Blitz R 15/15 Guide

Instruction Manual and Spare Parts
List
for Mobile Pit Lifts
Original Instruction Manual
Rev. D 118774 05/2019
Type
Serial Number
Date
Blitz R 15/15
R 20/15
R 15/15/15
Blitz X 15/15
X 20/15
X 15/15/15
Blitz M 15/15
M 20/15
M 15/15/15
Junior Jack 0,5 S3
2,0 S3
Master Jack 2,5
4,0


Attach name plate here
Type
Year of construction
Serial Number
EC Declaration of Conformity
under the terms of the EC Directive 2006/42/EC on machines
Name and Address of the Manufacturer
BlitzRotary GmbH
Hüfinger Str.55
78199 BRÄUNLINGEN, GERMANY
This declaration concerns only machines in the condition in
which they were marketed; parts later installed by the user and/or later interventions are not taken into consideration. This declaration
becomes invalid if the product is modified or changed without permission.
We hereby declare that the machine described below
Product designation Pit lift
Series/Type description
Blitz R, Blitz M, Blitz X, Junior Jack, Master Jack
Machine/Serial No.:
Year of construction: .........................
complies with all provisions of the Directive 2006/42/EC on machinery. The machine also complies with the provisions of
Directive 2014/30/EU on electromagnetic compatibility (protection targets were met pursuant to Appendix I, No. 1.5.1 of Directive
2006/42/EC on machinery).
Applied Harmonised Standards
Mobile or portable lifts and related equipment
Safety of machines - Basic terms
Electrical equipment of machines
DIN EN 1494:2009-05
EN ISO 12100:2011
EN 60204-1:2009
DIN EN 349:2008-09 Safety of machines - minimum distances
Other Applied Technological Standards and Specifications
DGUV Regel 100-500 Operation of work equipment
DGUV V3 Accident prevention regulations for electrical installations and work equipment
Representative for the Compilation of the Relevant Technological Documentation:
BlitzRotary GmbH, Hüfinger Str. 55, 78199 Bräunlingen
Location: Bräunlingen
Date : 23.05.2019
______________________
Doris Wochner-McVey
Manager

Instruction Manual for Mobile Jacks
4
Concerning this instruction manual
This instruction manual applies to several assembly series with two different designs:
H
Hydraulic (pneumatic) design
E
Electro-hydraulic design
Text sections marked with the symbols shown above apply only to lifts of the corresponding design.
Position numbers [1] in the instruction manual always refer to the figures and the component overview shown here.
Cross references must be taken into consideration.
Overview of the series
The overview in each case shows a variation of the series.
Component Overview for all Construction Series
[9]
[1]
Piston rod
[7]
[1]
[2]
Controls
[10]
[3]
Relief valve
[6]
[3]
[4]
Manual pump
[2]
[5]
Oil drain screw lifting
[4]
[6]
Compressed air connection
[7]
Oil dip stick lifting / oil filler neck
[11]
[8]
Oil drain screw return
[12]
[9]
Oil dips stick return / oil filler screw
[5]
[10]
Brake
[11]
Operating pressure measuring screw
Series:
Blitz M
[12]
Deflector rollers

Instruction Manual for Mobile Jacks
5
[1]
[9]
[1]
[9]
[8]
[3]
[4]
[8]
[7]
[3]
[7]
[4]
[2]
[6]
[2]
[10]
[6]
[12]
[10]
[12]
[5]
Series:
Blitz X
Series:
Blitz R
[1]
[6]
[1]
[8]
[6]
[3]
[7]
[8]
[8]
[5]
[10]
[4]
[3]
[5]
[4]
[2]
Series:
Junior Jack S3
Series:
Master Jack

Instruction Manual for Mobile Jacks
6
Contents
1Introduction & Basic Safety Instructions ........................................................................... 7
1.1 Intended Use ................................................................................................................................................ 7
1.2 Basic Instructions........................................................................................................................................ 7
1.3 Safety-relevant components ...................................................................................................................... 7
1.4 Explanation of Notes ................................................................................................................................... 7
2Storage......................................................................................................................................... 7
3Transport, Installation, and Assembly ................................................................................ 8
3.1 Prepare Lifting Cylinder for Operation ..................................................................................................... 8
3.2 Install and Assemble the Lift ..................................................................................................................... 8
3.3 Compressed Air Supply............................................................................................................................ 10
3.4 Electrical Connection................................................................................................................................ 11
4Commissioning........................................................................................................................ 11
5Operation................................................................................................................................... 11
5.1 Load-carrying Devices .............................................................................................................................. 11
5.2 Supporting Bridges and A-frames .......................................................................................................... 12
5.3 Advice on hazards ..................................................................................................................................... 13
5.4 Lifting, Lowering, and Transporting Loads ............................................................................................ 14
6Maintenance and Repair ....................................................................................................... 15
6.1 Maintenance intervals .............................................................................................................................. 15
6.2 Perform a function test............................................................................................................................. 15
6.3 Check the compressed air supply. .......................................................................................................... 15
6.4 Check the hydraulic fluid level. ............................................................................................................... 16
6.5 Perform a safety check. ............................................................................................................................ 16
6.6 Changing the hydraulic fluid ................................................................................................................... 16
6.7 Replacing the hydraulic hoses ................................................................................................................ 17
6.8 Bleed the lift ............................................................................................................................................... 17
6.9 Clean or Replace the Pneumatic Control Valve.................................................................................... 17
6.10 Replace the Hydraulic Block ................................................................................................................... 18
7Troubleshooting ...................................................................................................................... 19
8Shutting Down and Disposal ............................................................................................... 19

Instruction Manual for Mobile Jacks
7
1Introduction & Basic Safety Instructions
Blitz lifts are the result of long years of experience. The high quality standards and the superior
concept guarantee you reliability, long fatigue life, and efficiency. In order to avoid unnecessary
damage and hazards, you should read this instruction manual carefully and should always follow the
instructions. This instruction manual applies to rail-guided pit lifts as well as for freely movable lifts.
1.1 Intended Use
The lift is intended exclusively for partial lifting of vehicles and for the transport of vehicle parts
(engine, transmission). Any use beyond this shall be considered as not intended.
Lifting of persons is prohibited.
Always secure lifted vehicles with supporting bridges/A-frames.
The normal fatigue life is 10 years.
1.2 Basic Instructions
The lift may only be operated by workshop staff with corresponding training.
Electric, hydraulic, and pneumatic work may only be performed by specialists.
Please follow the instruction manual.
Always keep the instruction manual available at the place of use.
Refer to all safety and hazard notes on the lift, and keep them legible.
The workshop operator must insure that all safety regulations are observed by the workshop
staff.
Technical modifications of the lift are not permitted.
The instruction manual is a part of the product and must be passed on to subsequent users.
Please observe the maintenance intervals.
1.3 Safety-relevant components
Hydraulic pressure relief valve
Hydraulic counterbalance valve
Tilt protections [1] on the lift cylinder
1.4 Explanation of Notes
DANGER
Danger to life, risk of injury
Measures
WARNING
Risk of injury and material damage
Measures
CAUTION
Material damage
Measures
2Storage
Store the lift in a dry place and protected from the weather at an ambient temperature of -10 to +50
°C. Please contact the manufacturer if machine has been in storage for more than 6 months.

Instruction Manual for Mobile Jacks
8
3Transport, Installation, and Assembly
DANGER
Danger to life, risk of injury from improper transport
Always transport the lift with suitable hoists and transport equipment (for example fork lifts or
cranes).
Never loiter under raised loads.
Safety Notes
Hoist the lift only at pick-up points.
Transport the lift cylinder horizontally and with the controls at the top.
Secure moving and loose parts.
3.1 Prepare Lifting Cylinder for
Operation
Junior Jack S3
A
B
Remove cover A.
Screw in silencer B.
Blitz 15/15
Blitz 15/15/15
Master Jack
The above-named lifts are supplied
ready for operation (including oil)
and can be used immediately.
3.2 Install and Assemble the Lift
WARNING
Risk of injury and material damage from a toppling lift
Install the lift only on level and solid ground with sufficient load carrying capacity.
Use lifts with under floor carriage only on parallel rails with sufficient load capacity.
Safety Notes
Use hoists only with rollers fitting the rails.
Use lifts with an inground carriage only in the workshop pit for which they have been
manufactured.
Always adjust the guide rollers E so that the carriage cannot leave the rails.
There are three carriage types:
Carriage R (rail carriage)
Carriage M (free floor-running carriage)
Carriage X (free floor-running carriage), does not have to be disassembled

Instruction Manual for Mobile Jacks
9
Rail carriage (Blitz R)
A
B
C
D
E
Loosen brake A from the lift cylinder by removing the bolts.
Lift the lift unit from the carriage:
To do so, loosen the bolts B and remove the cover C.
Remove the lift cylinder through the opening D.
Lower the carriage onto the rails and install the lift cylinder again on the carriage.
Match rollers E to the pit width.
Check safe contact of the rollers over the entire length of the rails.
Free floor-running carriage (Blitz M)
A
B
E
F
C
Before assembly, it is helpful to support the base frame so that the rollers are free.
Loosen brake A from the lift cylinder by removing the bolts.
Lift the lift unit from the carriage:
For this, loosen the bolts B and remove the cover C.
Loosen springs D and remove the cover plate E.
Remove the lift cylinder through the opening F.

Instruction Manual for Mobile Jacks
10
Lower the carriage into the pit and install the lift cylinder again on the carriage.
Free floor-running carriages (Junior Jack S3)
Attention: Do not position the lift horizontally for installation of the feet!
A
B
D
E
F
A
B
C
Install the carriage parts on the lift cylinder:
To do so, gently tighten 2 washers A and 2 short oiled bolts B on both sides. On the bottom, gently
tighten 3 washers A, 3 nuts C, and long oiled bolts D.
Align the carriage parts on a level surface and tighten screw connections with a tightening torque
of 40 Nm.
Connect bracket E to hose F.
3.3 Compressed Air Supply
H
Required compressed air quality according to ISO8573-1:
Air quality: Pressure dew point ≤5 °C
Filtration of all solid particles > 3 micron
Connection pressure: Blitz Master Jack min. 9 bar max. 12 bar
Blitz Junior Jack min. 3 bar max. 6 bar
Air consumption for models with air motor: ca. 300 Nm³/min.

Instruction Manual for Mobile Jacks
11
Electrical Connection
E
WARNING
Risk of injury and material damage from electric shock
The electrical connection and the applicable national protection regulations shall be provided
and checked by a specialist.
The electrical connection must be composed of a cable with 5-pin CEE coupling 16 A, which is
connected to a 400 V/50 Hz mains supply. A circuit breaker of 3.8 A must exist.
The manufacturer recommends a suitable cable suspension system.
4Commissioning
Before initial operation:
Connect the compressed air supply or the electrical connection to the lift.
Check the hydraulic fluid level. (6.4)
Perform a safety check (6.5)
5Operation
5.1 Load-carrying Devices
Safety Notes
Do not stack extensions.
Always use original load-carrying devices of the manufacturer with suitable pins.
Support plate and extension
Traverse
Lift a vehicle at one point.
Lift vehicles gently at two points.

Instruction Manual for Mobile Jacks
12
Transmission plate
Safe removal, installation, and transport of
vehicle parts.
Use special support plates and extensions, when required, for load pick-up points which are difficult
to access. Contact the manufacturer for further information concerning all load pick-up devices.
5.2 Supporting Bridges and A-frames
Safety Notes
Insure safe contact of the supporting bridges/A-frames over the entire length of the pit or the
plant floor.
Supporting bridge
A-frame
For use in workshop pits.
For use on workshop floors,
e.g. under lift platforms.
Contact the manufacturer for further information concerning all load pick-up devices.

Instruction Manual for Mobile Jacks
13
5.3 Advice on hazards
CAUTION
Please refer to the instruction manual.
DANGER
Start movement of the lift only when there is no danger to personnel.
Always monitor lifting and lowering movements.
Use the lift only in a proper condition in relation to safety.
DANGER
Always check that the vehicle is secure at the pick-up points after a short lift.
Always use suitable load pick-up devices.
Use load pick-up devices only on horizontal, level, and stable
load pick-up points specified by the vehicle manufacturer.
DANGER
Always secure lifted vehicles with supporting bridges/A-frames.
DANGER
Do not exceed the max. permissible load capacity of the lift.
Secure vehicle part with chains or belts.
Transport vehicle parts only when lowered.
CAUTION
The lift may only be operated by workshop staff with the corresponding
training.
CAUTION
Lifting or persons or climbing onto the lift or the load is not permitted.
CAUTION
Never loiter under raised loads.
CAUTION
Use the lift only on level and solid ground.

Instruction Manual for Mobile Jacks
14
5.4 Lifting, Lowering, and Transporting Loads
DANGER
Danger to life, risk of injury from lifted vehicles
Only load lift and load pick-up devices centrically by positioning the center of gravity in the
middle.
Safety Notes
Always keep the movement range of the lift free.
Keep the movement range of the load and the load pick-up devices free.
Complete lifting of vehicles with one or more lifts is not permitted.
Always shut down and secure the lift immediately in case of malfunction. Always have
malfunctions repaired immediately.
Do not operate the lift with compressed air containing condensate or dirt.
For work with strongly adhesive underbody sealants or lacquers, cover the piston rod.
Keep the piston rod and the pins of load pick-up devices free of sand and dirt.
Disconnect the lift from the compressed air supply at the end of work or before longer breaks.
Remove the removable pump rods after each work process.
CAUTION
Damage to lifts and vehicles from load pick-up devices and extended piston rods
Piston rods must always be completely retracted when entering or leaving workshop pits and
lifting platforms.
A sufficient distance must exist between load pick-up devices and vehicle.
Considerable longitudinal forces can occur when vehicle axles are lifted.
Disengage the handbrake and shift to idle, so that the wheels can roll.
Raising a vehicle
Lift the vehicle slightly with the lift at the load pick-up point.
Check for safe support and secure seating of the vehicle.
Lift the vehicle to the desired height.
Secure the vehicle against rolling off, for example with drag shoes.
Secure lifted vehicle with supporting bridges/A-frames.
Lowering the vehicle
Remove the roll-away protection from the vehicle.
Lift the vehicle slightly with the lift and remove the supporting bridges/A-frames.
Lower the vehicle slowly.
Retract the piston rod [1] completely and make sure that the support plate is on the piston rod.
Transporting vehicle parts
Position the vehicle part on a lift with a suitable transmission plate in centered position.
Secure the vehicle part with chains or belts.
Retract the piston rod [1] completely and transport the vehicle part.

Instruction Manual for Mobile Jacks
15
6Maintenance and Repair
WARNING
Risk of injury and material damage
Always service and repair the lift without a load.
Safety Notes
Maintenance and repair work on the lift may be performed only by specialists.
Before all maintenance and repair work, disconnect the lift from the compressed air supply or
the mains.
After maintenance and repair work on the hydraulic system, the system must be vented.
Screwed connections loosened during maintenance and repair work always must be tightened
again.
Do not clean a lift with high-pressure or steam jets.
As there is high risk of slipping on an oily workshop floor, oil always must be caught in a
suitable container and must be disposed of correctly.
The safety regulations for the product must be observed when handling oil, grease, and
chemical substances.
Do not use aggressive cleaning agents to clean the lift.
Only use original spare parts of the manufacturer and approved supplies.
Always make sure that materials and comsumable (for example hydraulic fluid) and replaced
parts are disposed of in a safe and environmentally friendly manner.
6.1 Maintenance intervals
Lifts in continuous operation or in especially dirty environments should be serviced more frequently.
Weekly
Perform a function test (6.2)
Check the compressed air supply. (6.3)
Check the hydraulic fluid level. (6.4)
Check connection cables/hoses for damage and chafing.
Lubricate the rollers of the lift unit and the carriage.
Clean the lift and service it with anti-rust agents.
Yearly
Perform a safety check. (6.5)
Change the hydraulic fluid. (6.6)
Clean and lubricate all rollers.
Every 5 years
Replace the hydraulic hoses (6.7)
6.2 Perform a function test
Check the full functionality of the lift without a load.
Check the full functionality of the lift with a load.
Shut down and secure the lift immediately in case of malfunction. Always have malfunctions
repaired immediately and ensure trouble-free operation.
6.3 Check the compressed air supply.
H
Check and service the filter and the water trap according to the specifications of the
manufacturer.
Check the connection pressure. (3.3)

Instruction Manual for Mobile Jacks
16
6.4 Check the hydraulic fluid level.
Hydraulic fluid load lift
Retract the piston rod [1] completely.
Disconnect the lift from the compressed air supply or the mains.
Remove the load lifting dipstick [7] by turning it, and check the hydraulic fluid level. If required,
fill with hydraulic fluid up to the mark.
Replace the dipstick.
Hydraulic fluid level return
Extend the piston rod [1] completely.
Disconnect the lift from the compressed air supply or the mains.
Remove the return dipstick [9] by turning it, and check the hydraulic fluid level.
If required, fill with hydraulic fluid up to the mark.
Replace the dipstick.
6.5 Perform a safety check.
The safety check must be performed by a specialist:
Prior to initial commissioning
Periodically after initial commissioning (at the latest yearly)
After a change in the installation location
After repair work and construction changes
The following items must be checked on the lift:
Quick reference guide
Name plate
Markings on the lift
Correct installation of the carriage
Tilt protections on the lift cylinder
Pull-out protection on the carriage
Condition of the load pick-up devices and controls
Condition of the support structure and the welding seams
Leak-tightness of the hydraulic system
Hydraulic fluid level
Connection cables/hoses
Perform a function test
Enter the result into an inspection log
6.6 Changing the hydraulic fluid
The fluid change requires:
Receptacle for the hydraulic fluid
Hydraulic fluid, class HLP, viscosity ISO-VG 10, 22, or 32 (e.g. HLP 22).
Information concerning the oil capacity. (Specifications)
New O-rings. (Spare parts catalog)
Hydraulic fluid load lift
Retract the piston rod [1] completely.
Disconnect the lift from the compressed air supply or the mains.
Remove the load lifting fluid drain plug [5] by turning it, and drain the hydraulic fluid.
Replace the fluid drain plug with a new O-ring.
Remove the load lifting dipstick [7] by turning it, and fill with new hydraulic fluid up to the mark.
Replace the dipstick with a new O-ring.
Hydraulic fluid return
Extend the piston rod [1] completely.
Disconnect the lift from the compressed air supply or the mains.
Remove the return fluid drain plug [8] by turning it, and drain the hydraulic fluid.
Replace the fluid drain plug with a new O-ring.
Remove the return dipstick [9] by turning it, and fill with new hydraulic fluid up to the mark.
Replace the dipstick with a new O-ring.

Instruction Manual for Mobile Jacks
17
After the fluid change, bleed the lift. (6.8)
6.7 Replacing the hydraulic hoses
E
Retract the piston rod [1] completely.
Disconnect the lift from the mains.
Remove the bleed screw and install the cover D. (3.1)
Place the lift horizontally.
In case of inground carriages, remove the lift cylinder first. (3.2)
Disconnect the hydraulic hoses and attach new ones.
Position the lift vertically.
In the case of inground carriages, reset the lifting cylinder into the carriage.
Remove the cover D and check the load lifting hydraulic fluid level. (6.4)
Reinstall the bleed screw and bleed the lift. (6.8)
6.8 Bleed the lift
Operate the manual pump [4] approximately 5 to 10 times, and at the same time actuate the
drain valve [3].
Extend and retract the piston rod [1] completely.
Repeat as needed.
6.9 Clean or Replace the Pneumatic Control Valve
F
E
G
H
A
C
B
Disconnect the lift from the compressed air
supply.
Remove the snap ring A, pull out axle B, and
remove pedals C.
Remove bolt E and remove the cover F and the
control valve G to the front.
Replace the O-ring H, attach a new control
valve, and fasten again with the bolt E.
Attach the pedals C and the axle B and secure
with the snap ring A.

Instruction Manual for Mobile Jacks
18
6.10 Replace the Hydraulic Block
Does not apply for Junior Jack S3.
A
C
B
D
E
F
Disconnect the lift from the compressed air
supply.
Place the lift horizontally.
In the case of inground carriages, remove the
lift cylinder first. (3.2)
Pull out lowering lever A.
Remove the bolts B and remove the cover C.
Disconnect the compressed air lines on the
air motor.
Remove the screws D and remove the
hydraulic block E to the front.
Remove the strainer, clean it, and reinstall it.
Replace the O-rings F.
Attach a new hydraulic block and fasten it
again with the bolts D.
Reattach the compressed air lines.
Fasten the cover C again with the bolts B and
install the lowering lever A.
Set the lift vertically.
In the case of inground carriages, reset the
lifting cylinder into the carriage.
Check the load lift hydraulic fluid level.
(6.4)
Bleed the lift. (6.8)

Instruction Manual for Mobile Jacks
19
7Troubleshooting
If the lift does not function without problems, it may have a simple cause. Please contact customer
service in the case of an undefined problem.
Problem
Possible cause
Repair
Piston rod [1] moves down
under load.
Cylinder tube corroded, piston
sleeves worn, or ball valves
leaking.
Request customer service.
Hydraulic fluid contaminated.
Change the hydraulic fluid. (
6.6)
Hydraulic fluid leaks at the
piston rod [1].
Damage to the piston rod has
destroyed the seal.
Request customer service.
Hydraulic fluid leaks at the
pneumatic control valve.
Fluid level too high.
Water gets into the fluid tank
together with the compressed
air.
Check the hydraulic fluid level
(6.4), change the fluid in
case of too high fluid level
(6.6).
Check the air supply (3.3).
Piston sleeves at the lifting
cylinder is leaking.
Request customer service.
Controls [2] do not return to
the initial position.
Contamination.
Clean or replace the
pneumatic control valve.
(6.9)
Air leaks at the pneumatic
control valve.
Contamination, damage, or
defective seal.
Clean or replace the
pneumatic control valve.
(6.9)
8Shutting Down and Disposal
Drain the hydraulic fluid. (6.6)
Disassemble the lift. (3.2)
Correctly dispose of the hydraulic fluid and the lift.

Instruction Manual for Mobile Jacks
20
This manual suits for next models
12
Table of contents
Other Blitz Lifting System manuals
Popular Lifting System manuals by other brands
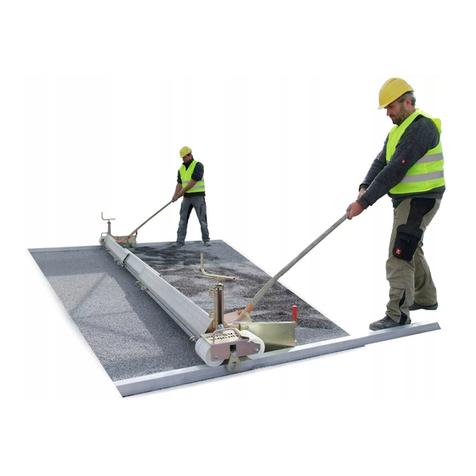
probst
probst TAS-UNI Translation of original operating instructions
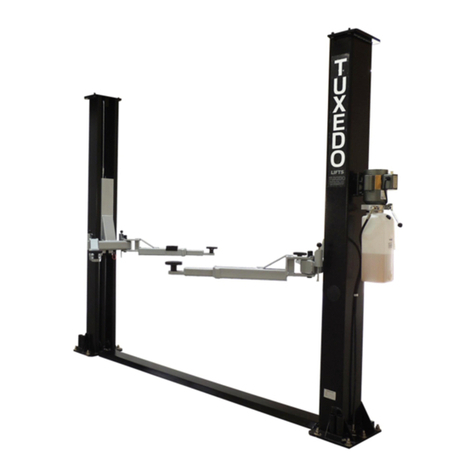
Tuxedo
Tuxedo TP9KF-TUX Installation & operation manual
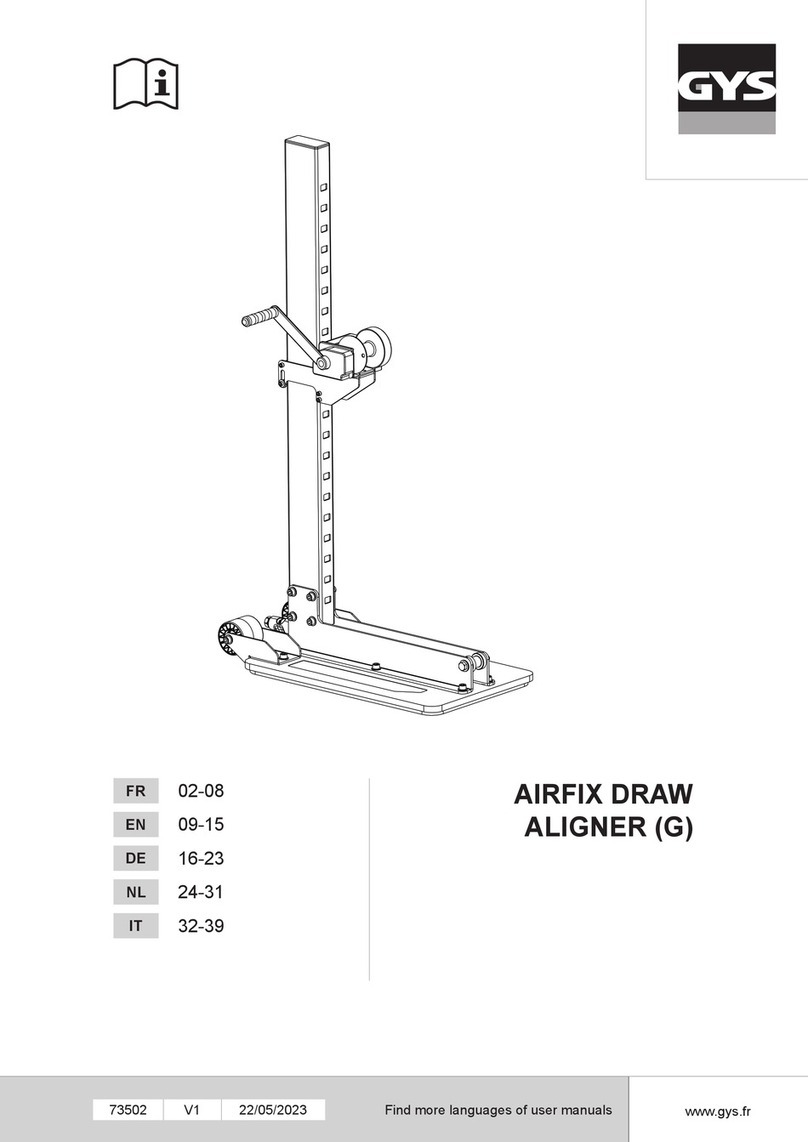
GYS
GYS AIRFIX DRAW ALIGNER G manual
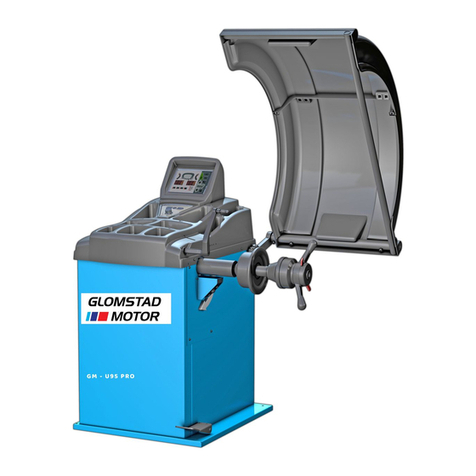
Glomstad Motor
Glomstad Motor GM - U95 PRO Use and maintenance manual

Challenger Lifts
Challenger Lifts 44060 Installation, operation & maintenance manual
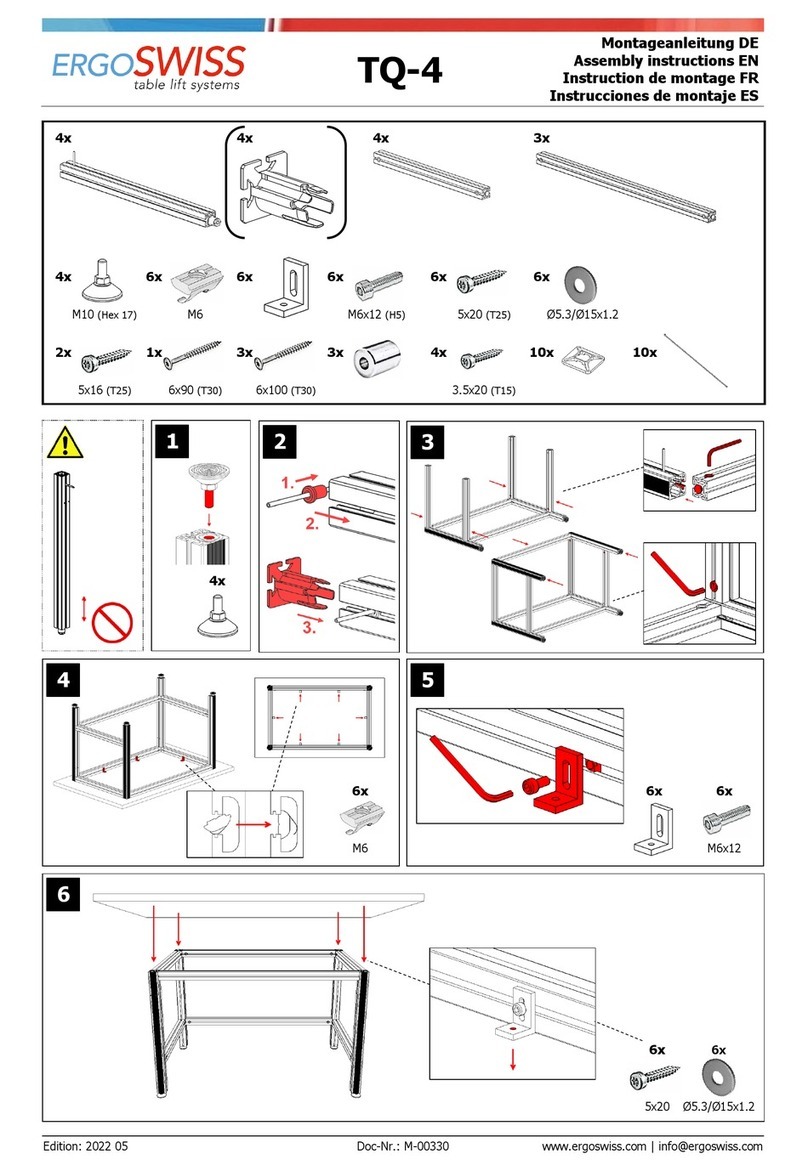
Ergoswiss
Ergoswiss TQ-4 Assembly instructions