Celerity UNIT 122 Series User manual

Artisan Technology Group is your source for quality
new and certied-used/pre-owned equipment
• FAST SHIPPING AND
DELIVERY
• TENS OF THOUSANDS OF
IN-STOCK ITEMS
• EQUIPMENT DEMOS
• HUNDREDS OF
MANUFACTURERS
SUPPORTED
• LEASING/MONTHLY
RENTALS
• ITAR CERTIFIED
SECURE ASSET SOLUTIONS
SERVICE CENTER REPAIRS
Experienced engineers and technicians on staff
at our full-service, in-house repair center
WE BUY USED EQUIPMENT
Sell your excess, underutilized, and idle used equipment
We also offer credit for buy-backs and trade-ins
www.artisantg.com/WeBuyEquipment
REMOTE INSPECTION
Remotely inspect equipment before purchasing with
our interactive website at www.instraview.com
LOOKING FOR MORE INFORMATION?
Visit us on the web at www.artisantg.com for more
information on price quotations, drivers, technical
specications, manuals, and documentation
Contact us: (888) 88-SOURCE | sales@artisantg.com | www.artisantg.com
SM
View
Instra

Analog and Digital
Mass Flow Controllers and Meters
User’s Manual
©2005 Celerity, Inc. #199-001-0006 REV.F 4/05
Artisan Technology Group - Quality Instrumentation ... Guaranteed | (888) 88-SOURCE | www.artisantg.com

Contents
1. OVERVIEW . . . . . . . . . . . . . . . . . . . . . . . . . . . . . . . . . . . . . . . . . . . . . . . . . . . . . . . . . . . . . . . . . 1
1.1 Flow Controller / Flow Meter Model Designations . . . . . . . . . . . . . . . . . . . . . . . . . . . . . . . . . . . . . . . 1
1.2 Flow Controller / Flow Meter Model Designations, by Applications. . . . . . . . . . . . . . . . . . . . . . . . . . . 1
2. STANDARD FEATURES . . . . . . . . . . . . . . . . . . . . . . . . . . . . . . . . . . . . . . . . . . . . . . . . . . . . . . . . 2
2.1 Attitude . . . . . . . . . . . . . . . . . . . . . . . . . . . . . . . . . . . . . . . . . . . . . . . . . . . . . . . . . . . . . . . . . . . . . . 2
2.2 Calibration Conditions. . . . . . . . . . . . . . . . . . . . . . . . . . . . . . . . . . . . . . . . . . . . . . . . . . . . . . . . . . . . 2
2.3 Standard Temperature and Pressure . . . . . . . . . . . . . . . . . . . . . . . . . . . . . . . . . . . . . . . . . . . . . . . . 2
2.4 Calibration Traceability . . . . . . . . . . . . . . . . . . . . . . . . . . . . . . . . . . . . . . . . . . . . . . . . . . . . . . . . . . . 2
2.5 Manufacturing Environment . . . . . . . . . . . . . . . . . . . . . . . . . . . . . . . . . . . . . . . . . . . . . . . . . . . . . . . 2
2.6 Purge Capability . . . . . . . . . . . . . . . . . . . . . . . . . . . . . . . . . . . . . . . . . . . . . . . . . . . . . . . . . . . . . . . . 2
3. OPTIONAL FEATURES. . . . . . . . . . . . . . . . . . . . . . . . . . . . . . . . . . . . . . . . . . . . . . . . . . . . . . . . . 2
3.1 Auto Shut-off Option. . . . . . . . . . . . . . . . . . . . . . . . . . . . . . . . . . . . . . . . . . . . . . . . . . . . . . . . . . . . . 2
3.2 Response Time Options . . . . . . . . . . . . . . . . . . . . . . . . . . . . . . . . . . . . . . . . . . . . . . . . . . . . . . . . . . 2
3.3 Connector Options . . . . . . . . . . . . . . . . . . . . . . . . . . . . . . . . . . . . . . . . . . . . . . . . . . . . . . . . . . . . . . 3
3.4 Special Adapters . . . . . . . . . . . . . . . . . . . . . . . . . . . . . . . . . . . . . . . . . . . . . . . . . . . . . . . . . . . . . . . 3
3.5 Valve Options . . . . . . . . . . . . . . . . . . . . . . . . . . . . . . . . . . . . . . . . . . . . . . . . . . . . . . . . . . . . . . . . . . 3
3.6 Flow Direction Options . . . . . . . . . . . . . . . . . . . . . . . . . . . . . . . . . . . . . . . . . . . . . . . . . . . . . . . . . . . 3
3.7 Auto-Zero Option . . . . . . . . . . . . . . . . . . . . . . . . . . . . . . . . . . . . . . . . . . . . . . . . . . . . . . . . . . . . . . . 3
3.8 Fittings Options . . . . . . . . . . . . . . . . . . . . . . . . . . . . . . . . . . . . . . . . . . . . . . . . . . . . . . . . . . . . . . . . 4
4. POWER SUPPLIES . . . . . . . . . . . . . . . . . . . . . . . . . . . . . . . . . . . . . . . . . . . . . . . . . . . . . . . . . . . 4
5. PRODUCT DRAWINGS. . . . . . . . . . . . . . . . . . . . . . . . . . . . . . . . . . . . . . . . . . . . . . . . . . . . . . . . . 4
6. PRODUCT SPECIFICATIONS . . . . . . . . . . . . . . . . . . . . . . . . . . . . . . . . . . . . . . . . . . . . . . . . . . . . 4
6.1 MFC side can label . . . . . . . . . . . . . . . . . . . . . . . . . . . . . . . . . . . . . . . . . . . . . . . . . . . . . . . . . . . . . 4
6.2 Traceability . . . . . . . . . . . . . . . . . . . . . . . . . . . . . . . . . . . . . . . . . . . . . . . . . . . . . . . . . . . . . . . . . . . 5
7. INSTALLATION . . . . . . . . . . . . . . . . . . . . . . . . . . . . . . . . . . . . . . . . . . . . . . . . . . . . . . . . . . . . . . 5
7.1 Unpacking . . . . . . . . . . . . . . . . . . . . . . . . . . . . . . . . . . . . . . . . . . . . . . . . . . . . . . . . . . . . . . . . . . . . 5
7.2 Purging before Installing the MFC. . . . . . . . . . . . . . . . . . . . . . . . . . . . . . . . . . . . . . . . . . . . . . . . . . . 5
7.3 Positioning the Controller . . . . . . . . . . . . . . . . . . . . . . . . . . . . . . . . . . . . . . . . . . . . . . . . . . . . . . . . . 5
7.4 Mounting the Controller . . . . . . . . . . . . . . . . . . . . . . . . . . . . . . . . . . . . . . . . . . . . . . . . . . . . . . . . . . 6
7.5 Connecting to gas supply line . . . . . . . . . . . . . . . . . . . . . . . . . . . . . . . . . . . . . . . . . . . . . . . . . . . . . . 6
©2005 Celerity, Inc. #199-001-0006 REV.F 4/05
Artisan Technology Group - Quality Instrumentation ... Guaranteed | (888) 88-SOURCE | www.artisantg.com

8. ELECTRICAL CONNECTIONS . . . . . . . . . . . . . . . . . . . . . . . . . . . . . . . . . . . . . . . . . . . . . . . . . . . . 6
8.1 Voltage and Pinouts . . . . . . . . . . . . . . . . . . . . . . . . . . . . . . . . . . . . . . . . . . . . . . . . . . . . . . . . . . . . . 6
8.2 Connections to a Power Supply . . . . . . . . . . . . . . . . . . . . . . . . . . . . . . . . . . . . . . . . . . . . . . . . . . . . 7
8.3 Warm Up . . . . . . . . . . . . . . . . . . . . . . . . . . . . . . . . . . . . . . . . . . . . . . . . . . . . . . . . . . . . . . . . . . . . . 7
9. MULTIFLO VIRTUAL INTERFACE . . . . . . . . . . . . . . . . . . . . . . . . . . . . . . . . . . . . . . . . . . . . . . . . . 7
9.1 Features. . . . . . . . . . . . . . . . . . . . . . . . . . . . . . . . . . . . . . . . . . . . . . . . . . . . . . . . . . . . . . . . . . . . . . 7
9.2 Configure the DMFC for Networking . . . . . . . . . . . . . . . . . . . . . . . . . . . . . . . . . . . . . . . . . . . . . . . . . 7
10. OPERATION AND PERFORMANCE CHECKS . . . . . . . . . . . . . . . . . . . . . . . . . . . . . . . . . . . . . . . . 8
10.1 Automatic Zero Initialization . . . . . . . . . . . . . . . . . . . . . . . . . . . . . . . . . . . . . . . . . . . . . . . . . . . . . . 8
10.2 Proper Sequencing. . . . . . . . . . . . . . . . . . . . . . . . . . . . . . . . . . . . . . . . . . . . . . . . . . . . . . . . . . . . . 8
10.3 Leak Test . . . . . . . . . . . . . . . . . . . . . . . . . . . . . . . . . . . . . . . . . . . . . . . . . . . . . . . . . . . . . . . . . . . . 8
10.4 Purge. . . . . . . . . . . . . . . . . . . . . . . . . . . . . . . . . . . . . . . . . . . . . . . . . . . . . . . . . . . . . . . . . . . . . . . 8
10.4.1 Non-Reactive Gases: . . . . . . . . . . . . . . . . . . . . . . . . . . . . . . . . . . . . . . . . . . . . . . . . . . . . . . . . . . 9
10.4.2 Reactive Gases:. . . . . . . . . . . . . . . . . . . . . . . . . . . . . . . . . . . . . . . . . . . . . . . . . . . . . . . . . . . . . . 9
10.5 Zero Check . . . . . . . . . . . . . . . . . . . . . . . . . . . . . . . . . . . . . . . . . . . . . . . . . . . . . . . . . . . . . . . . . . 9
10.6 Full Flow Check . . . . . . . . . . . . . . . . . . . . . . . . . . . . . . . . . . . . . . . . . . . . . . . . . . . . . . . . . . . . . . 10
10.7 Flow Control Response Check . . . . . . . . . . . . . . . . . . . . . . . . . . . . . . . . . . . . . . . . . . . . . . . . . . . 10
10.8 Calibration Check . . . . . . . . . . . . . . . . . . . . . . . . . . . . . . . . . . . . . . . . . . . . . . . . . . . . . . . . . . . . . 10
11. TROUBLESHOOTING. . . . . . . . . . . . . . . . . . . . . . . . . . . . . . . . . . . . . . . . . . . . . . . . . . . . . . . . 11
11.1 Environmental Factors . . . . . . . . . . . . . . . . . . . . . . . . . . . . . . . . . . . . . . . . . . . . . . . . . . . . . . . . . 11
11.2 MFC Troubleshooting Checklist. . . . . . . . . . . . . . . . . . . . . . . . . . . . . . . . . . . . . . . . . . . . . . . . . . . 11
12. REMOVAL. . . . . . . . . . . . . . . . . . . . . . . . . . . . . . . . . . . . . . . . . . . . . . . . . . . . . . . . . . . . . . . . 12
12.1 Purging before removing the MFC . . . . . . . . . . . . . . . . . . . . . . . . . . . . . . . . . . . . . . . . . . . . . . . . 12
12.2 Removing the MFC. . . . . . . . . . . . . . . . . . . . . . . . . . . . . . . . . . . . . . . . . . . . . . . . . . . . . . . . . . . . 12
12.3 Packaging the MFC . . . . . . . . . . . . . . . . . . . . . . . . . . . . . . . . . . . . . . . . . . . . . . . . . . . . . . . . . . . 12
12.4 Un-Packaging . . . . . . . . . . . . . . . . . . . . . . . . . . . . . . . . . . . . . . . . . . . . . . . . . . . . . . . . . . . . . . . 12
12.5 Cleaning. . . . . . . . . . . . . . . . . . . . . . . . . . . . . . . . . . . . . . . . . . . . . . . . . . . . . . . . . . . . . . . . . . . . 12
12.6 Shipping. . . . . . . . . . . . . . . . . . . . . . . . . . . . . . . . . . . . . . . . . . . . . . . . . . . . . . . . . . . . . . . . . . . . 12
12.7 Shipping Costs . . . . . . . . . . . . . . . . . . . . . . . . . . . . . . . . . . . . . . . . . . . . . . . . . . . . . . . . . . . . . . . 13
12.8 Returned Material Authorizations (RMA). . . . . . . . . . . . . . . . . . . . . . . . . . . . . . . . . . . . . . . . . . . . 13
12.9 Documentation. . . . . . . . . . . . . . . . . . . . . . . . . . . . . . . . . . . . . . . . . . . . . . . . . . . . . . . . . . . . . . . 13
13. MAINTENANCE. . . . . . . . . . . . . . . . . . . . . . . . . . . . . . . . . . . . . . . . . . . . . . . . . . . . . . . . . . . . 13
13.1 Emergency Service. . . . . . . . . . . . . . . . . . . . . . . . . . . . . . . . . . . . . . . . . . . . . . . . . . . . . . . . . . . . 13
13.2 Routine Maintenance . . . . . . . . . . . . . . . . . . . . . . . . . . . . . . . . . . . . . . . . . . . . . . . . . . . . . . . . . . 13
13.3 Factory Calibration and Service. . . . . . . . . . . . . . . . . . . . . . . . . . . . . . . . . . . . . . . . . . . . . . . . . . . 13
13.4 Field Service . . . . . . . . . . . . . . . . . . . . . . . . . . . . . . . . . . . . . . . . . . . . . . . . . . . . . . . . . . . . . . . . 13
13.5 Technical Support . . . . . . . . . . . . . . . . . . . . . . . . . . . . . . . . . . . . . . . . . . . . . . . . . . . . . . . . . . . . 14
©2005 Celerity, Inc. #199-001-0006 REV.F 4/05
Artisan Technology Group - Quality Instrumentation ... Guaranteed | (888) 88-SOURCE | www.artisantg.com

14. WARRANTY. . . . . . . . . . . . . . . . . . . . . . . . . . . . . . . . . . . . . . . . . . . . . . . . . . . . . . . . . . . . . . . 14
15. WEB SITE TECHNICAL RESOURCES . . . . . . . . . . . . . . . . . . . . . . . . . . . . . . . . . . . . . . . . . . . . 14
16. APPENDICES . . . . . . . . . . . . . . . . . . . . . . . . . . . . . . . . . . . . . . . . . . . . . . . . . . . . . . . . . . . . . 15
16.1 Connector Pinouts . . . . . . . . . . . . . . . . . . . . . . . . . . . . . . . . . . . . . . . . . . . . . . . . . . . . . . . . . . . . 15
16.2 Setting The MFC/MFM Zero . . . . . . . . . . . . . . . . . . . . . . . . . . . . . . . . . . . . . . . . . . . . . . . . . . . . . 18
16.3 9000 Series Supplement . . . . . . . . . . . . . . . . . . . . . . . . . . . . . . . . . . . . . . . . . . . . . . . . . . . . . . . 20
16.4 Troubleshooting Guide . . . . . . . . . . . . . . . . . . . . . . . . . . . . . . . . . . . . . . . . . . . . . . . . . . . . . . . . . 24
16.5 DeviceNet Operations LEDs . . . . . . . . . . . . . . . . . . . . . . . . . . . . . . . . . . . . . . . . . . . . . . . . . . . . . 26
16.6 Manufacturing, Sales, and Service Locations . . . . . . . . . . . . . . . . . . . . . . . . . . . . . . . . . . . . . . . . 27
16.7 Auto-Zero Feature (for Analog Mass Flow Controllers). . . . . . . . . . . . . . . . . . . . . . . . . . . . . . . . . . 28
©2005 Celerity, Inc. #199-001-0006 REV.F 4/05
Artisan Technology Group - Quality Instrumentation ... Guaranteed | (888) 88-SOURCE | www.artisantg.com

1
1. OVERVIEW
Celerity Mass Flow Controllers precisely monitor and control the mass flow of gases in processes
such as Plasma Etching, CVD, Diffusion, EPI, and Sputtering where superior accuracy is required.
Mass Flow Meters are identical to mass flow controllers, except that they do not have a controlling
valve. Therefore they do not control, but only accurately measure and report the gas flow that is
passing through them.
1.1 Flow Controller / Flow Meter Model Designations
Unit Mass Flow Controller models have the prefix of “UFC-“ (Unit Flow Controller), and Mass
Flow Meters have the prefix of “UFM-” (Unit Flow Meter).
Mass Flow Controllers: UFC-XXXX (Unit Flow Controller)
Mass Flow Meters: UFM-XXXX (Unit Flow Meter)
1.2 Flow Controller / Flow Meter Model Designations, by Applications
Table 1 shows the general applicability of each model covered by this manual.
Table 1. Model Designations by applications
Elastomer Seal Products - 32 µin Ra Finish
122 series Control Valves 1.1" 10 sccm - 30 slm 122
180 series Standard Flow Applications 1" 10 sccm - 30 slm 180HS /180HA
7300 series Standard Flow Applications 1.5" 10 sccm - 30 slm 7301 7304 7300
7320 series Standard Flow w/ Auto Shutoff 1.5" 10 sccm - 30 slm 7321 7324 7320
8100 series Standard Flow Applications 1.5" 10 sccm - 30 slm 8101 8105 8100
8130 series Setpoint Pressure Control 1.5" 10 sccm - 30 slm 8130
High Purity Metal Seal Products - 10 or 16 µin Ra Finish
132 series Control Valves 1.42" 10 sccm - 30 slm 132
1551 series Standard Flow Applications 1.5" 30 sccm - 6 slm 1551
1630 series Setpoint Pressure Control 1.5" 10 sccm - 30 slm 1630
1660 series Standard Flow Applications 1.5" 10 sccm - 30 slm 1661 1665 1660
1660 SDS series Safe Delivery Source 1.5" 10 sccm - 30 slm 1663 1664 1662/1662L
3160 series High Flow Applications 1.5" 30 slm - 100 slm 3161 3165
5360 series High Flow Applications 1.5" 30 slm - 100 slm 5361 5365
7360 series Standard Flow Applications 1.5" 10 sccm - 30 slm 7361 7364 7360
9660 series High Temperature Applications 1.5" 10 sccm - 30 slm 9660
Ultra High Purity Metal Seal Products - 4 µin Ra Finish
8160 series Standard Flow Applications 1.5" 10 sccm - 30 slm 8161 8165 8160
8160 SDS series Safe Delivery Source 1.5" 10 sccm - 30 slm 8163 8164 8162/8162L
8260 series Standard Flow Applications 1.5" mini 10 sccm - 30 slm 8261 8260
8560 series Standard Flow Applications 1.125" 10 sccm - 30 slm 8561 8565
8560 SDS series Safe Delivery Source 1.125" 10 sccm - 30 slm 8563 8564
9500 series High Temperature Applications 1.125" 10 sccm - 30 slm 9561 9565
9860 series High Temperature Applications 1.5" 10 sccm - 30 slm 9861 9865
Footprint
Full Scale
Flow Range
(Min - Max)
<Digital>
RS485
Analog
<Digital>
DeviceNet™
PROFIBUS
<Analog>
Analog
Protocol
Category / Model Family
©2005 Celerity, Inc. #199-001-0006 REV.F 4/05
Artisan Technology Group - Quality Instrumentation ... Guaranteed | (888) 88-SOURCE | www.artisantg.com

2
2. STANDARD FEATURES
2.1 Attitude
- Each MFC is built for a specific attitude either HOS (Horizontal on Side) or HOV (Horizontal
or Vertical).
- For further details, refer to Section 7.3 “Mounting Attitude”.
2.2 Calibration Conditions
- MFCs ordered as “Atmosphere” are calibrated with the MFC’s outlet exhausting to
Atmosphere.
- MFCs ordered as “Vacuum” are calibrated with the MFC’s outlet exhausting to Vacuum.
2.3 Standard Temperature and Pressure
- 0°C and 760 mm Hg
2.4 Calibration Traceability
- National Institute of Standards and Technology (N.I.S.T.)
2.5 Manufacturing Environment
- Assembled, Calibrated, Tested and Packaged in Class 100 Cleanroom Environment
2.6 Purge Capability
- Full purge capability with 1 slm purge minimum (depends on gas density and pressure).
3. OPTIONAL FEATURES
Options are set at the factory, unless otherwise specified.
3.1 Auto Shut-off Option
- With the Auto Shut-off option a setpoint command of less than 2% (0.1 VDC) closes the
MFC control valve.
- Since an MFC valve is not a positive shutoff valve, a shutoff valve in series with the MFC
may be needed.
- Users of digital MFCs can disable or increase the Auto Shutoff option to any value up to a
maximum of 10% of the full scale operational range using the MultiFlo Virtual Interface.
(Refer to the MultiFlo Virtual Interface User’s Manual.)
3.2 Response Time Options
Fast: ≤1 Sec to a setpoint command of 20%-100% (per SEMI E17-91)
Soft Start: Ramping gradually (5 second linear ramp)
Soft start options: 4-6, 6-10, 10-15, 20-30, or 40-60 seconds.
- This option is configured in the factory for analog MFCs, and cannot be adjusted by the
user.
Users of digital MFCs can select the Response Time to be 0-20 seconds using the MultiFlo
Virtual Interface. (Refer to the Details section of the MultiFlo Virtual Interface User’s Manual.)
©2005 Celerity, Inc. #199-001-0006 REV.F 4/05
Artisan Technology Group - Quality Instrumentation ... Guaranteed | (888) 88-SOURCE | www.artisantg.com

3
3.3 Connector Options
The electrical connector configurations are shown in Appendice 16.1, “Electrical
Connections”. This includes detailed information and pinouts.
3.4 Special Adapters
Retrofitting of the models of most competitors is accomplished using special electronic and
mechanical adapters. Contact Celerity’s Applications Engineering department for help with
your particular requirement.
3.5 Valve Options
The valve is configured at the time of manufacture to be Normally Closed or Normally Open,
and is not user modifiable.
- Normally-closed (standard): The valve is closed when there is no power applied to the unit.
- Normally-open (optional): The valve is fully open when there is no power applied to the
unit.
3.6 Flow Direction Options
There are two configurations of Flow Direction, and this is not user modifiable.
- “Standard”:
- The sensor is upstream and the valve is downstream.
- The valve buffers the sensor from downstream (process) pressure fluctuations.
- “Pressure buffered”:
- The valve is upstream and the sensor is downstream.
- The valve buffers the sensor from upstream pressure fluctuations.
3.7 Auto-Zero Option
- The Auto-Zero feature detects zero offset during no-flow conditions and electronically
re-zeros the output signal.
- Auto-Zero, on earlier Unit models, was of great benefit in reducing drift and increasing
equipment uptime.
- However, the current sensor models have a drift specification of less than .6% per year.
- The proper application of the Auto-Zero option depends entirely on the ability to ensure
absolutely no flow across the MFC sensor during the Auto-Zero cycle.
- With few exceptions, this means that there must be positive shutoff valves immediately
upstream and downstream of the MFC, and that there must be proper valve sequencing.
- All Digital Mass Flow Controllers have Auto-Zero circuitry installed, which can be enabled or
disabled using the MultiFlo Virtual Interface. (Refer to the MultiFlo Virtual Interface User’s
Manual.)
- For a more complete explanation of the the Auto-Zero Feature see Appendice 16.7.
- If you have any questions regarding the ordering or installing of an MFC with the Auto-Zero
feature please consult Applications Engineering first.
©2005 Celerity, Inc. #199-001-0006 REV.F 4/05
Artisan Technology Group - Quality Instrumentation ... Guaranteed | (888) 88-SOURCE | www.artisantg.com

4
3.8 Fittings Options
The fittings available for these units are:
- Swagelok®, VCR®, VCO®
- C-seal and W-seal surface-mount
- Ultraseal, Buttweld and Specials
Not all fittings are available for all gases and ranges. Fitting options will vary according to the
MFC model.
4. POWER SUPPLIES
Celerity manufactures a series of analog and digital power supplies. These are capable of
monitoring and/or controlling from 1 to 5 mass flow controllers or meters simultaneously. Call
Celerity Customer Service for further information.
5. PRODUCT DRAWINGS
You can access and download a product drawing for any specific model of mass flow controller
(MFC) via www.celerity.net (http://www.celerity.net/html/products/technical_data/drawings).
6. PRODUCT SPECIFICATIONS
You can access and download the exact product specifications for any specific model, via
www.celerity.net (http://www.celerity.net/html/products/literature/literature.html)
6.1 MFC side can label
MFC side can labels carry a detailed listing of all information about a specific MFCs statistics
as built at the factory.
Figure 1. MFC Side Can Label with Explanations
1. MFC Model Number
2. Nameplate Gas and Range
3. Customer Part Number
4. Serial Number
5. Calibration reference for traceability
6. N2 Calibration Reference
7. Response Speed-Exhaust Condition
(Atmosphere or Vacuum)
8. Operating Attitude
9. Valve Type (NC/NO)
Seal (and Seat) Material
10. Reference Temperature and Pressure
11. Electrical Connector Types
12. Options (Auto Shutoff/Auto Zero)
13. Customer Special Request Number
14. Main Firmware Revision
15. DeviceNet Firmware Revis
©2005 Celerity, Inc. #199-001-0006 REV.F 4/05
Artisan Technology Group - Quality Instrumentation ... Guaranteed | (888) 88-SOURCE | www.artisantg.com

5
7. INSTALLATION
7.1 Unpacking
Verify that the controller was not damaged in shipment. Notify the shipper immediately if you
find a problem. All products returned must have a Return Material Authorization number
(RMA #; see section 12.8) issued prior to return shipment to the factory.
NOTE: Do not remove the shipping caps covering the inlet and outlet fittings until
immediately prior to the actual MFC installation in the tool.
7.2 Purging before Installing the MFC
Before installing the MFC completely purge the gas lines with nitrogen or argon. The purge
gas must be moisture and oxygen free, to less than 100 ppb. The preferable method is to
cycle purge the line for a period of two to four hours, depending on the cleanliness required
by the process and the reactiveness of the process gas.
Cycle purging consists of evacuating to a low pressure, adequate to induce outgassing, and
then purging to remove adhered moisture and oxygen. The cycle is repeated several times to
complete the cleaning. Alternatively, eight to twenty-four hours of purging alone may be used
if vacuum is not available.
7.3 Positioning the Controller
The controller must be positioned so that the gas flow is in the direction of the arrow stamped
on the controller base. It is designed to be mounted only in the position for which it was
calibrated (See the side label of the MFC. Refer to Section 6.1). High Temperature models
(9000-series) are designed to be mounted in the horizontal position only.
©2005 Celerity, Inc. #199-001-0006 REV.F 4/05
6.2 Traceability
If you wish to replace an MFC, call Celerity with the serial number of the MFC you wish to
replace. Celerity will determine the part number for the equivalent MFC with the same
options.
Artisan Technology Group - Quality Instrumentation ... Guaranteed | (888) 88-SOURCE | www.artisantg.com

6
Mounting Attitude
Figure 1. Mounting Attitudes. Two Configurations: HOS and HOV
In order to provide optimum performance, Celerity calibrates all Mass Flow Controllers
and Mass Flow Meters to the position specified at the time of the order.
7.4 Mounting the Controller
Use two #8-32 screws to mount the controller. This will ensure the flow controller's
resistance to vibration from external sources.
7.5 Connecting to gas supply line
Once the unit is correctly mounted, connect the inlet and outlet fittings of the controller to the
gas supply line. Depending on the type of fittings used, connect and tighten per fitting
manufacturers specifications.
NOTE: You MUST use two wrenches to tighten each fitting of the unit, one for the nut and the
other to keep the fitting from receiving any rotational stress. If you do not do this you
could cause a leak, due to stress applied to the MFC’s internal seals.
8. ELECTRICAL CONNECTIONS
8.1 Voltage and Pinouts
- Check that the pin connections of the mating cable have the same pinout
(See Appendice 16.1).
- Most analog and digital MFCs use ±15 VDC power.
- DeviceNet MFCs use +11-25 VDC power.
- A Flow meter has the same pinout as a controller, except that the following pinouts do not
apply on a meter:
- Setpoint, Valve Test Point, Valve Off
- Auto-Zero Disable, Auto-Zero Alarm.
NOTE: Do not make any connections to any unlabeled connector pins.
HOS
Horizontal-On-Side
HOV
Horizontal-Or-Vertical
©2005 Celerity, Inc. #199-001-0006 REV.F 4/05
Artisan Technology Group - Quality Instrumentation ... Guaranteed | (888) 88-SOURCE | www.artisantg.com

8.2 Connections to a Power Supply
If you are using a power supply other than one from Celerity, check the pin assignments,
making sure they match those in Appendice 16.1, depending on connector type.
Celerity power supplies use a cable that has a 20 pin female header type connector at one
end and a 20 pin card edge (MFC) type at the other.
- The connectors are keyed at both ends.
- When making the connection, be sure to apply pressure directly down on the edge
connector.
NOTE: Do not rock the connector back and forth; this could cause damage to the electronic
circuits.
8.3 Warm Up
Once the power supply is securely connected to the MFC/MFM, please allow at least 60
minutes for the unit to stabilize.
9. MULTIFLO VIRTUAL INTERFACE
9.1 Features
To fully take advantage of all the outstanding operational features of Celerity’s digital mass
flow controllers, a Multiflo Virtual Interface User Kit is required. This will allow access to the
mass flow controllers through a conventional personal computer.
With it you can issue commands to, and access information from, up to 32 MFCs.
(See the MultiFlo Virtual Interface Operational Manual for details)
- Refer to Multiflo Virtual Interface User Manual to perform the following.
- Monitor Setpoint, Flow, and Valve Voltage
- Turn the Flow Off and On
- Archive and analyze collected data from these units.
- Make comparisons among units.
- Change the gas that the unit is configured for.
- Troubleshoot quickly.
- Correct for a calibration inaccuracy.
NOTE: The Digital MultiFlo MFC doesn’t need to be warmed up to be programmed for gas
and range.
9.2 Configure the DMFC for Networking
1. Power the MFC (see Section 8).
2. Starting from left to right configure each DMFC for a MacID address.
- The MacID address must be between 32 and 96, inclusive.
3. Using RJ-11 connectors, daisy chain up to 32 DMFC’s.
7
©2005 Celerity, Inc. #199-001-0006 REV.F 4/05
Artisan Technology Group - Quality Instrumentation ... Guaranteed | (888) 88-SOURCE | www.artisantg.com

4. Install the appropriate length RJ-11 connector to the final DMFC in the daisy chain and
connect to the “25 Pin” to “RJ-11” adapter on the RS-232/RS-485 converter supplied
with your MultiFlo Virtual Interface User Kit.
5. Connect the “25 Pin” to “9 Pin” adapter to the serial port of your personal computer or
Laptop.
6. Install MultiFlo Virtual Interface Software supplied in the Multiflo Virtual Interface User Kit.
10. OPERATION AND PERFORMANCE CHECKS
Perform the following checks after the mass flow controller has been installed into the system.
10.1 Automatic Zero Initialization
See Appendices 16.3 and Appendices 16.7.
10.2 Proper Sequencing
Systems using a microprocessor or computer for operating the MFC should sequence the
valve off between processes.
This is accomplished in the following way:
- MFC’s with Automatic Shut-off
- Simply provide a zero setpoint.
- Gas will automatically be shut off.
- MFC’s without Automatic Shut-off
- Switch Pin J off (if applicable).
Valves, whether upstream or downstream from the mass flow controller, should be
programmed to:
- turn on prior to turning on the MFC, and
- turn off after the MFC is turned off.
For units with Auto Zero, it is recommended that the upstream valve and downstream valve
be turned off for a minimum of three minutes prior to the start of a process. This is because
the Auto Zero function employs a 2 minute time delay before it begins to act upon any zero
offset.
10.3 Leak Test
It is important to test the mass flow controller connections for leak integrity, after it has been
installed into your system, with a helium leak detector.
10.4 Purge
There are two recommended purging processes, one for non-reactive gases and one for
reactive gases.
8
©2005 Celerity, Inc. #199-001-0006 REV.F 4/05
Artisan Technology Group - Quality Instrumentation ... Guaranteed | (888) 88-SOURCE | www.artisantg.com

10.4.1 Non-Reactive Gases:
From process tool control system fully open the MFC by setting the setpoint to 100% of
the full scale range. Purge the mass flow controller with clean, dry nitrogen or argon for a
minimum of two hours.
10.4.2 Reactive Gases:
Use one of the following three methods:
(See “Connecting to Gas Supply Line” Section 7.5)
- Cycle purge:
- Alternately evacuate and purge the mass flow controller for 2 to 4 hours with clean, dry
nitrogen or argon.
-For toxic and corrosive gases it is recommended to use 100 - 120 cycles.
- Continuous purge:
- Purge the mass flow controller with clean, dry nitrogen or argon for 8 to 24 hours.
- Evacuation purge:
- Evacuate the mass flow controller for 8 to 24 hours.
10.5 Zero Check
Reference Appendice 16.2
Note: For remote readouts, including analog-to-digital converters, ensure that the
readouts match the inputs to the controller. Adjust their zero and full-scale to match.
For more information on setting the MFC/MFM Zero, please refer to Appendice 16.2.
9
©2005 Celerity, Inc. #199-001-0006 REV.F 4/05
Artisan Technology Group - Quality Instrumentation ... Guaranteed | (888) 88-SOURCE | www.artisantg.com

10.6 Full Flow Check
1.Apply the gas at the appropriate inlet pressure.
2.Apply a Setpoint of 100%. This is accomplished by applying a 5.00 VDC setpoint (to pin A
relative to pin B or C on the cardedge connector.
3.Verify that the indicated flow output reads a steady 5 volts ±10 mV (pin 3 relative to pin B
(or C) on the cardedge connector. This is equivalent to a flow of 100% ±0.2%.
10.7 Flow Control Response Check
1.Close the valve by
(a) applying a 0% setpoint (where auto shut-off is enabled) or
(b) apply a Valve Off command (apply 0 volts to pin J of the cardedge connector).
2.Remove the Valve Off command.
- This accomplished by disconnecting pin J from pin 10.
3.Verify that the response time is correct.
- For “fast start” units refer to the response specifications for each model and range.
- For “slow start” (linear response) units the response time that is best for your application
was chosen at the time of your order
- 4-6 seconds, 6-10 seconds, 10-15 seconds, 20-30 seconds or 40-60 seconds
4.If the unit does not meet the response specifications contact Celerity for assistance.
10.8 Calibration Check
Calibration is checked by flowing gas through a calibration reference upstream from the
mass flow controller or meter.
- If the gas used for this calibration check is other than the specific surrogate gas or the
actual process gas (such as N2) MFC errors of up to ±10% can be expected. This is due
to the different characteristics among the different gases.
10
©2005 Celerity, Inc. #199-001-0006 REV.F 4/05
Artisan Technology Group - Quality Instrumentation ... Guaranteed | (888) 88-SOURCE | www.artisantg.com

11. TROUBLESHOOTING
Many problems that appear to be MFC-related may actually be caused by another part of the
system. Go through the step-by-step Troubleshooting Guide (Appendice 16.3) before removing the
MFC from service.
Environmental factors may affect MFC performance (see Table 1) but these are easily resolved
using a simple troubleshooting checklist (see Table 2).
11.1 Environmental Factors
Table 1. Environmental factors
11.2 MFC Troubleshooting Checklist
Check For These Factors:
- Verify that the supply voltage is correct.
- Verify that the grounding is consistent.
- Verify that the setpoint signal at the MFC connector is the same as the setpoint signal
coming from the tool.
- Verify that the Output (Indicated Flow) of the flow controller is the same at the input of the
tool.
- Verify the valve voltage response.
- Move the setpoint upward and downward, looking for the valve voltage to change
accordingly.
- Compare recent valve voltage to past valve voltage. If it has changed and the other
parameters have not then a failure is likely.
11
SYMPTOMS CAUSES
Inaccurate flow (span shifts)
•
Temperature (steady state and transient)
•
Inlet pressure (steady state and transient)
•
Power supply problems, electrical interference
Control problems
•
Differential pressure not within operating range
(cannot reach setpoint, oscillation)
•
Inlet pressure not stable
•
Cable losses (too much ground current
Zero problems
•
Temperature (steady state and transient)
(indicated zero not stable)
•
Inlet pressure (steady state and transient)
•
Power supply problems, electrical interference
•
Attitude sensitivity
©2005 Celerity, Inc. #199-001-0006 REV.F 4/05
Artisan Technology Group - Quality Instrumentation ... Guaranteed | (888) 88-SOURCE | www.artisantg.com

12. REMOVAL
The following procedures are designed to minimize or eliminate the contamination normally
associated with the most highly reactive gases. Celerity has also designated these
procedures to reduce the overall exposure of wafers to foreign particles.
12.1 Purging before removing the MFC
Before removing the MFC purge the gas lines with nitrogen or argon. The purge gas must be
moisture and oxygen free, to less than one hundred parts per billion. The preferable method
is to cycle purge the line for a period of two to four hours, depending on the cleanliness
required by the process and the reactiveness of the process gas.
Cycle purging consists of evacuating to a low pressure adequate to induce outgassing and
then purging to remove adhered moisture and oxygen. The cycle is repeated several times to
complete the cleaning. Alternatively, eight to twenty-four hours of purging alone may be used
if vacuum is not available.
12.2 Removing the MFC
Once the line has been purged, the MFC can be removed. Inspect the upstream and
downstream lines, as well as the MFC inlet and outlet, for signs of contamination.
Immediately hardcap the inlet and outlet fittings of the MFC and cap the line fittings as well.
The unit should be sealed in a cleanroom plastic bag before leaving the cleanroom area.
12.3 Packaging the MFC
The unit can now be transported to the service or calibration location. If the MFC is to be
transported outside of the facility, it should be packaged in its original carton or 1 inch of
foam cushion on all sides, adequate for shipping an instrument.
Be sure to include documentation of any contamination found, failure symptoms, and the
location of its installation. This documentation can facilitate future contamination analysis.
If a product is being returned to Celerity it must include your company name, contact,
Contaminination Disclosure Form, and RMA #. Call Unit for an RMA # prior to shipping.
12.4 Un-Packaging
When the MFC is received at a service or calibration facility, the bag should be opened only
within a cleanroom area (Class 1000 or better).
12.5 Cleaning
Cleaning of the MFCs should be done with semiconductor grade chemicals. Assembly,
calibration, response timing, and performance testing is to be accomplished in a Class 100 or
better environment.
12.6 Shipping
Once the unit has been cleaned, serviced and/or recalibrated, it must be hardcapped and
bagged for return. Include with the removal documentation any documentation relevant to
the calibration and service that was performed.
12
©2005 Celerity, Inc. #199-001-0006 REV.F 4/05
Artisan Technology Group - Quality Instrumentation ... Guaranteed | (888) 88-SOURCE | www.artisantg.com

12.7 Shipping Costs
Celerity prepays outgoing freight charges when any part of the service is performed under
warranty. All domestic shipments are sent via UPS ground transport. However, if the unit
has been returned collect to Celerity, the costs are added to the repair invoice. Import/export
charges, foreign shipping charges, or special customer specified handling will be paid for by
the customer.
12.8 Returned Material Authorizations (RMA)
All product returns must accompany a RMA number for proper material handling within
Celerity. Contact customer service at (714) 921-2640, for a Returned Material Authorization
number.
12.9 Documentation
The documentation of the service and calibration should be maintained, based on the
location, in order to determine the contamination of each gas line. These procedures should
provide maximum cleanliness. This is required for many of the new, more critical
semiconductor processes.
13. MAINTENANCE
13.1 Emergency Service
In addition to a fast turnaround time for regular service and repairs, Celerity can, in most
cases, provide an advance replacement unit for EMERGENCY PRODUCTION DOWN
situations. In this way, your production can get back on-line while your original unit is
repaired.
13.2 Routine Maintenance
Any precision instrument such as a mass flow controller requires occasional servicing. It is
especially important to perform this service if the flow controller has been operating for an
extended period of time or has been subjected to gases which leave excessive residue. If
non-reactive gases are used, the flow controller should be serviced annually. If reactive gases
are used, the flow controller should be serviced every six months.
Occasionally the Zero Offset should be checked. See the section, “Operation and
Performance Checks”, for adjustment instructions.
13.3 Factory Calibration and Service
Celerity provides a 5 day turnaround time for factory calibration and repair, and an even
shorter turnaround time for a nominal additional cost.
13.4 Field Service
Celerity Mass Flow Controllers are field serviceable by the factory. They should be maintained,
cleaned, and repaired by an authorized Celerity/Unit repair center.
13
©2005 Celerity, Inc. #199-001-0006 REV.F 4/05
Artisan Technology Group - Quality Instrumentation ... Guaranteed | (888) 88-SOURCE | www.artisantg.com

13.5 Technical Support
A factory technician is available to answer your questions by phone any time, 24 hours a day,
7 days a week 1-888-UNIT-INC.
14. WARRANTY
Celerity products are warranted against defects in materials and workmanship for a period of two or
three years, depending on the model, from the date of shipment, when used in accordance with
specifications and not subjected to physical damage, abuse, or contamination.
Table 3. Warranties
If units are judged to be out of warranty, Celerity will notify the owner of replacement or repair costs
before proceeding. Factory service and repairs include a ninety-day warranty on all parts and labor.
Normal turnaround time is five working days, or less, on any standard range item returned for
warranty service.
MFCs that are repaired by anyone other than Celerity service centers during the warranty period
void their warranty.
Check our website at www.celerity.net to find your local service center.
15. WEB SITE TECHNICAL RESOURCES
Celerity provides several technical information resources on our website, including “The Basics of
Thermal Mass Flow Control”.
14
MODEL TYPES ULTRA HIGH PURITY HIGH PURITY ELASTOMERIC MFCs
METAL SEAL MFCs METAL SEAL MFCs
MODEL NUMBERS8160 1551 8100
8161 1660 8101
8162 1661 8105
8163 1662 3101
8165 1663
8260 1665
8262 3161
8561 3165
8564
8565
WARRANTY LENGTHThree years Three years Two years
MODEL TYPES HIGH PURITY HIGH PURITY ELASTOMERIC MFCs
METAL SEAL MFCs METAL SEAL MFCs
MODEL NUMBERS7360 5361 180
7361 5365 7300
7364 7301
7304
5301
WARRANTY LENGTHThree years Two years Two years
©2005 Celerity, Inc. #199-001-0006 REV.F 4/05
Artisan Technology Group - Quality Instrumentation ... Guaranteed | (888) 88-SOURCE | www.artisantg.com

16. APPENDICES
16.1 Connector Pinouts
15
1
2
3
4
5
6
8
9
10
A
B
C
D
E
F
H
I
J
Case Ground
Power Common
Output (0-5 VDC)
+15 VDC
Sensor Out
Common
Setpoint (0-5 VDC)
Signal Common
Signal Common
Valve Test Point
-15 VDC
Zero Alarm
Valve Off
MFC CARDEDGE CONNECTOR
1
2
3
4
5
6
8
9
10
A
B
C
D
E
F
H
I
J
Case Ground
Power Common
Output (0-5 VDC)
+15 VDC
Sensor Out
Signal Common
Signal Common
-15 VDC
MFM CARDEDGE CONNECTOR
15 PIN D CONNECTOR
9 PIN D CONNECTOR
1
2
3
4
5
6
7
8
9
10
11
12
13
14
15
Common
+15 VDC
Output (0-5 VDC)
Power Common
Case Ground
Valve Off
-15 VDC
Valve Test Point
Signal Common
Signal Common
Setpoint (0-5 VDC)
15 PIN "D" CONNECTOR (UDU15)
1
2
3
4
5
6
7
8
9
10
11
12
13
14
15
Common
+15 VDC
Output (0-5 VDC)
Power Common
Case Ground
Valve Off
-15 VDC
Valve Test Point
Signal Common
Signal Common
Setpoint (0-5 VDC)
REMOTE "D" CONNECTOR OPTION (UDU15)
©2005 Celerity, Inc. #199-001-0006 REV.F 4/05
Artisan Technology Group - Quality Instrumentation ... Guaranteed | (888) 88-SOURCE | www.artisantg.com
This manual suits for next models
53
Table of contents
Popular Measuring Instrument manuals by other brands
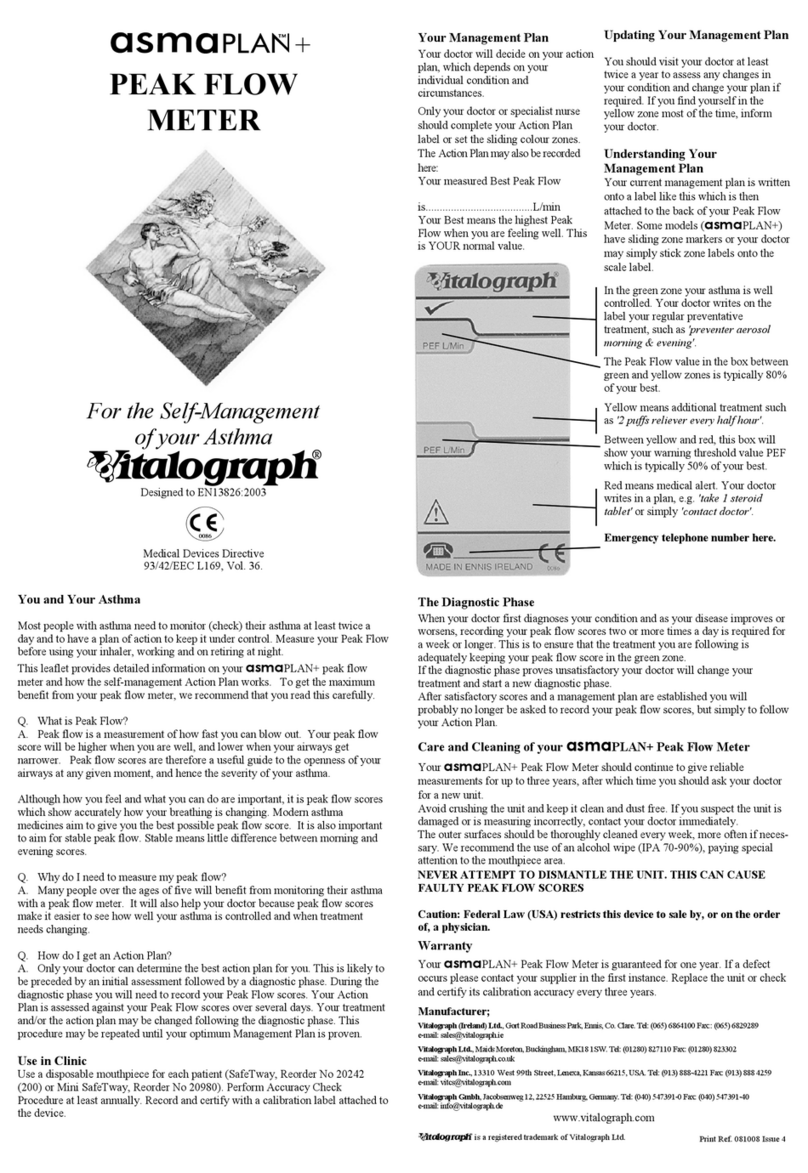
Vitalograph
Vitalograph asmaPLAN+ quick start guide

Prodigit
Prodigit 4016 Series Operation manual
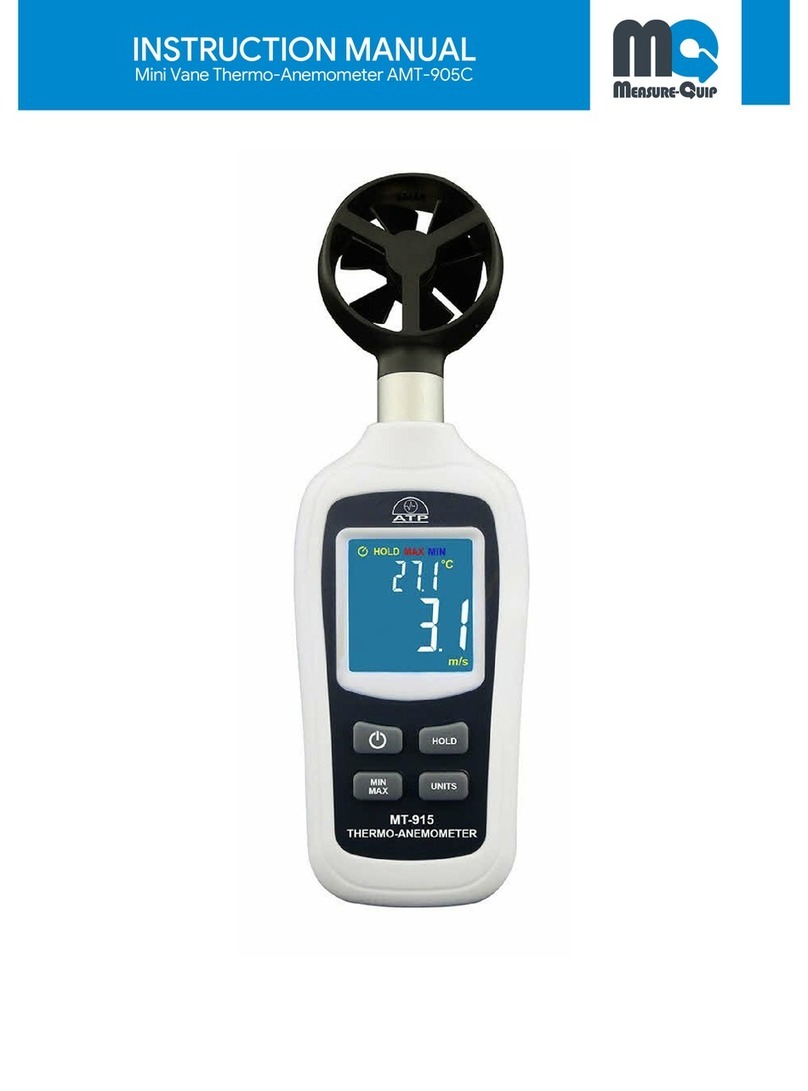
Measure-Quip
Measure-Quip Mini Vane Thermo-Anemometer AMT-905C instruction manual
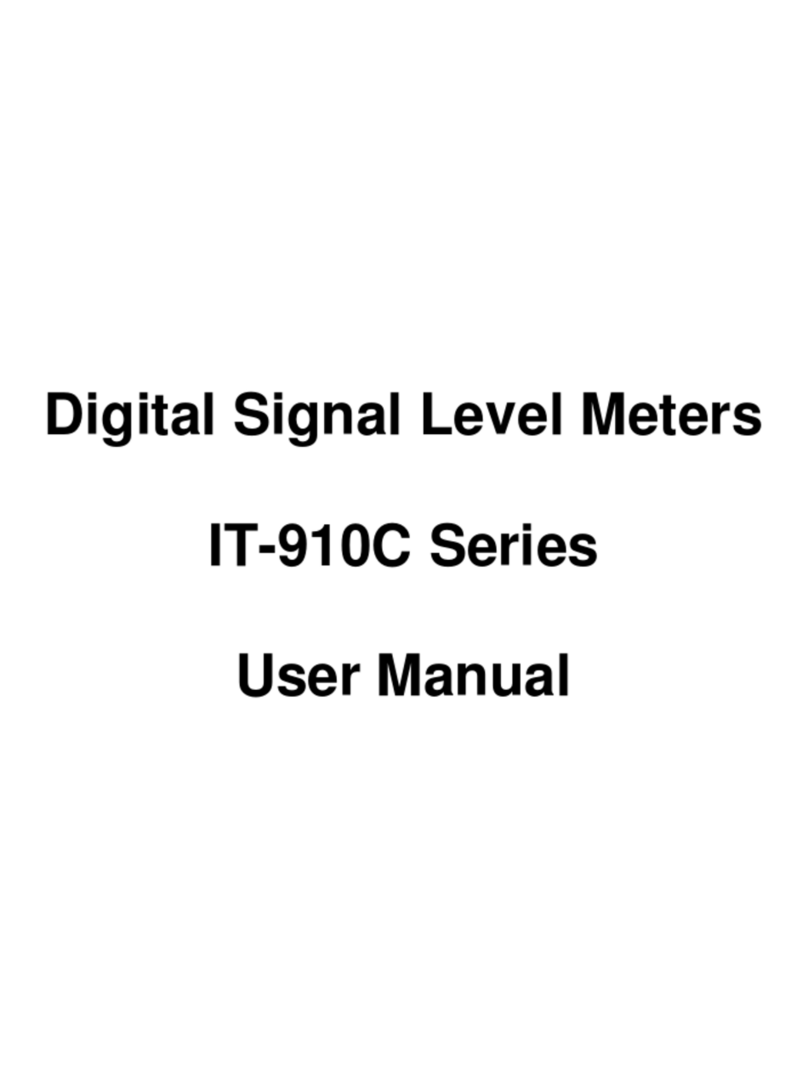
Inotech
Inotech IT-910C user manual

Kedida
Kedida CT-8022 instruction manual
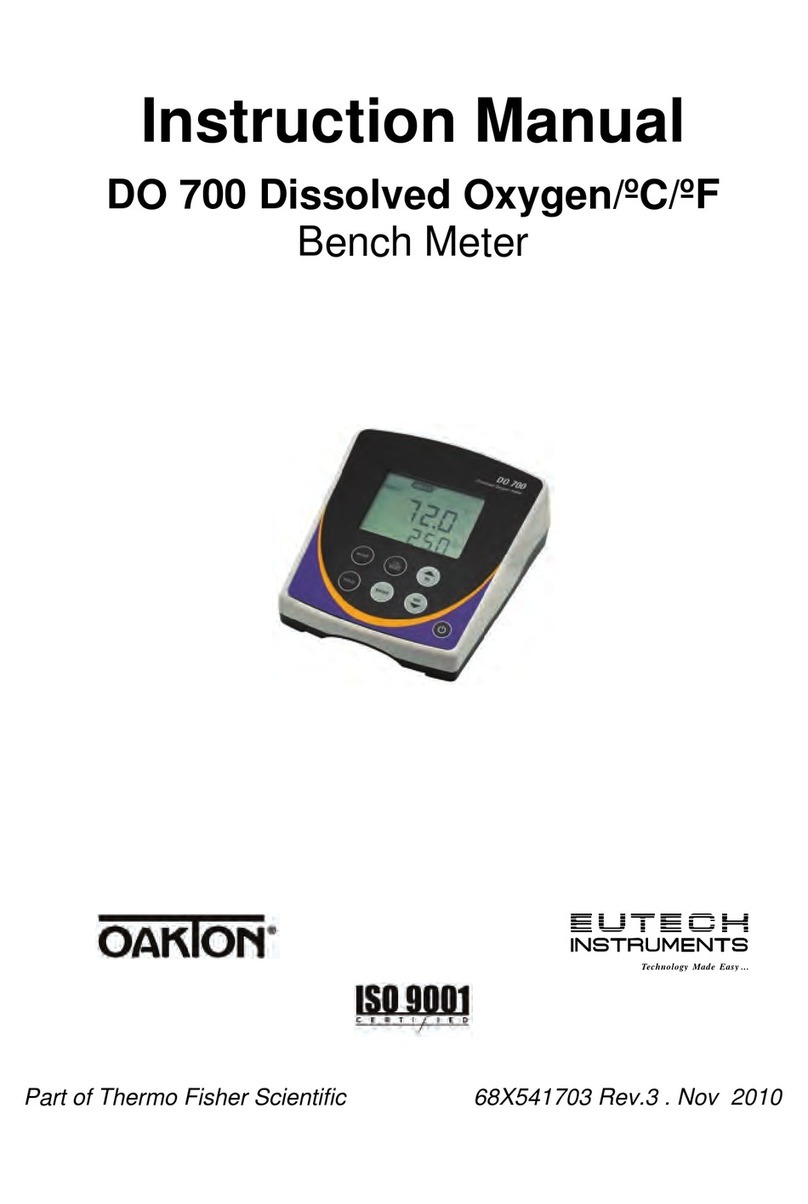
EUTECH INSTRUMENTS
EUTECH INSTRUMENTS DO 700 - REV 3 instruction manual