Chemtrac TM2200 User manual

OPERATIONS MANUAL
ONLINE TURBIDIMETER
3/25/07
TM2200


Page 2
TABLE OF CONTENTS
Section Title Page
IMPORTANT INSTRUCTIONS ........................................................................... 3
WARRANTY INFORMATION .............................................................................. 4
1 GENERAL INFORMATION ................................................................................. 5
Overview .......................................................................................... 5
Debubbler .......................................................................................... 5
Convertible Cuvette..................................................................................... 5
Light Source .......................................................................................... 5
Proper Sampling Point ................................................................................ 6
Technical Specifications.............................................................................. 8
2 MOUNTING AND INSTALLATION...................................................................... 9
Mounting .......................................................................................... 9
Wiring Safety .......................................................................................... 9
Wiring .......................................................................................... 9
Sample Connection ..................................................................................... 10
3 OPERATION .......................................................................................... 11
Display/User Interface…………………………………………………………… 11
Menus and Controls …………………………………………………………… 12
Main Screen ………………………………………………………………… 12
Menu Screen ………………………………………………………………… 13
4 INSTRUMENT CALIBRATION ............................................................................ 17
Primary Calibration ………………………………………………………. ..... 17
Secondary Calibration………………………………………………………….. 20
5 OUTPUT HOLD .………………………………………………………………... 21
6 I/O SETUP ………………………………………………………………… 23
7 MAINTENANCE ………………………………………………………………… 25
Lamp Replacement…………………………………………………………….. 25
Cleaning ………………………………………………………………... 25
Figures and Images
Figure 1 Sample Tap ……………………………………………………………….. 7
Figure 2 Mounting Dimensions………………………………………………………. 26
Figure 3 Electrical Connections……………………………………………………… 27
Photo 1 Cuvette Sample Connection……………………………………………….. 28
Photo 2 Cuvette Indexing……………………………………………………………... 29
Photo 3 Electrical Connections……………………………………………………… 29
Photo 4 Sample Inlet and Drain……………………………………………………… 30
Photo 5 Lamp Connections…………………………………………………………... 30

Chemtrac Systems, Inc.
Page 3
IMPORTANT INSTRUCTIONS
When using this instrument, basic safety precautions shall always be followed to
reduce the risk of fire, electrical shocks and injury to persons, including the
following:
5Before attempting to unpack, set up, or operate this instrument, please
read this entire manual.
5Follow all warnings marked on the instrument. Failure to follow these
precautions could result in personal injury or damage to the equipment.
5Do not attempt to disassemble the unit.
5Do not modify any internal electrical wiring or electronics.
5Make certain the unit is disconnected from the power source before
attempting to service or remove any component.
5Water must not enter the housing of the unit. Be sure to close and fasten
the covers of the unit following any opening.
5Use a mild non-abrasive cleanser when cleaning the outer cover of the
unit.
5Do not drop or jar the unit.
SAFETY PRECAUTIONS
In order to provide maximum user safety this instrument was designed with all electrical
circuitry enclosed within a protective non-conductive housing. The label below will be
visible at any location where high voltage is present.

Chemtrac Systems, Inc.
Page 4
WARRANTY INFORMATION
Chemtrac®Systems, Inc. warrants its equipment to be free from defects in
material and workmanship for a period of one (1) year from date of shipment to
the original purchaser. Upon receipt of written notice from purchaser, seller shall
repair or replace the equipment (at option of Chemtrac®Systems, Inc.).
Chemtrac®Systems, Inc. assumes no responsibility for equipment damage or
failure caused by:
1. Improper installation, operation, or maintenance of equipment
2. Abnormal wear and tear on moving parts caused by some processes
3. Acts of nature (i.e., lightning, etc.)
This warranty represents the exclusive remedy of damage or failure of
equipment. In no event shall Chemtrac®Systems, Inc. be liable for any special,
incidental, or consequential damage such as loss of production or profits.
Should you experience trouble with the equipment, please contact:
Chemtrac Systems, Inc
6991 Peachtree Industrial Blvd., Building 600
Norcross, GA 30092
Phone: 800-442-8722 (Inside US only), 770-449-6233
Fax: 770-447-0889
Website: www.chemtrac.com

Chemtrac Systems, Inc.
Page 5
SECTION 1
GENERAL INFORMATION
OVERVIEW
The Chemtrac TM2200 is an online nephelometric turbidimeter. The TM2200 continuously
monitors, records, and reports (integrated with SCADA) turbidity compliance data for municipal
water filtration processes. A local display prompts the user with calibration steps, diagnostic
data, and immediate turbidity data without the need for a laptop or data recorder. The TM2200
design permits easy access to the light source for maintenance and replacement. By
incorporating an all-in-one package, the TM2200 design simplifies installation and assists the
operator with monitoring water quality from multiple filter effluents.
Debubbler
The debubbler maximizes the removal of entrained air bubbles that would otherwise interfere
with the turbidity measurement. The debubbler unit is within the enclosure of the TM2200. The
separate inlet and outlet barbed tube connections facilitate an easy connection to the water
source. A slipstream is taken off of the debubbler for sampling and the constant head pressure
from the debubbler ensures a constant flow to the sample cell.
The modular design of the debubbler allows for convenient cleaning and maintenance.
Convertible Cuvette
The up-flow cuvette sample cell is a sampling improvement over the common approach of using
a larger reservoir for turbidity measurements.
The 35 mL cuvette same sample cell is easily converted for use in the calibration process. Index
marks on the cuvette and the seam created by the two parts of the sensor block assure that the
optical surface of the cell is consistently lined-up for the calibration and online phases of
operation. See Photo 2
Light Source
The light source does not come in direct contact with the sample, nor does it have any large air
spaces that could lead to the accumulation of dust or moisture.
The tungsten bulb has a better than 15,000 hour life expectancy (20+ months). For
replacement, the watertight bulb housing is conveniently accessible from the side of the sensor
head.

Chemtrac Systems, Inc.
Page 6
SELECTING PROPER SAMPLE POINT
The high sensitivity of the instrument makes sample handling and delivery critical for proper
operation. Poor results caused by improper sample handling will not only reduce the value of
the instrument to the user, but they can result in regulatory penalties. An increase in a small
number of particles in the filter effluent caused by poor sample control can cause a significant
increase in measured turbidity.
It is not difficult to achieve proper sample delivery in virtually any treatment plant. The important
thing is to make sure the sample is a proper representative of the process stream. There are
three ways in which the sample can be distorted:
1. Adding particles to the sample stream. Choosing an improper location for the sample
tap, such as the bottom of a pipe where sediment can accumulate, or an open sample
point where particles can be introduced from outside the process.
2. Losing particles from the sample stream. Long sample lines can cause particle dropout,
especially at low flow rates. If the sample line must be long (more than 10 or 15 feet), a
large pipe should be used with a flow rate that keeps the sample moving as fast as the
process stream. Particles will settle out of standing water.
3. Altering the particle distribution. Sample pumps can chop up larger particles creating
more small particles. Valves and other obstructions can cause "shedding.” Particles
collect on cracks and edges and then break loose later. "T-fittings” can cause larger
particles to miss the sample line because they do not necessarily make the sharp right
angle "turn.”
Of course, it is seldom possible to avoid all of these pitfalls. Valves are often needed to control
sample flow rates, or pumps are used to get the sample to a usable point. The important thing is
to minimize these problems. Filtered water can be pumped with fewer problems than raw or
settled water since only very small particles are usually present, and they are less likely to be
broken up. Ball valves, or other types with minimal edges to trap particles, can be used. "Y-
fittings” can be used instead of "T'-fittings.”
Sample Taps
The diagram below shows proper and improper sample locations on a process pipe. These are
the same as for any instrument requiring a representative sample flow. See Figure 1.
Make sure that the sample point has the minimum pressure available at all times to provide
enough flow.

Chemtrac Systems, Inc.
Page 7
Figure 1. Sample Tap

Chemtrac Systems, Inc.
Page 8
TECHNICAL SPECIFICATIONS
Compliance: USEPA 180.1
Range: 0 - 100 NTU
Resolution: 0.0001 Up to 2.0000 NTU;
0.001 From 2.001 to 9.999 NTU;
0.01 Greater than 9.999 NTU
Repeatability: Better than ± 1.0% of reading or ± 0.002 NTU
Signal Averaging: User selectable from 1-90 seconds
Sample Flow: 100 to 1000 mL/min.
Sample Temperature: 0-50°C, (32-122°F)
Operating Temperature: 0-50°C, (32-122°F)
Light Source: Tungsten lamp
Lamp Life (MTTF): Greater than 15,000 hours (20 months)
Outputs: Two selectable 4-20 mA isolated, adjustable over entire range
Both outputs transmit current turbidity value
Digital Communications: RS485 (Modbus RTU & Modbus ASCII), Ethernet (Modbus TCP),
& Bluetooth
Certifications: CSA, CE
Enclosure: NEMA 4X
Power Requirements: 100-240 VAC, 47-63 Hz, 0.5 A
Mounting: Single module design; wall, rack or stand mount
Dimensions: 53 cm H x 23 cm W x 20 cm D (21"H x 9"W x 8"D)
Shipping Weight: 6 Kg (13 Lbs.)

Chemtrac Systems, Inc.
Page 9
SECTION 2
MOUNTING AND INSTALLATION
MOUNTING
The TM2200 Turbidimeter should be permanently mounted in an upright position using the
mounting holes on the enclosure. See Figure 2 for details.
WIRING SAFETY
Please observe the following safety precautions prior to wiring the unit:
•Power must be locally fused or switched prior to entering the unit
•Disable power circuit prior to hardwiring the unit
•Observe polarity when connecting the unit. The unit may not function properly, and can
be damaged, if polarity is crossed
•All wire connections should be tinned prior to connecting to ensure proper contact and to
prevent corrosion
•The unit must be connected to earth ground
WIRING
Following the installation guidelines outlined in this manual should result in proper operation
with minimal problems. Individual plant requirements and layouts will vary, resulting in
alterations to the procedures. All wiring connections are located beneath the connection cover
plate. See Figure 3.
•Disable power circuit that supplies power to the unit
•During installation, a local isolation point must be supplied
•Mount the TM2200 in the upright position (Chemtrac logo upright) using the four
mounting holes on the back of the enclosure. Unit may be fastened to mounting
brackets, pipe stand or similar
•Wiring should be fed through the compression fitting on the bottom of the enclosure.
NOTE
When feeding wire into unit it is always important to feed through the compression fitting
that is closest to that wire connection.
All external electrical connections are shown in Figure 3.
Electrical power should be connected in the following order.
1. Insert the ground (earth) wire into the middle terminal labeled “G”
2. Insert the Line wire into the left terminal labeled “L”
3. Insert the neutral wire into the right terminal labeled “N”

Chemtrac Systems, Inc.
Page 10
SAMPLE CONNECTION
•Sample inlet and drain are connected to the debubbler (See Photo 4). The sample inlet
connection is a ¼” barbed fitting suited for ¼” ID tubing. The sample drain fitting is a ½”
barbed fitting suited for ½” ID tubing. The debubbler outlet connects to the cuvette inlet
with quick connect fittings requiring ¼” OD tubing. The outlet of the cuvette connects to
the drain section of the debubbler through quick connect fittings and ¼” OD tubing. See
Photo 1.
•Sample should flow to the debubbler at a rate of between 100mL/min to 1000mL/min.
Prior to starting sample flow, ensure the sample line has been adequately flushed to
prevent fouling of the debubbler or cuvette.

Chemtrac Systems, Inc.
Page 11
SECTION 3
OPERATION
DISPLAY/USER INTERFACE
The TM2200 is equipped with user interface keys, LED indicators, and audible beeps.
The interface keys are up (S), down (T), and the four function keys. The label directly
above each key on the display defines the function keys.
There are four red LED lights to the left of the graphical display. These are:
Power – Illuminates when AC power is applied and instrument is turned
on
Service – Illuminates if there is a hardware failure (electronics)
Alarm1 – High or low turbidity value, illuminates if turbidity value reaches
alarm set-point
Alarm2 – Lamp status alarm, illuminates if the lamp has failed
Graphically defined function
keys. Acsess by pressing on
button directly below.
10-Jan-2007 9:37
0.035
NTU
menu data syst alrm

Chemtrac Systems, Inc.
Page 12
TM2200 READOUT, MENUS, AND CONTROLS
The menu system for the TM2200 is simple to navigate; below you will find the different
screens accessible through the function keys (menu, data, syst and alrm):
TM2200 Home Screen
The Home screen on the TM2200 is the screen used under normal operation of the
instrument. From this screen, all other features and menus can be accessed.
The main screen displays:
•System date and time
•Present turbidity value (NTU’s)
•Function key labels
FUNCTION KEYS:
menu – Changes display to the Main Menu screen. From here, you can access:
•Alarms – To enable High or low alarms and adjust the setpoint for each alarm.
•Settings – To adjust system settings such as Time/Date, Signal Averaging, Log
Interval, etc.
•Service – To adjust critical system settings such as Calibration, Output Hold, etc.
Each of the options under the service menu will be explained in detail in a later
section.
data – Displays the data log. This log displays the last 60 logged values based on the
Log Interval selected in the Settings menu.
syst – Displays the system log. This function label is only present if the is information in
the system log. The system log contains such information as alarm occurrences and
date/time of calibrations.
alrm – Displays the status of each Alarms 1 & 2.
back – Will always bring you back to the previous screen.
exit – Will always bring you back to the main screen.
10-Jan-2007 9:37
0.035
NTU
menu data syst alrm

Chemtrac Systems, Inc.
Page 13
TM2200 Menu Screen
Use the up and down arrow buttons to highlight the desired menu item then press the function
button under “entr” to select.
ALARMS
Select the desired alarm and press the function button under “entr” to select.
•“Off” disables the alarm feature.
•Selecting “On” and pressing the function key below “entr” enables the alarm and brings
up the Setpoint screen.
entr exit
Ç
È
Main Menu
Quit
Alarms
Settings
Service
exit
Alarm 2
È
entrback
Alarms
Ç
Quit
Alarm 1
back exit
Alm1 On/Of
f
Ç
Of
f
On
È
entr

Chemtrac Systems, Inc.
Page 14
The alarm setpoint screen allows you to set the value at which an alarm will be triggered. Once
this value is set, the next screen “Reset” will allow you to set the value at which the alarm is
cancelled. By setting a “Reset” value below the setpoint, you create a high alarm (alarm will
trigger if turbidity increased to or above the setpoint). By setting a “Reset” value above the
setpoint, you create a low alarm (alarm will trigger if turbidity falls below the reset point).
Use the up and down arrow buttons to select the desired alarm setpoint and press the function
button labeled “entr” to store this value and proceed to the “Reset” screen.
Using the up and down arrow buttons, select the value at which the alarm will be cancelled.
Remember, a reset value below the setpoint will create a high alarm and a reset value above
the setpoint will create a low alarm.
Once the proper value has been entered, press the function button labeled “entr”. The screen
will return to the “Alarms” menu screen. From this screen, press the function button labeled
“exit” to return to the main screen or continue on with the other alarm setup.
SETTINGS
The “Settings” menu contains the following parameters:
exitback
Alm1 Set
Ç
0.03
È
entr
entr exit
Alm1 Reset
Ç
0.03
È
back
È
back entr exit
Time/Date
LCD/KeyPad
Signal Averaging
Log Interval
Settings
Ç

Chemtrac Systems, Inc.
Page 15
•Time/Date – Used to set system time and date. For data logging purposes, it is
important that the instrument’s time and date are set accurately.
**NOTE: The instrument will not automatically adjust for Daylight Savings Time.
•LCD/Keypad – Used to set display features including:
oKeypad Tone
– Beep when buttons are pressed (On/Off)
oBacklight
– Display backlight (On/Off/Auto) Auto turns the backlight off after 20
seconds without a button press.
oContrast
– Adjusts the contrast of the display.
•Signal Averaging – Select duration of instruments built in signal averaging.
oNone – signal averaging is turned off.
o5 seconds, 10 seconds, 15 seconds, 30 seconds, 60 seconds
•Log Interval – Selects the interval that the instrument logs turbidity value into its internal
memory. The instrument can log up to 36,000 data points. With a 15 minute log
interval, data will be stored for over 1 year before the oldest data is overwritten with new
data.
oOptions
– 1 minute, 5 minutes, 10 minutes, 15 minutes, 30 minutes, 60 minutes
•Resolution – Allows the user to select the maximum displayed resolution.
oOptions
– 4 decimal places (ex. X.XXXX), 3 decimal places (ex. X.XXX)
2 decimal places (ex. XX.XX), 1 decimal place (ex. XXX.X)
oNotes
– This feature only sets the maximum displayable resolution. For
example, if the resolution is set to 4 decimal places (X.XXXX) but the measured
turbidity is greater than 3.2 NTU, only 3 decimal places will be displayed (ex.
3.257).
•Output Scale – Selects the output scaling for the 4 – 20 mA analog outputs.
oOptions
-
1. 0 – 1 NTU (4 mA = 0, 20 mA = 1 NTU)
2. 0 – 2 NTU (4 mA = 0, 20 mA = 2 NTU)
3. 0 – 10 NTU (4 mA = 0, 20 mA = 10 NTU)
4. 0 – 100 NTU (4 mA = 0, 20 mA = 100 NTU)
•RS-485 Addr – Sets the instruments node address for Modbus communications.
Selectable from 1 – 247.

Chemtrac Systems, Inc.
Page 16
Service
The Service menu contains settings that are critical to the proper, accurate performance of the
TM2200 turbidimeter. These values should only be modified by properly trained plant
personnel.
The features accessible through the Service Menu include:
•Calibration – The calibration of the instrument is covered in Section 4 - Instrument
Calibration.
•Output Hold – Hold the 4-20mA analog output signal at the present value for a
specified period of time. The Output Hold feature is covered in Section 5 – Output
Hold
•I/O Setup – Allows the user to add an offset value to the 4-20mA analog output signal.
I/O Setup is covered in Section 6 – I/O Setup.
È
back entr exit
Calibration
Output Hold
I/O Setup
Service
Ç

Chemtrac Systems, Inc.
Page 17
Section 4
Instrument Calibration
EPA recommends that primary suspension standards should be used to initially calibrate on-line
turbidimeters, and then used at least every three months to calibrate the units in order to
prevent instrument drift (primary calibrations should also be performed more often if a need is
determined in the more frequently run secondary standard calibration process).
EPA recommends that on-line turbidimeters have calibration verified on a weekly basis, if being
utilized for combined filter effluent monitoring. Less frequent verification may be more
appropriate for turbidimeters monitoring individual filter turbidity, but EPA recommends
verification be conducted with a frequency of at least once per month. Calibration verification
can be completed using primary suspension standards, secondary suspension standards, or by
comparison to a properly calibrated turbidimeter. If verification indicates significant deviation
from the standard (true) value (greater than ±10%), the instrument should be thoroughly
cleaned and recalibrated using a primary standard.
The calibrations should be well documented and the standards should be replaced when they
exceed the expiration date. Although the EPA recommends a few different primary standards for
possible use, the TM2200 has been developed using Amco Clear® standards (available from
GFS Chemicals) for all calibrations.
Regardless of calibration results, turbidimeters should be thoroughly cleaned and calibrated
with primary standards at least quarterly.
The TM2200 Turbidimeter is designed with built in auto-ranging capabilities, which operate over
three distinct ranges, 0 – 2 NTU, 2 – 10, NTU and 10 – 100 NTU. It is only necessary for the
end user to calibrate the instrument in the ranges for which it will be used. For example, if the
instrument is installed to monitor a sample stream from a filter, where the turbidity never
exceeds 2 NTU, the end user might elect to calibrate the instrument only at 0 NTU and 2 NTU,
which will cover the only range that will ever be utilized by the turbidimeter. However, in an
application where the turbidity of the sample may range from 0 NTU to 15 NTU, the user should
calibrate the instrument at all 4 calibration points (0, 2, 10 and 100 NTU) to ensure accuracy at
all possible sample turbidities.
When performing either a primary or secondary calibration, it may be desirable to utilize the
Output Hold function of the instrument. See the section labeled Output Hold.
Primary Calibration
Primary calibration of the TM2200 Turbidimeter must be performed using the same cuvette that
will be used during normal operation.
To disconnect the cuvette:
1. Close the ball valve at the outlet of the debubbler and remove the locking pin located in
the probe block.
2. Remove the cuvette from the probe block and disconnect the tubing to drain the cuvette.
3. Thoroughly clean and rinse the cuvette.
4. Insert the provided plug into the fitting at the bottom of the cuvette.
5. Remove the top screw cap and fill the cuvette approximately half full with the proper
calibration standard.
6. Gently swirl the standard around the cuvette to rinse and discard the standard.

Chemtrac Systems, Inc.
Page 18
7. Fill the cuvette up to the threads and replace the top screw cap.
8. Insert the cuvette containing the proper standard into the probe block being certain to
align the indexing mark as indicated in Photo 2.
9. Close the probe block and insert the locking pin.
To begin the calibration function of the instrument, access the Service Menu and, using the up
and down arrow keys, highlight Calibration and press the function button labeled entr.
This will bring up the calibration menu shown below.
Once it has been determined which ranges are to be calibrated, select the first turbidity
standard value by using the up and down arrow keys to highlight the desired value and press
the function button labeled entr. The following screen will be displayed.
After inserting the proper standard, press the function button labeled entr. The calibration
process will begin, and the display will begin counting down from 60 seconds as shown below.
exit
Quit
È
back entr
Service
Ç
Calibration
Output Hold
Select Range
Ç
Zero NTU
2 NTU
10 NTU
È
back entr exit
exit
ENSURE 2 NTU
Standard is inserted
and press ENTER
entr

Chemtrac Systems, Inc.
Page 19
Once the calibration of the selected range is complete, the following screen will be displayed.
Press the function button labeled exit to return to the home screen. If additional ranges are to
be calibrated, follow the above steps again using the appropriate range and standard.
If there is a problem with the calibration, the following screen will be displayed.
If this error appears, verify that the proper standard has been inserted for the range being
calibrated and retry the calibration. If the error persists, contact the factory for assistance.
2 NTU Calibration
CALIBRATING 59
exit
Continue
2 NTU Cal Complete
Press EXIT to
exit
CALIBRATION ERROR
V
erify 2 NTU
Standard is Inserted
Table of contents
Other Chemtrac Measuring Instrument manuals
Popular Measuring Instrument manuals by other brands
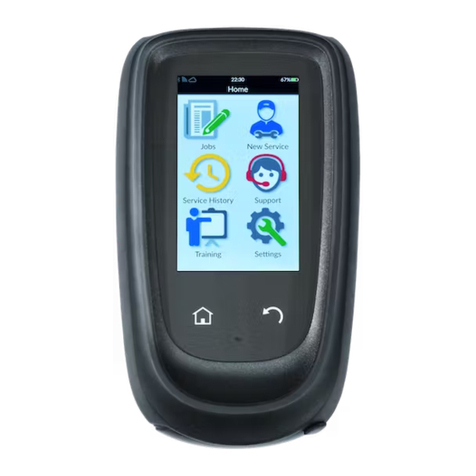
Bartec Auto ID
Bartec Auto ID TECH1000 user guide

LaserLiner
LaserLiner EvolutionCross-Laser 8P PowerBright operating instructions

Hach
Hach ORBISPHERE 410 Basic user manual
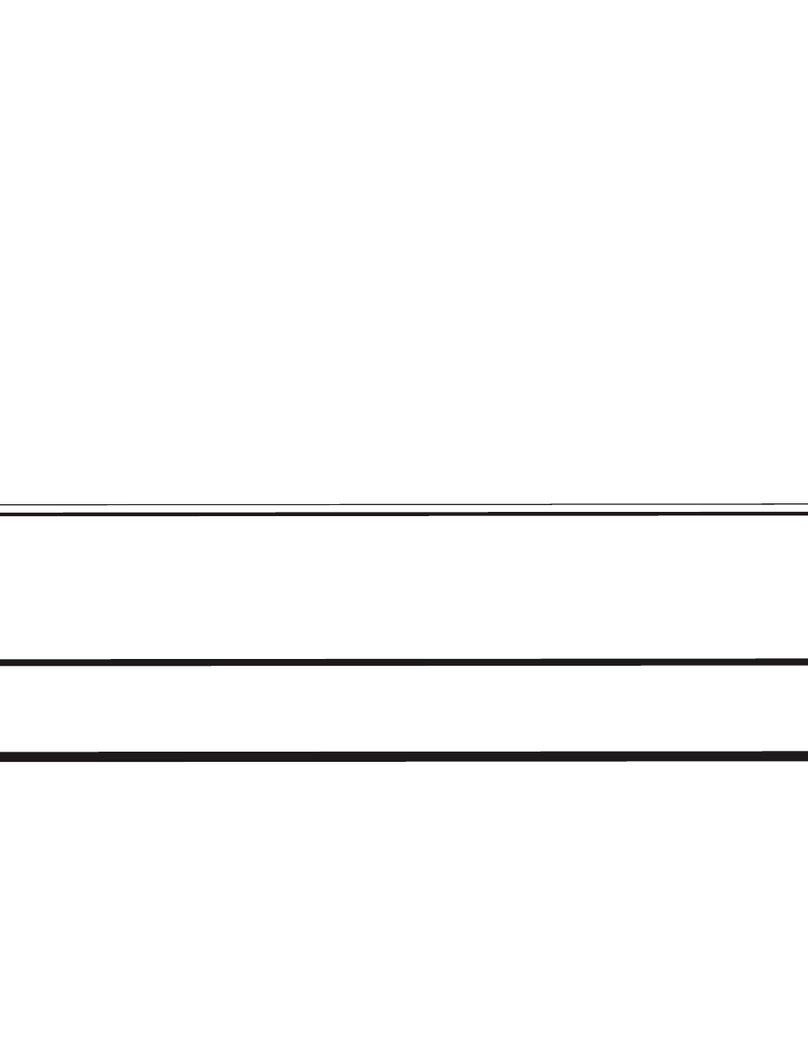
FLIR
FLIR Extech Instruments MA410 manual

PCE Health and Fitness
PCE Health and Fitness 5000H user manual
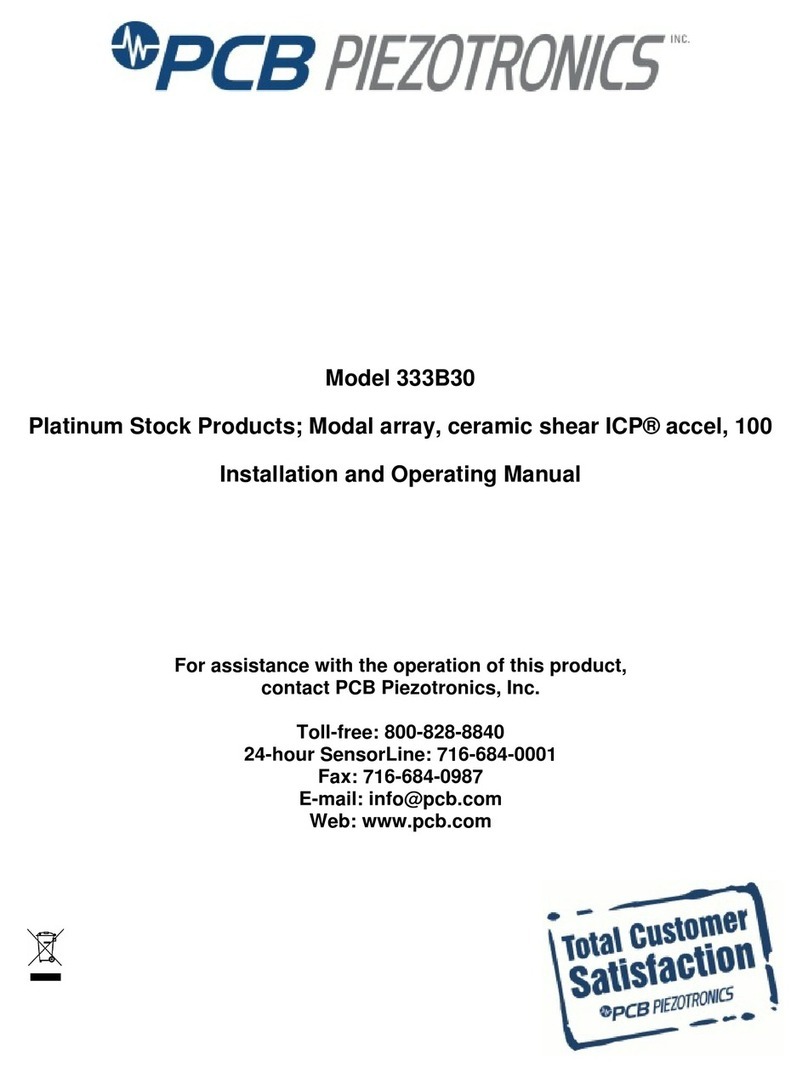
PCB Piezotronics
PCB Piezotronics ICP 333B30 Installation and operating manual