Carlson Boretrak2 User manual

BT2 user manual - H-5911-9004-02-B December 2021
Boretrak2
Borehole deviation survey system
User manual
H-5911-9004-02-B


BT2 user manual - H-5911-9004-02-B Page | 3
Contents
INTRODUCTION................................................................................................................................................................................................4
1Customer information...................................................................................................................................................................5
2Boretrak2 system concepts ..........................................................................................................................................................7
OPERATIONAL GUIDE......................................................................................................................................................................................9
3Boretrak2 deployments – gyro introduction ................................................................................................................................10
4Boretrak2 deployments – geo-referencing..................................................................................................................................13
5Boretrak2 deployments – a typical project in the field .................................................................................................................15
HARDWARE ....................................................................................................................................................................................................34
6Boretrak2 hardware description..................................................................................................................................................35
7Regular checks and preventative maintenance ..........................................................................................................................54
SOFTWARE.....................................................................................................................................................................................................56
8Setting up Carlson Boretrak software on an Android device.......................................................................................................57
9Setting up Carlson Boretrak software on a Windows device.......................................................................................................63
10 Carlson Boretrak - Introduction ..................................................................................................................................................68
11 Touch mode – Home screen ......................................................................................................................................................69
12 Touch mode – screen layout ......................................................................................................................................................84
13 Menu tab....................................................................................................................................................................................92
14 Project tab .................................................................................................................................................................................96
15 Control tab ...............................................................................................................................................................................108
16 Desktop mode..........................................................................................................................................................................120
17 Android version........................................................................................................................................................................124
PRODUCT INFORMATION............................................................................................................................................................................127
18 Product specifications ..............................................................................................................................................................128
19 System information ..................................................................................................................................................................129
20 Carlson Boretrak End User License Agreement .......................................................................................................................133

BT2 user manual - H-5911-9004-02-B Page | 4
INTRODUCTION

BT2 user manual - H-5911-9004-02-B Page | 5
1 Customer information
1.1 Carlson Software
Congratulations on purchasing a Boretrak2 hole deviation surveying system from Carlson Software.
Founded in 1983, Carlson Software specializes in CAD design software, surveying hardware, and machine control
products for the land surveying, civil engineering, construction, and mining industries worldwide, providing one-
source technology solutions from data collection to design to construction.
The Boretrak2 is designed and built with Carlson’s world-class levels of detail, quality and innovation.
Carlson’s renowned dedication to customer service is unique in the industry.
For any technical support issues related to your Boretrak2 system contact us directly or, alternatively, contact your
local Carlson-approved service and support centre. Details of all contacts are on our website: www.carlsonsw.com.
To ensure the best service when contacting Carlson about your Boretrak2, please make a note of the serial number.
This can be found on the instrument (see Figure 33).
1.2 User manual
The Boretrak2 system is designed to be easy to operate. However, please take the time to read these operating
instructions carefully before using the system and always them with the instrument.
This manual is divided into three main parts:
•Boretrak2 hardware: a description of all elements of a Boretrak2 system and associated accessories.
•Field operational guide: a quick guide to show a typical use of the Boretrak2 and software in the field.
•Carlson Boretrak software: a detailed description of all functionality and controls in the accompanying
Carlson Boretrak software.
Carlson Boretrak software is integral to the operation of the Boretrak2. There are two versions of this software:
one runs on Windows tablets and PCs, the other runs on Android-based mobile devices. The software is described
in detail from section 10 onwards.
This manual is also available via the About screen in both versions of Carlson Boretrak.
This document has been compiled with care. However, should you discover any errors, we would be grateful if you
could contact Carlson directly.
Reproduction of this document in whole or in part, including utilisation in machines capable of reproduction or
retrieval, without the express written permission of Carlson is prohibited. Reverse engineering is also prohibited.
The information in this manual is subject to change without notice.
For any feedback or comments, or if there are questions about the Boretrak2 which are beyond the scope of this
manual, contact Carlson Software.
1.3 Notes on probes running version 1.0 firmware
The first generation of Boretrak2 probes run firmware version 1.0.

BT2 user manual - H-5911-9004-02-B Page | 6
Subsequent generations of probes with later versions of firmware feature an enhanced alignment routine with a
more robust solution generated throughout each deployment. They also feature improved power management and
the ability to upgrade to future firmware versions remotely, via Bluetooth.
On connection with Carlson Boretrak software, if your probe is identified as running version 1.0 firmware, a
message appears.
Carlson recommends that users with first generation probes upgrade to the most recent version of firmware.

BT2 user manual - H-5911-9004-02-B Page | 7
2 Boretrak2 system concepts
2.1 System overview
The Boretrak2 system is a portable, simple-to-use, borehole deviation measurement system which is valuable in
many applications such as underground mining, open pit mining, quarrying, and in a variety of civil engineering
applications.
The Boretrak2 probe is designed to survey the route of drilled boreholes by measuring their inclination and heading
at fixed intervals along the hole.
The Boretrak2 is based on previous iterations of the Cabled and Rodded Boretrak products. The features of both
old units are combined into a single all-purpose system, capable (Advanced model only) of measuring boreholes in
any inclination: down, up or horizontal.
The Boretrak2 utilises a miniature inertial measurement unit (IMU) which contains a triaxial accelerometer,
magnetometer, and gyro. Prior to deployment, the probe is aligned against a known orientation on a supplied jig.
This establishes a starting, reference heading for the gyro. The IMU provides the Boretrak2 with an accurate heading
and inclination.
The Boretrak2 probe is attached to a cable or push rods and deployed along a borehole. The system is deployed
at a series of fixed intervals, most commonly 2 m. IMU data is recorded at each interval as the probe is deployed
along the borehole.
In this way, the Boretrak2 builds up a 3D map of the borehole.
The Boretrak2 is not reliant on magnetic sensors and is therefore ideally suited for measuring boreholes where
there may be material present which would influence a compass.
The Boretrak2 system can be rapidly deployed on site, at any inclination, and requires no specialised tools or
equipment other than those supplied with the system.
2.2 Basic and Advanced models
The Boretrak2 is available in two models: Basic and Advanced. The two models are differentiated by the range of
inclinations over which they can operate.
The Basic model operates over a range of +/-60° from vertically down. This model is primarily designed for
applications such as quarrying and open pit mining where all holes are inclined downwards. Usually, Basic units
are deployed exclusively on the supplied steel cable.
The Advanced model operates at all inclinations. This model is designed for underground mining applications where
holes are drilled in all directions: downwards, horizontally, and upwards. The Advanced unit can also be deployed
with the steel cable when being used downhole. However, for horizontal and uphole operations, the push rod system
or Boretrak rods must be used.
Your Boretrak2 probe will have been set as a Basic or Advanced unit in the factory. If your probe is set as a Basic
unit, you can purchase an upgrade to convert it into an Advanced unit. Contact Carlson for details.
2.3 Data communication and storage
During a Boretrak survey, the operator configures and controls the Boretrak2 project via Carlson Boretrak software
which runs on a tablet or mobile device.
The Boretrak2 and the tablet running Carlson Boretrak communicate via a Bluetooth link. However, during a

BT2 user manual - H-5911-9004-02-B Page | 8
deployment, this link will usually be disconnected. Therefore, before deployment, the date and time in the probe are
synchronised with the date and time in the tablet. From this point, the probe starts recording IMU data into its internal
memory. Readings are taken every second and the probe’s LEDs visually indicate that this process is ongoing.
Each sensor record in the probe is accompanied by a time stamp.
At each deployment interval, with the system held steady, the operator on the surface records a time stamp using
Carlson Boretrak.
Once a survey has been completed, and the Boretrak2 is back on the surface, the Bluetooth link is re-established
and all IMU data from the probe is automatically downloaded to Carlson Boretrak.
Carlson Boretrak reads the time stamps recorded on the tablet and extracts the records in the probe data which
have matching time stamps.
With reference to a starting hole collar coordinate and an initial alignment heading, these raw observations are
converted into a sequence of X, Y, Z coordinates. A model of the hole is then created, and a comparison can be
made to a design hole or another survey of the same hole.
2.4 Carlson Boretrak software
Carlson Boretrak software acts as the survey controller which enables you to set up projects, manage holes,
conduct the survey, and view results.
Versions of Carlson Boretrak are available to run on a Windows tablet or an Android mobile device.
Carlson Boretrak displays real-time data from the probe while the Bluetooth connection is live. During a
deployment, the probe is in a borehole, so the connection is usually disconnected. The connection is automatically
re-established when a hole survey is complete, and the probe has been retrieved to within Bluetooth range of the
tablet.
After downloading data, a visual inspection of the hole survey is possible. You can compare the surveyed hole with
design data and export the project for use in other software packages from Carlson or in third party packages.
Carlson Boretrak allows you to manage the geo-referencing of the holes, and to send final data directly from the
field.
Back in the office Carlson Boretrak can run in Desktop mode on an office PC. This allows a more comprehensive
data analysis to be conducted, and reports and exports can be generated.

BT2 user manual - H-5911-9004-02-B Page | 9
OPERATIONAL GUIDE

BT2 user manual - H-5911-9004-02-B Page | 10
3 Boretrak2 deployments – gyro introduction
The Boretrak2 is fitted with an Inertial Measurement Unit (IMU) which incorporates a 3-axis MEMS-based gyro and
a 3-axis accelerometer.
The IMU integrates information from both the gyro and the accelerometer, and the output orientation is determined
by fusing the outputs of both these sensors through a software-based Kalman filter model.
The advanced IMU solution ensures that the attitude and orientation of the Boretrak2 probe can always be tracked
as it is deployed along a borehole, whether it is pointing up, down or horizontal.
3.1 Gyro drift
The results from a gyro may drift with time. If you lay a gyro flat and absolutely still, it will output a heading. If you
leave the gyro in exactly the same position, the raw heading that it outputs will gradually change, even though the
gyro is not changing position or rotating. This is ‘drift’ and it is effectively an error that will affect raw data output
from a gyro.
The results from a gyro may also drift with temperature, with severe temperature changes causing greater drift in
the gyro output.
Processing in the Boretrak2 firmware and Carlson Boretrak software helps to mitigate these effects on the gyro in
the installed IMU. The raw gyro drift over a given time is kept to a minimum and constant checks on the drift
throughout the deployment ensure that temperature changes are mostly accounted for. If the accelerometers detect
that the Boretrak2 is held static at any point, then the gyro is effectively locked so that any drift during this period is
ignored.
However, from the moment the Boretrak2 is first aligned, the accuracy of the gyro is slowly deteriorating due to an
accumulating angular error. This means that the deployment operation should be as prompt and efficient as
possible.
In ideal circumstances, during operations, the drift of the gyro will be <1.0° per 30 minutes.
Each time the Boretrak2 is aligned in a known orientation, any error is reset to zero. Therefore, it is worthwhile
realigning the probe as often as is practically possible during field operations.
3.2 Gyro alignment
The gyro in the Boretrak2 does not output a heading with respect to true north. The gyro can measure the angle
that it is rotated through as it is deployed or as it is moved around on the surface, but it cannot determine which
direction it is pointing in when it is switched on.
For this reason, we must manually define the starting, ‘reference’ heading of the probe at the beginning of an
operation. Once we have determined this starting orientation, the gyro can then keep track of the changing heading
as it is moved around and deployed.
After the Boretrak2 is powered ON, and before it is deployed, the unit must undergo an alignment which is when
this starting heading is established.
During the alignment the probe should be located within the operations area, ready for the deployment to
commence. The probe should be laid out horizontally (roughly +/- 20° from horizontal) on a solid, stable surface. An
alignment jig is supplied to provide an easy mounting point for the probe.
The alignment lasts approximately 3 seconds. During this period, the Boretrak2 probe must be motionless. Site the
probe away from areas where knocks or excessive vibration may occur. If movement is detected, the alignment

BT2 user manual - H-5911-9004-02-B Page | 11
may automatically restart multiple times before it is successfully completed.
If it is suspected that the probe has moved during the alignment, or that the readings from the probe seem to be
unstable immediately after the alignment, then it is essential to realign the probe.
For the purposes of a Boretrak2 survey, the reference heading is defined by the orientation of the probe, pointing
in the direction of the nose cone, while it is held static in the alignment jig.
Using traditional survey techniques, establish this heading with respect to your site coordinate system while the
probe is held static in the alignment jig.
The surveyed, starting heading is entered into Carlson Boretrak software in the Alignment window (see section
15.4).
If the jig is held securely in place, multiple, repeatable alignments can be taken from the same position between
Boretrak2 deployments down different boreholes. Also, if required, the jig can be left in place for a surveyor to
observe with their total station after the deployment has been completed. The jig heading can then be entered into
Carlson Boretrak retrospectively (see section 14.1.5).
Note that other customised hardware devices which perform the same function as the alignment jig may be used if
they are more suitable for your specific operations.
3.3 Gyro limits
The gyro is limited to measuring rates of rotation of up to 960°/sec in each axis. In practice this should not be a
limiting factor providing no sudden rotational accelerations are encountered or constant rotations of greater than
~1.1Hz are not encountered.
If the gyro does rotate beyond its current limit, in any axis, an out-of-range error will be displayed. In this case you
must retrieve and realign the probe before starting the deployment again.
Note that this error can only be registered by Carlson Boretrak while the Boretrak2 probe and tablet have a live
Bluetooth communications link established. If the rotation limit is exceeded while the probe is out of Bluetooth range
of the tablet, then the message appears as soon as the Bluetooth connection is restored.
Any data collected since the alignment was lost will be unreliable. Therefore, whenever this message appears, you
should realign the probe and repeat the survey of the hole(s) surveyed since the alignment was lost.
To avoid exceeding this rotational speed limit, once the Boretrak2 is aligned, handle the probe carefully and steadily
as it is being moved into the hole. During the deployment, lower the probe carefully and steadily. If you deploy the
probe on the steel cable alone, try to ensure as little rotation as possible is introduced through twist in the cable.
Figure 1 Gyro exceeded rotational speed limit

BT2 user manual - H-5911-9004-02-B Page | 12
3.4 Gyro check
After the probe is retrieved from the hole it is possible to perform a gyro check to confirm that the dynamics, shocks
and rotations experienced during the deployment have not caused the gyro to drift or lose accuracy.
As long as the Broretrak2 is still aligned, place the probe back on the alignment jig and select Align > Verify
Alignment. An error factor is displayed to give an indication of the change in angle during the survey. See section
15.2.2.

BT2 user manual - H-5911-9004-02-B Page | 13
4 Boretrak2 deployments – geo-referencing
4.1 Georeferencing a survey
When using the Boretrak2 system, it is usually the case that the absolute position and orientation of the surveyed
hole will be required. For example, if deviation is detected in the borehole, in which direction is it inclined and how
does this relate to other features above or below the ground?
To establish the position and orientation of the surveyed data, two values are required:
1. The position of the borehole collar.
2. The orientation of the probe during the gyro alignment.
With these two values established, when the Boretrak2 probe is deployed down the borehole, all subsequent
readings can be related back to the starting position and orientation. The surveyed hole can also be referenced to
any other features surveyed on the same coordinate system: for example, a quarry face or an underground tunnel.
4.2 Position of the borehole
The position of the borehole can be established by:
•GPS.
•Traditional survey methods.
•A Carlson Quarryman Pro. The Quarryman Pro is used in quarrying operations to scan a quarry face and
to position borehole collars.
If the collar is very wide and uneven, take care to survey to the exact point from which the deployment is to be
measured.
4.3 Orientation and positioning of the alignment jig
Find a location for the alignment jig. The location must be close enough to the collar so that the Boretrak2 can be
promptly deployed when the alignment is complete.
The location should be solid and not subject to movement or vibrations. Ensure the jig is roughly horizontal (ie.
within 20° of level).
It is important to minimise handling of the Boretrak2 probe between the alignment and deployment. Therefore, if
convenient, keep the deployment device attached to the probe while it is being aligned. This may influence where
you choose to position the alignment jig, particularly if using the push rod system for deployments.
The heading of the Boretrak2 in the jig must be entered into Carlson Boretrak. The heading is that which is defined
by the direction of the Boretrak2 from the rod adaptor to the tip of the nose cone (see Figure 2).
This heading can be established by:
•A direct survey of the jig using traditional survey methods.
•Aligning the jig along a line of known azimuth – eg. along the centre of a tunnel underground, or along a
shotline in a quarry.
•Aligning the jig between two points with known coordinates – eg. between two surveyed hole collars. The
heading between the two holes can be computed in Carlson Boretrak software.

BT2 user manual - H-5911-9004-02-B Page | 14
•A good-quality, hand-held compass. This is the least accurate option. Stand behind the alignment jig and
take a compass bearing looking along the jig in the direction that the probe is, or will be, pointing. If using a
magnetic compass, ensure that the immediate area is free from external magnetic influences, such as drill
rigs or mobile phones.
Note that if a compass is used, the measured bearing will be relative to magnetic north. The relationship
between the magnetic bearing from the compass and any local grid north that is used for other survey data
will need to be established if data from the Boretrak2 is to be used in conjunction with data from other
systems such as GPS or the Quarryman Pro.
Note that the heading of the alignment jig is independent from the direction of the hole being surveyed. The
measured heading provides a starting reference for the survey. Once the gyro is aligned in this heading, the gyro
tracks any subsequent changes of orientation.
Establishing the reference heading of the jig can take place at any time before or after the deployment. As long as
the alignment jig is not moved between aligning the gyro and surveying the heading, you can establish the reference
heading when the Boretrak2 survey is not in progress.
Figure 2 Surveyed heading of the alignment jig

BT2 user manual - H-5911-9004-02-B Page | 15
5 Boretrak2 deployments – a typical project in the field
The procedure outlined below is a ‘quick start guide’ to using a Boretrak2 in the field.
The methodology is based around a borehole survey on a quarry. The project includes importing design holes into
the Carlson Boretrak project. The alignment jig is orientated during the survey by physically aligning it between
pre-surveyed holes. The project is run on a Windows tablet.
5.1 Preparing for the survey
Before your survey, ensure that the correct deployment device for your project has been determined. This will be
based on the inclination and length of the holes to be surveyed. In the case below, the holes are all near vertically
downwards and so the standard steel cable is used.
Ensure that all batteries – in your tablet & in the Boretrak2 probe – are fully charged before starting a project.
Place the rechargeable batteries into the Boretrak2 nose cone and screw the nose cone securely onto the probe.
The Boretrak2 is now ON.
The probe LEDs start by showing solid yellow while the power is stabilising. They progress to flashing blue if there
has been no Bluetooth connection, or flashing red if there has been a Bluetooth connection.
On your tablet, ensure Bluetooth is turned ON and that the Boretrak2 probe is already paired with the tablet (see
section 9.5).
5.2 Setting up Carlson Boretrak
5.2.1 New project
Open Carlson Boretrak software. Tap New to start a new project.
Figure 3 Touch mode Home screen

BT2 user manual - H-5911-9004-02-B Page | 16
The Project window opens.
Enter a Project Name. Enter the Surveyor and any Notes as required.
5.2.2 Import design holes
To import holes into the project, select the Holes tab, then Import.
The Browse window appears. Navigate to find the file containing the design holes. These may be in the form of a
standard ASCII text file such a *.TXT or *.CSV file, or else a Carlson *.DRL file.
Figure 4 New project window
Figure 5 Project window > Holes tab

BT2 user manual - H-5911-9004-02-B Page | 17
DRL files import directly into Carlson Boretrak.
To import holes from an ASCII text file, the ASCII Import window appears. Pre-defined import formats can be setup
so that the file is directly imported into Carlson Boretrak. When importing for the first time, manually assign fields
for the data in the *.CSV file. Tap on the header of a column then select the appropriate field from the Data drop
down list.
After defining the last column, click Confirm, then Import.
Figure 6 Import hole file
Figure 7 ASCII Import window

BT2 user manual - H-5911-9004-02-B Page | 18
The design holes are loaded into the project. They are visible in the 3D View, listed in the Project window Holes
tab, and also appear in the Project tab.
Tap Create to create the new project.
5.2.3 Connection
On creation of a new project, Carlson Boretrak automatically starts searching for a paired Boretrak within
communication range.
Figure 8 ASCII Import window > completing the import
Figure 9 Project window > Holes tab

BT2 user manual - H-5911-9004-02-B Page | 19
When Carlson Boretrak connects to the probe, the Control tab is populated with Boretrak controls.
If no connection is made, check:
•The Boretrak2 probe is powered ON and flashing red or blue.
•The Boretrak2 is paired to your tablet.
•Bluetooth is switched ON on your tablet.
•No other devices are connected to the same Boretrak2 probe.
Tap Find Boretraks to reattempt a connection.
5.3 Alignment
The survey will start at Hole 1. Position the alignment jig so that it is lined up between Hole 1 and Hole 2 (see Figure
11). Ensure the jig is on solid ground and reasonably close to level (i.e.: within 20 degrees).
Connect the steel cable securely to the Boretrak2 probe using the deployment adaptor (see section 6.6).
Position your probe in the supplied jig. The probe can be rolled around its axis in any rotation, but the nosecone
must point towards Hole 2.
Figure 10 Connecting to a Boretrak2

BT2 user manual - H-5911-9004-02-B Page | 20
Hole 2
Hole 1
Boretrak2 on
alignment jig
Heading computed
from hole 1 to hole 2
Steel cable attached
to Boretrak2 probe
Figure 11 The probe in the alignment jig aligned between two holes
Figure 12 Probe held in the alignment jig
Other manuals for Boretrak2
1
Table of contents
Other Carlson Measuring Instrument manuals
Popular Measuring Instrument manuals by other brands
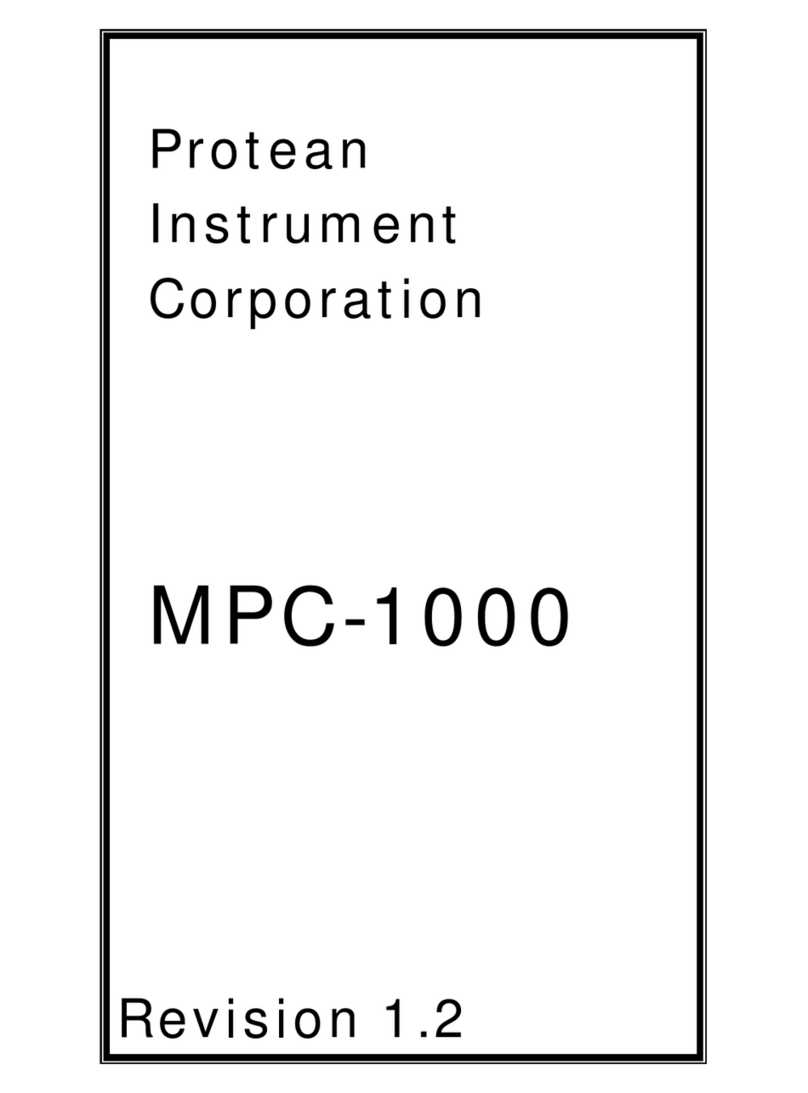
Protean Instrument
Protean Instrument MPC-1000 series user manual
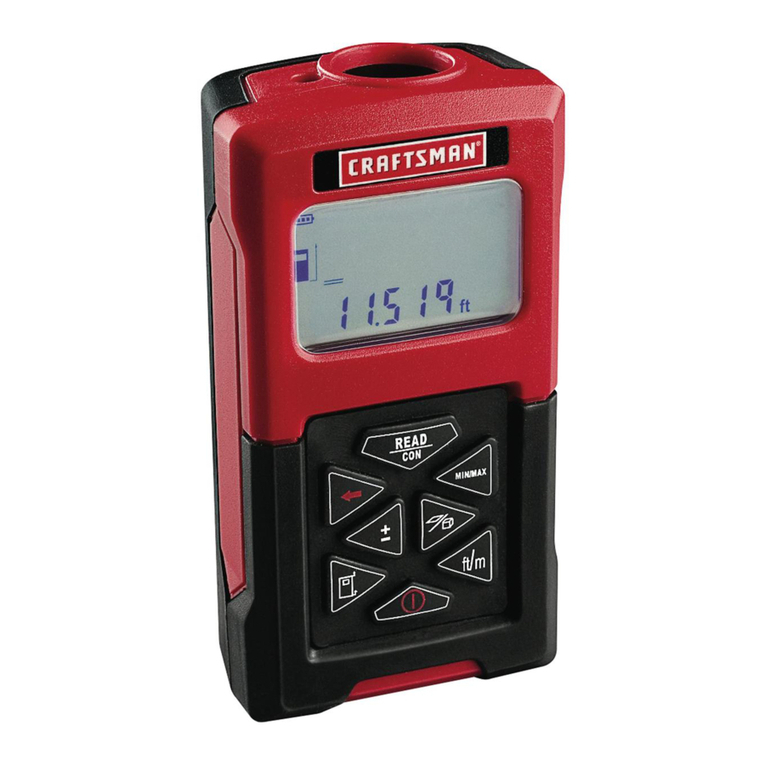
Craftsman
Craftsman 320.48277 owner's manual

KROHNE
KROHNE OPTIWAVE 6300 C quick start

Katronic
Katronic KATflow 210 operating instructions
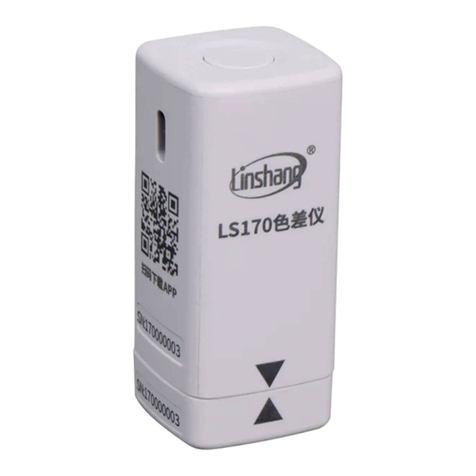
LINSHANG
LINSHANG LS170 user manual
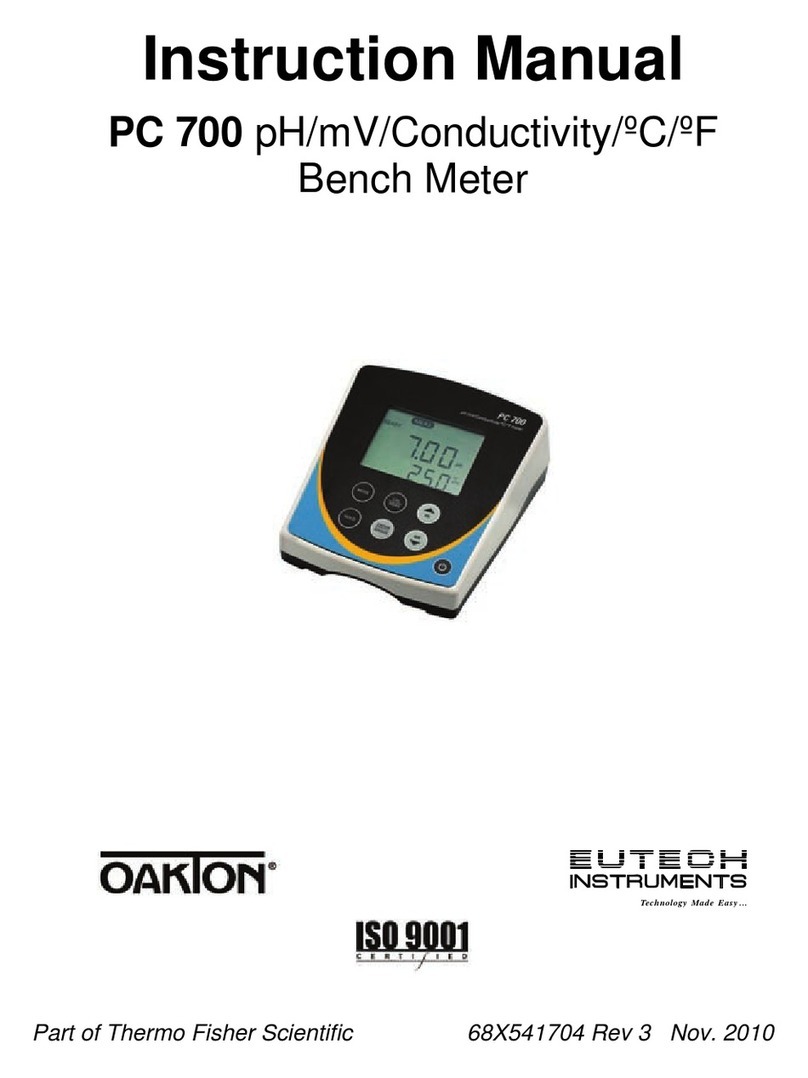
EUTECH INSTRUMENTS
EUTECH INSTRUMENTS PC 700 - REV 3 instruction manual