CLARCOR UAS DPM User manual

PULSE CONTROL PANEL:
DPM/DPC
OWNER’S MANUAL

KNOW YOUR EQUIPMENT
READ THIS MANUAL FIRST.
Your Pulse Control Panel should provide years of trouble-free service. This man-
ual will help you understand the operation of your new panel. It will also help you
understand how to maintain it in order to achieve top performance. For quick
future reference, fill in the spaces below. Should you need assistance, call the
United Air Specialists, Inc. customer service number shown below. To expedite your ser-
vice, have the following information available when contacting UAS.
UAS ORDER #: _________________________________________________________
UNIT MODEL #: ________________________________________________________
UNIT SERIAL #: ________________________________________________________
SYSTEM ACCESSORIES:
______________________________________________________________________
______________________________________________________________________
______________________________________________________________________
INSTALLATION DATE: ___________________________________________________
UNITED AIR SPECIALISTS, INC. CUSTOMER SERVICE
1-800-252-4647

TABLE OF CONTENTS
Page
SAFETY PRECAUTIONS ............................................................................................ii
1. PULSE TIMER BOARD .......................................................................................... 1
1.1 Specifications ................................................................................................. 1
1.2 Range Adjustments ........................................................................................ 1
1.3 Operation ....................................................................................................... 2
1.1.1 Continuous Clean Operation ................................................................... 2
1.1.2 Pressure Switch Operation ...................................................................... 2
1.1.3 Downtime Cleaning Operation ................................................................ 2
1.4 Connection Diagrams ..................................................................................... 2
1.5 Troubleshooting Guide ................................................................................... 4
2. DIGITAL PRESSURE GAUGE
2.1 DPC-A3 .......................................................................................................... 5
2.1.1 Model Number Configuration .................................................................. 5
2.1.2 Specifications .......................................................................................... 5
2.1.3 Installation ............................................................................................... 5
2.1.3.1 Mounting ........................................................................................... 5
2.1.3.2 Pressure Connections ....................................................................... 5
2.1.3.3 Electrical Connections ...................................................................... 6
2.1.4 Operation ................................................................................................. 6
2.1.4.1 Display Key Function ........................................................................ 6
2.1.5 Programming ........................................................................................... 7
2.1.6 Opti-Link .................................................................................................. 7
2.2 DPM-A2 .......................................................................................................... 7
2.2.1 Model Number Configuration .................................................................. 7
2.2.2 Specifications .......................................................................................... 7
2.2.3 Installation ............................................................................................... 8
2.2.3.1 Pressure Connection ........................................................................ 8
2.2.3.2 Electrical Connection ........................................................................ 8
2.2.4 Operation ................................................................................................. 8
2.2.4.1 Display .............................................................................................. 8
2.2.4.2 Key Function ..................................................................................... 8
2.2.5 Other Features ........................................................................................ 8
2.2.5.1 Opti-Link ............................................................................................ 8
2.2.5.2 Calibration ......................................................................................... 8
ii

ii
SAFETY PRECAUTIONS
We have provided many important safety messages in this manual. Always read and obey all safety messages.
• Use proper lifting and rigging equipment to install your
dust collector.
• The dust collector should be properly grounded.
• Disconnect power before servicing.
• Replace all access panels before operating.
• Electrical connections should only be made by qualified
personnel, and be in accordance with local and national
codes and regulations.
• Do not use in explosive atmospheres unless the dust
collector is equipped with the appropriate accessories.
• Keep flammable materials and vapors, such as gasoline,
away from dust collector.
• The unit should be inspected frequently and dirt removed
to prevent excessive accumulation which may result in
flash-over or fire damage.
• Operate only in a safe and serviceable condition.
• Do not allow any individual to put lit cigarettes or any
burning objects into the hood or ducting of any dust
control system.
!
! DANGER
! WARNING
! CAUTION
CAUTION
This is the safety alert symbol.
This symbol alerts you to potential hazards that can kill or hurt you and others. All safety messages will follow the
safety alert symbol and the word “DANGER”, “WARNING” or “CAUTION”. These words mean:
Indicates a hazardous situation which, if not avoided, will result in death or
serious injury.
Indicates a potentially hazardous situation which, if not avoided, could result
in death or serious injury.
Indicates a potentially hazardous situation which, if not avoided, may result
in minor or moderate injury.
CAUTION used without the safety alert symbol indicates a potentially
hazardous situation which, if not avoided, may result in property damage.
IMPORTANT SAFETY INSTRUCTIONS
To reduce the risk of fire, electric shock, or injury when using the air cleaner, follow these basic precautions:
! WARNING

1
Revised 10/10
Pulse Control Panel
DPM/DPC
1. PULSE TIMER BOARD
Before making changes to the pulse timer board, please
read this manual. The integrated circuit of the pulse
timer board has been designed to sequence solenoid
valves that supply pulses of compressed air to dust
collector cartridge filters. Unless otherwise specified,
the pulse timer board is factory set to a 0.1 second
pulse duration, a 10 second pulse delay, 10 solenoid
valve outputs and 0 downtime cleaning cycles. The
Customer is responsible for setting the correct number
of outputs, (SW6), required to match their system.
1.1 SPECIFICATIONS
Model 20-3048
120 or 240 VAC 50/60 hz, 150va
Power Requirement:
250mA Logic, 2A Output
Fusing:
-40°F to 140°F (-40°C to 60°C)
Operating Temperature:
(10) Solid State Switches @ 2 amps
max. each
Outputs:
Isolated contact required, normally open
Pressure Switch Input (PRESS SW):
Isolated contact required, normally open
Motor Starter Aux. Input (MOT AUX):
10 Per Output
Maximum Number of Valves:
! CAUTION
Do not install the pulse timer board enclosure on the
dust cleaning equipment due to vibration.
! IMPORTANT
A separate motor starter auxiliary isolated dry contact
should be supplied with the blower/ motor starter and
wired to the MOT AUX terminals at the terminal strip
of the pulse timer board.
SWITCH POSITION
Use a #4 screwdriver
to dial in the
appropriate value:
(SW7-4)
DT CYCLES
The number of
downtime cleaning
cycles performed upon
blower shutdown:
(SW7)
# OF OUTS
The number of outputs
(values) selected in the
sequence:
(SW6)
PULSE DURATION
The length of time
each output is active
during a pulse cycle:
(seconds)
(SW5)
PULSE DELAY
The length of time
before the next pulse
in the sequence:
(seconds)
(SW4)
1 1 1 0.025 5
2 2 2 0.050 10
3 3 3 0.100 20
4 4 4 0.125 40
5 5 5 0.150 60
6 6 6 0.175 120
7 7 7 0.200 300
8 8 8 0.500 600
9 9 0 1.000 Unused
1.2 RANGE ADJUSTMENTS
0 0 10 Unused Unused

2
Revised 10/10
Pulse Control Panel
DPM/DPC
1.3 OPERATION
1.1.1 CONTINUOUS CLEAN OPERATION
When using a Digital Pressure Monitor (DPM), or no
pressure gauge at all, SW2 on the timer board should
be set to CONTINUOUS CLEAN operation. Whenever
the blower is active, the system will continuously pulse
the cartridges. During continuous clean operation, the
CLEAN light will be illuminated.
1.1.2 PRESSURE SWITCH OPERATION
A separate pressure switch or Digital Pressure
Controller (DPC) isolated dry contact should be
supplied and wired to the PRESS SW terminals on TB3.
SW2 on the timer board should be set to PS (pressure
switch) operation. When the blower is active, the
system will pulse “On Demand” whenever the pressure
switch or DPC isolated dry contact is in the closed
position. The CLEAN light will be illuminated whenever
this dry contact is closed.
1.1.3 DOWNTIME CLEANING OPERATION
Upon motor/blower shutdown, downtime cleaning
can be performed in either pressure switch mode or
continuous clean mode. To perform downtime cleaning,
make certain the rotary switch labeled DT CYCLES is
set to the number of cycles desired (1 on the switch
indicates 1 cycle). During a downtime cleaning, the
CLEAN light will flash for the duration of the cycles
selected. The down time pulsing will begin 60 seconds
after the motorblower is turned off.
1.4 CONNECTION DIAGRAMS
Figure 1 shows the connection required for system
pulse cleaning operation. Notice the isolated normally
open motor starter auxiliary contact wired to the MOT
AUX terminals on the timer board. This is required for
either DPC, a DPM or no pressure gauge at all. When
using a DPM, make certain the SW2 is placed in the
CONTINUOUS CLEAN position. When using a DPC,
make certain SW2 is placed in the PS position.
! WARNING
Excessive downtime cleaning could pulse dust from
unit out of incoming ducting.
Figure 1
System Pulse Cleaning Operation

3
Revised 10/10
Pulse Control Panel
DPM/DPC
Figure 2 shows recommended interconnections between a separate combination motor starter with a 115VAC step-down
transformer, either a DPC or a DPM, and a pulse timer board (20-3048).
Figure 2
Standard Pulse Timer Board Connections

4
Revised 10/10
Pulse Control Panel
DPM/DPC
PROBLEM
Timer board does not
operate.
1. Be sure the proper power is applied to the terminals at TB1 at all times.
2. Be sure an isolated normally open motor starter auxiliary dry contact is wired to the MOT
AUX terminals on TB3.
3. Be sure PULSE DELAY and PULSE DURATION are not set to 0 (zero).
4. Check F1 and F2 fuses for open circuit, replace if blown.
1.5 TROUBLESHOOTING GUIDE
Use the troubleshooting guide (below) to correct any problems that occur with your dust collection unit. If the problem or
condition continues, contact UAS customer service at 1-800-252-4647.
Timer board does not pulse in
continuous mode.
1. Be sure SW2 is set to CONTINUOUS mode.
Timer board does not pulse in
pressure switch mode.
1. Be sure an isolated normally open pressure switch contact is wired to the PRESS SW
terminals on TB3.
2. Be sure SW2 is set to PS mode.
3. Be sure filter pressure drop is above pressure switch setpoint.
RECOMMENDED SOLUTIONS
Downtime cleaning does not
function.
1. Be sure power is applied to the terminals on TB1 even after the motor starter is shut down.
2. Be sure the isolated normally open motor starter auxiliary contact is wired to the MOT AUX
terminals on TB3. (Downtime cleaning begins when the blower motor starter is shut down.)
3. Be sure DT CYCLES is not set to 0 (zero).
Expanded operation does not
function.
1. Make sure one timer board has SW3 set to MASTER and the other timer board has SW3 set
to SLAVE.
2. Be sure MOT AUX and HANDSHAKING wiring is jumped from one board to the other (see
Figure 3).
3. Be sure PRESS SW (if used) is jumped from one board to the other (see Figure 3).
4. Be sure SW2 switch on both boards, is set to either CONTINUOUS or PS mode.
(Both boards should have the same selection.)
UAS 10 Channel Pulse Timer Board Test Procedure:
The firmware for the UAS 10 Channel Pulse Timer board
contains a test routine for easily testing all of the inputs and
outputs on the circuit board. This routine was included in
order to reduce the testing time of each circuit board in the
manufacturing process. Caution must be used when testing
a circuit board with AC power applied. This procedure should
be performed only by personnel with sufficient training or
experience that they can do it safely.
Test Procedure:
The steps of the test must be done in order. Skipping steps
does not work.
1. Turn off or disconnect AC power.
2. Place a jumper across the J2 (TEST) header pins.
3. Set all rotary switches to the 0 position.
4. Set SW2 to the PS position.
5. Remove any connections to the MOT AUX and PRESS
SW terminals.
6. Apply AC power.
7. If both the PWR and CLEAN lights are flashing re-
confirm steps 3 – 5. If steps 3 – 5 are correct and both
lights continue to flash, there is a problem causing an
incorrect input to the microcontroller.
8. If the PWR light is flashing and the CLEAN light is on
steady, continue with the following steps.
9. Rotate SW7-DT CYCLES to position 1. The OUT1 light
should turn on. The OUT1 position of the terminal block
should also be energized with AC power.
10. Rotate SW7-DT CYCLES through positions 2 through
0. The corresponding OUT light and terminal should
turn on. It is normal for some other lights to blink
briefly during rotation of the switches.
11. When switching from position 9 to position 0, the
OUT10 light and terminal should turn on for 2 seconds
followed by the CLEAN light turning off for 1 second.
12. Repeat steps 9 – 11 for the other 3 rotary switches
SW6-# OF OUTS, SW5-PULSE DURATION, and
SW4-PULSE DELAY.
13. Set SW2 to the CONT. CLEAN position. OUT1 will turn
on for 2 seconds.
14. Use a jumper wire to momentarily connect the two MOT
AUX terminals. OUT2 should turn on for 2 seconds.
15. Use a jumper wire to momentarily connect the two
PRESS SW terminals. OUT3 should turn on for 2
seconds.
16. Both the PWR and CLEAN lights should now be on
steady.
17. Turn off AC power.
18. Remove jumper on J2.
19. TEST COMPLETE.

5
Revised 10/10
Pulse Control Panel
DPM/DPC
2. DIGITAL PRESSURE GAUGES
2.1 DPC-A3
2.1.1 MODEL NUMBER CONFIGURATION
The DPC-A3 digital pressure controller provides control
of low differential pressure applications for air and other
compatible non-combustible gasses. These instruments
have a large LED display for pressure indication, a LCD
display for programming and additional LEDs to indicate
percentage of output, setpoints and alarm status. The
instruments are fully programmable from the key pad
face or by utilizing the Opti-Link™ communication port
for no-touch programming. Options for the instruments
include a 4-20 mA output. The base model does not
include the 4-20 mA option, which is a special
order option.
2.1.2 SPECIFICATIONS
Maximum Pressure: Ranges ≤ 4" w.c. = 2 PSI;
Ranges ≥ 5" w.c. = 10 PSI
Media compatibility: Air and compatible non-
combustible, non corrosive gasses
Accuracy: - 1.00%
Te mperature Ranges:
Compensated: 10° to 140°F (-12° to 60°C)
Operating: 10° to 140°F (-12° to 60°C)
Thermal Effect: +/- 0.02% FS/°F
Output Signal: 4-20 mA (option)
Loop Resistance: 750 Ω Max (for internally sourced
power); 1800 Ω Max (for externally sourced power
of 36 VDC)
Power Supply: Universal 20-240 VAC or VDC
Housing Material: Glass Filled Nylon
Enclosure Rating: Designed to meet NEMA 4X face
Relays: (2) SPDT 8 Amps @ 250 VAC resistive,
5A @30 VDC
Electrical Connections: screw terminals
Response Time: <100 ms
Display: 4 Digit, red LED, 1⁄2" digits;
LCD programming display
Process Connection: Push on connection
for 3/16" tubing
Agency Approvals: ETL, CE
2.1.3 INSTALLATION
2.1.3.1 MOUNTING
Flush Mounting – For new applications, cut a 4-9/16"
hole in the panel. Insert the control with the provided
gasket through the hole and secure it to the panel with
the provided mounting tabs and screws. Retrofitting old
technology is also easy with the DPC-A3. This gauge
has been designed to fit in industry standard holes
ranging from 4-9/16" to 4-13/16". Simply remove the old
device and insert the new control into the existing
cut out.
2.1.3.2 PRESSURE CONNECTIONS
Two 3/16" pressure connections are located on the back
of the unit, labeled “High” and “Low”. For best results,
connect 3/16" I.D. push on tubing to the pressure
connections. If the High connection has a greater
absolute value than the Low connection, the front
display will give a positive value. If the high connection
has a lower absolute value than the low connection,
the front display will give a negative value.

6
Revised 10/10
Pulse Control Panel
DPM/DPC
2.1.3.3 ELECTRICAL CONNECTIONS
NOTES:
1. Supply Voltage is universal
from 20-240 VAC or VDC.
2. For internally sourced 4-20 mA
loop, maximum loop resistance
is 750 Ω; for externally sourced
loop at 36 VDC, maximum loop
resistance is 1800 Ω.
Note: The base model does
not include the 4-20 mA
option. That is a special order
option. Please contact UAS to
purchase this.
3. Isolation:
Relays: 1000 VAC to all other
inputs and outputs
4-20 mA: 5000 VAC to all other
inputs and outputs.
2.1.4.1 DISPLAY KEY FUNCTION
The DPC-A3 has four buttons located on the face of the
control used for programming an up arrow, down arrow,
left arrow/cancel and a right arrow/accept button as
shown below.
To move from one program menu to another, hold the
up arrow or down arrow for one second to move up or
down one menu level. The control will start in the “Main”
menu, one level up is the “Set-up” menu, and one more
level up is the “Secure” menu.
The up and down arrows are used to navigate up and
down through the parameters in each menu. To change
a parameter, use the up and down arrows until the
parameter is highlighted, then press the right arrow.
This will advance you to another screen where you can
change the parameter. There are two different types
of parameter change screens: 1) You select a given
option or 2) You change a numerical value. To change
a number, use the left and right arrows to select the
digit you would like to change, and the up and down
arrow to increase or decrease the value by the amount
selected. Once you have made the change, hold the
accept button down for three seconds. This will accept
the change and take you back to the menu you were
currently in. At any point while in a parameter change
screen, you can hold the cancel button for one second
to return to the previous menu without accepting a
change to that parameter.
To manually reset the alarm after an alarm condition
has occurred (if this feature is used) hold the right and
left arrows simultaneously until the alarm resets.
up arrow down arrow left arrow /
cancel
right arrow /
accept
2.1.4 OPERATION

7
Revised 10/10
Pulse Control Panel
DPM/DPC
2.1.5 PROGRAMMING
The main menu consists of Set Point 1 Low (SP 1 lo), Set Point 1 High (SP 1 hi), Set Point 2 Low (SP 2 lo), and Set
Point 2 High (SP 2 hi). SP 1 lo and SP 1 hi is the pulse cleaning for the dust collection system with SP1 lo set at 2.5 and
SP 1 hi set at 3.0. Pulse cleaning will activate at 3.0 and deactivate at 2.5. There will be an occurrence in the service
life of the filters in which the pulse cleaning will not recover at SP1 lo of 2.5 requiring a setting revision to Sp 1 lo and
SP 1 hi. A setting revision should be completed in increments of 0.5 during the service life of the filters. The next setting
of SP 1 lo would be 3.0 with SP 1 hi at 3.5. Set Point 2 Low and Set Point 2 High is an alarm range indicating filters will
require a replacement. The filters should only be replaced when process ventilation is unsatisfactory.
MENU VARIABLE CODE SETTING
Main
Menu
➲ Set Point 1 Low SP1 lo 2.5
SP1 hi➲ Set Point 1 High
➲ Set Point 2 Low
➲ Set Point 2 High
SP2 lo
SP2 hi
3.0
3.5
5.0
2.1.6 OPTI-LINK™
Opti-link™ is an infrared communications technology
that allows the user to upload and download
program parameters from one unit to another with
a programming key. By using the PK-01 universal
programming key, the user may program one
unit, download those parameters to the universal
programming key and then upload that same program
from the key to other controls. By using a PK-02 lockout
programming key, a user may completely lock (or
unlock) the face keypad of the control to eliminate the
possibility of unwanted tampering of the control.
To download programs from a control to a programming
key, place the key within 1 to 6 inches of the Opti-
Link™ port on the control and hold the two outside
buttons simultaneously until the numeric LED on the
control turns off. The programming key should stay
within the 1 to 6 inch range while the download is in
progress. During the operation, the Process Arch on the
control will give the status of the download. When the
download is complete, the programming key will blink
green twice to indicate the program is stored on the
programming key.
To upload programs from a programming key to a
control, place the key within 1 to 6 inches of the Opti-
Link™ port on the control and hold the center button
until the numeric LED on the control turns off. The
programming key should stay within the 1 to 6 inch
range while the download is in progress. During the
operation, the Process Arch on the control will give the
status of the download. When the upload is complete,
the control will read “yes” to indicate the program has
been successfully uploaded to the control.
2.2 DPM-A2
2.2.1 MODEL NUMBER CONFIGURATION
The DPM-A2 is a microprocessor based digital
pressure gauge for positive, negative and differential
measurement designed to be a direct replacement
for mechanical gauges. The 1⁄2" LCD display gives
the gauge improved readability and precision. These
products also feature five user selectable engineering
units including in. w.c., mm w.c., cm w.c., kPa and Pa.
The DPM-A2 also has a “process arch” which gives the
gauge a similar look to mechanical gauges by giving a
continuous percent output status.
2.2.2 SPECIFICATIONS
Maximum Pressure: Ranges ≤ 4" w.c. = 2 PSI;
Ranges ≥ 5" w.c. = 10 PSI
Media compatibility: Air and compatible non-
combustible, non corrosive gasses
Accuracy: - 1.00%
Te mperature Ranges:
Compensated: -10° to 140°F (-23° to 60°C)
Operating: -10° to 140°F (-23° to 60°C)
Thermal Effect: +/- 0.02% FS/°F
Output Signal: 4-20 mA (option)
Loop Resistance: 750 Ω Max (for internally sourced
power); 1800 Ω Max (for externally sourced power
of 36 VDC)
Power Supply: Universal 20-240 VAC or VDC
Housing Material: Glass Filled Nylon
Enclosure Rating: Designed to meet NEMA 4X face
Electrical Connections: screw terminals
Response Time: <100 ms
Display: 4 Digit, red LED, 1⁄2" digits;
Process Connection: Push on connection
for 3/16" tubing
Agency Approvals: ETL, CE

8
Revised 10/10
Pulse Control Panel
DPM/DPC
2.2.4.2 KEY FUNCTION
The DPM-A2 has four buttons located on the face of the
gauge for set-up and calibration. There is a Span, Zero,
Units, and Lock button. The Units button changes the
unit of measure and the Lock button locks and unlocks
the keypad on the gauge. Span and Zero are used for
calibration (see calibration section 2.2.5.2).
By simultaneously pressing the Span and Zero buttons
for three seconds, the unit will be switched from
internally sourcing the power for the current loop to
requiring an external power supply.
2.2.3 INSTALLATION
2.2.3.1 PRESSURE CONNECTION
Two 3/16" pressure connections are located on the back
of the unit, labeled “High” and “Low”. For best results,
connect 3/16" I.D. push on tubing to the pressure
connections. If the High connection has a greater
absolute value than the Low connection, the front
display will give a positive value. If the High connection
has a lower absolute value than the Low connection,
the front display will give a negative value.
2.2.3.2 ELECTRICAL CONNECTION
NOTES:
1. Supply Voltage is universal
from 20-240 VAC or VDC.
2. For internally sourced 4-20 mA
loop, maximum loop resistance
is 750 Ω; for externally sourced
loop at 36 VDC, maximum loop
resistance is 1800 Ω.
3. Isolation: 4-20 mA: 5000 VAC to all other inputs and
outputs. Note: The base model does not include
the 4-20 mA option. That is a special order option.
Please contact UAS to purchase this.
2.2.4 OPERATION
2.2.4.1 DISPLAY
The DPM-A2 displays pressure on a four digit LED
display and will show three or four digits depending
on the range and accuracy of the product. Negative
pressure will be indicated by a negative sign before the
numerical indication. Units of measure are displayed
above the four digit LED display by LED indicators. The
DPM-A2 also has a process arch, which is designed
to mimic the indicating needle of a mechanical gauge.
The process arch will light up from left to right as the
pressure moves away from zero.
2.2.5 OTHER FEATURES
2.2.5.1 OPTI-LINK™
Opti-link™ is an infrared communications technology
that allows the user to upload and download
program parameters from one unit to another with
a programming key. By using the PK-01 universal
programming key, the user may program one
unit, download those parameters to the universal
programming key and then upload that same program
from the key to other controls. By using a PK-02 lockout
programming key, a user may completely lock (or
unlock) the face keypad of the control to eliminate the
possibility of unwanted tampering of the control.
2.2.5.2 CALIBRATION
ZERO - Periodically, it may be necessary to recalibrate
the gauge to maintain the accuracy of the product. To
“Zero” the gauge, remove the pressure connections
from both pressure ports and hold the Zero button for
three seconds.
SPAN - THIS FUNCTION SHOULD ONLY BE
PERFORMED BY CERTIFIED PERSONNEL.
This is a calibration parameter that allows re-calibration
of the span. To re-span the gauge, you’ll need a device
that can maintain a fixed amount of negative pressure.
For example, if your gauge goes to 8” inwc, then you’ll

9
Revised 10/10
Pulse Control Panel
DPM/DPC
need to apply 8” inwc of negative pressure to the
LOW pressure port on the gauge. Nothing should be
connected to the HIGH pressure port. You can reset the
value by holding the Span key for three seconds.
The 4-20 mA process output is set to give a linear
output from 0 to the full scale pressure range of the
product. Other pressure spans such as bidirectional
or reduced ranges can be scaled with an Opti-LinkTM
programming key. Consult the factory for details.

10
Revised 10/10
Pulse Control Panel
DPM/DPC
This page intentionally left blank

11
Revised 10/10
Pulse Control Panel
DPM/DPC
This page intentionally left blank

©2008 United Air Specialists, Inc.
Part No. 44-10493-0001
10/10
United Air Specialists, Inc.
reserves the right to change
design or specifications
without notice.
4440 Creek Road • Cincinnati, Ohio 45242 USA
National Phone: 1-800-252-4647
Telephone: (513) 891-0400 • Fax: (513) 891-4882
www.uasinc.com
UNITED AIR SPECIALISTS, INC.
LIMITED WARRANTY
UAS warrants to the original purchaser that all equipment will be free from defects in materials and
workmanship for one year from the date of shipment from UAS (three years for Smokeeter® and
VisionAir™ models other than CC and DC series) and that major structural components on SFC and MCB
series will be free from defects in materials and workmanship for ten years from the date of shipment
from UAS. This warranty applies only if equipment is properly installed, maintained, and operated under
normal conditions and does not apply to damage caused by corrosion, abrasion, abnormal use or misuse,
misapplication, or normal wear and tear. This warranty will be void with respect to equipment that is subject
to unauthorized repairs or modifications. UAS makes no warranty as to goods manufactured or supplied by
others. This warranty is subject to any limitations in UAS’ quotation and may not be modified except by a
written instrument signed by the President or Vice President of Sales of UAS.
THIS WARRANTY IS EXCLUSIVE AND IN LIEU OF ALL OTHER WARRANTIES, WHETHER
WRITTEN, ORAL OR IMPLIED, INCLUDING ANY IMPLIED WARRANTY OF MERCHANTABILITY,
FITNESS FOR A PARTICULAR PURPOSE OR NONINFRINGEMENT.
As Purchaser’s exclusive remedy for any defects in the equipment, UAS will exchange or repair any
defective parts during the warranty period, provided such parts are returned, prepaid, to UAS’ factory. The
obligation of UAS is limited to furnishing replacement parts F.O.B. UAS’ factory or making repairs at UAS’
factory of any parts that are determined, upon inspection by UAS, to be defective. In no event will UAS be
responsible for labor or transportation charges for the removal, reshipment or reinstallation of the parts.
IN NO EVENT WILL UAS BE RESPONSIBLE FOR ANY SPECIAL OR CONSEQUENTIAL
DAMAGES.
This manual suits for next models
1
Table of contents
Popular Control Panel manuals by other brands
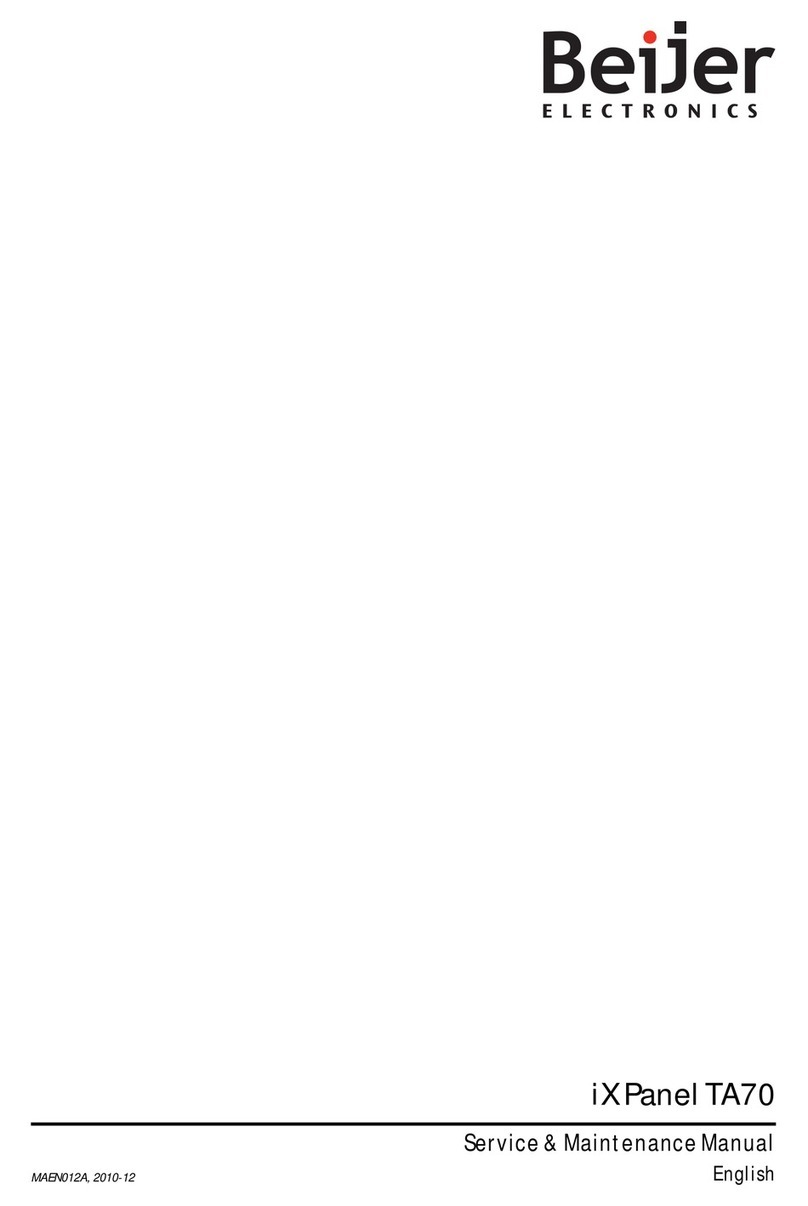
Beijer Electronics
Beijer Electronics iX Panel TA70 Service maintenance manual
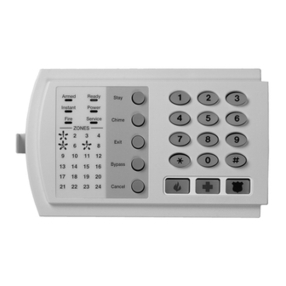
GE
GE NetworX NX-6 Installation and startup
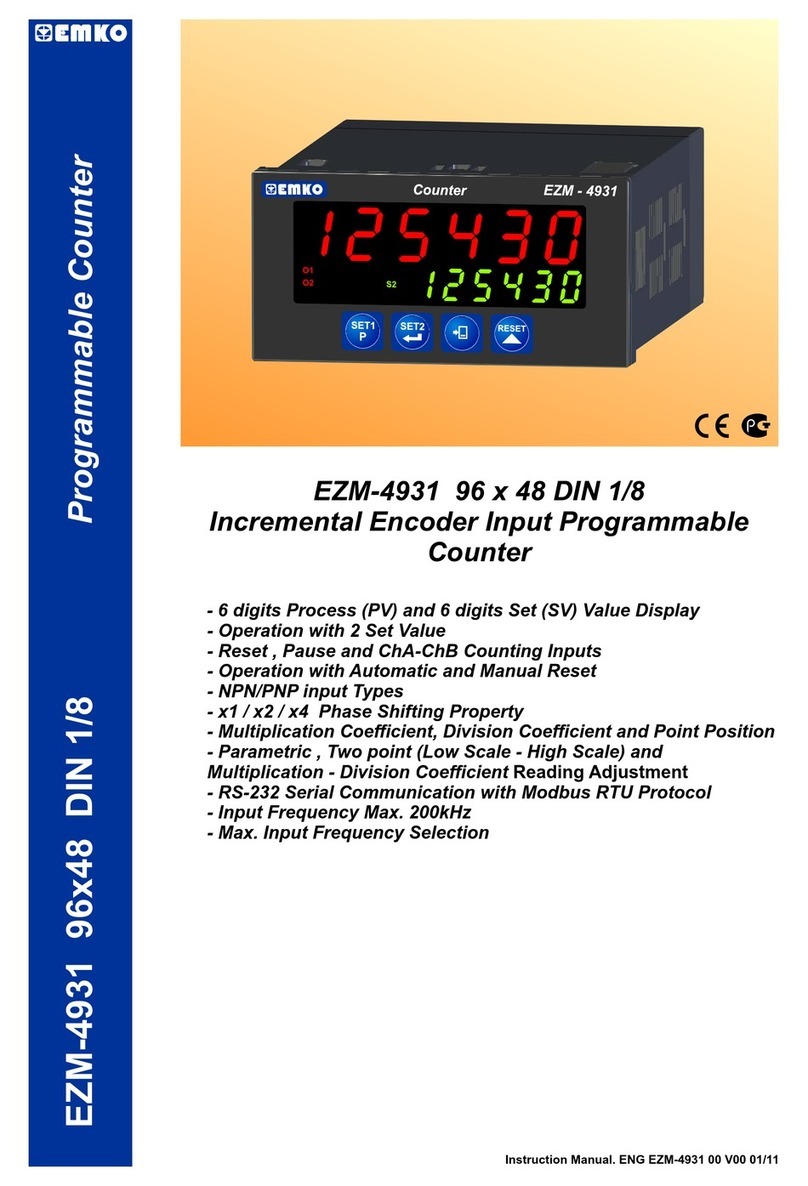
EMKO
EMKO EZM-4931 Series instruction manual
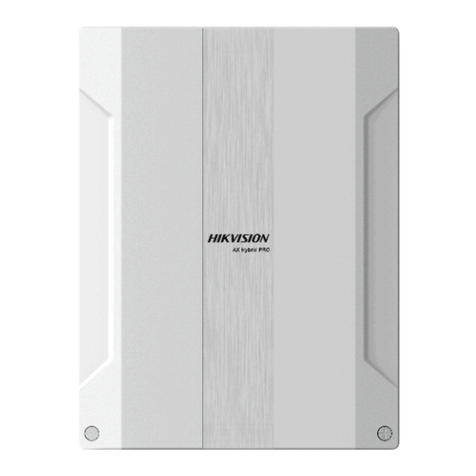
HIK VISION
HIK VISION AX HYBRID PRO user manual
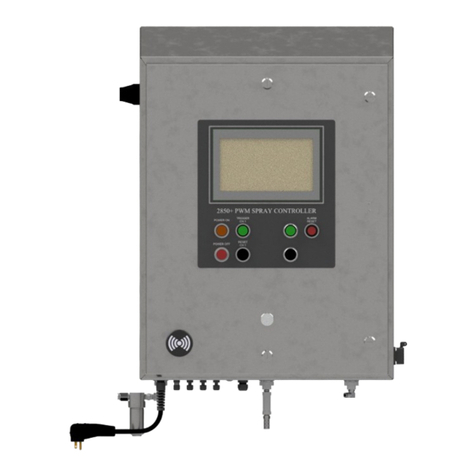
Spraying Systems
Spraying Systems AutoJet 2850+ owner's manual

HIK VISION
HIK VISION DS-PWA32-HR manual
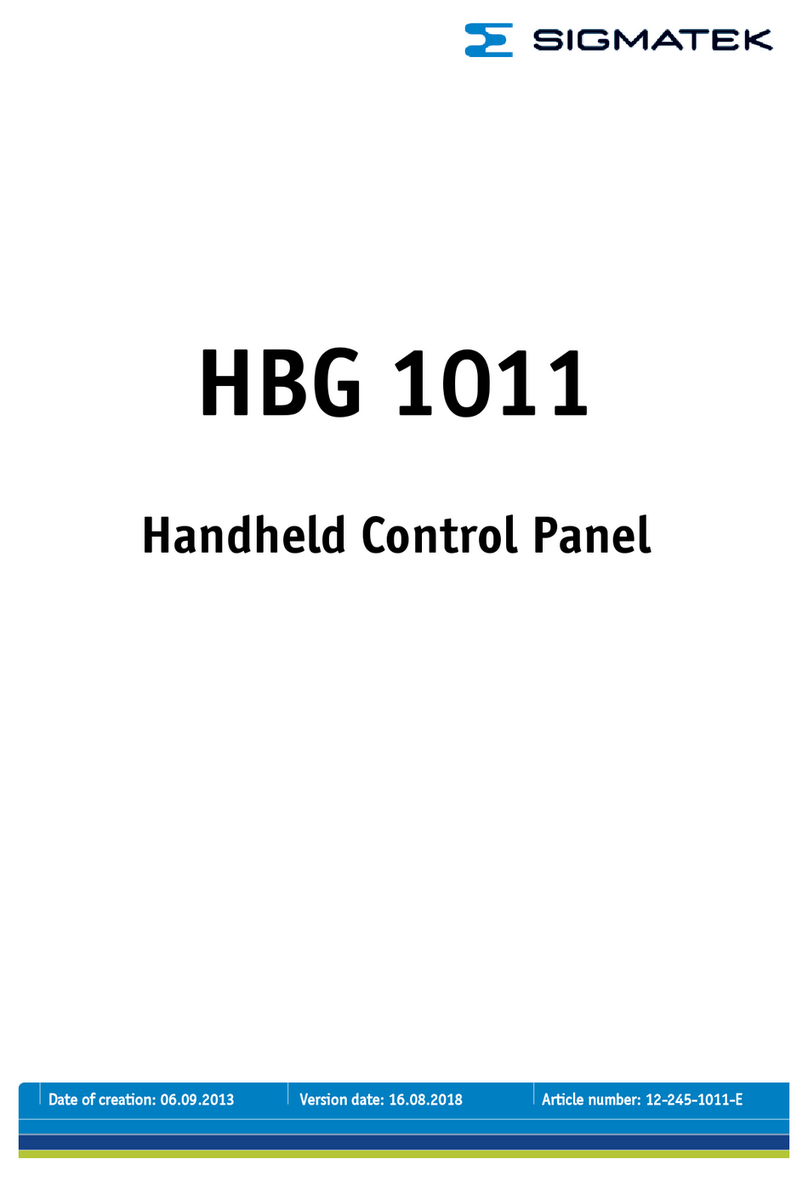
SIGMA TEK
SIGMA TEK HBG 1011 manual
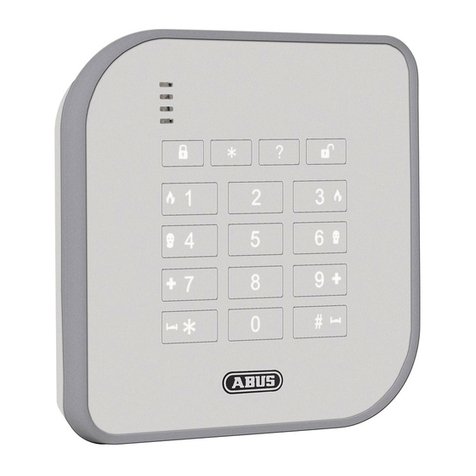
Abus
Abus FUBE50001 Installation instructions and user manual

Zero88
Zero88 Chillinet Instructions for installing and operating
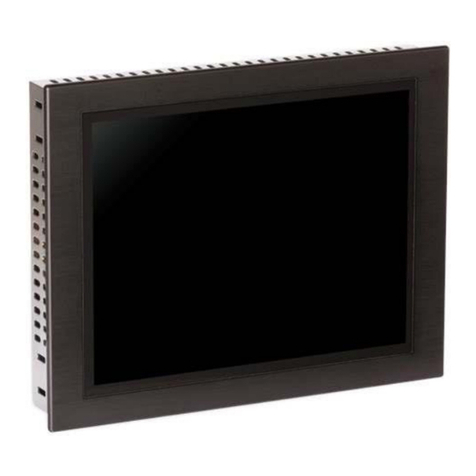
SIGMA TEK
SIGMA TEK ETV 0853-3 manual
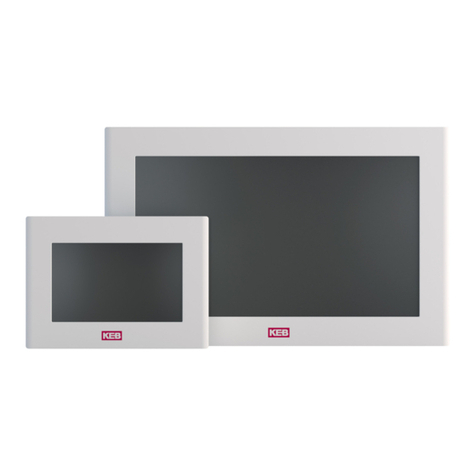
KEBCO
KEBCO COMBICONTROL C6 HMI instruction manual
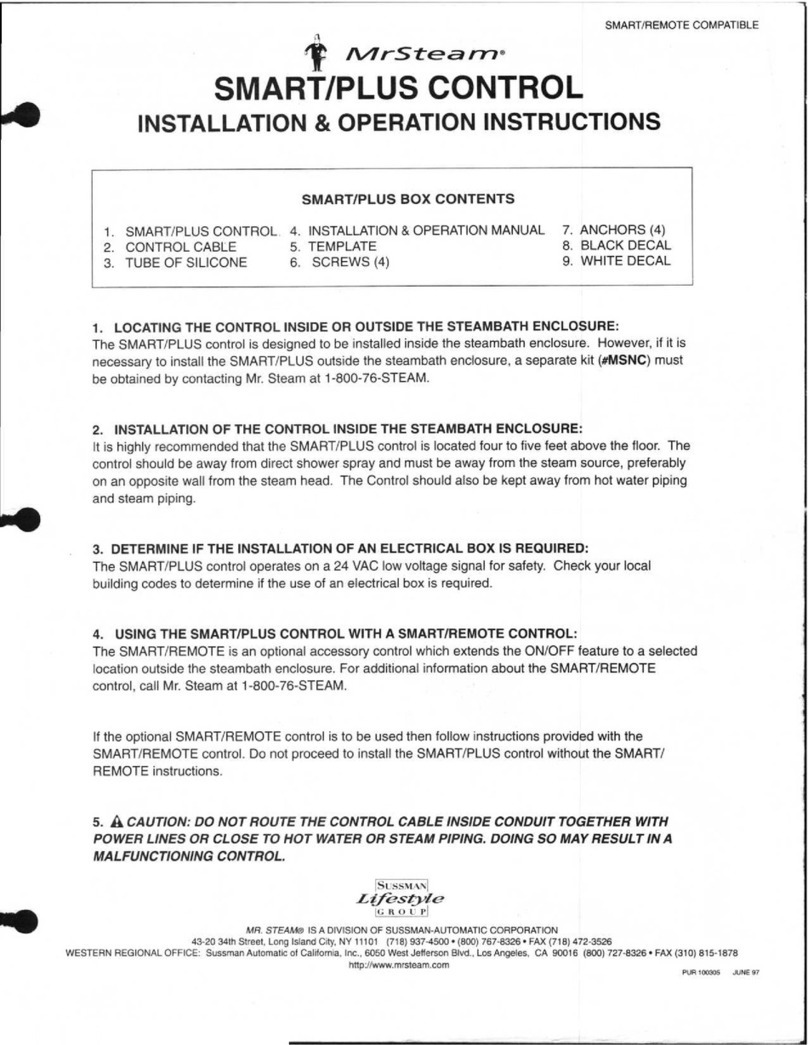
mr. steam
mr. steam SMART/PLUS Installation & operation instructions