BUG-O BGW-1000 Technical reference manual

INSTRUCTIONS
aNd
PaRTS MaNUaL
aLL TIME GIRTH WELdER
BGW-1000 BGW-2000
a dIVISION OF WELd TOOLING CORPORaTION
280 TECHNOLOGY dRIVE CaNONSBURG, PENNSYLVaNIa 15317-9564 USa
PHONE: 1-412-331-1776 http://www.bugo.com FaX: 1- 412- 331- 0383
Please record your equipment identication information below for future reference. This information can be found
on your machine nameplate.
Model Number
Serial Number
Date of Purchase
Whenever you request replacement parts or information on this equipment, always supply the information you have
recorded above.
LIT-BGW-IPM-1209

SAFETY
PROTECT YOURSELF AND OTHERS FROM SERIOUS INJURY OR DEATH. KEEP CHILDREN
AWAY. BE SURE THAT ALL INSTALLATION, OPERATION, MAINTENANCE AND REPAIR
PROCEDURES ARE PERFORMED ONLY BY QUALIFIED INDIVIDUALS.
EQUIPMENT DAMAGE
POSSIBLE.
ELECTRIC SHOCK can kill.
1) The equipment is not waterproof. Using the
unit in a wet environment may result in
serious injury. Do not touch equipment when
wet or standing in a wet location.
2) The unused connectors have power on
them. Always keep the unused connectors
covered with the supplied protective panels.
Operation of the machine without the
protective panels may result in injury.
3) Never open the equipment without first
unplugging the power cord or serious injury
may result.
4) Verity the customer-supplied power connec-
tions are made in accordance with all
applicable local and national electrical safety
codes. If none exist, use International
Electric Code (IEC) 950.
5) Never remove or bypass the equipment
power cord ground. Verify the equipment is
grounded in accordance with all applicable
local and national electrical safety codes. If
none exist, use International Electric Code
(IEC)950.
READ INSTRUCTIONS.
Read the instruction manual before installing and
using the equipment.
1) Do not plug in the power cord without first the
verifying the equipment is OFF and the cord
input voltage is the same as required by the
machine or serious damage may result.
2)Always verity both the pinion and wheels are
fully engaged before applying power or equip-
ment damage may occur.
3) Do not leave the equipment unattended.
Remove from the worksite and store in a safe
location when not in use.
1) Never try to stop the pinion from moving except
by removing power or by using the STOP
control.
2) Do not remove any protective panels, covers or
guards and operate equipment.
MOVING PARTS can
cause serious injury.
FALLING EQUIPMENT can
cause serious personal injury
and equipment damage.
Faulty or careless user installation is possible.
As a result, never stand or walk underneath
equipment.

PRECAUTIONS:
1) Some plasma or welding cables are strong sources of high frequency interference.
NEVER lay a plasma or welding cable across the controls of the machine.
2) Always physically separate the plasma or welding cable leads from the machine
cables. For example, the plasma or welding cable leads should NEVER be bundled
with a pendant cable or the machine power cord. Maximize the separation between
any machine cables and the plasma or welding cables.
3) Strictly follow the grounding procedures specified for the plasma or welding unit.
NOTE: Some plasma and welding units produce exceptionally large amounts of high
frequency noise. They may require a grounding rod be driven into the earth within six
feet (2 meters) of the plasma or welding unit to become compatible with an automatic
cutting or welding process.
4) If the high frequency is produced using a spark gap, adjust the points so the gap is as
small as possible. The larger the gap, the higher the voltage and the higher the inter-
ference.
5) Some plasma or welding units will inject high frequency interference into theAC
power line. Use separate power line branches whenever possible to power the
plasma or welding source and the machine. Do not plug them into the same outlet
box.
6) High frequency noise may enter the machine through the plasma or welding supply
remote contactor leads. Some plasma and welding sources can produce noise spikes
of up to several thousand volts. These sources are not compatible with automated
cutting and welding equipment. It is recommended that the remote contactor leads on
these plasma or welding sources not be connected to the machine. An alternate
solution is to purchase a separate remote contactor isolation box.
HIGHFREQUENCYWARNINGS
WARNING: HIGHFREQUENCY CAN EFFECT MACHINE
OPERATIONAND THEREFORE, WELD QUALITY.
SPECIAL PRECAUTIONS ARE REQUIRED WHEN USING PLASMA,
TIG OR ANY WELDING PROCESS THAT USES HIGH FREQUENCY
TO STRIKE AN ARC.
Read the precautions below before installing and using the equipment.

4
5 ........... General Description
5 ........... General Description / Single and Double Sided Welding
5 ........... General Description / Welding Process
5 ........... Technical Specifications
6 ........... Key Components
6 ........... Key Components / Main Frame
6 ........... Key Components / Dual Motor Drive
6 ........... Key Components / Welding Gear
7 ........... Key Components / Weld Head Assembly
7 ........... Key Components / Control
10 .......... Key Components / Flux Recovery
10 .......... Key Components / Electrical Cabinet & Power Supply Storage
11 .......... Key Components / Electric Flux Winch
11 .......... Installation andOperations
11 .......... Installation and Operations / Frame Setup
13 .......... Installation and Operations / Master Control Connection
13 .......... Installation andOperations / Installation
14 .......... Installation and Operations / Input Connection
14 .......... Installation and Operations / Operation
15 .......... Installation and Operations / Welding
16 .......... Welding Procedure Guidelines
16 .......... Welding Procedure Guidelines / Joint Design
16 .......... Welding Procedure Guidelines / Typical Welding Parameters
19-20 ..... Troubleshooting
21 .......... Maintenance
22 .......... Girth Welder / Parts List
23 .......... Girth Welder / Exploded View
24 .......... Control Box Assembly / Parts List
25 .......... Control Box Assembly / Exploded View
26 .......... Guide Wheel Assembly / Parts List
27 .......... Guide Wheel Assembly / Exploded View
28 .......... Operations Schematic
29 .......... Wiring Diagram
30 .......... Warranty
TABLE OF CONTENTS PAGE
BUG-OALL TIME GIRTH WELDER
INSTRUCTIONS AND PARTS MANUAL
PAGE

5
GENERALDESCRIPTION
The (BGW) Automatic Girth Welder is a self-propelled machine for horizontal girth (3 o’clock) welding of large
storage tank having 6' – 10.5' (1.8 – 3.2m) high plate courses.
The unit is supported by the shell plates to be welded; the machine has its own welding head, controls, flux belt
assembly and flux recovery unit.
The standard welding equipment integrated is the Lincoln Electric USA submerged arc welding system.
Single and Double Sided Welding
With variations in designs; the Automatic Girth Welder can perform single sided (BGW-1000) or double sided
(BGW-2000) operations.
BGW-1000
The single sided unit, BGW-1000 is the mostcommonly used unit due to its light weight and simplicity. It requires
only one operator.
BGW-2000
Designed with the same principle as BGW-1000, but with an “A” frame that carries one set of weld head on each
side.
One side, referred to as the master, can be used by itself for one side welding.The second side (slave) is hinged
to the top of the master frame and is used when welding two sides.
Theoperatorcan movefreelyfrom oneside of themachine toanotherby climbingupthe ladderon one sideto the
common roof of the double sided machine.
A safety rail is provided at the roof of the main frame for safety purpose.
The BGW-2000 requires two welding power supplies. Each unit has a flux recovery unit and controls.
Welding Process
The BGW-1000 is normally equipped for single wire submerged arc welding.
Typical weld procedure called for a welding travel speed of around 18 in/min (450mm/min), 400A, 28-30V and
WFS of 91'' (2300 mm). Single torch deposition rate is approximately 11 lbs/hr. (5kg/hr.)
TECHNICALSPECIFICATIONS
1. Inputvoltage: 3 phase, 380V±10% (Standard)
* Consult factory for non-standard power input
2. Inputfrequency: 50Hz±5% / 60Hz±5%
3. Operation temperature: 14°F--------+122°F(-10°C--------+50°C); Relative humidity: >90%;
4. Environmentalprotection: IP23 grade: F
5. Tank diameteroperationrange: > 15' (4.5 M)
6. Operation tank shell plate width: 6'-10.5' (1.8-3.2m) [Standard]
Max. 15' (4.5m) [Special]
* Models and specifications subject to change without notice.

6
KEY COMPONENTS
Main Frame
The Main frame of the girth welder is constructed of structural steel and square tube members. The slide square
tube mechanism with locking pins and pin holes is used to adjust the frame height for welding different sizes
of shell plates. The main frame of the girth welder is designed to support 550 lbs (250 kg) of weight, or enough
for two operators.
The frame contains two serrated hardened steel anged drive wheels manually adjusted to ride tank diameters
down to a minimum of 15’ (4.5 m.) The distance between wheel anges is 1.8’’ (45mm) [standard] to accommodate
the shell wall thickness.
The machine frame is equipped with a hand railed operator platform with seat, a ladder provides a means for
operator to climb to the roof and access to the electric ux winch and separator tank for ux rell.
Guide wheel assembly at the lower end of the frame to simplify loading and
unloading the machine on the tank. Canvas curtains offer arc and operator
protection in windy conditions.
Dual Motor Drive
Each single anged drive wheel is driven by an individual SAW motor /
reducer to provide extra tracking force to prevent slipping that could cause
weld defects. Drive motors are enclosed inside the frame top section with
aluminum panel for good weather protection.
Speeds for both motors are electronically synchronized and governed by an
inverter for accurate speed travel.
AC inverter:
1. Single-phase 220VAC input voltage
2. Automatic lift in torsion, 150% lift torsion in 6Hz.
3. Fully programmed & calibrated in factory
4. Soft PWM, running in low noise
5. 15 speed, PID, 4-20 MA input
6. Provides RS-485 communication
Caution: All the inverter drives inside the BGW control are pre-programmed before the girth welder is deliv-
ered to users on site. Please consult factory if re-programming is required.
The SEW motors and reducer requires minimal maintenance with advantages of
low noise & vibration, with 96% high efciency through the reducer. It consists of
a high rigid housing and spur gear; all parts are precisely machined with minimum
tolerance for accurate travel mechanism.
Welding Gear
The standard welding equipment supplied is the Lincoln USA NA3 control and weld
head tted with nozzle, wire feed rolls, wire straightener, and 50lbs (23Kg) wire reels
for feeding up to 3.2 mm (1/8’’) diameter wire.
Lincoln USA DC600 is the standard power supply
for the girth welder. Standard input power is 380V/3ph/50Hz and the line power
requirement is 40kVA. Other voltages and frequencies are available, please
consult factory for details.
Please refer to Lincoln’s NA3 and DC600 Instruction manuals for more informa-
tion on their welding equipment.
Power supplies are installed on a steel storage case with the electrical cabinet
for weather protection.

7
Weld Head Assembly
The BGW weld head is mounted on a manual cross slide system,
which allows the operator complete control of wire placement and
joint tracking.
Due to the lack of visibility of the submerged arc welding process, a
laser pointer is mounted on the nozzle to provide a position reference
for operator while welding.
Control
Welding Control
The Lincoln USA NA3 welding control is normally supplied with the
girth welder. It is mounted on the right hand side of the main frame for
the operator to access easily. Directly on top of the NA3 control is the
BGW master control.
Master Control
The BGW master control houses the electronic travel inverter drive
and associated control relays; it provides a mean of integrated control
of all the accessories of the girth welder (eg. flux vacuum, 220V single
phase aux outlet, lamp, flux winch).
The control panel includes all necessary control knobs and switches
such as the speed control potentiometer, direction switch, full speed
travel switch as well as emergency stop button.
110VAux Version Control System
The Bug-oAll Time BGW sold in the markets using 110V are equipped
withaspecial circuitrytoprovide 110V auxoutletand lamps.The 110V
outlet socket is identified with yellow color instead of blue as in the
standard 220V aux power outlet.

8
“Power source switch”
Turns on the main power of the control.
“Left-Stop-Right” travel direction switch (S1)
Placing the switch in the selected side causes the machine to move in that particular welding direction.
For automatic travel, the travel switch on the NA3 must be in the travel position. To operate manually,
the switch must be in the hand position.
“Speed potentiometer” (R1)
Accurately adjust speed travel speeds (cm/min) of the girth welder. The speed can be monitored at the
control display.
U.S. version of Bug-oAll Time BGW would be programmed to display travel speed in IPM (inch per minute).
Normal / full speed travel switch
Activate girth welder full speed travel when the welding equipment is set to “manual” mode or “off”.

9
“Flux recovery vacuum” switch (S2)
Turns on the power of the vacuum for flux recovery.
Inverter ON/OFF “Lighting switch”
Push button switches to power on / off the inverter. Switch on the hurricane lamp for night operation.
CAUTION: Switching the inverter on and off in Emergency stop short interval could cause damage to
the inverter. It is not recommended to switch on the inverter again for at least three minutes after is it
turned off.
“Lighting switch”
Switch on the hurricane lamp for night operation.
Emergency Stop
Push button stops all electronic functions including welding and travel.
Slave Control (for BGWII double sided model ONLY)
Used at the slave side of the double sided girth welder, it is basically the same as the master control, but without
the function to control the drive system.

10
Flux Recovery
The welding head assembly includes a flux belt mechanism for necessary flux recycling.
The flux belt is made of a heat resistant latex belt that can tolerate up to
250 degree C (480 F) of heat. The belt is mounted on two 6'' (150mm)
diameter rollers, which can be adjusted and positioned by the flux belt
assembly hand wheel.
Thewelding fluxthat fallson the
fluxbeltis extracted bythe suc-
tion hose and is returned to the
flux hopper 176 lbs. (80kg ca-
pacity)mountedontheplatform.
The suction force is created by a 1400W cylindrical vacuum.Amanual
valve is applied between the vacuum and flux recovery system for
necessary vacuum force adjustment.
Heavy Duty Blower Type Vacuum / Filter System
(OPTIONAL)
The Bug-o All Time BGW may be equipped with a heavy duty blower
type vacuum for multi shifts continuous operation. Such vacuum sys-
tems can be configured as follows to suitable various operation re-
quirements:
(a) Separator / Filter mounted on top of the operator platform.
(b) Separator / Filter mounted on frame roof (vacuum system would
move upward along with the roof and drive section of the BGW).
Electrical Cabinet & Power Supply Storage.
The electrical cabinet of the girth welder is inside the power source
storage. It consists of a main circuit breaker at the left to receive the
local 3 phase input (380V / 3ph/ 60Hz as standard) and distribute it to
the power supply and the step down transformer, which in turn steps
down the voltage to 220VAC single phase to the secondary circuit
breaker.
The single phase 220VAC is required by the master control and all
electrical accessories supported by the girth welder.
Flux Recovery System
Flux Feed Nozzle
Small Hopper
Flux Feed Hose
FluxFlowValve
Flux Belt
Flux
Pickup
Nozzle
Must be
Sealed
Flux
Hopper Vent VentVacuum

11
Electric flux winch
A 220VAC power winch is mounted on a “L” post at the roof of the girth welder, it
provides a max. lifting capacity of 375 lbs. (170 kg) to lift welding flux up to 98'
(30m) below the girth welder.
Please refer to the Winch MW170 manual for details.
INSTALLATION AND OPERATIONS
Correct installation and setup is critical to ensure proper operation of the BGW
and welding equipment.
Frame Setup
Remove the machine from the crate. A lifting device capable of lifting 4,409 lbs. (2000 kg) is required. Place a
crane hook to the lifting eye and carefully lift the machine upright.
CAUTION: When lifting the double frame (BGWII), please use the four lifting eyes at the middle of the
double sided frame.
drive wheel and
driven wheel
support belt
and wheel
expansion top
wheel
control
box
NA-3
seat
tooling
box
850

12
Remove the location pins of the four square tube members of the BGW, use the lifting device to adjust the height
of the BGW to the size of the shell plate. Relock the location pins when the appropriate position (pin holes) is
found and apply a locking pin to secure the location pin at the appropriate pin holes on the square tubes.
These pin holes are drilled at an interval of 4'' (100mm).
Set the separator tank on the roof and connect the flux hoses. Extra flux hose line is required to be added to the
installed hose when setting the machine for a higher shell plate. Except the models with flux recovery sys-
tems fixed right on top of the operator platform.
Adjust drive wheels of the travel mechanism to the diameters of the tank, then lock them into position.
Fig. Square tub mechanism
Brief Introduction of Lifting Frame
1. Liftingmechanismadoptsinsideandoutsideannular
tube structure which can complete in adjusting the
length of frame by fixing or releasing location pin.
2. Releasethe holddown screwofthe lower bracketat
first and then take down active floor at holddown.
3. Draw out forelock of location pin and then drop out
location pin.
4. Adjustthelengthoftheframe according to the length
of the shell.
5. Plug into forelock stretch.
6. Install holddown and wind up screw to eliminate
the gap.
Upper Bracket Lift Post
Hold Down
Compressed
Mounting
Bracket
Stretch Stick
Location Pin
Lower Bracket
Forelock
Holddown

13
Once the main frame is setup correctly, mount the cable
hanger (1), safety hand rail (2), flux lifting post (3)
and electric flux winch (4), on the frame roof.
Mount the NA-3 control and master control to the control
mounting plate at the right hand side of the frame.
Master Control Connections
There are nine sets of receptacles (eight sets for some
models) at the side of the control panel, each receptacle is
DIFFERENTandonly canmatewith thecorrect connectors
of the below components:
a) Flux Vacuum
b) Mainpower
c) 110or220VAC/1phauxoutput(forelectricalhandtools
such as a grinder)
d) Laser pointer
e) Lighting
f) NA3on/off
g) Dual motor drive
h) Flux lifting winch
i) Coolingfan
Installation
When all components of the BGW are in place, hook up the
lifting eye at the roof of the BGW with a crane and lift the
frame off the ground, then hang drive wheels on top of the
plate wall and lower it down, so the flanged wheel lands on
top of the shell plate.
Note: For double sided unit (BGWII), operator is required to expand the hydraulic jack above the opera-
tor platform to “open up” the hinged master and slave frame, allowing the opened “A” frame of the
double sided unit to straddle on the shell plate.
While loading, the angle between the lifting cable and the horizon
should not be greater than 60°.
The guide wheels should be extended to the maximum extension
with the hand wheel, and then bolted at the position perpendicular to
the ground surface, it provides a moving support to the frame and
prevents impact between the flux belt systems and the weld head to
the shell plate.
When the BGW frame is secured, straddle on the shell plate, retract
thesupportguide wheelbythe handwheel and boltthe orientation of
the support wheel to the horizontal position.
Theweight oftheBGWframeshouldthenbesupported bytheflanged
metal wheels at the top as well as the flux belt assembly.
The welding power supply is intended to be located on the floor in the center of the storage tank. All of the cables
are run from the power supply to the cable hanger at the roof of the machine frame.
All cable connections are made at this point and the hanger clamp fastened in a way that the connections them-
selves do not feel the strain of the cable weight.
Locate the power supply storage near the center of the tank. The storage case contains the main power distribu-
tion disconnect, distribution transformer, and the welding power supply.
1
23
4
1100
1400

14
Input Connection
WARNING!
Only a qualified electrician should connect the input leads to the BGW-1000. Connections should be made in
accordance with all local and national electrical codes.
Connect the three phase supply line (380V for standard BGW, 240V / 440V for special version) to L1, L2, L3 and
ground to the input lug of the 3-phase circuit breaker inside the electrical cabinet as illustrated to the input supply
connection diagram below.
Connect the output of the 3-phase circuit breaker with the welding power supply input.
The electrical cabinet also consists of a step down transformer and a secondary circuit breaker for 1 phase /
220V input tothe BGW. The BGWsare shipped connectedfor the input voltage specified for thedestination of the
machine in factory.
NOTE: Turn main input power of the machine OFF before performing reconnects procedure. Failure to do so will
result in damage to the machine.
Above:non-standardinput at 240V/3ph/60Hzconnection.
OPERATION
After the BGW frame is securely straddled on the shell plate, extend the guide wheel to support the
weight of the frame and clear the flux belt from the tank wall for welding setup.
Adjust the flux belt surface by manual cross slide and keep it .6''-.8'' (15 – 20 mm) below the weld seam.
Adjust the torch angle and contact tip placement to the appropriate welding position.
When the weld head setup is done, retract the guide wheels assembly and allow the weight of the frame to lean
ontheshell wall viathe flux belt,theflux beltwouldbe pressed tightlybelow the weldseam to preventdropoff the
weldingflux.
Connect the weld and ground cables.
Power up the main switches at the electric cabinet, verify the weld gears and drive system are functioning.
AC240V 3P 60HZ
GND

15
Test all the switches on the master control panel and monitor the LEDs.
NOTE: The BGW master control is powered by 220V/1ph VAC, please check for first time operation.
CAUTION: After switching off the inverter, please wait for at least 3 minutes before switching it on again.
Quick repetitions to switch the inverter on and off could damage the inverter due to the residual volt-
age. Please refer to the inverter manual for details.
Check the flux vacuum is properly powered by the toggle switch at the master control, make sure enough flux is
filled to the flux separator and the correct flux valves of the flux feed / recovery hoses are open.
Test the switches on the wire feeding control (eg. Lincoln NA3) make sure there is wire feed to the nozzle.
As soon as the inverter is powered up, the speed display should indicate the speed preset by the users. User can
test run the BGW at the preset speed and full speed.
NOTE: When the inverter is off, the display should indicate “000” when the frame is not moving.
WELDING
Choose the weld direction by setting the travel switch to left or right, adjust the weld speed according to the
welding procedure. Set NA-3 travel switch to” hand” so the frame would travel without welding.
Settocorrect CV-VV switch positioninside theNAControl.Presetappropriate weldingvoltage /current at theNA-
3 control, then switch NA-3 to “Auto”.
Release the flux valve to allow sufficient amount of flux to drop on the arc start area and cover the wire stick out.
NOTE:Formodels withelectric fluxvalveoption, theflux wouldfeedautomatically whenthe wiretouches thework
when the operator presses “inch down” to feed wire prior welding.
Press “start” pushbutton of the NA3 and the start the weld sequence (wire slowly feeds to the work, the arc
strikes and weld travel begins).
During welding, operator should closely observe if the welding arc is tracking the weld joint, use the laser pointer
as the position indicator and finely adjust the torch position via the manual cross slide if necessary.
When the welding operation is complete, simply press the “STOP” bottom at the NA3 control panel and the BGW
frame would stop traveling with the termination of the welding arc.
NOTE:
* For safety reasons, please power off the system before disconnecting any of the control cables to the
master control.
* In order to increase the consumed life of the flux belt mechanism, user is recommended to extend the support
guide wheels as the mean of support when the BGW is not welding (flux belt must be firmly in contact with the
shell plate during welding operation for flux recovery).
* Excessive suction force would prohibit flux feeding during the welding operation, adjust the vacuum hose
valve if necessary.
If the machine is going to weld in the direction opposite of what it was previously set up for, simply shut down the
manual hose valve at one side and open the hose valve at the other side.

16
WELDINGPROCEDUREGUIDELINES
JointDesign
Typical Welding Parameters (for 3.2mm wire)
Wall Thickness Voltage(V) Amp(A) Travel Speed Torch Angle Shell Course
.4''-.55'' 26-27 320-350 15-17in/min 15°-20° 1st
(10-14 mm) 380-420 (mm/min)
27-29 450-480 19-20in/min 2nd
480-520 (mm/min)
.63''-.71'' 26-27 380-420 15-18in/min 1st
(16-18 mm) 380-450 (mm/min)
27-29 450-480 19-20in/min 15°-20° 2nd
480-520 (mm/min)
28-31 450-520 20-26in/min 3rd
500-650 (mm/min)
26-27 380-420 15-18in/min 1st
380-450 (mm/min)
27-29 450-480 19-20.5 in/min 15°-20° 2nd
.79''-.87'' 480-520 (mm/min)
(20-22 mm) 28-31 450-520 20-26in/min 3rd
480-520 (mm/min)
28-31 470-520 22-26 (in/min) 4th
550-650 (mm/min)
26-27 380-420 15-18 (in/min) 1st
380-450 (mm/min)
.95''-1.26'' 27-29 450-480 19-20 (in/min) 15°-20° 2nd
(24-32 mm) 480-520 (mm/min)
28-31 450-520 20-26 (in/min) 3rd
500-650 (mm/min)
28-31 480-520 22-26 (in/min) 4th & up
550-650 (mm/min)
Note: The serviceability of a product or structure utilizing the information in these guidelines must be the sole
responsibly of the builder. Many variables in design, fabrication and service conditions affect the results obtained
in applying this type of information.
blunt side 2-3 mm
gap: 0mm
2/38
8
45°- 50°
45°- 50°

17
WELDINGPROCEDUREGUIDELINES,CONTINUED
Wire Diameter F2.4mm; F = Front; B = Back
WTδδ
δδ
δ=12 Current(A) Voltage(V) Travel Speed
F(1) .5'' (12mm) 380~400 25~26 20~24 in/min
50~60 cm/min
B(1) .5'' 12mm 360-380 25~26 20~24 in/min
50~60 cm/min
F(1) .5'' 12mm 400 26 22~26 in/min
55~65 cm/min
B(1) .5'' 12mm 380 25 22~26 in/min
55~65 cm/min
F(1) .5'' 12mm 380 25 26~28 in/min
65~70 cm/min
B(1) .5'' 12mm 380 25 26~28 in/min
65~70 cm/min
F(1) .5'' 12mm 360 24~25 28~30 in/min
70~75 cm/min
B(1) .5'' 12mm 350 24~25 28~30 in/min
70~75 cm/min
A) Shell Wall Thickness .4'' (10mm)
WTδδ
δδ
δ=10 Current(A) Voltage(V) Travel Speed
F(1) .4'' 10mm 360~380 25~26 28~30 in/min
70~75 cm/min
B(1) .4'' 10mm 360 26 28~30 in/min
70~75 cm/min
F(2) .4'' 10mm 380 24~25 30~31 in/min
75~80 cm/min
B(2) .4'' 10mm 360 24~25 30~31 in/min
75~80 cm/min
F(3) .4'' 10mm 350 25 31~33 in/min
80~85 cm/min
B(3) .4'' 10mm 320 24 31~33 in/min
80~85 cm/min
4
3

18
WELDINGPROCEDUREGUIDELINES,CONTINUED
B) Shell Wall Thickness .3'' (8mm)
WTδδ
δδ
δ=8 Current(A) Voltage(V) Travel Speed
F(1) .3'' (8mm) 320 24 31~33 in/min
80~85 cm/min
B(1) .3'' 8mm 300 23 31~33 in/min
80~85 cm/min
F(2) .3'' 8mm 300 24 33~37 in/min
85~95 cm/min
B(2) .3'' 8mm 280 24 33~37 in/min
85~95 cm/min
Note: The serviceability of a product or structure utilizing the information in these guidelines must be the sole
responsibly of the builder. Many variables in design, fabrication and service conditions affect the results obtained
in applying this type of information.

19
TROUBLESHOOTING
Problems Possible Causes RecommendedAction
Improper control or feeding Lincoln welding control or power supply 1.Check all fuses.
of welding wire. is abnormal. 2.Check Lincoln control switch is
“on”and polarity switch on the
power supplies must be in “+” or “-“.
3.Review Lincoln service manuals
and diagnose possible PCBs
failures.
The indication light of the 1. Power supply is off. 1.Turn on power supply.
master control fails to ignite. 2. 3 pin control cable connector is 2. Check 3 pin connector.
loose.
3. 3 pin control cable is bad. 3. Check 3 pin control cable.
Flux vacuum cannot operate. 1. Bad vacuum relay in the control. 1. Replace control relay/switch.
2. Vacuum itself is faulty. 2.Replace flux vacuum.
Lamp is off. 1. Bad lighting relay in the control. 1.Replace relay/switch.
2. Control cable is loose or bad. 2.Check control cable & connector.
3. Light bulb is bad. 3.Replace light bulb.
Electric winch does not work. 1. Control cable is loose or bad. 1.Check control cable & connector.
2. Winch failure. 2.Replace winch.
Main frame cannot travel. 1. Bad travel direction switch. 1.Replace switch.
2. Bad speed potentiometer. 2. Replace potentiometer.
3. Bad travel control relay . 3. Replace relay.
4. Incorrect inverter setting. 4. Check inverter setting *
5.Faultyinverter. 5. Replace inverter

20
TROUBLESHOOTING,CONTINUED
Problems Possible Causes RecommendedAction
Main frame travels at 1. Welding control faults. 1. Check welding control.
manual mode but not
under auto mode. * Please refer to Lincoln NA3
for details.
Vacuum fails to recover flux. 1. Both flux valves are open. 1.Close one of the valves.
2. Flux separator is open 2.Close separator lid.
3.Air leak at the flux hoses. 3.Repair or replace flux recovery
hose.
4. Flux valves are incorrectly adjusted. 4.Adjustflux valves.
5. Vacuum is blocked. 5.Check vacuum.
Nofluxfeeding 1. Flux inlet valve is too close. 1.Adjust and openupfluxvalve.
2. Flux hose leakage. 2.Repair or replace flux recovery
hose.
Insufficient amount of flux 1. Suction nozzle is too far from the 1.Adjust suction head position.
is recovered. weld.
2.Wrong flux suction nozzle setup. 2.Adjust suction head angle.
Flux belt is burnt by slag. 1. Flux support belt too close to the 1. Adjust the distance to .6''-.98''
weld seam. (15–25mm).
2. Weld travel is off. 2.Switch on weld travel.
Note: The electrical circuitry of the YS-BGW is straightforward and can usually be traced through by a local
electrician using the electrical schematic diagram included in this manual.
Consult the factory if all the above measures fail to resolve the problem.
This manual suits for next models
1
Table of contents
Other BUG-O Welding System manuals
Popular Welding System manuals by other brands

Lincoln Electric
Lincoln Electric AIR VANTAGE IM10066 Operator's manual
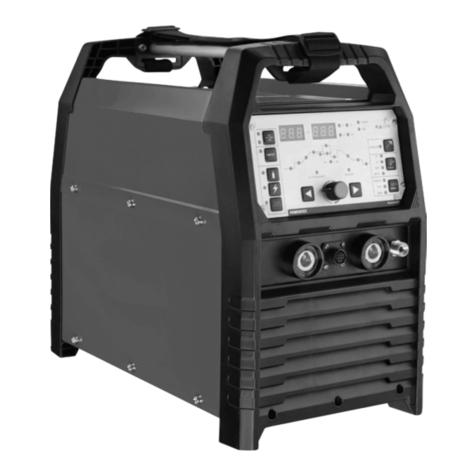
Power first
Power first SMART TIG AC/DC-200P user manual
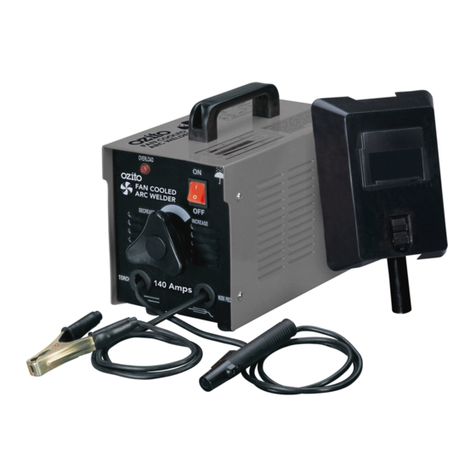
Ozito
Ozito AWG-964 Operation manual
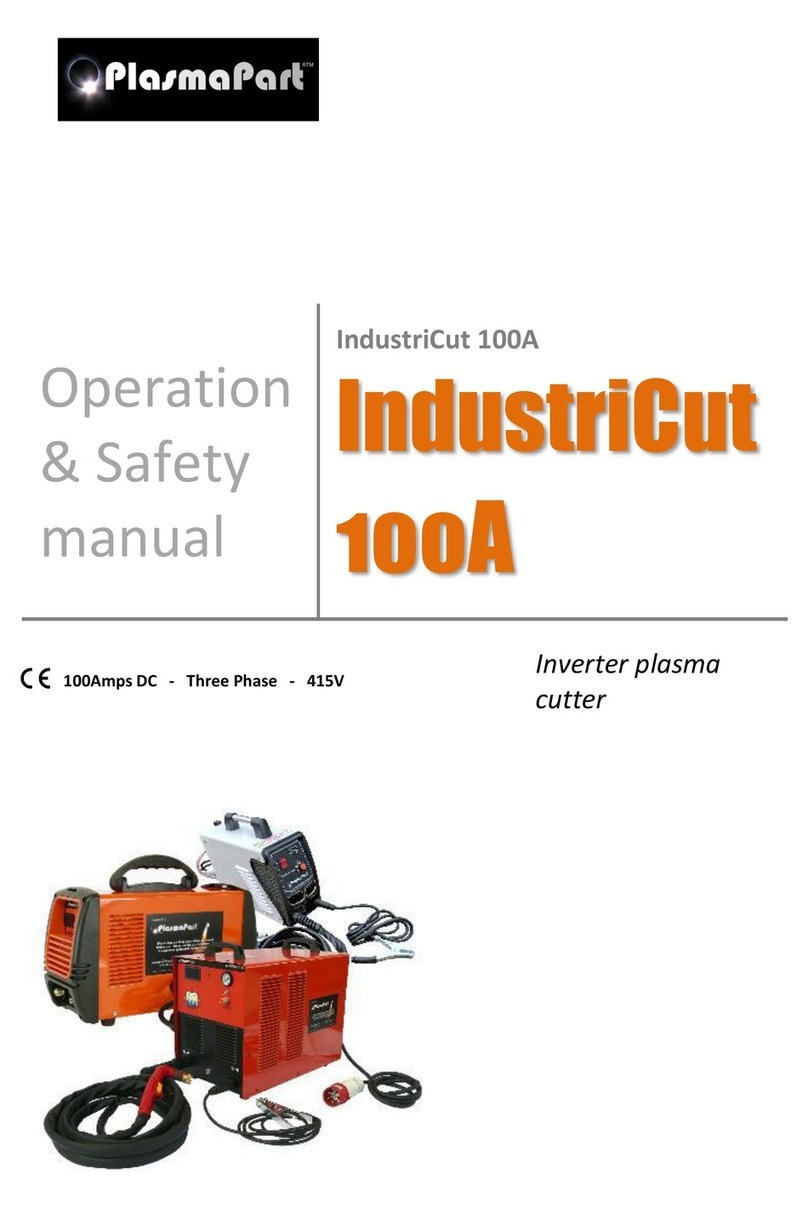
PlasmaPart
PlasmaPart IndustriCut 100A Operation & safety manual
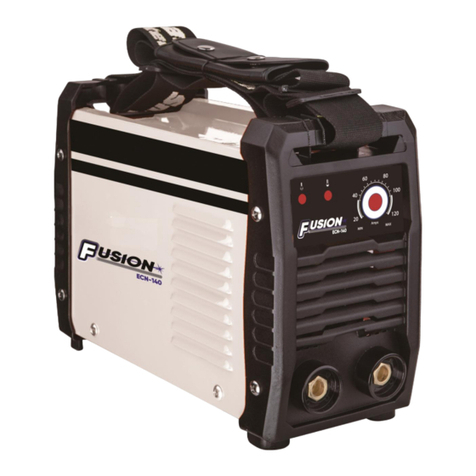
Autojack
Autojack ECN-140 Original instructions
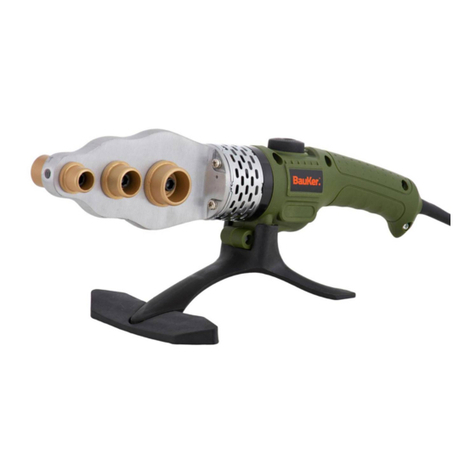
BAUKER
BAUKER PWM800-2 instruction manual
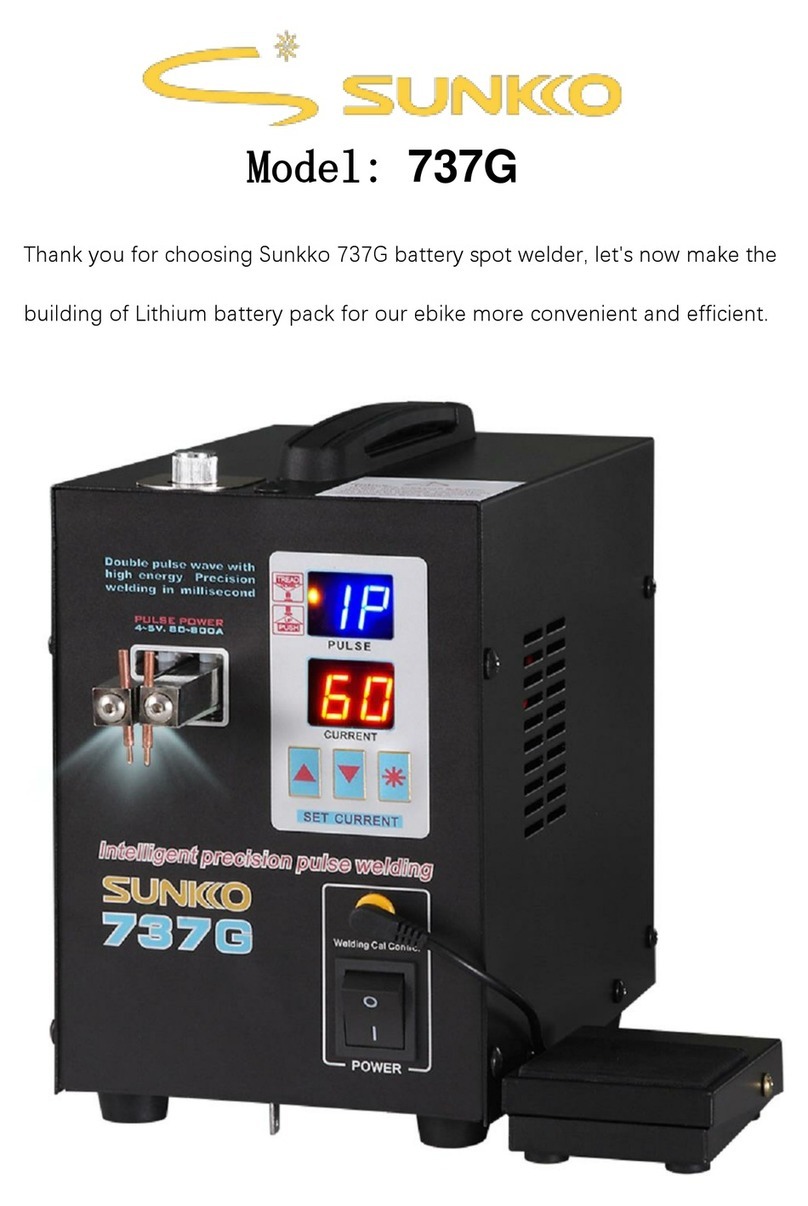
Sunkko
Sunkko 737G manual
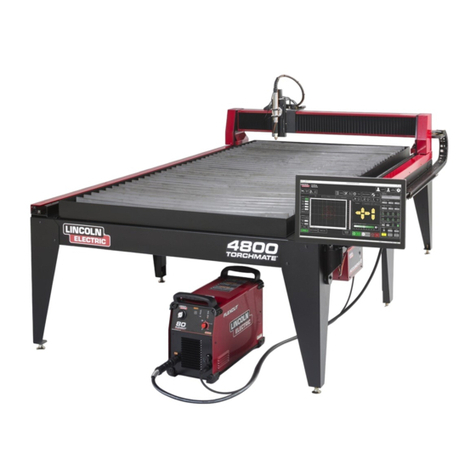
Lincoln Electric
Lincoln Electric Torchmate Flexcut 80 instructions

SHARKS
SHARKS MMA-160A Instruction for operation and maintenance
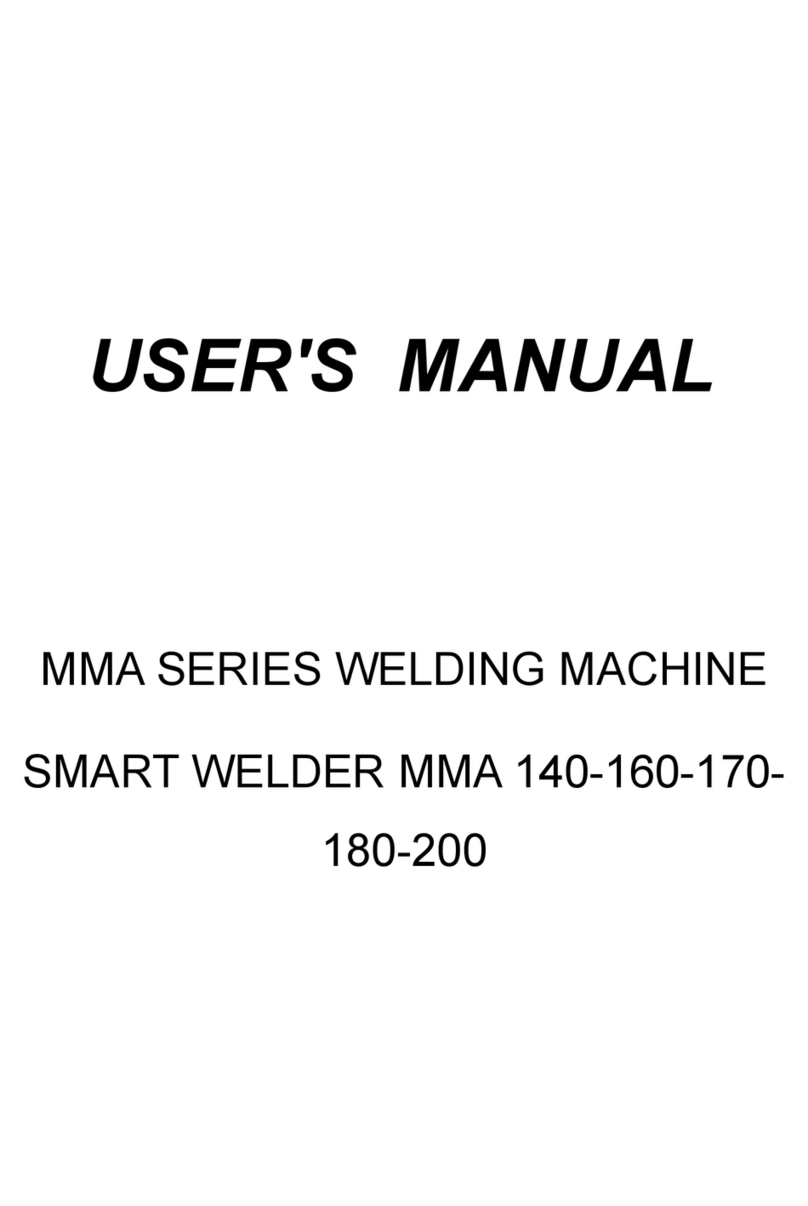
Ter Welding
Ter Welding Smart Welder MMA 140 user manual

Lincoln Electric
Lincoln Electric VANTAGE 300 IM992 Operator's manual
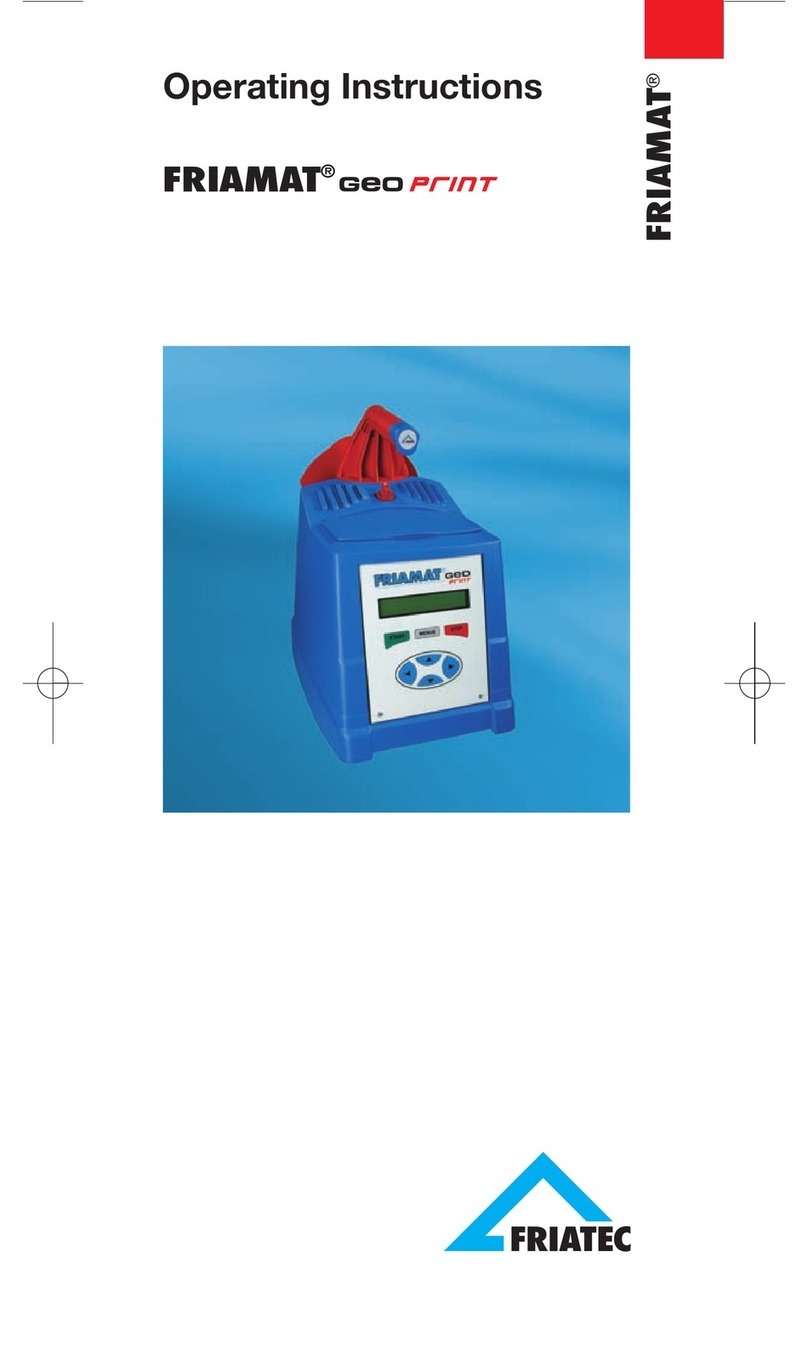
FRIATEC
FRIATEC FRIAMAT GEO PRINT operating instructions