Binks 84-411 User manual

Binks Model 84-411
FLUID REGULATOR
(5 – 100 PSI)
2 26
Replaces
Part Sheet
77-2011R-3
Part
Sheet
77-2011R-4
1 20-3699 ●SOC. HD. CAP SCREW,
10-24 x 1 IN. LONG ............................. 6
2 20-4456
LOCKNUT.......................................... 1
3 33-190
♦PIN, 1/8 IN. x 1/2 IN. LONG..................... 1
4 72-337 NUT, SWIVEL..................................... 1
5 73-50 NIPPLE D.M....................................... 1
6 83-1355 GAUGE, 5–100 PSI............................... 1
7 84-40 CONNECTOR..................................... 1
8 84-321 BONNET............................................ 1
9 84-322
♦SCREW .............................................. 1
10 84-323
♦WASHER ........................................... 1
11 84-324
♦STEM................................................. 1
12 84-325
♦STEM ASSEMBLY .............................. 1
13 84-326
♦FOLLOWER ....................................... 1
14 84-603 † DISC................................................... 2
15 84-330 † DIAPHRAGM..................................... 1
ITEM PART
NO. NO. DESCRIPTION QTY.
16 84-331 NUT................................................... 1
17 84-338 TAILPIECE.......................................... 1
18 84-340
♦KEY ................................................... 1
19 84-344 BODY ................................................ 1
20 84-347 INLET................................................. 1
21 84-354 SOCKET............................................. 1
22 84-388 † GASKET............................................. 1
23 84-395 ROD................................................... 1
24 84-399 † DIAPHRAGM..................................... 1
25 84-452
♦SPRING.............................................. 1
26 84-460
BODY ................................................ 1
27 84-463 † GASKET............................................. 1
28 84-467 † RETAINER.......................................... 1
29 84-468 † SEAT .................................................. 1
30 84-469 † VALVE ............................................... 1
31 84-470 CAP ................................................... 1
ITEM PART
NO. NO. DESCRIPTION QTY.
● Tighten all flange screws securely BEFORE installing regulator.
For remote control only. Not furnished. Please order separately.
♦Remove from regulator when converting from manual to remote control.
† Also available in Repair Kit 6-529. Please order separately.
PARTS LIST
When ordering, please specify Part No.
7
19
28
30
20
31
17
4
29
23
24
5
6
22
27
25
11
12
13
10
3
83-2052 LENS (ONLY)
9
18
8
21
16
14
1
15
* Item to be torqued to
35–45 in-lbs
** Items to be torqued to
150–160 in-lbs
**
**
*
**
**
**

2
Warning
!
In this part sheet, the words WARNING, CAUTION and NOTE are used to emphasize important safety information as follows:
CAUTION
Hazards or unsafe practices which could
result in minor personal injury, product
or property damage.
!
WARNING
Hazards or unsafe practices which could
result in severe personal injury, death or
substantial property damage.
!
NOTE
Important installation, operation or
maintenance information.
Read the following warnings before using this equipment.
READ THE MANUAL
Before operating finishing equipment, read and
understand all safety, operation and maintenance
information provided in the operation manual.
ELECTRIC SHOCK/GROUNDING
Improper grounding or sparks can cause a
hazardous condition and result in fire, explosion
or electric shock and other serious injury.
PROJECTILE HAZARD
You may be injured by venting liquids or gases
that are released under pressure, or flying debris.
INSPECT THE EQUIPMENT DAILY
Inspect the equipment for worn or broken parts
on a daily basis. Do not operate the equipment
if you are uncertain about its condition.
NEVER MODIFY THE EQUIPMENT
Do not modify the equipment unless the
manufacturer provides written approval.
FIRE AND EXPLOSION HAZARD
Improper equipment grounding, poor ventilation,
open flame or sparks can cause hazardous
conditions and result in fire or explosion and
serious injury.
KNOW WHERE AND HOW TO SHUT OFF THE
EQUIPMENT IN CASE OF AN EMERGENCY
STATIC CHARGE
Fluid may develop a static charge that must be
dissipated through proper grounding of the
equipment, objects to be sprayed and all other
electrically conductive objects in the dispensing
area. Improper grounding or sparks can cause a
hazardous condition and result in fire, explosion
or electric shock and other serious injury.
WEAR SAFETY GLASSES
Failure to wear safety glasses with side shields
could result in serious eye injury or blindness.
OPERATOR TRAINING
All personnel must be trained before operating
finishing equipment.
EQUIPMENT MISUSE HAZARD
Equipment misuse can cause the equipment to
rupture, malfunction, or start unexpectedly and
result in serious injury.
KEEP EQUIPMENT GUARDS IN PLACE
Do not operate the equipment if the safety
devices have been removed.
HIGH PRESSURE CONSIDERATION
High pressure can cause serious injury. Relieve all
pressure before servicing. Spray from the spray
gun, hose leaks, or ruptured components can
inject fluid into your body and cause extremely
serious injury.
PRESSURE RELIEF PROCEDURE
Always follow the pressure relief procedure in the
equipment instruction manual.
DE-ENERGIZE, DEPRESSURIZE, DISCONNECT
AND LOCK OUT ALL POWER SOURCES DURING
MAINTENANCE
Failure to De-energize, disconnect and lock out
all power supplies before performing equipment
maintenance could cause serious injury or death.
CA PROP
65
PROP 65 WARNING
WARNING: This product contains chemicals known
to the State of California to cause cancer and
birth defects or other reproductive harm.
FOR FURTHER SAFETY INFORMATION REGARDING BINKS AND DEVILBISS EQUIPMENT,
SEE THE GENERAL EQUIPMENT SAFETY BOOKLET (77-5300).
IT IS THE RESPONSIBILITY OF THE EMPLOYER TO PROVIDE THIS INFORMATION TO THE OPERATOR OF THE EQUIPMENT.

3
Binks MODEL 84-411 FLUID REGULATOR (5–100 PSI)
INSTALLATION DATA
OPERATING INSTRUCTIONS
MOUNTING
Regulator (3/8" NPT(m) inlet) may be
mounted in either a horizontal or vertical
position. However, in ALL cases:
to operate properly, gauge riser tube
MUST be in a vertical position.
REGULATION
Use slotted end of key. Clockwise rotation
increases pressure; counter-clockwise
rotation reduces pressure.
BLOW BACK
Use hexagon end of key. Turn count-
er-clockwise and gauge will read inlet pres-
sure (main line pressure).
To shut off, turn key clockwise and
gauge will return to normal regulated
reading when flow begins.
CLIMBING
When regulated pressure climbs, it normally
indicates dirt on the seat; trigger gun rapidly
to flush seat. If climbing continues, open
regulator to main line to flush. If climbing
still persists, replace valve and seat.
BUZZING
When in operation, buzzing indicates
trapped air within the regulator.
CAUTION
When blowing back to reverse-flush
regulator, be sure air pressure DOES NOT
exceed maximum rating of gauge.
!
NOTE
Fluid should be flowing through regula-
tor when regulating pressure.
Installation is simplified by the use of a swivel nut inlet connection
(see illustrations). This is standard on all models; it eliminates the
cost of a union, and provides a quick and convenient method to
easily remove the unit from the line.
Regulation Range: 5 to 100 PSI 7.0 kg/cm2
Max. Reg. Flow: 128 fl. oz./min. 3.78 l/min.
Max. Inlet Pressure: 200 PSI 14.06 kg/cm2
SERVICE INSTRUCTIONS
NOTE
Due to variations in diaphragm stretch, fluid flow may not shut
off when the pressure is backed off to zero. Install an inlet valve
if complete shut-off is required.
30
23 28 29 31
TO REPLACE FLUID VALVE & SEAT
Remove regulator from line by loosening
the swivel nut; always blow back regulator
before removing. At inlet, remove
(counter-clockwise rotation) slotted cap
nut with screw driver, ball valve will
slide off rod. Unscrew (counter-clock-
wise rotation) hexagon inlet retainer;
valve seat will be removed with retainer.
Remove valve seat from retainer and
replace if worn. Ball valve may be
released and reused unless both sides
are worn.
To reassemble: Insert valve seat into
retainer; note position of shoulder. Place
ball valve on rod, and screw cap nut on
rod and tighten. Screw hex retainer onto
body and tighten. Regulator requires no
adjustments.
TO REPLACE DIAPHRAGM
Remove regulator from line. At inlet,
remove slotted cap nut with screw driver;
ball valve will slide off rod.
Remove bonnet by loosening six socket
head cap screws. Clamp diaphragm
assembly in vise, loosen nut (16) and
remove diaphragm.
To reassemble: Reverse above procedure.

3/13 ©2013 Binks All rights reserved. Printed in U.S.A.
Binks Sales and Service: www.binks.com
WARRANTY
This product is covered by Binks’ 1 Year Limited Warranty.
77-2011R-5 Revisions: Trademark updates;
(P1) Added torque specs; (P2) Added Prop 65
warning; (P4) Updated contact information.
U.S.A./Canada Customer Service
195 Internationale Blvd.
Glendale Heights, IL 60139
630-237-5000
Toll Free Customer Service
and Technical Support
800-992-4657
Toll Free Fax
888-246-5732
Other Binks Controllers manuals
Popular Controllers manuals by other brands
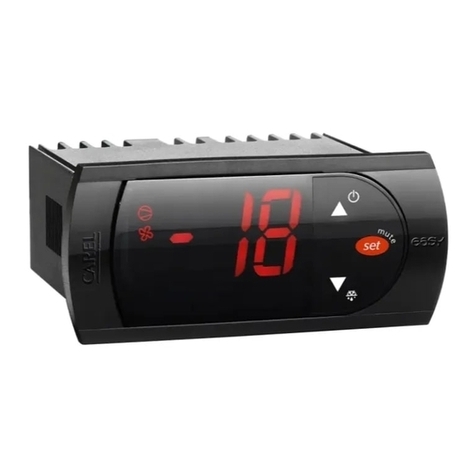
Carel
Carel PJEZ G Series quick start guide
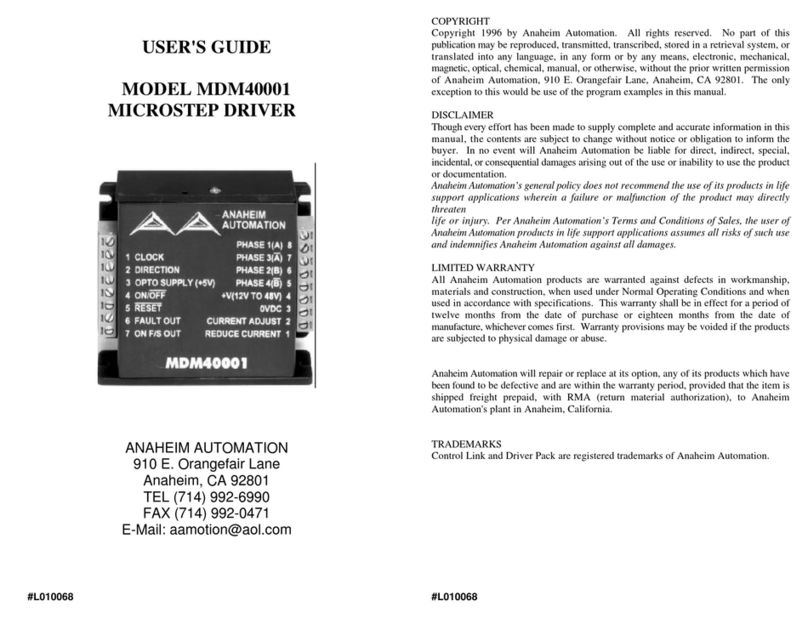
Anaheim Automation
Anaheim Automation MICROSTEP DRIVER MDM40001 user guide
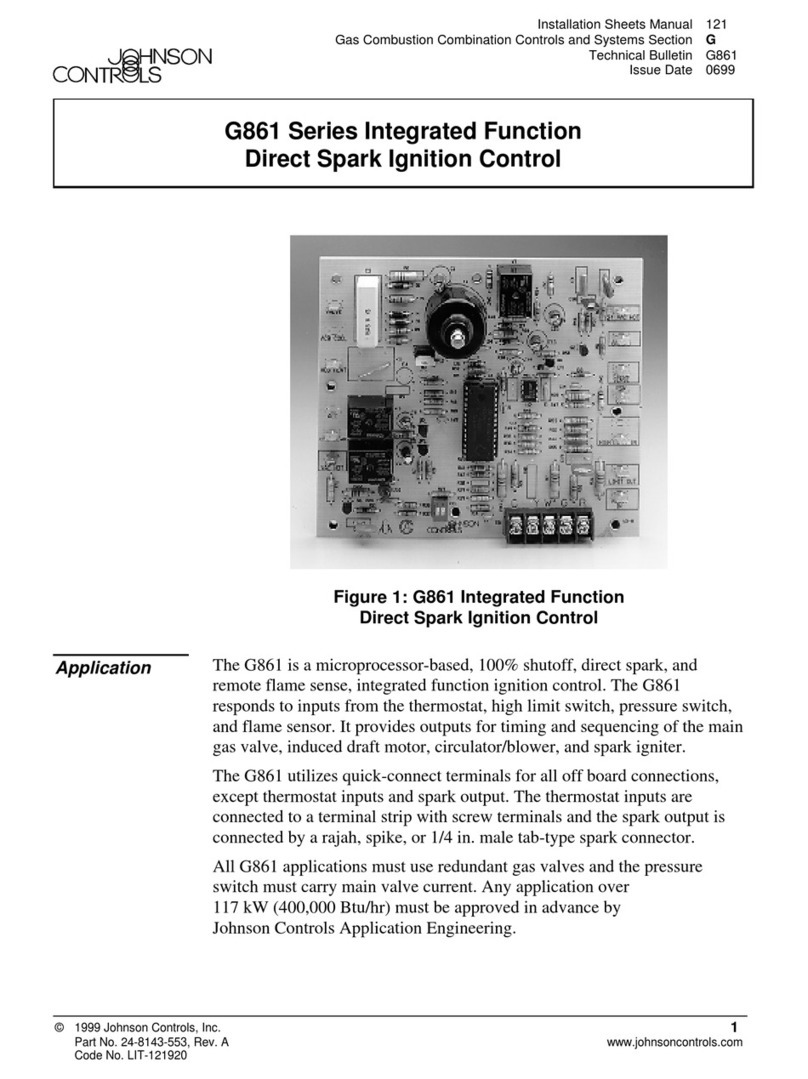
Johnson Controls
Johnson Controls G861 Series Technical bulletin
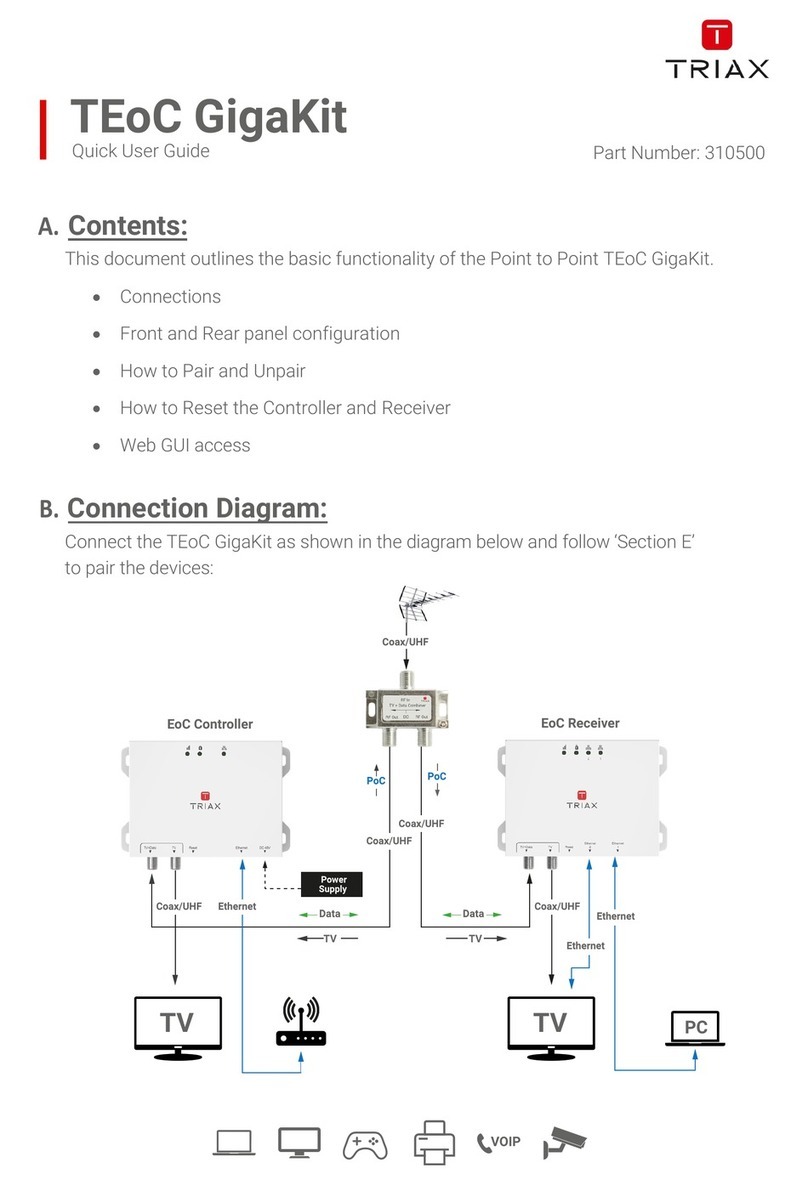
Triax
Triax TEoC GigaKit Quick user guide
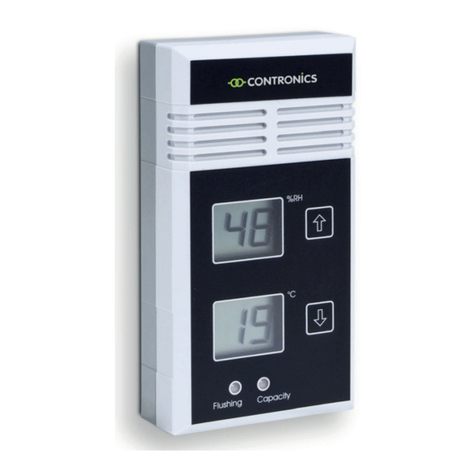
Contronics
Contronics HTR-10 user manual
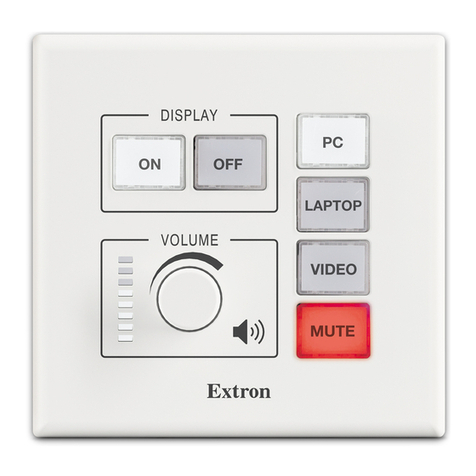
Extron electronics
Extron electronics MediaLink MLC Plus 50 Setup guide
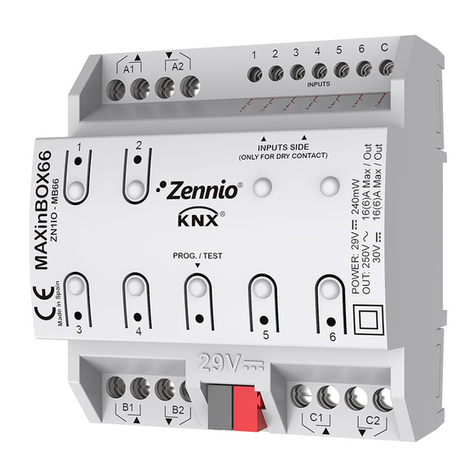
Zennio
Zennio MAXinBOX66 Technical documentation
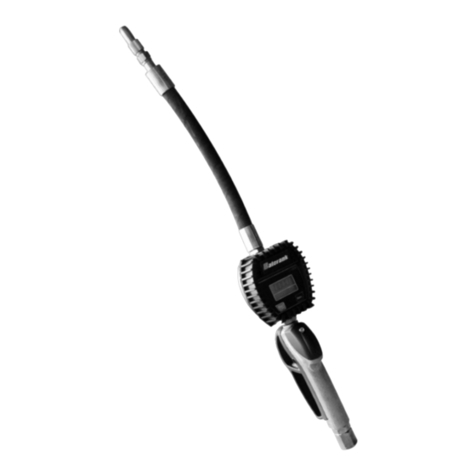
Balcrank
Balcrank 3330-142 Operation, installation, maintenance and repair guide
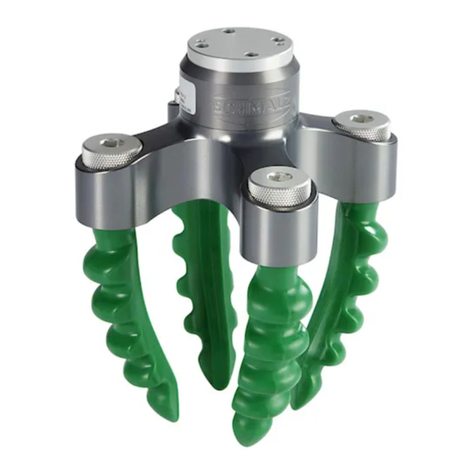
Schmalz
Schmalz OFG operating instructions
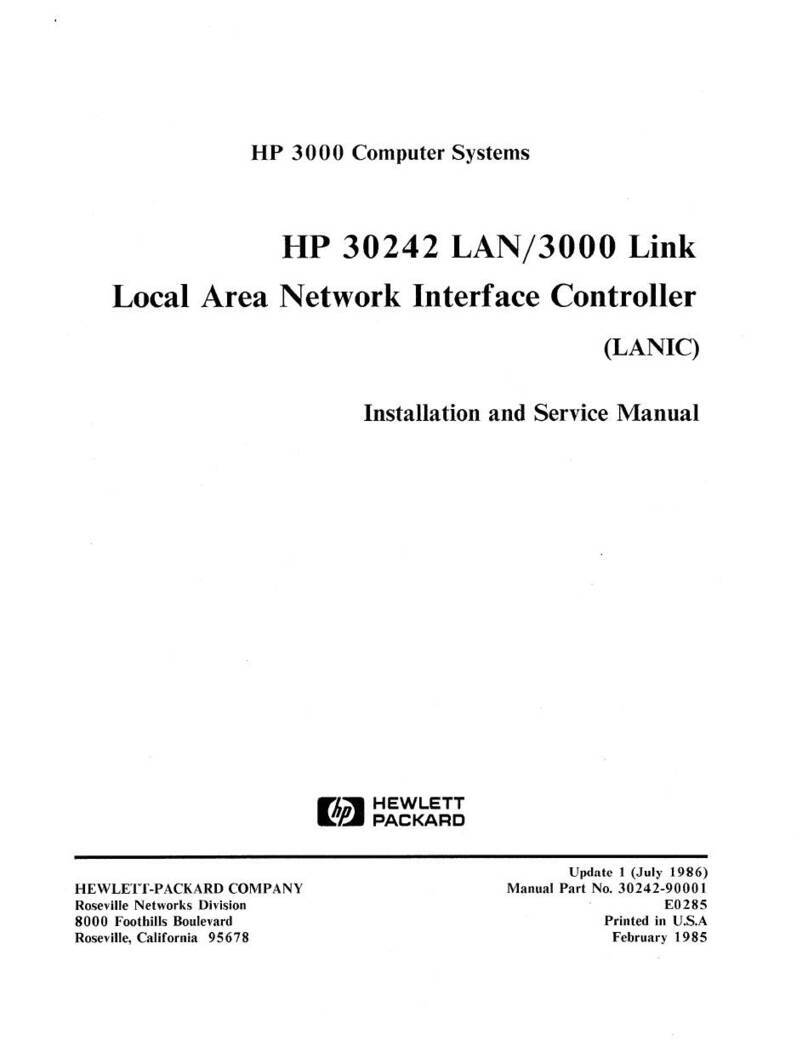
HP
HP 30242 Installation and service manual
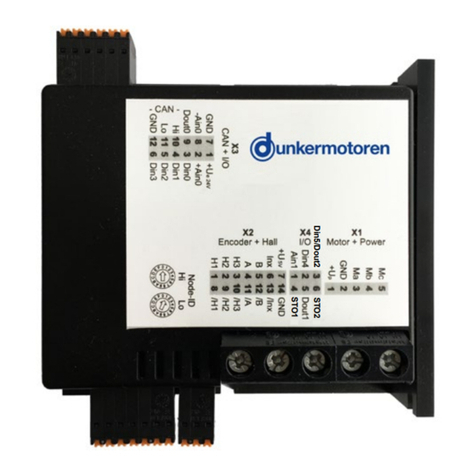
Ametek
Ametek Dunkermotoren BGE 6060 A EC Operation manual

Dräger
Dräger Regard 3900 Installation, operation and maintenance guide