BW Technologies Micro Clip XT User manual

1, 2, 3, and 4-Gas Detector
Operator Manual

1
GasAlertMicroClip
Introduction
The operator’s manual provides basic information for the
GasAlertMicroClip XT and XL. For complete operating
instructions, refer to the GasAlertMicroClip Technical Reference
Guide provided on the CD-ROM. The GasAlertMicroClip (“the
detector”) warns of hazardous gas at levels above user-defined
alarm setpoints. The detector is a personal safety device. It is
your responsibility to respond properly to the alarm.
Note
The detector is shipped with English as the default
displayed language. Additional languages provided are
Portuguese, Spanish, German, and French. The screens
for the additional languages are displayed on the detector
and in the corresponding operator s manuals.
Zeroing the Sensors
To zero the sensors, refer to steps #1-3 in Calibration on page 7.
ec Warning
This instrument contains a lithium polymer battery.
Dispose of lithium cells immediately. Do not disassemble
and do not dispose of in fire. Do not mix with the solid
waste stream. Spent batteries should be disposed of by a
qualified recycler or hazardous materials handler.

GasAlertMicroClip
Operator’s Manual
2
Safety Information - Read First
Use the detector only as specified in this manual and the
reference guide, otherwise the protection provided by the
detector may be impaired. Read the following cautions before
using the detector.
aCautions
•Warning: Substitution of components may impair
Intrinsic Safety.
• Caution For safety reasons, this equipment must be
operated and serviced by qualified personnel only.
Read and understand the user manual completely
before operating or servicing.
• Charge the detector before first time use. BW
recommends the detector be charged after every
workday.
• Before using the detector, refer to Sensor Poisons and
Contaminants.
• Calibrate the detector before first-time use and then on
a regular schedule, depending on use and sensor
exposure to poisons and contaminants. BW
recommends calibrating at least once every 180 days
(6 months).
• The combustible sensor is factory calibrated to 50%
LEL methane. If monitoring a different combustible gas
in the %LEL range, calibrate the sensor using the
appropriate gas.
• Only the combustible gas detection portion of this
instrument has been assessed for performance by
CSA International.
• Calibrate only in a safe area that is free of hazardous
gas and in an atmosphere of 20.9% oxygen.
• It is recommended that the combustible sensor be
checked with a known concentration of calibration gas
after any exposure to contaminants/poisons such as,
sulfur compounds, silicon vapors, halogenated
compounds, etc.
• BW recommends to bump test the sensors before each
day’s use to confirm their ability to respond to gas by
exposing the detector to a gas concentration that
exceeds the alarm setpoints. Manually verify that the
audible and visual alarms are activated. Calibrate if the
readings are not within the specified limits.
• Caution High off-scale readings may indicate an
explosive concentration.
• Any rapid up scaling reading followed by a declining or
erratic reading may indicate a gas concentration
beyond the upper scale limit, which can be hazardous.
• Extended exposure of the GasAlertMicroClip to certain
concentrations of combustible gases and air may stress
a detector element that can seriously affect its

GasAlertMicroClip
performance. If an alarm occurs due to a high
concentration of combustible gases, calibrate the
detector. If necessary, replace the sensor.
• Protect the combustible sensor from exposure to lead
compounds, silicones, and chlorinated hydrocarbons.
• Sensor exposure to certain organic vapors (such as
leaded gasoline and halogenated hydrocarbons) may
temporarily inhibit sensor performance. After exposure,
a bump test or calibration is recommended.
• For use only in potentially explosive atmospheres
where oxygen concentrations do not exceed 20.9%
(v/v).

GasAlertMicroClip
Operator’s Manual
6
Parts of the GasAlertMicroClip
8
6
9
4
5
3
7
10
11
2
2
1
2
Item Description
1 IntelliFlash
2 Visual alarm indicators (LEDs)
3 Alligator clip
4 Charging connector / IR interface
5 Pushbutton
6 Carbon monoxide (CO) sensor
7 Hydrogen sulfide (H2S) sensor
8 Oxygen (O2) sensor
9 Combustible (LEL) sensor
10 Audible alarm
11 Liquid crystal display (LCD)

GasAlertMicroClip
Display Elements
7
Display Elements
1
8
7
6
54
3
2
Item Description
1 Alarm condition
2 Automatically zero sensor
3 Numeric value
4 Stealth mode
5 Battery life indicator
6 Gas identifier bars
7 Gas cylinder
8 Automatically span sensor

GasAlertMicroClip
Operator’s Manual
8
Pushbuttons
Pushbutton Description
C
• To activate the detector, press C.
• To deactivate the detector, press and hold Cuntil the OFF countdown is complete and the LCD deactivates
• To view the TWA, STEL, and MAX (maximum) readings, press Ctwice. To clear the TWA, STEL, and MAX
readings, press Cwhen the LCD displays RESET.
• To initiate calibration, deactivate the detector. Press and hold Cwhile the detector performs the OFF
countdown. Continue holding Cwhile the LCD briefly deactivates and then begins the CAL countdown.
Release Cwhen the CAL countdown is complete.
• To activate the backlight while in normal operation, press C.
• To acknowledge latched alarms, press C.
• To acknowledge a low alarm and disable the audible alarm, press C(if the Low Alarm Acknowledge option
is enabled).

GasAlertMicroClip
Sensor Poisons and Contaminants
9
Sensor Poisons and Contaminants
Several cleaners, solvents, and lubricants can contaminate and
cause permanent damage to sensors. Before using cleaners,
solvents, and lubricants in close proximity to the detector
sensors, read the following caution and table.
aCaution
Use only the following BW Technologies by Honeywell
recommended products and procedures
• Use water based cleaners.
• Use non-alcohol based cleaners.
• Clean the exterior with a soft, damp cloth.
• Do not use soaps, polishes, or solvents.
Below are common products to avoid using around sensors.
Cleaners and Lubricants
• Brake cleaners
• Lubricants
• Rust inhibitors
• Window and glass cleaners
• Dishsoaps
• Citrus based cleaners
• Alcohol based cleaners
• Hand sanitizers
• Anionic detergents
• Methanol (fuels and antifreezes)
Silicones
• Silicone cleaners and protectants
• Silicone based adhesives, sealants, and gels
• Hand/body and medicinal creams containing silicone
• Tissues containing silicone
• Mold releasing agents
• Polishes
Aerosols
• Bug repellents and sprays
• Lubricants
• Rust inhibitors
• Window cleaners

GasAlertMicroClip
Operator’s Manual
10
Calibration
Procedure Display Procedure Display
aCaution
Calibrate only in a safe area that is free of
hazardous gas in an atmosphere of 20.9%
oxygen.
1. Press and hold Cas the detector
performs the OFF countdown. Continue
holding Cwhen the LCD briefly
deactivates.
4. When is displayed and
flashes, connect the gas cylinder (refer to
page 11) and apply gas at a flow rate of
250 to 500 ml/min.
After a sufficient amount of gas has been
detected (approximately 30 seconds), the
detector beeps and flashes
while the detector completes the
calibration.
2. The LCD then activates again and
performs the CAL countdown. Continue
holding Cuntil the countdown is complete
to enter calibration.
5. The LCD displays CAL DUE. Next, a
screen displays showing the number of
days remaining before calibration is due
for each sensor. The LCD then displays
the earliest calibration due date, as some
sensors require more frequent
calibrations.
3. flashes while the detector
zeroes all of the sensors and calibrates the
oxygen sensor. If a sensor fails to auto
zero, it cannot be calibrated. When auto
zero is complete, the LCD displays APPLY
GAS.
Note Only use the calibration cap during the calibration
span process and for bump tests.
Wind currents may cause false readings and poor calibrations.
Do not calibrate the detector during or immediately after
charging is complete.

GasAlertMicroClip
Attach the Gas Cylinder to the Detector
11
Attach the Gas Cylinder to the Detector

GasAlertMicroClip
Operator’s Manual
12
Bump Test
Gas Cylinder Connection
1. Connect the calibration hose to the 0.5 l/min regulator on the gas cylinder.
For use with the MicroDock II, use a demand flow regulator.
NOTE: Cylinders that are used with a demand flow regulator must meet
the following maximum inlet pressure specifications:
- Disposable cylinders 0-1000 psig/70 bar
- Refillable cylinders 0-3000 psig/207 bar
To perform an automated bump check, refer to the MicroDock II User Manual.
2. Connect the calibration hose to the calibration cap.
3. Attach the calibration cap to the detector.
4. Apply gas. Verify the visual and audible alarms activate.
5. Close the regulator and remove the calibration cap from the detector.
NOTE: The detector will temporarily remain in alarm until the gas clears from
the sensors.
6. Disconnect the hose from the calibration cap and the regulator.
Gas Cylinder Guidelines (Bump Test)
ƔTo ensure an accurate bump check, use a premium-grade gas. Use gases
approved by the National Institute of Standards and Technology.
ƔDo not use a gas cylinder that is past its expiration date.
Note
Only use the calibration
cap during calibration
and bump check.

GasAlertMicroClip
Alarms
13
Alarms
Refer to the following table for information about alarms and corresponding screens. If Stealth mode is enabled, the audible and
visual alarms are disabled. Only the vibrator alarm activates.
Alarm Display Alarm Display
Low Alarm
• Slow siren
• Slow alternating flash
•L and gas bar flash
• Vibrator alarm activates
TWA Alarm
• Slow siren
• Slow alternating flash
•Land gas bar flash
• Vibrator alarm activates
High Alarm
• Fast siren
• Fast alternating flash
•L and gas bar flash
• Vibrator alarm activates
STEL Alarm
•Fastsiren
• Fast alternating flash
•L and gas bar flash
• Vibrator alarm activates
Multi-Gas Alarm
• Alternating low and high alarm siren and
flash
•L and gas bars flash
• Vibrator alarm activates
Over Limit (OL) Alarm
• Fast siren and alternating flash
•Land gas bar flash
• Vibrator alarm activates
•OL displays

GasAlertMicroClip
Operator’s Manual
14
Alarm Display Alarm Display
Sensor Alarm
•During startup Error [sensor name]
displays
• During normal operation Err displays
Confidence Beep and IntelliFlash
• One beep and flash every second
Note: Confidence Beep and
IntelliFlash automatically
deactivate during low battery
alarm,self-test fail,calibrationfail,
bump test fail, or an alarm event.
Low Battery Alarm
• Sequence of 10 rapid sirens and
alternating flashes with 7 seconds of
silence in between (continues for
15 minutes)
• and
L
flash,
LOW BAT
displays, and the vibrator alarm activates
• After 15 minutes of the Low Battery
alarm, the Automatic Shutdown Alarm
sequence begins
•OFF displays before deactivating
Automatic Shutdown Alarm
• Sequence of 10 rapid sirens and
alternating flashes with 1 second of
silence in between (sequence reactivates
seven times)
•LOW BAT and Ldisplay, and
vibrator alarm activates
•OFF displays before deactivating
Note: Alarms can be set to latching or non-latching. To enable/disable
atching, select/deselect Latching Alarms in Fleet Manager II. Local
regulations may require a latching alarm.
If Low Alarm Acknowledge is enabled and a low alarm occurs, press
Cto disable the audible alarm. The visual and vibrator alarms remain
activated. If the alarm escalates to a high, STEL, or TWA alarm, the
audible alarm reactivates.

GasAlertMicroClip
User Options Menu
15
User Options Menu
To modify the user options, connect the detector to the R Link
adapter and open Fleet Manager II. Refer to the Fleet Manager
II Operator s Manual for complete instructions.
The following are the available user options:
1. Sensors (H2S, CO, LEL, and O2)
•Sensor Disabled Disables the sensor.
•Calibration Gas (ppm) / (%LEL) / (%O2) Defines the
calibration gas concentration for each sensor.
•Calibration Interval (days) Defines how often a
calibration should be performed.
•Bump Interval (days) Defines how often a bump test
should be performed.
•Low Alarm (ppm) / (%LEL) / (%O2) Defines the low
alarm setpoint.
•High Alarm (ppm) / (%LEL) / (%O2) Defines the high
alarm setpoint.
•TWA Alarm (ppm) Defines the time-weighted average
(TWA) alarm setpoint. H2S and CO sensors only.
•STEL Alarm (ppm) Defines the short-term exposure limit
(STEL) alarm setpoint. H2S and CO sensors only.
•STEL Interval (minutes) Defines the short-term
exposure limit (5-15 minutes). H2S and CO sensors only.
•Auto-Zero Startup When enabled, the detector
automatically zeros the H2S, CO, and LEL sensors during
the startup self-test.
•LEL By Volume CH4 When enabled, the LEL reading is
displayed as %vol., assuming a methane environment.
•O2 Auto-Calibration on Startup When enabled, the O2
sensor is automatically calibrated during startup.
2. User Options
•Confidence Beep When enabled, the detector beeps
once every second to verify the battery has sufficient
power to detect hazardous gas and emit an alarm.
Detector is shipped with Confidence Beep disabled.
•Latching Alarms When enabled, the audible, visual, and
vibrator alarms persist during a high or low alarm until the
gas concentration is below the low alarm setpoint and has
been acknowledged by pressing C.
•Safe Mode When enabled, SAFE continuously displays
on the LCD when all gas concentrations are normal or
below the alarm setpoints.
•Stealth Mode When enabled, the audible alarm, LEDs
and backlight are disabled. displays on the LCD.
•Low Alarm Acknowledge When enabled, the audible
alarm can be disabled during a low alarm. The vibrator,
LEDs, and LCD remain enabled. For H2S, CO, and LEL
sensors only.
•Datalog Interval (seconds) Enter a value
(1-120 seconds).

GasAlertMicroClip
Operator’s Manual
16
•Force Calibration When Overdue When enabled, the
detector automatically enters calibration during startup for
overdue sensors. If the sensors are not calibrated
immediately, the detector will deactivate.
•Cal Lock When enabled, the sensors can only be
calibrated using an IR device (IR Link with Fleet Manager
II or the MicroDock II base station).
•Force Bump When Overdue When enabled, a bump test
is required if the sensor has exceeded its bump test
interval. If a successful bump test is not performed, the
detector will deactivate.
•IntelliFlash When enabled, the green LED flashes to
provide continuous visual confirmation that the detector is
operating correctly.
IntelliFlash automatically deactivates during a low
battery alarm, a self-test fail, a calibration fail, a bump
test fail, or during an alarm event. To define how often
IntelliFlash occurs (1-60 seconds), refer to Confidence
Beep and IntelliFlash Interval. Default setting is
1 second. Detector is shipped with IntelliFlash enabled.
•Confidence Beep and IntelliFlash Interval Enter a
value (1-60 seconds) to define how often IntelliFlash
occurs and the detector beeps. Intelliflash and/or
Confidence Beep must be enabled in order to define
Confidence Beep and IntelliFlash Interval.
•Language Select the language to display on the LCD:
English, Français (French), Deutsch (German), Español
(Spanish), or Português (Portuguese).
Charging the Rechargeable Battery
aWarning
Only the manufacturer can replace the rechargeable
battery. Failure to adhere to this caution can lead to fire
and/or explosion.
Charge only in a safe area that is free of hazardous gas
and within temperatures of 0°C to 45°C (32°F to 113°F).
The charging adapter is specific to your region. Use of the
charging adapter outside your region will damage the
charger and the detector.
Do not calibrate during or immediately after charging.
aAvertissement
Seul le fabricant est habilité à remplacer la rechargeable
batterie. Le non-respect de cette consigne peut provoquer
un incendie et/ou une explosion.
Chargez le détecteur uniquement dans une zone sûre ne
renfermant pas de gaz dangereux et dont la température
ambiante reste comprise entre 0 à 45 °C (32 à 113 °F).
To charge the battery:
1. Deactivate the detector. Insert the charging adapter
plug into an AC outlet.

GasAlertMicroClip
Maintenance
17
2. Connect the charging adapter to the detector IR
interface.
3. Charge the battery.
4. Charge the battery after each workday.
Maintenance
To maintain the detector in good operating condition, perform
the following basic maintenance as required.
• Calibrate, bump test, and inspect the detector on a regular
schedule.
• Maintain an operations log of all maintenance, bump tests,
calibrations, and alarm events.
• Clean the exterior with a soft damp cloth. Do not use
solvents, soaps, or polishes.
Replacing a Sensor or Sensor Filter
aWarning
To avoid personal injury, use only sensors specifically
designed for the detector.
Use proper ESD handling practices.
aCaution
Ensure hands are clean or wear gloves before handling
components.
To replace a sensor or sensor filter, refer to the following
illustration, table, and procedures.
Item Description
1 Detector
2 IR and charger interface
3 Charging adapter
4 USB Cable
3
2
1
4

GasAlertMicroClip
Operator’s Manual
18
1. Deactivate the detector. On a clean surface, place the
detector face down.
2. Remove the six machine screws from the rear shell.
Remove the back cover by lifting the top and the
bottom upwards simultaneously to prevent damaging
the charging pins.
Replacing the sensor filter
1. Note the placement of the PCB to ensure it is
replaced correctly. Remove the two screws on the
PCB. Remove the PCB carefully.
aCaution
Ensure no damage occurs to the battery.
2. Remove the old sensor filter. t may be stuck to the
sensors.
3. Place the new sensor filter.
Note
When inserting a new sensor filter, ensure the black
gasket is facing the front shell.
4. To complete the detector, refer to Reassembling the
detector.
Item Description Item Description Item Description
1 Front shell 5 Rear shell 9 H2S sensor
2 LEL sensor 6 Machine screws (6) 10 O2sensor
3 PCB 7 Sealing rib 11 Sensor filter
4 PCB screws (2) 8 CO sensor
1
11
10
3
2
4
6
5
8
9
7

GasAlertMicroClip
Maintenance
19
Replacing H2S, CO, and LEL sensor
1. Note the placement of the PCB to ensure it is
replaced correctly. Remove the two screws on the
PCB. Remove the PCB carefully.
aCaution
Ensure no damage occurs to the battery.
a) If the sensor filter is stuck to the sensors,
remove and replace the sensor filter into the
front shell.
2. Slide the sensors out.
Note
Detectors that are configured for 1, 2, or 3 gases may
contain a dummy sensor in one of the four sensor
locations.
3. Insert the new sensor(s).
To complete the detector, refer to Reassembling the
detector.Replacing the oxygen sensor
Note
Detectors that are configured for 1, 2, or 3 gases may
contain a dummy sensor in one of the four sensor
locations.
Metal sensor posts
Plastic sensor post
Flex cable
Oxygen sensor
R gidified flex PCB

GasAlertMicroClip
Operator’s Manual
20
1. Gently remove the circular rigidified flex PCB atop the
sensor from the metal sensor posts. Take care not to
tear the flex cable.
2. Note the placement of the PCB to ensure it is
replaced correctly. Remove the two screws on the
PCB.
aCaution
Ensure no damage occurs to the battery.
3. Lift the PCB straight up. The oxygen sensor will stay
in the front shell. Remove the sensor.
4. On roughly the same spot on the front shell, place the
new sensor. Lower the PCB over the oxygen sensor.
5. Ensure the plastic sensor post is inserted into the
clear plastic hole. Carefully replace the circular
rigidified flex PCB atop the metal sensor posts. Take
care not to tear the flex cable.
6. Press down to secure the circular rigidified flex PCB
atop the metal sensor posts.
7. To complete the detector, refer to Reassembling the
detector.
Reassembling the detector
• Verify the PCB is seated correctly and inserted exactly as
it was removed (sensors face the front shell). Replace the
two PCB screws.
• Visually inspect the battery to ensure no damage has
occurred.
• When replacing the rear shell, ensure the charging pins
(bottom of inside rear shell) are aligned with the
corresponding holes on the PCB.
• Press the front and rear shells together firmly to ensure a
proper seal. Ensure the front and rear shell have a
uniform, tight 1/16 in. (1 mm) seal on all sides of the
detector.
• When replacing the screws, they must be seated properly
to prevent cross threading. Turn the screw counter-
clockwise until a click is heard and then begin tightening
the screw clockwise.
• New sensor(s) should be calibrated. Activate the detector
and calibrate the sensor(s). Refer to Calibration.
Note
Ensure the rib on the interior rear shell inserts
between the battery and the PCB . Refer to the
following illustrations.
1
2

GasAlertMicroClip
Specifications
21
XT Model
XL Model
Specifications
Instrument dimensions
XT 11.25 x 6 00 x 2.89 cm (4.4 x 2.4 x 1.1 in.)
XL 11.25 x 6.00 x 3.22 cm (4.4 x 2.4 x 1 2 in.)
Weight
XT 170 g (6.0 oz.)
XL 190 g (6.7 oz.)
Operating temperature -20°C to +50°C (-4°F to +122°F),
+50°C to +58°C is certified by CSA International on the
combustible sensor with ±5% accuracy
Storage temperature -40°C to +50°C (-40°F to +122°F)
Operating humidity 0% to 95% relative humidity
(non-condensing)
Alarm setpoints May vary by region and are user defined. All
setpoints automatically display during the startup self-test.
Detection range
H2S: 0 - 100 ppm (1 / 0.1 ppm increments)
CO: 0 - 500 ppm (1 ppm increments)
O2: 0 - 30.0% vol. (0.1% vol. increments)
Combustible (LEL): 0 - 100% (1% LEL increments) or
0 - 5.0% v/v methane
2
1
2
1
This manual suits for next models
1
Table of contents
Other BW Technologies Security System manuals
Popular Security System manuals by other brands
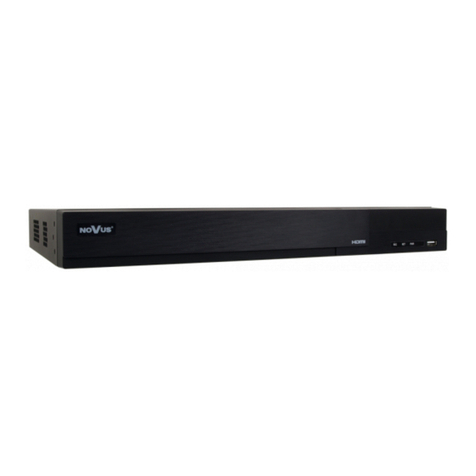
Novus
Novus NVR-6316P16-H2 user manual
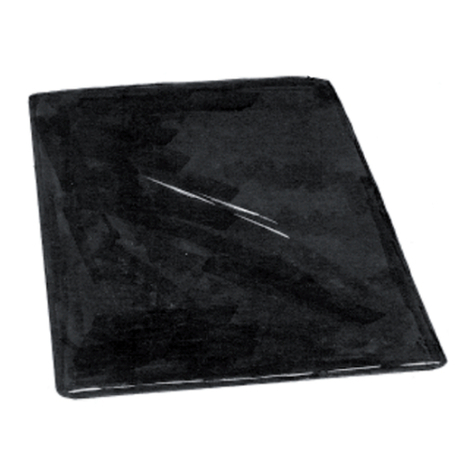
Skil-Care
Skil-Care Restraint-Free FloorPro 909286 manual
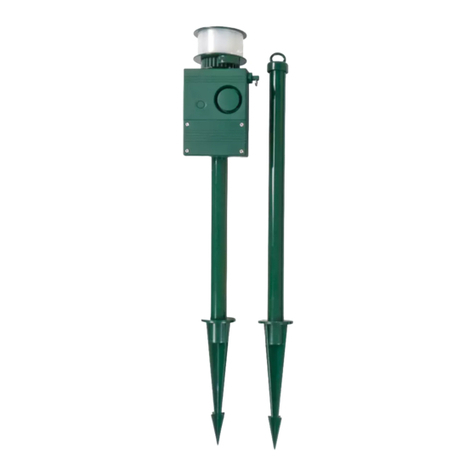
SuperFish
SuperFish Pond Alarm instructions

AmeriWater
AmeriWater 00850300 Installation & operation manual
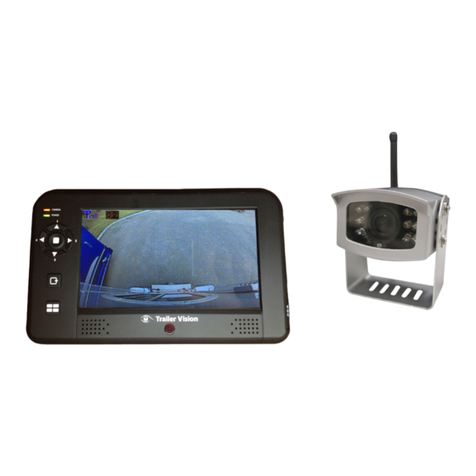
Trailer Vision
Trailer Vision Digi-Max2 Installation and user manual
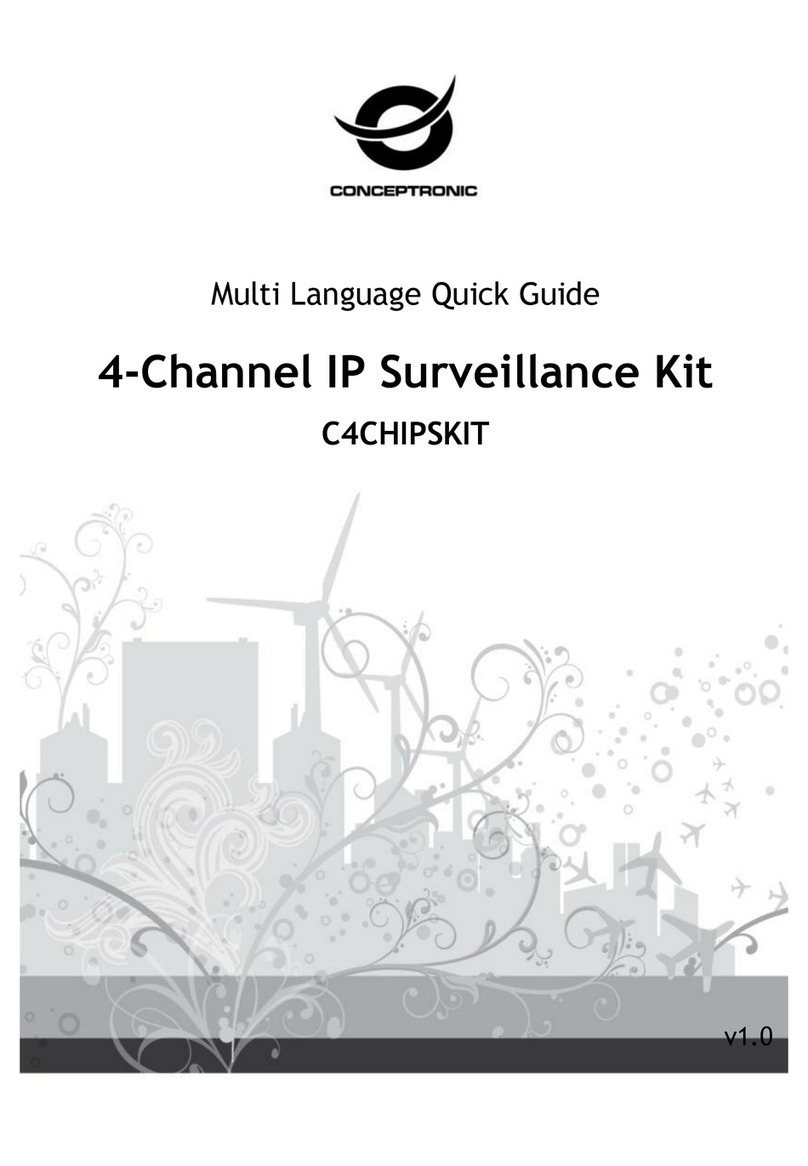
Conceptronic
Conceptronic C4CHIPSKIT quick guide