006 09:11:1908-05-2006 09:11:19
Table of contents
Popular Gate Opener manuals by other brands

CAME
CAME BXV10AGF installation manual

Hobart
Hobart 486259 Series Operation and maintenance manual
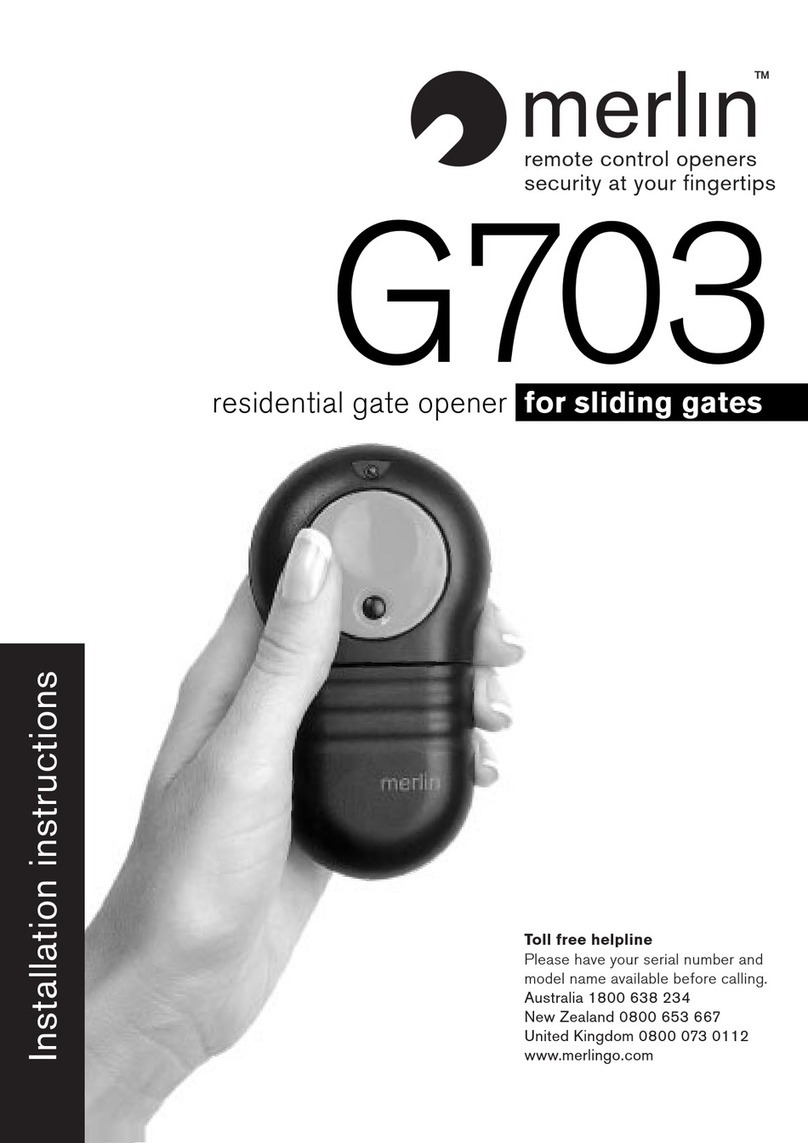
Merlin
Merlin G703 installation instructions
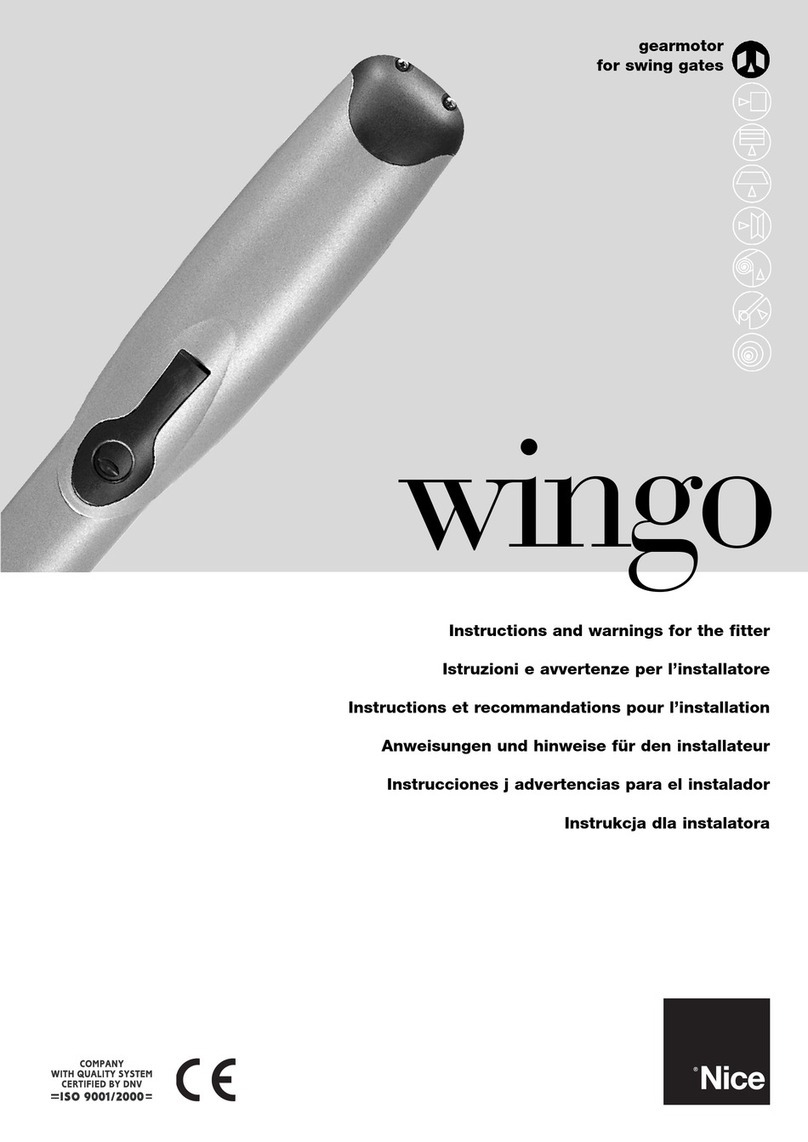
Nice
Nice Wingo Instructions and warnings for the fitter
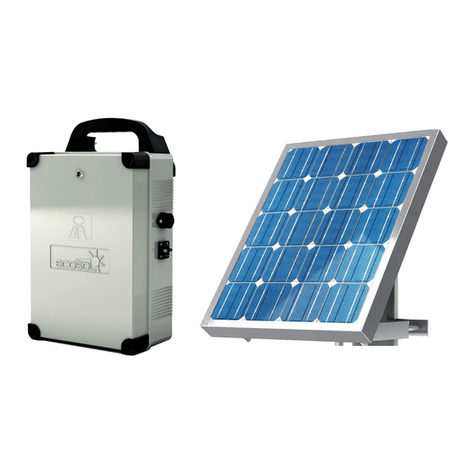
BFT
BFT ECOSOL installation manual
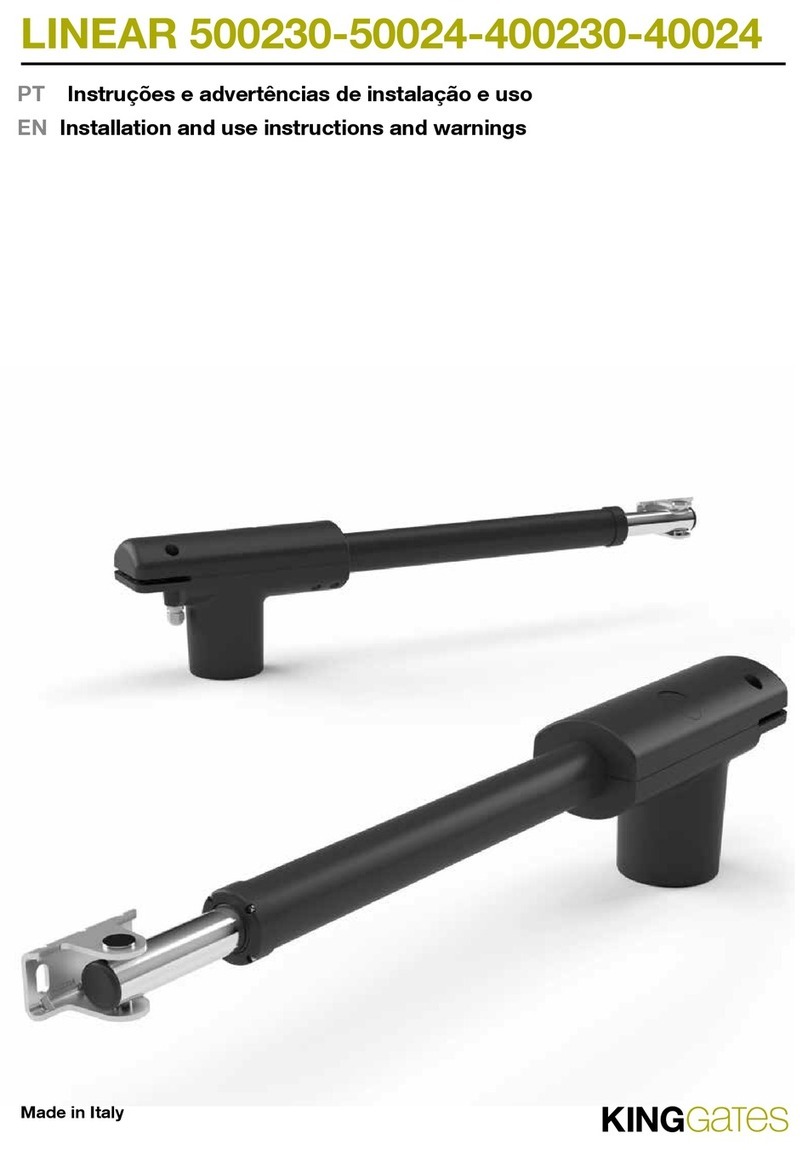
King gates
King gates LINEAR500230 Installation and use instructions and warnings