Burger & Brown SMARTFLOW SWAP SPV8 User manual

Form #SF-122 (11.20)
4500 E 142nd Street • Grandview, MO 64030
Tel. (816) 878-6675 • www.smartow-usa.com
SWAP®VAlVe
Installation and Operating Instructions
Applies to: SPV8 and SPV16
General
The Smartow SWAP Valve is a simple, manually
selectable device that supplies cooling water to the mold
during processing, or air to purge the water from the
mold before a mold change.
The SWAP Valve has three positions: WATER, PURGE
and VENT. The WATER position is selected for normal
processing. The PURGE position is selected to evacuate
the water before mold change. The VENT position is
selected to bleed-o trapped pressure and drain residual
water before a mold change.
An optional spring-loaded locking pin is available to
prevent accidental movement of the valve handle.
Assembly (as required)
1. Apply thread locking compound (Loctite 638 or
equivalent) to threaded end of valve handle. Screw
valve handle into the center disk threaded hole. See
figure 1.
2. Install mounting brackets (included) into desired
hole locations using included mounting screws.
3. Thread manual vent into the hole as shown in
figure 1. (No additional thread sealant is required.)
Mounting
Bracket
Water Inlet
Valve Handle
Center Disk
Threaded
Hole
Air/Water
Outlet
(back side)
Optional
Locking Pin
3/8"NPT(F)
Air Inlet
Manual Vent
Figure 1

2
SWAP Valve Instructions
burger & brown engineering, inc. www.smartflow-usa.com
Operation
The SWAP Valve should be mounted to a suitable
surface using the two standard angle mounting brackets
that are mounted to the valve base.
Line mounting to rigid water pipe in lieu of
bracket mounting is discouraged.
Connect water supply to the 1 or 2-inch NPT(F) Water
Inlet.
Connect shop air to the 3/8-inch NPT(F) Air Inlet with
either a permanent or quick-connect tting.
Connect the 1 or 2-inch NPT(F) Air-Water Outlet to the
cooling water Supply manifold.
Install the check valve (included) in the return water
line downstream from the Return water manifold
as shown in Figure 2. The check valve will prevent
water from back-owing into the mold after purging.
Depending on your installation, it may be desirable to
add a check valve to the air inlet ahead of the SWAP
Valve.
In closed loop systems, air separator installation is
recommended to bleed o residual air introduced by the
SWAP Valve. See gure 2.
Supply
Water In
Air In
Supply
Water Return
Check
Valve
(Included)
Return Manifold
Supply Manifold
Injection
Mold
Vent
SWAP
Valve
Optional Air
Check Valve
(not included)
Taco®
Air Separator
Figure 2
Recommended Closed Loop Installation
with Air Separator
Supply
Water In
Air In
Supply
Water Return
Check
Valve
(Included)
Return Manifold
Supply Manifold
Injection
Mold
Vent
SWAP™
Valve
Optional
Mold
Heater
Mold Heater Bypass
Temporary Hose
Quick-Disconnect
and Ball Valve
Quick-Disconnect
and Ball Valve
Optional Air
Check Valve
(not included) Figure 3
Alternate Closed Loop Installation
without Air Separator
C
B
Max.
Height
Max. Operating Width ADMax.
Manual Vent
with Drain [10-32(F)]
(typ.)
Water
Outlet
3/8"NPT(F)
Air Inlet
Water Inlet
WATER PURGE
VENT
Dimensions
Figure 4
Dimension SPV8 SPV16
A295mm/11.6" 395mm/15.5"
B221mm/8.7" 297mm/11.7"
C119mm/4.7" 173mm/6.8"
D130mm/5.1" 160mm/6.3"

3
SWAP Valve Instructions
burger & brown engineering, inc. www.smartflow-usa.com
Using a Smartflow Mold Temperature Regulator (MTR)
1. Stop the press.
2. Note the setting on the calibration scale, then move the knob to the "Flush" position (clockwise to the stop).
3. Perform the SWAP Purge Procedure (see OPERATION above).
4. On the MTR, return the knob on the calibration scale to the previous position. (It will be necessary to rotate the knob more than
one complete turn counterclockwise.)
5. Select WATER after the new mold is installed and the cooling water connections are secure.
Using a TCU (Temperature Control Unit in a closed loop system)
We recommend using a temporary bypass hose or TACO Air Separator per diagrams on page 2. Install bypass hose and open ball
valves on each end of the bypass before purging the mold (figure 3). An air separator may be installed in the location shown at the
highest point possible (figure 2). your installation may vary.
1. Stop the press.
2. Check the TCU manufacturer's instruction for Purge position or Bypass instructions.
3. Perform the SWAP Purge Procedure (see OPERATION above).
4. Reset the TCU to the original operating configuration.
5. Selecter WATER after the new mold is installed and the cooling water connections are secure.
For Normal
Processing
Select WAT ER .
Cooling Water is available to the
Supply manifold. Purge Air is
blocked.
To Evacuate
Cooling Water
See Note Below
Select PURGE.
Purge Air is available to the
Supply manifold. Cooling Water
is blocked.
To Bleed-O
Trapped Pressure
and Drain
Residual Water
Select VENT.
Press Manual Vent-Drain Valve.
Purge Air is blocked. Cooling
Water is blocked.
A
89 mm
3.5 in
SWAP
Valve
dia
clearance for
1/4-20 bolts
7.1 mm
.28 in
Figure 5
Mounting Bracket Hole Pattern
Dimension SPV8 SPV16
A99mm/3.9" 126mm/4.9"
Note: it is possible for the majority of the purge air to rush through the unrestricted water passages, leaving some water
in bubblers or baffles. After unrestricted mold passages have been purged, close valves on these passages so more
air is available to purge the restricted water passages. it may be necessary to purge longer or to purge restricted
passages individually to completely evacuate the water.
Caution: Confirm that the SWAP Valve is selected to VENT and that the manual vent button has been pressed to relieve
trapped air pressure or residual water before disconnecting any water lines. A drain tube can be connected to
the Manual Vent-Drain and run to a suitable drain.

4
SWAP Valve Instructions
burger & brown engineering, inc. www.smartflow-usa.com
Troubleshooting
Symptom Corrective Action
Air or water does not flow through the system • Verify check valve direction
• Check that the valve handle is in the correct position
Water leaks from the valve while in operation • Replace O-Rings (Contact the factory for repair or field replacement
procedure)
Mold does not evacuate completely • Check air pressure (80 to 125 psi required)
Replacement/Additional Parts
Description SPV8 (1-inch) SPV16 (2-inch)
O-ring Set......................................................... PVOSET-100A PVOSET-200A
Valve Handle Knob..........................................PVKB-100-A PVKB-100-A
Mounting Brackets (2 required per valve) .......PVB-100-A PVB-100-A
Air Check Valve 3/8" .......................................PVCV-3-A PVCV-3-A
Return Check valve.......................................... PVCV-100-A PVCV-200-A
Manual Vent.....................................................S15-2532-A S15-2532-A
This manual suits for next models
3
Popular Control Unit manuals by other brands

Taylor Valve Technology
Taylor Valve Technology 8200 Series user manual
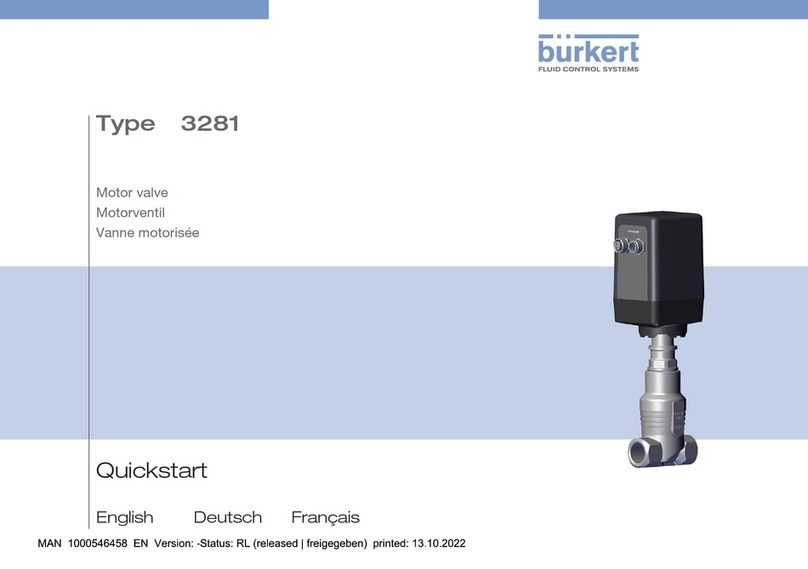
Burkert
Burkert 3281 quick start

Leonard
Leonard TM-1520A-DT INSTALLATION ADJUSTMENT SERVICE
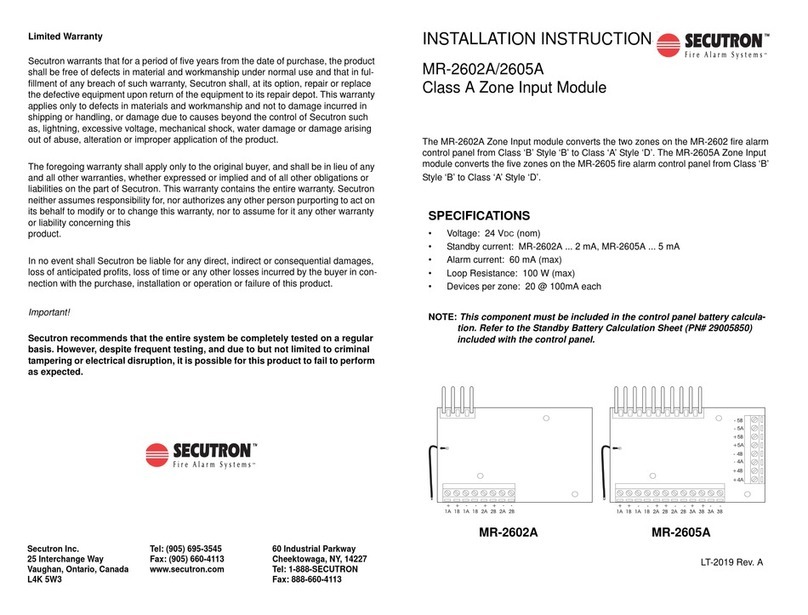
Secutron
Secutron MR-2602A Installation instruction
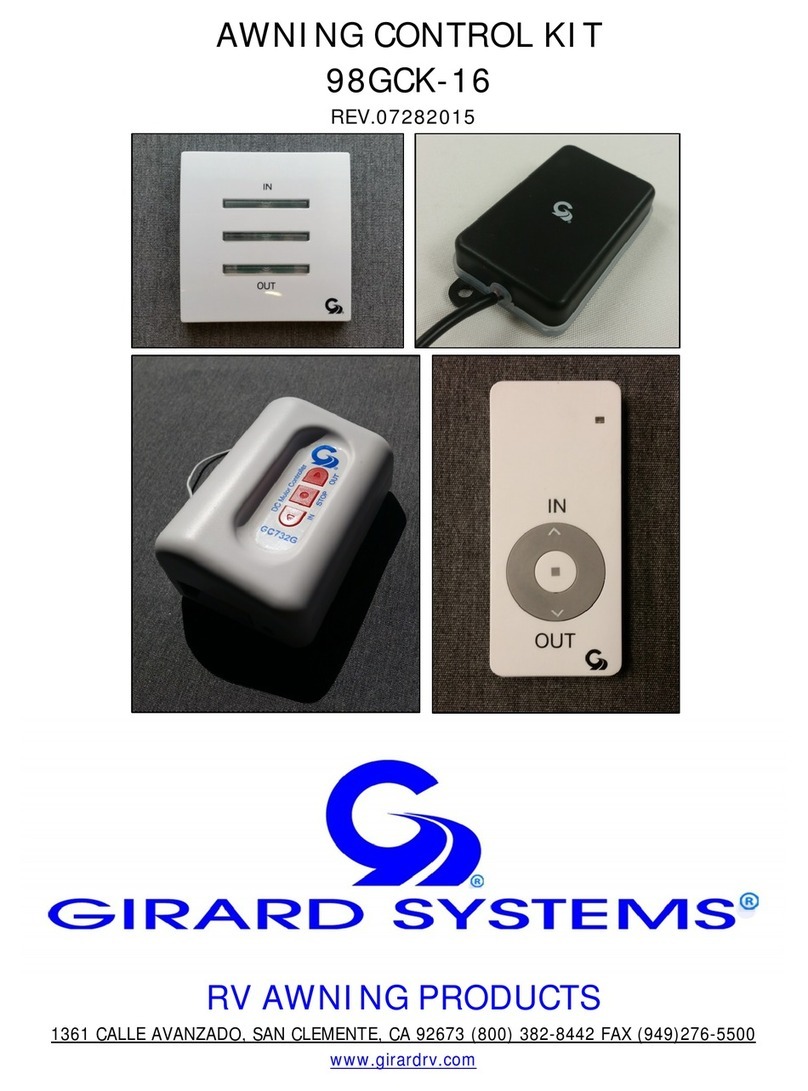
Girard Systems
Girard Systems 98GCK-16 manual
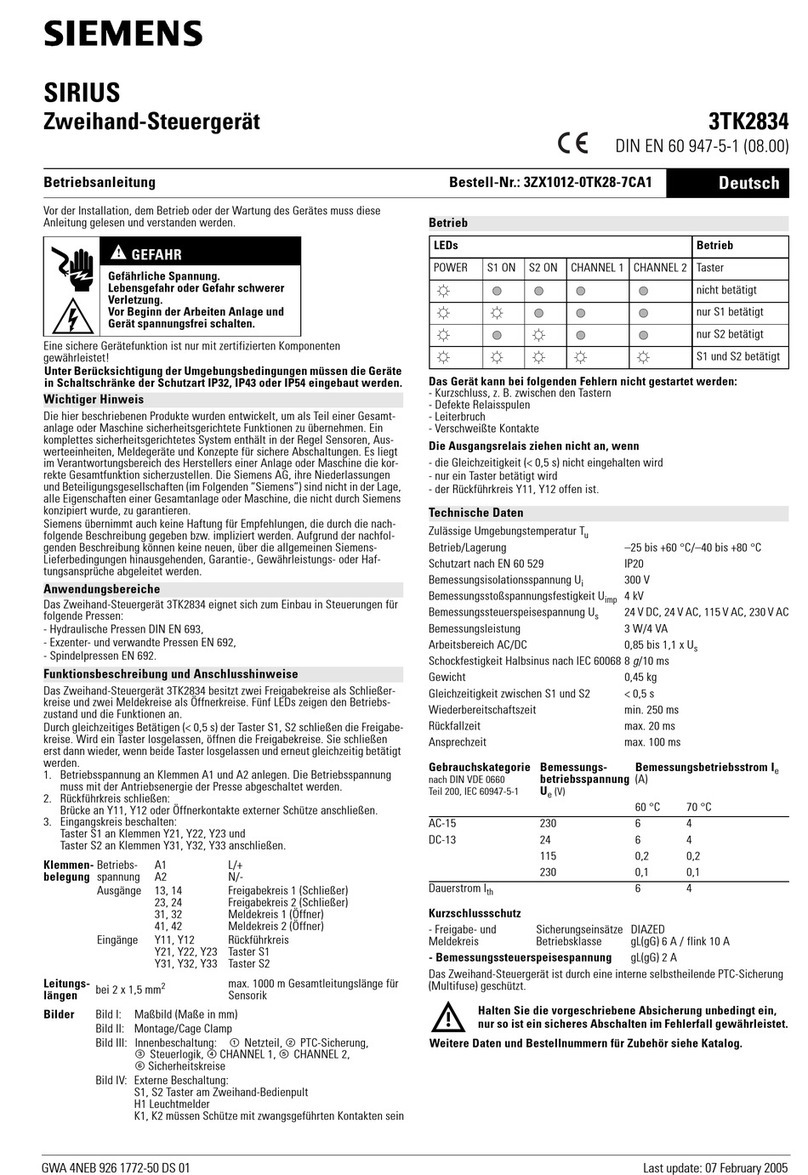
Siemens
Siemens SIRIUS 3TK2834 operating instructions