Brother MD-802 User manual

brother
DC
MOTOR
SERVICE
MANUAL
MD-802
(Single-Phase
Type)
MD-812
(Three-Phase
Type)
BROTHER
INDUSTRIES,
LTD.
KIA^nVA
IADAM

INTRODUCTION
This
service
manual
is
compiled
for
the
technical
staff
who
maintain
and
inspect
the
drive
motor
designed
for
the
auto¬
matic
thread
trimming
machine.
The
manual
describes
the
motor
and
the
control
box
and
also
covers
adjustments.
Read
the
service
manual
carefully
so
that
you
understand
the
right
handling
and
adjustment.
TABLE
OF
CONTENTS
(
tDESCRIPTION
OF
THE
MOTORj
)
1
(
^NAME
OF
EACH
COMPONENT^
).
2
((
JNAME
OF
EACH
PA^f^
).
3
((
configuration")).
4
(
(principle
of
control
system^
)
5
(
(
ADJUSTMENT
(
j)...
7
[T1
DC
Servomotor
.
7
|~2]
Needle
position
detector
(synchronizer).
7
[3]
Control
box.
9
[4]
Treadle.
10
[¥]
Brush
replacement.
10
[6]
Motor
brake
spacing.
11
[7]
Checking
the
lamp
terminal
code.
11
[8]
Standing
work
machine.
12
[9]
Application
to
production
control
system.
13
(j(
OPERATION
INSTRUCTION^)
fT]
Installation
of
operation
box
.
14
[2]
M
otor
and
control
box
(Models
DB2-B737
•
B747
■
B748
•
B791
-
B793
•
B795
•
B798).
14
[|]
Operation
box
(Models
DB2-B737
■
B747
•
B748
•
B791
•
B793-B795
•
B798).
15
(
tBLOCK
DIAGRAM
OF
CONTROL
CIRCUIT^
)
18
Q]
Single-phase/100V
(Models
DB2-B737
-
B747
•
B791
•
B793
•
B795
•
B798)
.
18
[2]
Three-phase/200V
(Models
DB2-B737
•
B747
■
B791
•
B793
•
B795
•
B798)
.
19
[3]
Single-phase/100V
type
#470B
(Model
DB2-B738)
.
20
[4]
Three-phase/200V
type
#470
(Model
DB2-B738).
21

(
f
DETAILS
OF
CONNECTOR
R4N^T7
))
22
[1]
Model
DB2-B737
•
B747
•
B748
•
B791
•
B793
■
B795
•
B798
(Type
300B).
22
[2]
Model
DB2-B738
(Type
#4706).
23
(
(
TROUBLE
SHOOTING
24
C
(CHECKING
THE
MOTOR
J
)
.
25
Q]
Motor.
25
[2]
Brake.
25
t
CHECKING
THE
MACHINE
SOLENOIDS
)
)
26
[~T~1
Solenoid
load
of
the
machine.
26
[j]
Hem
sensor.
26
|~3~1
B737
Machine
control
system
block
diagram..
27
[
4
]
B738
Machine
control
system
block
diagram.
28
[
5
]
B737
•
B738
Motor
drive
control
system
block
diagram.
29

(C
DESCRIPTION
OF
THE
MOTOlT))
★
The
Brother
DC
motor
is
best
suited
for
the
energy
saving
works.
To
save
sewing
labor
and
enhance
the
automation,
advanced
functions
are
installed
with
the
reliable
unit-design.
FEATURES
1.
Energy
Saving
Power
rates
is
saved
about
50%
with
the
DC
servomotor,
as
compared
with
the
clutch
motor
we
have
made.
When
the
sewing
machine
is
stopped,
the
DC
motor
is
also
stopped,
resulting
in
highly
effective
energy
saving.
2.
Quiet
Operation
While
the
clutch
motor
produces
windy
or
idling
sounds
and
vibrations,
the
DC
motor
is
free
from
them
because
it
does
not
run
when
the
sewing
machine
is
stopped.
3.
Easy
Maintenance
The
maintenance
is
easily
done
just
by
adjusting
the
solenoid
brake
spacing.
There
is
no
need
to
replace
the
moving
brake
plate.
4.
Reliability
The
microcomputer
and
hybrid
ICs
are
adopted
with
higher
integration,
so
that
higher
reliability
is
obtained.
5.
Free
Control
of
Sewing
Speed
The
sewing
speed
is
freely
controlled
just
by
the
adjustment
knob.
By
the
high
speed
volume
knob,
the
speed
is
con¬
trolled
from
215
spm
to
the
maximum
speed.
And
by
the
reinforcement
sewing
speed
knob,
the
speed
is
controlled
from
215
spm
to
3,000
spm.
6.
Applicable
to
Standing
Work
and
Automation
The
application
for
standing
works
and
automation
is
secured
just
by
connecting
the
switch
to
the
plug
of
the
control
box.
7.
Lightweight
The
DC
motor
weights
less
10
kg,
as
compared
with
the
clutch
motor.
[DB2-B737]
[DB2-B738]
★
Use
the
DC
motor
for
the
following
sewing
machines.
*The
DC
motor
is
also
applied
to
the
automatic
thread
trimming
machines,
models
DB2-B748,
B795,
and
B798.
[DB2-B793]
[DB2-B791
]


CONTROL
CIRCUIT
UNIT
NOTE:
The
sections
enclosed
by
the
broken
line
indicate
where
high
voltage
is
applied.
Handle
these
sections
with
great
care.
CAUTION:
1.
In
setting
down
the
machine
head
or
touching
the
needle,
be
sure
to
turn
off
the
power
switch
and
confirm
the
pilot
lamp
“OFF”.
2.
Ground
codes
are
provided
for
both
single-phase
and
three-phase
types.
Do
not
fail
to
ground.
(A
ground
code
is
not
Do
not
fail
to
ground.
(A
ground
code
is
not
provided
for
single-phase
110V
type,
however,
ground
the
motor
frame
if
necessary.)
3.
In
adjusting
the
volume
in
the
controi
box,
be
sure
to
turn
off
the
power
switch,
remove
the
front
cover
and
confirm
the
pilot
lamp
“OFF”.
*
It
is
dangerous
to
handle
the
control
box
inside
because
high
voltage
is
applied.
Handle
with
great
care.
4.
Keep
away
from
such
machines
which
make
strong
noise
as
high
frequency
welder
for
usage.

C(
PRINCIPLE
OF
CONTROL
SYSTEM
1.
When
the
power
switch
O
is
turned
on
and
the
treadle
3
is
stepped
on,
the
start
signal
and
the
voltage
correspond¬
ing
to
the
stepping
degree
are
supplied
to
the
control
box
©
by
the
treadle
unit.
The
voltage
is
supplied
to
the
motor
©
by
the
control
circuit
board
in
the
control
box
©
so
that
the
motor
runs
in
proportion
to
the
stepping
degree
to
drive
the
sewing
machine.
2.
When
the
treadle
©
is
returned
to
the
neutral
position
(with
foot
off),
the
neutral
signal
is
sent
to
the
control
box
©
by
the
treadle
unit
©
and
the
brake
command
is
given
by
the
control
circuit
board
to
decelerate
the
motor
©.
Then
the
signal
from
the
synchronizer
©,
mounted
on
the
pulley
of
the
sewing
machine,
is
sent
to
the
control
box
©
and
the
brakes
are
applied
so
that
the
operation
of
the
sewing
machine
is
stopped
at
the
needle
down
stop
position
set
by
the
synchronizer
©.
3.
When
the
treadle
is
stepped
on
again,
the
thread
trimming
signal
is
sent
to
the
control
box
©
by
the
treadle
unit
©
and
the
command
is
given
by
the
control
circuit
board
to
run
the
motor
©
at
the
thread
trimming
speed
(inching
speed).
Then
the
signal
from
the
synchronizer
©
is
sent
to
the
control
box
©
and
the
brakes
©
are
applied
so
that
the
operation
of
the
sewing
machine
is
stopped
at
the
needle
up
stop
position
set
by
the
synchronizer
©.

Drawing
for
Mounting
the

((
ADJUSTMENT
))
★
Set
down
the
machine
head
and
then
hang
the
belt
on
the
motor
pulley
and
the
machine
pulley.
★
The
belt
comes
to
fit
the
machine
pulley
and
the
motor
pulley,
which
happens
to
loosen
the
belt
tension
sometimes.
Check
the
belt
tension.
★
The
machine
rotates
counterclockwise
as
seen
from
the
pulley
side.
★
Adjust
the
belt
O
by
loosening
the
set
screw
0
and
turning
the
nut
0
so
that
it
loosens
about
10
mm
when
pressed
by
finger.
Needle
position
detector
(synchronizer)
Model
DB2-B747
•
B791
•
B793
•
B795
•
B798
★
Take
off
the
synchronizer
cover
for
adjustment.
Synchronizer
detects
the
needle
by
two
hole
IC
and
controls
the
needle
down
signal
and
the
thread
trimming
signal
by
one
hole
IC.
Needle
down
Needle
up
stop
position
stop
position
5
mm
Model
B798
22
~
26
mm
7.5
mm
11
~
1.4
mm
*In
adjusting
each
hole
IC,
do
not
fail
to
turn
off
the
power
switch.
Position
Adjustment
for
Needle
Down
Signal
★
Turn
the
machine
pulley
this
side
and
set
the
needle
5
mm
up
from
the
bottom
to
coincide
the
lower
end
of
the
magnet
O
with
the
upper
end
of
the
thread
trimming
needle
down
hole
IC
0
.
(As
for
the
model
B747
•
B748,
adjust
the
needle
7
mm
up
from
the
bottom
and
as
for
the
model
B798,
7.5
mm
up.)
When
the
lower
end
of
the
magnet
O
does
not
coincide
with
the
upper
end
of
the
thread
trimming
needle
down
hole
IC
0
,
loosen
the
screw
0
and
move
the
thread
trimming
needle
down
hole
IC
for
adjustment.
When
the
thread
trimming
needle
down
hole
IC
0
is
moved
in
the
rotating
direction,
the
needle
bar
comes
up.
And
when
in
the
reverse
direction,
the
needle
bar
comes
down.
Turn
on
the
power
switch
and
stop
the
machine
at
the
needle
down
stop
position
so
that
the
distance
between
the
top
of
the
needle
plate
and
the
lower
end
of
the
needle
clamp
screw
is
18-22
mm.
(As
for
the
model
B798,
the
distance
is
22-26
mm.)
Position
Adjustment
for
Needle
Up
Signal
★
Stop
the
machine
at
the
needle
up
stop
position.
The
needle
point
stops
9-11
mm
away
from
the
top
of
the
needle
plate
for
thin
and
medium
materials,
and
10-12
mm
for
thick
materials.
(As
for
the
model
B798,
the
needle
point
stops
11-14
mm
away.)
When
the
needle
point
does
not
stop
properly,
loosen
the
screw
0
and
move
the
needle
up
stop
hole
IC
0
for
adjustment.
When
the
needle
up
stop
hole
IC
0
is
moved
in
the
rotating
direction,
the
needle
bar
comes
down.
And
when
in
the
reverse
direction,
the
needle
bar
comes
up.
*
Tighten
the
screws
0
and
©by
the
force
of
6-10
kg-cm.

Synchronizer
Model
DB2-B737
•
B748
★
The
synchronizer
detects
the
needle
position
with
two
sensors.
The
thread
trimmer
signal
is
timed
to
the
needle
down
position
signal
and
the
treadle
reverse
signal.
★
When
the
power
is
turned
on
and
the
needle
stopped
in
the
down
position,
the
distance
between
needle
plate
top
and
needle
set
screw
bottom
should
be
18
to
22
mm.
When
the
needle
is
stopped
in
the
up
position
and
the
pulley
reference
line
is
within
the
belt
cover
reference
lines,
the
distance
between
needle
plate
top
and
needle
tip
should
be
10
to
12
mm
with
thin
and
regular
materials,
10
to
14
mm
with
thick
materials.
(As
for
the
Model
B748
the
needle
up
stop
position
10
~
14
mm.)
Adjust
as
follows
when
necessary.
★
Turn
the
power
off.
Needle
up
position
1.
S
lightly
loosen
the
two
screws
O
■
Move
the
set
screws
O
in
the
direction
of
normal
pulley
movement
to
raise
the
needle
bar
©
stop
position.
Turn
the
other
way
to
lower
the
needle
bar.
Needle
down
position
1.
Set
the
treadle
to
reverse
and
then
release
it
to
neutral.
(This
is
the
needle
down
stop
position.)
2.
The
needle
plate
top
to
needle
screw
bottom
gap
should
be
18
~
22
mm.
3.
Loosen
screw
©
and
move
the
synchronizer
©
to
adjust.
*
Check
the
needle
up
stop
position.
*
When
the
machine
pulley
is
removed
once,
provide
0.5
mm
clearance
between
the
pulley
bottom
and
the
synchro¬
nizer
for
installation.
(Improper
clearance
causes
improper
machine
operation)
When
the
Synchronizer
Is
Out
Of
Order
.
.
.
★
Turn
off
the
power
switch
and
pull
out
the
synchronizer
code.
Use
the
machine
with
standard
function
(without
thread
trimming)
until
the
synchronizer
is
replaced.

~3~]
Control
box
Control
Box
(Model
DB2-B737)
The
high
speed
volume,
backtack
stitch
volume,
power
lamp,
needle
position
switch,
one-stitich
modification
switch,
slow
start
switch
and
connector
for
synchronizer
and
connector
for
control
box
are
arranged
on
the
front
of
the
control
box.
All
these
parts
are
already
provided
on
the
control
circuit
board.
The
control
circuit
board
is
installed
on
the
inside
of
the
control
box.
The
power
circuit
board
is
at
the
back
and
the
treadle
unit
is
on
the
left
side
wall.
The
right
side
wall
is
furnished
with
one
15A
fuse
for
the
110-240V
single-phase
type,
two
5A
fuses
for
the
200-
240V
three-phase
type
and
two
3A
fuses
for
380-440V
three-phase
type.
The
control
circuit
board
is
provided
with
the
8A
fuse
for
solenoid
load.
*Do
not
fail
to
secure
the
fuse
holder
cap
after
replacing
or
inspecting
the
fuses.
*
Never
short-circuit
the
lamp
terminal
(AC
6V
terminal)
for
lighting,
or
the
transformer
may
be
broken.
Control
circuit
board
Explanation
of
Each
Volume
Knob
*Do
not
turn
the
volume
knobs
when
not
necessary.
Model
B737
•
B747
•
B748
B791
•
B793
•
B795
•
B798
1.
Take
off
the
front
cover.
2.
When
the
VR1
©
(low
speed
and
thread
trimming)
is
turned
clockwise,
the
low
machine
speed
is
adjusted
to
increase.
3.
When
the
VR2
©
(backtacking
speed)
is
turned
clockwise,
the
backtacking
speed
is
adjusted
to
increase.
4.
When
the
VR5
©
(brake-off
time
setting)
is
turned
clockwise,
the
brake
force
is
adjusted
to
increase.
And
when
counterclockwise,
it
is
ad¬
justed
to
decrease.
5.
When
the
TVR
©
(torque
setting)
is
turned
clock¬
wise,
the
torque
is
adjusted
to
increase.
CAUTION:
Other
volume
knobs
are
factory
set,
so
that
they
never
require
adjustment
anymore.
1.
Take
off
the
front
cover.
2.
When
theVRl
O
(low
speed
and
thread
trimming)
is
turned
clockwise,
the
low
machine
speed
is
adjusted
to
increase.
3.
The
VR2
©
(backtacking
speed)
is
preset
at
1800
spm,
so
it
never
requires
adjustment
any¬
more.
(Do
not
touch
the
VR2,
or
the
stop
position
varies.)
4.
The
VR3
0
(automatic
speed)
is
changed
by
the
maximum
sewing
speed
volume
knob,
so
the
VR3
requires
no
adjustment.
5.
When
the
TVR
©
(torque
setting)
is
turned
clock¬
wise,
the
torque
is
adjusted
to
increase.
6.
When
the
VR1
0
(brake-off
time
setting)
is
turned
clockwise,
the
brake
force
is
adjusted
to
increase.
And
when
counterclockwise,
it
is
ad¬
justed
to
decrease.
CAUTION:
Other
volume
knobs
are
factory
set,
so
that
they
never
require
adjustment
anymore.
NOTE
1:
It
is
dangerous
to
touch
the
volume
knobs
by
finger
because
high
voltage
is
applied.
Do
not
fail
to
turn
off
the
power
switch
before
adjustment.
To
check
the
setting,
turn
it
on
again.
NOTE
2:
Take
care
that
the
driver
does
not
touch
other
parts
but
the
volume
knobs
for
adjustment.
Adjust
the
volume
knobs
with
great
care.
They
may
be
broken
if
turned
over
the
stopper.
NOTE
3:
When
any
volume
knob
is
turned
by
mistake,
turn
it
back
so
that
the
red
paint
marks
match
with
each
other.

1~4~]
Treadle
Stepping
Pressure
★
If
the
machine
starts
running
at
low
speed
just
by
placing
your
foot
on
the
treadle
or
by
stepping
on
it
lightly,
the
adjustment
is
required
to
change
the
position
[(a)
through
(d)]
where
the
treadle
spring
O
is
hung
on
the
treadle
lever
@.
*
The
stepping
pressure
is
required
more
in
the
order
from
(a)
to
(d).
Stepping
Back
Pressure
★
Loosen
the
nut
0
and
turn
the
bolt
O
for
adjust¬
ment.
When
the
bolt
Q
is
tightened,
the
stepping
back
responds
heavily.
And
when
loosened,
it
responds
lightly.
Stepping
Stroke
★
When
the
nut
0
is
removed
and
the
connecting
joint
0
is
moved
as
shown
in
the
figures
A
and
B,
the
stepping
stroke
increases
by
80%.
When
the
stepping
stroke
is
changed,
the
stepping
and
the
stepping
back
pressures
change
and
require
re¬
adjustment.
1.
Be
sure
to
turn
off
the
power
switch.
2.
Disconnect
the
motor
plug.
3.
Remove
the
clamp
screws
O-
4.
Remove
the
brushes
0
5.
After
checking
the
reference
line
of
the
brush
©,
mount
the
usable
brush
0
so
that
the
reference
line
0
directs
toward
the
treadle
unit.
Replace
the
brush
used
to
the
reference
line
0
with
a
new
one.
6.
Tighten
the
clamp
screws
O
with
10-15
kg/cm
torque.
7.
Connect
the
motor
plug.

~6]
Motor
brake
spacing
★
Adjust
the
brake
spacing
when
about
two
years
have
passed.
And
also
adjust
when
the
brake
generates
abnormal
noises
and
does
not
stop
stably.
Adjustment
Procedures
1.
It
is
recommended
that
you
remove
the
motor
pulley
and
measure
the
brake
spacing
in
advance.
The
brake
spacing
is
factory
set
at
approx.
0.2
mm.
2.
Remove
the
screw
O
and
the
pulley
cover
©.
3.
Remove
the
V
belt.
4.
Remove
the
nut
©
and
the
motor
pulley
assembly
©.
5.
Remove
the
washer
©
from
the
shaft
©
so
that
the
brake
spacing
becomes
0.2
mm.
The
washer
©
is
available
with
the
thickness,
0.1
mm,
0.15
mm
and
0.3
mm.
Adjust
the
brake
spacing
approx.
0.2
mm
by
removing
the
washer
©.
|T]
Checking
the
lamp
terminal
code
★
The
lamp
terminal
code
O
is
provided
at
the
back
of
the
control
box.
The
AC
6
V
lamp
can
be
con¬
nected
with
this
lamp
terminal
code.
CAUTION:
Be
sure
to
wrap
the
end
of
the
cord
with
tape
after
disconnecting
the
lamp
code.

~8~1
Standing
work
machine
★
The
code
connection
and
the
treadle
lever
are
fixed
for
the
standing
work
machine.
In
modifying
to
the
standing
work
machine,
do
not
fail
to
turn
off
the
power
switch
before
connecting/disconnecting
the
plug.
1.
Code
Connection
★
Do
not
fail
to
turn
off
the
power
switch
before
connecting/disconnecting
the
plug.
★
Remove
the
motor
cover.
Disconnect
the
plug
A
and
connect
the
plug
B
instead.
★
For
the
standing
work
machine
modified,
the
power
source
for
the
timer,
relay,
sensor,
counter
and
so
on
is
available
from
the
4P
plug
in
the
control
box.
*The
power
up
to
DC
12
V*
100
mA
is
available
from
the
4P
plug
(red)
where
the
treadle
plug
is
connected.
(Take
great
care
not
to
apply
the
current
of
100
mA
or
more
to
affect
the
function
of
the
control
box,
or
the
machine
malfunctions.)
2.
Treadle
Lever
Position
★
While
keeping
the
treadle
lever
O
lowered,
turn
the
screw
©
and
set
into
the
recessed.
Secure
the
screw
©
with
the
nut
©
,
or
it
happens
to
be
loose.

~9~|
Application
to
production
control
system
1.
Models
DB2-B737
•
B747
•
B791
•
B793
•
B795
•
B798
★
The
control
circuit
board
is
prodded
with
the
tread
trimmi
This
terminal
is
available
for
connecting
to
the
external
equ
Collector
Control
circuit
board
Emitter
2
Terminal
not
used
2.
Model
B738
★
Output
signals
are
sent
from
the
open
collector
of
the
photo
transistor
of
the
photo
coupler.
(Use
the
CN11
plug.)
Max.
operating
current:
DC20
mA
or
less
Max.
operating
voltage:
DC20
V
or
less
★
With
special
connectors
(cycle
output),
connect
the
machine
to
the
external
equipments.
★
Output
signals
are
sent
from
the
open
collector
of
the
photo
transistor
of
the
photo
coupler.
Max.
operating
current:
DC20
mA
or
less
Max.
operating
voltage:
DC20
V
or
less

OPERATION
INSTRUCTION
[T]
Installation
of
operation
box
Models
DB2-B737
•
B747
B748
•
B791
Models
DB2-B793
•
B795
•
B798
Installing
on
the
Machine
Head
1.
Remove
the
two
screws
O
from
the
back
of
the
arm
bed.
2.
Four
screws
0
are
provided.
Use
two
large
screws
for
the
model
B737.
And
use
the
other
two
small
screws
for
the
models
B747
•
B748
•
B791
•
B793
■
B795
•
B798.
3.
Set
the
operation
box
mounting
plate
@
on
the
back
of
the
arm
bed
with
the
screws
0
[
2
]
Motor
control
and
control
box
use
(Models
Installing
on
the
Table
1.
Set
the
operation
box
mounting
plate
O
on
the
back
of
the
power
switch
mounting
plate
©
with
the
screws
©.
2.
Fix
the
mounting
plate
O
on
the
back
of
the
table
with
the
wood
screw
©
*
Secure
the
ground
wire
0
to
the
motor
with
the
screw
0
.
I-B737
•
B747
•
B748
B791
•
B795
•
B798)
★
Push
the
“ON”
button
of
the
power
switch
0
.
Then
the
power
lamp
0
goes
on.
★
When
the
speed
adjustment
knob
©
is
turned
clockwise,
the
machine
speed
increases.
And
when
counterclockwise,
it
decreases.
The
machine
speed
can
be
adjusted
from
215
spm
up
to
the
maximum.
★
When
the
backtack
speed
adjusting
knob
O
is
turned
clockwise,
the
start
backtack
speed
increases.
And
when
counter¬
clockwise,
it
decreases.
The
start
and
continuous
backtack
speeds
can
be
changed
from
215
spm
to
3,000
spm.
The
end
backtack
speed
allows
no
change
at
1,800
spm.
★
When
the
slow
start
switch
0
is
turned
on,
the
machine
starts
running
at
low
speed
for
the
first
two
stitches
(after
thread
trimming
and
stop
at
the
needle
up
position).
Then
the
machine
keeps
on
running
in
proportion
as
you
step
on
the
treadle.
★
When
the
correction
switch
©
is
turned
on
and
the
actuator
0
is
pushed
with
the
machine
stopped,
the
machine
starts
correction
sewing
operation.
When
the
actuator
is
pushed
during
operation,
the
sewing
operation
is
reversed.
★
When
the
needle
position
set
switch
0
is
set
to
the
needle
down
position
and
the
machine
is
stopped
during
the
sewing
operation,
the
needle
stops
at
the
needle
down
position.
When
it
is
set
to
the
needle
up
position
and
the
machine
is
stopped
during
the
sewing
operation,
the
needle
stops
at
the
needle
up
position.

3
Operation
box
(Models
DB2-B737
•
B747
•
B791
•
B793
•
B795
•
B798)
★
The
switch
settings
and
the
number
of
stitches
cannot
be
changed
during
the
machine
operation.
Check
the
preset
switch
settings
and
the
preset
number
of
stitches
before
working
with
the
machine.
★
When
the
backtack
switch
is
pressed,
the
indicator
turns
on.
It
goes
off
by
pressing
the
switch
again.
★
When
the
upper
counter
switch
is
pressed,
the
number
of
stitches
decreases.
And
when
the
lower
switch
is
pressed,
the
number
increases.
★
The
machine
runs
according
to
the
programmed
pattern
after
setting
as
follows.
Box
E-2
□
For
Backtacking
1.
Press
the
switch
O
for
start
backtacking,
forward
A
and
reverse
B.
2.
Press
the
switch
0
for
end
backtacking,
reverse
B
and
forward
A.
3.
Set
the
start
and
end
backtack
stitch
number
A
(0
to
9)
with
the
counter
©.
4.
Set
the
start
and
end
backtack
stitch
number
B
(0
to
9)
with
the
counter
©.
*Set
the
stitch
number
A
to
“0”
for
V
stitch.
*When
the
treadle
is
stepped
on,
the
machine
backtacks.
□
For
Half
Stitch
Switch
★
When
the
machine
is
stopped
with
the
half
stitch
switch
pressed,
the
needle
at
the
needle
down
stop
position
moves
to
the
needle
up
stop
position,
while
the
needle
at
the
needle
up
stop
position
moves
to
the
down
stop
position.
The
needle
moves
up
or
down
every
time
the
switch
©
is
pressed.
*
Thread
trimming
cannot
be
executed
after
this
switch
©
is
used.
First
of
all,
step
on
the
treadle
for
thread
trimming.
Box
E-4
□
For
Backtacking
1.
Press
the
switch
O
for
start
backtacking
A
and
B.
2.
Press
the
switch
©
for
end
backtacking
C
and
D.
3.
Set
the
start
backtack
stitch
number
A
(0
to
9)
with
the
counter
©.
4.
Set
the
start
backtack
stitch
number
B
(0
to
9)
with
the
counter
©.
5.
Set
the
end
backtack
stitch
number
C
(0
to
9)
with
the
counter
©.
6.
Set
the
end
backtack
stitch
number
D
(0
to
9)
with
the
counter
©.
□
For
Continuous
Backtacking
★
Press
the
continuous
backtack
switch
©,
and
set
the
stitch
number
with
the
counter
switches
A,
B,
C
and
D.
The
machine
runs
in
a
cycle
of
A,
B,
C,
and
D,
then
stops
running.
□
For
Fixed
Stitch
Sewing
1.
Press
the
switch
©
for
the
fixed
stitch
sewing
N.
2.
The
number
of
stitches
N
can
be
set
from
1
through
99
with
the
end
backtack
stitch
counters
C
©
and
D
©.
3.
The
number
of
stitches
for
the
end
backtacking
during
the
fixed
stitch
sewing
can
be
set
using
the
counter
A
(D)
and
B
(C).
□
For
Fixed
Stitch
Sewing
and
Thread
Trimming
With
the
switch
©
pressed,
the
fixed
stitch
sewing
is
completed
up
to
the
set
stitch
number
(1
through
99)
and
the
thread
trimming
is
done
just
by
stepping
on
the
treadle.
*The
half
stitch
switch
of
the
box
E-4
is
same
as
E-2.

a
Guide
to
E-2
and
E-4
switches
★
Items
indicated
with
a
circle
in
the
chart
below
require
a
stitch
number
setting.
Items
with
no
symbol
require
no
setting.
★
Symbols
used
in
figures
below
o
.
.
.
.
The
machine
works
by
one
correction
stitch
if
the
actuator
is
pressed
when
the
machine
is
stopped
and
the
correction
switch
is
ON.
If
the
actuator
is
pressed
while
the
machine
is
operating,
the
machine
enters
the
reverse
sewing
mode.
When
the
machine
is
at
the
sewing
start
position
after
thread
trimming,
the
machine
does
not
move
even
if
the
actuator
is
pressed.
•
,
.
.
.
Thread
trimming
(Thread
trimming
is
performed
when
the
treadle
is
pressed
to
the
reverse
position.)
.Indicates
thread
trimming
following
fixed
stitch
sewing
or
end
backtack.
(Thread
trimming
is
performed
without
pressing
the
treadle
to
the
reverse
position.)
E-2
Application
Start
backtack
switch
End
backtack
switch
Stitch
number
setting
Reference
figure
No.
A
B
Normal
lock
stitch
OFF
OFF
1
Start
backtack
ON
OFF
o
o
2
End
backtack
OFF
ON
o
o
3
Start/end
backtack
ON
ON
o
o
4
No.1
Normal
lock
stitch
No.2
Start
backtack
No.3
End
backtack
No.4
Start/end
backtack
■
V
A
,
A
_^
'
V
1
/
V
1
/
1/
/
1
\
i
1
A
<
A
/
•
'
i
/
i
/
i
4
<
»
V
4
_
*
4
Thread
trimming
is
performed
when
the
treadle
is
set
Thread
trimming
is
performed
after
end
backtack
to
reverse
position.
when
the
treadle
is
set
to
the
reverse
position.
E-4
Application
Start
backtack
switch
End
backtack
switch
Fixed
stitch
switch
Thread
trimming
switch
Continuous
backtack
switch
Stitch
number
setting
Reference
figure
No.
Note
A
|
B
c
D
(D)
•
(C)
N
Fixed
stitch
sewing
OFF
Normal
lock
stitch
OFF
OFF
OFF
OFF
OFF
1
Start
backtack
ON
OFF
OFF
OFF
OFF
o
o
2
End
backtack
OFF
ON
OFF
OFF
OFF
o
o
3
Start/end
backtack
ON
ON
OFF
OFF
OFF
o
o
o
o
4
Fixed
stitch
sewing
ON
(thread
trimming
activated
by
setting
treadle
to
reverse)
Fixed
stitch
sewing
OFF
OFF
ON
OFF
OFF
o
o
5
Start
backtack
ON
OFF
ON
OFF
OFF
o
o
o
o
6
End
backtack
OFF
ON
ON
OFF
OFF
o
o
o
o
7
End
back¬
tack
B/A
Start/end
backtack
ON
ON
ON
OFF
OFF
o
o
o
o
8
End
back¬
tack
B/A
Fixed
stitch
sewing
with
thread
trim¬
ming
ON
(thread
trimming
performed
with
treadle
depressed
forward)
Fixed
stitch
sewing
OFF
OFF
ON
ON
OFF
o
o
9
Start
backtack
ON
OFF
ON
ON
OFF
o
o
o
o
10
End
backtack
OFF
ON
ON
ON
OFF
o
o
o
o
11
End
back¬
tack
B/A
Start/end
backtack
ON
ON
ON
ON
OFF
o
o
o
o
12
End
back¬
tack
B/A
Continuous
backtack
(Automatic
thread
trimming
after
programmed
cycle
completed)
OFF
OFF
OFF
OFF
ON
o
o
o
o
13
Normal
lock
stitch
sewing
is
performed
after
the
fixed
stitch
sewing
sequence
is
completed
until
thread
trimming
is
completed.
(No.
5
through
8
in
the
above
table.)

No.1
Normal
lock
stitch
No.2
Start
backtack
No.3
End
backtack
No.4
Start/end
backtack
Actuator
correction
.
B
/
A|
/
1
/
A
C/
I
/
ID
'
i
A
C/
1
/
ID
Thread
trimming
activated
by
reversing
the
treadle.
No.5
Fixed
stitch
sewing
only
No.6
Start
backtack
and
fixed
stitch
sewing
Thread
trimming
activated
after
end
backtack
by
reversing
the
treadle.
No.7
Fixed
stitch
sewing
and
end
backtack
No.8
Start/end
backtack
and
fixed
stitch
sewing
Fixed
stitch
Actuator
correction
i
B/
,
K
'
'
i
V
N
Fixed
stitch
I
Fixed
stitch
I
/I
a!
i
S'
n!
Fixed
stitch
A
V
!a
Thread
trimming
activated
by
reversing
the
treadle.
No.9
Fixed
stitch
and
thread
trimming
No.
10
Start
backtack,
fixed
stitch
and
thread
trimmin
Thread
trimming
activated
after
end
backtack
by
reversing
the
treadle.
I
A
.
i
B/
|
A
|
/
I
1/
I
V
I
!
Ba'
1
,
1
/
N
1
No.13
Continuous
backtack
Sewing
completed
through
thread
trimming
by
holding
the
treadle
depressed.
\
/A
'
/
\
B
l
\
°l
A\
1
C
'
/
\
/
\
/
V
v
Sewing
completed
through
thread
trimming
by
holding
the
treadle
depressed.

((BLOCK
DIAGRAM
OF
CONTROL
CIRCUIT))
]T]
Single-phase/IOOV
(Models
DB2-B737
•
B747
■
B748
•
B791
•
B793
•
B795
•
B798)
1.
The
connector
is
shown
from
the
pin
side.
2.
The
section
indicated
by
the
broken
line
shows
the
inside
of
the
control
box.
j>&
oz
<o
<Q
3
IKIi
•PQ-Sbo.
C
^“""
er
Synchronizer
#12-n
(external)
This manual suits for next models
1
Table of contents
Other Brother Engine manuals
Popular Engine manuals by other brands
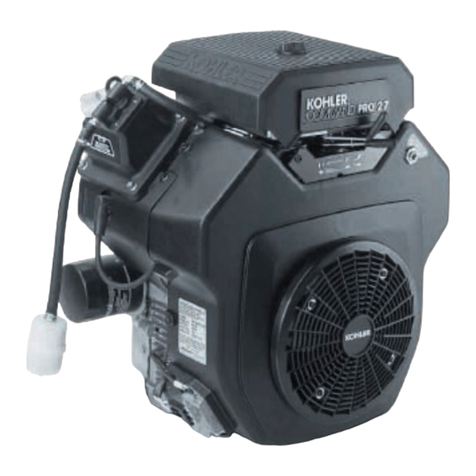
Kohler
Kohler Command PRO CH18 owner's manual
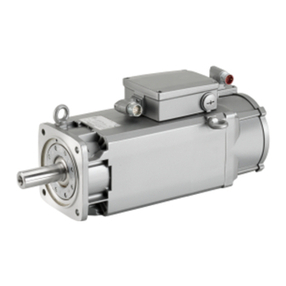
Siemens
Siemens SIMOTICS M-1PH8 Operating instructions & installation instructions
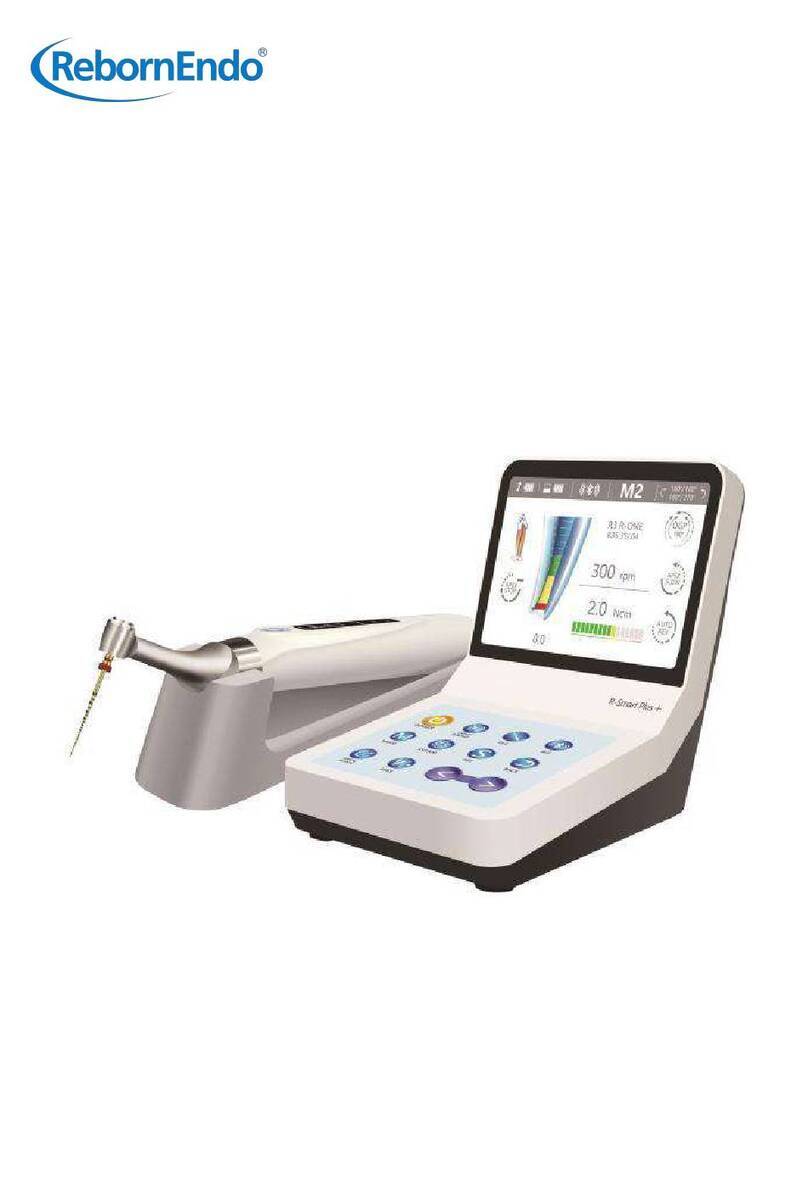
Reborn Endo
Reborn Endo R-Smart Plus+ instruction manual
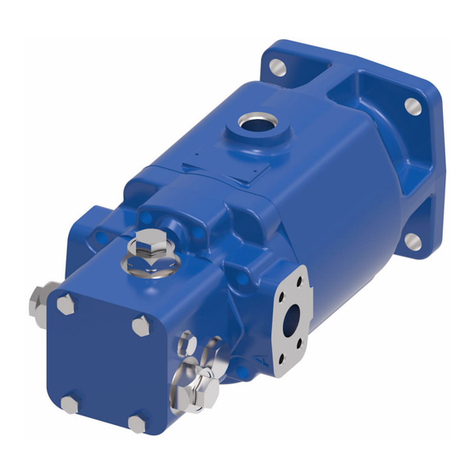
Eaton
Eaton 1 Series Parts and Service
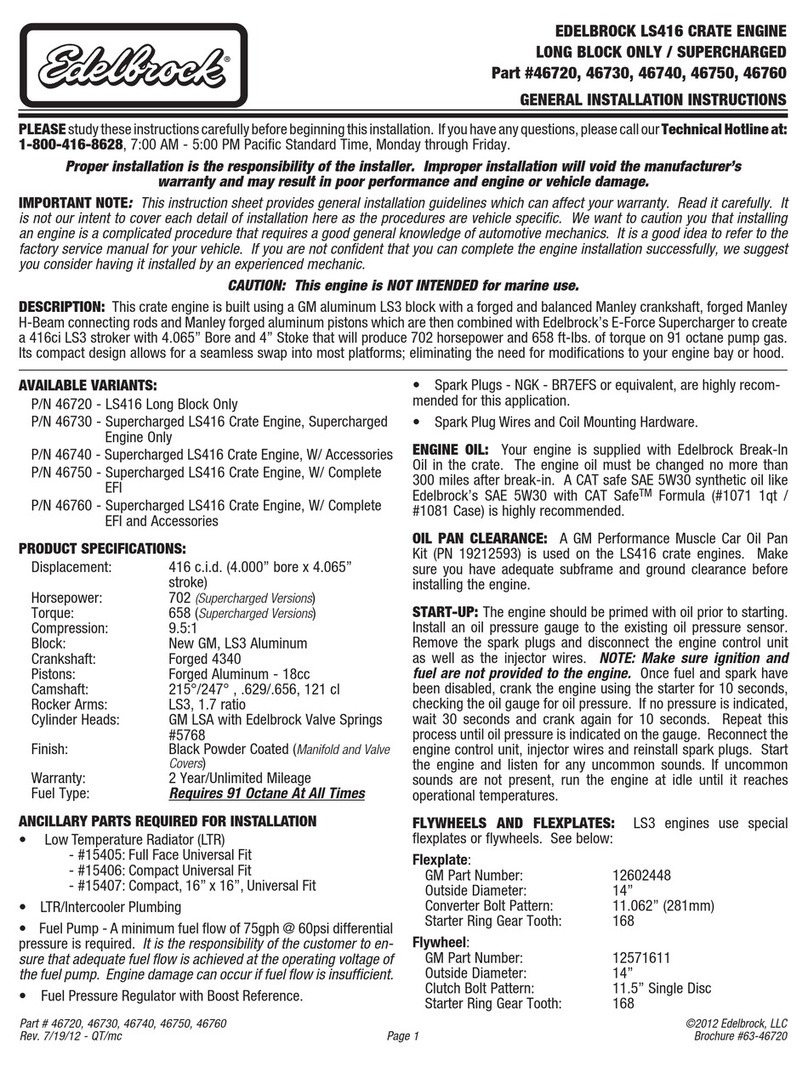
Edelbrock
Edelbrock LS416 installation instructions
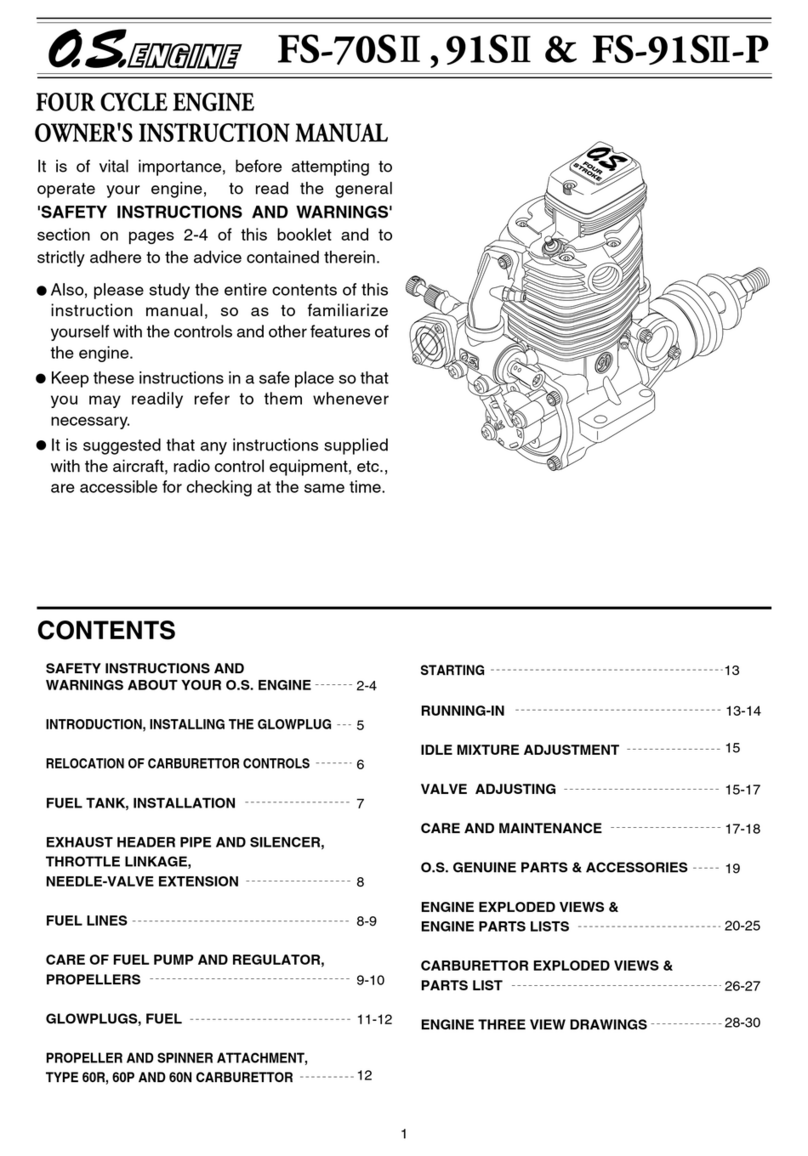
O.S. engine
O.S. engine fs-70II Owner's instruction manual