Coltri Compressors Tornado Guide

High pressure
compressed air chiller –dryer
EN - User’s maintenance and spare parts manual
74MD0040A0-EN_00

2 –EN TORNADO
Dear Customer,
thank you for choosing our product. In order to get the best performances out of this product, please read this
manual carefully.
To avoid incorrect operation of the equipment and possible physical risk to the operator, please read and
strictly follow the instructions contained in this manual.
Note, these instructions are in addition to the safety rules that apply in the country where the dryer is installed.
Before packing for shipment each TORNADO refrigerated air dryer undergoes a rigorous test to ensure the
absence of any manufacturing faults and to demonstrate that the device can perform all the functions for which
it has been designed.
Once the dryer has been properly installed according to the instructions in this manual, it will be ready for use
without any further adjustment. The operation is fully automatic, andthe maintenance is limited to few controls
and some cleaning operations, as detailed in the following chapters.
This manual must be maintained available in any moment for future references and it has to be
intended as inherent part of the relevant dryer.
Due to the continuous technical evolution, we reserve the right to introduce any necessary change without
giving previous notice.
Should you experience any trouble, or for further information, please do not hesitate to contact us.

TORNADO 3 –EN
Contents
1Identification plate 4
2Warranty conditions 4
3Safety rules 4
3.1 Definition of the conventional signs used in this manual 4
3.2 Warnings 5
3.3 Proper use of the dryer 5
3.4 Instructions for the use of pressure equipment according to PED directive 2014/68/EU 6
4Installation 6
4.1 Transport 6
4.2 Storage 6
4.3 Installation site 7
4.4 Connection to the compressed air system 7
4.5 Electrical connections 8
5Start-up 8
5.1 Preliminary operation 8
5.2 First start-up 8
5.3 Start-up and shut down 9
6Technical data 9
6.1 Technical data TORNADO 9
7Technical description 10
7.1 Control panel 10
7.2 Operation 10
7.3 Flow diagram 11
7.4 Refrigerating compressor 11
7.5 Condenser 11
7.6 Filter dryer 12
7.7 Capillary tube 12
7.8 Evaporator 12
7.9 Hot gas by-pass valve 12
7.10 Electronic instrument DMC35 13
7.10.1 How to switch on the dryer 13
7.10.2 How to switch off the dryer 13
7.10.3 How a service warning / alarm is displayed 13
7.10.4 How is controlled the condenser fan 14
7.10.5 How is controlled the drain solenoid valve 14
7.10.6 How to display the total hours of operation 14
7.10.7 How to change the operating parameters –SETUP menu 14
8Maintenance, troubleshooting, spare parts and dismantling 15
8.1 Checks and maintenance 15
8.2 Troubleshooting 15
8.3 Spare parts 17
8.4 Maintenance operation on the refrigeration circuit 17
8.5 Dismantling of the dryer 17
9Attachments 18
Exploded view –List of components 18
Electric diagram –List of components 18
9.1 Dryer dimension 19
9.1.1 TORNADO 19
9.2 Exploded view 20
9.2.1 TORNADO 20
9.3 Electric diagram 21
9.3.1 TORNADO 21
10 Blank pages 22
Pos: 1/ Beko Technisc heD okumentation/Ü berschriften/1/Sic herheitshinweise @ 0\m od_118363 7609261_6.doc @ 53 65

4 –EN TORNADO
1 Identification plate
The identification plate is located on the back of the dryer and shows all the primary data of the machine.
This data should always be referred to when calling the manufacturer or distributor. The removal or alteration
of the identification plate will void the warranty rights.
2 Warranty conditions
For 12 months from the installation date, but no longer than 14 months from the delivery date, the warranty
covers eventual faulty parts, which will be repaired or replaced free of charge, except the travel, hotel and
restaurant expenses of our engineer.
The warranty doesn’t cover any responsibility for direct or indirect damages to persons, animals or equipment
caused by improper usage or maintenance, and it’s limited to manufacturing faults only.
The right to warranty repairs is subordinated to the strict compliance with the installation, use and
maintenance instructions contained in this manual.
The warranty will be immediately voided in case of even small changes or alterations to the dryer. To require
repairs during the warranty period, the data reported on the identification plate must be notified.
3 Safety rules
3.1 Definition of the conventional signs used in this manual
Carefully read instruction manual before attempting any service or maintenance procedures on the
dryer.
Caution warning sign. Risk of danger or possibility of damage to equipment, if related text is not
followed properly.
Electrical hazard. Warning message indicates practices or procedures that could result in personal
injury or fatality if not followed correctly.
Danger hazard. Part or system under pressure.
Danger hazard. High temperature conditions exist during operation of system. Avoid contact until
system or component has dissipated heat.
Danger hazard. Treated air is not suitable for breathing purposes; serious injury or fatality may result
if precautions are not followed.
Danger hazard: In case of fire, use an approved fire extinguisher, water is not an acceptable means
in cases of fire.
Danger hazard. Do not operate equipment with panels removed.
Maintenance or control operation to be performed by qualified personnel only [1].
Compressed air inlet connection point
Compressed air outlet connection point
Operations which can be performed by the operator of the machine, if qualified [1].
NOTE: Text that specifies items of note to be taken into account does not involve safety precautions.
ARIA
AIR
LUFT
AIR
ARIA
AIR
LUFT
AIR

TORNADO 5 –EN
In designing this unit a lot of care has been devoted to environmental protection:
•CFC free refrigerants
•CFC free insulation parts
•Energy saving design
•Limited acoustic emission
•Dryer and relevant packaging composed of recyclable materials
This symbol requests that the user heed environmental considerations and abide with suggestions
annotated with this symbol.
[1] Experienced and trained personnel familiar with national and local codes, capable to perform the needed activities, identify and
avoid possible dangerous situations while handling, installing, using and servicing the machine. Ensuring compliance to all statutory
regulations.
3.2 Warnings
Compressed air is a highly hazardous energy source.
Never work on the dryer with pressure in the system.
Never point the compressed air or the condensate drain outlet hoses towards anybody.
The user is responsible for the proper installation of the dryer. Failure to follow instructions given in
the “Installation” chapter will void the warranty. Improper installation can create dangerous situations
for personnel and/or damages to the machine could occur.
Only qualified personnel are authorized to service electrically powered devices. Before attempting
maintenance, the following conditions must be satisfied:
•Ensure that main power is off, machine is locked out, tagged for service and power cannot be
restored during service operations.
•Ensure that valves are shut and the air circuit is at atmospheric pressure. De-pressurize the dryer.
This refrigerating air dryer contain R134a HFC type refrigerant fluid. Refer to the specific paragraph
- maintenance operation on the refrigerating circuit.
Warranty does not apply to any unit damaged by accident, modification, misuse, negligence or
misapplication. Unauthorized alterations will immediately void the warranty.
In case of fire, use an approved fire extinguisher, water is not an acceptable means in cases of
electrical fire.
3.3 Proper use of the dryer
This dryer has been designed, manufactured and tested for the purpose of separating the humidity normally
contained in compressed air. Any other use has to be considered improper.
The Manufacturer will not be responsible for any problem arising from improper use; the user will bear
responsibility for any resulting damage.
Moreover, the correct use requires the adherence to the installation instructions, specifically:
•Voltage and frequency of the main power.
•Pressure, temperature and flow-rate of the inlet air.
•Ambient temperature.
This dryer is supplied tested and fully assembled. The only operation left to the user is the connection to the
plant in compliance with the instructions given in the following chapters.
The purpose of the machine is the separation of water and eventual oil particles present in
compressed air.
The dried air cannot be used for breathing purposes or for operations leading to direct contact with
foodstuff.
This dryer is not suitable for the treatment of dirty air or of air containing solid particles.

6 –EN TORNADO
3.4 Instructions for the use of pressure equipment according to PED directive 2014/68/EU
To ensure the safe operation of pressure equipments, the user must conform strictly to the above directive
and the following:
1. The equipment must only be operated within the temperature and pressure limits stated on the
manufacturer’s data nameplate.
2. Welding on heat-exchanger is not recommended.
3. The equipment must not be stored in badly ventilated spaces, near a heat source or inflammable
substances.
4. Vibration must be eliminated from the equipment to prevent fatigue failure.
5. Automatic condensate drains should be checked for operation every day to prevent a build up of
condensate in the pressure equipment.
6. The maximum working pressure stated on the manufacturer’s data nameplate must not be exceeded.
Prior to use, the user must fit safety / pressure relief devices.
7. All documentation supplied with the equipment (manual, declaration of conformity etc.) must be kept for
future reference.
8. Do not apply weights or external loads on the vessel or its connecting piping.
TAMPERING, MODIFICATION AND IMPROPER USE OF THE PRESSURE EQUIPMENT ARE
FORBIDDEN. Users of the equipment must comply with all local and national pressure
equipment legislation in the country of installation.
4 Installation
4.1 Transport
Check for visible loss or damage, if no visible damage is found place the unit near to the installation point
and unpack the contents.
•To move the packaged unit we recommend using a suitable trolley or forklift truck. Hand carrying is not
recommended.
•Always keep the dryer in the upright vertical position. Damage to components could result if unit is laid on
its side or if placed upside down.
•Handle with care. Heavy blows could cause irreparable damage.
4.2 Storage
Even when packaged, keep the machine
protected from severity of the weather.
Keep the dryer in vertical position, also when
stored. Turning it upside down some parts could
be irreparably damaged.
If not in use, the dryer can be stored in its
packaging in a dust free and protected site at a
maximum temperature of 50 °C, and a specific
humidity not exceeding 90%. Should the stocking
time exceed 12 months, please contact the
manufacturer.
The packaging materials are recyclable. Dispose of material in compliance with the rules
and regulations in force in the destination country.
SCC0001

TORNADO 7 –EN
4.3 Installation site
Failure to install dryer in the proper ambient conditions will affect the dryer’s ability to condense
refrigerant gas. This can cause higher loads on the compressor, loss of dryer efficiency and
performance, overheated condenser fan motors, electrical component failure and dryer failure due
to the following: compressor loss, fan motor failure and electrical component failure. Failures of this
type will affect warranty considerations.
Do not install dryer in an environment of corrosive chemicals, explosive gasses, poisonous gasses;
steam heat, areas of high ambient conditions or extreme dust and dirt.
In case of fire, use an approved fire extinguisher, water is not an acceptable means in cases of fire.
Minimum installation requirements:
•Select a clean dry area, free from dust, and protected from atmospheric disturbances.
•The supporting area must be smooth, horizontal and able to hold the weight of the dryer.
•Minimum ambient temperature +1°C.
•Maximum ambient temperature +50°C.
•Ensure a proper cooling air replacement.
•Allow a sufficient clearance on each side of the dryer for proper ventilation and to facilitate maintenance
operations.
The dryer does not require attachment to the floor surface.
Do not block, even partially, ventilation grid.
Avoid any possible re-circulation of the exhaust cooling air.
Protect the dryer from air drafts or forced cooling air conditions.
4.4 Connection to the compressed air system
Operations to be performed by qualified personnel only.
Never work on system under pressure.
The user is responsible to ensure that the dryer will never be operated with pressure exceeding the
maximum pressure rating on the unit data tag.
Over-pressurizing the dryer could be dangerous for both the operator and the unit.
The air temperature and the flow entering the dryer must comply within the limits stated on the data
nameplate. The system connecting piping must be kept free from dust, rust, chips and other impurities, and
must be consistent with the flow-rate of the dryer. In case of treatment of air at particularly high temperature,
the installation of a final refrigerator could result necessary.
In case of heavily polluted inlet air (ISO 8573.1 class 3.-.3 or worse quality), we recommend
the additional installation of a pre-filter (5 micron minimum) to prevent a clogging of the heat
exchanger.
Pulsations and vibrations must be eliminated from the compressed air and IN/OUT piping to avoid
possible fatigue failure.
Do not use the dryer to treat air containing corrosive substances for copper and its alloys.

8 –EN TORNADO
4.5 Electrical connections
Qualified personnel should carry out connecting unit to the main power.
Be sure to check the local codes in your area.
Before connecting the unit to the electrical supply, verify the data nameplate for the proper electrical
information. Voltage tolerance is +/- 10%.
Dryer TORNADO is supplied with power cord and plug (two poles and ground).
Be sure to provide the proper fuses or breakers based on the data information located on the nameplate.
The mains socket must be provided with a mains magneto-thermal differential breaker (In =0.03A), adjusted
on the basis of the consumption of the dryer (see the nominal values on the data plate of the dryer). The
cross section of the power supply cables must comply with the consumption of the dryer, while keeping into
account also the ambient temperature, the conditions of the mains installation, the length of the cables, and
the requirements enforced by the local Power Provider.
Important: ensure that the dryer is earthed.
Do not use any socket adapters at the mains plug.
If the mains plug needs to be replaced, this must only be done by a qualified electrician.
5 Start-up
5.1 Preliminary operation
Verify that the operating parameters match with the nominal values stated on the data nameplate of
the dryer (voltage, frequency, air pressure, air temperature, ambient temperature, etc.).
This dryer has been thoroughly tested, packaged and inspected prior to shipment. Nevertheless, the unit
could be damaged during transportation, check the integrity of the dryer during first start-up and monitor
operation during the first hours of operation.
Qualified personnel must perform the first start-up.
When installing and operating this equipment, comply with all National Electrical Code and any
applicable federal, state and local codes.
Who is operating the unit is responsible for the proper and safe operation of the dryer.
Never operate equipment with panels removed.
5.2 First start-up
This procedure should be followed on first start-up, after periods of extended shutdown or following
maintenance procedures.Qualified personnel must perform the start-up.
Sequence of operations
•Ensure that all the steps of the “Installation” chapter have been observed.
•Ensure that the connection to the compressed air system is correct and that the piping is suitably fixed and
supported.
•Remove any packaging and other material which could obstruct the area around the dryer.
•Activate the mains switch.
•Turn ON the ON-OFF switch
•Ensure the consumption matches with the values of the data plate.
•Ensure the fan works properly –wait for its first interventions.
•Allow the dryer temperature to stabilise at the pre-set value.
•Slowly open the air inlet valve.
•Slowly open the air outlet valve.
•Check the piping for air leakage.

TORNADO 9 –EN
5.3 Start-up and shut down
Start-up
•Check the condenser for cleanliness.
•Turn ON the ON-OFF switch
•Wait a few minutes and switch on the air compressor.
Shut down
•Shut down the air compressor.
•After a few minutes, turn OFF the ON-OFF switch
During the operation, the refrigerant compressor will run continuously. The dryer must remain on during the
full usage period of the compressed air, even if the air compressor works intermittently.
The number of starts must be no more than 6 per hour.
The dryer must stop running for at least 5 minutes before being started up again.
Frequent starts may cause irreparable damage.
The user is responsible for compliance with these rules.
6 Technical data
6.1 Technical data TORNADO

10 –EN TORNADO
7 Technical description
7.1 Control panel
1
2
ON-OFF switch
Electronic instrument
7.2 Operation
Operating principle - The hot moisture ladenair enters in the evaporator, also known as theairto refrigerant
heat exchanger, causing water vapor to condense to liquid.
Refrigerant circuit - Refrigerant gas is cycled through the compressor and exits at high pressure to a
condenser where heat is removed causing the refrigerant to condense to a high-pressure liquid state. The
liquid is forced through a capillary tube where the resulting pressure drop allows the refrigerant to boil off at
a predeterminedtemperature. Low-pressure liquid refrigerant enters the heat exchanger where heat from the
incoming air is transferred causing the refrigerant to boil; the resulting phase change produces a low
pressure, low temperature gas. The low-pressure gas is returned to the compressor, where it is re-
compressed and begins the cycle again. During those periods when the compressed air load is reduced the
excess refrigerant is by-passed automatically back to the compressor via the hot gas by-pass valve circuit.
12
1
0
PQS0100
sec - min
Set
DMC35
ON

TORNADO 11 –EN
7.3 Flow diagram
1
Heat exchanger group
8
Condenser
1a
Air-to-refrigerant heat exchanger
9
Condenser fan
5
Refrigerant pressure switch PV (not installed)
10
Filter dryer
6
Compressor
11
Capillary tube
7
Hot gas by-pass valve
12
Temperature probe BT1 –DewPoint
Compressed air flow direction
Refrigerant gas flow direction
7.4 Refrigerating compressor
The refrigerating compressor is the pump in the system, gas coming from the evaporator (low pressure side)
is compressed up to the condensation pressure (high pressure side). The compressors utilized are
manufactured by leading manufacturers and are designed for applications where high compression ratios
and wide temperature changes are present.
The hermetically sealed construction is perfectly gas tight, ensuring high-energy efficiency and long, useful
life. Dumping springs support the pumping unit in order to reduce the acoustic emission and the vibration
diffusion. The aspirated refrigerant gas, flowing through the coils before reaching the compression cylinders
cools the electric motor. The thermal protection protects the compressor from over heating and over currents.
The protection is automatically restored as soon as the nominal temperature conditions are reached.
7.5 Condenser
The condenser is the component in which the gas coming from the compressor is cooled down and
condensed becoming a liquid. Mechanically, a serpentine copper tubing circuit (with the gas flowing inside)
is encapsulated in an aluminum fin package.
The cooling operation occurs via a high efficiency fan, creating airflow within the dryer, moving air through
the fin package. It’s mandatory that the ambient air temperature does not exceed the nominal values. It is
also important to keep the condenser unit free from dust and other impurities.
11 10
7
6
9M
5
8
PV
DGF0120
11a
T1 12

12 –EN TORNADO
7.6 Filter dryer
Traces of humidity and slag can accumulate inside the refrigerant circuit. Long periods of use can also
produce sludge. This can limit the lubrication efficiency of the compressor and clog the expansion valve or
capillary tube. The function of the filter drier, located before the capillary tubing, is to eliminate any impurities
from circulating through the system.
7.7 Capillary tube
It consists of a piece of reduced cross section copper tubing located between the condenser and the
evaporator, acting as a metering device to reduce the pressure of the refrigerant. Reduction of pressure is a
design function to achieve optimum temperature reached within the evaporator: the smaller the capillary tube
outlet pressure, the lower the evaporation temperature.
The length and interior diameter of the capillary tubing is accurately sized to establish the performance of the
dryer; no maintenance or adjustment is necessary.
7.8 Evaporator
The liquid formed in the condenser is evaporated in this part of the circuit. In the evaporation phase the
refrigerant tends to absorb the heat from the compressed air present in the other side of the exchanger.
Refrigerant and air are in counterflow, thus contributing to limit pressure drop and to provide efficient thermal
exchange.
7.9 Hot gas by-pass valve
This valve injects part of the hot gas (taken from the discharge side of the compressor) in the pipe between
the evaporator and the suction side of the compressor, keeping the evaporation temperature/pressure
constant at approx. +2 °C. This injection prevents the formation of ice inside the dryer evaporator at every
load condition.
ADJUSTMENT
The hot gas by-pass valve is adjusted during the manufacturing testing
phase. As a rule no adjustment is required; anyway if it is necessary the
operation must be carried out by an experienced refrigerating engineer.
WARNING
the use of ¼” Schrader service valves must be justified by a real
malfunction of the refrigerating system. Each time a pressure gauge is
connected, a part of refrigerant is exhausted.
Without compressed air flow through the dryer, rotate the adjusting
screw (position A on the drawing) until the following value is reached:
Hot gas setting : R134.a pressure 2.0 barg (+0.1 / -0 bar)
A
4 mm
5/32 in.
+
-
VLY0001

TORNADO 13 –EN
7.10 Electronic instrument DMC35
Led –Power ON
Led –Alarm active
Led - Drain ON
Led –Condenser fan ON
Button –Setup menu access
Button –Increase / Drain test
The DMC35 displays DewPoint temperature, controls the condenser fan activation, controls the timed
drainer and keep record of the total hours of operation of the dryer.
7.10.1 How to switch on the dryer
Power the dryer and switch it on using the ON-OFF switch (pos.1 paragraph 7.1).
During normal operation led is ON and the display shows the DewPoint temperature by means of
two coloured areas (green and red) above a 10 Led display :
• Green area - operating conditions ensuring an optimal DewPoint;
• Red area - DewPoint too high, the dryer is operating with high thermal load (high inlet air temperature,
high ambient temperature, etc.). Compressed air treatment may be improper.
Led shows that one or more service warnings / alarms are active.
Led shows that condensate drain solenoid valve is ON.
Led shows that condenser fan is ON.
The condensate drain test is always active using the button .
7.10.2 How to switch off the dryer
Switch it off using the ON-OFF switch (pos. 1 paragraph 7.1).
7.10.3 How a service warning / alarm is displayed
A service warning / alarm is an unusual event that must recall the attention of the operators / maintenance
technicians. It does not stop the dryer.
Service warnings / alarms are automatically reset as soon as the problem is solved and dryer is powered
again.
NOTE: the operator / maintenance technician must inspect the dryer and verify / solve the problem
that generated the service warning.
Service Warning / Alarm
Description
Led and display 1st (left) and 10th (right) led
are flashing
Failure BT1 (DewPoint) temperature probe.
Led and led are flashing
Failure BT2/BP2 (fan control) probe.
NOTE : fan is forced always ON.
Led and display 1st (left) led are flashing
DewPoint too low
(lower than -1°C / 30°F).
DMC35
PQS0091
DISPLAY
Set
ON
sec - min
ON
Set
ON

Technical description
14 –EN TORNADO
7.10.4 How is controlled the condenser fan
AMD 3-32 A temperature probe BT2 is located on the discharge side of the condenser. The condenser fan
is activated (ON) when the BT2 temperature is higher than FANon setting (approx. 35°C/96°F) and led
is ON. Condenser fan stops when BT2 temperatures is lower than FANoff setting (approx.
30°C/86°F).
7.10.5 How is controlled the drain solenoid valve
Drain solenoid valve is activated (ON) for TON seconds (standard 2 seconds) every TOFF minutes (standard 1
minute). Led shows that condensate drain solenoid valve is ON.
The condensate drain test is always active using the button .
NOTE : if an electronic drainer is installed, DMC35 is set to keep always powered the drain output, Led
is always OFF and condensate drain test does not work.
7.10.6 How to display the total hours of operation
Total hours of operation are recorded into DMC35 and are shown through the dew point indication bar (max
value 109900 hours, cannot be reset).
With dryer ON press buttons and for at least 5 seconds.
Led is lit and a certain numbers of leds of dew point indication bar are light up. The number of leds
lit define the 1st digit of hour counter (ie : no leds lit →1st digit =0)
Press button, led is lit and a certain numbers of leds of dew point indication bar are light up.
The number of leds lit define the 2nd digit of hour counter (ie : n.3 leds lit →2nd digit = 3)
Press button, led is lit and a certain numbers of leds of dew point indication bar are light up.
The number of leds lit define the 3rd digit of hour counter (ie : n.8 leds lit →3rd digit = 8)
Total operating hours : 0 3 8 x 100 (fixed multiplying ratio) = 3800 hours
Press button repeatedly to scroll the displaying of 3 digits again.
Press button to exit total hours display (if no button is pressed after 30 seconds the menu is exited
automatically).
7.10.7 How to change the operating parameters –SETUP menu
The setup menu can be used to change the dryer’s operating parameters.
Only qualified personnel must be allowed to access to the setup menu. The
manufacturer is not responsible for malfunctioning or failure due to modification to the
operating parameters.
With dryer ON press button for at least 2 seconds to enter the setup menu.
Access to the menu is confirmed by led flashing.
Keep pressed and use arrows to change the value. Release the button to confirm
the value. Press shortly to skip to following parameter.
Press to exit setup menu (if no button is pressed after 2 minutes the menu is exited automatically).
Display
Description
Limits
Resolution
Standard
setup
Synchronous flashing
led + led
TON –drain time ON : time ON
condensate drain valve (1)
1 … 6 sec
1 sec
2
Non-Synchronous flashing
led + led
TOFF - drain time OFF : pause
time for condensate drain valve
1 … 10 min
1 min
1
NOTE : parameter values are displayed on the 10 led display where 1st (left) led is the lowest limit and 10th
(right) is the highest limit.
NOTE (1): TON set at the 10th led (right) keep drain output always powered and led always off (used if
electronic drainer is installed).
Set
ON
Set
Set
ON
Set
Set
Set
ON
ON

Maintenance, troubleshooting, spare parts and dismantling
TORNADO 15 –EN
8 Maintenance, troubleshooting, spare parts and dismantling
8.1 Checks and maintenance
Only qualified personnel should perform troubleshooting and or maintenance
operations.
Prior to performing any maintenance or service, be sure that :
•no part of the machine is powered and that it cannot be connected to the mains
supply.
•no part of the machine is under pressure and that it cannot be connected to the
compressed air system.
•maintenance personnel have read and understand the safety and operation
instructions in this manual.
Before attempting any maintenance operation on the dryer, shut it down and wait at least
30 minutes. Some components can reach high temperature during operation. Avoid
contact until system or component has dissipated heat.
Daily
•Check the proper operation of the condensate drain systems.
•Verify the condenser for cleanliness
Every 200 hours or monthly
•With an air jet (max. 2 bar / 30 psig) blowing from inside towards outside
clean the condenser; repeat this operation blowing in the opposite way; be
careful not to damage the aluminum fins of the cooling package (Air-
Cooled)
Every 1000 hours or yearly
•Verify for tightness all the screws of the electric system and that all the “Disconnects-Tabs” type
connections are in their proper position inspect unit for broken, cracked or bare wires.
•Inspect refrigerating circuit for signs of oil and refrigerant leakage.
•Measure and record amperage. Verify that readings are within acceptable parameters as listed
in specification table.
•Inspect flexible hoses, and replace if necessary.
•At the end, check the operation of the machine.
8.2 Troubleshooting
Only qualified personnel should perform troubleshooting and or maintenance
operations.
Prior to performing any maintenance or service, be sure that :
•no part of the machine is powered and that it cannot be connected to the
mains supply.
•no part of the machine is under pressure and that it cannot be connected to
the compressed air system.
•maintenance personnel have read and understand the safety and operation
instructions in this manual.
Before attempting any maintenance operation on the dryer, shut it down and wait at least
30 minutes. Some components can reach high temperature during operation. Avoid
contact until system or component has dissipated heat.

Maintenance, troubleshooting, spare parts and dismantling
16 –EN TORNADO
SYMPTOM
POSSIBLE CAUSE - SUGGESTED ACTION
◆The dryer doesn't
start.
Verify that the system is powered.
Verify the electric wiring.
◆The compressor
doesn’t work.
Activation of the compressor internal thermal protection - wait for 30 minutes,
then retry.
Verify the electric wiring.
If the compressor still doesn’t work, replace it.
◆Condenser’s fan
doesn’t work.
Verify the electric wiring.
The DMC35 electronic instrument is faulty –replace it.
There is a leak in the refrigerant circuit - contact a refrigeration engineer.
If the fan still doesn't work, replace it.
◆Temperature shown
on thermometer too
high
The dryer doesn't start - see specific point.
The DewPoint probe BT1 doesn’t correctly detect the temperature - ensure the
sensor is pushed into the bottom of probe well.
The compressor doesn’t work - see specific point.
The ambient temperature is too high or the room aeration is insufficient - provide
proper ventilation.
The inlet air is too hot - restore nominal conditions.
The inlet air pressure is too low - restore nominal conditions.
The inlet air flow rate is higher than the rate of the dryer - reduce the flow rate -
restore nominal conditions.
The condenser is dirty - clean it.
The condenser fan doesn’t work - see specific point.
The dryer doesn’t drain the condensate.
The hot gas by-pass valve is out of setting - contact a refrigeration engineer to
restore nominal setting.
There is a leak in the refrigerant circuit - contact a refrigeration engineer.
◆Temperature shown
on thermometer too
low.
The fan is always ON - the yellow LED of DMC35 electronic instrument
is flashing - see specific point.
Ambient temperature is too low - restore nominal conditions.
The hot gas by-pass valve is out of setting - contact a refrigeration engineer to
restore nominal setting.
◆Excessive pressure
drop within the
dryer.
The condensate is frost and blocks the air.
Check for throttling the flexible connection hoses.
◆DMC35 -
Led and
display 1st (left) and
10th (right) led are
flashing.
Verify the electric wiring of BT1 DewPoint probe.
The BT1 DewPoint probe is faulty - replace it.
The electronic instrument is faulty - replace it.
◆DMC35
Led and led
are flashing
Verify the electric wiring of BT2/BP2 fan control probe.
The BT2/BP2 fan control probe is faulty - replace it.
The electronic instrument is faulty - replace it.
◆DMC35
Led and
display 1st (left) led
are flashing
DewPoint too low - see specific point.
The BT1 DewPoint probe is faulty - replace it.
The electronic instrument is faulty - replace it.
◆DMC35
Display 10th (right)
led is flashing
DewPoint too high - see specific point.
The BT1 DewPoint probe is faulty - replace it.
The electronic instrument is faulty - replace it.

TORNADO 17 –EN
8.3 Spare parts
The suggestedspareparts list will enable youto promptly intervene in caseof abnormal operation, so avoiding
to wait for the spares delivery. In case of failure of other parts, for example inside the refrigerating circuit, the
replacement must be worked out by a refrigerating systems specialist or in our factory.
Spare parts list is printed on a dedicated sticker applied inside the dryer.
NOTE: To order the suggested spare parts or any other part, it’s necessary to quote the data reported
on the identification plate.
8.4 Maintenance operation on the refrigeration circuit
Maintenance and service on refrigerating systems must be carried out only by certified refrigerating
engineers only, according to local rules.
All the refrigerant of the system must be recovered for its recycling, reclamation or destruction.
Do not dispose the refrigerant fluid in the environment.
This dryer comes ready to operate and filled with R134a type refrigerant fluid.
In case of refrigerant leak contact a certified refrigerating engineer. Room is to be aired before any
intervention.
If is required to re-fill the refrigerating circuit, contact a certified refrigerating engineers.
Refer to the dryer nameplate for refrigerant type and quantity.
Characteristics of refrigerants used:
Refrigerant
Chemical formula
TLV
GWP
R134a - HFC
CH2FCF3
1000 ppm
1430
8.5 Dismantling of the dryer
If the dryer is to be dismantled, it has to be split into homogeneous groups of materials.
Part
Material
Refrigerant fluid
R407C, R134a, Oil
Canopy and Supports
Carbon steel, Epoxy paint
Refrigerating compressor
Steel, Copper, Aluminium, Oil
Evaporator
Aluminium, Copper, Carbon steel
Condenser Unit
Aluminium, Copper, Carbon steel
Pipe
Copper
Fan
Aluminium, Copper, Steel
Valve
Brass, Steel
Insulation Material
Synthetic rubber without CFC, Polystyrene, Polyurethane
Electric cable
Copper, PVC
Electric Parts
PVC, Copper, Brass
We recommend to comply with the safety rules in force for the disposal of each type of material.
Refrigerant contains droplets of lubrication oil released by the refrigerating compressor.
Do not dispose this fluid in the environment. Is has to be discharged from the dryer with a suitable
device and then delivered to a collection centre where it will be processed to make it reusable.

Attachments
18 –EN TORNADO
9 Attachments
Exploded view –List of components
1
Heat exchanger group
11
Capillary tube
6
Compressor
12
Temperature probe
7
Hot-gas bypass valve
17
Electronic instrument
8
Condenser
22
Main switch
9
Condenser fan
51
Front panel
9.1
Motor
52
Back panel
9.2
Blade
53
Right lateral panel
9.3
Grid
55
Cover
10
Filter dryer
56
Base plate
Electric diagram –List of components
MC1
Compressor
KT
Compressor thermal protection
KR
Compressor starting relay
CS
Compressor starting capacitor
MV1
Condenser fan
CV
Fan starting capacitor
S1
ON-OFF switch
BT1
Temperature probe
DMC35
Electronic instrument
NT4
Provided and wired by customer
NT5
Limit of equipment

Attachments
TORNADO 19 –EN
9.1 Dryer dimension
9.1.1 TORNADO

Attachments
20 –EN TORNADO
9.2 Exploded view
9.2.1 TORNADO
Table of contents
Popular Chiller manuals by other brands
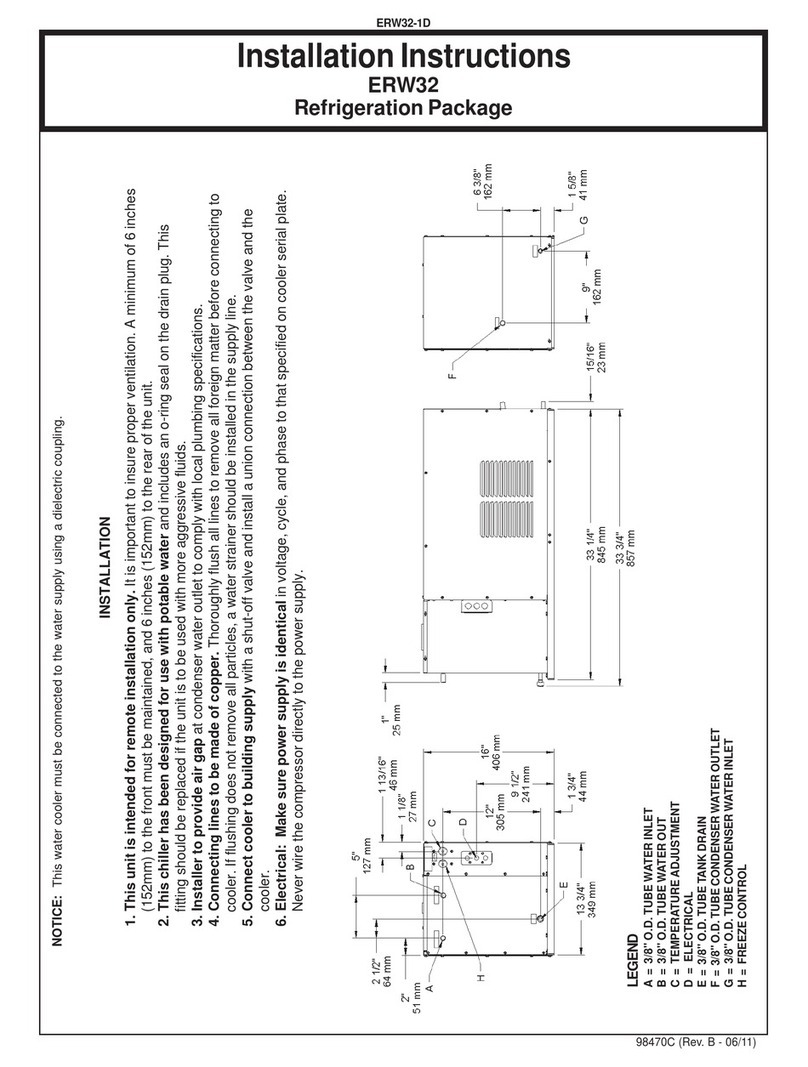
Elkay
Elkay ERW32 installation instructions
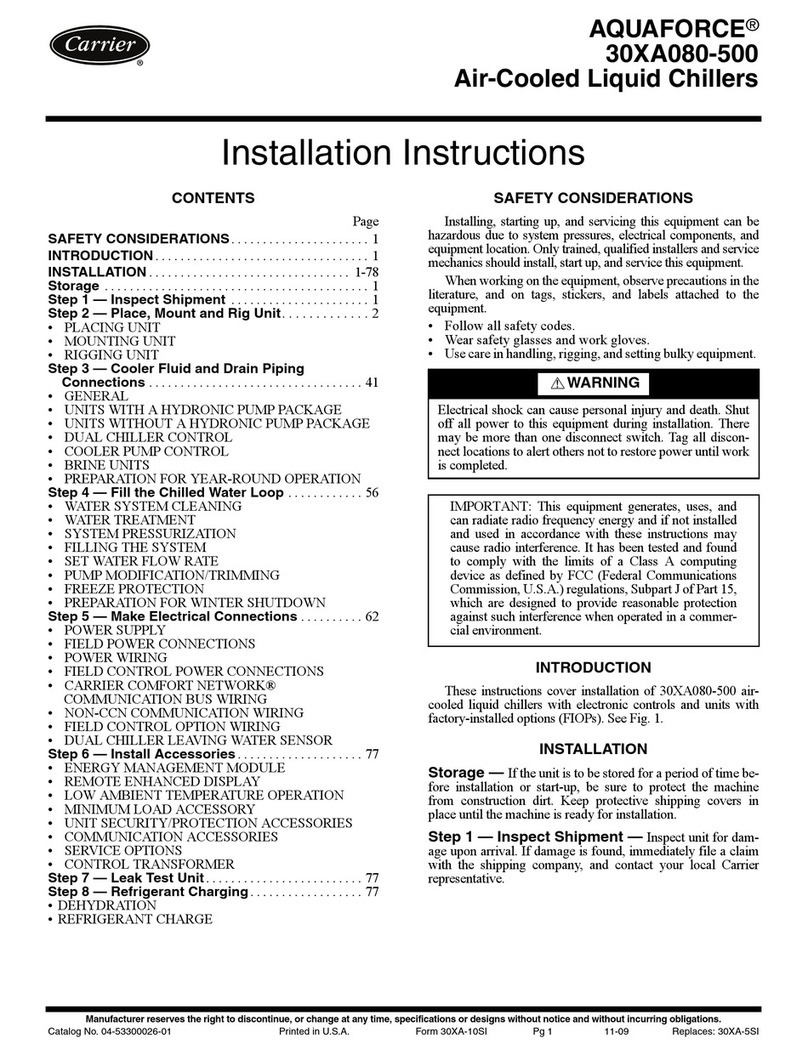
Carrier
Carrier AQUAFORCE 30XA080-500 installation instructions
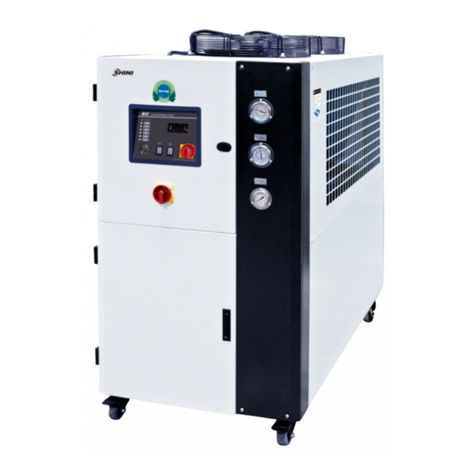
Shini
Shini SIC-A Series manual
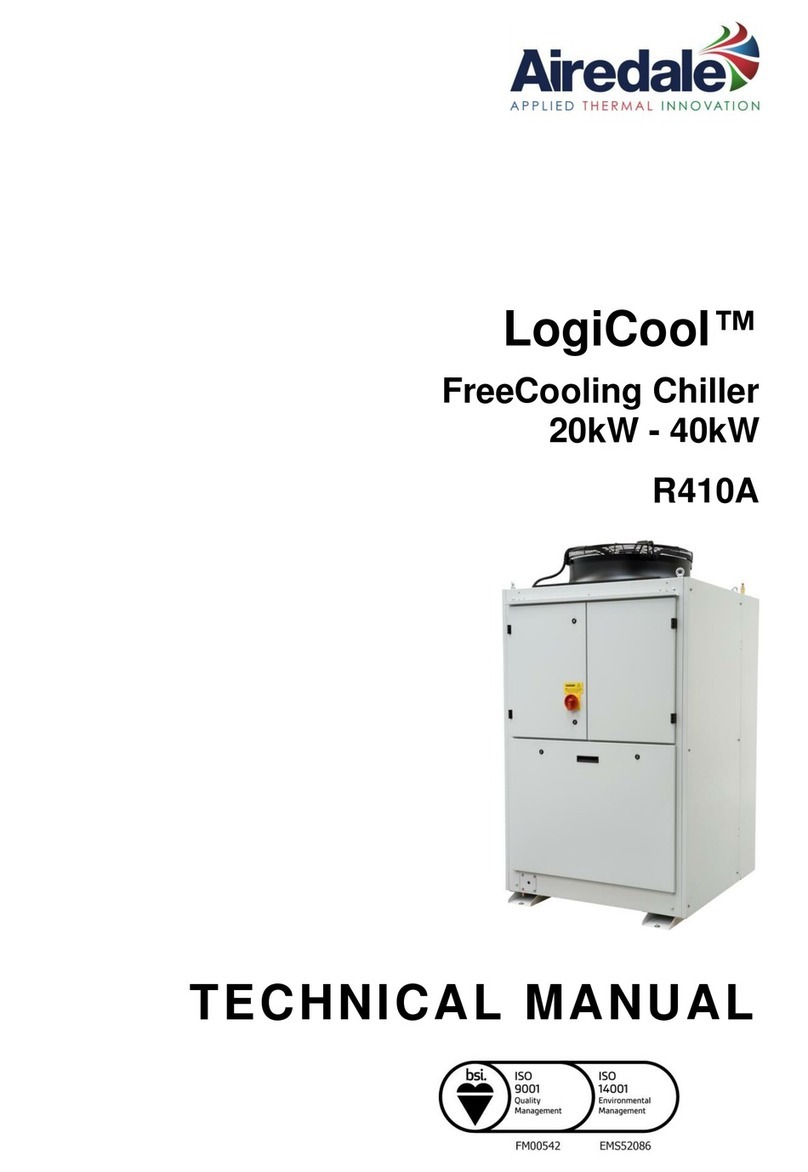
AIREDALE
AIREDALE LogiCool LCC20 Technical manual
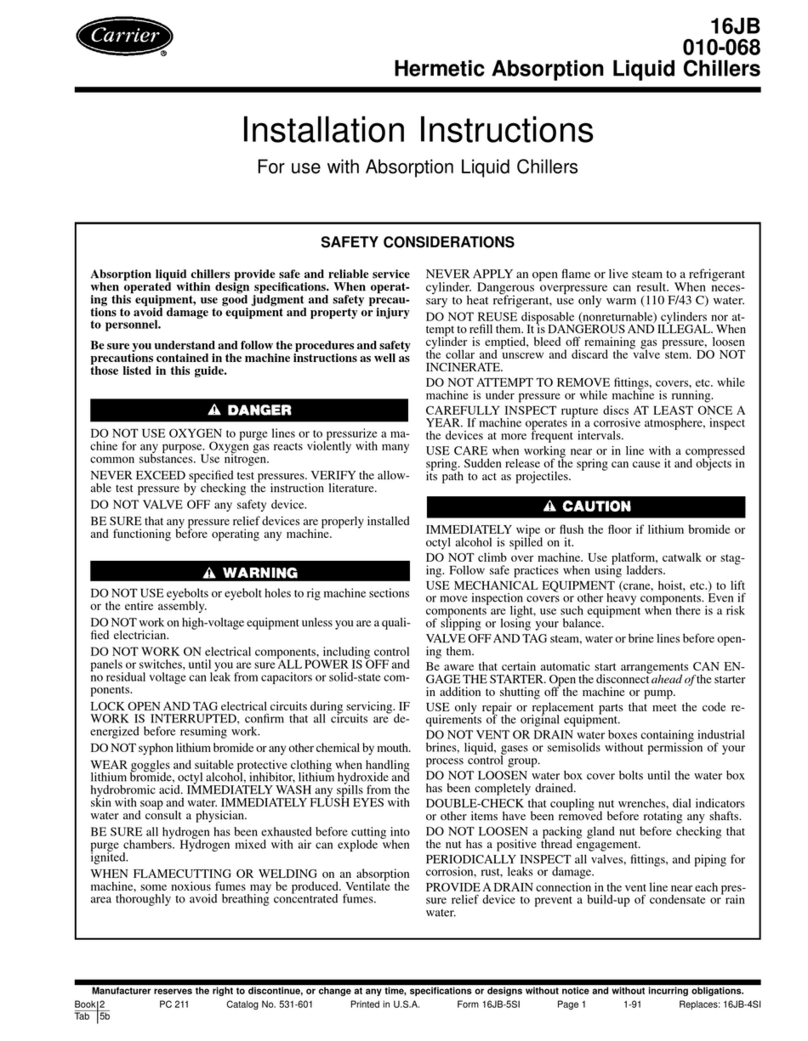
Carrier
Carrier HERMETIC ABSORPTION LIQUID CHILLER 16JB installation instructions
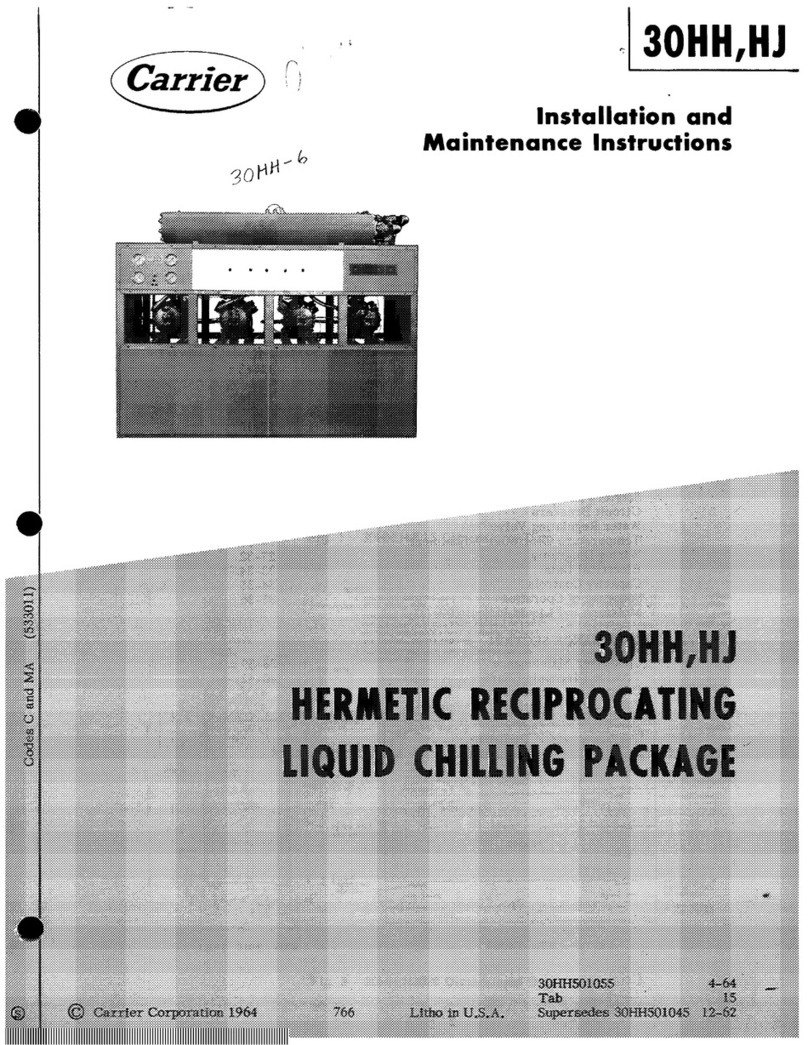
Carrier
Carrier 30HH Installation and maintenance instructions
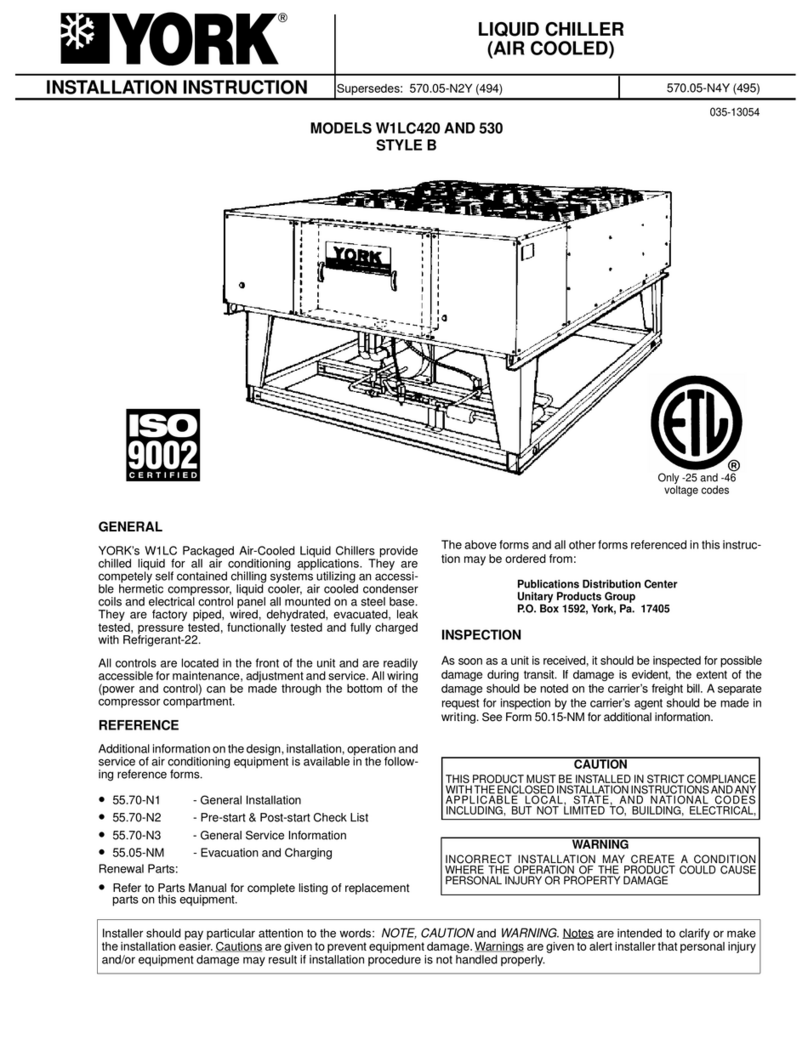
York
York W1LC420 Installation instruction
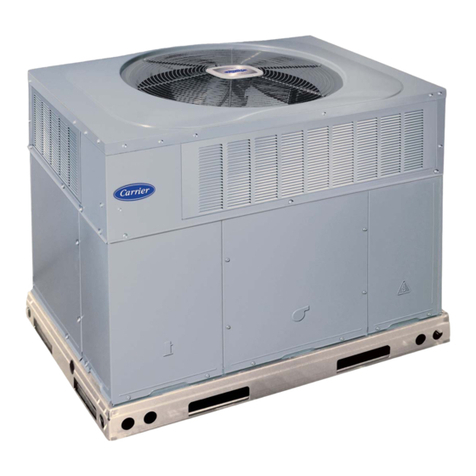
Carrier
Carrier PERFORMANCE 50VT-A24 installation instructions

York
York UL R134A user manual
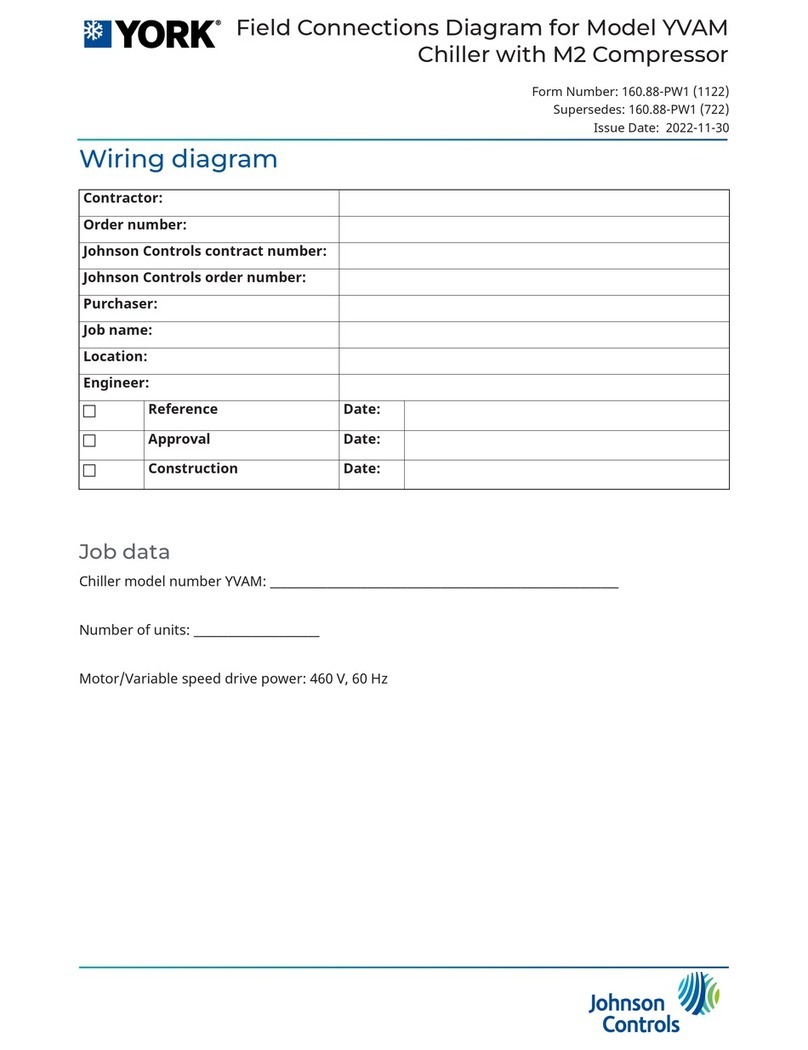
Johnson Controls
Johnson Controls YVAM 350 Wiring diagram
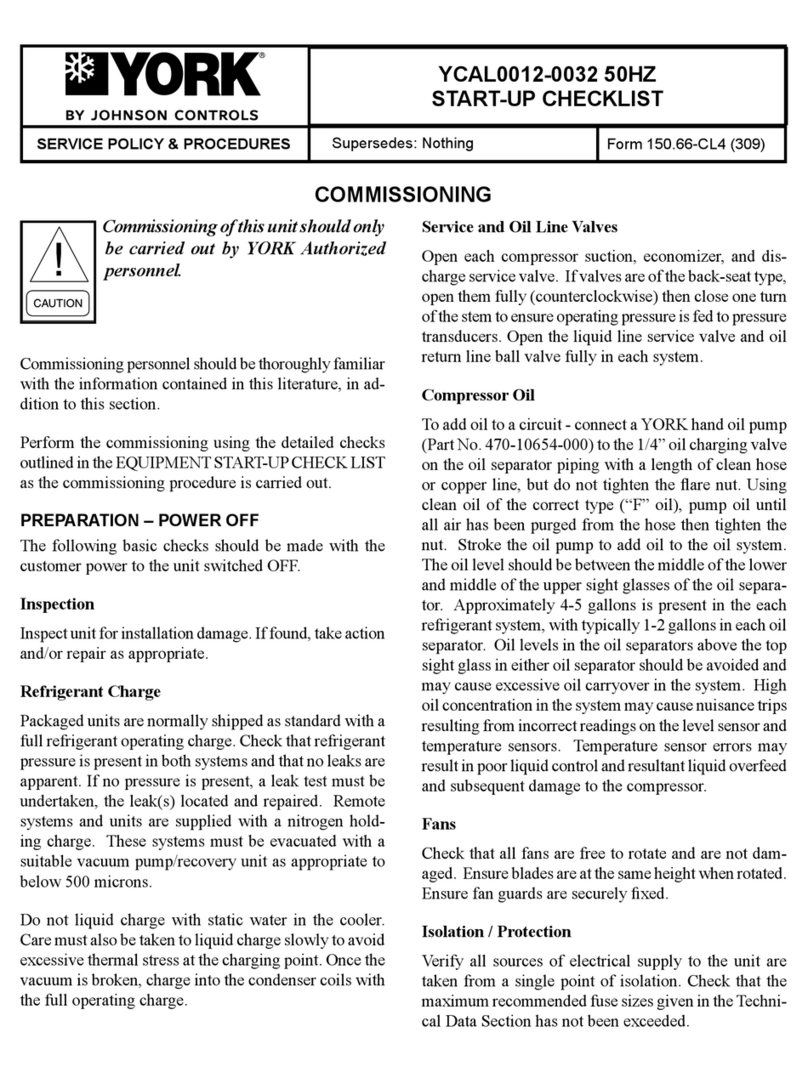
Johnson Controls
Johnson Controls York YCAL0012-0032 Start-Up Checklist
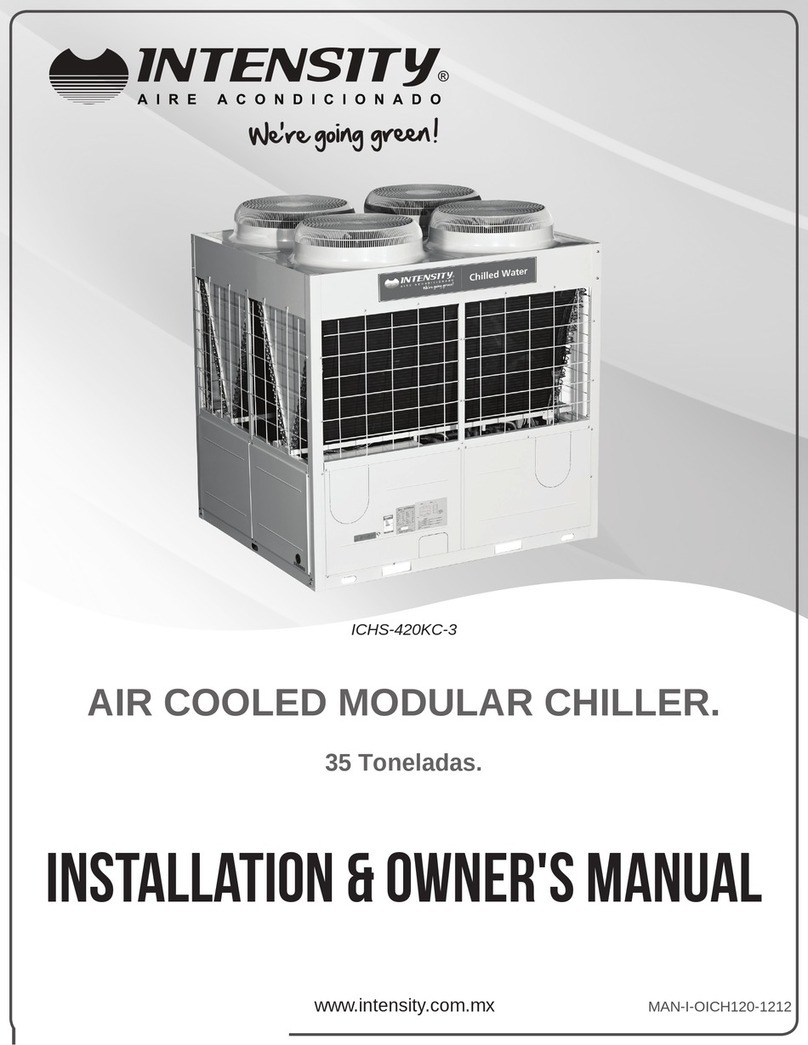
intensity
intensity ICHS-420KC-3 Installation & owner's manual