CLIVET WDAT-ik4 Reference manual

R513A
MANUAL
FORINSTALLATION,
USEANDMAINTENANCE
WDAT-ik4
120.1 - 580.2
MF500002‐0011/20

2
The data contained in this manual is not binding and may be changed by the manufacturer without prior
notice. Reproduction, even partial, is FORBIDDEN. © Clivet S.p.A. - Feltre (BL) - Italia
Dear Customer,
We congratulate you on choosing these product
Clivet has been working for years to oer systems able to assure the maximum comfort for
a long time with highly-reliable, ecient, high-quality and safe solutions.
The target of the company is to oer advanced systems, that assure the best comfort and
reduce energy consumption as well as the installation and maintenance costs for the entire
life-cycle of the system.
With this manual, we want to give you information that are useful for all phases: from
reception, installation and use to disposal - so that such an advanced system can provide
the best performances during installation and use.
Best regards and have a good read.
CLIVET Spa

3
Safety considerations 4
Before installation 7
Selecting the installation site 9
Water connections 11
Electrical connections 17
Start-up 24
Control 34
Maintenance 42
1
2
3
4
5
6
7
8
9 Antivibration mounts 49
10 Refrigerant leak detector 54
11 Decommissioning 55
12 Residual risks 56
13 Dimensional drawings 58
14 Operating range 72

4
1 SAFETY CONSIDERATIONS
Manual
The manual provides correct unit installation, use and
maintenance.
It is advisable to read it carefully so you will save time during
operations.
Follow the written indications so you will not cause damages to
things and injuries people.
Preliminaries
Only qualified personnel can operate on the unit, as required by
the regulation in force.
Risk situations
The unit has been designed and created to prevent injures to
people.
During designing it is not possible to plane and operate on all
risk situation.
Read carefully “Residual risk” section where all situation which
may cause damages to things and injuries to people are
reported.
Installation, starting, maintenance and repair required specific
knowledge; if they are carried out by inexperienced personnel,
they may cause damages to things and injuries people.
Intended use
Use the unit only:
cooling water or a water and glycol mix for air-conditioning
keep to the limits foreseen in the technical schedule and in
this manual
The manufacturer accepts no responsibility if the equipment is
used for any purpose other than the intended use.
Installation
Outdoor installation
The positioning, hydraulic system, refrigerating, electrics and the
ducting of the air must be determined by the system designer in
accordance with local regulations in force.
Follow local safety regulations.
Verify that the electrical line characteristics are in compliance
with data quotes on the unit serial number label.
Maintenance
Plan periodic inspection and maintenance in order to avoid or
reduce repairing costs.
Turn the unit off before any operation.
Pay particular attention to:
warnings / prohibitions / danger
indicating particularly important
operations or information, operations
that cannot be done, which compromise
the functionality of the unit or which
may cause damage to things or
persons.
Outdoor installation

5
Modification
All unit modifications will end the warranty coverage and the
manufacturer responsibility.
Breakdown/Malfunction
Disable the unit immediately in case of breakdown or malfunction.
Contact a certified service agent.
Use original spares parts only.
Using the unit in case of breakdown or malfunction:
voids the warranty
it may compromise the safety of the unit
it may increase time and repair costs
User training
The installer has to train the user on:
start-up/shutdown
set points change
standby mode
maintenance
what to do / what not to do in case of breakdown.
Data update
Continual product improvements may imply manual data changes.
Visit manufacturer web site for updated data.
Indications for the User
Keep this manual with the wiring diagram in an accessible place
for the operator.
Note the unit data label so you can provide them to the
assistance centre in case of intervention (see “Unit identification”
section).
Provide a unit notebook that allows any interventions carried out
on the unit to be noted and tracked making it easier to suitably
note the various interventions and aids the search for any
breakdowns.
In case of breakdown or malfunction
Immediately deactivate the unit
Contact a service centre authorized by the manufacturer
1 SAFETY CONSIDERATIONS

6
The installer must train the user, particularly on:
Start-up/shutdown
Set points change
Standby mode
Maintenance
What to do / what not to do in case of breakdown
Unit identification
The serial number label is positioned on the unit and allows to
indentify all the unit features.
The matriculation plate shows the indications foreseen by the
standards, in particular:
unit type
serial number (12 characters)
year of manufacture
wiring diagram number
electrical data
type of refrigerant
refrigerant charge
manufacturer logo and address
The matriculation plate must never be removed.
It contains fluorinated greenhouse gases.
Serial number
It identifies uniquely each unit.
Must be quoted when ordering spare parts.
Assistance request
Note data from the serial number label and write them in the
chart on side, so you will find them easily when needed.
1 SAFETY CONSIDERATIONS
Series
Size
Serial number
Year of manufacture
Number of electrical wiring diagram
Physical characteristics of the R513A refrigerant
Safety class (ISO 817) A1
Boiling point -29,2 °C
GWP 631

7
Reception
You have to check before accepting the delivery:
That the unit hasn’t been damaged during transport
That the materials delivered correspond with that indicated on
the transport document comparing the data with the
identification label positioned on the packaging.
In case of damage or anomaly:
write down on the transport document the damage you found
and quote this sentence: “Conditional acceptance clear
evidence of deficiencies/damages during transport”
wontact by fax and registered mail with advice of receipt to
supplier and the carrier.
NOTE
Any disputes must be made within 8 days from the date of
the delivery. Complaints after this period are invalid .
Storage
Respect the indications on the outside of the pack.
In particolar:
minimum ambient temperature –10°C
(possible components damages)
maximum ambient temperature +55°C
(possible safety valve opening)
maximum relative humidity 95%
(possible damages to electrical components
NOTE
The unit may not be tilted more than 15° during transport.
NOTE
Removal of packaging
Be careful not to damage the unit.
Recycle and dispose of the packaging material in compliance with
local regulations.
2 BEFORE INSTALLATION

8
2 BEFORE INSTALLATION
Handling
Check that all handling equipment complies with local safety
regulations (cran, forklifts, ropes, hooks, etc.).
Provide personnel with personal protective equipment suitable
for the situation, such as helmet, gloves, accident-prevention
shoes, etc.
Observe all safety procedures in order to guarantee the
safety of the personnel present and the of material.
Verify unit weight and handling equipment lifting capacity.
Identify critical points during handling (disconnected routes,
flights, steps, doors).
Suitably protect the unit to prevent damage.
Lifting with balance
Lifting with spacer bar
Align the barycenter to the lifting point
Gradually bring the lifting belts under tension, making sure
they are positioned correctly.
Before starting the handling, make sure that the unit is
stable.

9
3 SELECTING THE INSTALLATION SITE
Positioning
Installation must be in accordance with local regulations. If
they do not exist, follow EN378
.
During positioning consider these elements:
customer approval
unit weight and bearing point capacity
safe accessible position
functional spaces
spaces for the air intake/exhaust
electrical connections
max. distance allowed by the electrical connections
water connections
Functional spaces
Functional spaces are designed to:
guarantee good unit operation
carry out maintenance operations
protect authorized operators and exposed people
Respect all functional spaces indicated in the TECHNICAL
INFORMATION section.
Positioning
Units are designed to be installed:
EXTERNAL
in fixed positions
Put the unit in a position where any leaking gas cannot enter
buildings or stagnate in closed areas. In the latter case,
observe the rules for machinery rooms (ventilation, leak
detection, etc.).
Installation standards:
install the unit raised from the ground
bearing points aligned and leveled
discharged condensation water must not cause harm/danger
to people and property
the accumulation of snow must not cause clogging of the
coils
avoid installations in places subject to flooding
Limit vibration transmission:
use anti-vibration devices or neoprene strips on the unit
support points
install flexible joints on the hydraulic connections
Protect the unit with suitable fence in order to avoid access to
unauthorised personnel (children, vandals, etc.)
A correct circulation of the air is mandatory to guarantee the
good unit operating..
The unit must be level.

10
3 SELECTING THE INSTALLATION SITE
Avoid therefore:
obstacles to the airflow
exchange difficulties
leaves or other foreign bodies that can obstruct the exchange
batteries
winds that hinder or favour the airflow
heat or pollution sources close to the unit (chimneys,
extractors etc)
stratification (cold air that stagnates at the bottom)
recirculation (expelled air that is sucked in again)
positioning below the level of the threshold, close to very high
walls, attics or in angles that could give rise to stratification
or recirculation phenomenons.
Ignoring the previous indications could:
energy efficiency decrease
blocchi per ALTA PRESSIONE (in estate) o BASSA PRESSIONE
(in inverno).
Pressure relief valve gas side
The installer is responsible for evaluating the opportunity of
installing drain pipes in compliance with the local regulations in
force (EN 378).
If ducted, the valves must be sized according to EN13136 .

11
4 WATER CONNECTIONS
Water component for corrosion limit on
Copper
PH 7,5 ÷ 9,0
SO4-- < 100
HCO3-/ SO4-- > 1
Total Hardness 8 ÷ 15 °f
Cl- < 50 ppm
PO4 3- < 2,0 ppm
NH3< 0,5 ppm
Free Chlorine < 0,5 ppm
Fe3+< 0,5 ppm
Mn++ < 0,05 ppm
CO2< 50 ppm
H2S < 50 ppb
Temperature < 65 °C
Oxygen content < 0,1 ppm
Sand
10 mg/L
0.1 to 0.7mm max
diameter
Ferrite hydroxide
Fe3O4 (black)
Dose < 7.5 mg/L 50%
of mass
with diameter < 10
µm
Iron oxide Fe2O3
(red)
Dose < 7.5mg/L
Diameter < 1 µm
The warranty does not cover
damages caused by limestone
formations, deposits and impurities
from the water supply and/or from
failure to clean the systems.
Hydraulic system
The pipes must be designed and manufactured to limit pressure
drops as much as possible, i.e. optimise performance of the
system. Keep the following to a minimum:
overall length
number of bends
number of vertical changes of direction
If the unit is to replace an existing unit, clean the system
thoroughly: see Sequence of operations on the following pages
Water quality
The water quality can be checked by qualified personnel.
Water with inadequate characteristics can cause:
pressure drop increase
energy efficiency decrease
corrosive symptom increase
Water features:
within the limits indicated by table
Provide a water treatment system if values fall outside the limits.
Cleanliness
Before connecting the water to the unit, clean the system
thoroughly with specific products effective to remove residues or
impurities that may affect functioning. Existing systems must be
free from sludge and contaminants and protected against build-
ups.
New systems
In case of new installations, it is essential to wash the entire
installation (with the circulator uninstalled) before commissioning
the central installation. This removes residues of the installation
process (welding, waste, joint products...). The system must then
be filled with clean high-quality tap water.
Existing systems
If a new unit is installed on an existing system, the system must
be rinsed to avoid the presence of particles, sludge and waste.
The system must be drained before installing the new unit. Dirt
can be removed only with a suitable water flow. Each section
must then be washed separately. Particular attention must also be
paid to “blind spots” where a lot of dirt can accumulate due to
the reduced water flow. The system must then be filled with clean
high-quality tap water. If, after rinsing, the quality of the water is
still unsuitable, a few measures must be taken to avoid problems.
An option to remove pollutants is to install a filter.

12
4 WATER CONNECTIONS
The unit must always be protected
from freeze.
Otherwise irreversible damage may
occur.
Risk of freeze
If the unit or the relative water connections can be subject to
temperatures close to 0°C:
Mix water with ethylene glycol, or
Safeguard the pipes with heating cables placed under the
insulation, or
Empty the system in cases of long non-use
Anti-freeze solutions
Consider that the use of anti-freeze solution determines an
increase in a pressure drop.
Make sure that the glycol type utilized is inhibited (not
corrosive) and compatible with the hydraulic circuit components.
Do not use different glicol mixture (i.e. ethylic with propylene).
% ETHYLENE GLYCOL BY WEIGHT 5% 10% 15% 20% 25% 30% 35% 40% 45% 50%
Freezing temperature °C -2 -3.9 -6.5 -8.9 -11.8 -15.6 -19.0 -23.4 -27.8 -32.7
Safety temperature °C 3 1 -1 -4 -6 -10 -14 -19 -23.8 -29.4

13
4 WATER CONNECTIONS
Minimum water flow
Maximum water flow
Water flow-rate
The design water flow-rate must be:
inside the exchanger operating limits (see the TECHNICAL
INFORMATION chapter)
guaranteed also with variable system conditions (for example,
in systems where some circuits are bypassed in particular
situations)
If the system capacity is below the minimum flow, bypass the
system as indicated in the diagram.
If the system capacity exceeds the miaximum flow, bypass the
system as indicated in the diagram
Minimum system water content
For a proper functioning of the unit a minimum water content
has to the provided to the system, using the formula:
Minimum water content [l]
= 5 x kWf (air conditioning application)
= 10 x kWf (application with low outdoor temperature or low
loads required)
kWf = Nominal cooling capacity unit
Volume calculated does not consider internal heat exchanger
(evaporator) water content.
Water filter
Must be installed immediately in the water input of the unit,
in a position that is easily accessible for cleaning.
The filter never should be removed, this operation invalidates
the guaranty.
Recommended filter with N 25 mesh (French numbering) 0,87mm
size mesh
Size mesh = 0,87mm

14
4 WATER CONNECTIONS
Flow Switch
The flow switch must be present to ensure shutdown of the unit if
water is not circulating.
It has to be installed in a duct rectilinear part, not in proximity of
curves that cause turbulences.
Operations sequence
Before starting the unit pump:
1 Close all vents in the high points of the unit’s water circuit.
2 Close all drain shut-off valves in the low points of the unit’s
water circuit
Exchangers
Pumps
collectors
storage tanks
Thoroughly wash the system with clean water:
use the bypass to exclude the exchanger from the flow
(diagram on previous page) fill and drain the system several
times.
Apply additives to prevent corrosion, fouling, formation of mud
and algae.
Fill the system
do not use the unit pump
Conduct a leak test.
Isolate the pipes to avoid heat dispersions and formation of
condensate.
Leave various service points free (wells, vents, etc).
Neglecting to wash will lead to the filter having to be cleaned
many times and at worst may damage the exchangers and
compressors.
Admissible water flow-rate
Minimum (Qmin) and maximum (Qmax) admissible water flow for
the unit to operate correctly.
Flow switch
size 120.1 160.1 200.1 240.1 250.2 280.2 320.2 340.2 360.2 400.2 440.2 480.2 540.2 580.2
Qmin
l/s
7.0 9.9 12.0 15.4 15.4 16.9 19.9 23.6 26.4 24.8 31.9 31.9 31.2 42.2
Qmax
l/s 19,6 26,6 36,6 48 48 47,6 56,9 73,2 70,7 70,8 88,4 88,4 88,8 118,4
EXCELLENCE version
size 120.1 160.1 200.1 240.1 250.2 280.2 320.2 340.2 360.2 400.2 440.2 480.2 540.2 580.2
Qmin
l/s
8,4 8.4 14.5 14.3 14.3 18.2 16,9 18.5 23.6 23.6 24.8 33.5 31.9 31.2
Qmax
l/s 22 22 33,9 43,8 43,8 55 47,6 57,1 73,2 73,2 70,8 89,1 89,1 88,8
PREMIUM version

15
4 WATER CONNECTIONS
Standard unit Unit + pump
1 exchanger
2 antifreeze heater
3 water temperature probes
4 -
5 differential pressur switch
6 flexible couplings
7 piping supports
8 exchanger chemical cleaning bypass
9 system cleaning bypass
10 vent
11 drain
12 water flow switch
13 system loading safety pressure
switch
14 pressure gauge
15 check valve
16 pump
17 safety valve
18 shut-off valves
19 filter

16
Partial energy recovery
Option
A configuration which enables the production of hot water free-of-
charge while operating in the cooling mode, thanks to the partial
recovery of condensation heat that would otherwise be rejected to
the external heat source.
The maximum capacity available from the partial recovery is equal
to the 15% of the rejected heating capacity (cooling capacity +
compressor power input)
The recovery exchanger must be always maintained full of water
The lack of water amplifies the noise generated by the operation
When the temperature of the water to be heated is particularly
low, it is wise to insert a flow-rate control valve into the system
water circuit, in order to maintain the temperature at the recovery
output at above 35°C and thus avoid the condensation of the
refrigerant into the partial energy recovery device..
4 WATER CONNECTIONS

17
5 ELECTRICAL CONNECTIONS
The characteristics of the electrical lines must be determined by specialized personnel able to design
electrical installations; moreover, the lines must be in conformity with regulations in force.
The protection devices of the unit power line must be able to stop the presumed short circuit current,
whose value must be determined in function of system features.
The power cables and the protection cable section must be defined in accordance with the characteristics
of the protections adopted.
All electrical operations should be performed by trained personnel having the necessary requirements by the
regulations in force and being informed about the risks relevant to these activities.
Operate in compliance with safety regulations in force.
Electrical data
The serial number label reports the unit specific electrical data, included any electrical accessories.
The electrical data indicated in the technical bulletin and in the manual refer to the standard unit,
accessories excluded.
Refer to the electrical data report on the serial number label:
Tensione
F.L.A.: full load ampere, absorbed current at maximum admitted conditions
F.L.I.: full load input, full load power input at max. admissible condition
Electrical wiring diagram Nr
Connections
refer to the unit electrical diagram (the number of the diagram is shown on the serial number label).
verify that the network has characteristics conforming to the data shown on the serial number label.
Before starting work, verify that the sectioning device at the start of the unit power line is open, blocked
and equipped with cartel warning.
Primarily you have to realize the earthing connection.
Shelter the cables using adequate measure fairleads.
Before power the unit, make sure that all the protections that were removed during the electrical connection
work have been restored.
Power supply network requirements
1 The short circuit capacity of the line must be less than 15 kA
2 The units can only be connected to TN, TT distribution systems
3 Voltage 400-3-50 +/-10%
4 Phase unbalance < 2%
5 Harmonic distortion less than 12% (THDv<12%)
6 Voltage interruptions lasting no longer than 3ms and with at least 1 s between each one
7 Voltage dips not exceeding 20% of the RMS value, lasting no longer than a single period (50Hz) and
with at least 1 s between each dip.
8 Earth cable as specified in the table:
Cross-section of the line conductors
(mm2)
Minimum cross-section of the protective
conductor (PE) (mm2)
S ≤16 S
16 < S ≤35 16
S > 35 S/2

18
5 ELECTRICAL CONNECTIONS
Distribution systems
The compressors are compatible with TT or TN type systems.
They cannot be used in IT systems.
Signals / data lines
Do not overpass the maximum power allowed, which varies,
according to the type of signal.
Lay the cables far from power cables or cables having a different
tension and that are able to emit electromagnetic disturbances.
Do not lay the cable near devices which can generate
electromagnetic interferences.
Do not lay the cables parallel to other cables; cable crossings
are possible, only if laid at 90°.
Connect the screen to the ground, only if there aren’t
disturbances.
Guarantee the continuity of the screen during the entire
extension of the cable.
Respect impendency, capacity and attenuation indications.
Power input
Fix the cables: if vacated may be subject to tearing.
The cable must not touch the compressor and the refrigerant
piping (they reach high temparatures).
NO systems IT !
Hearth
Hearth
High
impedance
Remote ON-OFF
Do not perform short On Off cycles
Do not use the remote On Off with thermoregulation function.

19
5 ELECTRICAL CONNECTIONS
Size 120.1 160.1 200.1 240.1 250.2
Min. cable section Cu (mm²) 1 x 95 1 x 150 1 x 240 2 x 150 1 x 240
Max. cable section Cu (mm²) 1 x 185 1 x 240 1 x 240 2 x 300 1 x 240
Min. bar Cu section (mm²) nd nd nd 2 x 30 x5 nd
Max. bar Cu width (mm) 32.0 32.0 40.0 50.0 40.0
Tightening torque (Nm) 20.0 20.0 20.0 20.0 20.0
Size 280.2 320.2 340.2 360.2 400.2
Min. cable section Cu (mm²) 2 x 150 2 x 150 2 x 185 2 x 185 2 x 240
Max. cable section Cu (mm²) 2 x 300 2 x 300 2 x 300 2 x 300 4 x 185
Min. bar Cu section (mm²) 2 x 30 x5 2 x 30 x5 2 x 40 x 5 2 x 40 x 5 2 x 50 x 5
Max. bar Cu width (mm) 50.0 50.0 63.0 63.0 63.0
Tightening torque (Nm) 20.0 20.0 nd nd nd
Size 440.2 480.2 540.2 580.2
Min. cable section Cu (mm²) 2 x 240 nd nd nd
Max. cable section Cu (mm²) 4 x 185 4 x 185 4 x 185 4 x 185
Min. bar Cu section (mm²) 2 x 50 x 5 2 x 60 x 5 2 x 60 x 5 2 x 60 x 5
Max. bar Cu width (mm) 63.0 63.0 63.0 63.0
Tightening torque (Nm) nd nd nd nd
Power supply cables section

20
5 ELECTRICAL CONNECTIONS
This manual suits for next models
1
Table of contents
Popular Water System manuals by other brands

Kärcher
Kärcher WaterClean 600 LP operating instructions
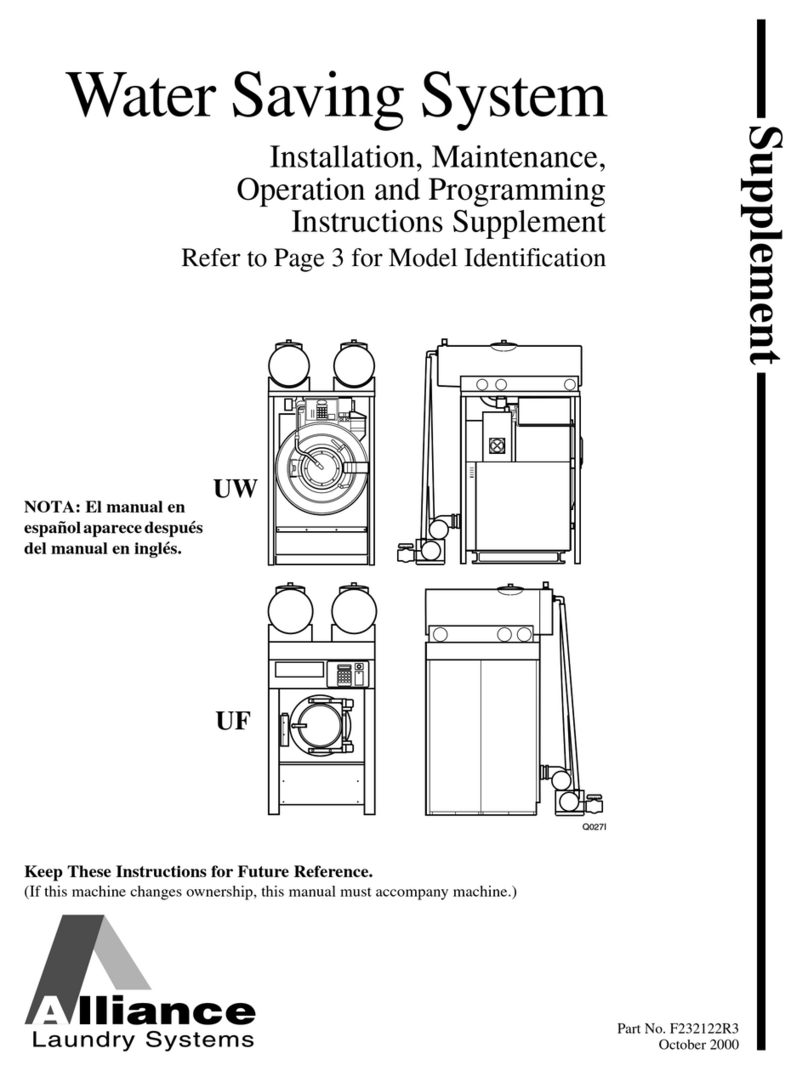
Alliance Laundry Systems
Alliance Laundry Systems F232122R3 Supplement
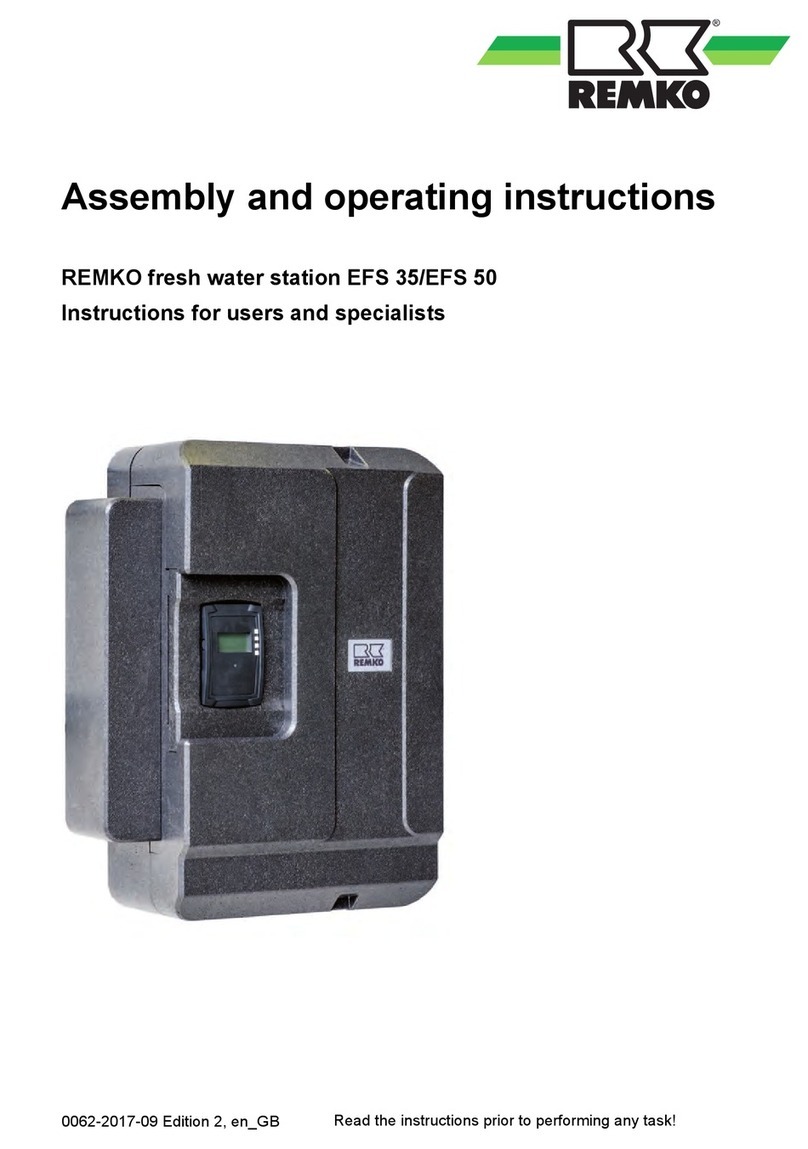
REMKO
REMKO EFS 50 Assembly and operating instructions
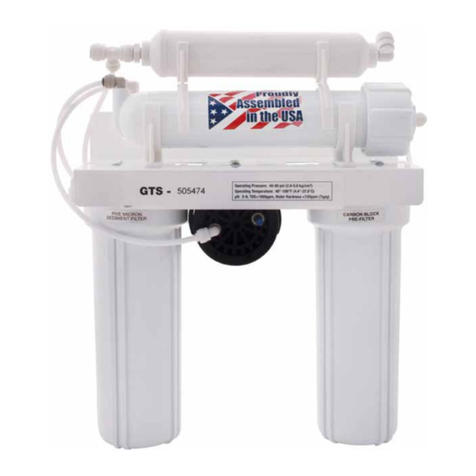
Watts
Watts FMRO4G-ERP-75 Installation, operation and maintenance
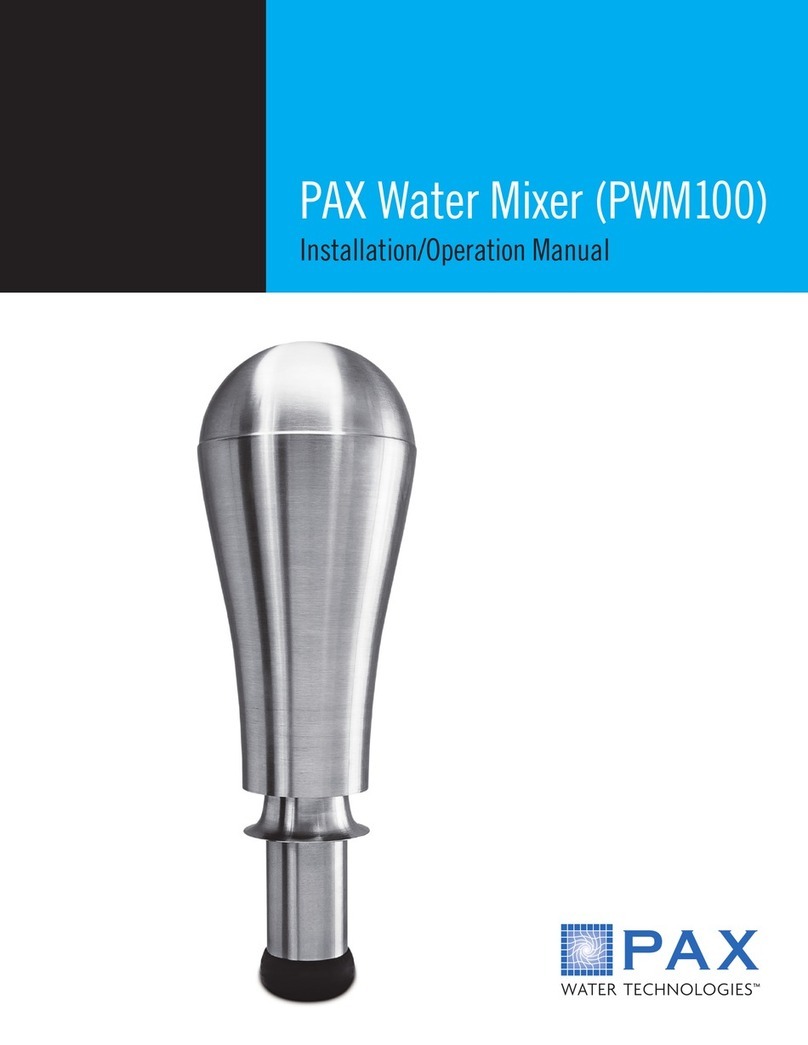
PAX
PAX PWM100 Installation & operation manual
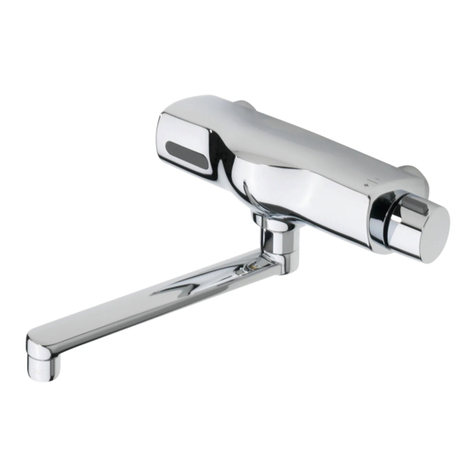
Oras
Oras Electra 6566 Installation and maintenance guide
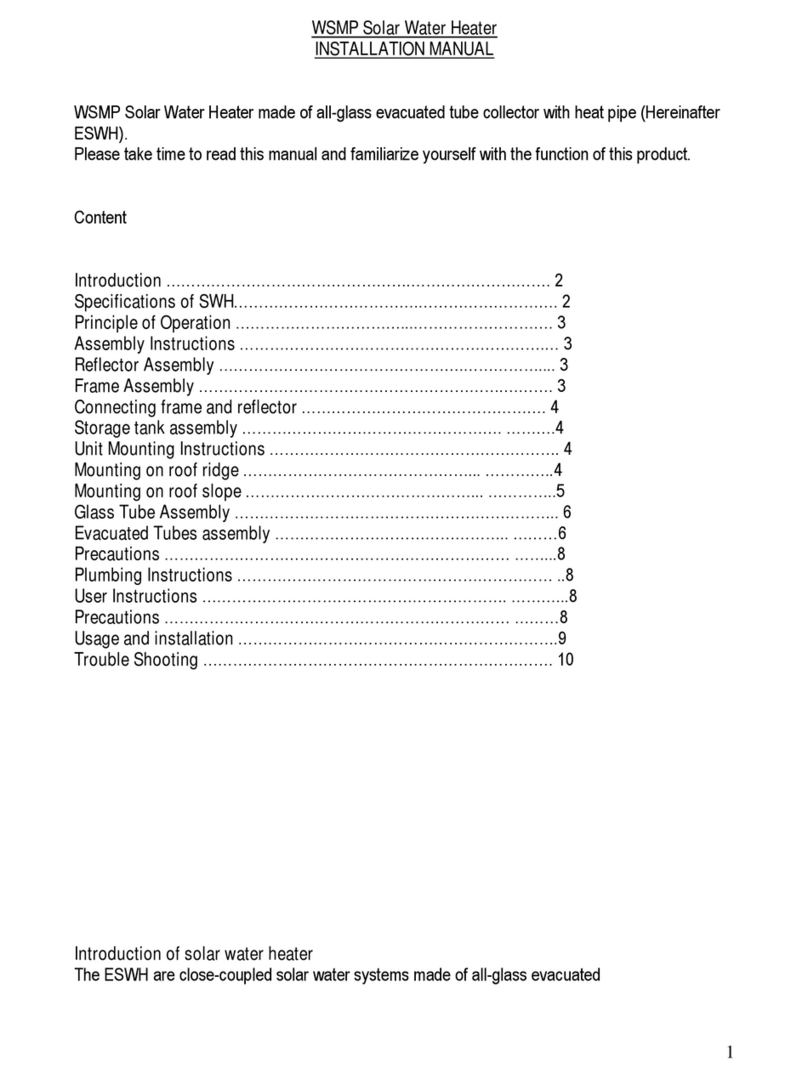
WSMP
WSMP JR-138 Installation & maintenance
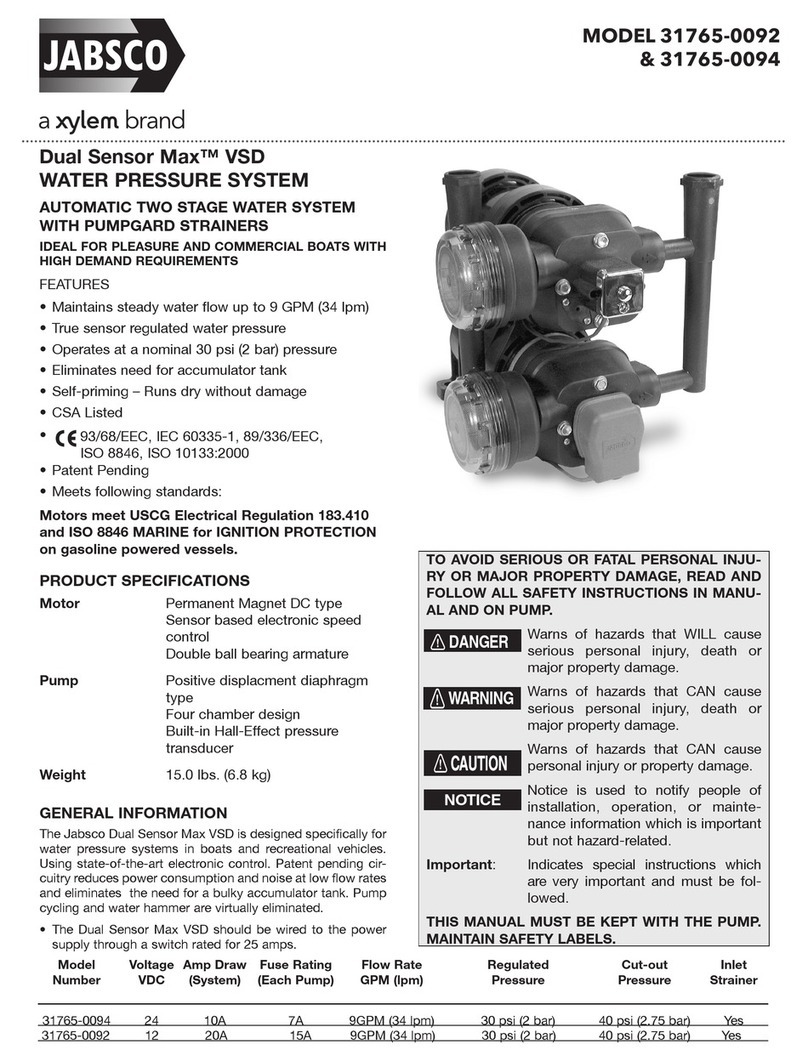
JABSCO
JABSCO 31765-0092 manual
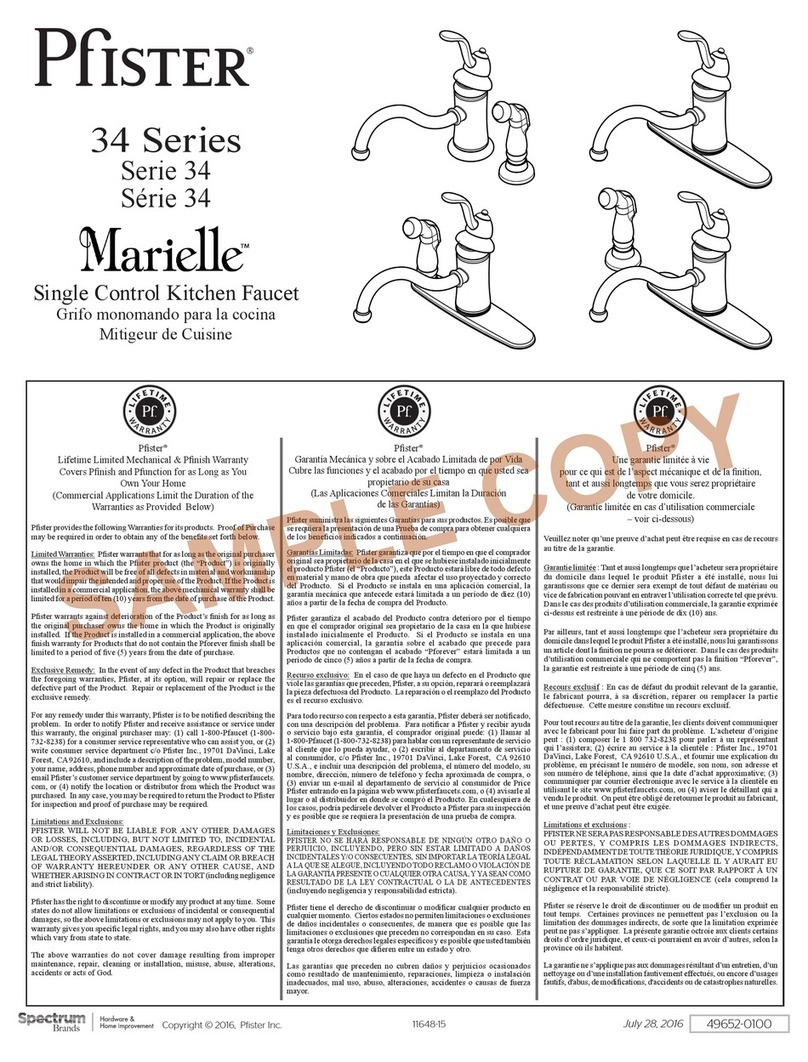
Pfister
Pfister Marielle 34 Series instructions
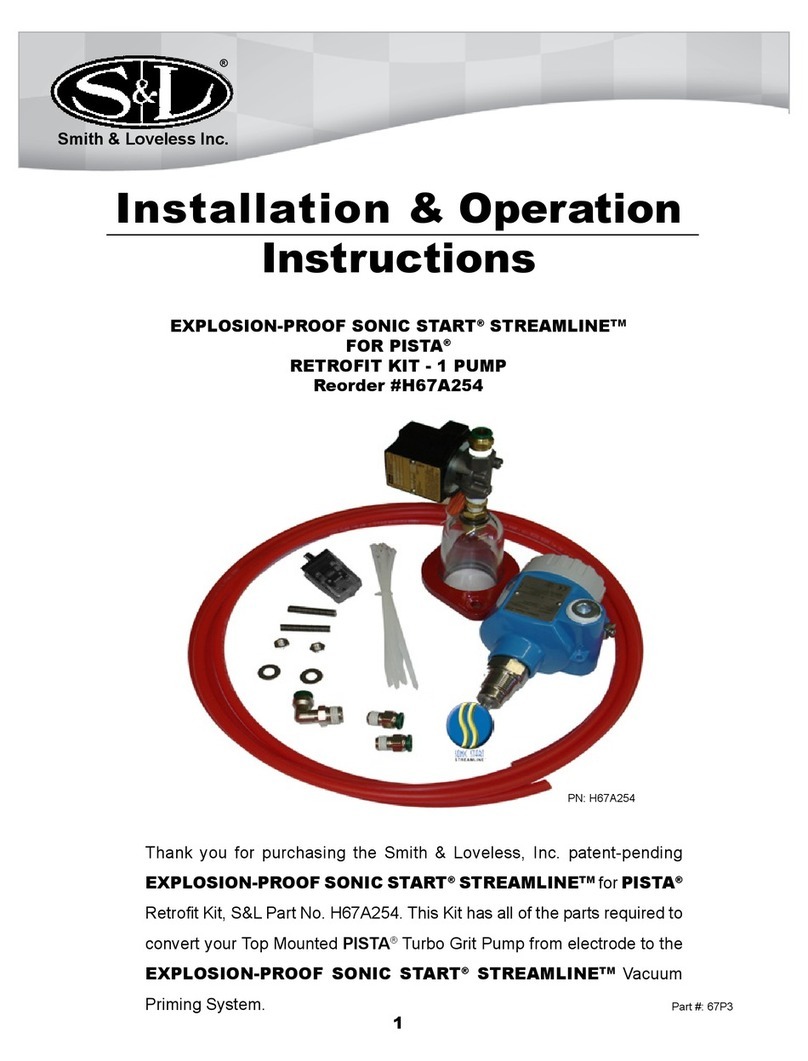
SMITH & LOVELESS
SMITH & LOVELESS STREAMLINE Installation & operation instructions

Clean Water Systems
Clean Water Systems 5900S Operation & maintenance manual

Everpure
Everpure ROM 10 Cartridge EV9273-91 Specification sheet