Bryant ASPAS1BBA007 User manual

GENERAC
POWER SYSTEMS, INC.
R
R
Parts, Adjustment and
Maintenance Manual
Air-cooled, Prepackaged
Automatic Standby Generators
Models:
ASPAS1BBA007 (6 kW NG, 7 kW LP)
ASPAS1BBA012 (12 kW NG, 12 kW LP)
ASPAS1BBA015 (13 kW NG, 15 kW LP)
DEADLY EXHAUST FUMES. OUTDOOR INSTALLATION ONLY!!
DANGER
Not intended for use as Primary Power in place of utility
or in life-support applications.
!!
L
I
S
T
E
D
CU
S

Bryant
INTRODUCTION
This Bryant model is a compact, high performance,
air-cooled, engine-driven generator designed to
automatically supply electrical power to operate critical
loads during a utility power failure.
This unit is factory installed in an all-weather, metal enclosure
that is intended exclusively for outdoor installation. This
generator will operate using either vapor withdrawn liquid
propane (LP) or natural gas (NG).
READ THIS MANUAL THOROUGHLY
Throughout this publication, and on tags and
decals affixed to the generator, DANGER, WARNING,
CAUTION and NOTE blocks are used to alert personnel
to special instructions about a particular operation that
may be hazardous if performed incorrectly or carelessly.
Observe them carefully. Their definitions are as follows:
After this heading, read instructions that, if not
strictly complied with, will result in serious
personal injury, including death, in addition to
property damage.
After this heading, read instructions that, if not
strictly complied with, may result in serious
personal injury or property damage.
After this heading, read instructions that, if not
strictly complied with, could result in damage to
equipment and/or property.
NOTE:
After this heading, read explanatory statements
that require special emphasis.
These safety warnings cannot eliminate the hazards
that they indicate. Common sense and strict
compliance with the special instructions while
performing the service are essential to preventing
accidents.
Four commonly used safety symbols accompany the
DANGER, WARNING and CAUTION blocks. The type of
information each indicates follows:
This symbol points out important safety
information that, if not followed, could
endanger personal safety and/or property of
others.
This symbol points out potential explosion
hazard.
This symbol points out potential fire hazard.
This symbol points out potential electrical
shock hazard.
The operator is responsible for proper and safe use
of the equipment. Bryant strongly recommends that the
dealer read this Parts, Adjustment and Maintenance
Manual and thoroughly understand all instructions before
using this equipment. Bryant also strongly recommends
instructing other users to properly start and operate the
unit. This prepares them if they need to operate the
equipment in an emergency.
CONTENTS
This manual contains pertinent information for three
different Bryant models:
•ASPAS1BBA007 – 6 kW NG, 7 kW LP, single-cylinder
GH-410 Engine
•ASPAS1BBA012 – 12 kW NG, 12 kW LP, V-twin GT-
990 Engine
•ASPAS1BBA015 – 13 kW NG, 15 kW LP, V-twin GT-
990 Engine
OPERATION AND MAINTENANCE
It is the operator's responsibility to perform all safety
checks, to make sure that all maintenance for safe
operation is performed promptly, and to have the
equipment checked periodically by a Bryant Dealer.
Normal maintenance service and replacement of parts
are the responsibility of the owner/operator and, as such,
are not considered defects in materials or workmanship
within the terms of the warranty. Individual operating
habits and usage contribute to the need for maintenance
service.
Proper maintenance and care of the generator ensures a
minimum number of problems and keep operating
expenses at a minimum. See a Bryant Dealer for service
aids and accessories.
HOW TO OBTAIN SERVICE
When the generator requires servicing or repairs, contact
a Bryant Dealer for assistance. Service technicians are
factory-trained and are capable of handling all service
needs.
When inquiring about parts or service, always supply the
complete model number and serial number of the unit as
given on its data decal, which is located on the generator.
See Figure 1.1 or Figure 1.2 in Section 1.4 of the Owner’s
Manual for decal location.
Model No. ____________ Serial No. ____________
!
DANGER

Table of Contents
Bryant Air-cooled 7 kW, 12 kW and 15 kW Generators
Bryant 1
Introduction ........................Inside Front Cover
Read This Manual Thoroughly ..............................IFC
Contents ................................................................IFC
Operation and Maintenance ..................................IFC
How to Obtain Service ..........................................IFC
Important Safety Instructions ........................2
Standards Index ........................................................3
Section 1 – Post Installation Start-up and
Adjustments ..............................................4
1.1 Before Initial Start Up ..........................................4
1.2 Check Transfer Switch Operation........................4
1.3 Electrical Checks ................................................4
1.4 Generator Tests Under Load ..............................5
1.5 Checking Automatic Operation............................5
1.6 Adjusting The Regulator (Natural Gas Only) ......5
1.7 Reconfiguring The Fuel System ..........................6
1.7.1 7kW, 410cc Engine ....................................6
1.7.2 12kW and 15kW, V-Twin Engines..............7
1.8 Engine Governor Adjustment ..............................7
1.8.1 7kW Units ..................................................7
1.8.2 12kW and 15kW Units................................8
1.9 Voltage Regulator Adjustment ............................8
1.10 Adjusting GH-410/GT-990 Valve Clearance........8
1.11 The Battery ..........................................................8
Section 2 – Troubleshooting ........................10
2.1 Troubleshooting Guide ......................................10
Section 3 – Maintenance ..............................11
3.1 Service Schedule ..............................................11
Section 4 – Electrical Data ............................12
Section 5 – Exploded Views and
Parts Lists....................................26
Section 6 – Unit Dimensions ........................47
Section 7 – Notes ............................................48

2 Bryant
Study these SAFETY RULES carefully before installing,
operating or servicing this equipment. Become familiar with
this Parts, Adjustment and Maintenance Manual and with the
unit. The generator can operate safely, efficiently and reliably
only if it is properly installed, operated and maintained. Many
accidents are caused by failing to follow simple and
fundamental rules or precautions.
Bryant cannot possibly anticipate every possible
circumstance that might involve a hazard. The warning in
this manual, and on tags and decals affixed to the unit
are, therefore, not all-inclusive. If using a procedure, work
method or operating technique that Bryant does not
specifically recommend, satisfy yourself that it is safe for
others. Also make sure the procedure, work method or
operating technique chosen does not render the generator
unsafe.
Despite the safe design of this generator,
operating this equipment imprudently, neglecting
its maintenance or being careless can cause
possible injury or death. Permit only responsible
and capable persons to install, operate or
maintain this equipment.
Potentially lethal voltages are generated by these
machines. Ensure all steps are taken to render the
machine safe before attempting to work on the
generator.
Parts of the generator are rotating and/or hot
during operation. Exercise care near running
generators.
GENERAL HAZARDS
• For safety reasons, Bryant recommends that this
equipment be installed, serviced and repaired by a Bryant
Dealer.
• The engine exhaust fumes contain carbon monoxide gas,
which can be DEADLY. This dangerous gas, if breathed
in sufficient concentrations, can cause unconsciousness
or even death. For that reason, adequate ventilation must
be provided. This exhaust system must be installed
properly, in strict compliance with applicable codes and
standards. Following installation, do nothing that might
render the system unsafe or in noncompliance with such
codes and standards.
• Keep hands, feet, clothing, etc., away from drive belts,
fans, and other moving or hot parts. Never remove any
drive belt or fan guard while the unit is operating.
• Adequate, unobstructed flow of cooling and ventilating air
is critical to correct generator operation. Do not alter the
installation or permit even partial blockage of ventilation
provisions, as this can seriously affect safe operation of
the generator. The generator must be installed outdoors.
• When working on this equipment, remain alert at all
times. Never work on the equipment when physically or
mentally fatigued.
• Inspect the generator regularly, and contact the nearest
Bryant Dealer for parts needing repair or replacement.
• Before performing any maintenance on the generator,
disconnect its battery to prevent accidental start up.
Disconnect the cable from the battery post indicated by a
NEGATIVE, NEG or (—) first. Reconnect that cable last.
• Never use the generator or any of its parts as a step.
Stepping on the unit can stress and break parts, and may
result in dangerous operating conditions from leaking
exhaust gases, fuel leakage, oil leakage, etc.
!
!
!
!
DANGER
SAVE THESE INSTRUCTIONS – The manufacturer suggests that these rules for safe
operation be copied and posted near the unit’s installation site. Safety should be stressed to
all operators and potential operators of this equipment.
!
!
The engine exhaust from this product
contains chemicals known to the state
of California to cause cancer, birth
defects or other reproductive harm.
WARNING:
!!
This product contains or emits chemicals
known to the state of California to cause
cancer, birth defects or other reproductive harm.
WARNING:
!!

ELECTRICAL HAZARDS
• All generators covered by this manual produce
dangerous electrical voltages and can cause fatal
electrical shock. Utility power delivers extremely high and
dangerous voltages to the transfer switch as well as the
standby generator. Avoid contact with bare wires,
terminals, connections, etc., on the generator as well as
the transfer switch, if applicable. Ensure all appropriate
covers, guards and barriers are in place before operating
the generator. If work must be done around an operating
unit, stand on an insulated, dry surface to reduce shock
hazard.
• Do not handle any kind of electrical device while standing
in water, while barefoot, or while hands or feet are wet.
DANGEROUS ELECTRICAL SHOCK MAY RESULT.
• If people must stand on metal or concrete while installing,
operating, servicing, adjusting or repairing this
equipment, place insulative mats over a dry wooden
platform. Work on the equipment only while standing on
such insulative mats.
• The National Electrical Code (NEC) requires the frame
and external electrically conductive parts of the generator
to be connected to an approved earth ground. This
grounding will help prevent dangerous electrical shock
that might be caused by a ground fault condition in the
generator set or by static electricity. Never disconnect the
ground wire. Local electrical codes also may require
proper grounding of the generator electrical system.
• After installing this home standby electrical system, the
generator may crank and start at any time without
warning. When this occurs, load circuits are transferred
to the STANDBY (generator) power source. To prevent
possible injury if such a start and transfer occur, always
set the generator's Auto/Off/Manual switch to its OFF
position before working on equipment and remove the
7.5A and 15A fuses from the generator control panel.
• In case of accident caused by electric shock,immediately
shut down the source of electrical power. If this is not
possible, attempt to free the victim from the live
conductor. AVOID DIRECT CONTACT WITH THE
VICTIM. Use a nonconducting implement, such as a dry
rope or board, to free the victim from the live conductor.
If the victim is unconscious, apply first aid and get
immediate medical help.
• Never wear jewelry when working on this equipment.
Jewelry can conduct electricity resulting in electric shock,
or may get caught in moving components causing injury.
FIRE HAZARDS
• Keep a fire extinguisher near the generator at all times.
Do NOT use any carbon tetra-chloride type extinguisher.
Its fumes are toxic, and the liquid can deteriorate wiring
insulation. Keep the extinguisher properly charged and
be familiar with its use. Consult the local fire department
for any questions pertaining to fire extinguishers.
EXPLOSION HAZARDS
• Do not smoke around the generator. Wipe up any fuel or
oil spills immediately. Ensure that no combustible
materials are left in the generator compartment, or on or
near the generator, as FIRE or EXPLOSION may result.
Keep the area surrounding the generator clean and free
from debris.
• Fuels such as natural gas and LP gas are extremely
EXPLOSIVE. Install the fuel supply system according to
applicable fuel-gas codes. Before placing the home
standby electric system into service, fuel system lines
must be properly purged and leak tested according to
applicable code. After installation, inspect the fuel system
periodically for leaks. No leakage is permitted.
STANDARDS INDEX
In the absence of pertinent standards, codes, regulations
and laws, the published information listed below may be
used as installation guide for this equipment.
1. NFPA No. 37, STATIONARY COMBUSTION ENGINES
AND GAS TURBINES, available from the National Fire
Protection Association, 470 Atlantic Avenue, Boston, MA
02210.
2. NFPA No. 76A, ESSENTIAL ELECTRICAL SYSTEMS
FOR HEALTH CARE FACILITIES, available same as
Item 1.
3. NFPA No. 54, NATIONAL FUEL GAS CODE, available
same as Item 1.
4. NFPA No. 58, AMERICAN NATIONAL STANDARD FOR
STORAGE AND HANDLING OF LIQUEFIED
PETROLEUM GAS, available same as Item 1.
5. NFPA No. 70, NFPA HANDBOOK OF NATIONAL
ELECTRIC CODE, available same as Item 1.
6. Article X, NATIONAL BUILDING CODE, available from
the American Insurance Association, 85 John Street,
New York, N.Y. 10038.
7. AGRICULTURAL WIRING HANDBOOK, available from
the Food and Energy Council, 909 University Avenue,
Columbia, MO 65201.
8. ASAE EP-3634, INSTALLATION AND MAINTENANCE
OF FARM STANDBY ELECTRICAL SYSTEMS,
available from the American Society of Agricultural
Engineers, 2950 Niles Road, St. Joseph, MI 49085.
9. NFPA No. 30, FLAMMABLE AND COMBUSTIBLE
LIQUIDS CODE, available same as Item 1.
◆
Bryant 3

4 Bryant
Section 1 — Post Installation Start-up and Adjustments
Bryant Air-cooled 7 kW, 12 kW and 15 kW Generators
1.1 BEFORE INITIAL START-UP
Before starting, complete the following:
1. Set the generator’s main circuit breaker to its OFF (or
open) position.
2. Set the generator's AUTO/OFF/MANUAL switch to
the OFF position.
3. Turn OFF the utility power supply to the transfer
switch using the means provided (such as the utility
main line circuit breaker).
4. Turn OFF all loads connected to the transfer switch
terminals T1 and T2.
5. Check the engine crankcase oil level and, if
necessary, fill to the dipstick FULL mark with the
recommended oil. Do not fill above the FULL mark.
6. Check the fuel supply. Gaseous fuel lines must have
been properly purged and leak tested in accordance
with applicable fuel-gas codes. All fuel shutoff valves
in the fuel supply lines must be open.
Never operate the engine with the oil level
below the “Add” mark on the dipstick. Doing
this could damage the engine.
1.2 CHECK TRANSFER SWITCH
OPERATION
Refer to Section 3.5, of the owner’s manual for manual
operation procedures.
Do not attempt manual transfer switch
operation until all power voltage supplies to
the transfer switch have been positively turned
off. Failure to turn off all power voltage
supplies will result in extremely hazardous and
possibly fatal electrical shock.
1.3 ELECTRICAL CHECKS
Complete electrical checks as follows:
1. Set the generator's main circuit breaker to its OFF (or
open) position.
2. Set the generator's Auto/Off/Manual switch to the
OFF position.
3. Turn OFF all loads connected to the transfer switch
terminals T1 and T2.
4. Turn on the utility power supply to the transfer switch
using the means provided (such as a utility main line
circuit breaker).
The transfer switch is now electrically “hot.”
Contact with “hot” parts will result in
extremely hazardous and possibly fatal
electrical shock. Proceed with caution.
5. Use an accurate AC voltmeter to check utility power
source voltage across transfer switch terminals N1
and N2. Nominal line-to-line voltage should be 240
volts AC.
6. Check utility power source voltage across terminals
N1 and the transfer switch neutral lug; then across
terminal N2 and neutral. Nominal line-to-neutral
voltage should be 120 volts AC.
7. When certain that utility supply voltage is compatible
with transfer switch and load circuit ratings, turn OFF
the utility power supply to the transfer switch.
8. On the generator panel, set the AUTO/OFF/
MANUAL switch to MANUAL. The engine should
crank and start.
9. Let the engine warm up for about five minutes to
allow internal temperatures to stabilize. Then, set the
generator’s main circuit breaker to its ON (or
CLOSED) position.
Proceed with caution! Generator power voltage
is now supplied to the transfer switch. Contact
with live transfer switch parts will result in
dangerous and possibly fatal electrical shock.
10. Connect an accurate AC voltmeter and a frequency
meter across transfer switch terminal lugs E1 and E2.
Voltage should be 242-252 volts; frequency should
read about 61-63 Hertz.
11. Connect the AC voltmeter test leads across terminal
lug E1 and neutral; then across E2 and neutral. In
both cases, voltage reading should be 121-126 volts
AC.
12. Set the generator’s main circuit breaker to its OFF (or
open) position. Let the engine run at no-load for a few
minutes to stabilize internal engine generator
temperatures.
13. Set the generator's AUTO/OFF/MANUAL switch to
OFF. The engine should shut down.
NOTE:
It is important not to proceed until certain that
generator AC voltage and frequency are correct and
within the stated limits. Generally, if both AC
frequency and voltage are high or low, the engine
governor requires adjustment. If frequency is
correct, but voltage is high or low, the generator’s
voltage regulator requires adjustment.
DANGER
DANGER
DANGER
!

1.4 GENERATOR TESTS UNDER LOAD
To test the generator set with electrical loads applied,
proceed as follows:
1. Set generator’s main circuit breaker to its OFF (or
OPEN) position.
2. Turn OFF all loads connected to the transfer switch
terminals T1 and T2.
3. Set the generator's AUTO/OFF/MANUAL switch to
OFF.
4. Turn OFF the utility power supply to the transfer
switch, using the means provided (such as a utility
main line circuit breaker).
Do not attempt manual transfer switch
operation until all power voltage supplies to
the transfer switch have been positively turned
off. Failure to turn off all power voltage
supplies will result in extremely hazardous and
possibly fatal electrical shock.
5. Manually set the transfer switch to the STANDBY
position, i.e., load terminals connected to the
generator's E1/E2 terminals. The transfer switch
operating lever should be down.
6. Set the generator's AUTO/OFF/MANUAL switch to
MANUAL. The engine should crank and start
immediately.
7. Let the engine stabilize and warm up for a few
minutes.
8. Set the generator’s main circuit breaker to its ON (or
closed) position. Loads are now powered by the
standby generator.
9. Turn ON electrical loads connected to transfer switch
T1 and T2. Apply an electrical load equal to the full
rated wattage/amperage capacity of the installed
generator.
10. Connect an accurate AC voltmeter and a frequency
meter across terminal lugs E1 and E2. Voltage
should be greater than 230 volts; frequency should
be greater than 58 Hertz.
11. Let the generator run at full rated load for 20-30
minutes. Listen for unusual noises, vibration or other
indications of abnormal operation. Check for oil
leaks, evidence of overheating, etc.
12. When testing under load is complete, turn OFF
electrical loads.
13. Set the generator's main circuit breaker to its OFF (or
OPEN) position.
14. Let the engine run at no-load for a few minutes.
15. Set the AUTO/OFF/MANUAL switch to OFF. The
engine should shut down.
1.5 CHECKING AUTOMATIC
OPERATION
To check the system for proper automatic operation,
proceed as follows:
1. Set generator’s main circuit breaker to its OFF (or
OPEN) position.
2. Check that the AUTO/OFF/MANUAL switch is set to
OFF.
3. Turn OFF the utility power supply to the transfer
switch, using means provided (such as a utility main
line circuit breaker).
4. Manually set the transfer switch to the UTILITY
position, i.e., load terminals connected to the utility
power source side.
5. Turn ON the utility power supply to the transfer
switch, using the means provided (such as a utility
main line circuit breaker).
6. Set the AUTO/OFF/MANUAL switch to AUTO. The
system is now ready for automatic operation.
7. Turn OFF the utility power supply to the transfer
switch.
With the AUTO/OFF/MANUAL switch at AUTO, the
engine should crank and start when the utility source
power is turned OFF. After starting, the transfer switch
should connect load circuits to the standby side. Let the
system go through its entire automatic sequence of
operation.
With the generator running and loads powered by
generator AC output, turn ON the utility power supply to
the transfer switch. The following should occur:
• After about six seconds, the switch should transfer
loads back to the utility power source.
• About one minute after retransfer, the engine should
shut down.
1.6 ADJUSTING THE REGULATOR
(NATURAL GAS ONLY)
Although the generator has been factory set to provide
maximum power, it may be necessary in some areas to
adjust this setting. Because natural gas has different BTU
or power content across the country the engine may not
perform as designed.
If experiencing engine problems at high or full load
conditions follow these steps. It will require a frequency
meter to perform this procedure.
1. Turn off utility power to the main distribution panel in
the house. This can be done by switching the service
main breaker to the off or open position.
2. Allow the generator to start. Before loading the
generator, confirm that the No Load Frequency, with
the top open and front panel off, is set to 63-63.5 Hz.
Transfer load to emergency circuits.
Section 1 — Post Installation Start-up and Adjustments
Bryant Air-cooled 7 kW, 12 kW and 15 kW Generators
Bryant 5

3. Turn on appliances, lights, pumps, etc., that are on
the emergency circuits in an attempt to fully load the
generator. Be cautious not to overload the generator.
Use the following chart as a guide:
4. When full load has been achieved. Connect a
frequency meter to the output lugs of the generator’s
main line circuit breaker.
5. The fuel regulator is fitted with one (7 kW), or two (12
& 15 kW) adjustment screws. While watching the
frequency meter, slowly turn the adjustment screws
clockwise or counterclockwise one at a time until the
highest frequency is read on the meter. Only limited
adjustment is available because of the set pin. Under
no circumstances should any of the pins be removed
(Figures 1.1 and 1.2).
Figure 1.1 — Dual Fuel Regulators
6. When the highest frequency is reached maximum
power has been set. From this point turn both
adjustment screws 1/4 turn counterclockwise. The
regulator is now set.
Figure 1.2 — Placement of Regulator
7. Turn utility power to the main distribution panel back
on. This can be done by switching the service main
breaker to the on or closed position. Allow the
generator to shut down.
Do not make any unnecessary adjustments.
Factory settings are correct for most
applications. However, when making
adjustments, be careful to avoid overspeeding
the engine.
1.7 RECONFIGURING THE
FUEL SYSTEM
1.7.1 7 KW, 410CC ENGINE
To reconfigure the fuel system from NG to LP,
follow these steps (Figure 1.3):
NOTE:
The primary regulator for the propane supply is NOT
INCLUDED with the generator. A fuel pressure of 11
to 14 inches of water column (0.4 to 0.5 psi) to the
fuel inlet of the generator MUST BE SUPPLIED.
1. Turn off the main gas supply (if connected).
2. Open the top and remove the front panel.
3. Remove the battery (if installed).
4. Disconnect wire #0 and wire #14 from the gas
solenoid on top of the demand regulator.
5. Remove the carburetor fuel hose from the outlet port
of the demand regulator.
6. Remove the demand regulator by removing the
fastener that retains the regulator mounting bracket.
7. Remove the square headed steel pipe plug from
outlet port #1 and the brass hose barb fitting from
outlet port #2.
8. Refit the brass hose barb fitting to outlet port #1 and
the square headed steel pipe plug to outlet port #2.
Figure 1.3 – Demand Regulator
◆
!
410
Adjustment
Screw
(One Side
Only)
Set
Pin
V-twin
Adjustment
Screw
(Both Sides)
Set Pin
(Both Sides)
Adjustment Screw
N
G
F
U
EL
S
Y
S
TE
M
LP F
U
EL
S
Y
S
TE
M
F
U
EL H
OSE
BRA
SS
H
OS
E
FITTIN
G
BRA
SS
H
OS
E
FITTIN
G
F
U
EL
J
E
T
OU
TLE
T
P
O
R
T
F
U
EL H
OSE
AD
JUS
TMEN
T
SC
RE
W
H
OS
E & PL
UG
S
WIT
C
HED
S
IDE
S
PIPE
PL
UG
Section 1 — Post Installation Start-up and Adjustments
Bryant Air-cooled 7 kW, 12 kW and 15 kW Generators
Unit 120 Volts 240 Volts
7 kW 50.0 amps 25.0 amps
12 kW 100.0 amps 50.0 amps
13 kW 108.3 amps 54.1 amps
6 Bryant

9. Reverse procedure steps 1-5 to reinstall demand
regulator.
10. Reverse the procedure to convert back to natural
gas.
1.7.2 12KW AND 15KW, V-TWIN ENGINES
To reconfigure the fuel system from NG to LP,
follow these steps:
NOTE:
The primary regulator for the propane supply is NOT
INCLUDED with the generator. A fuel pressure of 11
to 14 inches of water column (0.4 to 0.5 psi) to the
fuel inlet of the generator MUST BE SUPPLIED.
1. Turn off the gas supply. (if connected)
2. Open the top and remove the front panel.
3. Remove the battery. (if installed)
4. Remove the engine air in baffle located on the left-
hand side of the battery compartment. Two M6
screws are located on top of the baffle and two M6
screws are located on the inside of the baffle towards
the back.
5. Remove the small hose clamp and hose from the fuel
regulator. It may be necessary to pry the hose off of
the brass fitting using a screwdriver to gently lift up
the hose edge.
6. Remove the small brass hose fitting from the
regulator casting.
7. Place the small fuel jet, thread side first, into the
threaded hole originally occupied by the brass hose
fitting (Figure 1.4).
8. Using a short No. 2 Phillips screw driver, thread the
small fuel jet into the regulator casting. Do not over
tighten.
9. Apply thread sealant to the threads of the hose fitting
and replace it into the regulator body.
10. Re-attach the small hose and hose clamp and tighten
as necessary.
11. Replace the engine air in baffle using the four M6
screws.
12. Identify both brass adjustment screws on the
regulator.
NOTE:
One adjustment screw can be accessed from the
front of the unit and the second can be accessed
from the back of the unit enclosure by removing the
plastic hole plug. The screw can be turned with a
long flat blade screwdriver.
13. To adjust the system to run on LP fuel, turn BOTH
adjuster screws 1/2 TURN CLOCKWISE. The
system should now be set for maximum power and
best performance. DO NOT, UNDER ANY
CIRCUMSTANCES, REMOVE THE SET PINS
FROM THE REGULATOR HOUSING. THIS WILL
VOID THE WARRANTY.
14. It may be necessary to make minor adjustments to
the preset adjustment screw settings to achieve
maximum power, particularly at higher altitudes. If
experiencing problems with the unit producing
maximum power, follow the procedure in Section 1.6
(Adjusting the Fuel Regulator).
Figure 1.4 - Demand Regulator
1.8 ENGINE GOVERNOR ADJUSTMENT
If both AC frequency and voltage are correspondingly
high or low, adjust the engine governor as follows:
1.8.1 7 KW UNITS
1. Loosen the governor clamp bolt (Figures 1.5).
2. Hold the governor lever at its wide open throttle
position, and rotate the governor shaft clockwise as
far as it will go. Then, tighten the governor lever
clamp bolt to 70 inch-pounds (8 N-m).
3. Start the generator; let it stabilize and warm up at no-
load.
4. Connect a frequency meter (or high quality multi-
meter set to the frequency mode) across the
generators AC output leads.
5. Turn the speed adjust nut to obtain a frequency
reading of 63 Hertz.
Figure 1.5 — Engine Governor Adjustment
Single Cylinder Engines
◆
◆
BRA
SS
H
OS
E
FITTIN
G
IDLE
C
IR
CU
I
T
P
O
R
T
U
1
T
TAP
1
/8
NP
T
BRA
SS
H
OS
E
FITTIN
G
F
U
EL H
OSE
S
MAL
L
F
U
EL
J
E
T
RE
GU
LAT
OR
H
OUS
IN
G
P
O
R
T
AD
JUS
TE
R
SC
REW
S
OU
TLET P
O
RT
S
GOVERNOR
SHAFT
ADJUST
SCREW
GOVERNOR
CLAMP
BOLT
Section 1 — Post Installation Start-up and Adjustments
Bryant Air-cooled 7 kW, 12 kW and 15 kW Generators
Bryant 7

6. When frequency is correct at no load, check the AC
voltage reading. If voltage is incorrect, the voltage
regulator may require adjustment.
1.8.2 12 KW AND 15 KW UNITS
1. Loosen governor clamp bolt (See Figure 1.6).
2. Completely remove the idle spring.
3. With governor arm at wide open throttle position
(rotated fully clockwise), rotate governor shaft fully
clockwise. Tighten clamp bolt to 84 inch-pounds.
4. Start unit and apply full load. Use full load speed
adjust screw (Figure 1.7) to adjust frequency to 58
Hz.
5. Remove load, stop engine, loosen the idle adjust
screw and reconnect the idle spring.
6. Push the governor arm to the closed throttle position.
Make sure the idle spring does not stretch at all.
Figure 1.6 — Engine Governor Adjustment
V-twin Engines
Figure 1.7 — Full Load Speed Adjust Screw
V-Twin Engines
7. Restart the unit.
8. Slowly turn the idle adjust screw to adjust the no-load
idle frequency to 63-63.5 Hz (with top open).
9. The governor is now set.
1.9 VOLTAGE REGULATOR
ADJUSTMENT
With the frequency between 62-63 Hertz, slowly turn the
slotted potentiometer (Figure 1.8) until line voltage reads
247-252 volts.
Figure 1.8 – Voltage Adjustment Potentiometer
NOTE:
The access panel on top of the control panel must be
removed to adjust the voltage regulator.
NOTE:
The voltage regulator is housed above the
generator's control panel. The regulator maintains a
voltage in direct proportion to frequency at a 2-to-1
ratio. For example, at 62 Hertz, line-to-neutral voltage
will be 124 volts.
1.10 ADJUSTING GH-410/GT-990
VALVE CLEARANCE
After the first 6 months of operation, adjust the valve
clearance in the engine.
Important: If feeling uncomfortable about doing this
procedure or the proper tools are not available, please
contact a Bryant dealer for service assistance. This step
necessary to insure the longest life for the engine.
To adjust valve clearance:
• Make sure the engine is at room temperature.
• Make sure that the spark plug wire is removed from the
spark plug and out of the way.
◆
Governor Clamp Bolt
Governor
Shaft
(Rotate
Clockwise)
Idle Spring
No Load Idle
Adjustment Screw
Full Load
S
peed Adjust
S
crew
Section 1 — Post Installation Start-up and Adjustments
Bryant Air-cooled 7 kW, 12 kW and 15 kW Generators
8 Bryant

• Remove the four screws attaching the valve cover with
a #2 or #3 phillips screwdriver.
• Make sure the piston is at Top Dead Center (TDC) of
its compression stroke (both valves closed). To get the
piston at TDC, remove the intake screen at the front of
the engine to gain access to the flywheel nut. Use a
large socket and socket wrench to rotate the nut and
hence the engine. While watching the piston through
the spark plug hole. The piston should move up and
down. The piston is at TDC when it is up as high as it
can go.
• Loosen the rocker jam nut. Use an 10mm allen wrench
to turn the pivot ball stud while checking clearance
between the rocker arm and the valve stem with a
feeler gauge. Correct clearance is 0.002-0.004 inch
(0.05-0.1 mm).
NOTE:
Hold the rocker arm jam nut in place as the pivot ball
stud is turned.
When valve clearance is correct, hold the pivot ball stud
in place with the allen wrench and tighten the rocker arm
jam nut. Tighten the jam nut to 174 in/lbs. torque. After
tightening the jam nut, recheck valve clearance to make
sure it did not change.
Figure 1.9 - Valve Clearance Adjustment
• Install new valve cover gasket.
• Re-attach the valve cover.
NOTE:
Start all four screws before tightening or it will not be
possible to get all the screws in place. Make sure the
valve cover gasket is in place.
• Re-attach the spark plug wire to the spark plug.
• On GT-990, Repeat the process for the other cylinder.
NOTES:
Jam Nut
Pivot Ball
Stud
Rocker
Arm
Valve
Stem
Bryant 9
Section 1 — Post Installation Start-up and Adjustments
Bryant Air-cooled 7 kW, 12 kW and 15 kW Generators

Section 2 — Troubleshooting
Bryant Air-cooled 7 kW, 12 kW and 15 kW Generators
2.1 TROUBLESHOOTING GUIDE
PROBLEM CAUSE CORRECTION
The engine will not crank. 1. Fuse blown. 1. Replace 15A fuse in generator
control panel.
2. Loose, corroded or defective 2. Tighten, clean or replace
battery cables. as necessary.
3. Defective starter contactor. (7 kW) 3. *
4. Defective starter motor. 4. *
5. Dead Battery. 5. Charge or replace battery.
The engine cranks but 1. Out of fuel. 1. Replenish fuel.
will not start. 2. Defective fuel solenoid (FS). 2. *
3. Open #14 wire from 3. *
engine control board.
4. Defective spark plug(s). 4. Clean, re-gap or replace plug(s).
5. Valve lash out of adjustment. 5. *
The engine starts hard 1. Air cleaner plugged 1. Check, replace air cleaner.
and runs rough. or damaged.
2. Defective spark plug(s). 2. Clean, re-gap or replace plug(s).
3. Fuel Regulator not set. 3. Set Fuel Regulator.
4. Fuel Pressure incorrect. 4. Confirm fuel pressure to regulator
is 11-14” water column (0.4-0.5 psi)
for LP, and 5-7” water column (0.18-
0.25 psi) for natural gas.
The Auto/Off/Manual switch 1. Defective switch. 1. *
is set to OFF, but the engine 2. Auto/Off/Manual switch 2. *
continues to run. wired incorrectly.
3. Defective control board. 3. *
There is no AC output from 1. Main line circuit breaker open. 1. Reset circuit breaker
the generator. to ON (or closed).
2. Generator internal failure. 2. *
There is no transfer to 1. Defective transfer switch coil. 1. *
standby after utility 2. Defective transfer relay. 2. *
source failure. 3. Transfer relay circuit open. 3. *
4. Defective control logic board. 4. *
Unit consumes large Break-in procedure *
amounts of oil. not followed (see Section 3.1).
*Contact the nearest Bryant Dealer for assistance.
10 Bryant

Bryant 11
Section 3 — Maintenance
Bryant Air-cooled 7 kW, 12 kW and 15 kW Generators
3.1 SERVICE SCHEDULE
ATTENTION: It is recommended that all service work
be performed by the nearest Bryant Dealer.
SYSTEM/COMPONENT PROCEDURE FREQUENCY
X = Action Inspect Change Clean W = Weekly
R = Replace as Necessary M = Monthly
* = Notify Dealer Y = Yearly
if Repair is Needed.
FUEL
Fuel lines and connections* XM
LUBRICATION
Oil level XM
Oil X AFTER BREAK-IN,
AND Y
Oil filter X AFTER BREAK-IN,
AND Y
COOLING
Enclosure louvers XXW
BATTERY
Remove corrosion, XXM
ensure dryness
Clean and tighten XXM
battery terminals
Check charge state X R EVERY 6 M
Electrolyte level X R EVERY 6 M
(unsealed batteries only)*
ENGINE AND MOUNTING
Air cleaner XR Y
Spark plug(s) XR Y
GENERAL CONDITION
Vibration, Noise, Leakage, XM
Temperature*
COMPLETE TUNE-UP* TO BE COMPLETED BY A Y
BRYANT DEALER

CB3 - CIRCUIT BREAKER, EXTERNAL OUTLET, PUSH/PULL
CB3 - CIRCUIT BREAKER, EXTERNAL OUTLET, PUSH/PULL
TX - TRANSFORMER, 16 Vac 56 VA & 16 Vac 1 VA (DUAL SEC.)
TX - TRANSFORMER, 16 Vac 56 VA & 16 Vac 1 VA (DUAL SEC.)
CB2 - CIRCUIT BREAKER, ALTERNATOR EXCITATION
CB2 - CIRCUIT BREAKER, ALTERNATOR EXCITATION
BLACK
BLACK
CUSTOMER SUPPLIED
CUSTOMER SUPPLIED
BATTERY
BATTERY
12V
12V
LOP
LOP
HTO
HTO
SP
SP
86
86
85
85
IM
IM
D
D
CB1 - MAIN OUTPUT BREAKER
CB1 - MAIN OUTPUT BREAKER
BA - BRUSH ASSEMBLY
BA - BRUSH ASSEMBLY
BCR - BATTERY CHARGE RELAY
BCR - BATTERY CHARGE RELAY
D - DIODE
D - DIODE
SC - STARTER CONTACTOR
SC - STARTER CONTACTOR
ICT - INTERCONNECTION TERMINALS
ICT - INTERCONNECTION TERMINALS
IC - INLINE CONNECTOR
IC - INLINE CONNECTOR
HTO - HIGH OIL TEMPERATURE SWITCH
HTO - HIGH OIL TEMPERATURE SWITCH
GRD - CONTROL PANEL GROUND
GRD - CONTROL PANEL GROUND
FS - FUEL SOLENOID
FS - FUEL SOLENOID
SW1 - AUTO / OFF / MANUAL SWITCH
SW1 - AUTO / OFF / MANUAL SWITCH
LOP - LOW OIL PRESSURE SWITCH
LOP - LOW OIL PRESSURE SWITCH
IM - IGNITION MODULE
IM - IGNITION MODULE
F2 - FUSE 7.5 AMP
F2 - FUSE 7.5 AMP
F1 - FUSE 15 AMP
F1 - FUSE 15 AMP
SP - SPARK PLUG
SP - SPARK PLUG
TB - INSULATED TERMINAL BLOCK
TB - INSULATED TERMINAL BLOCK
SM - STARTER MOTOR
SM - STARTER MOTOR
SW2 - SET EXERCISE SWITCH
SW2 - SET EXERCISE SWITCH
DSW - PCB MOUNTED DIP SWITCH
DSW - PCB MOUNTED DIP SWITCH
DIAGRAM KEY
DIAGRAM KEY
PRINTED CIRCUIT BOARD
PRINTED CIRCUIT BOARD
DSW
DSW
CONTROL
CONTROL
4 - SPARE
4 - SPARE
ON - INDICATES
ON - INDICATES
2 - Remote Not Auto
2 - Remote Not Auto
3 - 50 Hz Operation
3 - 50 Hz Operation
1 - 20 Vac Sense Transformer
1 - 20 Vac Sense Transformer
L.E.D - ALARM INDICATORS
L.E.D - ALARM INDICATORS
2
2
SM
SM
RED
RED
16
16
SC
SC
ON
ON
1
1
13
13
IC
IC
IC
IC
0
0
56
56
0
0
IC
IC
14
14
56
56
13
13
86
86
C1
C1
3
3
1
1
2
2
86
86
56
56
85
85
18
18
0
0
85
85
18
18
14
14
6
6
4
4
5
5
0
0
14
14
14
14
16
16
17
17
J1
J1
4
4
3
3
3
3
J2
J2
1
1
2
2
5
5
4
4
11
11
13
13
12
12
15
15
14
14
7
7
8
8
9
9
10
10
15
15
224
224
225
225
0
0
66A
66A
14
14
239
239
15A
15A
17
17
2
2
5
5
4
4
3
3
6
6
1
1
86
86
56
56
194
194
23
23
18
18
4
4
351
351
13
13
14
14
18
18
56
56
TB
TB
4
4
351
351
13
13
0
0
4
4
0
0
ENGINE WIRING
ENGINE WIRING
0
0
FS
FS
14
14
13
13
0
0
224B
224B
13
13
0
0
BATTERY
BATTERY
(UTILITY)
(UTILITY)
CHARGER
CHARGER
225B
225B
225B
225B
224B
224B
14
14
13
13
0
0
0
4
CLOSEST TO BEARING
OUTPUT TO TRANSFER
240V GENERATOR
SWITCH CONTACTOR
8
2
0
13
15
0
15
66A
15A
239
17
23
194 66A
12VDC ACCESSORY SOCKET
+
15
-
F2
17
15B
239
13
15A
0
13
15
F1
13
224
225 0
0
351
13
224
4
0
225
0
N2
N1
13
N2
N1
VOLTAGE
REGULATOR
66A
0
0
4
162
4
6
0
22
11 11
4
22
SW2
351
1
MANUAL
1b
17
15
SW1
15A 239
AUTO 1a
0
CONNECTION
CUSTOMER
G
0
L
G
0
L
LINE
3
HOT
OUTLET
LOAD
1
HOT
WHITE
4
5
G
2
WHITE
EXTERNAL
GFCI
CB3
N
11
N2
23
351
N1
194
0
0
00
0
GRD
162
6
4
00
66A
0
055
0
G
77
55
6
66A
22
66
11
0
1
C2
4
3
2
7
6
5
225B
0
66
CONTROL PANEL BOX
224A
225B
14
224B
13
0
225
224
N2N1
224A
14
66
224B
TX
225A
BCR
225A
CB2
162
77 2
4
9
10
0
4
2
194
RELAY COIL
NEUTRAL CONNECTION
CB1
11
11
44 N 22 33
240VAC UTILITY INPUT
12Vdc TRANSFER
N1
23 N2
77
11
11
44
22
66
66A
55
22 33
44
611
BA
STATOR
2
2
1
1
3
3
1
1
2
2
+
+
-
-
64
97
BA
31
12 Bryant
Section 4 - Electrical Data
Bryant Air-cooled 7 kW, 12 kW and 15 kW Generators
Wiring Diagram — Single Cylinder — Drawing No. 0E9014

Bryant 13
Section 4 - Electrical Data
Bryant Air-cooled 7 kW, 12 kW and 15 kW Generators
Wiring Diagram — Single Cylinder — Drawing No. 0E9014
CB3 - CIRCUIT BREAKER, EXTERNAL OUTLET, PUSH/PULL
TX - TRANSFORMER, 16 Vac 56 VA & 16 Vac 1 VA (DUAL SEC.)
CB2 - CIRCUIT BREAKER, ALTERNATOR EXCITATION
BLACK
CUSTOMER SUPPLIED
BATTERY
12V
LOP
HTO
SP
86
85
IM
D
CB1 - MAIN OUTPUT BREAKER
BA - BRUSH ASSEMBLY
BCR - BATTERY CHARGE RELAY
D - DIODE
SC - STARTER CONTACTOR
ICT - INTERCONNECTION TERMINALS
IC - INLINE CONNECTOR
HTO - HIGH OIL TEMPERATURE SWITCH
GRD - CONTROL PANEL GROUND
FS - FUEL SOLENOID
SW1 - AUTO / OFF / MANUAL SWITCH
LOP - LOW OIL PRESSURE SWITCH
IM - IGNITION MODULE
F2 - FUSE 7.5 AMP
F1 - FUSE 15 AMP
SP - SPARK PLUG
TB - INSULATED TERMINAL BLOCK
SM - STARTER MOTOR
SW2 - SET EXERCISE SWITCH
DSW - PCB MOUNTED DIP SWITCH
DIAGRAM KEY
PRINTED CIRCUIT BOARD
DSW
CONTROL
4 - SPARE
ON - INDICATES
2 - Remote Not Auto
3 - 50 Hz Operation
1 - 20 Vac Sense Transformer
L.E.D - ALARM INDICATORS
2
SM
RED
16
SC
ON
1
13
IC
IC
0 56
0
IC
14
56
13
86
C1
3
1
2
86 56
85 18
0
85
18
14
6
4
5
0
14
14
1617
J1
4
3
3
J2
12 54
1113 1215 14 78910
15
224
225
0
66A
14
239
15A
17
254361
86
56
194
23
18
4
351
13
14
18
56
TB
4
351
13
0
4
0
ENGINE WIRING
0
FS
14 130
224B
13
0
BATTERY
(UTILITY)
CHARGER
225B
225B
224B
14
13
0
0
0
4
4
CLOSEST TO BEARING
CLOSEST TO BEARING
OUTPUT TO TRANSFER
OUTPUT TO TRANSFER
240V GENERATOR
240V GENERATOR
SWITCH CONTACTOR
SWITCH CONTACTOR
8
8
2
2
0
0
13
13
15
15
0
0
15
15
66A
66A
15A
15A
239
239
17
17
23
23
194
194
66A
66A
12VDC ACCESSORY SOCKET
12VDC ACCESSORY SOCKET
+
+
15
15
-
-
0
F2
F2
17
17
15B
15B
239
239
13
13
15A
15A
0
0
13
13
15
15
F1
F1
13
13
224
224
225
225
0
0
0
0
351
351
13
13
224
224
4
4
0
0
225
225
0
0
N2
N2
N1
N1
13
13
N2
N2
N1
N1
VOLTAGE
VOLTAGE
REGULATOR
REGULATOR
66A
66A
0
0
0
0
4
4
162
162
4
4
6
6
0
0
22
22
11
11
4
11
11
4
4
22
22
SW2
SW2
351
351
1
1
MANUAL
MANUAL
1b
1b
17
17
15
15
SW1
SW1
15A
15A
239
239
AUTO
AUTO
1a
1a
0
0
CONNECTION
CONNECTION
CUSTOMER
CUSTOMER
G
G
0
0
L
L
G
G
0
0
L
L
LINE
LINE
3
3
HOT
HOT
OUTLET
OUTLET
LOAD
LOAD
1
1
HOT
HOT
WHITE
WHITE
4
4
5
5
G
G
2
2
WHITE
WHITE
EXTERNAL
EXTERNAL
GFCI
GFCI
CB3
CB3
N
N
11
11
N2
N2
23
23
351
351
N1
N1
194
194
0
0
0
0
0
0
0
0
0
0
GRD
GRD
162
162
6
6
4
4
0
0
0
0
66A
66A
0
0
0
0
55
55
0
0
G
G
77
77
55
55
6
6
66A
66A
22
22
66
66
11
11
0
0
1
1
C2
C2
4
4
3
3
2
2
7
7
6
6
5
5
225B
225B
0
0
66
66
CONTROL PANEL BOX
CONTROL PANEL BOX
224A
224A
225B
225B
14
14
224B
224B
13
13
0
0
225
225
224
224
N2
N2
N1
N1
224A
224A
14
14
66
66
224B
224B
TX
TX
225A
225A
BCR
BCR
225A
225A
CB2
CB2
162
162
77
77
2
2
4
4
9
9
10
10
0
0
4
4
2
2
194
194
RELAY COIL
RELAY COIL
NEUTRAL CONNECTION
NEUTRAL CONNECTION
CB1
CB1
11
11
11
11
44
44
N
N
22
22
33
33
240VAC UTILITY INPUT
240VAC UTILITY INPUT
12Vdc TRANSFER
12Vdc TRANSFER
N1
N1
23
23
N2
N2
77
77
11
11
11
11
44
44
22
22
66
66
66A
66A
55
55
22
22
33
33
44
44
6
6
11
11
BA
BA
STATOR
STATOR
2
1
3
1
2
+
-
6
6
4
4
9
9
7
7
B
B
A
A
3
3
1
1

14 Bryant
13
13
77
77
CB3 - CIRCUIT BREAKER, EXTERNAL OUTLET, PUSH/PULL
CB3 - CIRCUIT BREAKER, EXTERNAL OUTLET, PUSH/PULL
(STATOR)
(STATOR)
CB1 - CIRCUIT BREAKER, MAIN OUTPUT
CB1 - CIRCUIT BREAKER, MAIN OUTPUT
HTO - HIGH OIL TEMPERATURE SWITCH
HTO - HIGH OIL TEMPERATURE SWITCH
SW1 - AUTO / OFF / MANUAL SWITCH
SW1 - AUTO / OFF / MANUAL SWITCH
CB2 - CIRCUIT BREAKER, ALT. EXCITATION
CB2 - CIRCUIT BREAKER, ALT. EXCITATION
TX - TRANSFORMER, 16 Vac 56 VA & 16 Vac 1 VA
(
DUAL SEC.
)TX - TRANSFORMER, 16 Vac 56 VA & 16 Vac 1 VA (DUAL SEC.)
DPE WINDING
DPE WINDING
BCR - BATTERY CHARGE RELAY
BCR - BATTERY CHARGE RELAY
BA - BRUSH ASSEMBLY
BA - BRUSH ASSEMBLY
F1 - FUSE 15 AMP
F1 - FUSE 15 AMP
F2 - FUSE 7.5 AMP
F2 - FUSE 7.5 AMP
SP - SPARK PLUG
SP - SPARK PLUG
FS - FUEL SOLENOID
FS - FUEL SOLENOID
IM - IGNITION MODULE
IM - IGNITION MODULE
HM - HOUR RUN METER
HM - HOUR RUN METER
SC - STARTER CONTACTOR
SC - STARTER CONTACTOR
SW2 - SET EXERCISE SWITCH
SW2 - SET EXERCISE SWITCH
SM - STARTER MOTOR
SM - STARTER MOTOR
LOP - LOW OIL PRESSURE SWITCH
LOP - LOW OIL PRESSURE SWITCH
D - DIODE
D - DIODE
DIAGRAM KEY
DIAGRAM KEY
REGULATOR
REGULATOR
ELECTRONIC
ELECTRONIC
VOLTAGE
VOLTAGE
CB2
CB2
2
2
C2-8
C2-8
2
2
6
6
162
162
0
0
4
4
11
11
22
22
C2-10
C2-10
4
4
0
0
11
11
22
22
0
0
0
0
351
351
J2
J2
CONTROL
CONTROL
PRINTED CIRCUIT
PRINTED CIRCUIT
BOARD
BOARD
55
55
C2-7
C2-7
6
6
0
0
FIELD
FIELD
6
6
BA
BA
77
77
0
0
C2-9
C2-9
C2-11
C2-11
0
0
C2-4
C2-4
0
0
1
1
3
3
2
2
85
85
C2-3
C2-3
ENGINE RUN
ENGINE RUN
4
4
(STATOR)
(STATOR)
WINDING
WINDING
66
66
0
0
66A
66A
C2-2
C2-2
HTO
HTO
C1-4
C1-4
0
0
15A
15A
10
10
14
14
17
17
16
16
15
15
12
12
11
11
13
13
225
225
224
224
17
17
15
15
0
0
194
194
14
14
4
4
23
23
66A
66A
2
2
J1
J1
6
6
7
7
9
9
8
8
3
3
5
5
4
4
4
4
5
5
1
1
86
86
194
194
239
239
14
14
66A
66A
23
23
18
18
56
56
86
86
4
4
SW2
SW2
C1-3
C1-3
LOP
LOP
0
0
14
14
225
225
224
224
239
239
66A
66A
0
0
194
194
23
23
4
4
22
22
225B
225B
BATTERY CHARGE
BATTERY CHARGE
WINDING
WINDING
BATTERY
BATTERY
CHARGER
CHARGER
C2-1
C2-1
0
0
3
3
1
1
2
2
13
13
2
2
1
1
11
11
224A
224A
77
77
224B
224B
225A
225A
6
6
1
1
66
66
3
3
9
9
9
9
7
7
7
7
14
14
BCR
BCR
0
0
225A
225A
224A
224A
13
13
225A
225A
13
13
224A
224A
225
225
224
224
11
11
22
22
CB3
OUTLET
EXTERNAL
17
239
SW1
C1-2
IM
15A
17
15
0
C1-6
C1-5
18
0
D
00
239
1715A
18
56
14
15
0 18
17
23
194
0
013
C1-1
56
14
13
15
G
SC FS
14
15A
15 15
CUSTOMER
SUPPLIED
BLACK
SP
G
RED
SC
SM
15
N
11
BATTERY
12V
G
N
GN
WINDING
(STATOR)
POWER
11
22
44 CB1
33
C2-5
F1
N2
225A
1VA
56VA
12VDC ACCESSORY
SOCKET
13
225
224
224A
0-
+
N1
22
11
TX
15
13
15B
F2
13
N2
22
11
C2-6
N1
15
15
194
23
22
22
11
N
23
194
N2
N1
GFCI
L
240V
L
120V
120V
CUSTOMER
CONNECTIONS
240VAC
TRANSFER
COIL
RELAY
INPUT
12Vdc
UTILITY
NEUTRAL
Section 4 - Electrical Data
Bryant Air-cooled 7 kW, 12 kW and 15 kW Generators
Electrical Schematic — Single Cylinder — Drawing No. 0E9015

Bryant 15
Section 4 - Electrical Data
Bryant Air-cooled 7 kW, 12 kW and 15 kW Generators
Electrical Schematic — Single Cylinder — Drawing No. 0E9015
13
77
CB3 - CIRCUIT BREAKER, EXTERNAL OUTLET, PUSH/PULL
(STATOR)
CB1 - CIRCUIT BREAKER, MAIN OUTPUT
HTO - HIGH OIL TEMPERATURE SWITCH
SW1 - AUTO / OFF / MANUAL SWITCH
CB2 - CIRCUIT BREAKER, ALT. EXCITATION
TX - TRANSFORMER, 16 Vac 56 VA & 16 Vac 1 VA (DUAL SEC.)
DPE WINDING
BCR - BATTERY CHARGE RELAY
BA - BRUSH ASSEMBLY
F1 - FUSE 15 AMP
F2 - FUSE 7.5 AMP
SP - SPARK PLUG
FS - FUEL SOLENOID
IM - IGNITION MODULE
HM - HOUR RUN METER
SC - STARTER CONTACTOR
SW2 - SET EXERCISE SWITCH
SM - STARTER MOTOR
LOP - LOW OIL PRESSURE SWITCH
D - DIODE
DIAGRAM KEY
REGULATOR
ELECTRONIC
VOLTAGE
CB2
2
C2-8 2
6
162
0
4
11
22
C2-10
4
0
11 22 0
0
351
J2
CONTROL
PRINTED CIRCUIT
BOARD
55
C2-7
6
0
FIELD
6
BA
77
0
C2-9
C2-11
0
C2-4
0
132
85
C2-3
ENGINE RUN
4
(STATOR)
WINDING
66
0
66A
C2-2
HTO
C1-4
0
15A
10
14
17
16
15
12
11
13
225
224
17
15
0
194
14
423
66A
2
J1
6
7
9
8
3
5
4
45
1
86
194
239
14
66A
23
18
56
86
4
SW2
C1-3
LOP
0
14225
224
239
66A
0
194
23
4
22
225B
BATTERY CHARGE
WINDING
BATTERY
CHARGER
C2-1
0
3
1
2
13
2
1
11
224A
77
224B
225A
61
66
3
9977
14
BCR
0
225A
224A
13
225A
13
224A
225
224
11
22
CB3
CB3
OUTLET
OUTLET
EXTERNAL
EXTERNAL
17
17
239
239
SW1
SW1
C1-2
C1-2
IM
IM
15A
15A
17
17
15
15
0
0
C1-6
C1-6
C1-5
C1-5
18
18
0
0
D
D
0
0
0
0
239
239
17
17
15A
15A
18
18
56
56
14
14
15
15
0
0
18
18
17
17
23
23
194
194
0
0
0
0
13
13
C1-1
C1-1
56
56
14
14
13
13
15
15
G
G
SC
SC
FS
FS
14
14
15A
15A
15
15
15
15
CUSTOMER
CUSTOMER
SUPPLIED
SUPPLIED
BLACK
BLACK
SP
SP
G
G
RED
RED
SC
SC
SM
SM
15
15
N
N
11
11
BATTERY
BATTERY
12V
12V
G
G
N
N
G
G
N
N
WINDING
WINDING
(STATOR)
(STATOR)
POWER
POWER
11
11
22
22
44
44
CB1
CB1
33
33
C2-5
C2-5
F1
F1
N2
N2
225A
225A
1VA
1VA
56VA
56VA
12VDC ACCESSORY
12VDC ACCESSORY
SOCKET
SOCKET
13
13
225
225
224
224
224A
224A
0
0
-
-
+
+
N1
N1
22
22
11
11
TX
TX
15
15
13
13
15B
15B
F2
F2
13
13
N2
N2
22
22
11
11
C2-6
C2-6
N1
N1
15
15
15
15
194
194
23
23
22
22
22
22
11
11
N
N
23
23
194
194
N2
N2
N1
N1
GFCI
GFCI
L
L
240V
240V
L
L
120V
120V
120V
120V
CUSTOMER
CUSTOMER
CONNECTIONS
CONNECTIONS
240VAC
240VAC
TRANSFER
TRANSFER
COIL
COIL
RELAY
RELAY
INPUT
INPUT
12Vdc
12Vdc
UTILITY
UTILITY
NEUTRAL
NEUTRAL

16 Bryant
GRD
CB3 - CIRCUIT BREAKER, EXTERNAL OUTLET, PUSH/PULL
CB3 - CIRCUIT BREAKER, EXTERNAL OUTLET, PUSH/PULL
TX - TRANSFORMER, 16 Vac 56 VA & 16 Vac 1 VA (DUAL SEC.)
TX - TRANSFORMER, 16 Vac 56 VA & 16 Vac 1 VA (DUAL SEC.)
CUSTOMER SUPPLIED
CUSTOMER SUPPLIED
BLACK
BLACK
BATTERY
BATTERY
12V
12V
0
0
HTO
HTO
SP2
SP2
SP1
SP1
LOP
LOP
0
0
86
86
85
85
IM2
IM2
85
85
IM1
IM1
D
D
D
D
BA - BRUSH ASSEMBLY
BA - BRUSH ASSEMBLY
DIAGRAM KEY
DIAGRAM KEY
CB2 - CIRCUIT BREAKER, ALTERNATOR EXCITATION
CB2 - CIRCUIT BREAKER, ALTERNATOR EXCITATION
CB1 - MAIN OUTPUT BREAKER
CB1 - MAIN OUTPUT BREAKER
BCR - BATTERY CHARGE RELAY
BCR - BATTERY CHARGE RELAY
SP1, SP2 - SPARK PLUGS
SP1, SP2 - SPARK PLUGS
SC - STARTER CONTACTOR
SC - STARTER CONTACTOR
IC - INLINE CONNECTOR
IC - INLINE CONNECTOR
HTO - HIGH OIL TEMPERATURE SWITCH
HTO - HIGH OIL TEMPERATURE SWITCH
GRD - CONTROL PANEL GROUND
GRD - CONTROL PANEL GROUND
ICT - INTERCONNECTION TERMINALS
ICT - INTERCONNECTION TERMINALS
TB - INSULATED TERMINAL BLOCK
TB - INSULATED TERMINAL BLOCK
SW2 - SET EXERCISE SWITCH
SW2 - SET EXERCISE SWITCH
SW1 - AUTO / OFF / MANUAL SWITCH
SW1 - AUTO / OFF / MANUAL SWITCH
LOP - LOW OIL PRESSURE SWITCH
LOP - LOW OIL PRESSURE SWITCH
IM2 - IGNITION MODULE, CYLINDER #2
IM2 - IGNITION MODULE, CYLINDER #2
IM1 - IGNITION MODULE, CYLINDER #1
IM1 - IGNITION MODULE, CYLINDER #1
SCR - STARTER CONTACTOR RELAY
SCR - STARTER CONTACTOR RELAY
DSW - PCB MOUNTED DIP SWITCH
DSW - PCB MOUNTED DIP SWITCH
F1 - FUSE 15 AMP
F1 - FUSE 15 AMP
F2 - FUSE 7.5 AMP
F2 - FUSE 7.5 AMP
FS - FUEL SOLENOID
FS - FUEL SOLENOID
SM - STARTER MOTOR
SM - STARTER MOTOR
D - DIODE
14
14
85
85
L.E.D - ALARM INDICATORS
L.E.D - ALARM INDICATORS
3 - 50 Hz Operation
3 - 50 Hz Operation
4 - SPARE
4 - SPARE
PRINTED CIRCUIT BOARD
PRINTED CIRCUIT BOARD
1 - 20 Vac Sense Transformer
1 - 20 Vac Sense Transformer
2 - Remote Not Auto
2 - Remote Not Auto
ON - INDICATES
ON - INDICATES
RED
RED
SM
SM
SC
SC
13
13
16
16
ON
ON
86
86
IC
IC
IC
IC
IC
IC
C1
C1
16
16
85
85
86
86
A
A
56
56
SCR
SCR
5
5
4
4
6
6
1
1
2
2
3
3
86
86
18
18
85
85
13
13
0
0
18
18
0
0
16
16
13
13
2
2
J1
J1
86
86
56
56
23
23
239
239
14
14
18
18
15A
15A
66A
66A
194
194
0
0
224
224
15
15
225
225
17
17
4
4
CONTROL
CONTROL
DSW
DSW
1
1
3
3
2
2
16
16
17
17
13
13
12
12
14
14
15
15
7
7
10
10
9
9
8
8
11
11
3
3
4
4
5
5
6
6
4
4
1
1
3
3
J2
J2
2
2
4
4
18
18
B
B
0
0
16
16
15
15
351
351
14
14
14
14
5
5
1
1
18
18
56
56
86
86
TB
TB
14
14
351
351
18
18
56
56
14
14
13
13
15
15
0
0
14
14
ENGINE WIRING
ENGINE WIRING
14
14
0
0
FS
FS
14
14
0
0
13
13
0
0
224B
224B
14
14
13
13
0
0
225B
225B
BATTERY
BATTERY
CHARGER
CHARGER
225B
225B
224B
224B
14
14
0
0
13
13
0
0
225
225
224
224
15
224
225
0
239
15A
66A
17
23
194
4
0
14
0
225B
224B
13
0
11
CLOSEST TO BEARING
240V GENERATOR
SWITCH CONTACTOR
CONNECTION
OUTPUT TO TRANSFER
4
06677
4
4
0
F2
12VDC ACCESSORY SOCKET
+
17
15
0
0
-
F1
15B
15
15
15
13
13
15
239
17
REGULATOR
VOLTAGE
13
194
23
15
351
66A
13
15
13
0
N1
N2
0
N1
4
66A
N2
15A
23
351
N2
N1
194
0
162
6
0
0
0
66A
6
162
0
MANUAL
SW2
239
AUTO
SW1
1b
1
1a
15A
0
0
0
351 L
G
CUSTOMER
HOT
WHITE
LINE
G
3
5
4
G
GFCI
LOAD
OUTLET
EXTERNAL
1
HOT
WHITE
2
CB1
N
0
0
00G
000
0
55
0
0
11
23
CB3
L
N1
N2
194
11
11 44
55 C2
3
2
1
66
N1
13
225B
N2
224B
TX
224
225 224A
225A
3
BCR
B
9
6
22
11
14
4
7
A
1
0
22
11
66
77
224A 225A
4
CB2
162
2
6
22
11
2
4
CONTROL PANEL BOX
7
5
6
9
8
10
22
6
2
0
4
N2
N1
NEUTRAL CONNECTION
240VAC UTILITY INPUT
N
22
RELAY COIL
12Vdc TRANSFER
194
33 23
22
44
11
33
55
66A
66
77
BA
STATOR
2
2
1
1
3
3
1
1
2
2
-
-
+
+
Section 4 - Electrical Data
Bryant Air-cooled 7 kW, 12 kW and 15 kW Generators
Wiring Diagram — V-Twin — Drawing No. 0E9016

Bryant 17
Section 4 - Electrical Data
Bryant Air-cooled 7 kW, 12 kW and 15 kW Generators
Wiring Diagram — V-Twin — Drawing No. 0E9016
GRD
GRD
CB3 - CIRCUIT BREAKER, EXTERNAL OUTLET, PUSH/PULL
TX - TRANSFORMER, 16 Vac 56 VA & 16 Vac 1 VA (DUAL SEC.)
CUSTOMER SUPPLIED
BLACK
BATTERY
12V
0
HTO
SP2
SP1
LOP
0
86
85
IM2
85
IM1
D
D
BA - BRUSH ASSEMBLY
DIAGRAM KEY
CB2 - CIRCUIT BREAKER, ALTERNATOR EXCITATION
CB1 - MAIN OUTPUT BREAKER
BCR - BATTERY CHARGE RELAY
SP1, SP2 - SPARK PLUGS
SC - STARTER CONTACTOR
IC - INLINE CONNECTOR
HTO - HIGH OIL TEMPERATURE SWITCH
GRD - CONTROL PANEL GROUND
ICT - INTERCONNECTION TERMINALS
TB - INSULATED TERMINAL BLOCK
SW2 - SET EXERCISE SWITCH
SW1 - AUTO / OFF / MANUAL SWITCH
LOP - LOW OIL PRESSURE SWITCH
IM2 - IGNITION MODULE, CYLINDER #2
IM1 - IGNITION MODULE, CYLINDER #1
SCR - STARTER CONTACTOR RELAY
DSW - PCB MOUNTED DIP SWITCH
F1 - FUSE 15 AMP
F2 - FUSE 7.5 AMP
FS - FUEL SOLENOID
SM - STARTER MOTOR 14
85
L.E.D - ALARM INDICATORS
3 - 50 Hz Operation
4 - SPARE
PRINTED CIRCUIT BOARD
1 - 20 Vac Sense Transformer
2 - Remote Not Auto
ON - INDICATES
RED
SM
SC
13
16
ON
86
IC
IC
IC
C1
16
85
86
A
56
SCR
5
4
6
1
2
3
86
18
85
13
0
18
0
16
13
2
J1 86
56
23
239
14
18
15A
66A
194
0
224
15
225
17
4
CONTROL
DSW
132
1617 13 121415 710 9811 3456
4
13
J2
24
18
B
0
16
15
351
14
14
5
1
18
56
86
TB
14
351
18
56 14
13
15
0
14
ENGINE WIRING
14
0
FS
14
0
13
0
224B
14
13
0
225B
BATTERY
CHARGER
225B
224B
14
0
13
0
225
225
225
225
224
224
224
224
15
15
224
224
225
225
0
0
239
239
15A
15A
66A
66A
17
17
23
23
194
194
4
4
0
0
14
14
0
0
225B
225B
224B
224B
13
13
0
0
11
11
CLOSEST TO BEARING
CLOSEST TO BEARING
240V GENERATOR
240V GENERATOR
SWITCH CONTACTOR
SWITCH CONTACTOR
CONNECTION
CONNECTION
OUTPUT TO TRANSFER
OUTPUT TO TRANSFER
4
4
0
0
66
66
77
77
4
4
4
4
0
0
F2
F2
12VDC ACCESSORY SOCKET
12VDC ACCESSORY SOCKET
+
+
17
17
15
15
0
0
0
0
-
-
F1
F1
15B
15B
15
15
15
15
15
15
13
13
13
13
15
15
239
239
17
17
REGULATOR
REGULATOR
VOLTAGE
VOLTAGE
13
13
194
194
23
23
15
15
351
351
66A
66A
13
13
15
15
13
13
0
0
N1
N1
N2
N2
0
0
N1
N1
4
4
66A
66A
N2
N2
15A
15A
23
23
351
351
N2
N2
N1
N1
194
194
0
0
162
162
6
6
0
0
0
0
0
0
66A
66A
6
6
162
162
0
0
MANUAL
MANUAL
SW2
SW2
239
239
AUTO
AUTO
SW1
SW1
1b
1b
1
1
1a
1a
15A
15A
0
0
0
0
0
0
351
351
L
L
G
G
CUSTOMER
CUSTOMER
HOT
HOT
WHITE
WHITE
LINE
LINE
G
G
3
3
5
5
4
4
G
G
GFCI
GFCI
LOAD
LOAD
OUTLET
OUTLET
EXTERNAL
EXTERNAL
1
1
HOT
HOT
WHITE
WHITE
2
2
CB1
CB1
N
N
0
0
0
0
0
0
0
0
G
G
0
0
0
0
0
0
0
0
55
55
0
0
0
0
11
11
23
23
CB3
CB3
L
L
N1
N1
N2
N2
194
194
11
11
11
11
44
44
55
55
C2
C2
3
3
2
2
1
1
66
66
N1
N1
13
13
225B
225B
N2
N2
224B
224B
TX
TX
224
224
225
225
224A
224A
225A
225A
3
3
BCR
BCR
B
B
9
9
6
6
22
22
11
11
14
14
4
4
7
7
A
A
1
1
0
0
22
22
11
11
66
66
77
77
224A
224A
225A
225A
4
4
CB2
CB2
162
162
2
2
6
6
22
22
11
11
2
2
4
4
CONTROL PANEL BOX
CONTROL PANEL BOX
7
7
5
5
6
6
9
9
8
8
10
10
22
22
6
6
2
2
0
0
4
4
N2
N2
N1
N1
NEUTRAL CONNECTION
NEUTRAL CONNECTION
240VAC UTILITY INPUT
240VAC UTILITY INPUT
N
N
22
22
RELAY COIL
RELAY COIL
12Vdc TRANSFER
12Vdc TRANSFER
194
194
33
33
23
23
22
22
44
44
11
11
33
33
55
55
66A
66A
66
66
77
77
BA
BA
STATOR
STATOR
2
1
3
1
2
-+

18 Bryant
77
77
13
13
FIELD
FIELD
DPE WINDING
DPE WINDING
(STATOR)
(STATOR)
CB3 - CIRCUIT BREAKER, EXTERNAL OUTLET, PUSH/PULL
CB3 - CIRCUIT BREAKER, EXTERNAL OUTLET, PUSH/PULL
CB2 - CIRCUIT BREAKER, ALT. EXCITATION
CB2 - CIRCUIT BREAKER, ALT. EXCITATION
SW1 - AUTO / OFF / MANUAL SWITCH
SW1 - AUTO / OFF / MANUAL SWITCH
CB1 - CIRCUIT BREAKER, MAIN OUTPUT
CB1 - CIRCUIT BREAKER, MAIN OUTPUT
HTO - HIGH OIL TEMPERATURE SWITCH
HTO - HIGH OIL TEMPERATURE SWITCH
TX - TRANSFORMER, 16 Vac 56 VA & 16 Vac 1 VA (DUAL SEC.)
TX - TRANSFORMER, 16 Vac 56 VA & 16 Vac 1 VA (DUAL SEC.)
0
0
BCR - BATTERY CHARGE RELAY
BCR - BATTERY CHARGE RELAY
BA - BRUSH ASSEMBLY
BA - BRUSH ASSEMBLY
F1 - FUSE 15 AMP
F1 - FUSE 15 AMP
D - DIODE
D - DIODE
F2 - FUSE 7.5 AMP
F2 - FUSE 7.5 AMP
SP1, SP2 - SPARK PLUGS
SP1, SP2 - SPARK PLUGS
SW2 - SET EXERCISE SWITCH
SW2 - SET EXERCISE SWITCH
SM - STARTER MOTOR
SM - STARTER MOTOR
IM1 - IGNITION MODULE, CYLINDER #1
IM1 - IGNITION MODULE, CYLINDER #1
IM2 - IGNITION MODULE, CYLINDER #2
IM2 - IGNITION MODULE, CYLINDER #2
LOP - LOW OIL PRESSURE SWITCH
LOP - LOW OIL PRESSURE SWITCH
FS - FUEL SOLENOID
FS - FUEL SOLENOID
SC - STARTER CONTACTOR
SC - STARTER CONTACTOR
SCR - STARTER CONTACTOR RELAY
SCR - STARTER CONTACTOR RELAY
DIAGRAM KEY
DIAGRAM KEY
ELECTRONIC
ELECTRONIC
REGULATOR
REGULATOR
VOLTAGE
VOLTAGE
C2-8
C2-8
2
162
162
6
6
4
4
0
0
11
11
22
22
CB2
CB2
C2-10
C2-10
4
4
0
0
22
22
C2-11
C2-11
11
11
0
0
SW2
SW2
PRINTED CIRCUIT
PRINTED CIRCUIT
C2-7
C2-7
C1-6
C1-6
6
6
BA
BA
0
0
0
0
0
0
C2-9
C2-9
0
0
55
55
C2-4
C2-4
CONTROL
CONTROL
BOARD
BOARD
1
1
4
4
3
3
2
2
J2
J2
66A
66A
4
C2-3
C2-3
ENGINE RUN
ENGINE RUN
WINDING
WINDING
(STATOR)
(STATOR)
0
0
66
66
85
85
351
351
C1-4
C1-4
C2-2
C2-2
HTO
HTO
0
0
0
0
17
17
11
11
16
16
17
17
13
13
12
12
15
15
14
14
225
225
15
15
224
224
0
0
194
194
86
86
66A
66A
14
14
3
3
7
7
8
8
9
9
10
10
4
4
5
5
6
6
5
5
J1
J1
1
1
2
2
4
4
66A
66A
23
23
56
56
239
239
15A
15A
194
194
18
18
23
23
C1-3
C1-3
4
4
86
86
0
0
LOP
LOP
14
14
66A
66A
224
224
15A
15A
239
239
13
13
225
225
14
14
15A
15A
23
23
194
194
0
0
224B
224B
BATTERY CHARGE
BATTERY CHARGE
BATTERY
BATTERY
CHARGER
CHARGER
C2-1
C2-1
3
3
1
1
2
2
WINDING
WINDING
13
13
1
1
2
2
225B
225B
11
11
22
22
7
7
77
77
1
1
6
6
66
66
3
3
4
4
224A
224A
7
7
9
9
225A
225A
9
9
BCR
BCR
0
0
14
14
13
13
13
13
0
0
13
13
224A
224A
225
225
225A
225A
224
224
11
11
22
22
CB3
N2
N1
23
194
CB1
EXTERNAL
OUTLET
GFCI
17
194
23
15A
IM1
IM2
17
C1-5
15
0
18
18
D
D
G
18
56
17 15
239
14
SCR
0
0
0
15
23
13
194
15A
17
0
15B
0
F2
239
14
15
13
C1-1
16
0
16
0
SC
0
C2-1
13 F1
15
15
15
15
SP2
SP1
G
SUPPLIED
CUSTOMER
FS
0
14
SM
BLACK
SC
RED
2391515
SW1
BATTERY
12V
N
G
N
11
POWER
(STATOR)
WINDING
N
11
22
11
44
N
33
C2-5
12VDC ACCESSORY SOCKET
TX
56VA
-
13
0
224A
225A
225
224
1VA
15B
+
N1
N2
11
22
N2
C2-6
N1
194 23 11 22
22
240V
L
L
120V
120V
CONNECTIONS
RELAY
240VAC
INPUT
UTILITY
12Vdc
NEUTRAL
COIL
CUSTOMER
Section 4 - Electrical Data
Bryant Air-cooled 7 kW, 12 kW and 15 kW Generators
Electrical Schematic — V-Twin — Drawing No. 0E9017
Other manuals for ASPAS1BBA007
3
This manual suits for next models
2
Table of contents
Other Bryant Portable Generator manuals
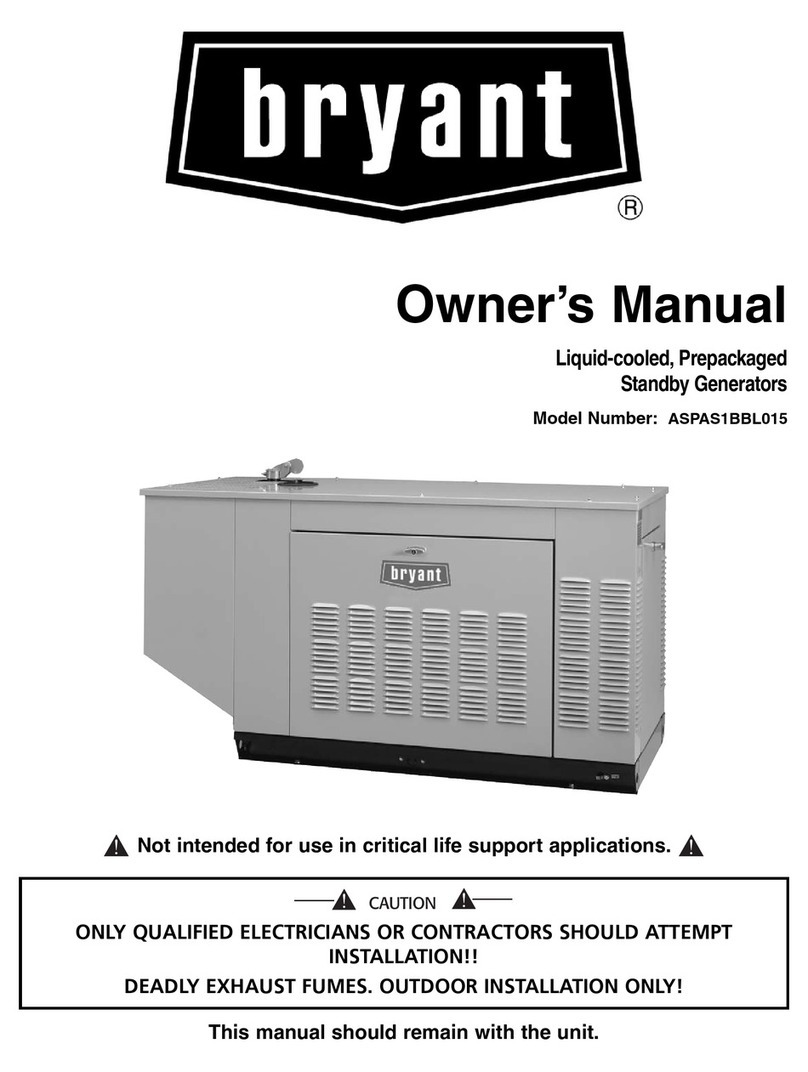
Bryant
Bryant ASPAS1BBL015 User manual
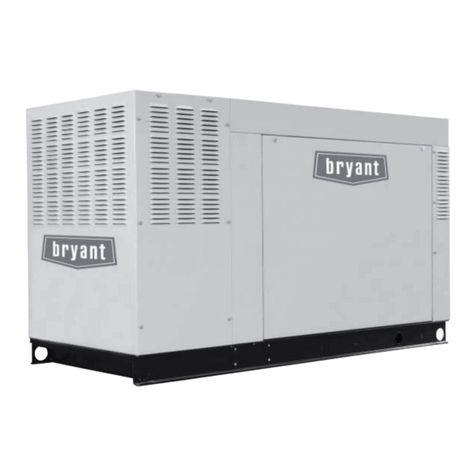
Bryant
Bryant ASPDA1BBL035 User manual
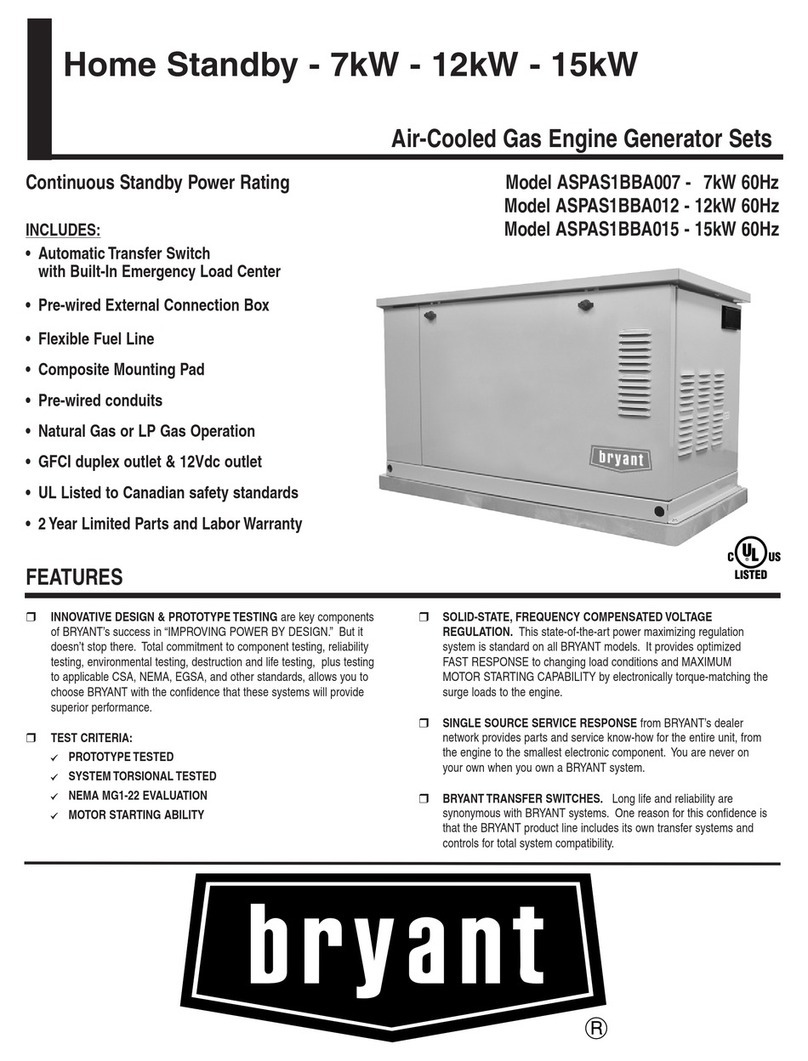
Bryant
Bryant ASPAS1BBA007 User manual
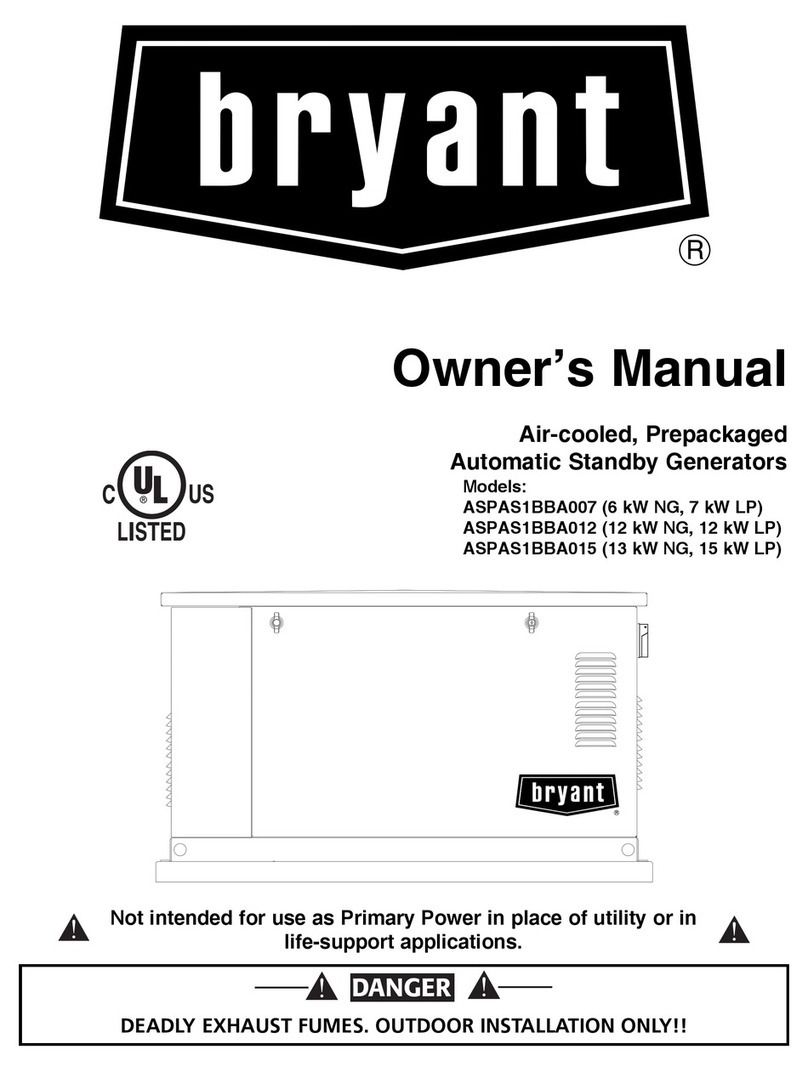
Bryant
Bryant ASPAS1BBA007 User manual
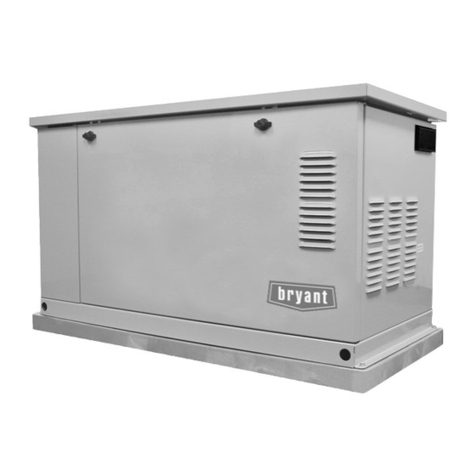
Bryant
Bryant ASPAS1BBA007 Operating instructions
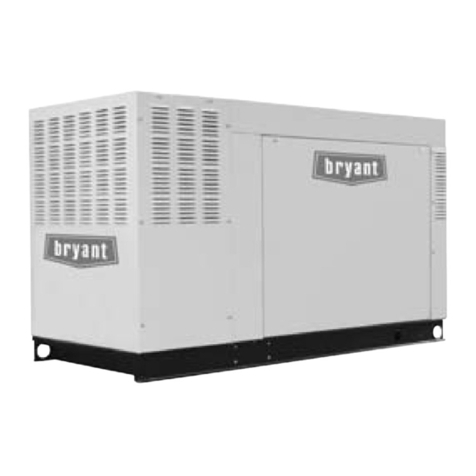
Bryant
Bryant ASPDA1BBL045 User manual
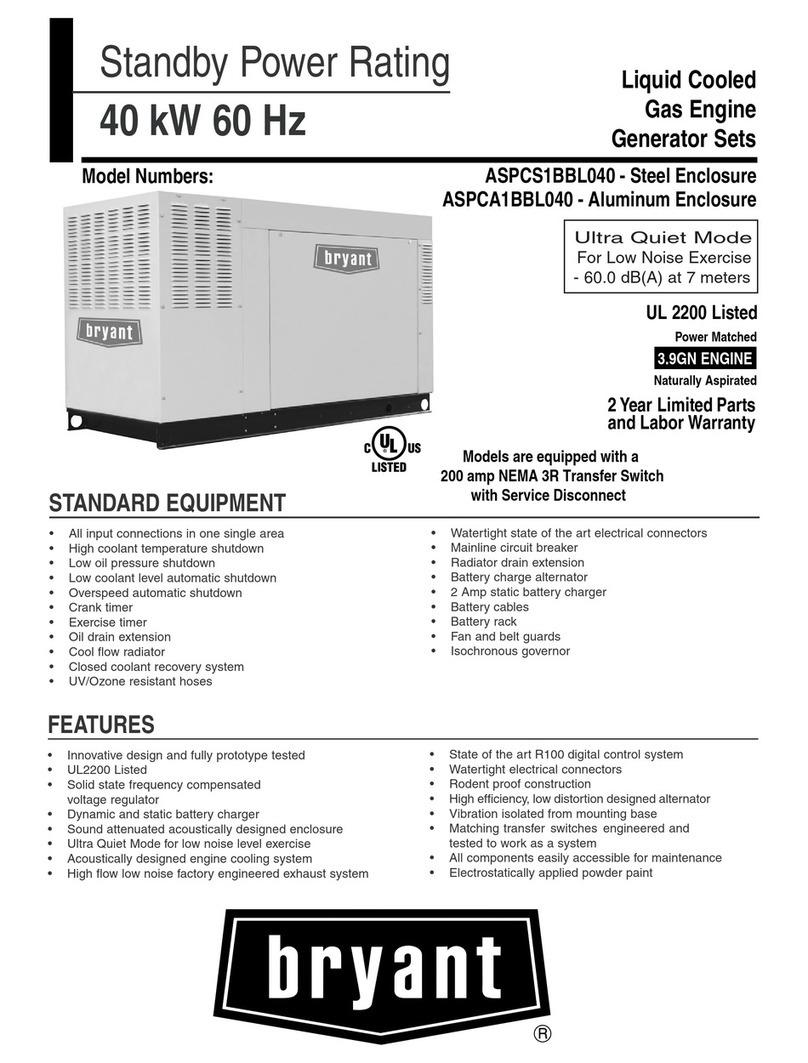
Bryant
Bryant ASPCA1BBL040 User manual
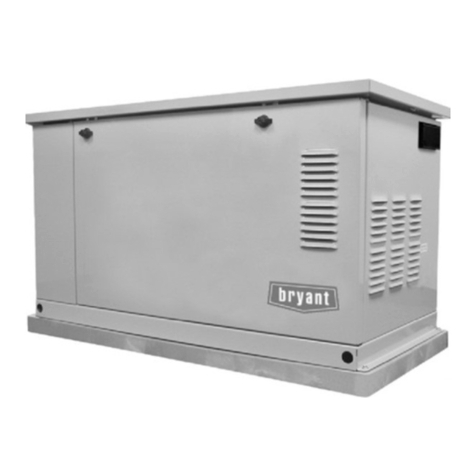
Bryant
Bryant ASPAX1BBA015 Installation instructions