Cleco 19P Series User manual

For additional product information visit our website at http://www.ClecoTools.com
Instruction Manual
PL12-1019EN
06/18/2019
19P & 19T Series
Pistol Grip Stall Screwdriver
For additional product information visit our website at http://www.ClecoTools.com
19P Series
19T Series

Page 2
PL12-1019EN
05/14/2013
Cleco®
General Information
For this Instruction Manual
This Instruction Manual is the Original Instruction Manual intended for all persons who will operate and maintain
these tools.
This Instruction Manual
• provides important notes for the safe and ecient use of these tools.
• describes the function and operation of the 19P and 19T series tools.
• serves as a reference guide for technical data, service intervals and spare parts ordering.
• provides information on optional equipment.
Identication text:
19P / 19T represents all models of the pistol grip pneumatic screwdrivers as described in this manual
Ú indicates a required action
• indicates a list
<..> indicates a reference number from the exploded parts drawings
Arial indicates an important feature or instruction written in Arial Bold
Identication graphic:
¢indicates a directional movement
òindicates a function or force
Copyright protection:
Apex Tool Group, LLC reserves the right to modify, supplement or improve this document or the product without
prior notice. This document may not be reproduced in any way, shape or form, in full or parts thereof, or copied
to another natural or machine readable language or to a data carrier, whether electronic, mechanical, optical or
otherwise without the express permission of Apex Tool Group, LLC.

Page 3
PL12-1019EN
05/14/2013
Cleco®
Nomenclature
19 X T S XX Q
Tool Series
19
Handle
P = Pistol Grip P-Handle
T = Pistol Grip T-Handle
Tool Type
T = Trigger
Torque Control
S = Stall
Maximum Torque
02 = 2.1 Nm
03 = 3.1 Nm
04 = 4.5 Nm
05 = 5.1 Nm
Output Drive
Q = Quick Change Chuck

Page 4
PL12-1019EN
05/14/2013
Cleco®
Contents
1 Safety 6
1.1 Warning and notes................................................................................................. 6
1.2 Basic requirements for safe working practices ...................................................... 7
1.3 Operator training.................................................................................................... 7
1.4 Personal protective equipment .............................................................................. 7
1.5 Designated use...................................................................................................... 8
1.6 Codes and standards ............................................................................................ 8
1.7 Noise and vibration................................................................................................ 8
2 Scope of supply, transport and storage 9
2.1 Items supplied ....................................................................................................... 9
2.2 Transport ............................................................................................................... 9
2.3 Storage ..................................................................................................................9
3 Product description 10
3.1 General description ............................................................................................. 10
3.2 Operation and functional elements...................................................................... 10
4 Accessories 11
5 Before initial operation 12
5.1 Ambient conditions .............................................................................................. 12
5.2 Air supply............................................................................................................. 12
5.3 Connecting the air supply to the tool ................................................................... 12
5.4 Tool set up ........................................................................................................... 13
6 First operation 14
6.1 Puting into use..................................................................................................... 14
7 Troubleshooting 15
8 Maintenance 16
8.1 Service schedule ................................................................................................. 16
8.1.1 Calculating a customer specic maintenance plan.............................................. 17
8.2 Lubricants ............................................................................................................17
9 Repair instructions 19
9.1 Motor disassembly and reassembly .................................................................... 19

Page 5
PL12-1019EN
05/14/2013
Cleco®
Contents
10 Spare parts
10.1 19P series screwdriver ........................................................................................ 20
10.2 19T series screwdriver ........................................................................................ 22
10.3 Motor assembly ................................................................................................... 24
10.4 301967PT Gearing assembly .............................................................................. 26
10.5 301086 Gearing assembly................................................................................... 26
10.6 301968PT Gearing assembly .............................................................................. 28
10.7 301969PT Gearing assembly .............................................................................. 28
10.8 301122 Spindle assembly.................................................................................... 30
11 Technical data 32
11.1 19PTS and 19TTS Specications........................................................................ 32
12 Service 33
12.1 Replacement parts .............................................................................................. 33
12.2 Tool repairs .......................................................................................................... 33
12.3 Warranty repairs .................................................................................................. 33
13 Disposal 34

Page 6
PL12-1019EN
05/14/2013
Cleco®
Safety
1 Safety
1.1 Warnings and notes
Warning notes are identied by a signal word and a pictogram.
• The signal word indicates the severity and probability of the impending danger.
• The pictogram indicates the type of danger.
---------------------------------------------------------------------------------------------------------------------------------------
WARNING identies a potentially hazardous situation which, if not avoided, may result in serious
injury.
---------------------------------------------------------------------------------------------------------------------------------------
---------------------------------------------------------------------------------------------------------------------------------------
CAUTION identies a potentially hazardous situation which, if not avoided, may result in minor or
moderate injury or property and environmental damage.
---------------------------------------------------------------------------------------------------------------------------------------
---------------------------------------------------------------------------------------------------------------------------------------
NOTE identies general information which may include application tips or useful information but no
hazardous situations.
---------------------------------------------------------------------------------------------------------------------------------------
---------------------------------------------------------------------------------------------------------------------------------------
Important information that must be read and understood by all personnel installing, operating or
maintaining this equipment.
---------------------------------------------------------------------------------------------------------------------------------------

Page 7
PL12-1019EN
05/14/2013
Cleco®
Safety
1.2 Basic requirements for safe working practices
All personnel involved with the installation, operation or maintenance of these tools must read and
understand all safety instructions contained in this manual. Failure to comply with these instructions
could result in serious injury or property damage.
These safety instructions are not intended to be all inclusive. Study and comply with all applicable
National, State and Local regulations.
---------------------------------------------------------------------------------------------------------------------------------------
Work Area:
ÚEnsure there is enough space in the work area.
ÚKeep the work area clean.
ÚKeep the work area well ventilated.
Personnel Safety:
ÚInspect the air supply hoses and ttings. Do not use damaged, frayed or deteriorated hoses.
ÚMake sure the air supply hose is securely attached to the tool.
ÚEnsure a secure standing position and maintain balance.
ÚMake sure the throttle is positioned relative to the head so the throttle will not become wedged
against an adjacent object in the ON position due to torque reaction.
ÚIf the tool is to be reversed, locate the throttle in a neutral position to prevent entrapment.
ÚKeep the tool clean and dry to provide the best possible grip.
ÚFirmly grasp the handle of the 19P/19T and apply the bit to the application before starting.
ÚBe prepared for high short-term reaction torques.
Safety working with and around fastening tools:
ÚUse only power tool sockets and bits available from Apex Tool Group.
ÚInspect socket or bit for visible damage and cracks. Replace damaged items immediately.
ÚDisconnect the air supply before installing or replacing the socket or bit.
ÚDo not attach the socket or bit at a slant.
ÚMake sure the socket or bit is fully assembled on the drive and locked in postion.
---------------------------------------------------------------------------------------------------------------------------------------
1.3 Operator training
All personnel must be properly trained before operating the 19P/19T tools. The 19P/19T tools are to be
repaired by fully trained personnel only.
1.4 Personal protective equipment
When working
• Wear eye protection to protect against ying metal splinters.
• Wear hearing protection
Danger of injury by being caught by moving equipment.
• Wear a hairnet
• Wear close tting clothing
• Do not wear jewelry

Page 8
PL12-1019EN
05/14/2013
Cleco®
Safety
1.5 Designated use
The 19P/19T are designed exclusively for fastening and releasing threaded fasteners.
The 19P/19T series screwdrivers are not equipped with a clutch. The output spindle is coupled to the
last stage of gearing. Torque output from a stall tool may be controlled within fairly reasonable limits
with an air pressure regulator.
• Do not modify the 19P/19T, any guard or accessory.
• Use only with accessory parts which are approved by the manufacturer.
• Do not use as a hammer, pry-bar or any other improper usage.
1.6 Codes and standards
It is mandatory that all national, state and local codes and standards be followed.
1.7 Noise and vibration
Noise level ≤ 79 dB(A) free speed (without load) according to ISO 12100: 2011
Vibration values < 2.5 m/s2 according to ISO 12100: 2011

Page 9
PL12-1019EN
05/14/2013
2 Scope of supply, transport and storage
2.1 Items supplied
Check shipment for transit damage and ensure that all items have been supplied:
1 19P or 19T
1 PL12-1019EN instruction manual
1 Declaration of Conformity
1 Lubrication sheet
1 Warranty statement
2.2 Transport
Transport and store the 19P/19T in the original packaging. The packaging is recyclable.
2.3 Storage
For short term storage (less than 2 hours) and protection against damage:
ÚPlace the 19P/19T in a location on the workbench to avoid accidental depression of the trigger.
or
ÚSuspend the 19P/19T from a suitable balancer or tool positioner.
For storage longer than 2 hours:
ÚDisconnect the air supply from the 19P/19T
Cleco®
Scope of Supply, Transport and Storage
Object Time Period Storage Temperature
19PT without air supply No guideline -13°F to 104°F (-25°C to 40°C)
19TT without air supply No guideline -13°F to 104°F (-25°C to 40°C)

Page 10
PL12-1019EN
05/14/2013
Cleco®
Product Description
3 Product description
3.1 General description
• Pistol grip or “T” handle pneumatic powered screwdriver
• Trigger actuated
• Clockwise/counterclockwise rotation
• Stall type tool (no clutch)
• Low vibration level
3.2 Operation and functional elements
This section describes the operational and functional elements of the 19P/19T.
3
5
6
1
2
Ref. Description
1 Air Inlet
2 Reversing Lever
3 Trigger
4 Two Interchangeable soft-touch grip sizes
5 Motor and Gearing
6 Quick Change Chuck
4

Page 11
PL12-1019EN
05/14/2013
Cleco®
Accessories
4 Accessories
Suspension Bail
Part Number: 931962
Exhaust Overhose
Part Number: 207107 (19T)
Small Handle
Part Number: 207595PT

Page 12
PL12-1019EN
05/14/2013
Cleco®
Before Initial Operation
5 Before initial operation
5.1 Ambient conditions
Ambient temperature: 41°F (5°C) to a maximum of 104°F (40°C)
Acceptable relative humidity: 25% to 90%, non-condensing
5.2 Air supply
To attain consistent results, maintain a constant working pressure using a suitable air line unit consisting
of a lter, regulator and lubricator.
ÚThe inside diameter of the air hose must be free of residue, clean if necessary.
ÚSpray a few drops of light air tool oil into the air inlet adapter.
ÚAdjust the lubricator to a minimum setting to reduce the amount of excess oil in the exhaust air.
Oil identification
5.3 Connecting the air supply to the tool
---------------------------------------------------------------------------------------------------------------------------------------
The air hose can disconnect from the tool by itself and whip around uncontrollably.
ÚTurn off the compressed air before connecting to the tool.
ÚSecurely connect the air hose to the tool.
ÚTurn on the compressed air.
---------------------------------------------------------------------------------------------------------------------------------------
Parameter Description
Air Hose
Minimum inside diameter: 3/16" (4,7 mm)
Maximum length: 16.4' (5 m)
Working pressure range
58 to 101.5 psi (400 to 700 kPa)
Recommended: 90 psi (620 kPa)
Compressed air
Air quality according to ISO 8573-1, quality class 2.4.3
The compressed air must be clean and dry.
Part No. Packaged Designation Vendor
540397 1 Quart (0.94 liter) Airlube 10W/NR-420LB DR Fuchs Lubricants Co.
533485 1 US Gallon (3.78 liter) Airlube 10W/NR-420LB DR Fuchs Lubricants Co.

Page 13
PL12-1019EN
05/14/2013
5.4 Tool set up
The tool must be congured for the application.
Cleco®
Before Initial Operation

Page 14
PL12-1019EN
05/14/2013
Cleco®
First Operation
6 First operation
6.1 Putting into use
ÚMake sure the air supply is securely attached and the compressor is turned on.
ÚMake sure the reverse lever is in the correct position.
ÚPlace the socket or bit on the application and depress the trigger to start the rundown.
ÚWhen the rundown is complete, release the trigger.
ÚRemove the tool from the application.

Page 15
PL12-1019EN
05/14/2013
Cleco®
Troubleshooting
7 Troubleshooting
Malfunction Possible causes Remedy
No or low air pressure
Make sure there is adequate air pressure at
the tool air inlet
Reversing lever out of position
Make sure the reversing lever is in the
clockwise or counterclockwise position
Broken gears
Tool disassembly required (parts
replacement)
Tool does not shut
off
Working pressure < 58 psi (400 kPa) Increase the working air pressure
Reduced air pressure Check air supply line for any obstructions
Lack of lubrication
Check the air line lubricator to make sure it is
full of lubricant and is working properly
Motor exhaust air is obstructed Clean or replace bronze mufflers
Swollen rotor blades from excessive
moisture
Check the air line filter, empty reservoir if
necessary
Worn rotor blades
Tool disassembly required (parts
replacement)
Worn gears or bearings
Tool disassembly required (parts
replacement)
Loose inlet adapter Tighten inlet adapter
Worn o-ring on inlet adapter Replace o-ring
Tool loses power
Air leak at inlet
adapter
Tool does not
start

Page 16
PL12-1019EN
05/14/2013
Cleco®
Maintenance
8 Maintenance
---------------------------------------------------------------------------------------------------------------------------------------
Danger of injury from accidental start up.
Turn off the compressed air before performing any maintenance.
---------------------------------------------------------------------------------------------------------------------------------------
8.1 Service schedule
Only qualied and trained personnel are permitted to perform maintenance on these tools.
Regular maintenance reduces operating faults, repair costs and downtime. In addition to the following
service schedule, implement a safetu related maintenance program that takes the local regulations for
repair and maintenance for all operating phases of the tool into account.
This maintenance schedule uses values that are valid for most applications. For a specic maintenance
interval, refer to 8.1.1 Calculating a customer-specic maintenance plan.
Maintenance
Interval
Rundowns
Daily Daily
Visual inspection of air supply hose and connections
Inspect airline filter, regulator and lubricator for proper operation
Check the tool for excessive vibration or unusual noises
Visual inspection of all external components of the tool
W1 100,000
Inspect the air hose for damage or wear
inspect the output spindle for damage or wear
Inspect the air inlet adapter for a secure fit
Check the maximum free speed
W2 500,000
Check individual parts and replace if necessary
Replace O-rings and seals
Clean bronze mufflers
W3 1,000,000
Check individual parts and replace if necessary
Throttle valve
Motor
Gearing
Quick change chuck
Designation

Page 17
PL12-1019EN
05/14/2013
Cleco®
Maintenance
8.1.1 Calculating a customer specic maintenance plan
A service interval W(1, 2, 3) depends on the following factors:
8.2 Lubricants
For proper function and long service life, use of the correct grease is essential.
Grease lubricants recommended for this tool.
Example for service interval W2:
After 500,000 rundowns (V),
a specific rundown time of 1.8 seconds (T1)
with an actual fastening time of 3 seconds (soft joint) and
3 completed shifts per day and 750 rundowns per shift.
V x T1 500000 x 1.8
T2 x S x VS 3 x 3 x 750
You will need to perform the maintenance indicated as W2 after an operating time of 133 days.)
W (1, 2, 3) = W2 = = 133 (days)
Factor
Value assumed in
"Service Schedule"
Description
V
V1 = 100,000
V2 - 500,000
V3 = 1,000,000
Number of rundowns after a maintenance measure is prescribed by Apex
Tool Group.
T1 1.8 seconds Specific rundown time, measured in life and endurance tests.
T2 2 seconds Actual rundown time, depending on the hardness of the joint.
S1; 2; 3 Number of shifts per day.
VS 750 Number of rundowns per shift.
T2, S and VS are variable factors and can differ depending on the specific application.
Part No. Packaged Designation Vendor
540450 18 oz. (0.51 kg) Black Pearl EP-NLGI-0 Chevron
540395 2 oz. (0.06 kg) Magnalube-G Carleton-Stuart Corp.
513156 16 oz. (0.45 kg) Magnalube-G Carleton-Stuart Corp.
541444 2 oz. (0.06 kg) Rheolube 363AX-1 Nye Lubricants, Inc.
541445 16 oz. (0.45 kg) Rheolube 363AX-1 Nye Lubricants, Inc.

Page 18
PL12-1019EN
05/14/2013
Cleco®
Blank Page

Page 19
PL12-1019EN
05/14/2013
9 Repair instructions
9.1 Motor disassembly and reassembly
Disassembly
R = Replace
1 2
1 2 3 4
Reassembly
O O
.0010” (.254mm)
to
.0015” (.031mm)
Cleco®
Repair Instructions

Page 20
PL12-1019EN
05/14/2013
Page 20
10.1 19P Series Screwdriver Models
19PTS(--)Q
Cleco®
Spare Parts
14
25
26
23
2
5
24
6
8
9
7
22
21
20
19
18
17
15
16
13
27
11
10
4
12
3
Torque:
95-105 in. lbs.
(10.7-11.8 Nm)
Torque:
5-7 in. lbs.
(0.6-0.8 Nm)
Other manuals for 19P Series
1
This manual suits for next models
9
Table of contents
Other Cleco Power Screwdriver manuals
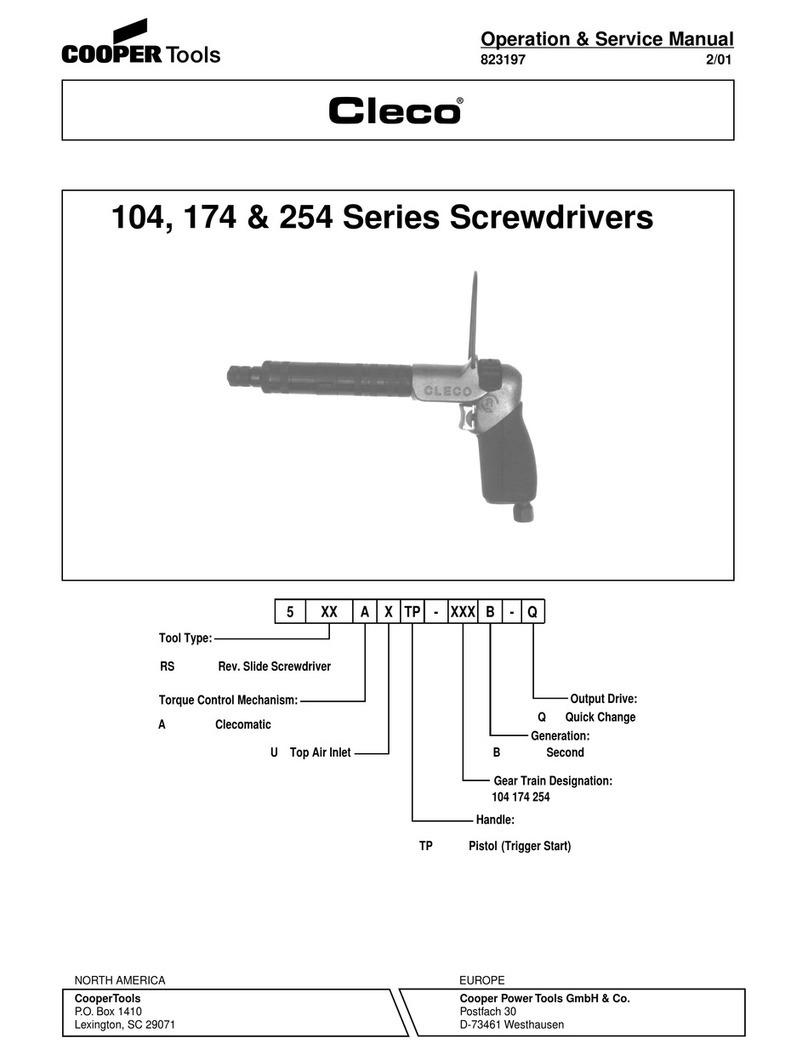
Cleco
Cleco 104 Series Installation and operating instructions
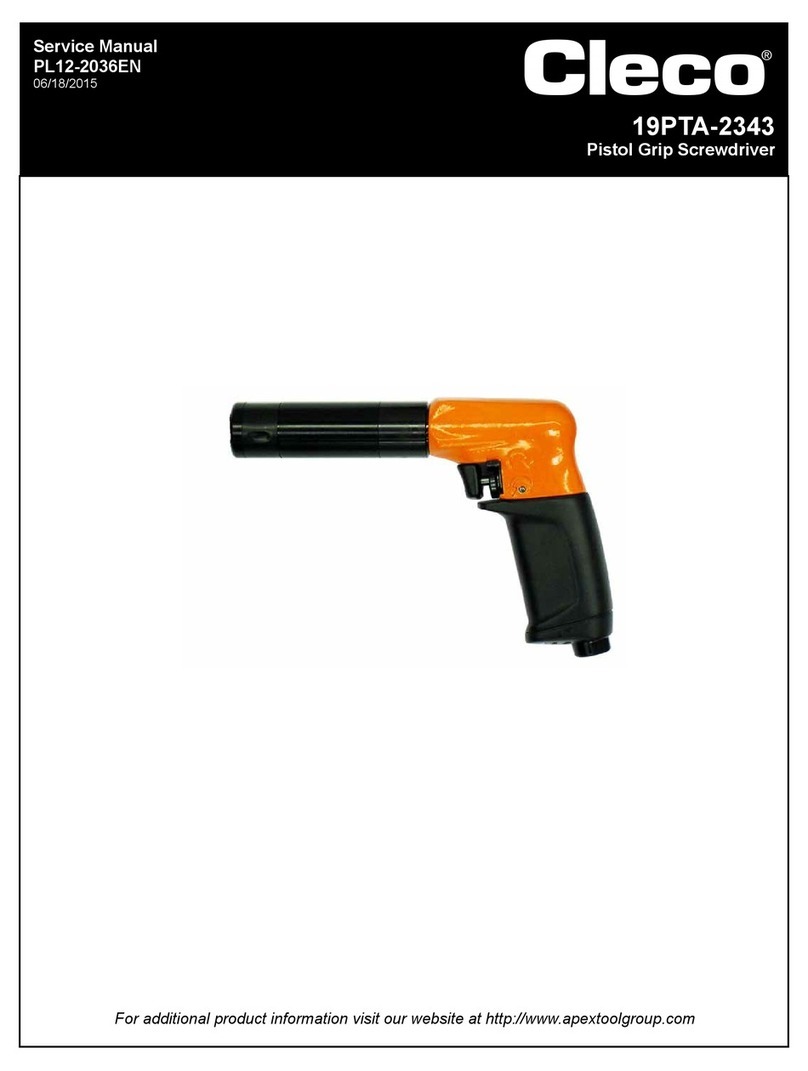
Cleco
Cleco 19PTA-2343 User manual
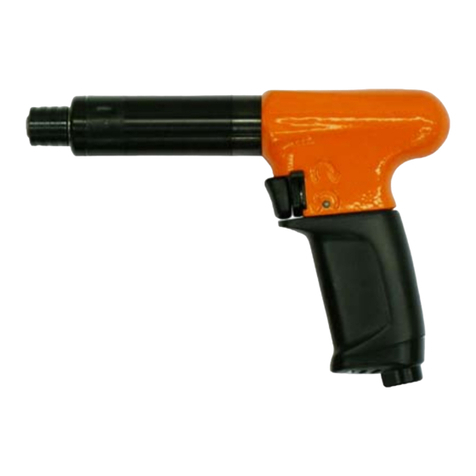
Cleco
Cleco 19P Series User manual

Cleco
Cleco 19BPA User manual

Cleco
Cleco BRSAUPT User manual
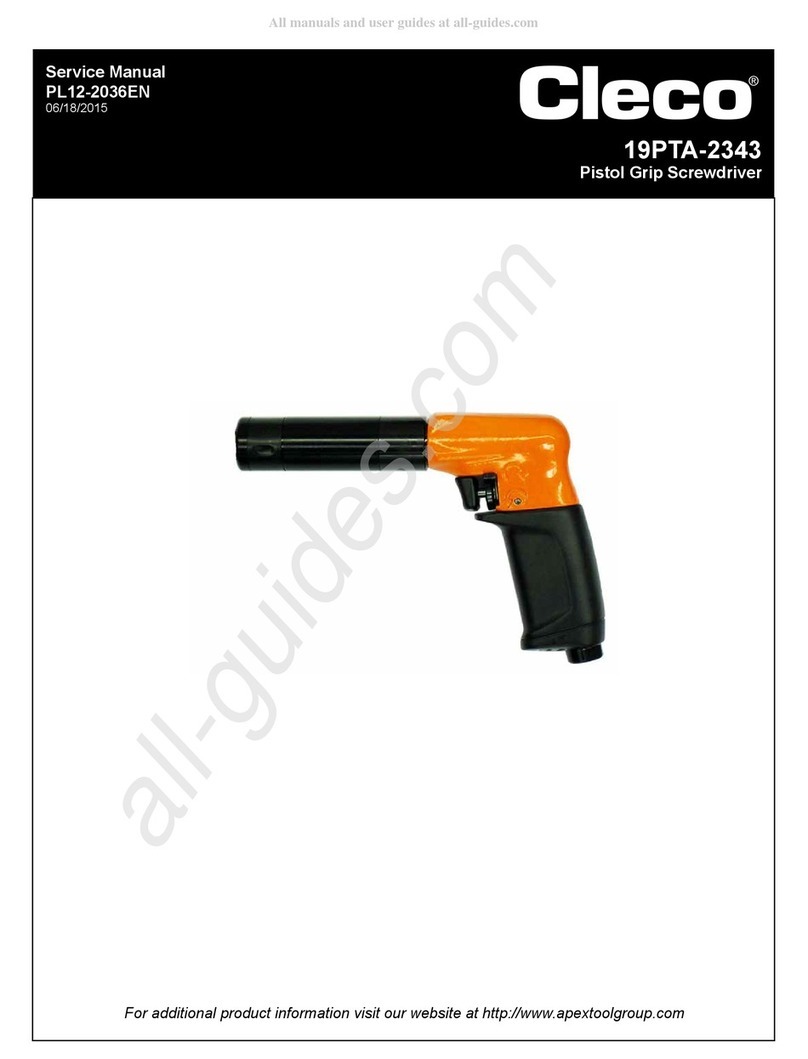
Cleco
Cleco 19PTA-2343 User manual
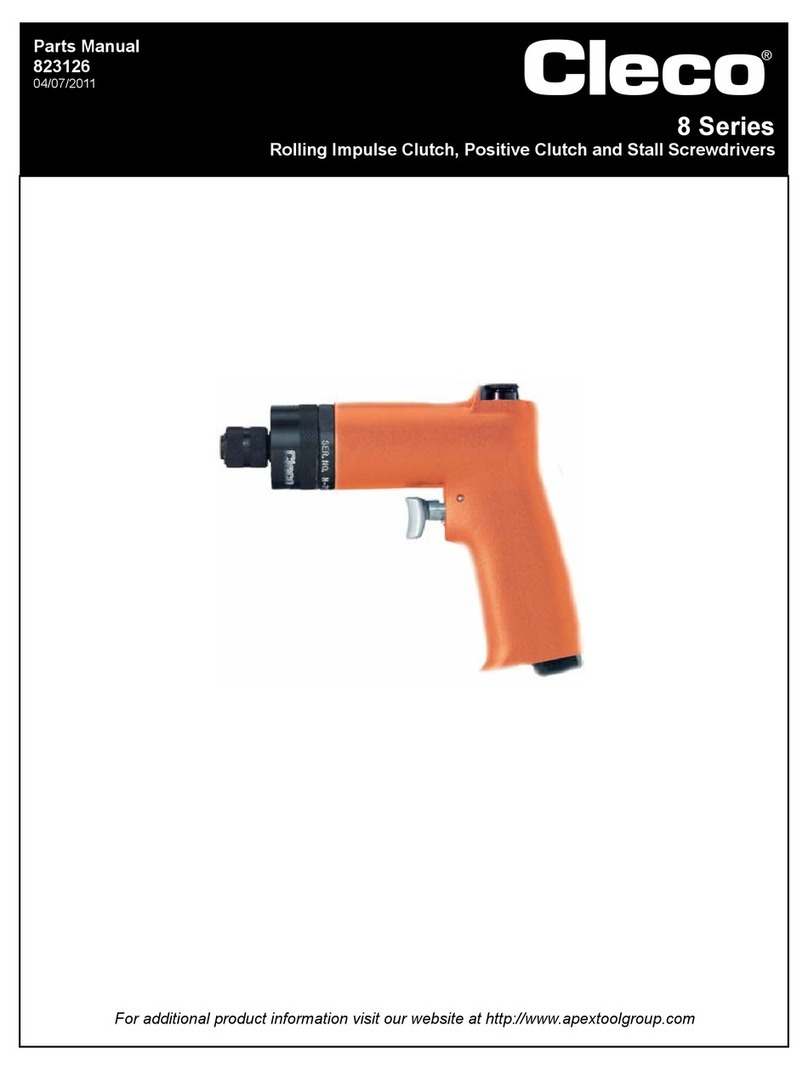
Cleco
Cleco 8 Series User manual
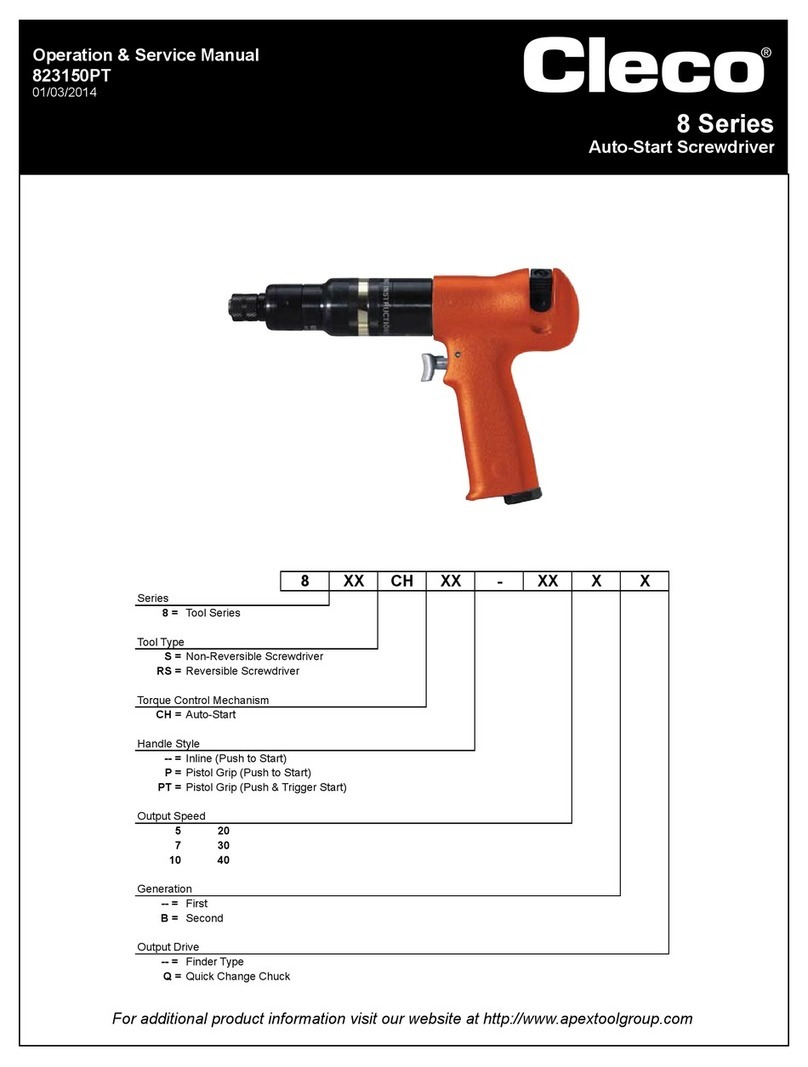
Cleco
Cleco 823150PT Installation and operating instructions