C&C Atlas Series User manual

API 6D Two - Piece Cast Trunnion
Mounted Ball Valve
Atlas Series
Document Number:
Revision:
Release Date:
EDC 506
0
01/03/2018
IOM: Installation, Operation and Maintenance Manual 1/17
Installation, Operation, and Maintenance Manual
API 6D Two - Piece Cast Trunnion Mounted Ball Valve –Atlas Series

API 6D Two - Piece Cast Trunnion
Mounted Ball Valve
Atlas Series
Document Number:
Revision:
Release Date:
EDC 506
0
01/03/2018
IOM: Installation, Operation and Maintenance Manual 2/17
TABLE OF CONTENTS
1SCOPE.............................................................................................................................................................................................3
1.1 RESPONSIBILITY FOR VALVE APPLICATION...................................................................................................................3
1.2 RECEIVING INSPECTION, HANDLING AND STORAGE ..................................................................................................3
2BILL OF MATERIAL....................................................................................................................................................................... 5
3INSTALLATION..............................................................................................................................................................................7
3.1 NAMEPLATE..............................................................................................................................................................................8
3.2 HIGH TEMPERATURE SERVICE........................................................................................................................................... 8
3.3 LOW TEMPERATURE SERVICE ...........................................................................................................................................8
4OPERATION................................................................................................................................................................................... 8
4.1 INITIAL START-UP/COMMISSIONING.................................................................................................................................. 8
4.2 NORMAL OPERATING ACTIVITY..........................................................................................................................................8
4.3 DOUBLE BLOCK AND BLEED OPERATION....................................................................................................................... 8
4.4 BODY CAVITY RELIEVING SYSTEM....................................................................................................................................9
5MAINTENANCE.............................................................................................................................................................................. 9
5.1 VALVE MAINTENANCE IN OPERATION..............................................................................................................................9
5.1.1 STEM LEAKAGE................................................................................................................................................................... 9
5.1.2 SEAT LEAKAGE..................................................................................................................................................................10
5.2 SCHEDULE OF ROUTINE MAINTENANCE.......................................................................................................................10
5.3 VALVE CLEANING..................................................................................................................................................................10
5.4 EMERGENCY REPAIR........................................................................................................................................................... 10
6DISASSEMBLY AND REASSEMBLY INSTRUCTIONS........................................................................................................ 11
6.1 DISASSEMBLY........................................................................................................................................................................11
6.2 RECONDITIONING .................................................................................................................................................................13
6.3 REASSEMBLY.........................................................................................................................................................................13
7PROPER VALVE TESTING........................................................................................................................................................14
7.1 SHELL TEST ............................................................................................................................................................................14
7.2 HYDROSTATIC SEAT TEST.................................................................................................................................................14
7.3 DOUBLE BLOCK AND BLEED (DBB) TEST ......................................................................................................................14
7.4 SUPPLEMENTAL AIR SEAT TEST......................................................................................................................................15
8BOLTS TIGHTENING TORQUE................................................................................................................................................15
9TROUBLESHOOTING................................................................................................................................................................. 15

API 6D Two - Piece Cast Trunnion
Mounted Ball Valve
Atlas Series
Document Number:
Revision:
Release Date:
EDC 506
0
01/03/2018
IOM: Installation, Operation and Maintenance Manual 3/17
1 SCOPE
The following instructions are very important for the maintenance, disassembling and assembling of C&C
Atlas series end entry two-piece trunnion ball valves.
The instructions make references to valves with emergency sealant injectors and with back up rings for
high pressure service. As the above-mentioned features are not standard, in some cases these parts may
not be found, or may be found partially during the disassembling of the valves.
1.1 RESPONSIBILITY FOR VALVE APPLICATION
The End User is responsible for ordering the correct valves for the intended application. C&C Valves are to
be installed in observance of the pressure rating and design temperature. Prior to installation, the valves
and nameplates should be checked for proper identification to be sure the valve is of the proper type,
material, and is of a suitable pressure class and temperature limit to satisfy the application requirements.
1.2 RECEIVING INSPECTION, HANDLING AND STORAGE
On arrival at site, an accurate checking must be carried out in order to verify if any damage has occurred
during transportation.
Compliance to purchase order requirements.
Correct type, pressure class, size, body, trim & seal material and end connections
(This information may be found on the nameplate or may be stamped on the body of the valve)
Each C&C valve has unique serial number hard stamped on the closure of the valve.
(This shall be always be quoted for any enquiry related to a particular valve)
Condition of valve paint and location of required Mylar tags.
End protectors on valve end are in place with a nonporous moisture barrier between the cover and
the metal flange or welding end.
Valve are shipped in the fully open position with wooden or plastic covers to protect the ends from
ingress of foreign materials.
It is recommended that lifting devices that are rated for the valve weight should be used when lifting any
C&C Valves. C&C Atlas series ball valves 6” full bore and larger are provided with lifting lugs integral to the
valve body. Operators like gearboxes or actuators may have their own lifting points that are intended and
designed to bear the load of the operator only. Operator lifting points shall not be used to lift the
valve/operator assembly.
We recommend that this entire document be read prior to proceeding
with any installation or repair.
Do not use any valve in applications where either the pressure or
temperature is higher than the allowable working values. Also, valves
should not be used in service media if not compatible with the valve
material of construction, as this may cause premature failure.

API 6D Two - Piece Cast Trunnion
Mounted Ball Valve
Atlas Series
Document Number:
Revision:
Release Date:
EDC 506
0
01/03/2018
IOM: Installation, Operation and Maintenance Manual 4/17
Recommended handling procedure when lifting with slings is shown in figure 1.
Pallets, boxes, crates are provided with lifting/piling indications that shall be followed at all times.
Operator lifting points shall not be used to lift the valve.
Other lifting equipment provided with hooks can be used instead.
Chains shall not be used instead of slings using procedures in figure 1.
Lifting equipment’s safe working load (SWL) shall always be double checked prior to any lift.
During lifting/handling always keep valve flange protection in place to avoid foreign material from
entering the valve bore
Pay attention, as not to damage the valve paint during lifting/handling procedures.
Special care to the marking applied on the crates, and particularly to piling instructions, must be taken during
storage/stowage of the box containing the valves. Unless otherwise agreed, CNC wooden boxes are not
suitable for storage/stowage one on top of the other. Non-observance of crate handling markings could result
in the serious injury of people and damages to the goods.
Do not store valve without end protection to prevent from ingress of foreign
materials

API 6D Two - Piece Cast Trunnion
Mounted Ball Valve
Atlas Series
Document Number:
Revision:
Release Date:
EDC 506
0
01/03/2018
IOM: Installation, Operation and Maintenance Manual 5/17
Whenever possible valve shall be stored indoors and out of weather. When stored without wooden
box, care must be taken not to put stainless steel valves and/or components in contact with any
carbon steel components and/or structures to avoid cross contamination. Also, grinding of carbon
steel components near stainless steel valves shall be avoided.
For open air storage, special precaution should be taken to avoid both package and valve damage
by environmental factors. Wooden boxes shall have minimum protection, using cellophane or
similar sheets without tears/holes adequately fixed and the boxes lifted from the ground. Box
condition shall be checked maximum every two months.
For storage periods over two months in un-covered areas, CNC does not take any responsibility
unless this requirement has been agreed on the purchase order.
Lubrication during storage is not recommended.
2 BILL OF MATERIAL
ITEM
Component
ITEM
Component
1
Body
24
Segment Ring Retainer
2
Closure
25
Stem Keys
3
Ball
26
Stem Pins
4
Stem
27
Stem Retaining Pin
5
Trunnion Support
28
Stem Fire Safe Seal
6
Seat Rings
29
Gland Flange
7
Seat Inserts
30
Gland Pin
8
Fire Safe Seat Seal
31
Cap Screws, Gland Flange
9
Seat O-Rings
32
Trunnion O-Ring
10
Seat Back up Rings
33
Trunnion Gasket
11
Springs
34
Trunnion Thrust Washer
12
Body O-Ring
35
Trunnion Bearing
13
Body Gasket
36
Cap Screws, Trunnion
14
Body Studs
37
Seat Injection Fittings
15
Body Nuts
38
Stem Injection Fitting
16
Antistatic Plunger/Ball
39
Check Valve
17
Antistatic Spring
40
Bleed Fitting
18
Stem Thrust Washer
41
Gear Stud
19
Stem Bearing
42
Gear Nut
20
Lantern Ring
43
Gear
21
Stem O-Rings
44
Lever
22
Stem Back up Rings
45
T-Lever
23
Segment Ring
46
Cap Screw, T-Lever
NOTE: Quantities of the valve components depend on valve sizes and classes. Valve sales drawing available upon
request shall specify quantities.

API 6D Two - Piece Cast Trunnion
Mounted Ball Valve
Atlas Series
Document Number:
Revision:
Release Date:
EDC 506
0
01/03/2018
IOM: Installation, Operation and Maintenance Manual 6/17
Figure 2: Atlas Series Ball Valve
Sizes 2” –4”

API 6D Two - Piece Cast Trunnion
Mounted Ball Valve
Atlas Series
Document Number:
Revision:
Release Date:
EDC 506
0
01/03/2018
IOM: Installation, Operation and Maintenance Manual 7/17
Figure 3: Atlas Series Ball Valve
3 INSTALLATION
Valves, as delivered, are ready for installation once valve flange protectors are removed and rust
preventative grease wiped off flange gasket surfaces. A light solvent may be used to fully remove grease
residue.
Install valve in system using proper size and type mating flanges and appropriate gaskets (for RF) or seal
rings (for RTJ). Valve design allows for line flow in either direction.
The pipeline where the valve is to be installed shall be clean, free from sand, welding slags, debris, pieces
of wood and/or any other foreign material that can damage the valve seats during operation.
Actuator and Gear stops are pre-set at the factory and should require no further adjustments. With the
exception of ‘fail-safe closed’ valves, all other valves are shipped in the open position. Valves should not be
closed until the bore of the valve has been cleaned of all debris.
Sizes 6” – 16”

API 6D Two - Piece Cast Trunnion
Mounted Ball Valve
Atlas Series
Document Number:
Revision:
Release Date:
EDC 506
0
01/03/2018
IOM: Installation, Operation and Maintenance Manual 8/17
3.1 NAMEPLATE
Nameplates provided on the products are designed to either advise operators of residual hazard or provide
information regarding the valve. Hiding or removing such information can be very dangerous to personnel
operating or maintaining the valve.
3.2 HIGH TEMPERATURE SERVICE
Some valves do have operating temperatures that can be very dangerous to people or animals. To avoid
any kind of injuries operators must ensure the valve surfaces that reach such temperatures are suitably
protected against accidental contact.
Operators are recommended to always provide an efficient protection/insulation of the valve surfaces that
may be touched by personnel and/or animals and that exceed, in lower or in higher, the human tolerable
limits (as a suggestion use -4F through +140F).
3.3 LOW TEMPERATURE SERVICE
Prior to exposure to freezing temperatures, it is highly recommended the valve be drained. Water that may
be trapped in the body cavity could freeze and impair the operation of the valve or damage the valve. If the
valve has a grease fitting in the lower drain, a sufficient amount of antifreeze injected into the body cavity
via the lower drain grease fitting will prevent accumulated water from freezing. It is also advisable to inject
a sufficient amount of valve lubricant into the grease fittings of valve and operator (if present) prior to
extended cold temperature exposure.
4 OPERATION
4.1 INITIAL START-UP/COMMISSIONING
Once installed in the line the valve should be left either in the fully open or fully closed position, depending
on the start-up/commissioning operation.
4.2 NORMAL OPERATING ACTIVITY
The valve is designed for on/off service only. Pressure - temperature limits are stated on the valve
nameplate. Do not use valve for flow control neither in the partially open position nor for throttling service,
as these could lead to premature failure. The valve can be operated from the fully open to the fully closed
position by acting on the hand wheel/lever (clockwise to close). When the stem flats or keyway are
perpendicular to the fluid bore, valve is closed. Positive stops and arrow indication are provided on handles
and gear operators.
4.3 DOUBLE BLOCK AND BLEED OPERATION
When pressure is applied to both ends of a closed valve, each seat will be forced against the ball, creating
a double block. The hex head bleed fitting (40) provides a safe and convenient method for checking closed
valve seat sealing effectiveness.
Do not leave the valve in partially open position for a long period. Ensure the
pipeline is free of any debris such as sand, tools, welding slag or weld
splatter and rod ends. This will damage the valve ball and seats during the
start-up/commissioning operations.

API 6D Two - Piece Cast Trunnion
Mounted Ball Valve
Atlas Series
Document Number:
Revision:
Release Date:
EDC 506
0
01/03/2018
IOM: Installation, Operation and Maintenance Manual 9/17
4.4 BODY CAVITY RELIEVING SYSTEM
Trunnion mounted ball valves do have a body cavity where pressure can be trapped in a closed volume.
Under this circumstance, any increase of the contained fluid temperature or any degradation of the
contained fluid can result in an uncontrolled pressure increase of the trapped fluid potentially above the
design pressures of the valve.
To avoid the above scenario, all of the C&C trunnion mounted ball valves are provided with one of the
following body cavity relieving systems (depending on the design of the seats):
Self-Relieving Seats:
The design of a self-relieving seat is such that when the pressure in the body cavity exceeds the
rated pressure of the valve, not to exceed 1.33 times the maximum operating pressure (MOP) then
the seat will automatically disconnect from the ball and allow pressure equalization between the
body cavity and the pipeline. When one or both of the seats are of the Self Relieving type, there is
no need for any other type of body cavity relieving systems.
Pressure Relief Valve:
When both of the seats are not of the self-relieving type (i.e. both of the seats are of the Double
Piston Effect Type), the body cavity must be protected from overpressure by means of a Pressure
Relieving Valve (PRV) set to relieve excess pressure.
The standard PRV connected to the body cavity has been pre-set and tested in the factory to
relieve at approximately of 1.33 times the maximum operating pressure (MOP) of the valve.
It is a mandatory requirement to keep body cavity pressure relieving system functioning correctly. Failure of
the body cavity pressure relieving system can lead to failure of the valve pressure containment capability
with consequent injures to personnel, damage to the environment and loss of production.
5 MAINTENANCE
Maintenance personnel performing this operation shall be fully trained to handle pressure-containing
equipment. Opening pressure containing equipment without having released all of the internal pressure
and having safely isolated the pipeline where the valve is assembled can lead to serious injury or even
death of the personnel involved. DO NOT PROCEED IF IN DOUBT. ALWAYS DOUBLE CHECK.
Some pipelines may contain fluids that are dangerous or lethal to human beings, animals and to the
environment. Always check with the HS&E manager before releasing any fluid to the atmosphere.
5.1 VALVE MAINTENANCE IN OPERATION
5.1.1 STEM LEAKAGE
The C&C Atlas series valve is provided with a stem sealant injector, stem leakages can be temporarily
stopped by injecting sealant into the stem fitting (38).
Before opening the bleed fitting, note orientation of the exhaust hole in the
bleed valve. Never open bleed fitting while valve is exposed to line pressure.

API 6D Two - Piece Cast Trunnion
Mounted Ball Valve
Atlas Series
Document Number:
Revision:
Release Date:
EDC 506
0
01/03/2018
IOM: Installation, Operation and Maintenance Manual 10/17
To replace all the stem O-Rings (21), it is necessary to depressurize the line and to disassemble the
stem-lantern ring group as per instructions in para 6.1.
5.1.2 SEAT LEAKAGE
If the valve has been provided with emergency seat sealant injection fittings (37), seat leakage can be
temporarily eliminated or, at least, considerably reduced by injecting sealant when the valve is in a fully
closed position. Seat sealant fittings (37) are located in the body (1) and closure (2). Disassembling the
valve and replacing the seat seal can eliminate seat leakages.
5.2 SCHEDULE OF ROUTINE MAINTENANCE
Valves are designed for a maintenance free life of 2-10 years depending upon severity of service.
Routine maintenance consists of injecting lubricant though the groove or channel inside the valve
leading to seal points around the ball thus topping off the lubricant. In order to guarantee efficient valve
operation, the valve shall be inspected on a regular basis during the operation and subject to scheduled
maintenance. Qualified person shall do all maintenance work.
Table 1: Recommended Lubrication Quantities
Valve
Sizes
Lubricant by valve size (ounces)
2"
2
3"
2
4"
2
6"
3
8"
3
10"
3
12"
3
14"
4
16"
4
18"
4
20"
6
24"
8
5.3 VALVE CLEANING
Valve cleaning is required when the valve does not seal properly and becomes hard to operate. Valve
cleaners are products that contains detergent, sealant and oils. They clear channel/passage where old
grease may have hardened. Inject cleaner through the seat injection fitting (37), leave it for three-to-four
hours. If possible, cycle the valve to evenly distribute the cleaner in the ball seat contact area. This
procedure is often successful in freeing seized, or hard to turn valves.
Note: Always replace the valve cleaner with equal quantities of Lubricant after cleaning
5.4 EMERGENCY REPAIR
All C&C Atlas series valves are designed to operate without lubrication. Sealant injection can be
used to stop/reduce leakage across the seats and/or through the stem seals as an emergency
temporary solution. Furthermore, there is no guarantee that after the injection of the sealant the
valve seats or stem seal will seal perfectly.

API 6D Two - Piece Cast Trunnion
Mounted Ball Valve
Atlas Series
Document Number:
Revision:
Release Date:
EDC 506
0
01/03/2018
IOM: Installation, Operation and Maintenance Manual 11/17
Sealant must be injected only when leakage occurs. See table 1 for volume of sealant required by
valve size.
Prior to injecting sealant, it is suggested to flush the seat with flushing fluid and set the valve to the
fully closed position.
A valve, which requires continuous heavy sealant injections, shall be either replaced or repaired
immediately.
6 DISASSEMBLY AND REASSEMBLY INSTRUCTIONS
6.1 DISASSEMBLY
To disassemble two piece end entry trunnion ball valves, no special tools are needed. A torque wrench
or bolt tightening tool is required to tighten nuts during reassembly. For tightening torque please refer to
section 8.
In case the valve is in operation, first, release the pressure from the line. For a complete
disassembly, the valve must be removed from the line.
Open the cavity bleed fitting (40) to discharge the residual pressure and operate the valve to the
fully open position. Always use the safety plug or bleed fitting provided either at the drain
connection to release the body cavity pressure.
Remove the valve from the line.
Before disassembling the valve, it is important to mark all the parts, in order to correctly reassemble
the valve.
The valve shall be positioned to have the flow axis along the horizontal axis and the upper part shall
be easily accessible.
Remove the valve operator, after having removed the gear studs (41) and nuts (42), which are
connected with the valve, remove/pull the actuator carefully until it is completely disconnected from
the stem (4).
Improper Selection of the lubricants may cause incompatibility of the
soft components of the valve with the products injected. The end user
is responsible to use the correct lubricants.
Never unscrew the flanged connections with residual pressure in the
line.
To avoid possibility of being struck by liquid or foreign soild
materials, position yourself so the hole of the bleed fitting is pointing
safely away from you.
Injection fittings should not be removed if there is pressure in the line.
Injection fittings should never be painted.
Be careful not to injure personnel performing this operation. Always
wear safety gloves, shoes and glasses.
.

API 6D Two - Piece Cast Trunnion
Mounted Ball Valve
Atlas Series
Document Number:
Revision:
Release Date:
EDC 506
0
01/03/2018
IOM: Installation, Operation and Maintenance Manual 12/17
During this operation, particular care shall be paid not to damage both the stem (4) and the key
(25).
Remove the stem key (25).
Unscrew the body nuts (15), leaving a few on closure for easier handling.
Turn the valve and rest it in one end flange. In this way, the valve bore will be in vertical position.
Pay attention not to damage the surface of the flanged end.
Unscrew the remaining body nuts (15) left on the closure (2).
Lift carefully the closure (2) paying attention not to damage the body O-Ring (12) and body gasket
(13) which can follow the closure or stay in the body cavity.
Unscrew the gland flange caps screw (31) and remove the gland pins (30) from the gland flange
using eyebolts fitted in the threaded hole in the pins.
Remove the stem fire safe seal (28).
Unscrew the trunnion cap screws (36).
Extract trunnion (5) from the body (1) and remove the trunnion O-Ring (32) and trunnion gasket
(33).
Welded connections shall not be removed.
Stem Retained in the body design (2”-4” for all pressure class up to 1500)
Remove the ball (3) from the body (1) by using nylon rope or strap without damage
Remove the stem (4) from the body through end entry.
Extract the lantern ring (20) from the body (1) through top.
It is possible to remove the stem injection fitting (38) for cleaning.
Stem Retaining Pin design (6” & larger for class 150 and 300)
Remove the stem injection fitting (38). Using an allen wrench, unscrew the stem retaining pin
(27) provided inside the fitting (38).
Extract the stem (4) and lantern ring (20) group from the body.
Remove the ball (3) from the body (1) by using nylon rope or strap without damage.
Segment Ring Design (8” & larger for class 300 and 6” & larger for class 600, 900 and 1500)
Remove the segment ring retainer (24) and extract the segment ring (23).
Extract the stem (4) and lantern ring (20) group from the body.
Remove the ball (3) from the body (1) by using nylon rope or strap without damage
Place the ball (3) on a wooden block.
Extract the seat ring (6) from the body (1) and closure (2). Seat seal can be either O-Rings (9) or an
insert (7).
It is not possible to remove seat insert (7), if found damaged, new seat rings (6) with inserts shall be
used during reassembly.
Remove trunnion thrust washer (34), where provided, if damaged only. Trunnion bearing (35) may
be removed using an extractor.
Remove stem thrust washer (18), and stem bearing (19) from the stem (4).
Remove the seat O-Rings (9) and the fire safe seat seal (8).
Remove the stem O-Rings (21) from the lantern ring (20).
Remove the seat springs (11) from their housing in the seat (8) or in the body (1) & closure (2),
where provided.

API 6D Two - Piece Cast Trunnion
Mounted Ball Valve
Atlas Series
Document Number:
Revision:
Release Date:
EDC 506
0
01/03/2018
IOM: Installation, Operation and Maintenance Manual 13/17
6.2 RECONDITIONING
The metallic parts can be cleaned using cloths wet with the cleaner.
To clean the O-Rings and gaskets use dry, clean cloths. If possible, it is recommended to wash the
O-Rings with soap and water, rinsing with clean water.
After cleaning components be sure that there are no damaged parts and, particularly, there are no
scores on metallic surfaces in moving or sealing areas. Also, check the condition of the O-Rings
and back-up rings, making sure that they have not been damaged.
Replace any damaged parts.
Lubricate O-Rings and metallic surfaces, which come into contact during the ball movement with
VALTEX 2000 grease. The stem /trunnion bearing (19)/ (35) are self-lubricated and do not require
any additional lubrication.
6.3 REASSEMBLY
(a) To reassemble the seat group in the body (1) and closure (2) proceed as follows:
Put the body gasket (13) and O-Ring (12) into their housing in the closure (2). The body O-Ring
(12), seat O-Rings (9), stem O-Rings (21) and trunnion O-Ring (32) must be fitted stretching them
slightly. Any damage on these O-Rings can cause breakages during the valve assembly.
During reassembling, refer to markings applied before disassembling.
Insert the seat springs (11) into the seats (6) or body (1) and closure (2), where provided.
Insert the seat O-Rings (9) and seat the fire safe seals (8), where provided
Press the seat assembly (6) into the body (1) and closure (2)
When pressing the seat into the body and closure, pay attention that the seat moves correctly,
parallel to the body and closure surfaces. For this operation, we recommend using clamps and a
rubber hammer.
It is not possible to replace the seat insert (7) only.
(b) Assemble the stem/lantern ring group as follows:
Insert in the upper part of the stem (4) into the stem thrust washer (18) and stem bearing (19).
Assemble to the stem O-Rings (21) on lantern ring (20).
Insert the stem (4) into the lantern ring assembly.
Insert the upper gland pins (30) in the body (1).
Insert the stem fire safe seal (28).
(c) Turn the valve bringing the stem axis in the vertical position.
(d) Fit the stem/lantern ring group following the markings made before disassembling. If parts are
correctly aligned, reassembly shall be easy.
(e) Reinstall the ball (3) into the body (1).
(f) Reassemble the segment ring (23) and segment ring retainer (24), if provided.
(g) Completely tighten the body studs & nuts (14 &15), of the valve, gland flange cap screws (31) and
trunnion cap screws. Refer to section 8.
(h) Be careful not to over-torque the nuts and cap screws. Damages to the threads can cause the
flanged joint to fail under pressure and injury personnel performing test operation.
(i) Insert the stem drive keys (25) on the stem (4)
(j) Reassemble the segment-retaining pin (27), if provided.
(k) Reassemble seat injection fitting (37), when provided; stem injection fitting (38), and the cavity
bleed fitting (40).
(l) Reassemble the gearbox operator (43), if provided ensuring that all the marks previously made
correspond and using only part of the fixing studs (41) and nuts (42). Carry out some opening and
closing operations, verifying the perfect functioning of the operator and the valve.

API 6D Two - Piece Cast Trunnion
Mounted Ball Valve
Atlas Series
Document Number:
Revision:
Release Date:
EDC 506
0
01/03/2018
IOM: Installation, Operation and Maintenance Manual 14/17
For either gear operated valves or actuated valves, make sure that both the travel ends act when
the valve is fully open and closed.
7 PROPER VALVE TESTING
Always perform an API 6D pressure test before re-installing the valve into the line to verify that the
maintenance operation have been satisfactorily performed and to re-certify pressure containment capability
of the valve.
7.1 SHELL TEST
There shall not be any leakage under the pressure when ball is partially open and both ends are blanked.
Testing pressure is 1.5 times the maximum operating pressure. Test duration are 2min for 4” and under
valves, 5min for 6” to 10” valves, 15min for 12” to 18” and 30min for 20” and larger.
(a) Fit the vent valve and set it in open position.
(b) Operate the valve to the half-open position.
(c) Fill in the valve with the fluid (Venting the air through the vent valve)
(d) Close the vent valve and apply pressure in accordance with maximum operating pressure of the
pipeline.
(e) Visually check the outside of the ball valve for leakage.
(f) Depressurize the valve.
7.2 HYDROSTATIC SEAT TEST
Valves are to be subjected to a hydrostatic seat test. There is to be no leakage under test pressure. Test
pressure is to be applied to the appropriate end of the valve. Testing pressures 1.1 times maximum
operating pressure. Test durations are 2min for 4” and under valves, 5min for 6” to 18” and 10mim for 20”
and larger valves.
(a) Operate the valve to the fully close position and open the vent valve.
(b) Pressurize one side in accordance with max operating pressure of the pipeline.
(c) From the body vent or bleed fitting, check for possible seat leakage.
(d) Repeat same operations as per points (b) & (c) on opposite side of the valve.
(e) Depressurize the valve.
7.3 DOUBLE BLOCK AND BLEED (DBB) TEST
If the valve seats have DBB function, then the seat test shall be performed as follows:
(a) With the valve unseated and partially open, the valve cavity shall be completely filled with test fluid.
(b) The valve shall then be closed and the vent valve opened to allow excess test fluid to overflow form
the valve –cavity test connection.
(c) The test pressure shall be applied simultaneously from both ends.
(d) Seat tightness shall be monitored from the cavity connection.
(e) Depressurize the valve.
Installing the valve in the line without pressure testing could cause leakage
of production fluid and, potentially hazardous situation.

API 6D Two - Piece Cast Trunnion
Mounted Ball Valve
Atlas Series
Document Number:
Revision:
Release Date:
EDC 506
0
01/03/2018
IOM: Installation, Operation and Maintenance Manual 15/17
7.4 SUPPLEMENTAL AIR SEAT TEST
The seat test specified in 7.2 shall be repeated at the test pressure between 80 psig and 100 psig using air
as the test medium.
8 BOLTS TIGHTENING TORQUE
Table 2: Recommended Bolt Torque
Bolt Size
Torque Values
(Inch-lbs.)
Bolt Size
Torque Values
(Inch-lbs.)
Inch
Metric
B7
B7M
Inch
Metric
B7
B7M
1/4
M6
62
53
1-1/4
M30
10798
9824
5/16
M8
142
124
1-3/8
M36
15002
14028
3/8
M10
248
221
1-1/2
M39
19799
18587
7/16
-
416
381
1-5/8
M42
25800
24286
1/2
M12
602
549
1-3/4
M45
32394
27756
9/16
M14
903
841
1-7/8
M48
39607
34695
5/8
M16
1204
1106
2
M52
49210
41634
3/4
M20
2168
2036
2-1/4
M56
71957
61761
7/8
M22
3629
3469
2-1/2
M64
99571
86914
1
M24
5532
5222
2-3/4
M68
134531
113113
1-1/8
M27
7877
7125
3
M76
175245
147808
Note: Tightening Torque Values ± 10%
9 TROUBLESHOOTING
Issue
Possible Cause
Solution
Valve will not open
or close
1. Improper setting of gear or
actuator stops
2. Ice inside operating device
1. Reset travel stop.
2. Remove operating device cover
and check for ice. Remove and
replace as necessary
Valve hard to
operate
1. Foreign material in line/valve
2. Lack of lubrication
1. Flush line to remove debris.
Clean the valve –see valve
cleaning procedure.
2. Lubricate seats utilizing sealant
injection fittings (37)

API 6D Two - Piece Cast Trunnion
Mounted Ball Valve
Atlas Series
Document Number:
Revision:
Release Date:
EDC 506
0
01/03/2018
IOM: Installation, Operation and Maintenance Manual 16/17
3. Gear hard to operate or stuck
3. Check gear. Lubricate or replace.
Leak around the
seat
1. Foreign material between seat
and ball.
2. Valve not fully closed
3. Worn or damaged seat inserts
and/or ball.
4. Worn or damaged seat O-Ring
seals
1. Clean and lubricate seats –see
Valve cleaning and emergency
repair section.
2. Check the gear operator for fully
closed position.
3. Disassemble the valve and
replace damaged component(s)
4. Disassemble the valve and
replace the O-Ring.
Leak around the
stem
1. Worn or damaged O-Ring seals
1. Grease the stem. Disassemble
the valve and replace the O-
Rings
Leak around
trunnion
1. Worn or damaged trunnion O-
Ring and/or gasket
2. Trunnion cap screws not properly
tightened
1. Disassemble the valve and
replace the O-Ring and/or
gasket.
2. Tightened cap screws to
specified torque.
Leakage from bleed
or injection fittings
1. Foreign material in the fittings
2. Fittings are loose
1. Inject small amount of cleaner to
flush foreign materials
2. Tighten fittings.

API 6D Two - Piece Cast Trunnion
Mounted Ball Valve
Atlas Series
Document Number:
Revision:
Release Date:
EDC 506
0
01/03/2018
IOM: Installation, Operation and Maintenance Manual 17/17
CNC Flow Control
10350 Clay Road, Suite 250
Houston, Texas 77041
Toll-free: (844) 398-6449
Phone: (713) 466-1644
Fax: (713) 466-1715
Website: www.cncflowcontrol.com
This manual is provided for informational purposes only and is solely intended for the installation, operation, and maintenance of C&C
Flow Control Atlas Series API 6D two-piece trunnion mounted ball valves. CNC Flow Control reserves the right to change information
contained in this manual without any notice. Contact CNC Flow Control at the above address for specific questions regarding this
manual or valve.
Although this manual has been checked for accuracy, the Purchaser or End User is ultimately responsible for the correct installation,
operation, and maintenance of any valve in their pipeline. Therefore, information contained in this manual shall not be construed as a
guarantee or product warranty.
This manual suits for next models
1
Table of contents
Popular Control Unit manuals by other brands
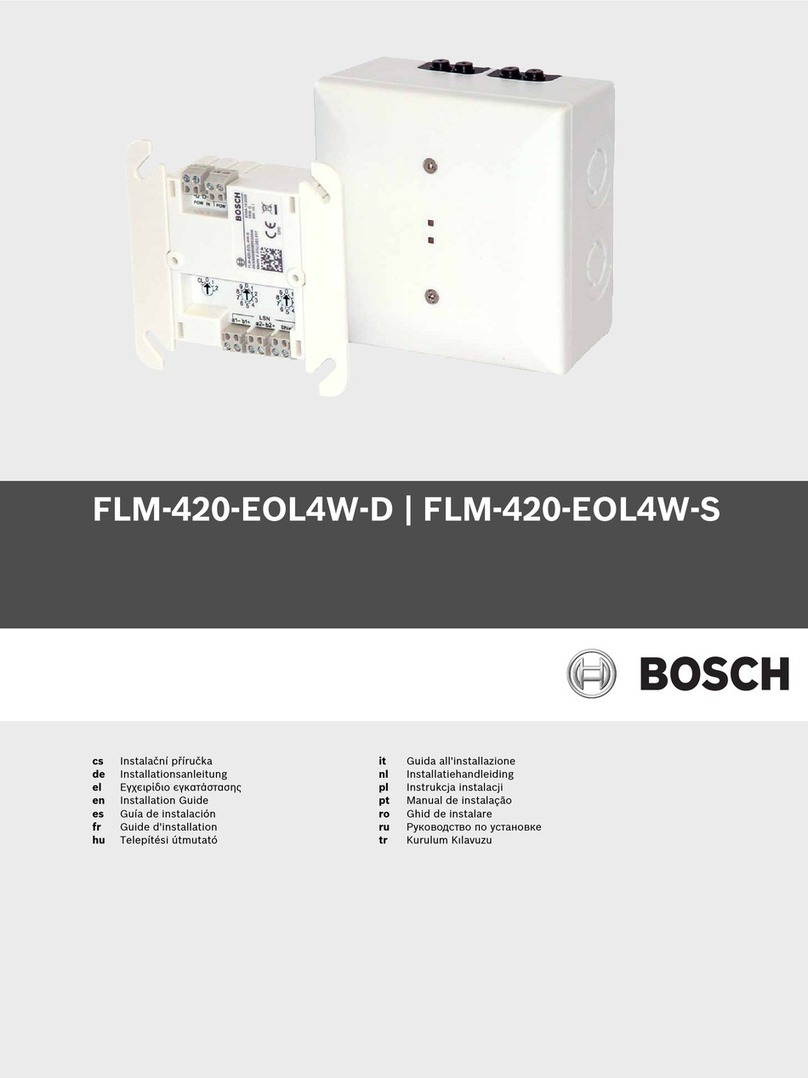
Bosch
Bosch FLM-420-EOL4W-D installation guide
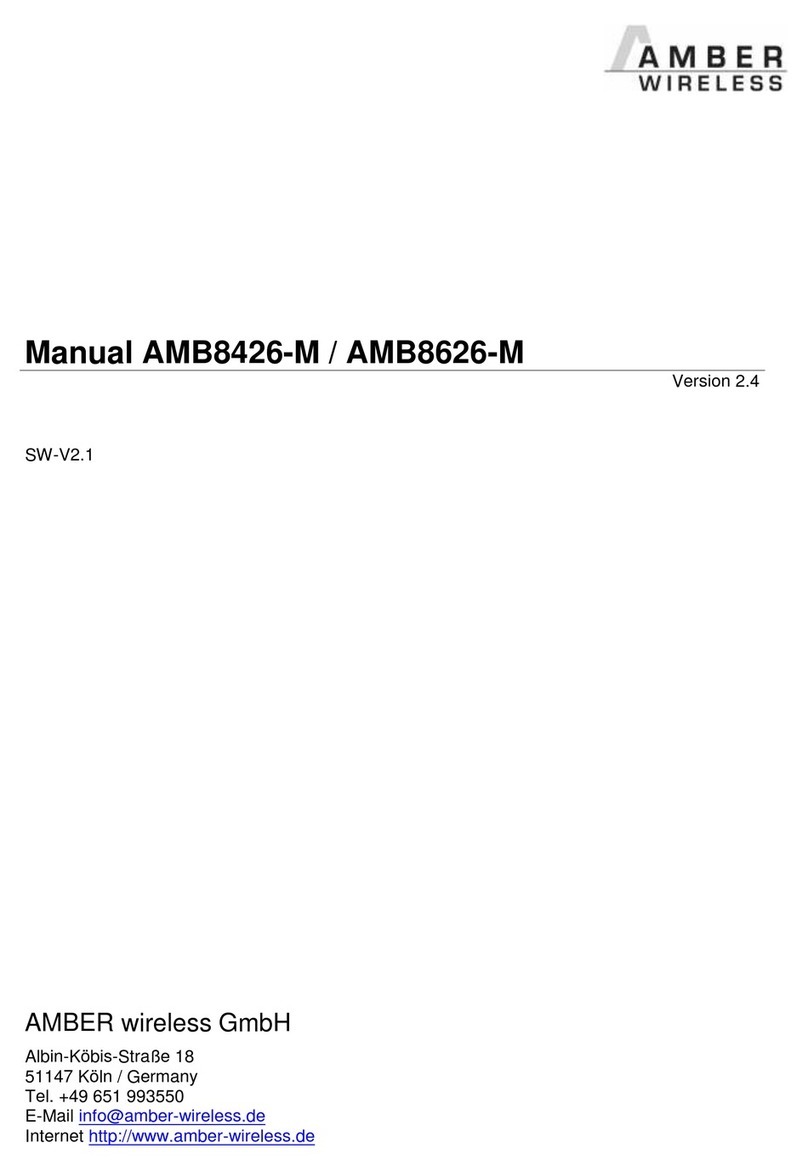
Amber Wireless
Amber Wireless AMB8426-M manual
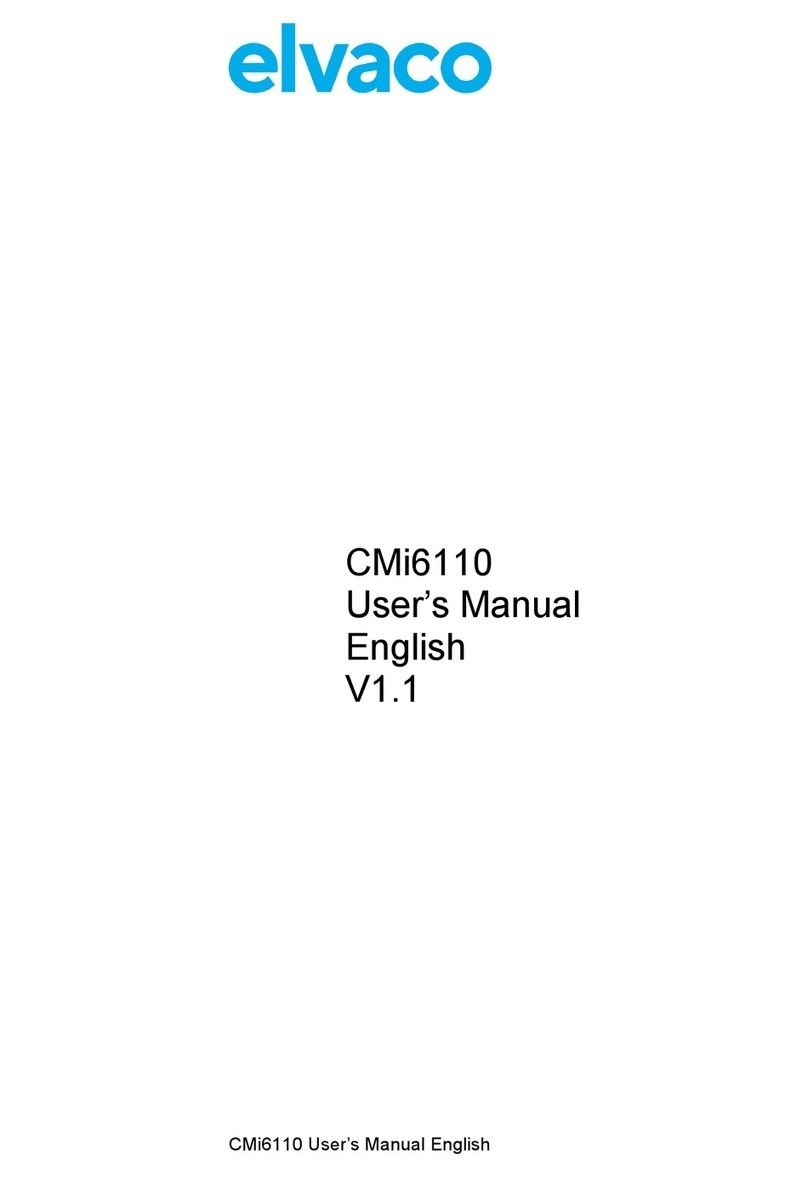
Elvaco
Elvaco CMi6110 user manual

PLEIGER ELEKTRONIK
PLEIGER ELEKTRONIK PPC-PLD-7 manual
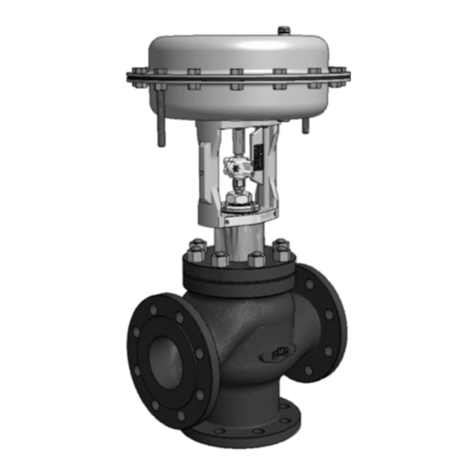
OMC
OMC AD20 Installation, operation and maintenance manual
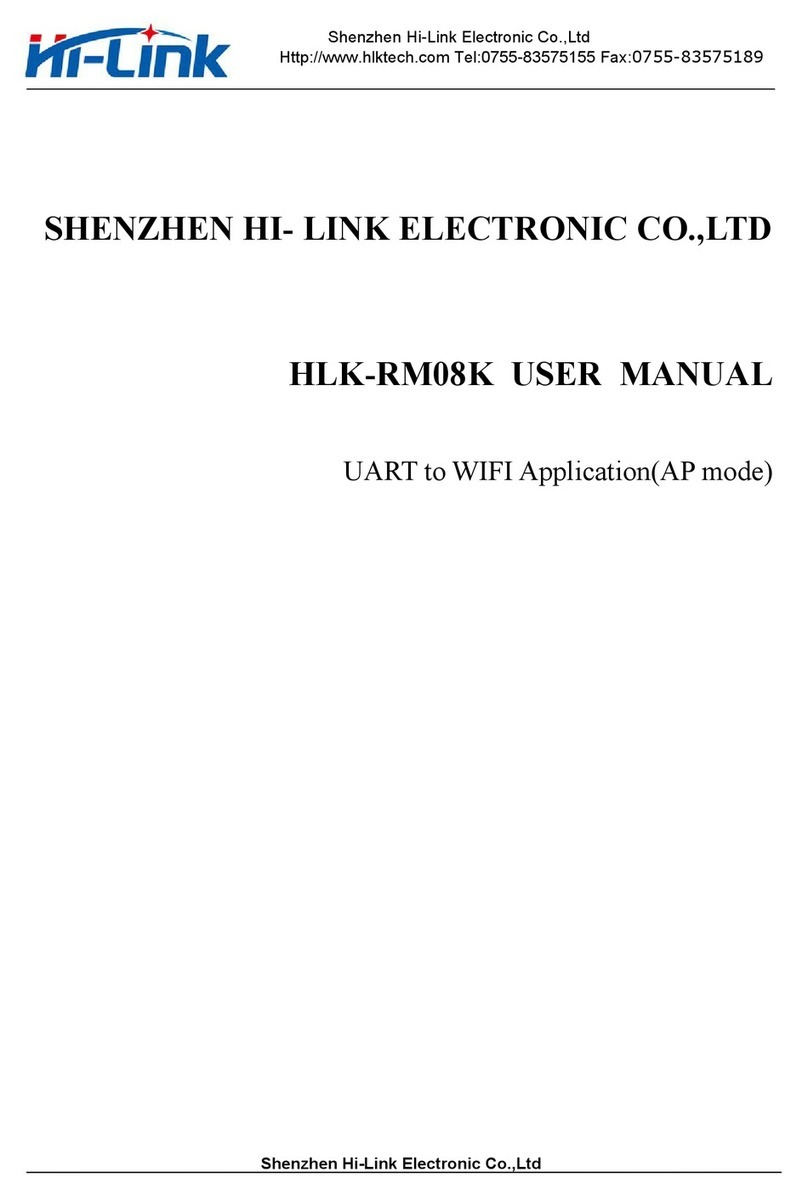
SHENZHEN HI- LINK ELECTRONIC
SHENZHEN HI- LINK ELECTRONIC HLK-RM08K user manual