Blacet Research VCO2100 User manual

Page 1
VCO
BLACET RESEARCH MODEL VCO2100
Voltage Controlled Oscillator Module
User & Assembly Manual
Rev B PCB
Blacet Research 94502 Stock Drive Lane, Lakeview, OR 97630
Contents Copyright. Rev 2-2014
Reproduction by any means including the Internet prohibited without permission.
This document contains proprietary and trade secret information of Blacet Research and is provided
as a service to the module owner. Any unauthorized duplication or transferral may violate trade secret laws.
Contents subject to change without notice.

Page 2
Introduction
The VCO2100 is a highly accurate and stable voltage controlled oscillator module that responds to a one volt per octave
control input.
Five different waveforms are generated across the ultra audio, audio and sub audio range. Sine, triangle, sawtooth, pulse and
VC wave are all simultaneously available. The VC wave uses a control voltage to morph from a triangle wave to various
highly distorted square waves. The pulse waveform has a width CV input which can be swept from extinction through
square to extinction.
The sawtooth wave has been especially designed for optimal use with the Mini Wave Module.
Frequency Modulation can be applied to the FM input which can be switched to a linear or exponential response and AC
or DC coupling. This input has an attenuator.
The sync input can be used with a pulse wave to have oscillators lock together when they are close in frequency.
The +/- Octave input allows precision switching up one octave with a CV > +2.5V or down one octave with a CV < -2.5V.
An on board tune button connects to the + octave circuitry, providing a convenient resource for calibration.
Frequency Control
Voltage Inputs
Synchronization Input
(Square or pulse)
Frequency
(Coarse)
Frequency
Modulation
Response, AC/DC
Frequency
Modulation Amount
VC Wave Shape
Pulse Width
Control Voltage Input
VC Wave
Control Voltage Input
Sine Wave Output
Triangle Wave Output
Sawtooth Wave
Output
Frequency
(Fine)
Pulse Width
(Center=square
)
+/- Octave Switching
Frequency
Modulation
Input
VC Wave Output
Pulse Wave Output

Page 3
Controls and Operation
Warm Up Time: All analog oscillators will drift a few Hertz as power is applied. This is due to the individual components
warming up at different rates as voltage flows through them. A portion of this voltage is converted to heat and will effect
the actual part values in a small way. Allow at least five minutes for warm up and resist the urge to tweek the Fine tune pot
during this time. After warmup, a very minor adjustment of the Fine tune knob may be necessary.
Freq. (coarse tune) and Fine Tune: Freq. sweeps the entire usable range of the VCO. Fine covers about one-half octave.
Sync In: Insert a pulse or square wave from another VCO to have the VCOs lock together when they are close in
frequency.
CV 1V/OCT: There are two jacks that allow precise control of the VCO. One of these might typically be attached to a
MIDI-CV converter or a keyboard with 1V/oct output. The other jack can be used for vibrato, for example.
+/- OCT: This jack allows precise octave switching with a +/- control voltage. When the CV is greater than +2.5V, the VCO
will jump up one octave. When the CV is less than -2.5V, the VCO will jump down one octave.
FM Input, Expo/Linear Switch, Level Control Pot: External CV, audio or waveforms from the same VCO can be used for
frequency modulation which causes interesting changes in the output wave. Using the Linear switch setting will result in less
frequency shifting of the VCO. The amount of FM is controlled by the Level pot. The FM input can be directly (DC) or
capacitively (AC) coupled.
VC Wave CV input,VC Wave Output, Wave Pot: At minimum CV in or with the Wave pot turned FCCW, the VC Wave
output is a triangle wave. With increasing CV or pot rotation, the wave will assume a more squarish shape. The wave
modulation circuit uses unsymmetrical diode clipping with green and white LEDs. The CV is designed to be in the range
of 0-10V. Negative control voltages will attenuate the waveform and may be used for envelope functions. You can also
feed any of the VCO waveforms back into the CV input.
PWM CV input, Pulse Wave Output, PWM pot: Applying a +/-5V CV or turning the pot will alter the pulse width from
off at -5V to an increasing pulse width. With no CV and the pot centered, the wave will be a square wave (on time = off
time). Increasing the pot rotation or applying a positive CV will cause the on portion of the wave to increase until it is on all
the time. At this point, no sound will be generated.
Power Input Jack JPWR: A source of regulated +/-15Vdc power must be supplied to this PCB jack to run the module.
Note the current requirements in the “Specifications” section.
Connections to this jack should be made only when the power supply is OFF and the connector must be positioned
correctly on the pins.
As using the wrong supply can cause damage to the unit, please contact us if you have any questions! Do not attempt to use
“wall warts” to power the module.

Page 4
Calibration
Calibration typically is best done with a scope, DMM and frequency counter. Adjusting RT5 and RT6 might be done by
ear. Adjusting RT1 and RT2 can be done by ear using a known accurate keyboard for a frequency reference. RT3 and
RT4 must be adjusted before RT1 and RT2.
Before calibration, power up the module for at least five minutes to allow the circuit to stabilize.
RT3: -1.00V Trim. Connect a voltage less than -2.5V to +/-OCT (J2) (-15V maximum is OK.)
Adjust the voltage at TP1 to -1.000V.
RT4: +1.00V Trim. Push S2 Tune on the PCB or connect a voltage greater than +2.5V to +/-OCT (J2) (+15V maximum is
OK.) Adjust the voltage at TP1 to +1.000V.
RT5: Triangle Symmetry Trim. This trimmer must be adjusted before RT6. Monitor the TRI output (J10) on the
oscilloscope. Adjust RT5 for best symmetry. If you are adjusting by ear, set the trimmer for the purest tone (fewest higher
frequencies).
RT6: Sine Distortion Trim. Monitor the Sine output (J12) on the oscilloscope. Adjust RT6 for best symmetry. If you are
adjusting by ear, set the trimmer for the purest tone (fewest higher frequencies).
RT1: Frequency CV Scale. (Start by setting RT2 (HF) to about 40% of rotation.) Monitor the SAW output (J11) with a
frequency counter. Adjust the Freq and Fine front panel pots to about mid point and dial in a reading of 100 Hz. Push the
on board Tune switch (S2). This is near the center of the PCB. The saw frequency should jump up one octave to 200 Hz.
Go back and forth, adjusting RT1 until you get the 100/200 octave.
Note that the actual frequency is not very important; the octave (2X F) ratio is important. If you are tuning by ear, use an
octave on a digital keyboard for reference.
RT2: High Frequency Trim. Set the Freq and Fine controls to about 4 KHz. Push the on board Tune switch (S2). Adjust
RT2 until you get about 8 KHz. Again, you are adjusting for a 2X frequency ratio. This trimmer adjusts for the tendency
of the VCOs higher frequencies to be a bit flat and is not critical.
RT1 and RT2 adjustments will interact a bit; go back and check the RT1 setting.
Specifications
Front Panel Size: 5.25 x 3" W
Module Depth: 4.5”
Input/Output Jacks: 3.5 mm (1/8”)
Frequency Voltage Control: exponential; 1V/Oct.
Frequency Range: 30S to 60 KHz
Waveforms: Sine, Triangle, Sawtooth (pos. ramp), Pulse, VC Wave
CV Range: Frequency, PWM, +/- OCT: +/-5V. VC Wave: 0-10V
Output Level: +/-5V nominal
Power: +/-15 Vdc @+55/-55 mA
Circuit Description
The VCO2100 is basically a device for generating audio waveforms in response to an analog voltage level. What makes
this task somewhat challenging is the industry requirement that the response to a voltage input is an output frequency that
changes one octave (a doubling of frequency) for every one volt change. This type of response curve is exponential, which
allows a huge frequency range to be covered. Since the human ear is very sensitive to changes in pitch, the VCO must also
be very stable and track very well. It is up against digital keyboards in most studios that use very stable crystal controlled
microprocessor based tone sources.
What makes the analog VCO worth designing is the sound, which is noticeably “warmer” and has more character than
most digital sources. The subtlety of tone is one of the key aspects of music.
The classic exponential VCO design dates from the 1960’s and has changed only in subtle ways during the ensuing years.
The basic approach is to convert an input voltage to an exponential current and use that current to charge a capacitor.
Higher voltage equals more current equals faster capacitor charging equals higher frequency. A comparator is used to
sense when the capacitor is fully charged. At this point the comparator switches a JFET, which shorts out the cap and
restarts the cycle. It is easy to see that the resulting waveform is a sawtooth.
Looking at the schematic, we see that one section of op amp U3 is used in a summing mode as a CV mixer. The LT1013
amp is chosen due to it’s low offset and excellent temperature stability. Voltages presented to U3 come from the coarse
and fine tune pots, external CVs, the external FM input, and the OCT +/- circuit. The output of U3 is scaled by R15 and
trimmer RT1. It is also further scaled by R17 and R18, resulting in a voltage to the base of Q1 of about 18 mV per one volt
of input voltage.
Note the +10 and -10V reference voltages used for the coarse and fine tune controls and the current source for Q1 based
on U4. These voltages are derived from a very stable reference diode. Typical VCO designs tend to use the power supply

Page 5
rails for reference, with some loss of stability. More on this circuit later...
At higher frequencies, the VCO will tend to run “flat” so an extra amount of current is added into Q1 via D2, R30 and
RT2.
FM (frequency modulation) can be exponential or linear. Linear FM is introduced through the second section of U3,
modulating the emitter current of Q1.
Q1 is a precision matched pair. At low voltages this transistor exhibits an exponential voltage to current conversion curve,
although the response is very temperature dependent. Using a pair reduces the first order temperature dependence. R18,
which is a temperature compensating resistor with a response of 3300 ppm/degree C eliminates the secondary temperature
effect. Any residual source of temperature instability (such as from C5) is eliminated by a thermometer circuit configured
around D3.
The current from Q1 is buffered by U4 and used to charge C5. A comparator, U6, senses when the cap is charged and
triggers Q2, which shorts out C5 and dumps the cap current. The resulting waveform is a sawtooth, which is level shifted and
buffered by U4 to +/-5V.
The pulse wave is generated by using U5 as a comparator on the sawtooth to provide an output based on the PWM CV from
R5 and J8. Various +/- CVs will trigger a comparator output at various points on the rising ramp of the sawtooth. This equals
a full spectrum of pulse waves from very narrow, through square wave to very broad.
The basic sawtooth is further processed by adding together mirrored versions of the saw to provide a triangle output. This
circuit is provided by Terry Michaels, a contributor to Electronotes and Grant Richter, of Wiard.
The triangle is processed by a classic overdriven VCA circuit to provide a sine wave. While an LM3080 is typically used
here, we need a VCA section for the VC wave, so one half of an LM13600 (U8) is used instead.
The VC wave is derived from the triangle wave by driving a diode clipping circuit through a VCA. Voltages from the Wave
CV and the Wave pot control the VCA (U8) which drives U7. Two green LEDs are used for the positive swing of the input
and a white LED is used for the negative swing. The LEDs have audibly different clipping characteristics which result in an
interesting array of triangle to distorted square waves as the CV increases. Using two green LEDs results in approximately
symmetrical clipping levels. Typical clipping for each green is 1.6V; for the white LED, it’s about 2.5V.
Reference diode D1 supplies 5.00V, which is scaled and inverted by two sections of U3 to provide stable reference voltages
of -10V and +10V. U3 is a TL054 op amp which has low offset and good temperature stability. These voltages are further
scaled and inverted to provide +1.00V and -1.00V. These voltages are used to switch octaves.
The Oct +/- input (J2) drives a dual comparator circuit based on two sections of op amp U5. This senses voltages greater
than +2.5V and less than -2.5V. The comparators drive the MAX365 quad analog switch which is used to insert +1.00V or -
1.00V into the VCO CV summer, resulting in a one octave jump up or down. Two switch sections are paralleled in each case
to lower the effects of the switch on resistance. Accuracy is further ensured by trimming the +/-1.00V voltages post analog
switch.
A bonus feature of the octave switching circuitry is that it can be a great help in scaling the VCO (trimmers RT1 and RT2).
The on board Tune pushbutton S2 provides a one octave up jump. This eliminates having to provide an external precision
voltage source for trimmer adjustment; saving time in production and for the kit builder.
PCB connector Jpwr supplies power to the circuitry. Protection against reverse supply or over current conditions are
provided by PS1, PS2, DA, and DB. The PS devices are resettable fuse-like devices that go from a very low resistance to a
very high resistance when subjected to high current flow. PS1 and PS2 are rated at 100 ma. If the supply connections are
reversed, DA and DB will essentially short circuit the supply, causing PS1 and PS2 to rise in resistance and limit the current
flow to minimal levels. A short on the board will also cause current limiting. When the fault conditions are removed, PS1
and PS2 will return to normal operation.
Kit Assembly Procedures:
• Caution! All front panel components are PCB mounted and must be aligned precisely if you ever hope to get the
front panel mounted. Be sure to follow the advice presented when mounting these components! When checking
alignment, close one eye. This will make your visual field 2D instead of 3D, which makes it easier to see alignment
problems.
• Caution! Use protective eyewear during assembly, especially during soldering and lead clipping operations.
• Caution! Solder contains lead, a toxic metal that can build up in the body if ingested. Be sure to wash your hands
after handling solder and avoid eating or touching your face while using it. (Lead traces left on your face or
hands may find their way into your mouth and this is the most common way lead enters the body.)
•The key piece of advice is to take your time, be sure you put the correct part in each location, and solder it

Page 6
correctly. Read thru this manual and check your parts against the Parts List before starting!
•Because this is a double sided board, removing parts will be more difficult than with a single sided board since
solder flows through the plated through holes. The usual method for replacing a part on a double sided board
involves cutting all the legs of the component and desoldering the pins one at a time, using a solder sucker. This
minimizes possible board damage due to excess heat. Needless to say, since you will be destroying the component,
you want to get things right before you solder!
•If you make a mistake or are missing a part and need a replacement component, please e-mail us. Include your
order invoice number and name.
•If you have not soldered a double sided board before, be aware that solder will flow through the plated board holes
and out onto the opposite pad. Use only as much solder as required to make the connection look good on both
sides of the board. A little care now will insure a long lasting reliable module.
•Do your assembly work on a soft towel or a few layers of paper towel. This will protect components from impact
and make picking up small parts easier. Be careful when opening part bags (use scissors) as small parts can fly off a
considerable distance!
Tools
•You will need a 15 to 25 watt soldering iron with a fine pointed tip.
•We very highly recommend Kester 331 as this can be cleaned up with warm water and solders very nicely.
Connections off the board or to the board that are inconvenient to clean may best be made with a “no clean”
solder such as Kester 245. Rosin core solder can be used but is really somewhat old fashioned and flux removal can
involve harmful chemicals. We build our boards with the 331 and 245 products and cannot guarantee results with
rosin core solders.
•You will also need a lead bender, needle nose pliers, side cutters, and a nut driver set or pliers. A DMM will be
necessary for checking voltages.
PCB Assembly
Use 331 solder.
Resistors:
• Insert all the resistors, bending the legs at 45 degrees.
•Start with the three 100K matched resistors, R8, R9, R10. These are in a separate bag.
• Note that R57-R61 and R27, R28 are located on the lower half of the -2 PCB. R62, R63 are on the upper right
of the -3 PCB.
•Check the values. Did you have any left over? Then solder in place. The resistor can be inserted in either direction,
although a good practice is to orient the color code so that it can be read from left to right along with the PCB
silkscreen. This simplifies checking the values and later troubleshooting/repairs. Don’t get confused over similar
color codes.
•The color code chart shows how to identify resistor values. The exact hue of the colors can vary a bit, so be sure
that you pick the right value. Using the parts list and putting the resistors into groups of the same value can help
clear up any confusion. The suffix “K” is used to denote thousand and “M” stands for million. A 56K resistor is
thus 56,000 ohms. The 1% resistors are blue in color and have 5 color bands, with the right one always being
brown, indicating “1” % tolerance. The rest of the color bands are read in the same fashion as the 5% resistors
with there being one more digit to consider. For example, a 75K 1% resistor reads from left to right: violet (7),
green (5), black (0), red (2 zeros) or 75000. A possible problem with this system comes when the first digit is 1
(brown). Since the tolerance is also brown, make sure that you don’t read the resistor the wrong way!

Page 7
Tolerance (gold = 5%, brown = 1%)
Multiplier (# of 0ʼs)
2nd digit
1st digit
Resistor Color Codes
Black = 0
Brown = 1
Red = 2
Orange = 3
Yellow = 4
Green = 5
Blue = 6
Violet = 7
Gray = 8
White = 9
3rd digit (only on 1% resistors)
For example: green (5), blue (6), orange (3 zeros), gold
(5%)= a 56000 or 56K ohm, 5% tolerance resistor.
For example: violet (7), green (5), black (0), red (2 zeros),
brown (1%)= a 75000 or 75K ohm, 1% resistor.
Diodes: Insert and solder the diodes: Note the orientation.
PCB Symbol
Diode
Resistor Networks: Observe the orientation.
IC Sockets: These will have a keyway or dot (pin 1) to indicate the correct orientation. Insert the socket and bend one leg
at two opposing corners 45 degrees or so. Solder these two pins and check to see that the socket is flush with the board.
Then solder all the pins.
Jacks: Load the 12 jacks into the PCBs. Since these will have to go through the front panel later, precise mounting is a
must. Carefully insert all jacks, noting that J12 goes on the solder side of the board.
•Tip: Keeping the jacks in the board can be challenging but one useful trick is to bend the front pin forwards just a
bit before inserting. Install the front pin first, pushing a bit forward to get the rear pins in place.
Solder only the front pin while applying a bit of pressure to the PCB in the vicinity of the jack. Do all the jacks and check
the mounting before soldering any other pins. Close one eye and sight down the row of jacks. Each jack must be flush to
the board and have no tilt from front to back. When everything looks perfect, solder the other pins.
Capacitors: (Cap). There are several different types. You may need a magnifier to read the code on the small ceramics.
• Note that the electrolytic type must be properly oriented. Insert the side which has the longer lead closest to the
“+” on the silkscreen. The opposite side of the capacitor should have a row of “-”.
Polyswitches: (PTC) PS1 and PS2. These have kinked legs.
Power Input Jack: JPWR; note the orientation as shown by the silkscreen.
Test Point: Loop a piece of resistor lead trimming and insert at “TP-1”. Leave a loop above the PCB and solder.
Reference Diode: D1. Note orientation of the T0-92 package.
Trim Pots :Install RT1, the 20T trimmer with the brass screw closest to the silkscreen dot. Install the other trimmers.
Transistors: Install, noting the correct orientation.
For the LS318 transistor: Q1, TO-72 (metal can, six leads), note the tab location on both the part and the PCB silkscreen.
Use a pair of small needle nose pliers to form the leads to fit the six holes on the PCB, Start with a 45 degree bend close to
the body (about .050 to .075) and then a right angle bend as needed to space the legs wide enough for the holes in the
PCB. Insert the transistor, making sure it is parallel to the board before soldering the outer four legs only.
Locate R18, the 1K temperature compensating resistor. Bend the legs to .4” and insert into the board so that it sits on top
of Q1. Carefully snug down the leads and solder along with the remaining two legs of Q1.
LEDS: Observe orientation as shown for the diodes above. Position above the board by about 0.2”.

Page 8
Pushbutton Switch: Install at S2.
Wash the PCB in warm water and rinse with distilled water. Allow to dry. Inspect all work very carefully.
Triple check your work.
Are all the solder connections done well? (A magnifier helps here).
Any shorts, cold solder joints or solder bridges?
Are all the electrolytic capacitors, diodes, transistors, etc. oriented properly?
Carefully snap apart the 4 boards.
*** Use 245 solder for the remaining assembly steps. ***
Slide Switches: Install the two switches. Solder one leg and double check that they are absolutely flat to the PCB. Finish
soldering.
Pots: Insert the five pots on the pcb and solder one mounting leg on each pot. Holding the PCB with one hand, remelt each
solder joint and press the pot down onto the PCB. With one eye closed, sight down the row of pots making sure they are
even and flat on the board. Solder the rest of the pot pins.
Angle Brackets: Mount the four angle brackets to the top front edge of the -1 and -2 PCBs with a 4-40 screw going
through the bottom of the board, through the unthreaded opening on the bracket and into a kep nut. Keeping the bracket
to the back of the board, tighten securely. Check the alignment and adjust using a pair of pliers so that the bracket is square
with the edge of the PCB.
ICs:
Install the ICs now as they will be less accessable once the PCBs are mounted to the front panel. Make sure all the legs are
straight and are actually going into the socket before seating the IC. Observe correct orientation.
Use a static free work station or wrist strap when installing the ICs.
Front Panel:
•Work on a soft surface such as a towel.
•Use the black screws to attach each board to the front panel.
The four PCBs are labeled “VC02100-1, -2 , -3 and -4”. The first three are mounted to the front panel in that order, left to
right.
Mount the tiny -4 PCB to the -2 PCB with three pins of the 1.2” header and the two .375 snap-in spacers.
Mount the -1 PCB to the front panel. Insert the two 8 pin solid headers into the board; do not solder.
Mount the -2 PCB, lining up the headers with the front row of holes on the -2 board.
Tighten all front panel screws. Check the operation of the two slide switches. Solder the headers and trim.
Take the ribbon cables and bend in half. (See next page). Open up the bend a bit and make a right angle bend on each end
of the cables at .25 to .375” from the end. Insert the cable into the rear set of holes on top of the -2 board and solder.
Mount the -3 board. Insert and solder the other end of the ribbon cables into the -3 board.
•Pots are mounted with a washer and hex nut.
•After assembly is completed, press on the five knobs.

Page 9
Testing
Connect a +/-15 V bipolar regulated power supply to the board. Make sure that the connector is properly positioned on the
header. Do not make the power connection to the board with the power supply turned on. These measures will help avoid
damage to the unit!
Use your DMM to monitor the +15V supply, using the left side of diode DA near the top of the power connector for
common and the right side for +15V.
Apply power. If your DMM does not indicate 15V or so, remove the power.
If +15 is present, check the -15 at the right side of the bottom diode DB under the power connector.
Check the ICs carefully to see if any are hot (they should not be). Are there any funny smells? If anything seems amiss,
remove the power.
Calibration
See the procedure on page 4.
Troubleshooting, Repair, Warranty
Most problems are caused by assembly errors.
Don’t panic!
Take a break, then check solder joints for good connection (no “cold” joints?), check for a blob of solder causing a short,
check all component locations and polarities, and check for the possibility of a broken trace or a hairline short caused by
under etching of the PCB, especially around the pots.
If you encounter problems that you can’t solve, contact us, preferably via e-mail with a description of the problem. Let us
know what does and does not work. We can then help you get your module working. We can also fix modules mailed to us
for a minimum fee of $29 (if not covered by warranty). Contact us for an RMA before shipping.
The parts contained in this unit have been carefully selected and tested. They are guaranteed for one year from the date of
purchase. If you believe that you have a defective part (or if you have a part missing), contact us so we can provide you
with a replacement or repair. Include your name and invoice number.
Store this Manual in a secure location and never, ever throw it away! It is the best information available for your
revision of this module. Manuals must be transferred to the new owner anytime you sell a module.

Page 10
We reserve the right to void the warranty or refuse to service any module that has been built with parts not supplied by us,
modified in any way, subjected to abuse, or damaged beyond repair.
Assembly Documents
•Parts list
• Schematic
•PCB phantom view
Table of contents
Popular Control Unit manuals by other brands
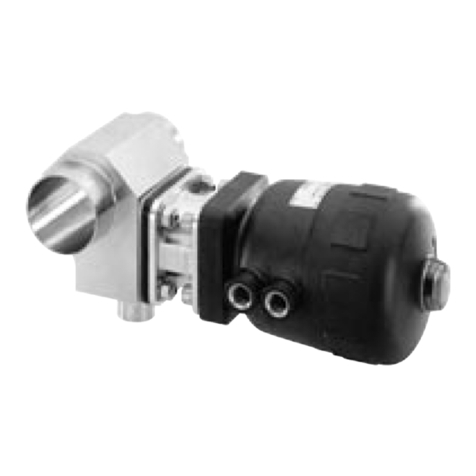
Burkert
Burkert 2031 instruction manual
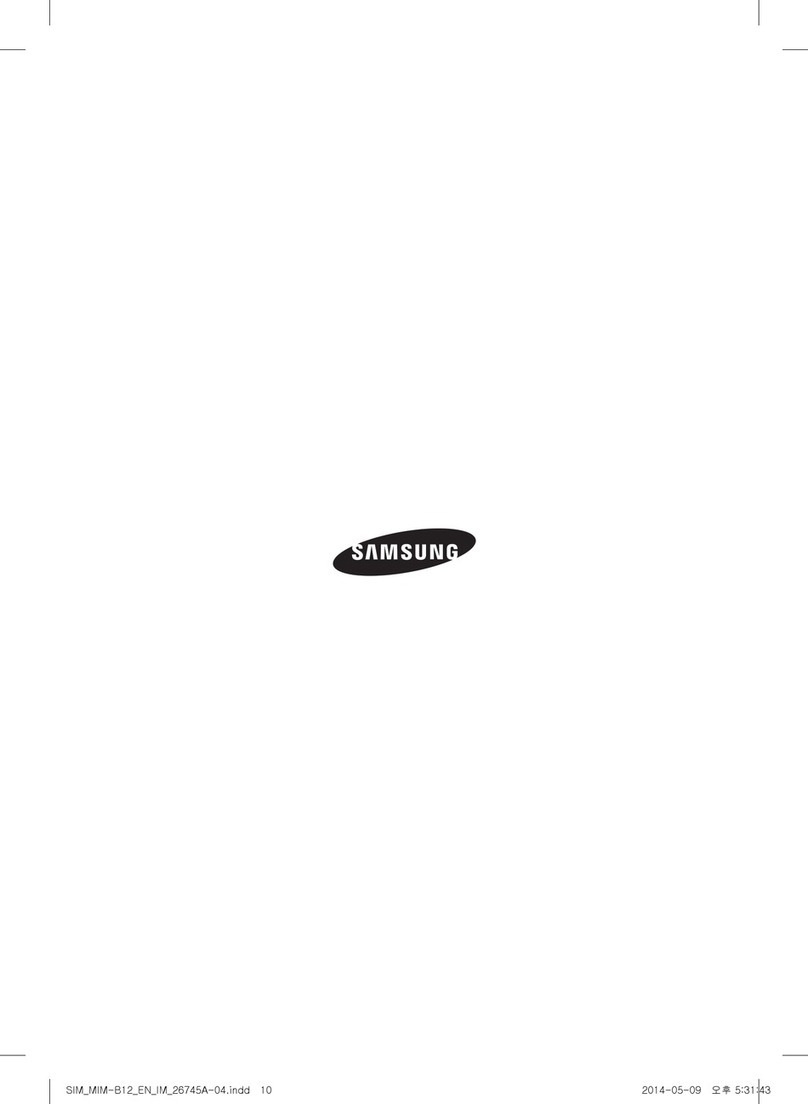
Samsung
Samsung MIM-B12 installation manual
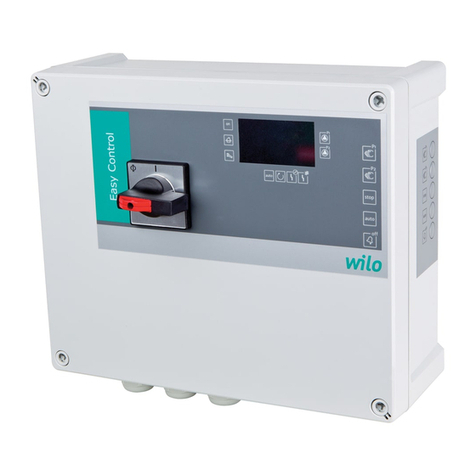
Wilo
Wilo Easy Control MS-L 1x4kW Installation and operating instructions
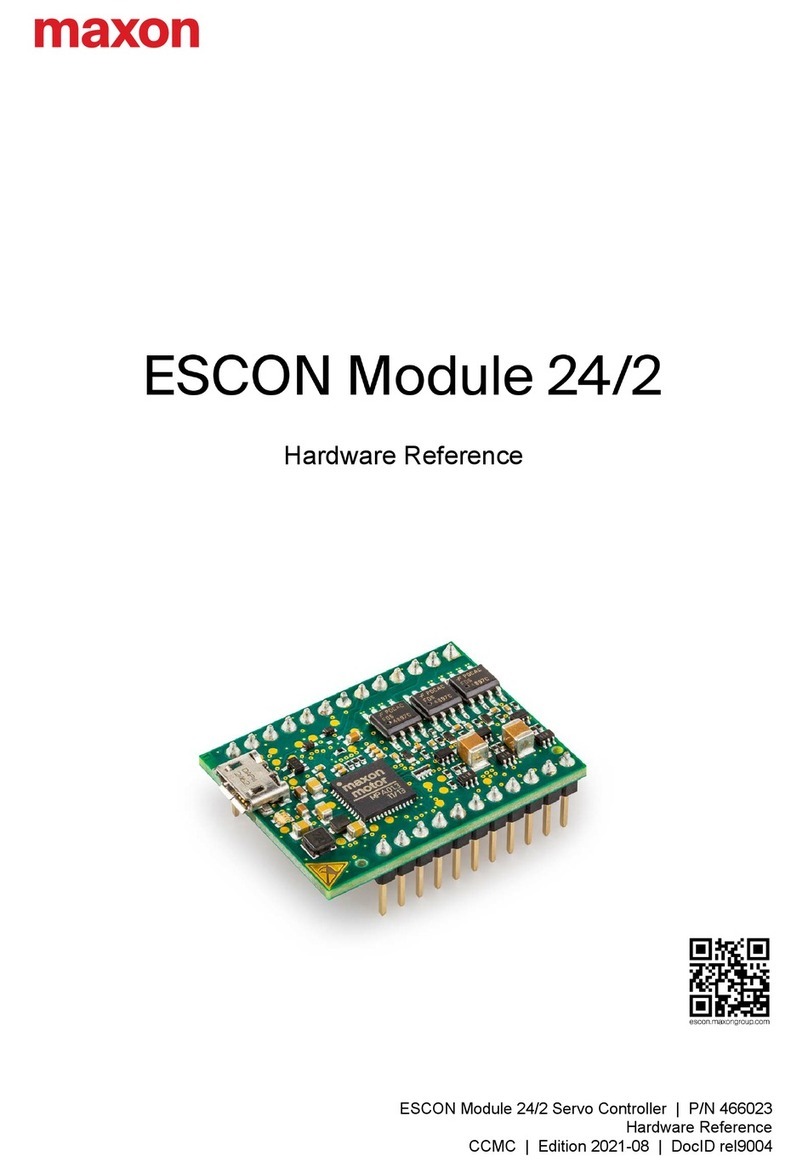
Maxon
Maxon ESCON 24/2 Hardware reference
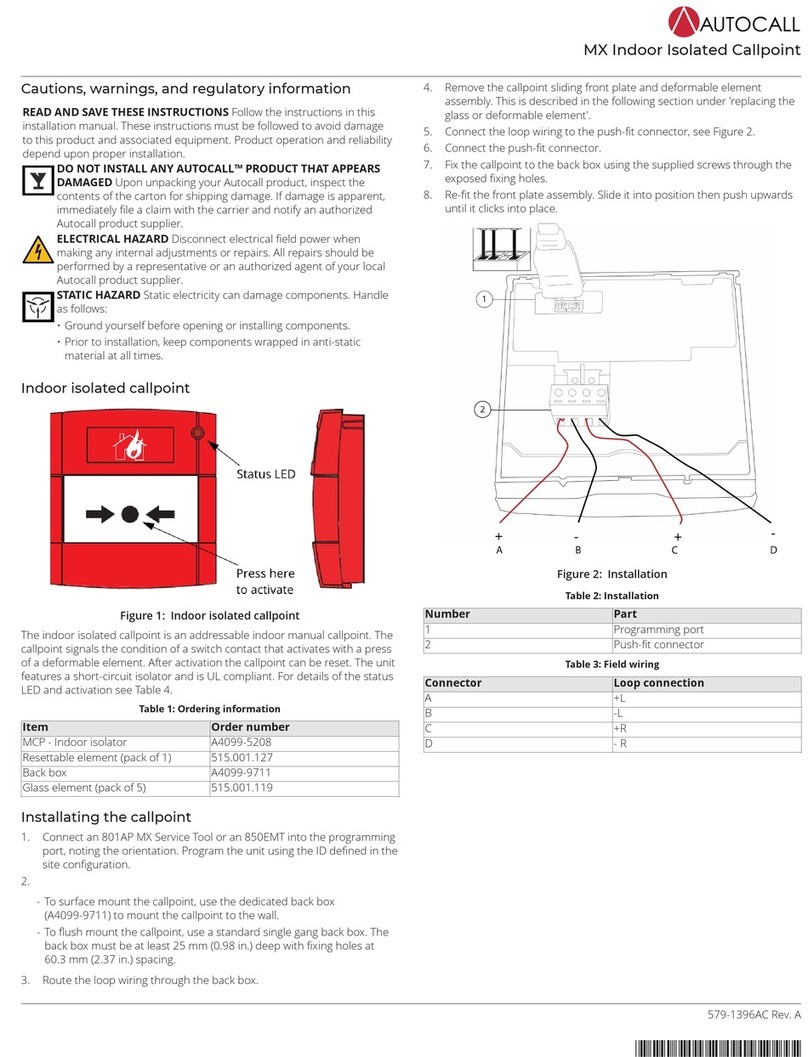
Johnson Controls
Johnson Controls Autocall MX Indoor Isolated Callpoint quick start guide
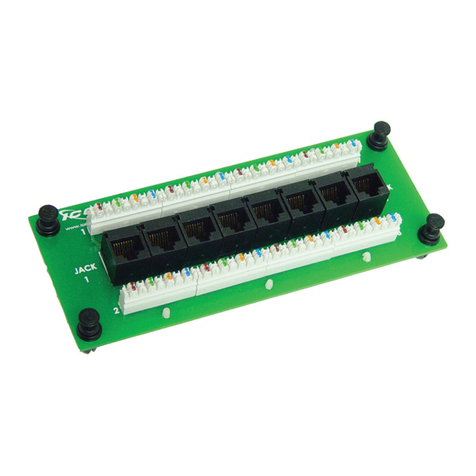
ICC
ICC CAT 5e quick start guide