Clemco ZERO Pulsar III-P User manual

NOTICE TO PURCHASERS AND USERS OF OUR
PRODUCTS AND THIS INFORMATIONAL MATERIAL
Clemco proudly provides products for the abrasive blast industry
and is confident that industry professionals will use their knowledge
and expertise for the safe and efficient use of these products.
The products described in this material and the information
relating to these products are intended for knowledgeable,
experienced users. It is the responsibility of the employer to
ensure that proper training of operators has been performed and
a safe work environment is provided.
No representation is intended or made as to the suitability of the
products described here for any purpose or application, or to the
efficiency, production rate, or useful life of these products. All
estimates regarding production rates or finishes are the
responsibility of the user and must be derived solely from the user’s
experience and expertise, not from information contained in this
material.
It is possible that the products described in this material may be
combined with other products by the user for purposes determined
solely by the user. No representations are intended or made as to
the suitability of, engineering balance of, or compliance with
regulations or standard practice of any such combination of products
or components the user may employ.
This equipment is only one component of a cabinet blasting
operation. Other products, such as air compressors, air filters and
receivers, abrasives, equipment for ventilating or dehumidifying, or
other equipment, even if offered by Clemco, may have been
manufactured or supplied by others. The information Clemco
provides is intended to support the products Clemco manufactures.
Users must contact each manufacturer and supplier of products
used in the blast operation for warnings, information, training, and
instruction relating to the proper and safe use of their equipment.
Pulsar® III-P & III-PE
Pulsar® VI-P & VI-PE
Pressure Blast Cabinets
O. M. 21527
DATE OF ISSUE: 05/95
REVISION: I, 02/19
© 2019 CLEMCO INDUSTRIES CORP.
One Cable Car Dr.
Washington, MO 63090
Phone (636) 239-4300
Fax (800) 726-7559
Email: [email protected]
www.clemcoindustries.com

PULSAR® III-P/III-PE and VI-P/VI-PE PRESSURE CABINETS Page 1
© 2019 CLEMCO INDUSTRIES CORP. www.clemcoindustries.com Manual No. 21527, Rev. I, 02/19
1.0 INTRODUCTION
1.1 Scope of Manual
1.1.1 These instructions cover the setup, operation,
maintenance, troubleshooting, and replacement parts for
the following Pulsar® Pressure Blast Cabinets:
Pulsar III-P Conventional, (stand-up model)
Pulsar III-PE Ergonomic, (sit-down model)
Pulsar VI-P Conventional, (stand-up model)
Pulsar VI-PE Ergonomic, (sit-down model)
A separate owner’s manual, stock no. 20951, is provided
for the Sentinel Media Metering Valve.
1.1.2 The instructions contain important information
required for safe operation of the cabinets. Before using
this equipment, all personnel associated with the blast
cabinet operation must read this entire manual and all
accessory manuals, to become familiar with their
operation, parts, and terminology.
1.2 Safety Alerts
1.2.1 Clemco uses safety alert signal words, based on
ANSI Z535.4-2011, to alert the user of a potentially
hazardous situation that may be encountered while
operating this equipment. ANSI's definitions of the signal
words are as follows:
This is the safety alert symbol. It is
used to alert you to potential physical
injury hazards. Obey all safety
messages that follow this symbol to
avoid possible injury or death.
NOTICE
Notice indicates information that is considered
important, but not hazard-related, if not
avoided, could result in property damage.
CAUTION
Caution indicates a hazardous situation that, if
not avoided, could result in minor or moderate
injury.
WARNING
Warning indicates a hazardous situation that, if
not avoided, could result in death or serious
injury.
DANGER
Danger indicates a hazardous situation that, if
not avoided, will result in death or serious
injury.
1.3 Table of Contents
SUBJECT SECTION LOCATION
INTRODUCTION ........................................................ 1.0
Scope of Manual ......................................................... 1.1
Safety Alerts ............................................................... 1.2
Table of Contents ....................................................... 1.3
General Description .................................................... 1.4
Theory of Operation .................................................... 1.5
Blast Machine and Controls ....................................... 1.6
Nozzle Options ........................................................... 1.7
Reclaimer Options ...................................................... 1.8
Metering Valve Options .............................................. 1.9
HEPA Filter ............................................................... 1.10
Blasting Media .......................................................... 1.11
Compressed-Air Requirements ................................ 1.12
Electrical Requirements ........................................... 1.13
INSTALLATION ......................................................... 2.0
General Installation Notes .......................................... 2.1
Connect Compressed-Air Supply Line ....................... 2.2
Ground the Cabinet .................................................... 2.3
Connect Electrical Service ......................................... 2.4
Standard single-phase wiring ................................ 2.4.1
Optional three-phase wiring .................................. 2.4.2
Set Air-Inlet Damper ................................................... 2.5
Final Assembly ........................................................... 2.6
FIELD INSTALLED ACCESSORIES ......................... 3.0
Aluminum Oxide (aggressive media) Kit .................... 3.1
Cabinet Curtains Installation ...................................... 3.2
Manometer ................................................................. 3.3
Reclaimer Differential-Pressure Gauge ..................... 3.4
Turntable with Workcar and Track ............................. 3 . 5
Dust-Collector Differential-Pressure Gauge ................ 3.6
Armrest ....................................................................... 3.7
OPERATION .............................................................. 4.0
Season Filter Cartridge ............................................... 4.1
Media Loading ............................................................ 4.2
Media Unloading ......................................................... 4.3
Loading and Unloading Parts ..................................... 4.4
Blasting Operation ...................................................... 4.5
Operation and Function of the Choke Valve ............... 4.6
Blasting Technique ..................................................... 4.7
Stop Blasting .............................................................. 4.8
Pulsing (cleaning) Dust-Collector Cartridge ............... 4.9
Shutdown .................................................................. 4.10
ADJUSTMENTS ......................................................... 5.0
Blasting Pressure (pilot regulator) .............................. 5.1
Media Metering (media flow) ...................................... 5.2
Reclaimer Static Pressure .......................................... 5.3

PULSAR® III-P/III-PE and VI-P/VI-PE PRESSURE CABINETS Page 2
© 2019 CLEMCO INDUSTRIES CORP. www.clemcoindustries.com Manual No. 21527, Rev. I, 02/19
Door Interlocks ........................................................... 5.4
Pulse Pressure .......................................................... 5.5
Cabinet Air-Inlet Damper ........................................... 5.6
Optional Manometer .................................................. 5.7
Foot Shelf (Ergonomic models only) .......................... 5.8
PREVENTIVE MAINTENANCE ................................ 6.0
Daily Inspection and Maintenance Before Blasting ..... 6.1
Check media level ............................................... 6.1.1
Inspect reclaimer debris screen and door gasket .. 6.1.2
Drain compressed-air filter .................................. 6.1.3
Inspect couplings ................................................. 6.1.4
Inspect dust container ......................................... 6.1.5
Daily Inspection and Maintenance During Blasting .... 6.2
Inspect couplings and blast hose ........................ 6.2.1
Inspect blast machine for air leaks ...................... 6.2.2
Inspect cabinet for dust leaks .............................. 6.2.3
Drain pulse reservoir ........................................... 6.2.4
Check exhaust air for dust ................................... 6.2.5
Additional cartridge pulsing ................................. 6.2.6
Weekly Inspection and Maintenance Before Blasting .. 6.3
Inspect view-window cover lens .......................... 6.3.1
Inspect gloves for wear ....................................... 6.3.2
Inspect nozzle ...................................................... 6.3.3
Inspect blast hose ................................................ 6.3.4
Inspect outlet valve .............................................. 6.3.5
Weekly Inspection During Blasting ............................ 6.4
Inspect blast machine plumbing for leaks ............ 6.4.1
Inspect flex hoses ................................................ 6.4.2
Monthly Inspection and Maintenance ........................ 6.5
Pop-up valve ......................................................... 6.5.1
Pop-up seal .............................................................. 6.5.2
SERVICE MAINTENANCE ........................................ 7.0
Gloves ......................................................................... 7.1
LED Light Assembly ................................................... 7.2
Blast Hose and Nozzle ............................................... 7.3
View-Window Cover Lens .......................................... 7.4
View-Window Replacement ........................................ 7.5
Window-Gasket Replacement .................................... 7.6
Window-Frame Removal ............................................ 7.7
Replacing Filter Cartridge ........................................... 7.8
Seasoning Filter Cartridge .......................................... 7.9
Pop-Up Valve Replacement ..................................... 7.10
Pop-Up Valve Seal Replacement ............................. 7.11
Replacing Reclaimer Wear Plate ............................... 7.12
Replacing or Installing Rubber Reclaimer Liners ..... 7.13
Removing or Replacing Reclaimer Inlet Baffle .......... 7.14
Sentinel Metering Valve ............................................ 7.15
TROUBLESHOOTING ............................................... 8.0
Poor visibility ............................................................... 8.1
Abnormally high media consumption .......................... 8.2
Reduction in blast cleaning rate ................................. 8.3
Plugged nozzle ............................................................ 8.4
Media bridging ............................................................. 8.5
Media surge ................................................................ 8.6
Air only (no media) from nozzle ................................... 8.7
Neither media nor air comes out the nozzle ............... 8.8
Blast machine does not pressurize ............................. 8.9
Blast machine does not depressurize or
depressurizes too slowly ........................................ 8.10
Heavy media flow ..................................................... 8.11
Media buildup in cabinet hopper; media does
not convey to reclaimer ......................................... 8.12
Static shocks ............................................................. 8.13
Dust leaking from cabinet ......................................... 8.14
Dust leaking from dust collector ............................... 8.15
Dust collector does not pulse when foot pedal
is pressed or released ........................................... 8.16
A steady stream of air is heard within the dust
collector when the foot pedal is not pressed .......... 8.17
ACCESSORIES AND REPLACEMENT PARTS ....... 9.0
Optional Accessories .................................................. 9.1
Foot-Pedal Assembly ................................................. 9.2
Cabinet Replacement Parts ........................................ 9.3
LED Light Assembly ................................................... 9.4
1" Diaphragm Outlet Valve .......................................... 9.5
View-Window Assembly .............................................. 9.6
Plumbing and Cabinet Controls .................................. 9.7
Blast Machine ............................................................. 9.8
Reclaimer .................................................................... 9.9
Dust Collector ........................................................... 9.10
1.4 General Description
1.4.1 Pulsar Pressure Cabinets enclose the blasting
environment to provide efficient blasting while maintaining
a clean surrounding work area. Production rates are
influenced by size of nozzle, compressor output, working
pressure, type and size of media, and angle and distance
of the nozzle from the blast surface. Refer to Figure 1 for
arrangement of components. Pulsar Pressure Cabinets
consist of two major components:
1. Cabinet Enclosure
2. 600 cfm Power Module
NOTE: All Pulsar® III-P and VI-P Pressure Cabinets
include 600 cfm Power Modules.
1.4.2 Cabinet enclosure: This manual covers two
Pulsar Cabinet model sizes. Each is available in a
conventional (stand-up style) and ergonomic (sit-down
style) representing four cabinet configurations.
Pulsar III-P/E Approximate work chamber dimensions:
36" wide x 35" deep x 37" high.
Pulsar VI-P/E Approximate work chamber dimensions:
50" wide x 39" deep x 43" high.
NOTE: The extended front on ergonomic style cabinets
provides approximately 12-inches additional depth from
the arm port and above, and is approximately 3-inches
narrower than the widths shown above.

PULSAR® III-P/III-PE and VI-P/VI-PE PRESSURE CABINETS Page 3
© 2019 CLEMCO INDUSTRIES CORP. www.clemcoindustries.com Manual No. 21527, Rev. I, 02/19
1.4.3 Power module: The 600 cfm power module is
approximate 50" wide x 32" deep. The module is
attached to the back of the cabinet and includes a 600
cfm reverse-pulse dust collector, and a 600 cfm
reclaimer mounted above a 1-cuft blast machine.
Pulsar VI pressure blast modules are easily converted
to suction systems, using the conversion kit listed in
Section 9.1: Optional Accessories.
1.5 Theory of Operation
1.5.1 Once the cabinet is correctly set up and turned
ON, the cabinet is ready for operation by actuation of
the foot pedal. Fully depressing down on the foot pedal
pressurizes the blast machine, causing media to be
propelled through the blast hose and out the nozzle.
After striking the object being blasted, the blast media,
fines, dust, and byproducts generated by blasting fall
through the grate into the cabinet hopper. These
particles are then drawn into the reclaimer for
Figure 1
Exhauster
Blow-Off Hose
Blast Hose
Compressed-
Air Filter
Debris Screen
Dust-Collector Inlet
Dust Collector
Dust Container
Dust-Collector Hopper
(Access Door)
Pulse Reservoir
Reclaimer
Blast Machine
Air-Inlet Damper
Door Interlock Actuator
Pilot Regulator
(Blast Pressure)
Foot Pedal
On-Off Switch
Exhaust Muffler
Lifting Eye
Blast Nozzle
Blow-Off Nozzle
Pressure Regulator
Dust-Collector Pulse
Door Interlock
Valve
Outlet Damper
Access from underneath.
120-V, 1-PH Supply Cord
Cover Plate
For optional HEPA Filter.
Grounding Lug
Pulsar Model VI-P shown. Model III-P is identical except size of cabinet enclosure is smaller.
Adjustable Foot Shelf
Ergonomic Models only.
Front view of Model VI-PE
ergonomic cabinet.
Rear view of Model VI-P
conventional cabinet.
Attachment for
compressed-air
supply line.

PULSAR® III-P/III-PE and VI-P/VI-PE PRESSURE CABINETS Page 4
© 2019 CLEMCO INDUSTRIES CORP. www.clemcoindustries.com Manual No. 21527, Rev. I, 02/19
separation. Dust and fines are first separated from
reusable media and pass into the dust collector. Next,
reusable media is screened for oversize particles and
returned to the reclaimer for reuse. Dust and fines
entering the dust collector are removed from the air
stream as they pass through the filters, discharging
clean air. When the foot pedal is released, the blast
machine depressurizes and blasting stops. Media
stored in the reclaimer automatically refill the blast
machine when blast machine pressure equalizes and
the pop-up valve drops.
1.5.2 The dust-collector filter cartridge is cleaned by a
pulse of high velocity compressed air expanding against
the inner surface of the cartridge. The pulse occurs each
time the foot pedal is pressed or released. The expanding
air momentarily reverses airflow through the cartridge to
release dust accumulated on the outer surface. The dust
particles fall away from the cartridges and into the hopper
for removal. An optional automatic pulse kit can be added
to pulse the cartridge at timed intervals during blasting.
(See Section 9.1: Optional Accessories.).
1.6 Blast Machine and Controls
1.6.1 Clemco certifies its blast machines (pressure
vessels) to conform to the ASME (American Society of
Mechanical Engineers) Boiler and Pressure Vessel
Code, Section VIII, Division 1. It is the owner’s
responsibility to maintain the integrity of the vessel in
accordance with state regulations. Regulations may
include regular inspection and hydrostatic testing as
described in National Board inspection code and
jurisdictional regulations and/or laws.
WARNING
Welding, grinding, or drilling on the blast
machine can weaken the vessel. Compressed-
air pressure can cause a weakened blast
machine to rupture, resulting in death or
serious injury. Welding, grinding, or drilling on
the vessel without a National Board R Stamp
voids the Clemco ASME certification.
1.6.2 All welding repairs to the vessel must be
performed by certified welders at shops holding a
National Board R stamp. Welding performed by any
welder not properly qualified per the ASME code voids
the Clemco ASME certification.
1.6.3 Do not exceed the maximum working pressure
rating (PSI) of the blast machine. The maximum
pressure rating is stamped into the ASME nameplate,
which is welded to the side of the vessel.
WARNING
Excessive compressed-air pressure can cause
a blast machine to rupture. To prevent serious
injury or death, do not exceed the rated
pressure of the blast machine.
1.6.4 OSHA does not require pressure-relief valves
on blast machines when air compressors supplying air
to the blast machines are built to American Society of
Mechanical Engineers Boiler and Pressure Vessel
Code, Section VIII, Division 1 and comply with OSHA
regulation 29 CFR 1910.169, which refers to the ASME
code when describing the necessity of pressure-relief
valves on compressed air equipment. DO NOT operate
blast machines with air compressors that are not
equipped with properly functioning pressure-relief valves
with maximum pressure less than or equal to the
maximum-allowable working pressure (MAWP) stamped
on the vessel nameplate.
1.6.5 When the cabinet is set up, the blast machine is
ready to blast by actuating the foot pedal. Pressing the
foot pedal opens the normally closed main inlet
regulator and closes the normally open outlet valve. The
incoming air pressurizes the blast machine, and blasting
begins. When pressure on the foot pedal is released,
the blast machine depressurizes and blasting stops.
1.7 Nozzle Options
1.7.1 Unless otherwise specified at the time of
purchase, the cabinet is provided with a 3/16" orifice
tungsten carbide nozzle. Optional 1/8" and 1/4" orifice
nozzles are also available.
1.7.2 Nozzles with an orifice larger than those
recommended could cause air leakage from the cabinet
and impair recovery from the cabinet hopper.
1.7.3 Use boron carbide nozzles when blasting with
aggressive media noted in Section 1.11.3. Nozzles lined
with boron carbide extend nozzle wear life. Refer to
Section 9.1: Optional Accessories.
1.8 Reclaimer Options
1.8.1 Replaceable rubber reclaimer liners: Rubber
liners are available for Pulsar VI, 600 cfm reclaimers
that have a removable top and that are designed to
accept liners. The liners prolong service life of the
reclaimer, and should be installed when using silicon
carbide, aluminum oxide, or other aggressive media, as
noted in Section 1.11.3. Rubber reclaimer liners are
shown in Section 9.1: Optional Accessories, Figure 40.

PULSAR® III-P/III-PE and VI-P/VI-PE PRESSURE CABINETS Page 5
© 2019 CLEMCO INDUSTRIES CORP. www.clemcoindustries.com Manual No. 21527, Rev. I, 02/19
1.9 Metering Valve Options
1.9.1 Unless specified at the time of purchase,
cabinets are supplied with a fine-mesh Sentinel
Metering Valve. The valve is for use with 50-mesh and
finer media, and #10 and finer glass bead. The optional
Sentinel Metering Valve is recommended when using
media coarser than 50-mesh. Conversions kits listed in
Section 9.1 easily convert the valves.
1.10 HEPA (high-efficiency particulate air) Filter
1.10.1 Optional HEPA afterfilter provides additional
filtration. A HEPA filter must be used when removing
lead coatings, Heavy metals, or any other toxic materials.
HEPA filter is listed in Section 9.1: Optional Accessories.
WARNING
All dust is hazardous to breath. Emissions can
occur from the dust collection system. Identify
all materials that are to be removed by blasting;
if any toxic materials such as lead dust or dust
from other heavy metals and corrosives, or any
other toxic materials are being removed, use a
HEPA afterfilter to assist in maintaining
inhalation hazards below the permissible
exposure limits (PELs). Prolonged exposure to
any dust can result in serious lung disease and
death. Short-term ingestion of toxic materials
can cause serious respiratory injury or death.
Filtration may not be adequate in reducing all
inhalation hazards. It remains the employer’s or
user’s responsibility to ensure all emissions
are safe to breath.
1.11 Blasting Media
Always use media specifically manufactured for blasting
and that are compatible with the surface being blasted.
Media produced for other applications may be inconsistent
in size and shape, contain particles that could jam the
metering valve, or cause irregular wear. Always obtain
the safety data sheet (SDS) for the blasting media prior to
blasting and identify material being removed by blasting,
paying particular attention to worker health risks and
presence of any hazardous/toxic substances.
1.11.1 Most common reusable media specifically
manufactured for blasting can be used in Pulsar®
cabinets. The listing of media sizes shown in this
section and in Figure 2 are provided as a guideline only.
The guideline is based on standard 3/16" nozzle and
average conditions with variables such as blast
pressure, media-air mixture, visibility inside the cabinet,
humidity, and reclaimer cleaning-rate.
Several variables that affect the reclaimer cleaning-rate
include blast pressure, media-air mixture, media
friability, contamination of parts being cleaned, damper
setting (static pressure), and dust-collector filter loading
(differential pressure across the dust filter cartridge).
When using larger nozzles, the maximum mesh size of
media will be smaller than those that are normally
recommended. Using media that is finer than those
recommended may decrease visibility and, at some
point, carry over to the dust collector. Media coarser
than those recommended may be too dense for the
reclaimer to recover from the cabinet hopper.
1.11.2 Sand and slag: Sand should NEVER be used
for abrasive blasting because of the respiratory hazards
associated with media containing free silica. Slags are not
recommended because they rapidly break down and are
not recyclable, making them unsuitable for cabinet use.
1.11.3 Silicon carbide, aluminum oxide, and garnet:
These are the most aggressive of the commonly used
media. Aggressive media may be used, but the service
life of any equipment components exposed to them will be
reduced. To avoid unscheduled downtime, periodically
inspect the reclaimer wear plate, exhauster housing and
paddle wheel, blast hose, and nozzle for wear.
When using aggressive media only occasionally, install
an optional aluminum oxide kit. The kit includes rubber
curtains for the cabinet interior and a boron carbide
lined nozzle. Nozzles lined with boron carbide extend
nozzle wear life. When using these media on a regular
basis, use a fully rubber lined reclaimer in addition to the
oxide kit. Rubber reclaimer liners are shown in Section
9.1: Optional Accessories, Figure 40.
1.11.4 Glass bead: Most beads are treated to ensure
free-flow operation, even in environments of moderately
high humidity. Glass beads subjected to excessive
moisture may be reused only after thorough drying and
breaking up of any clumps.
1.11.5 Steel: When the recovery hose diameter is
suitably sized, as shown in Figure 2, steel grit sized
between 80-mesh and 120-mesh and shot sized between
S-110 and S-70 may be used with a 1/4" or smaller nozzle.
Using steel media requires a smaller-diameter
conveying hose, usually reduced one size from
standard. Conveying hose on cabinets using steel media
should have a smooth durable lining. Rubber curtains
should be used to protect the cabinet walls from peening
and rapid wear. For these applications, cabinets can be
ordered with reduced-size flex hose appropriately sized
for steel grit, and with rubber curtains installed. They may
also be field installed later. See Section 9.1: Optional
Accessories.

PULSAR® III-P/III-PE and VI-P/VI-PE PRESSURE CABINETS Page 6
© 2019 CLEMCO INDUSTRIES CORP. www.clemcoindustries.com Manual No. 21527, Rev. I, 02/19
This table offers a guideline to media selection based on standard 3/16" orifice nozzle and average conditions,
such as air pressure, media-air mixture, visibility, contamination of parts being blasted, humidity, media friability,
reclaimer cleaning rate, etc. As a rule, larger nozzles deliver more media, requiring higher performance from the
reclaimer. Larger nozzles decrease the maximum mesh size of media from those recommended. Media that is
finer than those recommended may decrease visibility and carry over to the dust collector. Media coarser than
those recommended may be too dense for the reclaimer to recover from the cabinet hopper.
MEDIA TYPE
RECLAIMER SIZE STEEL GRIT STEEL SHOT GLASS BEAD ALUM. OXIDE FINE-MESH PLASTIC
600 cfm w/5" inlet Do not use Do not use No. 8 to No. 12 54 to 180-mesh See 1.9.6 See 1.9.7
600 cfm w/4" inlet 80 to 120 S-110 to S-70 Do not use 46 to 100-mesh Do not use Do not use
Figure 2
1.11.6 Fine-mesh media: When using media finer than
180-mesh, the reclaimer inlet baffle may need to be
removed. Reclaimers with welded-on tops require
grinding to remove the baffle, and once it is removed, it
cannot be replaced. Refer to Section 7.14 to remove
bolt-on baffle.
1.11.7 Plastic media: Plastic and similar media require
a blast machine with a 60-degree conical bottom. Refer
to Clemco’s Aerolyte brand of cabinet.
1.11.8 Bicarbonate of soda: Bicarbonate of soda is
not recommended for use in Pulsar Cabinets. Bicarb is a
one-use media and will quickly saturate the filter
cartridge(s). Refer to Clemco’s Aerolyte cabinet line for
cabinets that are specifically designed for use with
bicarbonate of soda.
1.12 Compressed-Air Requirements
Compressed Air Consumption *(cfm)
Nozzle Pressure (psi)
size 50 60 70 80
1/8" 11 13 15 17
3/16" 26 30 33 38
1/4" 47 54 61 68
* Figures are approximate and for reference only,
and they may vary for different working conditions.
Several variables, including media flow and nozzle
wear, affect cfm consumption.
Figure 3
1.12.1 The size of the compressor required to operate
the cabinet depends on the size of the nozzle and
blasting pressure. Unless otherwise specified, cabinets
are supplied with a 3/16" orifice nozzle. The table in
Figure 3 shows air consumption of nozzles when new. It
does not show the recommended compressor size. As
nozzles wear, they will consume 70% to 80% more air.
Consult with a compressor supplier for suggested
compressor size based on the air consumption.
1.12.2 The air filter at the blast machine inlet removes
condensed water from the compressed air. The filter
automatically drains when moisture fills the bowl to a
certain level. Its use is especially important in areas of
high humidity or when fine-mesh media are used.
Moisture causes media to clump and inhibits free flow
through the metering valve. If the filter does not remove
enough moisture to keep media dry and flowing, it may
be necessary to install an air dryer or aftercooler in the
air-supply line.
1.13 Electrical Requirements
1.13.1 Electrical requirements depend on the size and
phase of the exhauster motor. NOTE: Full load amps
(FLA) shown below are for the motor only; the lights
draw less than 1 amp. Standard cabinets are supplied
with 1 HP, 120/230V, 1 PH, 60 Hz, wired 120. FLA
120/12, 208/6.6, 230/6.2.
1.13.2 The standard motor is 120-volt, 1-phase, a
power cord is supplied. If the motor is optional 230/460-
volt, 3 PH, there will be a magnetic starter mounted in a
control box. Power from the user's disconnect has to be
wired to it. Additional wiring information is in Section 2.4.
2.0 INSTALLATION
2.1 General Installation Notes
2.1.1 Refer to Figure 1 for the general arrangement.
Select a location where compressed air and electrical
service are available. The cabinet location must comply
with OSHA and local safety codes. Allow for full access
to all doors and service areas and for efficient handling
of large parts.

PULSAR® III-P/III-PE and VI-P/VI-PE PRESSURE CABINETS Page 7
© 2019 CLEMCO INDUSTRIES CORP. www.clemcoindustries.com Manual No. 21527, Rev. I, 02/19
2.2 Connect Compressed-Air Supply Line
WARNING
Failure to observe the following before
connecting the equipment to the compressed-
air source can cause serious injury or death
from the sudden release of compressed air.
• Lockout and tagout the compressed-air supply.
• Bleed the compressed-air supply line.
2.2.1 Apply thread sealant to the male threads of an air
fitting that is compatible with the air-supply hose fitting, as
noted in Section 2.2.2, and install it onto the 1-NPT air
filter located at the blast machine inlet, as shown in
Figure 4. The style of connection shown is for reference
only.
WARNING
Hose disconnection while under pressure can
cause serious injury or death. Use safety lock
pins or safety wire to lock twist-on type air-hose
couplings together and prevent accidental
separation, and also use safety cables to prevent
hose from whipping should separation occur.
Safety lock pins and safety cables are listed in
Section 9.1: Optional Accessories.
WARNING
To avoid the risk of injury from compressed air,
install an isolation valve and bleed-off valve
where the air supply is tapped into the
compressed air system. This enables
depressurization of the compressed-air line
before performing maintenance.
2.2.2 Install an isolation valve at the compressed-air
source to enable depressurization for service. Connect
a 1" ID or larger air line from the air source to the air
filter. A smaller-diameter hose may reduce blasting
efficiency.
2.3 Ground the Cabinet
2.3.1 To prevent static electricity buildup, attach an
external grounded wire from an earth ground to the
grounding lug on the left rear of the power module.
2.4 Connect Electrical Service
WARNING
Shorting electrical components can result in
serious injury or death from electrical shock or
equipment damage. Electrical power must be
locked out and tagged out before performing
any electrical work. All electrical work or any
work done inside a control panel or junction
box must be performed by a qualified
electrician and comply with applicable codes.
2.4.1 Standard single-phase wiring
2.4.1.1 Standard Pulsar cabinets are 120-volt single
phase. Power is supplied by a U-ground plug; plug it into
a 120-volt outlet. No additional wiring is needed; the
wiring schematic shown in Figure 5 is for reference.
WARNING
Do not use electrical adaptors that eliminate the
ground prong on 120-volt plugs. Doing so can
cause electric shock and equipment damage.
Some items removed for clarity
Figure 4
Air-Supply Hose
1" NPT Air Filter
Use safety lock pins to secure twist-on couplings.
Air Fitting
Apply thread sealant to male threads.
Use safety cable to prevent separated hose from whipping.
Once installed, all slack must be removed from the cable.

PULSAR® III-P/III-PE and VI-P/VI-PE PRESSURE CABINETS Page 8
© 2019 CLEMCO INDUSTRIES CORP. www.clemcoindustries.com Manual No. 21527, Rev. I, 02/19
Figure 5
WARNING
Do not use electrical adaptors that eliminate the
ground prong on 120-volt plugs. Doing so can
cause electric shock and equipment damage.
2.4.2 Optional three-phase wiring
All wiring external of the cabinet is provided by the user
to comply with local electrical codes.
A wiring schematic is packed inside the cabinet’s control
panel. After wiring is completed, keep a copy of the
schematic with the manual for future reference and for
electrical replacement parts.
2.4.2.1 If the exhauster motor is optional 3-phase, a
magnetic starter is located in the electrical panel. User
supplied wiring will need to be run from a disconnect to
the panel. As much wiring as possible has been
completed at the factory. The user needs only to provide
power to the motor starter, mounted in the panel.
2.4.2.2 After wiring is completed, observe the warning
below, and check motor rotation. To check rotation, turn
the On-Off switch ON and quickly turn it OFF, causing the
motor to rotate slowly. Look through the slots in the fan
housing on top of the motor where rotation of the fan can
easily be observed. Proper rotation is indicated by the
arrow on the top section (exhauster housing) of the power
module. The fan should rotate clockwise when viewed
from the fan end of the motor. To reverse rotation, change
the wires as noted on the motor plate.
WARNING
Do not look into the reclaimer exhauster outlet
while the paddle wheel is turning. Injury to the
eye or face can occur from objects ejected from
the exhauster.
2.5 Set Air-Inlet Damper – Figure 6
2.5.1 The inlet damper is located on the top of the
cabinet and must be set to match the cabinet dimensions
and reclaimer size. The label on the damper shows the
settings in degrees. The air damper was preset prior to
shipment; confirm the initial setting, as noted below.
Figure 6
2.5.2 Loosen the lock nuts and align the damper
handle to the initial setting of 30 degrees. When
correctly positioned, tighten the lock nuts to maintain the
setting. Refer to Section 5.6 for adjustment procedure.
2.6 Final Assembly
2.6.1 Insert a section of 3/8" tubing into the automatic
drain at the bottom of the compressed-air filter, as
shown in Figure 7, and place the other end into a pail.
When the filter automatically drains, the water will drain
into the pail.
Figure 7
115 VOLT, 1 PH CABINET WIRING
Compressed-Air Filter
Water Pail
3/8" Tubing
Degrees Label
Air-Inlet Damper
Damper Handle
Align handle to degrees, as
noted in Section 2.5.2.

PULSAR® III-P/III-PE and VI-P/VI-PE PRESSURE CABINETS Page 9
© 2019 CLEMCO INDUSTRIES CORP. www.clemcoindustries.com Manual No. 21527, Rev. I, 02/19
2.6.2 Position the foot pedal on the floor at the front of
the cabinet or on the foot shelf on ergonomic models.
2.6.3 A package of five cover lenses is supplied with the
cabinet. To install a cover lens, remove the adhesive
backing and apply the lens to the clean, dry, inner surface
of the view window. Refer to Section 7.4. When the cover
lens becomes pitted or frosted, replace it.
3.0 FIELD INSTALLED ACCESSORIES
3.1 Aluminum Oxide (aggressive media) Kit
3.1.1 An optional aluminum oxide kit is available
factory installed or may be field installed later.
Factory-installed kits consist of black-rubber cabinet
curtains with grommets, curtain hardware, and a boron
carbide nozzle.
Field-installed (or replacement factory installed) kits
consist of black-rubber cabinet curtains (refer to Section
3.2 for curtain installation) a boron carbide nozzle, and
light-lined flex hose. If the existing flex hose is in good
condition, reserve the new hose for future replacement.
3.2 Cabinet Curtains Installation
3.2.1 Match curtains to corresponding walls and door.
3.2.2 Front and rear walls: Position the curtain on
the wall to be protected. Using the curtains as templates,
mark each mounting point through the grommet holes
along the upper edge of the curtain. NOTE: When laying
out the attachment points, the upper edge of the rear
curtain should be below the bottom edge of the air-duct
partition. Remove the curtains and drill a .187" (3/16")
diameter hole at each point marked. Install the curtains
using the fasteners provided (machine screw, 11/16 OD
flat washer, lock washer and nut) at each grommet. The
flat washer is used between the screw head and the
rubber curtain grommet on all curtains.
3.2.3 Doors: Use protectors against the curtains and
outer doors; clamp the door curtains in place. NOTE:
When laying out the attachment points, the upper edges
of the door curtains should be even with the outer edges
of the door’s soundproofing panel. Insert a #10 self-
drilling screw with an 11/16" OD flat washer through the
grommet holes. Use a screw gun with a 5/16" socket to
drill and thread the screws through the door’s inner wall
at each grommet.
3.2.4 Ergo side extensions: Position the curtain on
the wall to be protected. Use the curtain as a template
and mark the top mounting point through the grommet.
Remove the curtain and drill a .187" (3/16") diameter
hole at each point marked. Install the curtains using the
fasteners provided (machine screw, 11/16 OD flat
washer, lock washer and nut) at each grommet. The flat
washer is used between the screw head and the rubber
curtain grommet on all curtains. After hanging the
curtain, mark and drill the cabinet and attach the lower
grommets in like manner.
3.3 Manometer
The optional manometer kit is listed in Section 9.1:
Optional Accessories.
3.3.1 Consistent static pressure is necessary for
precise media separation, as the reclaimer's efficiency is
achieved by a centrifugal balance of air flow, particle
weight, and size. The manometer measures static
pressure. Reclaimer static pressure is set by adjusting the
dust-collector damper. Refer to Section 5.3 to adjust static
pressure. Refer to Section 5.7 for manometer instructions.
3.4 Reclaimer Differential-Pressure Gauge
Monitors reclaimer static pressure ‒ Figure 8
3.4.1 The reclaimer differential pressure gauge
continually measures reclaimer static pressure, similar
to a manometer slack tube but it uses a differential
pressure gauge.
3.4.2 The gauge panel, gauge, filter, and panel fittings
come fully assembled; the bushings, snubber fittings, and
tubing are loose. Mount the panel at a location where it
can be easily monitored. A 10-foot length of tubing is
included with the kit, allowing the panel to be mounted
within 10 feet of the connections. One suggestion is to
mount it on an accessible side of the power module.
3.4.3 Mounting holes are on the left and right sides of
the gauge panel. After selecting the location, match drill
holes and use nuts and cap screws to secure the panel.
Figure 8
3.4.4 Remove the 1/4" pipe plug from the reclaimer
body and install 1/4" x 1/8" bushing and barb fitting, as
shown in Figure 8.
Urethane Tubing
Differential
Pressure Gauge
Remove plug and install
bushing and barb fitting.

PULSAR® III-P/III-PE and VI-P/VI-PE PRESSURE CABINETS Page 10
© 2019 CLEMCO INDUSTRIES CORP. www.clemcoindustries.com Manual No. 21527, Rev. I, 02/19
3.4.5 Push the tubing onto the barb fittings on the
gauge and reclaimer, as shown. Cut the tubing to length.
3.4.6 Refer to the differential-pressure-gauge manual
provided for operation of the gauge.
3.5 Turntable with Workcar and Track
3.5.1 Components of the turntable and track assembly
are shown in Figure 9. The assembly consists of:
Inside track assembly, placed inside the cabinet.
Hinged track extension, attaches to the support table
and swings up to clear the cabinet door.
Track support table, placed outside the cabinet.
Turntable and workcar assembly.
Installation note: The track may be placed on either
side of the cabinet, allowing entry through either the right
side or left side door; the right side is shown in the
illustrations. When installing the inside track, place it so
the stops are opposite the entry door, as shown in Figure 10.
Figure 9
3.5.2 Place the inside track in the cabinet over the
existing grate, as shown in Figure 10.
Figure 10
3.5.3 Position the track support table and extension,
as shown in Figure 11. When the hinged extension is
lowered, the extension tracks must rest on the angled
locating supports welded to the bottom of the inside
tracks, and butt against the inside tracks.
3.5.4 Loosen the leveling-pad lock nuts and raise or
lower the pads, as needed to adjust the height of the
table, to make sure that the inside and outside tracks
are aligned, that the hinged extension rest evenly on the
support angles when the extension is lowered, and that
the table is level.
3.5.5 Raise the track extension, and then open and
close the door to make sure they function correctly.
When certain the table and tracks are aligned and level,
and that the workcar moves smoothly on all tracks,
tighten the leveling-pad lock nuts and anchor the
support table to the floor through the holes in the
leveling pads.
Figure 11
3.6 Dust-Collector Differential-Pressure Gauge –
Figure 12. Monitors differential pressure across the
filter cartridge.
3.6.1 The differential pressure gauge measures
pressure through the filter cartridge. The gauge is the
best way to monitor cleaning efficiency and dust buildup
on the cartridge.
3.6.2 The gauge panel, gauge, filter, and panel
fittings come fully assembled; the bushings, snubber
fittings, and tubing are loose. Mount the panel on the
cabinet or power module at a location where it can be
easily monitored. One suggestion is to mount it on top of
the cabinet at either side of the light assembly, or
choose another convenient location. A 20-foot length of
tubing is included with the kit, allowing the panel to be
mounted within 10 feet of the dust-collector connections.
3.6.3 Mounting holes are on left side and at the
bottom of the gauge panel. After selecting the location,
match drill holes and use nuts and cap screws to secure
Inside Track
Hinged Track Extension
Track Support Table
Turntable and Workcar
Grate
Stops
Entry Door
Leveling Pads (4)
Anchor Holes (4 places)
The Hinged Extension
must rest on the inside
track support angles
when lowered.
Extension
Support Angles

PULSAR® III-P/III-PE and VI-P/VI-PE PRESSURE CABINETS Page 11
© 2019 CLEMCO INDUSTRIES CORP. www.clemcoindustries.com Manual No. 21527, Rev. I, 02/19
Figure 12
the panel. NOTE: Make sure the panel is close enough
to the dust collector for 10 feet of tubing to reach.
3.6.4 Remove 1/4" pipe plugs from the dust collector
body and install 1/4" x 1/8" bushings and snubber
fittings, as shown in Figure 12.
3.6.5 Connect the 1/4" tubing to the snubber fittings
and gauge as shown by removing the fitting’s
compression nut, sliding it over the end of the tubing,
inserting the tubing into the fitting, and tightening the nut
onto the fitting.
3.6.6 Refer to the differential-pressure-gauge manual
provided for operation of the gauge.
3.7 Armrest
3.7.1 Assemble the armrest and mounting brackets,
as shown in Figure 13.
3.7.2 Position the assembly so the armrest is about
even with the bottom of the arm port opening. Mark one
hole location on the front of the cabinet at each
mounting bracket.
3.7.3 Drill a 3/8" hole at both locations and mount the
armrest using 5/16 cap screw, washers, and nuts. Install
the bolts from inside the cabinet to protect the threads from
abrasion, should the armrest need to be removed later.
3.7.4 Match drill the remaining four bracket holes and
install the remaining fasteners.
Figure 13
3.7.5 Loosen the fasteners on the slotted bracket and
raise or lower the armrest to a comfortable position.
5/16 x 1" Cap Screw,
Flat Washer, Lock
Washer, and Nut
3/8 x 1" Cap Screw
and Lock Washer
Armrest
Inline Filter, arrow pointing toward the gauge.
To Hi (+) Port on Gauge.
Tubing from the dirty side of the
collector (lower snubber) connects to
fitting with the inline filter and Hi (+)
port on the differential-pressure gauge.
Upper Snubber
1/4" x 1/8" Bushing
Lower Snubber
Tubing from the clean side of the
collector (upper snubber) connects
to fitting leading to the Lo (-) port
on the differential-pressure gauge.
To Lo (-) Port on Gauge
Upper snubber is clean side of
collector, to Lo (-) port.
Lower snubber is dirty side of
collector, to filter and Hi (+) port.
Differential-Pressure
Gauge
Gauge Panel
Remove pipe plugs and install
bushings and snubber fittings.

PULSAR® III-P/III-PE and VI-P/VI-PE PRESSURE CABINETS Page 12
© 2019 CLEMCO INDUSTRIES CORP. www.clemcoindustries.com Manual No. 21527, Rev. I, 02/19
4.0 OPERATION
4.1 Season Filter Cartridge
NOTICE
Do not pulse a new dust collector or
replacement filter cartridge until the cartridge is
seasoned, per Section 7.9. . Pulsing
unseasoned cartridges can cause premature
cartridge failure and decrease the efficiency of
dust collectors.
4.2 Media Loading
4.2.1 Media capacity: Media capacity of the Pulsar
Pressure Cabinet is approximately 1 cuft. Full capacity is
when media is at the level of the pop-up valve.
Overfilling will result in media carryover to the dust
collector and possibly a blockage in the conveying hose.
4.2.2 Media loading: With the exhauster OFF, add
clean, dry media by pouring it into the reclaimer through
the reclaimer fill door. Do not pour media directly into
the cabinet hopper, as overfilling or blockage may
occur. Overfilling will result in media carryover to the
dust collector and possible blockage in the conveying
hose. Refill only after all media has been recovered from
the cabinet.
4.3 Media Unloading
4.3.1 To empty the cabinet and blast machine of
media, turn ON the exhauster and blow off the cabinet
interior until all media is recovered from the cabinet.
Reduce pressure to 40 psi. Place an empty container,
such as a bucket, on the cabinet grating. Remove the
nozzle and nozzle washer, close the door, close the
choke valve, and press the foot pedal. Direct media flow
into the container. Empty the container when full or
before it is too heavy to handle, and repeat the process
until the machine is empty. Clean the nozzle holder
threads before reinstalling the nozzle washer and
nozzle. If complete purging of media is required, use a
vacuum to remove media residue in the cabinet hopper
and blast machine head.
4.4 Loading and Unloading Parts
4.4.1 Parts must be free of oil, water, grease, or other
contaminants that will clump media, or clog filters.
4.4.2 Load and unload parts through either door.
WARNING
Use solid fixturing to hold heavy parts in place.
Do not remove lift equipment until the part is
adequately supported to prevent movement.
Moving heavy, unsupported parts may cause
them to shift or topple, and cause severe injury.
This is especially important with the use of
turntables.
4.4.3 When blasting small parts or objects having
small pieces that could become dislodged and fall off,
place an appropriately sized screen over the grate (or
under the grate when frequently blasting small parts) to
prevent parts from falling into the hopper.
4.4.4 Close door; the door interlock system will
prevent blasting if either door is open.
4.5 Blasting Operation
W
ARNING
To avoid the inhalation of dust, which can
cause respiratory illness from short-term
ingestion or death from long-term ingestion:
Use the blow-off nozzle to blow media off
parts before opening doors.
After blasting, keep doors closed and
exhauster running until the cabinet is clear
of all airborne dust.
Always close cabinet, reclaimer, and dust-
collector doors before blasting. Keep all
doors closed during blasting.
Always wear blast gloves.
Stop blasting immediately if dust leaks are
detected.
4.5.1 Slowly open the air valve on the air-supply hose
to the cabinet. Check for air leaks on the initial startup
and periodically thereafter.
4.5.2 After the filter cartridge is seasoned, per Section
7.9, refer to Section 5.5 and adjust the pulse pressure
regulator to 60 psi.
4.5.3 Turn ON lights and exhauster. The ON/OFF
toggle switch performs both functions.
4.5.4 Load parts.
4.5.5 Close door; the door interlock system will
prevent blasting if either door is open.

PULSAR® III-P/III-PE and VI-P/VI-PE PRESSURE CABINETS Page 13
© 2019 CLEMCO INDUSTRIES CORP. www.clemcoindustries.com Manual No. 21527, Rev. I, 02/19
4.5.6 Insert hands into gloves.
4.5.7 To blast, firmly grasp the nozzle holder or hose
just behind the nozzle holder, point the nozzle toward
the object to be blasted, and apply pressure to the foot
pedal; blasting will begin almost immediately.
WARNING
Shut the cabinet immediately if dust leaks are
detected from the dust collector or cabinet.
Make sure the dust-collector filter(s) are
correctly seated and not worn or damaged.
Prolonged breathing of any dust can result in
serious lung disease or death. Short-term
ingestion of toxic dust such as lead, poses an
immediate danger to health. Toxicity and health
risks vary with type of media and dust
generated by blasting. Identify all material being
removed by blasting and obtain a safety data
sheet (SDS) for the blast media.
4.5.8 Adjust the pilot pressure regulator to the
required blasting pressure, per Section 5.1. The
regulator is located on the top-left side of the cabinet.
NOTE: Pressure registers on the gauge only while
blasting.
NOTE: When holding parts off the grate, use a solid
conductive backrest to support the part. Without this
assist, especially with longer blasting operations, the
operator will tire easily from resisting blast pressure, and
static electricity could build up in the ungrounded part
and cause static shocks. Whenever possible, avoid
holding small parts that require blasting into the glove.
4.5.9 If an object should fall through the grate, stop
blasting immediately and retrieve it.
NOTICE
To prevent rapid frosting of the view window,
install a view-window cover lens, per Section
7.4, and avoid pointing the blast nozzle toward
the view window
4.6 Operation and Function of the Choke Valve
Figure 14
4.6.1 Always fully open the choke valve while blasting;
open is when the handle is vertical and aligned with the
piping, as shown in Figure 14.
Figure 14
4.6.2 Closing the choke valve while blasting lowers
pressure in the pusher line from the pressure in the
vessel. Closing the valve forces media through the
metering valve to clear minor blockage, such as damp
media, or it is used to rapidly empty the machine to
change media.
NOTICE
Do not blast with choke valve closed or partially
closed. Prolonged blasting with the choke valve
partially closed will accelerate wear on the
metering valve.
4.7 Blasting Technique
4.7.1 Blasting technique is similar to spray painting
technique. Smooth, continuous strokes are usually most
effective. The distance from the part affects size of blast
pattern. Under normal conditions, hold the nozzle
approximately 6" from the surface of the part.
4.8 Stop Blasting
4.8.1 To stop blasting, remove pressure from the foot
pedal. The blast machine will depressurize each time the
foot pedal is released.
4.8.2. The blast machine refills with media stored in
the reclaimer each time the foot pedal is released and
the blast machine depressurizes. Refill takes
approximately 15 seconds when the machine is empty.
4.8.3 Use the blow-off nozzle to blow media off
cleaned parts.
4.8.4 Keep doors closed and exhauster running until
the cabinet is clear of all airborne dust.
Choke Valve
Valve is shown open;
the position of the
handle is aligned with
the piping.

PULSAR® III-P/III-PE and VI-P/VI-PE PRESSURE CABINETS Page 14
© 2019 CLEMCO INDUSTRIES CORP. www.clemcoindustries.com Manual No. 21527, Rev. I, 02/19
4.8.5 Unload parts, shut off the air-supply valve, drain
the air filter and pulse reservoir, and switch off the lights
and exhauster.
4.9 Pulsing (cleaning) Dust-Collector Cartridge
4.9.1 The dust-collector filter cartridge is pulsed each
time the foot pedal is pressed and again when it is
released. Prolonged periods of blasting or dusty
conditions may require the cartridge to be pulsed during
the blasting process, per Section 6.2.6, or upgrade to
the automatic pulse kit. Refer to Section 9.1: Optional
Accessories.
4.10 Shutdown
4.10.1 Shut off the air-supply valve, bleed the air-
supply line, and drain the compressed-air filter and dust-
collector pulse reservoirs.
4.10.2 Switch OFF the lights and exhauster.
5.0 ADJUSTMENTS
5.1 Blasting Pressure (pilot regulator) – Figure 15
5.1.1 The blast-pressure pilot regulator, located on the
top-left side of the cabinet, enables the user to adjust
blasting pressure to suit the application. The suitable
pressure for most purposes is about 80 psi. Lower
pressures may be used for delicate work. Higher
pressure may be required for difficult blasting jobs on
durable substrates, but it will increase media break down.
Optimal production can be achieved only when pressure
is carefully monitored.
Figure 15
5.1.2 When blasting below 40 psi, first pressurize the
blast machine at 40 psi and then turn the pressure to the
required setting before blasting the part. If the initial
pressure is below 40 psi, the pop-up valve may not seal.
5.1.3 Pressure registers on the gauge only while
blasting. While holding the nozzle securely, adjust air
pressure at the pilot regulator located on the top-left side
of the cabinet.
5.1.4 To adjust pressure, unlock the knob by pulling it
out, as shown in Figure 15, and turn it clockwise to
increase pressure or counterclockwise to decrease
pressure. Once operating pressure is set, push the knob
in to lock it and maintain the setting.
5.2 Media Metering (media flow) – Figure 16
These instructions are for a standard cabinet with
Sentinel Metering Valve. Optional metering valves
may function differently, but the process is similar.
5.2.1 Adjust media flow using the metering valve
located at the bottom of the blast machine. The valve is
closed when the handle is fully to the right. To adjust,
begin with the valve closed, press the foot pedal, and
have someone slowly move the handle to the left to
increase media flow. Allow time for the flow to stabilize
before further adjusting. The valve is fully open when the
handle is at the full-left position. The optimum flow rate
depends on the type and size of media and blasting
pressure, and can best be determined by experience.
Use as little media as possible to do the job while
maintaining the best cleaning rate. Generally, with the
correct mixture, media can be seen as light discoloration
as it exits the nozzle.
OPEN
CLOSE
Figure 16
Control Handle
Some items are
removed for clarity.
When viewed from the knob end,
turn clockwise to increase pressure;
turn counterclockwise to decrease pressure.
Adjustment Knob
Move handle to
the left to increase
media flow.
Move handle to the
right to decrease
media flow.
Blast-Pressure Pilot Regulator
Located on top-left-side of cabinet.
Push knob in to lock it.
Pull knob out to unlock
and ad
j
ust
p
ressure.

PULSAR® III-P/III-PE and VI-P/VI-PE PRESSURE CABINETS Page 15
© 2019 CLEMCO INDUSTRIES CORP. www.clemcoindustries.com Manual No. 21527, Rev. I, 02/19
5.3 Reclaimer Static Pressure (outlet damper)
5.3.1 Correct static pressure varies with size of
reclaimer and size, weight, and type of media.
5.3.2 Adjust static pressure by opening or closing the
outlet damper located above the reclaimer on the
underside of the power module top; refer to Figure 17. If
the damper is not opened far enough, the reclaimer will
not remove fines, resulting in dusty media and poor
visibility, or will not convey media, causing media
buildup in the hose between the cabinet hopper and
reclaimer. If the damper is opened too far, it may cause
carryover (usable media carried into the dust collector)
and result in excessive media consumption. Open the
damper only as far as necessary to achieve a balance of
maximum dust removal without media carryover.
Figure 17
5.3.3 A manometer is useful when adjusting and
monitoring static pressure. The manometer kit is listed in
Section 9.1: Optional Accessories. Refer to Section 5.7
for manometer operation. The following are static-
pressure starting points for given media. Static pressure
may need to be lower with finer media, higher with
coarser media. Run the media through several blast
cycles, allowing the reclaimer to function with these
settings. Inspect the media in the reclaimer and fines in
the dust collector, as noted in Paragraph 5.3.2. Continue
adjusting static pressure until optimum dust and fines
removal without carryover is attained.
Glass Bead No. 8 to 12 ................................. 3" – 3-1/2"
Aluminum Oxide 54-Mesh to 80-Mesh ................ 4" – 5"
Aluminum oxide 80-Mesh to 180-Mesh ............... 3" – 4"
* Steel Grit 80-Mesh to 120-Mesh ....................... 6" – 7"
* Steel Shot S-110 to S-70 .................................. 6" – 7"
* Refer to Section 1.11 for media limitations
5.3.4 As dust accumulates on the outer surface of the
cartridge, static pressure drops, requiring additional
pulsing of the cartridge, as described in Section 6.2.6, or
an increase in pulse pressure, per Section 5.5. When
pulsing no longer maintains the necessary static
pressure, readjust the damper.
5.4 Door Interlocks – Figure 18
WARNING
Never attempt to override the interlock system.
Doing so can result in injury from unexpected
blasting.
5.4.1 The door interlocks disable the blasting control
circuit when the doors are open. To enable blasting, the
door-interlock switches must be engaged when the doors
are closed. The interlocks are set at the factory and do not
normally require field adjustment unless parts are replaced.
When adjustment is required, proceed as follows:
5.4.2 Close cabinet doors.
5.4.3 Loosen the actuator bracket screws and
adjusting screw nut. Move the actuator bracket up or
down, and the adjusting screw sideways, to center the
adjusting screw on the over-travel stop. Tighten the
bracket screws.
Figure 18
5.4.4 Turn the adjusting screw in or out as required to
engage the switch without applying excessive pressure
on it. Tighten the adjusting screw nuts.
5.4.5 Test the operation with the doors open and then
closed. Negative pressure inside the cabinet may cause
Loosen nuts and slide damper
to adjust opening. Tighten nuts
to maintain the setting.
Outlet Damper
Screen
Cabinet Doo
r
Detent Sleeve
Over-Travel Stop
Loosen the bracket screws and
move the bracket up or down to
center the adjusting screw on the
over-travel stop.
Actuator Adjusting Bracket
Bracket Screws
A
djust the screw to push the
valve stem (over-travel stop)
in when door is closed.
Adjusting Screw
Loosen nut and move adjusting
screw sideways to center the
screw on the over-travel stop.
Adjusting Screw Nut

PULSAR® III-P/III-PE and VI-P/VI-PE PRESSURE CABINETS Page 16
© 2019 CLEMCO INDUSTRIES CORP. www.clemcoindustries.com Manual No. 21527, Rev. I, 02/19
the doors to flex inward. Tests should be performed with
the exhauster running. Point the nozzle away from the
door during the tests and open the door only enough to
disengage the interlock switch. The interlocks should
stop the blasting when either door is open and permit
blasting when the doors are closed.
5.5 Pulse Pressure – Figure 19
NOTICE
Do not pulse new dust collectors or
replacement cartridges until the cartridge is
properly seasoned. Refer to Section 7.9.
Pulsing unseasoned cartridges can cause
premature cartridge failure or decrease the
efficiency of dust collector.
5.5.1 Adjust pulse pressure using the regulator
mounted on the blast machine piping, as shown in
Figure 19. Begin pulse at 60 psi. To adjust pressure, pull
the knob to unlock it, as shown in Figure 19, and then
turn clockwise to increase pressure or counterclockwise
to decrease pressure. Once operating pressure is set,
push the knob to lock it and maintain the setting.
Figure 19
5.5.2 As the filter cartridge cakes with dust, it may be
necessary to pulse between blasting, per Section 6.2.6.
5.5.3 When pulsing alone does not adequately clean
the cartridge, increase pulse pressure in 5-psi increments
until the maximum of 90 psi is reached. As dust cakes on
the cartridge, the differential pressure increases. Using a
gauge to measure the differential pressure is a good
way to tell if the cartridge is heavily caked.
5.5.4 When the maximum pulse pressure of 90 psi is
attained, and additional pulsing as described in Section
6.2.6 does not increase visibility or decrease differential
pressure, replace the cartridge, per Section 7.8.
5.6 Cabinet Air-Inlet Damper
5.6.1 Once the damper is initially set, per Section 2.5,
it seldom requires readjustment. The initial setting
produces approximately 1/2" to 3/4" of static pressure
within the cabinet. Do not confuse cabinet static
pressure with reclaimer static pressure, which is
controlled by the outlet damper, as noted in Section
5.3. Reclaimer pressure must be set before cabinet
pressure.
5.6.2 Using a manometer (as noted in Section 5.7 and
listed in Section 9.1) is the most accurate method of
monitoring and adjusting cabinet pressure. Following the
instructions packed with the manometer, start the
exhauster and insert the needle into a glove, and adjust
pressure using the inlet damper. Open the damper
farther to decrease static pressure or close it farther to
increase pressure.
5.6.3 If a manometer is not available, use the gloves
as an indicator. With the exhauster ON, the gloves
should be inflated, but not elevated off the grate.
5.7 Optional Manometer
NOTE: These instructions show several methods of taking
static-pressure readings (negative pressure) on Pulsar
reclaimers by using a flexible-tube manometer. Use the
method best suited for the application. The instructions
explain the processes for taking periodic readings and
show how to permanently install the manometer for taking
frequent readings. Permanent fittings should be installed
when the manometer installation is permanent. Use
silicone sealer or other sealant to seal around the fitting to
prevent leaks. The fitting should be capable of being
capped when the manometer tube is removed. This will
prevent leaks that alter the reclaimer’s separation
efficiency. Taking readings at different locations could
produce different readings. Static-pressure readings at the
door are generally 0.5" to 1" lower than those taken above
the reclaimer. The readings are reference points, so
readings should be taken using the same method each
time a reading is taken.
5.7.1 Refer to the instructions packed with the
manometer for preparing and operating the manometer.
5.7.2 Connect one end of the 3/16" ID tubing to one of
the tubing connectors (elbow) at the top of the
manometer by pushing it over the barbed adaptor.
5.7.3 Open both manometer valves (elbows), per the
instructions with the manometer.
5.7.4 Magnets on the manometer hold it in position on
the reclaimer body or dust-collector body. The
Adjustment Knob
Push knob in to lock.
Pull knob out to unlock
and adjust pressure.
Pulse Pressure Regulator
Blast Machine Piping

PULSAR® III-P/III-PE and VI-P/VI-PE PRESSURE CABINETS Page 17
© 2019 CLEMCO INDUSTRIES CORP. www.clemcoindustries.com Manual No. 21527, Rev. I, 02/19
manometer must be vertical so the fluid is level on both
sides.
5.7.5 Adjust the slide rule to align the zero with the
fluid level. Refer to Figure 21.
5.7.6 Needle placement: Figure 20 shows the
manometer setup for taking both periodic and frequent
static-pressure readings.
Figure 20
5.7.6.1 To take frequent readings: Permanently install
the manometer for taking frequent readings. Remove the
1/4" NPT plug from the coupling on the reclaimer body
and install a fitting with a 1/8" hose barb. Use thread
sealer to prevent leaks. The fitting should be capable of
being capped when the manometer tube is removed.
Capping the fitting will prevent leaks that alter the
reclaimer’s separation efficiency.
5.7.6.2 To take occasional readings: Leave the
needle protector on the needle and insert the needle into
the unused end of the tubing. The ends of the tubing
must fit tight on the manometer and needle; leaks will
give inaccurate readings. Open the reclaimer fill door,
remove the needle protector, and place the needle so
the point is inside the door opening. Carefully close the
door on the needle. The side of the needle will embed
into the rubber door gasket, creating an airtight seal.
5.7.7 Open cabinet doors and turn the exhauster ON.
The negative (static) pressure will move fluid in the tube.
NOTE: Readings must be taken with the cabinet
doors open and with the exhauster running.
5.7.8 To find the static pressure, add the number of
inches the fluid travels up one column to the inches the
fluid travels down the other column. Refer to the
example in Figure 21.
Figure 21
5.7.9 After taking the readings, replace the needle
protector. Close the manometer valves and store the
manometer in the original container in a clean area.
NOTE: If the manometer installation is permanent, the
manometer may remain on the reclaimer body after the
valves are closed.
5.8 Foot Shelf (Ergonomic models only)
5.8.1 Raise the shelf to remove pressure from the
locating pins and remove the pins. Adjust the shelf
height and insert the pins.
The manometer must be vertical
when taking pressure readings.
Refer to Paragraph 5.7.6.2.
When taking occasional
readings, position the
needle so the point is
inside the door opening.
Carefully close the door
on the needle.
With the exhauster OFF,
slide the rule to align the
zero with the fluid level.
Refer to Paragraph 5.7.6.1.
For taking frequent readings,
remove plug and install a
permanent fitting in the
coupling, as shown.
To obtain the pressure reading: With the
exhauster ON, add the number of
inches the fluid travels up the column to
the inches the fluid travels down the
other column. The total is the static-
pressure reading.
Reclaimers are for reference and
may differ from those shown.
Reclaimer Fill Doo
r
In the example shown, fluid traveled up
the right column 1-3/4"
and down the left column 1-3/4".
Static pressure is determined by adding
the columns together. In the example,
the static pressure is 3-1/2".

PULSAR® III-P/III-PE and VI-P/VI-PE PRESSURE CABINETS Page 18
© 2019 CLEMCO INDUSTRIES CORP. www.clemcoindustries.com Manual No. 21527, Rev. I, 02/19
6.0 PREVENTIVE MAINTENANCE
WARNING
Failure to wear an approved respirator and
personal protection when servicing dust-laden
areas of the cabinet and dust collector, as well as
when emptying the container, could result in lung
disease, serious skin or eye irritation, or other
health issues. Toxicity and health risk vary with
type of media and dust generated by blasting.
The respirator must be approved for the type of
dust generated. Identify all material being
removed by blasting and obtain a safety data
sheet (SDS) for the blast media.
To avoid unscheduled downtime and to improve safety,
establish an inspection schedule. Inspect all parts
subjected to media contact, including the nozzle, blast
hose, flex hose, wear plate, and all items covered in this
section. Adjust frequency of inspections as needed,
based on the following:
Usage: Frequently used cabinet require more
maintenance and inspections than those
occasionally used.
Type of media: Aggressive media wears parts
faster than nonaggressive media.
Condition of parts being blasted: Heavily
contaminated parts require more maintenance to
the cabinet’s media recovery system and dust
collector.
Friability of media: Media that rapidly breaks
down require more maintenance to the cabinet’s
media recovery system and dust collector.
6.1 Daily Inspection and Maintenance Before
Blasting with Air OFF
6.1.1. Check media level: Check media level through
the reclaimer door and refill as necessary, per Section
4.2.
6.1.2 Inspect reclaimer debris screen and door
gasket: Check reclaimer debris screen for debris. The
screen is accessible through the reclaimer door. With
the exhauster OFF, remove the screen and empty it
daily and when loading media. Empty the screen more
often if part blasted causes excessive debris. Do not
operate the machine without the screen in place;
oversized byproduct from blasting could plug the nozzle.
While the door is open, inspect the door gasket for wear
or damage. Replace the gasket at the first sign of wear.
6.1.3 Drain compressed-air filter: Empty the drain
pail at least once a day, and more often if needed. Moist
air inhibits the flow of media. Drain the air line and
receiver tank regularly. If the filter does not remove
enough moisture to keep media dry and flowing, it may
be necessary to install an air dryer or aftercooler in the
compressed-air supply line.
6.1.4 Inspect couplings: Make sure couplings are
secure and lock pins and that safety cables are in place.
6.1.5 Inspect dust container: Empty the dust
container regularly. Start by checking the container at
least daily and when adding media, then adjust
frequency based on usage, contamination, and friability
of the media.
1. Turn off the exhauster and unlatch the lid lock ring from
the dust container, as shown in Figure 22.
2. Pry off the lid from the container (the lid's flexible inlet
hose allows easy removal) and remove the container.
Figure 22
3. Tie off or otherwise seal the top of the liner and
remove it from the container. Dispose of the sealed liner
into a suitable disposal receptacle.
NOTE: Blasting media is usually nontoxic; however,
some materials being removed by the blast process
may be toxic. Obtain SDS sheets for the media and
identify all material removed by the blast process.
Check with proper authorities for disposal
restrictions.
4. Place a new liner inside the container and drape it
over the top edge. Reattach the container to the lid and
latch the lock ring, making sure the lid and clamp are
secure. Replacement liners are shown in Section 9.10.
Drum Liner
Latch Catch
Swing the catch
up to unlock the
lock-ring latch.
Latch
Pull the latch away
from the ring and
remove the ring.

PULSAR® III-P/III-PE and VI-P/VI-PE PRESSURE CABINETS Page 19
© 2019 CLEMCO INDUSTRIES CORP. www.clemcoindustries.com Manual No. 21527, Rev. I, 02/19
6.2 Daily Inspection During Blasting – Have
Someone Do the Following:
6.2.1 Inspect couplings and blast hose: Inspect
blast-hose couplings and coupling gaskets for air leaks.
WARNING
Air leaks around couplings and nozzle holders
indicate worn or loose-fitting parts. Nozzle
holders and couplings that do not fit tightly on
hose, as well as nozzles that do not fit tightly in
nozzle holders, can disconnect while under
pressure. Impact from objects (nozzles,
couplings, hoses, or media) disconnected by
pressure during operation can cause severe
injury.
6.2.2 Inspect blast machine for air leaks: Check the
blast machine for air leaks. If leaks are found around the
pop-up valve, inspection door, or pipe fittings at the
bottom of the cone, stop blasting immediately and repair
or replace worn parts.
NOTICE
If leaks are allowed to continue, abrasive
erosion can cause extensive or irreparable
damage to the blast machine.
6.2.3 Inspect cabinet for dust leaks: During
operation, inspect cabinet door seals for media leaks.
Dust leaking from the inlet damper or other places on
the cabinet indicates saturated filter cartridge. Refer to
Section 6.2.6 for additional pulsing.
6.2.4 Drain pulse reservoir: Open the petcock to
drain the pulse reservoir at the end of each shift. Refer to
Figure 23.
Figure 23
6.2.5 Check exhaust air for dust: Dust discharge at
the outlet indicates a leaking or damaged filter cartridge.
Check immediately. Note that a small amount of dust
egress is normal for a short time before a new cartridge is
seasoned.
6.2.6 Additional cartridge pulsing: The cartridge is
pulsed each time the foot pedal is pressed or released.
Additional pulsing should be performed per the following
instructions every eight hours, or more often under dusty
conditions, to prevent clogging of the cartridge.
1. Turn OFF exhauster.
2. Hold the nozzle holder and rapidly press and release
the foot pedal three times. Activating the pedal more
than three times may cause dust to escape from the
enclosure.
3. Start the exhauster and let it run until all airborne dust
is cleared from the cabinet.
4. Repeat the process several times.
6.3 Weekly Inspection and Maintenance Before
Blasting with Air OFF
6.3.1 Inspect view-window cover lens: Inspect
view-window cover lens. Replace as needed, per
Section 7.4.
6.3.2 Inspect gloves: Inspect gloves for wear. The
first sign of deterioration may be excessive static
shocks. Replace as needed, per Section 7.1.
6.3.3 Inspect nozzle: Remove the nozzle and inspect
nozzle for wear. Replace the nozzle when the orifice
diameter is worn 1/16” larger than original size. Before
replacing the nozzle, inspect the nozzle washer. Make
sure the nozzle washer is in good condition, not worn or
otherwise damaged, and in place before reattaching the
nozzle.
WARNING
The threads on the nozzle and nozzle holder
must be inspected each time the nozzle is
secured to the holder. A loose-fitting nozzle
may eject under pressure and cause severe
injury. Check the threads for wear and make
sure the nozzle holder securely holds the
nozzle. The nozzle washer must also be
inspected for wear. When nozzle washers are
worn or missing, abrasive can erode nozzle
threads.
Drain
Pulse Reservoir
This manual suits for next models
3
Table of contents
Other Clemco Power Tools manuals
Popular Power Tools manuals by other brands
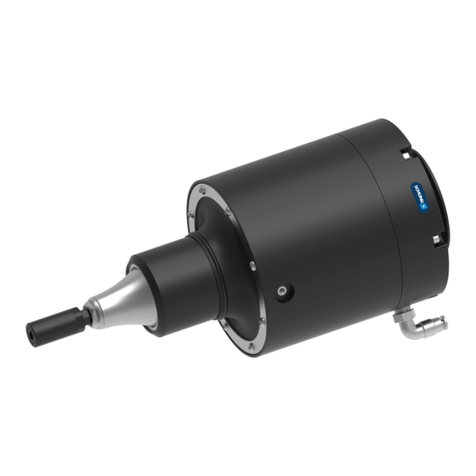
SCHUNK
SCHUNK CRT Assembly and operating manual

SUHNER ABRASIVE
SUHNER ABRASIVE WI 10 Technical document

Greenlee
Greenlee 805 instruction manual

SUHNER ABRASIVE
SUHNER ABRASIVE SP 500 Hook Technical document
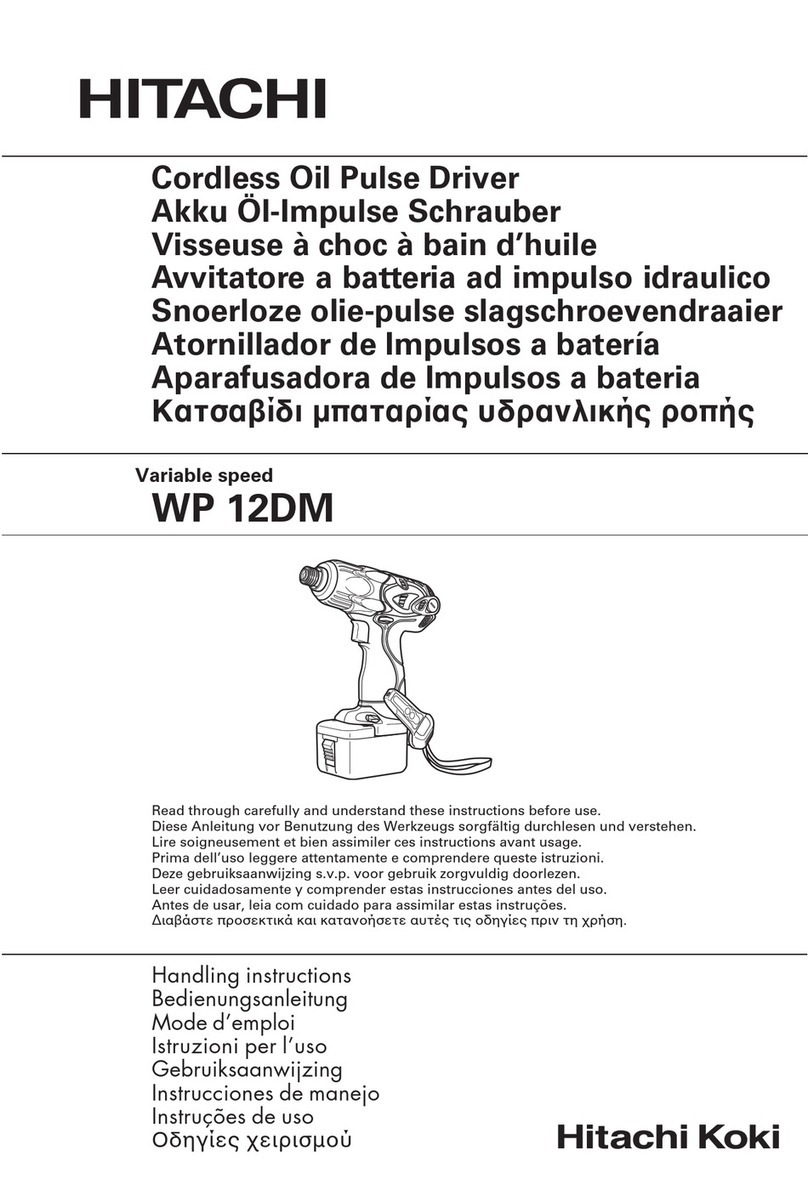
Hitachi
Hitachi WP 12DM Handling instructions
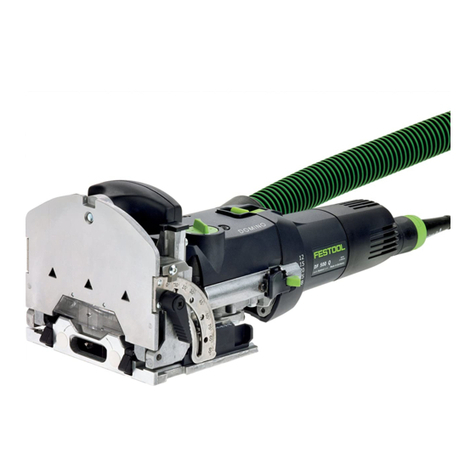
Festool
Festool Domino DF 500 Q Original operating manual