Bryant 582K 08 Series Installation and user guide

Manufacturer reserves the right to discontinue, or change at any time, specifications or designs without notice and without incurring obligations.
Catalog No. 04-53582013-01 Printed in U.S.A. Form No. SM582K-08-16-01 Pg 1 11-23 Replaces: New
Service and Maintenance Instructions
CONTENTS
Page
SAFETY CONSIDERATIONS . . . . . . . . . . . . . . . . . . . . . . 2
UNIT ARRANGEMENT AND ACCESS . . . . . . . . . . . . . . 2
General . . . . . . . . . . . . . . . . . . . . . . . . . . . . . . . . . . . . . . . . . . 2
Routine Maintenance . . . . . . . . . . . . . . . . . . . . . . . . . . . . . . 3
Filters . . . . . . . . . . . . . . . . . . . . . . . . . . . . . . . . . . . . . . . . . . . 3
SUPPLY FAN (BLOWER) SECTION . . . . . . . . . . . . . . . . 4
Supply Fan (Direct-Drive) . . . . . . . . . . . . . . . . . . . . . . . . . . 4
2-Speed Indoor Fan Motor System . . . . . . . . . . . . . . . . . . 12
COOLING . . . . . . . . . . . . . . . . . . . . . . . . . . . . . . . . . . . . . . 12
Condenser Coil . . . . . . . . . . . . . . . . . . . . . . . . . . . . . . . . . . 12
Condenser Coil Maintenance and Cleaning
Recommendation . . . . . . . . . . . . . . . . . . . . . . . . . . . . . . . . . 12
Evaporator Coil . . . . . . . . . . . . . . . . . . . . . . . . . . . . . . . . . 14
Evaporator Coil Metering Devices . . . . . . . . . . . . . . . . . . 14
THERMOSTATIC EXPANSION VALVE (TXV) . . . . . 14
TXV Operation . . . . . . . . . . . . . . . . . . . . . . . . . . . . . . . . . . 14
Replacing TXV . . . . . . . . . . . . . . . . . . . . . . . . . . . . . . . . . . 14
Refrigerant System Pressure Access Ports . . . . . . . . . . . . 14
PURON (R-410A) REFRIGERANT . . . . . . . . . . . . . . . . . 15
Refrigerant Charge . . . . . . . . . . . . . . . . . . . . . . . . . . . . . . . 15
COMPRESSOR . . . . . . . . . . . . . . . . . . . . . . . . . . . . . . . . . 26
Lubrication . . . . . . . . . . . . . . . . . . . . . . . . . . . . . . . . . . . . . 26
Replacing Compressor . . . . . . . . . . . . . . . . . . . . . . . . . . . . 26
Compressor Rotation . . . . . . . . . . . . . . . . . . . . . . . . . . . . . 26
Filter Drier . . . . . . . . . . . . . . . . . . . . . . . . . . . . . . . . . . . . . 26
Condenser-Fan Adjustment . . . . . . . . . . . . . . . . . . . . . . . . 26
Troubleshooting Cooling System . . . . . . . . . . . . . . . . . . . . 27
CONVENIENCE OUTLETS . . . . . . . . . . . . . . . . . . . . . . 28
Convenience Outlets . . . . . . . . . . . . . . . . . . . . . . . . . . . . . . 28
Installing Weatherproof Cover . . . . . . . . . . . . . . . . . . . . . 28
Non-Powered Type . . . . . . . . . . . . . . . . . . . . . . . . . . . . . . . 28
Unit-Powered Type . . . . . . . . . . . . . . . . . . . . . . . . . . . . . . . 28
Duty Cycle . . . . . . . . . . . . . . . . . . . . . . . . . . . . . . . . . . . . . . 29
Maintenance . . . . . . . . . . . . . . . . . . . . . . . . . . . . . . . . . . . . 29
Fuse on Powered Type . . . . . . . . . . . . . . . . . . . . . . . . . . . . 29
SMOKE DETECTORS . . . . . . . . . . . . . . . . . . . . . . . . . . . 29
System . . . . . . . . . . . . . . . . . . . . . . . . . . . . . . . . . . . . . . . . . 29
Controller . . . . . . . . . . . . . . . . . . . . . . . . . . . . . . . . . . . . . . 29
Smoke Detector Sensor . . . . . . . . . . . . . . . . . . . . . . . . . . . . 29
Smoke Detector Locations . . . . . . . . . . . . . . . . . . . . . . . . . 30
Completing Installation of Return Air Smoke Detector . . . 31
FIOP Smoke Detector Wiring and Response . . . . . . . . . . 32
SENSOR AND CONTROLLER TESTS . . . . . . . . . . . . . 32
Sensor Alarm Test . . . . . . . . . . . . . . . . . . . . . . . . . . . . . . . 32
Controller Alarm Test . . . . . . . . . . . . . . . . . . . . . . . . . . . . 32
Dirty Controller Test . . . . . . . . . . . . . . . . . . . . . . . . . . . . . 32
Dirty Sensor Test . . . . . . . . . . . . . . . . . . . . . . . . . . . . . . . . 33
Changing the Dirt Sensor Test . . . . . . . . . . . . . . . . . . . . . 33
Remote Station Test . . . . . . . . . . . . . . . . . . . . . . . . . . . . . . 33
SD-TRK4 Remote Alarm Test Procedure . . . . . . . . . . . . 33
Remote Test/Reset Station Dirty Sensor Test . . . . . . . . . 33
Dirty Sensor Test Using an SD-TRK4 . . . . . . . . . . . . . . . 34
Detector Cleaning . . . . . . . . . . . . . . . . . . . . . . . . . . . . . . . . 34
Indicators . . . . . . . . . . . . . . . . . . . . . . . . . . . . . . . . . . . . . . 34
Troubleshooting . . . . . . . . . . . . . . . . . . . . . . . . . . . . . . . . . 35
PROTECTIVE DEVICES . . . . . . . . . . . . . . . . . . . . . . . . . 35
Compressor Protection . . . . . . . . . . . . . . . . . . . . . . . . . . . 35
Relief Device . . . . . . . . . . . . . . . . . . . . . . . . . . . . . . . . . . . . 36
Control Circuit, 24-V . . . . . . . . . . . . . . . . . . . . . . . . . . . . . 36
GAS HEATING SYSTEM . . . . . . . . . . . . . . . . . . . . . . . . 37
General . . . . . . . . . . . . . . . . . . . . . . . . . . . . . . . . . . . . . . . . 37
Fuel Types and Pressures . . . . . . . . . . . . . . . . . . . . . . . . . 37
Flue Gas Passageways . . . . . . . . . . . . . . . . . . . . . . . . . . . . 38
Combustion-Air Blower . . . . . . . . . . . . . . . . . . . . . . . . . . . 38
Burners and Igniters . . . . . . . . . . . . . . . . . . . . . . . . . . . . . 39
Burner Ignition . . . . . . . . . . . . . . . . . . . . . . . . . . . . . . . . . . 42
Orifice Replacement . . . . . . . . . . . . . . . . . . . . . . . . . . . . . . 42
Troubleshooting Heating System . . . . . . . . . . . . . . . . . . . 45
ECONOMIZER SYSTEMS . . . . . . . . . . . . . . . . . . . . . . . 47
EconoMi$er IV (Field-Installed Accessory) . . . . . . . . . . . 48
EconoMi$er X (Factory-Installed Option) . . . . . . . . . . . . 56
PRE-START-UP/START-UP . . . . . . . . . . . . . . . . . . . . . . 66
START-UP, GENERAL . . . . . . . . . . . . . . . . . . . . . . . . . . 67
Unit Preparation . . . . . . . . . . . . . . . . . . . . . . . . . . . . . . . . . 67
Additional Installation/Inspection . . . . . . . . . . . . . . . . . . 67
Gas Piping . . . . . . . . . . . . . . . . . . . . . . . . . . . . . . . . . . . . . . 67
Return-Air Filters . . . . . . . . . . . . . . . . . . . . . . . . . . . . . . . 68
Outdoor-Air Inlet Screens . . . . . . . . . . . . . . . . . . . . . . . . . 68
Compressor Mounting . . . . . . . . . . . . . . . . . . . . . . . . . . . . 68
Internal Wiring . . . . . . . . . . . . . . . . . . . . . . . . . . . . . . . . . . 68
Refrigerant Service Ports . . . . . . . . . . . . . . . . . . . . . . . . . 68
Compressor Rotation . . . . . . . . . . . . . . . . . . . . . . . . . . . . . 68
Cooling . . . . . . . . . . . . . . . . . . . . . . . . . . . . . . . . . . . . . . . . 68
Main Burner . . . . . . . . . . . . . . . . . . . . . . . . . . . . . . . . . . . . 68
Heating . . . . . . . . . . . . . . . . . . . . . . . . . . . . . . . . . . . . . . . . 68
Ventilation (Continuous Fan) . . . . . . . . . . . . . . . . . . . . . . 68
FASTENER TORQUE VALUES . . . . . . . . . . . . . . . . . . . 69
APPENDIX A — MODEL NUMBER
NOMENCLATURE . . . . . . . . . . . . . . . . . . . . . . . . . . . . 70
APPENDIX B — PHYSICAL DATA . . . . . . . . . . . . . . . . 71
APPENDIX C — GAS HEAT DATA . . . . . . . . . . . . . . . . 74
APPENDIX D — FAN PERFORMANCE . . . . . . . . . . . . 75
APPENDIX E — WIRING DIAGRAMS . . . . . . . . . . . . . 96
APPENDIX F — LOW AMBIENT CONTROL
SENSOR LOCATION . . . . . . . . . . . . . . . . . . . . . . . . . 110
START-UP CHECKLIST . . . . . . . . . . . . . . . . . . . . . . . CL-1
582K*08-16
Single Package Rooftop Gas Heat/Electric Cooling Unit
with Puron® (R-410A) Refrigerant
7.5 to 15 Nominal Tons

2
SAFETY CONSIDERATIONS
Installation and servicing of air-conditioning equipment can be
hazardous due to system pressure and electrical components. Only
trained and qualified service personnel should install, repair, or
service air-conditioning equipment. Untrained personnel can per-
form the basic maintenance functions of replacing filters. Trained
service personnel should perform all other operations.
When working on air-conditioning equipment, observe precau-
tions in the literature, tags and labels attached to the unit, and other
safety precautions that may apply. Follow all safety codes. Wear
safety glasses and work gloves. Use quenching cloth for unbrazing
operations. Have fire extinguishers available for all brazing
operations.
Follow all safety codes. Wear safety glasses and work gloves. Use
quenching cloth for brazing operations. Have fire extinguisher
available. Read these instructions thoroughly and follow all warn-
ings or cautions attached to the unit. Consult local building codes
and National Electrical Code (NEC) for special requirements.
Recognize safety information. This is the safety ALERT symbol
. When you see this symbol on the unit and in instructions or
manuals, be aware of the potential for physical injury hazards.
Understand the signal words DANGER, WARNING, and
CAUTION. These words are used with the safety ALERT sym-
bol. DANGER indicates a hazardous situation which, if not avoid-
ed, will result in death or severe personal injury. WARNING in-
dicates a hazardous situation which, if not avoided, could result in
death or personal injury. CAUTION indicates a hazardous situa-
tion which, if not avoided, could result in minor to moderate injury
or product and property damage. IMPORTANT is used to ad-
dress practices not related to physical injury. NOTE is used to
highlight suggestions which will result in enhanced installation,
reliability, or operation.
UNIT ARRANGEMENT AND ACCESS
General
Figures 1-4 show general unit arrangement and access
locations.
Fig. 1 — Typical Access Panel Locations
(size 8-14 units)
WARNING
UNIT OPERATION AND SAFETY HAZARD
Failure to follow this warning could cause personal injury,
death and/or equipment damage.
R-410A refrigerant systems operate at higher pressures
than standard R-22 systems. Do not use R-22 service
equipment or components on R-410A refrigerant
equipment.
WARNING
FIRE, EXPLOSION HAZARD
Failure to follow this warning could result in death, serious
personal injury and/or property damage.
Disconnect gas piping from unit when pressure testing at
pressure greater than 0.5 psig (3450 Pa). Pressures greater
than 0.5 psig will cause gas valve damage resulting in
hazardous condition. If gas valve is subjected to pressure
greater than 0.5 psig, it must be replaced before use. When
pressure testing field-supplied gas piping at pressures of
0.5 psig or less, a unit connected to such piping must be
isolated by closing the manual gas valve(s).
WARNING
FIRE, EXPLOSION HAZARD
Failure to follow this warning could result in death, serious
personal injury and/or property damage.
Never use non-certified refrigerants in this product. Non-
certified refrigerants could contain contaminates that could
lead to unsafe operating conditions. Use ONLY refrigerants
that conform to AHRI Standard 700.
CAUTION
UNIT DAMAGE HAZARD
Failure to follow this caution may result in reduced unit
performance or unit shutdown.
High velocity water from a pressure washer, garden hose,
or compressed air should never be used to clean a coil. The
force of the water or air jet will bend the fin edges and
increase airside pressure drop.
WARNING
ELECTRICAL OPERATION HAZARD
Failure to follow this warning could result in personal
injury or death.
Units with convenience outlet circuits can use multiple
disconnects. Check convenience outlet for power status
before opening unit for service. Locate the disconnect
switch and lock it in the open position it.
LOCKOUT/TAGOUT this switch to notify others.
IMPORTANT: Lockout/tag-out is a term used when electri-
cal power switches are physically locked preventing power
to the unit. A placard is placed on the power switch alerting
service personnel that the power is disconnected.
Filter Access Panel
Indoor Coil Access Panel

3
Fig. 2 — Typical Access Panel Locations
(size 16 units)
Fig. 3 — Blower Access Panel Location
(size 8-14 units)
Fig. 4 — Blower Access Panel Location
(size 16 units)
Routine Maintenance
These items should be part of a routine maintenance program, to
be checked every month or two, until a specific schedule for each
can be identified for this installation:
QUARTERLY INSPECTION (AND 30 DAYS AFTER
INITIAL START)
• Return air filter replacement
• Outdoor hood inlet filters cleaned
• Condenser coil cleanliness checked
• Condensate drain checked
SEASONAL MAINTENANCE
These items should be checked at the beginning of each season (or
more often if local conditions and usage patterns dictate):
Air Conditioning
• Ensure outdoor fan motor mounting bolts are tight
• Ensure compressor mounting bolts are tight
• Inspect outdoor fan blade positioning
• Ensure control box is clean
• Check control box wiring condition
• Ensure wire terminals are tight
• Check refrigerant charge level
• Ensure indoor coils are clean
• Check supply blower motor amperage
Heating
• Heat exchanger flue passageways cleanliness
• Gas burner condition
• Gas manifold pressure
• Heating temperature rise
Economizer or Outside Air Damper
• Check inlet filters condition
• Check damper travel (economizer)
• Check gear and dampers for debris and dirt
Air Filters and Screens
Each unit is equipped with return air filters. If the unit has an econ-
omizer, it will also have an outside air screen. If a manual outside
air damper is added, an inlet air screen will also be present.
Each of these filters and screens will need to be periodically re-
placed or cleaned.
Filters
RETURN AIR FILTERS
Return air filters are disposable fiberglass media type. Access
to the filters is through the small lift-out panel located on the
rear side of the unit, above the evaporator/return air access
panel. (See Fig. 5.)
Filter Access Panel
Indoor Coil Access Panel
Control Box
Access Panel
Indoor
Access
Panel
Flue
Hood
Control Box
Access Panel
Blower
Access Panels
CAUTION
EQUIPMENT DAMAGE HAZARD
Failure to follow this CAUTION can result in premature
wear and damage to equipment.
DO NOT OPERATE THE UNIT WITHOUT THE
RETURN AIR FILTERS IN PLACE.
Dirt and debris can collect on heat exchangers and coils
possibly resulting in a small fire. Dirt buildup on
components can cause excessive current used resulting in
motor failure.

4
To remove the filters:
1. Grasp the bottom flange of the upper panel.
2. Lift up and swing the bottom out until the panel disen-
gages and pulls out.
3. Reach inside and extract the filters from the filter rack.
4. Replace these filters as required with similar replacement
filters of same size.
To re-install the access panel:
1. Slide the top of the panel up under the unit top panel.
2. Slide the bottom into the side channels.
3. Push the bottom flange down until it contacts the top of
the lower panel (or economizer top).
OUTSIDE AIR HOOD
Outside air hood inlet screens are permanent aluminum-mesh
type filters. Check these for cleanliness. Remove the screens
when cleaning is required. Clean by washing with hot low-pres-
sure water and soft detergent and replace all screens before re-
starting the unit. Observe the flow direction arrows on the side of
each filter frame.
ECONOMIZER INLET AIR SCREEN
This air screen is retained by filter clips under the top edge of the
hood. (See Fig. 5.)
Fig. 5 — Filter Installation
To remove the filter, open the filter clips. Re-install the filter by
placing the frame in its track, then closing the filter clips.
MANUAL OUTSIDE AIR HOOD SCREEN
This inlet screen is secured by a retainer angle across the top edge
of the hood. (See Fig. 6.)
Fig. 6 — Screens Installed on Outdoor-Air Hood
To remove the screen, loosen the screws in the top retainer and
slip the retainer up until the filter can be removed. Re-install by
placing the frame in its track, rotating the retainer back down,
and tightening all screws.
SUPPLY FAN (BLOWER) SECTION
Supply Fan (Direct-Drive)
All 582K units have the Axion™ Fan Technology direct drive
vane axial fan system. The fan is driven by an ECM motor with
speed that is user set through the Unit Control Board (UCB).
Speeds are fully configurable from 40% to 100% of motor’s max-
imum speed. (See Fig. 7 and 8.)
Fig. 7 — Direct-Drive Supply Fan Assembly
Fig. 8 — ECM Motor Plug Connectors
Divider
Outside
Air
Hood
Filter
Filter Clip
Cleanable
Aluminum
Filter
Barometric
Relief
Screws
WARNING
ELECTRICAL SHOCK HAZARD
Failure to follow this warning could result in personal
injury or death.
Before performing service or maintenance operations on
unit, LOCKOUT/TAG-OUT the main power switch to unit.
Electrical shock and rotating equipment could cause severe
injury.
Motor
Plug
Fan
Motor
ECM Motor
123
456
789
10 11 12
CTL Signal CommonSerial (R/T)
Safety Relay
Power L1
Power L2
Power L3
10 vdc Source
0-10 vdc signal
Earth Ground
Safety Relay
PWM signal
WHITE
BLACK
YELLOW
BLUE
YEL/GRN
RED
GRAY
RED
PINK
ORANGE
VIOLET

5
EVALUATING MOTOR SPEED
The direct drive ECM blower motor uses a constant speed design.
Motor speed is controlled by a 0-10 vdc signal, where 10 vdc is
equal to motor’s maximum rpm.
SELECTING FAN SPEED
All units come factory set for 9.0 vdc or approximately 90% of the
motor’s maximum speed. Fan speed should be set per job specifi-
cation cfm (cubic feet per minute) and ESP (external static pres-
sure) required and per Fan speed set up label included on the unit’s
high voltage cover. In some cases, the Fan Speed Set Up label may
already include the field setting if unit was previously installed.
Check the box on the lower half of the label to see if the field volt-
age setting was filled in and if so, set fan speed to that voltage.
Otherwise see detailed instructions below.
NOTE: Fan Speed Set-Up is for full load airflow. All 582K*08-16
units have multiple speeds of fan control. Low cool and ventila-
tion will operate at lower fan rpms. This offset is factory set and
controlled by the UCB. If fan speed verification is being done with
a strobe, fan speed should be verified in all unit operation modes.
Units with Electro-mechanical controls
The Fan Speed set up controls are located on the lower section of
the Unit Control Board (UCB). See Fig. 9 for location.
1. Check the job specifications for the cfm (cubic feet per
minute) and ESP (external static pressure) required.
2. Using the chart on the Fan Speed Set Up labels (see Fig. 10),
calculate the vdc from the cfm and ESP for the base.
3. If installing any accessories listed at the bottom of the Set
Up Label, add accessory vdc to base unit vdc in upper por-
tion of label.
NOTE: The Fan Speed Set Up labels are located on the High
Voltage cover in the Control Box.
4. Connect a multimeter to the vdc terminals on the UCB.
5. Set the Range Switch to either A, B, or C per the Switch
Range table.
6. Using a straight blade screwdriver turn the vdc control dial
to fine tune the vdc reading.
7. Record the reading in the Field Setting field.
NOTE: For units equipped with the Perfect Humidity™ option,
when replacing the UCB cut JMP 1,2 and 3 in the REHEAT/HP
section of the replacement UCB.
Fig. 9 — UCB Fan Speed Controls - 3-Phase Units
Fan Speed Set Up Controls

6
NOTE(S):
Values in the Field Accessories section are VDC adders.
Fig. 10 — Example of Fan Speed Set Up Labels for Electro-Mechanical Controls
Factory Setting:
9.0 VDC
Field Setting:
V
Switch Range:
A
B
C
B
AC
Field Accessories:
ESP in. wg
VDC Calculator
CFM
0.2
5.6
6.0
6.4
6.8
7.2
7.6
8.0
8.5
8.9
3000
3250
3500
3750
4000
4250
4500
4750
5000
0.4
0.4
6.1
6.4
6.8
7.2
7.6
8.0
8.4
8.8
9.2
0.4
0.6
6.5
6.8
7.2
7.5
7.9
8.3
8.7
9.1
0.4
0.8
6.9
7.2
7.6
7.9
8.2
8.6
9.0
0.4
1.0
7.3
7.6
7.9
8.2
8.6
0.4
1.2
7.6
7.9
8.2
8.6
0.4
1.4
8.0
8.3
8.6
0.4
1.6 1.8 2.0
8.3
0.4 0.4 0.4Economizer
UNIT MODEL NUMBER
4.1 - 7.5
6.9 - 8.7
7.7 - 10.0
8.6
8.9
8.9
9.28.9
9.2
9.6
9.5
9.2
9.5
8.6
8.9
9.2
9.5
8.9
9.2
9.5
9.7
9.8
9.8
9.8
8.9
9.3
9.6 9.9
9.3
9.79.4 10.0
Record field setting here
*
* Overlap in A, B, C switch range
designed for maximum field
adjustment potential. For example
7.2 can be set at either A or B.

7
TROUBLESHOOTING THE ECM MOTOR
Axion™ Fan Technology motors are designed with several built-
in protections included in the motor software. If the motor detects
a fault it will safely shut down. See Table 5, “Supply Fan Motor
Logic and Safety Relays” on page 36 for a complete list.
Troubleshooting the motor requires a voltmeter.
1. Disconnect main power to the unit.
2. Disconnect motor plug in supply section of the unit.
3. Restore main unit power.
4. Check for proper line voltage at motor power leads Black
(PL1-3), Yellow (PL1-6), and Blue (PL1-9).
5. Disconnect main power.
6. Reconnect motor plug in supply section of unit.
7. Restore main power.
8. Check for proper motor control voltage signal of 9.7 vdc to
10.3 vdc at IFM-1 and IFM-3 on Unit Control Board
(UCB). See Fig. 11.
9. Using a jumper wire from unit control terminals R to G,
engage motor operation.
10. Verify control signal from user speed selection switch by
placing voltmeter taps in provided terminals marked vdc.
Signal should be between 3.8 vdc and 10.3 vdc.
11. If the motor does not start and run, remove the fan assembly
and replace the motor with one having the same part number.
Do not substitute with an alternate design motor as the
voltage/speed programming will not be the same as that on an
original factory motor. Fig. 11 — Supply Fan Control Wiring Diagram
582K Unit Voltage Motor Voltage Min-Max Volts
208/230 230 187-253
460 460 360-506
575 575 517-633
NOTE: 2-PIN LOW SPEED DIP SWITCH POSITIONS ARE FACTORY SET AS SHOWN.
EXCEPTION ON T1 8.5 TON UNITS, THESE ARE SET TO “ON-ON”.

8
Removing the Motor and Fan Assembly
NOTE: Due to press fit design of composite Rotor on Motor, it is
highly recommended that any time a motor is replaced the fan ro-
tor is replaced as well. The rest of the assembly may be reused.
See Fig. 12.
1. Unplug motor harness from control box harness and cut
wire tie at the fan deck.
2. Unplug connectors from stator temperature limit switch.
3. Remove four brackets at front of stator on fan deck.
4. Slide fan assembly forward a couple of inches to clear rear
brackets and lift assembly out.
Fig. 12 — Fan Assembly Removal
2
3
4
1

9
Disassembling Standard/Medium Motor and Fan Assembly
See Fig. 13.
NOTE: Refer to “Model Number Nomenclature” on page 70,
position 13 for specific unit requirements.
1. Remove 4 screws from U-clips in fan casing.
2. Remove casing from assembly.
3. Remove 3 screws connecting rotor to motor flange.
4. Remove rotor from motor.
5. Remove 4 screws connecting motor to stator.
6. Remove stator from motor.
7. If required, remove fan limit switch from stator.
Fig. 13 — Disassembling Standard or Medium Static
Motor and Fan Assembly
Disassembling High Static Motor and Fan Assembly
See Fig. 14.
NOTE: Refer to “Model Number Nomenclature” on page 70,
position 13 for specific unit requirements.
1. Remove 4 screws from U-clips in fan casing.
2. Remove casing from assembly.
3. Remove 3 screws connecting rotor to motor flange.
4. Remove rotor from motor.
5. Remove 6 screws connecting motor to stator.
6. Remove motor from stator.
7. If required, remove fan limit switch from stator.
Fig. 14 — Disassembling High Static Motor and Fan
Assembly

10
Reassembly of Standard/Medium Motor and Fan Assembly
See Fig. 15.
NOTE: Refer to “Model Number Nomenclature” on page 70,
position 13 for specific unit requirements.
1. Place motor on flat surface.
2. If required, reinstall limit switch on stator with two plastic
fastener plugs (P/N: 48TM005675).
3. Line up keying features on stator and motor and set stator
onto motor. Install four 1/4-20 x 1-in. screws
(P/N: AC67AP170) to attach stator to motor. Tighten to
50 in.-lb (5.65 Nm).
4. Set rotor onto motor flange. Install three 1/4-20 x 1-in.
screws (P/N: AC67AP170) to attach rotor to motor.
Tighten to 50 in.-lb (5.65 Nm).
5. Set casing onto stator. Install four #10-16 x 3/4-in. screws
(P/N: AP13AD128) through U-Clips in casing. Tighten to
14 in.-lb (1.58 Nm).
6. Pull motor harness out through guide feature in stator if
not already completed.
Fig. 15 — Standard/Medium Fan System Re-
Assembly
Reassembly of High Static Motor and Fan Assembly
See Fig. 16.
NOTE: Refer to “Model Number Nomenclature” on page 70,
position 13 for specific unit requirements.
1. Place stator on flat surface.
2. If required, reinstall limit switch on stator with two plastic
fastener plugs (P/N: 48TM005675).
3. Line up keying features on stator and motor and set motor
onto stator. Motor wire Harness should align with guide
feature in stator. Install six 1/4-20 x 1-in. screws
(P/N: AC67AP170) to attach stator to motor. Tighten to
30 in.-lb (3.39 Nm).
4. Set rotor onto motor flange. Install three 1/4-20 x 1-in.
screws (P/N: AC67AP170) to attach rotor to motor.
Tighten to 50 in.-lb (5.65 Nm).
5. Set casing onto stator. Install four #10-16 x 3/4-in. screws
(P/N: AP13AD128) through U-Clips in casing. Tighten to
14 in.-lb (1.58 Nm).
6. Pull motor harness out through guide feature in stator if
not already completed.
Fig. 16 — High Static Fan System Re-Assembly

11
Reinstalling Motor and Fan Assembly
See Fig. 17.
1. Align motor harness/grommet at ~7 o’clock (facing
installer) and align the bottom flats on right and left sides
of fan stator with fan deck ribs. Drop fan assembly down
into fan deck opening and slide back until aluminum stator
is under the rear fan deck brackets.
2. Replace four front brackets and secure each with 2 #10 x
5/8-in. hex head screws (P/N: AL48AM217). Tighten to
50 in.-lb (5.65 Nm).
3. Reconnect wires for stator temperature limit switch.
4. Pull motor harness tight through grommet and plug it in to
the control box harness and secure in the corner with snap-
in wire tie.
Fig. 17 — Fan Assembly Installation
3
2
4
1

12
2-Speed Indoor Fan Motor System
All 582K*08-16 units with Axion™ Fan Technology come facto-
ry set to automatically adjust the indoor fan motor speed in se-
quence with the unit’s ventilation, cooling, and heating operation.
See Table 1 for fan operation for various modes.
COOLING
Condenser Coil
The condenser coil is fabricated with round tube copper hairpins
and plate fins of various materials and/or coatings (see Model
Number Nomenclature in Appendix A to identify the materials
provided in this unit). The coil may be one-row or composite-type
two-row. Composite two-row coils are two single-row coils fabri-
cated with a single return bend end tubesheet.
Condenser Coil Maintenance and Cleaning
Recommendation
Routine cleaning of coil surfaces is essential to maintain proper
operation of the unit. Elimination of contamination and removal of
harmful residues will greatly increase the life of the coil and ex-
tend the life of the unit. The following maintenance and cleaning
procedures are recommended as part of the routine maintenance
activities to extend the life of the coil.
REMOVE SURFACE LOADED FIBERS
Surface loaded fibers or dirt should be removed with a vacuum
cleaner. If a vacuum cleaner is not available, a soft non-metallic
bristle brush may be used. In either case, the tool should be ap-
plied in the direction of the fins. Coil surfaces can be easily dam-
aged (fin edges can be easily bent over and damage to the coating
of a protected coil) if the tool is applied across the fins.
NOTE: Use of a water stream, such as a garden hose, against a
surface loaded coil will drive the fibers and dirt into the coil. This
will make cleaning efforts more difficult. Surface loaded fibers
must be completely removed prior to using low velocity clean wa-
ter rinse.
PERIODIC CLEAN WATER RINSE
A periodic clean water rinse is very beneficial for coils that are ap-
plied in coastal or industrial environments. However, it is very im-
portant that the water rinse is made with a very low velocity water
stream to avoid damaging the fin edges. Monthly cleaning as de-
scribed below is recommended. Rinsing coils in the opposite di-
rection of airflow is recommended.
ROUTINE CLEANING OF COIL SURFACES
Periodic cleaning with Totaline®environmentally balanced coil
cleaner is essential to extend the life of coils. This cleaner is avail-
able from Replacement Components Division as P/N: P902-0301
for a one gallon container, and P/N: P902-0305 for a 5 gallon con-
tainer. It is recommended that all coils, including standard alumi-
num, pre-coated, copper/copper or e-coated coils be cleaned with
the Totaline environmentally balanced coil cleaner as described
below. Coil cleaning should be part of the unit’s regularly sched-
uled maintenance procedures to ensure long life of the coil. Failure
to clean the coils may result in reduced durability in the environ-
ment.
Avoid use of:
• coil brighteners
• acid cleaning prior to painting
• high pressure washers
• poor quality water for cleaning
Totaline environmentally balanced coil cleaner is nonflammable,
hypo-allergenic, non-bacterial, and a USDA accepted biodegrad-
able agent that will not harm the coil or surrounding components
such as electrical wiring, painted metal surfaces, or insulation. Use
of non-recommended coil cleaners is strongly discouraged since
coil and unit durability could be affected.
Clean coil as follows:
1. Turn off unit power, tag disconnect.
2. Remove all screws from the top panel except the screws
securing the condenser fan to the top panel. See Fig. 18.
Fig. 18 — Location of Screws and Coil Corner Post
3. Remove condenser coil corner post. See Fig. 18. To hold
top panel open, place coil corner post between top panel
and center post. See Fig. 19.
Table 1 — Percentage of Vdc Setting
UNIT HIGH COOL HEAT LOW COOL VENT
582K*08 100% 100% 60% 60%
582K*09 100% 100% 50% 50%
582K*12 100% 100% 60% 60%
582K*14 100% 100% 60% 60%
582K*16 100% 100% 66% 66%
WARNING
UNIT OPERATION AND SAFETY HAZARD
Failure to follow this warning could cause personal injury,
death and/or equipment damage.
This system uses Puron®refrigerant which has higher pres-
sures than R-22 and other refrigerants. No other refrigerant
may be used in this system. Gauge set, hoses, and recovery
system must be designed to handle Puron refrigerant. If unsure
about equipment, consult the equipment manufacturer.
Top Panel
Remove screws
from all sides
of top panel
Remove
Screws
Condenser
Fan
Condenser
Coil
Condenser Coil
Corner Post
Center
Post
Compressor
Access Panel

13
Fig. 19 — Propping Up Top Panel
4. Remove the compressor access panel to access the lower coil
clip. The condenser coil corner post may also be removed.
5. Remove the screws from both sides of the 4 coil retaining
clips on the hairpin end of the coil tube sheets. See Fig. 20.
6. Remove the 4 retaining clips.
Fig. 20 — Condenser Coil Clips
7. Draw the inner coil inward to separate the coils for cleaning.
8. Insert a spacer (field-supplied) between the tube sheets to
hold the coils apart. See Fig. 21.
9. Clean the outer coil surface to remove surface loaded
fibers or dirt. See “Remove Surface Loaded Fibers” on
page 12 for details.
10. Use a water hose or other suitable equipment to flush down
between the 2 coil sections to remove dirt and debris. If a
coil cleaner is used be sure to rinse the coils completely
before reassembly.
11. Move the inner coil back into position. Reinstall the 4 coil
clips. Reinstall the top panel and replace all screws.
Fig. 21 — Separating Coil Sections
(Top View)
Totaline Environmentally Balanced Coil Cleaner Application
Equipment
• 2-1/2 gallon garden sprayer
• Water rinse with low velocity spray nozzle
Totaline Environmentally Balanced Coil Cleaner Application
Instructions
1. Proper eye protection such as safety glasses is recommended
during mixing and application.
2. Remove all surface loaded fibers and dirt with a vacuum
cleaner as described above.
3. Thoroughly wet finned surfaces with clean water and a low
velocity garden hose, being careful not to bend fins.
4. Mix Totaline environmentally balanced coil cleaner in a 2-1/2
gallon garden sprayer according to the instructions included
with the cleaner. The optimum solution temperature is 100°F.
NOTE: Do NOT USE water in excess of 130°F, as the enzy-
matic activity will be destroyed.
5. Thoroughly apply Totaline environmentally balanced coil
cleaner solution to all coil surfaces including finned area, tube
sheets and coil headers.
Top Panel
Center
Baffle
Support
(Field-
Supplied)
CAUTION
UNIT DAMAGE HAZARD
Failure to follow this caution may result in reduced unit
performance or unit shutdown.
High velocity water from a pressure washer or garden hose,
or compressed air should never be used to clean a coil. The
force of the water or air jet will bend the fin edges and
increase airside pressure drop.
CAUTION
UNIT DAMAGE HAZARD
Failure to follow this caution may result in accelerated
corrosion of unit parts.
Harsh chemicals, household bleach or acid or basic
cleaners should not be used to clean outdoor or indoor coils
of any kind. These cleaners can be very difficult to rinse out
of the coil and can accelerate corrosion at the fin/tube
interface where dissimilar materials are in contact. If there
is dirt below the surface of the coil, use the Totaline
environmentally balanced coil cleaner.

14
6. Hold garden sprayer nozzle close to finned areas and apply
cleaner with a vertical, up-and-down motion. Avoid spraying
in horizontal pattern to minimize potential for fin damage.
7. Ensure cleaner thoroughly penetrates deep into finned areas.
Interior and exterior finned areas must be thoroughly cleaned.
Finned surfaces should remain wet with cleaning solution for
10 minutes. Ensure surfaces are not allowed to dry before
rinsing. Reapply cleaner as needed to ensure 10-minute
saturation is achieved.
8. Thoroughly rinse all surfaces with low velocity clean water
using downward rinsing motion of water spray nozzle.
Protect fins from damage from the spray nozzle.
Evaporator Coil
Cleaning the Evaporator Coil
1. Turn unit power off. Install lockout tag. Remove evapora-
tor coil access panel.
2. If economizer or two-position damper is installed, remove
economizer by disconnecting Molex®1 plug and removing
mounting screws.
3. Slide filters out of unit.
4. Clean coil using a commercial coil cleaner or dishwasher
detergent in a pressurized spray canister. Wash both sides
of coil and flush with clean water. For best results, back-
flush toward return-air section to remove foreign material.
Flush condensate pan after completion.
5. Reinstall economizer and filters.
6. Reconnect wiring.
7. Replace access panels.
Evaporator Coil Metering Devices
582K*08-16 units with or without the Perfect Humidity™ op-
tion use a TXV-distributer system.
THERMOSTATIC EXPANSION VALVE (TXV)
The TXV is a bi-flow, bleed port expansion valve with an external
equalizer. The TXVs are specifically designed to operate with
Puron®refrigerant. Use only factory-authorized TXVs.
TXV Operation
The TXV is a metering device that is used in air conditioning and
heat pump systems to adjust to the changing load conditions by
maintaining a preset superheat temperature at the outlet of the
evaporator coil.
The volume of refrigerant metered through the valve seat is de-
pendent upon the following:
1. Superheat temperature is sensed by cap tube sensing bulb
on suction tube at outlet of evaporator coil. This tempera-
ture is converted into pressure by refrigerant in the bulb
pushing downward on the diaphragm, which opens the
valve using the push rods.
2. The suction pressure at the outlet of the evaporator coil is
transferred through the external equalizer tube to the
underside of the diaphragm.
3. The pin is spring loaded, which exerts pressure on the under-
side of the diaphragm. Therefore, the bulb pressure works
against the spring pressure and evaporator suction pressure to
open the valve. If the load increases, the temperature
increases at the bulb, which increases the pressure on the top
side of the diaphragm. This opens the valve and increases the
flow of refrigerant. The increased refrigerant flow causes the
leaving evaporator temperature to decrease. This lowers the
pressure on the diaphragm and closes the pin. The refrigerant
flow is effectively stabilized to the load demand with
negligible change in superheat.
Replacing TXV
1. Recover refrigerant.
2. Remove TXV support clamp using a 5/l6-in. nut driver.
3. Remove TXV using a wrench and an additional wrench on
connections to prevent damage to tubing.
4. Remove equalizer tube from suction line of coil. Use file
or tubing cutter to cut brazed equalizer line approximately
2 inches above suction tube.
5. Remove bulb from vapor tube inside cabinet.
6. Install the new TXV using a wrench and an additional
wrench on connections to prevent damage to tubing while
attaching TXV to distributor.
7. Attach the equalizer tube to the suction line. If the coil has
a mechanical connection, then use a wrench and an addi-
tional wrench on connections to prevent damage. If the
coil has a brazed connection, use a file or a tubing cutter to
remove the mechanical flare nut from the equalizer line.
Then use a new coupling to braze the equalizer line to the
stub (previous equalizer line) in suction line.
8. Attach TXV bulb in the same location where the original
(in the sensing bulb indent) was when it was removed,
using the supplied bulb clamps. See Fig. 22.
9. Route equalizer tube through suction connection opening
(large hole) in fitting panel and install fitting panel in place.
10. Sweat the inlet of TXV marked “IN” to the liquid line. Avoid
excessive heat which could damage the TXV valve. Use
quenching cloth when applying heat anywhere on TXV.
Refrigerant System Pressure Access Ports
There are two access ports in the system: on the suction tube near
the compressor and on the discharge tube near the compressor.
These are brass fittings with black plastic caps. The hose connec-
tion fittings are standard 1/4-in. SAE male flare couplings.
The brass fittings are two-piece high flow valves, with a receptacle
base brazed to the tubing and an integral spring-closed check
valve core screwed into the base. See Fig. 23. This check valve is
permanently assembled into this core body and cannot be serviced
separately; replace the entire core body if necessary. Service tools
are available from RCD that allow the replacement of the check
valve core without having to recover the entire system refrigerant
charge. Apply compressor refrigerant oil to the check valve core’s
bottom o-ring. Install the fitting body with 96 ± 10 in.-lb
(10.85 ± 1.1 Nm) of torque; do not over-tighten.
1. Third-party trademarks and logos are the property of their respective
owners.

15
Fig. 22 — TXV Valve and Sensing Bulb Location
PURON (R-410A) REFRIGERANT
This unit is designed for use with Puron®(R-410A) refrigerant.
Do not use any other refrigerant in this system.
Puron (R-410A) refrigerant is provided in pink (rose) colored cyl-
inders. These cylinders are available with and without dip tubes;
cylinders with dip tubes will have a label indicating this feature.
For a cylinder with a dip tube, place the cylinder in the upright po-
sition (access valve at the top) when removing liquid refrigerant
for charging. For a cylinder without a dip tube, invert the cylinder
(access valve on the bottom) when removing liquid refrigerant.
Because Puron (R-410A) refrigerant is a blend, it is strongly rec-
ommended that refrigerant always be removed from the cylinder
as a liquid. Admit liquid refrigerant into the system in the dis-
charge line. If adding refrigerant into the suction line, use a com-
mercial metering/expansion device at the gauge manifold; remove
liquid from the cylinder, pass it through the metering device at the
gauge set and then pass it into the suction line as a vapor. Do not
remove Puron (R-410A) refrigerant from the cylinder as a vapor.
Refrigerant Charge
Amount of refrigerant charge is listed on the unit’s nameplate. Re-
fer to Bryant GTAC2-5 Charging, Recovery, Recycling and Recla-
mation training manual and the following procedures.
Unit panels must be in place when unit is operating during the
charging procedure.
NO CHARGE
Use standard evacuating techniques. After evacuating system,
weigh in the specified amount of refrigerant.
LOW-CHARGE COOLING
Using Cooling Charging Charts, Fig. 24-33, vary refrigerant until
the conditions of the appropriate chart are met. Note the charging
charts are different from type normally used. Charts are based on
charging the units to the correct sub-cooling for the various operat-
ing conditions. Accurate pressure gauge and temperature sensing
device are required. Connect the pressure gauge to the service port
on the liquid line. Mount the temperature sensing device on the
liquid line and insulate it so that outdoor ambient temperature does
not affect the reading. Indoor-air cfm must be within the normal
operating range of the unit.
EXAMPLE:
Model: . . . . . . . . . . . . . . . . . . . . . . . . . . . . . . . . . . . . . . 582K*08
Outdoor Temperature . . . . . . . . . . . . . . . . . . . . . . . 85°F (29°C)
Suction Pressure . . . . . . . . . . . . . . . . . . . . . . 140 psig (965 kPa)
Suction Temperature should be . . . . . . . . . . . . . . . 65°F (16°C)
USING COOLING CHARGING CHARTS
Take the outdoor ambient temperature and read the liquid pressure
gauge. Refer to chart to determine what liquid temperature should
be. If liquid temperature is low, add refrigerant. If liquid tempera-
ture is high, carefully recover some of the charge. Recheck the liq-
uid pressure as charge is adjusted.
Fig. 23 — CoreMax™1Access Port Assembly
VIEW WITH TXV BULB
INSULATION COVER REMOVED
TXV BULB
TXV BULB PROCESS TUBE
BULB CAPILLARY TUBE
SUCTION LINE
582K SIZE DESIGNATION NOMINAL TONS REFERENCE
08 7.5
09 8.5
12 10.0
14 12.5
16 15.0
1. Third-party trademarks and logos are the property of their respective owners.
5/8" HEX 0.47
30°
0.596
1/2-20 UNF RH
1/2" HEX
45°
Washer
O-Ring
7/16-20 UNF RH
Depressor per AHRI 720
+.01/–.035
From Face of Body
This surface provides a metal to metal seal when
torqued into the seat. Appropriate handling is
required to not scratch or dent the surface.
SEAT CORE
(Part No. EC39EZ067)

16
COOLING CHARGING CHARTS
Fig. 24 — Cooling Charging Chart - 7.5 Ton
1034 1379 1723 2068 2413 2758 3102 3447 3792 4136
-6.7
4.4
15.5
26.6
37.7
48.8
59.9
20
40
60
80
100
120
140
150 200 250 300 350 400 450 500 550 600
Outdoor Coil Leaving Temperature (°C/°F)
Compressor Discharge Pressure (psig/kPa)
Remove Charge if Below the Curve
Add Charge if Above Curve
7.5 Ton Entry Tier R-410A Charging Chart
(Unit must have both compressors and
outdoor fans on high speed)
48TM006268 Rev. -

17
COOLING CHARGING CHARTS
Fig. 25 — Cooling Charging Chart - 8.5 Ton
1034 1379 1723 2068 2413 2758 3102 3447 3792 4136
-6.7
4.4
15.5
26.6
37.7
48.8
59.9
20
40
60
80
100
120
140
150 200 250 300 350 400 450 500 550 600
Outdoor Coil Leaving Temperature (°C/°F)
Compressor Discharge Pressure (psig/kPa)
Remove Charge if Below the Curve
Add Charge if Above Curve
8.5 Ton Entry Tier R-410A Charging Chart
(Unit must have both compressors and
outdoor fans on high speed)
48TM006269 Rev. -

18
COOLING CHARGING CHARTS
Fig. 26 — Cooling Charging Chart - 10 Ton
1034 1379 1723 2068 2413 2758 3102 3447 3792 4136
-6.7
4.4
15.5
26.6
37.7
48.8
59.9
20
40
60
80
100
120
140
150 200 250 300 350 400 450 500 550 600
Outdoor Coil Leaving Temperature (°C/°F)
Compressor Discharge Pressure (psig/kPa)
Remove Charge if Below the Curve
Add Charge if Above Curve
10 Ton Entry Tier R-410A Charging Chart
(Unit must have both compressors and
outdoor fans on high speed)
48TM006270 Rev. -

19
COOLING CHARGING CHARTS
Fig. 27 — Cooling Charging Chart - 12.5 Ton
1034 1379 1723 2068 2413 2758 3102 3447 3792 4136
-6.7
4.4
15.5
26.6
37.7
48.8
59.9
20
40
60
80
100
120
140
150 200 250 300 350 400 450 500 550 600
Outdoor Coil Leaving Temperature (°C/°F)
Compressor Discharge Pressure (psig/kPa)
Remove Charge if Below the Curve
Add Charge if Above Curve
12.5 Ton Entry Tier R-410A Charging Chart
(Unit must have both compressors and
outdoor fans on high speed)
48TM006271 Rev. -

20
COOLING CHARGING CHARTS
Fig. 28 — Cooling Charging Chart - 15.0 Ton
1034 1379 1723 2068 2413 2758 3102 3447 3792 4136
-6.7
4.4
15.5
26.6
37.7
48.8
59.9
20
40
60
80
100
120
140
150 200 250 300 350 400 450 500 550 600
Outdoor Coil Leaving Temperature (°C/°F)
Compressor Discharge Pressure (psig/kPa)
Remove Charge if Below the Curve
Add Charge if Above Curve
15 Ton Entry Tier R-410A Charging Chart
(Unit must have both compressors and
outdoor fans on high speed)
50TM002022 Rev. -
This manual suits for next models
4
Table of contents
Other Bryant Heater manuals
Popular Heater manuals by other brands
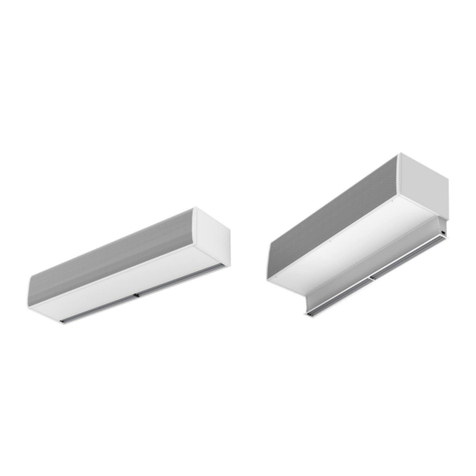
Airtecnics
Airtecnics FLY K 1000 A Installation, operation and maintenance manual

Thermofilm
Thermofilm ELEX euro 2000 user manual

Hyundai
Hyundai H-HV15-10-UI617 instruction manual
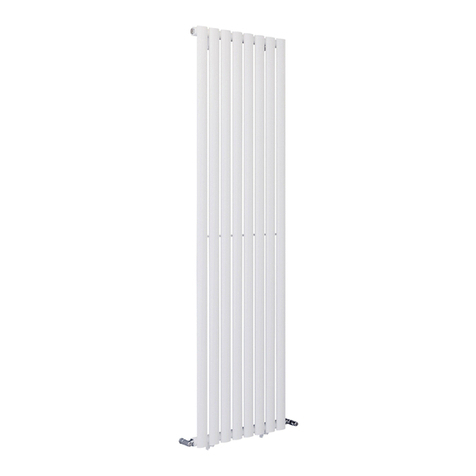
Blyss
Blyss Wickham 3663602847533 quick start guide
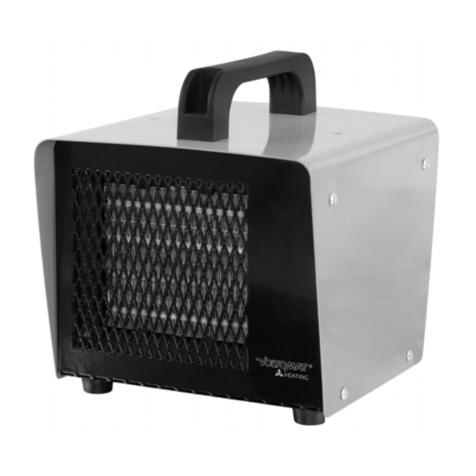
VOLTOMAT HEATING
VOLTOMAT HEATING FH-107760.1 instruction manual
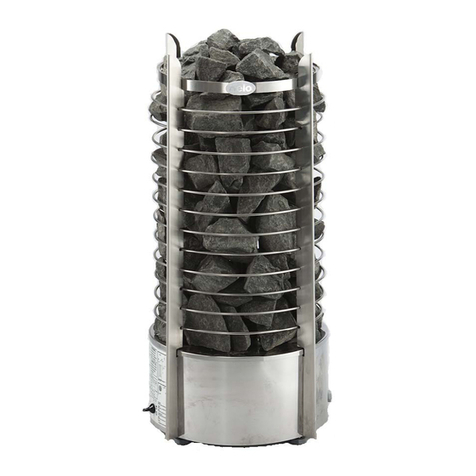
Helo
Helo Ring1118-600-0405 Installation and user manual

emerio
emerio PH-117295.1 instruction manual
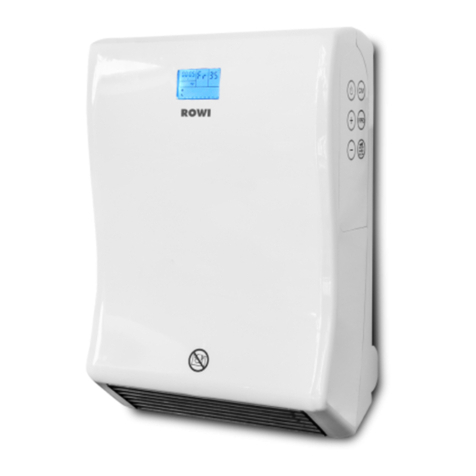
Rowi
Rowi HBS 2000/2/1 instruction manual
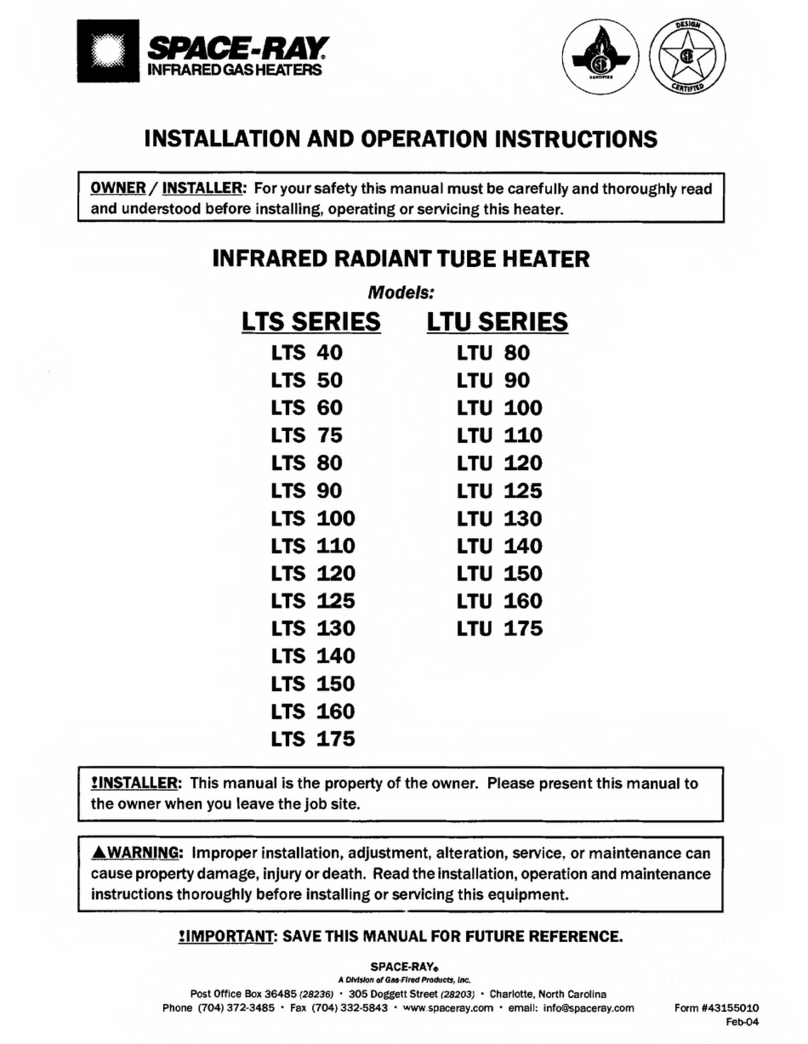
Space-Ray
Space-Ray LTS Series Assembly, installation and operation instructions
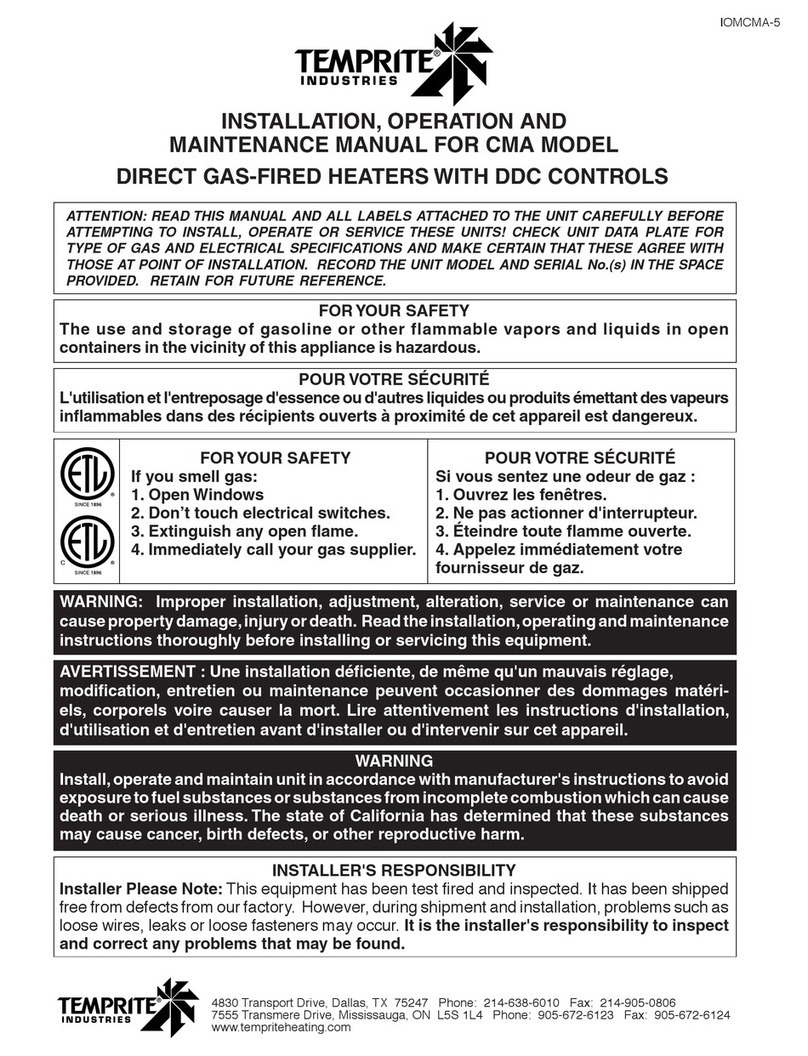
Temprite Industries
Temprite Industries CMA Installation, operation and maintenance manual
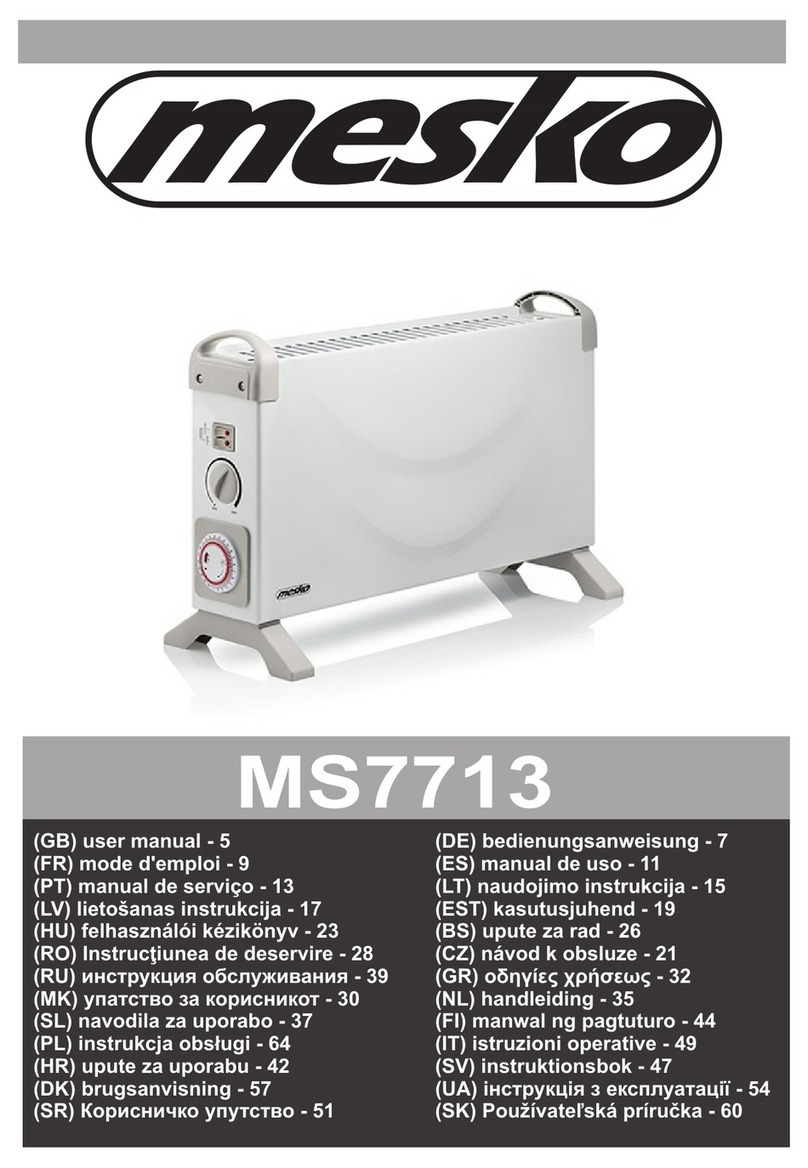
Mesko
Mesko MS7713 user manual
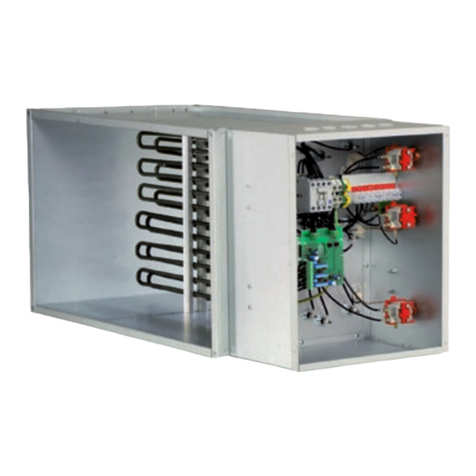
VEAB
VEAB VFLPG manual