BLUELIGHT BL6-U User manual

BL6-U Parallel Integrated Controller Quick Commissioning User Manual
Contents
1 BL6-U PARALLEL INTEGRATED CONTROLLER MODEL & SPECIFICATIONS ................................. 1
1.1 MODEL DESCRIPTION............................................................................................................................1
1.2 SPECIFICATIONS ...................................................................................................................................2
2 BL6-U PARALLEL INTEGRATED CONTROLLER MAIN BOARD TERMINALS.................................. 4
3 PG CARD TERMINALS & ASSEMBLAGE.................................................................................. 8
3.1 PG_V6 .............................................................................................................................................8
3.2 PG_V6X ........................................................................................................................................... 9
3.3 SPG_V6 ........................................................................................................................................... 9
3.4 SPG_V6E ....................................................................................................................................... 11
4 PARAMETER NEED TO SET BEFORE INSPECTION RUN .......................................................... 12
5 MOTOR INITIAL ANGLE TUNING (ONLY FOR SYNCHRONOUS MACHINE)............................... 14
6 ASYNCHRONOUS MOTOR ADJUSTMENT............................................................................. 19
6.1 MOTOR PARAMETERS CONFIRMATION ...................................................................................................19
6.2 ENCODER PARAMETERS CONFIRMATION.................................................................................................19
6.3 PI PARAMETERS CONFIRMATION...........................................................................................................20
6.4 ELEVATOR SYSTEM CONFIRMATION........................................................................................................20
7 INSPECTION RUNNING....................................................................................................... 22
7.1 THINGS TO CHECK BEFORE INSPECTION RUNNING: ....................................................................................22
7.2 INSPECTION RUNNING.........................................................................................................................22
8 HOISTWAY PARAMETER LEARNING .................................................................................... 23
8.1 PERFORM HOISTWAY PARAMETER LEARNING WITH DIGITAL OPERATOR ........................................................23
8.2 PERFORM HOISTWAY PARAMETER LEARNING WITH DIGITAL TUBES &OPERATION KEYS...................................24
8.3 HOISTWAY PARAMETER LEARNING FAULT DIAGNOSIS ................................................................................24
9 START-UP COMFORT LEVEL ADJUSTMENT........................................................................... 26
9.1 COMFORT LEVEL ADJUSTMENT WITH WEIGHING DEVICE .............................................................................26
9.2 START WITHOUT LOAD COMPENSATION SETUP ........................................................................................ 26
9.3 ELEVATOR NORMAL SPEED COMFORT LEVEL ADJUSTMENT...........................................................................28
10 LEVELING PRECISION ADJUSTMENT.................................................................................. 29
10.1 BASIC CONDITIONS FOR ELEVATOR LEVELING.........................................................................................29
10.2 LEVELING PARAMETER ADJUSTMENT ...................................................................................................29
11 INTEGRATED CONTROLLER TERMINAL WIRING DIAGRAM ................................................. 30
APPENDIX I BL6-U PARALLEL INTEGRATED CONTROLLER TEST COMMISSIONING.................. 31
APPENDIX II BL6-U PARALLEL INTEGRATED CONTROLLER OPERATOR MENU ........................ 32
APPENDIX III LEVELING SWITCHES & FLAG INSTALLATION ................................................... 33
APPENDIX IV PARAMETERS................................................................................................ 34
APPENDIX V ELEVATOR SYSTEM FAULTS.............................................................................. 45
APPENDIX VI DRIVER FAULT ............................................................................................... 48
APPENDIX VII MENU OPERATION PROCESSES WITH DIGITAL TUBES & OPERATION KEYS ...... 53

BL6-U Parallel Integrated Controller Quick Commissioning User Manual
1
1BL6-U Parallel Integrated Controller Model & Specifications
1.1 Model description
Model description of BL6-U Parallel Integrated Controller is shown as figure 1(take 22KW closed
type controller as example).
Specifications list in chart 1.
BL6 -UO4 0 2 2 -B
Controller series
Additional Type
None: Serial integrated
controller (with glass shell
or no shell)
W: with metal shell
B: parallel
C: Ultra-thin without shell
S: Small size
H: For home lift
N: Plastic shell
M: Modularization
Controller type
U: Elevator in-built controller
S: High performance inverter
Maximum
machine power
005:5.5KW
007:7.5KW
011:11KW
015:15KW
018:18.5KW
022:22KW
030:30KW
037:37KW
045:45KW
055:55KW
075:75KW
Protective structure
C: Closed type
O: Open type
Voltage level
4:380V
2:220V
FIGURE 1.1 MODEL DESCRIPTION DIAGRAM

BL6-U Parallel Integrated Controller Quick Commissioning User Manual
2
1.2 Specifications
Specifications of BL6-U Parallel Integrated Controller in chart 1.
CHART 1.1 SPECIFICATIONS
MODEL BL6-U40-B
4005
4007
4011
4015
4018
4022
4030
4037
4045
4055
4075
MAX MOTOR CAPACITY(KW)
5.5
7.5
11
15
18.5
22
30
37
45
55
75
RATED OUTPUT
RATED OUTPUT CAPACITY(KVA)
9
12
18
22
27
32
43
53
63
78
106
RATED OUTPUT CURRENT(A)
14
18
27
34
41
48
65
80
96
128
165
MAX OUTPUT VOLTAGE(V)
Three-phase, AC380(corresponding to the input voltage)
RATED FREQUENCY(HZ)
50
MAX OUTPUT FREQUENCY(HZ)
120
POWER INPUT
RATED VOLTAGE(V)
Three-phase, AC380
RATED FREQUENCY(HZ)
50
RATED INPUT CURRENT(A)
17
22
32
41
49
58
78
96
115
147
190
ALLOWABLE VOLTAGE FLUCTUATION
±15%
ALLOWABLE FREQ FLUCTUATION
±5%
MODEL BL6-U20-B
2003
2005
2007
2011
2015
2018
2022
MAX MOTOR CAPACITY(KW)
3.7
5.5
7.5
11
15
18.5
22
RATED
OUTPUT
RATED OUTPUT CAPACITY(KVA)
7
10
14
20
27
33
40
RATED OUTPUT CURRENT(A)
17
25
33
49
66
80
96
MAX OUTPUT VOLTAGE(V)
Three-phase, AC220(corresponding to the input voltage)
RATED FREQUENCY(HZ)
50
MAX OUTPUT FREQUENCY(HZ)
120
POWER INPUT
RATED VOLTAGE(V)
Three-phase, AC220V
RATED FREQUENCY(HZ)
50
RATED INPUT CURRENT(A)
21
27
40
52
68
92
110
ALLOWABLE VOLTAGE FLUCTUATION
+10%, -15%
ALLOWABLE FREQ FLUCTUATION
±5%
BASIC FEATURES
ELEVATOR CONTROL MODE
Simplex Collective, Duplex Collective, 3~8 units Group Control
ELEVATOR SPEED RANGE
0.5~4m/s
APPLICABLE HIGHEST FLOORS
15 levels
APPLICABLE ELEVATOR TYPE
Passenger, Hospital, Panoramic, Goods, Villa Elevator
APPLICABLE MOTOR
Gear Traction Machine, Gearless Traction Machine
COMMUNICATION MODE
CAN bus serial communication
LEVELING ACCURACY
≤3mm
DRIVE CONTROL
FEATURES
CONTROL MODE
Space vector PWM (SVPWM) closed loop vector control
CARRIER FREQUENCY
8KHz (6~12KHz adjustable)
SPEED CONTROL RANGE
1:1000
SPEED CONTROL ACCURACY
±0.05% (25 C±10 C)
SPEED RESPONSE
30Hz
TORQUE LIMIT
Yes (Set by parameters)
DRIVE CONTROL
FEATURES
TORQUE ACCURACY
±5%
FREQUENCY CONTROL RANGE
0~120Hz
FREQUENCY ACCURACY
Digital Ref: ±0.01% (-10 C~+40 C)
FREQUENCY REF RESOLUTION
Digital Ref: 0.01Hz
OUTPUT FREQ RESOLUTION
0.01Hz
OVERLOAD CAPACITY
150% rated current 60s; 180% rated current 10s
STARTING TORQUE
180% rated current 0Hz
DECELERATION TIME
0.001~600s

BL6-U Parallel Integrated Controller Quick Commissioning User Manual
3
CHART 1.1 SPECIFICATIONS
DRIVE CONTROL
FEATURES
MAIN CONTROL FUNCTIONS
START WITHOUT LOAD COMPENSATION,BATTERY OPERATION,AUTO TUNING,
LOAD COMPENSATION,COOLING FAN CONTROL,BASE BLOCK,TORQUE LIMIT,
CAN COMMUNICATION REF,ACCELERATION/DECELERATION TIME,SCURVE
ACCELERATION/DECELERATION,MONITOR OF MAIN MACHINE FOR WHICH
ELECTRIC CURRENT CAN BE EFFECTIVELY INTERDICT OR NOT WHEN THE CAR
STOPS;INTERNAL BRAKE,PG FREQ DIVIDING OUTPUT,AUTOMATIC FAULT RETRY,
AUTOMATIC FAULT RESET,PARAMETER COPY
CONTROL/INPUT/
OUTPUT INTERFACE
OC INPUT CONTROL POWER
ISOLATED EXTERNAL DC24V
RELAY OUTPUT CONTROL POWER
ISOLATED INTERNAL DC24V
LOW OPTO-ISOLATED INPUTS
46-CHANNEL SWITCHES:RATED LOAD 7MA/DC24V, UPPER FREQ 100HZ
HIGH OPTO-ISOLATED INPUTS
2-CHANNEL SWITCHES:RATED LOAD 8MA/AC110V, UPPER FREQ 100HZ
PROGRAMMABLE RELAY OUTPUT
24-CHANNEL SWITCHES:1NO, CONTACT CAPACITY 5A/30VDC,5A/250VAC
CAN COMMUNICATION INTERFACE
1CHANNEL:(DUPLEX/GROUP CONTROL,REMOTE WIRELESS MONITORING)
RS232 COMMUNICATION
INTERFACE
2CHANNELS:DIGITAL OPERATOR/PC MONITORING/PROGRAMMABLE INTERFACE;
SECURITY DOG COMMUNICATION
DISPL
AY
DIGITAL OPERATOR
LCD DISPLAY IN CHINESE/ENGLISH
MONITORING SOFTWARE
INTERFACE
MENU/PARAMETER/STATE/VARIABLE TIMING/DIGITAL OSCILLOSCOPE ETC.
MAIN PROTECTION FUNCTIONS
INSTANTANEOUS OVERCURRENT
PROTECTION
STOP AT OVER 200% RATED OUTPUT CURRENT
FUSE PROTECTION
STOP AT FUSED
OVERLOAD PROTECTION
STOP AT 150% RATED CURRENT 60S/180% RATED CURRENT 10S
OVERVOLTAGE PROTECTION
STOPS AT DC BUS VOLTAGE OVER 720V (400V DRIVE)OR 410V (200V DRIVE)
UNDERVOLTAGE PROTECTION
STOPS AT DC BUS VOLTAGE UNDER 380V (400V DRIVE)OR 190V (200V DRIVE)
HEATSINK OVERHEAT PROTECTION
PROTECT BY THERMISTORS
IGBT INTERNAL PROTECTION
IGBT OVERCURRENT/OVERHEAT/SHORT CIRCUIT/UNDERVOLTAGE PROTECTION
MOTOR PROTECTION
PROTECT BY ELECTRONIC THERMAL DEVICES
IMPACT RESTRAINING CIRCUIT
PROTECT BY CONTACTOR FEEDBACK
OVERSPEED PROTECTION
PROTECT AT SPEED EXCEED THE MAXIMUM ALLOWABLE SETTING
SPEED DEVIATION PROTECTION
PROTECT AT SPEED DEVIATION EXCEEDS ALLOWABLE VALUE
PG FAULT PROTECTION
PROTECT AT PG DISCONNECTION/PHASE ERROR
AUTO TUNING PROTECTION
PROTECT AT AUTO TUNING FAULT
OPEN-PHASE PROTECTION
PROTECT AT INPUT/OUTPUT PHASE LOST
DOOR INTERLOCK FAULT
PROTECT AT DOOR INTERLOCK CIRCUIT OPEN WHEN RUNNING
SAFETY CIRCUIT FAULT
PROTECT AT SAFETY CIRCUIT OPEN WHEN RUNNING
BRAKE FAULT
NO BRAKE OPEN FEEDBACK SIGNAL AFTER OUTPUT BRAKE OPEN COMMAND
LEVELING ZONE SIGNAL FAULT
PROTECT AT LEVELING ZONE SIGNAL FAULT
MAIN PROTECTION
FUNCTIONS
OUTPUT CONTACTOR FAULT
PROTECT AT OUTPUT CONTACTOR FAULT
RUNNING TIME PROTECTION
PROTECT AT SINGLE RUNNING TIME EXCEEDS LIMIT
FLOOR COUNTER FAULT
PROTECT AT FLOOR COUNTER FAULT
COMMUNICATION INTERFERENCE
FAULT
PROTECT AT COMMUNICATION INTERFERENCE FAULT
HOISTWAY PARAMETER LEARNING
FAULT
HOISTWAY PARAMETER LEARNING FAULT PROTECTION
STRUCTUR
E
PROTECTION DEGREE
C: CLOSED IP20; O: OPEN IP00
COOLING
FORCED AIR COOLING
INSTALLATION
CABINET EMBEDDED INSTALLATION/HANGING INSTALLATION
AMBIENT TEMPERATURE
-10 C~+40 C
USING
AMBIENT
HUMIDITY
5~95%RH, NO CONDENSATION
STORAGE TEMPERATURE
-20 C~+60 C
APPLICATION SITUATION
INDOOR (NO CORROSIVE GAS,FLAMMABLE GAS,DUST AND DIRECT SUNLIGHT)
ALTITUDE
BELOW 1000M
VIBRATION
10~20HZ,<9.8M/S²; 20~50HZ,<2M/S²

BL6-U Parallel Integrated Controller Quick Commissioning User Manual
4
2BL6-U Parallel Integrated Controller Main Board Terminals
FIGURE 2.1 TERMINAL ARRANGEMENTS FOR CONTROL CIRCUIT
4x Φ 4.0
204
213
213
189
Digital operator
interface
Digital tubes & operation keys
Power & CAN Bus
Output interface
PG card
interface
Bidirectional interface
Input interface

BL6-U Parallel Integrated Controller Quick Commissioning User Manual
5
CHART 2.1 Control Circuit Port definition and Function
Port
No.
Terminal
Symbol
Location
Definition
Usage
Interface Tech Spec
Interface
Type
Rated
Capacity
On/off
Time
Max
Speed
J1
X36+
J1-1
Door inter-lock input + (110V-220VAC)
Input
OC
AC110V
8mA
10mS
100Hz
X36-
J1-2
Door inter-lock input –(110V-220VAC)
Y0
J1-3
KBC brake output
Output
Relay
DC10A30V
AC10A250V
5/10mS
20cpm
Y1
J1-4
KDY auxiliary contact output
COM1
J1-5
Y0-Y1 common terminal
Y2
J1-6
KKM Door open 1 control output
Y3
J1-7
KGM Door close 1 control output
Y4
J1-8
KKM2 door open 2 control output
J2
Y5
J2-1
KGM2 door close 2 control output
Output
Relay
DC10A30V
AC10A250V
5/10mS
20cpm
CM2
J2-2
Y2-Y5 common terminal
Y6
J2-3
KXFL fire linkage output
Y7
J2-4
Illumination switch-off output
Y8
J2-5
KDZZ arrival gong output
CM3
J2-6
Y6-Y8 common terminal
Y9
J2-7
Ea low 7 segment code a display
Y10
J2-8
Eb low 7 segment code b display
J3
Y11
J3-1
Ec low 7 segment code c display
Output
Relay
DC10A30V
AC10A 250V
5/10mS
20cpm
Y12
J3-2
Ed low 7 segment code d display
Y13
J3-3
Ee low 7 segment code e display
Y14
J3-4
Ef low 7 segment code f display
Y15
J3-5
Eg low 7 segment code g display
Y16
J3-6
EHbc high 7 segment code bc display
(Inspection output when floor display is
not in 7-seg-code mode. when floor
display is in 7-seg-code mode, and the
high bit is not used, Inspection output
can be set by function code FU-05)
Y17
J3-7
EHg high 7 segment code g display
Y18
J3-8
ES up arrow display
J4
Y19
J4-1
EX down arrow display
Output
Relay
DC 10A30V
AC 10A250V
5/10mS
20cpm
CM4
J4-2
Y9~Y19 common terminal
Y20
J4-3
Cut-off power after parking (disabled
output after parking)
Y21
J4-4
ECZ overload output
Y22
J4-5
FMQ buzzer control output
CM5
J4-6
Y20~Y22 common terminal
Y23
J4-7
Cut main contactor output
CM6
J4-8
Y23 common terminal
J5
I0
J5-1
SKYC door open delay input
I1
J5-2
Full Collective/Simplex Collective
Car call input 1/ Car call input 1
I2
J5-3
Full Collective/Simplex Collective
Car call input 2/ Car call input 2
I3
J5-4
Full Collective/Simplex Collective
Car call input 3/ Car call input 3

BL6-U Parallel Integrated Controller Quick Commissioning User Manual
6
CHART 2.1 Control Circuit Port definition and Function ()
Port
No.
Terminal
Symbol
Location
Definition
Usage
Interface Tech Spec
Interface
Type
Rated
Capacity
On/off
Time
Max
Speed
J5
I4
J5-5
Full Collective/Simplex Collective
Car call input 4/ Car call input 4
Input
Output
Input:
Optical-couple
Output: OC
Input:
DC 24V
7mA
Output:
300mA
Input:
10mS
Input:
100Hz
I5
J5-6
Full Collective/Simplex Collective
Car call input 5/ Car call input 5
I6
J5-7
Full Collective/Simplex Collective
Car call input 6/ Car call input 6
I7
J5-8
Full Collective/Simplex Collective
Car call input 7/ Car call input 7
I8
J5-9
Full Collective/Simplex Collective
Call up input 1/ Car call input 8
I9
J5-10
Full Collective/Simplex Collective
Call up input 2/ Car call input 9
J6
I10
J6-1
Full Collective/Simplex Collective
Call up input 3/ Call input 1
Input
Output
Input:
Optical-couple
Output: OC
Input:
DC 24V
7mA
Output:
300mA
Input:
10mS
Input:
100Hz
I11
J6-2
Full Collective/Simplex Collective
Call up input 4/ Call input 2
I12
J6-3
Full Collective/Simplex Collective
Call up input 5/ Call input 3
I13
J6-4
Full Collective/Simplex Collective
Call up input 6/ Call input 4
I14
J6-5
Full Collective/Simplex Collective
Call down input 2/ Call input 5
I15
J6-6
Full Collective/Simplex Collective
Call down input 3/ Call input 6
I16
J6-7
Full Collective/Simplex Collective
Call down input 4/ Call input 7
I17
J6-8
Full Collective/Simplex Collective
Call down input 5/ Call input 8
I18
J6-9
Full Collective/Simplex Collective
Call down input 6/ Call input 9
I19
J6-10
Full Collective/Simplex Collective
Call down input 7/ Call input 10
J7
X0
J7-8
SJX Inspection/auto input
X1
J7-7
SSXW up limit input
X2
J7-6
SXXW down limit input
X3
J1-5
SSMQ up leveling input
X4
J1-4
SXMQ down leveling input
X5
J1-3
SKDY auxiliary contactor input
X6
J1-2
KBC brake contactor feedback
X7
J1-1
Door open limit 2 input
J8
X8
J8-8
Door close limit 2 input
X9
J8-7
Safe plates 2 input
X10
J8-6
SJT Emergency stop input
X11
J8-5
SMB door inter-lock input
X12
J8-4
Left brake feedback input
X13
J8-3
SXF fire input
X14
J8-2
SMS jog up input (Attendant up)
X15
J8-1
SMX jog down input (Attendant
down)

BL6-U Parallel Integrated Controller Quick Commissioning User Manual
7
CHART 2.1 Control Circuit Port definition and Function ()
Port
No.
Terminal
Symbol
Location
Definition
Usage
Interface Tech Spec
Interface
Type
Rated
Capacity
On/off
Time
Max
Speed
J9
X16
J9-10
SSDZ top terminal input
Input
OC
DC24V
7mA
10mS
100Hz
X17
J9-9
SXDZ bottom terminal input
X18
J9-8
ARD input
X19
J9-7
SKM door open signal input 1
X20
J9-6
SGM door close signal input 1
X21
J9-5
SKMW1 door open limit input 1
X22
J9-4
SGMW1 door close limit input 1
X23
J9-3
STAB1 safe plate 1 input
X24
J9-2
SDS electronic lock signal input
X25
J9-1
SCZ over-load input
J10
X26
J10-10
SMZ full-load input
Input
OC
DC 24V
7mA
10mS
100Hz
X27
J10-9
Spare/ Re-leveling condition input
X28
J10-8
Light-load anti-nuisance input/
Rear door lock detection
X29
J10-7
SZH Attendant input
X30
J10-6
SZS Bypass drive input
X31
J10-5
Right brake feedback input
X32
J10-4
Thermal switch input
X33
J10-3
SKM2 door open input 2
X34
J10-2
SGM2 door close Input 2
X35
J10-1
Standby/ Re-leveling sensor input
J11
+24V1
J11-1
Input common terminal
24V_GND
J11-2,
J11-3
Input power ground
Power
Power
DC24V10A
+24V
J11-4
Input power
AG0 IN
J11-5
Analog input
Input
Analog
-10V~+10V
GND1
J11-6
Input ground
Analog input
ground
1H
J11-7
Duplex/Group control
communications +
Communication
Interface
CAN
80mA
25Khz
1L
J11-8
Duplex/Group control
communications -

BL6-U Parallel Integrated Controller Quick Commissioning User Manual
8
3PG Card Terminals & Assemblage
Note: With the hardware version upgrade, the corresponding pictures may be changed. Reference to
prevail in kind.
3.1 PG_V6
PG_V6 interface card is sync/async machine universal pulse encoder speed feedback and
frequency dividing output card.
PG_V6 is in supporting use of 5V line driver output type encoder. Encoder for async machine:
A/B, and encoder for sync machine: A/B/Z/U/V/W.
FIGURE 3.1 PG_V6 CARD
FIGURE 3.1 PG-V6 Card Port definition and Function
Port
No.
Terminal
Symbol
Location
Definition
Usage
Interface Tech Spec
Interface Type
Rated Capacity
On/off
Time
Max
Speed
JENDATA
(short for JEN)
+12V
JEN-1
OC/Push-pull type
power
12V power
Power output
+150Ma/12V±5%
A+
JEN-2
Freq dividing
signal OC output A
Sync freq dividing
OC/Push pull
output
±50Ma
500KHz
B+
JEN-3
Freq dividing
signal OC output B
Sync freq dividing
OC/Push pull
output
±50Ma
500KHz
0V
JEN-4
Power ground
Power ground
Power ground
—
GE
JEN-5
Shield ground
Shield ground
—
GE
JEN-6
Shield ground
Shield ground
—
JG1
+5V
JG1-1
+5V
5V Power
Power output
+400Ma/5V±5%
U+
JG1-2
U+
differential signal U+
differential input
±20Ma/3.1-5V
500KHz
Z+
JG1-3
Z+
differential signal Z+
differential input
±20Ma/3.1-5V
500KHz
B+
JG1-4
B+
differential signal B+
differential input
±20Ma/3.1-5V
500KHz
A+
JG1-5
A+
differential signal A+
differential input
±20Ma/3.1-5V
500KHz
GND
JG1-6
GND
5V ground
Power ground
—
U-
JG1-7
U-
differential signal U-
differential input
±20Ma/3.1-5V
500KHz
Z-
JG1-8
Z--
differential signal Z-
differential input
±20Ma/3.1-5V
500KHz
B-
JG1-9
B-
differential signal B-
differential input
±20Ma/3.1-5V
500KHz
A-
JG1-10
A-
differential signal A-
differential input
±20Ma/3.1-5V
500KHz
GND
JG1-11
GND
5V ground
Power ground
—
V+
JG1-12
V+
differential signal V+
differential input
±20Ma/3.1-5V
500KHz
V-
JG1-13
V-
differential signal V-
differential input
±20Ma/3.1-5V
500KHz
W+
JG1-14
W+
differential signal W+
differential input
±20Ma/3.1-5V
500KHz
W-
JG1-15
W-
differential signal W-
differential input
±20Ma/3.1-5V
500KHz
57
117

BL6-U Parallel Integrated Controller Quick Commissioning User Manual
9
3.2 PG_V6X
PG_V6X interface card is async machine universal pulse encoder speed feedback and frequency
dividing output card.
PG_V6X is in supporting use of 12V OC output and push-pull output type pulse encoder.
Encoder for async machine: A/B.
FIGURE 3.2 PG_V6X CARD
FIGURE 3.2 PG-V6X Card Port definition and Function
Port No.
Terminal
Symbol
Location
Definition
Usage
Interface Tech Spec
Interface Type
Rated Capacity
On/off
Time
Max
Speed
JENDATA (short for JEN)
0V
JEN-1
Power ground
Power ground
Power ground
—
IA
JEN-2
OC/Push-pull type A
phase input
Input signal A
OC/Push pull
input
-10Ma/12V-15V
500KHz
IB
JEN-3
OC/Push-pull type B
phase input
Input signal B
OC/Push pull
input
-10Ma/12V-15V
500KHz
+12V
JEN-4
OC/Push-pull type
power
12V Power
supply
Power output
+150Ma/12V±5%
JEN-5
+12V
JEN-6
OC/Push-pull type
power
12V Power
supply
Power output
+150Ma/12V±5%
A+
JEN-7
Freq dividing signal OC
output A
Sync freq
dividing
OC/Push pull
output
±50Ma
500KHz
B+
JEN-8
Freq dividing signal OC
output B
Sync freq
dividing
OC/Push pull
output
±50Ma
500KHz
0V
JEN-9
Power ground
Power ground
Power ground
—
GE
JEN-10
Shield ground
Shield ground
—
3.3 SPG_V6
SPG_V6 interface card is sync/async machine universal sine cosine encoder speed feedback and
frequency dividing output card.
SPG_V6 is in supporting use of 5V line driver output type sine cosine encoder. Encoder for async
57
117

BL6-U Parallel Integrated Controller Quick Commissioning User Manual
10
machine: A/B, and encoder for sync machine: A/B/R/C/D.
Refer to Figure 3.3 below for detail.
FIGURE 3.3 SPG_V6 CARD
FIGURE 3.3 SPG_V6 Interface card Port definition and Function
Port
No.
Terminal
Symbol
Locatio
n
Definition
Usage
Interface Tech Spec
Interface Type
Rated Capacity
On/off
Time
Max
Speed
JENDAT(short for JEN)
+12V
JEN-1
OC/Push-pull type
power
12V Power supply
Power output
+150mA/12V±5%
A+
JEN-2
Freq dividing signal
OC output A
Sync freq dividing
OC/Push pull
output
±50mA
500KHz
B+
JEN-3
Freq dividing signal
OC output B
Sync freq dividing
OC/Push pull
output
±50mA
500KHz
0V
JEN-4
Power ground
Power ground
Power ground
—
GE
JEN-5
Shield ground
Shield ground
—
GE
JEN-6
Shield ground
Shield ground
—
JG1
B-
JG1-1
B-
differential signal B-
differential input
40KHz
*
JG1-2
—
—
—
R+
JG1-3
R+
differential signal R+
differential input
40KHz
R-
JG1-4
R-
differential signal R-
differential input
40KHz
A+
JG1-5
A+
differential signal A+
differential input
40KHz
A-
JG1-6
A-
differential signal A-
differential input
40KHz
0V
JG1-7
GND
5V ground
Power ground
B+
JG1-8
B+
differential signal B+
differential input
40KHz
5V
JG1-9
+5V
5V Power supply
Power output
500mA/5V±2.5%
Voltage ripple
lower than 50mV
C-
JG1-10
C-
differential signal C-
differential input
40KHz
C+
JG1-11
C+
differential signal C+
differential input
40KHz
D+
JG1-12
D+
differential signal D+
differential input
40KHz
D-
JG1-13
D-
differential signal D-
differential input
40KHz
*
JG1-14
—
—
—
*
JG1-15
—
—
—
57
117

BL6-U Parallel Integrated Controller Quick Commissioning User Manual
11
3.4 SPG_V6E
SPG_V6E interface card is sync/async machine universal sine cosine encoder speed feedback and
frequency dividing output card. SPG_V6 is in supporting use of 5V line driver output type sine cosine
encoder. Encoder for async machine: A/B, and encoder for sync machine: A/B/C/D. (Suitable for
ECN1313)
FIGURE 3.4 SPG_V6E CARD
CHART 3.4 SPG_V6E TERMINAL DEFINITION &FUNCTION
56
50
111
117
Termin
al
Name
Terminal
Mark
Location
Definition
Usage
Interface Technical Specification
Interface Type
Rated
Capacity
On/Off
Time
Max
Speed
JENDAT
+12V
JEN -1
OC / push-pull Power
Supply
12V power supply
Power output
+150mA/12V
±5%
A+
JEN -2
Frequency signal OC
output A
Sync-frequency
division
OC/ push-pull
output
±50mA
500KHZ
B+
JEN -3
Frequency signal OC
output B
Sync-frequency
division
OC/ push-pull
output
±50mA
500KHZ
0V
JEN -4
Power supply ground
Power ground
Power ground
--
PE
JEN -5
Shield ground
Shield ground
D-output
--
PE
JEN -6
Shield ground
Shield ground
PGND
--
JG1
B-
JG1-1
B-
Differential signal B-
Differential
input
40KHz
*
JG1-2
--
--
--
*
JG1-3
*
JG1-2
--
--
--
*
JG1-4
*
JG1-2
--
--
--
JG1
A+
JG1-5
A+
Differential signal A+
D-input
40KHz
A-
JG1-6
A-
Differential signal A-
D-input
40KHz
0V
JG1-7
GND
5V Ground
PGND
B+
JG1-8
B+
Differential signal B+
D-input
40KHz
5V
JG1-9
+5V
5Vpower
Power output
+500mA/5V±
2.5%
Voltage
ripple<50mV
C-
JG1-10
Clock-
Differential signal C-
D-input
40KHz
C+
JG1-11
Clock+
Differential signal C+
D-input
40KHz
D+
JG1-12
Data+
Differential signal D+
D-input/output
40KHz
D-
JG1-13
Data-
Differential signal D-
D-input/output
40KHz
*
JG1-14
--
--
--
*
JG1-15
--
--
--

BL6-U Parallel Integrated Controller Quick Commissioning User Manual
12
4Parameter Need to set before Inspection Run
Note: Parameters must be saved after setting operation, otherwise the original value will be saved
after power off.
FIGURE 4.1 Parameter Need to set before Inspection Run
Parameter List
Setup Method
Parameter
No.
Name
Use BL
Sync-machine
Use Non-BL Sync-machine
Automatic Generate
F5-00
Motor Type
In blue-light
machine input,
these parameters
can generate
automatically, see
instructions below
for detail.
0: Sync machine,1: async machine. Fill in
according to actual situation.
F5-01
Poles
Follow motor nameplate
F5-02
Sync Frequency
Follow motor nameplate
F5-03
Rated Power
Follow motor nameplate
F5-04
Rated Speed
Follow motor nameplate
F5-08
Motor rated current
Follow motor nameplate
F8-00
Encoder PPR
Base on site condition
F8-02
PG card Type
PG card type (0: Incremental encoder, 1:
Sine/Cosine encoder)
Manual Input based on Site Condition
F1-00
Car Speed
Base on site condition
F1-01
Motor Speed
Motor speed at elevator rated speed (calculated)
F5-09
No-Load Current
Only for asynchronous machine; no need to set synchronous
machine. Normally set for 25%-40% of rated current.
F5-10
Rated Slip
Only for asynchronous machine; No need to set synchronous
machine. Setting according to actual situation. Calculation
method: Rated Slip = rated frequency -(rated speed * pole
pairs/60). e.g.: The motor rated slip is50-(1440*2/60)=2Hz,
when motor frequency is 50Hz, rated speed is 1440rmp, and
motor type is four-pole motor.
F6-03
DirSel (direction select)
Select according to the motor installation direction in actual
situation, Select motor running direction
(0/1: Motor rotates anti- clockwise, car move down/up).
F9-11
Load Comp Enable
Load Compensation: 1 enable; 0 Unable. If use incremental
encoder set this to 1; If use 1387 encoder at no-weighing
mode, set this to 0.
When using Blue-Light Integrated Controller, if the traction machine is also made by Blue-Light,
you only need to input the machine model number and encoder information on the machine name
plate to finish the parameter setting of the machine.

BL6-U Parallel Integrated Controller Quick Commissioning User Manual
13
Motor parameters automatically generated:
Enter the “BL Machine Input” interface as shown below from the main menu. Press [LEFT] or
[RIGHT] key to move the cursor left or right cyclically. Press [UP] or [DOWN] key to set the content of
the pointed area. The input content has three parts, separated by “.”. The first part is the model
number (separated in 4 digits), the middle part is encoder resolution information, and the last part is
the PG model.
The detail information is showing below
BL Machine Input
S1.0 D-.2.0
PG MODEL
2:2048ppr
8:8192ppr
Encoder Resolution
Machine Model
0:Incremental Encoder
1:Sine/Cosine Encoder
FIGURE 4.1 BL Machine Input Interface
Press [ENTER] button after entering complete motor and encoder information. BL series
integrated controller automatically generates motor parameters corresponding to current motor
model. Wait to exit the interface until prompting success. Then save the parameters.
If motor model entered invalid, or information entered incompletely (for example, only input
the motor model but did not enter the encoder information), interface will indicate “Invalid model”.
Please conform model and encoder information is correct before proceeding.
Try again if interface indicates fail.
BL Machine Input
-0.0 --.-.-
BL Machine Input
S1.0 D-.2.0
BL Machine Input
S1.0 D-.2.0
Waiting
BL Machine Input
S1.0 D-.2.0
Success
[ENTER]
[∧][∨]
[<][>]
BL Machine Input
S1.0 D-.2.0
Failure
FIGURE 4.2 BL Machine Input Interface
BL Machine Input
-0.0 --.-.-
BL Machine Input
S1.0 DC.2.0
Invalid model
BL Machine Input
S1.0 DC.2.0
BL Machine Input
-0.0 --.-.-
[∧][∨]
[<][>][ENTER]

BL6-U Parallel Integrated Controller Quick Commissioning User Manual
14
5Motor Initial Angle Tuning (Only for Synchronous Machine)
For machines without attached steel rope and no load, please follow section 1 “Motor Initial
Angle Tuning with no load”. For machines attached with steel rope and have load, please follow
section 2 "Motor Initial Angle Tuning with load".
(The two angle tuning modes can achieve the same effort. Please choose one of them according
to the actual situation.)
5.1 Motor Initial Angle Tuning with no load
Please set PG type F8-02 correctly, set AutoTuneModeSel FC-13 to 0 before perform Motor
initial tuning with no load (Do not attach steel ropes). Procedures required before tuning:
1) Ensure synchronous motor (traction machine) has no load (DO NOT attach steel ropes);
2) Connect running contactor output Y1 (J1-4) and COM1 (J1-5) to make it close;
3) Connect brake contactor output Y0(J1-3) and COM3 (J1-5) to release the brake;
Perform motor initial angle tuning with digital operator based on following procedures shown
below:
Angle Tune ( X0)
Para Tune ( X1)
Angle Tune ( X0 )
Tune start?
[ENTER]to start
Angle Tune ( X0 )
Tune start
Waiting
Angle Tune ( X0)
Tune End
Success
Display:success
or error codes
[ENTER]
[ENTER]
[ESC]
Press Up or
Down button
Motor Tune
FIGURE 5.1 Motor initial tuning with no load (Do not attach steel ropes) sketch
Note: Rotation angle tuning no longer distinguish encoder type.
After pressing “Enter”, tuning starts. First, motor rotates to a firm position, then it rotates
forward(facing to driving shaft, anticlockwise rotation is forward direction)in a constant speed,
rotation speed and time depends on the pole number and initial position, it stops after maximum
one round rotation, then it rotates to one position and remains for 2 seconds again, motor stops and
indicates success. The whole tuning procedure lasts less than 20 seconds.
Chart 5.1 Motor Initial Angle Rotation Tuning Fault List
Error
Code
Definition
Possible Causes
Possible Solution
RF100
Controller fault
The drive has a failure and
cannot do Initial Angle
Rotation Tuning.
Controller has met fault.
First solve fault according to error code,
then angle tuning again. Refer to Chart
VI Driver Fault List.
RF226
Give voltage limit
Already give limit force
during angle tuning, but
feedback current cannot
reach least requirement.
1. Incorrect parameters of
motor or encoder;
2. The difference between
the actual parameters of
the motor and the
estimated parameters of
the driver is too large;
3. Power matching imbalance
between motor and driver
(The motor power is far
less than the drive).
1. Check parameters of motor and
encoder;
2. Decrease F5-08 to complete tuning,
then recover F5-08;
3. Check if the power of inverter is
adapted to motor, refer 2.

BL6-U Parallel Integrated Controller Quick Commissioning User Manual
15
Chart 5.1 Motor Initial Angle Rotation Tuning Fault List (Cont'd)
Error
Code
Definition
Possible Causes
Possible Solution
RF227
Output current over limit
During the tuning process,
the driver controller
detects that the output
current has reached the
limit and stops the output,
indicating that the current
is out of limit.
1. Incorrect parameters of
motor or encoder;
2. The difference between
the actual parameters of
the motor and the
estimated parameters of
the driver is too large;
3. Power matching
imbalance between motor
and driver (The motor
power is far more than the
drive).
1. Check parameters of motor and
encoder;
2. Increase F5-08 to complete tuning,
then recover F5-08;
3. Check if the power of inverter is
adapted to motor, refer 2.
RF228
ESC input
During the tuning process,
ESC input is effective, and
self-tuning is cancelled.
The hand operator triggers the
ESC button to cancel angle
tuning.
Angle tuning interruption, failure to
complete, please do angle tuning again.
RF229
Over time at zero speed
In the process of tuning,
when the rotor is
positioned, the feedback
speed is not zero for a
long time, and it cannot
locate accurately.
1. Motor carrying partial
load;
2. Bad feedback speed of
encoder.
1. Ensure brake is off;
2. Remove interference of encoder.
RF231
CD signals of encoder is
abnormal
In the process of tuning, it
is found that CD feedback
position value is
abnormal, and it is
impossible to identify the
CD line sequence.
1. Parameters of motor or
encoder have been
wrongly input;
2. Interference in encoder;
3. Error input of motor or
encoder;
4. Wrong PG type set.
1. Check CD signals wiring;
2. Remove interference;
3. Verify parameters of motor and
encoder;
4. Check PG type set.
RF232
Motor does not rotate
In the process of tuning,
the driver cannot control
the normal rotation of the
motor.
1. Encoder connection fault,
no feedback speed;
2. Motor has load or brake
close;
3. The power difference
between the motor and
the driver is too large and
does not match.
1. Check encoder A&B signal
connection, elimination of encoder
signal interference;
2. Make sure motor has no load &
brake open;
3. Check the parameters of the
number of the motor and the
number of the encoder;
4. Detect of power matching of motor
and driver controller, reduce the
rated current [F5-08], and resume
F5-08 after tuning.
RF233
Motor rotates in wrong
direction
In the process of tuning,
the direction of the motor
is not consistent with the
control direction, and
there is a reverse rotation.
Motor phase sequences does
not match encoder.
1. Adjust motor phase sequence;
2. Adjust encoder A-, A+ or B-, B+.
RF234
Encoder R pulse signal
error
R pulse signal was not
detected for a long time in
the process of tuning.
1. No detection of R pulse
signal;
2. Interference of encoder
signal;
3. Error input of motor or
encoder;
4. In the course of tuning,
the motor is rotated in
distress.
1. Check wiring for R pulse signal;
2. Elimination of encoder signal
interference;
3. Verifying the number of motor
poles and the number of encoder
lines;
4. Open or close the brake in the
process of self-learning.

BL6-U Parallel Integrated Controller Quick Commissioning User Manual
16
Note:
1. Above description is for SIN/COS encoder;
2. For increment encoder, RF231 correspond to UVW signals, RF234 correspond to Z
pulse. The solution is same, and other faults are same too.
5.2 Motor Initial Angle Tuning with load
For this tuning method, tuning can be carried out with steel rope attached, but please make
sure the following procedures are finished correctly before tuning:
1) Wiring in control cabinet is completely correct, and system under inspection state;
2) Set running parameter(F1), motor parameter(F5), encoder parameter(F8) correctly;
3) All mechanical faults in hoistway are eliminated!
5.2.1 Motor Initial Angle Tuning with Digital Operator
Correctly set PG type F8-02 on digital operator, set tuning method parameter (FC-13) to “1”
(default setting is 1 in BL Series Integrated Controller), perform motor initial angle tuning based on
following procedures shown below:
Angle Tune ( X0)
Para Tune ( X1)
Angle Tune ( X0 )
Tune start?
[ENTER]to start
Angle Tune ( X0 )
Tune start
Waiting
Angle Tune ( X0)
Tune End
Success
Display:success
or error code
[ENTER]
[ENTER]
[ESC]
Press Up or
Down button
Motor Tune
FIGURE 5.2 Motor initial tuning with load (attach steel ropes) sketch
After pressing “Enter”, tuning starts. When digital operator indicates “waiting” , press jog up or
down button , contactor KDY closes, motor will vibrate a little and give a noise, the duration depends
on motor rated power and rated current, but no longer than 5 seconds, this is static tuning
period.(Motor keep still in this procedure.);(Make sure jog up or down button is pressed constantly,
DO NOT release the button during this period.)Motor will then start and run in inspection speed, jog
up or down, until digital operator indicates success, this is a test running period. Finally, release the
jog up or down button and finish the tuning procedure.
5.2.2 Motor Initial Angle Tuning With digital tubes and operation keys on the upper left of main
board
Prefer to contents of appendix VII.
5.2.3 Please note the following items at Motor initial Angle tuning with load (attach steel ropes):
1) To ensure safety, during tuning process, people are not allowed to stay in car/hoistway.
2) Press jog up or down button can base on the current cabin position;
3) The whole tuning procedures can be divided into two steps: static tuning and motor test run,
make sure there is no gap between two steps. If no fault happens, before digital operator
indicates success, press the jog up or down button constantly (Except fault or error exists!);
4) If car running direction is opposite to inspection run button, correct this through F6-03.0:
traction sheaves counterclockwise rotation & car run down;1: traction sheaves clockwise
rotation & car run up (facing to traction sheaves). Set according to actual situation.

BL6-U Parallel Integrated Controller Quick Commissioning User Manual
17
Chart 5.2 Motor initial Angle tuning with load (attach steel ropes) error code
Error
Code
Definition
Possible Causes
Possible Solution
RF100
Controller fault
The drive has fault and
cannot do tuning.
Controller has met fault
First solve fault according to error code,
then angle tuning again. Refer to Chart
VI Driver Fault List.
RF226
Give voltage limit
Already give limit force
during angle tuning, but
feedback current
cannot reach least
requirement.
1. Incorrect parameters of motor
or encoder;
2. The difference between the
actual parameters of the motor
and the estimated parameters
of the driver is too large;
3. Power matching imbalance
between motor and driver (The
motor power is far less than
the drive).
1. Check parameters of motor and
encoder;
2. Decrease F5-08 to complete
tuning, then recover F5-08;
3. Check if the power of inverter is
adapted to motor, refer 2.
RF227
Output current over
limit
During the tuning
process, the driver
controller detects that
the output current has
reached the limit and
stops the output,
indicating that the
current is out of limit.
1. Incorrect parameters of motor
or encoder;
2. The difference between the
actual parameters of the motor
and the estimated parameters
of the driver is too large;
3. Power matching imbalance
between motor and driver (The
motor power is far more than
the drive).
1. Check parameters of motor and
encoder;
2. Increase F5-08 to complete tuning,
then recover F5-08;
3. Check if the power of inverter is
adapted to motor, refer 2.
RF228
ESC input
During the tuning
process, ESC input is
effective, and
self-tuning is cancelled.
1. Release Up or Down button
while tuning;
2. Fault occurs during angle
tuning.
1. Angle tuning interruption, failure
to complete, please do angle
tuning again. Do not forced to run,
there is a danger of losing control.
2. Check whether there is elevator
logic fault, resulting in stop tuning.
Refer to Chart V Elevator System
Faults List.
RF229
Over time at zero speed
Over time at zero speed
Before start, feedback
speed is not zero for a
long time
1. Brake open or brake force is
not enough;
2. There’s interference in encoder.
1. Ensure brake is off;
2. Remove interference of encoder.
RF230
Current detection error
During the tuning
process, the feedback
current value
ultra-lower limit and
the self-tuning
condition is not
satisfied.
1. Broken circuit at load side or
lack of phase;
2. Imbalance phase of motor side
or rated current wrongly set;
3. Inverter cannot adapt to motor.
(Motor capacity is highly lower
than inverter)
1. Ensure 3-phase connection to
motor;
2. Ensure motor parameters setting;
3. Ensure motor should adapt to
inverter.
RF231
CD signals of encoder is
abnormal
In the process of tuning,
it is found that CD
feedback position value
is abnormal, and it is
impossible to identify
the CD line sequence.
1. Parameters of motor or
encoder have been wrongly
input;
2. Interference in encoder;
3. Error input of motor or
encoder;
4. Wrong PG type set.
1. Check CD signals wiring;
2. Remove interference;
3. Verify parameters of motor and
encoder;
4. Check PG type set.

BL6-U Parallel Integrated Controller Quick Commissioning User Manual
18
Chart 5.2 Motor initial Angle tuning with load (attach steel ropes) error code (Cont'd)
Error
Code
Definition
Possible Causes
Possible Solution
RF237
Motor moved while static
angle calculation
When the motor angle position
is inferred static, the motor
cannot rotate to obtain the
determined current position.
1. Brake open or brake force
is not enough;
2. Bad encoder wire or
interference in encoder.
1. Ensure brake is closed;
2. Check encoder A, B signals,
remove interference
PF238
Detection current is too small
In the Initial angle static tuning
process, the output current
value is lower than the lower
limit, and the tuning condition
is not satisfied.
1. The rated current of the
motor may not be in
conformity with the actual
motor;
2. Motor/Controller
connection is incorrect.
(Break circuit or phase
lost)
1. Check motor/controller
connection;
2. Check rated current and rated
power of motor.
PF239
Encoder R pulse signal lost
No encoder R pulse signal
detected after motor tuning for
10s
1. Interference in R pulse
signal;
2. A & B signals connection
error;
3. Inspection elevator speed
setting is too low.
1. Check the encoder wiring;
2. Remove the encoder
interference;
3. Ensure the normal operation of
the motor;
4. Inspection elevator speed
setting is too low.
RF252
While static angle tuning,
motor speed is over proof
During static angle tuning, after
initial location, motor need to
rotate for 3 rounds. During
rotating, system give out speed
but receive no feedback and
the lasting time of this status
has been over limit. Then
system announce error.
1. Check if there is feedback from
SIN/COS encoder;
2. Check the phase of power
input.
Note:
1. Above description is for SIN/COS encoder;
2. For increment encoder, RF231 correspond to UVW signals, RF234 and RF239
correspond to Z pulse. The solution is same, and other faults are same too.

BL6-U Parallel Integrated Controller Quick Commissioning User Manual
19
6Asynchronous Motor Adjustment
Asynchronous motor does not need angle tuning. But compared with synchronous motor,
NO-Load Current (F5-9) and Rated Slip (F5-10) should be adjusted. The parameters and information
below should be confirmed as well (parameters below are different with synchronous motor).
6.1 Motor Parameters Confirmation
Chart 6.1 Motor Parameters Confirmation
Para
No.
Display
Content
Range
Parameter setting
requirements
F5-00
Motor Type
Set motor type
0: sync- outer rotor,
1: async machine,
2: sync-inner rotor
0~2
1
F5-01
Poles
Motor poles
(Nameplate)
1~99
Fill in according to actual
motor parameters
F5-02
Sync Freq
Motor synchronous
frequency
(Nameplate)
0.001~50
Fill in according to actual
motor parameters
F5-03
Rated Power
Motor rated power
(Nameplate)
1~50
Fill in according to actual
motor parameters
F5-04
Rated Speed
Motor rated speed
(Nameplate)
1~1999
Fill in according to actual
motor parameters
F5-08
Rated FLA
Motor rated current.
(Nameplate)
0~99.999
Fill in according to actual
motor parameters
F5-09
NO-Load Current
For asynchronous
machine, no-load
excitation current.
0.1~50
Fill in according to 30% rated
current, adjustable in 20% to
40%;
If rated current is set too
small, motor will run with
howling sound; If set too
large, fluctuation feeling will
be obvious in steady speed
period.
F5-10
Rated Slip
For asynchronous
machine rated slip.
(Nameplate)
0.1~10
Rated Slip=rated freq-(Rated
Speed× pole pairs/60)
If rated Slip is set too small,
motor speed could not keep
pace during acceleration--OE
fault.
If set too large, motor could
not keep pace with
acceleration Ref in steady
period or indicate
overcurrent fault.
6.2 Encoder Parameters Confirmation
Table of contents
Popular Controllers manuals by other brands
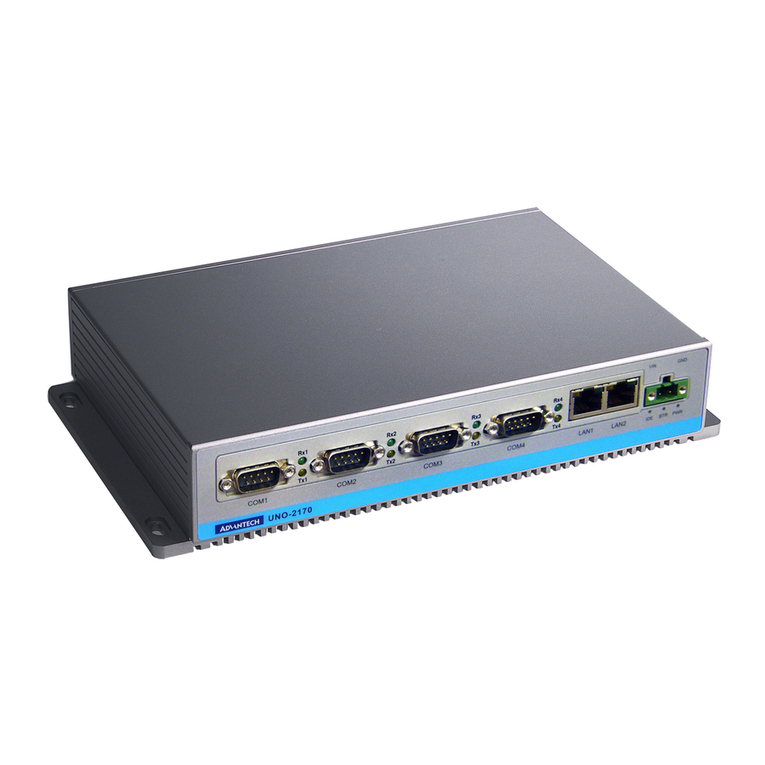
Advantech
Advantech Celeron M Universal Network Controller with PC/104 Extension... user manual
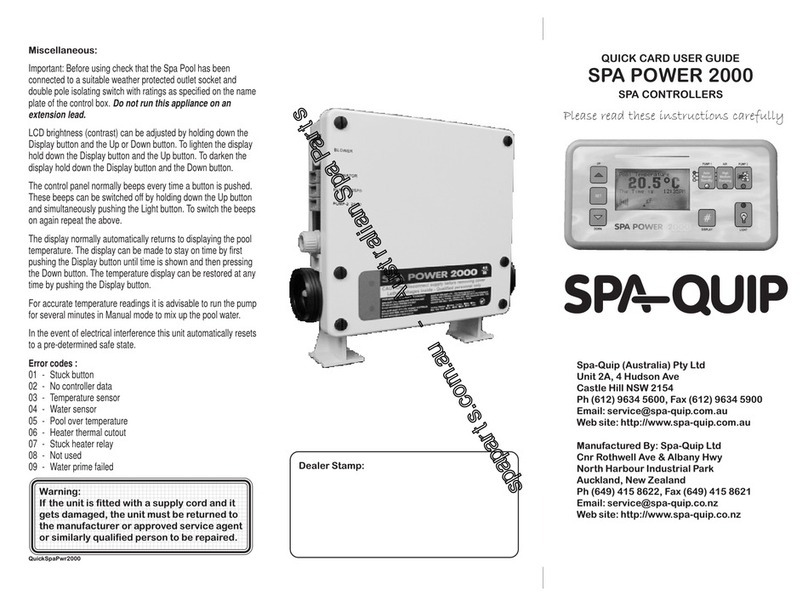
Spa-Quip
Spa-Quip SPA Power 2000 user guide
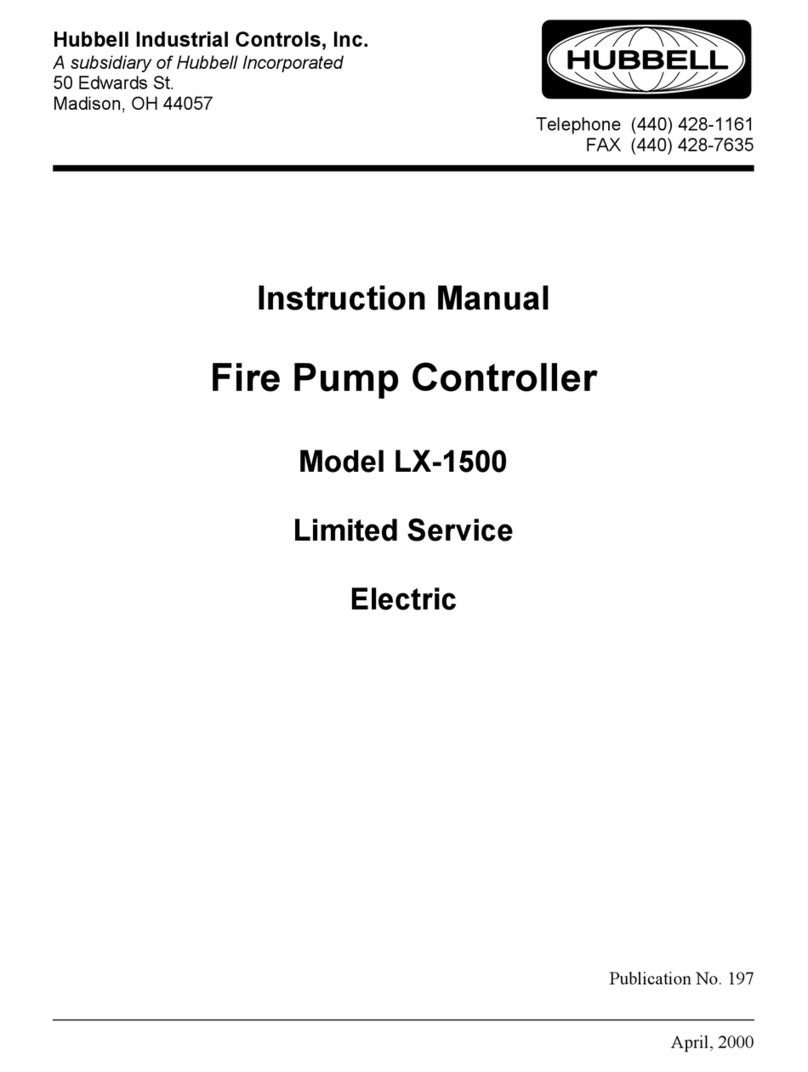
Hubbell
Hubbell Fire Pump Controller LX-1500 instruction manual
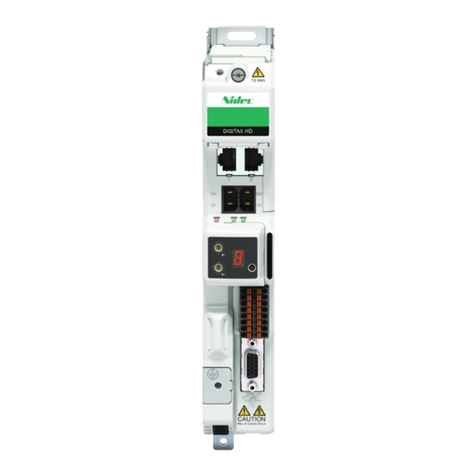
Nidec
Nidec Digitax HD M75 Series Installation and technical guide
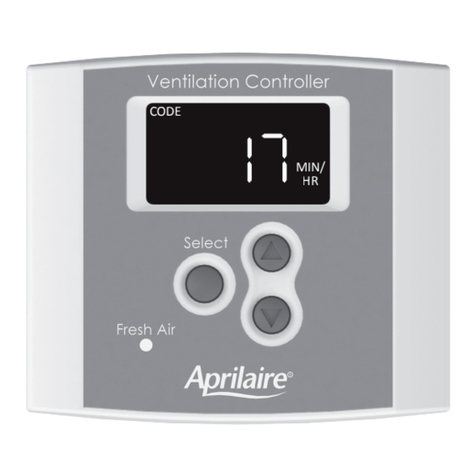
Aprilaire
Aprilaire 8120X Installation and operation manual
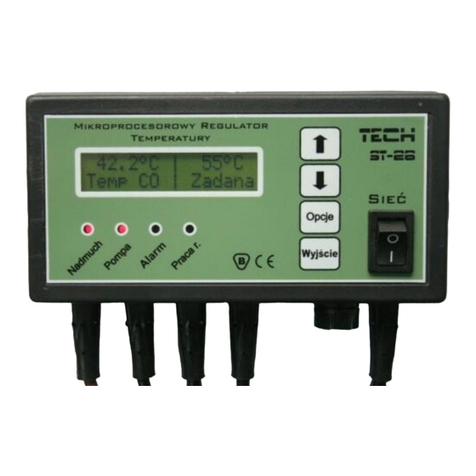
TECH
TECH ST-26 Manual guide
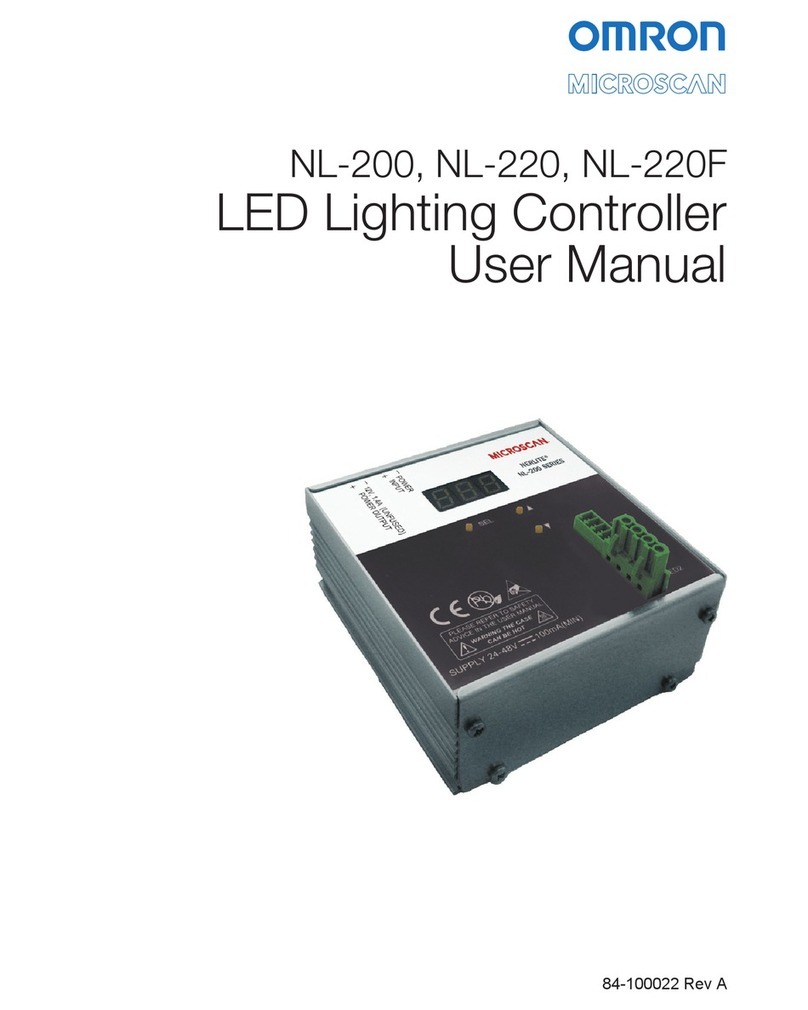
Omron
Omron NL-200 user manual
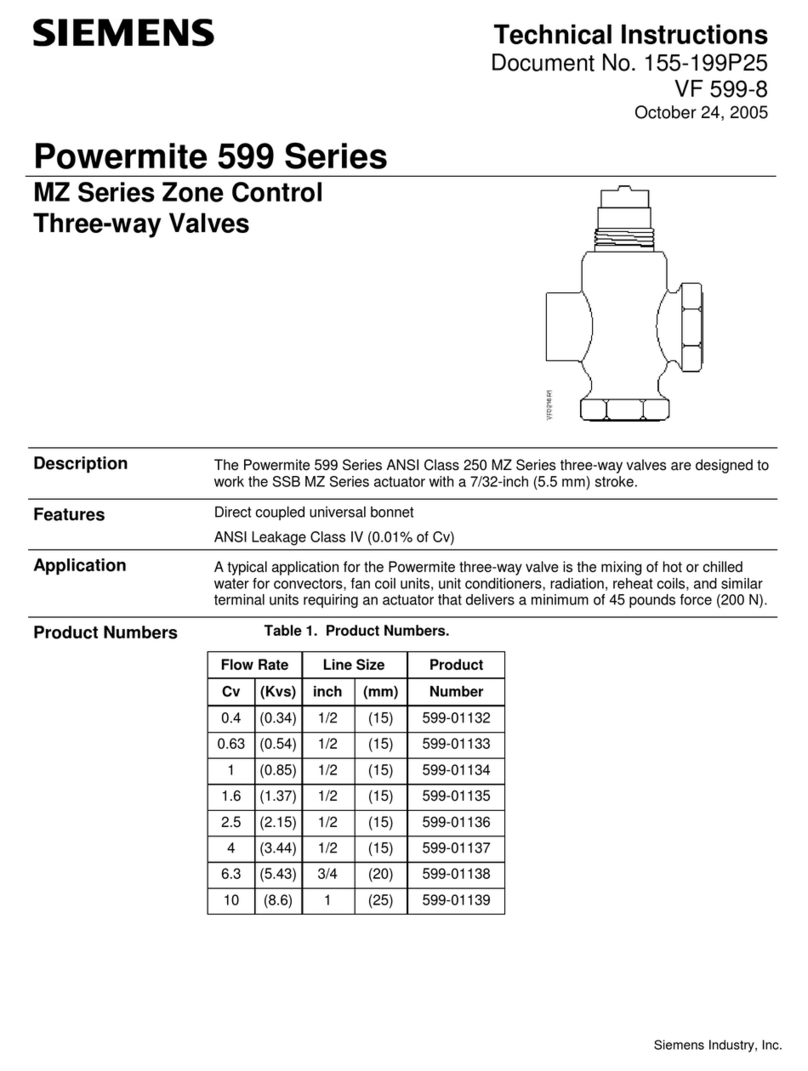
Siemens
Siemens Powermite 599 Series Technical instructions
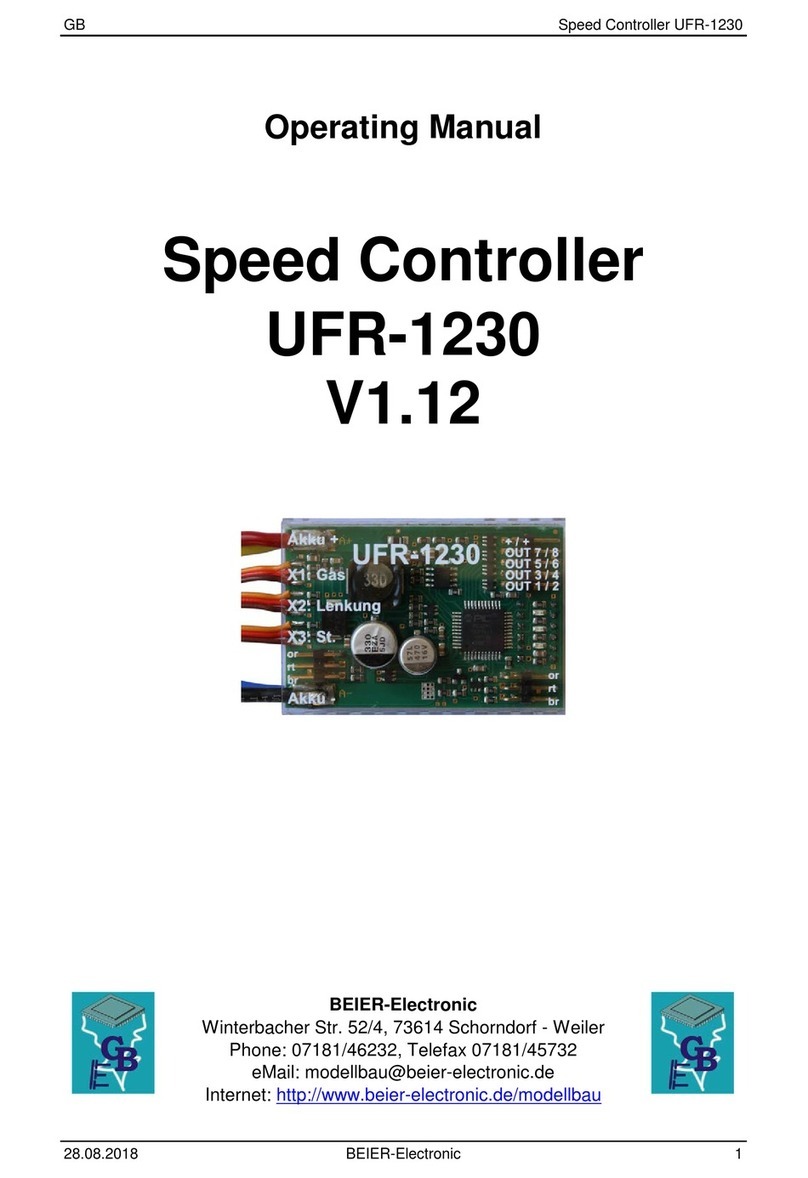
BEIER-Electronic
BEIER-Electronic UFR-1230 operating manual
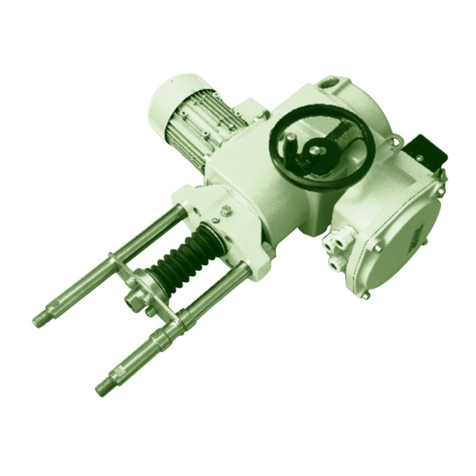
ZPA Pecky, a.s.
ZPA Pecky, a.s. MODACT MTNED Series Mounting instructions
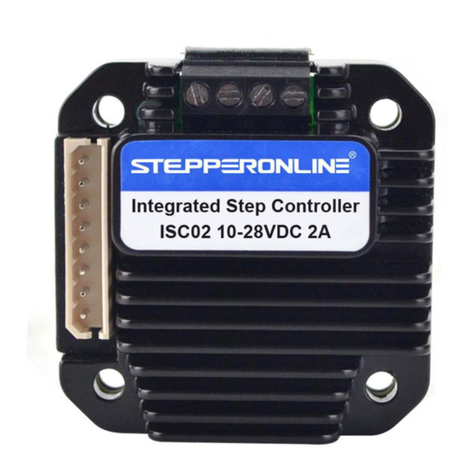
StepperOnline
StepperOnline ISC02 user manual

LOVATO ELECTRIC
LOVATO ELECTRIC ATL500 instruction manual