Blichmann BeerGun Installation instructions

Blichmann Engineering, LLC 2016 BeerGun Owners Manual NEW-V1
For replacement parts visit blichmannengineering.com
1
BeerGun®
Bottle Filler
Assembly, Operation & Maintenance
Congratulations on your purchase, and thank you for selecting the BeerGun® bottle filler from Blichmann
Engineering™. We are confident that it will provide you years of service and many gallons of outstanding beer.
This manual will familiarize you with the assembly, operation, and maintenance of the BeerGun® bottle filler.
The patented BeerGun® is the lowest foaming and lowest oxygen pickup filler on the market achieving
dissolved oxygen levels as low as massive automated commercial bottle fillers! Rest assured that your beer will
stay as fresh as the big craft breweries beer!
IMPORTANT!!
**** PLEASE READ THOROUGHLY PRIOR TO USE FOR IMPORTANT SAFETY INFORMATION ****
Warning:
Sections labeled “Warning” can lead to serious injury or death if not followed. Please read
these thoroughly and understand them completely before use. If you do not understand
them or have any questions, contact your retailer or Blichmann Engineering™
(www.BlichmannEngineering.com) before use. Do NOT at ANY time operate the product
until you thoroughly read and understand these instructions!
Caution: Sections labeled “Caution” can lead to equipment damage or unsatisfactory performance of
the equipment. Please read these sections thoroughly. If you have any questions, contact
your retailer or Blichmann Engineering™ (www.BlichmannEngineering.com) before use.
Important:
Sections labeled “Important” are critical to the proper performance and life of the product.
Assembly:
The BeerGun® comes fully assembled. However, prior to use it is recommended to disassemble for cleaning and
sanitizing.

Blichmann Engineering, LLC 2016 BeerGun Owners Manual NEW-V1
For replacement parts visit blichmannengineering.com
2
Prior to Assembly / Disassembly
Ensure you have all the parts included in the table below. Please contact your retailer if any parts are missing.
Name
Part Number
Qty
BeerGun® Handle Assembly
BE-000576-00
1
Valve seat clip
BE-000526-00
1
Valve seat
BE-000578-01
2
Beer trigger
BE-000524-02
1
Spring
BG-006-01
1
Beer tube
BG-002-06
1
CO2tube
BE-000577-03
1
Beer Hose – 10 ft anti-microbial
BE-000721-00
1
CO
2
Hose – 5 ft
BE-000703-00
1
Black Liquid Ball Lock
BE-000639-00
1
Brush
BG-008-00
1
Storage case
BE-000941-00
1
Note: The BeerGun® requires two outlets on your CO2tank as shown in Figure 9 below. Either a dual regulator
or a “Y” fitting setup will suffice. Regulators and “Y” fittings are not included with the product, but are available
through your retailer.
Caution: Do not disassemble until you have fully read this manual. Do not use excessive force on any of
the parts during assembly or disassembly or they may be permanently damaged. The sheet metal valve clip
and the beer trigger are made of heat-treated stainless steel, but can still be deformed, and the tube grooves
can be permanently damaged or bent.
Do NOT use any cleaner or sanitizer containing chlorine such as bleach. Over time, this will pit and erode
stainless steel. Any other non-chlorine sanitizer is acceptable to use. IodophorTM or StarSanTM both work very
well and do not require rinsing. In any case, a few minute soak is all that is needed to properly sanitize the
product. Extended soaking can lead to damage.
Prior to assembly, completely disassemble the filler and wash with a mild detergent. The included tube brush
makes it easy to clean the interior of the beer and CO2tubes. Rinse all parts well and soak in your preferred non-
chlorine, no-rinse sanitizer, including all the hoses and keg connectors.
CO2tube
Beer tube
Spring
Beer Trigger
Valve Seat and Clip
Handle Assembly

Blichmann Engineering, LLC 2016 BeerGun Owners Manual NEW-V1
For replacement parts visit blichmannengineering.com
3
Assembly:
Step One:Install the 3/8” diameter stainless CO2tube into the top of the
grip. The tube is held in place with an o-ring located inside of the grip. Push
the tube until it hits the stop inside the grip. (Figure 2)
Step Two: Slide the smaller diameter (1/4”) beer tube inside the CO2tube
and through the hole in top of the grip. (Figure 3)
Step Three: Slide the spring onto the CO2tube and then slide the beer
trigger onto the tube. (Figure 4)
Step Four: Install the small black silicone valve seat onto pin of the “U”
shaped stainless beer clip as shown.Then install the beer clip onto the
groove on the end of the CO2tube. (Figure 5)
Step Five:Pull the beer trigger over the top of the grip and snap the slot
into the groove of the beer tube. (Figure 6)
Fig. 2
Fig. 3
Fig. 4
Fig. 5
Fig. 6

Blichmann Engineering, LLC 2016 BeerGun Owners Manual NEW-V1
For replacement parts visit blichmannengineering.com
4
Step Six: Slip the 10ft length of 3/16 ID beer hose onto the end of
the beer tube about 3/8” as shown.Sliding it on further makes it more
difficult to remove and is unnecessary for sealing. Install the black
liquid ball lock connector to the other end of the hose. (Figure 7)
Step Seven: Connect the CO2hose to the fitting on the rear of the
grip. A snug fit is all that is needed – take care not to overtighten this
fitting. (Figure 8)
Step Eight: Connect the CO2hose to the regulator “Y” fitting or to the
second regulator as shown. (Figure 9)
If you have a dual regulator setup, it is convenient to use one regulator
to purge bottles at 15-20 PSI, and the other regulator to pressurize the
keg for dispensing.
3/8”
To Keg
To CO
2
Valve
Fig. 9
Fig. 8
Fig. 7

Blichmann Engineering, LLC 2016 BeerGun Owners Manual NEW-V1
For replacement parts visit blichmannengineering.com
5
Operation
Sanitize keg posts with a spray bottle of sanitizer and install ball lock connector. Set CO2
regulator to ½ of the normal dispensing pressure (approximately 6 psi) and open the
pressure relief valve to reduce keg pressure to new setting.
TIP: While you can fill bottles at the full dispensing pressure to fill faster, the lower setting
generally leads to less foaming (CO2loss) and a more gentle entry of beer into the bottle.
Feel free to experiment with the pressure that works best for you.
Purge CO2line of air by depressing the thumb actuated valve for a few seconds.
Purge the beer line by pulling the beer trigger quickly open until the beer flows through it
and all foam is out of the line. (Figure 10)
Important:Always QUICKLY OPEN AND CLOSE the beer valve to prevent foaming.
Insert the stem of the filler all the way to the bottom of the bottle as shown. Depress the
CO2valve for about 5 seconds to purge the oxygen out of the bottle. (Figure 11)
TIP: The BeerGun® can be used to fill ANY depth of bottle since the tip of the filler does
not need to be depressed to actuate the beer flow. Simply purge the bottle a little
longer and the CO2(heavier than air) will purge the oxygen out of the bottle!
Note: A little CO2 will escape from the gap between the beer tube and top of the grip.
This is normal. The small clearance is needed to ensure smooth operation of the beer
tube.
Holding the bottle at an angle with the stem of the filler in the bottom corner of the
bottle as shown helps to quickly submerge the tip in beer. To fill the bottle,
QUICKLY pull the beer trigger and flood the tip of the filler as quickly as possible to
reduce foaming. After the tip has been immersed in beer, you can return the bottle
to an upright position. (Figure 12)
Fill the bottle until any foam has spilled out of the neck and the bottle is completely
full of beer. Then QUICKLY release the trigger to stop the flow of beer.
For bottles larger than 22oz and growlers, the stem may not reach to the bottom of
the bottle. Keep the bottle at an angle, letting the beer run down the side of the
bottle until the tip of the filler is submerged, then fill as described above.
After the stem of the filler has been removed you will have the perfect fill level.
Place the tip of the BeerGun® into the head space as shown and apply a short burst
of CO2to displace any air that has been drawn back into the bottle. Cap
immediately.(Figure 13)
Tips For Success
Fig. 11
Fig. 13
Fig. 10
Fig. 12

Blichmann Engineering, LLC 2016 BeerGun Owners Manual NEW-V1
For replacement parts visit blichmannengineering.com
6
• QUICKLY open and close the beer trigger.
• Start with about 6 PSI keg pressure. Increase pressure to fill faster, but balance fill speed with foaming.
• Ensure that you use the full 10 ft of 3/16” ID hose to reduce the beer pressure on the way to the filler
• About 5 sec of CO2 flow will purge a 12 oz bottle at 6 PSI.
• Never exceed serving pressure when initially carbonating your beer or you will likely experience
foaming issues
Trouble-shooting
The BeerGun® is a very reliable product with tens of thousands in use all over the world and has been used to
help homebrewers and commercial breweries win countless competitions. Over the years we’ve found the
following things to be the most common issues while using this product.
Excessive foaming: Make sure that you are QUICKLY opening and closing the beer trigger. Throttling the
trigger will cause foaming.
The other common cause of excessive foaming is over-carbonated beer. This happens when you exceed the
normal carbonation pressure to speed along force carbonation. Typically you should use 12-13 PSI at 40 F beer
temperature. The beer will be fully carbonated in 7-10 days. If you wish to speed along carbonation we
recommend the Blichmann Engineering QuickCarb™ which will carbonate your beer in less than an hour
without risk of over-carbonation. If you believe you have over-carbonated your beer, you will need to vent the
excess gas over several days by pulling the pressure relief valve on the top of the keg to vent the pressure. Do
this several times per day until you have vented the excess carbonation.
Bottling highly carbonated or high protein beer styles can be a little challenging. If your normal procedure isn’t
providing the desired result, try chilling your bottles and, if possible, reduce the temperature of your beer to
about 35F – but make sure to remove the CO2ball lock before chilling or you will over-carbonate your beer!
This will help keep the CO2in solution while you fill your bottles.
Beer clip / Beer trigger is loose: very gently bend the tines of the beer clip/trigger back together with pliers, a
little bit at a time until it snaps onto CO2/ beer tube firmly by hand. To prevent beer clip damage, do not pull
unnecessarily hard on the trigger, and do not force the clips aggressively onto the grooves.
we’ll be glad to help!
Maintenance
Disassemble and clean the BeerGun® bottle filler after each use. It is not necessary or recommended to remove
the thumb actuated CO2 lever from the grip. Completely disassemble the BeerGun® bottle filler and soak the
parts and hoses in a hot solution of Five Star Chemical’s Powdered Brewery Wash (PBW) or similar product. Use
the included brush to clean the inside of the tubes. Rinse all parts in hot water and then soak in your favorite
non-chlorine sanitizer. Do not exceed the recommended soaking time – usually just a few minutes is all that is
needed. Hang the hoses to dry overnight and place the other parts on a clean towel. When all parts are
thoroughly dry store them in the convenient storage case for the next use!

Blichmann Engineering, LLC 2016 BeerGun Owners Manual NEW-V1
For replacement parts visit blichmannengineering.com
7
Blichmann Engineering Product Warranty
A. Limited Warranty
1. Blichmann Engineering warrants to the original purchaser that this product will be free from manufacturing defects in material and workmanship for a period of one (1) year from the date of
purchase by the customer. Proof of purchase is required. Blichmann Engineering’s obligation to repair or replace defective materials or workmanship is the sole obligation of Blichmann
Engineering under this limited warranty.
2. This product is for home use only. The limited warranty covers only those defects that arise as a result of normal use of the product and does not cover any other problems, including, but not
limited to, those that arise as a result of:
a. Improper maintenance or modification;
b. Damage due to incorrect voltage or improper wiring by customer;
c. Operation outside of the product's specifications;
d. Carelessness or neglect to operate the product in accordance with instructions
provided with the product;
e. Damaging the tamper label on the product;
f. Damage by over-tightening the fasteners;
g. Failure to follow cleaning and / or maintenance procedures; or
h. Exceeding published operational temperatures.
3. Blichmann Engineering reserves the right to request delivery of the defective component for inspection before processing the warranty claim. If Blichmann Engineering receives, during the
applicable warranty period, notice of a defect in any component that is covered by the warranty, Blichmann Engineering shall either repair or replace the defective component with a new or
rebuilt component at Blichmann Engineering's option.
4. Blichmann Engineering must be notified within seven (7) days of the delivery date of any shipping damage. Customer is responsible for shipping damage outside of this time period. Approval
for return must be provided by Blichmann Engineering prior to any return. Customer is responsible for keeping all original packaging material for warranty returns. Blichmann Engineering is
not responsible for damage from improperly packaged warranty returns, and these repair costs will be the sole responsibility of the customer. Shipping costs for warrantee returns are covered
only for the contiguous United States.
5. Blichmann Engineering’s limited warranty is valid in any country where the product is distributed.
B. Limitations of Warranty
1. Any implied warranty that is found to arise by way of state or federal law, including any implied warranty of merchantability or any implied warranty of fitness, is limited in duration to the
terms of this limited warranty and is limited in scope of coverage to this warranty. Blichmann Engineering disclaims any express or implied warranty, including any implied warranty of fitness
for a particular purpose or merchantability, on items excluded from coverage as set forth in this limited warranty.
2. Blichmann Engineering makes no warranty of any nature beyond that contained in this limited warranty. No one has authority to enlarge, amend, or modify this limited warranty, and
Blichmann Engineering does not authorize anyone to create any other obligation for it regarding this product.
3. Blichmann Engineering is not responsible for any representation, promise, or warranty made by any independent dealer or other person beyond what is expressly stated in this limited
warranty. Any selling or servicing dealer is not Blichmann Engineering’s agent, but an independent entity.
C. Limitations of Liability
1. The remedies provided in this warranty are the customer's sole and exclusive remedies.
2. Except for the obligations specifically set forth in this warranty, in no event shall Blichmann Engineering be liable for direct, indirect, special, incidental, or consequential damages, whether
based on contract, tort, or any other legal theory and whether or not advised of the possibility of such damages.
3. This warranty does not cover, and in no event shall Blichmann Engineering be liable for, travel, lodging, or any other expense incurred due to manufacturing defects in material and
workmanship, or any other reason.
4. Any performance of repairs after the warranty coverage period has expired or performance of repairs regarding anything excluded from coverage after this limited warranty shall be
considered good-will repairs and they will not alter the terms of this limited warranty, or extend any warranty coverage period.
5. Venue for any legal proceedings relating to or arising out of this warranty shall be in Tippecanoe County, Indiana, United States, which courts will have exclusive jurisdiction.
D. Local Law
1. This warranty gives the customer specific legal rights. The customer may also have other rights that vary from state to state in the United States or other countries.
2. To the extent that this warranty is inconsistent with local law, it shall be deemed modified, only to the extent necessary to be consistent with such local law.
This product uses FDA and/or NSF approved food grade materials anywhere the product touches the beverage.
Warning: This product contains or may contain chemical(s) known to the State of California to cause cancer, birth defects, or other reproductive harm.
Table of contents
Popular Water Filtration System manuals by other brands
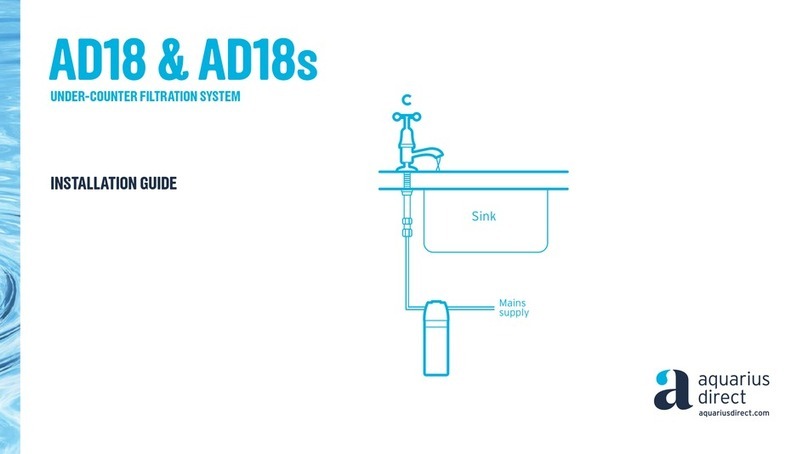
AQUARIUS
AQUARIUS AD18 installation guide
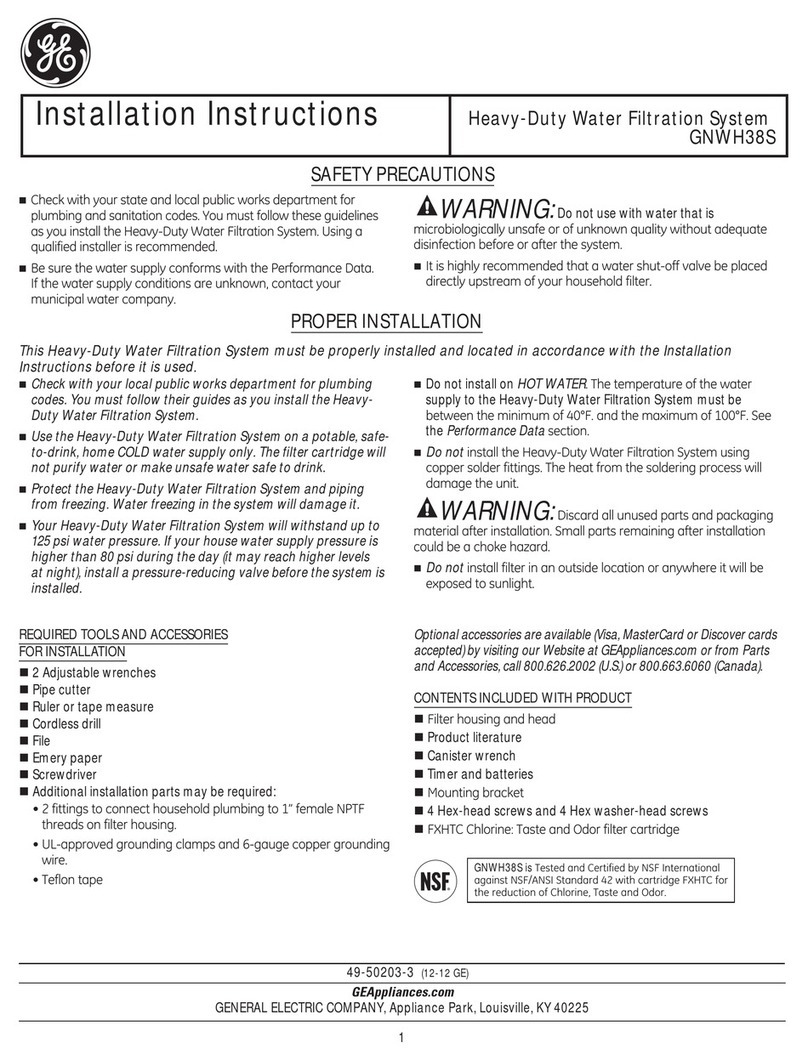
GE
GE GNWH38S installation instructions
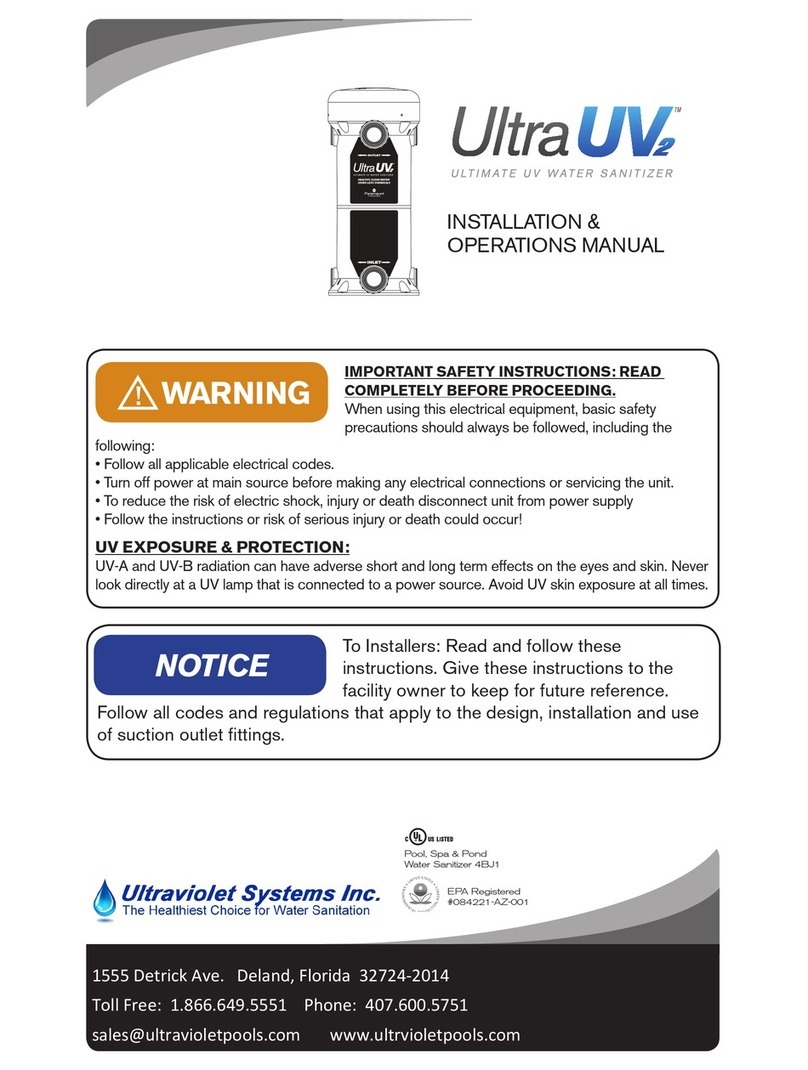
Ultraviolet Sysrtems Inc.
Ultraviolet Sysrtems Inc. Ultra UV2 Installation & operation manual

Bluevua
Bluevua RO100ROPOT-Lite-Bluevua manual

Pool Technologie
Pool Technologie Minisalt 30 user manual
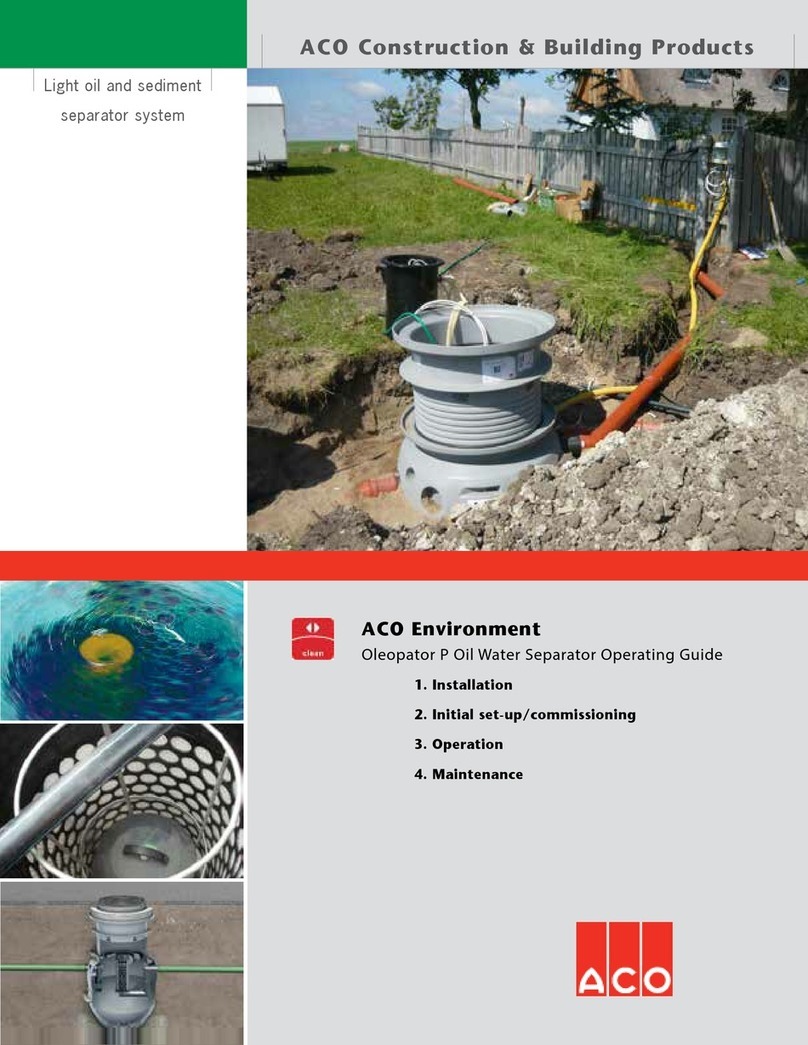
ACO
ACO Oleopator P Series operating guide
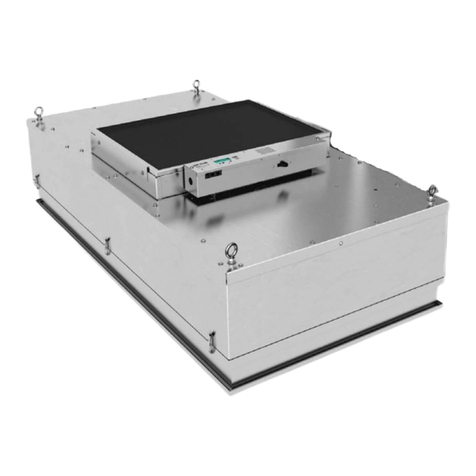
Price
Price FFU series Installation and service manual
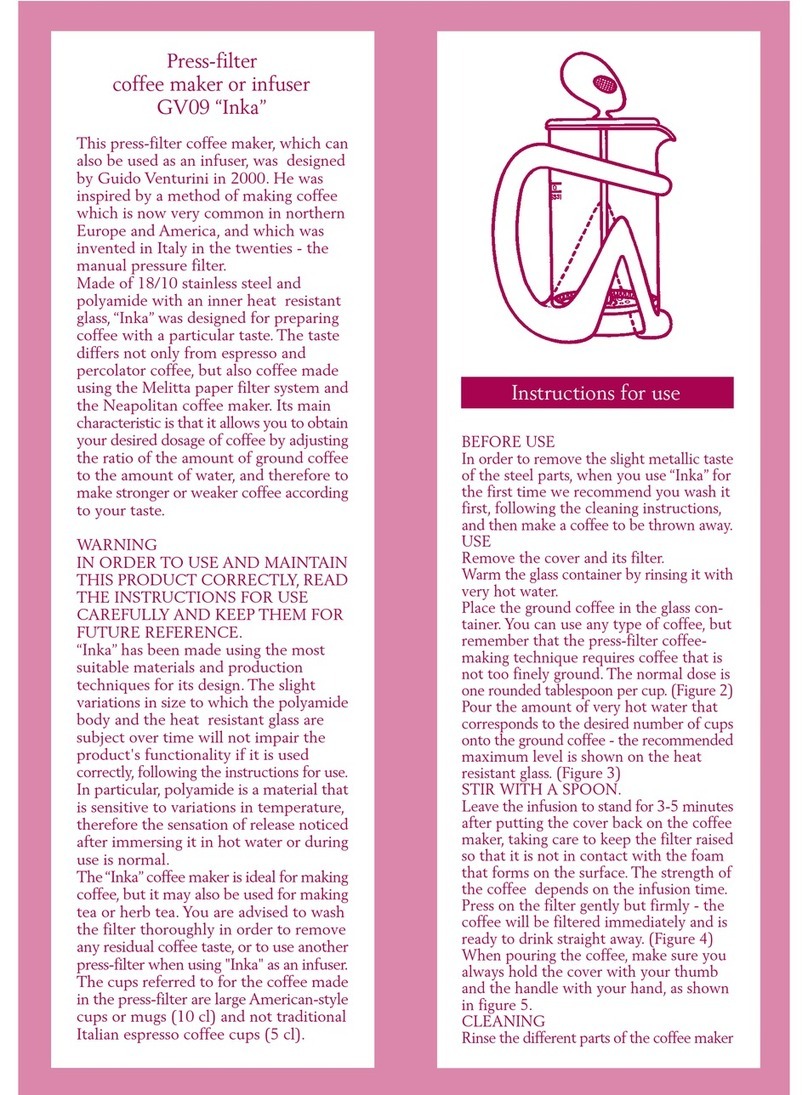
Alessi
Alessi GV09 quick guide

GE
GE GNUL30B Owner's manual and installation
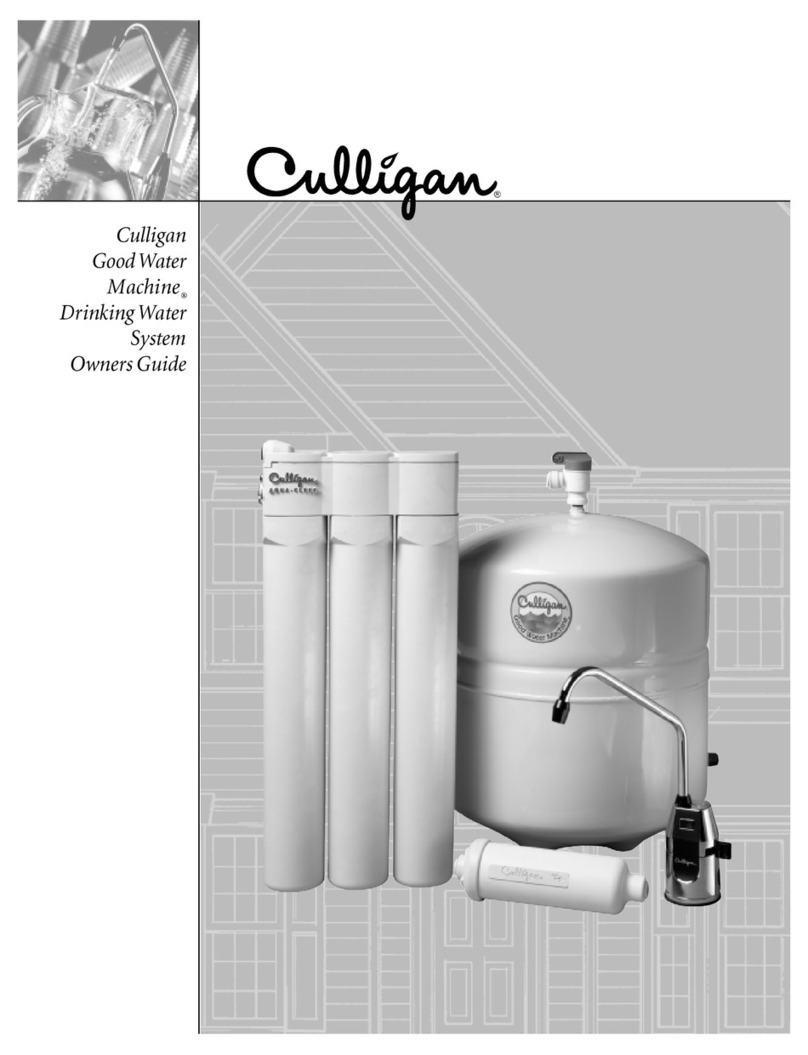
Culligan
Culligan GoodWater Machine DrinkingWater System owner's guide
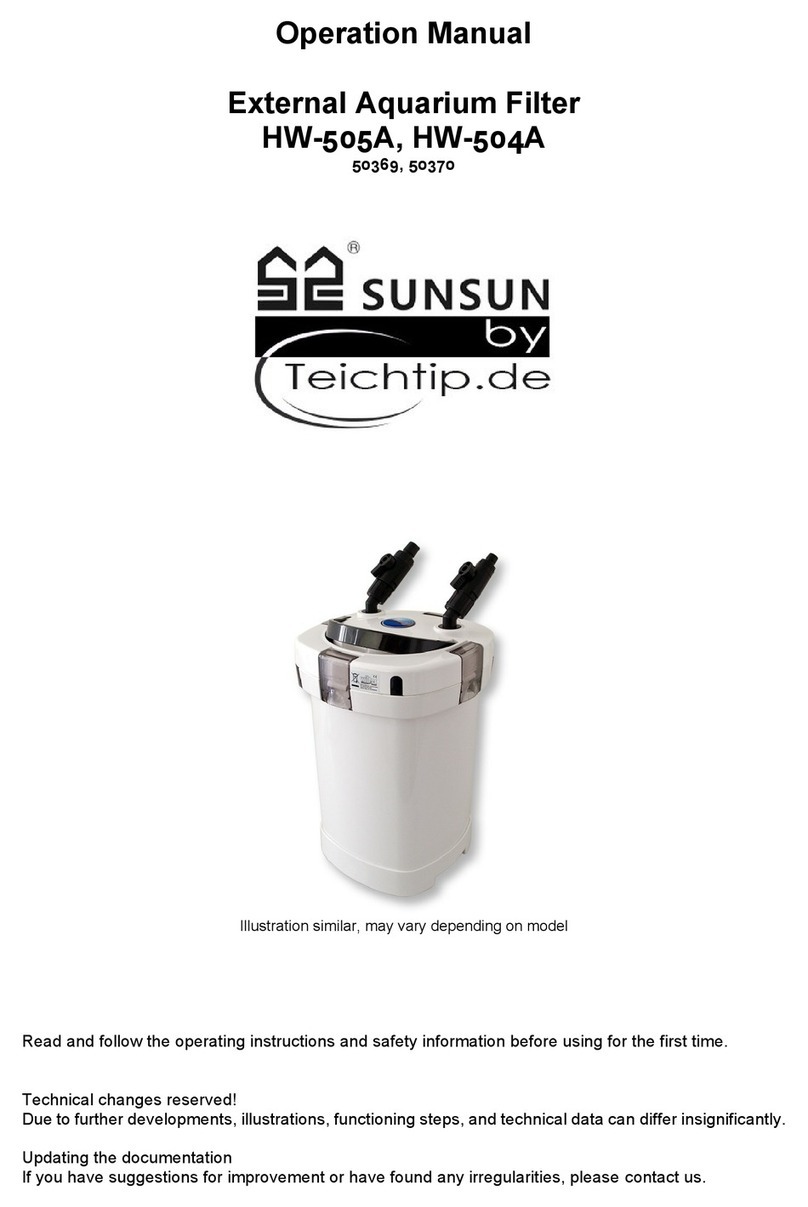
TeichTip
TeichTip SunSun HW-505A Operation manual

Franklin Water Treatment
Franklin Water Treatment PNR1-0948 Installation instructions and owner's manual