Chip Hyde VISION 3D User manual

INSTRUCTIONS FOR CHIP HYDE VISION 3D
Copyright 2004 – Chip Hyde Products
Chip Hyde Products
999 East Fry Boulevard
Suite 316
Sierra Vista
Arizona
85635
520 234 4848
www.chiphyde.com

Liability Exclusion and Damages
You have acquired a kit, which can be assembled into a fully working
R/C model when fitted out with suitable accessories, as described in the
instruction manual with the kit.
However, we at Chip Hyde Products Inc. are not in a position to influence the way you build
and operate your model, and we have no control over the methods you use to install, operate
and maintain the radio control system components. For this reason we are obliged to deny all
liability for loss, damage or costs which are incurred due to the incompetent or incorrect
application and operation of our products, or which are connected with such operation in any
way. Unless otherwise prescribed by binding law, the obligation of Chip Hyde Products Inc. to
pay compensation is excluded, regardless of the legal argument employed.
This applies to personal injury, death, damage to buildings, loss of turnover and business,
interruption of business or other direct and indirect consequent damages.
BY OPERATING THIS MODEL YOU ASSUME FULL RESPONSIBILITY
FOR YOUR ACTIONS.
It is important to understand that Chip Hyde Products Inc. is unable to monitor whether you
follow the instructions contained in this instruction manual regarding the construction,
operation and maintenance of the aircraft, nor whether you install and use the radio control
system correctly. For this reason we at Chip Hyde Products Inc. are unable to guarantee or
provide a contractual agreement with any individual or company that the model you have
made will function correctly and safely. You, as operator of the model, must rely upon your
own expertise and judgment in acquiring and operating this model.
An R/C aircraft is not a toy! If misused, it can cause serious bodily harm and damage to
property. Fly only in open areas, preferably AMA (Academy of Model Aeronautics) approved
flying sites, following all instructions included with your radio and engine. Do not fly this or any
other model airplane after consuming any alcohol and/or drugs (both legal and/or illegal).
SUPPLIMENTARY SAFETY NOTES:
Before every session check that all of the model’s working systems function correctly, and be
sure to carry out a range check.
The first time you fly any new model aircraft we strongly recommend that you enlist the help
of an experienced modeler to help you check the model and offer advice while you are flying.
He should be capable of detecting potential weak points and errors.
Be certain to keep to the recommended CG position and control surface travels. If
adjustments are required, carry them out before operating the model. Be aware of any
instructions and warnings of other manufacturers, whose product(s) you use to fly this
particular aircraft, especially engines and radio equipment.
Please don’t ignore our warnings, or those provided by other manufacturers. They refer to
things and processes, which, if ignored, could result in permanent damage or fatal injury.

Contents of Vision 3D Assembly Manual
1. Introduction ......................................................................................................... 4
2. Intended Use ....................................................................................................... 4
3. Warranty.............................................................................................................. 4
4. Kit Contents......................................................................................................... 5
5. Items Needed to Complete the Vision 3D ........................................................... 7
5.1 Components and Hardware Needed to Complete the Vision 3D ................ 7
5.2 Tools Needed to Complete the Vision 3D ................................................... 8
5.3 Adhesives Needed to Complete the Vision 3D ........................................... 8
6Vision 3D Building Instructions............................................................................ 9
6.1 Overview and Useful Information ................................................................ 9
6.2 Covering ...................................................................................................... 9
7Wing Assembly ................................................................................................. 10
7.1 Fitting and Hinging the Ailerons ................................................................ 10
7.2 Aileron Servo Installation........................................................................... 12
8Engine Installation............................................................................................. 16
8.1 Mounting the Engine ................................................................................. 16
8.2 Fitting the Ignition Module ......................................................................... 18
8.3 Fitting the Exhaust and Fibreglass Pipe Tunnel........................................ 18
9. Undercarriage and Tail Wheel Unit Installation................................................. 20
9.1 Undercarriage Installation ......................................................................... 20
9.2 Tail Wheel Unit Installation........................................................................ 20
10. Fin, Rudder and Rudder Servo/linkage Installation....................................... 21
10.1 Fin Preparation and Gluing ....................................................................... 21
10.2 Fitting and Hinging the Rudder.................................................................. 22
10.3 Rudder Servo and Control Linkage Installation......................................... 22
11 Horizontal Stabilizers and Servos/linkages Installation..................................... 24
11.1 Elevator Servos Installation....................................................................... 24
11.2 Fitting and Hinging the Elevators .............................................................. 24
11.3 Fitting the Horizontal Stabilizers................................................................ 25
11.4 Fitting the Elevator Control Rods and Ball Raced Horns........................... 26
12. Wing Retainer Installation ............................................................................. 27
12.1 Wing Retainer Method............................................................................... 27
18. Final Finishing and Checks ........................................................................... 36
19. Chip’s Recommended Control Throws.......................................................... 37

1. Introduction
The Vision 3D is a highly aerobatic monoplane designed and sold by world
renowned aerobatic RC pilot Chip Hyde - multiple USA National, World and
TOC champion. The model is fully capable of both precision F3A type
aerobatics and full blown more extreme 3-D aerobatics.
The Vision 3D may be assembled rapidly due to plug-in wings and plug-in
horizontal stabilizers. Not only does this make assembly at your flying site
fast, but makes the model easy and accurate to construct.
The wings and stabilizers slide onto pre-fitted tubes and are aligned by anti-
rotation pins. There is a minimal amount of gluing and drilling required to
complete the assembly. This greatly reduces the time to assemble the model
and get you to your flying site.
The Vision 3D can be disassembled and broken down into two wing panels,
two stabilizer halves and a fuselage to facilitate transportation in almost any
size of vehicle. The larger the vehicle, the less you will need to remove!
The Vision 3D is designed for gas motors in the 50-cc category. The
recommended motor is the DA 50 that is shown in the assembly instructions.
The final choice of power plant is left up to the builder.
A computer radio is recommended for the Vision 3D. This is primarily because
then the Pilot can take advantage of the full capabilities of this model, using
the various mixing and servo adjustments functions that are typically
available.
Either a single or a pair of servos may be used for each aileron. The allows
either a single high torque servo to be used to drive each aileron, or in the
event only lower powered servos are available; a pair may be used.
2. Intended Use
The Vision 3D should not be regarded as a toy. This is an advanced aerobatic
plane and is recommended for pilots who are well beyond the trainer-stage
and are comfortable with flying at least an aerobatic sport plane.
3. Warranty
Defective parts will be exchanged/replaced once the original item is returned
at the owner’s expense. Contact Chip Hyde Products if you are located in
North America or Probuild Aircraft if you are located in Europe.

4. Kit Contents
The contents of the Vision 3D shipping box should be as follows:

Qty Description
2 Wing panels
2 Ailerons
1 Light weight aluminium wing tube
4 Light weight aluminium wing panel retaining fixtures & wooden mounts
2 Horizontal stabilizer panels
2
Elevators
1 Carbon fibre horizontal stabilizer tube
1 Light weight aluminium horizontal stabilizer anti rotation pin
1 Fin
1 Rudder
1 Painted fibreglass cowl
1 Fuselage
1 Fuselage hatch
1 Canopy
1 Light weight aluminium undercarriage, in three pieces + 4 retaining bolts
2 Painted fibreglass wheel pants
6 Anodised light weight aluminium control horns with integral bearings and
fixing screws
8 Black Plastic, metal pinned clevises
1 Tail wheel unit with 3 mounting screws, spring and plastic spring retainer
1 Lite-ply fuel tank mounting plate
2 4mm black cap head bolts for the U/C centre plate
2 3mm silver Philips head screws for retaining the tail plane

5. Items Needed to Complete the Vision 3D
5.1 Components and Hardware Needed to Complete the
Vision 3D
Qty Description
1
50cc Motor and Propeller
1
3-1/2 inch ultimate Truturn spinner
1
16-24oz fuel tank
2
3-1/2 inch main wheels
2
4 & ¼ inch 4-40 thread elevator pushrods
2
4 & ¼ inch 4-40 thread in-board aileron servo pushrods WHEN USING ONE
SERVO PER AILERON
4 4 & ¼ inch 4-40 thread in-board aileron servo pushrods WHEN USING TWO
SERVOS PER AILERON
1
Bag of 4-40 lock nuts for all linkages
6
4-40 pin clevises
6
4-40 ball-links
2
Aileron servos (130 oz inch) WHEN USING ONE SERVO PER AILERON
4
Aileron servos (60 oz inch) WHEN USING TWO SERVOS PER AILERON
1
Rudder servo (200 oz inch)
2
Elevator servos (130 oz inch)
1
Throttle Servo
Extension
Leads
• 2 x for in-board aileron servos (approx. 16 - 20 inches in length)
• 2 x for out-board aileron servos (approx. 40 – inches in length) WHEN
USING TWO SERVOS PER AILERON
• 2 x for elevator servos (approx. 28 inches in length)
• 1 x for rudder servo (approx. 28 inches in length)
• 2 x for permanent connection to Rx aileron connectors (short)
1
Receiver
1
Receiver switch (heavy duty)
1
Receiver battery (2000 mAh minimum)

1
Ignition switch (heavy duty)
1
Ignition battery
2
Axels – Dubro Cat No. 249 suggested
5.2 Tools Needed to Complete the Vision 3D
• Modelling Knife
• Fine blade saw
• Flat file
• Circular file
• Electric drill and a selection of drill bits
• 3mm tap
• 4mm tap
• Philips screwdriver (small)
• Pliers
• Allen wrenches/keys both USA and Metric
• A cordless drill
• Drill sets both USA and Metric
• Dremel sanding drum tool
• Sand paper
• A thin marker pen 1/32 line thickness or thinner
5.3 Adhesives Needed to Complete the Vision 3D
• Thin CA
• Medium CA
• Slow CA
• CA kicker (optional)
• 20 minute Epoxy

6 Vision 3D Building Instructions
6.1 Overview and Useful Information
Welcome to the assembly instruction for you Vision 3D. These instructions
have been sequenced to make the handling of the model as easy as possible
and ensure that it is fitted out in a logical order.
For example the batteries are not fitted until very near to the end of the
assembly process, allowing them to be positioned to achieve a perfect centre
of gravity without the addition of extra, unnecessary weight.
Items such as radio gear, engine and other equipment/components are shown
as options and examples. As the owner and builder of this model you are at
liberty to substitute products of your own preference.
The Vision 3D is intended for experienced builders and pilots and NOT as a
first model. As such it is assumed that the builder will have previously
assembled other models.
Accordingly these instructions are not exhaustive as it is assumed that the
builder will have experience of the basics required to assemble a radio
controlled model aeroplane.
We strongly suggest that the builder obtains a foam cradle to hold the
fuselage during the assembly and fitting out process. This will provide support
and protect the covering from becoming damaged or marked when sitting on
a workbench surface.
We also recommend that the wings and stabs are placed on a large sheet of
soft foam during their assembly and fitting out, again to protect them against
marks or damage from a workbench surface.
6.2 Covering
It is important to seal all the edges of the film covering & trim of the
model with a sealing iron from out of the box before attempting to
fly the model – especially the up-wind portions. In the event that
any sections of film will not seal due to oil or dirt residue clean
them with Windex or 409 cleaner.
To greatly increase the life span of the covering it is advisable to
seal all the edges of the film with clear nail varnish. This procedure
will prevent trim from detaching during the life of the model.

7 Wing Assembly
7.1 Fitting and Hinging the Ailerons
Each aileron is supplied with 7 Mylar hinges.
First mark a centerline across each hinge – be careful to orientate the hinge
correctly, drawing the centerline across the width of the hinge.
Then fold the hinge a few times along the centerline and gently compress the
hinge line fold with a pair of pliers, to help form a good hinge point.
Next use two pins to center each hinge, as pictured below. The pins are
pushed through the hinge centerline.
Now fit an aileron (leaving the hinge pins in place) to its corresponding wing
panel. Ensure that all 7 hinges have been fitted.
There should be no gap between the leading edge of the aileron and the
training edge of the wing panel.

Now remove the pins and then carefully drip thin CA onto the exposed section
of each hinge as pictured below. Gently work the aileron up and down while
adding CA. This will help the CA to fully wick into each hinge.
We suggest adding CA to the inner and outer most hinges first, as this will
help ensure that the aileron is properly aligned with the wing itself and avoid
tapering wing/aileron gaps.
Repeat the above process for the second wing panel and aileron.
If available, use Acetone dripped onto a rag to wipe away any excess CA that
happens to run. Use denatured alcohol to clean up later.

7.2 Aileron Servo Installation
The Vision 3D is designed to use either a single high torque (130 oz inch)
aileron servo, or a pair of medium torque (60 oz inch) aileron servos.
While either approach will work successfully, we prefer the use of a single
high torque servo and the following instructions describe the fitting process.
Select a wing panel and a servo. Add an extension lead to the servo long
enough that the lead can exit the wing root and be fed into the fuselage,
leaving sufficient extension lead length to reach the receiver – approximately
8 inches.
Ensure the servo lead/extension lead connectors are taped or tied together to
provide a secure connection that will not pull apart once installed. Shrinking a
1inch length of heat shrink tubing over the joined connectors is a particularly
good solution.
Pull cords are fitted to the outer servo mounting points. These are only used
when fitting two aileron servos per wing panel.
When using a single servo, hold the wing panel vertically with the face of the
wing tip pointing upwards. Now feed the end of the extension lead attached to
the servo into the inboard servo mounting point. There is a generous hole
located in the wing rib just inboard of the mounting point. Feed the extension
lead through this hole until the end of the lead has been fed through to the
wing root.
Now insert the servo into its mounting point as pictured below.
Using a suitably sized drill bit for your chosen servos, drill holes into the servo
mounting plates for the servo mounting screws.

Remove the servo and add a few drops of thin CA into each hole.
Finally re-fit the servo and screw it into place. Cover over the unused
mounting position for the optional second aileron servo.
7.3 Aileron Linkage Installation
IMPORTANT
THIS SECTION WILL EXPLAIN THE AILERON LINAKGE
INSTALLATION. AS PART OF THIS YOU WILL INSTALL THE BALL
BEARING CONTROL HONRNS AND ACCOMPANYING METAIL
PINNED CLEVISES.
DO NOT TRY TO INSTALL THE CLEVIS INTO THE BALL BEARING
CONTROL HORNS BUY SPREADING THE CLEVIS WITH A FLAT TIP
SCREW DRIVER, THAT IS NOT THE WAY THEY ARE DESIGNED TO
WORK.
UNSCREW THE PHILLIPS HEAD SCREW PIN AND REMOVE IT
COMPLETELY FROM THE CLEVIS ITSELF. THEN SLIP THE HORN
TROUGH THE EMPTY SLOT AND REINSTALLL THE SCREW IN THE
CLEVIS.
NOT FOLLOWING THESE INSTRUCTIONS CAN CAUSE THE PLASTIC
THE CLEVIS IS MADE FROM TO FATIGUE AND FAILURES IN THE
BALLBEARING FROM THE EXCESSIVE SIDE LOADS PUT ON THE
INNER RACE. THIS IS NOT THE TYPE OF LOADS THESE BEARINGS
ARE DESIGNED TO WITHSTAND.
WE RECOMMEND THE USE OF THE SUPPLIED CLEVIS ONLY AS
THEY WERE DESIGNED SPECIFICALLY FOR THIS HORN.
CHIP

If it is not already in place, fit the servo arm - it will be used as a guide. We
recommend the use of 1inch length servo arms.
Now use a small square to set the position of the end of the horn, so that the
aileron control rod will be positioned at 90 degrees to the hinge line of the
ailerons. Mark this position on the leading edge of the aileron itself using a
fine marker pen. Now draw a second parallel line on the aileron 1/5th inch
inboard (as marked in the diagram below in blue).
This is the correct center line position of the aileron ballbearing control horn,
which will stop large servo arm movements from straining the aileron ball
bearing control horn and clevis.
A
ileron
servo
MARK CONTROL
HORN CENTRE
LINE HERE!
Control rod
centre line
90°
90°
Now place a ballbearing control horn onto the plywood triangular mounting
plate that is installed into the surface of the aileron. The center of the horn
should be over the centerline you have just marked, facing down this line and
angled very slightly towards the end of the servo horn/arm.
The center of the control horn ball bearing should be positioned directly over
the hinge point.
Dry fitting the aileron control rod to the servo arm and ball bearing aileron
control horn may assist with the above alignment procedures, as will taping
the servo into the neutral position with masking tape.

Once properly aligned mark the positions for the ball bearing aileron control
horn fixing screws and then using a 1/32 drill bit, drill fixing holes into the
aileron. Be careful not to drill the whole way through the aileron!
Remove a small triangle of covering material in between the three screw
holes you have just drilled. Finally apply a layer of CA (slow cure CA) to the
wood area exposed by the film removal, & also a small amount of CA to each
hole drilled for the horn mounting holes, then immediately screw the horn into
place, this provides an extremely strong & light weight fixing of the control
horn.
You may now fit the aileron control rod. The supplied metal pin clevises are
used to connect to the ball bearing control horn and we recommend ball links
for attachment to the servo horn.
Now repeat the above steps on the opposite wing panel.
In the event you are fitting dual aileron servos, obviously the above steps will
have to be repeated 3 more time to complete both wings. Care should be
taken when using dual servos to ensure that the servos are not ‘fighting’ each
other through their movement ranges.
This may be achieved by fitting match boxes, or by cutting each aileron in
half, plugging each servo into an individual receiver channel with appropriate
transmitter mixing and then matching each servos movement using end point
transmitter adjustments.

8 Engine Installation
8.1 Mounting the Engine
The Vision 3D has been specifically designed for the DA50R gas motor,
designed and manufactured by Desert Aircraft.
Many other suitable motors are available that can be used to power the Vision
3D, but the next steps in the instructions describe the mounting and fitting out
process for the DA50R.
First, using the template provided below (a template of the correct size is at
the end of these instructions), mark mounting holes for the 4 DA50R
standoffs.
The template positions the motor with the cylinder head at about the 7 O’clock
position. This will allow a pitts style muffler or header for a pipe to be fitted,
with minimal cutting required in the side of the cowling to clear these items.
Now drill the standoff mounting holes and remove the section of firewall that is
required to clear the carburetor.
It is important that 1-inch squares of 2-6 oz per sq inch fiberglass cloth are
applied to the firewall over each standoff mounting position. This will stop the
standoff from compressing and more importantly wearing the wood, which will
cause the motor to loosen. Clue the squares of cloth in place using medium
CA.

Loosely mount the motor in place as pictured below:
1 & ¼ inch long standoffs are needed to obtain the correct balance point for
the Vision 3D with convenient battery positioning/mounting.
Mark the hole positions for the firewall for the throttle and choke linkages. Also
mark the hole positions for the fuel tube line from the tank to the carburetor
and a filler tube line to the tank.
Remove the motor and drill the required holes for the linkages and fuel tubing.
Fuel proof the firewall and other exposed wood around the underbelly area.
Once dry, securely re-mount the motor.
Use large diameter washers on the bolts that pass through the firewall into the
standoffs, again to stop the wood being compressed and eliminate wear. Use
red Loctite on the 8 standoff bolts to stop them from vibrating loose.

8.2 Fitting the Ignition Module
Mount the ignition module on a foam pad or within a foam box. We suggest
that the module is mounted within the fuselage immediately behind the
firewall.
It is important to ensure that the ignition leads are kept away from sharp
edges. Broken shielding on the plug lead may cause radio interference!
A ring of foam used to line the fuselage cut out hole for the leads will provide
protection against chafing, as pictured below:
8.3 Fitting the Exhaust and Fibreglass Pipe Tunnel
Now fit the exhaust system of your choice.
For pipe muffler systems a header is available that has been specifically
designed to fit the Vision 3D.
We advise that pipe mufflers (such as the MTW TD75) are supported at both
ends.
Because the manifold is non-flexible, it is advisable to install the pipe on a
flexible mounting system front & rear of the silencer. The Dave Brown “Hush
clamps” work well, but have to be insulated from the heat of the Gas engine
exhaust. You will have to find a larger “o” ring from a motorist store of
sufficient length for the large diameter of the MTW silencer.
Hard mounting points for the pipe mounts can be installed between the
fuselage formers prior to the fitting of the pipe tunnel. We would recommend
Dave brown 40 Hush clamp for the front mounting, this being placed on the
manifold /pipe joiner which is made of a Teflon material, as this will help
isolate the heat from the hush clamp.

To further insulate the hush clamp, slide a length of appropriate sized silicon
tube over the Teflon tube where the hush clamp will be placed. The silicon
isolator will protect the “o” ring as well as the clamp from the intense heat of
the exhaust.
The rear pipe mount needs insulating from the heat also, we recommend the
“60” Hush clamp with silicon insulation as described for the front hush clamp
installation.
The fibreglass pipe tunnel may now be fitted, ensure that any holes necessary
for the installation of the pipe mounts are already drilled to ensure a easy
installation.
This can be screwed in place or glued with 20 minute epoxy and micro
balloons. The section of the tunnel over the undercarriage mounting plate
(between the two adjacent formers) will need to be carefully removed with the
razor saw, after the tunnel has been fixed in place.

9. Undercarriage and Tail Wheel Unit Installation
9.1 Undercarriage Installation
The vision 3D has been designed with a three-piece undercarriage assembly
that allows the legs to be removed, for easier transportation and storage of
the fuselage. This assembly is pictured below:
The fuselage is supplied with captive nuts fitted in place for the 4mm
undercarriage mounting bolts. Using the 6 mounting bolts fit the undercarriage
in place. Use red Loctite on the two center bolts for the joining plate; as in the
event the undercarriage legs are removed these bolts will be left in place.
For now leave the axels, wheels and pants unfitted.
9.2 Tail Wheel Unit Installation
While the fuselage is still upside down from fitting the undercarriage, fit the tail
wheel unit using the supplied mounting screws as shown in the picture below.
Add some thin CA to the fixing holes after drilling them and before screwing
the tail wheel unit and black plastic (rudder) spring retainer in place.
Table of contents
Popular Toy manuals by other brands
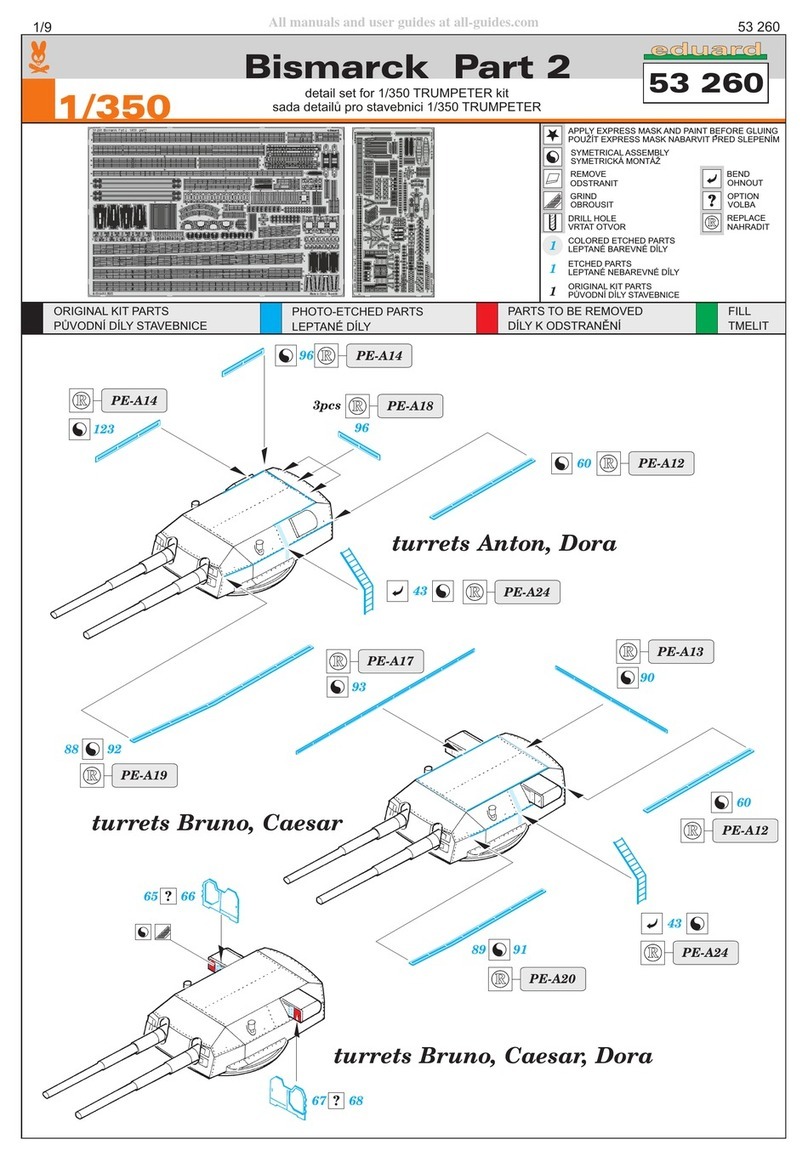
Eduard
Eduard Bismarck Part 2 Assembly instructions
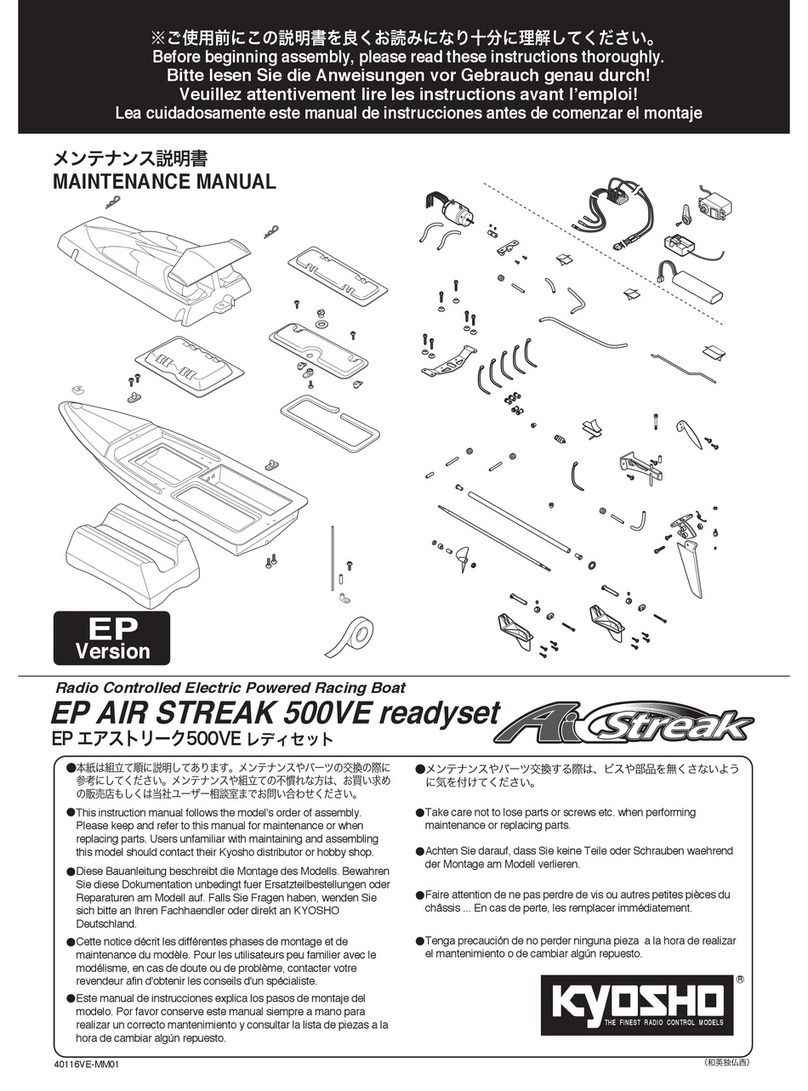
airstreak
airstreak 500VE EP Maintenance manual

Eduard
Eduard B-26B-50 Invader Assembly instructions
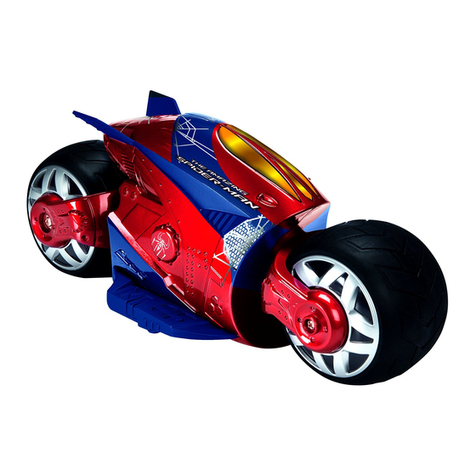
majorette
majorette THE AMAZING SPIDER-MAN CYBER CYCLE operating instructions

B.toys
B.toys B. play Walk 'n' POP! BX4501 quick start guide
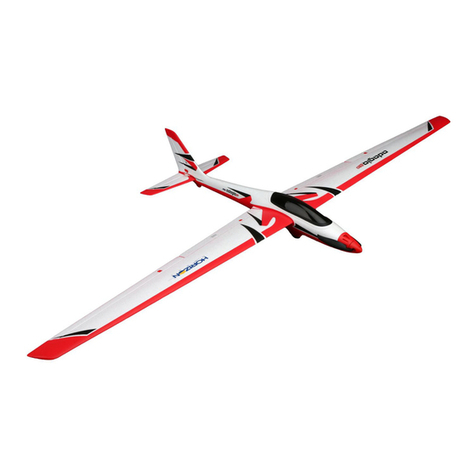
E-FLITE
E-FLITE Adagio 280 instruction manual