Chrontel CH7033B Guide

AN-B012
Application Notes
206-1000-012 Rev1.9, 06/30/2020 1
Chrontel
PCB Layout and Design Guide for CH7033B
1.0 INTRODUCTION
Chrontel CH7033B is specifically designed for consumer electronics device and PC markets for which multiple high
definition content display formats are required. With its advanced video encoder, flexible scaling engine and easy-
to-configure audio interface, the CH7033B satisfies manufactures’ products display requirements and reduces their
cost of development and time-to-market.
This application note focuses only on the basic PCB layout and design guidelines for CH7033B
HDTV/VGA/HDMI/DVI encoder. Guidelines in component placement, power supply decoupling, grounding, input
/output signal interface are discussed in this document.
The discussion and figures that follow reflect and describe connections based on the 88-pin QFN package of the
CH7033B. And in the figures, only HDMI connector will been shown. Please refer to the CH7033B datasheet for
the details of the pin assignments.
2.0 COMPONENT PLACEMENT AND DESIGN CONSIDERATIONS
Components associated with the CH7033B should be placed as close as possible to the respective pins. The
following discussion will describe guidelines on how to connect critical pins, as well as describe the guidelines for
the placement and layout of components associated with these pins.
2.1 Power Supply Decoupling
The optimum power supply decoupling is accomplished by placing a 0.1μF ceramic capacitor to each of the power
supply pins as shown in Figure 1. These capacitors (C1, C2, C4, C5, C7, C8, C10, C11, C13, C14, C16, C18, C19,
C22) should be connected as close as possible to their respective power and ground pins using short and wide traces
to minimize lead inductance. Whenever possible, a physical connecting trace should connect the ground pins of the
decoupling capacitors to the CH7033B ground pins, in addition to ground vias.
2.1.1 Ground Pins
The analog and digital grounds of the CH7033B should be connected to a common ground plane to provide a low
impedance return path for the supply currents. Whenever possible, each of the CH7033B ground pins should be
connected to its respective decoupling capacitor ground lead directly, then connected to the ground plane through a
ground via. Short and wide traces should be used to minimize the lead inductance. Refer to Table 1 for the Ground
pins assignment.
2.1.2 Power Supply Pins
The power supply include AVDD, AVDD_DAC, VDDH, AVDD_PLL, VDDIO, DVDD, VDDMQ, VDDMS.
Refer toTable1 for the Power supply pins assignment. Refer to Figure 1 for Power Supply Decoupling.

CHRONTEL AN-B012
2 206-1000-012 Rev1.9, 06/30/2020
Table 1: Power Supply Pins Assignment of the CH7033B
Pin Assignment
#Of Pins
Type
Symbol
Description
30,41
2
Power
VDDH
DVI/HDMI Power Supply (3.3V)
10,42
2
Power
DVDD
Digital Power Supply (1.8V)
23,46
2
Power
AVDD
Analog Power Supply (3.3V)
73, 77
2
Power
AVDD_DAC
DAC power supply (3.3V)
71
1
Power
AVDD_PLL
PLL Power Supply (1.8V)
53,61
2
Power
VDDMQ
SDRAM output buffer Power Supply (3.3V)
9,60
2
Power
VDDMS
SDRAM Power Supply (3.3V)
33,38
2
Ground
VSSH
DVI/HDMI Ground
83
1
Power
VDDIO
IO Power Supply (1.2-3.3V)
45
1
Ground
DGND
Digital Ground
22,47
2
Ground
AGND
Analog Ground
75, 79
2
Ground
AGND_DAC
DAC Ground
70
1
Ground
AGND_PLL
PLL Ground
52,62
2
Ground
GNDMQ
SDRAM output buffer Ground
59,11
2
Ground
GNDMS
SDRAM Ground
L8 47R 100MHz
1 2
L1 47R 100MHz
1 2
AVDD_PLL
C10
0.1uF C11
0.1uF
AVDD
C12
10uF
L2 47R 100MHz
1 2
L3 47R 100MHz
1 2
L4 47R 100MHz
1 2
C16
0.1uF
C6
10uF
VDDMS
C18
10uF
VDDIOVDDIO
DVDD
C9
0.1uF
C8
0.1uF
VCC3_3
C7
10uF
C21
0.1uF
C22
10uF
C15
0.1uF
C13
10uF
C5
0.1uF
C17
0.1uF
QFN
U1
VDDIO
83
DVDD 10,42
VDDMQ
53,61
VDDMS 9,60
AVDD 23,46
AVDD_PLL 71
VDDH
30,41
DGND 45
GNDMQ
52,62
GNDMS 11,59
AGND 22,47
AGND_PLL 70
VSSH
33,38
AGND
22,47
AVDD_DAC
73,77
AGND_DAC
75,79
C4
0.1uF
VCC1_8
C3
0.1uF
C2
0.1uF
C1
10uF
VCC3_3
AVDD_DAC
VDDMQ
VDDHVDDHVDDHVDDHVDDHVDDHVDDHVDDH
C14
0.1uF
C20
0.1uF
C19
10uF
L5 47R 100MHz
1 2
L6 47R 100MHz
1 2
L7 47R 100MHz
1 2
Figure 1: Power Supply Decoupling and Distribution
Note:
1. All the Ferrite Beads described in this document are recommended to have an impedance of less than 0.05 Ω
DC; 23 Ωat 25MHz & 47 Ωat 100MHz. Please refer to Fair Rite part #2743019447 for details or an equivalent
part can be used for the diagram. .
2.1.3 On chip power-on reset function’s sequence
There are two methods for chip power-on reset.
1. The ResetB signal can be generated by on board Resistor and Capacitor delay which can be refer to Figure 2. For
hard ware circuit, please refer to 2.3 RESETB.

CHRONTEL AN-B012
206-1000-012 Rev1.9, 06/30/2020 3
Figure 2: Power-on Reset Function’s Sequence on board
2. ResetB signal is generate by system global reset. In this case, the power supply should be valid and stable for at
least 20ms before the reset signal is valid. The pulse width of valid reset signal should be at least 100us. Otherwise,
the chip can’t work well. The timing is shown in Figure 3.
Figure 3: Power-on Reset Function’s Sequence external global reset
Note:
1. The rising threshold of RSTB is 2.4V.
2. The falling threshold of RSTB is 0.4V.
2.2 Internal Reference Pins
• ISET pin
This pin sets the DAC current. A 1.2K ohm, 1% tolerance resistor should be connected between this pin and
AGND_DAC as shown in Figure 4. This resistor should be placed with short and wide traces as near as possible to
CH7033B.
<9ms
AVDD
Other
Powers
ResetB
>20ms
AVDD
Other
Powers
ResetB
>100
us

CHRONTEL AN-B012
4 206-1000-012 Rev1.9, 06/30/2020
U1
ISET 80
AGND_DAC 79
R1
1.2K(1%)
QFN
Figure 4: ISET pin connection
2.3 General Control Pins
• RESETB
This pin is the chip reset pin for CH7033B, which is internally pulled-up, places the device in the power on reset
condition when this pin is low. A power reset switch can be placed on the RESETB pin on the PCB as a hardware
reset for CH7033Bor connect to the system’s global reset as shown in Figure 5. When the pin is high, the reset
function can also be controlled through the serial port.
Global reset
U1
RESETB 7
AVDD
SW1
P8058SS-ND
ResetB
C1
0.1uF
R1
1M
U2
RESETB 7Global ResetResetB
AVDD
C2
0.1uF
R2
1M
On board reset
Figure 5: RESETB pin connection
• GPIO
This pin is general purpose input/output. It can be connected to the input signals such as the DE, GCLK, H,V for
checking input signals available or achieving other functions.

CHRONTEL AN-B012
206-1000-012 Rev1.9, 06/30/2020 5
• XI/FIN and XO
CH7033B have capability to accept external crystal with frequencies from 2.3 MHz to 64 MHz. However, we
recommend predefined crystal frequency is 13.5MHz or 27MHz. The crystal must be placed as close as possible to
the XI and XO/FIN pins, with traces connected from point to point, overlaying the ground plane. Since the crystal
generates timing reference for the CH7033B, it is very important that noise should not couple into these input pins.
Traces with fast edge rates should not be routed under or adjacent these pins. In addition, the ground reference of the
external capacitors connected to the crystal pins must be connected very close to the CH7033B.
The crystal load capacitance, CL, is usually specified in the crystal spec from the vendor. As an example to show the
load capacitors Figure 6 gives a reference design for crystal circuit design.
QFN
U1
XI/FIN 68
XO 67
X1
535-9118-1-ND(27 MHz)
GND
4
P1
1GND 2
P2 3
XI/FIN
C2
18pF
12
XO C1
18pF
12
Figure 6: Crystal Pins
Reference Crystal Oscillator
CH7033B integrate an oscillator circuit that allows a predefined-frequency crystal to be connected directly.
Alternatively, an externally generated clock source may be supplied to CH7033B. If an external clock source is used,
it should be of CMOS level specifications. The clock should be connected to the XI pin, and the XO pin should be left
open. The external source must exhibit ±20ppm or better frequency accuracy, and have low jitter characteristics.
If a crystal is used, the designer should ensure that the following conditions are met:
The crystal is specified to be predefined-frequency, ±20 ppm fundamental type and in parallel resonance (NOT series
resonance). The crystal should also have a load capacitance equal to its specified value (CL).
External load capacitors have their ground connection very close to CH7033B (Cext).
To be able to tune, a variable capacitor may be connected from XI to ground.
Note that the XI and XO pins each has approximately 10 PF (Cint) of shunt capacitance internal to the device. To
calculate the proper external load capacitance to be added to the XI and XO pins, the following calculation should be
used:
Cext = (2 x CL) - Cint - 2CS
Where
Cext = external load capacitance required on XI and XO pins.
CL= crystal load capacitance specified by crystal manufacturer.

CHRONTEL AN-B012
6 206-1000-012 Rev1.9, 06/30/2020
Cint = capacitance internal to CH7033B (approximately 10-15 pF on each of XI and XO pins).
CS= stray capacitance of the circuit (i.e. routing capacitance on the PCB, associated capacitance of crystal holder
from pin to pin etc.).
In general,
CintXI = CintXO = Cint
CextXI = CextXO = Cext
Such that
CL= (Cint + Cext) / 2 + CSand Cext = 2 (CL- CS) - Cint=2CL- (2CS+ Cint)
Therefore CLmust be specified greater than Cint /2 + CSin order to select Cext properly.
After CL(crystal load capacitance) is properly selected, care should be taken to make sure the crystal is not operating
in an excessive drive level specified by the crystal manufacturer. Otherwise, the crystal will age quickly and that in
turn will affect the operating frequency of the crystal.
For detail considerations of crystal oscillator design, please refer to AN-06.
2.4 Serial Port Control for CH7033B
• SPC and SPD
SPD and SPC function as a serial interface where SPD is bi-directional data and SPC is an input only serial clock. In
the reference design, SPD and SPC pins are pulled up to +1.8V ~ +3.3Vwith 6.8 kΩresistors as shown in Figure 7.
• DDC_SC and DDC_SD
DDC_SC and DDC_SD are used to interface with the DDC of DVI/HDMI receiver and the serial PROM. This DDC
pair needs to be pulled up to 5V through 1.8 KΩ resistors (Refer to Figure 7).
• SPCM and SPDM
SPCM and SPDM can load firmware from external CH9904 BOOT ROM (QFN). In the reference design, SPDM and
SPCM pins are pulled up to +3.1V ~ +3.5Vwith 6.8 KΩresistors as shown in Figure 7.
Note: CH9903 hard wire address mustn’t be 50h
CH9904 hard wire address should be 57h.

CHRONTEL AN-B012
206-1000-012 Rev1.9, 06/30/2020 7
DDC_SD
DDC_SC
U2
CH9903
GP1
1
GP2
2
GP3
3
GND
4SPD 5
SPC 6
WE 7
VCC 8
VDD5
R4
1.8K
1 2
R5
1.8K
1 2
R6 10K
R11
6.8K
VDD5_DDC
R10
6.8K
C1
0.1uF
SPDM
R12
6.8K
1 2
R14 10K
R13
6.8K
1 2
U3
CH9904
GP1
1
GP2
2
GP3
3
GND
4SPD 5
SPC 6
WE 7
VCC 8
SPCM
VCC3_3
C2
0.1uF
12
VCC3_3VCC3_3
Reserved, please don't solder
U24
GTL2002
GND
1
SREF
2
S1
3
S2
4D2 5
D1 6
DREF 7
GREF 8
U1
SPDM
69
DDC_SD
64 DDC_SC
63
SPCM
72
SPD
55 SPC
54
R17
10K
1 2
R16
10K
1 2
VDD5_DDC
MONSDA
MONSCL
R15
200K
1 2
R1
6.8K
1 2
SPD
SPC
R2
6.8K
1 2
VCC3_3
R3
6.8K
VDD5
R9
6.8K
DDC_SC and DDC_SD connect to HDMI connector, MONSCL and MONSDA connect to VGA connector
It is highly recommended to use VDD5_DDC, the diode can prevent the back driver from TV
or Monitor
For HDMI compliance test, please makesure the DDC pull up voltage(VDD5_DDC) is less than
5.5V and more than 4.5V, then the diode forward voltage must be less than 0.5V
The address of CH9904 is 57h and for auto loading firmware;
CH9903 for HDCP;
QFN
D13
SM5817
VDD5
Figure 7: Serial Port Interface: DDC_SC, DDC_SD, SPCM, SPDM and SPC, SPD pins of CH7033B
2.5 Input Pins
Data Inputs
CH7033B can accept up to 24 data inputs, as shown in Figure 8, from a digital video port of a graphics controller.
The swing is defined by VDDIO (1.2 ~ 3.3V).
Unused Data input pins should be pulled low with 10kΩresistors or shorted to Ground directly.
H/V Sync Pins
The horizontal/vertical sync pins can be used as inputs as shown in Figure 8.
DE/CSB
The DE/CSB pin is used as a data input indicator (Refer to Figure8). When the pin is high, the input data is active.
When the pin is low, the input data is blanking.
If DE/CSB is not used, it can be left open or pulled down to the Ground.
GCLK

CHRONTEL AN-B012
8 206-1000-012 Rev1.9, 06/30/2020
The GCLK input is the clock signal input to the device for using with the H, V, DE and D [23:0] data.
QFN
D [ 0 ]
29
D [ 1 ]
28
D [ 2 ]
27
D [ 3 ]
26
D [ 4 ]
25
D [ 5 ]
21
D [ 6 ]
20
D [ 7 ]
19
D [ 8 ]
18
D [ 9 ]
17
D [ 1 0 ]
16
D [ 1 1 ]
15
D [ 1 2 ]
14
D [ 1 3 ]
13
D [ 1 4 ]
12
D [ 1 5 ]
8
D [ 1 6 ]
6
D [ 1 7 ]
5
D [ 1 8 ]
4
D [ 1 9 ]
3
D [ 2 0 ]
2
D [ 2 1 ]
1
D [ 2 2 ]
88
D [ 2 3 ]
87
V
85 H / W E B
86
G C L K
82
D E /C S B
84
Controller
Graphics
Figure 8: CH7033B Data Input Pins
2.6 SPDIF Interface
SPDIF (pin 56) is an SPDIF audio input pin.
The SPDIF signal to CH7033B is required to be VL<0.4V and VH>2.4V. SPDIF signal has two input ways for
CH7033B. SPDIF signal from audio codec is 0-2.5V, then it can be connected to the CH7033B directly; if through a
RCA connector, the signal on RCA connector is AC coupled signal, signal level of which is 0.5V to 1V. Therefore,
voltage level shifting is strongly recommended. If the current SPDIF circuit is considered too complicated, a simple
circuit can be used (Refer to Figure 9).

CHRONTEL AN-B012
206-1000-012 Rev1.9, 06/30/2020 9
1
2
H1
H2
J2
SPDIF IN
C1
1uF
1
2
H1
H2
J4
SPDIF IN
SPDIF
SPDIF
VCC2_5/3_3
1 2
147
U1A
74HCU04/SO_0
3 4
147
U1B
74HCU04/SO_0
SPDIF
R5
330
R1
75
1
2
H1
H2
J3
SPDIF IN R4
10K
C2
0.1uF
R2
100
R3
10K
Au dio codec is 0 -2.5V
AC coupled signa l,strongly recommended circuit
AC coupled signa l,simple circuit
Figure 9: SPDIF pin of CH7033B
2.7 I2S Interface
I2S audio input can be configured through programming CH7033B registers. An I2S bus design consists of three
serial bus lines: a line with data channel [SD], a word select line [WS], and a clock line [SCK]. Data is transmitted
two's complement, MSB first.
U1
I2S_D/SPDIF 56
I2S_CK 58
I2S_WS 57
I2S Source
Figure 10: CH7033B I2S Input Pins

CHRONTEL AN-B012
10 206-1000-012 Rev1.9, 06/30/2020
2.8 DVI/HDMI Outputs
The TLC, TLC*, TDC [2:0], TDC [2:0]* signals are high frequency differential signals that need to be routed with
special precautions. Since those signals are differential, they must be routed in pairs.
2.8.1 Differential Pair Impedance
To match the external cable impedance and maintain the maximal energy efficiency it is important to meet the
impedance target of 100 Ω±10% for the differential data/clock traces. The restriction of this impedance target is to
prevent any loss of signal strengths resulting from a reflection of unwanted signals. The impedance can be acquired
by proper design of trace length, trace width, signal layer thickness, board dielectric, etc. The DVI/HDMI differential
pairs should be routed on the top layer directly to the DVI/HDMI connector pads if possible.
2.8.2 Trace Routing Length
To prevent from capacitive and impedance loading, trace lengths should be kept as minimal as possible. Vias and
bends should always be minimized; inductive effects may be introduced, causing spikes in the signals. Trace routing
lengths from CH7033B to the HDMI/DVI connector are limited to a maximum of 2 inches. The CH7033B should be
as close to the HDMI/DVI connector as possible.
2.8.3 Length Matching for Differential Pairs
The HDMI/DVI specifies the intra-pair skew and the inter-pair skew as in Table 2. The intra-pair skew is the
maximum allowable time difference on both low-to-high and high-to-low transitions between the true and
complement signals. The inter-pair skew is the maximum allowable time difference on both low-to-high and high-to-
low transitions between any two single-ended data signals that do not constitute a differential pair.
Table 2: Maximum Skews for the HDMI/DVI Transmitter
Skew Type
Maximum at Transmitter
Intra-Pair Skew
0.15 Tbit
Inter-Pair Skew
0.20 TPixel
Where Tbit is defined as the reciprocal of Data Transfer Rate and TPixel is defined as the reciprocal of Clock Rate.
Therefore, TPixel is 10 times Tbit. In other words, the intra-pair length matching is much more stringent than the inter-
pair length matching.
It is recommended that length matching of both signals of a differential pair be within 5 mils. Length matching should
occur on a segment by segment basis. Segments might include the path between vias, resistor pads, capacitor pads, a
pin, an edge-finger pad, or any combinations of them, etc. Length matching from one pair to any other should be
within 100 mils.
Note that lengths should only be counted to the pins or pad edge. Additional etch within the edge-finger pad, for
instance, is electrically considered part of the pad itself.
2.8.4 ESD Protection for HDMI/DVI Interface
In order to minimize the hazardof ESD, a set of protection diodes are highly recommended for each DVI/HDMI
Output (data and clock).
International standard EN 55024:1998 establishes 4kV as the common immunity requirement for contact discharges
in electronic systems. 8kV is also established as the common immunity requirement for air discharges in electronic
systems. International standard EN 61000-4-2:1995 / IEC 1000-4-2:1995 establishes the immunity testing and
measurement techniques.

CHRONTEL AN-B012
206-1000-012 Rev1.9, 06/30/2020 11
System level ESD testing to International standard EN 61000-4-2:1995 / IEC 1000-4-2:1995 has confirmed that the
proper implementation of Chrontel's recommended diode protection circuitry, using SEMTECH Rclamp0524P diode
array devices, will protect the CH7033B device from DVI/HDMI panel discharges of greater than 8kV (contact) and
16kV (air). The RClamp0524P have a typical capacitance of only 0.30pF between I/O pins. This low capacitance
won’t bring too much bad effect on DVI/HDMI eye diagram test.
Figure11(A) and (B) show the connection of DVI/HDMI connectors, including the recommended design of
SEMTECH Rclamp0524P diode array devices. DVI/HDMI connector is used to connect the CH7033B DVI/HDMI
outputs to the display panels.
QFN
U1
TLC* 31
TDC2* 39
TDC2 40
TLC 32
TDC0* 34
TDC0 35
TDC1* 36
TDC1 37
IRQ 81
HPD 51
IRQ
HPD
C1
0.5PF
TLC
R1
68
C4
0.5PF
TLC*
TDC2
TDC2*
R3
68
C3
0.5PF
TDC1*
TDC1
C2
0.5PF
R2
68
TDC0
TDC0*
R4
68
Figure 11(A): The connection of the DVI/HDMI outputs

CHRONTEL AN-B012
12 206-1000-012 Rev1.9, 06/30/2020
TLC*
TDC2*
TLC*
TDC2
TLC
TDC2
TLC
TDC2*
RClamp0524P
I/O 1
1
I/O 7 9
I/O 2
2
GND
3
I/O 3
4
I/O 4
5I/O 5 6
I/O 6 7
GND 8
I/O 8 10
TDC2*
TDC0
TDC0*
TDC1
TDC1*
TLC
TLC*
VDD5
C1
0.1uf C2
10uf
HDMI Conn
TMDA Data2+
1TMDA Data2 Shield 2
TMDA Data2-
3TMDA Data1+ 4
TMDA Data1 Shield
5TMDA Data1- 6
TMDA Data0+
7TMDA Data0 Shield 8
TMDA Data0-
9TMDA Clock+ 10
TMDA TMDA Clock Shi eld
11 TMDA Clock- 12
CEC
13 Reserved 14
SCL
15 SDA 16
DDC/CEC Ground
17 +5V Power 18
HPDET
19
R1
47k
HPDHPD
DDC_SC DDC_SD
F1 MINISMDC050CT-ND
TDC2
TDC1*
TDC0*
TDC1*
TDC0
TDC1
TDC0
TDC1
RClamp0524P
I/O 1
1
I/O 7 9
I/O 2
2
GND
3
I/O 3
4
I/O 4
5I/O 5 6
I/O 6 7
GND 8
I/O 8 10
TDC0* DDC_SD
DDC_SC
HPD
DDC_SC
HPD
DDC_SD
RClamp0524P
I/O 1
1
I/O 7 9
I/O 2
2
GND
3
I/O 3
4
I/O 4
5I/O 5 6
I/O 6 7
GND 8
I/O 8 10
Figure 11(B): The connection of the HDMI outputs-CH7033B HDMI connectors
The following is the description for each DVI/HDMI interface pins
• DVI/HDMI Link Data Channel (TDC [2:0] and TDC [2:0]*)
These pinsprovide DVI/HDMI differential outputs for datachannel 0 (blue), data channel 1 (green) and data channel 2 (red). It
is recommended that an impedance compensation circuit be added for each differential pair, including DVI/HDMI Clock
outputs (Refer to Figure 11 (A)).
• DVI/HDMI Link Clock Outputs (TLC and TLC*)
These pins provide the DVI/HDMI differential clock outputs for DVI/HDMI corresponding to data on the TDC [2:0] and TDC
[2:0]*outputs (Refer to Figure 11 (A)).
• HPD (DVI/HDMI Hot Plug Detect)
This input pin determines whether the DVI/HDMI link is connected to a DVI/HDMI panel. When the panel is connected, the
HPD will be given a voltage greater than 2.4 volts. Refer to Figure 11 (B) for the design example.
•IRQ
This pin should be connected with graphic controller directly.
2.9 Video Output
YPbPr and RGB + Csync output
CH7033B support both RGB+Csync and HDTV YPbPr output format. The resolution is from 480P to 720P 1080i and
1080P. In RGB+Csync output format, the Csync high level is the same with AVDD power supply. Csync pin is a
COMS push-pull output pin, customer can use other circuit to change is high level to 0.7V or other voltage level
according to different Receivers. ( Refer to Figure 12)
VGA output

CHRONTEL AN-B012
206-1000-012 Rev1.9, 06/30/2020 13
VGA standard output signal level of Hsync and Vsync is more than 2.4V. CH7033B Hsync and Vsync output signal
level is same with AVDD power supply. Customer can use 74ACT08 (AND GATE) to pull high this signal level to
5V(recommend to add the diode). It is recommended but not necessary. ( Refer to Figure 12)
R39 75
12
C46
10pF
12
MONHSYNC
MONRED
C48
22pF
12
C49
10pF
12
JP6
Y_GREEN
12
3
C51
10pF
12
L20
47R 100MHz
12
JP7
Pr_RED
12
3
JP8
Pb_BLUE
12
3
C52
22pF
12
L21
47R 100MHz
12
C53
10pF
12
MONVSYNC
CSYNC1
R40 75
12
It is hi g hly re c ommen d to add th e d iode i n po w er
supply of 74ACT08, it can prevent the back drive
from TV or Monitor
U5A 74ACT08
A1
B2
Y
3
DAC01
U5B 74ACT08
A4
B5
Y
6
DAC11
DAC21
VSO1
HSO1
Pr
BLUE
RED
Y
Pb
GREEN
MONGREEN
MONBLUE
L17
47R 100MHz
1
2
L18
47R 100MHz
1
2
C47
22pF C50
22pF
L19
150-220R100MHz
1
2
L16
150-220R100MHz
1
2
C43
10pF
12
C44
22pF
12
CSYNC CN1
RCA JACK
1
2
L12
0.33uH
12
C37 1pF
12
C39
27pF
12
C38 100pF
12
C40 1pF
12
L13
0.33uH
12
C41 100pF
12
C42
27pF
12
CN3
RCA JACK
1
2
CN4
RCA JACK
1
2
C34 1pF
12
R38 75
12
C36 100pF
12
L11
0.33uH
12
CN2
RCA JACK
1
2
C35
27pF
12
Y/R
Pr/B
Pb/G
D1
AZ5125-01H
12
C45
10pF
12
P1
VGA
11
22
33
44
55
66
77
88
99
10 10
11 11
12 12
13 13
14 14
15 15
16
16 17 17
L15
47R 100MHz
1
2
L14
47R 100MHz
1
2
CSYNC
D2
AZ5125-01H
12
D3
AZ5125-01H
12
D4
AZ5125-01H
12
D5
AZ5125-01H
12
D6
AZ5125-01H
12
D7
AZ5125-01H
12
D8
AZ5125-01H
12
D9
AZ5125-01H
12
MONSCL
D10
AZ5125-01H
12
MONSDA
D11
AZ5125-01H
12
Figure 12: CH7033B YpbPr, RGB+Csync and VGA output
Note:In order to minimize the hazard of ESD, a set of protection diodes (AZ5125-01H) are highly recommended for each
DAC and Sync Output.

CHRONTEL AN-B012
14 206-1000-012 Rev1.9, 06/30/2020
2.10 Thermal Exposed Pad Package
The CH7033B are available in 88-pin QFN package with thermal exposed pad package. The advantage of the thermal
exposed pad package is that the heat can be dissipated through the ground layer of the PCB more efficiently. When
properly implemented, the exposed pad package provides a means of reducing the thermal resistance of the CH7033B.
Careful attention to the design of the PCB layout is required for good thermal performance. For maximum heat
dissipation, the exposed pad of the package should be soldered to the PCB as shown in Figure 14.
Die
Exposed Pad
Solder
PCB
Pin
Figure 14: Cross-section of exposed pad package
Thermal pad dimension is from 6.6mm to 6.9mm (min to max), 6.6mm x 6.6mm is the minimum size recommended
for the thermal pad, and 6.9mm x 6.9mm is the maximum size. The thermal land pattern should have a 5x5 grid array
of 1.0 mm pitch thermal vias connected to the ground layer of the PCB. These vias should be 0.3mm in diameter with
1 oz copper via barrel plating. Please refer to Figure 15.
6.6 mm
6.6 mm Exposed Pad
land pattern
Thermal Via Array
(5x5) 1 mm Pitch
0.3 mm diameter
Figure 15: Thermal Land Pattern
When applying solder paste to the thermal land pattern, the recommended stencil thickness is from 5 to 8 mils. Thermal
resistance was calculated using the thermal simulation program called ANSYS.

CHRONTEL AN-B012
206-1000-012 Rev1.9, 06/30/2020 15
2.11 QFN Package Assembly
For the assembly process, it is important to limit the amount of solder paste that is put under the thermal pad. If too
much paste is put on the PCB, the package may float during assembly. Compared with the solder mask of thermal
pad, the paste mask should be shrank to70%~80%. Figure 16 shows a paste mask pattern in gray for the thermal pad.
Figure16: Thermal Pad Paste Mask Pattern

CHRONTEL AN-B012
16 206-1000-012 Rev1.9, 06/30/2020
3.0 REFERENCE DESIGN EXAMPLE
The figures below are the reference schematic of CH7033B, which is provided here for design reference only. Please
contact Chrontel Applications group if necessary. Table 3 provides the BOM list for the reference schematic.
3.1 Reference Schematic

CHRONTEL AN-B012
206-1000-012 Rev1.9, 06/30/2020 17
(a) QFN connection

CHRONTEL AN-B012
18 206-1000-012 Rev1.9, 06/30/2020
(b) YpbPr, RGB+Csync and VGA output

CHRONTEL AN-B012
206-1000-012 Rev1.9, 06/30/2020 19
RClamp0524P
I/O 1
1
I/O 7 9
I/O 2
2
GND
3
I/O 3
4
I/O 4
5I/O 5 6
I/O 6 7
GND 8
I/O 8 10
DDC_SC2,4
DDC_SD2,4
HPD2,4
DDC_SC 2,4
DDC_SD 2,4
HPD 2,4
It is highly recommended to use VDD5_DDC, the
diode can prevent the back driver from TV or
Monitor
It is highly recommended to use VDD5_DDC, the diode can prevent the back
driver from TV or M o n it o r
TLC2,4
TDC1*2,4
TDC12,4
TLC*2,4
RClamp0524P
I/O 1
1
I/O 7 9
I/O 2
2
GND
3
I/O 3
4
I/O 4
5I/O 5 6
I/O 6 7
GND 8
I/O 8 10
DDC_SD 2,4
DDC_SC2,4
DDC_SD 2,4
DDC_SC2,4
C60
0.1uF
VDD5_DDC
C61
10uF
U9
HDMI Conn TY PE C
TMDS Data2 Shield
1TMDS Data2+ 2
TMDS Data2-
3TMDS Data1 Shield 4
TMDS Data1+
5TMDS Data1- 6
TMDS Data0 Shield
7TMDS Data0+ 8
TMDS Data0-
9TMDS Clock Shiel d 10
TMDS Clock+
11 TMDS Clock- 12
DDC/CEC Ground
13 CEC 14
SCL
15 SDA 16
N.C
17 +5V Power 18
HPDET
19
R35
47K
F2 MINISMDC050CT-ND
HPD 2,4
TDC2*2,4
TLC* 2,4
TDC1* 2,4
TLC2,4
TDC0*2,4
U9 HDMI TYP E C Co n n e c to r
U6 HDMI TYP E A Co n n e c to r
C58
0.1uF
VDD5_DDC
C59
10uF
R34
47K
U6
HDMI Conn TY PE A
TMDA Data2+
1TMDA Data2 Shield 2
TMDA Data2-
3TMDA Data1+ 4
TMDA Data1 Shield
5TMDA Data1- 6
TMDA Data0+
7TMDA Data0 Shield 8
TMDA Data0-
9TMDA Clock+ 10
TMDA TMDA ClockShield
11 TMDA Clock- 12
CEC
13 Reserved 14
SCL
15 SDA 16
DDC/CEC Ground
17 +5V Power 18
HPDET
19 F1 MINISMDC050CT-ND
TDC2 2,4
HPD 2,4
TDC1* 2,4
TDC1 2,4
TDC22,4
TLC* 2,4
TLC 2,4
TDC2*2,4
TDC12,4
TDC02,4
Reserved, please don't solder
TDC0*2,4
TDC02,4
TDC2*2,4
TDC22,4
TDC2* 2,4
TDC2 2,4
TDC0*2,4
RClamp0524P
I/O 1
1
I/O 7 9
I/O 2
2
GND
3
I/O 3
4
I/O 4
5I/O 5 6
I/O 6 7
GND 8
I/O 8 10
TDC0 2,4
TDC0* 2,4
TDC0* 2,4TLC* 2,4
TLC 2,4
TDC1* 2,4
TDC1 2,4
(c) HDMI output

CHRONTEL AN-B012
20 206-1000-012 Rev1.9, 06/30/2020
3.2 Reference Board Preliminary BOM
Table 3: CH7033B Reference Design BOM List
Item
Quantity
Reference
Part
1
9
D3, D4, D5, D6, D7, D8, D9,D11, D12
AZ5125-01H
2
1
D13
SM5817
3
20
C1, C2, C4, C5, C8, C10, C11, C13, C14, C16, C18, C19,
C21, C22, C24, C25, C28, C35, C58, C60
0.1uF
4
11
C3, C6, C7, C9, C12, C15, C17, C20, C23, C59, C61
10uF
5
3
C38, C41, C44
1PF
6
8
C29, C30, C47, C49, C50, C53, C55, C57
10pF
7
2
C26, C27
18pF
8
5
C48, C51, C52, C54, C56
22pF
9
3
C39, C42, C45
100pF
10
3
C40, C43, C46
27pF
11
2
C31, C32
1uF
12
4
C33, C34, C36, C37
0.5PF
13
2
F1, F2
MINISMDC050CT-ND
14
2
JP3, JP4
Header 4
15
1
JP2
Header 20x2
16
5
JP1. JP5, JP6, JP7, JP8
Header 3
17
7
J1, J2, J3, CN1, CN2, CN3, CN4
RCA
18
12
L1, L2, L3, L4, L5, L6, L7, L8, L9, L10, L16, L17
FB
19
3
L11, L12, L13
0.33uH
20
6
L14, L15, L18, L19, L20, L21
47 Ω_100M
21
1
P1
VGA
8
R1, R2, R3, R4, R5, R11, R15, R16
6.8 k Ω
23
1
R17
0 Ω
24
1
R19
1MΩ
25
1
R9
200K
26
1
R22
1.2 k Ω(1%)
27
7
R6, R7, R8, R14, R20, R24, R29
10 k Ω
28
2
R12, R13
1.8 k Ω
29
1
R27
330 Ω
30
1
R28
100 Ω
31
4
R26,R31,R32,R33
75 Ω
32
2
R34, R35
47k Ω
33
4
R21, R23, R25, R30,
68 Ω
34
1
SW1
P8058SS-ND
35
1
U1
CH9904
36
1
U2
CH7033B
37
1
U3
CH9903
38
1
U4
74HCU04/SO_10
39
1
U12
74ACT08
40
1
U6
HDMI connector TYPEA
41
3
U7, U8, U16
Rclamp0524P
42
1
U9
HDMI connector TYPEC
43
1
X1
535-9118-1-ND (27MHz)
44
1
U11
GTL2002
Table of contents
Popular Power Distribution Unit manuals by other brands
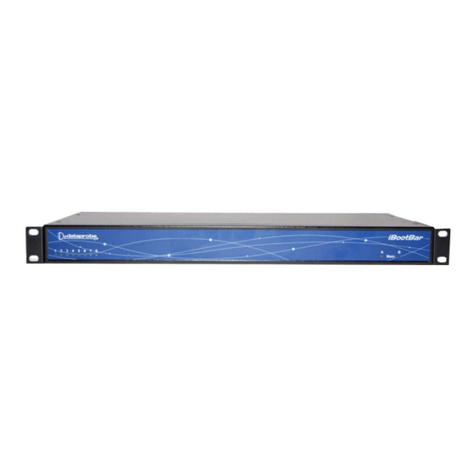
Dataprobe
Dataprobe iBootBar iBB-N15 Installation and operations
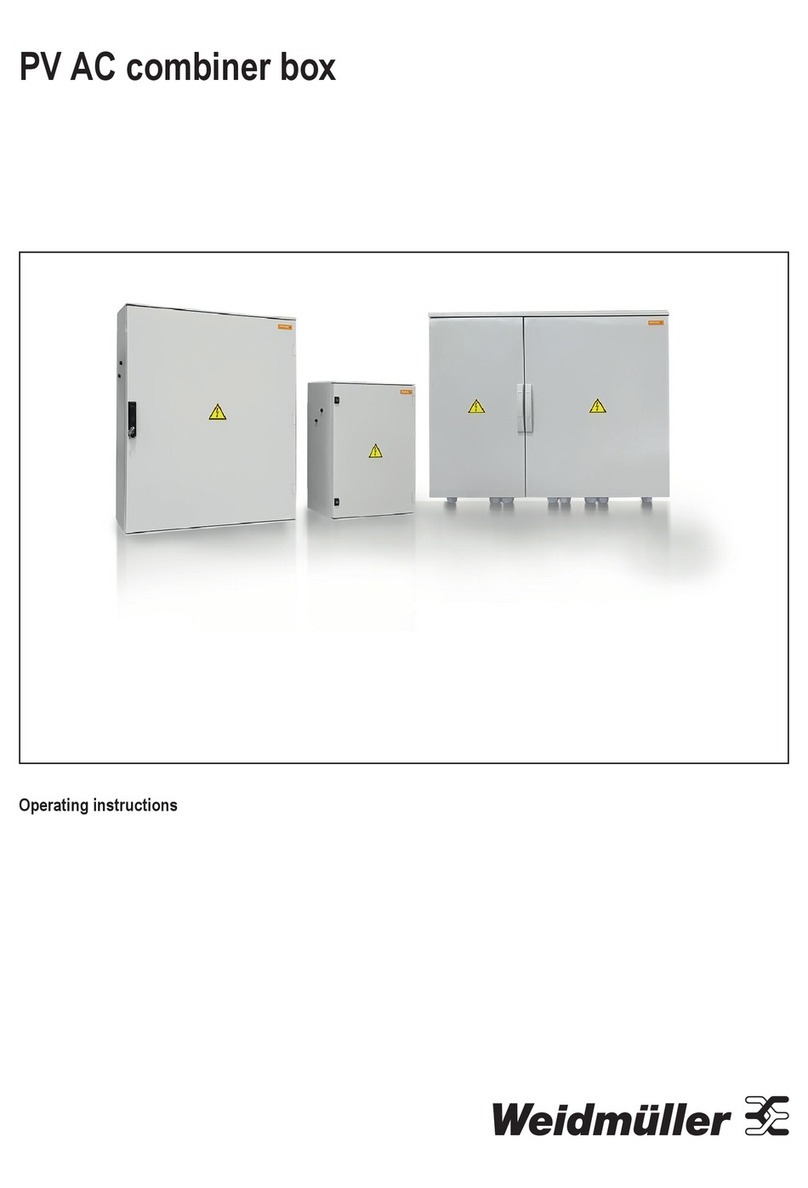
Weidmüller
Weidmüller 40201S2V4C2A0ES operating instructions

CyberPower
CyberPower PDU81001 user manual
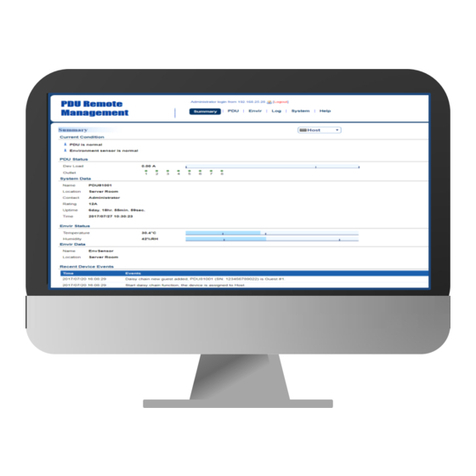
CyberPower
CyberPower PDU31 Series user guide
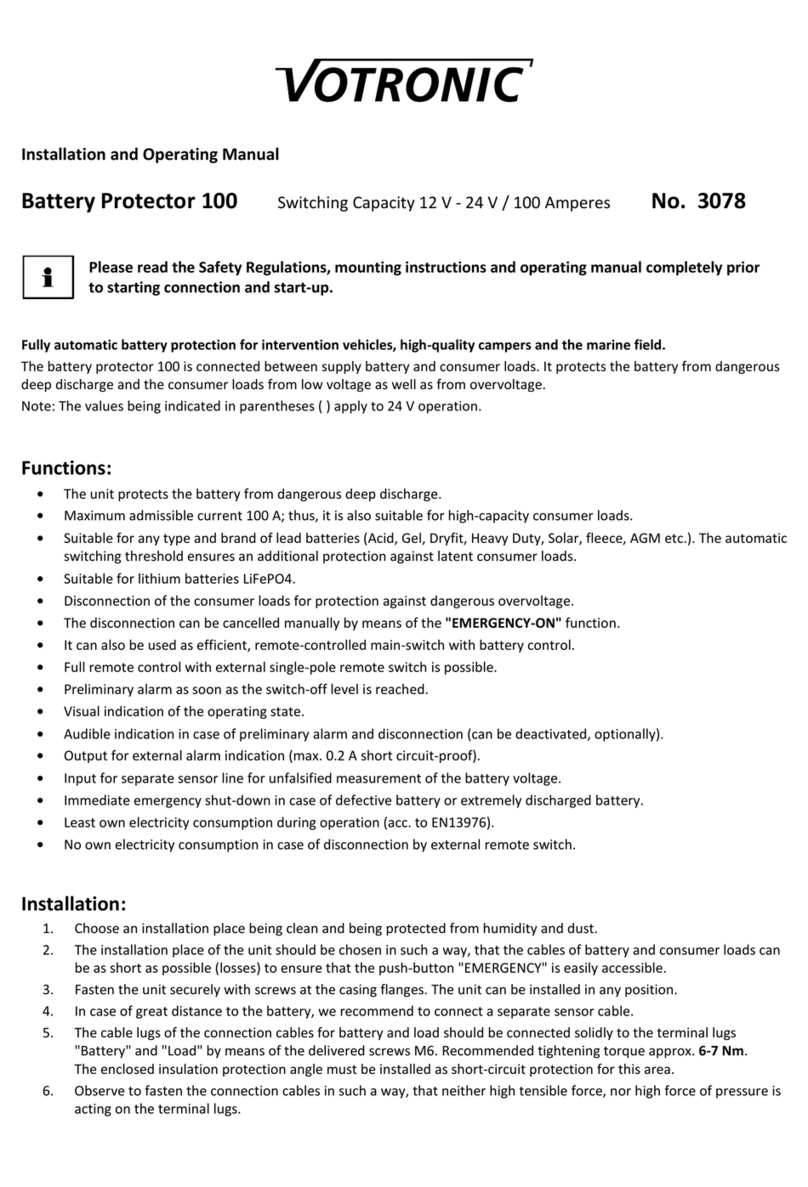
Votronic
Votronic Battery Protector 100 Installation and operating manual
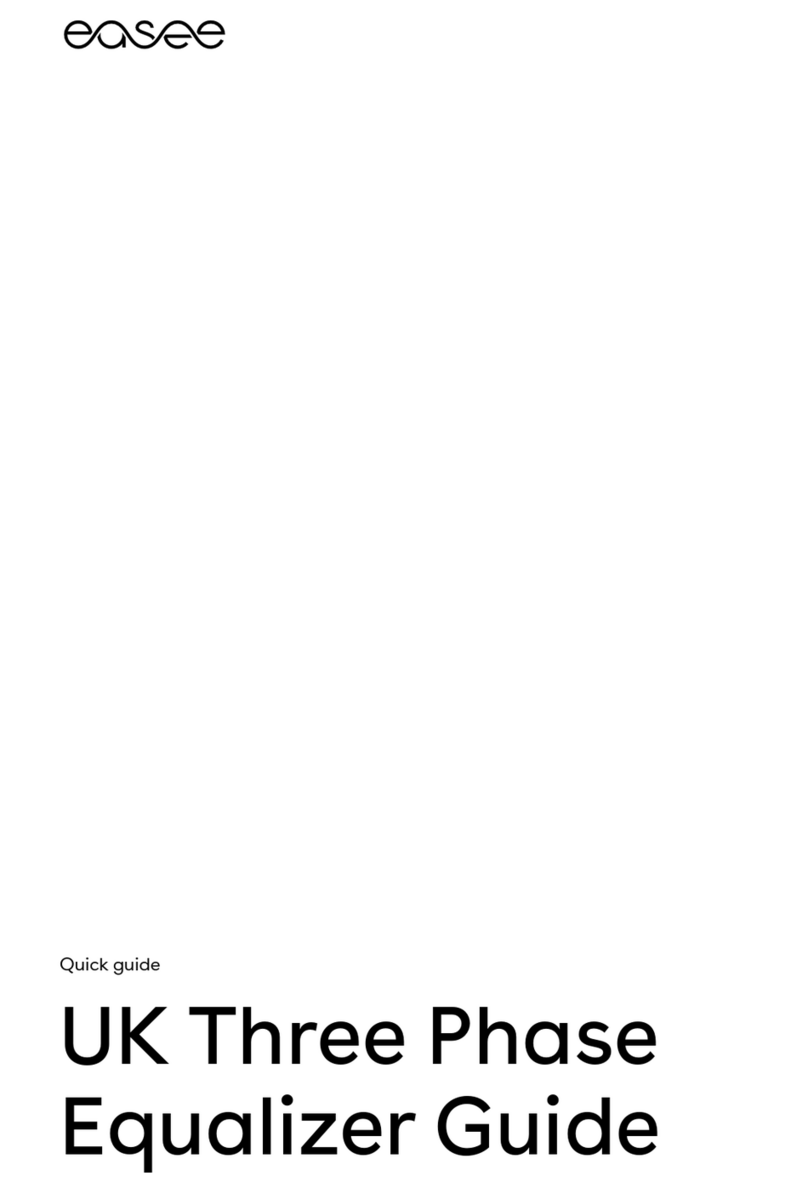
Easee
Easee Equalizer quick guide